高炉喷煤工艺
高炉喷煤工艺流程
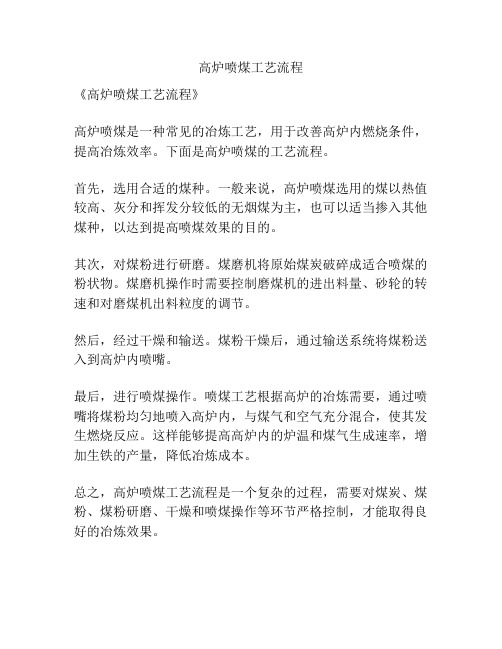
高炉喷煤工艺流程
《高炉喷煤工艺流程》
高炉喷煤是一种常见的冶炼工艺,用于改善高炉内燃烧条件,提高冶炼效率。
下面是高炉喷煤的工艺流程。
首先,选用合适的煤种。
一般来说,高炉喷煤选用的煤以热值较高、灰分和挥发分较低的无烟煤为主,也可以适当掺入其他煤种,以达到提高喷煤效果的目的。
其次,对煤粉进行研磨。
煤磨机将原始煤炭破碎成适合喷煤的粉状物。
煤磨机操作时需要控制磨煤机的进出料量、砂轮的转速和对磨煤机出料粒度的调节。
然后,经过干燥和输送。
煤粉干燥后,通过输送系统将煤粉送入到高炉内喷嘴。
最后,进行喷煤操作。
喷煤工艺根据高炉的冶炼需要,通过喷嘴将煤粉均匀地喷入高炉内,与煤气和空气充分混合,使其发生燃烧反应。
这样能够提高高炉内的炉温和煤气生成速率,增加生铁的产量,降低冶炼成本。
总之,高炉喷煤工艺流程是一个复杂的过程,需要对煤炭、煤粉、煤粉研磨、干燥和喷煤操作等环节严格控制,才能取得良好的冶炼效果。
高炉工艺高炉喷煤
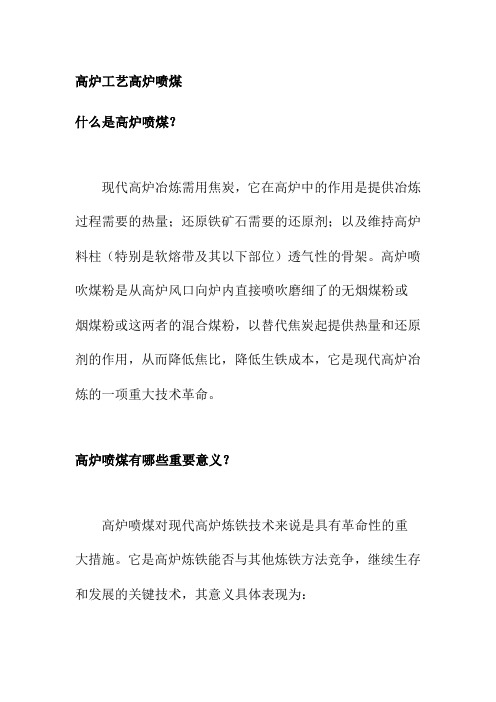
高炉工艺高炉喷煤什么是高炉喷煤?现代高炉冶炼需用焦炭,它在高炉中的作用是提供冶炼过程需要的热量;还原铁矿石需要的还原剂;以及维持高炉料柱(特别是软熔带及其以下部位)透气性的骨架。
高炉喷吹煤粉是从高炉风口向炉内直接喷吹磨细了的无烟煤粉或烟煤粉或这两者的混合煤粉,以替代焦炭起提供热量和还原剂的作用,从而降低焦比,降低生铁成本,它是现代高炉冶炼的一项重大技术革命。
高炉喷煤有哪些重要意义?高炉喷煤对现代高炉炼铁技术来说是具有革命性的重大措施。
它是高炉炼铁能否与其他炼铁方法竞争,继续生存和发展的关键技术,其意义具体表现为:(1)以价格低廉的煤粉部分替代价格昂贵而日趋匮乏的冶金焦炭,使高炉炼铁焦比降低,生铁成本下降;(2)喷煤是调剂炉况热制度的有效手段;(3)喷煤可改善高炉炉缸工作状态,使高炉稳定顺行;(4)喷吹的煤粉在风口前气化燃烧会降低理论燃烧温度,为维持高炉冶炼所必需的T理,需要补偿,这就为高炉使用高风温和富氧鼓风创造了条件;(5)喷吹煤粉气化过程中放出比焦炭多的氢气,提高了煤气的还原能力和穿透扩散能力,有利于矿石还原和高炉操作指标的改善;(6)喷吹煤粉替代部分冶金焦炭,既缓和了焦煤的需求,也减少了炼焦设施,可节约基建投资,尤其是部分运转时间已达30年需要大修的焦炉,由于以煤粉替代焦炭而减少焦炭需求量,需大修的焦炉可停产而废弃;(7)喷煤粉代替焦炭,减少焦炉座数和生产的焦炭量,从而可降低炼焦生产对环境的污染。
高炉喷煤工艺系统由哪些方面组成?高炉喷煤工艺系统主要由原煤贮运、煤粉制备、煤粉输送、煤粉喷吹、干燥气体制备和供气动力系统组成。
高炉喷吹煤粉工艺有几种模式?从煤粉制备和喷吹设施的配置上来分,高炉喷煤工艺有两种模式,即间接喷吹模式和直接喷吹模式。
制粉系统和喷吹系统结合在一起直接向高炉喷吹的工艺叫直接喷吹工艺;制粉系统和喷吹系统分开,通过罐车或气动输送管道将煤粉从制粉车间送到靠近高炉的喷吹站,再向高炉喷吹煤粉的工艺叫间接喷吹工艺。
高炉喷吹煤粉的工艺
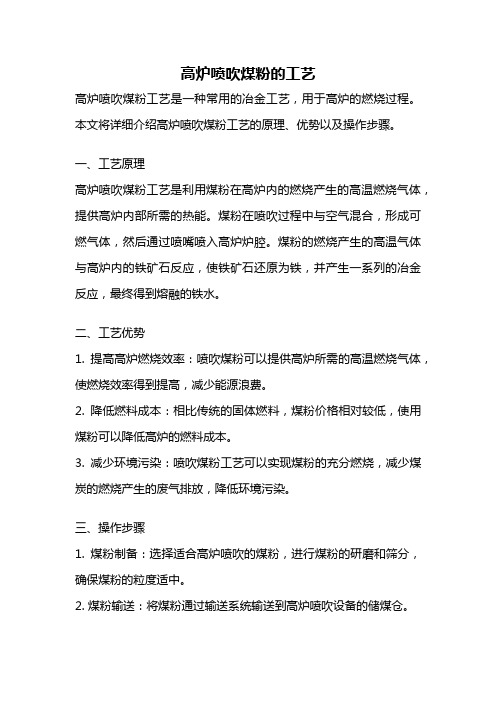
高炉喷吹煤粉的工艺高炉喷吹煤粉工艺是一种常用的冶金工艺,用于高炉的燃烧过程。
本文将详细介绍高炉喷吹煤粉工艺的原理、优势以及操作步骤。
一、工艺原理高炉喷吹煤粉工艺是利用煤粉在高炉内的燃烧产生的高温燃烧气体,提供高炉内部所需的热能。
煤粉在喷吹过程中与空气混合,形成可燃气体,然后通过喷嘴喷入高炉炉腔。
煤粉的燃烧产生的高温气体与高炉内的铁矿石反应,使铁矿石还原为铁,并产生一系列的冶金反应,最终得到熔融的铁水。
二、工艺优势1. 提高高炉燃烧效率:喷吹煤粉可以提供高炉所需的高温燃烧气体,使燃烧效率得到提高,减少能源浪费。
2. 降低燃料成本:相比传统的固体燃料,煤粉价格相对较低,使用煤粉可以降低高炉的燃料成本。
3. 减少环境污染:喷吹煤粉工艺可以实现煤粉的充分燃烧,减少煤炭的燃烧产生的废气排放,降低环境污染。
三、操作步骤1. 煤粉制备:选择适合高炉喷吹的煤粉,进行煤粉的研磨和筛分,确保煤粉的粒度适中。
2. 煤粉输送:将煤粉通过输送系统输送到高炉喷吹设备的储煤仓。
3. 煤粉喷吹:将煤粉从储煤仓中提取,通过喷吹设备喷入高炉炉腔。
喷吹设备通常由喷嘴、煤粉输送管道和控制系统组成。
4. 燃烧控制:通过控制系统对喷吹煤粉的供给量、喷吹速度和喷吹位置进行调节,以实现高炉内的燃烧控制。
5. 燃烧效果监测:通过监测高炉内的温度、压力和煤粉燃烧产物的含量等参数,对燃烧效果进行实时监测和调整。
总结:高炉喷吹煤粉工艺是一种高效、低成本、环保的冶金工艺。
通过喷吹煤粉,可以提高高炉的燃烧效率,降低燃料成本,并减少环境污染。
在操作过程中,需要进行煤粉制备、输送、喷吹和燃烧控制等步骤,并通过监测燃烧效果进行调整。
高炉喷吹煤粉工艺的应用将进一步推动冶金行业的发展,实现资源的高效利用和环境的可持续发展。
高炉喷煤操作规程

1.4、停止喷吹的调节
1.4.1、因故停喷未慢风并停喷未超过0.5小时,应在复喷时补上少喷的煤量,如慢风可酌情少补煤量。
1.4.2、超过0.5小时的停喷,应在上部补足相应的焦炭,保持综合负荷基本稳定。
2.1.3、确认大倾角皮带振打器固定架牢固,无松动开焊现象。
2.1.4、据各原煤需要量要求行车工按比例抓煤入配煤斗。
2.1.5、确认称重给煤机电源送上,给煤量值设定好。
2.1.6、带混合煤,确认3#,4#配料斗为烟煤,1#,2#配料斗为无烟煤。
2.2、操作程序
2.2.1、送上电源开关,依次启动4#,3#皮带,2#皮带及除铁器,启动1#皮带机,启动振打器。
高炉喷煤作为下部调剂的重要手段,与过去传统的加湿鼓风相比,具有本质的区别,将引起相对矿焦比、料柱透气性、炉缸工作状态、热制度等一系列变化,并将使高炉冶炼技术复杂化。高炉工长应掌握喷煤冶炼操作,使我厂高炉喷煤逐步达到大喷煤量、高置换比、炉况长期稳定顺行的冶炼效果,促进高炉强化冶炼,提高高炉利用系数,全面改善高炉技术经济指标。
3.2、及时清除各处挂钩和蓖子上的杂物。
3.3、加强对2#倾角皮带的运行监控,发现皮带裙边拉裂、冷扣断裂、隔板脱落、托轮不正,要及时停机处理。
二、喷煤工艺:
原煤经汽车和火车两种运输方式进入原煤库,单一原煤经过配煤斗卸到胶带运输机,两种及两种以上原煤通过配煤斗按预定比例卸到胶带运输机上混合,送至制粉系统原煤仓。
制粉系统开始运行,中速磨磨煤,原煤被研磨成粉。
干燥气体从中速磨机进气口进入中速磨,煤粉颗粒被干燥气体烘干并被携带上升进入粗粉分离器,细度合格的煤粉从中速磨的出口通过煤粉管道进入布袋收粉器后卸入煤粉仓。
高炉煤粉喷吹系统工艺简介.
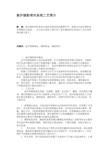
高炉煤粉喷吹系统工艺简介摘要:高炉煤粉喷吹是优化炼铁系统结构的重要环节,是国内外高炉炼铁技术发展的大趋势,。
本文结合实际工程介绍了高炉煤粉喷吹系统的工艺及其取得的重大意义。
关键词:高炉原煤储运;煤粉制备;煤粉喷吹一、高炉煤粉喷吹概述近年来随着钢铁行业的高速发展,矿石资源和焦炭资源日趋紧张,节能降耗已经成为钢铁行业刻不容缓的重大课题,而炼铁系统又占钢铁行业能耗的70%左右,是名副其实的耗能大户,而高炉煤粉喷吹系统在高炉生产过程中已成为节焦和改进冶炼工艺最有效的措施之一。
喷煤工艺种类繁多,按喷吹方式可分为直接喷吹和间接喷吹,按喷罐布置可分为并罐布置和串罐布置,按喷吹管路可分为多管路喷吹和单管路加分配器喷吹,按制粉系统烟气循环方式可分为引热风炉废气和烟气自循环方式。
完整的高炉喷煤工艺流程应包括原煤储运系统、制粉系统、煤粉输送系统、喷吹系统、供气系统和煤粉计量系统,最新设计的高炉喷煤系统还包括整个喷煤系统的计算机控制中心。
二、工艺介绍高炉喷煤就是把原煤(无烟煤、烟煤)经过烘干、磨细,用压缩空气输送,通过喷煤枪从高炉风口直接喷入炉缸的生产工艺。
高炉喷煤系统的工艺流程主要由原煤贮运、煤粉制备、煤粉喷吹、热烟气和供气等几个部分组成。
如下图所示。
1. 原煤储运系统:为保证高炉喷煤作业的连续性和有效性,在喷煤工艺系统中,首先要考虑的是建立合适的原煤储运系统,该系统应包括综合煤场、煤棚、储运方式。
为控制原煤粒度和除去原煤中的杂物,在原煤储运过程中还必须设置筛分破碎装置和除铁器。
筛分破碎即可以控制磨煤机入口的原煤粒度,除铁器则主要用于清除煤中的磁性金属杂物2. 煤粉制备系统: 煤粉制备是指通过磨煤机将原煤加工成粒度和含水量均符合高炉喷吹需要的煤粉。
制粉系统主要由给料、干燥与研磨、收粉与除尘几部分组成。
3. 喷吹系统:喷吹系统由不同形式的喷吹罐组和相应的钟阀、流化装置等组成。
煤粉喷吹通常是在喷吹罐组内充以压缩空气,在自混合器引入二次压缩空气将煤粉经管道和喷枪喷入高炉风口。
高炉喷煤工艺流程
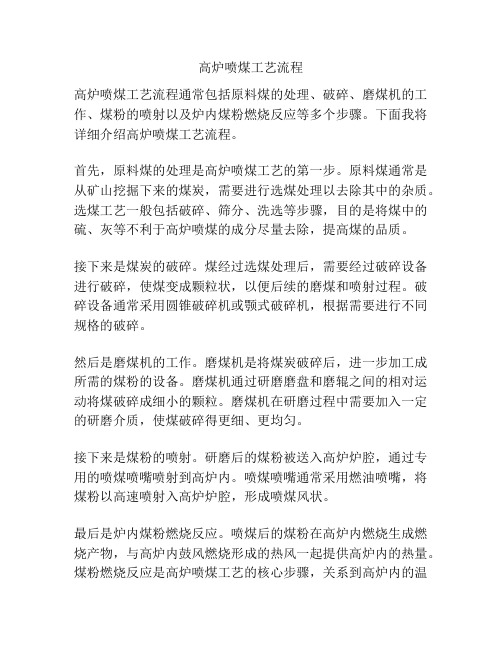
高炉喷煤工艺流程
高炉喷煤工艺流程通常包括原料煤的处理、破碎、磨煤机的工作、煤粉的喷射以及炉内煤粉燃烧反应等多个步骤。
下面我将详细介绍高炉喷煤工艺流程。
首先,原料煤的处理是高炉喷煤工艺的第一步。
原料煤通常是从矿山挖掘下来的煤炭,需要进行选煤处理以去除其中的杂质。
选煤工艺一般包括破碎、筛分、洗选等步骤,目的是将煤中的硫、灰等不利于高炉喷煤的成分尽量去除,提高煤的品质。
接下来是煤炭的破碎。
煤经过选煤处理后,需要经过破碎设备进行破碎,使煤变成颗粒状,以便后续的磨煤和喷射过程。
破碎设备通常采用圆锥破碎机或颚式破碎机,根据需要进行不同规格的破碎。
然后是磨煤机的工作。
磨煤机是将煤炭破碎后,进一步加工成所需的煤粉的设备。
磨煤机通过研磨磨盘和磨辊之间的相对运动将煤破碎成细小的颗粒。
磨煤机在研磨过程中需要加入一定的研磨介质,使煤破碎得更细、更均匀。
接下来是煤粉的喷射。
研磨后的煤粉被送入高炉炉腔,通过专用的喷煤喷嘴喷射到高炉内。
喷煤喷嘴通常采用燃油喷嘴,将煤粉以高速喷射入高炉炉腔,形成喷煤风状。
最后是炉内煤粉燃烧反应。
喷煤后的煤粉在高炉内燃烧生成燃烧产物,与高炉内鼓风燃烧形成的热风一起提供高炉内的热量。
煤粉燃烧反应是高炉喷煤工艺的核心步骤,关系到高炉内的温
度、热风成分等关键参数。
综上所述,高炉喷煤工艺流程包括原料煤的处理、破碎、磨煤机的工作、煤粉的喷射以及炉内煤粉燃烧反应等多个步骤。
这些步骤相互配合,使得煤炭能够有效地利用于高炉的炉腔燃烧反应中,提供所需的热量和燃料,实现高炉生产的稳定性和高效性。
喷煤工艺流程_(1)

三安钢铁炼铁厂喷煤工艺流程前言为适应新建成3#高炉配套的喷煤站的生产操作需要,在结合原喷煤系统技术操作规程的基础上,做了较大的修订,特制定本规程。
其主要内容包括采用高炉煤气新型烟气发生炉,中速磨煤机制粉系统,采用压缩空气作为输送煤粉介质的并列罐全制动控制喷吹系统,以及配套喷混合煤的安全防暴系统。
本规程适用于炼铁厂喷煤车间技术操作岗位。
本规程自2011年10月1日起实施。
本规程由福建三安钢铁股份有限公司提出。
本规程由福建三安钢铁技术中心归口。
本规程由福建三安钢铁炼铁厂负责起草。
本规程主要起草人:本规程2011年首次发布。
,实际生产操作中如有出入,可根据实际需要进行修改。
目录炼铁厂高炉喷煤技术操作规程(试行)第1章喷煤工操作规程 (1)第2章烟气升温操作规程 (2)第3章制粉工操作规程 (5)第4章喷吹工技术操作规程 (8)炼铁厂高炉喷煤技术操作规程(试行)第一章喷煤工操作规程一、主要设备技术参数1、桥式抓斗起重机型号U127跨度31.5m工作制度重级抓斗容积5m3提升高度15m起重量10t2、DPG60型电子皮带秤给煤机技术参数标定给煤量60t/h 最小、最大给煤量8~60t/h计量精度≤±0.5% 控制精度≤±1%对煤质要求适应堆积煤比重0.7~1.1t/m3 粒度≤60mm 水分≤10%3、电磁除铁器型号PDC-8煤粒度<50m 堆密度:0.9t/m3 废钢铁堆密度:7.8t/m3配B=800mm胶带机,V1.0m/s Q=200t/h4、大倾角皮带机型号DJ-800 B=800mm输送物料:原煤物料密度0.9t/m3 带速1.6m/s 输送量120t头尾轮水平距离56.33m 头尾轮中心高度34.5m 倾斜角度40℃5.水平皮带机型号TD75B800*13m B=800输送带规格棉帆布带CC-56 输送带断面型式槽型30度,输送速度1.0m/s 输送量200t/h二、操作规程1、开机前的检查与准备工作①检查各机电设备完整,电动机的接线头是否松动,接地线是否良好。
高炉喷煤工艺流程

高炉喷煤工艺流程高炉喷煤工艺是指在高炉炉缸内喷射煤粉,以取代部分焦炭作为还原剂,从而提高高炉的生产效率和降低生产成本。
本文将介绍高炉喷煤工艺的流程。
一、原料准备在高炉喷煤工艺中,煤粉是最主要的原料。
煤粉的选用应根据其挥发分、灰分、硫分等指标进行筛选。
煤粉的粒度应适中,一般在80-120目之间。
此外,还需要准备一些辅助气体,如空气、氧气等。
二、喷煤系统高炉喷煤系统主要由煤粉输送系统、煤粉燃烧系统和煤粉喷射系统三部分组成。
(一)煤粉输送系统煤粉输送系统是将煤粉从煤粉仓库中输送至高炉炉缸的系统。
煤粉输送系统包括煤粉仓、煤粉输送管道、煤粉输送机构等。
煤粉输送机构一般采用密闭式输送,以避免煤粉在输送过程中出现粉尘污染。
(二)煤粉燃烧系统煤粉燃烧系统是指将煤粉与空气或氧气混合后进行燃烧的系统。
煤粉燃烧系统包括煤粉燃烧器、煤粉燃烧室、煤粉燃烧风机等。
在煤粉燃烧室内,煤粉与空气或氧气混合后进行燃烧,产生高温高压的煤气。
(三)煤粉喷射系统煤粉喷射系统是将煤粉喷射至高炉炉缸内的系统。
煤粉喷射系统包括煤粉喷射枪、煤粉喷射器、煤粉喷射管等。
煤粉喷射器将煤粉与煤气混合后喷射至高炉炉缸内,起到还原剂的作用。
三、喷煤工艺流程高炉喷煤工艺的流程一般分为两个阶段:喷煤前期和喷煤后期。
(一)喷煤前期在喷煤前期,首先需要打开高炉炉门,清理炉缸内的焦炭和渣铁,使炉缸内空间达到最大。
然后关闭高炉炉门,将煤粉输送至煤粉燃烧器中,与空气或氧气混合后进行燃烧,产生高温高压的煤气。
最后,通过煤粉喷射系统将煤粉喷射至高炉炉缸内。
(二)喷煤后期在喷煤后期,需要根据高炉内的状况进行调整。
一般来说,如果高炉内的温度过高,可以适当减少煤粉的喷射量;如果高炉内的温度过低,可以增加煤粉的喷射量。
此外,还需要定期检查煤粉输送系统、煤粉燃烧系统和煤粉喷射系统的运行情况,及时处理故障。
四、总结高炉喷煤工艺流程是一个复杂的系统工程,需要多个部门的协作配合。
在实际应用中,需要根据高炉的具体情况进行调整,以达到最佳的生产效果和经济效益。
炼铁原理与工艺13(喷煤操作)
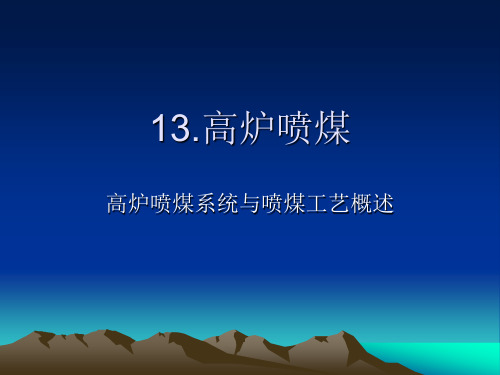
13.4高炉喷吹操作
② A. 煤粉温度的控制 首先要控制好各点的温度。磨煤机出口干燥剂温度和煤 粉温度不得超过规定值,且无升温趋势,否则要引入冷 废气、氮气或尽快将煤粉喷空。 煤粉升温严重时应采取“灭火”或排放煤粉的措施。另 外要防止静电火花。 在检修管道阀门、软连接时,动火前必须用惰性气体吹 扫。 喷吹罐下面的混合器应全部投入运行,在高炉不允许全 部运行的情况下应轮换使用,以防积粉自燃。
13.2高炉制煤系统
煤粉制备主要设备有:原煤仓, 给煤 机,磨煤机,袋式收粉器,主排风机,煤 粉振动筛,仓顶除尘器。 粗粉分离器 :粗粉分离器的任务是把经 过磨制的过粗煤粉分离出来,送回磨煤机 再磨,在磨煤机顶部。 细粉分离器:一、二级旋风除尘器。 锁气器是装在旋风分离器下部的卸粉装置。
制粉设备
13.4高炉喷吹操作
7. ① A. B.
C.
喷煤量的调节方法 对于喷射型混合器,通常调节煤量有3种方法: 喷枪数量,喷枪数量越多,喷煤量越大。 喷煤罐罐压。喷煤罐内压力越高,则喷煤量越 大。而且罐内煤量越少,在相同罐压下喷煤量 越大。 混合器内喷嘴位置及喷嘴大小。喷嘴位置可以 前后调节,其效果极为明显。喷嘴直径适当缩 小,可提高气(空气)煤混合比,增加喷吹量, 但过小则相反。但一般不动。
13.3高炉喷吹系统
① 螺旋泵 ② 混合器 : 混合器是将压缩空气与煤粉混合并使煤粉启 动的设备,由壳体和喷嘴组成. ③ 分配器 : 把煤粉均匀分配到各风口。目前使用效果较 好的分配器有瓶式、盘式和锥形分配器等几种。 ④ 喷煤枪
13.3高炉喷吹系统
⑤ 仓式泵 ⑥ 贮煤罐、喷吹罐、输送系统 ⑦ 喷吹烟煤的防火、防爆设施 : 氧浓度监测仪 ,氮气或蒸汽灭火装置,煤粉 温度监测 ,防爆孔 等
高炉喷煤工艺流程
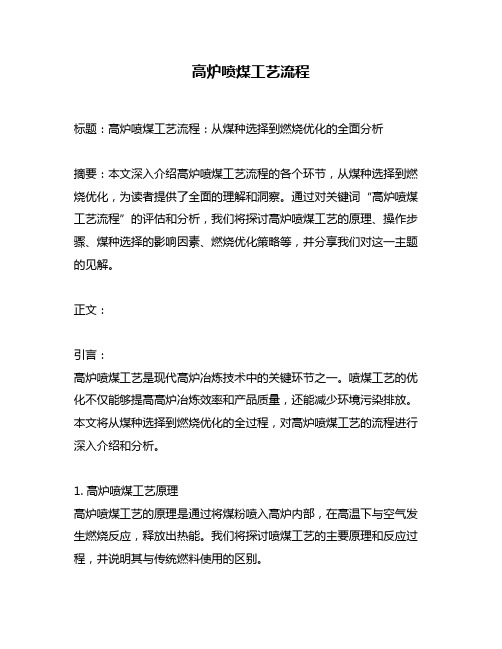
高炉喷煤工艺流程标题:高炉喷煤工艺流程:从煤种选择到燃烧优化的全面分析摘要:本文深入介绍高炉喷煤工艺流程的各个环节,从煤种选择到燃烧优化,为读者提供了全面的理解和洞察。
通过对关键词“高炉喷煤工艺流程”的评估和分析,我们将探讨高炉喷煤工艺的原理、操作步骤、煤种选择的影响因素、燃烧优化策略等,并分享我们对这一主题的见解。
正文:引言:高炉喷煤工艺是现代高炉冶炼技术中的关键环节之一。
喷煤工艺的优化不仅能够提高高炉冶炼效率和产品质量,还能减少环境污染排放。
本文将从煤种选择到燃烧优化的全过程,对高炉喷煤工艺的流程进行深入介绍和分析。
1. 高炉喷煤工艺原理高炉喷煤工艺的原理是通过将煤粉喷入高炉内部,在高温下与空气发生燃烧反应,释放出热能。
我们将探讨喷煤工艺的主要原理和反应过程,并说明其与传统燃料使用的区别。
2. 喷煤工艺的操作步骤在高炉喷煤工艺中,操作步骤的正确执行对工艺效果至关重要。
我们将介绍喷煤工艺的各个操作步骤,包括煤粉的研磨、输送系统的设计、喷煤装置的选型以及喷煤参数的控制等,并探讨每个步骤的优化方法。
3. 煤种选择对喷煤工艺的影响选择适合喷煤工艺的煤种是关键决策之一。
本节将介绍影响煤种选择的因素,如煤质特性、燃烧性能、价格等,并解释不同煤种对喷煤工艺的影响,为读者提供煤种选择的指导。
4. 喷煤工艺的燃烧优化喷煤工艺的燃烧优化对高炉冶炼效率和环境影响具有重要意义。
我们将介绍喷煤工艺的燃烧优化策略,包括调整喷煤参数、优化空气分布、控制煤气成分等,并解释这些策略对高炉运行的影响。
总结与回顾:通过对高炉喷煤工艺流程的全面介绍和分析,我们深入探讨了煤种选择、燃烧优化等关键环节。
我们认为高炉喷煤工艺的优化对高炉冶炼效率、产品质量和环境保护至关重要。
在煤种选择方面,需要综合考虑煤质特性、燃烧性能和价格等因素,并选择合适的煤种。
在燃烧优化方面,通过调整喷煤参数、优化空气分布和控制煤气成分等策略,可以提高高炉运行效率、降低排放物产生,实现可持续发展。
高炉喷煤工艺流程
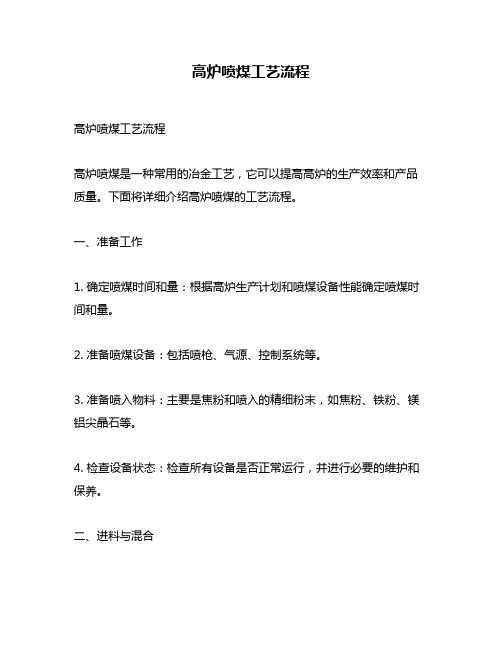
高炉喷煤工艺流程高炉喷煤工艺流程高炉喷煤是一种常用的冶金工艺,它可以提高高炉的生产效率和产品质量。
下面将详细介绍高炉喷煤的工艺流程。
一、准备工作1. 确定喷煤时间和量:根据高炉生产计划和喷煤设备性能确定喷煤时间和量。
2. 准备喷煤设备:包括喷枪、气源、控制系统等。
3. 准备喷入物料:主要是焦粉和喷入的精细粉末,如焦粉、铁粉、镁铝尖晶石等。
4. 检查设备状态:检查所有设备是否正常运行,并进行必要的维护和保养。
二、进料与混合1. 进料:将焦粉通过输送机输送到深井式加料器中,同时将精细粉末通过气力输送管道输送到加料器中。
2. 混合:在加料器内对焦粉和精细粉末进行深度混合,以保证二者均匀分布,并达到最佳配比。
三、预加压1. 压缩空气进入加料器:通过气源将压缩空气送入加料器中,对焦粉和精细粉末进行预加压。
2. 调节预加压力:根据喷煤设备的要求,调节预加压力,以保证喷出的物料量和速度达到最佳状态。
四、喷煤1. 喷煤开始:在高炉内形成一定的风幕后,开启喷枪进行喷煤。
2. 喷煤过程:在喷枪的作用下,经过高速气流的冲击和摩擦,焦粉和精细粉末被分散、雾化,并与高温空气混合后进入高炉内。
3. 控制喷煤量:根据生产需要,通过控制系统对喷煤量进行调节和控制。
五、监测与调整1. 监测高炉状态:通过各种监测设备对高炉内温度、压力等参数进行实时监测,并及时调整喷煤量和配比等参数。
2. 调整喷煤参数:根据实际情况对喷枪位置、角度、距离等参数进行调整,以获得最佳喷煤效果。
六、结束工作1. 喷煤结束:根据生产计划和需要,结束喷煤工作。
2. 喷枪清洗:将喷枪内残留的物料清除干净,并进行必要的维护和保养。
3. 设备检查:对所有设备进行检查和维护,以保证下次使用时的正常运行。
以上就是高炉喷煤的详细工艺流程。
在实际生产中,需要严格按照规定操作流程进行操作,并加强监测和调整,以确保高炉生产效率和产品质量。
高炉喷煤系统最佳操作法和常见故障(工程师培训)

高炉喷煤系统最佳操作法和常见故障前言一、工艺简述:高炉喷煤就是把原煤(无烟煤、烟煤)经过烘干、磨细、用压缩空气(或氮气)输送,通过喷煤枪从高炉风口直接喷入炉缸的生产工艺。
高炉喷吹燃料从风口直接把辅助燃料吹入炉缸,代替燃烧的焦炭增加热量,以降低焦比,强化冶炼。
高炉可以喷吹的燃料分液体(重油、轻油、原油、焦油及沥青等)、固体(无烟煤、烟煤、焦粉等)和气体(天然气、焦炉煤气以及炉身喷吹用还原性气体等)三类。
中国主要喷吹煤粉。
高炉喷吹燃料产生以下后果:①焦比大幅度降低中国首都钢铁公司1号高炉1966年通过富氧和提高风温,油、煤喷吹量达入炉燃料量的45%,焦比月平均366公斤/吨铁,目前中国多数高炉每吨铁喷煤60~120公斤。
焦比降低的主要原因是燃料中的碳代替了风口前燃烧焦炭的碳量;燃料中含有H2(如重油含H2达10~12%),促进高炉内的还原。
②要求热补偿喷入高炉的燃料在风口前是冷的。
在燃烧前汽化分解时要消耗部分热量,使炉缸温度降低(冷化作用),必须提高风温来补偿。
此外,喷吹燃料可促进富氧鼓风。
苏联喷吹天然气的高炉鼓风含氧可富化到30%以上。
③促进高炉顺行可用来调节炉况高炉喷吹燃料后炉缸中心气流增强,温度提高,风口平面上沿半径温度梯度减小,炉缸工作更均匀。
但如喷吹量超过一定限度,中心过吹,则会破坏顺行。
遇此情况应采取上部调节,加重中心负荷;下部调节,扩大风口直径,缩短风口长度;以及富氧鼓风等措施。
利用改变喷吹量可调节炉况:当炉况向凉时,加大喷吹量;炉况向热时,减少喷吹量。
但炉况已凉或已热后则不宜采用。
高炉刚开始喷吹燃料,由于“冷化作用”,炉温不高;几小时后,预还原的炉料进入炉缸,炉温又逐渐升高。
这段凉热变化期称为“热滞后”时间,可作调节炉况的依据。
④较高压差操作由于喷吹燃料产生的煤气量比被替代的焦炭产生的多,使煤气的浮力增加,加之喷吹燃料后焦比降低,料批中焦炭比例减少,都使料柱阻力增大,压差升高(在高炉顺行前提下,压差略高,仍可维持正常生产)。
喷煤工艺流程图及概述

炼铁一厂喷煤系统工艺流程图及概述山西中阳钢铁有限公司一体系升级改造项目高炉工程制粉喷吹系统,制粉、收粉系统全部利旧;干燥系统除热风炉废气管道需改造外,其他设施利旧;对喷吹系统进行局部改造。
制粉喷吹系统主要工艺现状:制粉喷吹站厂房为混凝土结构,全封闭。
煤粉制备系统采用单系列全负压制粉工艺,喷吹系统采用1个煤粉仓、下部六罐并列(每三罐分别对应405m³高炉)。
整个系统即1套干燥气发生炉系统、1套磨煤机制粉系统、1套煤粉收集系统、2套喷吹系统(一个煤粉仓,下部六罐并列)。
新建1780m3高炉投产后,2座405m3高炉拟全部拆除,现有制粉喷吹站只为新1780m3高炉供给煤粉。
新建1780m3高炉主管及分配器设置方案为:2根喷吹主管(一个主管对应一个分配器)及2个炉前分配器(1#分配器对应奇数风口,2#分配器对应偶数风口)的直接喷吹工艺。
喷吹系统与原系统的交接界面为:喷吹罐输煤阀后的喷吹主管起点。
喷吹煤粉主管及分配器平台为本工程设计范围。
1、工艺条件及要求1)原煤条件单一煤种和混合煤均可喷吹,通常使用三种煤组成混合煤,安全措施上按强爆炸性烟煤设计。
原煤的理化指标见表2.10-1。
表1 原煤的理化指标表成分工业分析( % )粒度mm哈氏可磨系数HGIV daf A ad M t S t.ad设计要求≤25 ≤12 ≤14 ≤0.8 ≤50 ≥502)煤粉条件煤粉质量要求见表2.10-2。
表2 煤粉质量要求表项目数值备注煤粉粒度:-200目70~80%<1mm 100%煤粉水份≤1.3%3)制粉喷吹能力按高炉正常日产铁水量4005吨,正常喷吹能力为160kg/t铁计,高炉正常喷吹所需煤粉量为26.7t/h;按高炉正常日产铁水量4005吨,喷吹能力为200kg/t 铁计,高炉最大喷吹所需煤粉量为33.4t/h。
2、主要工艺参数制粉喷吹系统主要工艺参数见表2.10-3。
表3 喷吹系统工艺参数序号名称单位数值备注1 高炉公称容积m317802 风口数个223 高炉热风压力(最大)MPa 0.354 喷吹站到最远风口距离m ~1505 高炉喷吹量t/h 26.7 最大33.46 吨铁理论喷煤量kg/t 160 设备能力2007 系统现状能力kg/t 110~120 不改造喷吹罐8 加压、流化用氮气量Nm3/h 1600 0.85MPa(g)9 喷吹用压缩空气量Nm3/h 1400 0.85MPa(g)10 喷吹罐倒罐周期min 40~503、主要工艺流程分配器及煤粉主管流程图见附图。
高炉喷吹煤粉系统

•精选ppt
7.1 煤粉制备系统
•精选ppt
7.1.1 煤粉制备工艺
一. 按磨煤机分为两类: 球磨机制粉、中速磨制粉
1. 球磨机制粉工艺
2. 80年代广为采用球磨机制粉工艺流程
。
•精选ppt
1-原煤仓;2-给煤机;3-一次风机;4-一级旋风分离器;5-二级旋风 离器;6-布袋收粉器;7-二次风机;8-煤粉仓;9-球磨机;10-木屑分 离器;11-粗粉分离器;12-锁气器;13-冷风调节阀;14-切断阀;
改造后的工艺流程如下:
•精选ppt
改进后的球磨机制粉工艺流程图
•精选ppt
2. 中速磨制粉工艺 中速磨煤机本身带有粗粉分离器,从
中速磨出来的气粉混合物直接进入布袋收 粉器,被捕捉的煤粉落入煤粉仓,尾气经 排粉风机排入大气。
•精选ppt
中速磨制粉工艺流程图
•精选ppt
二. 按煤种分三种: 烟煤制粉工艺 无烟煤制粉工艺 烟煤与无烟煤混合制粉工艺
为煤粉仓、中间罐和喷吹罐。
•精选ppt
串罐喷吹工艺
1-塞头阀;2-煤粉仓电子称; 3-煤粉仓;4-软连接;5-放散阀;6-上 钟阀;7-中间罐充压阀;8-中间罐电子
称;9-均压阀;10-中间罐; 11-中间罐流化阀;12-中钟阀; 13-软连接;14-下钟阀;15-喷吹罐充
阀;16-喷吹罐电子称; 17-喷吹罐;18-流化器; 19-给煤球阀;20-混合器
r/min
•精选ppt
在实际生产时圆筒的最佳转速为:
球磨机的优点: 对原煤品种的要求不高,它可以磨制各种不同硬度的
380m3高炉喷煤工艺设计说明

380m3高炉喷煤工艺设计说明380m3高炉喷煤工艺设计说明1 总论1.1 主要设计原则a) 系统设计主要原则可靠,在保证满足生产稳定性、可靠性的前提下降低喷煤系统投资。
b) 结合生产实际,设有煤粉筛,加强煤粉的筛分,扩大煤种的适应性,保证煤粉的顺利输送与喷吹,防止高炉堵枪。
c) 具备超大粉仓,提供系统生产过程中足够的检修时间,防止设备检修对高炉喷煤的影响,保证喷煤的可靠性。
d) 设计有独立的煤粉仓,保证系统生产过程中煤粉存放的安全性。
e) 喷吹设计足够的喷吹能力,满足高炉以后喷煤能力的发展。
f) 空压机为两台高压空压机,保证足够的喷吹能力。
开二备一,保证喷煤系统生产的可靠性。
g) 工程包括废气系统,便于控制系统氧含量,保证安全生产。
h) 系统预留氮气接口,便于烟煤喷吹。
主要设计参数项目参数备注高炉容积(m3)380设计日产量(t/d) 1600设计煤比(Kg/t.Fe) 160设计喷煤能力(t/h) 12磨机选型HRM1300设计制粉能力(t/h) 16-20收尘器面积(m2)935粉仓设置(m3)100 独立粉仓煤粉筛MZS120-200喷吹罐(m3)16上料系统皮带B650 100t/h料坑给料机DK1600 2台螺杆空压机23m3 1.0MPa 2原煤仓(m3)90系统总功率(Kw)9001.2 设计煤种:无烟煤或贫瘦煤挥发分:8%≤Vf≤16%灰分:Af≤16%全硫:Sf≤0.6%水分:Wf≤10%哈氏可磨系数:HGI>75粒度:≤40mm1.3 设计范围包括中速磨制粉、一级布袋收粉、并列罐喷吹系统及其配套设施。
1.4 喷煤工艺本着先进、可靠、简单、实用的设计的原则,380m3高炉采用直接喷煤短流程(包括中速磨制粉、一次布袋收粉器)、流化上出料浓相输送高浓度喷吹、计算机自动控制等先进的喷煤工艺技术和设备。
其主要工艺设施包括:原煤上料系统、两套制粉系统、喷吹系统及其附属设施。
其工艺流程及喷吹主要参数简述如下:1、储煤场:受煤斗→大倾角皮带机→原煤仓;2、制粉间:原煤仓→给料机→中速磨→一次布袋收粉器;3、喷吹间:一次布袋收粉器→煤粉仓→喷吹罐→分配器→喷煤枪。
喷煤工艺流程图及概述
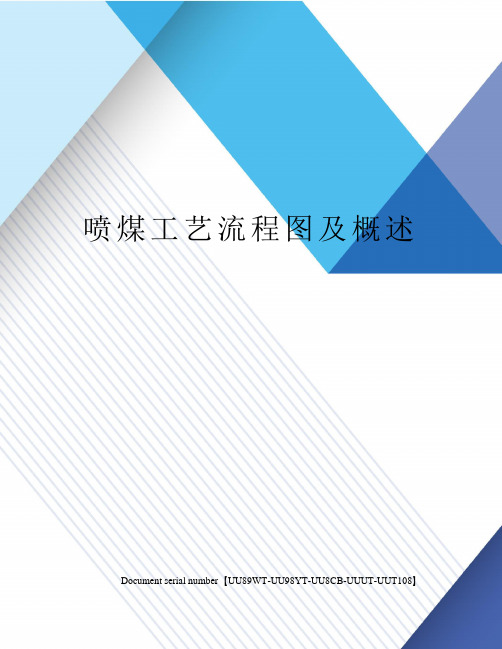
喷煤工艺流程图及概述 Document serial number【UU89WT-UU98YT-UU8CB-UUUT-UUT108】炼铁一厂喷煤系统工艺流程图及概述山西中阳钢铁有限公司一体系升级改造项目高炉工程制粉喷吹系统,制粉、收粉系统全部利旧;干燥系统除热风炉废气管道需改造外,其他设施利旧;对喷吹系统进行局部改造。
制粉喷吹系统主要工艺现状:制粉喷吹站厂房为混凝土结构,全封闭。
煤粉制备系统采用单系列全负压制粉工艺,喷吹系统采用1个煤粉仓、下部六罐并列(每三罐分别对应405m3高炉)。
整个系统即1套干燥气发生炉系统、1套磨煤机制粉系统、1套煤粉收集系统、2套喷吹系统(一个煤粉仓,下部六罐并列)。
新建1780m3高炉投产后,2座405m3高炉拟全部拆除,现有制粉喷吹站只为新1780m3高炉供给煤粉。
新建1780m3高炉主管及分配器设置方案为:2根喷吹主管(一个主管对应一个分配器)及2个炉前分配器(1#分配器对应奇数风口,2#分配器对应偶数风口)的直接喷吹工艺。
喷吹系统与原系统的交接界面为:喷吹罐输煤阀后的喷吹主管起点。
喷吹煤粉主管及分配器平台为本工程设计范围。
1、工艺条件及要求1)原煤条件单一煤种和混合煤均可喷吹,通常使用三种煤组成混合煤,安全措施上按强爆炸性烟煤设计。
原煤的理化指标见表-1。
表1 原煤的理化指标表2)煤粉条件煤粉质量要求见表-2。
表2 煤粉质量要求表3)制粉喷吹能力按高炉正常日产铁水量4005吨,正常喷吹能力为160kg/t铁计,高炉正常喷吹所需煤粉量为h;按高炉正常日产铁水量4005吨,喷吹能力为200kg/t铁计,高炉最大喷吹所需煤粉量为h。
2、主要工艺参数制粉喷吹系统主要工艺参数见表-3。
表3 喷吹系统工艺参数3、主要工艺流程分配器及煤粉主管流程图见附图。
喷煤工艺流程:该系统采用磨辊中速磨制粉,双管路加分配器浓相输粉的新工艺流程。
高炉喷吹煤粉工艺系统主要由:原煤贮运、煤粉制备、煤粉输送、煤粉喷吹、干燥气体制备和供气动力系统组成。
喷煤技术
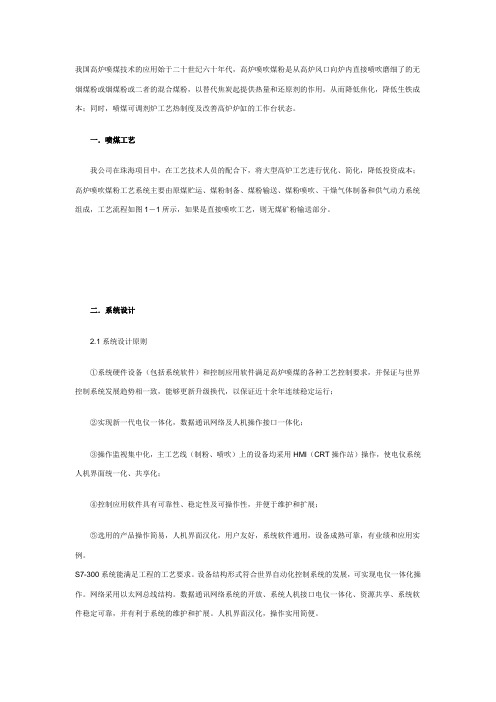
我国高炉喷煤技术的应用始于二十世纪六十年代,高炉喷吹煤粉是从高炉风口向炉内直接喷吹磨细了的无烟煤粉或烟煤粉或二者的混合煤粉,以替代焦炭起提供热量和还原剂的作用,从而降低焦化,降低生铁成本;同时,喷煤可调剂炉工艺热制度及改善高炉炉缸的工作台状态。
一.喷煤工艺我公司在珠海项目中,在工艺技术人员的配合下,将大型高炉工艺进行优化、简化,降低投资成本;高炉喷吹煤粉工艺系统主要由原煤贮运、煤粉制备、煤粉输送、煤粉喷吹、干燥气体制备和供气动力系统组成,工艺流程如图1-1所示,如果是直接喷吹工艺,则无煤矿粉输送部分。
二.系统设计2.1系统设计原则①系统硬件设备(包括系统软件)和控制应用软件满足高炉喷煤的各种工艺控制要求,并保证与世界控制系统发展趋势相一致,能够更新升级换代,以保证近十余年连续稳定运行;②实现新一代电仪一体化,数据通讯网络及人机操作接口一体化;③操作监视集中化,主工艺线(制粉、喷吹)上的设备均采用HMI(CRT操作站)操作,使电仪系统人机界面统一化、共享化;④控制应用软件具有可靠性、稳定性及可操作性,并便于维护和扩展;⑤选用的产品操作简易,人机界面汉化,用户友好,系统软件通用,设备成熟可靠,有业绩和应用实例。
S7-300系统能满足工程的工艺要求。
设备结构形式符合世界自动化控制系统的发展,可实现电仪一体化操作。
网络采用以太网总线结构。
数据通讯网络系统的开放、系统人机接口电仪一体化、资源共享、系统软件稳定可靠,并有利于系统的维护和扩展。
人机界面汉化,操作实用简便。
2.2系统硬件及设备设计2.2.1控制系统硬件及设备设计概要随着自动化技术的不断发展和计算机技术的飞速进步,今天的自动化控制概念也发生了巨大的变化。
在传统的自动化解决方案中,自动化控制实际上是由各种独立的、分离的技术和不同厂家的产品来搭配起来的,比如一个大型工厂经常是由过程控制系统、可编程控制器、上位监控计算机、SCADA系统和人机界面产品共同进行控制。
- 1、下载文档前请自行甄别文档内容的完整性,平台不提供额外的编辑、内容补充、找答案等附加服务。
- 2、"仅部分预览"的文档,不可在线预览部分如存在完整性等问题,可反馈申请退款(可完整预览的文档不适用该条件!)。
- 3、如文档侵犯您的权益,请联系客服反馈,我们会尽快为您处理(人工客服工作时间:9:00-18:30)。
Kuettner 喷煤系统的分配精度,不是靠分配器后各支管的严格等距离来 获得的,而是靠分配器、以及分配器后的阻流管、再加上设置在总管上 的流量测量和控制装置来保证的。
(3) 使用寿命长
Kuettner 喷煤系统采用的是低速浓相输送,加上独特的内部设计,可以 保证在分配器和管道内几乎没有磨损,实际上根本没有更换的必要。投 产至今的所有喷煤装置,尚无任何一套分配器更换过,甚至从来还没有 维修过。运行时间最长的已超过十五年。从而大大节约了设备的运行成 本,增加了设备的作业率。
沙钢的三座 2600 m3 的高炉和首钢京唐钢铁公司的二座 5500m3 的高炉都采 用了氧煤喷枪技术。
4
2.11 特殊的操作软件 由 Kuettner 公司独立开发的软件,包含了所有制粉系统和喷吹系统的技术 诀窍和工艺诀窍,也是确保上述各项特点得以充分体现的最重要因素。 Kuettner 的软件对计算机硬件没有限制,适用于当今任何计算机系统。
2.2 低速浓相输送 煤粉输送速度低: 2~4 m/s 煤粉输送比高: 60 kg 煤粉 / kg 输送气体 由于煤粉的输送速度低,保证了管道和分配器内几乎没有磨损,对有关设备 的磨损也微乎其微,从而极大地延长了设备的寿命,长期不需要大修。使用 寿命大于 20 年。 此外,由于实现了高输送比,进入高炉的煤粉输送气体只有稀相方式的一 半,甚至是三分之一,由此节约了大量炉内用于将输送气体从 80°C 加热至 2150°C 的焦碳消耗。仅此一项,Kuettner 的喷煤技术将可以为用户每年节 约焦碳消耗几十万美元。这还尚未计算置换焦碳所节约的成本。在蒂森高炉 上使用的 Kuettner 的喷煤系统,其实际输送比已达到 90 kg 煤粉以上。
特殊设计的减震装置,使得振动筛工作时对厂房框架几乎没有任何振动。
2.6 二个喷吹罐
Kuettner 还掌握了一套喷吹装置只需要二个喷吹罐的技术诀窍。设备的可靠 性和作业率远远高于高炉本身。这些装置运用至今,还从来没有出现过由于 喷吹罐的原因而影响高炉喷煤的情况。使用时间最长的喷煤装置使劲至今已 超过 15 年。
2.3 置换比高 采用 Kuettner 的煤粉浓相输送及喷吹工艺,可以确保获得更高的焦碳置换 比。这主要归功于其独特设计的工艺流程和喷枪系统。Kuettner 在上钢一厂
1
的高炉喷煤装置投产后,目前的焦碳置换比达到 1:1.1。即每喷入 1 公斤煤 粉,置换出 1.1 公斤的焦碳。
2.4 远距离喷煤 总管带分配器的配置是专为远距离喷煤而设计的。1986 年/1989 年,在蒂森 克虏伯的高炉上装备了 Kuettner 开发的总管带分配器的喷煤系统。这一发展 与 Kuettner 公司的原有技术相结合,使得喷煤装置可以向 500~600 米距离 以外的高炉喷煤,最远可以达到 1000 米以上ner 公司的又一独家技术诀窍,至今尚无其它公司开发成 功。Kuettner 的氧煤喷枪系统于 1991 年在蒂森克虏伯 Hoesch 的高炉上首 先投入生产使用,当年就达到了更高的喷煤率和更低的焦碳消耗量。目前 氧煤喷枪已是标准配置之一,在新装置中被广泛采用。
Kuettner 高炉喷煤系统
1. 制粉系统
Kuettner 公司同时具有制粉系统和喷吹系统二方面的经验和技术诀窍。这是 其他竞争者所无法抗衡的一大技术优势。而且,将制粉和喷吹二个系统联合 布置在同一幢建筑物内,完全是 Kuettner 公司的首创。
2. 喷吹系统
2.1 全氮气
整个喷吹系统采用全氮气操作,确保了喷吹 100% 烟煤的操作安全,而氮气 的总消耗量仅与稀相输送系统相同。输送气体不需要另外再加压缩空气。从 而大大降低了进入高炉的输送气体量。
5
2.5 振动筛 Kuettner 喷煤装置的配置中,在煤粉仓和每个喷吹罐之间,特别设置有振动 筛。这是保证将煤粉仓的纤维状物和煤粉仓内可能形成的结团物彻底排除的 最后一道屏障。从而确保进入喷吹罐的煤粉完全适合喷吹。这就是为什么 Kuettner 可 以 保 证 喷 吹 管 道 不 存 在 堵 塞 的 重 要 原 因 之 一 。 因 此 , 采 用 Kuettner 的工艺,整个总管设置被大大地简化了,既不需要辅助修车道,也 不需要进行法兰连接。这使得用户的辅助投资大大地节约了。
与传统的喷枪比较,在使用氧煤喷枪的条件下,在高喷吹率时的氧气消耗 量可以极大地降低,并可以大大提高煤粉的气化速度,实现煤粉的充分燃 烧,提高置换比。使用氧煤喷枪,在喷煤率大于 180 kg/t 铁时,富氧率不 超过 2%。在同样条件下,使用氧煤喷枪可以多喷煤 30 kg/t 铁。氧煤喷枪 的寿命大于 12 个月。
二个喷吹罐换罐时,喷吹继续进行,而且检测不到任何波动,这也是成熟的 Kuettner 技术诀窍。在特殊的情况下,装置还具备只用一个喷吹罐单独循环 喷吹的功能。
2.7 二个总管、二个分配器
喷吹系统采用了二个喷吹罐、二根等直径总管和二个分配器,这是 Kuettner 的标准配置。目前世界上只有 Kuettner 公司掌握了这种技术。二个分配器后 的支管分别对应奇数风口和偶数风口。
2.9 分配器
(1) 布置简单、合理
Kuettner 喷煤系统对分配器的位置和分配器后各支管的布置和长度没有 严格限定,因而,不影响高炉其他系统的布局。这对于喷煤装置的安装 和检修都极为方便,尤其是适用于现有高炉的改造。
3
分配器一般设置在炉前平台附近或高炉厂房外侧。分配器后各支管的长 度不要求严格相等,也不需要特殊设计和制造,更不需要特殊走向和安 装。由于分配精度是靠工艺和设备来保障的,因而大大简化了对支管设 计、制造和安装的要求,极大地降低了维修费用。
Kuettner 还成功掌握了从一个喷吹罐引出三根总管的技术。
2.8 一套喷煤装置喷三座高炉
由于 Kuettner 成功掌握了从一个喷吹罐引出三根总管的技术,而且,三根总 管的煤粉流量可以分别独立调节,由此,开创了用一套喷吹装置同时向三座 高炉喷煤的先河。这全世界第一套一对三的喷煤装置,在重庆钢铁公司 2001 年当年签约,当年投产。梅山也采用了这种技术。
采用了二个分配器的另一个突出优点是,在实现喷吹率大范围调整时,并不 需要更换系统内的任何部件,例如分配器后的阻流管等,而且分配器之间的 切换,对现有的喷吹率没有任何干扰,喷吹始终连续不断。二个分配器的操 作的灵活性由此得以充分体现。此外,用这种方式还可以实现不停产维修, 如果需要维修的话。
总之,二个分配器和一个分配器相比,喷吹率调节范围更大,装置可靠性和 作业率更高,高炉操作更容易。二个分配器给用户带来的综合优势,是一个 分配器所无法比拟的。
2
采用上述技术的关键是从一个喷吹罐直接引出二根直径完全相同的总管。这 是一项极其重要的技术进步,是实现一座高炉用二个分配器喷吹的先决技术 条件。二根总管的煤粉流量可以分别单独测量和调整。Kuettner 公司这项独 特的技术诀窍经过了十五年多的生产应用,已达到了完美的程度。
实践证明,这种二根等直径总管带二个分配器的工艺配置,是确保喷吹率大 幅度变化时,系统仍保持浓相输送的有效手段。低喷吹率条件下的浓相输 送,可以方便地通过切断其中一根总管来实现。由于每个分配器是按奇偶数 风口分布的,因此,分配精度仍有可靠保证。