热喷涂技术讲义
热喷涂技术 ppt课件

阴极是电子发射源,选用熔点高和电子发射能力强 的材料制成,一般采用钨电极。喷嘴为阳极,通过其 孔道对电弧进行压缩而形成等离子弧。
五、热喷涂装置和设备 3.等离子喷涂装置
缺点:粉尘、烟雾大、噪声大。
三、热喷涂工序 1.表面预处理
(1)基体表面的清洗、脱脂:碱性溶液或丙酮、 汽油。
(2)基体表面氧化膜处理
(3)基体表面粗化处理:提高涂层与基体结合 强度(喷砂、机械加工如开槽、车螺纹、滚花等)
(4)基体表面预热处理:提高涂层与基体结合 强度
(5)非喷涂表面的保护
三、热喷涂工序 2.喷涂 (1)喷涂打底层:Mo、Ni-Cr、Ni-Cr-Al 等。厚度50-100微米。 (2)喷涂工作层璃等几乎所有固体材料。
喷涂层的性能:耐磨、耐蚀、耐热、抗氧化、润 滑等。
喷涂层的厚度:0.5-5mm。
应用:宇航、国防、机械、冶金、石油、化工、 机车车辆、电力等部门。
如果将喷涂层再加热重熔,产生冶金结合,称为 喷熔。
一、热喷涂原理 1.涂层形成过程及形成原理
等离子弧是压缩电弧, 按接电的方法不同,等 离子弧有三种形式: ①非转移弧;正极接在 喷嘴上,工件不带电; ②转移弧:喷嘴不接电 源,工件接正极; ③联合弧:喷嘴、工件 均接正极。
五、热喷涂装置和设备 3.等离子喷涂装置
等离子弧和自由电弧 相比较,其弧柱细, 电流密度大,气体电 离度高,因此具有温 度高、能量集中、弧 稳定性好等特点。
四、热喷涂材料
(一)热喷涂线材:
(4)镍及镍合金主要用于耐蚀、耐磨、耐高温涂 层。
表面处理第十一讲热喷涂

热喷涂层的机械性能
热喷涂层的硬度
硬度是热喷涂层机械性能的重要指标之一。 硬度高的涂层具有更好的耐磨性和耐腐蚀性 ,但同时也可能较脆。因此,在选择热喷涂 层时,需要综合考虑其硬度与其他机械性能 的关系。
热喷涂层的韧性
韧性是热喷涂层在受到外力作用时抵抗开裂 和剥落的能力。良好的韧性可以提高涂层的 抗冲击性和使用寿命,特别是在承受交变应 力的场合。
特点
热喷涂技术具有适用范围广、涂层种 类多、涂层性能优良等特点,能够满 足各种不同的表面处理需求。
热喷涂的应用领域
航空航天
用于飞机和航天器的发 动机部件、结构件和功 能件的表面强化和修复
。
能源
用于燃气轮机、蒸汽轮 机等能源设备的耐磨、 耐腐蚀和隔热涂层的制
备。
汽车
用于发动机部件、车身 和底盘的防腐、隔热、 耐磨和装饰涂层的制备
02
环保型喷涂气体
开发环保型喷涂气体,如惰性气 体、还原性气体等,减少对大气 的污染。
03
废旧涂层的回收与 再利用
研究废旧涂层的回收技术,实现 资源的有效利用,降低对环境的 影响。
06
CATALOGUE
热喷涂案例分析
航空航天领域的热喷涂应用
飞机发动机热端部件
热喷涂技术常用于飞机发动机热端部件的表面处理,如涡 轮叶片和燃烧室,以提高耐高温、抗氧化和抗腐蚀性能。
纳米材料
纳米碳管
具有出色的导电、导热性 能,可用于制备功能性涂 层。
纳米氧化物
具有优异的耐腐蚀、抗氧 化性能,可用于制备防腐 、抗氧化涂层。
纳米陶瓷
具有高硬度、高耐磨性, 可用于制备硬质、耐磨涂 层。
03
CATALOGUE
第八讲-热喷涂的原理和特点

局限性:
热效率低 材料利用率低,浪费大 涂层与基体结合强度较低
四、热喷涂的应用
① 防腐蚀 主要用于大型水闸钢闸门、造纸机烘缸、煤矿井 下钢结构、高压输电铁塔、电视台天线、大型钢桥梁、 化工厂大罐和管道的防腐喷涂。 ② 防磨损 通过喷涂修复已磨损的零件,或在零件易磨损部 位预先喷涂上耐磨材料,如风机主轴、高炉风口、汽 车曲轴、机床主轴、机床导轨、柴油机缸套、油田钻 杆、农用机械刀片等。
③ 特殊功能层 通过喷涂获得表层某些特殊性能,如耐高温、隔 热、导电、绝缘、防幅射等,在航空航天和原子能等 部门应用较多。
பைடு நூலகம்
说明:
① 喷涂热源可用燃气火焰、电弧、等离子弧或激光束等。 ② 喷涂材料可为金属、合金、金属氧化物和碳化物、陶 瓷和塑料等,材料形态可为线材、棒料或粉末。 ③ 喷涂的基体可为金属、陶瓷、玻璃、塑料、石膏、木 材、布、纸等固体材料。 ④ 喷涂的涂层厚度为几十微米至数毫米。
二、热喷涂基本原理
1.热喷涂的基本过程
从喷涂材料进入热源到形成涂层,喷涂过程一般 经历四个阶段: (1)喷涂材料被加热到熔化或半熔化状态 (2)喷涂材料的熔滴被雾化 (3)雾化或软化的微细颗粒喷射飞行 (4)微细颗粒撞击基体表面形成涂层
2.涂层的结构
由无数变形粒子互相交错呈波浪式堆叠在一起而 形成的层状组织结构。 组成:变形颗粒、氧化物、气孔和未熔化颗粒
一热喷涂的定义二热喷涂基本原理三热喷涂的分类和特点四热喷涂的应用热喷涂是利用热源将喷涂材料加热到熔化或半熔化状态用高速气流将其雾化并喷射到基体表面形成涂层的技术
第八讲 热喷涂的原理和特点
主要内容
一、热喷涂的定义 二、热喷涂基本原理 三、热喷涂的分类和特点 四、热喷涂的应用
金属表面热喷涂技术
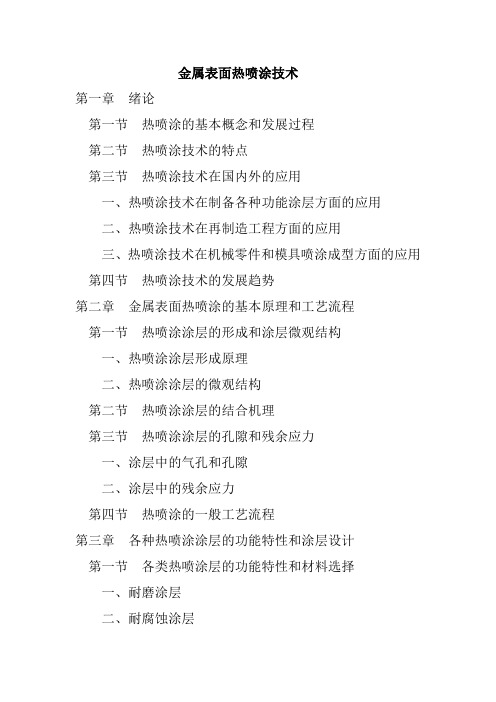
金属表面热喷涂技术第一章绪论第一节热喷涂的基本概念和发展过程第二节热喷涂技术的特点第三节热喷涂技术在国内外的应用一、热喷涂技术在制备各种功能涂层方面的应用二、热喷涂技术在再制造工程方面的应用三、热喷涂技术在机械零件和模具喷涂成型方面的应用第四节热喷涂技术的发展趋势第二章金属表面热喷涂的基本原理和工艺流程第一节热喷涂涂层的形成和涂层微观结构一、热喷涂涂层形成原理二、热喷涂涂层的微观结构第二节热喷涂涂层的结合机理第三节热喷涂涂层的孔隙和残余应力一、涂层中的气孔和孔隙二、涂层中的残余应力第四节热喷涂的一般工艺流程第三章各种热喷涂涂层的功能特性和涂层设计第一节各类热喷涂层的功能特性和材料选择一、耐磨涂层二、耐腐蚀涂层三、耐热与抗高温氧化涂层四、热障涂层五、导电和电绝缘涂层六、间隙控制涂层七、尺寸恢复涂层八、其他特殊功能涂层第二节热喷涂涂层的设计和工艺选择一、热喷涂涂层设计的主要内容和基本步骤二、热喷涂涂层设计的命名和表示方法三、有关涂层设计方法的几个具体问题第四章热喷涂材料第一节热喷涂工艺对喷涂材料的要求第二节热喷涂材料的分类和制备方法一、热喷涂材料的分类二、热喷涂材料的制备方法第三节热喷涂丝材和棒材一、铁基合金丝二、非铁金属和合金丝三、复合丝四、陶瓷棒第四节热喷涂粉末一、纯金属、合金和复合材料粉末二、自熔性合金粉末三、陶瓷和金属陶瓷粉末四、有机材料粉末五、复合粉末六、纳米粉末第五章热喷涂基体的表面预处理第一节表面预加工第二节表面净化处理一、除油处理二、除锈处理第三节表面粗化处理一、喷砂二、机加工粗化三、电火花拉毛粗化第四节黏结底层的制备第五节特殊材质工件的表面预处理第六节非喷涂表面的遮蔽保护一、胶带保护二、涂料保护三、机械保护四、其他保护方法第六章火焰喷涂第七章电弧喷涂第八章等离子喷涂第九章爆炸喷涂和反应喷涂第十章其他喷涂技术及新工艺第十一章热喷涂层的后续处理和加工第十二章热喷涂层生产的质量控制和性能检测第十三章热喷涂的生产安全和环境保护。
表面处理第十一讲 热喷涂
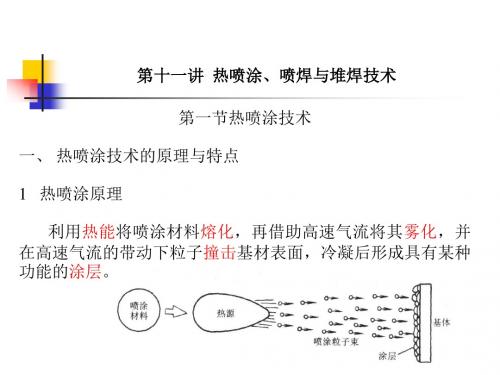
热喷涂材料的要求
(1)热稳定性好,在高温焰流中不升华,不分解(复合粉末)。 (2) 有较宽的液相区,使熔滴在较长时间内保持液相。 ( 3 )与基材有相近的热膨胀系数,以防止因膨胀系数相差过 大产生较大的热应力。 (4) 喷涂材料在熔融状态下应和基材有较好的浸润性,以保 证涂层与基材之间有良好的结合性能。
氩气:易于引弧,等离子弧稳定,有很好的气体保护作用。
氢气:可作为辅助气体起到提高热焓和防氧化的作用。
等离子喷涂工艺(2)
3) 供粉速率:速率过大使熔化不良的粉粒增多,涂层组织 疏松、气孔率增大;速率过低则降低喷涂效率。 4) 喷涂距离和喷涂角:喷涂金属粉末时喷距为75~130mm; 喷涂陶瓷粉末时喷距为50~100mm。喷涂角度以90°为最佳。 5) 喷枪与工件的相对移动速度:移动速度快些为好,可防 止一次喷涂过厚导致涂层内应力过大,还可避免局部过热。
粗化处理的方法(2) 2) 开槽;
粗化处理的方法(3) 3) 电火花拉毛;
4) 喷涂粘结底层。
表 6—2 粘结底层材料及最高使用温度 涂层(质量分数) 温度/℃ 钼 315 620 80% Ni— 20% Al 1010 95% Ni— 5% Al 1260 80% Ni— 20% Cr 980 94% Ni— 6% A1 1316 Ni(Co)CrY
3 涂层结构(1) 涂层是由无数变形粒子互相交错堆叠 在一起,形成一层堆积而成的层状结构。 涂层性能具有方向性,垂直和 平行涂层方向上的性能不一致。 涂层中伴有氧化物等夹杂,存 在部分孔隙,孔隙率4%-20%。
涂层结构(4) 涂层内有一定比例的孔隙,产生原因是: (1) 喷涂角度不同造成的遮蔽效应;空气干燥型酚醛、乙烯树脂、硅树脂、 煤焦油、聚氨酯、亚麻子油、聚酯 烘烤酚醛、酚醛树脂、环氧树脂、聚酯、聚酰胺树脂 环氧树脂、聚酯、聚氨酯 硅酸钠、磷酸盐
第四章 热喷涂技术
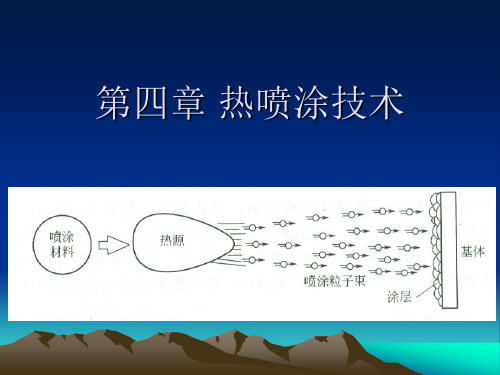
• 2)不锈钢复合丝 • 由不锈钢、镍、铝等几种合金元素复合而 成。 • 其特点是既有Ni-Al放热反应,又有其他强 化元素改善性能,可用于“一步”喷涂, 即涂层同时具有打底层和工作层功能,尤 其适合火焰喷涂, • 主要应用于油泵转子、轴承、汽缸衬里和 机械导轨的表面层。
• 3)Al-Cr2O3药芯管状复合丝 • 用铝皮包覆Cr2O3药芯可制备成分为62% Al-38%Cr2O3的管状复合丝。
待喷涂基体表面的粗化处理已成为不可缺少的
重要的预处理工序。
(2)物理结合 借助于分子(原子)之间的范德华力使喷 涂层附着于基体表面的结合方式。当高速运动 的熔融粒子撞击基体表面、充分变形后,涂层 原子或分子与基体表面原子之间的距离接近晶 格的尺寸时,就进人了范德华力的作用范围。
范德华力虽然不大,但在涂层与基体的结合中
• 5)不锈钢喷涂丝 • 用于焊接的不锈钢丝均可作为热喷涂丝材。 • 铬不锈钢主要用于对强度和硬度要求较高、 耐蚀性要求不太高的场合,其涂层不易开裂, 适宜作为轴类零件层。 • 镍铬不锈钢有良好的工艺性能,在多数酸、 碱介质中具有优异的耐腐蚀性和耐磨性,用 于喷涂水泵轴等。
• 6)Mo喷涂丝 • 钼是一种自黏结材料,可与黑色金属、镍合 金、镁合金、铝合金等形成牢固的结合,常 用作打底层材料。 • 钼是金属中唯一能耐热盐酸腐蚀的金属;钼 与氢不发生反应,可用于氢气保护或真空条 件下的高温涂层;钼涂层中会残留一部分 MoS2杂质,或与硫发生反应生成MoS2固体 润滑膜,适用于喷涂活塞环和摩擦片。 • 但钼不能作为铜和铜合金、镀铬表面和硅铁 表面的涂层。
涂层冷凝收缩时,涂层外层的拉应力、涂层内层的 压应力、组织转变产生的微观应力,结果使涂层产生 残余张应力,应力大小与涂层厚度成正比,当张应力 超过涂层与基材之间结合强度时,涂层残余应力 措施:
热喷涂技术原理及应用课件PPT
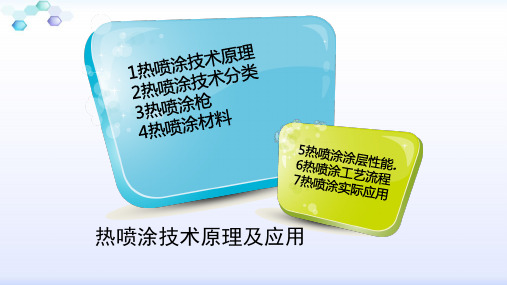
通过喷涂方法的选择可以避免和减轻这一现象的发生。
对东喷方枪 明喷珠咀电部视分塔作钢适结当构变天热动线喷后喷,铝涂可涂用于层喷中涂塑不料可粉末避。免地存在着孔隙,孔隙度的大小与颗粒的温度和速度以及喷涂 例如,如果是陶瓷涂距层,离则和最好喷选涂用等角离度子喷等涂喷; 涂参数有关。一般来说,温度及速度都低的火焰喷涂和电弧喷涂涂 电Sp热la法t fo:rm高a频tio喷n:涂、层线材的电孔爆喷隙涂度都比较高,一般达到百分之几,甚至可达百分之十几。而高温的等离子喷涂 汽轮机、压缩机汽缸涂在长层期及的使高用速中其的中超分面音由速于微火振焰、热喷汽涂流腐涂蚀层及热则变孔形等隙而度发生较变低形状。、最面积低不可等及达深0浅.5各%异的以表下面破。坏,引起泄漏。
3) 熔粒与周围大气接触时间短:这可避免碳化物材料分解和脱碳; 4) 喷涂粉末细微,涂层光滑:粉末粒度为5-45μm,可获得表面光
滑的涂层; 5) 涂层致密,结合强度高:涂层的孔隙率可小于0.1%,结合力可大
于100N/mm2; 6) 气体耗量大、喷涂噪声大:目前喷枪所消耗的气体远大于一般火
焰喷涂; 7) 被广泛使用来制备碳化物(WC-Co、NiCr-Cr3C2)涂层和耐蚀
涂层断面形貌(层状结构)
7热喷涂的实际应用-钢结构防腐当中的应用
汽轮机、压缩机汽缸在长期的使用中其中分面由于微振、热汽流腐蚀及热变形等而发生变形状、面积不等及深浅各异的表面破坏,引起泄漏。
40mm 厚的热障陶瓷涂层,就能使金属零件表面的温度降低 200~300 ℃,并使热端部件免受燃气腐蚀和冲蚀。
它能把高温部件与高温燃气隔离开来,仅 0.
汽轮机、压缩机汽缸在长期的使用中其中分面由于微振、热汽流腐蚀及热变形等而发生变形状、面积不等及深浅各异的表面破坏,引起泄漏。
第八章 热喷涂技术
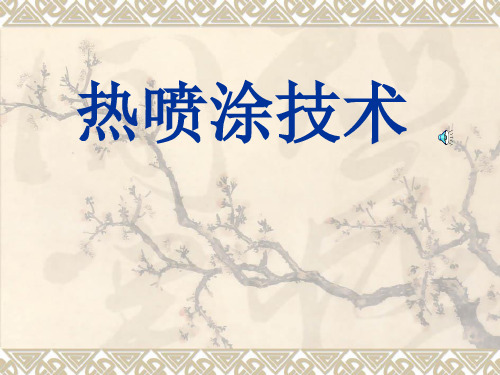
喷涂层的结构特点:
⑴喷涂层是由无数变形粒子相互交错堆叠在一起的层状结构
⑵喷涂层中会出现氧化物夹杂.这是喷涂中,喷涂粒子与周围气体 发生氧化作用.
⑶喷涂粒子和粒子之间会出现孔隙,涂层不致密.这是由于粒子的 变形不充分或有未熔融的粒子冲击到工件表面的缘故.
(二)喷涂层与基体的结合机理
1:机械结合
当熔融的金属粒子以一定的温度和速度撞击到经过净化和粗化 处理的工件表面时,由于表面是凸凹不平的,此时,颗粒变形并 填满基材表面纵横交错的沟槽.同时,颗粒冷凝收缩,与表面的 凹凸处机械地紧紧咬合在一起,而形成“机械结合”,即所谓 “抛锚效应”.
缺点:1:喷涂层与基体结合强度不太高且存在孔隙 2:喷焊件存在变形问题
❖ 热喷涂技术分类及其特点:
二:喷涂层的结构和喷涂层与基体的结合机理
❖ (一)喷涂层的结构
喷涂过程中,具有一定速度和温度的喷涂材料粒子到达工 件表面时,喷涂粒子以一定的动能冲击工件表面,在产生 碰撞的瞬间,粒子的动能转化为热能传给工件,并与工件 的粗糙表面紧密接触产生变形,迅速冷凝收缩呈扁平状 粘结在工件上.喷涂材料粒子连续不断地冲击,在粒子与 工件表面和粒子与粒子之间就会相互交错地粘接在一 起形成喷涂层.其示意图如下:
第三节:氧-乙炔火焰喷涂
❖ 一:氧-乙炔火焰粉未喷涂的原理
它是以氧-乙炔火焰为热源,将喷涂材料粉未加热到熔融状 态,同时借助高速火焰流喷射到经过制备的工件表面上, 冷却后形成喷涂层.
❖
二:氧-乙炔火焰
C2 H2
炔和氧气混合物质的量之比为1:2.5,因空气原因,实
四:氧-乙炔火焰粉未喷涂工艺(课本)
(一)表面预处理.切除工件表面坏层(如疲劳层,腐蚀层,原喷涂 层等);采用一切方法(如加热300℃除油)除去疏松工件表面 的油污;采用酸洗,碱洗,机械方法去除工件表面的氧化层;采 用喷砂,机械方法等使工件表面粗化,粗糙表面可使涂层与 基体形成较强的机械结合,提高涂层的结合强度;对不需要 喷涂的部位进行遮盖,涂刷涂料进行保护.
第五章-热喷涂技术PPT课件

表面粗化处理与清洗过程同样重要。工件表面经过粗化处理后, 可以增大工件表面的活性和增大喷涂层的接触面积,在有些情况 (如喷砂)还可以使工件产生表面压应力,有助于增强工件的抗疲 劳性能。
热喷涂的基本工艺流程图如图2所示
工件表面制备
喷
涂
表 表 表预
底
面面面
净 化
预 加 工
粗热 化
层
喷
喷后处理
涂
工
机封
作
械
层
加 工空
图2 热喷涂的基本工艺流程图
2021
19
1)表面净化
喷涂前,首先须将待喷涂表面净化,彻底清除附着在表面的油 污、油漆、氧化物等,显露出新鲜的金属表面。
2)表面预加工
表面预加工的主要目的是预留一定的喷涂层厚度。
2021
11
涂层形成过程示意图如下:
冲击
碰撞
变形
图1 涂层形成过程示意图
2021
凝固-收缩
12
热喷涂原理示意图
2021
13
涂层形成示意图
2021
14
涂层的结构
涂层结构示意图
2021
15
涂层的形成过程表明,涂层是由无数变形粒子互相交错呈波浪式 堆叠在一起而形成的层状组织结构。
在喷涂过程中由于熔融的颗粒在熔化、软化、加速及飞行及基材表 面接触过程中与周围截至发生了化学反应,使得喷涂材料经喷涂后 会出现氧化物,而且,由于颗粒的陆续堆叠和部分颗粒的反弹散失, 在颗粒之间不可避免地存在一部分孔隙式空洞。因此,喷涂层是由 变形颗粒,气孔和氧化物所组成。
2021
8
热喷涂的主要应用特性
与其他表面工程技术相比,热喷涂在实用性方面有以下方 面的特点:
- 1、下载文档前请自行甄别文档内容的完整性,平台不提供额外的编辑、内容补充、找答案等附加服务。
- 2、"仅部分预览"的文档,不可在线预览部分如存在完整性等问题,可反馈申请退款(可完整预览的文档不适用该条件!)。
- 3、如文档侵犯您的权益,请联系客服反馈,我们会尽快为您处理(人工客服工作时间:9:00-18:30)。
缺点:燃料消耗大,喷涂效率比爆炸Байду номын сангаас涂高,但成本仍然比较高。
现代热喷涂枪
从上至下: 超音速火焰喷枪,
等离子喷枪, 火焰喷枪, 电弧喷枪
第二节 典型热喷涂简介
常用热喷涂的工艺分类
热喷涂工艺
燃烧法
电加热法
火焰喷涂 爆炸喷涂
电弧喷涂 等离子喷涂
线材火焰喷涂 粉末火焰喷涂 超音速火焰喷涂 大气等离子喷涂 低压等离子喷涂 感应等离子喷涂 水稳等离子喷涂
2.1 火焰喷涂
火焰喷涂的基本原理是通过乙炔、氧气喷嘴出口处 产生的火焰,将线材(棒材)或粉末材料加热熔化, 借助压缩空气使其雾化成微细颗粒,喷向经预先处理 的粗糙工件表面使之形成涂层。燃烧气体还可以用丙 烷、氢气或天然气等。
垂直喷射—事实上不可能
二、影响热喷涂涂层质量的主要因素
1. 喷涂工艺的影响 ①工艺方法:
火焰
等离子
电弧
爆炸
超音速
T ~3000℃ ~16000 ℃ 7400 ℃
5000 ℃ 2900 ℃
v 50-200m/s 350m/s
200m/s
720m/s
986m/s
②粉体在加热介质中的运行时间t----t↑,T↑
涂层的形成
二、涂层与基体间的结合强度
1 机械结合: 高速粒子—撞击—粒子微变形—咬合
可见,表面粗化有利于结合强度提高。
2 金属键结合: 当颗粒与基体表面达到原子间距时,会产生金 属键结合。----理论上的确存在,实际上作用极小
3 微扩散结合:高速、高温、熔融或半熔融的粒子撞击到基体 表面,在界面上会造成微小的扩散,使结合力增加。
2. 基体温度低:基材温度一般在30~200℃之间,因此变形小。 3. 操作灵活:可喷涂各种规格和形状的物体,特别适合于大面积涂
层,并可在野外作业。 4. 涂层厚度可控, 范围宽:从几十微米到几毫米的涂层都能制备。 5. 喷涂效率高、成本低:生产效率为每小时数公斤到数十公斤。 6. 局限性:主要体现在热效率低,材料利用率低、浪费大和涂层与
沉积效率
喷涂材料形态
结合强度 (Mpa) 最小孔隙率
最大涂层厚度
喷涂成本
50~100
20~80
60~80% 50~80% 粉末,线材
>7
<12% 0.2~1.0
低
30~500
20~300
90% 70~90%
线材 >10
<10% 0.1~3.0
低
200~1200 800~1200 300~1200
30~800
层可有效地提高基体材料的耐磨损、耐高温或耐腐蚀性能。 Al2O3 、TiO2、Cr2O3、ZrO2等氧化物为最常用的一类陶瓷喷涂 材料。 Al2O3 、TiO2、Cr2O3常用于耐磨损零件,而ZrO2主 要用作热障涂层。
一、按形态分类-----线、棒、粉末 二、按功能分类
耐磨损----陶瓷,铁基,Co基,Ni基合金和难熔 金属
耐腐蚀----Zn、Al、Ni基合金和Al2O3类陶瓷 抗高温----氧化物类陶瓷、Ni-Cr合金和Co基合金 三、按成分分类 金属材料 陶瓷材料 塑料材料 复合材料
3.3 粉末材料
一、非复合型粉末 每个颗粒内成分是均匀一致的,如金属粉、高分子粉、陶瓷粉等。
特点:电弧喷涂只能用于具有导电性能的金属线材。 电弧喷
涂的涂层密度可达70~90%,比火焰喷涂涂层要致密、结合 强度(10~40 MPa)高。且运行费用较低,沉积效率高。电弧 温度可达5000℃, 雾化颗粒速度可达180—335m/s。 应用:是喷涂大面积涂层尤其是长效防腐锌、铝涂层的最佳 选择。
缺点:喷涂效率非常低,运行成本相对较高 。
2.5 超音速喷涂(High Velocity Oxygen Fuel,简称HVOF)
原理:采用高压水冷的反应腔和细长的喷射管,燃料(煤油、乙炔、 丙烯和氢气)和氧气送入反应腔,燃烧产生高压火焰。燃烧火焰被 喷射管压缩并加速喷射出去。喷涂粉末可以用高压轴向送入或从 喷射管侧面送入。
四、喷涂
喷底层(Ni包Al,Al包Ni)--粗化, ↑结合力
喷涂层----0.15-0.2mm/次,总厚度﹤2mm
五、封孔
工件加热到~95℃,涂上石蜡----防腐蚀
表面预处理 表面粗化
预热 喷涂 封孔
热喷涂基体表面预处理
基体金属表面的预处理状况,决定着热喷涂涂层与基体的 结合性能,因此对其使用寿命有决定性的影响。 表面预处理包括表面净化,除去金属表面的油脂、其他污 物、锈、氧化皮、旧涂层、焊接熔粒,以及对表面的粗化 处理。 喷砂、车螺纹、滚花和电拉毛。
2.4 爆炸喷涂
原理:氧气、燃料(如乙炔)和粉末输送到枪管内,点燃混合气体产生 爆炸,使粉末加热、加速,以超音速喷出,沉积在基体表面。每 次喷射后通入氮气流清洗枪管。目前,爆炸喷涂的频率达60Hz。
特点:喷射速度快、结合强度高(85Mpa);涂层密度可达99.9%。焰 流温度不太高,不适合喷涂陶瓷等高熔点材料,但可解决碳化物 高温分解 难题。 一般专用于喷涂碳化物或金属陶瓷涂层。
1.2 热喷涂涂层的质量及影响因素
一、热喷涂涂层常见的缺陷及预防措施 1. 涂层剥落
原因:冷却时涂层与基体收 缩不一致,涂层中产生拉应力。
结合强度低于涂层拉 应力时,剥落。 措施:工件表面--清洁、粗糙 喷涂颗粒—速度↑、
T↑ 工件预热-- ↓涂层应力 涂层保护点—在工件边
缘预置小槽,或堆焊一周。
0.07
0.09
Dmax, μm
26
72
96
110
显然,TaC最易喷涂----实际上仍是Dr所决定
③ 材料的粒径: D↓--T↑、v ↑--结合力↑,涂层质量↑
D太小--价格↑,且易被气流带走。
1.3 热喷涂技术的特点
1. 可在各种基体上制备各种材质的涂层:金属、陶瓷、金属陶瓷以 及工程塑料等都可用作热喷涂的材料;几乎所有固体材料都可以 作为热喷涂的基材。
~800
100~1000
35~55% 50~80%
粉末 >35
未知 未知 粉末 >85
50~70% 70~90%
粉末 >70
<2% 0.05~0.5
高
<0.1% 0.05~0.1
高
<0.1% 0.1~1.2mm
较高
设备特点
简单,可现场 简单,可现场施 复杂,但适合高 较复杂,效率 一般,可现场施工
施工
铝、镍/铝
耐磨保护涂层 轴承修复
耐腐蚀涂层
抗热氧化涂层
2.2 等离子喷涂
等离子喷涂法是利用等离子焰的热能将引入的喷涂粉末 加热到熔融或半熔融状态,并在高速等离子焰的作用下, 高速撞击工件表面,并沉积在经过粗糙处理的工件表面形 成很薄的涂层。涂层与母材的结合主要是机械结合.
2.2 等离子喷涂
原理:等离子喷枪的作用是产生等离子火焰并喷射出高速气流。等 离子喷枪由铜阳极嘴和钨阴极头组成。气体从阴极流向阳极,经 压缩、离化后从阳极喷射出去。压缩后的等离子电弧,通过阳极 孔道喷出后,离子气发生急剧膨胀,将压缩气流加速到亚音速甚 至超音速水平,粉末被迅速加热、加速,并喷涂到基体表面。
2. 裂纹 原因:同上,涂层中拉应力小于膜基结合强度而又大于涂层的抗 拉强度时,涂层开裂。 措施:每次喷涂,薄而均匀(﹤0.15mm)。太厚,收缩应力↑ ↑ 涂层T不要太高,否则收缩应力↑ ↑ (矛盾!因T ↓,结合力↓,涂层易剥落。) 工件预热,缓慢冷却,收缩应力↓
3. 多孔疏松 原因:
孔隙率:2-20%。--是喷涂难题之一 措施: ↑粉末T,全熔最好—但应力又↑
③粉体在加速介质中的运行时间t----t↑,v↑
② 、 ③都取决于工件与喷嘴间的距离s,
S
近距
中距
远距
T 加热不充分,T↓ ~100mm左右T、v 远离热源,冷却,T↓
v
加速不充分,v↓ 最高
空气阻力, v↓
总而言之,喷涂工艺问题就是T、v问题
2. 喷涂材料的影响
①材料成分----决定材料的热扩散系数Dr
粉末火焰喷涂的原理示意图
火焰喷涂特点 1.中心火焰最高可达3000℃ 2.雾化颗粒速度可达10-20m/s 3.适用于熔点低于2500℃材料 4.设备简单,投资低
常用的火焰喷涂涂层及作用
涂层 锌、铝 镍/铝
钼
应用 钢结构的防腐涂层
粘结底层 粘结底层,优异的抗粘着磨损性能
高铬钢 青铜,巴氏合金 不锈钢、镍、塑料
1. 自熔性粉末 在铁、钴、镍基合金中加入强脱氧元素B、Si后,成为一种
能自行脱氧、造渣的低熔点金属。 特点:⑴ 自熔性; B、Si是强脱氧元素,具有脱氧、造渣能力。 ⑵ 低熔点; B、Si加入—形成共晶—熔点↓↓。 ⑶ 湿润性; B、Si使表面氧化物溶解—表面张力↓↓。 ⑷ 良好的固态流动性。
2. 陶瓷材料 具有硬度高、熔点高、热稳定性及化学性能好的特 点,用作涂
第二章 热喷涂技术
定义: 热喷涂—是将喷涂材料加热到熔融或半熔
融状态,用高速气流将其雾化、加速,使其高 速喷射到工件表面形成具有特殊性能的涂层。
热喷涂TiC
第一节 热喷涂的原理及分类
1.1 热喷涂的基本 原理
一、基本过程 1. 加热、加速、熔化
(颗粒状) 2. 雾化(10-100
μm ),再加速--形成高速粒子流。 3. 熔融与半熔融的高 速粒子流撞击到基 材,变形、凝固, 形成涂层。
常用热喷涂技术的工艺特性