钢中氢的来源及控制对策 ppt课件
10-应力腐蚀开裂-氢致开裂

四、氢致开裂的机理——氢鼓泡(生成氢分子)
氢鼓泡机理示意图
➢ H2S是弱酸,在酸性溶 液中主要以分子形式存在;
➢ 在金属表面阴极反应生 成大量的氢原子;
➢ 氢原子渗入金属内部, 通过扩散达到缺陷处,析出 氢气产生高压;
➢ 非金属夹杂物(如Ⅱ型 MnS)为裂纹的主要形核位 置。
34
抑制氢鼓泡的措施
机械原因:材料受力变形时造成钝化 膜破坏。
17
2、溶解(裂纹扩展)
➢ 裂纹扩展的可能途径:预先存在活性通道和应变产生的 活性通道。 ➢ 活性通道理论(拉伸应力较小时)
大的应力作用在裂缝尖端应力集中,使表面膜破裂。 合金中预先存在一条对腐蚀敏感的通道,在特定介质条 件下成为活性阳极。 形成活性通道可能性有:合金成分结构差异;晶界或亚 晶界;局部应力集中及应变引起阳极晶界区;应变引起表面 膜局部破裂;塑性变形引起的阳极区等。
氢原子
d
氢分子
a
c b
表面铁原子
e
h
+
++
++ h’
f
渗碳体或
g
固溶体碳原子
g’
内部铁原子
钢的氢腐蚀机理模型示意图
31
铁素体晶体结构和显微组织 含碳少
奥氏体晶体结构和显微组织 含碳多
抑制氢腐蚀的措施
➢ 温度:各种钢发生氢腐蚀的起始温度为200oC以上。 ➢ 氢分压:氢分压低时,发生表面脱碳难以鼓泡或开裂。 ➢ 介质气体:含氧或水蒸气时,降低氢进入钢中的速度; 含H2S时,孕育期变短。 ➢ 合金元素:碳含量增加,孕育期变短;加入形成碳化物 金属(Ti、Nb、Mo、W、Cr),减少甲烷生成;MnS为裂 纹源的引发处,应去除。 ➢ 热处理和冷加工。
氢腐蚀开裂PPT课件

• 低的氢溶解度 • 无散裂 • 自始至终形成氢化物的微粒 • 对失效高灵敏 • 一般发生在从高温冷却到室温的过程中
氢化物形成的开裂
• 钝化
Ti
氢化物形成的开裂
• 钝化
Ti
氢化物形成的开裂
• 钝化
Ti
氢化物形成的开裂
• 钝化
Ti
氢化物形成的开裂
• 防护措施
– 内在现象 – 氢和金属高温反应的结果 – 补救措施
氢脆
裂缝端
σ
氢脆
• 机理
σ
H2(气体)
游离的化学吸附 物理吸附
σ
氢脆
• 机理
σ
H2(气体)
氢扩散
σ
氢脆
• 恢复始态理论
σ
σ σmax
H2(气体) x
σ
氢脆
• 表面减少理论
– 氢的吸附减少了金属的表面自由能 – 裂缝尖端扩展 – 可以解释低压氢环境下高强度钢的裂纹扩展
氢脆
• 平面压力理论
– 在金属成型期间渗氢发生 – 在微孔中可能形成高压氢 – 与氢鼓泡同样机理
• 降低操作温度 • 热处理
氢化物形成的开裂
• 设计指标
– 降低材料强度 – 减少高温操作时的碳含量 – 避免高温操作时使用钛
• 减少氢含量
– 热处理 (加工和焊接) – 使用缓蚀剂 – 保持储存时的干燥环境
– 脆裂可能发生在焊缝周围 – 含氢的焊棒可能引入氢脆 – 措施
• 将低氢焊棒储存在干燥处 • 焊接后进行局部热处理
氢脆
• 防护措施
– 设计: 降低材料强度 – 生产: 在生产区域和热处理时减少氢源 – 焊接: 妥善储存和处理焊接棒 – 补救措施: 在减压条件下,100-650°C烘烤可
浅谈钢中氢的危害和防止措施

圆点 , 2为典型 的开放型气孔截面形貌。 图
钢中自点从发 现这种 缺 陷到现在 已有 9 0多年 了, 但对其形成机理仍 不十分清楚 。 目前 , 较为普
遍的观点是 , 白点的产生与钢 中的氢 有关 , 即在 由奥
性能 ; 破坏钢 材 的连续性 , 钢材易 于脆断 ; 使 由于 白
点 严 重破 坏 了 金 属 基 本 的 连 续 性 , 且 又 有 成 群 出 而
现的特点 , 一个炉号的钢中有 白点存 在时 , 用该炉号 钢锭锻造 的大多数工件都有 , 通常是 全炉报废 , 对钢 材危害极 大, 因此又把 白点称为钢材的癌症 。
增大 , 气泡有 向薄弱处或 者表 面移动 的趋势 。气 泡
2 1 年第 4期 00
南钢 科技 与管理
3 7
内壁呈现涟漪状 , 无氧化 , 也不 会 出现脱碳 现象。这 是 由于气泡形 成于凝 固过程 中, 内壁 与外界 空气 隔 绝所致 ( 如图 1 所示 ) 。即使气泡上浮 的速度大 于钢 水凝 固的速度 , 有时也会产生气孔 , 因为在结 晶器壁 钢水 弯月面处 , 气体排 除仍然 困难 , 种情况下产生 这 的气孔 大多 为 开放 型。此类 气 孔截 面 呈冰 糖 葫芦
关键词 : 气泡 气孔 白点 延迟裂纹 氢
Dic so n Ha m f Hy o e o S e la d Pr v ntv e s r s s us i n o r o dr g n t t e n e e i e M a u e
金属冶炼中的氢对材料性能的影响

02
氢对金属材料性能的影响
氢对金属力学性能的影响
总结词
氢在金属中可以形成氢化物,降低金属的强度和韧性,使金属变脆,力学性能下降。
详细描述
在金属冶炼过程中,氢可以溶解在金属中形成氢化物。这些氢化物在金属晶体中形成空位或位错,阻碍了金属的 滑移和攀移,导致金属的强度和韧性降低。因此,氢对金属的力学性能具有显著的负面影响,使金属变脆,容易 发生断裂。
分子态氢
在金属熔体表面或气相中,氢可 以以分子形式存在,如氢气或水 蒸气。
氢与金属的相互作用机制
溶解与扩散
在高温下,氢在金属中的溶解度较高 ,并随着温度的降低而降低。溶解的 氢会通过扩散作用在金属中迁移。
氢与金属元素的反应
在某些条件下,氢与金属元素可以发 生化学反应生成氢化物。这些氢化物 的形成会对金属的性能产生影响。
氢冶金工艺优化
通过改进工艺流程和设备,提高氢冶金过程 的效率和安全性。
降低成本与能耗
通过开发新型催化剂和优化反应条件,降低 氢冶金过程的成本和能耗。
基础理论研究
深入研究氢与金属的相互作用机制,为新型 氢冶金技术的开发提供理论支持。
环保与可持续发展
结合绿色化学理念,发展环境友好的氢冶金 技术,减少对环境的负面影响。
优化冶炼工艺
通过改进熔炼、连铸和轧制等工艺,降低氢的含量和 分布。
氢检测与监控
定期对金属材料进行氢含量检测,并实时监控冶炼过 程中的氢浓度。
氢对环境的影响与处理
温室效应
氢气是一种温室气体,大 量排放会对气候变化产生 影响。
爆炸风险
高浓度的氢气可能引发爆 炸或火灾,对工业安全构 成威胁。
污水处理
金属冶炼过程中产生的含 氢废水需要经过处理后才 能排放,以避免对环境造 成污染。
氢冶金第次三修订 ppt课件
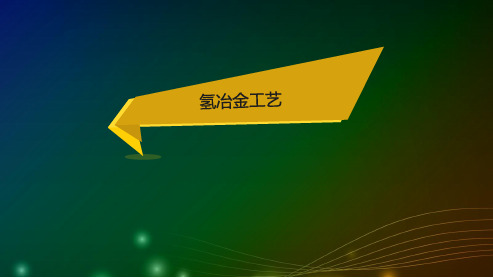
三·直接还原炼铁与氢冶金
气基自重整竖炉中直接还原反应机理如下: CH4+H2O→CO+H2 CH4+3Fe→Fe3C+2H2 H2+FeO→Fe+H2O CO+FeO→Fe+CO2 CO2+H2→CO+H2O
从反应式中不难看出:
(1)原料中的CH4参与反应,产生H2,为氢冶金提供氢源。 (2)氧化铁还原主要靠氢(还原性气体中H2含量要求达到70%,30%的CO当然也
Fe2O3+3CO→2Fe+3CO2
H2/CO=18.667/1.333=14.0
经过化学方程式计算,可以得到氢的还原潜能与一氧化碳的还原潜能相比较,前者是后 者的14.0倍。
由此可见,大力开发和发展氢冶金,可以大大提高金属还原效率,成倍地提高金属冶炼的 生产能力和生产效率。同时,可以大大减少金属冶炼过程中碳还原剂的消耗,从而大大降低 钢铁生产中的煤耗,确保钢铁工业可持续发展。
还原:Fe2O3+3H2=2Fe+3H2O 供热:2C+O2=2CO 制氢:CO+H2O=H2+CO2 总反应为:Fe2O3+3C+3/2O2=2Fe+3CO2
该工艺思想解决了当前熔融还原工艺碳直接还原需高热量和强还原气氛的矛盾。该工艺每吨铁 的理论碳耗为320kg/t。铁浴炉中铁氧化物的还原是一个非常复杂的过程,煤加入反应器中 无法完全避免参与还原,因此,实际能耗要高于理论值。如何发挥氢气在熔融还原中的作用,是该 工艺的关键。
还原氢气的制取
由于钢铁企业生产属于大规模生产,如何制 取足量氢气是氢冶金工艺应用于生产必须面临的 问题。目前常用的氢气制取方法有电解水法和石 油裂化法,但这两种方法不仅资源利用效率低, 所用能量来源依然以含碳能源为主,无法有效降 低碳排放。
熔敷金属中扩散氢测试方法
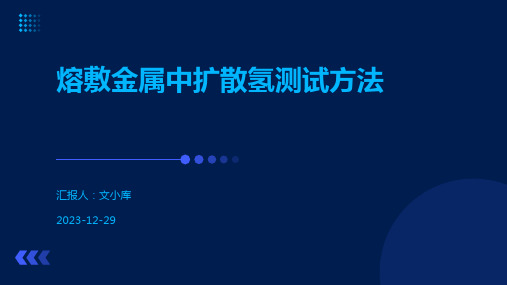
在焊接过程中,应合理选择焊接工艺参数,如焊接电流、电压和焊接速度等。这些参数的选择将直接影响氢在熔 敷金属中的溶解和扩散行为。通过调整这些参数,可以有效地控制扩散氢的含量,从而降低熔敷金属中的扩散氢 含量。
对熔敷金属进行后处理
要点一
总结词
对熔敷金属进行后处理是控制其扩散氢含量的有效方法之 一。通过适当的后处理,如热处理、真空除氢等,可以降 低熔敷金属中的扩散氢含量,提高其质量。
通过优化焊接工艺和后处理措施,提高焊接接头的抗氢脆性能和整体性能稳定性。
THANKS
谢谢您的观看
03
熔敷金属中扩散氢的影响因素
温度的影响
01
温度越高,氢在熔敷金属中的溶 解度越大,扩散速度越快。
02
温度变化会影响氢的扩散行为, 进而影响扩散氢的测试结果。
熔敷金属成分的影响
不同成分的熔敷金属对氢的吸附能力 和扩散速度不同。
合金元素的存在可能会影响氢的扩散 行为,进而影响测试结果。
焊接工艺参数的影响
焊接电流、电压、焊接速度等工艺参数会影响熔敷金属中氢 的含量和分布。
焊接工艺参数的选择和优化对于控制熔敷金属中扩散氢的含 量至关重要。
04
熔敷金属中扩散氢的控制措施
选用低氢焊接材料
总结词
选用低氢焊接材料是控制熔敷金属中扩散氢含量的有效措施之一。低氢焊接材料中的含 氢量较低,可以减少焊接过程中氢的溶解和扩散,从而降低熔敷金属中的扩散氢含量。
熔敷金属中扩散氢测试方法
汇报人:文小库 2023-12-29
目录
• 熔敷金属中扩散氢的来源 • 熔敷金属中扩散氢的测试方法 • 熔敷金属中扩散氢的影响因素 • 熔敷金属中扩散氢的控制措施 • 熔敷金属中扩散氢的未来研究
钢中氢、氮、氧的来源及其控制对策

钢中氢、氮、氧的来源及其控制对策高海潮摘要:比较了国内外钢中氢、氮、氧的水平,叙述了国外对纯净钢要求不断提高的过程,分析了钢中氢、氮、氧的来源,讨论了氢和氧的变化规律、吹氧过程中氮的变化以及碳和氧的关系,提出了减少钢污染的有效方法,总结出净化钢液的主要技术措施。
关键词:纯净钢来源钢污染控制措施Sources and Control Measures of Hydrogen,Nitrogen andOxygen in SteelGao Haichao(Ma Anshan Iron & Steel Co.Ltd.)Abstract:The contents of hydrogen, nitrogen and oxygen in steel produced in our country and other countries are compared in this paper. The requirements for clean steel are increased. The analysis on sources of H,N,O in steel have been carried out. The rule of changes in H and O contents, N change in oxygen-blowing process and the relationship between C and O have been discussed herein. The effective measures of decreasing steel pollution are put forward, and the main technology for mloten steel cleaning is then concluded.Keyworks:clean steel source steel pollution control measure1 前言1996年,我国的钢产量突破1亿 t,成为世界第一产钢大国。
钢中氢气体知识问答(3)
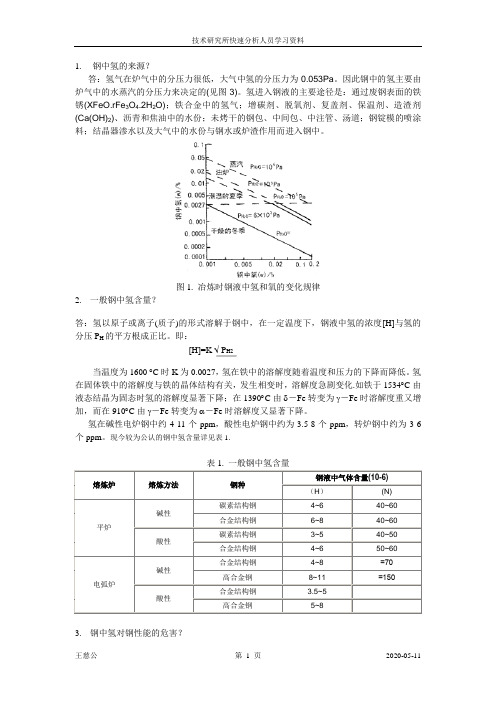
1.钢中氢的来源?答:氢气在炉气中的分压力很低,大气中氢的分压力为0.053Pa。
因此钢中的氢主要由炉气中的水蒸汽的分压力来决定的(见图3)。
氢进入钢液的主要途径是:通过废钢表面的铁锈(XFeO.rFe3O4.2H2O);铁合金中的氢气;增碳剂、脱氧剂、复盖剂、保温剂、造渣剂(Ca(OH)2)、沥青和焦油中的水份;未烤干的钢包、中间包、中注管、汤道;钢锭模的喷涂料;结晶器渗水以及大气中的水份与钢水或炉渣作用而进入钢中。
图1. 冶炼时钢液中氢和氧的变化规律2.一般钢中氢含量?答:氢以原子或离子(质子)的形式溶解于钢中,在一定温度下,钢液中氢的浓度[H]与氢的分压P H的平方根成正比。
即:[H]=K √ P H2当温度为1600 ︒C时K为0.0027,氢在铁中的溶解度随着温度和压力的下降而降低。
氢在固体铁中的溶解度与铁的晶体结构有关,发生相变时,溶解度急剧变化.如铁于1534︒C由液态结晶为固态时氢的溶解度显著下降;在1390︒C由δ-Fe转变为γ-Fe时溶解度重又增加,而在910︒C由γ-Fe转变为α-Fe时溶解度又显著下降。
氢在碱性电炉钢中约4-11个ppm,酸性电炉钢中约为3.5-8个ppm,转炉钢中约为3-6个ppm。
现今较为公认的钢中氢含量详见表1.表1. 一般钢中氢含量3.钢中氢对钢性能的危害?答:氢溶入钢中会降低钢的塑性和韧性。
研究表明,氢含量高不仅会导致钢的伸长率和面缩率急剧降低,还易产生氢致裂纹缺陷。
钢在冷却放置过程中,氢呈过饱和固溶体状态,由于其具有极强的扩散能力,很可能聚集在某些部位,使钢产品的局部压力增高,产生白点,形成内裂,进一步诱发高碳钢的疲劳损伤,严重影响其使用性能。
另一方面,冷却放置时,氢也能扩散到大气中,从而降低钢中的氢含量,减弱其危害。
4. 如何降低钢中氢?答:溶解在钢中的氢和氮以原子状态存在,其溶解反应为:{}[]H H =2%21在一定温度下达到平衡时: []212%H H P H K =[]2%H H P K H ⋅=上式说明氢在钢中的溶解度与作用在钢液面上的氢的分压的平方根成正比,即称西华特定律。
钢中氢的来源及低成本控制对策
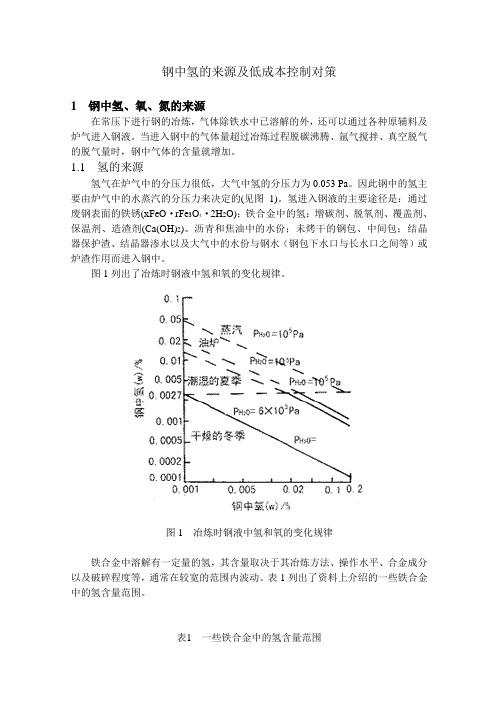
钢中氢的来源及低成本控制对策1钢中氢、氧、氮的来源在常压下进行钢的冶炼,气体除铁水中已溶解的外,还可以通过各种原辅料及炉气进入钢液。
当进入钢中的气体量超过冶炼过程脱碳沸腾、氩气搅拌、真空脱气的脱气量时,钢中气体的含量就增加。
1.1氢的来源氢气在炉气中的分压力很低,大气中氢的分压力为0.053 Pa。
因此钢中的氢主要由炉气中的水蒸汽的分压力来决定的(见图1)。
氢进入钢液的主要途径是:通过废钢表面的铁锈(xFeO·rFe3O4·2H2O);铁合金中的氢;增碳剂、脱氧剂、覆盖剂、保温剂、造渣剂(Ca(OH)2)、沥青和焦油中的水份;未烤干的钢包、中间包;结晶器保护渣、结晶器渗水以及大气中的水份与钢水(钢包下水口与长水口之间等)或炉渣作用而进入钢中。
图1列出了冶炼时钢液中氢和氧的变化规律。
图1冶炼时钢液中氢和氧的变化规律铁合金中溶解有一定量的氢,其含量取决于其冶炼方法、操作水平、合金成分以及破碎程度等,通常在较宽的范围内波动。
表1列出了资料上介绍的一些铁合金中的氢含量范围。
表1一些铁合金中的氢含量范围1.2氧的来源氧在各种炼钢炉冶炼终点时都以一定量存在于钢水中,氧是我们供给的这是不言而喻的。
因为炼钢过程首先是氧化过程,脱[P]、脱[S]、脱[Si]、脱[C]都需要向铁水供氧。
但随着炼钢过程的进行,尽管工艺操作千变万化,可是炼钢炉内熔池中钢液的[C]、[O]的关系却有着共同的规律性。
即随着[C]的逐步降低,[O]却在逐步增高,[C]和[O]有着相互对应的平衡关系。
1.3氮的来源氮气在炉气中的分压力很高,大气中氮的分压力大体保持在7.8×104 Pa。
因此钢中的氮主要是钢水裸露过程中吸入并溶解的。
电炉炼钢,包括二次精炼的电弧加热,加速了气体的解离,故[N]含量偏高;铁合金、废钢铁和渣料中的氮也会随炉料带入钢水。
2炼钢生产防止氢污染的主要技术措施(节源:基础工作)从管理上降低钢中原始氢含量,既是最经济的、符合降成本需要的,也是企业实现环境友好、资源节约的需要。
高强度钢零件环境氢脆的成因和预防措施
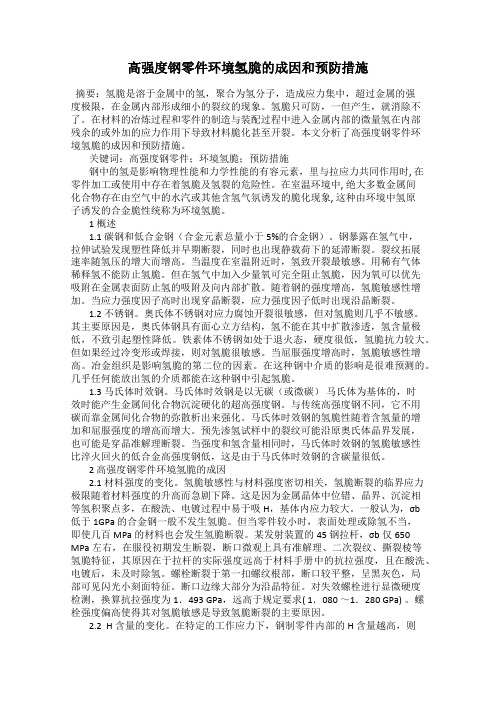
高强度钢零件环境氢脆的成因和预防措施摘要:氢脆是溶于金属中的氢,聚合为氢分子,造成应力集中,超过金属的强度极限,在金属内部形成细小的裂纹的现象。
氢脆只可防,一但产生,就消除不了。
在材料的冶炼过程和零件的制造与装配过程中进入金属内部的微量氢在内部残余的或外加的应力作用下导致材料脆化甚至开裂。
本文分析了高强度钢零件环境氢脆的成因和预防措施。
关键词:高强度钢零件;环境氢脆;预防措施钢中的氢是影响物理性能和力学性能的有容元素,里与拉应力共同作用时, 在零件加工或使用中存在着氢脆及氢裂的危险性。
在室温环境中, 绝大多数金属间化合物存在由空气中的水汽或其他含氢气氛诱发的脆化现象, 这种由环境中氢原子诱发的合金脆性统称为环境氢脆。
1 概述1.1 碳钢和低合金钢(合金元素总量小于5%的合金钢)。
钢暴露在氢气中,拉伸试验发现塑性降低并早期断裂,同时也出现静载荷下的延滞断裂。
裂纹拓展速率随氢压的增大而增高。
当温度在室温附近时,氢致开裂最敏感。
用稀有气体稀释氢不能防止氢脆。
但在氢气中加入少量氧可完全阻止氢脆,因为氧可以优先吸附在金属表面防止氢的吸附及向内部扩散。
随着钢的强度增高,氢脆敏感性增加。
当应力强度因子高时出现穿晶断裂,应力强度因子低时出现沿晶断裂。
1.2 不锈钢。
奥氏体不锈钢对应力腐蚀开裂很敏感,但对氢脆则几乎不敏感。
其主要原因是,奥氏体钢具有面心立方结构,氢不能在其中扩散渗透,氢含量极低,不致引起塑性降低。
铁素体不锈钢如处于退火态,硬度很低,氢脆抗力较大。
但如果经过冷变形或焊接,则对氢脆很敏感。
当屈服强度增高时,氢脆敏感性增高。
冶金组织是影响氢脆的第二位的因素。
在这种钢中介质的影响是很难预测的。
几乎任何能放出氢的介质都能在这种钢中引起氢脆。
1.3 马氏体时效钢。
马氏体时效钢是以无碳(或微碳)马氏体为基体的,时效时能产生金属间化合物沉淀硬化的超高强度钢。
与传统高强度钢不同,它不用碳而靠金属间化合物的弥散析出来强化。
钢结构工程常见质量问题及防治措施PPT
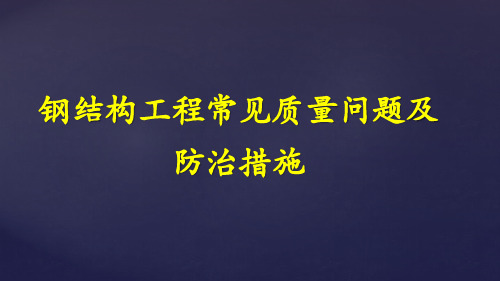
(4)预应力构件就位安装时,孔道灌浆强度不得低于15MPa。
屋架扶直时下弦垫点
1—屋架端头;2—道木墩
三、钢结构焊缝出现裂纹
1.现象 钢结构焊缝焊后出现结晶裂纹、液化裂纹、再热裂纹、氢致延迟裂纹等。焊接裂纹是焊接 接头最危险的缺陷,是导致结构断裂的主要原因。 2.原因分析 (1)钢结构在焊接后,不仅会产生变形,当焊件超厚大于30mm,刚度较大,而且焊缝内部 存在残余应力,以及不合理的装配顺序,焊接工艺不当,焊条含氢超标等,都会使焊缝焊后出 现裂纹。 (2)结晶裂纹是焊缝金属在凝固过程中由冶金因素与力学因素共同作用所致的裂纹,凝固 温度区间越宽越易生成裂纹,其中以碳、硫危害最大。 (3)热影响区液化裂纹是施焊时晶间层物质重新熔化,而局部形成液相,当快速冷却时在 熔合线附近出现的裂纹。
拉索预应力实腹梁截面形式
杆件截面的各种形式
3.压制封头常见的缺陷。 (1)起皱
1)原因分析 加热不均匀,压边力太小或不均匀,上下模间隙太大,曲率不均。
2)防治措施 加热要均匀,压边力大小和模具间隙要合理。 (2)起包
1)原因分析 加热不均匀材质差,上下模间隙太大,压边力太小,压边圈未起作用。
2)防治措施 保证坯料材质合格,加热均匀,模具间隙合理。
(7)孔的变形。 1)原因分析
孔边距弯曲线太近,内侧受压缩变形,外侧受拉伸变形,导致孔的变化。 2)防治措施
保证从孔边到弯曲半径R中心的距离大于一定值。
(8)端部鼓起 1)原因分析
弯曲时,纵向被压缩而缩短,宽度方向伸长,使宽度方向边缘出现突起,这以厚板小角度 弯曲尤为明显。
2)防治措施 在弯曲部位两端预先做成圆弧切口,将毛坯毛刺一边放在弯曲内侧。
(7)钢结构上放线要用钢划针,线宽一般为0.2mm。 (8)把轴线放到已安好的柱顶上,轴线应在柱顶上 三面标出,如下图所示。假定X方向钢柱一侧位移值为a ,另一侧轴线位移值为b,实际上钢柱柱顶偏离轴的位 移值为(a+b)/2,柱顶扭转值为(a-b)/2。沿Y方向 的位移值为c值,应做修正值,通过计算才能如实反映 实际情况。
2. 炼钢过程中氢和氮的控制

3
Hydris – Direct measurement of hydrogen Hydris – 直接测量氢
Schematic of the measuring system showing the gas flow through the pneumatic unit and the immersion probe. 测量系统展示气体流经气动单元 和浸没探头简图
脱氢处理才实现。
1
Hydrogen sampling methods 氢的取样
• Silica tube 石英管
• Hydris
2
Loss of hydrogen in pin sample 针样品中氢的损失
Hydrogen diffuses out of the sample unless it is kept in very low temperature. 氢会从样品中扩散出去,除非 它能保持在非常低的温度下。
Low hydrogen steels e.g. Line pipe grades for severe weather applications require a hydrogen level of less than 3ppm, which can only be achieved via a tank or RH degasser. 低氢钢 ,例如某些气候下应用的管线钢要求氢含量低于3ppm, 只能通过真空罐或RH
23
Nitrogen control in steelmaking 炼钢过程中氮的控制
• • • • • • • Hot metal nitrogen content 铁水中氮含量 Hot metal ratio 铁水比 Partial pressure of N2 in blowing oxygen 氧气中的氮含量 BOF lining life 转炉炉衬寿命 BOF blowing practice 转炉吹炼工艺 Ore consumption 铁矿石消耗 Scrap melting 废钢熔化情况
氢脆现象的原因和处理措施

氢脆钢材中的氢会使材料的力性能脆化,这种现象称为氢脆。
氢脆主要发生在碳钢和低合金钢。
钢中氢的来源主要为下列四个方面:(1)冶炼过程中溶解在钢水中的氢,在结晶冷凝时没有能及时逸出而存留在钢材中;(2)焊接过程中由于水分或油污在电弧高温下分解出的氢溶解入钢材中;(3)设备运行过程中,工作介质中的氢进入钢材中;(4)钢试件酸洗不当也可能导致氢脆。
含氢的钢材,当应力大于某一临界值时,就会发生氢脆断裂。
氢对钢材的脆化过程是一个微观裂纹在高应力作用下的扩展过程。
脆断应力可低达屈服极限的20%。
钢材的强度愈高(所承受的应力愈大),对氢脆愈敏感。
容器中的应力水平,包括工作应力及残余应力是导致氢脆很重要的因素。
氢脆是一种延迟断裂,断裂迟延的时间可以仅几分钟,也可能几天。
氢脆断裂只发生在100~150C的温度范围内,很低的温度不利于氢的移动和聚集,不易发生氢脆,而较高的温度可以使氢从钢中逸出,减少钢中的氢浓度,从而避免脆化。
焊后保温及热处理就是利用高温下氢能从钢中扩散逸出的原理,用来降低焊缝中氢含量,它是改善焊接接头力学性能的有效措施。
氢对钢铁材料的危害性较大,由于氢而导致材质劣化的现象统称为氢损伤。
氢损伤的形式有很多种,除了氢脆以外,还有因氢在钢板分层处聚集引起的氢鼓泡;氢在钢材中心部位聚集造成的细微裂纹群,称为白点;以及钢在高温高压氢(对碳钢,温度大于250℃.氢分压大于2MPa)作用下的氢腐蚀。
发生氢腐蚀时,钢的组织发生脱碳,渗碳体分解,沿晶界出现大量微裂纹,钢的强度、韧性丧失殆尽。
无损检测不能检测和判定清脆。
其余种类的氢损伤检测:氢鼓泡一般用肉眼便可观察到;白点可应用超声波检测方法测出来;氢致表面裂纹可应用磁粉或渗透方法检测出来;氢腐蚀可通过硬度试验和金相方法检测和判定。
实验室制取氢气PPT课件

可编辑课件
2
氢能是一种新能源,它放热效率高;它清 洁无污染,原料资源丰富。空气中氢气的 量及其低,这就需要我们去制取。
之前我们学过了氧气的实验室制法,回 顾一下:氧气的实验室制法是从哪几个方 面进行研究的?
品 4、检验纯度 5、收集氢气
检验纯度的方法:收集一试管的氢气,将 试管口靠近点燃的酒精灯火焰。
<小结> 请同学回顾一下本节课的内容, 我们是从哪几个方面探究了实验室制取氢气的 方法? 从中思考我们又懂得了什么?
对比实验室制取氧气和二氧化碳的实验装 置,各有什么相同点和不同点?
可编辑课件
10
实验室制取氢气
可编辑课件
1
• 教学目标:
• 1、懂得实验室制备氢气的原理,并初步学会实验 室制取氢气的方法,能尝试改进实验的发生装置;
• 2、通过观察不同金属与酸的反应,能选择实验室 制取氢气的药品;
• 3、通过已有知识的迁移,能选择正确的发生装置 和气体收集方法;
• 4、通过阅读“制取氢气的几种方法”,能选择实 验室制取氢气的方法;
锌与稀硫酸反应生成氢气,如果蒸发反应 剩下的液体后,会得到白色的硫酸锌晶体。
书写的方程式
可编辑课件
5
<提问>反应原理解决后, 我们来学习:发生装置。根据什么来选择正确 的发生装置?
根据反应物的状态和反应的条件。因为反
应物为固态和液态,并且不用加热,选择第二
套装置。
可编辑课件
6
❖ 那么如何设计装置,让反应随时开始随时 停下,使反应可控?即:做到使锌粒与稀 硫酸能接触,又能巧妙的分开?
- 1、下载文档前请自行甄别文档内容的完整性,平台不提供额外的编辑、内容补充、找答案等附加服务。
- 2、"仅部分预览"的文档,不可在线预览部分如存在完整性等问题,可反馈申请退款(可完整预览的文档不适用该条件!)。
- 3、如文档侵犯您的权益,请联系客服反馈,我们会尽快为您处理(人工客服工作时间:9:00-18:30)。
9
钢中氢的来源及控制对策
4.2.2 大吹氩时间与增氢量的关系 随大吹氩时间增加,炉气中的水分分解后进入钢液的氢量增加,结果如 图3,该阶段增[H]量占LF总增[H]量的16.66%。 4.2.3 LF加热时间对增氢的影响 在其它工艺一致的条件下,随加热时间的延长,钢液[H]增加。该阶段 增[H]的主要因素是炉气中的水被电弧电离后溶入钢水。 4.2.4 钙处理工艺与增氢量的关系 (1) 喂SiCa线速度与增氢量的关系 SiCa喂入量相同的前提下,增氢量随喂线速度增加有由大变小,再变大 的趋势,结果如图4所示。当喂线速度为180m/min左右时,增氢量最小。
表1 钢液测氢试验方案
名称
检测内容
转炉速补料
水分含量、用量、补炉后烘烤时间
转炉用辅料及合金
水分含量及用量、加入时机
出钢结束
钢液测氢
LF用辅料及合金
水分含量及用量
LF精炼过程
钢液测氢
连铸中间罐、结晶器覆盖剂
水分含量及用量
ቤተ መጻሕፍቲ ባይዱ
中间罐
钢液测氢
N2、O2、Ar气体
水分含量
钢中氢的来源及控制对策
3.试验结果
3.1 原辅料水分 炼钢过程辅料及合金水分含量分析结果见表2,从分析结果可以看出:转炉速补料、化 渣剂等部分材料水分较高,部分试样水分接近20%,部分石灰制品水分含量〉1.2%。
钢中氢的来源及控制对策
3.2 各工位钢液[H]测试 转炉炼钢+LF炉+连铸各工位各工位钢液[H]测试结果见表3,从表3可以看出: 转炉冶炼、LF精炼、浇注过程均存在钢液增[H]现象,转炉冶炼过程增[H]量 占 中 间 罐 总 量 的 66.4% 、 LF 占 25.95% 、 浇 注 过 程 占 7.57% 。 中 间 罐 [H]〉 5.0ppm的炉次占44.8%,个别炉次含量高达9.8ppm。
数值
钢水升温结束后氢增量(PPm)
4.5
4
3.5
3
2.5
合金及其 它辅料综
2
合水分含
量/%水分
1.5
含量
1
[H]含量/%
0.5
0
时间
1月份 2月份 3月份 4月份 5月份 6月份
图1 出钢过程合金及其它辅料水分含量对[H]的影响
1.2 1.0 0.8 0.6 0.4 0.2 0.0
0.00 2.00 4.00 6.00 8.00 10.00 12.00 14.00 渣料水分总量(kg)
3
钢中氢的来源及控制对策
2.试验条件
2.1 试验工艺及主要设备参数 80tLD-CB(冶炼周期31min)→80tLF(冶炼周期35—55min)→240×1400mm断面弧形 板坯铸机(中包容量15t,浇注周期35min)。 2.2 试验方案 为了检测钢液中真实的氢含量,采用浸入式直读测氢仪(Multi—LabHydris System) 对“转炉炼钢+LF炉+连铸”各工位钢液在线测氢及对原辅料进行详细的水分分析,详 细的测试方案见表1。
表5 合金对钢水[H]含量的影响
项目
试验炉次
加入量/Kg
使用金属锰的炉次
30
1100
使用低磷锰铁的炉次
30
1100
出钢后[H]含量/ppm 3.5 2.5
8
钢中氢的来源及控制对策
4.1.4 出钢过程合金及辅料水分含量对[H]的影响 合金及其它辅料水分含量对[H]的影响如图1所示,随着合金及其它辅料水分含 量的增加,钢液中[H]含量增加。 4.2 LF精炼过程对[H]的影响 4.2.1 各种渣料水分与增氢量的关系 LF精炼过程,随渣料中水分总量增加,化渣升温阶段氢含量量增加,结果如图 2,该阶段增[H]量占LF总增[H]量的47.12%。
关键词 转炉炼钢 氢 来源 变化规律
钢中氢的来源及控制对策
1.前前言言
氢在钢中的危害主要表现为引起“氢脆”, “白点”以及点状偏析、静载疲劳断裂等严重缺陷, “氢脆”将使钢的塑性下降,脆性增大,并且在低 于其极限强度的应力作用下造成钢结构或钢件的突 然脆性断裂[1]。在冶金生产中氢会导致铸坯形成气 泡、裂纹和针孔[2]。为了掌握炼钢过程中钢水氢含 量变化规律,重钢引进Hydris定氢仪,对“转炉炼 钢+LF炉+连铸”过程中[H]的来源进行研究,掌握了 炼钢过程钢液氢含量变化规律及控制增氢的措施。
4.分析与讨论
4.1 转炉冶炼过程中对[H]的影响 4.1.1 后吹过程原辅料水分对氢的影响 转炉后吹过程中即:脱碳速度减弱,氧含量增加,炉温升高,炉内动力学 热力学条件均有助于钢液增[H]的发生。当向炉内加入水分含量较高的原 辅料将导致氢的平衡分压增加,[H]向钢中扩散速率增加,钢水[H]含量增 加[2],结果如表4。从表4可以看出:后吹过程中未加辅料炉次出钢后[H] 平均含量为2.5ppm,比后吹过程中加辅料的炉次低1.07ppm。
表4 转炉吹炼过程辅料加入时机与钢水[H]含量的关系
项目 后吹过程加辅料
辅料水分含量 /%
3.0~5.5
试验炉次 30
辅料加入量/Kg 290
出钢后[H]含量/ppm 3.57
后吹过程未加辅料
/
28
0
2.5
7
钢中氢的来源及控制对策
4.1.2 耐材的影响 转炉补炉后耐材干燥程度对钢液[H]含量有直接影响,2008年因转炉补炉后耐 材未彻底干燥导致6炉钢[H]〉8.0ppm引发铸坯皮下气孔判废。 4.1.3 合金的影响 试验过程中发现,使用电解法生产的合金对钢液氢含量影响较大,在相同的生 产工艺条件下使用金属锰的炉次比未使用的炉次高1ppm,结果如表5。
钢中氢的来源及控制对策
Power Design
2011.3 昆明
钢中氢的来源及控制对策
摘要
通过采用浸入式直读测氢仪对“转炉炼钢+LF炉+连 铸”过程中[H]的来源进行研究,试验结果表明:转 炉冶炼、LF精炼、浇注过程均存在钢水增[H]现象。 增氢原因有:原辅材料及合金水分、系统耐材水分、 耐材化学成分分解的碳氢化合物、钢液二次氧化导 致钢水增[H]。分析影响钢液增氢的主要因素及环节, 并提出了改进措施。
表3 炼钢过程不同工序[H]含量
工序名称
出钢结束
LF升温后
LF合金化 后
钙处理前
精炼结束
中间罐
[H]含量 7.8 ~ 2.1 8.4 ~ 2.6 8.6 ~ 2.8 9..1 ~ 3.2 9.1 ~ 3.4 9.8 ~ 4.0
/ppm
3.606
4.155
4.376
4.74
4.94
5.328
6
钢中氢的来源及控制对策
表2 炼钢过程辅料及合金水分含量
名称
试验炉数/炉
水分含量/%
转炉速补料
5~19
镁球及化渣剂
3.2~19.2
转炉用其它辅料综合水分含量
1.04~1.47
转炉及LF各类合金
221
LF用辅料综合水分含量
<0.05 1.1~1.6
中包渣
<0.40
结晶器保护渣
<0.35
N2、O2、Ar气体
3
≤4ppm 5
897..64811~~~32243..4.18602 34544..6.31.9072546485