金属切削过程中的振动与共振现象分析
金属切削过程中的振动对加工质量的影响分析

金属切削过程中的振动对加工质量的影响分析引言:随着工业的发展,金属切削成为了制造过程中常用的方法之一。
然而,金属切削过程中的振动问题一直以来都是一个困扰制造业的难题。
振动不仅会对加工质量造成负面影响,还会导致工具磨损、机械失效、甚至对操作者的健康造成威胁。
因此,深入分析金属切削过程中振动对加工质量的影响,对于提高制造业的效率和质量至关重要。
1. 振动引起的切削质量问题金属切削过程中的振动主要表现为切削面粗糙度增加、切削刃磨损加剧、切削力增大、切削面失真等问题。
振动会使切削刀具发生剧烈振动,导致对工件的切削不稳定,进而影响加工表面的精度。
振动还可能导致刀具切削边缘的磨损加剧,从而缩短刀具的使用寿命。
此外,振动还会在切削过程中产生附加切削力,增加了工件上的切削力,使加工效率降低。
最后,振动还会使金属切削过程中的加工表面发生形变,导致工件的尺寸失准和表面质量下降。
2. 振动的产生机理振动产生的机理包括不平衡力、共振效应、弹性变形和切削参数选择不合理等。
不平衡力是最主要的振动产生机理之一。
不平衡的刀具或工件会在高速旋转时产生力的不平衡,导致振动。
共振效应指的是系统在特定频率下振幅增大的现象,当切削频率接近刚性结构的固有频率时,共振效应会引发严重的振动问题。
弹性变形是由于工件和刀具之间的接触力引起的,当接触面不均匀时会产生振动。
切削参数选择不合理也是引发振动的原因之一,过大或过小的进给量和转速都会导致振动的发生。
3. 减振方法和技术为了降低金属切削过程中的振动对加工质量的影响,需要采取一系列的振动减振方法和技术。
其中包括:a) 刀具结构设计优化:通过设计合适的刀具结构,减少切削过程中产生的不平衡力,降低振动的发生。
b) 切削参数优化:合理选择进给量和转速,避免因切削参数选择不当而引发振动。
c) 刀具磨损监测与更换:定期检查和更换磨损严重的刀具,减少切削过程中的振动。
d) 切削稳定性改善:采用稳定的切削方式,如切削过程中使用软刦等方法,降低振动的发生。
金属切削中的振动现象对刀具磨损的影响

金属切削中的振动现象对刀具磨损的影响切削加工是一种常见的金属加工方法,其通过通过刀具对工件进行削除材料的过程。
然而,在金属切削中,振动现象常常会对刀具产生负面影响,导致刀具的磨损加剧。
本文将讨论振动现象对刀具磨损的影响,并探讨可能的解决方案。
首先,振动现象在金属切削过程中可能引起刀具的不均匀磨损。
振动会导致刀具与工件之间的相对运动受到干扰,使得刀具无法均匀地接触工件表面。
当刀具在振动状态下工作时,刀具的切削力和切削温度会发生变化。
这种不均匀的切削力分布将导致刀具表面的磨损不均匀,使刀具的寿命大大缩短。
其次,振动还可能引起刀具的疲劳破裂。
由于振动会导致刀具产生应力集中,这些应力集中区域容易形成裂纹。
随着切削过程的持续,裂纹将逐渐扩展并最终导致刀具的疲劳破裂。
疲劳破裂会导致刀具的可用寿命大大降低,并且对于高强度材料的切削加工来说尤其严重。
另外,振动还会对切削表面质量产生负面影响。
振动导致切削力的不稳定变化,这将导致切削表面产生不规则的纹理和凹凸不平的表面。
对于需要高精度加工的工件来说,这种表面质量的损坏是无法容忍的。
那么,如何减轻振动现象对刀具磨损的影响呢?首先,优化切削条件是减轻振动现象的关键。
合适的切削速度、进给量和切削深度能够减少切削力的变化,从而降低振动的程度。
此外,选择合适的刀具材料和几何形状也能够减轻振动现象对刀具磨损的影响。
采用具有抗振动能力的刀具材料,如硬质合金,以及刀具几何形状设计上的优化,可以显著降低刀具的磨损。
其次,刀具的装夹和刀具路径的设计也是减轻振动现象的重要因素。
正确的刀具装夹能够减少刀具的振动,并提高切削稳定性。
同时,针对工件和刀具的几何形状特点,设计合理的切削路径也能够减轻振动现象的产生。
采用合理的路径能够平衡切削力,降低振动的风险。
最后,使用先进的切削工具和技术也是减轻振动现象的有效手段。
近年来,先进的切削工具如超硬刀具和复合刀具的发展为减轻振动带来了新的解决方案。
金属加工机械的振动与噪声分析与控制

金属加工机械的振动与噪声分析与控制金属加工机械在生产过程中起着至关重要的作用。
然而,这些机械在运行过程中产生的振动与噪声问题也给生产环境和操作人员带来了许多不便。
本文将重点分析金属加工机械振动与噪声的产生原因,并提出相应的控制措施。
1. 振动与噪声的产生原因金属加工机械在运行过程中,振动与噪声的产生主要可以归结为以下几个方面:1.1 机械结构设计不合理机械结构设计不合理是导致振动与噪声的一个重要原因。
例如,机架的结构刚度不足、零部件之间的配合间隙不当等都会导致机械运行过程中的振动与噪声。
1.2 加工过程中产生的高频振动金属加工过程中,如车削、铣削、磨削等操作产生的高频振动也是振动与噪声的一个重要来源。
这些振动会传播到整个机械结构中,导致噪声的产生。
1.3 机械零件的磨损与故障机械零件在长时间运行过程中,由于磨损和故障,会导致振动与噪声的产生。
例如,轴承磨损、齿轮损坏等都会导致机械运行过程中的振动与噪声。
针对上述振动与噪声的产生原因,可以采取以下控制措施:2.1 优化机械结构设计通过优化机架的结构刚度、合理设置零部件之间的配合间隙等方法,可以有效降低机械运行过程中的振动与噪声。
2.2 采用减振材料和隔振措施在金属加工过程中,采用减振材料和隔振措施可以有效降低高频振动对整个机械结构的影响。
例如,在机械结构中加入橡胶减振垫、采用隔振支架等。
2.3 定期维护和检查通过定期对机械零件进行维护和检查,及时发现并解决磨损和故障问题,可以有效降低振动与噪声的产生。
3. 结论金属加工机械振动与噪声的产生原因复杂多样,需要从多个方面进行分析和控制。
通过优化机械结构设计、采用减振材料和隔振措施以及定期维护和检查,可以有效降低振动与噪声问题,提高生产环境和操作人员的舒适度。
以上内容为金属加工机械振动与噪声分析与控制左右。
后续内容将详细介绍振动与噪声的测量方法、分析手段以及具体的控制方案等。
为了有效地分析和控制金属加工机械的振动与噪声,首先需要对其进行准确的测量。
金属切削中的刀具动态负荷分析与振动控制

金属切削中的刀具动态负荷分析与振动控制随着制造业的发展和技术的进步,金属切削已成为现代加工工艺中不可或缺的环节。
金属材料的切削加工过程中,刀具承受着巨大的动态负荷,而这些负荷会导致刀具的振动,进而影响加工的精度和表面质量。
因此,对金属切削中刀具的动态负荷进行分析和振动控制具有重要意义。
刀具动态负荷分析主要通过建立数学模型来描述切削过程中的力学性能。
一般来说,刀具动态负荷分析需要考虑以下几个方面的因素:首先是切削力的分析。
切削力是指在切削过程中刀具受到的力的大小和方向。
切削力主要由切削阻力和切削热导致的材料变形引起的应力引起。
通过分析切削力的分布和变化规律,可以评估刀具的负荷程度,从而为刀具的设计和选择提供科学依据。
其次是动态特性的分析。
刀具的动态特性是指刀具在受力作用下振动的频率和振幅。
刀具的振动对加工过程和加工结果具有重要影响,因此需要进行动态特性的分析。
常用的分析方法包括有限元分析和模态分析等。
通过这些分析方法,可以得到刀具的振动模态及其频率等关键参数,为后续的振动控制提供依据。
最后是振动控制的方法。
根据刀具的动态特性分析结果,可以采取一系列的振动控制措施来减小刀具的振动。
常见的振动控制方法包括动平衡、刚性支撑和减振器等。
动平衡是指通过增加或减少刀具上的质量分布,使刀具的振动幅值减小。
刚性支撑是指在切削过程中给予刀具充分的支撑,使其振动减小。
减振器是一种通过阻尼材料或装置来减小振动幅值的方法。
通过采取这些振动控制方法,可以有效地降低刀具的振动,提高加工质量和效率。
在金属切削中的刀具动态负荷分析与振动控制中,还需要考虑到刀具和材料之间的磨损和热变形等因素。
刀具的磨损会导致切削力的变化,进而影响刀具的动态负荷和振动。
而材料的热变形会引起刀具的振动,甚至导致刀具的断裂。
因此,在分析和控制刀具的动态负荷时,还需要考虑到这些因素的影响,并采取相应的措施进行修正和优化。
总之,金属切削中的刀具动态负荷分析与振动控制是一项重要的技术研究领域。
剖析金属切削加工中的振动及其抑制措施

剖析金属切削加工中的振动及其抑制措施摘要:金属切削加工中普遍存在振动现象,也是一种无法忽视的有害现象。
如果金属切削加工中出现振动现象,会导致刀具与工件之间产生航相对位移,则会造成加工表面出现振动痕迹,对零件的质量和性能容易造成不良影响。
其振动产生噪音会对人体听力造成损害,对于这些情况则需要对金属切削加工中的振动现象给予重视。
本文主要是对金属切削加工中的振动现象进行了分析,并提出科学合理的抑制措施。
关键词:金属切削加工;振动;抑制措施;引言:在金属切削加工中产生振动是非常普遍的现象,容易对工艺系统的正常切削过程造成不良影响,发生振动现象的原因比较多,一般是因为各种因素的影响所造成的。
但是对其产生原因进行排查和分析,根据分析结果采用具有针对性的抑制措施,便可以在一定程度上抑制振动的产生,同时还能控制振动造成的破坏影响,从而有效提升工件的加工质量,以及延长刀具的使用期限。
1.金属切削加工中振动现象的产生原因比如说在车削加工中也会产生振动,在车床安装的过程中通过加设隔振地基、且保障传动系统并不存在缺陷的情况下,在进行加工的过程中依旧还是会产生一定程度上的振动。
一般来说在金属切削加工中的振动类型分别是:自激振动、强迫振动[1]。
通常在机床中强迫振动的产生频率达到50%~60%,自激振动的产生频率占有40%左右。
1.强迫振动。
其产生原因主要在于在存在不平衡的情况下则会造成离心惯性力,当设备在运行的过程中,其质量存在偏心问题,当机床在运转的时候则会产生离心惯性力,也就是导致机床产生振动的原因。
2.机床传动机构存在缺陷。
一般来说在机床传动系统中的旋转零件,由于在制造的过程中存在误差问题,导致在转动的过程中会形成下干扰力,并且具有周期性的特点,进一步会产生出现强迫振动的激振力。
比如在制造齿轮的时候没有准确把握齿形的制造质量,以及没有精准控制啮合刚度,从而导致齿轮的轴向、切向等产生振动现象,甚至还能通过轴承、轴对其他零部件造成振动影响。
高速切削加工中的振动问题综述
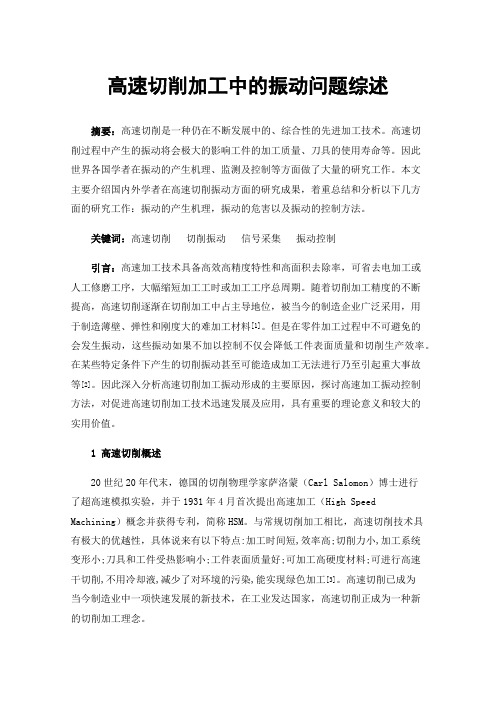
高速切削加工中的振动问题综述摘要:高速切削是一种仍在不断发展中的、综合性的先进加工技术。
高速切削过程中产生的振动将会极大的影响工件的加工质量、刀具的使用寿命等。
因此世界各国学者在振动的产生机理、监测及控制等方面做了大量的研究工作。
本文主要介绍国内外学者在高速切削振动方面的研究成果,着重总结和分析以下几方面的研究工作:振动的产生机理,振动的危害以及振动的控制方法。
关键词:高速切削切削振动信号采集振动控制引言:高速加工技术具备高效高精度特性和高面积去除率,可省去电加工或人工修磨工序,大幅缩短加工工时或加工工序总周期。
随着切削加工精度的不断提高,高速切削逐渐在切削加工中占主导地位,被当今的制造企业广泛采用,用于制造薄壁、弹性和刚度大的难加工材料[1]。
但是在零件加工过程中不可避免的会发生振动,这些振动如果不加以控制不仅会降低工件表面质量和切削生产效率。
在某些特定条件下产生的切削振动甚至可能造成加工无法进行乃至引起重大事故等[2]。
因此深入分析高速切削加工振动形成的主要原因,探讨高速加工振动控制方法,对促进高速切削加工技术迅速发展及应用,具有重要的理论意义和较大的实用价值。
1高速切削概述20世纪20年代末,德国的切削物理学家萨洛蒙(Carl Salomon)博士进行了超高速模拟实验,并于1931年4月首次提出高速加工(High Speed Machining)概念并获得专利,简称HSM。
与常规切削加工相比,高速切削技术具有极大的优越性,具体说来有以下特点:加工时间短,效率高;切削力小,加工系统变形小;刀具和工件受热影响小;工件表面质量好;可加工高硬度材料;可进行高速干切削,不用冷却液,减少了对环境的污染,能实现绿色加工[3]。
高速切削已成为当今制造业中一项快速发展的新技术,在工业发达国家,高速切削正成为一种新的切削加工理念。
2高速切削中的振动在高速铣削过程中,振动现象时有发生。
一般情况,产生振动的原因是多方面的[4]:(1)高速机床结构。
金属切削中的振动与动态切削力检测

金属切削中的振动与动态切削力检测金属切削是制造业中常见的一项技术,广泛应用于机械加工、汽车制造、航空航天等领域。
在金属切削过程中,振动与动态切削力是关键参数,对于切削加工质量的控制和工具寿命的评估具有重要意义。
因此,了解金属切削中的振动与动态切削力检测是十分必要的。
切削振动即工具或工件在切削过程中发生的振动现象。
此振动可能来自于切削力、机械结构刚度、工艺条件等多个方面的因素。
振动不仅会降低加工质量,还可能导致加工中断或工具损坏。
因此,准确检测和分析切削振动对于有效控制切削过程至关重要。
动态切削力是指切削过程中在时间和位置上变化的力。
它受切削速度、进给速度、切削深度等参数的影响,能够反映切削过程中材料的变形、断裂以及切削液的流动等情况。
因此,通过检测和分析动态切削力,可以掌握切削过程中的刀具磨损情况、切削液的流体状态以及加工质量等信息,为切削过程的优化提供依据。
为了准确检测金属切削中的振动与动态切削力,有几种常用的方法可供选择。
首先,常见的方法是使用加速度传感器来检测切削过程中的振动。
这种方法可以将振动信号转化为电信号,并通过信号分析仪器进行处理。
通过分析振动信号的频谱和振幅,可以获得切削过程中的振动变化情况,从而判断切削过程中是否存在异常振动。
其次,动态切削力可以通过力传感器来检测。
这种传感器通过测量切削过程中产生的力大小和方向来获取动态切削力信息。
力传感器通常安装在刀具或切削床上,能够实时监测切削过程中的力变化,并将数据传输给显示仪器进行分析和记录。
通过分析动态切削力曲线,可以推测切削过程中的材料变形、断裂等情况。
此外,还可以使用振动传感器与力传感器相结合的方式进行检测。
振动传感器用于检测振动信号,力传感器用于检测动态切削力信号。
这种方法能够全面综合分析振动和切削力信息,提供更准确的切削过程监测结果。
通过对振动和切削力数据的联合分析,可以更好地掌握切削过程中的变化规律,提高加工质量和效率。
综上所述,金属切削中的振动与动态切削力检测是重要的技术。
车削加工中振动产生原因及消除措施

车削加工中振动产生原因及消除措施摘要:工作人员在进行车削加工时不难发现会导致一定的振动,这种振动使正常的加工系统受到影响,影响正常的工作甚至加工产品的外表,因为振动系统受损后导致外观模型变样。
一旦发生这种情况,还会导致整个车削加工加床和刀片的受损,从而大大降低工作效率,影响工作人员的工作情绪。
如果降低一定的噪音,则可以提升工作效率,所以掌握车削加工中导致产生振动的原因十分重要。
关键词:车削加工;振动;原因引言在进行车削加工过程中,导致振动的现象有很多,文章主要针对产生原因,根据不同振动现象提出了相应的改善建议和改进措施。
希望能够对车削加工提供一定的帮助,大大减少车削加工过程中所产的噪音和振动,从而提高加工效率,减轻工作人员的烦躁情绪,使加工人员能够更好地投入到工作中。
1振动的类型在机械加工中产生的振动,按产生的原因来分类,都具有自由振动、受迫振动和自激振动,与机床、夹具、刀具和工件组成的工艺系统的动态特性有关。
自由振动是当振动系统的平衡被破坏,由弹性力来维持系统的振动。
是切削力的突然变化或其它外力冲击引起的。
可快速衰减,对车床加工影响非常小,可忽略不计。
受迫振动产生的原因是由系统外部或内部周期变化的激振力(也叫振源)的作用下而产生的振动,共振是受迫振动中的一个特例。
此振动主要由以下几方面原因产生高速回转存在不不衡,例如卡盘和工件、主轴、电动机转子、带轮等。
就是因为零件的不平衡而产生激振力F(也叫离心惯性力),车床传动存在误差,车床传动当中的齿轮组,由于制造误差、装配误差产生了周期变化的激振力;液压传动中油液脉动、轴承滚动体尺寸差、皮带接缝等因素。
自激振动是在没有外激励作用的情况下由系统自身激发所产生的一种振动,特点是一种不衰减的振动过程本身能引起周期性变化的力,此力可从非交变特性的能源中周期性地获得能量的补充,以维持这个振动。
主要是车削过程中工件系统的弯曲振动(低频振动)和车刀的变形产生的弯曲振动(高频振动)。
机床切削时的振动分析及预防措施
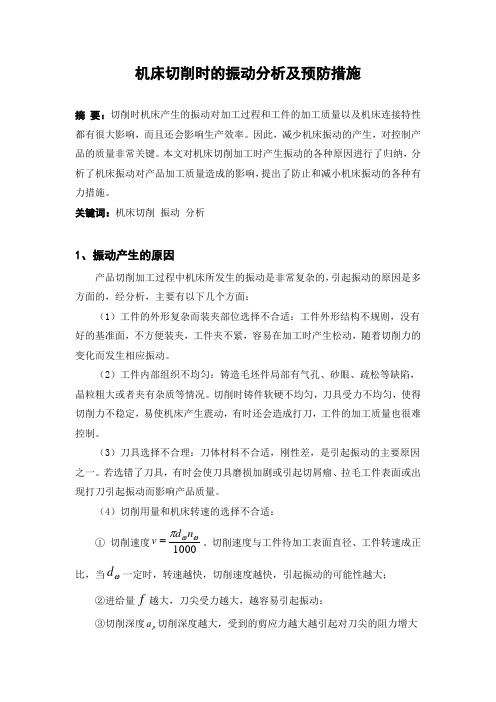
机床切削时的振动分析及预防措施摘 要:切削时机床产生的振动对加工过程和工件的加工质量以及机床连接特性都有很大影响,而且还会影响生产效率。
因此,减少机床振动的产生,对控制产品的质量非常关键。
本文对机床切削加工时产生振动的各种原因进行了归纳,分析了机床振动对产品加工质量造成的影响,提出了防止和减小机床振动的各种有力措施。
关键词:机床切削 振动 分析1、振动产生的原因产品切削加工过程中机床所发生的振动是非常复杂的,引起振动的原因是多方面的,经分析,主要有以下几个方面:(1)工件的外形复杂而装夹部位选择不合适:工件外形结构不规则,没有好的基准面,不方便装夹,工件夹不紧,容易在加工时产生松动,随着切削力的变化而发生相应振动。
(2)工件内部组织不均匀:铸造毛坯件局部有气孔、砂眼、疏松等缺陷,晶粒粗大或者夹有杂质等情况。
切削时铸件软硬不均匀,刀具受力不均匀,使得切削力不稳定,易使机床产生震动,有时还会造成打刀,工件的加工质量也很难控制。
(3)刀具选择不合理:刀体材料不合适,刚性差,是引起振动的主要原因之一。
若选错了刀具,有时会使刀具磨损加剧或引起切屑瘤、拉毛工件表面或出现打刀引起振动而影响产品质量。
(4)切削用量和机床转速的选择不合适:① 切削速度1000ωωπn d v =。
切削速度与工件待加工表面直径、工件转速成正比,当ωd 一定时,转速越快,切削速度越快,引起振动的可能性越大; ②进给量f 越大,刀尖受力越大,越容易引起振动:③切削深度p a 切削深度越大,受到的剪应力越大越引起对刀尖的阻力增大而引起振动。
(5)机床自身状况的影响机床本身的精度不够也是振动产生的一个方面。
机床主轴箱内各啮合齿轮、轴承等配合精度低,导轨的磨损,各夹紧装置的不可靠等,在切削中都可能产生振动。
(6)机床周围环境的影响附近有产生振动的大型设备,或有重型车辆在行驶,引起地基振动,并传递到床身.易造成共振。
2、振动对加工质量的影响振动对加工质量的影响是非常大的,主要表现在以下几个方面:(1)加工过程中的振动降低了加工表面的质量,引起加工表面的振动波纹,表面粗糙度值大。
金属切削中刀具振动与共振的原因与解决方法
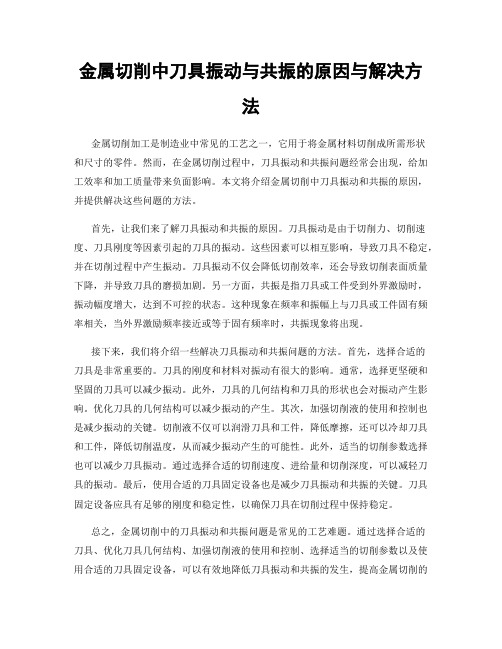
金属切削中刀具振动与共振的原因与解决方法金属切削加工是制造业中常见的工艺之一,它用于将金属材料切削成所需形状和尺寸的零件。
然而,在金属切削过程中,刀具振动和共振问题经常会出现,给加工效率和加工质量带来负面影响。
本文将介绍金属切削中刀具振动和共振的原因,并提供解决这些问题的方法。
首先,让我们来了解刀具振动和共振的原因。
刀具振动是由于切削力、切削速度、刀具刚度等因素引起的刀具的振动。
这些因素可以相互影响,导致刀具不稳定,并在切削过程中产生振动。
刀具振动不仅会降低切削效率,还会导致切削表面质量下降,并导致刀具的磨损加剧。
另一方面,共振是指刀具或工件受到外界激励时,振动幅度增大,达到不可控的状态。
这种现象在频率和振幅上与刀具或工件固有频率相关,当外界激励频率接近或等于固有频率时,共振现象将出现。
接下来,我们将介绍一些解决刀具振动和共振问题的方法。
首先,选择合适的刀具是非常重要的。
刀具的刚度和材料对振动有很大的影响。
通常,选择更坚硬和坚固的刀具可以减少振动。
此外,刀具的几何结构和刀具的形状也会对振动产生影响。
优化刀具的几何结构可以减少振动的产生。
其次,加强切削液的使用和控制也是减少振动的关键。
切削液不仅可以润滑刀具和工件,降低摩擦,还可以冷却刀具和工件,降低切削温度,从而减少振动产生的可能性。
此外,适当的切削参数选择也可以减少刀具振动。
通过选择合适的切削速度、进给量和切削深度,可以减轻刀具的振动。
最后,使用合适的刀具固定设备也是减少刀具振动和共振的关键。
刀具固定设备应具有足够的刚度和稳定性,以确保刀具在切削过程中保持稳定。
总之,金属切削中的刀具振动和共振问题是常见的工艺难题。
通过选择合适的刀具、优化刀具几何结构、加强切削液的使用和控制、选择适当的切削参数以及使用合适的刀具固定设备,可以有效地降低刀具振动和共振的发生,提高金属切削的效率和质量。
这些方法不仅适用于金属切削加工,也适用于其他领域中涉及刀具振动和共振问题的加工过程。
金属材料加工中的振动利用问题分析
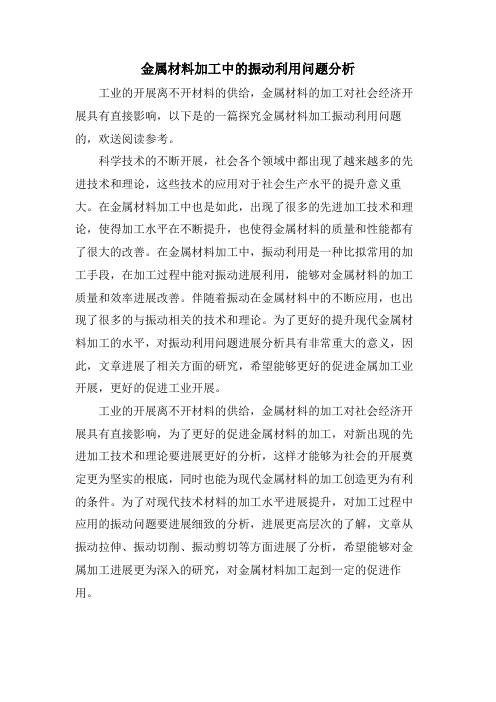
金属材料加工中的振动利用问题分析工业的开展离不开材料的供给,金属材料的加工对社会经济开展具有直接影响,以下是的一篇探究金属材料加工振动利用问题的,欢送阅读参考。
科学技术的不断开展,社会各个领域中都出现了越来越多的先进技术和理论,这些技术的应用对于社会生产水平的提升意义重大。
在金属材料加工中也是如此,出现了很多的先进加工技术和理论,使得加工水平在不断提升,也使得金属材料的质量和性能都有了很大的改善。
在金属材料加工中,振动利用是一种比拟常用的加工手段,在加工过程中能对振动进展利用,能够对金属材料的加工质量和效率进展改善。
伴随着振动在金属材料中的不断应用,也出现了很多的与振动相关的技术和理论。
为了更好的提升现代金属材料加工的水平,对振动利用问题进展分析具有非常重大的意义,因此,文章进展了相关方面的研究,希望能够更好的促进金属加工业开展,更好的促进工业开展。
工业的开展离不开材料的供给,金属材料的加工对社会经济开展具有直接影响,为了更好的促进金属材料的加工,对新出现的先进加工技术和理论要进展更好的分析,这样才能够为社会的开展奠定更为坚实的根底,同时也能为现代金属材料的加工创造更为有利的条件。
为了对现代技术材料的加工水平进展提升,对加工过程中应用的振动问题要进展细致的分析,进展更高层次的了解,文章从振动拉伸、振动切削、振动剪切等方面进展了分析,希望能够对金属加工进展更为深入的研究,对金属材料加工起到一定的促进作用。
在常规的金属材料加工过程中,振动是一种不希望出现的因素,主要是因为振动会导致金属材料的加工进度受到影响,同时对金属材料的性能也能产生一定的影响。
因此,在金属材料加工过程中,对振动进展应用能够减小振动带来的影响,同时也能够对加工效率以及加工质量进展提高。
很多的专家学者对金属材料加工过程中存在的振动问题进展了研究,对如何消除振动问题一直没有找到很好的解决措施,因此,在金属材料加工中对振动进展了利用,这样将之前出现的弊端转化为了优势,不仅仅对振动问题进展了解决,同时,也提高了加工质量。
金属切削中的刀具振动与热变形分析

金属切削中的刀具振动与热变形分析金属切削是制造业中常见的工艺过程之一,而刀具振动与热变形是影响切削质量和效率的重要因素。
本文将从理论与实践两方面进行探讨,并提出相应的分析方法和改进措施。
刀具振动是切削中常见的问题,它会导致切削表面质量下降、刀具寿命缩短甚至工件退正。
刀具振动的主要原因有切削力不平衡、刀具结构刚度不足、刃粒堆积等。
其中,切削力不平衡是最主要的因素之一。
切削力不平衡是由于切削过程中刀具与工件之间存在的刃粒堆积导致的。
切削力越大,刀具振动越严重。
此外,刀具结构刚度不足也会导致刀具振动。
传统的刀具结构通常是一根刚性的杆状物,但这种结构容易发生弯曲和振动。
刀具结构刚度不足会导致刃部挠曲和刀具弯曲,进而产生振动。
为了降低刀具振动,在设计阶段可以采取一些措施。
首先,针对切削力不平衡问题,可以通过提高刀具的刚度和加强冷却条件来减少振动。
其次,可以通过优化刃部几何形状和切削参数选择来降低振动。
刃部几何形状的优化可以提高切削刚度,增加切削效率,减少切削力。
切削参数选择的优化可以降低切削张力,减少切削力不平衡的可能性。
另一个影响金属切削过程的因素是刀具的热变形。
在切削过程中,刀具表面因摩擦和切削热而受热,进而导致刀具的热膨胀和热变形。
这些热变形会直接影响切削质量和尺寸精度。
热变形的主要原因是刀具材料的热膨胀系数不同导致的温度差。
而材料的热膨胀系数又会受到切削参数、冷却方式、刀具材料等因素的影响。
为了减少刀具的热变形,可以采取一些措施。
首先,可采用合适的切削参数和冷却方式,以降低刀具表面的温度。
其次,可以选择具有良好热导性的刀具材料,以增加热量的传导速度。
此外,还可以通过刀具表面的涂层来改善机床刀具的热稳定性。
涂层可以提高切削温度的承载能力,防止刀具表面的粘着和氧化。
综上所述,金属切削中的刀具振动与热变形是影响切削质量和效率的重要因素。
在刀具设计阶段,可以采取合理的刃部几何形状和切削参数选择来降低振动。
金属切削中刀具振动的原因及控制方法研究
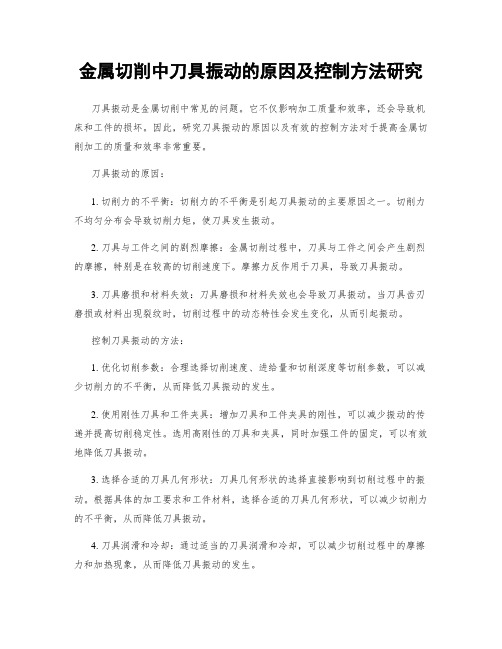
金属切削中刀具振动的原因及控制方法研究刀具振动是金属切削中常见的问题。
它不仅影响加工质量和效率,还会导致机床和工件的损坏。
因此,研究刀具振动的原因以及有效的控制方法对于提高金属切削加工的质量和效率非常重要。
刀具振动的原因:1. 切削力的不平衡:切削力的不平衡是引起刀具振动的主要原因之一。
切削力不均匀分布会导致切削力矩,使刀具发生振动。
2. 刀具与工件之间的剧烈摩擦:金属切削过程中,刀具与工件之间会产生剧烈的摩擦,特别是在较高的切削速度下。
摩擦力反作用于刀具,导致刀具振动。
3. 刀具磨损和材料失效:刀具磨损和材料失效也会导致刀具振动。
当刀具齿刃磨损或材料出现裂纹时,切削过程中的动态特性会发生变化,从而引起振动。
控制刀具振动的方法:1. 优化切削参数:合理选择切削速度、进给量和切削深度等切削参数,可以减少切削力的不平衡,从而降低刀具振动的发生。
2. 使用刚性刀具和工件夹具:增加刀具和工件夹具的刚性,可以减少振动的传递并提高切削稳定性。
选用高刚性的刀具和夹具,同时加强工件的固定,可以有效地降低刀具振动。
3. 选择合适的刀具几何形状:刀具几何形状的选择直接影响到切削过程中的振动。
根据具体的加工要求和工件材料,选择合适的刀具几何形状,可以减少切削力的不平衡,从而降低刀具振动。
4. 刀具润滑和冷却:通过适当的刀具润滑和冷却,可以减少切削过程中的摩擦力和加热现象,从而降低刀具振动的发生。
5. 刀具动态平衡:对于高速切削、精密加工等对刀具平衡性要求较高的场景,可以采用动态平衡技术,通过对刀具进行平衡校正,减少刀具振动的产生。
6. 切削液的选择:使用适合切削工艺的切削液,可以帮助减少切削力和摩擦,从而减小刀具振动。
总结:金属切削中刀具振动的原因复杂多样,但通过合理优化切削参数、使用刚性刀具和工件夹具、选择合适的刀具几何形状、刀具润滑和冷却、刀具动态平衡以及切削液的选择等控制方法,可以有效地降低刀具振动的发生。
对于提高金属切削加工的质量和效率具有重要的意义。
金属切削原理与刀具切削过程中的振动分析

金属切削原理与刀具切削过程中的振动分析金属切削是一种常见的加工方法,广泛应用于制造业中。
在金属切削过程中,刀具与工件的相对运动会引发振动现象,这种振动对刀具的寿命和加工质量都有着重要的影响。
因此,对金属切削原理和刀具切削过程中的振动进行分析和研究,有助于优化加工过程,提高切削效率与加工质量。
金属切削原理是指在加工过程中,刀具对工件施加一定的切削力,以达到去除工件材料的目的。
刀具切削过程中的振动是由多种因素引起的,包括刀具材料和几何参数、切削速度与进给速度、加工液等。
其中,刀具材料和几何参数对振动的影响较为显著。
刀具材料决定了刀具的硬度、强度和耐磨性,对切削振动有重要影响。
通常情况下,刀具应具有较高的硬度和强度,以保证在切削过程中不易发生塑性变形和断裂。
如果刀具硬度过低,容易造成刀具齿刃的快速磨损,导致振动加剧。
刀具的几何参数,如刀尖半径、后角、刀片刃数等,也会对振动产生影响。
较大的刀尖半径或后角会导致切削过程中的力矩增大,从而引发振动,而合适的刀片刃数能够减轻振动的产生。
切削速度和进给速度也是影响振动的重要因素。
较高的切削速度和进给速度会增加切削力,从而导致振动加剧。
因此,在实际切削过程中,需要根据工件材料和形状选择合适的切削速度和进给速度,以降低切削振动的发生。
加工液在金属切削过程中也扮演着重要的角色。
适量的加工液可以起到润滑冷却的作用,减少热量积聚和摩擦,降低振动的产生。
合理选择和使用加工液,可以显著改善切削过程中的振动情况。
对于刀具切削过程中的振动进行分析,有助于优化切削过程,提高加工效率与加工质量。
常见的振动分析方法包括模态分析和频谱分析。
模态分析是指通过计算机仿真或实验测试,确定切削系统的固有频率和振型。
通过模态分析,能够了解切削系统在不同工况下的振动特性,为避免共振现象、减轻振动干扰提供依据。
频谱分析则是通过采集切削过程中的振动信号,并将其转换成频谱图。
通过分析频谱图,可以判断振动频率的分布情况,确定引起振动的原因,并进一步优化切削参数和刀具结构。
金属切削加工中的振动分析及控制途径

金属切削加工中的振动分析及控制途径摘要:在金属切削加工过程中,如果产生振动,会造成很多不良的影响,不仅严重影响机器和零部件本身的性能和工艺,而且振动中产生的噪音还会对操作者本身的身体健康产生有害的影响。
本文将通过分析金属切削加工中产生振动的原因、主要类型和特点,重点提出控制甚至消除振动的有效途径,以促进金属切削加工技术的发展。
关键词:切削加工振动原因振动类型振动特点控制途径引言:近些年来,随着机械制造行业的不断发展,各种先进的制造技术也不断被研发出来,金属切削加工则是这些技术中的佼佼者,已经被应用到各个领域的机械制造和生产中。
在设计机床和刀具、制订机器零件的切削工艺及其定额、合理地使用刀具和机床以及控制切削过程时,都要利用金属切削原理的研究成果,使机器零件的加工达到经济、优质和高效率的目的。
金属切削加工过程中,刀具与工件之间相互作用和各自的变化规律现已经成为了一门学科。
在金属切削加工过程中,如果产生振动,会造成很多不良的影响,不仅严重影响机器和零部件本身的性能和工艺,而且振动中产生的噪音还会对操作者本身的身体健康产生有害的影响。
下面本文将通过分析金属切削加工中产生振动的原因、主要类型和特点,重点提出控制甚至消除振动的有效途径。
一、振动的基本类型从一般情况而言,在金属切削加工过程中所产生的振动大致可以分为两种类型,即:自激振动和强迫振动。
相比较而言,这两种振动中自激振动的概论一般低于40%,而强迫振动则占主要方面,大约为60%。
二、产生振动的主要原因通过统计分析我们可以清晰的看出,金属切削加工过程中产生振动的类型基本分为两种:自激振动和受迫振动。
因此,在机械制造过程中,根据这两种不同类型的振动,可以通过机床不同的运行状态来分析振动产生的原因。
(一)空转时存在的振动及原因分析当机床在空转时也有可能产生一定的振动。
造成振动的主要原因可能是床鞍导轨之间的爬行,也可能是是由于外部传来的振动,例如:地基周期或者非周期的干扰力。
机床切削时的振动分析
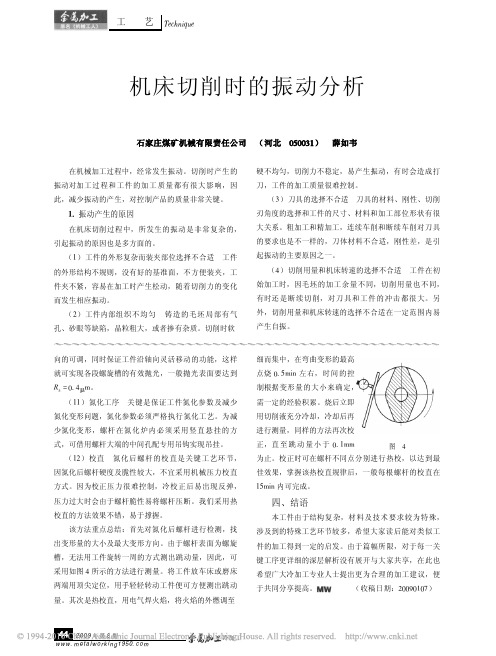
!" 振动产生的原因
在机床切削过程中,所发生的振动是非常复杂的, 引起振动的原因也是多方面的。 ( " ) 工件的外形复杂而装夹部位选择不合适 ! 工件 的外形结构不规则,没有好的基准面,不方便装夹,工 件夹不紧,容易在加工时产生松动,随着切削力的变化 而发生相应振动。 ( # ) 工件内部组织不均匀 ! 铸造的毛坯局部有气 孔、砂眼等缺陷,晶粒粗大,或者掺有杂质。切削时软
由于篇幅所限对于每一关键工序更详细的深层解析没有展开与大家共享在此也希望广大冷加工专业人士提出更为合理的加工建议便于共同分享提高
! ! ! ! ! ! !
工! ! 艺
!"#$%&’("
! ! !
机床切削时的振动分析
石家庄煤矿机械有限责任公司! ( 河北 ! "#""$% ) ! 薛如韦
! ! 在机械加工过程中,经常发生振动。切削时产生的 振动对加工过程和工件的加工质量都有很大影响,因 此,减少振动的产生,对控制产品的质量非常关键。 硬不均匀,切削力不稳定,易产生振动,有时会造成打 刀,工件的加工质量很难控制。 ( $ ) 刀具的选择不合适! 刀具的材料、刚性、切削 刃角度的选择和工件的尺寸、材料和加工部位形状有很 大关系。粗加工和精加工,连续车削和断续车削对刀具 的要求也是不一样的,刀体材料不合适,刚性差,是引 起振动的主要原因之一。 ( % ) 切削用量和机床转速的选择不合适 ! 工件在初 始加工时,因毛坯的加工余量不同,切削用量也不同, 有时还是断续切削,对刀具和工件的冲击都很大。另 外,切削用量和机床转速的选择不合适在一定范围内易 产生自振。
!" 振动对加工质量的影响
振动对加工质量的影响是非常大的,主要表现在以 下几个方面: ( $ ) 振动降低了加工表面的质量! 加工过程中的振 动,引起加工表面的振动波纹,表面粗糙度值大。它还 会使工件和刀具之间产生相对位移,影响正常的运动轨 迹。这样,就降低了加工表面的质量和尺寸精度。 ( % ) 降低了刀具的使用寿命! 由于振动的产生,影 响刀具的正常切削条件,加快了刀具的磨损,甚至会引 起切削刃的崩裂,大大降低了刀具的使用寿命。 ( & ) 影响和降低了生产效率 ! 为了避免剧烈的振 动,不得不降低切削用量。同时,由于降低了刀具的使 用寿命,频繁换刀、磨刀,使生产效率下降。 ( ’ ) 使机床的原始精度下降! 由于振动使机床的运 动元件之间松动,间隙增大,加快了机床零件的磨损, 造成机床精度下降,影响切削质量,降低机床的使用寿 命。 ( " ) 影响工作环境! 因振动会产生刺耳的噪声,使 操作者的身心健康受到损害,降低工作效率。
金属切削过程中的刀具振动及其影响分析
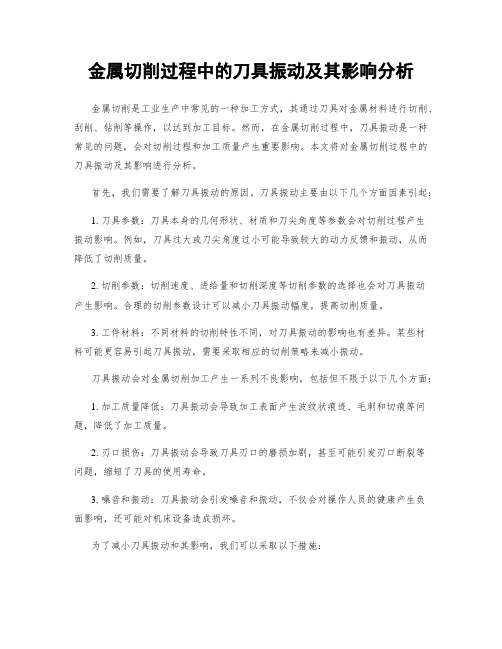
金属切削过程中的刀具振动及其影响分析金属切削是工业生产中常见的一种加工方式,其通过刀具对金属材料进行切削、刮削、钻削等操作,以达到加工目标。
然而,在金属切削过程中,刀具振动是一种常见的问题,会对切削过程和加工质量产生重要影响。
本文将对金属切削过程中的刀具振动及其影响进行分析。
首先,我们需要了解刀具振动的原因。
刀具振动主要由以下几个方面因素引起:1. 刀具参数:刀具本身的几何形状、材质和刀尖角度等参数会对切削过程产生振动影响。
例如,刀具过大或刀尖角度过小可能导致较大的动力反馈和振动,从而降低了切削质量。
2. 切削参数:切削速度、进给量和切削深度等切削参数的选择也会对刀具振动产生影响。
合理的切削参数设计可以减小刀具振动幅度,提高切削质量。
3. 工件材料:不同材料的切削特性不同,对刀具振动的影响也有差异。
某些材料可能更容易引起刀具振动,需要采取相应的切削策略来减小振动。
刀具振动会对金属切削加工产生一系列不良影响,包括但不限于以下几个方面:1. 加工质量降低:刀具振动会导致加工表面产生波纹状痕迹、毛刺和切痕等问题,降低了加工质量。
2. 刃口损伤:刀具振动会导致刀具刃口的磨损加剧,甚至可能引发刃口断裂等问题,缩短了刀具的使用寿命。
3. 噪音和振动:刀具振动会引发噪音和振动,不仅会对操作人员的健康产生负面影响,还可能对机床设备造成损坏。
为了减小刀具振动和其影响,我们可以采取以下措施:1. 优化刀具设计:合理选择刀具的几何形状、材质和刀尖角度等参数,以减小刀具振动。
同时,确保刀具的精确加工和保持刀具的锐利度。
2. 调整切削参数:根据具体切削情况,合理选择切削速度、进给量和切削深度等参数,以减小刀具振动的幅度。
经过试验和实践,确定合适的切削参数范围。
3. 选择合适的冷却润滑剂:适当使用冷却润滑剂,可以降低刀具温度,减小刀具振动。
冷却润滑剂还可以减少切削力和切削温度,提高工件表面质量。
4. 定期维护和检修设备:及时保养和更换机床设备和刀具,以保持其良好状况。
金属切削过程中由受迫振动引起的振纹诊断
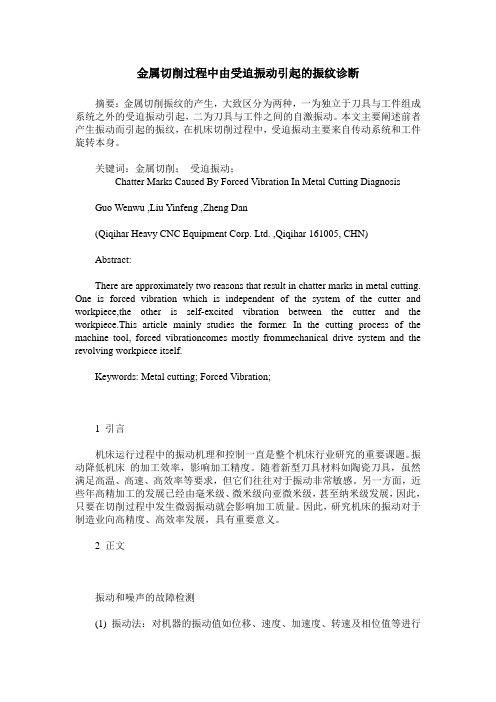
金属切削过程中由受迫振动引起的振纹诊断摘要:金属切削振纹的产生,大致区分为两种,一为独立于刀具与工件组成系统之外的受迫振动引起,二为刀具与工件之间的自激振动。
本文主要阐述前者产生振动而引起的振纹,在机床切削过程中,受迫振动主要来自传动系统和工件旋转本身。
关键词:金属切削;受迫振动;Chatter Marks Caused By Forced Vibration In Metal Cutting Diagnosis Guo Wenwu ,Liu Yinfeng ,Zheng Dan(Qiqihar Heavy CNC Equipment Corp. Ltd. ,Qiqihar 161005, CHN)Abstract:There are approximately two reasons that result in chatter marks in metal cutting. One is forced vibration which is independent of the system of the cutter and workpiece,the other is self-excited vibration between the cutter and the workpiece.This article mainly studies the former. In the cutting process of the machine tool, forced vibrationcomes mostly frommechanical drive system and the revolving workpiece itself.Keywords: Metal cutting; Forced Vibration;1 引言机床运行过程中的振动机理和控制一直是整个机床行业研究的重要课题。
振动降低机床的加工效率,影响加工精度。
- 1、下载文档前请自行甄别文档内容的完整性,平台不提供额外的编辑、内容补充、找答案等附加服务。
- 2、"仅部分预览"的文档,不可在线预览部分如存在完整性等问题,可反馈申请退款(可完整预览的文档不适用该条件!)。
- 3、如文档侵犯您的权益,请联系客服反馈,我们会尽快为您处理(人工客服工作时间:9:00-18:30)。
金属切削过程中的振动与共振现象分析
摘要:金属切削过程中的振动与共振现象对切削效果和加工精度有着重要影响。
本文通过分析金属切削中的振动与共振现象,探讨了造成振动和共振的原因,以及采取的一些控制措施。
通过合理的切削参数选择、工具结构设计和切削工艺优化等措施,可以降低振动和共振现象,提高金属切削加工的质量和效率。
1. 引言
金属切削作为现代制造业中常用的一种加工方法,广泛应用于机械、汽车、航
空等领域。
然而,在金属切削过程中经常会遇到振动和共振现象,导致切削效果和加工精度下降,甚至带来安全隐患。
因此,研究金属切削中的振动与共振现象是提高切削质量和效率的重要问题。
2. 振动与共振现象的原因
2.1 切削力激振
金属切削过程中,切削力是主要的激振源。
当切削力在切削过程中频繁变化时,容易引起工件和刀具系统的振动。
切削力的大小和方向都会对振动引起的频率、振幅和相位角等产生影响。
2.2 切削系统的刚度和阻尼
切削系统的刚度和阻尼是影响振动和共振现象的重要因素。
刚度过低会导致切
削系统产生过大的挠度和变形,从而引起振动和共振。
而刚度过高会导致共振频率过高,难以找到合适的激振频率,也容易引起振动和共振。
阻尼过低则不利于振动的消除,阻尼过高则会降低系统的灵敏度。
3. 振动与共振的影响
3.1 切削质量与效率下降
金属切削中的振动和共振现象会导致加工表面粗糙度增加、刀具寿命缩短、加工精度降低等问题,从而影响切削质量和工件的功能性能。
同时,振动和共振还会降低切削效率,增加切削成本。
3.2 安全隐患
振动和共振现象引起的高频振动会对切削系统和机械结构产生巨大的冲击和振动载荷,不仅会导致设备破坏,还可能造成安全事故。
因此,控制振动和共振现象也是确保切削操作安全的重要措施。
4. 振动与共振的控制策略
4.1 合理选择切削参数
合理选择切削参数是控制金属切削过程中振动和共振现象的关键。
通过调整进给速度、切削深度和切削速度等参数,可以控制切削力的大小和方向,从而减小振动和共振的产生。
4.2 优化工具的结构设计
优化工具的结构设计是降低振动和共振现象的有效手段之一。
通过加强工具的刚度和阻尼特性,提高刀具的稳定性和切削性能,可以减小振动和共振的发生。
4.3 优化切削工艺
优化切削工艺也是减小振动和共振的重要措施。
通过改变切削方式、切削轨迹和切削液的使用等,可以减小切削力的波动,降低振动和共振的发生。
5. 结论
金属切削过程中的振动与共振现象对切削质量和加工效率具有重要影响。
通过合理选择切削参数、优化工具的结构设计和切削工艺的优化,可以有效控制振动和共振的发生,提高切削加工的质量和效率。
进一步的研究还可以从切削系统的模态分析和动态特性研究等方面深入探索振动和共振现象的机理,为切削工艺的进一步
优化提供理论依据。
最后需要指出的是,振动与共振现象分析研究需要相互交流与分享,以期望取得更进一步的研究成果。