罩式退火和连续退火优缺点
(完整word版)连续退火与罩式退火工艺比较_F

邯钢附企公司冷轧工程连续退火与罩式退火工艺比较10:29 AM目录1.概述 (1)2.两种工艺的比较 (2)2.1罩式退火工艺 (2)2.2 连续退火工艺 (4)2.3 两种退火工艺比较 (4)2.4 连续退火工艺的优势 (5)2.5实例 (6)3.生产成本比较 (8)4。
工程投资比较 (9)5.工程退火工艺选择建议 (9)1.概述带钢经过冷轧机大压下率冷轧,晶粒组织被延伸和硬化,不能进行进一步的加工成形,因此必须进行再结晶退火,控制晶粒的成长形成适当的组织,恢复材料塑性,这就是退火的目的。
低碳钢的退火通常是在还原性气氛中加热到A1点温度附近,并在该温度下保温一段时间后冷却,这种退火称为光亮退火。
根据退火炉的形式和操作方法可分为罩式退火工艺和连续退火工艺。
罩式退火工艺(也称为分批退火)是指对冷轧后的钢卷按工序顺序分别在脱脂机组(若需要)、罩式退火炉、平整机组、重卷机组进行相应处理,以整卷分批次退火生产冷轧商品卷的工艺。
在罩式退火工序,钢卷除装炉和卸炉外,以紧卷方式在炉内按一定卷数堆垛、静止放置,随炉温升降而加热和冷却。
罩式退火时钢卷有充分的加热和均热时间,使晶粒生长和取向结晶增加,通过缓慢的冷却过程使均热时多余的固溶碳和氮充分析出,得到良好的材质.紧卷的缺点在于热量传到钢卷内部缓慢,生产率低;由于钢卷多层叠压,造成各层钢卷间和同一钢卷内有温度差,这样钢卷沿长度方向机械性能不均;同时冷却时,紧卷收缩易造成带钢粘连。
连续退火工艺是将清洗、退火、平整、拉矫和分卷等工序集成在一条连续生产线上,将带钢进行连续展开退火生产冷轧商品卷的工艺。
具有生产周期短、布置紧凑、便于生产管理、劳动生产率高以及产品质量优良等优点。
因为连续生产,退火周期非常短,仅5分钟左右。
用连续退火时其特有的快速加热和冷却可得到较硬的材质,早期的连续退火机组大都用于硬质镀锡原板生产,不作为软钢板的退火。
近些年来通过钢的成分调整和热轧高温卷取使再结晶晶粒变大,经短时间过时效处理固溶碳完全析出,可以用连续退火生产有深冲性的冷轧钢板。
340MPa 高强IF 钢冷轧薄板罩式退火工艺研究

340MPa 高强IF 钢冷轧薄板罩式退火工艺研究王宝景北京科技大学分类号:____________密 级:______________ UDC:____________ 单位代码:______________北京科技大学硕士学位论文论文题目:340MPa 高强IF 钢冷轧薄板罩式退火工艺研究学 号:_________________________作 者:_________________________专 业 名 称:_________________________2004年02月26日王宝景 公开 10008 材料加工工程 S2*******TG156.2北京科技大学硕士学位论文论文题目:作者:_________________________指 导 教 师: 单位:协助指导教师: 单位:单位:论文提交日期:2004年 02月 26日学位授予单位:北 京 科 技 大 学王先进 教授北京科技大学 康永林 教授北京科技大学 340MPa 高强IF 钢冷轧薄板罩式退火工艺研究 王宝景340MPa高强IF钢冷轧薄板罩式退火工艺研究Study of Batch Annealing Technology on the Cold-Rolled 340MPa Grade HighStrength Steel Sheet研究生姓名:王宝景指导教师姓名:王先进北京科技大学材料学院北京100083,中国Candidate: Wang BaojingSupervisor: Wang XianjinSchool of MaterialsUniversity of Science and Technology Beijing30 Xueyuan Road,Haidian DistrictBeijing 100083,P.R.CHINA独创性说明本人郑重声明:所呈交的论文是我个人在导师指导下进行的研究工作及取得研究成果。
罩式退火炉介绍.

4、退火周期示意图
加热
均热
空气/水冷却
冷却
在室温下,原子的动能少,扩散 力差,扩散速度慢,导致这种倾向无 法实现,须施加激活力,这种激活力 就是将钢加热到一定温度,使原子获 得足够的扩散动能,消除晶格畸变, 使组织、性能发生变化。
因此经过冷轧后的钢材必须经过 退火。
2、退火的目的及作用
退火是将带钢加热到一定的温度保温后再冷却的工 艺操作。
a 立式炉 b 卧式炉 2、间歇式退火炉(罩式炉) a 单垛式 b 多垛式
三、强对流全氢罩式炉技术特点
1、强对流
罩式退火炉通过内罩对 带钢进行间接加热,带钢获得 热量多少取决于内罩壁的辐射 传热和气体对流传热的能力。
增加内罩壁与保护气体 之间对流传热的主要途径是加 大保护气体的流速,采用保护 气体流速高、流量大的循环系 统,把内罩上的热量尽快传递 给钢卷。
φ610 mm
最大钢卷重量: 33.3t
最大堆垛高度: 5500mm
2、车间配置
冷却罩
内罩 加热罩
炉台
对流板 终冷台
运卷车
阀站
放加 热罩及 点火
冷密封 测试及 吹扫
放内罩 及压紧装料源自退火吊加热罩, 扣冷却罩
风冷
喷淋
吊冷 却罩
移走 内罩
等待下一次装料
卸料至 终冷台 冷却
完 成
3、罩式炉工艺操作流程
罩式退火炉介绍
介绍内容
一、为什么要退火? 二、退火炉分类 三、强对流全氢罩式炉技术特点 四、罩式退火炉车间简介
一、为什么要退火?
1、冷轧板的组织结构 钢材经过冷轧变形后金属内部组
织产生晶粒拉长、晶粒破碎和晶体缺 陷大量存在现象,导致金属内部自由 能升高,处于不稳定状态,具有自发 地恢复到比较完整、规则和自由能低 稳定状态的趋势。
冷轧罩式退火工艺及原理201807

应力过大造成的粘结风险,尤其对于特殊规格,根据实际温度差采用
相应时间的带罩缓慢冷却,降低冷却过程中的压应力,最大程度上减 少粘结风险;同时合理配炉,采用规格和卷位的合理搭配,减少易发
生粘结钢卷的粘结倾向。
• 平整生产的张力和速度控制:对于粘结较严重的钢卷在采用大张力和 高速生产,大于500m/min,使粘结情况减弱。
轧钢工培训材料
2018年7月
罩式退火工艺及原理
1、冷轧工序组织变化 2、退火原因 3、退火目的及作用 4、罩退与连续退火线比较 5、罩式退火工艺流程图 6、常用退火工艺曲线 7、罩式退火温度分布特点 8、退火粘结问题 9、钢卷在加热过程热应力分布
1、冷轧工序组织变化
酸轧工序压下率控制标准,以及带 钢组织演变机理和特点
加热过程的温度分布
冷却过程的温度分布
因钢卷整卷退火,在退火过程中温度存在差异。加热过程中,钢卷 外圈温度高芯部温度低,钢卷膨胀外圈受拉应力,内圈受压应力; 反之在冷却过程中外圈温度低芯部温度高,钢卷整体外圈受压应力 ,内圈受拉应力。
8、退火粘结问题
在冷硬卷的紧卷立卷再结晶退火过程中,经常发生相邻卷层间粘到一 起,增加了后道工序平整机的开卷张力,并且在开卷过程中会造成板 带撕裂,出现皱痕等情况,并且因同样的粘结力会造成不同程度板形 缺陷,这种缺陷就是我们通常称为的罩式炉粘钢。
4、罩退与连续退火线比较区别
• 罩式退火:生产周期长(几十个小时), 与清洗线、平整线分开布置,整体联成一条冷板生产流程,但 可选择的进行脱脂清洗,且钢种及规格对整体生产的影响较小, 可小批量灵活的组织生产,单炉台生产,炉台数量可根据产量 和品种变化随时增减,中间工序有库存缓冲,产量和品种适应 能力强,适合多品种,小批量生产及试验生产。 • 连续退火:生产周期短(几分钟),脱脂清洗、退火、平整联 成一条整体生产线,生产效率高,但受计划影响启停和规格品 种切换等成本高,产品规格覆盖范围不宜太宽, 产量不宜太低。 适合大批量,少品种生产。
罩式炉功能概述
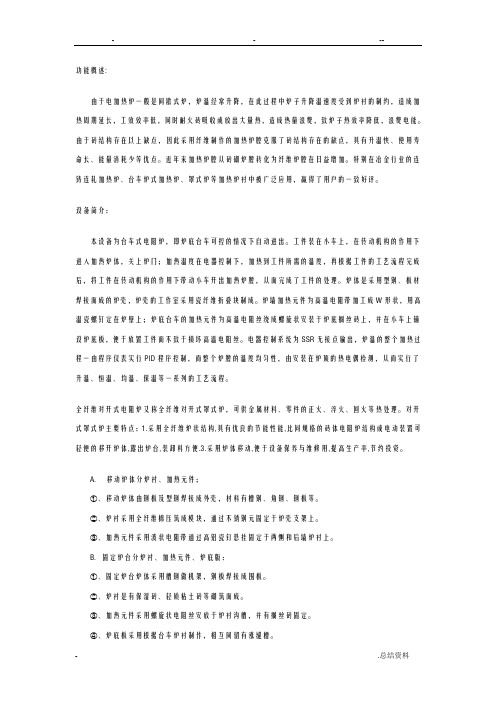
功能概述:由于电加热炉一般是间歇式炉,炉温经常升降,在此过程中炉子升降温速度受到炉衬的制约,造成加热周期延长,工效效率低,同时耐火砖吸收或放出大量热,造成热量浪费,致炉子热效率降低,浪费电能。
由于砖结构存在以上缺点,因此采用纤维制作的加热炉膛克服了砖结构存在的缺点,具有升温快、使用寿命长、能量消耗少等优点。
近年来加热炉膛从砖砌炉膛转化为纤维炉膛在日益增加。
特别在冶金行业的连铸连轧加热炉、台车炉式加热炉、罩式炉等加热炉衬中被广泛应用,赢得了用户的一致好评。
设备简介:本设备为台车式电阻炉,即炉底台车可控的情况下自动进出。
工件装在小车上,在传动机构的作用下进入加热炉体,关上炉门;加热温度在电器控制下,加热到工件所需的温度,再根据工件的工艺流程完成后,将工件在传动机构的作用下带动小车开出加热炉膛,从而完成了工件的处理。
炉体是采用型钢、板材焊接而成的炉壳,炉壳的工作室采用瓷纤维折叠块制成。
炉墙加热元件为高温电阻带加工成W形状,用高温瓷螺钉定在炉壁上;炉底台车的加热元件为高温电阻丝绕成螺旋状安装于炉底搁丝砖上,并在小车上铺设炉底板,便于放置工件而不致于损坏高温电阻丝。
电器控制系统为SSR无接点输出,炉温的整个加热过程一由程序仪表实行PID程序控制,而整个炉膛的温度均匀性,由安装在炉顶的热电偶检测,从而实行了升温、恒温、均温、保温等一系列的工艺流程。
全纤维对开式电阻炉又称全纤维对开式罩式炉,可供金属材料、零件的正火、淬火、回火等热处理。
对开式罩式炉主要特点:1.采用全纤维炉状结构,具有优良的节能性能,比同规格的砖体电阻炉结构或电动装置可轻便的移开炉体,露出炉台,装卸料方便.3.采用炉体移动,便于设备保养与维修用,提高生产率,节约投资。
A.移动炉体分炉衬、加热元件;①、移动炉体由钢板及型钢焊接成外壳,材料有槽钢、角钢、钢板等。
②、炉衬采用全纤维棉压筑成模块,通过不锈钢元固定于炉壳支架上。
③、加热元件采用波状电阻带通过高铝瓷钉悬挂固定于两恻和后墙炉衬上。
退火粘接分析

退火粘接分析罩式退火粘接分析及治理1、前言退火是冷轧钢带不可缺少的一个重要生产工序,其主要目的:消除钢带冷轧变形产生的加工硬化和内应力,使带钢具有客户要求的金相组织、良好的机械性能和光亮的表面。
退火炉有罩式退火和连续退火两种形式,其中罩式退火以投资省、占地面积小、生产组织灵活、适合品种钢开发等优点在中小企业得到广泛的应用,但罩式退火的生产特点决定了在罩式退火过程中容易出现粘结缺陷,使得产品质量降级甚至判废。
莱芜市泰山冷轧板有限公司950产线以SPCC为主,产品规格主要集中在0.15-0.5mm*712-830mm,退火采用的是罩式退火,产品质量稳定。
但进入2011年后粘接缺陷在冷轧内部缺陷中一直处于首位,严重影响了产品质量的提升和企业的信誉和效益,因此有必要对造成粘接缺陷的因素进行系统分析并彻底根治。
2、粘接缺陷机理分析关于罩式炉中产品粘接的机理在国内外众多刊物上都有介绍和分析,究其根本原因是:在退火过程中钢卷内部存在温度梯度和压应力,高温作用下局部压应力过大超过屈服极限而产生塑性变形,处于热激活状态的铁原子发生跨金属界面迁移在界面处形成共生晶粒而产生粘接。
钢卷内部的压应力主要是由两部分组成:一部分是退火温度变化而带来的热应力,主要取决于退火工艺制度;另外一部分则是钢卷进入退火炉之前的原始内应力,主要取决于轧机或脱脂机组卷取张力的设定。
在加热阶段,钢卷内外层升温速率大于芯部,造成外层与芯部间压应力减小,内层与芯部间压应力增大,使得内层与芯部之间的钢带存在粘接趋势。
在冷却阶段,内外层降温速率大于芯部.造成外层与芯部间因冷缩不均匀产生较大压应力。
尤其在冷却初始骱段,温度梯度逐渐增大,压应力也随之增大。
当卷芯温度降至一定温度时,卷芯与外层温度梯度最大,压应力也最大,使得外层与芯部之间的钢带存在粘接趋势。
在高温作用下带卷的屈服强度大幅降低,带卷层与层之间在压应力作用下局部(厚度不均、凸起部位)会产生塑性变形,使层间接触面积显著增大,界面间铁原于扩散速度加快,当扩散层达到一定深度,即形成粘结。
环行罩式退火炉简介

环行罩式退火炉简介蒋铭才 (科学技术协会)摘 要 环行罩式退火炉是一种连续作业炉,其突出优点是热效率高,经济效益好。
关键词 环行 罩式 退火炉1 前言目前国内外使用的罩式退火炉多为间歇式炉,自动化程度低、劳动强度大、能耗高、经济效益有待提高。
硅钢退火的环行罩式退火炉较好地解决了这些问题。
2 ROF 炉简介2.1 ROF 炉的基本结构与退火工艺二十世纪末,武汉钢铁集团公司建造了我国最大的环行罩式退火炉--ROF 炉。
ROF 炉是日本新日铁公司在美国A llegeny 钢铁公司取向硅钢隧道式退火炉技术基础上发展起来的新型退火炉,是国际国内最先进的热工设备。
ROF 炉为旋转炉底明火罩式连续退火炉,主要设备为环状形隧道炉体(简称环状炉体)、多部台车组成的环状形炉底(简称环状炉底)和内罩。
由液压设施传动的环状炉底在环状炉体内作周而复始的间歇圆周运动,从而实现连续作业。
环状炉底上装有内罩、底板、立柱各50个以及被退火的钢卷2 50个,见图1。
图1 ROF 炉部分结构示意钢卷按顺序排列成50组,每组并排两个钢卷,算作一个段。
按退火工艺和退火周期,每个工艺段包含的段数见图2。
图2 ROF 炉退火工艺制度钢卷的退火过程为:一、首先经P H 工艺段(1-2段)预热;二、经1S 工艺段(3-8段)进行均热、脱水;三、、经1H 工艺段(9-19段)加热;四、经2S 工艺段(20-29段)保温;五再依次经1C 工艺段(30-33段)、2C 工艺段(34-38段)、3C 工艺段(39-43段)、4C (44-48段)工艺段冷却;六、最后经(49-50段)出炉,完成整个退火工序。
ROF 炉工艺稳定,根据各种钢卷的退火曲线不同,其工艺段的长度和温度可按需要变化。
2.2 ROF 炉的不足虽然ROF 炉是当前世界上最先进的连续退火炉,但有两个不足:一、传输保护气体的换向阀存在动密封,易泄露;二、ROF 炉只能在最初运转时,分析内罩里的气体成分和测定露点。
钢铁工业退火板卷-连续退火法、罩式退火法的系数计算

钢铁工业退火板卷-连续退火法、罩式退火法的系数计算钢铁工业中,退火是一种重要的热处理工艺,用于改善钢材的力学性能和组织结构。
在退火过程中,常用的两种方法是连续退火法和罩式退火法。
1. 连续退火法:连续退火法是指将钢板卷通过连续生产线进行退火。
在连续退火过程中,钢板经过预热、退火、冷却等多个连续阶段。
该方法可以有效提高生产效率。
计算连续退火法的系数时,通常需要考虑以下几个因素:a. 加热速度:加热速度对退火效果有很大影响,通常以升温速度来表示。
升温速度越快,钢板的退火效果越差。
系数可根据实际经验确定。
b. 保温时间:保温时间是指钢板在退火温度下停留的时间。
保温时间越长,退火效果越好。
系数可根据实际经验确定。
c. 冷却速度:冷却速度是指钢板从退火温度降温的速度。
冷却速度越慢,退火效果越好。
系数可根据实际经验确定。
2. 罩式退火法:罩式退火法是指将钢板卷放入具有特定气氛的容器中进行退火。
在罩式退火过程中,钢板表面被罩中的气氛包围,并通过加热使其均匀退火。
该方法常用于对钢板表面进行退火,以达到改善表面性能的目的。
计算罩式退火法的系数时,主要考虑以下几个因素:a. 罩气体成分:罩气体成分对钢板的退火效果有很大影响,通常要求罩气体中含有一定的还原性气体(如氢气)。
系数可根据实际经验确定。
b. 罩气体压力:罩气体的压力对退火效果有一定影响。
通常要求罩气体的压力保持在一定范围内。
系数可根据实际经验确定。
c. 加热温度:加热温度是罩式退火的关键参数之一。
加热温度越高,退火效果越好,但同时也会增加能耗和材料损失。
系数可根据实际经验确定。
以上是钢铁工业中连续退火法和罩式退火法系数计算的一些基本考虑因素,具体系数的确定需要结合实际生产情况和工艺要求,通过试验和经验总结来确定。
罩式退火机组工艺介绍
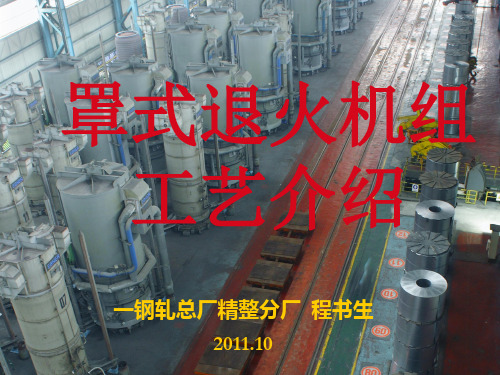
27
谢谢大家
28
谢谢大家! 谢谢大家!
2011.7
29
内罩的作用:封闭炉台钢 卷,使钢卷与外界隔绝, 使钢卷在氢气气氛下退火; 内罩高度为6.28米,采用 波纹式设计,主要是为了 扩大热传导面以及使得加 热、冷却时受力均匀; 一般情况下,一炉里面装 有4~5卷钢卷;
11
2.罩式退火机组介绍-加热罩
加热罩的作用:对钢卷进 行加热、保温; 加热罩上下两层共8个煤气 烧嘴,另加一个废氢烧嘴; 采用的是焦炉煤气做为热 源;加热罩最高工作温度 为870度,我们现在采用的 加热罩设定最高温度为850 度;另外每个加热罩上有 一个换热器,可通过吸收 烟道废气的余热来预热助 燃空气;
17
2.罩式退火机组介绍—工艺参数
罩式退火机组关键的工艺参数有三个参数,分 别为热点温度、冷点温度以及出炉温度,冷点 温度的设置是否合理与实际生产中能否真正达 到所设定的冷点温度,都直接影响钢卷的性能; 罩式退火机组的加热时间、冷却时间都与上述 三个参数有关,都是由上述三个参数以及钢卷 本身的如厚度、宽度、重量等参数确定出来;
模型的建立为整个 罩式退火工艺最关 键的部分,涉及大 量传热的知识与计 算 计算机模型 计算出需多少时间冷 却能使卷芯温度低于 钢卷氧化温度
2.罩式退火机组介绍之工艺曲线
20
3.罩式退火机组生产特点
罩式退火机组的生产特点是: 1、不受规格与品种的限制,生产灵活,非连续 性生产。 2、加热时间与冷却时间全部由计算机控制; 3、生产周期长; 4、产品性能稳定、能适应不同的需要; 5、产能的释放依靠不了机组速度,而影响产能 的释放受外界的影响因素多;
18
2.罩式退火机组介绍—工艺参数
钢卷厚度 钢卷宽度 炉台所装卷数 整个炉台所装重量 钢种等级(冷点温度) 热点温度 钢卷厚度 钢卷宽度 炉台所装卷数 整个炉台所装重量 钢种等级(冷点温度) 热点温度 钢卷氧化温度(160度)
冷轧罩式退火介绍

气体气氛露点、工作载荷空间的密封性三大方面
主要集中在以下几个方面:
人为错误提高出炉温度(使得出炉后,卷心温度高于氧化温度
160度)、热电偶检测错误、冷却速度过快、工作载荷空间内氢气循 环量不足、氢气氮气纯度不够、炉台表面不清洁不干燥、工作载荷空 间的设备表面有水分、炉台密封圈老化、内罩有裂缝、通往炉内的管 道不密封。
热应力在罩式退火机组肯定存在,不能避免,而热应力的影响 因素主要受加热冷却速度、板形(特别是中浪) 、卷取张力等; 氧化色:
氧化色是由于钢卷在高温下接触氧气而形成的钢卷表面与氧气 反应而生成的一种表面淡黄色或黄色的氧化现象, 氧化色缺陷给冷轧 产品出厂后给涂镀或外观带来一定量的损失; 氧化色是一种可逆缺陷, 如果发现及时,可修复;
粘结:粘接为罩式炉特有缺陷,其特征是形貌呈月牙形,是有 曲线形状的应变条纹带钢在退火过程中有时产生局部粘接, 造成平整 开卷时粘接处发生撕裂变形、凸起,经平整后形成弯月状、马蹄状或 弧形的凹印。因粘接处变形产生加工硬化、塑性降低、冲压性能差使 带钢产生部分或整卷的废次品。 因此,对于用罩式退火炉来进行消除 酸轧轧后带钢产生的内应力的冷轧产品生产厂家来说, 如何预防、 减 少粘接的产生,提高产品的合格率是各冷轧产品生产厂家所面临的重 要课题之一。
对于不同的材料来说,其再结晶温度不一样,没有固定值,在 实际生产中,可调整的影响因素是变形程度、加热速度;变形程序越 大,再结晶温度越底,加热速度极快或慢都会使再结晶温度升高。
罩式退火机构成:
全封闭炉台
内罩
加热罩
冷却罩
终冷台
对流板
目前,罩式退火机组所退的品种除原来所设计的CQ、DQ、DDQ
带钢连续退火工艺技术介绍

带钢在热轧时,就必须满足合适的条件,诸如完全析出以及粗大的碳化物和氮化物的生成。均匀一致大的铁素体晶粒。
连续退火处理的低碳钢深冲性较差是因为在过时效处理期间钢组织内部所形成细微碳化物弥散所至,因此在连续退火里,只有通过采用IF钢,才能获得特深冲级别的高rm和nm值。对IF钢的罩式退火和连续退火来讲,二者的组织结构之间没有显著的区别(见图12.5.2.5B-3)。
从金相的观点来看,采用连续退火生产冷轧高强钢具有潜在的优越性,譬如通过形成精细晶粒结构和精细碳化物析出,可用来提高钢的屈服强度(2)。
连续退火过程中加热期间,带钢中碳化物结构将部分或完全被溶解.这取决于含碳量以及碳化物的大小,如图12.5.2.5B-1所示。该过程还受加热速度快慢、退火温度高低和碳化物粗大程度的反作用影响。
钢被加热到退火温度并均热后,碳的溶解达到了平衡,并且根据退火温度会发生有限的晶粒生长。然而,连续退火机组里较高的冷却速度阻碍了固溶碳的析出,使其在冷却阶段的碳化物析出偏离平衡,只有通过调整冷却和过时效参数,才能控制碳化物的分布和固溶碳含量,从而获得合适的机械性能并消除时效影响。
使用这二种方法的不同退火周期,可以制造各种质量的钢种,包括CQ(商用级),DQ(冲压级),DDQ(深冲级),HSS(高强钢)等品种。
(1) 低碳软钢、商用钢和冲压钢的连续退火原理(3)
冷轧板要求具备如下的可成形性:CQ板延展性、DQ板的延展性和慢速时效性(低屈服点延长)、DDQ板延展性和非时效性(几乎无屈服点延长)和深冲性(Landford值)。
板带生产过程中退火工序的比较

XINCAILIAOXINZHUANGSHII新材料新装饰板带生产过程中退火工序的比较杨柳(中冶华天工程技术有限公司243000)摘要:本文就板带生产过程中后续热处理方式做了阐述,并从生产工艺、产品质量、设备投资、运行能耗几个方面做了较为深入的论析与比较关键词:罩式退火、连续退火0 引言在板带生产过程中,冷轧大压下率轧制后,必须经过退火处理,以消除内应力,使得结晶再恢复,从而使产品的机械性能利于最终客户进行冲压、拆弯等再加工处理。
根据设备不同,退火又分为罩式退火与连续退火,两种退火工艺各自有优缺点。
1生产工艺的比较1.1 罩式退火板带生产的变化分为三个阶段:沸腾钢、镇静钢、无间隙原子钢,目前,镇静钢是板带生产的主流,而罩式退火最早是针对镇静钢开发出来的,因此,罩式退火炉用于当前的的生产能够有效的保证产品的性能,而无间隙原子钢是未来特种钢发展的趋势,在生产无间隙原子钢方面,罩退机组有着先天性的劣势,冷却速度远远达不到要求,因此无法生产诸如无间隙原子钢等高强度钢板。
罩式退火设备包括:炉台、加热罩、冷却罩、内罩,可根据需要布置炉台以及加热罩、冷却罩、内罩的数目。
工艺流程:冷轧钢卷、上料、内罩放置到炉台上并夹紧、冷泄露试验、初次吹扫、压力控制、加热工序、保温时的泄露测试、(空冷+水冷)冷却、最后吹扫、卸料、最终冷却。
1.2 连续退火连续退火工艺将钢卷的脱脂、退火、平整、拉矫、切边、涂油等工序综合到同一条生产线上,生产周期十分短,但对原料的化学成分、热轧工艺冷轧工艺等要求较求。
因此其设备也比较复杂,对于场地要求也较高;工艺流程一般为:入口步进梁、开卷、切头、焊接、月牙剪切边、清洗、入口活套、立式(卧式)再结晶退火炉、出口活套、平整机、矫直机、检查活套(平台)、切边剪、出口测宽、检查平台、涂油机、卷取机;1.3 两种退火参数的比较加热和冷却参数罩退连退加热速度(℃/S)10-210再结晶温度范围(℃)560~680 650~800退火温度(℃)650~710 700~880冷却速度(℃/s)10-3101~3退火周期2~3天4~8min1.4 两种退火原理的比较罩式退火整个退火过程工艺包括提高深冲性决定因素(再结晶织构形成)的升温段、提高延展性(晶粒和析出物大小)的保温段以及防止时效(固熔碳和氮)的冷却段,整个退火周期约2~3天;连续退火整个退火过程工艺包括急速升温使热轧高温卷取的板带形成粗碳化合物阶段、短暂保温使晶粒长大的阶段、急速冷却阶段、过时效工艺(使碳和氮部分固熔部分析出)阶段;2产品质量的比较罩式退火的产品质量缺陷:粘结、氧化色、碳化边;退火后板形不受控制。
冷轧各工序质量缺陷汇

冷轧各工序质量缺陷汇总冷轧带钢的生产工序流程主要包括:热轧来料、推拉式盐酸酸洗、单机可逆冷轧、电解脱脂清洗、全氢(或氮氢)退火炉、单机平整、重卷纵切(或横切)、拉伸弯曲矫直、包装储存和运输等。
为使全体干部职工对各生产工序有可能造成的产品质量缺陷有一全面了解,以达到全员、全过程控制的目的,现将冷轧各工序有可能产生或存在的质量缺陷汇总如下:一、酸洗工序在酸洗过程中由于工艺参数控制不当,操作不认真或操作失误,将影响酸洗质量,产生各种缺陷,归纳起来缺陷的品种有:酸洗气泡(氢气病),过酸洗,欠酸洗,锈蚀,夹杂,划伤,压痕等,占冷轧产品缺陷的2%左右。
1、酸洗气泡由于酸与裸露的金属作用,生成氢所造成的,外观特征是条状的小鼓泡,破裂后呈黑色细裂缝,冷轧时气泡破裂及延伸扩大,降低产品的冲击韧性。
2、过酸洗金属在酸液中停留时间过长,使金属表面在酸液作用下变得粗糙麻面的现象。
产生的主要原因:开卷、焊接时间过长,穿带时间过长,机械故障停机,调配酸液浓度时停机等,使金属在酸液中滞留时间过长所致,一旦出现过酸洗,将严重影响带材质量,也给轧制生产带来困难:延伸性降低,容易断带、粘轻,很难轧出成品。
3、欠酸洗带钢酸洗后,表面残留局部未酸洗掉的氧化铁皮时称为欠酸洗。
产生的原因:带钢表面严重氧化,氧化皮厚薄不均,较厚的氧化皮需较长的酸洗时间。
酸液的温度低,浓度低,运行速度快,铁盐含量过高等,另外矫直不彻底,波浪大,酸洗时局部未浸泡在酸液中,也容易产生欠酸洗。
一旦出现欠酸洗,在轧制时使产品表面出现暗色,严重时氧化皮压入,形成条状照斑。
4、锈蚀带钢酸洗后表面重新出现锈层的现象叫锈蚀。
产生的原因:清洗槽水中的酸含量超标,带钢清洗后没有完全干燥,表面上还残留有酸和水而使表面重新生锈。
另外,酸洗后在清洗槽中停留时间过长,也将导致锈蚀。
1防止措施:严格执行酸洗、清洗、烘干操作规程,及时进行钝化或涂油处理,并堆放到干燥的地方。
5、窝边、划伤、压痕等由于设备问题、操作不认真引起,上卷时夹盘未对正,运行时跑偏易造成窝边。
低碳钢连续退火工艺介绍

时效 S 120 120 120 120 120 120 120 120
CQ ( 屈 CS B TC2 ZT3 服 801 ≤275Mpa ) A08 08Al SPCD St13 DQ(低碳) DC03 DS( 低 碳 钢 投 料 ) 821 CSA01 低 碳 钢 投 料 的 SPCC 4E80 DQ( 超 低 超 St12 DC01 SPCD St13 碳钢) 1 DC03 DS M30
对冲压加工厂或冲压车间来说,以光轧平整或在辊子参差配置的板材矫正机上,将板料向两个 方向轻微地反复弯曲,使板料得到不大的冷变形(1%),便可以消除上述现象。但其效果是暂时的, 甚至只经过几天,机械性能就有显著变化。因此,板料光轧工序应直接在冲压以前进行。
鞍钢冷轧钢板(莆田)有限公司
商用钢、低碳软钢和冲压钢的连 退原理
DP 450780 TRIP 590980 TWIP 980
CS
DS
DDS
鞍钢冷轧钢板(莆田)有限公司
连退带钢金属热处理工艺
鞍钢冷轧钢板(莆田)有限公司
鞍钢冷轧钢板(莆田)有限公司
鞍钢冷轧钢板(莆田)有限公司
鞍钢冷轧钢板(莆田)有限公司
鞍钢冷轧钢板(莆田)有限公司
钢板的时效性
时效:SPCC、SPCD板和08F板,平整后可保存8天; SPCE平整后可保存6个月内不出现冲压滑移线,即凸起线。 时效性机理:在退火或有时效的低碳钢拉伸曲线上具有明显的屈服平台。 这在冲压成形时,会出现损害外观的作为滑移线。 当变形超过屈服平台以后,滑移线消失,而板面变得稍微有点粗糙。 所以,供冲压用的低碳钢板,在经过冷轧和退火以后,要进行调质 轧制, 使其变形量超过屈服平台,以防止冲压时发生滑移线。 时效性的消除:含溶解氮的沸腾钢板,从调质轧制以后,到冲压加工以前, 若经过一段时间,会发生所谓应变时效现象,再次出现屈服平台, 同样会发生滑移线。
罩式退火炉工作原理

罩式退火炉工作原理罩式退火炉是一种常用的热处理设备,其工作原理基于金属材料的退火过程。
本文将详细介绍罩式退火炉的工作原理及其相关原理知识。
一、罩式退火炉的基本构造罩式退火炉主要由炉体、加热装置、控制系统和废气处理系统等组成。
炉体通常由耐火材料制成,具有良好的隔热性能,能够承受高温环境。
加热装置主要为电加热器或燃气加热器,通过加热装置提供的热能,使炉内温度达到退火要求。
控制系统负责调节和监控炉内温度、时间等参数,以确保退火工艺的准确执行。
废气处理系统用于处理炉内产生的废气,以减少对环境的污染。
二、罩式退火炉的工作原理1. 加热阶段首先将待处理的金属材料放入炉内,并将炉门密封,以确保炉内空气的隔绝。
然后打开加热装置,通过电加热或燃气加热使炉内温度逐渐升高。
在加热过程中,控制系统会实时监测和调节炉内温度,以确保温度的均匀性和稳定性。
2. 保温阶段当炉内温度达到退火要求后,控制系统将保持温度恒定,进入保温阶段。
在保温阶段,金属材料的晶粒会逐渐长大,内部应力得到释放,达到退火效果。
保温时间根据金属材料的特性和退火要求而定,通常需要较长的时间。
3. 冷却阶段完成退火工艺后,关闭加热装置,开始冷却阶段。
冷却速度通常要控制在一定范围内,以避免产生过度硬化或变形。
常见的冷却方法有自然冷却和强制冷却。
自然冷却是指将金属材料从炉内取出,自然散热至室温。
强制冷却则是通过外部冷却介质,如水或空气,进行快速冷却。
三、罩式退火炉的优势1. 温度均匀性好:罩式退火炉采用密封式结构,能够有效防止炉内温度的波动,保证金属材料的均匀加热。
2. 适用性广:罩式退火炉可以处理各种金属材料,包括铁、钢、铜、铝等,适用范围广泛。
3. 自动化程度高:罩式退火炉配备了先进的控制系统,能够实现自动化操作和远程监控,提高工作效率和生产质量。
4. 应用灵活:罩式退火炉可根据不同的工艺需求进行调整和优化,满足不同材料的退火要求。
四、罩式退火炉的应用领域罩式退火炉广泛应用于金属加工、制造业和热处理行业。
罩式退火和连续退火优缺点
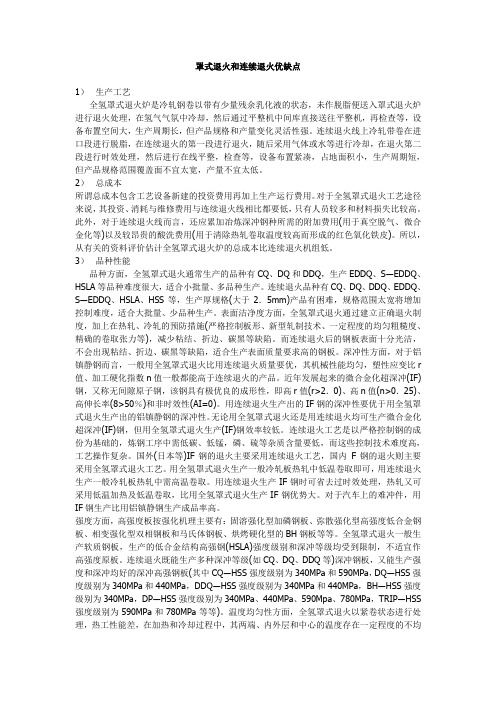
罩式退火和连续退火优缺点1)生产工艺全氢罩式退火炉是冷轧钢卷以带有少量残余乳化液的状态,未作脱脂便送入罩式退火炉进行退火处理,在氢气气氛中冷却,然后通过平整机中间库直接送往平整机,再检查等,设备布置空间大,生产周期长,但产品规格和产量变化灵活性强。
连续退火线上冷轧带卷在进口段进行脱脂,在连续退火的第一段进行退火,随后采用气体或水等进行冷却,在退火第二段进行时效处理,然后进行在线平整,检查等,设备布置紧凑,占地面积小,生产周期短,但产品规格范围覆盖面不宜太宽,产量不宜太低。
2)总成本所谓总成本包含工艺设备新建的投资费用再加上生产运行费用。
对于全氢罩式退火工艺途径来说,其投资、消耗与维修费用与连续退火线相比都要低,只有人员较多和材料损失比较高。
此外,对于连续退火线而言,还应累加冶炼深冲钢种所需的附加费用(用于真空脱气、微合金化等)以及较昂贵的酸洗费用(用于清除热轧卷取温度较高而形成的红色氧化铁皮)。
所以,从有关的资料评价估计全氢罩式退火炉的总成本比连续退火机组低。
3)品种性能品种方面,全氢罩式退火通常生产的品种有CQ、DQ和DDQ,生产EDDQ、S―EDDQ、HSLA等品种难度很大,适合小批量、多品种生产。
连续退火品种有CQ、DQ、DDQ、EDDQ、S―EDDQ、HSLA、HSS等,生产厚规格(大于2.5mm)产品有困难,规格范围太宽将增加控制难度,适合大批量、少品种生产。
表面洁净度方面,全氢罩式退火通过建立正确退火制度,加上在热轧、冷轧的预防措施(严格控制板形、新型轧制技术、一定程度的均匀粗糙度、精确的卷取张力等),减少粘结、折边、碳黑等缺陷。
而连续退火后的钢板表面十分光洁,不会出现粘结、折边、碳黑等缺陷,适合生产表面质量要求高的钢板。
深冲性方面,对于铝镇静钢而言,一般用全氢罩式退火比用连续退火质量要优,其机械性能均匀,塑性应变比r 值、加工硬化指数n值一般都能高于连续退火的产品。
近年发展起来的微合金化超深冲(IF)钢,又称无间隙原子钢,该钢具有极优良的成形性,即高r值(r>2.0)、高n值(n>0.25)、高伸长率(8>50%)和非时效性(AI=0)。
《罩式退火炉介绍》课件

4
冷却放空
停止加热系统,让金属材料自然冷却,直到其温度达到室温,然后打开罩体,取出金属材料。
罩式退火炉的应用领域和优势
金属管件
罩式退火炉可用于管件加工、改善 材料强度和韧性等。
合金材料
罩式退火炉可用于合金材料的热处 理,改善其力学性能和耐蚀性。
不锈钢锻件
罩式退火炉可用于不锈钢锻件的回 火退火处理,使其获得更好的抗拉 强度和韧性。
加热系统
负责产生所需的热量,并保证加热温度和升温速度。
控制系统
负责控制加热时间、温度和压力等参数,确保得到所需热处理效果。
罩式退火炉的工作过程
1
预热准备
对罩式退火炉进行清洁和维护,并设置加热温度和升温速度。
2
材料装载
将金属材料放入罩体中,安排好位置和数量。
3
加热处理
启动加热系统,将温度逐渐升高至所需温度,然后保温一段时间。
总结及展望
罩式退火炉作为一种重要的材料热处理设备,其应用范围和效果不断扩大和 提高。今后,随着技术的发展,罩式退火炉将更加智能化、高效化和节能化。
罩式退火炉介绍
欢迎来学习罩式退火炉,这是一种具有广泛应用和丰种对金属材料进行热处理的设备,其原理是将金属材料放在 容器中,将其封闭并加热至一定温度,通过控制温度和保温时间,改善材料 的物理和化学性质。
罩式退火炉的主要组成部分
罩体
负责封闭金属材料和保温。
罩式退火炉的发展趋势
随着新材料、新工艺、新技术的出现,罩式退火炉将越来越多地应用于高强度、高温度、复杂结构的材料和产品的 加工中。
罩式退火炉的维护和保养
1 清洁机器和部件
2 检查设备状态
3 有效保养设备
定期清洗和涂油,保持设备 干净和润滑。
- 1、下载文档前请自行甄别文档内容的完整性,平台不提供额外的编辑、内容补充、找答案等附加服务。
- 2、"仅部分预览"的文档,不可在线预览部分如存在完整性等问题,可反馈申请退款(可完整预览的文档不适用该条件!)。
- 3、如文档侵犯您的权益,请联系客服反馈,我们会尽快为您处理(人工客服工作时间:9:00-18:30)。
罩式退火和连续退火优缺点
1)生产工艺
全氢罩式退火炉是冷轧钢卷以带有少量残余乳化液的状态,未作脱脂便送入罩式退火炉进行退火处理,在氢气气氛中冷却,然后通过平整机中间库直接送往平整机,再检查等,设备布置空间大,生产周期长,但产品规格和产量变化灵活性强。
连续退火线上冷轧带卷在进口段进行脱脂,在连续退火的第一段进行退火,随后采用气体或水等进行冷却,在退火第二段进行时效处理,然后进行在线平整,检查等,设备布置紧凑,占地面积小,生产周期短,但产品规格范围覆盖面不宜太宽,产量不宜太低。
2)总成本
所谓总成本包含工艺设备新建的投资费用再加上生产运行费用。
对于全氢罩式退火工艺途径来说,其投资、消耗与维修费用与连续退火线相比都要低,只有人员较多和材料损失比较高。
此外,对于连续退火线而言,还应累加冶炼深冲钢种所需的附加费用(用于真空脱气、微合金化等)以及较昂贵的酸洗费用(用于清除热轧卷取温度较高而形成的红色氧化铁皮)。
所以,从有关的资料评价估计全氢罩式退火炉的总成本比连续退火机组低。
3)品种性能
品种方面,全氢罩式退火通常生产的品种有CQ、DQ和DDQ,生产EDDQ、S―EDDQ、HSLA等品种难度很大,适合小批量、多品种生产。
连续退火品种有CQ、DQ、DDQ、EDDQ、S―EDDQ、HSLA、HSS等,生产厚规格(大于2.5mm)产品有困难,规格范围太宽将增加控制难度,适合大批量、少品种生产。
表面洁净度方面,全氢罩式退火通过建立正确退火制度,加上在热轧、冷轧的预防措施(严格控制板形、新型轧制技术、一定程度的均匀粗糙度、精确的卷取张力等),减少粘结、折边、碳黑等缺陷。
而连续退火后的钢板表面十分光洁,不会出现粘结、折边、碳黑等缺陷,适合生产表面质量要求高的钢板。
深冲性方面,对于铝镇静钢而言,一般用全氢罩式退火比用连续退火质量要优,其机械性能均匀,塑性应变比r 值、加工硬化指数n值一般都能高于连续退火的产品。
近年发展起来的微合金化超深冲(IF)钢,又称无间隙原子钢,该钢具有极优良的成形性,即高r值(r>2.0)、高n值(n>0.25)、高伸长率(8>50%)和非时效性(AI=0)。
用连续退火生产出的IF钢的深冲性要优于用全氢罩式退火生产出的铝镇静钢的深冲性。
无论用全氢罩式退火还是用连续退火均可生产微合金化超深冲(IF)钢,但用全氢罩式退火生产(IF)钢效率较低。
连续退火工艺是以严格控制钢的成份为基础的,炼钢工序中需低碳、低锰,磷、硫等杂质含量要低,而这些控制技术难度高,工艺操作复杂。
国外(日本等)IF钢的退火主要采用连续退火工艺,国内F钢的退火则主要采用全氢罩式退火工艺。
用全氢罩式退火生产一般冷轧板热轧中低温卷取即可,用连续退火生产一般冷轧板热轧中需高温卷取。
用连续退火生产IF钢时可省去过时效处理,热轧又可采用低温加热及低温卷取,比用全氢罩式退火生产IF钢优势大。
对于汽车上的难冲件,用IF钢生产比用铝镇静钢生产成品率高。
强度方面,高强度板按强化机理主要有:固溶强化型加磷钢板、弥散强化型高强度低合金钢板、相变强化型双相钢板和马氏体钢板、烘烤硬化型的BH钢板等等。
全氢罩式退火一般生产软质钢板,生产的低合金结构高强钢(HSLA)强度级别和深冲等级均受到限制,不适宜作高强度原板。
连续退火既能生产多种深冲等级(如CQ、DQ、DDQ等)深冲钢板,又能生产强度和深冲均好的深冲高强钢板(其中CQ―HSS强度级别为340MPa和590MPa,DQ―HSS强度级别为340MPa和440MPa,DDQ―HSS强度级别为340MPa和440MPa,BH―HSS强度级别为340MPa,DP―HSS强度级别为340MPa、440MPa、590Mpa、780MPa,TRIP―HSS 强度级别为590MPa和780MPa等等)。
温度均匀性方面,全氢罩式退火以紧卷状态进行处理,热工性能差,在加热和冷却过程中,其两端、内外层和中心的温度存在一定程度的不均
匀性。
连续退火以带钢状态进行连续处理,传热条件好,带钢温度均匀,同时还可通过炉内张力及纠偏装置控制和改善带钢平直度,板形优良。
4)灵活性
全氢罩式退火炉体积小,分批处理,自成系统,炉台数量可随品种和产量变化随时增减,十分灵活。
连续退火炉穿带一次要用上千米钢带,改换品种要一定的调整时间和一定量的过度钢带,适合大批量生产,小批量生产不合算。
5)生产效率
全氢罩式退火属间歇式生产,为了充分保证带钢性能均匀,生产周期比较长(退火周期一般40~6Oh),生产效率低。
连续退火属连续生产,带钢速度快(退火工艺段一般40Ore/rain 左右,最高达80Ore/rain以上)。
生产周期短(退火周期一般5~lOmin),生产效率很高。
6)产品开发
全氢罩式退火为避免钢卷层间粘结,退火温度一般不超过72O℃,成卷长时间保温后冷却速度不可能太快,生产产品有相当局限性。
而在连续退火中,退火温度处于双相区(α+γ),可达850℃,短时间保温后冷却速度自由度大,大大扩大品种范围。
但是,连续退火要求冷轧板必须在短时间内再结晶和进行晶粒充分长大,这就需要材质纯净。
全氢罩式退火只能生产高强钢中的低合金结构钢(HS―LA),强度级别和深冲等级均受到限制,生产表面质量O3级产品尚可,但生产表面质量要求高的05级产品比较困难,不适宜作表面质量要求高钢板。
连续退火除能生产深冲等级钢板以外,还能生产多种强度级别和多种深冲等级的高强钢,能满足汽车、家电、建筑等行业对冷轧板的多种要求,可以生产05级汽车外板,适宜作表面质量要求高的钢板。
全氢罩式退火与普通的罩式退火相比,具有效率高、质量好、能耗低等优势,全氢罩式退火正逐渐取代普通的罩式退火。
全氢罩式退火和连续退火相比,全氢罩式退火具有生产软质钢板的优势,生产灵活,建设投资少,但在高强度钢板生产上有所欠缺,且属间歇式生产,生产周期长,效率偏低,适合小批量、多品种生产,该退火工艺在小型冷轧厂中十分流行。
连续退火既能生产软质钢板又能生产级别较高的高强钢板,产品开发优势明显,且生产连续化,生产周期短,板形好,表面光洁,但投资大,技术复杂,适合大批量、少品种生产,该退火工艺在大型冷轧厂中日益盛行。
全氢罩式退火和连续退火均为先进的退火工艺。
今后相当长一段时期内全氢罩式退火和连续退火将同时并存,两种退火工艺优势互补。