整车匹配计算与分析 [兼容模式]
新能源汽车的动力系统整车匹配研究

新能源汽车的动力系统整车匹配研究随着环保意识的增强以及对传统燃油汽车的排放和资源消耗问题的担忧,新能源汽车逐渐成为了人们关注的焦点。
而新能源汽车的动力系统是其核心技术之一,对整车性能和性价比起到至关重要的作用。
本文将就新能源汽车的动力系统整车匹配研究进行探讨。
一、新能源汽车动力系统简介新能源汽车动力系统包括电动机、电池组和电控系统。
其中,电动机是提供动力的核心部件,电池组则储存电能,电控系统则实现对整个动力系统的控制和调节。
二、动力系统整车匹配原则在新能源汽车的动力系统整车匹配中,需要考虑多个方面的因素,确保整车性能和实际使用需求的匹配。
1. 动力系统的动力性能与整车匹配不同型号的新能源汽车需要提供不同的动力性能,如加速性、续航里程等。
所以在动力系统整车匹配时,应根据车辆的使用场景和功率需求来选择合适的电动机类型和功率输出。
2. 电池组能量与整车匹配电池组的储能能力直接决定了新能源汽车的续航里程。
因此,在整车匹配中,应选择电池组的储能容量和放电性能以满足车辆的需求。
同时还需考虑电池组的重量、体积等因素对整车的影响。
3. 电控系统的稳定性与整车匹配电控系统是新能源汽车的大脑,负责控制电动机和电池组的工作状态。
在整车匹配中,需要确保电控系统的稳定性,并根据动力系统的特点进行参数调节以提供更好的驾驶体验。
4. 动力系统整车热管理与匹配新能源汽车动力系统的高效运行需要保持合适的温度范围。
散热系统的设计和匹配将直接影响整车性能和动力系统的寿命。
因此,在动力系统整车匹配中,应注意热管理系统的设计与匹配。
三、动力系统整车匹配研究方法为了实现新能源汽车动力系统的整车匹配,研究人员采用了多种方法和技术。
1. 整车仿真模拟利用计算机仿真软件,构建新能源汽车的整车模型,对不同参数进行模拟和优化,从而得到最佳的动力系统整车匹配方案。
2. 硬件原型测试通过搭建新能源汽车的硬件原型,进行实际测试和数据采集。
根据测试结果,对动力系统进行调整和优化,以达到最佳的整车匹配效果。
增程式电动车参数匹配与分析

增程式电动车参数匹配与分析蒋建华;范港;张翀【摘要】针对增程式电动车研发中动力系统的参数匹配问题,以整车动力性和续航里程为设计目标,从电驱动系统、动力电池系统、内燃式增程器系统等方面出发,设计了增程式电动车动力系统参数,并以软件AVL CRUISE为仿真平台,采用增程器恒功率控制策略搭建了整车模型,验证了所设计的增程式电动车的整车动力性和续航里程.研究结果表明,车辆的最高车速、加速性能和爬坡性能满足车辆动力性能要求;车辆在10 km/h和15 km/h匀速工况下纯电动续航里程和增程模式的续航里程也满足车辆续航里程要求.【期刊名称】《机电工程》【年(卷),期】2016(033)003【总页数】5页(P373-377)【关键词】增程式电动车;动力系统;参数匹配;仿真【作者】蒋建华;范港;张翀【作者单位】浙江大学动力机械及车辆工程研究所,浙江杭州310007;浙江大学动力机械及车辆工程研究所,浙江杭州310007;浙江大学动力机械及车辆工程研究所,浙江杭州310007【正文语种】中文【中图分类】TP391.9目前纯电动车受到动力电池比能量小,价格高等因素的影响,并且充电设施复杂充电时间过长,就存在续航里程短不能满足远距离行驶的问题。
为延长EV的续航里程,将燃油发动机和电机组成的发电机作为增程器,与动力蓄电池一起构成动力源,是一种可供选择的方案。
增程式电动车是一种以蓄电池为主动力的电动汽车,只是在车上装了另一个较小功率的车载发电机(增程器)并配置合适大小的油箱,以增加续航里程[1]。
增程式电动车跟串联式电动车的结构相似,发动机仅有的功能是发电。
在串联式混合动力车中,动力电池实际上起到平衡发动机输出功率和电动机输入功率的作用,使发动机一直工作在最佳稳定区,致使电池的电能主要来自发动机而且发动机基本在车辆运行时都在工作。
但是增程式电动车的设计目标是尽量使用电网给蓄电池充电的能量,当蓄电池的SOC低于限定限值后,发动机启动给蓄电池充电的同时又给车辆供给动力,所以发动机的启动频率很低。
数字货运中车货匹配的算法
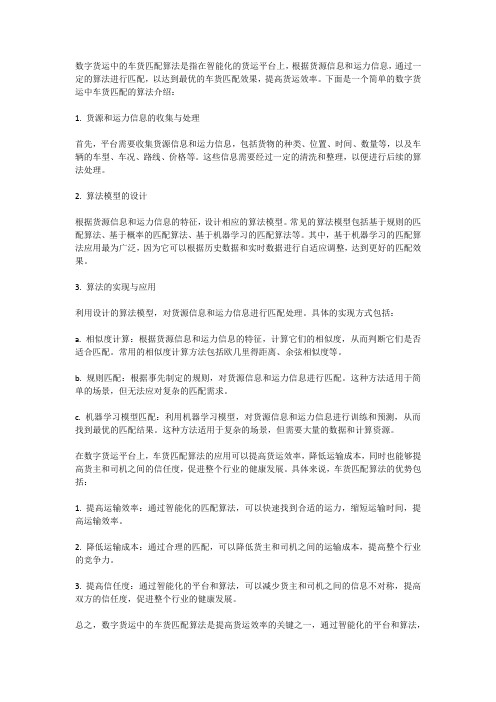
数字货运中的车货匹配算法是指在智能化的货运平台上,根据货源信息和运力信息,通过一定的算法进行匹配,以达到最优的车货匹配效果,提高货运效率。
下面是一个简单的数字货运中车货匹配的算法介绍:1. 货源和运力信息的收集与处理首先,平台需要收集货源信息和运力信息,包括货物的种类、位置、时间、数量等,以及车辆的车型、车况、路线、价格等。
这些信息需要经过一定的清洗和整理,以便进行后续的算法处理。
2. 算法模型的设计根据货源信息和运力信息的特征,设计相应的算法模型。
常见的算法模型包括基于规则的匹配算法、基于概率的匹配算法、基于机器学习的匹配算法等。
其中,基于机器学习的匹配算法应用最为广泛,因为它可以根据历史数据和实时数据进行自适应调整,达到更好的匹配效果。
3. 算法的实现与应用利用设计的算法模型,对货源信息和运力信息进行匹配处理。
具体的实现方式包括:a. 相似度计算:根据货源信息和运力信息的特征,计算它们的相似度,从而判断它们是否适合匹配。
常用的相似度计算方法包括欧几里得距离、余弦相似度等。
b. 规则匹配:根据事先制定的规则,对货源信息和运力信息进行匹配。
这种方法适用于简单的场景,但无法应对复杂的匹配需求。
c. 机器学习模型匹配:利用机器学习模型,对货源信息和运力信息进行训练和预测,从而找到最优的匹配结果。
这种方法适用于复杂的场景,但需要大量的数据和计算资源。
在数字货运平台上,车货匹配算法的应用可以提高货运效率,降低运输成本,同时也能够提高货主和司机之间的信任度,促进整个行业的健康发展。
具体来说,车货匹配算法的优势包括:1. 提高运输效率:通过智能化的匹配算法,可以快速找到合适的运力,缩短运输时间,提高运输效率。
2. 降低运输成本:通过合理的匹配,可以降低货主和司机之间的运输成本,提高整个行业的竞争力。
3. 提高信任度:通过智能化的平台和算法,可以减少货主和司机之间的信息不对称,提高双方的信任度,促进整个行业的健康发展。
整车匹配计算(改)

06
整车匹配计算案例研究
案例一:某电动汽车的底盘系统匹配
底盘系统匹配
底盘系统是电动汽车的重要组成部分,包括悬挂系统、制动系统、转向系统等。在底盘系 统匹配过程中,需要考虑多种因素,如车辆性能要求、行驶工况、动力电池特性等。
计算方法
采用多体动力学、有限元分析等计算方法,对底盘系统的各个子系统进行建模和仿真分析 ,以确定最佳的匹配参数和设计方案。
Байду номын сангаас果评估与优化
总结词
评估性能和改进方案
详细描述
根据性能仿真的结果,评估整车的性能指标 是否满足设计要求,如果不满足,则需要对 参数进行优化调整,重复性能仿真的过程, 直到满足设计要求为止。最终输出的结果可
以为实际生产提供指导和参考。
04
整车匹配计算工具与技 术
CAD建模技术
总结词
CAD建模技术是整车匹配计算中的基础工具,用于创 建车辆零部件和整车的三维模型。
车身系统匹配
车身系统匹配是指根据车辆的外观设计、结构强度、空气动力学等要求,选择合 适的车身材料、结构、工艺等,并确定它们之间的匹配关系。
车身系统匹配需要考虑车辆的美观性、耐久性、经济性等多个方面,以确保车辆 在长期使用过程中的优异表现。
03
整车匹配计算流程
需求分析
总结词
明确计算目标
详细描述
在整车匹配计算中,首先需要明确计算的目标和要求,包括需要优化的性能指标、约束条件以及计算精度等,为 后续的参数设计和性能仿真提供指导。
底盘系统匹配需要考虑车辆的操控稳 定性、舒适性、安全性等多个方面, 以确保车辆在各种行驶条件下的优异 表现。
电气系统匹配
电气系统匹配是指根据车辆的用电需 求,选择合适的电池、电机、控制器 等关键部件,并确定它们之间的匹配 关系。
车身匹配总结

车身匹配总结1. 简介车身匹配是一项重要的技术,它的主要作用是根据车辆颜色、车牌号码等信息,将车辆与其所有者或相关的数据库进行匹配。
这项技术广泛应用于交通管理、停车场管理、追踪盗车等领域。
本文将对车身匹配技术进行总结和分析,包括其原理、应用和未来发展趋势。
2. 车身匹配原理车身匹配的核心原理是基于计算机视觉和图像处理技术。
它主要包括以下几个步骤:2.1 图像采集与预处理首先,需要通过摄像头或其他图像采集设备获取车辆的图像。
然后,对图像进行预处理,包括去噪、图像增强等操作,以提高匹配的准确性。
2.2 特征提取在车身匹配中,主要提取的特征有车辆的颜色、车牌号码等。
通过计算车辆图像中的像素值和颜色分布等特征,可以对车辆进行描述和区分。
2.3 数据库匹配通过将提取到的特征与事先建立好的车辆特征数据库进行匹配,可以找到与目标车辆最相似的记录。
匹配算法可以根据实际需求选择,如K近邻算法、支持向量机算法等。
2.4 匹配结果输出最后,根据匹配结果,可以输出匹配的车辆信息,如车主信息、车辆状态等。
3. 车身匹配应用车身匹配技术有广泛的应用场景,下面将介绍其中几个典型的应用。
3.1 交通管理在交通管理中,车身匹配可以用于追踪违法停车、逆向行驶等交通违法行为,并对相应的车辆进行处罚。
通过将车辆图像与交通管理数据库进行匹配,可以快速准确地找到相关车辆和驾驶员。
3.2 停车场管理车身匹配在停车场管理中也有重要作用。
通过车辆图像的匹配,可以实现自动车牌识别和车辆进出记录的管理。
这样可以提高停车场的安全性和管理效率。
3.3 盗车追踪车身匹配可以应用在车辆盗窃案件的调查中。
通过对盗窃车辆的图像进行匹配,可以追踪其行踪和定位,为相关部门提供有力的证据和线索。
4. 车身匹配的挑战与未来发展车身匹配技术在实际应用中仍然面临一些挑战。
首先,车辆图像的质量和角度变化可能会对匹配结果产生影响。
因此,如何提高图像质量和处理角度变化是值得研究的。
电动车辆电磁兼容性整车测量与分析
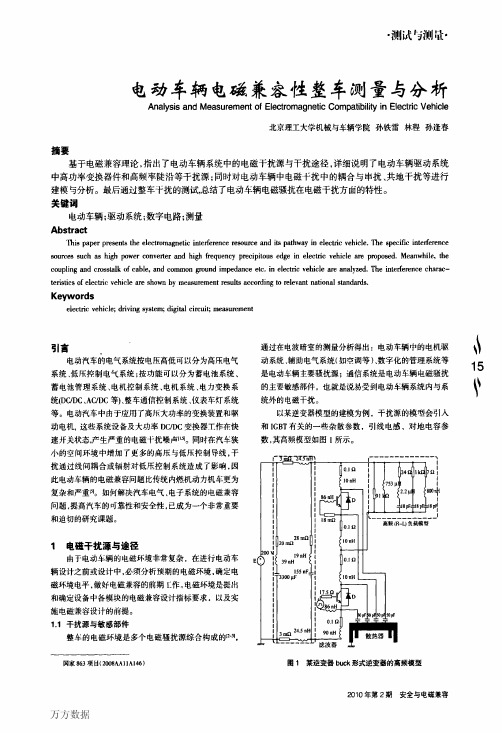
万方数据万方数据作指令。
CAN总线系统非常重要,其节点覆盖整个车体,当局部差模辐射或共模辐射强度增大时,CAN就会受到强烈的电磁干扰,严重影响CAN总线系统的正常通信,通常以错误帧和负载率来衡量总线受到干扰的程度。
如何抑制CAN总线的干扰问题。
提高汽车的可靠性和安全性,已经成为电动车辆工业界面临的一个非常重要和迫切的研究课题。
2整车干扰的测试2.1试验环境与对象某电动汽车生产企业的BJ6123XXXX型电动汽车根据GB14023、GB18387进行整车测试[91,其中规定的实验环境如图3所示。
l一半电波暗室;2一电动车辆;3一天线;4一接收机图3整车电磁辐射限值测量系统2.2试验系统图3中电动车辆在半波屏蔽室中。
电场天线(HFH2一Z6)、磁场天线(HFH2-Z2)分别放在试验车辆前lin与3m距离的位置(左侧是指车辆前进方向的左侧),与接收机(ESIB26)4相连。
电动车辆以一定的速度行驶,测得结果以峰值计量。
3测试结果与分析电动车辆的电气系统主要包括交、直流电源设备、仪器仪表、照明设备和连接电缆,这些组件及连接电路在电动车辆内部构成了庞大的电气系统。
考虑电动车辆电磁兼容的主要问题有:一是电动车辆是否满足不影响对外电磁系统的T作,二是在复杂的电磁环境条件下自身的系统是否能够不受这些自身电磁干扰的影响。
一般情况下,在电动车辆系统的辐射干扰中,共模高频干扰占据着主导地位,而其他频段干扰较小。
对电动汽车整车按照GB14023、CB18387进行电磁辐射干扰测试,测试结果如图4和图5所示,由此可得出如下结论:(1)由图4(a)和图4(b)整车测量结果对比,发现在频率9—150kHz频段,车辆高速时的辐射大于车辆低速·测试!j测适·图4左侧电场垂直极化方向频谱图(9kHz一30GHz)图5左侧电场垂直极化方向频谱图(30MHz一1GHz)时的辐射,这可能是由于电驱动系统功率的增大,其驱动系统的功率变换电路辐射增强,buck逆变器的频率分量及谐波占据此频段,故大速度时的电场强度与小速度时的辐射电场强度相比增大。
混合动力汽车动力系统匹配计算方法研究

混合动力汽车动力系统匹配计算方法研究混合动力汽车动力系统匹配计算方法研究混合动力汽车动力系统的匹配计算方法可以分为以下几个步骤:步骤一:确定车辆性能需求首先,我们需要确定混合动力汽车的性能需求,包括最大速度、加速度、续航里程等。
这些需求将直接影响到动力系统的设计和匹配。
步骤二:确定主要动力源根据车辆性能需求和市场趋势,我们需要确定主要动力源,即内燃机还是电动机。
内燃机可以提供较高的动力输出和长续航里程,但排放较高。
电动机则具有零排放和高效能的优点,但续航里程受到电池容量限制。
步骤三:计算动力需求根据车辆性能需求和主要动力源的选择,我们可以计算出动力需求,即所需的平均功率和峰值功率。
平均功率是为了满足日常驾驶需求,而峰值功率是为了应对加速和爬坡等特殊情况。
步骤四:选择辅助动力源在混合动力汽车中,通常还会配备一个辅助动力源,用于提供额外的动力支援或充电。
常见的辅助动力源包括发电机、超级电容器和燃料电池等。
选择辅助动力源需要考虑其功率输出、能量转换效率和成本等因素。
步骤五:匹配动力系统组件根据动力需求和选择的主要动力源和辅助动力源,我们可以开始匹配动力系统的组件。
这包括选择合适的内燃机或电动机、电池容量、发电机功率和燃料电池堆的大小等。
匹配过程需要综合考虑动力输出、能量转换效率和整车重量等因素。
步骤六:模拟和优化在确定初始动力系统配置后,我们可以通过模拟和优化的方法来评估其性能和经济性。
通过模拟可以预测车辆的动力性能、续航里程和排放等指标,以及整车的燃料消耗和成本。
优化可以帮助我们调整动力系统配置,以达到最佳的性能、经济性和环保性。
步骤七:实际测试和验证最后,为了验证计算结果的准确性,我们需要进行实际的测试和验证。
这包括在实际路况下测试车辆的加速性能、续航里程和排放等指标,以及对整车的燃料消耗和成本进行实际测量。
通过实际测试和验证,我们可以进一步优化动力系统的配置和调整。
综上所述,混合动力汽车动力系统的匹配计算方法包括确定车辆性能需求、选择主要动力源、计算动力需求、选择辅助动力源、匹配动力系统组件、模拟和优化,以及实际测试和验证。
某纯电动汽车动力系统匹配计算报告
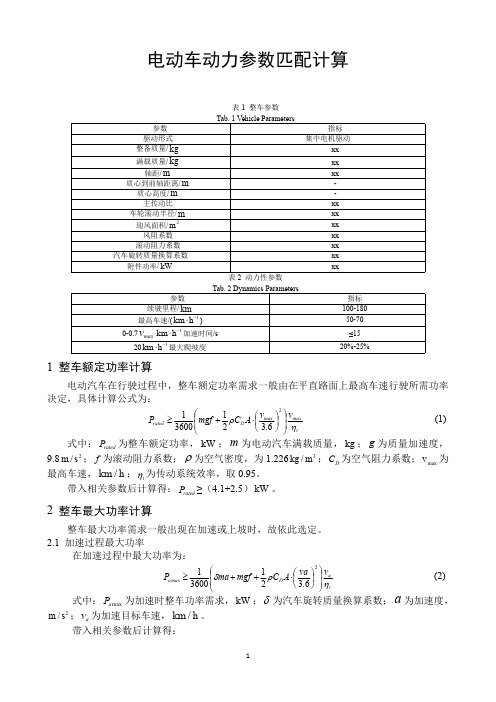
电动车动力参数匹配计算表2动力性参数Tab.2Dynamics Parameters参数指标续驶里程/km 100-180最高车速/(1km h -⋅)50-700-0.7max v 1km h -⋅加速时间/s≤15201km h -⋅最大爬坡度20%-25%1整车额定功率计算电动汽车在行驶过程中,整车额定功率需求一般由在平直路面上最高车速行驶所需功率决定,具体计算公式为:t max max D ratedv .v A C mgf P ηρ⎪⎪⎭⎫ ⎝⎛⎪⎭⎫ ⎝⎛⋅+≥2632136001(1)式中:rated P 为整车额定功率,W k ;m 为电动汽车满载质量,kg ;g 为质量加速度,9.82s /m ;f 为滚动阻力系数;ρ为空气密度,为1.2263m /kg ;D C 为空气阻力系数;max v 为最高车速,h /km ;t η为传动系统效率,取0.95。
带入相关参数后计算得:rated P ≥(4.1+2.5)W k 。
2整车最大功率计算整车最大功率需求一般出现在加速或上坡时,故依此选定。
2.1加速过程最大功率在加速过程中最大功率为:t aD maxa v .a v A C mgf ma P ηρδ⎪⎪⎭⎫ ⎝⎛⎪⎭⎫ ⎝⎛⋅++≥2632136001(2)式中:max a P 为加速时整车功率需求,W k ;δ为汽车旋转质量换算系数;a 为加速度,2s /m ;a v 为加速目标车速,h /km 。
带入相关参数后计算得:表1整车参数Tab.1Vehicle Parameters参数指标驱动形式集中电机驱动整备质量/kg xx满载质量/kg xx 轴距/mxx 质心到前轴距离/m -质心高度/m -主传动比xx 车轮滚动半径/m xx 迎风面积/2m xx 风阻系数xx 滚动阻力系数xx 汽车旋转质量换算系数xx 附件功率/Wk xx在0-0.7max v h /km 加速时功率需求分别为:max a P ≥(13.7+2.5)W k ;0-max v h /km 加速时功率需求分别为:max a P ≥(22.8+2.5)W k 。
车货匹配算法策略
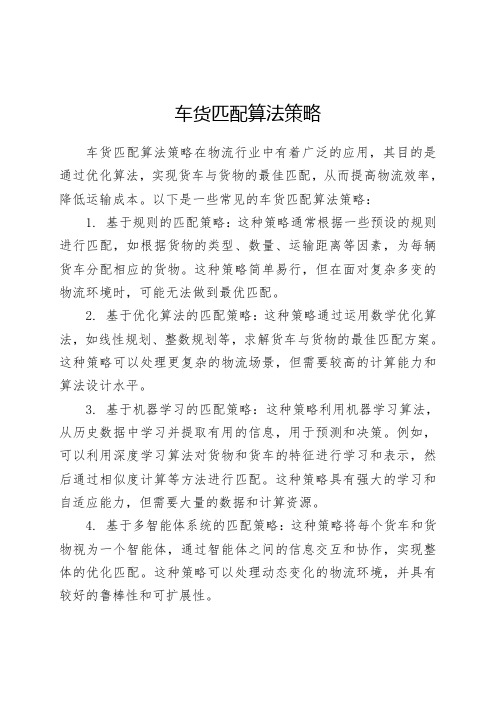
车货匹配算法策略车货匹配算法策略在物流行业中有着广泛的应用,其目的是通过优化算法,实现货车与货物的最佳匹配,从而提高物流效率,降低运输成本。
以下是一些常见的车货匹配算法策略:1. 基于规则的匹配策略:这种策略通常根据一些预设的规则进行匹配,如根据货物的类型、数量、运输距离等因素,为每辆货车分配相应的货物。
这种策略简单易行,但在面对复杂多变的物流环境时,可能无法做到最优匹配。
2. 基于优化算法的匹配策略:这种策略通过运用数学优化算法,如线性规划、整数规划等,求解货车与货物的最佳匹配方案。
这种策略可以处理更复杂的物流场景,但需要较高的计算能力和算法设计水平。
3. 基于机器学习的匹配策略:这种策略利用机器学习算法,从历史数据中学习并提取有用的信息,用于预测和决策。
例如,可以利用深度学习算法对货物和货车的特征进行学习和表示,然后通过相似度计算等方法进行匹配。
这种策略具有强大的学习和自适应能力,但需要大量的数据和计算资源。
4. 基于多智能体系统的匹配策略:这种策略将每个货车和货物视为一个智能体,通过智能体之间的信息交互和协作,实现整体的优化匹配。
这种策略可以处理动态变化的物流环境,并具有较好的鲁棒性和可扩展性。
在实际应用中,可以根据具体的物流场景和需求,选择合适的车货匹配算法策略。
同时,也可以将多种策略进行组合和优化,以进一步提高匹配效果。
例如,可以先使用基于规则的匹配策略进行初步筛选,然后再使用优化算法或机器学习算法进行精细匹配。
此外,为了实现更高效的车货匹配,还可以考虑以下因素:1. 实时性:确保算法能够及时响应物流需求的变化,实时更新匹配结果。
2. 准确性:提高算法的匹配准确率,减少误配和空驶现象。
3. 稳定性:确保算法在不同场景下都能保持稳定的性能表现。
4. 可扩展性:随着物流规模的不断扩大和业务需求的增加,算法应具备良好的可扩展性,以适应更大的物流网络和更复杂的匹配需求。
整车设计计算讲解
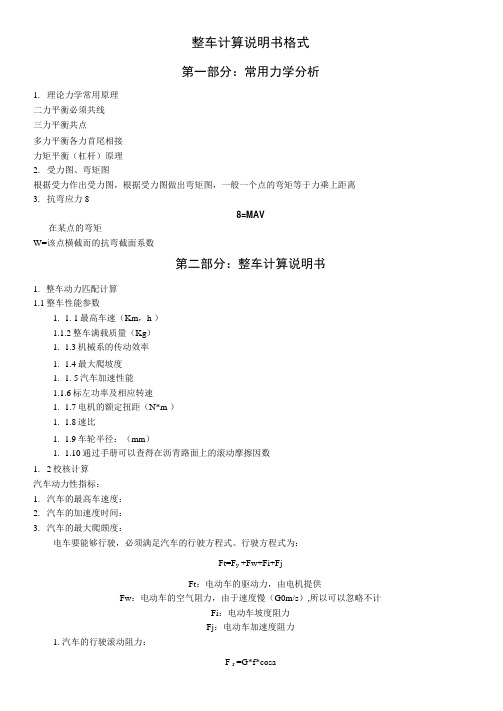
整车计算说明书格式第一部分:常用力学分析1.理论力学常用原理二力平衡必须共线三力平衡共点多力平衡各力首尾相接力矩平衡(杠杆)原理2.受力图、弯矩图根据受力作出受力图,根据受力图做出弯矩图,一般一个点的弯矩等于力乘上距离3.抗弯应力88=MAV在某点的弯矩W=该点横截而的抗弯截面系数第二部分:整车计算说明书1.整车动力匹配计算1.1整车性能参数1. 1. 1最高车速(Km,h )1.1.2整车满载质量(Kg)1. 1.3机械系的传动效率1. 1.4最大爬坡度1. 1. 5汽车加速性能1.1.6标左功率及相应转速1. 1.7电机的额定扭距(N*m )1. 1.8速比1. 1.9车轮半径:(mm)1. 1.10通过手册可以查得在沥青路面上的滚动摩擦因数1.2校核计算汽车动力性指标:1.汽车的最高车速度:2.汽车的加速度时间:3.汽车的最大爬颇度:电车要能够行驶,必须满足汽车的行驶方程式。
行驶方程式为:Ft=F y +Fw+Fi+FjFt:电动车的驱动力,由电机提供Fw:电动车的空气阻力,由于速度慢(G0m/s),所以可以忽略不计Fi:电动车坡度阻力Fj:电动车加速度阻力1.汽车的行驶滚动阻力:F r =G*f*cosa其中G:汽车的自重;f:汽车在沥青路面上的滚动摩擦因数;a:汽车在行驶时的上坡的坡度,在平直路而上行驶时a=0°2.Fw:电动车的空气阻力,计算公式为:F W=C*A*U M2/21. 15其中:C:电车的空气阻力系数:A:电车的迎风面积;u:电车的速度:3.Fi:电动车坡度阻力,计算公式为:Fi=G*Sina4.Fj:电动车加速度阻力,计算公式为:Fj=m*aa:电车的加速度;5.Ft:电动车的驱动力,计算公式为:Ft二Tt/rTt:作用在驱动轮上面的转矩:r :车轮的半径Tt=T* i*i]T:电机的扭矩:i:汽车的速比:m系统的传动效率:1.2.1最高车速的计算因此在汽车的最高车速下,电机需要提供驱动扭矩:T= F ( *r/i *耳貝中:F『:行驶滚动阻力r:汽车车轮半径i:汽车的速比电机需提供的转速:n=V*i/2*n*r其中:V:汽车的速度电机需提供的功率:P二F / *s/i]其中S:汽车在Is里面行驶的距离n:汽车传动系的效率122最大爬坡度的计算忽略汽车的空气阻力,因此汽车上坡时,必须克服汽车的滚动阻力(Ff)和坡度阻力(Fi)。
电动汽车动力性能匹配计算基本方法

电动汽车动力性能匹配计算基本方法
电动汽车的动力性能主要包括加速性能、最高速度、爬坡能力和能耗
等指标。
在计算动力性能匹配时,首先需要确定电动汽车的车辆质量、车
辆空气阻力系数和滚动阻力系数等基本参数。
其次,需要根据所需的加速
性能和最高速度,计算出所需的功率和扭矩需求。
动力性能匹配计算的基本方法包括以下几个步骤:
1.估算行驶阻力:根据电动汽车的车辆质量、车辆空气阻力系数和滚
动阻力系数等参数,计算出电动汽车在不同速度下所受到的总行驶阻力。
2.计算所需的最大功率:根据所需的最高速度和行驶阻力,计算出电
动汽车在最高速度下所需的最大功率。
这个功率是电动汽车所需的最大输
出功率,也是电机功率的一个重要参考值。
3.估算加速性能:根据所需的加速性能和总行驶阻力,计算出电动汽
车所需的加速度。
通过加速度和车辆质量,可以估算出电动汽车在加速过
程中所需的平均功率。
4.确定电机配置:根据所需的最大功率和加速性能,确定电动汽车所
需的电机配置。
这包括电机的功率、扭矩和减速比等参数。
5.计算电池容量:根据所需的续航里程和能耗,计算出电动汽车所需
的电池容量。
这个容量在一定程度上决定了电动汽车的续航能力。
以上是电动汽车动力性能匹配计算的基本方法。
在实际计算中,还需
要考虑其他因素,如电机效率、电池充放电效率和系统整体效率等。
此外,随着电动汽车技术的不断发展,也需要根据新的技术和需求进行适当的调
整和改进。
轿车零件匹配问题分析及解决方案
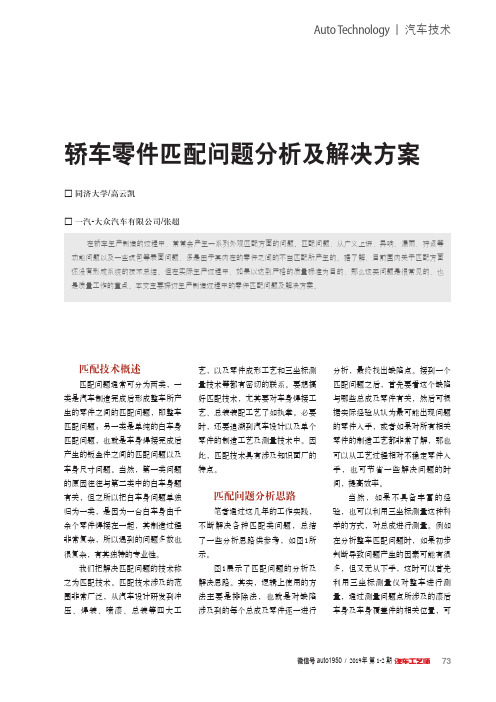
匹配技术概述匹配问题通常可分为两类,一类是汽车制造完成后形成整车所产生的零件之间的匹配问题,即整车匹配问题;另一类是单纯的白车身匹配问题,也就是车身焊接完成后产生的钣金件之间的匹配问题以及车身尺寸问题。
当然,第一类问题的原因往往与第二类中的白车身题有关,但之所以把白车身问题单独归为一类,是因为一台白车身由千余个零件焊接在一起,其制造过程非常复杂,所以遇到的问题多数也很复杂,有其独特的专业性。
我们把解决匹配问题的技术称之为匹配技术。
匹配技术涉及的范围非常广泛,从汽车设计研发到冲压、焊装、喷漆、总装等四大工轿车零件匹配问题分析及解决方案□同济大学/高云凯□一汽-大众汽车有限公司/张超在轿车生产制造的过程中,常常会产生一系列外观匹配方面的问题。
匹配问题,从广义上讲,异响、漏雨、拧紧等功能问题以及一些坑包等表面问题,多是由于其内在的零件之间的不当匹配所产生的。
据了解,目前国内关于匹配方面还没有形成系统的技术总结。
但在实际生产过程中,如果以达到严格的质量标准为目的,那么这类问题是很常见的,也是质量工作的重点。
本文主要探讨生产制造过程中的零件匹配问题及解决方案。
艺,以及零件成形工艺和三坐标测量技术等都有密切的联系。
要想搞好匹配技术,尤其要对车身焊接工艺、总装装配工艺了如执掌。
必要时,还要追溯到汽车设计以及单个零件的制造工艺及测量技术中。
因此,匹配技术具有涉及知识面广的特点。
匹配问题分析思路笔者通过这几年的工作实践,不断解决各种匹配类问题,总结了一些分析思路供参考,如图1所示。
图1展示了匹配问题的分析及解决思路。
其实,逻辑上使用的方法主要是排除法,也就是对缺陷涉及到的每个总成及零件逐一进行分析,最终找出缺陷点。
接到一个匹配问题之后,首先要看这个缺陷与哪些总成及零件有关,然后可根据实际经验从认为最可能出现问题的零件入手,或者如果对所有相关零件的制造工艺都非常了解,那也可以从工艺过程相对不稳定零件入手,也可节省一些解决问题的时间,提高效率。
一种针对起步能力的整车匹配计算方法
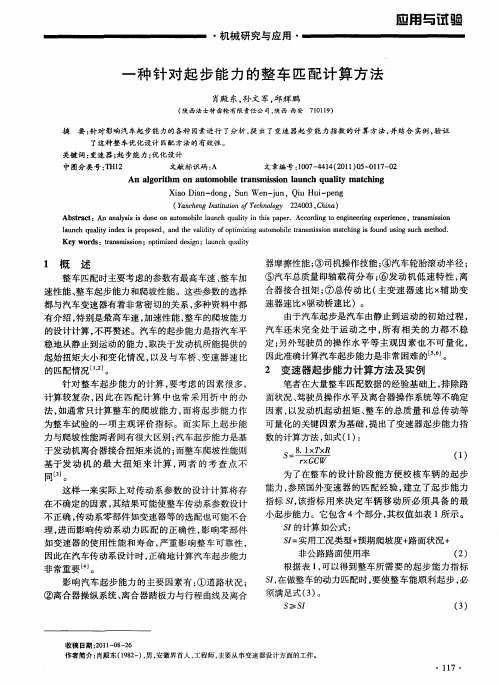
针 对 整 车 起 步 能力 的计算 , 要考 虑 的因 素很 多 ,
计 算较 复杂 , 此 在 匹 配 计 算 中也 常 采 用 折 中 的办 因
面状况 、 驾驶员操作水平及离合器操作系统等不确定 因素 , 以发动机起动扭矩 、 整车的总质量和总传 动等 可 量化 的关键 因素 为基 础 , 出 了变速 器起 步 能力 指 提 数 的计算 方法 , 如式 ( ) 1:
8S 1 J1 8 8 S1 g J l A
1 .0 14 9. 2 3
7. 4 9 60 .9
5. 3 6 4. 6 0
4. 6 0 3. 0 1
2. 1 8 2. 0 3
1 9 .6 1.0 5
13 .9 1 0 .0
10 .0
O7 .6 2. 7l 2 1 .l
的匹 配情 况 ¨2。 . J
汽 车还未 完 全 处 于运 动 之 中 , 有 相 关 的 力 都 不 稳 所 定; 另外 驾驶 员 的操 作 水 平 等 主 观 因 素也 不 可 量 化 ,
因此准确计算汽车起步能力是非常困难 的 J 。
2 变速器起步能 力计算方法及 实例
笔者 在大 量整 车匹 配数据 的经验基 础 上 , 除 路 排
更换 变 速 箱 , 问题 得 以解 决 。 当然 , 了得 到 同样 的 为 起 步能 力 , 如果 选 用 了 头 档 速 比更 大 的变 速 箱 , 据 根
式 ( ) 需 要 的 发 动 机 怠 速 扭 矩 可 更 小 , 发 动 机 的 1, 对
要 求下 降 了 , 如表 3所 示 。
1 概
述
器摩擦性能 ; ③司机操作技能 ; ④汽车轮胎滚动半径 ;
⑤汽车总质量即轴载荷分 布; ⑥发动机低速特性 , 离 合器 接合 扭 矩 ; 总传 动 比 ( 变速 器 速 比 × 助 变 ⑦ 主 辅
新能源汽车动力系统的整车匹配与优化设计

新能源汽车动力系统的整车匹配与优化设计随着环境保护意识的增强和能源短缺问题的日益凸显,新能源汽车作为一种环保节能的交通工具,受到了广泛的关注和推广。
新能源汽车采用的动力系统不同于传统的燃油动力系统,其整车匹配与优化设计显得尤为重要。
本文将针对新能源汽车动力系统的整车匹配与优化设计进行探讨。
一、新能源汽车动力系统概述新能源汽车动力系统主要包括电池组、电动机以及电控系统等核心部件。
其中,电池组作为新能源汽车的能量储存装置,主要负责提供动力。
电动机则是将电能转化为机械能,驱动汽车行驶。
而电控系统则是对电池组和电动机进行控制和管理,确保其正常工作。
二、整车匹配的意义整车匹配是指将新能源汽车动力系统中的各个部件协调配合,以实现最佳的性能和效能。
通过整车匹配,可以使得动力系统间的能量转化和传递更加高效,提高整车的能源利用率。
同时,整车匹配还能够将新能源汽车的动力系统与车身结构、传动系统等其他部件相协调,从而提升车辆的安全性和乘坐舒适度。
三、匹配与优化设计的原则1. 动力与负载匹配原则:根据新能源汽车的负载特点和使用环境,选择适合的电池组容量和电动机功率。
充分考虑新能源汽车在不同工况下的动力需求,确保汽车在加速、爬坡和高速巡航等不同使用情况下都能够提供稳定的动力输出。
2. 效能与能量利用匹配原则:新能源汽车的动力系统需要在不同工况下以最高效的方式运转,以提高能量利用效率。
通过合理配置电池组能量密度和电动机转速范围等参数,以满足不同工况下的能量需求。
3. 安全与可靠匹配原则:新能源汽车动力系统在整车匹配时,应考虑系统的安全性和可靠性,确保电池组的温度、电流等参数在安全范围内运行,防止因过度放电或充电等操作导致事故风险。
四、优化设计策略1. 多学科协同优化:在新能源汽车动力系统的整车匹配中,需要进行多学科的协同优化。
通过系统级的匹配与优化设计,充分考虑电池组、电机和控制系统等部件之间的协调关系,实现整个系统的最优性能。
新能源纯电动汽车动力匹配计算

新能源纯电动汽车动力匹配计算一、电动汽车介绍电动汽车:主要以动力电池为能量源、全部或部分由电机驱动的汽车。
1、基本结构由机械、电子、能源、计算机、信息技术等集成2、组成系统3、整车系统构架构图二、动力匹配计算驱动电机1、驱动力与行驶阻力-驱动力驱动力:推动汽车前进的外力式中:M为电机转矩;ig为变速器传动比;io为主减速器传动比;r为车轮半径,η为机械传动效率。
汽车行驶方程式由以上(1)(2)(3)(4)(5)(6)式得:式中:f为滚动阻力系数(沥青路面通常为0.01-0.02);CD为空气阻力系数(轿车为0.3-0.41,货车为0.6-1.0);δ为旋转质量换算系数(一般为1.1-1.4)。
2、功率平衡汽车行驶过程中,不仅驱动力与行驶阻力相互平衡,电机功率与行驶阻力功率也相互平衡,即:3、评价电动汽车动力性能的主要指标有:1)最高车速Vmax(Km/h);2)加速时间t(S);3)最大爬坡度imax;4)续驶里程S(Km)。
GB/T 28382-2012 纯电动乘用车技术条件对VMAX、t、imax、S都有要求。
3.2 根据加速时间确定电机功率以加速时间确定电机功率Pm2:依照电动汽车法规要求,车辆0km/h加速到50km/h,加速时间不超过10s;此时还应考虑后备功率,后备功率系数一般为1.2。
3.3 根据最大爬坡度确定电机功率电动汽车最大爬坡度,指在满载时在良好路面上的最大坡度。
爬坡度是坡度角度的正切值的百分数,即:imax=tanamaxX100% 例如:坡度为20%的坡角为11.3°;坡度为30%的坡角为16.7° 。
以最大爬坡度确定电动机的最大功率Pm3:通常以车速为30km/S,爬坡度为20%计算最大功率。
纯电动车的峰值功率Pm:Pm>MAX(Pm1 ,Pm2 ,Pm3)3.4 续航里程3.5 传动比的选择传动比的大小对电动汽车动力性及耗电经济性有较大影响,一般传动比越大,爬坡及加速性能越强,但耗电经济性较差;反之,最高车速较高,经济型较好,但爬坡及加速性能较差。
整车模态分解与匹配分析

整车模态分解与匹配分析1各系统模态频率分布的思考试验与仿真模态结果的对标工作是模态分解及匹配工作的重要基础,在取得了较为准确的建模和计算方法后,就可以根据NVH开发的需要开展整车模态匹配工作了。
承载式车辆由车体、动力驱动和底盘这三大总成组成,车体包含车身、内外饰件和电器;底盘可细分为转向系统、底盘附件、悬架系统和制动系统等;动力驱动系统分为进/排气系统、发动机、离合器、变速箱、传动系和行驶系统。
汽车上各系统以不同的方式相互连接在一起,比如动力总成、悬架系统、转向系统、排气系统和开闭件直接与车身相连,排气系统与传动系统又与动力总成相连[4]。
动力总成系统的模态分布及振动问题需要从两个方面进行考虑:一方面是动力总成的刚性体及弹性体模态振动频率,一般说来,刚体振动模态(含动力悬置系统)频率范围大概为5~20Hz,要求相邻模态的频率间隔1Hz以上,解耦率70%以上。
其中最为关重的Bounce (上下弹跳)和Roll(绕曲轴轴线旋转)两个主方向模态的解耦率要求大于90%,这两阶模态与相邻模态之间的频率间隔要求尽量大于2Hz,这样的设置将会给动力总成的振动控制带来较好的基础。
对于横置发动机平台的动力总成来说,其弹性体模态频率一般大于200Hz,高于NVH的常规结构振动、噪声仿真分析的范围。
另一方面,由于发动机上的旋转部件中心与旋转中心的天生不一致带来了惯性不平衡力,随之引发发动机本体的振动并通过动力悬置系统传递至车体内并引发部分结构振动,这部分振动频率与发动机缸数及转速有关,通常600~1000r/min的怠速转速对应覆盖的频率(二阶点火频率)为20~33Hz。
对于车体来说,车身结构的振动不仅容易引起自身结构的疲劳损坏,还是车内低频结构辐射噪声的源头,其关注的主要频率范围为10~80Hz。
一般来说,其一阶扭转和一阶弯曲振动模态均需避开发动机的怠速激励频率,以免引起怠速工况下的车内抖动及轰鸣音;对于顶棚结构,要求其第一阶模态尽可能高于50Hz;对于地板模态也是尽可能避开怠速激励频率。
整车质量分布计算分析报告
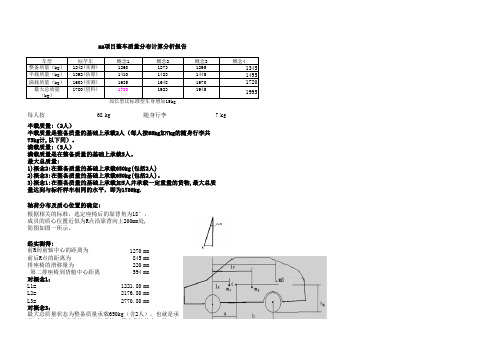
车型标竿车概念1概念2概念3概念4整备质量(kg)1242(实测)1260127312951345半载质量(kg)1392(估算)1410142314451495满载质量(kg)1603(实测)1635164816701720最大总质量(kg)1780(资料)1780192319451995每人按68kg 随身行李7kg1270mm 845mm 220mm 594mm L1=1221.80mm L2=2176.80mm L3=2770.80mm xx项目整车质量分布计算分析报告前R到前轴中心的距离为前后R点的距离为排座椅的滑移量为轴荷分布及质心位置的确定:根据相关的标准,选定座椅后的靠背角为18°,成员的质心位置近似为R点沿靠背向上200mm处,简图如图一所示。
对概念3:半载质量:(2人)半载质量是整备质量的基础上承载2人(每人按68kg加7kg的随身行李共75kg计,以下同)。
满载质量:(5人)满载质量是在整备质量的基础上承载5人。
最大总质量:1)概念2:在整备质量的基础上承载650kg(包括2人)2)概念3:在整备质量的基础上承载650kg(包括2人)。
3)概念1:在整备质量的基础上承载加5人并承载一定重量的货物,最大总质量达到与标杆样车相同的水平,即为1780kg.第二排座椅到货舱中心距离经实测得:对概念1:最大总质量状态为整备质量承载650kg(含2人),也就是承载2人的基础上再承载500kg的货物,假定货物均布,质心在后部货箱地板的中心2693mm 608mm 170mm 150mm 1877mm L1=1221.80mm L2=2176.80mm L3=2382.5mm L1=1221.80mm L2=2176.80mm L3=2382.50mmL1L2L3概念11221.802176.802770.80概念21221.802176.802382.50概念31221.802176.802382.5概念41221.802176.802382.5假定人所带的7kg 的行李全部作用在后厢中部上m1m2m3000136001362040最大总质量 概念1136204145最大总质量概念21360500最大总质量概念3136500半载状态(2人)满载状态(5人)根据力学平衡的原理可得如下方程式G×a+m1×L1+m2×L2+m3 × L3=F2×L整备状态后悬加长为车后端至备门内面距离为货舱长度为对概念2:状态最大总质量状态为整备质量承载650kg(含2人),也就是承载2人的基础上再承载500kg的货物,假定货物均布,质心在后部货箱地板的中心整车轴距为(L)后悬长为和4.最大总质量状态(估算)时轴荷分布和 a +b=L存在问题1、最大总质量状态概念1和概念2的轴荷分布的百分比超出了推荐值的范围。
- 1、下载文档前请自行甄别文档内容的完整性,平台不提供额外的编辑、内容补充、找答案等附加服务。
- 2、"仅部分预览"的文档,不可在线预览部分如存在完整性等问题,可反馈申请退款(可完整预览的文档不适用该条件!)。
- 3、如文档侵犯您的权益,请联系客服反馈,我们会尽快为您处理(人工客服工作时间:9:00-18:30)。
整车匹配计算与分析崔华标2007-04-26Yuchai Machinery Company Ltd.,内容介绍•整车动力性、经济型计算原理介绍车力性济算介•计算工具(Excel表格)详细介绍•常用车型的匹配准则•几个典型范例Yuchai Machinery Company Ltd.,整车动力性、经济型计算原理介绍整车动力性经济型计算原理介绍•评定汽车行驶的动力特性,一般采用三个指标指标:1.最高车速2.最大道路坡度3.加速能力Yuchai Machinery Company Ltd.,汽车行驶要克服的阻力•汽车的运动阻力来自四个方面:汽车力来自个G()G1.道路滚动阻力F f =f×G=(K1×V+K2)×2.空气阻力F w=K×V2×G33.上坡阻力F i=Gsinα4.加速阻力F a=(W+ΔW)/g×dv/dt=(1+ΔW/ W)×W/g×dv/d 在平路和匀速行驶状态下,般不考虑上•在平路和匀速行驶状态下,一般不考虑上坡阻力和加速阻力Yuchai Machinery Company Ltd.,发动机性能和汽车行驶动力性能之动力因数概念动力因数D=(车辆驱动力-空气阻力)/车重•动力因数是评价车辆动力性最有效的参数•驱动力没有考虑车重,不能真实反映车辆动驱动力没有考虑车重不能真实反映车辆动力性•和加速度相比,它不用考虑道路条件差异Yuchai Machinery Company Ltd.,等速燃油经济型计算等速燃油经济型计算2•在发动机部分负荷特性里插值,计算各个在发动机部分负荷特性里插值计算各个点的油耗Yuchai Machinery Company Ltd.,内容介绍•整车动力性、经济型计算原理介绍车力性济算介•计算工具(Excel表格)详细介绍•常用车型的匹配准则•几个典型范例Yuchai Machinery Company Ltd.,计算模型示例Yuchai Machinery Company Ltd.,模型需要输入参数还有:•发动机外特性扭矩曲线•发动机部分负荷特性油耗曲线Microsoft Excel 工作表Microsoft Word文档Yuchai Machinery Company Ltd.,模型参数输入1•主减速比、变速箱各个档位速比:来源于主减速比变速箱各个档位速比汽车厂•迎风面积:来自汽车厂,或车高×车宽Yuchai Machinery Company Ltd.,模型参数输入2实•滚动阻力系数:根据道路与轮胎的实际情况,我们一般计算的是普通等级公路,取滚动阻力系数:f=0.0055×1000×9.8+0.29×V/3.6•风阻系数:由汽车厂提供,一般厂家无法提供此参数,初步:客车选0.5,卡车选0.6提供此参数初步:客车选05卡车选06Yuchai Machinery Company Ltd.,模型参数输入3•风阻系数K、滚动阻力K1、K2可以由滑行系数滚力试结果计算得如从开始试验结果计算得出,比如:从50km/h开始,记录滑行到40km/h、20km/h到停止的时间,就可以计算出:F V K+V K1+K2•F=V2×ו50-V=F×tYuchai Machinery Company Ltd.,模型参数输入4•传动效率:一般选择0.75传动效率般选择变速箱效率一般选:0.9-0.95离合器:0.97-0.98097098传动轴:0.97-0.98主减速器:0.95-0.96减速器半轴:0.97-0.98轮胎:0.90左右•综合效率:0.75•东风公司有轮毂试验结果,表明效率只有0.70-0.75Yuchai Machinery Company Ltd.,模型参数输入5•附件吸收扭矩的选择:空调客车一般选择调卡车带调客车50Nm,空调卡车选30Nm,不带空调客车与卡车选20Nm,•原理上附件吸收扭矩应该与转速挂钩,但是我们得不到附件与转速关系的曲线,只能大致估算Yuchai Machinery Company Ltd.,计算输出内容介绍•整车动力性、经济型计算原理介绍车力性济算介•计算工具(Excel表格)详细介绍•常用车型的匹配准则•几个典型范例Yuchai Machinery Company Ltd.,整车匹配的目的•保证车辆充足的动力性保车辆充力性•车辆最佳的燃油经济型•车辆各个部件的最佳可靠性•车辆排放与噪声符合国家标准•最合理的成本Yuchai Machinery Company Ltd.,车辆匹配一般准则车辆匹配般准则1Ⅱ档最大动力最高档最大动最高车速汽车类别因数D Ⅰmax 力因数D 0max 最高档最大爬坡能力%Va max km/h 016001003732%城市公交车0.16±0.01≥0.037≥3.2%75~90高速客车、长途运输客车≥0.14≥0.028≥2.1%≥115长途普通载货车(实际超载最大载荷)≥0.015≥1.0%≥105自卸车、山区专用载货车辆(实际超载最大载荷)≥0.021≥1.5%70~90长途牵引车(实际超载最大载荷)≥0.015≥0.95%≥105Yuchai Machinery Company Ltd.,车辆匹配般准则2车辆匹配一般准则•对于路况复杂的使用、或需要经常更换档位的行驶需要,如:公交车、山区行驶、国道、工地等,档位越多、动力性与经济国道工地等档位越多动力性与经济性越好•各个档位间以等比数列排列最优•匹配的原则是让驾驶员尽可能的多使用最高档Yuchai Machinery Company Ltd.,车辆匹配般准则3车辆匹配一般准则•为了省油,在动力性许可的情况下,优选低排量的发动机•同样为了省油,同型号的发动机,优选最大扭矩与功率的机型,这样可以确保高档大扭矩与功率的机型这样可以确保高档位的使用频率•为了可靠性,优选大排量、较低功率密度的发动机Yuchai Machinery Company Ltd.,车辆匹配般准则4车辆匹配一般准则•尽可能让车辆在高档位、较低转速行驶尽可能让车辆在高档位较低转速行驶Yuchai Machinery Company Ltd.,内容介绍•整车动力性、经济型计算原理介绍车力性济算介•计算工具(Excel表格)详细介绍•常用车型的匹配准则•几个典型范例Yuchai Machinery Company Ltd.,实例1:湖北宜昌国通汽运公司湖北宜昌国通汽运公司YC6M28020,•使用陕汽奥龙车,以山路为主配YC6M280-20车辆作业总重50吨。
¾爬坡主要使用3档¾发动机爬坡转速一般1500-2000r/min¾原使用综合油耗69升/100公里¾从苟家娅到宜昌53升/100公里•计算整改后,更换为YC6M340-20。
¾爬坡主要使用4档¾发动机爬坡转速一般1200-1500r/min¾从苟家娅到宜昌38升/100公里Yuchai Machinery Company Ltd.,实例2:山西阳泉煤矿山西阳泉煤矿z东风EQ3243VB翻斗车配YC6M280-20车辆作业总重50吨。
YC6M28020吨¾爬坡主要使用1、2、3档¾发动机爬坡转速一般1500-2000r/minz计算整改后,更换为加大低速扭矩的工程机。
¾爬坡主要使用2、3、4档¾发动机爬坡转速一般1200-1500r/minz2辆车一起作业1.5天后,由于增压器无法换带阀整改前后辆车起作业15天后由于增压器无法换带阀的,效果已经打折扣¾整改前的车加油732元,运行60趟,12.2元/趟¾整改后车加油685元,运行62趟,11.0元/趟¾节油10.9%Yuchai Machinery Company Ltd.,实例3:公交专用柴油机开发应用•4112柴油机在8-9米城市公交车上普遍存在起步动力不足,匹配不好冒烟,油耗相对6缸机无优势。
匹配不好冒烟油耗相对缸机无优势玉柴专门开发针对米城市公交车甚至•8-9米城市公交车,甚至10米非空调城市公交专用柴油机(G0900),专门针对低速开发,在福州公交得到成功应用:¾加速烟度大幅度改善¾起步动力性明显改进,使用档位提高一个¾油耗比原机平均节省2升/100公里•4气门公交专用柴油机(G2A00)相对G0900:¾烟度更好¾动力性更突出¾油耗比原G0800少3-3.5升/100公里,比G0900少0.83升/100公里Yuchai Machinery Company Ltd.,实例4:10米公交车上用YC4G200代替YC6J210•福州康驰公交公司,青岛申沃10米城市公交车•原来匹配YC6J210-20,使用油耗27-30升/100公里•YC4G200-20,动力性完全满足使用,后匹配YC4G20020动力性完全满足使用使用油耗23-25升/100公里Yuchai Machinery Company Ltd.,实例南梧高速试验限速对油耗的贡献5:南梧高速试验:限速对油耗的贡献•江淮HFC4182K2R1牵引车,以平路为主,配YC6M340-20,车辆作业总重55吨,装集装箱拖车。
¾主要以最高档8档行驶为主¾车辆行驶80km/h以上,平均车速82km/h¾原高速公路使用油耗56.65升/100公里•计算整改后,将最高车速进行限制最高空转从2400r/min降低为2000r/min¾2400/i2000/i¾主要以最高档8档行驶为主¾车辆行驶80km/h以下,平均车速69km/h¾高速公路使用油耗49.86升/100公里¾整改节油率13.62%Yuchai Machinery Company Ltd.,示例6:档位增多对车辆的好处•柳州10米黄海车配•宇通ZK6830配6108ZQ•配YC4G180-20柴油机,原来使用5档(带超速6档(不带超速档)变速箱比5档平均省油2档)变速箱,在山路和其它路况行驶困难,升/100km (8%)油耗也高•改为6档箱后,动力性与经济型都改善Yuchai Machinery Company Ltd.,谢谢Yuchai Machinery Company Ltd.,。