数控刀柄发展性能
数控技术的发展历程及发展趋势

数控技术的发展历程及发展趋势随着汽车、航空航天等工业轻合金材料的广泛应用,高速加工已成为制造技术的重要发展趋势。
高速加工具有缩短加工时间、提高加工精度和表面质量等优点,在模具制造等领域的应用也日益广泛。
机床的高速化需要新的数控系统、高速电主轴和高速伺服进给驱动,以及机床结构的优化和轻量化。
高速加工不仅是设备本身,而是机床、刀具、刀柄、夹具和数控编程技术,以及人员素质的集成。
高速化的最终目的是高效化,机床仅是实现高效的关键之一,绝非全部,生产效率和效益在"刀尖"上。
数控技术的发展历程及发展趋势如何?本文开门见山直接列举了数控技术的发展历程及未来的发展趋势。
数控技术的发展历程是什么1948年,美国帕森斯公司接受美国空军委托,研制直升飞机螺旋桨叶片轮廓检验用样板的加工设备。
由于样板形状复杂多样,精度要求高,一般加工设备难以适应,于是提出采用数字脉冲控制机床的设想。
1949年,该公司与美国麻省理工学院(MIT)开始共同研究,并于1952年试制成功第一台三坐标数控铣床,当时的数控装置采用电子管元件。
1959年,数控装置采用了晶体管元件和印刷电路板,出现带自动换刀装置的数控机床,称为加工中心( MC Machining Center),使数控装置进入了第二代。
1965年,出现了第三代的集成电路数控装置,不仅体积小,功率消耗少,且可靠性提高,价格进一步下降,促进了数控机床品种和产量的发展。
60年代末,先后出现了由一台计算机直接控制多台机床的直接数控系统(简称 DNC),又称群控系统;采用小型计算机控制的计算机数控系统(简称 CNC),使数控装置进入了以小型计算机化为特征的第四代。
1974年,研制成功使用微处理器和半导体存贮器的微型计算机数控装置(简称 MNC),这是第五代数控系统。
20世纪80年代初,随着计算机软、硬件技术的发展,出现了能进行人机对话式自动编制程序的数控装置;数控装置愈趋小型化,可以直接安装在机床上;数控机床的自动化程度进一步提高,具有自动监控刀具破损和自动检测工件等功能。
数控刀具及其选用

一、选择刀具时应考虑的因素 (1)被加工工件的材料类别(黑色金属,有色金属或合金); (2)工件毛坯的成形方法(铸造,锻造,型材等); (3)切削加工工艺方法(车,铣,钻,扩,铰,镗,粗加工,半精加工,精加工等); (4)工件的结构与几何形状,精度,加工余量以及刀具能承受的切削用量等因素; (5)其他因数包括生产条件和生产类型。
数控刀具及选用
1.1 数控机床刀具的特点
数控机床刀具的特点是标准化、系列化、规格化、模块化和通用化。 为了达到高效、多能、快换、经济的目的,对数控机床使用的刀具有如下要求: (1)具有较高的强度、较好的刚度和抗振性能; (2)高精度、高可靠性和较强的适应性; (3)能够满足高切削速度和大进给量的要求; (4)刀具耐磨性及刀具的使用寿命长,刀具材料和切削参数与被加工件材料之间要适宜; (5)刀片与刀柄要通用化、规格化、系列化、标准化,相对主轴要有较高位置精度,转位、拆 装时要求重复定位精度高,安装调整方便。
1.5 常用数控刀具结构
一、整体式刀具结构 整体式刀具是指刀具切削部分和夹持部分为一体式结构的刀具。 制造工艺简单,刀具磨损后可以重新修磨。
二、机夹式刀具结构 机夹式刀具是指刀片在刀体上的定位形式。 机夹式刀具分为机夹可转位刀具和机夹不可转
位刀具。数控机床一般使用标准的机夹可转位刀具。 机夹可转位刀具一般由刀片、刀垫、刀体和刀
1.4 数控机床刀具分类
按照刀具材料可分为:高速钢刀具,硬质合金刀具,陶瓷刀具,立方氮化硼刀具和金刚石刀具。 按照刀具结构可分为:整体式,焊接式,机夹式(可转位和不转位),内冷式和减振式。 按照切削工艺分为:车削刀具,孔加工刀具(如钻头,丝锥和镗刀等),铣削刀具等。 按照数控工具系统的发展可分为:由整体式工具系统向模块式工具系统发展。有利于提高劳动 生产率,提高加工效率,提高产品质量。 标准化数控刀具已形成了三大系统,即车削刀具系统、钻削刀具系统和镗铣刀具系统。
数控刀柄标准
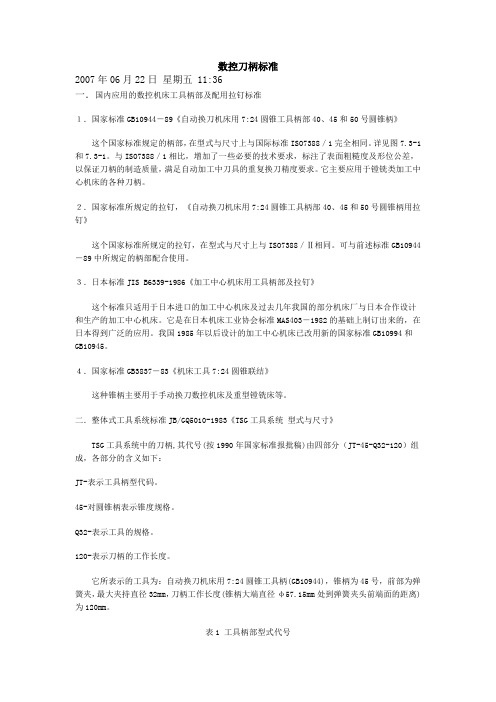
数控刀柄标准2007年06月22日星期五 11:36一.国内应用的数控机床工具柄部及配用拉钉标准1.国家标准GB10944-89《自动换刀机床用7:24圆锥工具柄部40、45和50号圆锥柄》这个国家标准规定的柄部,在型式与尺寸上与国际标准ISO7388/1完全相同。
详见图7.3-1和7.3-1。
与ISO7388/1相比,增加了一些必要的技术要求,标注了表面粗糙度及形位公差,以保证刀柄的制造质量,满足自动加工中刀具的重复换刀精度要求。
它主要应用于镗铣类加工中心机床的各种刀柄。
2.国家标准所规定的拉钉,《自动换刀机床用7:24圆锥工具柄部40、45和50号圆锥柄用拉钉》这个国家标准所规定的拉钉,在型式与尺寸上与ISO7388/Ⅱ相同。
可与前述标准GB10944-89中所规定的柄部配合使用。
3.日本标准JIS B6339-1986《加工中心机床用工具柄部及拉钉》这个标准只适用于日本进口的加工中心机床及过去几年我国的部分机床厂与日本合作设计和生产的加工中心机床。
它是在日本机床工业协会标准MAS403-1982的基础上制订出来的,在日本得到广泛的应用。
我国1985年以后设计的加工中心机床已改用新的国家标准GB10994和GB10945。
4.国家标准GB3837-83《机床工具7:24圆锥联结》这种锥柄主要用于手动换刀数控机床及重型镗铣床等。
二.整体式工具系统标准JB/GQ5010-1983《TSG工具系统型式与尺寸》TSG工具系统中的刀柄,其代号(按1990年国家标准报批稿)由四部分(JT-45-Q32-120)组成,各部分的含义如下:JT-表示工具柄型代码。
45-对圆锥柄表示锥度规格。
Q32-表示工具的规格。
120-表示刀柄的工作长度。
它所表示的工具为:自动换刀机床用7:24圆锥工具柄(GB10944),锥柄为45号,前部为弹簧夹,最大夹持直径32mm,刀柄工作长度(锥柄大端直径φ57.15mm处到弹簧夹头前端面的距离)为120mm。
CNC介绍

(5)驱动装置。驱动装置把经过伺服单元放大的指令信号变为机 械运动,通过机械连接部件驱动机床工作台,使工作台精确定 位或按规定的轨迹作严格的相对运动,加工出形状、尺寸与精 度符合要求的零件。目前常用的驱动装置有直流伺服电机和交 流伺服电机,交流伺服电机正逐渐取代直流伺服电机。
伺服单元和驱动装置合称为伺服驱动系统,它是机床工作 的动力装置,计算机数控装置的指令要靠伺服驱动系统付诸实 施,伺服驱动装置包括主轴驱动单元(主要控制主轴的速度)、 进给驱动单元(主要控制进给系统的速度和位置)。伺服驱动 系统是数控机床的重要组成部分。从某种意义上说,数控机床 的功能主要取决于数控装置,而数控机床的性能主要取决于伺 服驱动系统。 (6)机床本体。即数控机床的机械部件,包括主运动部件、进给 运动执行部件(工作台、拖板及其传动部件)和支承部件(床 身、立柱等),还包括具有冷却、润滑、转位和夹紧等功能的 辅助装置。加工中心类的数控机床还有存放刀具的刀库、交换 刀具的机械手等部件,数控机床机械部件的组成与普通机床相 似。由于数控机床高速度、高精度、大切削用量和连续加工的 要求,其机械部件在精度、刚度、抗振性等肯面要求更高。
数控刀具国内外排行性能总汇.
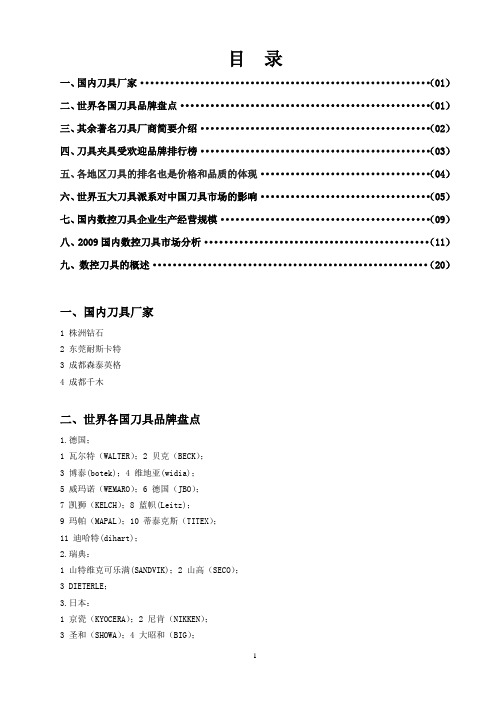
目录一、国内刀具厂家 (01)二、世界各国刀具品牌盘点 (01)三、其余著名刀具厂商简要介绍 (02)四、刀具夹具受欢迎品牌排行榜 (03)五、各地区刀具的排名也是价格和品质的体现 (04)六、世界五大刀具派系对中国刀具市场的影响 (05)七、国内数控刀具企业生产经营规模 (09)八、2009国内数控刀具市场分析 (11)九、数控刀具的概述 (20)一、国内刀具厂家1 株洲钻石2 东莞耐斯卡特3 成都森泰英格4 成都千木二、世界各国刀具品牌盘点1.德国;1 瓦尔特(WALTER);2 贝克(BECK);3 博泰(botek);4 维地亚(widia);5 威玛诺(WEMARO);6 德国(JBO);7 凯狮(KELCH);8 蓝帜(Leitz);9 玛帕(MAPAL);10 蒂泰克斯(TITEX);11 迪哈特(dihart);2.瑞典:1 山特维克可乐满(SANDVIK);2 山高(SECO);3 DIETERLE;3.日本:1 京瓷(KYOCERA);2 尼肯(NIKKEN);3 圣和(SHOWA);4 大昭和(BIG);5 三菱(MITSUBISHI);6 弥漫和(YAMAWA)絲攻;7 OSG 絲攻;8 优能 UNION 微型铣刀;9 日立(HITACHI);10 东芝泰柯珞(TOSHIBA);11 二不越荔枝(NACHI);12 住友(SUMITOMO);13 元刀(ASADA);14 冈崎(OKAZAKI);15 鹰牌(EAGLE);16 (FP)铰刀;17 戴杰(DIJET)铣刀;18 富士(H.T.D)絲攻;19 神户直冈(kobelco);20 小笠原(OGASAWARA);4.以色列:依斯卡(ISCAR);5.美国:1 肯纳(kenna);2 昂思路(Onsrud);3 LBK;4 切削王(Mastercut);5 铣星(MILLSTAR);6 SGS;7 国洛泰克(NTK)Mast;6.韩国:1 YESTOOL;2 多仁(DINE);3 HEADONG;4 HANBOO;5 克洛依(KORLOY);6 特固克(TAEGUTEC);7.西班牙:LAT;8.意大利:1 FIUDI.;2 DELFER;三、其余著名刀具厂商简要介绍1 英迈工具(INMIND):专业钨钢铣刀、丝锥、钻头生产厂家,著名刃具品牌。
数控刀柄标准 JIS B 6339(MAS 403 BT)
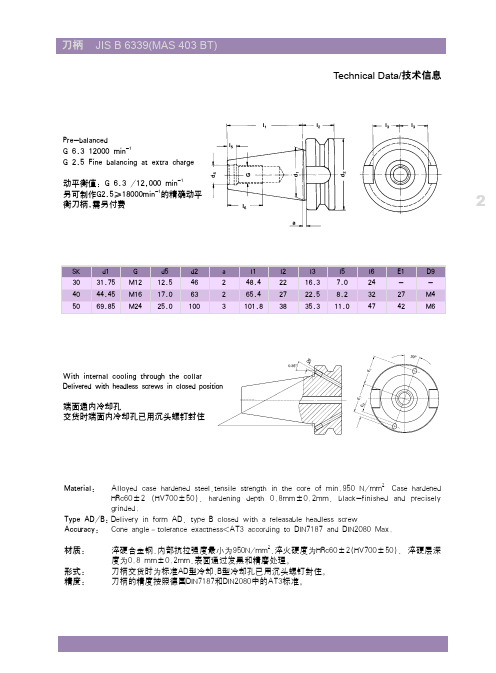
库存状况
◎ ◎
◎ ◎
◎ ◎ ◎ ◎ ◎ ◎ ◎ ◎ ◎ ◎ ◎ ◎
只提供AD型刀柄
非常备库存 ◎
ห้องสมุดไป่ตู้
刀柄 JIS B 6339(MAS 403 BT)
Collet chuck ER for collets according to DIN 6499 to clamp tools with cylindrical shank ER弹簧夹头刀柄 使用DIN 6499标准的ER弹簧夹头 用于夹持直柄刀具
Order No 订货号 312.E16.070* 312.E16.100* 312.E25.070* 312.E25.100* 312.E32.070* 312.E32.100* 312.E40.070* 412.E16.063 412.E16.100 412.E16.160 412.E25.060 412.E25.100 412.E25.160 412.E32.070 412.E32.100 412.E32.160 412.E40.080 412.E40.100 412.E40.160 512.E16.100 512.E16.160 512.E25.060 512.E25.100 512.E25.160 512.E32.070 512.E32.100 512.E32.160 512.E40.080 512.E40.100 512.E40.160 * Form AD *
BT 30 30 30 30 30 30 30 40 40 40 40 40 40 40 40 40 40 40 40 50 50 50 50 50 50 50 50 50 50 50
Collect 夹头 ER16 ER16 ER25 ER25 ER32 ER32 ER40 ER16 ER16 ER16 ER25 ER25 ER25 ER32 ER32 ER32 ER40 ER40 ER40 ER16 ER16 ER25 ER25 ER25 ER32 ER32 ER32 ER40 ER40 ER40
数控机床刀柄的分类
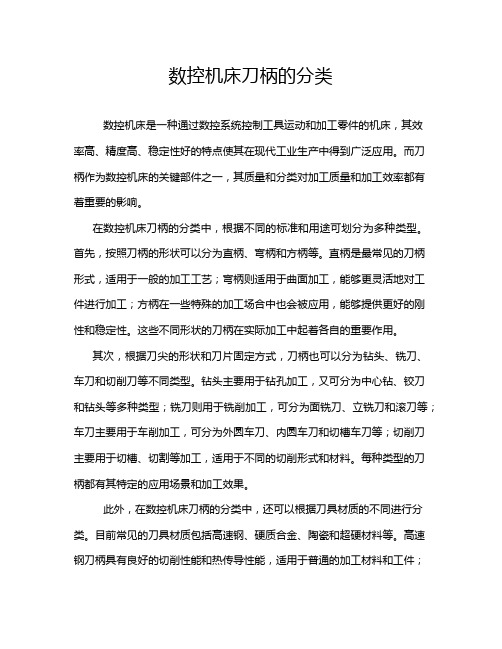
数控机床刀柄的分类数控机床是一种通过数控系统控制工具运动和加工零件的机床,其效率高、精度高、稳定性好的特点使其在现代工业生产中得到广泛应用。
而刀柄作为数控机床的关键部件之一,其质量和分类对加工质量和加工效率都有着重要的影响。
在数控机床刀柄的分类中,根据不同的标准和用途可划分为多种类型。
首先,按照刀柄的形状可以分为直柄、弯柄和方柄等。
直柄是最常见的刀柄形式,适用于一般的加工工艺;弯柄则适用于曲面加工,能够更灵活地对工件进行加工;方柄在一些特殊的加工场合中也会被应用,能够提供更好的刚性和稳定性。
这些不同形状的刀柄在实际加工中起着各自的重要作用。
其次,根据刀尖的形状和刀片固定方式,刀柄也可以分为钻头、铣刀、车刀和切削刀等不同类型。
钻头主要用于钻孔加工,又可分为中心钻、铰刀和钻头等多种类型;铣刀则用于铣削加工,可分为面铣刀、立铣刀和滚刀等;车刀主要用于车削加工,可分为外圆车刀、内圆车刀和切槽车刀等;切削刀主要用于切槽、切割等加工,适用于不同的切削形式和材料。
每种类型的刀柄都有其特定的应用场景和加工效果。
此外,在数控机床刀柄的分类中,还可以根据刀具材质的不同进行分类。
目前常见的刀具材质包括高速钢、硬质合金、陶瓷和超硬材料等。
高速钢刀柄具有良好的切削性能和热传导性能,适用于普通的加工材料和工件;硬质合金刀柄耐磨性好、寿命长,适用于加工硬质、高硬度的工件;陶瓷刀柄具有优异的耐磨性和热稳定性,适用于高速切削和加工难加工材料;超硬刀柄具有极高的硬度和耐磨性,适用于高硬度材料的加工。
选择适合材料和加工方式的刀柄材质能够提高加工效率和加工质量。
综上所述,数控机床刀柄的分类是根据刀柄的形状、刀具类型和材质等多个因素综合决定的。
在实际的数控加工生产中,正确选择和使用不同类型的刀柄对于提高加工质量、加工效率和延长刀具寿命都具有着重要的意义。
因此,对于数控机床刀柄的分类及其应用有着深入的研究和实践意义。
希望通过本文的介绍,能够对读者对数控机床刀柄分类有更深入的了解和认识,从而更好地应用于实际生产中。
数控刀具中刀柄的应用知识

数控刀具中刀柄的应用知识数控刀具中刀柄的应用知识加工中心的主轴锥孔通常分为两大类,即锥度为7:24的通用系统和1:10的HSK真空系统。
7:24锥度的通用刀柄锥度为7:24的通用刀柄通常有五种标准和规格,即NT(传统型)、DIN 69871(德国标准)、IS0 7388/1 (国际标准)、MAS BT(日本标准)以及ANSI/ASME(美国标准)。
NT型刀柄德国标准为DIN 2080,是在传统型机床上通过拉杆将刀柄拉紧,国内也称为ST;其它四种刀柄均是在加工中心上通过刀柄尾部的拉钉将刀柄拉紧。
目前国内使用最多的是DIN 69871型(即JT)和MAS BT 型两种刀柄。
DIN 69871型的刀柄可以安装在DIN 69871型和ANSI/ASME主轴锥孔的机床上,IS0 7388/1型的刀柄可以安装在DIN 69871型、IS0 7388/1 和ANSI/ASME主轴锥孔的机床上,所以就通用性而言,IS0 7388/1型的刀柄是最好的。
(1)DIN 2080型(简称NT或ST)DIN 2080是德国标准,即国际标准ISO 2583 ,是我们通常所说NT型刀柄,不能用机床的机械手装刀而用手动装刀。
(2)DIN 69871 型(简称JT、DIN、DAT或DV)DIN 69871 型分两种,即DIN 69871 A/AD型和DIN 69871 B 型,前者是中心内冷,后者是法兰盘内冷,其它尺寸相同。
(3)ISO 7388/1 型(简称IV或IT)其刀柄安装尺寸与DIN 69871 型没有区别,但由于ISO 7388/1 型刀柄的D4值小于DIN 69871 型刀柄的D4值,所以将ISO 7388/1型刀柄安装在DIN 69871型锥孔的机床上是没有问题的,但将DIN 69871 型刀柄安装在ISO 7388/1型机床上则有可能会发生干涉。
(4)MAS BT 型(简称BT)BT型是日本标准,安装尺寸与DIN 69871、IS0 7388/1 及ANSI 完全不同,不能换用。
数控刀柄标准
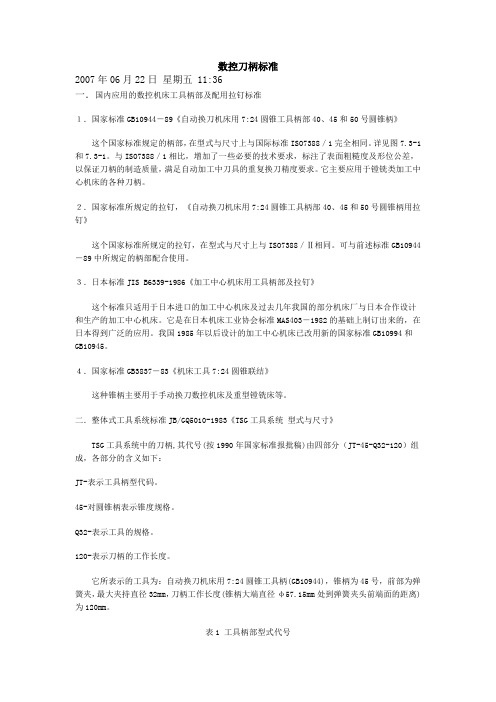
数控刀柄标准2007年06月22日星期五 11:36一.国内应用的数控机床工具柄部及配用拉钉标准1.国家标准GB10944-89《自动换刀机床用7:24圆锥工具柄部40、45和50号圆锥柄》这个国家标准规定的柄部,在型式与尺寸上与国际标准ISO7388/1完全相同。
详见图7.3-1和7.3-1。
与ISO7388/1相比,增加了一些必要的技术要求,标注了表面粗糙度及形位公差,以保证刀柄的制造质量,满足自动加工中刀具的重复换刀精度要求。
它主要应用于镗铣类加工中心机床的各种刀柄。
2.国家标准所规定的拉钉,《自动换刀机床用7:24圆锥工具柄部40、45和50号圆锥柄用拉钉》这个国家标准所规定的拉钉,在型式与尺寸上与ISO7388/Ⅱ相同。
可与前述标准GB10944-89中所规定的柄部配合使用。
3.日本标准JIS B6339-1986《加工中心机床用工具柄部及拉钉》这个标准只适用于日本进口的加工中心机床及过去几年我国的部分机床厂与日本合作设计和生产的加工中心机床。
它是在日本机床工业协会标准MAS403-1982的基础上制订出来的,在日本得到广泛的应用。
我国1985年以后设计的加工中心机床已改用新的国家标准GB10994和GB10945。
4.国家标准GB3837-83《机床工具7:24圆锥联结》这种锥柄主要用于手动换刀数控机床及重型镗铣床等。
二.整体式工具系统标准JB/GQ5010-1983《TSG工具系统型式与尺寸》TSG工具系统中的刀柄,其代号(按1990年国家标准报批稿)由四部分(JT-45-Q32-120)组成,各部分的含义如下:JT-表示工具柄型代码。
45-对圆锥柄表示锥度规格。
Q32-表示工具的规格。
120-表示刀柄的工作长度。
它所表示的工具为:自动换刀机床用7:24圆锥工具柄(GB10944),锥柄为45号,前部为弹簧夹,最大夹持直径32mm,刀柄工作长度(锥柄大端直径φ57.15mm处到弹簧夹头前端面的距离)为120mm。
数控机床ATC系统

2.5 数控加工自动换刀系统
(1) 换刀机械手构造
--单臂单爪机械手: 只有一种手臂换刀,因此换刀时间长。
--回转式单臂双爪机械手: 它旳双爪可同步工作,通过手臂回转互
换刀具位置,因此换刀时间短。 --双臂机械手:
能同步抓取和装卸机床主轴和刀库集中 旳刀具,因此换刀深入时间缩短。 --双刀库机械手:
(3)工作长度
27
2.5 数控加工自动换刀系统 3) 常用刀柄
面铣刀刀柄
整体钻夹头刀柄
28
2.5 数控加工自动换刀系统 镗刀柄
29
2.5 数控加工自动换刀系统
莫式锥 度刀柄
钻夹头 刀柄
快换式丝 锥刀柄
30
2.5 数控加工自动换刀系统
ER弹簧夹头刀柄
侧压式立铣刀柄
ER型卡簧
KM型卡簧
31
2.5 数控加工自动换刀系统
在转塔旳各主轴头上预先装好所需刀具, 换刀时依次转至加工位置,接通主运动,带动刀 具旋转。
长处:省去了自动松夹、装卸刀具、夹紧及 刀具搬动等一系列复杂操作,缩短了换刀时间, 提高了换刀可靠性。
缺陷:主轴部件旳刚性差且主轴旳数目不也 许太多。
45
2.5 数控加工自动换刀系统 (1) 多主轴转塔头构造
换刀动作: 刀架抬起; 刀架转位; 刀架锁紧; 油缸复位;
43
2.5 数控加工自动换刀系统 (2) 液压控制旳六角回转刀架
换刀动作: 刀架抬起; 刀架转位; 刀架锁紧; 油缸复位;
44
2.5 数控加工自动换刀系统
3) 转塔式更换主轴头自动换刀装置
更换主轴头换刀一般有卧式和立式两种。换 刀时运用转塔旳转位来更换主轴头,以实现自动 换刀。转塔主轴相称于一种转塔刀库。
BT数控ER刀柄的规格范围
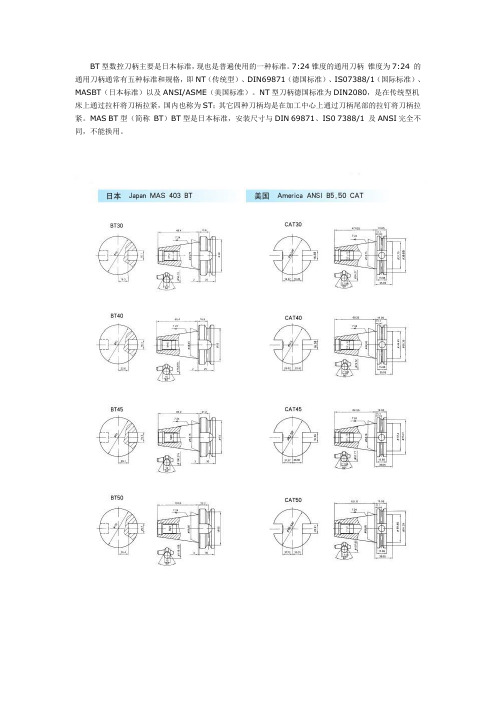
BT型数控刀柄主要是日本标准,现也是普遍使用的一种标准。
7:24锥度的通用刀柄锥度为7:24 的通用刀柄通常有五种标准和规格,即NT(传统型)、DIN69871(德国标准)、IS07388/1(国际标准)、MASBT(日本标准)以及ANSI/ASME(美国标准)。
NT型刀柄德国标准为DIN2080,是在传统型机床上通过拉杆将刀柄拉紧,国内也称为ST;其它四种刀柄均是在加工中心上通过刀柄尾部的拉钉将刀柄拉紧。
MAS BT型(简称BT)BT型是日本标准,安装尺寸与DIN 69871、IS0 7388/1 及ANSI完全不同,不能换用。
BT型刀柄的对称性结构使它比其它三种刀柄的高速稳定性要好。
刀柄有30、35、40、45、50和60的规格,它表示在锥柄某处(具体位置在不同的标准中并不同)直径的大小。
锥体的规格通常是由机床厂商根据机床的有效功率或使用刀具的总体长度来选择的,也与出产国有关(欧洲为DIN标准,美国为ANSI标准,日本为JIS标准)。
常用的刀柄规格30,40,50,其中40应用最广泛。
R筒夹俗称弹簧夹头,是一种装在机床主轴上的钻夹头,其功能是锁紧刀具和主轴的衔接。
ER弹簧夹头由瑞士REGO-FIX公司发明制造。
现今广泛使用于各类机械加工夹持领域。
主要用于钻孔,铣削,铰孔,攻丝和磨削中使用。
因期有16条槽的设计,允许一个较大的夹持范围并同时拥有是佳的径向跳动误差,且分为ER8,ER11,ER16,ER20,ER25,ER32,ER40和ER50这几种规格,实用于所有的刀具夹持。
目前工业市场使用的筒夹材料为:65Mn。
ER筒夹的规格:规格d(H7)D D1 D2 L L1 L2 L3 弹性收缩量ER弹簧夹头8 0.5-5.0 8 8.5 6.5 13.5 2.7 1.5 1.20.5ER弹簧夹头11 1.0-7.0 11 11.5 9.5 18.0 3.8 2.5 2.00.5ER弹簧夹头16 1.0-2.0 16 17 13.8 27.5 6.26 4.0 2.70.5>2.0-10.0 1.0ER弹簧夹头20 1.0-2.5 20 21 17.4 31.5 6.36 4.8 2.80.5 >2.5-13.0 1.0ER弹簧夹头25 1.0-2.5 25 26 22.0 34.0 6.66 5.0 3.10.5 >2.5-16.0 1.0ER弹簧夹头32 2.0-3.5 32 33 29.2 40.0 7.16 5.5 3.60.5 >3.5-20.0 1.0ER弹簧夹头40 3.0-26.0 40 41 36.2 46.0 7.66 7.0 4.11.0 ER弹簧夹头50 6.0-10.0 50 52 46.0 60.0 12.6 8.5 5.51.0 >10.0-34.0 2.0。
数控刀柄标准 JIS B MAS BT

2Technical Data/技术信息Pre-balancedG 6.3 12000 min-1G 2.5 Fine balancing at extra charge动平衡值: G 6.3 /12,000 min-1另可制作G2.5≥18000min-1的精确动平衡刀柄,需另付费Material:Alloyed case hardened steel,tensile strength in the core of min.950 N/mm2 Case hardened HRc60±2 (HV700±50), hardening depth 0.8mm±0.2mm, black-finished and preciselygrinded.Type AD/B:Delivery in form AD, type B closed with a releasable headless screwAccuracy:Cone angle–tolerance exactness<AT3 according to DIN7187 and DIN2080 Max.材质:淬硬合金钢,内部抗拉强度最小为950N/mm2,淬火硬度为HRc60±2(HV700±50), 淬硬层深度为0.8 mm±0.2mm,表面通过发黑和精磨处理。
形式:刀柄交货时为标准AD型冷却,B型冷却孔已用沉头螺钉封住。
精度:刀柄的精度按照德国DIN7187和DIN2080中的AT3标准。
With internal cooling through the collarDelivered with headless screws in closed position端面通内冷却孔交货时端面内冷却孔已用沉头螺钉封住Order No 订货号BT Collect 夹头Clamping rang 夹持范围A D 库存状况312.E16.070*30ER161-107032312.E16.100*30ER161-1010032312.E25.070*30ER252-167042312.E25.100*30ER252-1610042◎312.E32.070*30ER322-207050312.E32.100*30ER322-2010050◎312.E40.070*30ER403-267063412.E16.06340ER161-106332412.E16.10040ER161-1010032412.E16.16040ER161-1016032412.E25.06040ER252-166042412.E25.10040ER252-1610042◎412.E25.16040ER252-1616042◎412.E32.07040ER322-207050412.E32.10040ER322-2010050412.E32.16040ER322-2016050◎412.E40.08040ER403-268063412.E40.10040ER403-2610063◎412.E40.16040ER403-2616063◎512.E16.10050ER161-1010032◎512.E16.16050ER161-1016032◎512.E25.06050ER252-166042◎512.E25.10050ER252-1610042◎512.E25.16050ER252-1616042◎512.E32.07050ER322-207050512.E32.10050ER322-2010050◎512.E32.16050ER322-2016050◎512.E40.08050ER403-268063512.E40.10050ER403-2610063◎512.E40.16050ER403-2616063◎* Form AD* 只提供AD型刀柄非常备库存 ◎Collet chuck ERfor collets according to DIN 6499 to clamp tools with cylindrical shank ER 弹簧夹头刀柄使用DIN 6499标准的ER弹簧夹头用于夹持直柄刀具刀柄 JIS B 6339(MAS 403 BT)。
数控刀具知识点总结归纳
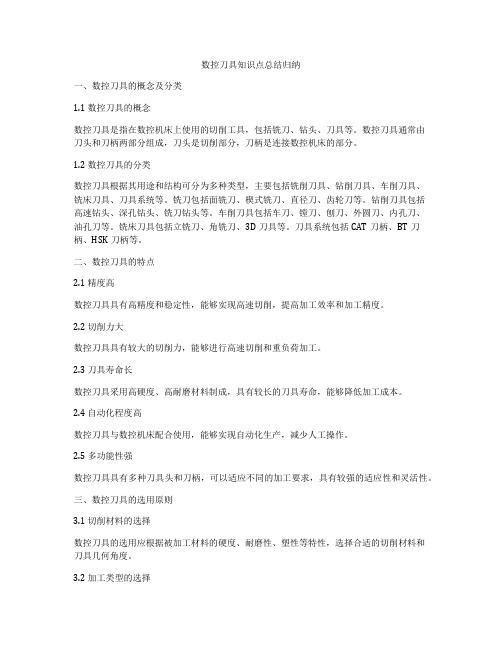
数控刀具知识点总结归纳一、数控刀具的概念及分类1.1 数控刀具的概念数控刀具是指在数控机床上使用的切削工具,包括铣刀、钻头、刀具等。
数控刀具通常由刀头和刀柄两部分组成,刀头是切削部分,刀柄是连接数控机床的部分。
1.2 数控刀具的分类数控刀具根据其用途和结构可分为多种类型,主要包括铣削刀具、钻削刀具、车削刀具、铣床刀具、刀具系统等。
铣刀包括面铣刀、楔式铣刀、直径刀、齿轮刀等。
钻削刀具包括高速钻头、深孔钻头、铣刀钻头等。
车削刀具包括车刀、镗刀、刨刀、外圆刀、内孔刀、油孔刀等。
铣床刀具包括立铣刀、角铣刀、3D刀具等。
刀具系统包括CAT刀柄、BT刀柄、HSK刀柄等。
二、数控刀具的特点2.1 精度高数控刀具具有高精度和稳定性,能够实现高速切削,提高加工效率和加工精度。
2.2 切削力大数控刀具具有较大的切削力,能够进行高速切削和重负荷加工。
2.3 刀具寿命长数控刀具采用高硬度、高耐磨材料制成,具有较长的刀具寿命,能够降低加工成本。
2.4 自动化程度高数控刀具与数控机床配合使用,能够实现自动化生产,减少人工操作。
2.5 多功能性强数控刀具具有多种刀具头和刀柄,可以适应不同的加工要求,具有较强的适应性和灵活性。
三、数控刀具的选用原则3.1 切削材料的选择数控刀具的选用应根据被加工材料的硬度、耐磨性、塑性等特性,选择合适的切削材料和刀具几何角度。
3.2 加工类型的选择数控刀具的选用应考虑加工类型,包括粗加工、精加工、半精加工等,选择合适的刀具结构和材料。
3.3 切削性能的选择数控刀具的选用应考虑切削速度、进给速度和切削深度等切削参数,选择合适的刀具材料和刀具形状。
3.4 经济性的选择数控刀具的选用应考虑加工成本和生产效率,选择经济性合适的刀具。
3.5 安全性的选择数控刀具的选用应考虑刀具的安全性能,包括刀具的断裂、飞溅、抛射等安全因素。
四、数控刀具的保养和维护4.1 刀具的清洁数控刀具在使用前后应进行清洁,去除切削刀具上的杂质和切屑,减少切削面的摩擦和磨损。
数控机床刀柄及连接方式的选择与应用

数控机床刀柄及连接方式的选择与应用数控机床是现代制造业中不可或缺的重要设备之一,它的出现大大提高了加工效率和精度。
而数控机床的刀柄及连接方式对于加工效果和加工质量影响巨大。
本文将对数控机床刀柄及连接方式的选择与应用进行介绍与分析。
首先,数控机床刀柄的选择是十分重要的。
刀柄作为数控机床加工刀具的连接部件,它的质量直接影响到加工效果和刀具寿命。
在选择刀柄时,首先要考虑的是刀具的类型和加工需求。
不同的加工任务对刀柄的要求也不同,比如对于铣削加工,常用的刀柄有直柄、刀臂和组合刀柄等。
而对于车削加工,常用的刀柄有筒柄、槽柄和内螺纹刀柄等。
因此,在选择刀柄时需要根据具体的加工需要进行合理的选择。
其次,刀柄的材料也是影响选择的一个重要因素。
常见的刀柄材料有碳钢、高速钢、硬质合金和陶瓷等。
碳钢刀柄价格低廉,但强度和硬度较低,适用于低强度、低速度的加工。
高速钢刀柄具有较高的强度和硬度,适用于中等强度、中等速度的加工。
硬质合金刀柄具有极高的硬度和耐磨性,适用于高强度、高速度的加工。
陶瓷刀柄具有优异的热稳定性和硬度,适用于高温、高速度的加工。
因此,在选择刀柄材料时需要根据加工强度、速度和材料的特性进行合理的选择。
另外,连接方式也是选择刀柄时需要考虑的一个重要因素。
常见的连接方式有刀片夹持、刀柄夹持和刀柄与机床主轴的连接。
刀片夹持是常见的连接方式,通过夹持机构将刀片固定在刀柄上,适用于铣削加工和一些车削加工。
刀柄夹持是将整个刀柄固定在机床主轴上,适用于车削和镗削等加工。
刀柄与机床主轴的连接方式有直接连接和液压缩变连接等。
直接连接适用于切削力较小的加工,而液压缩变连接适用于切削力较大的加工。
最后,值得注意的是,数控机床刀柄及连接方式的选择与应用需要根据具体的加工任务和机床的性能进行合理的搭配。
不同的切削工艺和材料需要采用不同的刀柄及连接方式,以确保加工质量和效率。
综上所述,数控机床刀柄及连接方式的选择与应用对于加工效果和加工质量至关重要。
1 数控机床常用刀柄的分类

1 数控机床常用刀柄的分类与普通加工方法相比,数控加工对刀具的刚度、精度、耐用度及动平衡性能等方面要求更为严格。
刀具的选择要注重工件的结构与工艺性分析,结合数控机床的加工能力、工件材料及工序内容等因素综合考虑。
数控加工常用刀柄主要分为钻孔刀具刀柄、镗孔刀具刀柄、铣刀类刀柄、螺纹刀具刀柄和直柄刀具类刀柄(立铣刀刀柄和弹簧夹头刀柄)。
2 数控机床常用刀柄的选择刀柄结构形式数控机床刀具刀柄的结构形式分为整体式与模块式两种。
整体式刀柄其装夹刀具的工作部分与它在机床上安装定位用的柄部是一体的。
这种刀柄对机床与零件的变换适应能力较差。
为适应零件与机床的变换,用户必须储备各种规格的刀柄,因此刀柄的利用率较低。
模块式刀具系统是一种较先进的刀具系统,其每把刀柄都可通过各种系列化的模块组装而成。
针对不同的加工零件和使用机床,采取不同的组装方案,可获得多种刀柄系列,从而提高刀柄的适应能力和利用率。
刀柄结构形式的选择应兼顾技术先进与经济合理:①对一些长期反复使用、不需要拼装的简单刀具以配备整体式刀柄为宜,使工具刚性好,价格便宜(如加工零件外轮廓用的立铣刀刀柄、弹簧夹头刀柄及钻夹头刀柄等);②在加工孔径、孔深经常变化的多品种、小批量零件时,宜选用模块式刀柄,以取代大量整体式镗刀柄,降低加工成本;③对数控机床较多尤其是机床主轴端部、换刀机械手各不相同时,宜选用模块式刀柄。
由于各机床所用的中间模块(接杆)和工作模块(装刀模块)都可通用,可大大减少设备投资,提高工具利用率。
刀柄规格数控刀具刀柄多数采用7:24 圆锥工具刀柄,并采用相应型式的拉钉拉紧结构与机床主轴相配合。
刀柄有各种规格,常用的有40 号、45 号和50 号。
目前在我国应用较为广泛的有ISO7388-1983、GB10944-1989、MAS403-1982、ANSI/ASME B5.50-1985 等,选择时应考虑刀柄规格与机床主轴、机械手相适应。
刀柄的规格数量整体式的TSG 工具系统包括20 种刀柄,其规格数量多达数百种,用户可根据所加工的典型零件的数控加工工艺来选取刀柄的品种规格,既可满足加工要求又不致造成积压。
锥度 sk40标准
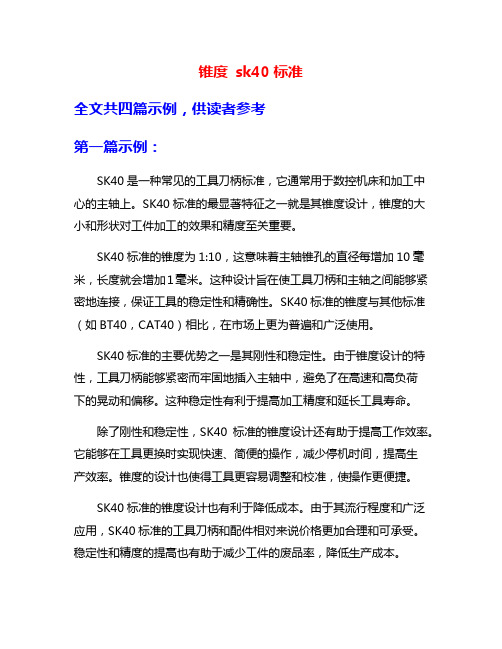
锥度sk40标准全文共四篇示例,供读者参考第一篇示例:SK40是一种常见的工具刀柄标准,它通常用于数控机床和加工中心的主轴上。
SK40标准的最显著特征之一就是其锥度设计,锥度的大小和形状对工件加工的效果和精度至关重要。
SK40标准的锥度为1:10,这意味着主轴锥孔的直径每增加10毫米,长度就会增加1毫米。
这种设计旨在使工具刀柄和主轴之间能够紧密地连接,保证工具的稳定性和精确性。
SK40标准的锥度与其他标准(如BT40,CAT40)相比,在市场上更为普遍和广泛使用。
SK40标准的主要优势之一是其刚性和稳定性。
由于锥度设计的特性,工具刀柄能够紧密而牢固地插入主轴中,避免了在高速和高负荷下的晃动和偏移。
这种稳定性有利于提高加工精度和延长工具寿命。
除了刚性和稳定性,SK40标准的锥度设计还有助于提高工作效率。
它能够在工具更换时实现快速、简便的操作,减少停机时间,提高生产效率。
锥度的设计也使得工具更容易调整和校准,使操作更便捷。
SK40标准的锥度设计也有利于降低成本。
由于其流行程度和广泛应用,SK40标准的工具刀柄和配件相对来说价格更加合理和可承受。
稳定性和精度的提高也有助于减少工件的废品率,降低生产成本。
SK40标准的锥度设计在加工行业中具有重要的地位和作用。
其刚性、稳定性、效率和成本优势使其成为许多加工厂和机床制造商的首选标准。
随着科技的不断发展和进步,SK40标准将继续发挥其重要作用,为工件加工提供更高效、更精确的解决方案。
第二篇示例:锥度是一种常见的工程标准,用于描述工具与工件之间的连接方式。
在机械加工领域,各种工具和设备都需要通过一定的锥度标准来确保其连接牢固、稳定。
本文将重点介绍SK40标准,探讨其特点和应用。
SK40是一种常见的机械连接标准,主要用于夹具和机床之间的连接。
SK40标准定义了连接部件的锥度、角度和尺寸等参数,确保不同设备之间的互换性和兼容性。
SK40标准通常应用于数控机床的主轴和刀柄的连接,可以有效提高加工精度和稳定性。
数控刀柄标准

数控刀柄标准本文有爱数控 提供一.国内应用的数控机床工具柄部及配用拉钉标准1.国家标准GB10944-89《自动换刀机床用7:24圆锥工具柄部40、45和50号圆锥柄》这个国家标准规定的柄部,在型式与尺寸上与国际标准ISO7388/1完全相同。
详见图7.3-1和7.3-1。
与ISO7388/1相比,增加了一些必要的技术要求,标注了表面粗糙度及形位公差,以保证刀柄的制造质量,满足自动加工中刀具的重复换刀精度要求。
它主要应用于镗铣类加工中心机床的各种刀柄。
2.国家标准所规定的拉钉,《自动换刀机床用7:24圆锥工具柄部40、45和50号圆锥柄用拉钉》这个国家标准所规定的拉钉,在型式与尺寸上与ISO7388/Ⅱ相同。
可与前述标准GB10944-89中所规定的柄部配合使用。
3.日本标准JIS B6339-1986《加工中心机床用工具柄部及拉钉》这个标准只适用于日本进口的加工中心机床及过去几年我国的部分机床厂与日本合作设计和生产的加工中心机床。
它是在日本机床工业协会标准MAS403-1982的基础上制订出来的,在日本得到广泛的应用。
我国1985年以后设计的加工中心机床已改用新的国家标准GB10994和GB10945。
4.国家标准GB3837-83《机床工具7:24圆锥联结》这种锥柄主要用于手动换刀数控机床及重型镗铣床等。
二.整体式工具系统标准JB/GQ5010-1983《TSG工具系统型式与尺寸》TSG工具系统中的刀柄,其代号(按1990年国家标准报批稿)由四部分(JT-45-Q32-120)组成,各部分的含义如下:JT-表示工具柄型代码。
45-对圆锥柄表示锥度规格。
Q32-表示工具的规格。
120-表示刀柄的工作长度。
它所表示的工具为:自动换刀机床用7:24圆锥工具柄(GB10944),锥柄为45号,前部为弹簧夹,最大夹持直径32mm,刀柄工作长度(锥柄大端直径φ57.15mm处到弹簧夹头前端面的距离)为120mm。
数控技术的发展趋势

数控技术的发展趋势 中国作为⼀个制造⼤国,主要还是依靠劳动⼒、价格、资源等⽅⾯的⽐较优势,⽽在产品的技术创新与⾃主开发⽅⾯与国外同⾏的差距还很⼤。
下⾯,店铺就为⼤家讲讲数控技术的发展趋势,⼀起来了解⼀下吧! 数控技术的发展趋势 数控技术不仅给传统制造业带来了⾰命性的变化,使制造业成为⼯业化的象征,⽽且随着数控技术的不断发展和应⽤领域的扩⼤,它对国计民⽣的⼀些重要⾏业的发展起着越来越重要的作⽤。
尽管⼗多年前就出现了⾼精度、⾼速度的趋势,但是科学技术的发展是没有⽌境的,⾼精度、⾼速度的内涵也在不断变化,正在向着精度和速度的极限发展。
从世界上数控技术发展的趋势来看,主要有如下⼏个⽅⾯: 1.机床的⾼速化、精密化、智能化、微型化发展 随着汽车、航空航天等⼯业轻合⾦材料的⼴泛应⽤,⾼速加⼯已成为制造技术的重要发展趋势。
⾼速加⼯具有缩短加⼯时间、提⾼加⼯精度和表⾯质量等优点,在模具制造等领域的应⽤也⽇益⼴泛。
机床的⾼速化需要新的数控系统、⾼速电主轴和⾼速伺服进给驱动,以及机床结构的优化和轻量化。
⾼速加⼯不仅是设备本⾝,⽽且是机床、⼑具、⼑柄、夹具和数控编程技术,以及⼈员素质的集成。
⾼速化的最终⽬的是⾼效化,机床仅是实现⾼效的关键之⼀,绝⾮全部,⽣产效率和效益在“⼑尖”上。
2.五轴联动加⼯和复合加⼯机床快速发展 采⽤五轴联动对三维曲⾯零件进⾏加⼯,可⽤⼑具最佳⼏何形状进⾏切削,不仅光洁度⾼,⽽且效率也⼤幅度提⾼。
⼀般认为,1台五轴联动机床的效率可以等于2台三轴联动机床,特别是使⽤⽴⽅氮化硼等超硬材料铣⼑进⾏⾼速铣削淬硬钢零件时,五轴联动加⼯可⽐三轴联动加⼯发挥更⾼的效益。
但过去因五轴联动数控系统主机结构复杂等原因,其价格要⽐三轴联动数控机床⾼出数倍,加之编程技术难度较⼤,制约了五轴联动机床的发展。
当前数控技术的发展,使得实现五轴联动加⼯的复合主轴头结构⼤为简化,其制造难度和成本⼤幅度降低,数控系统的价格差距缩⼩。
数控机床的刀柄选择与使用要点

数控机床的刀柄选择与使用要点刀柄是数控机床上非常重要的配件之一,它直接影响到机床的加工效率和加工质量。
正确选择和使用刀柄对于实现高效加工具有重要意义。
本文将介绍数控机床刀柄的选择和使用要点,供读者参考。
首先,在选择刀柄时应考虑以下几个要点。
刀柄材质:刀柄的材质应根据加工材料的种类和切削性能来选择。
常用的材料有硬质合金、高速钢等。
硬质合金刀柄具有耐磨性好、强度高等特点,适用于加工难加工材料和大批量生产;高速钢刀柄则适用于加工薄壁零件和散热要求高的情况。
刀柄接口:刀柄接口分为直柄和刀杆两种形式。
直柄简单易用,适合加工小批量产品;而刀杆则适合大批量生产,可以提高加工效率。
刀柄长度:刀柄的长度应根据具体的加工情况来选择。
一般来说,加工较深孔或需要进行倒角的工件,应选择较长的刀柄;而加工薄壁零件则需要选择较短的刀柄。
刀柄形状:刀柄的形状应根据加工工件的轮廓和不同切削操作来选择。
常见的刀柄形状有直柄、插削刀柄、铣刀柄等。
直柄适用于钻孔、扩孔和镗孔等操作;插削刀柄适用于斜面、槽面等面铣削;铣刀柄适用于铣削面。
其次,在使用刀柄时还需注意以下要点。
刀柄的安装:刀柄的安装应遵循机床的使用说明书和刀具的生产厂家提供的指导。
安装前需检查刀柄与夹头的匹配度,确认无松动或损坏,以免造成事故或工件加工不合格。
刀柄的保养:刀柄在使用过程中需定期进行保养和清洁。
保持刀柄表面的清洁并定期涂抹润滑油,以减少磨损和延长使用寿命。
同时,应定期检查刀柄是否出现裂纹或变形,如有异常应及时更换。
刀柄的刀具安装:刀柄与刀具的安装应牢固可靠,避免出现刀具脱落或垂直度偏差过大的情况。
在安装过程中应确保刀具与工件的角度、位置和切削深度等参数符合要求。
刀柄的切削参数:刀柄在使用过程中需要根据具体加工工件选择合适的切削参数,如切削速度和进给速度。
选择合适的切削参数有助于提高加工效率和加工质量。
刀柄的修磨和更换:刀柄在经过一段时间的使用后,可能会出现磨损或损坏的情况。
HSK-100A型刀柄/主轴联接性能分析

量 的变 化对 刀柄 / 主轴联 接所 受接 触应 : 匀的影 响 。
2 1 夹 紧力 变化 对 接 触 应 力 的 影 响 .
HS K刀柄 夹 紧是利 用锥 面定 位 夹 紧 和端 面定 位夹紧H , 其夹紧力 的作用体现在以下 2个方面: J ( ) 服刀 柄和 主轴 锥 孔 接 触处 产生 的摩擦 阻力 ; 1克 () 2 产生 端 面接触 的实 际夹 紧力 。
20 9 ) 10 4
摘 要 : 机床 主 轴与 刀具相 联接 的 刀柄 是 影响 机床 加 工精 度 、 将 刀具 磨 损 及加 工 效率 的 关键 部 件 。
针 对 高速 切 削对 刀柄 的要 求 , 立 了 HS 建 K一10 0 A型 刀柄 的 三维 实体模 型 , 同时利 用有 限元 方 法 , 对 影 响 HS K一10 型 刀柄 / 0A 主轴 联接 性 能 的参 数进 行 了分析 , HS 刀柄的 实 际应 用提 供 一 定 为 K
1 建 立有 限 元模 型
由于 刀 柄 的几 何 形 状 以及 刀 柄 在 高速 旋 转 时 所 受离 心力 均 为轴对 称 , 以有 限元模 型可 以采用 所
在 A S S中分析不 同夹 紧力下 H K 刀柄/ NY S 主轴接触锥面的联接情况 , 主要分析在不同夹紧力
下 锥 面接触 应 力 和端 面接 触 应力 的变 化 情况 。其 中采用 过盈 量 为 8 m, 速为 1 0rmi, 紧力 转 20 0/ n 夹 分别 取 3k 4k 4 k 5 k 5 N、0 N、5 N、0 N。分 析 结 果 数 据
高速生产 的需要 , :4锥度实心长柄存在锥 柄质 72 量 大 、 度 长 、 向精 度低 、 持外 径小 等不 足 。早 长 轴 支 在2 0世 纪 9 0年 代 , 国亚琛 工业 大! R H 德 学( WT A ce) 床研 究 所 就 研 制 出 了一 种 新 型 高速 刀 ahn机
- 1、下载文档前请自行甄别文档内容的完整性,平台不提供额外的编辑、内容补充、找答案等附加服务。
- 2、"仅部分预览"的文档,不可在线预览部分如存在完整性等问题,可反馈申请退款(可完整预览的文档不适用该条件!)。
- 3、如文档侵犯您的权益,请联系客服反馈,我们会尽快为您处理(人工客服工作时间:9:00-18:30)。
最近推出的一些切削刀具概念使医疗行业的小零件加工更为高效,并且大幅提升了生产效率。
尤其是用于小零件加工的纵切机床得到进一步发展,也带动了切削刀具不断推陈出新,由此便可提供最大化机床利用率所需的高性能。
某些切削刀具领域已提升到新的性能水平–螺纹旋风铣和采用高压冷却(HPC)功能的车削就是两个突出的例子。
随着制造业的竞争压力越来越大,大批量生产高性能金属材料的数控刀柄,也呈增加之势。
医疗行业的供应商通常会面临这种情况,其中诸如此类产品的加工量在日益增加,螺纹旋风铣是成熟的加工方法。
该工序的固有稳定性使其非常适合于大批量生产和加工要求苛刻的金属。
旋风铣时可采用更为坚固的切削刃,这样就为推出耐磨性更高的新刀具材料提供了更多可能性。
其益处是HSK刀具使用寿命的延长,这意味着生产中的机床停机时间的缩短。
另外,切削刃的刃线韧性得到改善,使切削刃更加锋利,切削时也更安全。
在其他加工领域合理利用这些技术进步,并开发出适合小零件旋风铣的特殊可转位刀片和刀具,由此而巩固制造医疗零件的经济优势。
刀片技术的不断发展为改进切削刃提供了更大空间,以充分利用螺纹旋风铣加工方法的诸多好处。
例如,采用涂层硬质合金刀片可获得更长且更易预测的刀具寿命,并且能够应用更高的切削速度。
这就导致了更高的零件产出,并使公差和表面光洁度保持一致。
新刀片材质(比如具有PVD/TiAlN涂层的材质)具有独特的薄涂层,与HSK刀柄基体的附着力极佳。
这种材质非常适合于加工螺纹旋风铣所用的各种工件材料(比如接骨螺钉所采用的金属材料)。
高切削数控刀柄性能发展趋势:
1. 较高的系统精度
系统精度包括系统定位夹持精度和刀具重复定位精度,前者指刀具与数控刀柄、刀柄与机床主轴的连接精度;后者指每次换刀后刀具系统精度的一致性。
刀具系统具有较高的系统精度,才能保证高速加工条件下刀具系统应有的静态和动态稳定性。
2. 较高的系统刚度
刀具系统的静、动刚度是影响加工精度及切削性能的重要因素。
刀具系统刚度不足会导致刀具系统振动,从而降低加工精度,并加剧刀具的磨损,降低刀具的使用寿命。
3. 较好的动平衡性
高速切削加工条件下,微小质量的不平衡都会造成巨大的离心力,在加工过程中引起机床的急剧振动。
因此,高速刀具系统的动平衡非常重要。