水基切削液
水基切削液与油基切削液的区别
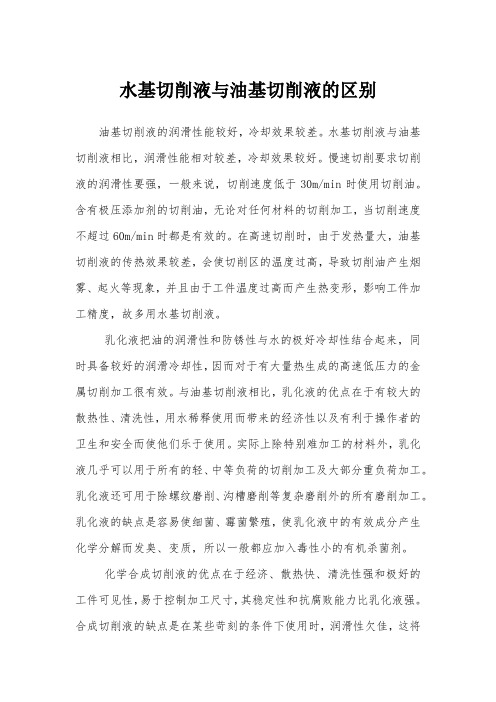
水基切削液与油基切削液的区别油基切削液的润滑性能较好,冷却效果较差。
水基切削液与油基切削液相比,润滑性能相对较差,冷却效果较好。
慢速切削要求切削液的润滑性要强,一般来说,切削速度低于30m/min时使用切削油。
含有极压添加剂的切削油,无论对任何材料的切削加工,当切削速度不超过60m/min时都是有效的。
在高速切削时,由于发热量大,油基切削液的传热效果较差,会使切削区的温度过高,导致切削油产生烟雾、起火等现象,并且由于工件温度过高而产生热变形,影响工件加工精度,故多用水基切削液。
乳化液把油的润滑性和防锈性与水的极好冷却性结合起来,同时具备较好的润滑冷却性,因而对于有大量热生成的高速低压力的金属切削加工很有效。
与油基切削液相比,乳化液的优点在于有较大的散热性、清洗性,用水稀释使用而带来的经济性以及有利于操作者的卫生和安全而使他们乐于使用。
实际上除特别难加工的材料外,乳化液几乎可以用于所有的轻、中等负荷的切削加工及大部分重负荷加工。
乳化液还可用于除螺纹磨削、沟槽磨削等复杂磨削外的所有磨削加工。
乳化液的缺点是容易使细菌、霉菌繁殖,使乳化液中的有效成分产生化学分解而发臭、变质,所以一般都应加入毒性小的有机杀菌剂。
化学合成切削液的优点在于经济、散热快、清洗性强和极好的工件可见性,易于控制加工尺寸,其稳定性和抗腐败能力比乳化液强。
合成切削液的缺点是在某些苛刻的条件下使用时,润滑性欠佳,这将引起机床活动部件的粘着和磨损,而且化学合成液留下的粘稠状残留物会影响机器零件的运动,还会使这些零件的重叠面产生锈蚀。
一般在下列的情况下应选用水基切削液:1)对油基切削液潜在发生火灾危险的场所;2)高速和大进给量的切削,使切削区趋于高温,冒烟激烈,有火灾危险的场合;3)从前后工序的流程上考虑,要求使用水基切削液的场合;4)希望减轻由于油的飞溅及油雾的扩散而引起机床周围污染和肮脏,从而保持操作环境清洁的场合;5)从价格上考虑,对一些易加工材料及工件表面质量要求不高的切削加工,采用一般水基切削液已能满足使用要求,又可大幅度降低切削液成本的场合。
水基切削液

水基切削液分为三大类,即乳化液、合成切削液和半合成切削液。
①乳化液:它由乳化油与水配置而成。
乳化油主要是由矿物油(含量为50%~80%)、乳化剂、防锈剂、油性剂。
极压剂和防腐剂等组成。
稀释液不透明,呈乳白色。
但由于其工作稳定性差,使用周期短,溶液不透明,很难观察工作时的切削状况,故使用量逐年减少。
②合成切削液:它的浓缩液不含矿物油,由水溶性防锈剂、油性剂、极压剂。
表面活性剂和消泡剂等组成。
稀释液呈透明状或半透明状。
主要优点是:使用寿命长;优良的冷却和清洗性能,适合高速切削;溶液透明,具有良好的可见性,特别适合数控机床、加工中心等现代加工设备上使用。
但合成切削液容易洗刷掉机床滑动部件上的润滑油,造成滑动不灵活,润滑性能相对差些。
③半合成切削液:也称微乳化切削液。
它的浓缩液由少量矿物油(含量为5%~30%),油性剂、极压剂、防锈剂、表面活性剂和防腐剂等组成。
稀释液油滴直径小于1µm,稀释液呈透明状或半透明状。
它具备乳化液和合成切削液的优点,又弥补了两者的不足,是切削液发展的趋势。
合成切削液包括三种:一种化学合成的切削液是含有水溶性防锈剂的真溶液,如亚硝酸钠、碳限钠、三乙醇胺等组成的水溶性液。
这类溶液具有一定的冷却、清洗、防锈性,不易变质,使用周期较长,但其润滑性和润湿性较差,表面张力较大(与水接近),并且在水分蒸发后,金属表面会留下硬的结晶残留物,所以这类切削液只适合于一般的磨削加工。
象我们威尔的固体切削液。
另一种化学合成的切削液是由表面活性剂、水溶性防锈剂和水溶性润滑剂组成,是一种颗粒极小的胶体溶液。
这种切削液表面张力低,一般小于400Pa。
其润湿性好,渗透能力强,冷却和清洗性能好,也有一定的润滑作用。
由于合成以上上两种合成切削液是单相体系,其稳定性较乳化液好,使用周期长,但由于不含油,且清洗能力强,很容易把机床导轨面上的润滑油清洗掉,造成刀架移动困难,并容易在这些可移动部件的接触面产生锈蚀,所以在使用合成切削液时要注意加强设备的防锈管理。
【水基切削液配方】水基切削液的配方是什么

水基切削液是一种用在金属切、削、磨加工过程中,用来冷却和润滑刀具和加工件的工业用液体,切削液由多种超强功能助剂经科学复合配伍而成,同时具备良好的冷却性能、润滑性能、防锈性能、除油清洗功能、防腐功能、易稀释特点。
克服了传统皂基乳化液夏天易臭、冬天难稀释、防锈效果差的的毛病,对车床漆也无不良影响,适用于黑色金属的切削及磨加工,属当前最领先的磨削产品。
切削液各项指标均优于皂化油,它具有良好的冷却、清洗、防锈等特点,并且具备无毒、无味、对人体无侵蚀、对设备不腐蚀、对环境不污染等特点。
水基切削液是将油剂用大量的水稀释的切削液,通常含油剂百分之五至二十,其用量约占全部切削液的百分之九十五。
水基切削液一般分为乳化液(可溶性油,Soluble Oil)、微乳液、和化学水溶液。
市场上称后两种为半合成和全合成。
水基切削液的配方是什么15号基础油 200~220g/L蓖麻油三乙醇胺 200~220g/L妥尔油30~80g/L硼酸150~200g/L杀菌剂10~30g/L消泡剂10~30g/L表面活性剂(tx-10)25~50g/L聚乙二醇25~50g/L石油磺酸钠100~130g/L磷酸钠100~130g/L水余量g/L水基切削液有哪些优点呢一、优良的防锈性能(防锈时间三个月以上)二、溶液碧绿透明,具有良好的可见性,特别适合数控机床,加工中心等现代加工设备上使用。
三、环保配方:不含氯、三嗪、二级胺、芳香烃、亚硝酸钠等对人体有害成份,对皮肤无刺激性,对操作者友好。
四、切削液变质发臭控制:精选进口添加剂,抗菌性极强,在中央系统或单机油槽中都有很长的寿命(一年以上不发臭变质)五、低泡沫:出色的抗泡性,可用于高压系统及要求高空气释放性的操作条件,软硬水适用。
六、润滑性:配方中含有独特的表面活性剂,乳化剂。
润滑性能远高于同类产品,明显降低刀具成本,提高表面加工精度,可替代切削油使用,为操作者创造良好的环境。
七、沉屑性:排油性配方具有良好的沉屑性,提供切削屑及切削细分的快速沉降,维持系统清洁及容易清洗排除污染物,浮油很快在切削液的液面上完全分离。
油基切削液和水基切削液的区别
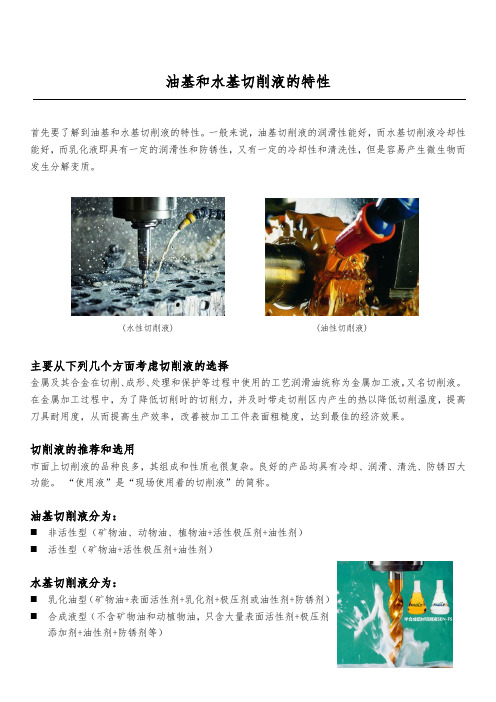
油基和水基切削液的特性首先要了解到油基和水基切削液的特性。
一般来说,油基切削液的润滑性能好,而水基切削液冷却性能好,而乳化液即具有一定的润滑性和防锈性,又有一定的冷却性和清洗性,但是容易产生微生物而发生分解变质。
主要从下列几个方面考虑切削液的选择金属及其合金在切削、成形、处理和保护等过程中使用的工艺润滑油统称为金属加工液,又名切削液。
在金属加工过程中,为了降低切削时的切削力,并及时带走切削区内产生的热以降低切削温度,提高刀具耐用度,从而提高生产效率,改善被加工工件表面粗糙度,达到最佳的经济效果。
切削液的推荐和选用市面上切削液的品种良多,其组成和性质也很复杂。
良好的产品均具有冷却、润滑、清洗、防锈四大功能。
“使用液”是“现场使用着的切削液”的简称。
油基切削液分为:⏹ 非活性型(矿物油、动物油、植物油+活性极压剂+油性剂)⏹ 活性型(矿物油+活性极压剂+油性剂)水基切削液分为:⏹ 乳化油型(矿物油+表面活性剂+乳化剂+极压剂或油性剂+防锈剂)⏹ 合成液型(不含矿物油和动植物油,只含大量表面活性剂+极压剂添加剂+油性剂+防锈剂等)(水性切削液)(油性切削液)⏹半合成液型(含少量矿物油+表面活性剂+极压剂+油性剂+防锈剂)⏹化学溶液型(无机盐类、有机胺+表面活性剂等)⏹乳化油通常称为“可溶行油”,其中含油量一般在70%以上。
其缺点是:冷却性差,而且高温下易挥发,产生油雾,污染环境,必需安装排油污设备,甚至有引起火灾的危险。
不受细菌腐蚀影响,几乎不会引起皮肤病,使用中混入其他润滑油除了会降低添加剂浓度外,无其他不良影响。
关于“原液”和“使用液”油基切削液的原液就是其本身,水基切削液的原液系指稀释前的母液。
像华南地区的FABLE/福邦润滑油旗下的SEN系列的半合成切削液就一直广受客户的好评。
油基切削液靠油的优良润滑作用降低摩擦生热,达到冷却的目的,水基切削液靠水的热导率、比热容、汽化热比油大,粘度比油小的特点达到冷却的目的。
金属切削液配方与制备

金属切削液配方与制备一、金属切削液的配方1.油基切削液配方油基切削液是以矿物油或合成油为基础油,并加入相应的添加剂而配制而成。
其配方主要包括基础油、极压抗磨剂、添加剂、乳化剂和稀释剂等。
其中,基础油的选择应根据切削材料的特性来决定。
2.水基切削液配方水基切削液是以水为基础溶剂,并加入乳化剂和添加剂配制而成。
其配方主要包括水、乳化剂、防锈剂、添加剂和稀释剂等。
水基切削液相比油基切削液具有环保、易清洗和成本低等优点。
3.胶体切削液配方胶体切削液是以水为基础溶剂,并加入胶体材料和添加剂而配制而成。
其配方主要包括水、乳化剂、稀释剂和添加剂等。
胶体切削液由于含有胶体材料,能够形成一层均匀的润滑膜,提高切削液的附着性和切削效果。
二、金属切削液的制备1.配方设计:根据切削材料、切削条件和要求来确定金属切削液的配方。
2.原料准备:根据配方选择相应的原料,并准备好所需的添加剂、乳化剂和稀释剂等。
3.混合制备:按照一定比例将基础油、添加剂、乳化剂和稀释剂等原料加入搅拌容器中进行混合搅拌。
在混合搅拌过程中,可以根据需要进行温度控制、pH调节和气氛保护等操作。
4.包装:将混合制备好的金属切削液装入相应的容器中,并进行密封包装,以保持其稳定性和持久性。
需要注意的是,金属切削液在制备过程中需要考虑材料的相容性和稳定性。
同时,对于不同的切削材料和切削条件,金属切削液的配方和制备要根据具体情况进行调整和改进,以达到最佳的切削效果。
总之,金属切削液的配方和制备对于切削加工的效率和切削质量有着重要的影响。
合理选择配方和掌握制备技术,能够提高金属切削液的附着性、润滑性和冷却性,提高切削质量和刀具寿命。
油基切削液和水基切削液有什么区别
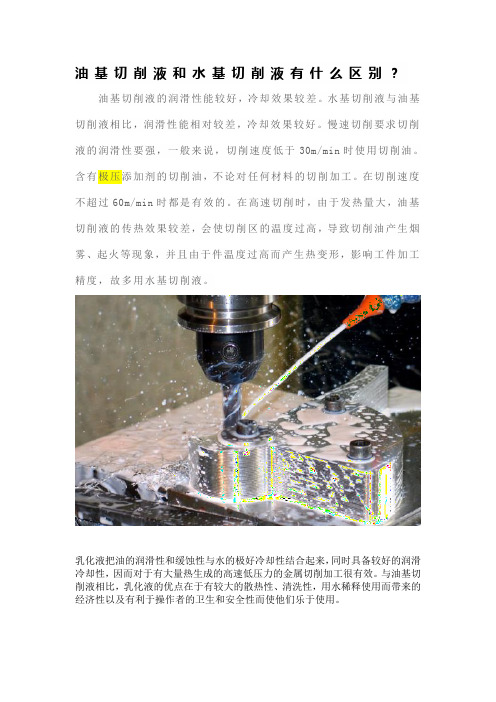
油基切削液和水基切削液有什么区别?油基切削液的润滑性能较好,冷却效果较差。
水基切削液与油基切削液相比,润滑性能相对较差,冷却效果较好。
慢速切削要求切削液的润滑性要强,一般来说,切削速度低于30m/min时使用切削油。
含有极压添加剂的切削油,不论对任何材料的切削加工。
在切削速度不超过60m/min时都是有效的。
在高速切削时,由于发热量大,油基切削液的传热效果较差,会使切削区的温度过高,导致切削油产生烟雾、起火等现象,并且由于件温度过高而产生热变形,影响工件加工精度,故多用水基切削液。
乳化液把油的润滑性和缓蚀性与水的极好冷却性结合起来,同时具备较好的润滑冷却性,因而对于有大量热生成的高速低压力的金属切削加工很有效。
与油基切削液相比,乳化液的优点在于有较大的散热性、清洗性,用水稀释使用而带来的经济性以及有利于操作者的卫生和安全性而使他们乐于使用。
实际上除特别难加工的材料外,乳化液几乎可以用于所有的轻、中等负荷的切削加工及大部分重负荷加工。
乳化液还可用于除螺纹磨削、沟槽磨削等复杂磨削外的所有磨削加工。
乳化液的缺点是容易使细菌、霉菌繁殖,使乳化液中的有效成分产生化学分解而发臭、变质,所以一般都应加入毒性小的有机杀菌剂。
化学合成切削液的优点在于经济、散热快、清洗性强和极好的工件可见性,易于控制加工尺寸,其稳定性和抗腐败能力比乳化液强。
什么情况下该选择水基切削液?1)对油基切削液潜在发生火灾危险的场所。
2)高速和大进给量的切削,使切削区趋于高温,冒烟激烈,有火灾危险的场合。
3)从前后工序的流程上考虑,要求使用水基切削液的场合。
4)希望减轻由于油的飞溅及油雾的扩散而引起的机床周围污染和肮脏,从而保持操作环境清洁的场合。
5)从价格上考虑,对一些易加工材料及工件表面质量要求不高的切削加工,采用一般水基切削液已能满足使用要求,又可大幅度降低切削液成本的场合。
2刀具的寿命对切削的经济性占有较大比重的场合(如刀具价格昂贵,刃磨刀具困难,装卸刀具辅助时间长等),机床精密度高,绝对不允许有水混入(以免造成腐蚀)的场合,机床的润滑系统和冷却系统容易串通的场合,以及不具备废液处理设备和条件的场合,均应考虑选用油基切削液。
水基切削液成分
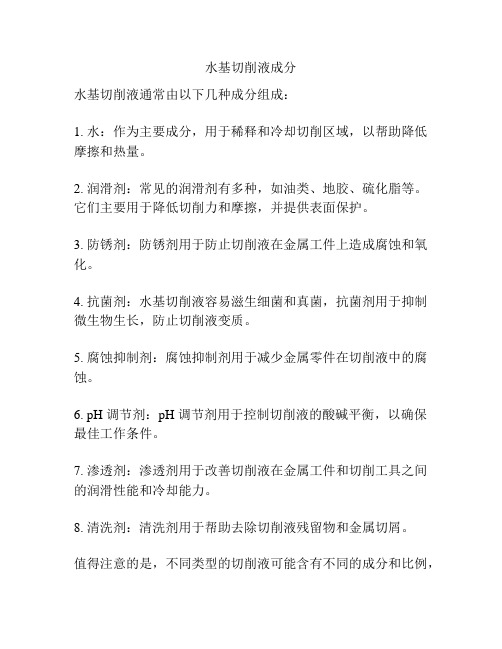
水基切削液成分
水基切削液通常由以下几种成分组成:
1. 水:作为主要成分,用于稀释和冷却切削区域,以帮助降低摩擦和热量。
2. 润滑剂:常见的润滑剂有多种,如油类、地胶、硫化脂等。
它们主要用于降低切削力和摩擦,并提供表面保护。
3. 防锈剂:防锈剂用于防止切削液在金属工件上造成腐蚀和氧化。
4. 抗菌剂:水基切削液容易滋生细菌和真菌,抗菌剂用于抑制微生物生长,防止切削液变质。
5. 腐蚀抑制剂:腐蚀抑制剂用于减少金属零件在切削液中的腐蚀。
6. pH 调节剂:pH 调节剂用于控制切削液的酸碱平衡,以确保最佳工作条件。
7. 渗透剂:渗透剂用于改善切削液在金属工件和切削工具之间的润滑性能和冷却能力。
8. 清洗剂:清洗剂用于帮助去除切削液残留物和金属切屑。
值得注意的是,不同类型的切削液可能含有不同的成分和比例,
具体配方可能因应用和要求而有所变化。
所以,具体配方需参考切削液的技术资料或咨询生产商。
水基与油基切削液的区别与选用
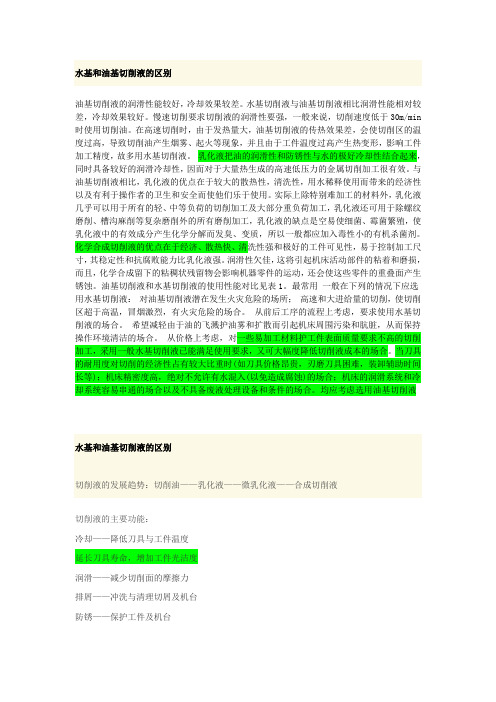
水基和油基切削液的区别油基切削液的润滑性能较好,冷却效果较差。
水基切削液与油基切削液相比润滑性能相对较差,冷却效果较好。
慢速切削要求切削液的润滑性要强,一般来说,切削速度低于30m/min 时使用切削油。
在高速切削时,由于发热量大,油基切削液的传热效果差,会使切削区的温度过高,导致切削油产生烟雾、起火等现象,并且由于工件温度过高产生热变形,影响工件加工精度,故多用水基切削液。
乳化液把油的润滑性和防锈性与水的极好冷却性结合起来,同时具备较好的润滑冷却性,因而对于大量热生成的高速低压力的金属切削加工很有效。
与油基切削液相比,乳化液的优点在于较大的散热性,清洗性,用水稀释使用而带来的经济性以及有利于操作者的卫生和安全而使他们乐于使用。
实际上除特别难加工的材料外,乳化液几乎可以用于所有的轻、中等负荷的切削加工及大部分重负荷加工,乳化液还可用于除螺纹磨削、槽沟麻削等复杂磨削外的所有磨削加工,乳化液的缺点是空易使细菌、霉菌繁殖,使乳化液中的有效成分产生化学分解而发臭、变质,所以一般都应加入毒性小的有机杀菌剂。
化学合成切削液的优点在于经济、散热快、清洗性强和极好的工件可见性,易于控制加工尺寸,其稳定性和抗腐败能力比乳化液强。
润滑性欠佳,这将引起机床活动部件的粘着和磨损,而且,化学合成留下的粘稠状残留物会影响机器零件的运动,还会使这些零件的重叠面产生锈蚀。
油基切削液和水基切削液的使用性能对比见表1。
最常用一般在下列的情况下应选用水基切削液:对油基切削液潜在发生火灾危险的场所;高速和大进给量的切削,使切削区超于高温,冒烟激烈,有火灾危险的场合。
从前后工序的流程上考虑,要求使用水基切削液的场合。
希望减轻由于油的飞溅护油雾和扩散而引起机床周围污染和肮脏,从而保持操作环境清洁的场合。
从价格上考虑,对一些易加工材料护工件表面质量要求不高的切削加工,采用一般水基切削液已能满足使用要求,又可大幅度降低切削液成本的场合。
当刀具的耐用度对切削的经济性占有较大比重时(如刀具价格昂贵,刃磨刀具困难,装卸辅助时间长等);机床精密度高,绝对不允许有水混入(以免造成腐蚀)的场合;机床的润滑系统和冷却系统容易串通的场合以及不具备废液处理设备和条件的场合。
一、油基切削液与水基相比各有何特点?
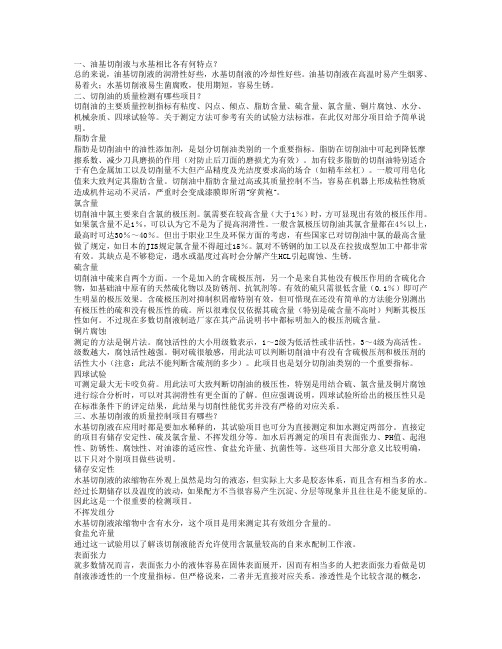
一、油基切削液与水基相比各有何特点?总的来说,油基切削液的润滑性好些,水基切削液的冷却性好些。
油基切削液在高温时易产生烟雾、易着火;水基切削液易生菌腐败,使用期短,容易生锈。
二、切削油的质量检测有哪些项目?切削油的主要质量控制指标有粘度、闪点、倾点、脂肪含量、硫含量、氯含量、铜片腐蚀、水分、机械杂质、四球试验等。
关于测定方法可参考有关的试验方法标准,在此仅对部分项目给予简单说明。
脂肪含量脂肪是切削油中的油性添加剂,是划分切削油类别的一个重要指标。
脂肪在切削油中可起到降低摩擦系数、减少刀具磨损的作用(对防止后刀面的磨损尤为有效)。
加有较多脂肪的切削油特别适合于有色金属加工以及切削量不大但产品精度及光洁度要求高的场合(如精车丝杠)。
一般可用皂化值来大致判定其脂肪含量。
切削油中脂肪含量过高或其质量控制不当,容易在机器上形成粘性物质造成机件运动不灵活,严重时会变成漆膜即所谓“穿黄袍”。
氯含量切削油中氯主要来自含氯的极压剂。
氯需要在较高含量(大于1%)时,方可显现出有效的极压作用。
如果氯含量不足1%,可以认为它不是为了提高润滑性。
一般含氯极压切削油其氯含量都在4%以上,最高时可达30%~40%。
但出于职业卫生及环保方面的考虑,有些国家已对切削油中氯的最高含量做了规定,如日本的JIS规定氯含量不得超过15%。
氯对不锈钢的加工以及在拉拔成型加工中都非常有效。
其缺点是不够稳定,遇水或温度过高时会分解产生HCL引起腐蚀、生锈。
硫含量切削油中硫来自两个方面。
一个是加入的含硫极压剂,另一个是来自其他没有极压作用的含硫化合物,如基础油中原有的天然硫化物以及防锈剂、抗氧剂等。
有效的硫只需很低含量(0.1%)即可产生明显的极压效果。
含硫极压剂对抑制积屑瘤特别有效,但可惜现在还没有简单的方法能分别测出有极压性的硫和没有极压性的硫。
所以很难仅仅依据其硫含量(特别是硫含量不高时)判断其极压性如何。
不过现在多数切削液制造厂家在其产品说明书中都标明加入的极压剂硫含量。
水基化学全合成切削液使用须知
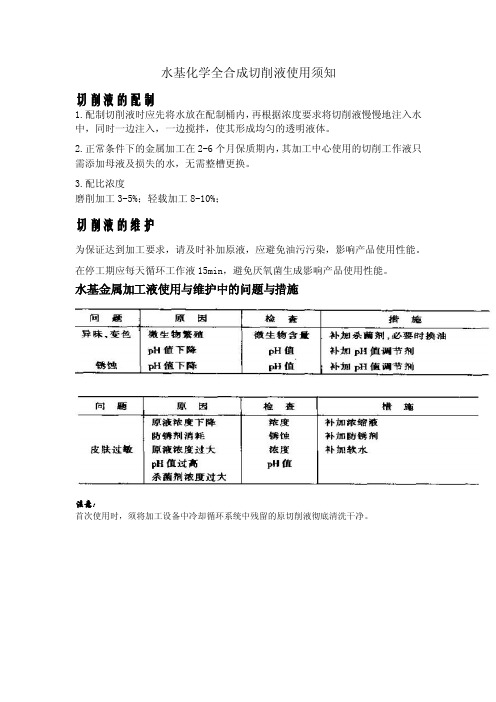
水基化学全合成切削液使用须知
切削液的配制
1.配制切削液时应先将水放在配制桶内,再根据浓度要求将切削液慢慢地注入水中,同时一边注入,一边搅拌,使其形成均匀的透明液体。
2.正常条件下的金属加工在2-6个月保质期内,其加工中心使用的切削工作液只需添加母液及损失的水,无需整槽更换。
3.配比浓度
磨削加工3-5%;轻载加工8-10%;
切削液的维护
为保证达到加工要求,请及时补加原液,应避免油污污染,影响产品使用性能。
在停工期应每天循环工作液15min,避免厌氧菌生成影响产品使用性能。
水基金属加工液使用与维护中的问题与措施
注意:
首次使用时,须将加工设备中冷却循环系统中残留的原切削液彻底清洗干净。
水基全合成切削液

水基全合成切削液
一、水基全合成切削液简介:
水基全合成切削液即加美润滑油水基全合成切削液,具有优秀的润滑性能,防锈性能和冷却性能。
另外还有废屑沉淀快,含有特效防氧化成份。
【江苏加美切削液诚邀全国地区合作加盟,共同发展】。
加美润滑油水基全合成切削液可适用于各种合金材料的切削、磨削、钻孔、冲压等金属加工方式,并且加美水基全合成切削液目前与许多知名企业都有合作。
二、水基全合成切削液参数说明:
三、水基全合成切削液产品特点:
四、加美切削液格言:。
水基切削液技术标准

水基切削液技术标准
水基切削液是一种常用于金属加工中的切削液,其主要作用是在加工过程中降温、润滑、清洁和保护工件表面。
以下是常见的水基切削液技术标准:
1.GB/T 7614-2006《水基切削液》:该标准规定了水基切削液的分类、要求、试验方法、检验规则等内容。
其中,水基切削液的分类包括乳化液、半合成液和全合成液三种类型。
2.GB/T 14039-2008《切削液》:该标准规定了切削液的分类、要求、试验方法、检验规则等内容。
其中,切削液的分类包括油基切削液、乳化液、全合成液和半合成液四种类型。
3.GB/T 17411-1998《水溶性切削液》:该标准规定了水溶性切削液的分类、要求、试验方法、检验规则等内容。
其中,水溶性切削液的分类包括乳化液和全合成液两种类型。
4.GB/T 6144-2010《合成切削液》:该标准规定了合成切削液的分类、要求、试验方法、检验规则等内容。
其中,合成切削液的分类包括乳化液、全合成液和半合成液三种类型。
以上是常见的水基切削液技术标准,不同的标准适用于不同类型的水基切削液。
在选择和使用水基切削液时,需要根据具体的加工要求和材料特性选择适合的切削液,并按照相关标准进行检测和评估。
金属加工液使用指南(3篇)

第1篇一、前言金属加工液,又称切削液、冷却液,是用于金属切削、磨削、拉丝、电镀等加工过程中的一种专用液体。
它具有冷却、润滑、清洗、防锈等功能,对提高加工效率、保证加工质量、延长刀具寿命等方面具有重要作用。
正确使用金属加工液,不仅能提高生产效率,还能降低生产成本,以下是金属加工液使用指南。
二、金属加工液的种类及特点1. 水基切削液水基切削液是以水为基础,加入各种添加剂制成的。
其优点是环保、成本低、冷却效果好,但易受细菌、霉菌等微生物污染,需定期更换。
2. 油基切削液油基切削液是以矿物油、动植物油、合成油等为基础,加入各种添加剂制成的。
其优点是润滑性能好、防锈性能强,但成本较高,且对环境有一定污染。
3. 半合成切削液半合成切削液是以水基切削液和油基切削液为基础,加入一定比例的添加剂制成的。
其优点是兼具水基和油基切削液的特点,性能稳定,使用成本低。
4. 合成切削液合成切削液是以合成油为基础,加入各种添加剂制成的。
其优点是性能稳定、使用寿命长、环保,但成本较高。
三、金属加工液的使用方法1. 储存(1)储存容器应密封良好,避免阳光直射和高温环境。
(2)储存温度不宜过高,一般控制在10℃~40℃之间。
(3)储存时,应避免与易燃、易爆物品混放。
2. 配制(1)根据加工工艺和工件材料,选择合适的金属加工液。
(2)按照产品说明书,按照比例配制金属加工液。
(3)配制过程中,应搅拌均匀,避免产生气泡。
3. 使用(1)将金属加工液注入机床切削液箱中,液面高度控制在规定范围内。
(2)在加工过程中,保持切削液循环,避免液面过低。
(3)定期检查切削液浓度,确保其在规定范围内。
(4)加工过程中,注意观察切削液的使用情况,如有异常,应及时处理。
4. 更换(1)根据切削液的使用情况和性能变化,定期更换切削液。
(2)更换切削液时,应将机床内的旧切削液排空,并用清水冲洗机床切削液箱。
(3)更换后的切削液,应按照配制要求进行配制。
四、金属加工液的管理与维护1. 建立切削液管理制度,明确责任人和使用流程。
水基切削液(参考资料)

水基切削液一、名词解释:水基切削液:是将油剂或浓缩液---也就是我们通常所说的原液---用大量的水稀释的切削液,我们现在接触的水基切削液配比一般是100(水):3~8(原液),某些切削液的配比也会达到100:20。
水基切削液一般分为三大类,即乳化液、半合成切削液和全合成切削液。
乳化液:由乳化油与水配置而成。
乳化油主要是由50%~80%的矿物油、乳化剂、防锈剂、油性剂、极压剂和防腐剂等组成。
稀释液不透明,呈乳白色。
半合成切削液:半合成切削液也称微乳化切削液,它的浓缩液由少量矿物油(含量为5%~30%),油性剂、极压剂、防锈剂、表面活性剂和防腐剂等组成。
稀释液油滴直径小于1µm,稀释液呈透明状或半透明状全合成切削液:合成切削液浓缩液不含矿物油,由水溶性防锈剂、油性剂、极压剂。
表面活性剂和消泡剂等组成。
稀释液呈透明状或半透明状。
二、水基切削液的特性乳化液润滑极压性较好,清洗性能较好。
但乳化液中的油相油滴较大,导致金属加工冷却性较差。
同时由于乳化液稳定性差,所以乳化液在使用一段时间后,会出现变味变臭的现象,这种情况在夏天温度高的时候尤为明显。
另外,由于乳化液呈乳白色不透明,所以在加工过程中很难观察切削状况,但是乳化液在三种水基切削液中是最便宜的一种。
半合成切削液与乳化液很相似,但是由于半合成切削液添加了更多的表面活性剂,所以油滴分散得更细小,更稳定,所以相对于乳化液来说更不容易变质,使用的时间更长。
加工过程中的冷却性、润滑性都比较好,清洗性也很好。
全合成切削液中不含任何油基(如矿物油)成分,而采用具有润滑作用的水溶性合成酯类添加其他成分配制而成。
全合成切削液除的润滑性、加工冷却性和清洗方面的性能尤为优异。
但是全合成切削液容易洗掉机床部件上的润滑油,而对机床的润滑造成影响,并且能够在一些接触面上形成锈蚀,所以使用全合成切削液对机床的防锈管理提出了更高要求。
三、使用水基切削液中需要注意的问题1、选择首先是安全,关注切削液的MSDS(Material Safety Data Sheet即化学品安全说明书),它提供化学品的理化参数、燃爆性能、对健康的危害、安全使用贮存、泄漏处置、急救措施以及有关的法律法规等十六项内容,避免使用者受到化学品的潜在危害。
- 1、下载文档前请自行甄别文档内容的完整性,平台不提供额外的编辑、内容补充、找答案等附加服务。
- 2、"仅部分预览"的文档,不可在线预览部分如存在完整性等问题,可反馈申请退款(可完整预览的文档不适用该条件!)。
- 3、如文档侵犯您的权益,请联系客服反馈,我们会尽快为您处理(人工客服工作时间:9:00-18:30)。
水基切削液
一、名词解释:
水基切削液:是将油剂或浓缩液---也就是我们通常所说的原液---用大量的水稀释的切削液,我们现在接触的水基切削液配比一般是100(水):3~8(原液),某些切削液的配比也会达到100:20。
水基切削液一般分为三大类,即乳化液、半合成切削液和全合成切削液。
乳化液:由乳化油与水配置而成。
乳化油主要是由50%~80%的矿物油、乳化剂、防锈剂、油性剂、极压剂和防腐剂等组成。
稀释液不透明,呈乳白色。
半合成切削液:半合成切削液也称微乳化切削液,它的浓缩液由少量矿物油(含量为5%~30%),油性剂、极压剂、防锈剂、表面活性剂和防腐剂等组成。
稀释液油滴直径小于1µm,稀释液呈透明状或半透明状
全合成切削液:合成切削液浓缩液不含矿物油,由水溶性防锈剂、油性剂、极压剂。
表面活性剂和消泡剂等组成。
稀释液呈透明状或半透明状。
二、水基切削液的特性
乳化液润滑极压性较好,清洗性能较好。
但乳化液中的油相油滴较大,导致金属加工冷却性较差。
同时由于乳化液稳定性差,所以乳化液在使用一段时间后,会出现变味变臭的现象,这种情况在夏天温度高的时候尤为明显。
另外,由于乳化液呈乳白色不透明,所以在加工过程中很难观察切削状况,但是乳化液在三种水基切削液中是最便宜的一种。
半合成切削液与乳化液很相似,但是由于半合成切削液添加了更多的表面活性剂,所以油滴分散得更细小,更稳定,所以相对于乳化液来说更不容易变质,使用的时间更长。
加工过程中的冷却性、润滑性都比较好,清洗性也很好。
全合成切削液中不含任何油基(如矿物油)成分,而采用具有润滑作用的水溶性合成酯类添加其他成分配制而成。
全合成切削液除的润滑性、加工冷却性和清洗方面的性能尤为优异。
但是全合成切削液容易洗掉机床部件上的润滑油,而对机床的润滑造成影响,并且能够在一些接触面上形成锈蚀,所以使用全合成切削液对机床的防锈管理提出了更高要求。
三、使用水基切削液中需要注意的问题
1、选择
首先是安全,关注切削液的MSDS(Material Safety Data Sheet即化学品安全说明书),它提供化学品的理化参数、燃爆性能、对健康的危害、安全使用贮存、泄漏处置、急救措施以及有关的法律法规等十六项内容,避免使用者受到化学品的潜在危害。
不宜选用会使操作者有不适感的切削液,如含有亚硝酸盐、苯酚、甲醛或硫类化合物的切削液。
在机床安全方面,有些切削液会腐蚀机床的金属部件,造成滑动面生锈,或是在丝杆和导轨上产生胶状沉淀物而影响机床运行,这些切削液也不宜采用。
为了保证工件的安全,同样不宜采用会腐蚀工件的切削液,如加工铜件时不能用含硫的切削液,加工铝时不能采用稀释后PH偏碱性的切削液。
然后是切削性能,主要包括润滑性能、冷却性能和清洗性能,加工负荷大需要的润滑性
就高,加工速度快需要的冷却性就高,对于一些精密工件对清洗性要求会很高。
一般而言:
润滑性:乳化液>半合成加工液>全合成加工液;
冷却性:全合成加工液>半合成加工液>乳化液;
清洗性:全合成加工液>半合成加工液>乳化液;
2、切削液的日常管理
(1)浓度管理
水基切削液应该按照切削液生产厂家推荐的使用浓度进行配比,这样才能获得较好的效果。
如果浓度过低,则其润滑、防锈和切削性能下降,使机床发生锈蚀现象,而且容易变质而发出臭味;如果浓度过高,切削液容易起泡沫,刺激皮肤,并且经济性也不好,造成不必要的浪费。
在配比切削液时,应该明白厂家推荐的浓度是体积比浓度还是体积百分比浓度,例如,有些厂家的切削液配比方式是100:5,则表示的是体积比浓度,需用5体积的切削液原液加入到100体积的水中;有些厂家的切削液推荐的使用浓度为5%,则表示需用5体积的切削液原液加入到95体积的水中。
切削液的浓度配比一方面要依据切削液厂家推荐的浓度,另外要根据实际生产要求而定,例如我们使用的Milacron CIMTECH310切削液,厂家推荐的浓度是5%,这个浓度可以保证切削液的防锈性,同时可以满足大部分的铣削加工,表面效果一般,但是对于加工面光洁度要求高的情况下,这个浓度就很难达到,当浓度为8%时,可以达到最佳的效果。
注意:
●配制切削液时,一定要先向容器中加入足够的水,然后再向水中加入切削液,不能先加切削液再加水。
●在使用折光仪进行浓度检测时一定要先向切削液厂家咨询切削液的折光系数,切削液实际浓度=折光仪读数×折光系数。
(2)水质管理
配制切削液时应使用低硬度的自来水,或使用软化水。
水质硬度太高的水会破坏切削液的防锈能力和润滑能力,容易产生不溶物沉淀在机床上,同时使切削液的稳定性变差,容易腐败变臭;水质太软的水会导致切削液在使用过程中产生大量泡沫。
(3)防腐败管理
防腐败管理能够有效延长切削液的使用寿命,更重要的是防腐败管理能够避免因切削液问题导致的机床生锈和故障,不止是节约切削液的使用成本,更是节约机床的维护成本。
●不能向切削液中丢弃废弃物,避免引入任何杂物,定期清理切削液循环系统中的切屑、粉末和霉菌衍生物等。
切屑对切削液加工性能影响很大,配备切屑分离装置或切削液过滤装置是必要的。
●定期清理切削液表面的浮油和脏物。
●定期检查切削液中的细菌生长情况,及时采取相应的措施。
大部分切削液的生产厂家
都有对切削液的抑菌措施,如加入防腐剂等。
●定期检查浓度,浓度过低时切削液也容易变质,发现浓度有变化时要及时进行处理。
●机床长时间停用时,应对切削液进行通风,以抑制厌氧菌的生长,一般的方法是每天使切削液循环30分钟或咨询切削液厂家,在厂家指导下进行。
●定期补充切削液,由于加工飞溅、工件带走、蒸发等导致切削液减少,要及时加入新的切削液并监控浓度。
●定期对切削液进行全部更换,虽然在机床使用过程中由于损耗,会不断添加新的切削液,但是使用时间越长的切削液,加工性能下降的越多,所以每隔一定的时间就必须将全部切削液进行更换。
更换的周期可咨询切削液厂家。
在使用新的切削液时,必须对切削液循环系统进行清洗,如果是更换不同品牌的切削液,更需要对切削液循环系统进行彻底的清洗。
总结:
水基切削液相对于油性切削液来说,有更好的经济性,但是不会用、用不好不仅不会节约成本,反而会造成严重的机床故障,不仅造成更大的机床维修成本,还有因机床停产而造成的损失。
所以,做好水基切削液的日常维护至关重要。
水基切削液由于不同厂家的生产工艺和配方不同,造成切削液本身的性状有很大区别,如气味、变质速度、起沫程度等,在使用过程中对加工效果的影、防锈性能、对非金属材料的腐蚀情况等也有很大差别!
用于配切削液的水,可用水质检测笔进行检测。
切削液要求的水质在20~100ppm为最适合。
低于20ppm,容易产生泡沫,高于100ppm,水基切削液特别是乳化液的安定性不好,容易腐败,防锈性能和润滑性能下降。