喷煤工艺流程的研究与探索
喷煤工艺流程
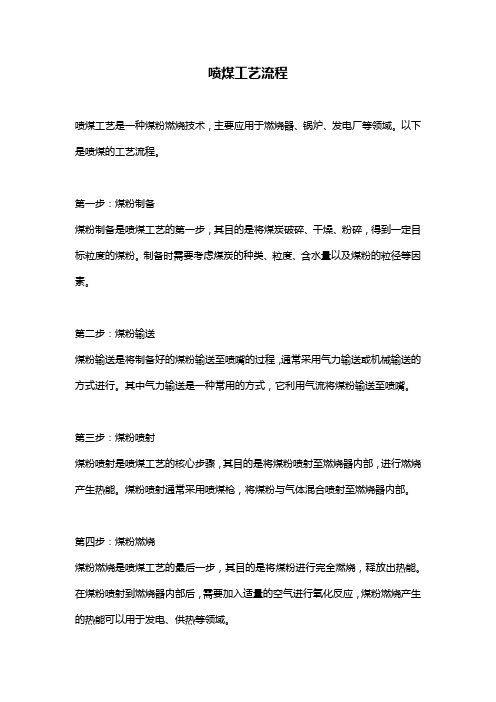
喷煤工艺流程
喷煤工艺是一种煤粉燃烧技术,主要应用于燃烧器、锅炉、发电厂等领域。
以下是喷煤的工艺流程。
第一步:煤粉制备
煤粉制备是喷煤工艺的第一步,其目的是将煤炭破碎、干燥、粉碎,得到一定目标粒度的煤粉。
制备时需要考虑煤炭的种类、粒度、含水量以及煤粉的粒径等因素。
第二步:煤粉输送
煤粉输送是将制备好的煤粉输送至喷嘴的过程,通常采用气力输送或机械输送的方式进行。
其中气力输送是一种常用的方式,它利用气流将煤粉输送至喷嘴。
第三步:煤粉喷射
煤粉喷射是喷煤工艺的核心步骤,其目的是将煤粉喷射至燃烧器内部,进行燃烧产生热能。
煤粉喷射通常采用喷煤枪,将煤粉与气体混合喷射至燃烧器内部。
第四步:煤粉燃烧
煤粉燃烧是喷煤工艺的最后一步,其目的是将煤粉进行完全燃烧,释放出热能。
在煤粉喷射到燃烧器内部后,需要加入适量的空气进行氧化反应,煤粉燃烧产生的热能可以用于发电、供热等领域。
总之,喷煤工艺是一种高效、环保的煤粉燃烧技术,其工艺流程包括煤粉制备、煤粉输送、煤粉喷射和煤粉燃烧等步骤,能够有效地利用煤炭资源,减少二氧化碳等有害气体的排放。
《综采工作面喷雾降尘理论及应用研究》范文
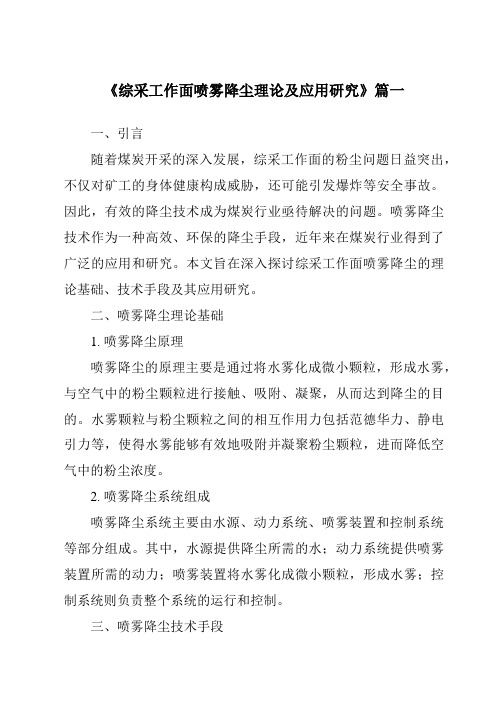
《综采工作面喷雾降尘理论及应用研究》篇一一、引言随着煤炭开采的深入发展,综采工作面的粉尘问题日益突出,不仅对矿工的身体健康构成威胁,还可能引发爆炸等安全事故。
因此,有效的降尘技术成为煤炭行业亟待解决的问题。
喷雾降尘技术作为一种高效、环保的降尘手段,近年来在煤炭行业得到了广泛的应用和研究。
本文旨在深入探讨综采工作面喷雾降尘的理论基础、技术手段及其应用研究。
二、喷雾降尘理论基础1. 喷雾降尘原理喷雾降尘的原理主要是通过将水雾化成微小颗粒,形成水雾,与空气中的粉尘颗粒进行接触、吸附、凝聚,从而达到降尘的目的。
水雾颗粒与粉尘颗粒之间的相互作用力包括范德华力、静电引力等,使得水雾能够有效地吸附并凝聚粉尘颗粒,进而降低空气中的粉尘浓度。
2. 喷雾降尘系统组成喷雾降尘系统主要由水源、动力系统、喷雾装置和控制系统等部分组成。
其中,水源提供降尘所需的水;动力系统提供喷雾装置所需的动力;喷雾装置将水雾化成微小颗粒,形成水雾;控制系统则负责整个系统的运行和控制。
三、喷雾降尘技术手段1. 喷雾装置的选择根据综采工作面的实际情况,选择合适的喷雾装置至关重要。
常用的喷雾装置包括旋转式、喷嘴式、气流式等。
在选择时,应考虑其雾化效果、喷雾范围、耐久性等因素。
2. 喷雾参数的优化喷雾参数包括喷雾压力、喷雾量、喷雾角度等。
通过对这些参数的优化,可以提高喷雾降尘的效果。
例如,增加喷雾压力可以提高水雾的覆盖范围和吸附能力;适当调整喷雾量可以保证降尘效果的同时避免水资源的浪费。
四、喷雾降尘应用研究1. 实际应用效果在综采工作面应用喷雾降尘技术,可以有效地降低空气中的粉尘浓度,改善工作面的环境质量。
同时,由于水雾的吸附和凝聚作用,还可以减少粉尘对设备的磨损和污染。
此外,喷雾降尘技术还可以与其它除尘技术相结合,进一步提高降尘效果。
2. 应用中存在的问题及解决方案尽管喷雾降尘技术在综采工作面得到了广泛的应用,但仍存在一些问题。
例如,在某些特殊的工作面条件下,喷雾降尘的效果可能受到影响;同时,如何合理选择和使用喷雾装置、优化喷雾参数等问题也需要进一步研究和探索。
喷煤工艺介绍
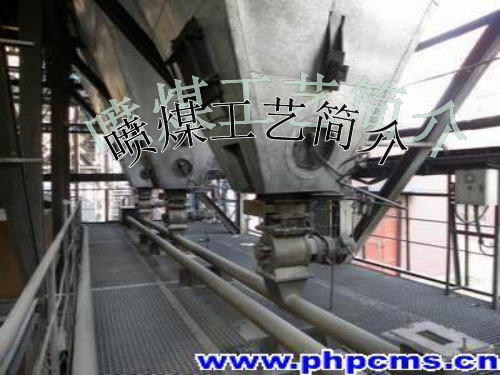
快速停机动作: 快速停机动作:
1)打开热风炉废气换向阀(FHF),磨机入 口温度调节阀全开 2)烟气废气放散阀打开(YFF); 3)混合烟气换向阀关闭(HHF) 4)给煤机停(延时0-15S) 5)磨煤机停(延时0-15S)
3喷煤喷吹工艺流程 喷煤喷吹工艺流程
1)煤粉喷吹设计参数 ) 最大喷煤量:200kg/t 正常喷煤量:125kg/t 每座高炉14个风口全部喷煤。 2)喷吹设施 ) 四座高炉的喷吹站与制粉间合建在一起,每座高炉的喷吹系统设计采用两个并列喷吹罐,单管路加炉前分配器 的喷吹方式,共设有八个喷吹系列。每座高炉的两个并列罐交替喷吹,通过可编程序控制器进行自动喷吹与换 罐。制粉间的磨煤机室、喷吹站的喷吹间为封闭外式的混凝土结构。 3)喷吹工艺及特点 ) 四座高炉的喷吹站与制粉间合建在一起,设有一个喷煤主控室。 ——喷吹形式 每座高炉的喷吹罐采用并列式布置,两个并列罐上出料浓相交替喷吹。主要设备为两个煤粉仓,两个喷吹罐。 煤粉仓有效容积60m3,储煤粉量可以满足高炉在最大喷吹量的条件下连续喷吹6小时。煤粉仓采用料位计进行 料位监测,喷吹罐采用电子称进行重量监测。由煤粉仓卸下的煤粉加入到喷吹罐内,可使喷吹罐交替向高炉喷 吹煤粉。喷吹罐设计有效容积为14m3,直径∅2000mm,按高炉喷吹量200kg/t计算,一罐煤粉可以供高炉连续 喷吹40分钟。 ——补气调节器 高炉喷煤采用上出料浓相喷吹形式,采用补气调节器,通过调节补气量的大小改变调节器内煤粉的输送状态, 达到调节喷吹量的目的。煤粉经管道、炉前分配器,通过喷枪喷入高炉。 ——喷吹罐设置自动稳压装置,工作压力自动稳定在设定值。使喷吹罐压力不因煤粉输出而降低,以确保输煤 速率的稳定均匀。 ——喷吹系统各阀门采用气动煤粉专用球阀。电磁阀在电磁阀站内集中维护管理。 4)喷吹系统安全措施 ) 为保证喷吹烟煤的安全可靠,采取一系列的防火防爆措施。例如:煤粉仓内设有CO分析仪时实监控煤粉仓内的 CO浓度,若CO浓度超标则进行紧急充氮气保护;喷吹罐内设有温度、压力等检测仪表。 5)喷吹系统主要设备组成 ) 喷吹系统由喷吹罐、喷吹主管路、炉前分配器、喷吹支管路、喷枪组成。
钢铁厂喷煤车间喷吹工艺流程

钢铁厂喷煤车间喷吹工艺流程英文回答:The process of coal spraying in the steel mill is an important step in the production of steel. It involves the use of coal dust to generate heat and reduce the impurities in the iron ore, resulting in a higher quality steel product. The coal spraying workshop is responsible for the preparation and application of the coal dust.The process begins with the preparation of the coal dust. The coal is crushed into fine particles and then mixed with a binding agent to form a coal dust mixture. This mixture is then loaded into a coal spraying machine.Once the coal dust is prepared, the spraying process can begin. The coal spraying machine is equipped with a nozzle that sprays the coal dust onto the iron ore. The nozzle is controlled by a computer system that regulates the amount and direction of the coal dust spray. Thisensures that the coal dust is evenly distributed and covers the entire surface of the iron ore.During the spraying process, the coal dust reacts with the impurities in the iron ore, causing them to separate and form a slag. The slag is then removed, leaving behind a purified iron ore. This purified iron ore is then further processed to produce steel.The coal spraying process requires skilled operators who are responsible for monitoring the spraying machine and adjusting the settings as needed. They also need to ensure that the coal dust mixture is prepared correctly and that the spraying process is carried out efficiently.In addition to the technical aspects, there are also safety considerations in the coal spraying workshop. The operators need to wear protective gear, such as helmets and goggles, to protect themselves from the coal dust. They also need to follow safety procedures to prevent accidents and ensure the well-being of everyone in the workshop.Overall, the coal spraying process in the steel mill is a crucial step in the production of high-quality steel. It requires skilled operators and careful monitoring to ensure that the spraying is done effectively and safely.中文回答:钢铁厂喷煤车间的喷吹工艺是钢铁生产中的重要环节。
喷煤工艺流程

喷煤工艺流程喷煤工艺流程是一种以喷煤机为主体来进行的煤炭加工工艺。
喷煤工艺流程可以将煤炭喷入炉内进行燃烧,提供热能。
下面我们来详细介绍一下喷煤工艺流程。
首先,喷煤工艺流程的第一步是原料准备。
在进行喷煤工艺之前,需要对煤炭进行预处理。
这个过程主要包括煤炭的破碎、筛分和干燥等工序。
煤炭破碎是将煤炭破碎成小块,以便于后续的处理和喷煤。
筛分是将煤炭进行分级,分离出不同尺寸的煤炭,以满足不同的喷煤需求。
干燥是将煤炭中的水分去除,提高煤炭的燃烧效率。
接下来,喷煤工艺流程的第二步是煤粉输送。
经过破碎、筛分和干燥处理的煤炭会被输送到喷煤机内。
喷煤机通过旋转的喷头将煤粉喷入燃烧器中进行燃烧。
煤粉输送的过程中需要注意保证输送的稳定性和流动性,以确保煤粉的均匀喷入燃烧器中。
第三步是燃烧过程。
在燃烧器中,煤粉与空气进行混合,形成可燃气体。
燃烧过程中需要达到适当的温度和压力,以保证煤炭的完全燃烧。
同时,还需要通过控制煤粉的喷入速度和量来控制燃烧的强度和稳定性。
第四步是废气处理。
煤炭燃烧过程会产生大量的废气,其中包括煤烟、烟尘和有害气体等。
这些废气为环境带来一定的污染。
因此,在喷煤工艺流程中,必须进行废气处理,减少对环境的污染。
常见的废气处理方法包括除尘器、脱硫装置、脱氮装置等。
除尘器可以过滤掉煤烟中的烟尘;脱硫装置可以去除煤烟中的二氧化硫;脱氮装置可以去除煤烟中的氮氧化物。
最后,喷煤工艺流程的最后一步是能量利用。
经过燃烧的煤炭会产生大量的热能,可以用于发电、供暖和工业生产等方面。
喷煤工艺流程需要对燃烧后的残渣进行处理,提取其中的热能,并将其转化为有用的能源。
综上所述,喷煤工艺流程是一种以喷煤机为主体的煤炭加工工艺。
喷煤工艺流程涉及到原料准备、煤粉输送、燃烧过程、废气处理和能量利用等一系列工序。
通过喷煤工艺流程,可以将煤炭进行高效利用,提供热能,同时最大限度地减少对环境的污染。
《综采工作面喷雾降尘理论及应用研究》范文
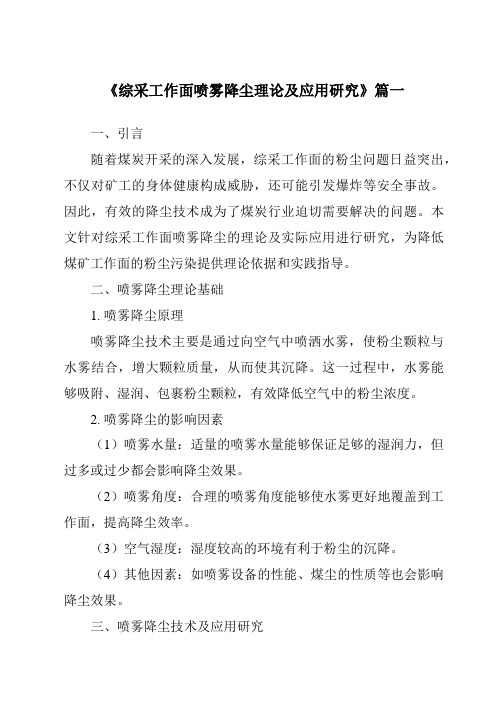
《综采工作面喷雾降尘理论及应用研究》篇一一、引言随着煤炭开采的深入发展,综采工作面的粉尘问题日益突出,不仅对矿工的身体健康构成威胁,还可能引发爆炸等安全事故。
因此,有效的降尘技术成为了煤炭行业迫切需要解决的问题。
本文针对综采工作面喷雾降尘的理论及实际应用进行研究,为降低煤矿工作面的粉尘污染提供理论依据和实践指导。
二、喷雾降尘理论基础1. 喷雾降尘原理喷雾降尘技术主要是通过向空气中喷洒水雾,使粉尘颗粒与水雾结合,增大颗粒质量,从而使其沉降。
这一过程中,水雾能够吸附、湿润、包裹粉尘颗粒,有效降低空气中的粉尘浓度。
2. 喷雾降尘的影响因素(1)喷雾水量:适量的喷雾水量能够保证足够的湿润力,但过多或过少都会影响降尘效果。
(2)喷雾角度:合理的喷雾角度能够使水雾更好地覆盖到工作面,提高降尘效率。
(3)空气湿度:湿度较高的环境有利于粉尘的沉降。
(4)其他因素:如喷雾设备的性能、煤尘的性质等也会影响降尘效果。
三、喷雾降尘技术及应用研究1. 技术研究(1)智能喷雾系统:通过安装传感器、控制器等设备,实现自动检测、自动调节喷雾水量和角度等功能,提高降尘效果。
(2)高效雾化喷嘴:采用先进的技术和材料,制造出具有高雾化效果、高覆盖率的喷嘴,提高降尘效率。
(3)节能技术:通过优化系统设计、使用高效能电机等措施,降低喷雾降尘系统的能耗。
2. 应用研究(1)综采工作面应用:在综采工作面安装喷雾系统,对工作面进行全面喷雾降尘,有效降低粉尘浓度。
(2)与其他降尘技术的结合:将喷雾降尘技术与湿式除尘、除尘袋等技术相结合,形成综合降尘系统,提高降尘效果。
(3)实践应用效果:经过实际应用,发现喷雾降尘技术能够显著降低综采工作面的粉尘浓度,改善矿工的工作环境,降低职业病发生率。
同时,该技术还具有投资成本低、操作简单等优点。
四、结论与展望本文对综采工作面喷雾降尘的理论及应用进行了研究。
研究结果表明,喷雾降尘技术能够有效降低工作面的粉尘浓度,改善矿工的工作环境。
钢铁厂喷煤车间喷吹工艺流程

钢铁厂喷煤车间喷吹工艺流程英文回答:The spraying process in the coal spraying workshop of the steel mill involves several steps. Let's take a look at the detailed process:1. Preparation: Before starting the spraying process, the necessary preparations need to be made. This includes checking the equipment, ensuring that it is in good working condition, and preparing the coal dust and other materials required for spraying.2. Mixing: The coal dust is mixed with a binder to forma slurry. The binder helps to improve the adhesion of the coal dust to the surface being sprayed. The ratio of coal dust to binder may vary depending on the specific requirements of the spraying process.3. Spraying: The prepared slurry is then loaded intothe spraying equipment. The spraying equipment typically consists of a spray gun or nozzle, which is connected to a compressed air source. The slurry is sprayed onto the surface to be coated, creating a thin layer of coal dust.4. Drying: After the coal dust is sprayed onto the surface, it needs to be dried. This can be done using various methods, such as natural drying or using drying equipment. The drying process helps to remove moisture from the coal dust and allows it to adhere firmly to the surface.5. Curing: Once the coal dust is dried, it undergoes a curing process. Curing involves allowing the sprayed coal dust to harden and form a solid coating. The duration ofthe curing process may vary depending on the specific requirements of the spraying process.6. Inspection: After the curing process is complete,the coated surface is inspected for quality. This mayinvolve checking for any defects, such as uneven coating or areas with insufficient coal dust coverage. Any defects found may need to be rectified before the final product isconsidered acceptable.7. Finishing: Once the inspection is complete and any necessary rectifications are made, the coated surface may undergo additional finishing processes. This may include sanding, polishing, or applying a protective layer to enhance the appearance and durability of the coating.中文回答:钢铁厂喷煤车间的喷吹工艺流程包括以下几个步骤:1. 准备工作,在开始喷吹工艺之前,需要进行必要的准备工作。
喷煤工艺流程的研究与探索
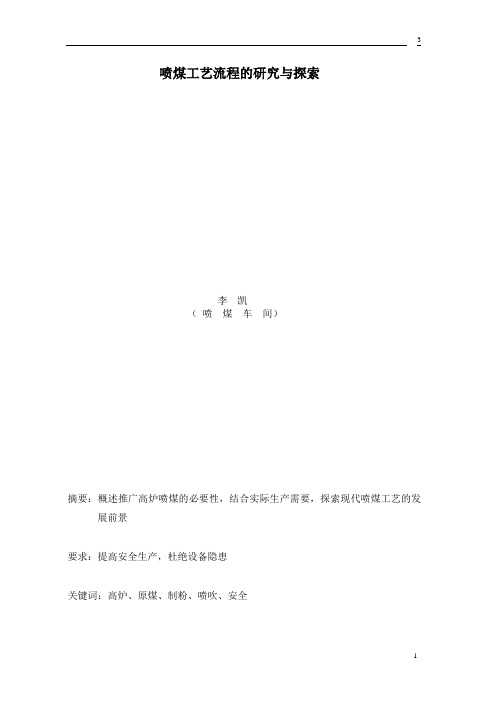
3喷煤工艺流程的研究与探索李凯(喷煤车间)摘要:概述推广高炉喷煤的必要性,结合实际生产需要,探索现代喷煤工艺的发展前景要求:提高安全生产,杜绝设备隐患关键词:高炉、原煤、制粉、喷吹、安全目录一概述(一)前言............................ (1)(二)简述喷煤的的出现和发展 (1)(三)高炉喷煤的定义 (1)(四)高炉喷煤的重要意义 (1)(五)高炉喷煤图 (2)二高炉用煤(一)煤的物理性质 (3)(二)煤的工艺性能 (4)(三)煤的性能要求 (6)三煤粉的制备(一)制粉系统工艺流程 (6)(二)制粉设备组成 (7)(三)制粉操作规程 (10)(四)制粉系统故障及处理 (12)(五)设备维护规程 (17)四煤粉的喷吹(一)计算 (17)(二)高炉喷吹设施的布置方式 (18)(三)高炉喷吹罐的出粉方式 (18)(四)高炉喷吹主要设备 (19)(五)喷煤操作 (19)(六)喷煤系统的故障及处理 (20)五高炉喷煤的防火防爆安全措施(一)煤粉爆炸的条件 (21)(二)高炉喷吹烟煤的安全措施 (22)(三)高炉喷煤系统气氛的懒化 (23)(四)受压容器的安全管理 (23)(五)防止明火和静电 (23)六结语一概述(一)前言随着高炉炼铁规模不断扩大和对生铁需求量的日益增加,高炉喷煤辅助燃料是现代高炉炼铁生产广泛采用的新技术,同时它还是现代高炉路况调节所不可缺少的重要手段之一。
论文主要介绍煤的一般特性、煤粉的制备喷吹和设备等内容。
注重新的喷煤工艺和各系统的设备点检等内容的介绍。
理论联系实际,使其内容具有一定的实用性。
(二)高炉喷煤的出现和发展自20世纪60年代初喷吹技术在法国获得了成功以后,美国、前苏联主要喷吹天然气,西欧、日本则自20世纪80年代初由喷吹重油转为喷吹煤粉。
我国是开发喷煤技术较早的国家,自20世纪60年代初开始试验,至今已有50多年历史,特别是近十几年来,高炉喷煤技术的到了广泛的应用和发展,从而促进了我国的钢铁工业的迅猛发展,减少了炼铁生产受炼焦碳资源、投资、环保等多方面的限制和影响。
高炉喷煤工艺流程
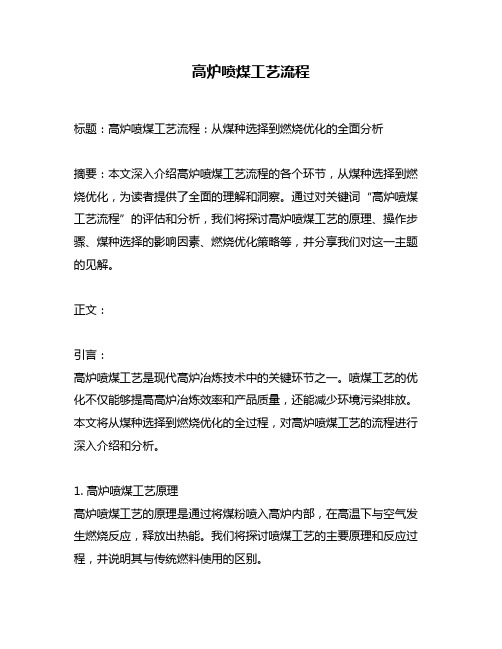
高炉喷煤工艺流程标题:高炉喷煤工艺流程:从煤种选择到燃烧优化的全面分析摘要:本文深入介绍高炉喷煤工艺流程的各个环节,从煤种选择到燃烧优化,为读者提供了全面的理解和洞察。
通过对关键词“高炉喷煤工艺流程”的评估和分析,我们将探讨高炉喷煤工艺的原理、操作步骤、煤种选择的影响因素、燃烧优化策略等,并分享我们对这一主题的见解。
正文:引言:高炉喷煤工艺是现代高炉冶炼技术中的关键环节之一。
喷煤工艺的优化不仅能够提高高炉冶炼效率和产品质量,还能减少环境污染排放。
本文将从煤种选择到燃烧优化的全过程,对高炉喷煤工艺的流程进行深入介绍和分析。
1. 高炉喷煤工艺原理高炉喷煤工艺的原理是通过将煤粉喷入高炉内部,在高温下与空气发生燃烧反应,释放出热能。
我们将探讨喷煤工艺的主要原理和反应过程,并说明其与传统燃料使用的区别。
2. 喷煤工艺的操作步骤在高炉喷煤工艺中,操作步骤的正确执行对工艺效果至关重要。
我们将介绍喷煤工艺的各个操作步骤,包括煤粉的研磨、输送系统的设计、喷煤装置的选型以及喷煤参数的控制等,并探讨每个步骤的优化方法。
3. 煤种选择对喷煤工艺的影响选择适合喷煤工艺的煤种是关键决策之一。
本节将介绍影响煤种选择的因素,如煤质特性、燃烧性能、价格等,并解释不同煤种对喷煤工艺的影响,为读者提供煤种选择的指导。
4. 喷煤工艺的燃烧优化喷煤工艺的燃烧优化对高炉冶炼效率和环境影响具有重要意义。
我们将介绍喷煤工艺的燃烧优化策略,包括调整喷煤参数、优化空气分布、控制煤气成分等,并解释这些策略对高炉运行的影响。
总结与回顾:通过对高炉喷煤工艺流程的全面介绍和分析,我们深入探讨了煤种选择、燃烧优化等关键环节。
我们认为高炉喷煤工艺的优化对高炉冶炼效率、产品质量和环境保护至关重要。
在煤种选择方面,需要综合考虑煤质特性、燃烧性能和价格等因素,并选择合适的煤种。
在燃烧优化方面,通过调整喷煤参数、优化空气分布和控制煤气成分等策略,可以提高高炉运行效率、降低排放物产生,实现可持续发展。
喷煤工艺流程

喷煤工艺流程
《喷煤工艺流程》
喷煤工艺是一种燃煤取暖或发电的技术,它利用喷嘴将煤粉喷入锅炉或燃烧室中,通过燃烧产生热能。
喷煤工艺通常被广泛应用于工业和发电厂,能够提高煤炭的利用率并减少对环境的影响。
喷煤工艺的流程大致如下:首先,原料煤经过粉碎设备破碎成细小的煤粉,然后通过输送设备将煤粉送入喷煤系统。
在喷煤系统中,煤粉与空气混合并喷入锅炉或燃烧室进行燃烧,产生高温和高压的烟气。
接下来,烟气经过锅炉和热交换器,传热给水,使水变成蒸汽。
生成的蒸汽可以驱动汽轮机进行发电,也可以通过热力传递给其他设备进行加热或加工。
烟气中的灰渣被收集并处理,以减少对环境的污染。
在整个喷煤工艺中,需要精密的控制系统和设备来保障稳定的煤粉喷射和燃烧效果。
同时也需要对煤粉进行处理和控制,以确保煤粉的质量和燃烧效率。
此外,对于废气的处理和排放也需要符合严格的环保标准,以保护环境和人类健康。
总的来说,《喷煤工艺流程》是一种高效、节能、环保的燃煤技术,它在工业生产和能源领域发挥着重要作用。
随着技术的不断进步,喷煤工艺也不断得到改进和优化,为推动清洁能源和可持续发展发挥着重要作用。
喷煤工艺流程图及概述
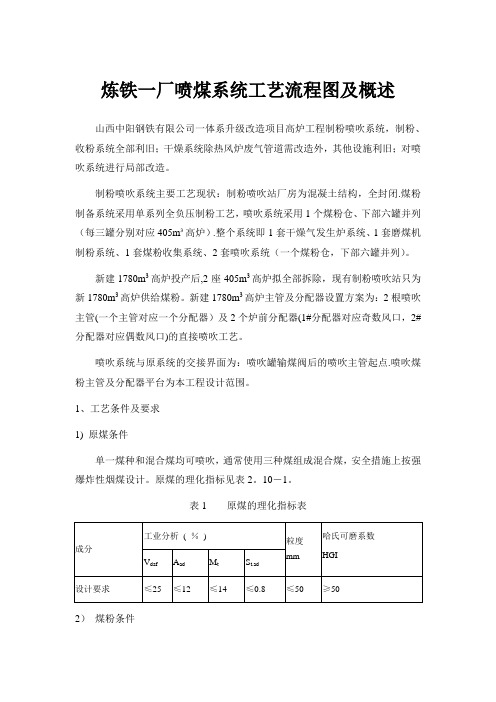
炼铁一厂喷煤系统工艺流程图及概述山西中阳钢铁有限公司一体系升级改造项目高炉工程制粉喷吹系统,制粉、收粉系统全部利旧;干燥系统除热风炉废气管道需改造外,其他设施利旧;对喷吹系统进行局部改造。
制粉喷吹系统主要工艺现状:制粉喷吹站厂房为混凝土结构,全封闭.煤粉制备系统采用单系列全负压制粉工艺,喷吹系统采用1个煤粉仓、下部六罐并列(每三罐分别对应405m³高炉).整个系统即1套干燥气发生炉系统、1套磨煤机制粉系统、1套煤粉收集系统、2套喷吹系统(一个煤粉仓,下部六罐并列)。
新建1780m3高炉投产后,2座405m3高炉拟全部拆除,现有制粉喷吹站只为新1780m3高炉供给煤粉。
新建1780m3高炉主管及分配器设置方案为:2根喷吹主管(一个主管对应一个分配器)及2个炉前分配器(1#分配器对应奇数风口,2#分配器对应偶数风口)的直接喷吹工艺。
喷吹系统与原系统的交接界面为:喷吹罐输煤阀后的喷吹主管起点.喷吹煤粉主管及分配器平台为本工程设计范围。
1、工艺条件及要求1) 原煤条件单一煤种和混合煤均可喷吹,通常使用三种煤组成混合煤,安全措施上按强爆炸性烟煤设计。
原煤的理化指标见表2。
10-1。
表1 原煤的理化指标表2)煤粉条件煤粉质量要求见表2。
10-2。
表2 煤粉质量要求表3) 制粉喷吹能力按高炉正常日产铁水量4005吨,正常喷吹能力为160kg/t铁计,高炉正常喷吹所需煤粉量为26。
7t/h;按高炉正常日产铁水量4005吨,喷吹能力为200kg/t 铁计,高炉最大喷吹所需煤粉量为33.4t/h。
2、主要工艺参数制粉喷吹系统主要工艺参数见表2。
10-3。
表3 喷吹系统工艺参数3、主要工艺流程分配器及煤粉主管流程图见附图。
喷煤工艺流程:该系统采用磨辊中速磨制粉,双管路加分配器浓相输粉的新工艺流程。
高炉喷吹煤粉工艺系统主要由:原煤贮运、煤粉制备、煤粉输送、煤粉喷吹、干燥气体制备和供气动力系统组成.4、干燥气发生炉系统热风炉废气管道改造干燥气发生炉所用热源,来自于热风炉废气的载热和煤气燃烧的化学热,热风炉废气由新建高炉热风炉烟囱前的烟道引出,热风炉废气使用量为95000m3/h,废气温度为140~180℃(不经余热回收时~310℃),废气管道直径为φ1420mm,采用外保温方式。
回转窑喷煤工艺

回转窑喷煤工艺
回转窑喷煤工艺是一种重要的工业技术,广泛应用于冶金、化工、建材等领域。
这种工艺主要是将煤粉喷入回转窑内,在高温下与空气发生燃烧反应,释放出大量的热能,用于加热物料或提供反应所需的热量。
回转窑喷煤工艺具有许多优点。
首先,它可以提高燃烧效率,减少能源浪费。
通过将煤粉直接喷入窑内,可以使燃料与空气充分混合,提高燃烧速度和燃烧效率。
其次,这种工艺可以灵活调整燃烧强度和热量分布,适应不同的生产需求。
此外,回转窑喷煤工艺还可以降低污染物的排放,提高环保性能。
在实际应用中,回转窑喷煤工艺需要严格控制各项操作参数。
例如,煤粉的粒度、喷煤量、喷煤速度等都需要根据具体情况进行调整。
同时,回转窑的转速、通风量、温度等也需要进行实时监测和控制,以确保工艺的稳定性和安全性。
此外,回转窑喷煤工艺还需要注意密封装置的要求。
密封装置是防止漏风、保证窑内气氛稳定的关键部件。
它需要具有良好的密封性能,能够减少漏风量,避免热量损失和环境污染。
总之,回转窑喷煤工艺是一种高效、环保、灵活的工业技术。
通过合理控制操作参数和注意密封装置的要求,可以实现高效、稳定、安全的工业生产。
随着科技的不断进步和工业的不断发展,回转窑喷煤工艺将会得到更广泛的应用和推广。
回转窑喷煤工艺
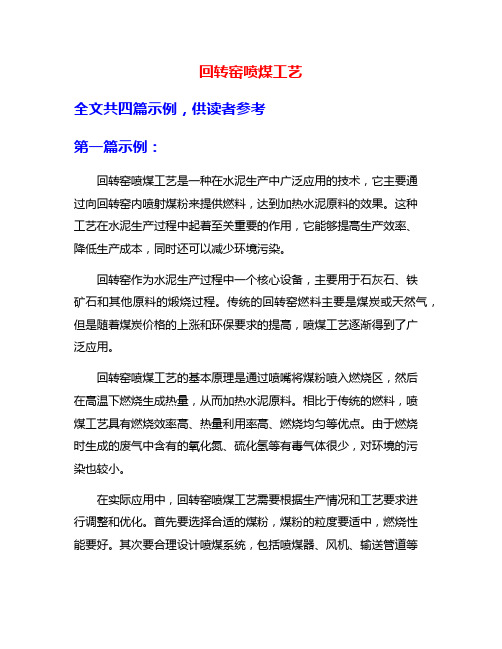
回转窑喷煤工艺全文共四篇示例,供读者参考第一篇示例:回转窑喷煤工艺是一种在水泥生产中广泛应用的技术,它主要通过向回转窑内喷射煤粉来提供燃料,达到加热水泥原料的效果。
这种工艺在水泥生产过程中起着至关重要的作用,它能够提高生产效率、降低生产成本,同时还可以减少环境污染。
回转窑作为水泥生产过程中一个核心设备,主要用于石灰石、铁矿石和其他原料的煅烧过程。
传统的回转窑燃料主要是煤炭或天然气,但是随着煤炭价格的上涨和环保要求的提高,喷煤工艺逐渐得到了广泛应用。
回转窑喷煤工艺的基本原理是通过喷嘴将煤粉喷入燃烧区,然后在高温下燃烧生成热量,从而加热水泥原料。
相比于传统的燃料,喷煤工艺具有燃烧效率高、热量利用率高、燃烧均匀等优点。
由于燃烧时生成的废气中含有的氧化氮、硫化氢等有毒气体很少,对环境的污染也较小。
在实际应用中,回转窑喷煤工艺需要根据生产情况和工艺要求进行调整和优化。
首先要选择合适的煤粉,煤粉的粒度要适中,燃烧性能要好。
其次要合理设计喷煤系统,包括喷煤器、风机、输送管道等设备的选型和布置。
最后要严格控制喷煤量和进风量,保证煅烧过程的稳定性和效率。
通过回转窑喷煤工艺,不仅可以提高水泥生产的效率和质量,还可以减少燃料成本和节约能源资源。
这种工艺在水泥行业的应用前景十分广阔。
随着技术的不断进步和环保意识的提高,相信回转窑喷煤工艺将在未来得到更广泛的推广和应用。
第二篇示例:回转窑喷煤工艺是一种常用的水泥生产工艺,通过喷煤技术可以提高窑炉内的燃烧效率,降低生产成本,保护环境,提高水泥质量。
下面将详细介绍回转窑喷煤工艺的原理、优势和应用。
一、回转窑喷煤工艺原理回转窑是水泥生产中常用的烧成设备,利用其旋转运动使原料在高温下热处理。
回转窑喷煤工艺就是在回转窑燃烧区域通过喷煤器喷入适量的煤粉,与石灰石一起燃烧,生成高温燃烧气体,为水泥熟料的煅烧提供热量。
喷煤工艺不仅可以提高燃烧效率,还可以降低燃料成本,减少CO2排放。
1. 提高燃烧效率:喷煤工艺可以使煤粉均匀燃烧,在提高热效率的同时减少二次燃烧过程,降低燃料消耗。
高炉喷煤工艺过程
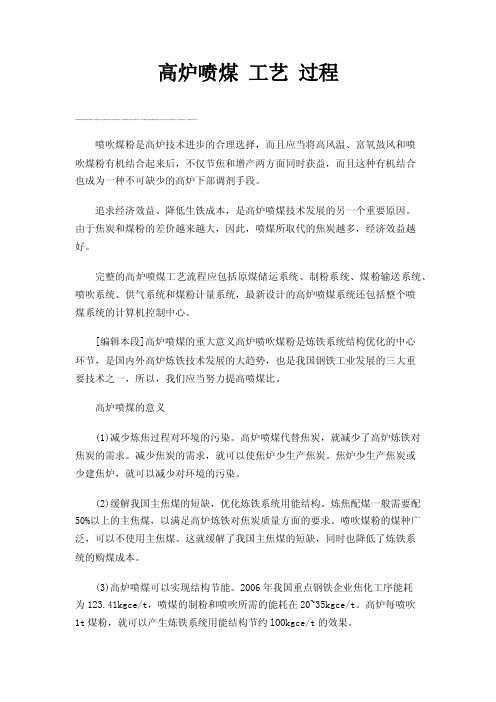
高炉喷煤工艺过程喷吹煤粉是高炉技术进步的合理选择,而且应当将高风温、富氧鼓风和喷吹煤粉有机结合起来后,不仅节焦和增产两方面同时获益,而且这种有机结合也成为一种不可缺少的高炉下部调剂手段。
追求经济效益、降低生铁成本,是高炉喷煤技术发展的另一个重要原因。
由于焦炭和煤粉的差价越来越大,因此,喷煤所取代的焦炭越多,经济效益越好。
完整的高炉喷煤工艺流程应包括原煤储运系统、制粉系统、煤粉输送系统、喷吹系统、供气系统和煤粉计量系统,最新设计的高炉喷煤系统还包括整个喷煤系统的计算机控制中心。
[编辑本段]高炉喷煤的重大意义高炉喷吹煤粉是炼铁系统结构优化的中心环节,是国内外高炉炼铁技术发展的大趋势,也是我国钢铁工业发展的三大重要技术之一,所以,我们应当努力提高喷煤比。
高炉喷煤的意义(1)减少炼焦过程对环境的污染。
高炉喷煤代替焦炭,就减少了高炉炼铁对焦炭的需求。
减少焦炭的需求,就可以使焦炉少生产焦炭。
焦炉少生产焦炭或少建焦炉,就可以减少对环境的污染。
(2)缓解我国主焦煤的短缺,优化炼铁系统用能结构。
炼焦配煤一般需要配50%以上的主焦煤,以满足高炉炼铁对焦炭质量方面的要求。
喷吹煤粉的煤种广泛,可以不使用主焦煤。
这就缓解了我国主焦煤的短缺,同时也降低了炼铁系统的购煤成本。
(3)高炉喷煤可以实现结构节能。
2006年我国重点钢铁企业焦化工序能耗为123.41kgce/t,喷煤的制粉和喷吹所需的能耗在20~35kgce/t。
高炉每喷吹1t煤粉,就可以产生炼铁系统用能结构节约lOOkgce/t的效果。
(4)高炉喷煤可降低炼铁系统的投资。
据统计,国外建设喷煤车间的投资是焦化厂单位投资的25%~30%,转换为冶金焦的单位投资是30%~40%;中国喷煤车间的单位投资是焦化厂建设单位投资的12%~16%,为冶金焦部分投资的15%~20%。
所以,在新建和扩容高炉时,喷煤车间必须同步实施,这样会有较大的经济效益。
(5)煤粉代替焦炭会有巨大的经济效益。
喷煤工艺流程图及概述
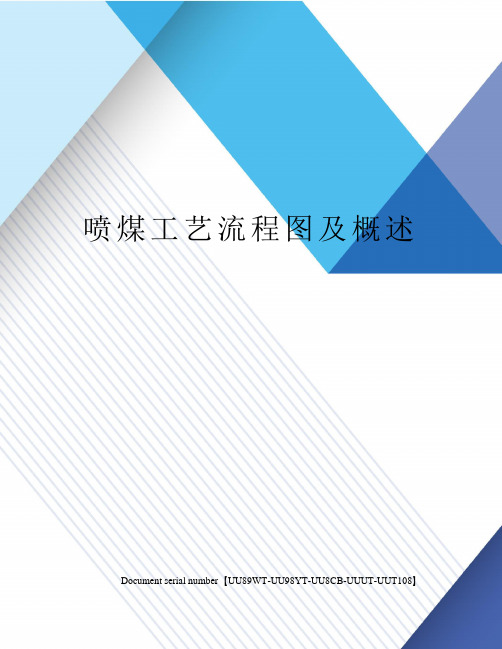
喷煤工艺流程图及概述 Document serial number【UU89WT-UU98YT-UU8CB-UUUT-UUT108】炼铁一厂喷煤系统工艺流程图及概述山西中阳钢铁有限公司一体系升级改造项目高炉工程制粉喷吹系统,制粉、收粉系统全部利旧;干燥系统除热风炉废气管道需改造外,其他设施利旧;对喷吹系统进行局部改造。
制粉喷吹系统主要工艺现状:制粉喷吹站厂房为混凝土结构,全封闭。
煤粉制备系统采用单系列全负压制粉工艺,喷吹系统采用1个煤粉仓、下部六罐并列(每三罐分别对应405m3高炉)。
整个系统即1套干燥气发生炉系统、1套磨煤机制粉系统、1套煤粉收集系统、2套喷吹系统(一个煤粉仓,下部六罐并列)。
新建1780m3高炉投产后,2座405m3高炉拟全部拆除,现有制粉喷吹站只为新1780m3高炉供给煤粉。
新建1780m3高炉主管及分配器设置方案为:2根喷吹主管(一个主管对应一个分配器)及2个炉前分配器(1#分配器对应奇数风口,2#分配器对应偶数风口)的直接喷吹工艺。
喷吹系统与原系统的交接界面为:喷吹罐输煤阀后的喷吹主管起点。
喷吹煤粉主管及分配器平台为本工程设计范围。
1、工艺条件及要求1)原煤条件单一煤种和混合煤均可喷吹,通常使用三种煤组成混合煤,安全措施上按强爆炸性烟煤设计。
原煤的理化指标见表-1。
表1 原煤的理化指标表2)煤粉条件煤粉质量要求见表-2。
表2 煤粉质量要求表3)制粉喷吹能力按高炉正常日产铁水量4005吨,正常喷吹能力为160kg/t铁计,高炉正常喷吹所需煤粉量为h;按高炉正常日产铁水量4005吨,喷吹能力为200kg/t铁计,高炉最大喷吹所需煤粉量为h。
2、主要工艺参数制粉喷吹系统主要工艺参数见表-3。
表3 喷吹系统工艺参数3、主要工艺流程分配器及煤粉主管流程图见附图。
喷煤工艺流程:该系统采用磨辊中速磨制粉,双管路加分配器浓相输粉的新工艺流程。
高炉喷吹煤粉工艺系统主要由:原煤贮运、煤粉制备、煤粉输送、煤粉喷吹、干燥气体制备和供气动力系统组成。
喷煤工艺[1]
![喷煤工艺[1]](https://img.taocdn.com/s3/m/2eca8576da38376bae1fae61.png)
PPT文档演模板
喷煤工艺[1]
高炉喷吹的煤配成混合煤的好处
➢磨煤机台时产量趋近理想的经济产量; ➢提高煤粉在风口前的燃烧率,扩大喷吹量; ➢达到较高的置换比,和高炉生产技术经济指标; ➢煤的价格经济合理; ➢综合利用各种煤资源,供煤、运输合理而有保证。
PPT文档演模板
喷煤工艺[1]
三、干燥气系统
工作原理:原煤从中心给煤管喂入,落到磨碗(或磨盘)上,磨碗 (或磨盘)由电动机通过星型齿轮带动旋转,落到旋转碗或(盘)上的 煤,在离心力的作用下,甩向碗(或盘)周边,平盘式的煤则移动进入 磨槽内,三个独立的弹簧加载磨棍,按120°角相隔分布,正好位于磨 碗(或磨槽)之上。两者之间保持一定的间隔,无直接的金属接触,当 原煤通过磨辊与磨碗之间时,被研磨成粉,已磨好的煤粉继续向外移动, 最后沿磨周溢出。
给煤机
中速磨机 热 烟 气
PPT文档演模板
星形缷灰 阀
煤粉振动 筛
消音器 主排粉风机
煤粉仓
喷吹罐
喷煤工艺[1]
制粉系统主要设备参数
PPT文档演模板
设备名称 中速磨机
给煤机 布袋除尘器
主排粉风机
参数名称 产量 磨碗转速 电机功率 电压 给煤能力 中心距 计量精度 过滤面积 最大处理风量 布袋长度 耐压 工作温度 全压 流量 转速 电机电压 电机功率
煤 种 褐煤 长焰煤 不粘煤 贫煤 无烟煤 着火点℃ 267~300 275~330 320~350 360~390 365~420
煤粉具有流动性 新磨碎的煤粉能够吸附气体,在煤粒表面形成气膜,它使煤粉
颗粒之间的摩擦阻力变得较小,另外煤粒均为带电体,都是同性电 荷,同性电荷具有相斥作用,所以煤粒具有较好的流动性。
高炉制粉喷煤技术的研究与应用

高炉制粉喷煤技术的研究与应用作者:王维乔1. 技术研发历程高炉喷吹煤粉可以降低焦炭消耗,减少炼焦污染,调节炉况,促进高炉稳定顺行,强化高炉冶炼。
首钢作为我国高炉喷煤技术的开创者和先行者,早在196 3年,就进行了系统的研究与试验,并于1964年在国内率先将其在高炉上进行工业化试验。
1966年,首钢在全公司的高炉上进行推广应用,当时的年平均喷煤量达159kg/tHM,最高月平均喷煤量达到279kg/tHM,创造了当时的世界纪录。
1994年,在首钢1726-2536m3四座高炉上应用,采用集中制粉,间接喷吹,串联罐多管路喷煤。
2000年,首钢进行重大技术改进,采用中速磨煤机制粉,布袋一级收粉,双系列串联罐直接喷吹,在首钢两座(1780m3、2536m3)高炉上应用,达到国际先进水平。
2004年,首钢国际工程公司设计的湘钢1800m3高炉,采用中速磨制粉,并列罐间接喷吹。
2007年,首钢国际工程公司设计的迁钢2号2650m3高炉,采用并列罐直接喷吹,并实现全自动喷煤操作。
2009年,首钢国际工程公司设计的京唐1号5500m3高炉,采用并列罐直接喷吹,全自动喷煤操作,并实现浓相输送。
2010年,首钢国际工程公司设计的迁钢3号4000m3高炉,采用并列罐直接喷吹,全自动喷煤。
2010年,首钢国际工程公司设计的京唐2号5500m3高炉,采用并列罐直接喷吹,浓相输送,全自动喷煤。
经过几十年的发展,首钢国际工程公司不断完善和优化设计,掌握了从原煤料场到煤粉制备和喷吹的全套高炉喷煤工艺设计。
近年来,首钢国际工程公司还参与编制了国家标准GB 50607-2010《高炉喷吹煤粉工程设计规范》。
2. 高炉喷吹煤粉技术的主要技术特点2.1 长距离直接喷吹,紧凑型布局由首钢国际工程公司设计的首钢2号、3号高炉喷煤工程,完全采用国产化技术和设备,采用紧凑型短流程工艺,实现了煤粉长距离直接喷吹。
2号高炉喷煤总管长度达到452m,已被列入第九批《中国企业新记录》。
高炉喷煤工艺流程毕业论文

我国的钢铁企业为了节约生产成本,探索了多种节能降耗的手段,而高炉喷煤是钢铁企业降焦比增效益的有效途径。
我国对高炉喷煤技术的开发和应用尽管较早,但从近儿年的发展悄况来看,国家产业政策对高能源消耗进行了限制,高炉要想在激烈的竞争环境中取得生存和发展,只有努力寻求技术创新和进步,着力降低能耗,提高经济效益,减少和控制污染。
关键词:高炉喷煤;工艺流程图;磨煤机;干燥炉RiJ s第一章绪论第二章高炉喷煤工艺介绍第三章磨煤机. 第四章干燥炉前言高炉喷煤技术始于1840年$・M. Banks关于喷吹焦炭和无烟煤的设想;世界最早的工业应用即是根据这一设想于1840-1845年间在法国博洛涅附近的马恩省炼铁厂实现的。
高炉喷吹煤粉是从高炉风口向炉内直接喷吹磨细了的无烟煤粉或烟煤粉或这两者的混合煤粉,以替代焦炭起提供热量和还原剂的作用,从而降低焦比,降低生铁成本,它是现代高炉冶炼的一项重大技术革命。
由此背景引出本次毕业设计•的题U高炉喷煤工艺流程。
课题主要阐述了高炉喷煤工艺流程的粉吹和喷吹工艺全过程。
第一章绪论1.1课题研究的意义U前高炉喷煤对现代高炉炼铁技术来说是具有革命性的重大措施。
它是高炉炼铁能否与其他炼铁方法竞争,继续生存和发展的关键技术,其意义具体表现:(1)以价格低廉的煤粉部分替代价格昂贵而日趋匮乏的冶金焦炭,使高炉炼铁焦比降低,生铁成本下降;(2)喷煤是调剂炉况热制度的有效手段;喷煤可改善高炉炉缸工作状态, 使高炉稳定顺行:1.2高炉喷煤技术的现状及发展趋势高炉喷煤杲大幅度降低然比和生铁成本的重大技术描施,是推动炼铁系统技术进步的核心力量。
自80年代初高炉喷煤技术在世界范圉内广泛开发应用以来, 世界各国钢铁厂的高炉喷煤量不断地提高。
其中西欧、日本等国发展尤其迅猛, 在1993年左右就有部分高炉的喷煤比达到200kg/t铁,在世界处于领先地位,U前部分高炉年均喷煤比已达160〜200kg/t铁,最高月平均喷煤比达到210〜250kg/t铁。
《综采工作面喷雾降尘理论及应用研究》范文
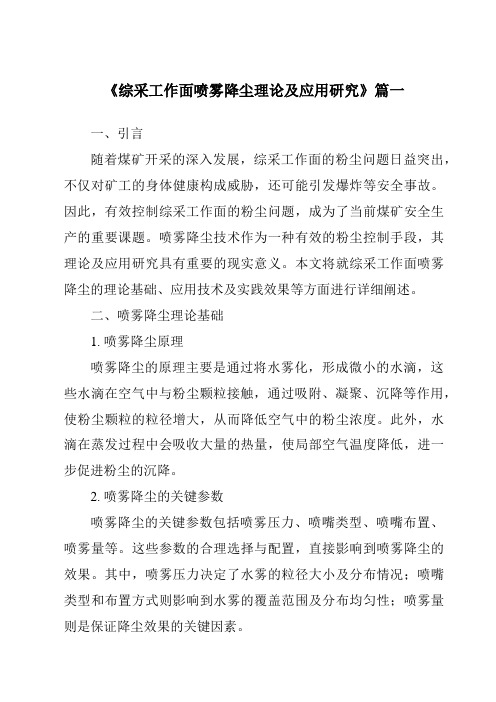
《综采工作面喷雾降尘理论及应用研究》篇一一、引言随着煤矿开采的深入发展,综采工作面的粉尘问题日益突出,不仅对矿工的身体健康构成威胁,还可能引发爆炸等安全事故。
因此,有效控制综采工作面的粉尘问题,成为了当前煤矿安全生产的重要课题。
喷雾降尘技术作为一种有效的粉尘控制手段,其理论及应用研究具有重要的现实意义。
本文将就综采工作面喷雾降尘的理论基础、应用技术及实践效果等方面进行详细阐述。
二、喷雾降尘理论基础1. 喷雾降尘原理喷雾降尘的原理主要是通过将水雾化,形成微小的水滴,这些水滴在空气中与粉尘颗粒接触,通过吸附、凝聚、沉降等作用,使粉尘颗粒的粒径增大,从而降低空气中的粉尘浓度。
此外,水滴在蒸发过程中会吸收大量的热量,使局部空气温度降低,进一步促进粉尘的沉降。
2. 喷雾降尘的关键参数喷雾降尘的关键参数包括喷雾压力、喷嘴类型、喷嘴布置、喷雾量等。
这些参数的合理选择与配置,直接影响到喷雾降尘的效果。
其中,喷雾压力决定了水雾的粒径大小及分布情况;喷嘴类型和布置方式则影响到水雾的覆盖范围及分布均匀性;喷雾量则是保证降尘效果的关键因素。
三、喷雾降尘应用技术1. 喷雾降尘系统设计喷雾降尘系统主要包括水源、水泵、输水管路、喷嘴等部分。
在设计时,需要根据综采工作面的实际情况,确定合适的水源、水泵及输水管路;同时,还需根据粉尘的来源、分布及运动规律,合理布置喷嘴,以保证水雾的覆盖范围及分布均匀性。
2. 智能控制系统为提高喷雾降尘的效果及效率,可引入智能控制系统。
通过安装粉尘浓度传感器、温度传感器等设备,实时监测综采工作面的粉尘浓度及环境温度;根据监测数据,自动调节喷雾系统的运行参数,实现自动化的喷雾降尘。
四、实践应用及效果1. 实践应用在综采工作面,通过安装喷雾降尘系统,实现了对粉尘的有效控制。
在实际应用中,根据工作面的实际情况,合理配置喷雾系统的各项参数,如喷雾压力、喷嘴类型及布置等;同时,结合智能控制系统,实现了自动化的喷雾降尘。
- 1、下载文档前请自行甄别文档内容的完整性,平台不提供额外的编辑、内容补充、找答案等附加服务。
- 2、"仅部分预览"的文档,不可在线预览部分如存在完整性等问题,可反馈申请退款(可完整预览的文档不适用该条件!)。
- 3、如文档侵犯您的权益,请联系客服反馈,我们会尽快为您处理(人工客服工作时间:9:00-18:30)。
喷煤工艺流程的研究与探索凯(喷煤车间)摘要:概述推广高炉喷煤的必要性,结合实际生产需要,探索现代喷煤工艺的发展前景要求:提高安全生产,杜绝设备隐患关键词:高炉、原煤、制粉、喷吹、安全目录一概述(一)前言............................ (1)(二)简述喷煤的的出现和发展 (1)(三)高炉喷煤的定义 (1)(四)高炉喷煤的重要意义 (1)(五)高炉喷煤图 (2)二高炉用煤(一)煤的物理性质 (3)(二)煤的工艺性能 (4)(三)煤的性能要求 (6)三煤粉的制备(一)制粉系统工艺流程 (6)(二)制粉设备组成 (7)(三)制粉操作规程 (10)(四)制粉系统故障及处理 (12)(五)设备维护规程 (17)四煤粉的喷吹(一)计算 (17)(二)高炉喷吹设施的布置方式 (18)(三)高炉喷吹罐的出粉方式 (18)(四)高炉喷吹主要设备 (19)(五)喷煤操作 (19)(六)喷煤系统的故障及处理 (20)五高炉喷煤的防火防爆安全措施(一)煤粉爆炸的条件 (21)(二)高炉喷吹烟煤的安全措施 (22)(三)高炉喷煤系统气氛的懒化 (23)(四)受压容器的安全管理 (23)(五)防止明火和静电 (23)六结语一概述(一)前言随着高炉炼铁规模不断扩大和对生铁需求量的日益增加,高炉喷煤辅助燃料是现代高炉炼铁生产广泛采用的新技术,同时它还是现代高炉路况调节所不可缺少的重要手段之一。
论文主要介绍煤的一般特性、煤粉的制备喷吹和设备等容。
注重新的喷煤工艺和各系统的设备点检等容的介绍。
理论联系实际,使其容具有一定的实用性。
(二)高炉喷煤的出现和发展自20世纪60年代初喷吹技术在法国获得了成功以后,美国、前联主要喷吹天然气,西欧、日本则自20世纪80年代初由喷吹重油转为喷吹煤粉。
我国是开发喷煤技术较早的国家,自20世纪60年代初开始试验,至今已有50多年历史,特别是近十几年来,高炉喷煤技术的到了广泛的应用和发展,从而促进了我国的钢铁工业的迅猛发展,减少了炼铁生产受炼焦碳资源、投资、环保等多方面的限制和影响。
(三)什么是高炉喷煤高炉喷煤是指将磨细的无烟煤粉、烟煤煤粉或两者的混合物。
利用高压气体从高炉风口向高炉部输送煤粉,从而达到提高炉温,降低成本的作用。
(四)高炉喷煤的重要意义1.41用煤粉代替焦炭,降低成本及煤比1)解决焦炭短缺问题焦炭资源的短缺;环境保护限制(炼焦生产环境负荷大,污染严重;焦炉寿命25-30年,欧美焦炉多在70年代投产,已到寿命;环境意识增强,限制新焦炉投产)2)降低生产成焦炭昂贵,焦炭价高,来源少;煤资源丰富,来源广,价格低;改善还原可以降低焦比3)综合能耗降低1.42有利于采用高风温和富氧鼓风技术1)解决高风温产生的问题;高炉不能接受高风温:(理论燃烧温度过高,造成煤气体积增大,实际流速过高,增加炉压差;提高燃烧焦点温度,SiO2还原产生的大量SiO,气态的SiO 在高炉中上部氧化为SiO2堵塞炉料的空隙,恶化料柱透气性,增加炉压差)喷煤的作用:喷煤降低理论燃烧温度,降低压差。
降低燃烧焦点温度,减少SiO2还原,产生的SiO减少。
2)解决富氧鼓风产生的问题理论燃烧温度过高;燃烧焦点过高;煤气量降低,炉身部炉料加热变差喷煤的作用:降低理论燃烧温度;降低燃烧焦点温度;增加炉缸煤气量1.43有利于调节炉况,改善高炉冶炼过程1)增加调节手段,调节炉温较快调节炉况手段:风温;通常不适用风量;通常不适用焦炭负荷;滞后鼓风湿分;灵敏,但不利于降低能耗喷煤调节路况:较快2)改善高炉的还原过程煤气含H2量增加,有利于降低直接还原,有利于降低焦比。
增加炉缸煤气量,改善还原。
(五)高炉喷煤车间简易图二高炉用煤(一)煤的物理性能:为了获得更好的经济技术指标,保证安全顺利的生产,应根据煤的物理性质对它进行检测。
煤的物理性质有孔隙率、可磨性、煤的比表面积、黏结性、结焦性等。
2.11煤的孔隙率它反映煤的反应性能和强度的性质。
孔隙率打的煤其表面积大,反应性能好,但强度较小。
这种美德可磨性和燃烧性好,炉未燃煤气化反应好。
有利于高炉稳定顺利和提高煤焦置换比。
煤的孔隙率也是决定煤层瓦斯含量的主要因素之一,是计算煤层中游离瓦斯含量的重要依据。
2.12煤的可磨性煤的可磨性主要是指把煤磨成粉的难易程度。
它主要与没的变质程度有关,不同型号的煤具有不同的可磨性。
一般来说,焦煤、肥煤易磨,即能磨细;无烟煤、褐煤难磨,即不宜磨细。
此外煤的可磨性还随着没种的水分和灰分的增加而减少。
同一种煤,水分和灰分越高,其可磨性就越差2.13煤的比表面积煤的比表面积是指单位重量的煤粒的表面积的总和,成为这种煤在该粒度围的比表面积,单位mm2/g。
煤的比表面积是煤的重要性质。
对研究煤的破碎、着火、燃烧反应等性能均有重要意义。
煤粉比表面积的测定是用透气式比表面积测定仪测定的,测量原理是根据气流通过一定厚度的煤粉层受到阻力而产生压力降来测定的。
2.14煤的黏结性把煤碎的煤隔绝空气并逐渐加热到200-500度时,煤中会析出一部分气体并形成粘稠状胶质,再继续加热粘稠状胶质继续分解,一部分不能分解为气体,其余部分逐渐固化将碳粒结合在一起成为焦块,这种结合牢固程度叫黏结性。
用黏结指数CR-1表示,它是评价炼焦用煤的主要指标。
2.15煤的结焦性煤的结焦性是指煤在工业焦炉或模拟工业焦炉的炼焦条件下结成一定块度和足够强度焦炭的能力,人们把具有这种性能的煤叫做炼焦煤。
它们有气煤、肥煤、焦煤和瘦煤。
因为炼焦煤必须具有黏结性,即在干流过程中能软熔成胶质体并固化粘结成块状交谈的能力,所以,炼焦煤必然是粘结性煤。
(二)煤的工艺性能煤粉是由1-300um各种不同的尺寸、形状的微粒按一定的分布规律组成的颗粒群。
它的工艺性能的好坏直接影响到高炉喷吹,高炉喷吹用煤的工艺性能有:着火点温度、煤灰融入性、流动性、粒度、爆炸性、煤对CO2的反应性2.21煤的着火温度煤的着火温度是指在氧化剂(空气、氧气)和煤共存的条件下,把煤加热到开始燃烧的温度叫煤的着火温度,也叫煤的燃点。
各种煤的的着火围:2.22煤灰的熔融性煤灰熔融性是指在规定条件下,随加热温度变化,煤的灰分的变形、软化和流动特征的物理状态。
煤的灰分的主要成分是:SiO2、Al2O3、CaO、MgO、Fe2O3D 等,它没有固定的熔点,当其加热到一定的温度时开始局部融化,随着温度升高,融化部分增加,到某一温度时全部融化。
这种逐渐融化过程,使煤灰试样产生变形、软化和流动。
所以人们就以与这三态相应的温度来表征煤的熔融性。
2.23煤粉的流动性煤粉具较好的流动性,是因为新磨碎的煤粉能够吸附气体(如空气),使气体在煤粒表面形成气膜,使煤粉颗粒之间的摩擦阻力变小;另外煤粒均为带电体,且都带有电荷,同性电荷具有相斥作用,所以煤粉具有流动性。
在一定速度的载体中,煤粉能够随载体一起流动,这就是煤粉能被气力输送的原理。
但随着煤粉存放时间的延长,流动性变差,所以要求煤粉的贮存时间应小于8h.2.24煤粉的粒度煤粉的细度是煤粉颗粒群组粗细程度的反应,它对磨煤制粉的能耗和喷吹煤粉的燃烧速度以及不完全燃烧的热损失都具有决定性的意义。
此特性用筛分分析来表示。
喷吹无烟煤时粒度应小些,-200网目的应达到70%~80%:喷吹烟煤时,粒度可以大些,-200网目的达到60%~70%即可。
2.25煤粉的爆炸性煤粉的爆炸性决定着喷煤系统安全措施的采用。
可燃粉尘爆炸的必要条件有:1)可燃粉尘浓度处于爆炸爆炸上下限的爆炸空间;2)有足够的氧化剂支持;3)有足够能量的点火源点点燃粉尘;4)分散悬浮的粉尘处于定容空间。
随挥发分含量增加爆炸性增加。
一般认为:可燃基挥发分小于10%为基本无爆炸性煤;大于10%为有爆炸性煤。
而且,煤粉越细,越易于爆炸。
控制系统部适宜的含氧浓度是防止煤粉着火爆炸的关键,若系统含氧量低于一定浓度的(小于14%)就可以避免着火爆炸。
2.26煤对CO2反应性煤对CO2的反应性是指在一定的温度下,煤中的碳与CO2进行还原反应的反应能力。
反应式为:C + CO2 = CO。
或者说,煤将CO2还原成CO能力。
以被还原成CO的CO2量占参加反应的CO2总量的百分数来表示。
在一定温度下,该反应速度越大,表明煤粉的可燃性越好。
高炉喷吹反应性强的煤,不仅可以提高煤粉的燃烧率,扩大喷煤量,而且,风口区未燃烧的煤粉在高炉其他部位参加了与CO2的气化反应,减少了焦炭的气化反应,这就在某种程度上对焦炭的强度起到了保护作用,有利于提高炉料的透气性。
另外,煤的反应性也与煤的挥发分含量有关,挥发分越高的煤反应性强,如挥发分高的褐煤反应性最强,烟煤反应性较强,无烟煤反应性最小。
(三)高炉喷吹煤的性能要求高炉喷吹用煤的要求包括两方面:1)对高炉喷吹所用原煤性能要求;2)对磨制出的煤粉质量要求。
2.31对原煤的性能要求2.32对磨制煤粉的质量要求三煤粉的制备(一)制粉系统工艺流程(二)一期制粉设备制粉系统主要由干燥气系统、磨煤系统及煤粉收集等三大部分组成。
3.21一期制粉系统设备组成及参数喷煤车间一期喷煤制粉设备组成序号设备名称型号数量工艺参数1 磨煤机ZGM95G 2台台时产量33t/h入口温度≤350℃出口温度≤95℃磨机出口压力(绝对值)9.5kpa3.22制粉设备油品型号磨机减速机→→ L-CKD320#齿轮油→补油周期2个月,OB油浴润滑磨机磨辊→→ 680#工业齿轮油稀油站→→→ L-CKD320#齿轮油→补油周期2个月,OB油浴润滑液压站→→→ L-HM46#低锌抗磨液压油→油量850L,周期按质换油其他减速机→→ L-CKD150#齿轮油轴承→→→ 2#通用锂基脂(黄油)(三)制粉系统操作规程3.31启机前的准备和检查:1)检查系统各积粉点有无积粉自燃现象,磨机进出口有无积煤,如有应清除干净。
2)检查主排风机、密封风机、烟气引风机有无卡机现象。
3)检查设备各润滑点油质、油温、油量是否符合要求。
4)检查系统所有气动,电动阀门开关是否灵活。
5)检查设备及管道连接部位密封是否严密,各检查孔、防爆阀是否严密完好。
6)检查设备冷却水是否开通。
7)检查系统各仪表是否完好。
8)确定原煤仓存煤量高于下料位。
9)各减速箱保持规定油量,各传动部位润滑良好。
3.32中速磨启机操作程序:1)有主控室制粉操作工通知高压运行电工送电并确认到位后,通知中速磨工、加热炉工、风机工准备起机。
2)启动磨机稀油站、液压站。
并确认油压处于正常围。
3)启动密封风机。
并确认密封风压力、风量满足。
4)启动振动筛、卸灰阀、布袋收粉器。
并确认其运转、反吹正常。
5)启动主排粉风机,带电流稳定后逐渐开启主抽调节阀,保证系统负压大于或等于1000pa,6)启动引风机,带引风机电流稳定后开启引风机切断阀。