高炉富氧喷煤
高炉喷煤概论
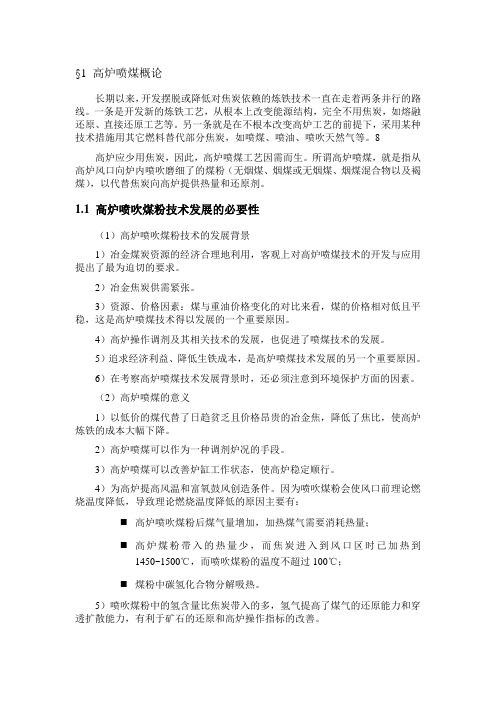
§1 高炉喷煤概论长期以来,开发摆脱或降低对焦炭依赖的炼铁技术一直在走着两条并行的路线。
一条是开发新的炼铁工艺,从根本上改变能源结构,完全不用焦炭,如熔融还原、直接还原工艺等。
另一条就是在不根本改变高炉工艺的前提下,采用某种技术措施用其它燃料替代部分焦炭,如喷煤、喷油、喷吹天然气等。
8高炉应少用焦炭,因此,高炉喷煤工艺因需而生。
所谓高炉喷煤,就是指从高炉风口向炉内喷吹磨细了的煤粉(无烟煤、烟煤或无烟煤、烟煤混合物以及褐煤),以代替焦炭向高炉提供热量和还原剂。
1.1 高炉喷吹煤粉技术发展的必要性(1)高炉喷吹煤粉技术的发展背景1)冶金煤炭资源的经济合理地利用,客观上对高炉喷煤技术的开发与应用提出了最为迫切的要求。
2)冶金焦炭供需紧张。
3)资源、价格因素:煤与重油价格变化的对比来看,煤的价格相对低且平稳,这是高炉喷煤技术得以发展的一个重要原因。
4)高炉操作调剂及其相关技术的发展,也促进了喷煤技术的发展。
5)追求经济利益、降低生铁成本,是高炉喷煤技术发展的另一个重要原因。
6)在考察高炉喷煤技术发展背景时,还必须注意到环境保护方面的因素。
(2)高炉喷煤的意义1)以低价的煤代替了日趋贫乏且价格昂贵的冶金焦,降低了焦比,使高炉炼铁的成本大幅下降。
2)高炉喷煤可以作为一种调剂炉况的手段。
3)高炉喷煤可以改善炉缸工作状态,使高炉稳定顺行。
4)为高炉提高风温和富氧鼓风创造条件。
因为喷吹煤粉会使风口前理论燃烧温度降低,导致理论燃烧温度降低的原因主要有:⏹高炉喷吹煤粉后煤气量增加,加热煤气需要消耗热量;⏹高炉煤粉带入的热量少,而焦炭进入到风口区时已加热到1450~1500℃,而喷吹煤粉的温度不超过100℃;⏹煤粉中碳氢化合物分解吸热。
5)喷吹煤粉中的氢含量比焦炭带入的多,氢气提高了煤气的还原能力和穿透扩散能力,有利于矿石的还原和高炉操作指标的改善。
6)喷吹煤粉代替了部分焦炭,不仅缓解了焦煤的供需紧张状况,也减少了对炼焦设施的投资和建设,降低了炼焦生产对环境的污染。
高炉富氧喷煤学习材料

高炉富氧喷煤学习材料1. 富氧喷煤技术简介富氧喷煤技术是高炉冶炼中一种重要的能源替代技术,通过在高炉炉缸内加入富氧气体,提高燃烧炉温和还原性能,减少燃料投入和温室气体排放。
2. 富氧喷煤技术的原理与优势富氧喷煤技术是指在高炉冶炼过程中,通过将煤粉与富氧气体混合后,在炉缸内喷入加热煤气,实现高温下的高效燃烧和脱硫脱硝的目的。
其原理基于以下几点:•炉温的升高:富氧气体中氧气含量较高,能够提供充足的燃料氧化剂,使燃烧反应快速进行,从而提高炉温。
•还原性能的提升:富氧气体中氧气含量较高,能够提供更多的还原剂,加速铁矿石还原反应,提高冶炼效率。
•炉渣质量的改善:富氧喷煤技术能够将煤气中的部分二氧化碳直接还原为一氧化碳,降低炉缸内CO2含量,减少炉渣粘结,有利于炉渣顺畅排出。
相比传统燃烧技术,富氧喷煤技术具有以下优势:•提高高炉炉温,增强冶炼能力。
•减少燃料投入,降低能耗。
•燃烧效率高,减少环境污染物排放。
•降低温室气体排放,符合环保要求。
3. 富氧喷煤技术的应用案例富氧喷煤技术在高炉冶炼领域已经被广泛应用。
以下是一些应用案例的简要介绍:3.1 案例一:某钢铁公司高炉富氧喷煤项目该钢铁公司自主研发了高炉富氧喷煤技术,通过在高炉炉缸内喷入高温富氧气体和煤粉混合物,实现了燃料的高效燃烧和冶炼过程的优化。
该技术的应用使钢铁生产能力大幅提升,炉渣质量得到改善,同时还能满足环保要求。
3.2 案例二:某煤矿高炉富氧喷煤试验项目某煤矿开展了高炉富氧喷煤试验项目,旨在提高煤矿煤炭资源利用率和环境保护能力。
试验结果表明,通过富氧喷煤技术,煤矿产能得到提升,燃烧效率大幅提高,废气排放浓度显著降低,达到了预期的经济和环境效益。
4. 富氧喷煤技术的发展趋势富氧喷煤技术作为一种重要的高炉冶炼技术,目前已经取得了显著的进展,但仍有一些问题需要解决。
今后富氧喷煤技术的发展趋势主要集中在以下几个方面:•燃烧稳定性优化:进一步优化喷煤设备和工艺参数,提高煤粉与气体的混合均匀性,增强燃烧稳定性,降低喷煤风口振动和爆炸的风险。
高炉富氧喷煤现状及提高煤比的措施(论文)

高炉富氧喷煤现状及提高煤比的措施(论文)高炉富氧喷煤现状及提高煤比的措施张维彬丛胜刚摘要:对我国高炉富氧喷煤现状进行了总结与评价,分析了存在的问题,并提出了改进意见。
分析认为,随着原燃料条件改善,我国高炉喷煤水平不断提高,并有进一步提升的空间,但幅度有限。
若要大幅度提高喷煤水平,必须采取狠抓原燃料质量、改善高炉透气性、优化高炉操作制度、提高风温、加强炉前管理等措施。
关键词:高炉喷煤煤比1、引言高炉喷煤是从高炉风口想炉内直接喷吹磨细了的无烟煤粉或煤粉或这两者的混合煤粉,以替代焦炭起提供热量和还原剂的作用,从而降低焦比,降低生铁成本,它是现代高炉冶炼的一项重大技术革命[1]。
高炉喷煤代替了较昂贵的焦炭,可以改善高炉的行程,取得了较好的经济社会效益。
但由于能源政策问题,高炉喷煤技术没有的得到更大的发展。
上世纪70年代膜,发生第二次石油危机,高炉世界性地停止喷油。
为了避免全焦操作,高炉又开始大量喷煤,尤其是西欧、日本发展很快,高炉大量喷吹煤粉已成为明显趋势[2]。
我国从1964年开始喷煤,是世界上使用喷煤技术较早的国家之一。
最早起步的企业是鞍钢、首钢。
鞍钢于1966年建成第一座煤粉车间,5座高炉同时开始喷吹无烟煤。
首钢于1966年1月3座高炉都实现了喷吹煤粉。
继鞍钢、首钢成功之后,武钢、太钢、本钢等企业都开始喷煤工业生产。
上世纪90年代以来,我国高炉喷煤技术取得了迅速发展。
到了本世纪初期,高炉喷煤技术的发展势头更加高涨。
2、我国高炉富氧喷煤现状2、1 喷吹用煤我国高炉在上世纪90年代结束了单一喷吹无烟煤的历史。
目前我国大多数采用无烟煤和烟煤混喷。
无烟煤和烟煤的配比根据各企业不同的生产情况自行确定。
2、2 煤比水平近年来,随着矿山系统提铁降硅的成功和铁前系统大规模技术改造,我国部分钢铁企业结束了使用热烧结矿的历史,高炉各项技术经济指标均有不同程度的提高。
表1[3][4][5][6]是我国部分高炉近年来的主要经济技术指标,从中可以看出我国高炉的煤比水平。
高炉大规模富氧喷煤技术改造首选膜分离制氧
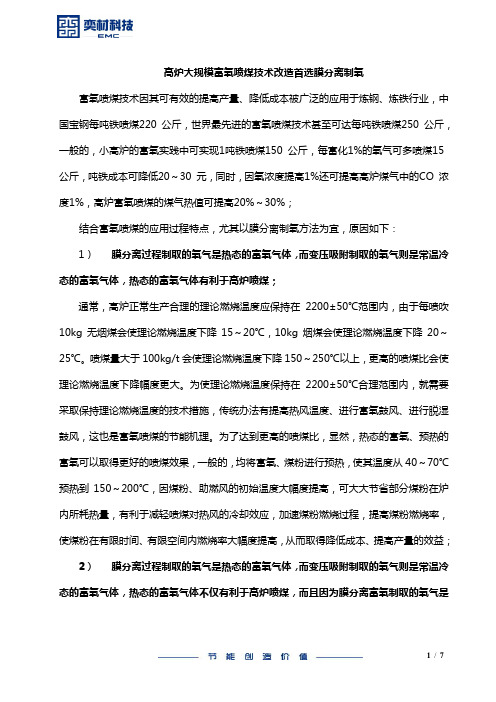
高炉大规模富氧喷煤技术改造首选膜分离制氧富氧喷煤技术因其可有效的提高产量、降低成本被广泛的应用于炼钢、炼铁行业,中国宝钢每吨铁喷煤220 公斤,世界最先进的富氧喷煤技术甚至可达每吨铁喷煤250 公斤,一般的,小高炉的富氧实践中可实现1吨铁喷煤150 公斤,每富化1%的氧气可多喷煤15 公斤,吨铁成本可降低20~30 元,同时,因氧浓度提高1%还可提高高炉煤气中的CO 浓度1%,高炉富氧喷煤的煤气热值可提高20%~30%;结合富氧喷煤的应用过程特点,尤其以膜分离制氧方法为宜,原因如下:1)膜分离过程制取的氧气是热态的富氧气体,而变压吸附制取的氧气则是常温冷态的富氧气体,热态的富氧气体有利于高炉喷煤;通常,高炉正常生产合理的理论燃烧温度应保持在2200±50℃范围内,由于每喷吹10kg无烟煤会使理论燃烧温度下降15~20℃,10kg烟煤会使理论燃烧温度下降20~25℃。
喷煤量大于100kg/t会使理论燃烧温度下降150~250℃以上,更高的喷煤比会使理论燃烧温度下降幅度更大。
为使理论燃烧温度保持在2200±50℃合理范围内,就需要采取保持理论燃烧温度的技术措施,传统办法有提高热风温度、进行富氧鼓风、进行脱湿鼓风,这也是富氧喷煤的节能机理。
为了达到更高的喷煤比,显然,热态的富氧、预热的富氧可以取得更好的喷煤效果,一般的,均将富氧、煤粉进行预热,使其温度从40~70℃预热到150~200℃,因煤粉、助燃风的初始温度大幅度提高,可大大节省部分煤粉在炉内所耗热量,有利于减轻喷煤对热风的冷却效应,加速煤粉燃烧过程,提高煤粉燃烧率,使煤粉在有限时间、有限空间内燃烧率大幅度提高,从而取得降低成本、提高产量的效益;2)膜分离过程制取的氧气是热态的富氧气体,而变压吸附制取的氧气则是常温冷态的富氧气体,热态的富氧气体不仅有利于高炉喷煤,而且因为膜分离富氧制取的氧气是热态的富氧,有效的回收了动力设备的压缩能,因此,其制氧能量消耗远低于变压吸附方法,可大幅节约运行成本:膜分离技术制氧时:鼓风机提供约2KPa的低压空气作为原料空气进入膜分离器,所作的压缩功很少,主要以真空泵做功抽取富氧,达到2倍的分离压力比以获得纯度约27%的富氧空气,也因为真空泵抽取富氧时2倍的压缩比所压缩的是富氧,因此,所做的压缩功变成了富氧的温升(约100℃),因此,回收了这部分压缩能源,制氧电力消耗低的多;变压吸附技术制氧时:鼓风机提供约39KPa的低压空气作为原料空气进入变压吸附系统的分子筛床层,因分子筛对吸附温度有严格的要求,超过35℃将大幅降低分子筛的吸附容量,进而降低产氧量,因此,鼓风机压缩的空气(约75℃)应先经水冷换热器冷却至常温(约25℃)后进入床层,也因此,鼓风机的压缩能不仅不能回收,反而要消耗大量的冷却水去冷却压缩气体形成的热能;当经过冷却的原料空气进入分子筛床层后,因吸附床层的分子筛吸附氮气而输出为富氧,装置出口为常温的富氧气体,当分子筛吸附饱和后,以真空泵做功抽取床层中的富氮气体并向大气排放从而使床层内分子筛彻底解吸,恢复吸附性能,也因此,该真空泵尽管抽至约-60KPa所做的功无法回收因压缩产生的压缩能;以供氧纯度23%,供氧量126000m3/hr为例,如下表反映出两种技术的能源消耗:序比较项目采用膜分离工艺采用变压吸附工艺备注1 客户富氧空气量需求,m3/h 126000 126000客户富氧纯度需求23% 23%2 制氧装置流量需求,m3/h 42694.2 3740.8制氧装置氧气纯度27% 90%制氧装置折成100%氧气的供氧量,m3/h11527.4 3366.7 100%纯氧量制氧装置出口富氧温度,℃100.0 25.0需要配入的空气量,m3/h 83305.8 122259.2空气氧含量20.95% 20.95%混合后富氧气流量,m3/h 126000 126000混合后富氧气纯度23% 23%3 制氧装置鼓风机升压,Kpa 1.5~2.5 39.2制氧装置鼓风机流量,m3/h 341554 46760制氧装置鼓风机最低装机轴功率,KW398.5 623.5制氧装置真空泵升压,Kpa 50 60制氧装置真空泵抽速,m3/h 85388 65463制氧装置真空泵最低装机轴功率,KW1494.3 1036.5制氧装置最低总装机轴功率,KW 1892.8 1660.0制氧装置名义单耗,KW/m3氧气0.044 0.444 27%/90%纯度消耗制氧装置折成100%氧气单耗,KW/m30.164 0.493 100%纯氧量4 混合前制氧装置制取的富氧带入热量,KJ14790247.7 1035424.7富氧空气的定容比热容0.718KJ/kg.k 常温25℃下富氧具有的焓值,KJ 11817532.7 1035424.7 常温富氧焓值富氧因温升带入焓值,KJ 2972714.9 0.0混合前富氧带入的焓值即显热折算成KWH 825.8 0.01W.S=1J,1KWH=1000*3600J因此,两种制氧方法实际功率消耗,KW1067.0 1660.0 折算成126000m3/h的23%的富氧单耗,KW/m3@23%纯度富氧0.008 0.013年可节约电力能源,万KWH/年474.4 0.0 按年运行8000小时计折算成电力成本可节省的运行成本,万元/年284.6 0.0电费按0.6元/KWH计算以供氧纯度25%,供氧量126000m3/hr为例,如下表反映出两种技术的能源消耗:序比较项目采用膜分离工艺采用变压吸附工艺备注1 客户富氧空气量需求,m3/h 126000 126000客户富氧纯度需求25% 25%2 制氧装置流量需求,m3/h 84347.1 7390.3制氧装置氧气纯度27% 90%制氧装置折成100%氧气的供氧量,m3/h22773.7 6651.3 100%纯氧量制氧装置出口富氧温度,℃100.0 25.0需要配入的空气量,m3/h 41652.9 118609.7空气氧含量20.95% 20.95%混合后富氧气流量,m3/h 126000 126000混合后富氧气纯度25% 25%3 制氧装置鼓风机升压,Kpa 1.5~2.5 39.2制氧装置鼓风机流量,m3/h 674777 92379制氧装置鼓风机最低装机轴功率,KW787.2 1231.7制氧装置真空泵升压,Kpa 50 60制氧装置真空泵抽速,m3/h 168694 129330制氧装置真空泵最低装机轴功率,KW2952.1 2047.7制氧装置最低总装机轴功率,KW 3739.4 3279.4制氧装置名义单耗,KW/m3氧气0.044 0.444 27%/90%纯度消耗制氧装置折成100%氧气单耗,KW/m30.164 0.493 100%纯氧量4 混合前制氧装置制取的富氧带入热量,KJ29219757.6 2045595.1富氧空气的定容比热容0.718KJ/kg.k 常温25℃下富氧具有的焓值,KJ23346833.0 2045595.1 常温富氧焓值富氧因温升带入焓值,KJ 5872924.6 0.0混合前富氧带入的焓值即显热折算成KWH 1631.4 0.01W.S=1J,1KWH=1000*3600J因此,两种制氧方法实际功率消耗,KW2108.0 3279.4 折算成126000m3/h的23%的富氧单耗,KW/m30.017 0.026年可节约电力能源,万KWH/年937.1 0.0 按年运行8000小时计折算成电力成本可节省的运行成本,万元/年562.3 0.0电费按0.6元/KWH计算3)辅助能源、冷却水消耗低:以供氧纯度23%,供氧量126000m3/hr为例,因为膜分离所需要配入的空气量为83305.8 m3/h,少于变压吸附所需配入的空气量122259.2 m3/h,因此,所需的这部分配入空气的能源消耗也较变压吸附低;此外,变压吸附因为需要将鼓风机升压后的气体冷却至常温,因此,要消耗大量的冷却水去冷却气体,还有,为提高真空泵的真空度,通常还需要消耗软化水加入真空泵去提高真空度,而膜分离设备则无需消耗这些冷却水,更无需消耗软化水;4)可靠性高:膜分离过程是静态分离,设备极其简单、故障率低,可靠性非常高;而变压吸附制氧过程是动态分离,无论双塔还是多塔,需要很多阀门进行切换,可靠性与膜分离相比要差的多;5)安全,即开即用,产氧迅速:膜分离设备与变压吸附制氧过程均是纯物理过程制氧,无相变等,安全性好,两种设备的启停都可实现即开即用,尤其膜分离设备,泵开即开,泵停即停,无需复杂的控制手段,开机5分钟即可达到供氧纯度,变压吸附过程则需大约40分钟的周期才能产生符合要求的氧气;6)设备供货周期短:膜分离设备为模块化拼装设备,设备供货周期短,无需复杂设计,以供氧纯度23%,供氧量126000m3/hr为例,一般交货周期为2~3个月,而变压吸附则至少需要4个月的交付周期;7)占地小、可模块化扩产:膜分离设备为模块化拼装设备,可跟随客户安装场地任意摆放,无需特定的安装位置要求,占地面积较变压吸附小的多的多,并且,可随意增加模块扩展产量,而无需担心变更原系统;综上述,采用膜分离系统进行高炉富氧喷煤是首选的技术方案。
关于高炉富氧喷煤技术问题的探讨

关于高炉富氧喷煤技术问题的探讨.52一鹃首钢科技1996拒1o4关于高炉富氧喷煤技术问题的探讨设计院张福明丁Ff,钙———___一k文蕾文章简介了高炉煤粉燃烧过程和燃烧机理.探讨了提高煤粉燃烧率及喷煤量的一系列技术问题.分析认为,煤粉在风I:2I区的燃烧是一复杂的物理化学反应过程,其在风口匾旋区内的燃烧率一般只有70~80.未燃烧煤粉对高炉颇行的破坏作用不容忽视.关■两高炉,喷煤.燃烧效率.富氧鼓风,(或称半焦)与氧化性气体进行燃烧的多相前言反应,该反应占煤粉燃烧全过程50以上的时间(图l,图2).发展高炉富氧喷煤技术是我国九五一期间钢铁工业结构优化的重点.高炉喷煤已不仅仅是一个以煤代焦,降低能耗的技术问题,它关系到整个钢铁工业主流程的结构优化,具有深远的战略意义.目前,高炉炼铁技术正面临着直接还原,熔融还原等非高炉炼铁技术的挑战,实现富氧大喷煤是其最终出路.富氧喷煤技术的关键是提高煤粉燃烧率,这是实现高炉大喷煤(煤比200ks/t以上)的限制性环节.本文就提高煤粉燃烧率及喷煤量的一系列技术问题进行了探讨.一,煤粉燃烧过程和燃烧机理煤粉在由喷枪进人直吹管,风口,回旋区的过程中,快速进行着热量质量和动量的传输以及一系列物理化学反应.研究表明,煤粉由喷枪进人直吹管后,首先被热风快速加热(煤粉温度一般为5O~80℃,热风温度1000~1250=C),预热时间一般只有lores左右,随后进行脱气和快速热分解(即煤的热分解和挥发分的二次热分解),然后着火,挥发物进行燃烧反应,最后是残炭囤1煤粉燃烧过程和机理示意图2煤粉燃烧时间和温度关于煤粉的燃烧过程和机理,近年来又取得了一些薪的研究成果:1.煤粉在预热阶段,辐射传热是其主要的传热过程.在此阶段,粒度7J,p.m的煤粉的加热速率为10~10."Cts.煤粉在直吹管内的传热和运动状态对脱气和热分解非常重要c1).首铜科技?53?2.高速加热条件下,煤粉的脱气和快速热分解几乎同时进行,燃烧与气化的第一步受煤粉热分解过程的制约(2).3.煤种对快速热分解及燃烧气化过程有决定性影响.烟煤的热分解及燃烧气化速度快于无烟煤,但热分解后形成大量冷凝物和烟碳I气氛对于高速加热快速热分解影响较小,而对其后的多相燃烧气化反应影响较大【3).4.残炭的燃烧气化为扩散反应.燃烧动力学研究表明,在高炉生产条件下,其反应速率主要受氧向残炭表面传质速度的限制,残炭燃尽所需时间取决于燃烧区的温度气相中的氧浓度,煤粉粒度及其化学性质在粒度,温度相同的条件下,煤粉燃烧速度随气相中氧浓度成正比地增加(4).上述关于煤粉燃烧过程和机理的研究,育助于采取有效措施,提高煤粉燃烧率和喷煤量.二,煤粉燃烧率和未燃煤粉文献[4]认为,喷人的煤粉在回旋区内未能完全燃烧,煤粉燃烧率最高只有70~80%(图8),因而残炭或半焦的最终气化是在回旋区以外进行的.lO080§60v402O■鞍锕9号高炉b首铜l号高炉_.0距0风0口艘篱{¨图8风口区煤粉燃烧率变化规律有关专家将煤粉燃烧率定义为.=;Ⅷ.式中1——煤粉燃烧率IA.——煤粉燃烧前的灰分(%)IA——煤粉部分燃烧后的灰分().理论和实测结果都表明,煤粉在风口回旋区不可能100燃烧,必然有一部分未燃煤粉存在.未燃煤粉在高炉内的行为主要是与COi,HO等氧化性气体发生气化反应I参与铁殛非铁元素的直接还原和生铁渗碳等反应,并有少量未燃煤粉进人炉渣或随煤气逸出炉外.凡仃…一富氧太喷堞图4高炉喷煤时风口回冼区结构国5未燃煤粉在高炉内的沉积位孟-54?1996年第6期一般说来,高炉喷煤后风口回旋区的结构将发生变化(图4).风口回旋区内尚未燃尽的煤粉(残炭)将在煤气流的带动下沉稠在软熔带根部和炉缸死焦柱内(图5).由此可知,如果未燃煤粉大量增加,则势必会造成焦窗堵塞,炉缸中心堆积,料柱透气性和透液性变差.日本和国内一些高炉,在喷煤虽提高以后出现了边缘气流过分发展, 炉墙热负荷增加的现象,就可能是未燃煤粉过多所致.研究表明,未燃煤粉活性较高,在高炉内比焦炭更易于与二氧化碳发生气化反应(图6).从这个意义上讲,部分柬燃煤粉吸附在焦炭表面,可优先与COt发生气化反应,从而保护焦炭,减少焦炭的熔损.一l.U圈8焦炭和束燃焯将的气化牟目前高炉能接受的最大柬燃煤粉量尚不清楚,但可做如下推测t在高炉条件下,碳素溶解反应温度区间为6D0~1200X],目前我国焦炭反直性约为30%,如果发生碳素溶解反应的焦炭有7O由未燃煤粉代替,高炉喷煤时焦比为4ookg/t,则高炉可接受的未燃煤粉量为400x30%X70%=84kg/t.1966年,首钢1号高炉在大喷煤条件下煤粉利用率高达97%以上,但这并不说明未燃煤粉量无论多大都可保证有较高的煤粉利用率,因为该高炉较高的煤粉利用率是在风温1050~1150X],富氧率2~4%,理论燃烧温度]>2050X]风口前煤粉燃烧率达70~80%的条件下获得的.笔者认为,片面强调未燃煤粉对焦炭的保护作用,甚至想利用高反应性未燃煤粉保护焦炭,从而降低焦比,提高喷煤量的观点是值得商榷的.因为高炉焦炭在下降过程中,其粒度和理化性能将发生变化,尤其在块状带中下部,焦炭和CO:气体发生碳素溶解反应(c焦+CO:=2C0),使焦炭粒度变小,强度变差.在此区域内保护焦炭,减少焦炭的碳素溶解损失,虽然会使焦炭在软熔带,滴落带,风口带以及死焦柱区具有适宜的粒度和较高的强度,改善料柱的透气性和透液性,从而有利于高炉_页行,但问题是未燃煤粉能否随煤气流穿透软熔带到达块状蒂以及在块状带内能否有效地保护焦炭,目前尚无定论.而且未燃煤粉过多,也势必给高炉操作带来困难,并降低煤粉利用率.因此,提高风口前煤粉燃烧率才是提高喷煤量的最有效的途径.三,提高煤粉燃烧率的途径1.提高鼓风舍氯量煤粉在高炉风口前的燃烧主要受氧的扩散传质限制,因此,提高煤粉燃烧区气相中的氧浓度可以促进煤粉燃烧.有关专家证实,热风温度600~1100℃时,煤粉燃烧率几乎与风温成正比,将鼓风含氧量从21%增至25%,效果比风温从1000~(2提高到1IO0~C 约好4倍(6].鼓风含氧量与煤粉燃烧率的关系见图7,风温与煤粉燃烧率的关系见图8(6].从图7,图8可以看出,增加鼓风含氧量比提高风温对煤粉燃烧率的影响更大.图7鼓风含氧率与煤耠燃烧率的关系蛋一首钢科技?56?目前宦氧鼓风已成为提高煤粉燃烧率祀喷煤量的有效措施.卢森堡P.W公司曾根据欧洲高炉的喷煤实践,对喷煤量和富氧率提出了这样的定性关系z煤比<120kg/t时,不必富氧,煤比在120~160kg/t时,需鼓风富氧2~3,煤比>180k窟/t对,除鼓风富氧外还可采用氧煤枪.国内外一些高炉鼓风富氧与喷煤量的关系见表l,喷煤量与富氧率的关系见图9国内外一些高炉鼓风富氧与喷煤量的关系表1炉窖i时间l堞比富氧室(m)}(年.月)(kE,t)(弼)蔓国剁铣公司斯肯索昔厂维多利亚女王号高炉I5341992144.2T.32 荷兰霍戈文公司戈莫伊登厂6号高炉2,q2T19驰1774.q德国普森公司施韦尔根厂i号高炉43372203.24美国锅铁盐司盖瑞厂l3号高炉2958293.56~T日丰NKK盐司福山厂4号高炉42B91994.102193鞍钢3号高炉8311995.8~112033.24首钢原l号高炉5T91966225:2.1图9喷煤量与富氧率的关系喷煤量与富氧率的关系可用风口前氧过剩系数(EXO)进行定量分析.假定煤粉中可燃成分碳氢完全燃烧.生成co和HO,则可导EXO的表达式:x.=器:——∑(=!!:力+)x亚2…2.4]/n整理得:EX0式中Vb——入炉风量(m./min),f一鼓风湿度(),w——鼓风含氧鸯()Ip——喷煤量(kg/h),0——煤扮中碳含量(),H,——煤粉中氢含量()}n——送风风口数目(个)In——喷煤风口数目(个)根据菖钢高炉富氧喷煤实践,当EXO>1.15对,煤粉在风口前的燃烧率可达7O% 以上.文献C73研究发现,EXO同煤粉置换比也有密切关系(圈l∞.从中可看出,EXO越高,置换比电越高,大喷煤时颓提高鼓风含氧量以保证有较高的EXO(≥1.n5),从而获得较高的煤份燃烧率(>80)和置换561996年第5期比(>0.8).图10置换比与氧过剩系数的关系2.选择适宜的煤粉粒度文献(8]指出,直径为d的固体碳燃烧时,若受气体扩散的控制,则煤粉燃烧时间与其粒径的平方有如下关系;tbBo×d,式中tb——煤粉燃烧时间(ms),B.一当气氛中氧浓度一定时为常数(ms/m),d.一煤粉粒径(m).由此可知,煤粉粒度越细,比表面积越太,则反应能力越强,燃烧时间越短,因此细粒煤粉有利于提高煤粉燃烧率.六十年代,喷吹细粒煤粉(<200目占8O以上)曾是首钢高炉太喷煤的经验之一.文献[93对不同煤种的粒径与燃烧率的关系进行了更深入的研究,认为当煤粉可燃基挥发分<20% 时,粒径越细燃烧率趟高,但当可燃基挥发分在25~40时,煤粉燃烧率并不随粒径变细而增加,而是在<200目占6O时燃烧率最高,当可燃基挥发分>40时,煤粉粒径越细,燃烧率反而下降.一般说来,高变质程度的煤种,粒度<200目的应控制在7O% 以上,中低变质程度的煤种,粒度<200目的可扩大到6O左右.因此,要综合考虑煤种,煤质,加工成本,燃烧率等因素,并通过试验选择台适的煤粉粒度.英国钢铁公司斯肯索普厂喷吹粒煤,其中粒径<2ram的占9,<74m的占10~30,平均径粒0.6mm.美国DAYY公司和德国Aachen大学曾对该厂喷吹的粒煤进行了研究,认为这是一种含有较高结晶水的褐煤,高温下会发生爆裂,而且会大幅度降低风口前理论燃烧温度,喷吹此种粒煤,需用较高的风温和鼓风富氧(富氧率7~l0)来补偿理论燃烧温度的下降.目前我国钢铁工业用氧十分紧缺(尤其是高炉用氧),所以笔者认为目前我国高炉应以喷吹粉煤为主,不宜提倡喷吹粒煤.5.提高热风温度提高热风温度可以促进煤粉的预热,脱气,热分解等反应,提高煤粉燃烧率.煤粉预热,脱气,热分解需要热量补偿,补偿温度可通过下式计算:+Q1BD0—可'式中t——喷吹煤粉时的补偿温度(℃), Q.——煤粉热分解吸收的热量(kJ/kg),Q-.——煤粉温度提高到1500~C时所需的物理热,Vb——入炉风量(m./t?h?m),c——热风在t风温时的热容(kJ/cm0?℃)煤粉燃烧动力学的研究结果表明,在高炉风口区对于提高煤粉燃烧率而言,提高风温的作用不及鼓风富氧的作用显着,但从热力学角度分析,煤粉燃烧前的预热,脱气,热分解对煤粉燃烧过程的影响也很大,而这一过程是需耍热鸯(温度)来补偿的.提供补偿热量最有效的途径就是依靠热风的物理热,这比鼓风富氧产生的化学热更易获得,其作用也更明显.综台鼓风富氧,提高风温等因素对煤粉燃烧的影响,可用风口前理论燃烧温度进行定量分析,其表达式为:.捌.首钢科技?57?旦!±!±!=VE?C'式中tr——风口前理论燃烧温度CC), Q.——人炉碳紊生成CO产生灼热量(kJ)}Q|——焦炭带人风口区的热量(kJ)l Qf——鼓风带人的物理热(kJ)}Qx——煤粉预热到1500℃对及热分解所吸收的热量(kJ)IV——炉缸煤气量(m./0}c——沪缸煤气的平均热客(kJ/m.?K)国内外经验表明,在大喷煤条件下,理论燃烧温度一般为205O~235O℃.也可按日本新日铁公司提出的经验公式进行简易计算t t=1550+0.839tb一6.033Wm一一(2.37,2.75)Wc+4.973V o式,{t——风口前理论燃烧温度(℃),t——鼓风温度(℃)1wm——鼓风湿度(g/m),wc——每立方米鼓风的喷煤量(kg/m.)IV o——每立方米鼓风富氧量(m./m).由上式可知,提高风愠和官氧星理论燃烧温度升高,提高喷煤t理论燃烧温度降低.因此,喷煤时须通过提,苗风温,富氧鼓风等措施维持合理趵埋论燃烧温度,保证高炉顺行.4.确定合理的喷艳位置理论和实践都表明,喷枪插入位置对煤粉燃烧率有重要影响(图11).据文献(1o3介绍,在喷枪出口距直吹管前端720mm时, 煤粉在直吹管内的燃烧率约为1.92~8%. 煤粉呈流殴状态由喷枪进入直吠管内,被速度为200m/s左右的热风包围,很快被吹散成"煤粉云,并快速进行预热,脱气,热分解和挥发物燃烧等一系列反应.在喷枪出口处,煤流是连续稳定的(流化不好的则在喷枪出口处呈脉动煤流),煤粉在直吹管及风口的停留时间很短(一般10ms左右).尽管煤粉在直欢管内的然烧率不超过2O,但这一过程对煤粉的预热,脱气,热分解,着火等反直非常重要.煤粉在高速热风的扰动下与热风混台良好,有利于传热和氧的传质,为煤粉在回旋区内燃烧创造了有耐条件.但喷枪距风口前端距离过长,则可能会出现直吹营和风口内壁结渣,喷袍结焦等现象,这对需适当调整喷枪位置及插桤角度, 以减少煤流对风口的磨蚀(12).在喷煤量提高时,会出现风压升高翱直吹管的微压震动,这时若将喷枪出口位置靠近风口前端,则因直嗷誉内的煤粉燃烧置减少而使炉壁侧焦炭消耗和F洚速变增细,炉壁热负荷降低,因此需确定一个高燃烧率的最佳喷枪位置,使煤粉在直吹管内彤成均匀燃烧区,减少"煤扮云在直吹管内的随机波动,使煤粉分散均匀,提高燃烧率.图11蝶粉燃烧率与喷枪位置的关系图l2最佳喷枪位置的选择日本田村建二等通过数学模型计算,得出了喷枪最佳位置与喷煤量,煤粉粒度之间58-1996年第5期的关系,并回归成下式:≤式中——喷枪距风口前端位置);d一煤粉粒度(ram),P,——煤比(kg/t).在煤比为80~l80kg/t,粒度为0.074mm时, 由上式可以得出L≤0.277~0.092m.5.喷吹混煤与填加煤粉促燃剂国内外研究结果表明,在煤粉中填加少量促燃(催化剂),如生石灰,石灰石,白云石,KMnO溶液等,对改善煤粉的燃烧性能,提高谋粉燃烧率有一定作用.这是由于煤粉燃烧过程主要受氧的扩散控制,在煤粉中填加少量含氧促燃剂,可提高燃烧区氧或氧化性物质的浓度,改善煤粉燃烧时的供氧条件,促进煤粉燃烧,从而提高煤粉燃浇率.德国蒂森公司是通过向煤粉申添加CaCOa粉来提高煤粉燃烧率的.另外,煤种对煤粉燃烧率也有较大影响.实验表明,煤的种类对煤粉的快速热分解和挥发物燃烧有决定性影响.挥发分高的煤,挥发物燃烧迅速,残嵌表面有连通裂纹和微孔,比表面积大,有利于氧的扩散和碳一氧反应的进行,因此,在相同条件下,烟煤的燃烧率高于无烟煤.但烟煤的c/H低,置换比也低于无烟煤.将烟煤和无烟煤混合喷吹,其效果优于喷吹单一煤种.一方面,在无烟煤申加人烟煤对无烟煤有助燃作用,可降低着火温度,提高燃烧率,另一方面,通过配煤可以保证有较高的置换比,而且同喷吹高挥发分的烟煤相比,萁安全性也更有保障.德国蒂森盐司认为混煤的挥发分控制在20~25%最佳,这样既可保证煤粉在风口前有较高的燃烧率,又可得到较高的置换比.6.关于氯攥舱的应用为提高煤粉在风口回旋区的燃烧率,各种结构型式的氧煤枪(氧煤燃烧器)相继涧世.其主要特点是;在世l粉燃烧区局部寓氧,增加该区域的局部氧浓度,促进氧的扩散,强化煤粉燃烧过程,从而提高煤粉燃烧率.高炉风口处的风速约180~260m/s,燃粉由喷枪出口到回旋区的停留时间很短,在高速热风的扰动下,煤流周围的氧浓度迅速发生变化.这就要求煤粉着火后,"燃粉云"周围仍能保持较高的氧浓度(要太子鼓风中的氧浓度),以发挥氧煤枪局部富氧促进煤粉燃烧的作用.如果煤粉着火后,"煤粉云"周围的氧浓度与鼓风富氧时的氧浓度相差无几,则氧煤枪富氧便失去了其实用意义.从国内外高炉喷煤实践看,煤比在150kg/t以上的高炉大多采用鼓风富氧的方式,仅在德国,英国,日本,瑞典等国家的部分高炉上试用氧煤枪,氧煤枪的应用尚不普遍.另外,氧煤枪的供氧系统较复杂,安全供氧不可忽视.因此笔者认为,当煤比在200kg/t以下时,采用鼓风富氧更为经济可行,当煤比在200k窖/t以上时,可以考虑使用新型结构的氧煤枪.但氧煤枪的结构,寿命,安全供氧等问题还有待于进一步研究. 四,结论1.高炉富氧喷煤是我国钢铁工业结构优化的重点,九五期间我国部分钢铁企业的煤比将达~fJ200kg/t,并最终实现高,炉半煤半焦操作(即煤比250kg/t,焦比250kg/t).2.进一步研究煤粉在风口回旋区的燃烧机理,以燃烧动力学和热力学的角度掌握煤粉燃烧过程的动量,热量,质量的传输机理,特别是模拟直吹管及风口回旋区条件的实验研究更具有实际意义.3.大喷煤量操作应有较高的煤粉燃烧率,这是获得较高置换比和稳定顺行的前提,不宜过分夸大未燃煤粉在高炉内的积极作用.未燃煤粉在高炉内的行为还有待于进首铜科技?59?一步研究.4.富氧,高风温是进行大喷煤量操怍时维持高炉稳定顺行重要的前提条件,可以用理论燃烧温度进行定量分析和控制.5.煤种,煤粉粒度及喷枪位置对煤粉燃烧率,置换比及喷煤量j都有重要影响.6.当煤比在200kg/t以下时,采用鼓风富氧比较经济可行,当煤比大于200kg/t时,应考虑使用新型氧煤枪.参考文献[1]丁玉龙等:高炉直吹管条件下粉煤热解前的传热舟醑,北京科技大学*,19932,P.145.[2]S.Bortzeta|:ExrimentsonPulver—i2edcoa1comh11sti011underconditi0n—sim11lati"gblastfurnaceenvjrOnmen—ts.《IroDma~"ingandSteelmaking.1983.5.P.222..[33扬天钩:煤粉高速加热条件下的快速热分解, 《北京钢铁学院.1988.3,P.279.[4]沈颐身等:氧煤燃烧器的研究与开发,钢铁静,1991.1,P.11.E52杨永宜等:进一步提高高炉喷煤量而不降低煤利用室的可行性研究.北京钢铁学院学报,1986.2,P.1.6]周渝生等:高炉氧煤强化炼铁艺的开发.《北京科技大学》,1993.3.P.387.(7]魏开明等:影响煤焦置换比因素的分析,《首钢科技》.1幽1.3,P.69.(8]D.13.SPalding:《燃烧与传质*.1969.P.208.r9]颇飞等:高炉喷吱煤粉的煤种及粒径研究, 《钢铁》,1996..P.11.[101安朝俊主编:《高炉生产——苷钢炼铁三十芷.1a983,P.351.(n]田村建二等:高炉V—多工部r微粉炭燃烧量限界吹人位置0适正化,《铁钢》,1991.6,P.775.。
浅谈高炉富氧喷煤

浅谈高炉富氧喷煤浅谈高炉富氧喷煤顾爱军王世达张文青王亚利(宣钢炼铁厂)摘要:高炉富氧喷煤是实现高炉生产稳产、高产、优质、低耗的必要手段,是高炉炼铁技术进步的重要标志。
高炉的富氧和喷煤是互为条件,互为依存的。
喷煤量不断增加,就需要有足够的氧气来促进煤粉的燃烧,以提高煤焦置换比和保证高炉顺行。
关键词:高炉富氧喷煤冶炼操作高炉富氧鼓风是指往高炉中加入工业氧,使鼓风中的氧含量超过大气中的含氧量。
高炉使用富氧鼓风可以加速碳燃烧,在燃料比不变的情况下使产量增加。
但富氧鼓风使进入高炉的风量减少,带入高炉的热量也减少。
因此,高炉鼓风中的富氧率也受到一定限制。
高炉富氧鼓风的目的是:提高冶炼强度;增加产量;强化喷吹燃料在风口前燃烧。
1 富氧鼓风对高炉的影响1.1 提高了冶炼强度。
由于风中含氧量增加,因而每吨铁所需风量减少。
若保持入炉风量不变,冶炼强度可以提高。
1.2 有利于高炉顺行。
富氧后因带入氮减少,所以单位生铁的煤气量减少,富氧鼓风并定风量时,压差降低,利于顺行。
1.3 提高了理论燃烧温度。
富氧后虽然风量减少使鼓风带入热量减少,但煤气量也相应减少,故能提高理论燃烧温度。
1.4 增加了煤气中CO的含量,有利于间接还原。
富氧鼓风改变了煤气中CO和N2的比例,CO升高,有利于间接还原的发展。
当富氧鼓风与喷吹燃料相结合时,炉缸煤气中CO和H2增加,对间接还原更有利。
1.5 降低了炉顶煤气温度。
富氧后单位生铁煤气量减少,上部热交换区扩大,炉顶煤气温度降低。
高温区集中在高炉下部,这使高炉竖向温度场发生变化。
这个影响与喷吹燃料的影响相反,因而富氧鼓风与喷吹燃料相结合可优势互补2 高炉富氧喷煤的冶炼特征富氧鼓风使理论燃烧温度升高,鼓风焓变小,煤气量减少,高温区下移,炉顶温度降低,冶炼行程加快,炉料在炉内停留时间缩短;而喷吹煤粉则使理论燃烧温度降低,鼓风焓变大,煤气量增加,中心气流发展,炉缸温度均匀,高中温区扩大,炉顶温度升高,焦比降低,料柱矿焦比例增加,炉料在炉内停留时间增长。
涟钢6号高炉富氧喷煤生产实践
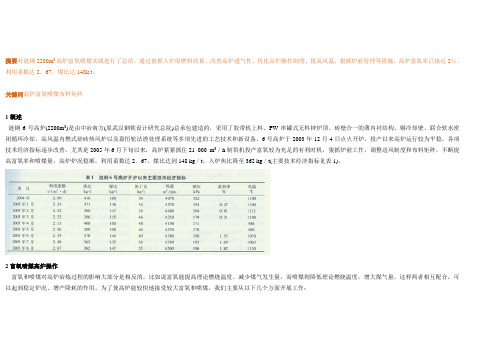
摘要对涟钢2200m3高炉富氧喷煤实践进行了总结。
通过狠抓入炉原燃料质量、改善高炉透气性、优化高炉操作制度、提高风温、狠抓炉前管理等措施,高炉富氧率已接近2%,利用系数达2.67,煤比达148k/t。
关键词高炉富氧喷煤布料矩阵1概述涟钢6号高炉(2200m3)是由中冶南方(原武汉钢铁设计研究总院)总承包建造的,采用了胶带机上料、PW串罐式无料钟炉顶、砖壁合一的薄内衬结构、铜冷却壁、联合软水密闭循环冷却、高风温内燃式硅砖热风炉以及嘉恒轮法渣处理系统等多项先进的工艺技术和新设备。
6号高炉于2003年12月4日点火开炉,投产以来高炉运行较为平稳,各项技术经济指标逐步改善。
尤其是2005年6月下旬以来,高炉紧紧抓住21 000 m3/h制氧机投产富氧较为充足的有利时机,狠抓炉前工作,调整送风制度和布料矩阵,不断提高富氧率和喷煤量,高炉炉况稳顺,利用系数达2.67,煤比达到148 kg/t,入炉焦比降至362 kg/t(主要技术经济指标见表1)。
2富氧喷煤高炉操作富氧和喷煤对高炉冶炼过程的影响大部分是相反的,比如说富氧能提高理论燃烧温度、减少煤气发生量,而喷煤则降低理论燃烧温度,增大煤气量,这样两者相互配合,可以起到稳定炉况、增产降耗的作用。
为了使高炉能较快地接受较大富氧和喷煤,我们主要从以下几个方面开展工作:2.1狠抓入炉原燃料质量,改善高炉透气性(1)2005年,烧结矿由于产能不足,加之矿粉采购困难,因此,量与质的矛盾较为突出。
一方面,烧结矿产量不足,被迫经常提碱度(最高达2.6倍),致使高炉烧结矿配比严重偏低且不稳定,最低时为53%,高炉炉料结构见表2;另一方面,烧结矿粒度偏小,返矿量大,重新烧结时又影响烧结矿质量,形成恶性循环。
针对这种情况,公司决定将槽下烧结返矿集中筛分,>5 mm部分返回高炉直接入炉,大大减少了烧结矿生产过程中返矿的配入量,此举有力地促进了烧结矿粒度组成的改善和碱度稳定。
500m3高炉富氧烟煤无烟煤混喷技术Ⅰ——工程实践

500m3高炉富氧烟煤无烟煤混喷技术Ⅰ——工程实践摘要:本文以西宁特钢股份有限公司500m3高炉实施富氧喷煤技术实践为例,考察了不同煤种、煤比及富氧量对生产的影响。
结果表明:选择60%无烟煤+40%的烟煤配比,富氧率为2%~3%时冶炼效果较佳,可使日产量提高541.595t,利用系数增加0.601t/m3•d,焦比降低40kg/t,达到了节能、降耗、增效的效果。
关键词:高炉;富氧;烟煤无烟煤;混合喷吹中图分类号:TF543.2 文献标识码:A 文章编号:1671-6035(2013)06-0000-02一、前言目前,高炉高富氧、高喷煤比是高炉有效降低焦碳消耗、降低高炉能耗、提高高炉经济技术指标的重要技术手段[1][2],高炉每多喷1公斤煤,可降低0.8公斤的焦炭消耗,因煤焦价差,可使吨铁的燃料成本降低400元左右,具有显著的经济效益。
高炉富氧能加速风口前碳的燃烧过程,提高理论燃烧温度,既提高了产量,又弥补了喷煤量增加造成的理论燃烧温度下降和氧过剩系数降低的缺点,富氧和喷吹煤粉是互补技术。
西宁特殊钢股份有限公司450m3高炉富氧系统于2009年1月投运,2010年结合高炉实际生产,首次开展了富氧与喷煤,烟煤、无烟煤混喷,高炉喷煤后高炉调剂规律的工业性试验。
2011年两座高炉成本降低4859.5788万元,节能8228.63吨标煤,达到了节能、降耗的目的。
2012年各项技术进入成熟应用阶段,高炉喷煤与高炉实际生产进入了正常运行阶段。
二、富氧混喷工艺和主要设备(一)工艺流程。
高炉富氧喷煤工艺流程图如图1所示。
图1 高炉富氧喷煤工艺流程图高炉富氧喷煤系统主要由喷煤工艺及富氧工艺两部分组成。
煤粉经管道、炉前分配器,通过喷枪喷入高炉。
从制氧厂出来1.6MPa的高压氧气经减压站减压至0.7Mpa后进入高炉区,为其提供富氧环境。
其中,高炉喷煤采用上出料浓相喷吹形式,采用补气调节器,通过调节补气量的大小改变调节器内煤粉的输送状态,达到调节喷吹量的目的。
最新-高炉富氧喷煤学习材料2 精品

高炉富氧喷煤学习材料篇一:对新钢九、十号高炉富氧喷煤几个问题的探讨对新钢九、十号高炉富氧喷煤问题的探讨李伟华(一铁厂)摘要新钢九、十号高炉从富氧大喷煤以来,注意对适宜的理论燃烧温度的控制,氧过剩系数的控制,保证了炉况顺行,从而使富氧大喷煤顺利进行。
关键词高炉富氧喷煤理论燃烧温度氧过剩系数炉况1、前言高炉喷煤是高炉生产中大幅度降低焦比和提高经济效益的重要措施之一,是优化高炉生产工艺结构的重要手段。
现在国内外已得到广泛的应用。
九、十号高炉从炉况稳定顺行,实现富氧、喷煤生产,吨铁喷煤量已达到全国领先地位。
厂领导对此特别重视,成立了试验攻关组,已开展了工作,为使试验攻关顺利进行,现就将试验中遇到的问题作如下探讨。
2、富氧喷煤与理论燃烧温度高炉的热量主要来自风口前炭的燃烧热和鼓风带入的物理热。
炉缸状态的主要标志就是风口前的理论燃烧温度理。
理论燃烧温度不仅影响渣铁温度,还直接影响到软熔带的形状、煤气流的分布和还原反应。
所以,适宜的理论燃烧温度应能满足高炉正常生产所需的炉缸温度和热量,即保证液态渣铁加热充分,炉缸热交换和还原反应正常进行,喷吹燃料在风口前充分燃烧。
高富氧喷煤时如果理论燃烧温度过低,将使煤粉燃烧不完全,引起炉料加热和还原不足而导致炉凉。
反之,理论燃烧温度过高,使炉缸热量集中,炉缸径向温度分布不均,高温带下移。
富氧量超过一定限度时,炉缸温度过高,炉内透气性及顺行恶化。
因此,理论燃烧温度控制在适合的范围,即富氧量的上限,从而使富氧鼓风的效果取得最佳值。
所以富氧喷煤的高炉控制适宜的理论燃烧温度十分重要。
正常情况下随着鼓风中含氧量提高,满足正常冶炼所需的理论燃烧温度也应逐渐升高,有经验证明提高1%富氧率,理论燃烧温度可提高35~45。
左右,(因富氧率提高后,风量减少,煤气量也减少但煤气热值升高了)。
但同时因富氧率提高,相应的喷煤量也要随之增加,因喷煤量增加就需要较多的热补偿,所以应维持较高的理论燃烧温度。
高富氧大喷煤技术分析
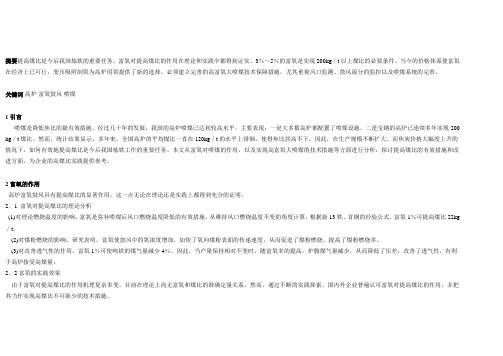
摘要提高煤比是今后我国炼铁的重要任务。
富氧对提高煤比的作用在理论和实践中都得到证实。
3%~5%的富氧是实现200kg/t以上煤比的必要条件。
当今的价格体系使富氧在经济上已可行,变压吸附制氧为高炉用氧提供了新的选择。
必须建立完善的高富氧大喷煤技术保障措施,尤其重视风口监测、鼓风湿分的监控以及喷煤系统的完善。
关键词高炉富氧鼓风喷煤1引言喷煤是降低焦比的最有效措施。
经过几十年的发展,我国的高炉喷煤已达到较高水平,主要表现:一是大多数高炉都配置了喷煤设施,二是宝钢的高炉已连续多年实现200 kg/t煤比。
然而,统计结果显示,多年来,全国高炉的平均煤比一直在120kg/t的水平上徘徊,使得焦比居高不下。
因此,在生产规模不断扩大、而焦炭价格大幅度上升的情况下,如何有效地提高煤比是今后我国炼铁工作的重要任务。
本文从富氧对喷煤的作用,以及实现高富氧大喷煤的技术措施等方面进行分析,探讨提高煤比的有效措施和改进方面,为企业的高煤比实践提供参考。
2富氧的作用高炉富氧鼓风具有提高煤比的显著作用,这一点无论在理论还是实践上都得到充分的证明。
2.1 富氧对提高煤比的理论分析(1)对理论燃烧温度的影响。
富氧是弥补喷煤后风口燃烧温度降低的有效措施。
从维持风口燃烧温度不变的角度计算,根据新13铁、首钢的经验公式,富氧1%可提高煤比22kg /t。
(2)对煤粉燃烧的影响。
研究表明,富氧使鼓风中的氧浓度增加,加快了氧向煤粉表面的传递速度,从而促进了煤粉燃烧,提高了煤粉燃烧率。
(3)对改善透气性的作用。
富氧1%可使吨铁的煤气量减少4%。
因此,当产量保持相对不变时,随富氧率的提高,炉腹煤气量减少,从而降低了压差,改善了透气性,有利于高炉接受高煤量。
2.2富氧的实践效果由于富氧对提高煤比的作用机理复杂多变,目前在理论上尚无富氧和煤比的准确定量关系。
然而,通过不断的实践探索,国内外企业普遍认可富氧对提高煤比的作用,并把其当作实现高煤比不可缺少的技术措施。
高炉富氧喷煤冶炼特征及生产实践

另一方面,全面做好入炉原燃料的筛分工作,减少人炉粉末,保证炉况顺行。
383
2.I.2不断提高焦炭质量。
使用质量较高的自产焦炭,焦炭的反应性和热强度控制在25%1)./下及65%1)./_h。焦炭质量如表2。
表2 2009年焦炭分析I%)
2.1.3加强对入炉原燃料质量的监控管理。
通过不断探索和完善高炉的富氧喷煤操作技术在外部原燃料条件逐步改善的情况下合理喷煤积极调整高炉操作制度冶炼低硅生铁加强炉内及炉前管理采用高风温高富氧大喷煤烟煤混喷技术实现了提高喷煤比烟煤比的目标煤比达到150kgt以上
高炉富氧喷煤冶炼特征及生产实践
顾爱军
(河北钢铁集团宣化钢铁公司炼铁厂)
摘要:宣钢三座1000m3高炉。通过不断探索和完善高炉的富氧喷煤操作技术,在外部原燃料条件逐步改善的情况 下,合理喷煤,积极调整高炉操作制度,冶炼低硅生铁,加强炉内及炉前管理,采用高风温、高富氧大喷 煤、烟煤混喷技术,实现了提高喷煤比、烟煤比的目标,煤比达到150kg/t以上.烟煤比达到了65%,经济效 益显著。 关键词:高炉富氧喷煤生产实践
2.2合理调整各部制度
(1)下部调剂。高炉富氧以后,单位生铁煤气量减少,而随着煤比的增加,焦炭负荷不断加重, 料柱透气性也会随着不断恶化。为保证炉况顺行,高炉上下部必须合理而且相互适应,为此,对风 口布局和进风面积进行了合理的调整。 (2)上部调剂。上部布料必须根据冶炼条件的变化与下部制度相适应。随着送风制度的变化, 保证足够的中心焦炭量,进一步将矿石布往中心和边缘,这样既保持合理的中心煤气流,又改善煤 气利用,煤气利用率稳定在45%水平。 (3>控制合理的热制度和造渣制度。由于钛负荷高,为防止炉缸产生粘结,必须保持fSi)+{瓢l受 控,做好低硅冶炼,关键是保证充足的物理热。实践中采用控制较高渣碱度及较高的煤气利用来确 保低硅高物理热,控制铁温1470.1500℃,严禁铁温低于1460气2。 2.3提高风温 实现大喷煤以后,风口前理论燃烧温度大幅度降低,根据实践,每增加煤比lOkg/t,约降低理 论燃烧温度20.25。12,为保证适宜的理论燃烧温度,就必须通过富氧和提高风温度来予以补偿。我厂 利用热风炉烧炉产生的烟气对高炉煤气和助燃空气进行预热,以提高热风温度,保证热风温度在 1100'12以上,为煤比及烟煤比的提高提供了保障。
高炉富氧后的特征

o高炉富氧: 1,提高理论燃烧温度 2,煤气量减少,因为富氧多了,相应的进入的空气含量降低,氮气减少3,间接还原基本不变 4,煤气发热值高间接还原基本不变:富氧提高的话,氮气变少,一氧化碳变多,煤气量多,CO浓度对氧化铁还原的影响是递减的;而且由于富氧后间接还原温度场分布改变,富氧后因常量提高,使炉料在间接还原区停留时间缩小,这两方面都不利于间接还原反应的进行。
富氧量超过一定限度,风量降幅太大,导致进入高炉内热量减少,影响炉料的加热还原,提高焦比。
高炉喷煤:(高炉喷煤后压差总是升高)1,煤气量和鼓风动能增加 2,间接还原反应改善,直接还原降低3,理论燃烧温度降低,中心温度升高 4,料柱阻损增加,压差升高5,热补偿 6,热滞后时间 7,冶炼周期延长煤粉在风口前和风口内就形成高速气流,增加煤气量,同时热滞后时间,煤粉初期吸热分解,直至新增加的煤粉燃烧所产生的热量蓄积和她带来的煤气量和还原性气体浓度的改变,而改善矿石的加热和还原的炉料下降到炉缸后,才开始提高炉缸温度,我靠,真TMD慢啊2未燃烧煤粉在高炉的行为:参加碳的气化反应生铁渗碳混在渣中影响渣的黏度和流动性沉积在软溶带和料柱中恶化透气性随煤气逸出炉外附录:理论燃烧温度—如果在保持定压或定容的条件下,燃料在给定的过量空气中完全燃烧,并且燃烧过程中燃烧反应系统和外界完全绝热,没有任何热量散失,则燃烧生成物所达到的温度,称为理论燃烧温度。
这个温度也是所给条件下燃料燃烧可能达到的最高温度。
理论燃烧温度的计算按定压燃烧的能量转换关系式,有Q p=H P-H R当定压燃烧系统和外界完全绝热时,Q p=0,由上式可以得到H P=H R这就是说,在绝热条件下进行定压燃烧时,随着全部反应物本身发生化学变化转变成生成物,反应物的焓也全部转变成生成物的焓。
根据焓和温度的关系,就可按照生成物的焓值确定定压燃烧系统的理论燃烧温度。
同样地,对于在绝热条件下进行的定容燃烧过程,可以按照定容燃烧的能量关系式Q V=U P-U R考虑到Q V=0,即可得到U P=U R这就是说,根据热力学能和温度的关系,就可按照生成物的热力学能的数值,确定定容燃烧系统的理论燃烧温度。
- 1、下载文档前请自行甄别文档内容的完整性,平台不提供额外的编辑、内容补充、找答案等附加服务。
- 2、"仅部分预览"的文档,不可在线预览部分如存在完整性等问题,可反馈申请退款(可完整预览的文档不适用该条件!)。
- 3、如文档侵犯您的权益,请联系客服反馈,我们会尽快为您处理(人工客服工作时间:9:00-18:30)。
高炉富氧喷煤
摘要:提高煤比是今后我国炼铁的重要任务。
富氧对提高煤比的作用在理论和实践中都得到证实。
3%一5%的富氧是实现200kg/t以上煤比的必要条件。
当今的价格体系使富氧在经济上已可行,变压吸附制氧为高炉用氧提供了新的选择。
必须建立完善的高富氧大喷煤技术保障措施,尤其重视风口监测、鼓风湿分的监控以及喷煤系统的完善。
关键词:高炉富氧鼓风喷煤
Blast furnace oxygen-enriched coal spray
Abstract :High coal ratio is a target of ironmaking in future and the role of oxygen enrichment in high coal ratio has been proved in theory and practice.3%~5%oxygen enrichment is essential for realizing the coal ratio higher than 200 kg/t.The current price system makes the oxygen enrichment feasible economically and oxygen generation by absorption at variable pressure provides new routine of oxygen supply for blast furnace.It is very important to set up a complete technical system of pulverized coal injection with high oxygen enrichment,monitoring of tuyere status and water content in blasting air.
Key words: blast furnace air blasting with oxygen enrichment pulverized coal injection
1.概述
高炉是生产率和热效率都很高的炼铁设备,其主要目的是用燃料和铁矿石及溶剂,经济而高效率地得到温度和成分合乎要求的液态生铁。
目前,炼铁系统正受到投资、资源、成本、能源、环境和运输等方面金融风暴的巨大影响,面临着严重的挑战。
而利用技术进步减轻这些压力是高炉炼铁系统继续生存和发展的关键。
高炉富氧喷煤技术可以使高炉大幅度降低焦碳消耗,缓解各方面的压力,提高高炉的竞争力。
高炉富氧喷煤技术是炼铁系统结构优化的中心环节。
2 高炉富氧鼓风
2.1何谓高炉富氧鼓风
富氧鼓风是指往高炉鼓风加入工业氧(一般含氧99.5%),使鼓风含氧超过大气含氧量,其目的是提高冶炼强度以增加高炉产量和强化喷吹燃料在风口前燃烧。
2.2富氧鼓风的方法
富氧鼓风的方法主要有两种:一种是从鼓风机吸入口加入低压氧气,其优点是氧气不用专门氧压机加压,可节约投资与电耗,高炉操作方便;其缺点是需设高炉专用制氧机,氧漏损较多,该方法在前苏联普遍采用;另一种是采用高压供氧即工业氧通过加压后直接加入高炉管道内,其优点是可与炼钢用氧联网,保持制氧机全负荷运行,比较经济,但需增设氧压机加压,投资多,电耗高。
最近一些国家正在研究发展高炉氧煤燃烧器,即将工业氧通过氧煤燃烧器送入,与喷吹煤粉有效混合,实现充分燃烧和大量喷吹煤粉。
2.3 高炉富氧鼓风对冶炼的影响
(1)提高冶炼强度:
(2)提高理论燃烧温度;
(3)增加煤气中的CO含量,促进间接还原;
(4)降低炉顶煤气温度。
2.4 高炉富氧鼓风对产量和焦比的影响
(1)富氧鼓风加速碳素燃烧,煤比不变则产量增加,提高含氧l%可增产4.76%,这是理论增产率,随着富氧率提高,增产率递减。
(2)一般原来焦比较高,富氧率不变时,因热能利用改善,焦比将有所降低。
3.高炉喷煤冶炼
3.1喷煤的定义
喷煤是指把原煤烘干磨细,用输送气体做载体商接喷进高炉风口,以代替焦炭向高炉提供热量和还原剂。
喷煤可以降低焦比,降低生铁成本:喷煤可以作为调剂炉况的手段:喷煤有利于高炉稳定顺行;喷煤为提高风温和富氧鼓风创造条件。
3.2喷吹煤粉对高炉的影响
(1)炉缸煤气量增加,鼓风动能增加燃烧带扩大,径向温度趋于均匀,中心温度升高,中心气流得以发展。
此时需扩大风口面积,选择适当的鼓风动能来维持合理的气流分布。
(2)理论燃烧温度下降,因为用于加热产物的热量增加较多,煤粉的温度为80"C 左右,带进的物理热少。
(3)料柱阻损增加,压差升高。
料柱的矿/焦比值增大,炉内料柱中透气性好的焦炭量减少,则造成料柱透气性变差。
(4)间接还原发展直接还原降低:喷吹煤粉以后,改变了高炉燃料结构,进而改变了铁氧化物还原和碳气化条件,明显地有利于间接还原的发展和直接还原度的降低。
喷煤后单位生铁的炉料容积减少使炉料在炉内停留时间增长。
3.3 高炉喷吹煤粉的“热补偿”
高炉喷吹煤粉时,以常温进入高炉在风口区需加热和裂解,消耗部分热量,致使理论燃烧温度降低,炉缸热量不足。
为保持原有的状态,需要热补偿,严格地说这个补偿包括了温度和热量两个方面,主要措施有提高风温和富氧率等。
3.4喷吹煤粉的“热滞后”现象
增加喷吹量时,煤粉在炉缸分解吸热增加,初期使炉缸温度降低,直到新增加喷吹量带来的煤气量和还原气体浓度(尤其是H2量)的改变,而改善了矿石的加热和还原下到炉缸后,开始提高炉缸温度,此过程所经历的时间则称为“热滞后”时间。
一般滞后时间在2~4小时。
3.5喷吹煤粉对冶炼周期的影响
随着煤比的提高,炉料中含铁炉料比例显著增加,相对地增加了含铁炉料和煤气的接触时间,由于煤粉大量代替风口焦炭,炉料的冶炼周期也相应延长。
3.6煤粉的燃烧率
煤粉的燃烧率是煤粉燃烧好坏的标志,定义为煤粉中可燃物气化率。
强化煤粉在风口的燃烧是高炉进行大喷吹的一个最基本的前提。
提高煤粉的燃烧率因素有:
(1)使用精料;
(2)提高风温:
(3)进行适当的富氧鼓风混合喷吹;
(4)使用易燃烧的煤种;
(5)在煤粉中添加一些氧化物和碳酸盐对煤的燃烧起到催化作用的助燃剂:
(6)优化喷煤工艺流程实现均喷稳喷;
(7)采用相应的高炉操作调剂措施,如上下部调剂,中心加焦,改善高炉料柱的透气性等。
3.7煤粉的置换比
喷吹1kg煤粉能替换多少焦炭,叫喷吹煤粉的置换比。
它是衡量喷吹煤粉效果如何的重要指标。
置换比越高说明喷吹煤粉的效果越好。
影响置换比的因素主要有:
(1)煤的质量;
(2)煤的燃烧好坏;
(3)气化程度;
(4)高炉操作;
(5)风温;
(6)富氧;
(7)高炉压力;
(8)高炉直接还原度。
4.展望
随着钢铁工业不断发展,传统的高炉炼铁工艺所需要的大量炼焦煤日趋枯竭,迫使炼铁工作者寻求新的焦炭代用品。
因此,在发展富氧大量喷吹燃料的同时,高炉全氧(无氮)鼓风喷煤技术是近年各国广泛关注的新工艺,在日本、前苏联等国家已进行了试验研究。
这种工艺具有高生产率、高喷煤量、低焦比、128高煤气热值、环境污染少、投资省的特点。
1986年日本钢管公司在3.9m3试验炉上进行了全氧鼓风试验,每吨铁喷吹煤粉量增加到320kg/t,高炉炉况稳定顺行,利用系数达到5.1t/(m3.d),直接还原度与入炉焦比均降低一半以上,生铁质量明显改善。
中国炼铁工作者在大量实验室研究的基础上,也已提出了一种新的高炉氧煤炼铁工艺,2006年宝钢300万吨的还原炉投产。