7转炉炼钢工艺II
转炉炼钢用的工艺方案

转炉炼钢用的工艺方案一、炼钢的“火炉”——转炉说起炼钢,大家第一反应肯定是钢铁工厂里那熊熊燃烧的火焰吧。
没错,那就是我们所说的转炉!这家伙可不简单,不光能炼钢,而且炼出来的钢可是强度、硬度、韧性一个不拉的。
转炉炼钢的基本原理其实很简单。
钢铁从铁矿石中提炼出来,炼钢时就得把这些原料放进大大的炉子里。
然后,炉子就开始加热,让铁矿石里的杂质去掉,剩下的就是我们需要的钢铁啦。
我都能感受到那种高温和火花飞溅的场面,真的是一团火热的激情啊!这个转炉就像一台巨大的“翻锅”机器,炉内的金属液体不停翻滚,铁和废料的氧化反应使得不纯净的物质和钢铁分离。
锅里的金属液面也像个能“说话”的小孩子,随着温度的升高,“咚咚”的响声就像是敲响了钢铁之路的号角。
那时,原料在转炉里翻腾,好像是给它们洗个大澡,把那些脏东西洗得干干净净,剩下的钢才够强硬够耐用,才能在后面的各个环节中“大展身手”。
二、转炉炼钢的具体步骤咱们聊聊转炉炼钢的具体流程。
其实它的流程并不复杂,先把炉子加热到一千多度。
炉内有个叫“空气氧化”的过程,通过向炉子里吹入氧气,把金属液体里的杂质(比如硫、磷、碳啥的)氧化掉。
简直就是给它们“瘦身”,再把这些氧化物赶出去。
就像你去美容院做面部护理,精致的五官都需要多做几道工序,一点点剔除杂质。
整个过程相当于“减肥塑形”,把钢液处理得轻松优雅。
等到这些杂质被“清理”掉之后,炉子就得加入合金元素了。
不同的钢需要不同的合金配方,就像煮汤一样,你得根据不同的口味放进去适当的食材。
比如说,做不锈钢时,得加点铬,增强钢铁的抗腐蚀能力。
而如果是造汽车的钢,可能要加点锰,增强钢的强度。
一块块普通的钢铁,经过转炉这一“魔法”的洗礼后,成了“超级英雄”,强大到无敌!三、转炉炼钢的特点大家知道,转炉炼钢可不是一蹴而就的事情,它有几个显著的特点。
首先就是它的效率超高,特别适合大规模生产。
想想看,一台转炉在短短几个小时内就能处理几百吨的钢铁。
真的是“快准狠”,每一吨钢铁的生产都像是赛车比赛一样快速而精准。
转炉炼钢工艺分析

转炉炼钢工艺分析简介转炉炼钢是一种重要的钢铁生产工艺。
它采用转炉作为熔炼设备,通过氧化钢水的方式去除杂质,从而获得高纯度的钢水。
工艺流程转炉炼钢的工艺流程一般包括以下几个步骤:1.亚稳态钢水倒入转炉中,同时注入氧气;2.氧气与铁水反应生成氧化物,从而去除杂质;3.在适当的条件下加入渣剂,将浮渣与钢水分离;4.投入合适的合金和调节剂,调节钢水的成分和性质;5.倒出钢水至铸铁机或连铸机中,制成钢材。
工艺优势相对于其他炼钢工艺,转炉炼钢具有以下优势:1.钢水纯度高,化学成分稳定,可以得到各种不同技术要求的钢材;2.工艺流程简单,可自动化控制,生产效率高;3.单次生产能力大,适用于大批量生产。
工艺不足然而,转炉炼钢也存在一些问题,主要包括:1.熔炼过程中,由于氧化反应的过程比较复杂,会产生大量的烟尘和废气污染;2.熔炼后再行铸造需要添加铝、钛等金属,也会对环境造成一定的污染。
工艺改进针对转炉炼钢存在的问题,研究人员进行了多方面的工艺改进研究。
主要包括以下几个方面:1.减少污染:采用高热效应烟气脱硫技术和洗涤重金属离子等方法,减少烟尘、废水排放,改善环境;2.提高产能:对炉况和操作条件进行优化调整,提高单次生产能力;3.提高效益:加入合适的合金和调节剂,调节钢水的成分,生产高附加值、高品质的钢材。
市场应用目前,转炉炼钢工艺已经在全球范围内广泛应用。
根据统计数据,仅中国一国的转炉炼钢产量就占全球的60%以上。
随着技术的不断进步,转炉炼钢工艺在钢铁生产中的地位将更加重要。
结论综上所述,转炉炼钢是一种重要的钢铁生产工艺,具有钢水纯度高、生产效率高等诸多优点。
但其存在烟尘、废气污染等问题。
通过改善工艺和技术手段的引入,可以实现减少污染、提高产能和效益的目标。
这一工艺在全球范围内得到广泛应用,将在未来发展中继续发挥重要作用。
转炉炼钢工艺
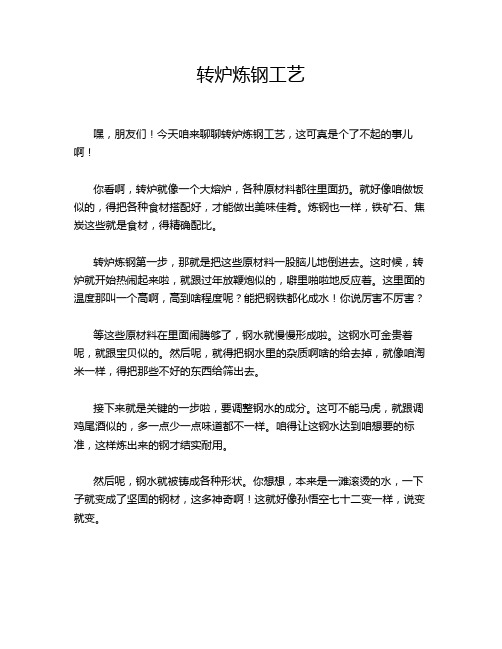
转炉炼钢工艺嘿,朋友们!今天咱来聊聊转炉炼钢工艺,这可真是个了不起的事儿啊!你看啊,转炉就像一个大熔炉,各种原材料都往里面扔。
就好像咱做饭似的,得把各种食材搭配好,才能做出美味佳肴。
炼钢也一样,铁矿石、焦炭这些就是食材,得精确配比。
转炉炼钢第一步,那就是把这些原材料一股脑儿地倒进去。
这时候,转炉就开始热闹起来啦,就跟过年放鞭炮似的,噼里啪啦地反应着。
这里面的温度那叫一个高啊,高到啥程度呢?能把钢铁都化成水!你说厉害不厉害?等这些原材料在里面闹腾够了,钢水就慢慢形成啦。
这钢水可金贵着呢,就跟宝贝似的。
然后呢,就得把钢水里的杂质啊啥的给去掉,就像咱淘米一样,得把那些不好的东西给筛出去。
接下来就是关键的一步啦,要调整钢水的成分。
这可不能马虎,就跟调鸡尾酒似的,多一点少一点味道都不一样。
咱得让这钢水达到咱想要的标准,这样炼出来的钢才结实耐用。
然后呢,钢水就被铸成各种形状。
你想想,本来是一滩滚烫的水,一下子就变成了坚固的钢材,这多神奇啊!这就好像孙悟空七十二变一样,说变就变。
在整个转炉炼钢过程中,工人们就像是魔法师,操控着这一切。
他们得时刻关注着,温度高了不行,低了也不行;成分不对不行,杂质多了更不行。
他们就靠着自己的经验和技术,让这一切都顺顺利利的。
你说要是没有这些工人,没有这转炉炼钢工艺,咱的生活能这么便利吗?那些高楼大厦怎么建起来?那些汽车、火车怎么跑起来?所以啊,可别小看了这转炉炼钢工艺,它可是咱们现代生活的大功臣呢!咱再回过头来想想,这转炉炼钢工艺不就跟咱人生一样吗?得经历各种磨炼,得去掉那些不好的东西,才能变得更加优秀。
而且啊,在这个过程中,咱也得有那些像炼钢工人一样的人来引导我们、帮助我们。
总之,转炉炼钢工艺是个伟大的工艺,它为我们的生活带来了太多太多。
咱得好好感谢那些炼钢工人,也得好好珍惜这来之不易的钢铁啊!。
转炉炼钢实用工艺流程

转炉炼钢工艺流程这种炼钢法使用的氧化剂是氧气。
把空气鼓入熔融的生铁里,使杂质硅、锰等氧化。
在氧化的过程中放出大量的热量〔含1%的硅可使生铁的温度升高200摄氏度〕,可使炉达到足够高的温度。
因此转炉炼钢不需要另外使用燃料。
转炉炼钢是在转炉里进展。
转炉的外形就像个梨,壁有耐火砖,炉侧有许多小孔〔风口〕,压缩空气从这些小孔里吹炉,又叫做侧吹转炉。
开始时,转炉处于水平,向注入1300摄氏度的液态生铁,并参加一定量的生石灰,然后鼓入空气并转动转炉使它直立起来。
这时液态生铁外表剧烈的反响,使铁、硅、锰氧化(FeO,SiO2 , MnO,) 生成炉渣,利用熔化的钢铁和炉渣的对流作用,使反响遍与整个炉。
几分钟后,当钢液中只剩下少量的硅与锰时,碳开始氧化,生成一氧化碳〔放热〕使钢液剧烈沸腾。
炉口由于溢出的一氧化炭的燃烧而出现巨大的火焰。
最后,磷也发生氧化并进一步生成磷酸亚铁。
磷酸亚铁再跟生石灰反响生成稳定的磷酸钙和硫化钙,一起成为炉渣。
当磷与硫逐渐减少,火焰退落,炉口出现四氧化三铁的褐色蒸汽时,明确钢已炼成。
这时应立即停止鼓风,并把转炉转到水平位置,把钢水倾至钢水包里,再加脱氧剂进展脱氧。
整个过程只需15分钟左右。
如果空气是从炉低吹入,那就是低吹转炉。
随着制氧技术的开展,现在已普遍使用氧气顶吹转炉〔也有侧吹转炉〕。
这种转炉吹如的是高压工业纯氧,反响更为剧烈,能进一步提高生产效率和钢的质量。
转炉一炉钢的根本冶炼过程。
顶吹转炉冶炼一炉钢的操作过程主要由以下六步组成:〔1〕上炉出钢、倒渣,检查炉衬和倾动设备等并进展必要的修补和修理;〔2〕倾炉,加废钢、兑铁水,摇正炉体〔至垂直位置〕;〔3〕降枪开吹,同时参加第一批渣料〔起初炉噪声较大,从炉口冒出赤色烟雾,随后喷出暗红的火焰;3~5min后硅锰氧接近完毕,碳氧反响逐渐激烈,炉口的火焰变大,亮度随之提高;同时渣料熔化,噪声减弱〕;〔4〕3~5min后参加第二批渣料继续吹炼〔随吹炼进展钢中碳逐渐降低,约12min后火焰微弱,停吹〕;〔5〕倒炉,测温、取样,并确定补吹时间或出钢;〔6〕出钢,同时〔将计算好的合金参加钢包中〕进展脱氧合金化。
转炉炼钢工艺

转炉炼钢工艺1转炉炼钢的原材料引言转炉炼钢所用原材料可分为金属料和非金属料两大类。
原材料质量的好坏,不仅关系到吹炼操作的难易,而且会影响钢的产量、质量和生产成本。
1.1 金属料转炉炼钢的金属料主要是铁水、废钢和铁合金。
1.1.1铁水1 作用:转炉炼钢的主原料,一般占装入量的70%以上。
2 要求铁水应符合一定要求,以简化和稳定操作并获得良好技术经济指标。
1)温度≥1250℃而且稳定铁水温度的高低,标志着其物理热的多少。
较高的铁水温度,不仅能保证转炉吹炼顺利进行,同时还能增加废钢的配加量,降低生产成本。
因此,希望铁水的温度尽量高些,一般应保证入炉时仍在1250℃~1300℃以上。
另外,还希望铁水温度相对稳定,以利于冶炼操作和生产调度。
2)成分合适而且波动小转炉炼钢的适应性较强,可将各种成分的铁水吹炼成钢。
但是,为了方便转炉操作及降低生产成本,铁水的成分应该合适而稳定。
(1)铁水的含磷量≤0.4%:磷会使钢产生“冷脆”现象,是钢中的有害元素之一。
转炉单渣法冶炼时的脱磷效果为85%~95%,普碳钢的含磷量通常要求≤0.04%,因此,国标规定铁水的含磷量小于0.4%。
需要指出的是,高炉内不能去磷,如果铁水的含磷量超过0.4%,或者吹炼低磷钢,则需采用双渣法冶炼或对铁水进行预脱磷处理。
(2)铁水的含硫量≤0.07%:硫会使钢产生“热脆”现象,也是钢中的有害元素。
转炉的脱硫效果不理想,单渣法冶炼时的脱硫率仅为30%~35%,而通常要求钢液的含硫量在0.05%以下,因此国标规定铁水含硫量≤0.07%。
如果铁水含硫量超过0.07%或吹炼低硫钢,则需采用双渣法冶炼或对铁水进行预脱硫处理。
(3)铁水的含硅量:铁水中的硅是转炉炼钢的主要发热元素之一,含硅量每增加0.1%,废钢比可增加1.3%~1.5%。
对于大、中型转炉,铁水含硅量以0.5%~0.8%为宜。
小型转炉的热损较大,铁水的含硅量可以高些。
若含硅量低于0.5%,铁水的化学热不足,会导致废钢比下降,小容量转炉甚至不能正常吹炼;反之,如果铁水含硅量高于0.8%,不仅会增加造渣材料的消耗,而且使炉内的渣量偏大,过多的渣量容易引起喷溅,增加金属损失。
转炉炼钢的工艺流程
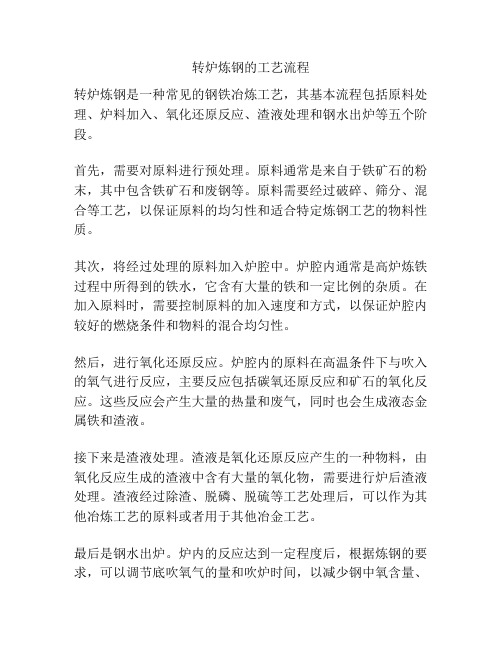
转炉炼钢的工艺流程转炉炼钢是一种常见的钢铁冶炼工艺,其基本流程包括原料处理、炉料加入、氧化还原反应、渣液处理和钢水出炉等五个阶段。
首先,需要对原料进行预处理。
原料通常是来自于铁矿石的粉末,其中包含铁矿石和废钢等。
原料需要经过破碎、筛分、混合等工艺,以保证原料的均匀性和适合特定炼钢工艺的物料性质。
其次,将经过处理的原料加入炉腔中。
炉腔内通常是高炉炼铁过程中所得到的铁水,它含有大量的铁和一定比例的杂质。
在加入原料时,需要控制原料的加入速度和方式,以保证炉腔内较好的燃烧条件和物料的混合均匀性。
然后,进行氧化还原反应。
炉腔内的原料在高温条件下与吹入的氧气进行反应,主要反应包括碳氧还原反应和矿石的氧化反应。
这些反应会产生大量的热量和废气,同时也会生成液态金属铁和渣液。
接下来是渣液处理。
渣液是氧化还原反应产生的一种物料,由氧化反应生成的渣液中含有大量的氧化物,需要进行炉后渣液处理。
渣液经过除渣、脱磷、脱硫等工艺处理后,可以作为其他冶炼工艺的原料或者用于其他冶金工艺。
最后是钢水出炉。
炉内的反应达到一定程度后,根据炼钢的要求,可以调节底吹氧气的量和吹炉时间,以减少钢中氧含量、降低杂质含量和改善钢水中的成分均匀性。
一段时间后,钢水可以从转炉中出炉,经过连铸工艺可以制成各种形状的钢材。
总体而言,转炉炼钢工艺流程包括原料处理、炉料加入、氧化还原反应、渣液处理和钢水出炉等五个阶段。
这一工艺在现代钢铁冶炼中得到广泛应用,能够实现大规模的、高效的钢铁生产。
同时,随着技术的不断发展,该工艺也在不断地改进和优化,为钢铁行业的可持续发展做出了重要贡献。
转炉炼钢工艺课件(PPT 54页)

1)硅(Si)
硅是重要的发热元素,铁水中含Si量高,炉内的化学热增加,铁水中Si量增加
0.10%,废钢的加入量可提高1.3%-1.5%。 铁水含Si量高,渣量增加,有利于脱磷、脱硫。 硅含量过高会使渣料和消耗增加,易引起喷溅,金属收得率降低,同时渣中
是指终点温度和成分的控制。
脱氧及合金化
•脱氧:向钢液加入某些脱氧元素,脱除其中多余氧的操作。
•合金化:加入一种或几种合金元素,使其在钢中的含量达到钢种规格 要求的操作。
•区别:合金元素的价格通常较高,希望尽量少氧化;脱氧元素则比较便 宜,先加入,让其充分脱氧以免后加入的合金元素氧化。
•联系:二者都是向钢液加入铁合金,同时加入钢液的脱氧剂必然会有 部分溶于钢液而起合金化的作用,如使用Fe-Si、Fe-Mn脱氧的同时调整 钢液的硅锰含量;加入钢液的合金元素,因其与氧的亲和力大于铁也势 必有一部分被氧化而起脱氧作用。转炉的脱氧与合金化的操作常常是同 时进行的。
1951年碱性空气侧吹转炉炼钢法首先 在我国唐山钢厂试验成功,并于1952年 投入工业生产。1954年开始厂小型氧气 顶吹转炉炼钢的试验研究工作,1962年 将首钢试验厂空气侧吹转炉改建成3t氧气 顶吹转炉,开始了工业性试验。在试验取 得成功的基础上,我国第1个氧气顶吹转 炉炼钢车间(2x30t)在首钢建成,于 1964 年12月26日投入生产。
转炉冶炼中,高碳钢种时,使用含杂质很少的 石油焦作为增碳剂。
3 、氧化剂
氧气是转炉炼钢的主要氧化剂,其纯度达到或超过 99.5%,氧气压力要稳定,并脱除水分。
氧化铁亦称铁磷,是钢坯加热,轧制和连铸过程中 产生的氧化壳层,铁量约占70%-75%。氧化铁皮 还有助于化渣和冷却作用,使用时应加热烘烤,保 持干燥。
转炉炼钢的五大工艺制度

转炉炼钢的五大工艺制度引言:转炉炼钢是一种常见的冶炼工艺,通过炼钢炉中高温条件下的氧气吹吹炼,将铁水和废钢等原料加工成高质量的钢材。
为了提高炼钢效率和质量,转炉炼钢采用了多种工艺制度。
本文将介绍转炉炼钢的五大工艺制度,包括氧枪喷吹工艺、钢包倾吊工艺、渣氧平衡工艺、碱性炉温保护工艺和连续浇铸工艺。
一、氧枪喷吹工艺氧枪喷吹工艺是转炉炼钢的核心工艺之一。
该工艺通过氧气喷吹,使铁水中的杂质和不良元素在高温条件下被氧化和吹出,从而提高钢材的纯度和质量。
在氧枪喷吹工艺中,需要控制氧气的流量和喷吹位置,以确保各种元素的氧化速率和炉温的控制。
二、钢包倾吊工艺钢包倾吊工艺是转炉炼钢的关键环节之一。
在钢包倾吊过程中,将经过炼钢炉炼制的钢水倾倒到钢包中,然后再将钢包倾倒到连铸坑中进行连铸。
倾吊时需要注意钢水的温度控制和倾吊速度,以确保钢水的质量和均匀性。
三、渣氧平衡工艺渣氧平衡工艺是转炉炼钢中用于控制渣铁比和氧气利用率的重要工艺。
通过合理控制渣铁比,可以提高转炉炼钢的冶炼效率和钢材质量。
同时,通过优化氧气利用率,可以减少能耗和炼钢成本。
渣氧平衡工艺需要根据具体炼钢情况进行调整,以达到最佳的效果。
四、碱性炉温保护工艺转炉炼钢中的高温条件对炉衬的腐蚀和寿命造成了严重挑战。
为了保护炉衬,常采用碱性炉温保护工艺。
该工艺通过添加适量的碱性物质,形成一层保护性的渣膜,减少炉衬的腐蚀和磨损。
碱性炉温保护工艺的成功应用,延长了转炉炼钢炉衬的使用寿命,降低了生产成本。
五、连续浇铸工艺连续浇铸工艺是转炉炼钢生产线的最后一个环节,也是实现高效率生产和优质钢材的关键。
在连续浇铸中,将炼制好的钢水连续地注入到均质的结晶器中,并通过提拉辊、冷却器等设备进行快速冷却和连续成形。
这种工艺既提高了钢材的质量,又提高了生产效率,逐渐成为转炉炼钢的主流工艺。
结论:转炉炼钢的五大工艺制度,即氧枪喷吹工艺、钢包倾吊工艺、渣氧平衡工艺、碱性炉温保护工艺和连续浇铸工艺,共同构成了转炉炼钢生产线的关键环节。
转炉炼钢法

转炉炼钢法一、引言转炉炼钢法是目前钢铁工业中广泛采用的一种炼钢方法。
它的优点在于生产效率高、质量稳定、成本低廉等方面,因此被广泛应用于各种不同类型的钢铁生产中。
本文将详细介绍转炉炼钢法的原理、工艺流程和应用。
二、原理转炉炼钢法是一种基于氧化还原反应的化学反应过程。
在这个过程中,将生铁和废钢等材料放入转炉中,并通过喷吹氧气来使其加热并进行氧化还原反应,最终得到高质量的钢材。
具体来说,转炉内部被分为两个区域:上部为碱性区域,下部为酸性区域。
在碱性区域中,喷吹进去的氧气与铁水反应生成二氧化碳和水蒸汽,同时也会将一部分硅、锰等杂质氧化掉。
而在酸性区域中,则会喷吹进去适量的生铁或废钢等回收物质,以便再次进行还原反应,同时也会将一部分碳、磷等杂质氧化掉。
三、工艺流程转炉炼钢法的工艺流程主要包括以下几个步骤:1. 装料:在转炉中加入生铁和废钢等原料。
2. 预热:通过加热器将原料预先加热到适宜的温度,以便更好地进行反应。
3. 吹氧:喷吹氧气使原料快速加热并进行氧化还原反应。
这个过程中需要控制好吹氧量和时间,以确保反应能够顺利进行。
4. 加入合金元素:在适当的时候向转炉中加入合金元素,以调整钢材的成分和性质。
5. 出钢:经过一定时间的反应后,将得到高质量的钢材。
此时需要将其从转炉中取出,并通过连铸机等设备进行成形和冷却处理。
四、应用转炉炼钢法是目前广泛应用于各种不同类型的钢铁生产中的一种方法。
其中最常见的使用场景包括:1. 生产低合金结构钢、碳素结构钢等常规钢材。
2. 生产高强度、高耐磨、高韧性等特殊钢材。
3. 回收和利用废钢等回收资源,以提高资源利用率。
4. 生产不锈钢、合金钢等特殊材料。
总之,转炉炼钢法是一种非常重要的炼钢方法,它具有生产效率高、质量稳定、成本低廉等优点,在各种不同类型的钢铁生产中都得到了广泛应用。
转炉炼钢原理及工艺介绍

2MeO=2Me+O2
在一定温度下,分解反应达到平衡时,其平衡常数等于气相中氧的分压,即: K=PO2,此PO2称为该氧化物的分解压。通过实验测得不同温度下的分解压,即可绘出 PO2-t℃的关系曲线图(见下页)。图中曲线的位置愈低,表明该氧化物的分解压愈 小,该氧化物愈稳定,即该元素易被氧化。由图还可以看出:
(3)炉渣的分子理论
★ 炉渣组成 炉渣由自由的氧化物分子和复杂的化合物分子所组成。自由氧 化物分子有:CaO、MgO、MnO、FeO、Fe203、 A l203、P205、SiO2等; 复杂化合物分子主要有五种:2FeO· Si02、2MnO·Si02、Ca0·Si02、 4CaO·P205、3CaO·P2O5。此外,还有硫化物:FeS、MnS等。 ★ 炉渣之间动态平衡 氧化物分子和化合物分子之间的反应处于动平衡状态,例如: Ca0·Si02=CaO+Si02,随着温度的升高,分解程度增大,自由氧化物 分子的浓度增而。
2[P] + 5(FeO) = (P2O5) + 5[Fe]
3(FeO) +(P2O5) = (3FeO·P2O5) 在炼钢过程中,由于上述化学反应是一个放热反应,炼钢初期,炉温不高时对 脱磷反应是有利的。由于生成的磷酸铁( 3FeO·P2O5)在高温下是不稳定的化合物, 当炉温升高时,它可以重新分解,使磷又进入金属。为了使磷酸铁不发生分解反应, 需向炉内加入石灰,使磷酸铁转比为稳定的磷酸钙,其反应为: (3FeO·P2O5) + 4(CaO) = (4CaO·P2O5 + 3(FeO) 综上所述,碱性炼钢炉内脱磷的总反应为: 2[P] + 5(FeO) + 4(CaO) =(4CaO·P2O5) + 5[Fe]
转炉炼钢原理及工艺

转炉炼钢原理及工艺
转炉炼钢是通过加热合金材料,然后将其在氧气中抽出到转炉,形成一个旋转坩埚里,再使材料在转炉内不断熔化、混合、渣滓沉淀,达到钢的熔化和净化,最后冷却固化,即可获得均匀的高质量的钢的过程。
转炉炼钢的工艺路径主要包括:原料进炉、熔炼、净化、合金添加、出炉等步骤。
1、原料进炉:将碳钢和合金料装入转炉,加热至溶化温度,开始熔融。
2、熔炼:转炉内熔融的温度受多种因素的影响,如加料量、加料温度、炉气系统的平衡性、熔炼时间等。
3、净化:即清洁熔化渣滓,消除杂质,把金属液中的杂质置于渣滓中,让金属液纯度升高。
4、合金添加:将净化后的钢液入合金添加系统,加入合金钢料,使钢液按照要求的成分,营造钢种具有相应的技术性能。
5、出炉:金属液改变形态,冷却成指定的形状和尺寸,经过纯化后形成高质量钢。
7、转炉炼钢工艺II
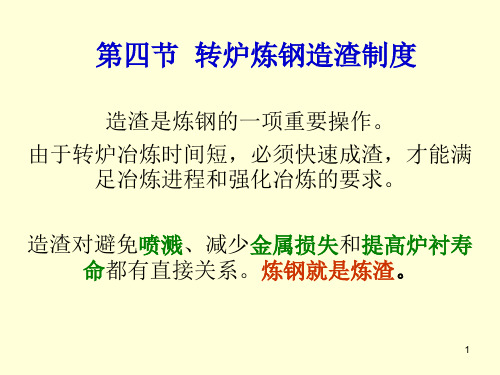
7
吹炼末期: 要保证去P、S所需的炉渣高碱度R ,同时要控制好 终渣氧化性∑( FeO) ,末期渣要化透作粘。
8
转炉炼钢造渣制度
冶炼钢种不同,对炉渣的要求也不同. 如: 对冶炼含碳量≥ 0.10%的镇静钢,终渣氧化铁∑(FeO) 通常应控制<15~20%。 在保证去P的前提下,渣∑(FeO) 尽可能控制在低限;
20
2 3 2 RFe 83pm, RFe 67 pm, RO 132pm
转炉炼钢造渣制度
石灰熔化速度
vCaO k (CaO 1.35MgO 1.09SiO2 2.75FeO 1.9 MnO 39.1) exp{ k __ 系数; T __ 温度, K ; vC __ 脱碳速度. 2550 0.7 0.5 }vC G T
0 +1.9MnO-39.1)exp{-2550/T} vC.7 G 0.5
式中: k—系数; VC—脱碳速度; T—温度,K; G—石灰重量。
18
转炉炼钢造渣制度
影响石灰熔化速度的主要因素有: 参与熔化反应成分的浓度; 流体力学有关的传质; 熔池温度; 反应面积; 石灰质量等。 炉渣成分—— 首先,FeO对石灰的熔化速度具有决定性的有利作用, 它是石灰熔化的基本熔剂。
钙镁橄榄石: 是锰橄榄(2MnO.SiO2)、铁橄榄石(FeO. SiO2) 、镁橄 榄石(MgO.SiO2)和硅酸二钙(2CaO SiO2)的混合晶 体。
11
转炉炼钢造渣制度
吹炼中期: 由于炉温升高石灰进一步熔化,同时因为Vc加快而导 致渣中∑(FeO)逐渐降低,使石灰熔化速度有所减缓。
随着C-O反应进行,炉渣泡沫化程度迅速提高。
第四节 转炉炼钢造渣制度
转炉炼钢工艺流程介绍

转炉炼钢工艺流程介绍
转炉炼钢是一种常见的钢铁生产工艺,下面是其工艺流程的介绍:
1. 铁水预处理:首先,将铁水经过除渣工序,去除其中的杂质和非金属物质,提高炉内的纯净度和质量。
2. 转炉兑炉:之后,将预处理后的铁水加入转炉中,同时加入适量的废钢、废铁等回收材料。
这些回收材料能够提供多种元素和合金,有助于调整并优化转炉内的化学成分。
3. 吹氧气:然后,通过吹氧装置向转炉中喷吹氧气。
氧气与铁水中的杂质反应生成氧化物,如氧化碳、氧化硅等,这些氧化物随废气排出转炉。
4. 炼钢反应:转炉内的铁水经过吹氧反应后,温度升高,同时炉内的化学反应也进行着。
在高温和高氧气作用下,铁水中的碳、硅等元素会逐渐氧化和燃烧,生成气体和渣。
5. 加入合金:根据需要,再加入一定量的合金,如镍、铬、锰等。
合金的加入可以调整钢的成分和性能,改善钢的质量。
6. 钢包炉脱氧:在转炉炼钢过程中,钢中可能还含有一定量的氧气。
为了降低钢中的氧含量,通常还需将钢浇入预先加入了脱氧剂的钢包炉中,并进行搅拌。
脱氧剂能与钢中的氧气反应生成气体,进一步减少钢中的氧含量。
7. 出钢和连铸:最后,将炼制好的钢浇入连铸机中,进行连续铸造,制成钢坯。
这些钢坯经过后续的轧制和加工,可制成各种形状和规格的钢材。
值得注意的是,转炉炼钢是一个复杂的过程,涉及到许多工艺参数和控制指标,操作人员需要根据实际情况进行调整和控制,以达到所需的钢材质量。
转炉炼钢主要工艺介绍(PPT 68页)

6
1.金属料
• 1)铁水:占钢铁料的(75~100%) 主要要求 成分:[Si]、[Mn]、[P]、[S] 温度: T
7
铁水成分及温度影响
• Si影响 • 转炉炼钢重要发热元素,[Si]↑0.1%,废钢比↑1.0%。 • 铁水合适的[Si]0.3-0.5%。 • [Si] >0.6%,渣量增加并引起喷溅;渣中(SiO2)↑。 • 石灰加入量=(2.14×R× [Si] )×1000 /(石灰CaO
• 热来源于:
• 转炉炼钢不需要外来热源;
铁水物理热及元素氧化化学热。 铁水及废钢的合理配比须根据炉子的热平衡计算确定。 • 硅的作用 优点:因发热量大,增大废钢加入量,一般铁水中Si增 加0.1%,废钢比增大1%。 缺点:增大渣量,侵蚀炉衬一般控制在0.3-0.5%。
29
转炉兑铁水操作现场图示
一范围 0.75-1.1Mpa。 • 枪位,由冲击深度决定,1/3-1/2。 • 供氧强度(Nm3/t.min) 决定冶炼时间,但太大,喷溅可
能性增大,一般3.0-4.0。
34
氧枪
氧枪是转炉供氧的 主要设备,它是由 喷头、枪身和尾部 结构组成。 喷头是用导热性良 好的紫铜经锻造和 切割加工而成,也 有用压力浇铸而成 的。喷头的形状有 拉瓦尔型、直筒型 和螺旋型等。目前 应用最多的是多孔 的拉瓦尔型喷头。
30
2.2造渣制度
• 造渣制度就是确定合适的造渣方法、渣料加入量和时 间,以及如何快速成渣。
• 炼钢就是炼渣。通过造渣,快速脱P、脱S,减少喷溅, 保护炉衬,降低终点氧含量。
• 石灰的熔解: 加开石始灰后吹,氧由时2渣Fe中O·主Si要O2是→CSaiOO·2F,eOM·nSOi,O2F→eO2,C是aO酸·S性iO渣2 ,, 2CaO·SiO2难熔渣,石灰溶解有些停滞,出现返干。
转炉炼钢工艺流程(DOC 85页)

转炉炼钢工艺流程(DOC 85页)1、转炉装料实施转炉炼钢时,铁水和废钢是常用的原材料。
装料过程通常分为以下几个步骤:1.1、预热在铁水、废钢的混合物装入转炉后,需要预热以提高装料温度,矫正温度误差,快速分离铁水和渣等,塞子还需热扩张到顶部口,用以克服钢水重力作用自由流出,保持均匀的镁砖渗透不锈,防止醒炉等问题。
1.2、加料加料的目的是在转炉中形成充分的钢水池,同时保持钢水池边界的位置,包括质心位置、钢水表面、钢水表面高度的稳定等。
一般将铁水或废钢当量在30吨左右,先进行静置,等到泡沫降低后,将料装入转炉中。
此时,需要持续对氧气的供氧量和氮气的泡沫造成的支撑力进行调控,防止钢水波动,以避免产生物料堵口、倒爆等问题。
1.3、出钢当减量完成、稳步脱碳后,将熔钢炉盖打开,快速开孔,掏出钢水,并用滑道将钢水导入铸锭机进行铸造。
1.4、出渣在将钢水倒出之前,需要先将渣体清空,控制渣体含量较低,渣量控制在6%以下。
此时需要将氧气加注量逐渐增大,切割剂加量缩小,减小气泡的大小和数量,降低上渣的难度,以确保和稳定出渣。
2、转炉炼钢工艺路线在钢铁生产中,炼钢是一个重要的环节,生产过程要涉及多个工序,包括转炉熔炼、连铸浇铸等。
以下是转炉炼钢工艺路线的详细流程:2.1、预热在炉前铁水池加压,使其经过预热后降至转炉送风口(或高炉迎风口),并在炉内通入氧气、切割剂,将两种气体切割,形成燃料气体包,快速将铁水预热至1000℃以上。
预热时要保证铁水流畅,通风量,防止“水过桥”造成漏钢、涨钢和浪涌等问题。
2.2、炼钢炼钢过程分为软化温度、脱硫、切割、脱磷、调钢、脱碳、出钢和出渣等工序。
其中,软化温度、脱硫、调钢和出钢是关键环节。
一般在这些过程中,需要严格控制氧气、切割剂和氮气的加注量,以达到钢锭的化学成分标准要求;如果处理不当,就会导致脱硫不彻底、磷钢减少、浪涌、固定夹杂物等问题。
2.3、出钢出钢是整个炼钢过程的最后一步,需要严格控制出钢温度和温度偏差,以达到出口规范的要求。
转炉炼钢工艺

转炉炼钢工艺引言转炉炼钢工艺是一种常用的钢铁生产工艺,其原理是使用巨大的转炉进行冶炼,通过高温燃烧将生铁中的杂质熔化分离,得到高品质的钢铁产品。
本文将详细介绍转炉炼钢工艺的过程、设备和优势。
工艺过程转炉炼钢工艺主要由以下几个步骤组成:1.加炉:在转炉中加入一定数量的生铁和废钢,根据不同的钢种和质量要求控制添加比例。
2.预热:通过燃料燃烧加热炉体,将炉体温度升至一定的范围,为后续冶炼做准备。
3.唤氧:将预先加入的氧气注入转炉中,氧气与炉内的碳、硫等元素发生反应,使其氧化生成气体冒出炉口。
4.碱性脱硫:在钢水中加入一定量的含碱性物质的脱硫剂,使浸渍在钢水中的硫元素氧化为气体并脱出。
5.酸性脱磷:在钢水中加入一定量的含酸性物质的脱磷剂,使浸渍在钢水中的磷元素氧化为气体并脱出。
6.合金化:根据需要,在钢水中加入一定量的合金元素,如铬、锰等,以调节钢的性能。
7.保温装钢:将炉中冶炼好的钢水倒入铸钢坑、铸型等装置中进行冷却和凝固。
设备转炉炼钢工艺需要使用专用的转炉设备,该设备主要由以下几个组成部分:1.转炉本体:转炉本体是整个工艺最关键的部分,它承载着冶炼过程的全部任务。
转炉一般采用大型圆筒形设计,底部有一定数量的喷孔以供氧气进入。
2.转炉支承:转炉支承是将转炉本体固定在地基上的部分,以保证炉体的稳定运行。
3.强制鼓风系统:由鼓风机、风箱等组成,用于向转炉中供给氧气,促进燃烧和炉内反应的进行。
4.喷吹系统:包括氧枪、煤粉喷吹器等,用于将氧气、燃料喷入转炉中,以调节炉内的温度和氧气含量。
5.出渣系统:用于将炉内产生的渣料排出转炉,保持炉内清洁。
工艺优势转炉炼钢工艺相比于其他炼钢工艺具有以下优势:1.生产能力强大:转炉炼钢工艺灵活可调,产能大。
转炉设备可以进行批量生产,快速完成大批量的钢水冶炼,满足市场需求。
2.冶炼效率高:转炉炼钢工艺采用高温燃烧和强制鼓风系统,能够快速将生铁中的杂质熔化脱除,同时还可以进行合金化调节,提高钢的质量和性能。
转炉炼钢原理及工艺介绍

转炉炼钢原理及工艺介绍引言转炉炼钢是一种常用的钢铁生产工艺,具有高效、灵活、环保等特点。
本文将介绍转炉炼钢的原理及工艺流程。
一、转炉炼钢原理转炉炼钢是通过在高温下将生铁与废钢等原料进行反应,去除杂质,调整合金成分来生产钢铁。
其原理基于以下几个重要的化学反应步骤:1.氧化反应:在高温下,将生铁中的杂质氧化为气体或溶于渣中。
主要的氧化反应有:Fe+C+O2=FeO+CO、Mn+C+O2=MnO+CO等。
2.还原反应:在氧化反应的基础上,通过还原剂(如脱氧剂)来还原产生的氧化物。
主要还原反应有:FeO+CO=Fe+CO2、MnO+CO=Mn+CO2等。
3.合金化反应:在还原反应的基础上,通过加入适量合金元素来调整合金成分。
合金化反应可以通过添加合金块、废钢等方式实现。
通过以上化学反应的组合,转炉炼钢可以控制合金成分、去除杂质、调整温度等,从而得到符合要求的钢铁产品。
二、转炉炼钢工艺介绍转炉炼钢的工艺可以分为以下几个主要步骤:1.预处理:生铁、废钢等原料经过破碎、除尘等处理后,进入转炉炉前料斗。
2.加料:原料从炉前料斗通过螺旋输送机被输送至转炉炉缸中。
3.预热:将炉缸中的原料进行预热,以提高反应效果。
4.吹炼:将炉底引入的高纯氧吹入炉缸中,通过氧化反应和还原反应去除杂质、调整合金成分。
5.加料:在吹炼过程中,适量添加合金块、废钢等调整合金成分。
6.测温:通过测温仪器监测和调节炉内温度。
7.出渣:通过倾炉装置将产生的渣浆从转炉中排出。
8.抽炉:将炉内得到的钢液通过倾炉装置倾出,并进行钢液处理(如脱氧、出气、精炼等)9.浇铸:将经过处理的钢液进行浇铸,得到需要的钢铁产品。
三、转炉炼钢的优势转炉炼钢工艺具有以下几个优势:1.高效:转炉炼钢的操作灵活,能够快速调整合金成分和生产规格,生产效率高。
2.资源利用:转炉炼钢可以利用废钢等再生资源,减少资源浪费。
3.环保:转炉炼钢排放的烟尘、废气等污染物可以通过环保设施进行处理,达到环保要求。
- 1、下载文档前请自行甄别文档内容的完整性,平台不提供额外的编辑、内容补充、找答案等附加服务。
- 2、"仅部分预览"的文档,不可在线预览部分如存在完整性等问题,可反馈申请退款(可完整预览的文档不适用该条件!)。
- 3、如文档侵犯您的权益,请联系客服反馈,我们会尽快为您处理(人工客服工作时间:9:00-18:30)。
ⅰ炉渣“返干”、喷溅,中期渣粘度 要适宜;
ⅱ泡沫渣过渡喷溅; ⅲ氧枪操作不当引起喷溅。
“返干”—转炉炼钢的吹炼中期 , 由于脱碳速度
大 , 大量的 CO 气泡能冲破渣层而排出 , 炉渣碱
度高Fe,O(
) 较低 ,SiO2 、 P205 表面活性物质
通常应控制<15~20%。
在保证去P的前提下,渣∑(FeO) 尽可能控制在低限;
冶炼沸腾钢时,终渣∑(FeO) 通常>12%,需避免终渣 氧化性过弱或过强。
9
总之,炉渣泡沫化不足,将显著降低金属脱磷、脱 硫率;
炉渣过泡,容易导致剧烈溢渣和喷溅,增加吹损, 降低炉子寿命。
2.转炉成渣过程 吹炼初期: 液态炉渣主要来自铁水中Si、Mn、Fe的氧化物。
c.流动性 ;d.适度泡沫化。
2
炉渣氧化性的表示方法有: ⅰ、∑( FeO) = ( FeO) %+1.35 ( Fe2O3)%; 1.35---1g Fe2O3中氧量相当的FeO中氧量。
ⅱ、(TFe)表示FeO含量 TFe=0.78× ( FeO) +0.7 × ( Fe2O3)。 0.78--- 1g ( FeO) 中含铁量; 0.7----- 1g ( Fe2O3)中含铁量。
转炉条件下石灰熔化速度的近似公式为:
vCaO = k(CaO+1.35MgO+1.09SiO2+2.75FeO
+1.9MnO-39.1)exp{-2550/T}
v 0.7 C
G
0.5
式中: k—系数; VC—脱碳速度; T—温度,K; G—石灰重量。
18
转炉炼钢造渣制度
影响石灰熔化速度的主要因素有: 参与熔化反应成分的浓度; 流体力学有关的传质; 熔池温度; 反应面积; 石灰质量等。 炉渣成分—— 首先,FeO对石灰的熔化速度具有决定性的有利作用,
第二步,炉渣与石灰在反应区进行化学反应并形成 新相,反应不仅在石灰块外表面上进行,而且在 内部气孔表面上进行;
第三步,反应产物离开反应区向炉渣熔体中转移。
17
显然,加速石灰熔化的关键是克服石灰熔化的限制环 节。首先应极力避免形成高熔点坚硬致密的2CaO SiO2壳层,当其产生后,应该设法迅速破坏掉这一 阻碍石灰熔化的壳层,以保成炉渣组分能够迅速不 断地向石灰表面和内部渗入。
12
转炉炼钢造渣制度
原因: 随着炉渣R的提高,CaO与SiO2的亲和力比其它氧化物
大,CaO逐渐取代钙镁橄榄石中的其它氧化物,在石 灰表面生成高熔点的坚硬致密的2CaO SiO2壳层,阻 碍了新鲜炉渣向石灰内部的渗入,导致石灰溶解速度 下降。
石灰与钙镁橄榄石和玻璃体SiO2作用时,生成CaO SiO2,3 CaO 2SiO2,2 CaO SiO2和3 CaO SiO2等产 物,其中最可能和最稳定乃是熔点2130℃为的2 CaO SiO2。
的活度降低 , 因此引起泡沫渣的条件不如吹炼初
期 , 熔渣出现 固相质点即" 返干 " 现象 。
6
7
吹炼末期: 要保证去P、S所需的炉渣高碱度R ,同时要控制好
终渣氧化性∑( FeO) ,末期渣要化透作粘。
8
转炉炼钢造渣制度
冶炼钢种不同,对炉渣的要求也不同. 如: 对冶炼含碳量≥ 0.10%的镇静钢,终渣氧化铁∑(FeO)
二.石灰熔化机理
石灰熔化关系到成渣的快慢,成渣又影响脱、脱硫。
从炉渣下层取出未熔石灰块,观察其断面并分析从
外到内各层的化学成分可知,炉渣由表及里向石灰 块内部渗透,表面有反应产物形成。
石灰熔化 是复杂的多相(固-液)反应。
液态渣
固态
16
其过程可分为:
第一步,液相炉渣经石灰块外部扩散边界层向反应 区扩散,并沿气孔向石灰块内部迁移;
P198~199 13
14
转炉炼钢造渣制度
吹炼末期: Vc下降,渣中∑(FeO)再次增高,石灰继续熔化并
加快了熔化速度。同时,熔池中乳化和泡沫现象 趋于减弱和消失。
在吹炼末期,RO相急剧增加,生成的3 CaO SiO2 也分解为CaO SiO2和CaO,并有2CaO.Fe2O3生 成。
15
转炉炼钢造渣制度
3
主要成分是: CaO、MgO、SiO2、Al2O3、MnO、 FeO、P2O5、CaS、FeS、MnS等。
炉渣的作用: ①、脱磷、硫; ②、保温、防止金属再氧化及吸气; ③、吸收上浮的夹杂物及反应产物; ④、减少炉衬的蚀损。
4
冶炼各期炉渣特点
吹炼初期:
要保持炉渣具有较高的氧化性∑( FeO),以促进石灰 熔化,迅速提高炉渣碱度R。
11
转炉炼钢造渣制度
吹炼中期: 由于炉温升高石灰进一步熔化,同时因为Vc加快而导
致渣中∑(FeO)逐渐降低,使石灰熔化速度有所减缓。
随着C-O反应进行,炉渣泡沫化程度迅速提高。
由于C-O反应大量消耗渣中∑(FeO),以及有时得不到 超过渣系液相线的正常过热温度,使化渣条件恶化, 引起炉渣异相化,并出现“返干”。
10
转炉炼钢造渣制度
加入炉内的大量石灰块,由于温度低表面形成冷凝外 壳,造成熔化滞止期,随着Fe的氧化和温度升高, 促进了石灰的熔化,使碱度R逐渐提高。
取样表明:初期渣的主要矿物为钙镁橄榄石 m[氧(F化e.物Mn(R.MOg)相.C很a)S少iO。4]和玻璃体(SiO2)<7~8%,自由
钙镁橄榄石: 是榄体锰石。橄(榄M(g2OM.nSOiO.S2)i和O2硅)、酸铁二橄钙榄(2石C(aFOeOS.iOS2i)O的2)混、合镁晶橄
第四节 转炉炼钢造渣制度
造渣是炼钢的一项重要操作。 由于转炉冶炼时间短,必须快速成渣,才能满
足冶炼进程和强化冶炼的要求。
造渣对避免喷溅、减少金属损失和提高炉衬寿 命都有直接关系。炼钢就是炼渣。
1
ห้องสมุดไป่ตู้
转炉炼钢造渣制度
一.成渣过程
来源: 渣料、金属元素氧化产物和脱磷、硫产物、炉
衬等。 1.炼钢对炉渣要求 转炉冶炼各期,都要求炉渣具有一定的: a.碱度R; b.合适的氧化性∑( FeO)
尽量提高前期去磷去硫率和避免酸性渣侵蚀炉衬,前 期要防止炉渣过稀;
冶炼前期,熔池较弱, [C]-[O]反应滞后,温度偏低,
渣中
积Fe累O。
但当硅氧化结束, [C]-[O]反应开始,温度上升,大
炼钢液滴进入炉渣,与( FeO)反应,产生大量CO
气泡,而累积层极大的膨胀功带动炉渣从炉口喷出。
5
吹炼中期: