压铸产品常见缺陷和解决方法
常见压铸件缺陷解决方法
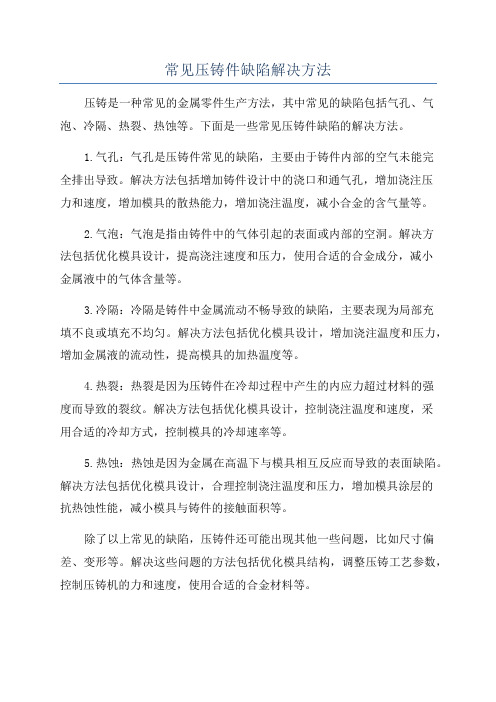
常见压铸件缺陷解决方法
压铸是一种常见的金属零件生产方法,其中常见的缺陷包括气孔、气泡、冷隔、热裂、热蚀等。
下面是一些常见压铸件缺陷的解决方法。
1.气孔:气孔是压铸件常见的缺陷,主要由于铸件内部的空气未能完
全排出导致。
解决方法包括增加铸件设计中的浇口和通气孔,增加浇注压
力和速度,增加模具的散热能力,增加浇注温度,减小合金的含气量等。
2.气泡:气泡是指由铸件中的气体引起的表面或内部的空洞。
解决方
法包括优化模具设计,提高浇注速度和压力,使用合适的合金成分,减小
金属液中的气体含量等。
3.冷隔:冷隔是铸件中金属流动不畅导致的缺陷,主要表现为局部充
填不良或填充不均匀。
解决方法包括优化模具设计,增加浇注温度和压力,增加金属液的流动性,提高模具的加热温度等。
4.热裂:热裂是因为压铸件在冷却过程中产生的内应力超过材料的强
度而导致的裂纹。
解决方法包括优化模具设计,控制浇注温度和速度,采
用合适的冷却方式,控制模具的冷却速率等。
5.热蚀:热蚀是因为金属在高温下与模具相互反应而导致的表面缺陷。
解决方法包括优化模具设计,合理控制浇注温度和压力,增加模具涂层的
抗热蚀性能,减小模具与铸件的接触面积等。
除了以上常见的缺陷,压铸件还可能出现其他一些问题,比如尺寸偏差、变形等。
解决这些问题的方法包括优化模具结构,调整压铸工艺参数,控制压铸机的力和速度,使用合适的合金材料等。
总的来说,解决压铸件缺陷的方法需要综合考虑材料、模具设计、工艺参数等多个因素,通过不断的实验和改进来提高铸件的质量。
压铸件常见缺陷及解决办法

压铸件常见缺陷及解决办法
1、尖角缺陷:表现为在压铸件的边缘和表面出现尖利的角,其
原因是模具的固定不牢,模具合模前没有铂精加光等操作,模具和表
面间的空隙较大,导致铸件连续流和溅射的金属物料的冷凝无法完全
填充到模具内。
解决办法是在压铸件的模具制作中要注意模具的固定,还要在合模前进行铂精加光,使模具缝隙尽量控制在最小。
2、翘曲缺陷:表现为铸件胚体过大或模具设计不当,导致部分
孔表面被填充的金属物料过度凝固后发生变形。
解决办法是提高铸件
的成型质量,在模具设计时应注意做到模具中高低正常,同时要增加
相应的引流装置,降低铸件表面在压铸过程中的温度,减少物料凝固
时间。
3、凹槽缺陷:表现为压铸件内壁或内孔出现浅深不均、粗糙凹槽,一般出现在内壁与模穴孔面间,其原因是模具合模时并未完全排
除空气,另外铸件内孔口位、形喉与内壁模穴间距过大,空气中的熔
融物料的细沙子难以充分清除也会导致此缺陷的产生。
解决办法是采
取真空压铸成型,即采用真空室和真空阀将空气真空,以消除空气;
另外应改变合模方式和模具设计,减少内孔口位与形喉与内壁模穴间距。
常见压铸件缺陷及解决方法
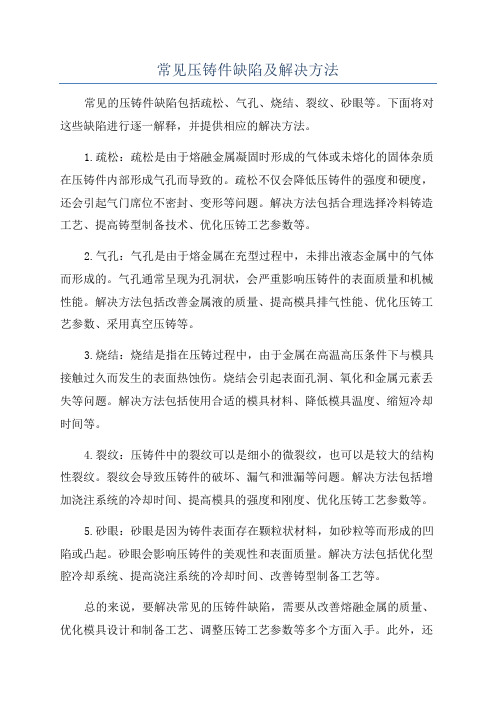
常见压铸件缺陷及解决方法常见的压铸件缺陷包括疏松、气孔、烧结、裂纹、砂眼等。
下面将对这些缺陷进行逐一解释,并提供相应的解决方法。
1.疏松:疏松是由于熔融金属凝固时形成的气体或未熔化的固体杂质在压铸件内部形成气孔而导致的。
疏松不仅会降低压铸件的强度和硬度,还会引起气门席位不密封、变形等问题。
解决方法包括合理选择冷料铸造工艺、提高铸型制备技术、优化压铸工艺参数等。
2.气孔:气孔是由于熔金属在充型过程中,未排出液态金属中的气体而形成的。
气孔通常呈现为孔洞状,会严重影响压铸件的表面质量和机械性能。
解决方法包括改善金属液的质量、提高模具排气性能、优化压铸工艺参数、采用真空压铸等。
3.烧结:烧结是指在压铸过程中,由于金属在高温高压条件下与模具接触过久而发生的表面热蚀伤。
烧结会引起表面孔洞、氧化和金属元素丢失等问题。
解决方法包括使用合适的模具材料、降低模具温度、缩短冷却时间等。
4.裂纹:压铸件中的裂纹可以是细小的微裂纹,也可以是较大的结构性裂纹。
裂纹会导致压铸件的破坏、漏气和泄漏等问题。
解决方法包括增加浇注系统的冷却时间、提高模具的强度和刚度、优化压铸工艺参数等。
5.砂眼:砂眼是因为铸件表面存在颗粒状材料,如砂粒等而形成的凹陷或凸起。
砂眼会影响压铸件的美观性和表面质量。
解决方法包括优化型腔冷却系统、提高浇注系统的冷却时间、改善铸型制备工艺等。
总的来说,要解决常见的压铸件缺陷,需要从改善熔融金属的质量、优化模具设计和制备工艺、调整压铸工艺参数等多个方面入手。
此外,还需要采用适当的检测手段,如金相分析、X射线检测、超声波检测等,对压铸件进行质量检验,及时排除可能存在的缺陷。
压铸件常见缺陷及改善对策

压铸件常见缺陷及改善对策压铸件是常用的金属制造工艺之一,用于制造各种产品,如汽车零件、电子设备外壳等。
然而,压铸件在制造过程中往往会出现一些常见的缺陷,例如气孔、缩松、热裂纹等。
为了提高压铸件的质量,需要采取适当的改善对策。
首先,气孔是压铸件中常见的缺陷之一、这主要是由于金属液中溶解的气体在凝固时无法完全排除,导致气孔形成。
改善对策包括以下几个方面:1.改善炉内冶炼过程:合理调节熔化温度和熔化时间,增加金属液中的液体相和气体相之间的接触时间,有助于气体的溶解和脱除。
2.调节压铸机参数:增加射压和射速,可以改善金属液流动性,减少气体残留的可能性。
3.优化压铸模具结构:设计合理的浇口和废渣口,有利于气体的排除,减少气孔的生成。
其次,缩松是另一个常见的缺陷。
缩松是指压铸件中因内部金属液冷却不均匀而形成的孔洞或松散区域。
改善对策包括以下几个方面:1.控制金属液的冷却速度:通过调整铸型温度、浇注温度和浇注速度等参数,使金属液冷却均匀,减少缩松的可能性。
2.优化浇口和冷却系统:设计合理的浇口和冷却系统,有利于金属液的流动和冷却,减少缩松的生成。
3.采用适当的金属合金:一些合金具有较好的流动性和凝固性,能够减少缩松的产生。
最后,热裂纹是压铸件常见的缺陷之一、这是由于金属在冷却过程中由于内部应力过大而发生裂纹。
改善对策包括以下几个方面:1.控制冷却速率:通过调节冷却速率,使金属在冷却过程中应力得到释放,减少热裂纹的发生。
2.优化模具设计:设计合理的模具结构,减少金属液在冷却过程中的应力集中,可以减少热裂纹的生成。
3.采用合适的退火工艺:通过合适的退火工艺,使金属在冷却过程中应力得到释放,减少热裂纹的发生。
总之,压铸件常见的缺陷包括气孔、缩松和热裂纹等,需要采取一系列的改善对策来提高压铸件的质量。
通过优化工艺参数、改善模具设计和采用合适的金属合金,可以减少这些缺陷的发生,并提高压铸件的品质。
压铸件常见缺陷及解决办法手册 (完整版)
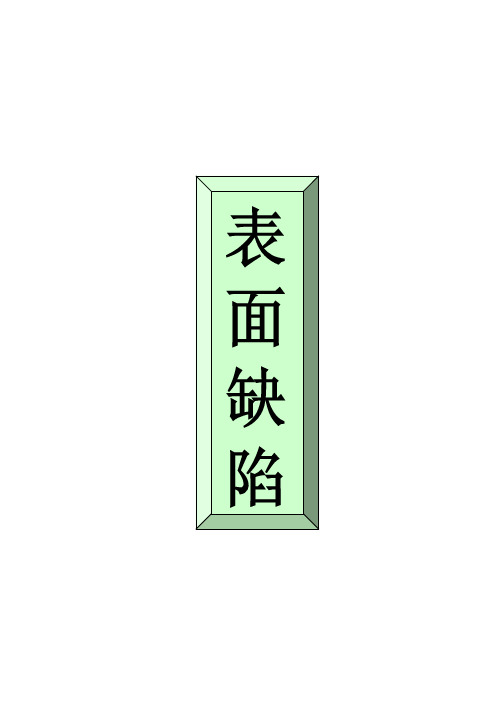
产生原因分析判断及解决办法1、金属液浇注温度低或模具温度低;2、合金成分不符合标准,流动性差;3、金属液分股填充,熔合不良;4、浇口不合理,流程太长;5、填充速度低或排气不良;6、压射比压偏低。
1、产品发黑,伴有流痕。
适当提高浇注温度和模具温度;2、改变合金成分,提高流动性;3、烫模件看铝液流向,金属液碰撞产生冷隔出现一般为涡旋状,伴有流痕。
改进浇注系统,改善内浇口的填充方向。
另外可在铸件边缘开设集渣包以改善填充条件;4、伴有远端压不实。
更改浇口位置和截面积,改善排溢条件,增大溢流量;5、产品发暗,经常伴有表面气泡。
提高压射速度,6、铸件整体压不实。
提高比压(尽量不采用)。
缺陷1 ---- 冷隔缺陷现象:温度较低的金属流互相对接但未熔合而出现的缝隙,呈不规则的线形,有穿透的和不穿透的两种,在外力的作用下有发展的趋势。
其他名称:冷接(对接)缺陷2 ---- 擦伤其他名称:拉伤、拉痕、粘模伤痕缺陷现象:顺着脱模方向,由于金属粘附,模具制造斜度太小而造成铸件表面的拉伤痕迹,严重时成为拉伤面甚至产生裂纹。
产生原因 分析判断及解决办法 1、型芯、型壁的铸造斜度太小或出现倒斜度; 2、型芯、型壁有压痕; 3、合金粘附模具;4、铸件顶出偏斜,或型芯轴线偏斜;5、型壁表面粗糙;6、涂料常喷涂不到;7、铝合金中含铁量低于0.6%; 8、合金浇注温度高或模具温度太高;9、浇注系统不正确, 直接冲击型壁或型芯 ; 10、填充速度太高;11、型腔表面未氮化。
1、产品一般拉出亮痕,不起毛。
修正模具,保证制造斜度; 2、产生拉毛甚至拉裂。
打光压痕、更换型芯或焊补型壁; 3、拉伤起毛。
抛光模具; 4、单边大面积拉伤,顶出时有异声修正模具结构; 5、拉伤为细条状,多条。
打磨抛光表面; 6、模具表面过热,均匀粘铝。
涂料用量薄而均匀,不能漏喷涂料; 7、型腔表面粘附铝合金。
适当增加含铁量至0.6~0.8%;8、型腔表面粘附铝合金,尤其是内浇口附近。
压铸件常见缺陷排除基本措施
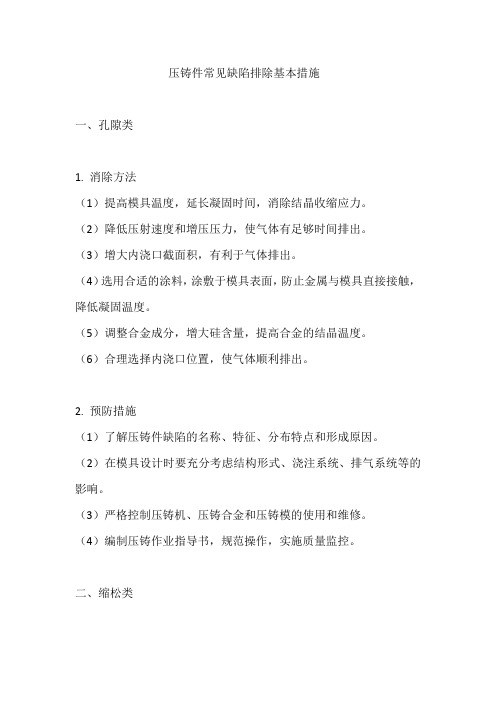
压铸件常见缺陷排除基本措施一、孔隙类1. 消除方法(1)提高模具温度,延长凝固时间,消除结晶收缩应力。
(2)降低压射速度和增压压力,使气体有足够时间排出。
(3)增大内浇口截面积,有利于气体排出。
(4)选用合适的涂料,涂敷于模具表面,防止金属与模具直接接触,降低凝固温度。
(5)调整合金成分,增大硅含量,提高合金的结晶温度。
(6)合理选择内浇口位置,使气体顺利排出。
2. 预防措施(1)了解压铸件缺陷的名称、特征、分布特点和形成原因。
(2)在模具设计时要充分考虑结构形式、浇注系统、排气系统等的影响。
(3)严格控制压铸机、压铸合金和压铸模的使用和维修。
(4)编制压铸作业指导书,规范操作,实施质量监控。
二、缩松类1. 消除方法(1)提高模具温度,促进合金液在压力作用下充型和补缩。
(2)降低压射速度和增压压力,延长补缩时间。
(3)采用高压力射流,减小浇道截面积,提高补缩效率。
(4)采用压铸件热处理工艺,实现局部补缩,消除缩松缺陷。
2. 预防措施(1)了解压铸件缺陷的特征、分布特点和形成原因。
(2)在模具设计时要充分考虑结构形式、浇注系统、排气系统等的影响。
(3)严格控制压铸机、压铸合金和压铸模的使用和维修。
(4)编制压铸作业指导书,规范操作,实施质量监控。
三、偏芯类1. 消除方法(1)调整内浇口位置和大小,改变浇注系统,使充型压力分布均匀。
(2)调整模具温度,减小零件内外温差,减弱热应力。
(3)采用定模或动模定置结构设计,确保定位精度和稳定成型。
(4)采用抽芯结构,减少抽芯受力不均的影响。
(5)在工艺上采取相应措施,如采用二级抽芯等,减小抽芯力。
2. 预防措施(1)了解压铸件缺陷的特征、分布特点和形成原因。
(2)在模具设计时要充分考虑结构形式、浇注系统、排气系统等的影响。
(3)严格控制压铸机、压铸合金和压铸模的使用和维修。
(4)编制压铸作业指导书,规范操作,实施质量监控。
四、裂纹类1. 消除方法(1)调整合金成分,提高收缩率,增强抗裂纹能力。
压铸产品的几种常见缺陷和对应分析
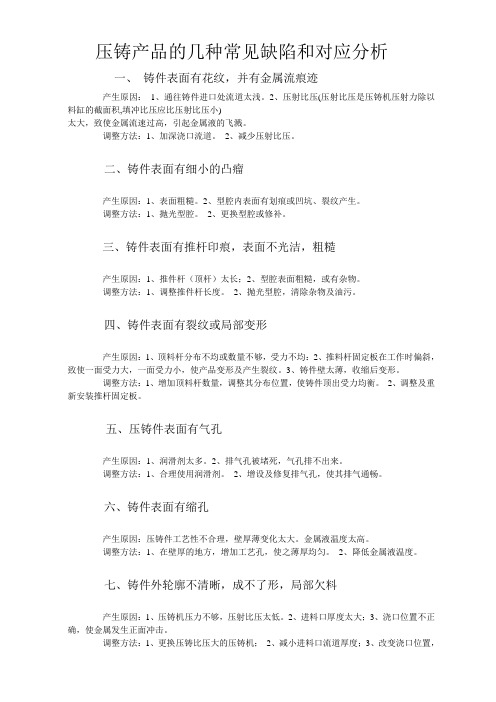
压铸产品的几种常见缺陷和对应分析一、铸件表面有花纹,并有金属流痕迹产生原因:1、通往铸件进口处流道太浅。
2、压射比压(压射比压是压铸机压射力除以料缸的截面积,填冲比压应比压射比压小)太大,致使金属流速过高,引起金属液的飞溅。
调整方法:1、加深浇口流道。
2、减少压射比压。
二、铸件表面有细小的凸瘤产生原因:1、表面粗糙。
2、型腔内表面有划痕或凹坑、裂纹产生。
调整方法:1、抛光型腔。
2、更换型腔或修补。
三、铸件表面有推杆印痕,表面不光洁,粗糙产生原因:1、推件杆(顶杆)太长;2、型腔表面粗糙,或有杂物。
调整方法:1、调整推件杆长度。
2、抛光型腔,清除杂物及油污。
四、铸件表面有裂纹或局部变形产生原因:1、顶料杆分布不均或数量不够,受力不均:2、推料杆固定板在工作时偏斜,致使一面受力大,一面受力小,使产品变形及产生裂纹。
3、铸件壁太薄,收缩后变形。
调整方法:1、增加顶料杆数量,调整其分布位置,使铸件顶出受力均衡。
2、调整及重新安装推杆固定板。
五、压铸件表面有气孔产生原因:1、润滑剂太多。
2、排气孔被堵死,气孔排不出来。
调整方法:1、合理使用润滑剂。
2、增设及修复排气孔,使其排气通畅。
六、铸件表面有缩孔产生原因:压铸件工艺性不合理,壁厚薄变化太大。
金属液温度太高。
调整方法:1、在壁厚的地方,增加工艺孔,使之薄厚均匀。
2、降低金属液温度。
七、铸件外轮廓不清晰,成不了形,局部欠料产生原因:1、压铸机压力不够,压射比压太低。
2、进料口厚度太大;3、浇口位置不正确,使金属发生正面冲击。
调整方法:1、更换压铸比压大的压铸机;2、减小进料口流道厚度;3、改变浇口位置,防止对铸件正面冲击。
八、铸件部分未成形,型腔充不满产生原因:1、压铸模温度太低;2、金属液温度低;3、压机压力太小,4、金属液不足,压射速度太高;5、空气排不出来。
调整方法:1、2、提高压铸模,金属液温度;3、更换大压力压铸机。
4、加足够的金属液,减小压射速度,加大进料口厚度。
压铸常见缺陷原因及其改善方法

压铸常见缺陷原因及其改善方法1).冷紋:原因:熔汤前端的温度太低,相叠时有痕迹.改善方法:1.检查壁厚是否太薄(設計或制造) ,较薄的区域应直接充填.2.检查形狀是否不易充填;距离太远、封閉区域(如鳍片(fin) 、凸起) 、被阻挡区域、圆角太小等均不易充填.並注意是否有肋点或冷点.3.缩短充填时间.缩短充填时间的方法:…4.改变充填模式.5.提高模温的方法:…6.提高熔汤温度.7.检查合金成分.8.加大逃气道可能有用.9.加真空裝置可能有用.2).裂痕:原因:1.收缩应力.2.頂出或整缘时受力裂开.改善方式:1.加大圆角.2.检查是否有热点.3.增压时间改变(冷室机).4.增加或缩短合模时间.5.增加拔模角.6.增加頂出銷.7.检查模具是否有錯位、变形.8.检查合金成分.3).气孔:原因:1.空气夾杂在熔汤中.2.气体的来源:熔解时、在料管中、在模具中、离型剂.改善方法:1.适当的慢速.2.检查流道转弯是否圆滑,截面积是否渐減.3.检查逃气道面积是否够大,是否有被阻塞,位置是否位於最后充填的地方.4.检查离型剂是否噴太多,模温是否太低.5.使用真空.4).空蚀:原因:因压力突然減小,使熔汤中的气体忽然膨胀,冲击模具,造成模具損伤.改善方法:流道截面积勿急遽变化.5).缩孔:原因:当金属由液态凝固为固态时所占的空间变小,若无金属补充便会形成缩孔.通常发生在较慢凝固处.改善方法:1.增加压力.2.改变模具温度.局部冷却、噴离型剂、降低模温、.有时只是改变缩孔位置,而非消缩孔.6).脫皮:原因:1.充填模式不良,造成熔汤重叠.2.模具变形,造成熔汤重叠.3.夾杂氧化层.改善方法:1.提早切換为高速.2.缩短充填时间.3.改变充填模式,浇口位置,浇口速度.4.检查模具強度是否足夠.5.检查銷模裝置是否良好.6.检查是否夾杂氧化层.7).波紋:原因:第一层熔汤在表面急遽冷却,第二层熔汤流過未能将第一层熔解,却又有足夠的融合,造成組织不同.改善方法:1.改善充填模式.2.缩短充填时间.8).流动不良产生的孔:原因:熔汤流动太慢、或是太冷、或是充填模式不良,因此在凝固的金属接合处有孔.改善方法:1.同改善冷紋方法.2.检查熔汤温度是否稳定.3.检查模具温充是否稳定.9).在分模面的孔:原因:可能是缩孔或是气孔.改善方法:1.若是缩孔,減小浇口厚度或是溢流井进口厚度.2.冷却浇口.3.若是气孔,注意排气或捲气問题.10).毛边:原因:1.鎖模力不足.2.模具合模不良.3.模具強度不足.4.熔汤温度太高.11).缩陷:原因:缩孔发生在压件表面下面.改善方法:1.同改善缩孔的方法.2.局部冷却.3.加热另一边.12).积碳:原因:离型剂或其他杂质积附在模具上.改善方法:1.减小离型剂喷洒量.2.升高模温.3.选择适合的离型剂.4.使用软水稀釋离型剂.13).冒泡:原因:气体捲在铸件的表面下面.改善方式:1.減少捲气(同气孔).2.冷却或防低模温.14).粘模:原因:1.鋅积附在模具表面.2.熔汤冲击模具,造成模面损坏.改善方法:1.降低模具温度.2.降低划面粗糙度.3.加大拔模角.4.镀膜.5.改变充填模式.6.降氏浇口速度.引言:在纯铝中加入一些金属或非金属元素所熔制的铝合金是一种新型的合金材料,由于其比重小,比强度高,具有良好的综合性能,因此被广泛用于航空工业、汽车制造业、动力仪表、工具及民用器具制造等方面。
压铸件常见的缺陷分析及其改善措施
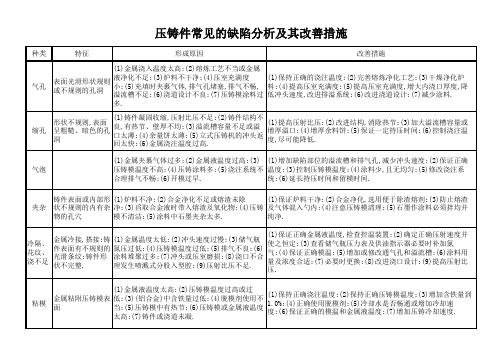
粘模
金属粘附压铸模表 面
(1)金属液温度太高;(2)压铸模温度过高或过 低;(3)(铝合金)中含铁量过低;(4)脱模剂使用不 当;(5)压铸模中有热节;(6)压铸模或金属液温度 太高;(7)铸件或浇道未凝.
(1)保持正确浇注温度;(2)保持正确压铸模温度;(3)增加含铁量到 1.0%;(4)正确使用脱模剂;(5)冷却水是否畅通或增加冷却速 度;(6)保证正确的模温和金属液温度;(7)增加压铸冷却速度.
纯净.
ቤተ መጻሕፍቲ ባይዱ
冷隔、 花纹、 浇不足
金属冷接,搭接;铸 (1)金属温度太低;(2)冲头速度过慢;(3)储气瓶
件表面有不规则的 氮压过低;(4)压铸模温度过低;(5)排气不良;(6)
光滑条纹;铸件形 涂料堆聚过多;(7)冲头或压室磨损;(8)浇口不合
状不完整.
理发生喷溅式分股入型腔;(9)压射比压不足.
(1)保证正确金属液温度,检查控温装置;(2)确定正确压射速度并 使之恒定;(3)查看储气瓶压力表及供油指示器必要时补加氮 气;(4)保证正确模温;(5)增加或修改通气孔和溢流槽;(6)涂料用 量及浓度合适;(7)必要时更换;(8)改进浇口设计;(9)提高压射比 压.
气泡
(1)金属夹裹气体过多;(2)金属液温度过高;(3) (1)增加缺陷部位的溢流槽和排气孔,减少冲头速度;(2)保证正确
压铸模温度不高;(4)压铸涂料多;(5)浇注系统不 温度;(3)控制压铸模温度;(4)涂料少,且无均匀;(5)修改浇注系
合理排气不畅;(6)开模过早.
统;(6)延长持压时间和留模时间.
压铸件常见的缺陷分析及其改善措施
种类
特征
形成原因
改善措施
气孔
(1)金属浇入温度太高;(2)熔炼工艺不当或金属
一体化压铸十大缺陷及解决方案
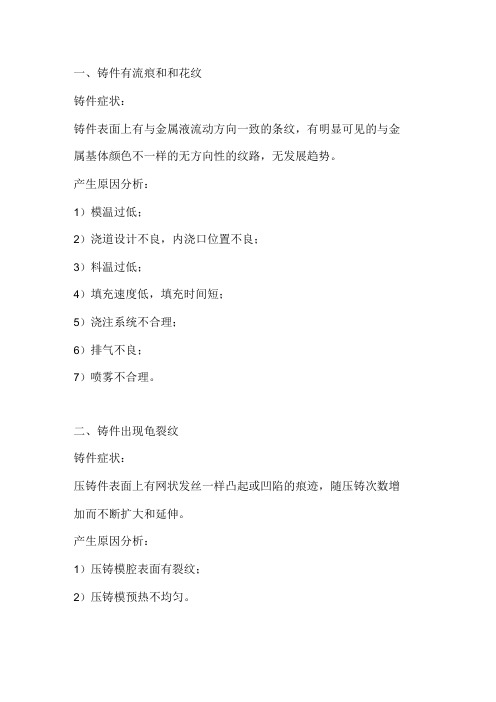
一、铸件有流痕和和花纹铸件症状:铸件表面上有与金属液流动方向一致的条纹,有明显可见的与金属基体颜色不一样的无方向性的纹路,无发展趋势。
产生原因分析:1)模温过低;2)浇道设计不良,内浇口位置不良;3)料温过低;4)填充速度低,填充时间短;5)浇注系统不合理;6)排气不良;7)喷雾不合理。
二、铸件出现龟裂纹铸件症状:压铸件表面上有网状发丝一样凸起或凹陷的痕迹,随压铸次数增加而不断扩大和延伸。
产生原因分析:1)压铸模腔表面有裂纹;2)压铸模预热不均匀。
三、铸件产生冷隔铸件症状:压铸件表面有明显的、不规则的、下陷线性型纹路(有穿透与不穿透两种)形状细小而狭长,有时交接边缘光滑,在外力作用下有断开的可能。
产生原因分析:1)两股金属流相互对接,但未完全熔合而又无夹杂存在其间,两股金属结合力又很薄弱;2)浇注温度或压铸模温度偏低;3)浇道位置不对或流路过长;4)填充速度低。
四、铸件出现缩陷(凹痕)铸件症状:比较厚实的铝铸件,大部分的表面上有平滑的凹痕(状如盘碟)。
产生原因分析:1)由收缩引起压铸件设计不当壁厚差太大;浇道位置不当;压射比压低,保压时间短;压铸模局部温度过高。
2)冷却系统设计不合理;3)开模过早;4)浇注温度过高。
五、铸件产生印痕铸件症状:铸件表面与压铸模型腔表面接触所留下的痕迹或铸件表面上出现阶梯痕迹。
产生原因分析:1)由顶出元件引起顶杆端面被磨损;顶杆调整长短不一致;压铸模型腔拼接部分和其他部分配合不好。
2)由拼接或活动部分引起镶拼部分松动;活动部分松动或磨损;铸件的侧壁表面,由动、定模互相穿插的镶件所形成。
六、铸件伴有粘附物痕迹铸件症状:小片状及金属或非金属与金属的基体部分熔接,在外力的作用下剥落小片状物,剥落后的铸件表面有的发亮、有的为暗灰色。
产生原因分析:1)在压铸模型腔表面有金属或非金属残留物;2)浇注时先带进杂质附在型腔表面上。
七、铸件夹皮及剥落铸件症状:在铸件局部有金属的明显层次。
压铸产品常见缺陷和解决方法

脱模剂喷涂不均匀
模具型腔表面未做氮化和PVD涂 层
铝合金含铁量低于0.6%
培训操作工或者调整自动喷涂的喷嘴方向 重新处理模仁 重新熔炼
2
缺料
产生原因
解决方法
铝液含气量过高
铝液增加除气工序
模具排气不畅
优化排气块,或增加抽真空设备
脱模剂喷涂过多或者没有吹干 培训操作工,或者减少喷涂时间增加吹气时间(自动喷涂)
优化排气块,或者增加抽真空 铝液增加除气工序
培训操作工,或者减少喷涂时间增加吹气时间(自动喷涂) 验证PQ2曲线图,优化压铸参数 尝试调整切换点
4
裂纹
产生原因
圆角太小 顶针布局不合理 模具或产品存在拉伤 抽芯的分型线位置设计不良 铝液或模具温度太低 去除浇口时开裂 铝液铁含量大于0.9%
解决方法
与客户协商加大圆角。 尽量在受力位置,如筋条上布置顶针。如果一定要在壁薄的
压铸产品常见缺陷和解决方法
1
拉伤,粘模
产生原因
拔模斜度不够 铝液冷却速度慢 模具表面碰伤
解决方法
尽量在前期设计保证拔模斜度合理。后期增加顶针尖山顶出 不平衡带来的拉伤。
检查模具的工作温度,保证220度左右;增加冷却,特别是 高压点冷。
补焊修复。
模具冲蚀
验证PQ2曲线图,优化压铸参数,别是浇口速度。
增压建压时间过长
检查压铸机工况和品牌
铝液含气量过高
铝液增加除气工序
10
夹渣
产生原因 铝液质量变差
解决方法 合理安排维护保养设备
11
12
地方布置顶针,则需要增加顶针凸台。 检查铁含量和检查修复模具。
需要增加在动模处的挂台或特征。 常规:铝液680度,模具220度。
压铸不良原因与措施

压铸不良原因与措施压铸是一种常见的金属加工方法,用于制造各种各样的金属零件。
然而,在压铸过程中常常会出现一些不良情况,导致产品质量下降或无法使用。
以下是一些常见的压铸不良原因及相应的措施。
1.缩孔(针眼)原因:高温熔融金属凝固时,金属液缩小所形成的孔洞。
措施:-控制材料的熔点和凝固温度,避免温度过高。
-提高注入压力和速度,确保金属充实完全。
-控制铸造工艺参数,如浇注温度、压力和速度,减少气体夹杂物。
2.气孔原因:熔融金属中混入空气或水分,冷凝成孔洞。
措施:-净化材料,确保金属液没有杂质。
-增加浇注温度,减少金属和气体冷凝。
-提高注入速度,使气体远离金属液。
3.热裂纹原因:金属在凝固过程中,由于残余应力、金属浓缩和组织缺陷等原因引起的开裂。
措施:-优化铸造工艺,减少或消除金属残余应力。
-控制金属的凝固速度,避免快速凝固造成应力集中。
-添加合适的合金元素,改善金属组织结构。
4.狭长缺陷原因:熔融金属填充模腔的过程中,金属液流动不均匀,形成局部过渡缩小的缺陷。
措施:-设计合理的铸造模具,确保金属液能够均匀填充模腔。
-调整铸造工艺参数,如入口和出口位置、浇注温度和速度,改善金属液流动状态。
-使用合适的流道和浇口设计,使金属流动更加均匀。
5.长气孔原因:金属液注入模腔的过程中,气体无法顺利排出,形成长而突出的孔。
措施:-增大出口尺寸,提高气体排出的通道。
-调整浇注顺序,避免气泡在金属液中积聚。
-使用适当的排气装置,确保顺畅排出气体。
6.表面不良原因:压铸件表面出现裂纹、气孔、疤痕等缺陷。
措施:-增加模具的冷却系统,提高金属液凝固速度。
-优化模具表面处理,减少摩擦和热传导。
-控制铸造工艺参数,如浇注温度和速度,减少金属液与模具的接触时间。
总之,压铸不良的原因和措施是多种多样的,需要根据不同情况采取相应的措施。
通过优化材料、设计模具、调整工艺参数等方法,可以有效地减少压铸不良,提高产品质量。
压铸常见缺陷、原因及改进措施

渗漏
水、
合金选择不当
提高比压 改进浇注系统 选用良好合金
排气不良
改进排气系统
二十四、 化学成分 不符合要
求
经化学分析,铸件合 金不符要求或杂质太
多
配料不正确 原材料及回炉料未加分析即行投入使用
炉料应经化学分析后才能配用
炉料应严格管理,新旧料要按一定比例 配用 严格遵守熔炼工艺,熔炼工具应刷涂料
编制:
涂料不纯或用量过多 涂料中石墨含量过多
充型过程中由于模具 填充时金属分散成密集液滴,高速撞击
十四、麻 面
温度或合金液温度过 低,在近似于欠压条 件下铸件表面形成的
型壁
细小麻点状分布区域 内浇口厚度偏小
涂料使用应薄而均匀,不能堆积,要用 压缩空气吹散
减少涂料中的石墨含量或选用无石墨水 基涂料
正确设计浇注系统,避免金属液产生喷 溅,改善排气条件,避免液流卷入过多 气体,降低内浇口速度并提高模具温度
合金收缩率大 内浇口截面积太小
比压偏低
模具温度过高
合理设计浇注系统,避免合金液直接冲 击型芯、型壁,适当降低填充速度
修正模具
打光表面,保证粗糙度符合要求 涂料使用薄而均匀,不能漏喷涂料
适当增加含铁量至0.8-1%
改善铸件结构,使壁厚稍为均匀,厚薄 相差较大的连接处应逐步缓和过渡,消 队热节
选择收缩率较小的合金
合金液过热或保温时间过长
合金不宜过热,避免合金长时间保温
二十二、 碎性
铸件基本金属粒过于 粗大或细小,使铸件
易断裂或碰碎
激烈过冷,结晶过细 铝合金中杂质锌、铁等含量太多
铝合金中含铜量超出规定范围
提高模具温度,降低浇注温度
严格控制合金化学成分
压铸件常见缺陷及解决办法

压铸件常见缺陷及解决办法
一、压铸件缺陷
1、压铸凹痕:压铸凹痕是指在压铸后件表面出现的凹痕或沟等处的缺陷。
2、拉伤表面:这种缺陷是指当件拉伸出模后,件毛刺或表面斑点等特
征缺陷。
3、起火晶:起火晶是指压铸件中凝固过程中熔料里存在的大量小气泡
缺陷。
4、压型:这种缺陷是指模具中几个竖向型腔偏移位置,影响压铸件内
部夹紧、定位等缺陷。
二、解决办法
1、压铸凹痕:首先要检查有没有流淌痕或模具内应有的空气渗入,来
找出原因,同时要及时修整和修复模具。
2、拉伤表面:要检查压铸模具表面的震动是否合理,如果表面粗糙可
以适当采用打磨,以降低拉伤表面。
3、起火晶:保证熔料温度合适,及时移动和改变拳头垫针,使熔料流
动均匀;改进圠充,减少浪涌现象;改变压力以降低小气泡形成的机会;合理的检查温度之间的差异。
4、压型:检查模具的型腔,确保它们定位准确,消除产品的分离现象;合理更换冷却介质等以降低成型环境的温度差异。
压铸件缺陷产生原因及对应措施

1.铝合金中杂质锌、铁超过规定范围 1.严格控制金属中杂质成分
4
脆性
铸件基体金属晶粒过于粗大或 2.合金液过热或保温时间过长,导致 2.控制熔炼工艺
极小,使铸件易断裂或磁碎 晶粒粗大
3.降低浇注温度
3.激烈过冷,使晶粒过细
4.提高模具温度
1.压力不足,基体组织致密度差
1.提高比压
5
渗漏
压铸件经耐压试验,产生漏气 、渗水
2. 浇注温度或压铸模温度偏低 3.选择合金不当,流动性差 4. 浇道位置不对或流路过长 5.填充速度低
2. 提高压射比压,缩短填充时间 3.提高压射速度,同时加大内浇口截面 积 4.改善排气、填充条件 5.正确选用合金,提高合金流动性
6.压射比压低
1.不合适的脱模剂
2. 脱模剂用量过多,局部堆积
分。对原材料控制基体金相组织中的
初晶硅数量
1.首先进入型腔的金属液形成一个极
5
铸件表面上有与金属液流动方
流痕和花纹
向一致的条纹,有明显可见的 与金属体颜色不一样的无方向
性的纹路,无发展趋势
薄的而又不完全的金属层后,被后来 的金属液所弥补而留下的痕迹 2.模温过低,模温不均匀 3. 内浇道截面积过小及位置不当产生 喷溅 4.作用于金属液的压力不足
2. 压铸模材质不当或热处理工艺不正 金
网状发丝一样凸起或凹陷的痕 确
3. 模具预热要充分
8 网状毛翅 迹,随压铸次数增加而不断扩 3.压铸模冷热温差变化大
4. 压铸模要定期或压铸一定次数后退
大和延伸
4.浇注温度过高
火,消除内应力
5.压铸模预热不足
5. 打磨成型部分表面,减少表面粗糙
6. 型腔表面粗糙
压铸缺陷及解决方法

压铸缺陷及解决方法1. 流痕 其他名称:条纹 特征:铸件表面上呈现与金属液流动方向相一致的,用手感觉得出的局部下陷光滑纹路。
此缺陷无发展倾向,用抛光法能去除。
产生原因 排除措施①两股金属流不同步充满型腔而留下的痕迹。
②模具温度低,如锌合金模温低于150℃,铝合金模温低于180℃,都易产生这类缺陷。
③填充速度太高。
④涂料用量过多。
①调整内浇口截面积或位置。
②调整模具温度,增大溢流槽。
③适当调整填充速度以改变金属液填充型腔的流态。
④涂料适用薄而喷匀。
2. 冷隔其他名称:冷接特征:温度较低的金属流互相对接但未熔合而出现的缝隙。
呈现不规则的线形,有穿透的和不穿透的两种,在外力作用下有发展趋势。
产生原因 排除措施①金属液浇注温度低或模具温度低。
②合金成分不符合标准,流动性差。
③金属液分股填充,融合不良。
④浇口不合理,流程太长。
⑤填充速度低或排气不良。
⑥比压偏低。
①适当提高浇注温度和模具温度。
②改变合金成分,提高流动性。
③改进浇注系统,改善填充条件。
④改善排溢条件,加大溢流量。
⑤提高压射速度,改善排气条件。
⑥提高比压。
3. 擦伤其他名称:拉伤、拉痕、粘模伤痕特征:顺着脱模方向,由于金属粘附,模具制造斜度太小而造成铸件表面的拉伤痕迹,严重时称为拉伤面。
产生原因 排除措施①型芯、型壁的铸造斜度大小或出现倒斜度。
②型芯、型壁有压伤痕。
③合金粘附模具。
④铸件顶出偏斜或型芯轴线偏斜。
⑤型壁表面粗糙。
⑥涂料常喷涂不到。
⑦铝合金中含铁量低于0.6% ①修正模具,保证制造斜度。
②打光压痕。
③合理设计浇注系统避免金属流对冲型芯型壁,适当降低填充速度。
④修正模具结构。
⑤打光表面。
⑥涂料用量薄而均匀,不能漏喷涂料。
⑦适当增加含铁量至适当增加含铁量至0.6~0.8%。
4. 凹陷其他名称:缩凹、缩陷、憋气、塌边特征:铸件平滑表面上出现凹瘪的部分,其表面呈自然冷却状态。
产生原因 排除措施①铸件结构设计不合理,有局部厚实部位,产生热节。
压铸件常缺陷原因及解决方法

压铸件常缺陷原因及解决方法压铸件常缺陷原因及解决方法压铸件常缺陷分析压铸件抛丸后产品表面变色, 主要是使用的抛丸有问题。
若是使用不锈钢丸,在里面加少量铝丸,抛后产品表面白亮。
压铸件表面经常有霉点,严重影响铸件的外观质量,主要是脱模剂造成。
目前,市面上大大小小生产脱模剂的厂家有一大批,其中不少厂质量存在各种问题,最主要的就是对压铸件会产生腐蚀作用。
一般压铸件厂不太注意,压铸件时间放得长一些,表面就会有白斑(霜状、去掉后呈黑色)出现,实际上已产生腐蚀。
主要是脱模剂中有会产生腐蚀作用的成分。
所以选择脱模剂一定不要只追求价格低,要讲性价比。
压铸件在抛丸后经常出现表面起皮现象,般由如下一些原因造成:1.模具或压射室(熔杯)未清理干净; 2.压射压力不够,(还需注意压射时动模有否退让现象);3.浇注系统开设有点问题,合金液进入型腔有紊流现象;4.模温问题等5.压射时金属液飞溅严重。
脱模剂一般不会渗透到压铸件里面。
但劣质脱模剂会对压铸件表面产生腐蚀作用,而且会向内部渗透;另外,脱模剂发气量大的话,会卷入压铸件里面形成气孔。
如果使用脱模膏之类的涂料不当时,会产生夹渣等缺陷。
用7005焊丝焊接7005压铸件,在焊接处出现油污和气泡,焊接方式为氩弧焊。
一般存在如下问题:1.焊丝与压铸件表面有油污,未清洗干净; 2.氩气不纯净,市售氩气有的里面杂质多,甚至含有水气,应选优质气。
合金压铸如果出模角度控制不好,经常出现粘模现角,如何来计算这个角度?压铸模出模斜度根据合金和铸件高度不同,有所不同。
一般铝合金压铸件拔模高度从3mm~250mm:内壁出模斜度按5º30´~0º30´,外壁出模斜度取其一半;圆型芯的出模斜度,按4º~0º30´。
文字符号的出模斜度按10º~15º具体如何细分挡次和各挡次斜度值的选取,请参阅模具设计手册或压铸件标准等资料。
压铸常见不良及改善对策
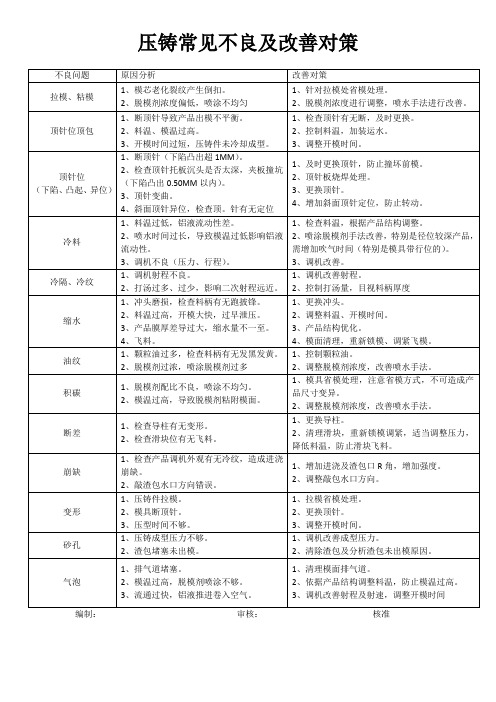
2、调整脱模剂浓度,改善喷水手法。
积碳
1、脱模剂配比不良,喷涂不均匀。
2、模温过高,导致脱模剂粘附模面。
1、模具省模处理,注意省模方式,不可造成产品尺寸变异。
2、调整脱模剂浓度,改善喷水手法。
断差
1、检查导柱有无变形。
2、检查滑块位有无飞料。
1、更换导柱。
2、清理滑块,重新锁模调紧,适当调整压力,降低料温,防止滑块飞料。
1、调机改善射程。
2、控制打汤量,目视料柄厚度
缩水
1、冲头磨损,检查料柄有无跑披锋。
2、料温过高,开模大快,过早泄压。
3、产品膜厚差导过大,缩水量不一至。
4、飞料。
1、更换冲头。
2、调整料温、开模时间。
3、产品结构优化。
4、模面清理,重新锁模、调紧飞模。
油纹
1、颗粒油过多,检查料柄有无发黑发黄。
2、脱模剂过浓,喷涂脱模剂过多
2、控制料温,加装运水。
3、调整开模时间。
顶针位
(下陷、凸起、异位)
1、断顶针(下陷凸出超1MM)。
2、检查顶针托板沉头是否太深,夹板撞坑(下陷凸出0.50MM以内)。
3、顶针变曲。
4、斜面顶针异位,检查顶。针有无定位
1、及时更换顶针,防止撞坏前模。
2、顶针板烧焊处理。
3、更换顶针。
4、增加斜面顶针定位,防止转动。
压铸常见不良及改善对策
不良问题
原因分析
改善对策
拉模、粘模
1、模芯老化裂纹产生倒扣。
2、脱模剂浓度偏低,喷涂不均匀
1、针对拉模处省模处理。
2、脱模剂浓度进行调整,喷水手法进行改善。
顶针位顶包
1、断顶针导致产品出模不平衡。
- 1、下载文档前请自行甄别文档内容的完整性,平台不提供额外的编辑、内容补充、找答案等附加服务。
- 2、"仅部分预览"的文档,不可在线预览部分如存在完整性等问题,可反馈申请退款(可完整预览的文档不适用该条件!)。
- 3、如文档侵犯您的权益,请联系客服反馈,我们会尽快为您处理(人工客服工作时间:9:00-18:30)。
培训操作工,或者减少喷涂时间增加吹气时间(自动喷涂) 验证PQ2曲线图,优化压铸参数 尝试调整切换点
4
裂纹
产生原因
圆角太小 顶针布局不合理 模具或产品存在拉伤 抽芯的分型线位置设计不良 铝液或模具温度太低 去除浇口时开裂 铝液铁含量大于0.9%
解决方法
与客户协商加大圆角。 尽量在受力位置,如筋条上布置顶针。如果一定要在壁薄的
脱模剂喷涂不均匀
模具型腔表面未做氮化和PVD涂 层
铝合金含铁量低于0.6%
培训操作工或者调整自动喷涂的喷嘴方向 重新处理模仁 重新熔炼
2
缺料
产生原因
解决方法
铝液含气量过高
铝液增加除气工序
模具排气不畅
优化排气块,或增加抽真空设备
脱模剂喷涂过多或者没有吹干 培训操作工,或者减少喷涂时间增加吹气时间(自动喷涂)
手段。 降低浇口速度,验证PQ2曲线图,优化压铸参数。
割镶件修复
6
飞料
产生原因
锁模力不足 模具受力不平衡 新模配模存在问题 旧模具配合存在问题 分型面有杂物 铸造压力过高 模仁和模架的刚性不足 模仁和模架热变形
解决方法
计算验证投影面积,检查机台工况。 调整压射中心,确认产品在压铸机板的中心位置。 对于新模具冷配模的效果与模具加热后存在差异。
压铸产品常见缺陷和解决方法
1
拉伤,粘模
产生原因
拔模斜度不够 铝液冷却速度慢 模具表面碰伤
解决方法
尽量在前期设计保证拔模斜度合理。后期增加顶针尖山顶出 不平衡带来的拉伤。
检查模具的工作温度,保证220度左右;增加冷却,特别是 高压点冷。
补焊修复。
模具冲蚀
验证PQ2曲线图,优化压铸参数,别是浇口速度。
重新配模,必要时成型部分降面处理。 生产时要定期清理。 调机检查工艺参数。
模具制作前的评估要重点评估此项是否达标。 需要强化冷不平衡
产品离开模具后自然冷却变形 粘定模导致变形
去除浇口的方式不当 产品摆放不当 粘模导致变形
脱模剂喷涂不均匀
解决方法
检查顶针布局是否合理。尽量在受力位置,如筋条上布置顶 针。如果一定要在壁薄的地方布置顶针,则需要增加顶针凸
压室充满度 产品壁厚不均匀 铝液和模具温度太低
早期要合理计算评估充满度;后期减少冲头直径(成本略高)
早期与客户协商优化产品结构。增加挤压销或者增加渣包和 辅助浇口
常规:铝液680度,模具220度
3
气泡
产生原因
模具排气不畅 铝液含气量过高 脱模剂喷涂过多或者没有吹干 浇口速度过高 高速切换位置过早
解决方法
增压建压时间过长
检查压铸机工况和品牌
铝液含气量过高
铝液增加除气工序
10
夹渣
产生原因 铝液质量变差
解决方法 合理安排维护保养设备
11
12
地方布置顶针,则需要增加顶针凸台。 检查铁含量和检查修复模具。
需要增加在动模处的挂台或特征。 常规:铝液680度,模具220度。
改用锯床或者冲模去除浇口。 降低铁含量。
5
龟裂
产生原因
模具冷热交替 模具预热温度不够
浇口速度过高 补焊修复处龟裂
解决方法
选择好的模仁材料,并每5000模次去应力热处理 必须要用火烤或者用高温油循环加热,不能用铝液作为加热
压室充满度
早期要合理计算评估充满度;后期减少冲头直径(成本略高)
没有在铝液流动末端增加排气和 渣包
流道或浇口面积过小,压力和流 量低
根据模流分析或实际情况增加 重新计算并加大
流道入射角
根据模流分析优化流道
紊流
根据模流分析优化流道
产品壁厚过大,产生紊流
前期优化产品,采取抽真空或者半固态压铸
增压不足
检查压铸机工艺参数和压铸机工况
台
强化模具冷却特别是产品四周的冷却。后期校正。
在动模对应地方增加倒扣,或增加定模拔模斜度,或在对应 位置增加钩针。
改用冲模或者锯床
改善工艺
与改善拉伤,粘模一致
培训操作工或者调整自动喷涂的喷嘴方向。
8
多料
产生原因
模具蹦坏
解决方法
补焊或割镶件修复
9
气孔,缩孔
产生原因
解决方法
模具排气不畅
优化排气块,或增加抽真空设备