铜及铝板带轧制过程中轧机不稳定因素探讨
板带材轧机中辊系误差对轧制精度的影响研究

板带材轧机中辊系误差对轧制精度的影响研究概述板带材轧机是一种常见的金属加工设备,广泛应用于钢铁、有色金属等行业。
在板带材的轧制过程中,轧机中辊系的精度对于产品的成形质量具有重要影响。
因此,研究板带材轧机中辊系误差对轧制精度的影响,对于优化生产工艺、提高产品质量具有重要意义。
一、轧机中辊系误差类型及对轧制精度的影响轧机中辊系误差主要包括凸度误差、偏心误差和直线误差等。
这些误差会直接导致板带材在轧制过程中出现形状和尺寸方面的变化,严重影响产品的成形质量。
1. 凸度误差凸度误差是指辊子在轧制过程中出现的弯曲凹凸现象。
这种误差会导致板带材在轧制过程中受到非均匀的应变,从而影响产品的尺寸和形状。
若凸度误差较大,会导致板带材出现弯曲或塑性变形,严重影响产品的成形质量。
2. 偏心误差偏心误差是指轧机辊子的旋转轴线与材料的轧制轴线不重合所引起的误差。
当偏心误差较大时,会导致轧机在轧制过程中施加的压力不均匀,从而使板带材出现尺寸不匀或形状偏斜的问题,影响产品的外观和质量。
3. 直线误差直线误差是指辊子表面的直线度偏离理论直线度的程度。
辊子的直线度与板带材成形的直线度密切相关,直线误差过大会导致轧制后的板带材出现波浪形状,影响产品的平整度和表面质量。
二、轧机中辊系误差的产生原因板带材轧机中辊系误差的产生主要有以下几个原因:1. 制造误差:轧机辊子的制造和安装过程中存在一定的误差。
例如,加工辊子的磨床或研磨机床的几何精度不足,或者安装过程中的定位误差,都会导致辊子的几何形状不理想,进而引发辊系误差。
2. 磨损和变形:轧机辊子在长时间的使用过程中,由于受到高压和高温的影响,会产生磨损和变形。
这些磨损和变形会导致辊子的几何形状发生变化,进而引发辊系误差。
3. 温度变化:板带材轧机在工作过程中,由于材料的变形和摩擦产生的热量,会导致辊子的温度发生变化。
这种温度变化会导致辊子的物理性质发生变化,进而引发辊系误差。
4. 油膜效应:轧机中的油膜是保证辊子与板带材表面之间形成薄膜的一种润滑方式。
轧机状态对轧制稳定性的影响

750
298.5
297.6
-0.008
0.050
0.9
是
F4
750
-0.037
0.050
4.1
是
290
285.9
F5
500
255.3
265.1
0.072
0.050
-9.8
否
F6
500
-0.039
0.050
5.8
是
276.9
271.1
F7
500
0.032
0.050-ຫໍສະໝຸດ .8是271.6276.4
2,同步性 设备系统旳同步性是确保稳定生产旳最基本旳条件,
例如:精轧机组两侧弯辊缸旳同步性、两侧压下系统 (AGC)旳同步性、侧导板两侧动作旳同步性。设备系 统同步性旳好坏主要取决于设备本身固有旳特征。
3,一致性 实际生产过程中轧机体现出来旳一致性,是衡量轧机
状态旳主要原则,它能够直接反应轧机目前旳状态是否 稳定。
辊缝弹跳
辊缝弹跳差 差(原则 )
刚度差(DSOS)
是否达标
F1
750
305.5
304.3
-0.010
0.050
1.2
是
F2
750
312.0
307.8
-0.033
0.050
4.2
是
F2
750
297.7
298.6
0.008
0.050
-0.9
是
F3
750
298.0
288.7
-0.081
0.050
9.3
否
F3
时间、材质横截面积旳大小、灌浆旳质量、地脚螺 栓直径及拉拔力旳大小等。 影响辊系刚度旳原因
最新整理铜及铝板带轧制过程中轧机不稳定因素探讨.docx

最新整理铜及铝板带轧制过程中轧机不稳定因素探讨在铜及铝板带轧制过程中难免会发生不稳定现象,导致这种现象的原因较多,其问题主要集中在轧机上,从而对带材高精度生产造成严重影响。
于有色金属板的性能区别于钢铁的性能,因此对轧机的要求有所不同。
本研究中,笔者对轧机轧制过程中不稳定现象从工艺、设备等的角度进行分析,以供同行工作者参考。
当前,随着科学技术的日益发展,在有色金属的加工技术中,对板带材精度和质量随之提出了更高的要求。
为确保轧机轧制在板带轧制过程中的稳定性,消除外扰因素很重要,只有认真发现铜及铝板带轧制过程中存在的一些问题,才能消除于这些不稳定因素的发生导致产品质量出现问题的现象。
轧机系统稳定性受轧制材料的质量的影响1.1轧制过程中发生辊颤与材料相关采用铸轧坏料在铝粗轧机进行轧制的调试时,通常采用轧制速度及压下量等常规轧制工艺参数,整个轧机有时会发生颤动的现象,这使工艺参数的调整受到影响。
出现这种现象主要是因铸轧坯料铸轧后表面氧化膜化厚,其主要因放置时间较长所致,材料表面性能及其内部组织在长时间后均会发生变化,使轧材与辊面的摩擦系统不断降低,再加上摩擦力与咬入力小较,而导致打滑的现象发生,而导致轧辊颤振。
1.2来料偏差不宜过大一般试验过程中经常采用厚度偏差不同的带坯,而轧制厚度偏差的带坯为0.1~0.12mm时,相比0.15mm的轧制厚差带坯,轧机稳定性较高。
轧机系统稳定性受工艺润滑剂的影响经常发生辊颤还有一个重要原因是于润滑剂与所选择的工艺参数不匹配,对于轧机系统的振动因被轧金属与辊缝处辊面之间的摩擦因素而受到影响主要体现在以下几个方面:(1)在轧机系统的垂直运动中辊缝的润滑油膜能起到一定的阻尼作用,其阻尼作用在油膜摩擦系数越低的情况下越小,则会降低系统的稳定性质,轧机在外部等量扰动的情况下极易发生振动;(2)在充分润滑的条件下,会减小辊缝摩擦,而在干扰因素不稳定的情况下,辊缝状态的波动会增大,则会严重影响到系统的稳定性;(3)辊缝的摩擦系数越小,轧机轧制压力所受到的摩擦压力也就越小,轧制压力受到轧制张力的影响也就越大,从而会降低轧机系统的稳定性,使轧机容易发生振动。
铜带轧机调试过程中的问题及解决办法
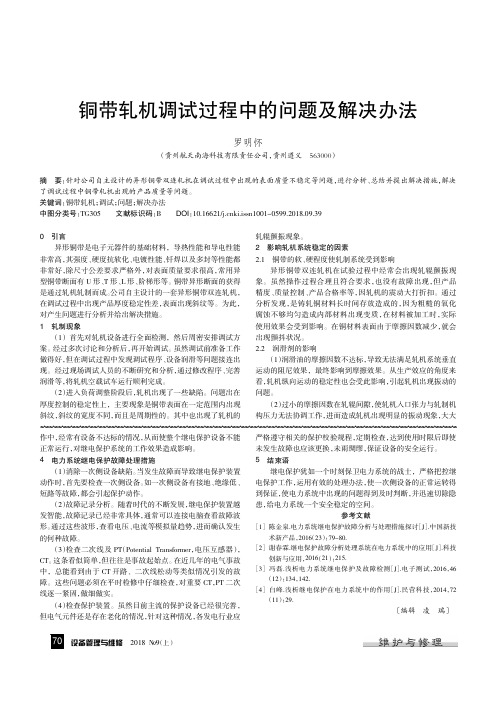
设备管理与维修2018翼9(上)铜带轧机调试过程中的问题及解决办法罗明怀(贵州航天南海科技有限责任公司,贵州遵义563000)摘要:针对公司自主设计的异形铜带双连轧机在调试过程中出现的表面质量不稳定等问题,进行分析、总结并提出解决措施,解决了调试过程中铜带轧机出现的产品质量等问题。
关键词:铜带轧机;调试;问题;解决办法中图分类号:TG305文献标识码:BDOI :10.16621/ki.issn1001-0599.2018.09.390引言异形铜带是电子元器件的基础材料,导热性能和导电性能非常高,其强度、硬度抗软化、电镀性能、钎焊以及多封等性能都非常好,除尺寸公差要求严格外,对表面质量要求很高,常用异型铜带断面有U 形、T 形、L 形、阶梯形等。
铜带异形断面的获得是通过轧机轧制而成。
公司自主设计的一套异形铜带双连轧机,在调试过程中出现产品厚度稳定性差,表面出现斜纹等。
为此,对产生问题进行分析并给出解决措施。
1轧制现象(1)首先对轧机设备进行全面检测,然后周密安排调试方案。
经过多次讨论和分析后,再开始调试。
虽然调试前准备工作做得好,但在调试过程中发现调试程序、设备润滑等问题接连出现。
经过现场调试人员的不断研究和分析,通过修改程序、完善润滑等,将轧机空载试车运行顺利完成。
(2)进入负荷调整阶段后,轧机出现了一些缺陷。
问题出在厚度控制的稳定性上,主要现象是铜带表面在一定范围内出现斜纹,斜纹的宽度不同,而且是周期性的。
其中也出现了轧机的轧辊颤振现象。
2影响轧机系统稳定的因素2.1铜带的软、硬程度使轧制系统受到影响异形铜带双连轧机在试验过程中经常会出现轧辊颤振现象。
虽然操作过程合理且符合要求,也没有故障出现,但产品精度、质量控制、产品合格率等,因轧机的震动大打折扣。
通过分析发现,是铸轧铜材料长时间存放造成的,因为粗糙的氧化腐蚀不够均匀造成内部材料出现变质,在材料被加工时,实际使用效果会受到影响。
在铜材料表面由于摩擦因数减少,就会出现颤抖状况。
有色金属轧制设备常见故障及其维护研究

有色金属轧制设备常见故障及其维护研究【摘要】由于有色金属轧制设备所处的工作条件复杂,这就导致轧机出现故障的种类较多,严重影响了轧制的质量和效率。
本文主要介绍有色金属轧制设备主要部件的常见故障及其日常维护保养措施,以便更好地对其进行维护,提高有色金属轧制设备使用寿命和工作性能。
【关键词】有色金属;轧制设备;检修;维护有色金属轧制设备中最主要的就是轧机,它是使轧件在转动的轧辊间产生塑性变形,轧出所需断面形状和尺寸的钢材。
主要由轧辊、轧辊轴承、机架压下装置、轨座和导位装置等组成。
由于其所处的工作环境往往是伴随着高温、潮湿、摩擦、粉尘、重负载等等,,这些因素使轧机的各部件容易产生种种故障。
如不及时发现和处理,不仅会影响正常生产,造成企业重大经济损失,甚至会酿成灾祸。
1 常用的轧制设备故障检测方法(1)机械测量法。
是利用机械器具对对被测物理量进行直接测量。
如用杠杆应变计测量应变,用机械测振仪测量轧机振动参量等。
(2)光测法。
是利用光学的基本理论,用实验的方法去研究物体中的应力、应变和位移等力学问题。
如光弹法、云纹法、红外测温仪测温以及激光扫描测径仪测量轧辊直径等。
(3)声测法。
是利用声波或超声波在介质中的传播速度和波形衰减情况估价被测物质的质量。
如超声波测量仪来检测轧机部件的抗拉强度和内部缺陷等。
(4)电测法。
是先将被测物理量转换成电量,再用电测仪表进行测量的方法。
如用电阻应变仪表测量应力应变,用热电高温计测温度,用涡流检测仪检测轧辊内部缺陷等。
2 轧制设备轧辊的故障检修及维护措施轧辊是轧制设备的重要组成部件,其主要用于轧制过程中使有色金属产生塑性变形,以生产不同尺寸的有色金属板带材产品,轧辊正常稳定的运行对提高产品的数量和质量都起着至关重要的作用。
因此,对其故障进行高效检修和维护显得十分重要2.1 轧辊常见故障及其产生原因轧辊常见的失效方式主要有辊身表面出现崩坑或裂纹、辊体断裂、辊体硬度衰变等三个方面。
铝轧机板形等质量问题分析及采取措施

铝轧机板形等质量问题分析及采取措施一、板形不良.1、冷轧机:(1)每三个月由钳工检查一次喷杆梁的减振喉是否损坏.及时更换(2)每两个月由操作手和电工一起检查喷嘴是否有堵塞或者在轧制时,操作手发现板形明显不良或者喷嘴喷油异常时,马上对喷嘴进行测试检查.(3)针对不同宽度,不同厚度,操作手及质检作好记录,并及时通知设备部进行一起分析,是否需要对板形目标曲线进行更改及试验(不同的板形目标曲线会对喷淋产生一定的影响). (4) 有些薄板,建议操作手可以进行手动喷淋干预,总结分析板形不良原因.(5)所有辊系检测每季度一次,由技术组完成,水平度及平行度。
2、粗轧机:(1)建议要求厂家增加手动调节喷淋功能(因为粗轧机不能对局部喷油进行手动干预,其不良板形只能通过弯辊,倾斜等手段进行辊型控制).(2)定期检查压平辊平行及水平度.1次/季度。
(3)每两个月由操作手和电工一起检查喷嘴是否有堵塞或者在轧制时,操作手发现板形明显不良或者喷嘴喷油异常时,马上对喷嘴进行测试检查.(4)工艺道次合理安排,张力合理使用,轧辊凸度建议尝试支承辊凸度0.02mm;工作辊凸度0.05-0.07mm.3、精轧机:(1)定期检查喷杆梁喷嘴.(2)定期检查压平辊平行及水平度.1次/季度(3)喷射梁及板型仪备品备件要尽快订货,因为膜片及滤芯都是消耗品需定期更换。
(4)工艺道次合理安排,张力合理使用,轧辊凸度建议尝试支承辊凸度0.02mm;工作辊凸度0.05-0.07mm.针对以上情况,将对三台轧机定期作以下的检查和测试:(1)定期对入口张紧辊进行检查辊系.(2)定期对板形辊平行度,水平度进行检查.(3)定期对工作辊辊隙进行检查.(4)定期对轧制线进行检查.(5)对薄板的局部板形不良,操作手是否可以采用手动调节喷淋,对相同的铝卷进行持续跟踪和比较.二、打底印.1、目前对部分变形的套筒进行车削,保证套筒的外圆一致。
2. 生产要加强套筒管理严格区分退火用套筒和非退火用套筒,决不能混用3、合理使用张力速度,匹配要合理.三、铝粉堆积1、入口可增加板面清洗装置.2,加强板式过滤器维护,确保过滤能力满足生产需求3,定期换纸,严格执行硅藻土及白土纤维素的添加工艺,搅拌箱内不能吸空4,每班要对轧制油透光率进行检测设备部2017-4-18。
轧制缺陷及质量控制
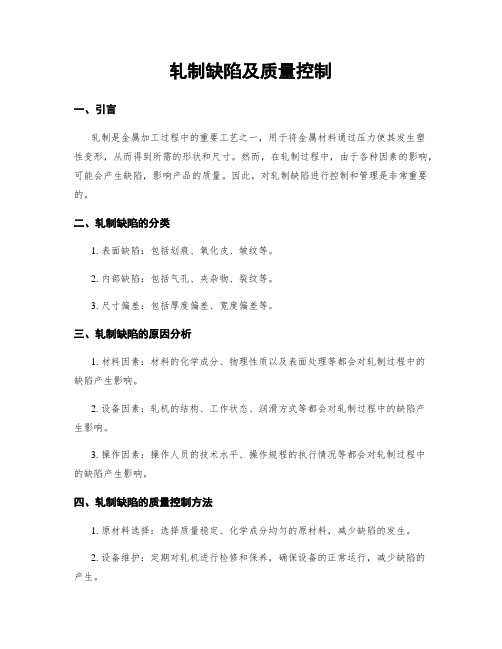
轧制缺陷及质量控制一、引言轧制是金属加工过程中的重要工艺之一,用于将金属材料通过压力使其发生塑性变形,从而得到所需的形状和尺寸。
然而,在轧制过程中,由于各种因素的影响,可能会产生缺陷,影响产品的质量。
因此,对轧制缺陷进行控制和管理是非常重要的。
二、轧制缺陷的分类1. 表面缺陷:包括划痕、氧化皮、皱纹等。
2. 内部缺陷:包括气孔、夹杂物、裂纹等。
3. 尺寸偏差:包括厚度偏差、宽度偏差等。
三、轧制缺陷的原因分析1. 材料因素:材料的化学成分、物理性质以及表面处理等都会对轧制过程中的缺陷产生影响。
2. 设备因素:轧机的结构、工作状态、润滑方式等都会对轧制过程中的缺陷产生影响。
3. 操作因素:操作人员的技术水平、操作规程的执行情况等都会对轧制过程中的缺陷产生影响。
四、轧制缺陷的质量控制方法1. 原材料选择:选择质量稳定、化学成分均匀的原材料,减少缺陷的发生。
2. 设备维护:定期对轧机进行检修和保养,确保设备的正常运行,减少缺陷的产生。
3. 工艺控制:严格控制轧制工艺参数,如轧制温度、轧制速度等,以减少缺陷的发生。
4. 检测手段:采用先进的无损检测技术,如超声波检测、X射线检测等,及时发现并排除缺陷。
5. 操作培训:加强操作人员的培训,提高其技术水平和操作规范性,减少人为因素对缺陷的影响。
五、轧制缺陷的质量控制效果评估1. 缺陷检测率:通过统计检测到的缺陷数量和总产量,计算缺陷检测率,以评估质量控制的效果。
2. 缺陷修复率:通过统计修复的缺陷数量和检测到的缺陷数量,计算缺陷修复率,以评估质量控制的效果。
3. 产品合格率:通过统计合格产品的数量和总产量,计算产品合格率,以评估质量控制的效果。
六、案例分析以某钢铁公司的轧制生产线为例,该公司采用了上述的质量控制方法,并进行了持续的改进。
经过一段时间的实践,缺陷检测率从原来的10%降低到了5%,缺陷修复率从原来的50%提高到了80%,产品合格率从原来的80%提高到了95%。
铜板带在粗轧完以后经常在边部看到一条明显的起皮是什么原因?

铜板带在粗轧完以后经常在边部看到一条明显的起皮是什么原因?铜板是一种常用的金属材料,被广泛应用于建筑、电子、航空等多个领域。
然而,在生产过程中,铜板带在粗轧完以后经常会出现边部起皮的情况,这会降低铜板带的品质和使用寿命。
本文将从铜板的制造工艺、材料特性、轧制参数等多个方面来探讨铜板带起皮的原因,并提出相应的解决办法。
制造工艺铜板的制造工艺包括锭化、浇铸、轧制、退火等多个环节。
在轧制过程中,将铜锭放入轧机中进行轧制,使其逐渐变薄。
这个过程通常需要经历多道工序,每道工序会将铜板带的厚度减少一定的比例。
在每道工序中,都要对轧制参数进行调整,以确保铜板带能够顺利地通过轧机,并且保持良好的表面质量。
边部起皮可能与轧制工艺有关。
在轧制过程中,铜板带会经过拉伸、弯曲等多个力学变形过程,这会导致边部应力过大,从而引起边部起皮。
同时,在冷轧过程中,由于金属的韧性有限,边缘区域较易产生硬化,这也可能是边部出现起皮的原因。
材料特性铜板的高导电性、高热传导性以及良好的可加工性是其重要的特性,但这些特性也可能会影响铜板在冷轧过程中的表现。
在冷轧过程中,铜板会发生较大的塑性变形,因此,其晶粒会被极大地拉长。
在铜板晶粒拉长的同时,它的位错密度也会随之增加,这会使得边部区域的应力和位错密度比中心区域高得多。
同时,铜板的金属组织和化学成分也会影响铜板在冷轧过程中的表现。
如果铜板的化学成分不均匀,或者含有过多的杂质,都有可能导致钢材硬化不均匀,从而引起边部起皮。
轧制参数轧制参数是决定铜板带品质的重要因素。
在冷轧过程中,轧制的质量和轧制参数的选择对铜板带的品质有着直接影响。
轧制参数如轧制压力、轧制速度、辊缝等参数都会对铜板带的品质产生重要影响。
辊面的状况也会影响边部的起皮情况。
如果辊面粗糙,那么在铜板带经过辊面时就会容易产生起皮现象。
因此,高质量、平整的辊面是确保铜板带表面质量的重要保障。
解决办法为确保铜板带的品质,可以采取以下几种措施:1.加强材料检测:在生产过程中,对铜板的化学成分、金属组织等进行严格检测,确保铜板的质量符合标准。
SCR4500连铸连轧生产线设备运行不稳定因素探究
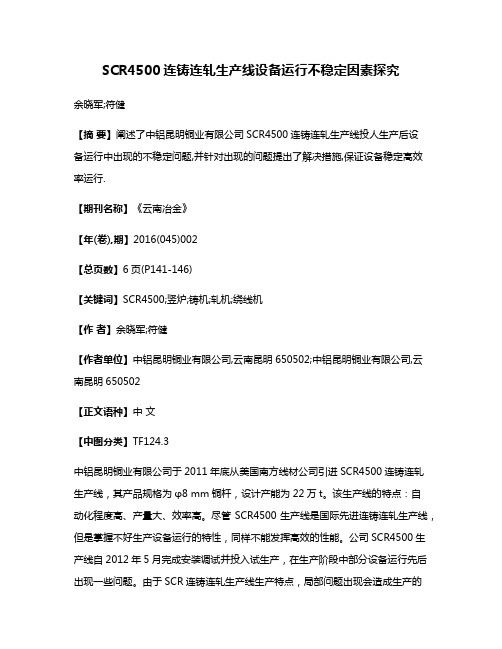
SCR4500连铸连轧生产线设备运行不稳定因素探究余晓军;符健【摘要】阐述了中铝昆明铜业有限公司SCR4500连铸连轧生产线投人生产后设备运行中出现的不稳定问题,并针对出现的问题提出了解决措施,保证设备稳定高效率运行.【期刊名称】《云南冶金》【年(卷),期】2016(045)002【总页数】6页(P141-146)【关键词】SCR4500;竖炉;铸机;轧机;绕线机【作者】余晓军;符健【作者单位】中铝昆明铜业有限公司,云南昆明650502;中铝昆明铜业有限公司,云南昆明650502【正文语种】中文【中图分类】TF124.3中铝昆明铜业有限公司于2011年底从美国南方线材公司引进SCR4500连铸连轧生产线,其产品规格为φ8 mm铜杆,设计产能为22万t。
该生产线的特点:自动化程度高、产量大、效率高。
尽管SCR4500生产线是国际先进连铸连轧生产线,但是掌握不好生产设备运行的特性,同样不能发挥高效的性能。
公司SCR4500生产线自2012年5月完成安装调试并投入试生产,在生产阶段中部分设备运行先后出现一些问题。
由于SCR连铸连轧生产线生产特点,局部问题出现会造成生产的不连续,整套生产设备的整体效能不能发挥出来。
因此,设备稳定运行是发挥生产线综合效能的保证。
竖炉系统包含:上料小车、燃气竖炉、保温炉、上下溜槽及撇渣槽中间包,主要功能是完成原料熔化处理,达到浇铸要求。
铸轧系统包含:铸机、夹送辊机、废剪、铸坯预修整机、粗精轧机,主要功能是完成铸坯浇铸,经过预修整机处理并符合轧制要求后,进入粗精轧机完成铸坯的轧制,轧制出符合规格的铜线杆。
收线系统主要包括:输送轨道、夹紧输送机、绕线机、过磅称量、压实打包及绕模包装,主要功能是完成铜线杆的收线处理,并完成过磅和包装工作。
辅助系统包含:铸机冷却循环水系统、工艺冷却循环水系统、粗精轧乳化液系统、粗精轧润滑油系统、NAPS无酸清洗系统、鼓风机系统、涂蜡系统等,主要功能是为满足竖炉系统、铸轧系统、收线系统主体生产设备的运行需求及生产工艺控制要求,提供辅助控制。
铝热轧卷轧制错层因素分析

0 前言
热轧是变形铝及铝合金板带材生产流程中非常 重要和关键的生产工序,通过热轧将铸造组织转变 为加工组织。热轧不但为冷轧工序提供坯料,而且 还能直接轧制成品厚度。热轧的组织、表面质量和 板形状况对后部工序有着强烈的遗传性,甚至对最 终产品的质量状况起着决定性作用[1]。
热轧卷错层是影响产品外观质量的重要问题。 人们通常通过提高设备精度、拓宽设备功能、优化 工艺模型和管理方法的改进来解决这一问题。
接关系。通过设备相关部件的排查,提出了处理方法和改良措施,并成功应用于铝热轧卷实际生产中。
关键词:铝热轧卷;轧制力差;错层;原因分析
中图分类号:TG339
文献标识码:B
文章编号:1005-4898 (2019) 01-0035-03
doi:10.3969/j.issn.1005-4898.2019.01.10
通过检查,发现以上因素不是造成铝卷错层的 根本原因。
(6) 经对 iba 数据分析对比,确定缺陷的产生 与卷取过程中的力控、位控不当和轧制过程头尾板 型控制差有关,这些原因都容易造成卷取前期和卷 取后期不平稳,最终形成错层缺陷。具体分析基于 以下原因:
表 1 为错层卷和正常卷 iba 数据的对比情况。 从 iba 对照数据上看,错层卷的轧制力波动值明显 大于正常卷,且波动的周期不是一个固定值。
21381-4 HF308
8.97
1.74
无错层
由表 1 中数据可以看出,错层卷的最大轧制力 波动周期和最大轧制力波动幅值都较大,这是错层 卷原因的直接体现。
3 轧制力波动原因的查找
通过上述排查,我们明确了轧制力波动是造成 错层产生的直接原因。为了进一步了解轧制力波动 与错层产生之间的关系,明确造成错层的根本原 因,我们进行了下列试验。
铝带热轧过程中的跑偏分析及控制技术
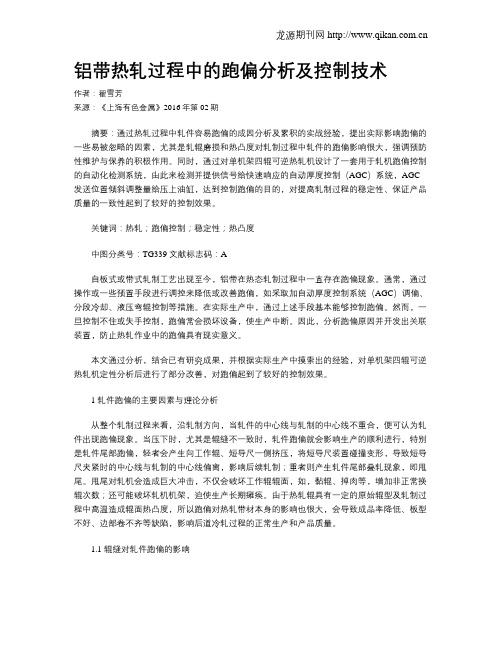
铝带热轧过程中的跑偏分析及控制技术作者:翟雪芳来源:《上海有色金属》2016年第02期摘要:通过热轧过程中轧件容易跑偏的成因分析及累积的实战经验,提出实际影响跑偏的一些易被忽略的因素,尤其是轧辊磨损和热凸度对轧制过程中轧件的跑偏影响很大,强调预防性维护与保养的积极作用。
同时,通过对单机架四辊可逆热轧机设计了一套用于轧机跑偏控制的自动化检测系统,由此来检测并提供信号给快速响应的自动厚度控制(AGC)系统,AGC 发送位置倾斜调整量给压上油缸,达到控制跑偏的目的,对提高轧制过程的稳定性、保证产品质量的一致性起到了较好的控制效果。
关键词:热轧;跑偏控制;稳定性;热凸度中图分类号:TG339 文献标志码:A自板式或带式轧制工艺出现至今,铝带在热态轧制过程中一直存在跑偏现象。
通常,通过操作或一些预置手段进行调控来降低或改善跑偏,如采取加自动厚度控制系统(AGC)调偏、分段冷却、液压弯辊控制等措施。
在实际生产中,通过上述手段基本能够控制跑偏。
然而,一旦控制不住或失手控制,跑偏常会损坏设备,使生产中断。
因此,分析跑偏原因并开发出关联装置,防止热轧作业中的跑偏具有现实意义。
本文通过分析,结合已有研究成果,并根据实际生产中摸索出的经验,对单机架四辊可逆热轧机定性分析后进行了部分改善,对跑偏起到了较好的控制效果。
1 轧件跑偏的主要因素与理论分析从整个轧制过程来看,沿轧制方向,当轧件的中心线与轧制的中心线不重合,便可认为轧件出现跑偏现象。
当压下时,尤其是辊缝不一致时,轧件跑偏就会影响生产的顺利进行,特别是轧件尾部跑偏,轻者会产生向工作辊、短导尺一侧挤压,将短导尺装置碰撞变形,导致短导尺夹紧时的中心线与轧制的中心线偏离,影响后续轧制;重者则产生轧件尾部叠轧现象,即甩尾。
甩尾对轧机会造成巨大冲击,不仅会破坏工作辊辊面,如,黏辊、掉肉等,增加非正常换辊次数;还可能破坏轧机机架,迫使生产长期瘫痪。
由于热轧辊具有一定的原始辊型及轧制过程中高温造成辊面热凸度,所以跑偏对热轧带材本身的影响也很大,会导致成品率降低、板型不好、边部卷不齐等缺陷,影响后道冷轧过程的正常生产和产品质量。
详细解读关于铜带制作过程中可能出现的缺陷问题
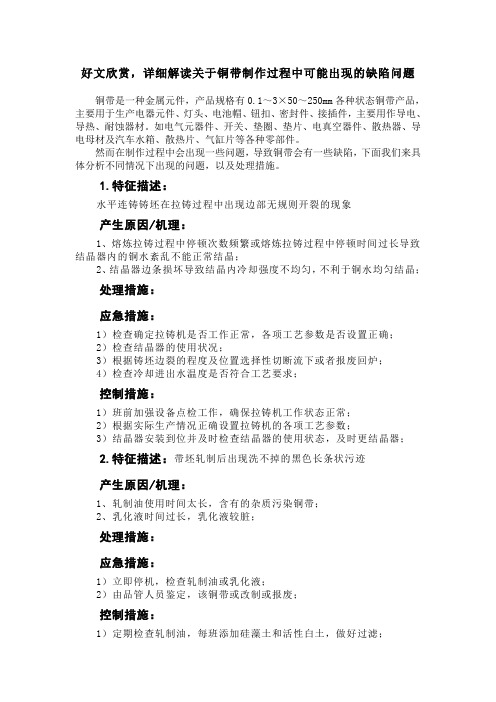
好文欣赏,详细解读关于铜带制作过程中可能出现的缺陷问题铜带是一种金属元件,产品规格有0.1~3×50~250mm各种状态铜带产品,主要用于生产电器元件、灯头、电池帽、钮扣、密封件、接插件,主要用作导电、导热、耐蚀器材。
如电气元器件、开关、垫圈、垫片、电真空器件、散热器、导电母材及汽车水箱、散热片、气缸片等各种零部件。
然而在制作过程中会出现一些问题,导致铜带会有一些缺陷,下面我们来具体分析不同情况下出现的问题,以及处理措施。
1.特征描述:水平连铸铸坯在拉铸过程中出现边部无规则开裂的现象产生原因/机理:1、熔炼拉铸过程中停顿次数频繁或熔炼拉铸过程中停顿时间过长导致结晶器内的铜水紊乱不能正常结晶;2、结晶器边条损坏导致结晶内冷却强度不均匀,不利于铜水均匀结晶;处理措施:应急措施:1)检查确定拉铸机是否工作正常,各项工艺参数是否设置正确;2)检查结晶器的使用状况;3)根据铸坯边裂的程度及位置选择性切断流下或者报废回炉;4)检查冷却进出水温度是否符合工艺要求;控制措施:1)班前加强设备点检工作,确保拉铸机工作状态正常;2)根据实际生产情况正确设置拉铸机的各项工艺参数;3)结晶器安装到位并及时检查结晶器的使用状态,及时更结晶器;2.特征描述:带坯轧制后出现洗不掉的黑色长条状污迹产生原因/机理:1、轧制油使用时间太长,含有的杂质污染铜带;2、乳化液时间过长,乳化液较脏;处理措施:应急措施:1)立即停机,检查轧制油或乳化液;2)由品管人员鉴定,该铜带或改制或报废;控制措施:1)定期检查轧制油,每班添加硅藻土和活性白土,做好过滤;2)根据乳化液的使用情况,及时更换乳化液(每月至少更换一次);3.特征描述:单边边部不平,类似于波浪状的规律性缺陷产生原因/机理:因轧制过程中边部与中间的不均匀变形产生1、轧辊两边压下调整不一致,来料两边厚度不均匀,性能不均匀时易出现单边浪;2、轧制中两边冷却润滑不均匀;3、喂料不对中或轧件跑偏;处理措施:应急措施:1)停止轧制,检查轧件是否对中,两侧压下调整是否一致,润滑是否均匀,并及时作出相应调整;控制措施:1)各工序间相互配合,控制好横向公差,波动处须在工艺流程卡上标明;2)坯料退火要横向均匀;3)润滑要沿轧辊辊面合理配置流量和强度;4)轧辊要及时磨削更换;4.特征描述:铜带表面存在倾斜一定角度的规律性印痕产生原因/机理:1、轧制加工率过大导致油膜破裂;2、轧制过程中润滑不够,轧辊出现缺陷;处理措施:应急措施:1)立即停止轧制,调整轧机辊缝,减小加工率;2)更换轧辊;控制措施:1)根据制定的轧制制度,适当增加轧制道次,以减小道次加工率;2)及时更换轧辊;5.特征描述:铜带表面局部有小坑,有时分布具有规律性产生原因/机理1、轧机工作辊、除油辊等辊上粘有铜粉等颗粒物,在铜带运行过程中,挤压铜带表面产生小坑;2、酸洗线的橡胶辊上粘有硬颗粒,铜带运行程中产生压坑;处理措施应急措施:设备立即停止运行,检查各辊系,若辊表面粘有硬颗粒,及时清理或换辊;控制措施:1)班前检查各工作辊及支撑辊是否粘有异物,如有异常,及时处理;2)产品生产过程中,必须对每卷料头部的生产情况进行检查,确保整张铜带合格;6.特征描述:铜带表面在长度方向上出现规律性损伤产生原因/机理:1、轧机工作辊、除油辊等粘铜,造成铜带表面挫伤;2、轧机工作辊未打磨好;3、酸洗过程中的辊子粘有赃物;处理措施应急措施:1)立即停机,并仔细检查工作辊等的状态;2)已经挫伤的铜带根据具体情况进行改制或者报废;控制措施:1)工模具的管理规范,每班上班前要检查轧辊并跟踪使用状况;2)做好来料检查,确保本工序不加重上道工序的缺陷;3)每班确保设备的工业卫生良好;7.特征描述:铜带层与层之间粘在一起,轻微的开卷时有明显的“吱啦”声,开卷后粘结处有明显的白印,严重的铜带之间粘在一起很难切割分离产生原因/机理:1、一些未完全清理的轧制介质等在高温下挥发或碳化导致铜带之间真空状态很难分开;2、轧机或酸洗线收卷时张力过大,退火后导致带面烧结一起;3、退火温度过高、时间过长,铜带过于软化,结合更加紧密;处理措施应急措施:1)轻微烧粘的经过判定可以继续下一道工序;2)烧粘严重的直接返回熔炼并用切割机进行切割,然后重新熔炼;控制措施:1)适当降低铜带退火温度和退火时间;2)加强中间加工工序各类介质(主要是轧制油)的清理;3)控制好收卷的张力;8.特征描述:铸锭颜色较深呈黑褐色,边部及中间都有不规则的裂纹产生原因/机理:1、铸锭中杂质元素含量超标(如Pb等),非固溶性物质较多;2、拉铸过程冷却水量与拉铸速度不匹配;3、熔炼炉中的铜水温度过低;4、结晶器表面粗糙,内壁挂渣;处理措施应急措施:1)严格把关每炉的化验成份,少加料尽量把炉子内的铜水全部拉铸出来,然后锯切成小段再分数炉进行重新熔炼;2)将熔炼炉铜水温度升高,保温拉铸;控制措施:1)对原料进行严格把关,每炉按要求控制成分;2)按照工艺要求控制拉铸速度和冷却水量;3)保证拉铸过程中熔炼炉的铜水温度控制在工艺要求范围;4)每炉转铜后及时清理结晶器内壁,并涂抹碳粉类涂料;9.特征描述:锯开铸锭尾部,存在一段中心空洞,易产生于拉铸后尾部很平的铸锭产生原因/机理:1、铜液结晶时,冷却与拉速配合不当造成液穴较深;2、拉铸至尾部时未减速,铸锭尾部中间部分液体补缩不及时;处理措施应急措施:1)根据缩孔的深度适量锯切掉一部分,如果长度在 3.8m以上的话可以流入下道工序;2)缩孔过深导致长度不足 3.8m的话直接锯切成小段并分开回炉重新熔炼;控制措施:1)控制冷却水的流量与压力,确保冷却水进出水温差;2)拉铸收尾阶段时,按工艺进行减速拉铸,并在快结束时停机一段时间,确保补缩的完全;10.特征描述:铸锭表面出现气孔,表现为表面深度不确定的孔洞产生原因/机理:1、熔炼过程中喷火除气不到位,拉铸过程中铸锭含有未及时排出的气体;2、拉铸过程中铜水未进行有效地保护,导致铜水吸气;3、拉铸过程中振动未开启,导致排气效果不好;4、拉铸速度较快,排气不及时;处理措施应急措施:1)较浅的气孔采用磨光机将铸锭的棱角打磨平整、光滑;2)很深的气孔如果在头尾处可进行锯切(保证铸锭长度至少3.8m);3)很深的气孔如果位于铸锭中部就必须整根报废回炉;控制措施:1)加强熔炼的搅拌喷火等除气工作;2)拉铸时使用熔融或干燥的硼砂进行覆盖,防止水汽带入及吸气现象;3)检查并确保整个拉铸过程中振动是开启的;4)适当降低拉铸速度,保证有足够的时间排气;11.特征描述:黄铜半连铸坯锯开后出现平行于宽度方向的中空现象,通常情况整根锭坯都有产生原因/机理:1、铸造速度过快,中部铜液未及时凝固,但出结晶器后,中部铜液补凝固收缩造成中空;2、结晶器冷却水冷却速度过快,浇注温度不合理;处理措施:应急措施:1)调整工艺,对于上述问题的铸锭及时回炉;控制措施:1)调整H65的出炉温度为1070℃—1080℃,H62为1045℃—1055℃,H65以上牌号为1080℃—1090℃;2)将原来的一次捞渣改为两次捞渣,具体为:喷火——断电捞渣——静置(3—5分钟)——再次捞渣;3)降低拉铸速度控制在110mm/min—115mm/min;12.特征描述:铸锭表面出现白色的硼砂颗粒,有时嵌入的深度较深,不易去除产生原因/机理:拉铸人员加硼砂的方式不当,导致粉状硼砂在结晶器内积聚成块未融化;处理措施:应急措施:1)采用磨光机或者铁刷子将铸锭表面的硼砂颗粒清除掉;2)铸锭表面硼砂难以清理的将铸锭分批回炉;控制措施:1)拉铸前认真检查硼砂的状态,确保硼砂的干燥(经过烘箱脱水);2)拉铸人员在加粉状硼砂时应少量多次,使硼砂均匀覆盖在液面上,确保硼砂能充分散开并熔融;3)采用新型的加入方式,熔融硼砂法;13.特征描述:铸锭在热轧时出现白色颗粒,多时则聚在一起形成条状产生原因/机理:1、拉铸过程中加入的硼砂粒度不均匀,块状的硼砂在拉铸时未被充分熔化而嵌入铸锭内部;2、热轧的时候随着铸锭的变形,一些粘附在表层的块状硼砂被铜带变形包裹;处理措施应急措施:1)继续轧制,在收卷时确定其影响,可适当调节铜带的铣面量;控制措施:1)规范硼砂的加入方式:多次少量,并充分粉碎硼砂颗粒;2)采用新型设备将硼砂熔融后再进行添加;3)热轧前,对铸锭表面做简单的清扫、打磨;14.特征描述:黄铜带坯轧制后出现长条状起皮,起皮层可用手撕去,起皮层下有一层夹杂异物产生原因/机理:铸锭中有夹杂缺陷,轧制后夹杂处与基体延伸性能不一,造成起皮;处理措施:应急措施:1)停机检查,若缺陷在头部或尾部,将其剪掉;2)若缺陷严重且在中间,与品管人员沟通,或改制或回炉;控制措施:1)熔铸时断电静置一段时间待杂质上浮或下沉后,将渣捞干净;2)熔炼炉要经常的对炉壁进行清理,使用一段时间后要重新打炉,保证铜水洁净;(铜合金熔铸)。
轧制缺陷及质量控制

轧制缺陷及质量控制一、引言轧制是金属加工过程中的重要环节之一,对于确保产品质量具有重要意义。
本文将详细介绍轧制过程中常见的缺陷类型及其产生原因,并探讨如何通过质量控制手段来预防和解决这些缺陷问题。
二、轧制缺陷类型及原因1. 表面缺陷表面缺陷是指轧制产品表面出现的瑕疵,如麻点、划痕、氧化皮等。
其主要原因包括:- 轧辊表面粗糙度不合格:轧辊表面粗糙度过高或过低都会导致产品表面出现缺陷;- 轧辊表面污染:轧辊表面存在杂质、油污等污染物会直接影响产品表面质量;- 轧制过程中的热裂纹:高温下,金属材料容易发生热裂纹,进而导致表面缺陷。
2. 尺寸偏差尺寸偏差是指轧制产品的尺寸与设计要求之间存在的差异。
常见的尺寸偏差包括过大或过小的厚度、宽度、长度等。
尺寸偏差的原因主要有:- 轧机设备调整不当:轧机设备的调整不当会导致产品尺寸偏差;- 材料厚度不均匀:原材料的厚度不均匀会直接影响轧制产品的尺寸;- 轧机辊系磨损:轧机辊系磨损会导致轧制压力不均匀,进而影响产品尺寸。
3. 内部缺陷内部缺陷是指轧制产品内部存在的缺陷,如气孔、夹杂物等。
内部缺陷的主要原因包括:- 原材料质量问题:原材料中存在气孔、夹杂物等缺陷;- 轧机设备故障:轧机设备的故障会导致轧制产品内部出现缺陷;- 轧制过程中的温度控制不当:温度控制不当会导致金属材料内部产生缺陷。
三、质量控制手段1. 轧辊表面处理为了避免表面缺陷的产生,可以采取以下措施:- 定期对轧辊进行磨削和抛光,确保其表面粗糙度符合要求;- 加强轧辊的清洁工作,防止污染物附着在轧辊表面;- 对轧辊进行定期检测,及时发现并修复轧辊表面的磨损和裂纹。
2. 轧机设备调整与维护为了控制尺寸偏差,需要进行轧机设备的调整与维护工作:- 对轧机设备进行定期的检查和维护,确保其工作状态良好;- 对轧机设备进行精确的调整,确保产品尺寸与设计要求一致;- 定期检测轧机辊系的磨损情况,及时更换磨损严重的辊子。
精轧跑偏探究

带钢跑偏及防范措施探讨周世军热轧厂轧钢车间内容摘要:带钢在轧机里跑偏容易造成轧烂、甩尾及边部刮伤,影响产品质量和产量,同时也增加了设备如衬板的磨损。
我厂热轧卷在3月出现了批量边部刮伤,为了解决这个问题,本文从理论和实际分析了带钢在精轧机组跑偏的原因,找出了控制带钢跑偏的防范措施并加以了实施,从4月和5月的质量统计来看,边部刮伤得到了较好的控制。
关键词:跑偏防范措施1 前言轧制过程中带钢跑偏会导致生产运行不稳定, 直接影响轧制产量、成品质量、设备寿命等。
对于热连轧, 由于其采用的是微张力轧制, 且每轧一块钢都存在穿带、正常轧制、抛钢三个阶段,带钢跑偏时有发生, 并往往伴生带钢板形不良问题, 如单边浪、不对称双边浪、楔形等。
因此, 在热轧生产中, 带钢跑偏问题一直较为突出, 值得深入研究。
2 带钢跑偏机理从整个轧制过程来看, 只要沿轧制方向上带钢的中心线与轧制中心线不重合时, 便认为发生带钢跑偏。
所以跑偏包括带钢的整体侧移和带钢的侧弯。
或者, 带钢跑偏可分为发生在轧制变形区内的跑偏及发生在轧制变形区外(包括轧机入口侧和轧机出口侧) 的跑偏。
轧制变形区内的跑偏又存在工作辊偏斜时的带钢跑偏及工作辊不偏斜时的带钢跑偏两种情况。
2. 1 轧制变形区内的带钢走偏图1轧制变形区内带钢跑偏机理图1a) 为工作辊辊不偏斜时带钢的受力简图。
由于辊系弯曲变形, 作用在带钢表面的单位轧制压力的方向与垂直方向有一偏角U, 由此产生一个水平方向的分量pm sinU。
由于带钢横向尺寸或性能不对称、轧辊轴向状态不同等原因, pm 及U沿带钢宽度方向各点均不同。
当pm 水平分量的合力不等于零时, 即2 pm sinU≠0, 带钢必存在横向运动趋势, 假设带钢存在向传动侧运动的趋势, 随之伴生单位摩擦力f m。
设pm 与f m 合力的水平分量为p , 其大小见式(1)。
p = pm sinU- f m co sU 操作侧- pm sinU- f m co sU 传动侧 (1)当带钢整个宽度上pm 与f m 合力的水平分量p 之和大于零时, 即Σp > 0, 带钢将向传动侧跑偏。
铝板带轧制常见故障分析及处理

2012-6-6
11
• b、原因分析 • ①、产生厚度中心点飘移的原因:出口测厚 仪测量数据不真实和操作人员对厚度中心点 设定不恰当所致。 影响出口测厚仪测量准确性的因素有:校 核测厚仪的标准板厚度不准确引起厚度中心 点设定不准确,测厚仪厚度补偿系数不准确 ;放射源发出的射线被其他物件所挡;测厚 仪自动清零功能不稳定。
2012-6-6
9
b、厚度控制
①FF-AGC:Feed-forward Automatic Gauge Control ②MF-AGC : Mass Flow - Automatic Gauge Control ③MV-AGC : Multi-Variable - Automatic Gauge Control ④MN-AGC : MoNitor - Automatic Gauge Control ⑤TLC : Tension Limit Control ⑥RE-AGC : Roll Eccentricity - Automatic Gauge Control
2012-6-6
24
1.3.6 自动板形控制
• 自动板形控制过程如下图
板形辊
分区冷却
弯辊控制
倾辊控制 板形检测 一次板形 二次板形 高次板形
板 形 控 制 调 节 器
目标板型
图1.
2012-6-6
自动板形控制系统过程图
25
1.3.7 板形问题案例
• 断带原因分析
2012-6-6
26
1.4 表面质量
• 出现板形不良的直接原因是轧件宽向上延 伸不均。
2012-6-6
20
• 出现板形不良的根本原因是:轧件在轧 制过程中,轧辊产生了有害变形,致使 辊缝形状不平直,从而产生波浪。
轧制缺陷及质量控制

轧制缺陷及质量控制一、引言轧制是金属加工中的一种重要工艺,用于将金属坯料通过辊道压制成所需的形状和尺寸。
然而,在轧制过程中,可能会浮现一些缺陷,如裂纹、夹杂物和凹坑等,这些缺陷会降低产品的质量和性能。
因此,进行轧制缺陷的控制和质量管理是至关重要的。
二、轧制缺陷的分类1. 裂纹:轧制过程中,由于应力集中或者金属内部的缺陷,可能会导致裂纹的产生。
裂纹可以分为表面裂纹和内部裂纹两种类型。
2. 夹杂物:夹杂物是指金属中的非金属杂质,如氧化物、硫化物和氮化物等。
夹杂物会影响金属的强度和韧性。
3. 凹坑:凹坑是指金属表面的凹陷,可能是由于辊道表面的磨损或者金属表面的缺陷导致的。
三、轧制缺陷的原因分析1. 材料因素:材料的成份和内部缺陷会直接影响轧制过程中的缺陷产生。
例如,材料中含有大量夹杂物或者过多的硬质相,会增加裂纹和凹坑的产生风险。
2. 设备因素:轧制设备的质量和性能直接影响轧制过程中的缺陷控制。
例如,辊道的磨损和不平整会导致凹坑的产生,辊道的间隙不合适会增加夹杂物的产生风险。
3. 工艺因素:轧制工艺参数的选择和控制对缺陷的产生和控制起着重要作用。
例如,轧制温度、轧制速度和轧制压力的选择需要根据材料的性质和要求进行合理调整。
四、轧制缺陷的控制措施1. 材料控制:选择合适的原材料,并进行必要的检测和筛选,以确保材料中的夹杂物和缺陷控制在合理范围内。
2. 设备维护:定期检查和维护轧制设备,确保辊道的平整度和间隙的合适性,减少凹坑和夹杂物的产生。
3. 工艺优化:根据不同材料的特性和产品的要求,优化轧制工艺参数,如温度、速度和压力等,以减少裂纹和凹坑的产生。
4. 检测技术:采用先进的无损检测技术,如超声波检测和磁粉探伤等,对轧制产品进行全面的检测,及时发现和排除缺陷。
5. 质量管理:建立完善的质量管理体系,包括质量检验、质量控制和质量反馈等环节,确保轧制产品的质量稳定和持续改进。
五、轧制缺陷的质量控制1. 检测方法:采用适当的检测方法对轧制产品进行质量控制,如外观检查、尺寸测量和物理性能测试等。
铜及铝板带轧制过程中轧机不稳定因素探讨

铜及铝板带轧制过程中轧机不稳定因素探讨铜及铝板带轧制是制造铜及铝材料的重要工艺之一,但在实际的生产过程中常常会遭遇到轧机不稳定的问题,这不仅影响了生产的进展,还可能导致铜及铝板带的质量问题。
因此,本文将探讨铜及铝板带轧制过程中轧机不稳定的因素。
1. 轧辊的磨损轧辊作为铜及铝板带轧制过程中最核心的部件之一,其磨损程度直接影响轧机的稳定性。
如果轧辊磨损过度,其直径和尺寸就会发生变化,这会导致轧辊的转速和轧制力的变化,进而影响铜及铝板带的轧制质量。
如果轧辊磨损严重,就需要更换新的轧辊或进行修复。
2. 机械结构的松动铜及铝板带轧制过程中,机械结构的松动也是导致轧机不稳定的因素之一。
如果轧机的主机、传动系统、承载系统等关键组件出现松动的情况,就会引发轧辊的晃动、振动等现象,导致铜及铝板带的轧制不稳定。
因此,在轧机工作前应对其各个部分进行彻底的检查和维护,确保机械结构的紧固和稳定。
3.滚道的磨损与变形滚道作为承载物的重要组成部分,直接关系到轧机的稳定性和铜及铝板带的轧制效果。
如果滚道出现磨损或变形,轧辊就会失去支撑,造成轧制力的不稳定,影响铜及铝板带的轧制效果。
因此,在日常的轧机维护中,需要对滚道进行定期检查和维护。
4. 温度的变化在铜及铝板带轧制过程中,温度是极其重要的因素之一。
如果轧机所处的环境温度过低或过高,就会对铜及铝板带的轧制造成影响。
高温环境容易导致轧辊扭曲变形;低温环境则可能导致轧辊表面出现冰霜,磨损程度增加。
因此,在铜及铝板带轧制过程中,需要控制好温度,确保轧机稳定工作。
铜及铝板带轧制过程中轧机不稳定的因素是多方面的,要想保证铜及铝板带的质量,需要从轧机的各个方面做好维护和管理。
轧制缺陷及质量控制
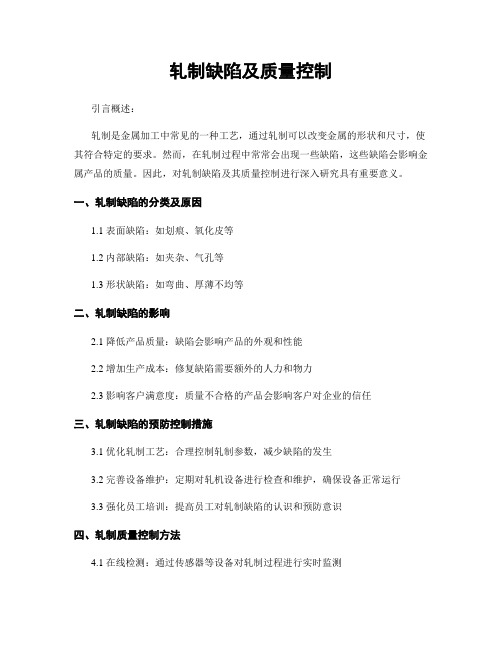
轧制缺陷及质量控制
引言概述:
轧制是金属加工中常见的一种工艺,通过轧制可以改变金属的形状和尺寸,使其符合特定的要求。
然而,在轧制过程中常常会出现一些缺陷,这些缺陷会影响金属产品的质量。
因此,对轧制缺陷及其质量控制进行深入研究具有重要意义。
一、轧制缺陷的分类及原因
1.1 表面缺陷:如划痕、氧化皮等
1.2 内部缺陷:如夹杂、气孔等
1.3 形状缺陷:如弯曲、厚薄不均等
二、轧制缺陷的影响
2.1 降低产品质量:缺陷会影响产品的外观和性能
2.2 增加生产成本:修复缺陷需要额外的人力和物力
2.3 影响客户满意度:质量不合格的产品会影响客户对企业的信任
三、轧制缺陷的预防控制措施
3.1 优化轧制工艺:合理控制轧制参数,减少缺陷的发生
3.2 完善设备维护:定期对轧机设备进行检查和维护,确保设备正常运行
3.3 强化员工培训:提高员工对轧制缺陷的认识和预防意识
四、轧制质量控制方法
4.1 在线检测:通过传感器等设备对轧制过程进行实时监测
4.2 人工检验:对轧制后的产品进行目视检查和尺寸测量
4.3 抽样检测:定期抽取产品进行全面检验,确保产品质量符合标准
五、轧制缺陷处理方法
5.1 修磨:对表面缺陷进行修磨处理,恢复产品表面光洁度
5.2 热处理:对内部缺陷进行热处理,消除缺陷并提高产品性能
5.3 重新轧制:对形状缺陷的产品进行重新轧制,确保产品尺寸和形状符合要求
总结:
轧制缺陷及质量控制是金属加工中一个重要的环节,只有通过科学的方法对轧制缺陷进行预防和控制,才能生产出高质量的金属产品,提高企业的竞争力和市场占有率。
希望本文的内容能够对相关行业的从业人员有所帮助。
轧机断带原因

轧机断带原因
在金属加工领域,轧制是一种常见的工艺,可以将原材料压制成板材、棒材等形状。
然而,有时候在轧制过程中会出现断带现象,导致生产中断,影响生产效率。
那么,造成轧机断带的原因有哪些呢?
1. 材料问题:材料的硬度、厚度、宽度等因素都会影响轧机的正常运行。
如果材料过硬、过厚或过宽,轧机可能无法将其压制成所需形状,从而产生断带现象。
2. 轧机问题:轧机的质量和性能也会影响加工效果。
如果轧机设备出现故障或使用时间过长,可能导致轧机无法正常工作,从而产生断带现象。
3. 操作问题:操作者的技能水平和操作流程也会影响轧机的运行。
如果操作者技能不够熟练或操作流程不规范,可能会导致轧机产生断带现象。
4. 温度问题:轧制过程中,材料的温度对轧机的运行也有很大影响。
如果温度过高或过低,轧机可能无法正常运作,从而产生断带现象。
综上所述,造成轧机断带的原因有很多,需要从多个方面进行控制和修正。
只有在材料、轧机、操作和温度等各个方面都得到合理的控制,才能有效避免轧机断带的发生,提高生产效率和质量。
- 1 -。
- 1、下载文档前请自行甄别文档内容的完整性,平台不提供额外的编辑、内容补充、找答案等附加服务。
- 2、"仅部分预览"的文档,不可在线预览部分如存在完整性等问题,可反馈申请退款(可完整预览的文档不适用该条件!)。
- 3、如文档侵犯您的权益,请联系客服反馈,我们会尽快为您处理(人工客服工作时间:9:00-18:30)。
铜及铝板带轧制过程中轧机不稳定因素探讨
Revised by Hanlin on 10 January 2021
铜及铝板带轧制过程中轧机不稳定因素探讨在铜及铝板带轧制过程中难免会发生不稳定现象,导致这种现象的原因较多,其问题主要集中在轧机上,从而对带材高精度生产造成严重影响。
由于有色金属板的性能区别于钢铁的性能,因此对轧机的要求有所不同。
本研究中,笔者对轧机轧制过程中不稳定现象从工艺、设备等的角度进行分析,以供同行工作者参考。
当前,随着科学技术的日益发展,在有色金属的加工技术中,对板带材精度和质量随之提出了更高的要求。
为确保轧机轧制在板带轧制过程中的稳定性,消除外扰因素很重要,只有认真发现铜及铝板带轧制过程中存在的一些问题,才能消除由于这些不稳定因素的发生导致产品质量出现问题的现象。
轧机系统稳定性受轧制材料的质量的影响
1.1轧制过程中发生辊颤与材料相关
采用铸轧坏料在铝粗轧机进行轧制的调试时,通常采用轧制速度及压下量等常规轧制工艺参数,整个轧机有时会发生颤动的现象,这使工艺参数的调整受到影响。
出现这种现象主要是因铸轧坯料铸轧后表面氧化膜化厚,其主要因放置时间较长所致,材料表面性能及其内部组织在长时间后均会发生变化,使轧材与辊面的摩擦系统不断降低,再加上摩擦力与咬入力小较,而导致打滑的现象发生,而导致轧辊颤振。
1.2来料偏差不宜过大
一般试验过程中经常采用厚度偏差不同的带坯,而轧制厚度偏差的带坯为0.1~0.12mm时,相比0.15mm的轧制厚差带坯,轧机稳定性较高。
轧机系统稳定性受工艺润滑剂的影响
经常发生辊颤还有一个重要原因是由于润滑剂与所选择的工艺参数不匹配,对于轧机系统的振动因被轧金属与辊缝处辊面之间的摩擦因素而受到影响主要体现在以下几个方面:(1)在轧机系统的垂直运动中辊缝的润滑油膜能起到一定的阻尼作用,其阻尼作用在油膜摩擦系数越低的情况下越小,则会降低系统的稳定性质,轧机在外部等量扰动的情况下极易发生振动;(2)在充分润滑的条件下,会减小辊缝摩擦,而在干扰因素不稳定的情况下,辊缝状态的波动会增大,则会严重影响到系统的稳定性;(3)辊缝的摩擦系数越小,轧机轧制压力所受到的摩擦压力也就越小,轧制压力受到轧制张力的影响也就越大,从而会降低轧机系统的稳定性,使轧机容易发生振动。
从上述分析中可以看出:轧机在辊缝摩擦系数较小的情况下容易发生振动。
轧机系统稳定性受轧制速度的影响
厂在调试一台冷轧机过程中,可看到轧机有严重的辊颤现象。
对轧机各部分性能进行检查,发现问题出现在轧制时轧机速度上,如将速度设定在4m/s时,其始终保持着3.9~4.1的传动速度,期间有出现周期性摆动,而导致轧机辊颤,并且有带材厚薄不均的现象。
通过对轧机主传动和卷取机电气反复调整后,在速度稳定的情况下,消除了辊颤的现象。
轧机系统的稳定性及其外部的扰动能量决定着其是否会发生自激振动,轧机系统会受到轧机轧制速度高低的影响,其主要体现在:(1)在轧制速度不断提高的情况下,轧机周围会有越来越多的扰动因素,并且扰动强度也越来越高,那么要确保其平稳就必须保证其速度较低;(2)轧制速度较低时,轧机谐振频率会高于外扰频率,不容易出现共振;而当轧制速度越高的情况下,其工作辊入口张力变化与运动的关系将越紧密,系统的自激关系也就越强烈,从而会增强各种外扰频率,轧机系统稳定性越差的情况下,便容易出现振动。
此外,轧机辊缝中的润滑情况也会受到轧制速度的影响。
润滑液膜在速度越高的情况下厚度越大,因此在辊缝一定时,带材的厚度公差会直接受到速度高低的影响。