轴系部件的选择与设计
轴系结构实验报告

轴系结构实验报告轴系结构实验报告引言:轴系结构是工程学中一个重要的研究领域,它关注的是轴承的设计、轴线的布置以及轴系的稳定性等问题。
在实际工程中,轴系结构的设计和优化对于保证机械设备的正常运行起着至关重要的作用。
本实验旨在通过对轴系结构的实验研究,探讨轴系结构的性能特点和优化方法。
实验一:轴承选型与布置在轴系结构中,轴承的选型和布置是关键的一步。
在本实验中,我们选择了两种常见的轴承类型:滚动轴承和滑动轴承,并进行了对比研究。
实验结果显示,滚动轴承具有较高的承载能力和较低的摩擦系数,适用于高速旋转的轴系结构。
而滑动轴承则具有较低的噪音和振动特性,适用于要求较高平稳性的轴系结构。
根据实际需求,我们可以灵活选择不同类型的轴承,并进行合理的布置,以满足工程项目的要求。
实验二:轴系稳定性研究轴系的稳定性是轴系结构设计和优化的重要考虑因素之一。
在本实验中,我们通过改变轴系的几何参数,研究了轴系的稳定性变化。
实验结果显示,当轴系的刚度较小时,轴系容易发生振动和共振现象,导致整个机械系统的运行不稳定。
而当轴系的刚度较大时,轴系的稳定性得到了明显改善。
因此,在轴系结构设计中,我们需要合理选择轴材料、增加轴系的刚度,以提高轴系的稳定性。
实验三:轴系优化方法为了进一步提高轴系结构的性能,我们进行了轴系的优化研究。
通过改变轴系的结构参数,我们探讨了不同优化方法对轴系性能的影响。
实验结果显示,通过合理设计轴系的结构参数,如减小轴系的质量、增加轴系的刚度等,可以显著提高轴系的性能。
此外,我们还发现,采用轴系的动态平衡技术能够有效减小轴系的振动和噪音,提高整个机械系统的运行效率。
结论:通过本次轴系结构的实验研究,我们深入了解了轴系的性能特点和优化方法。
轴承的选型和布置、轴系的稳定性研究以及轴系的优化方法都对轴系结构的性能起着重要的影响。
在实际工程中,我们应根据具体需求,合理选择轴承类型、优化轴系结构,并采取相应的措施提高轴系的稳定性和性能。
哈工大_机械设计大作业_轴系部件设计_5.3.5
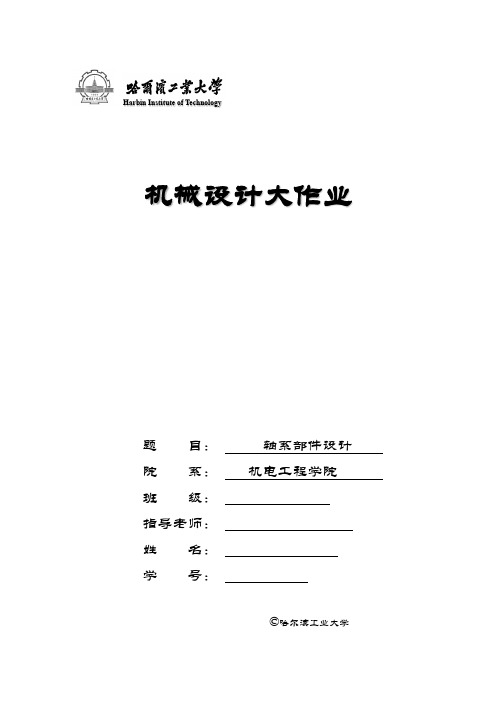
Harbin Institute of Technology机械设计大作业题目:轴系部件设计院系:机电工程学院班级:指导老师:姓名:学号:©哈尔滨工业大学目录一、材料选择 (3)二、初算轴径 (4)三、轴系结构设计 (4)3.1轴承部件的结构型式及主要尺寸 (4)3.2及轴向固定方式 (4)3.3选择滚动轴承类型 (4)3.4 轴的结构设计 (5)3.5 键连接设计 (5)四、轴的受力分析 (6)4.1 画出轴的结构和受力简图 (6)4.2 计算支承反力 (6)4.3 画出弯矩图 (7)4.4 画出扭矩图 (7)五、校核轴的强度 (8)六、校核键连接强度 (9)七、校核轴承寿命 (9)7.1 当量动载荷 (9)7.2 校核轴承寿命 (9)八、轴上的其他零件 (10)8.1 毡圈 (10)8.2 两侧挡油板 (10)8.3 轴承端盖螺钉连接 (10)九、轴承端盖设计 (10)9.1 透盖 (10)9.2 轴承封闭端盖 (10)十、轴承座 (10)十一、参考文献 (11)轴系部件设计任务书题目: 设计绞车(带棘轮制动器)中的齿轮传动高速轴轴系部件结构简图见下图:。
原始数据如下:室内工作、工作平稳、机器成批生产一、材料选择通过已知条件和查阅相关的设计手册得知,该传动机所传递的功率属于中小型功率。
因此轴所承受的扭矩不大。
故选45号钢,并进行调质处理。
二、初算轴径对于转轴,按扭转强度初算直径:min d C ≥其中2P ——轴传递的功率,=2 3.0P KW m n ——轴的转速,r/min ,296.5/min m n r =C ——由许用扭转剪应力确定的系数。
查表10.2得C=106~118,考虑轴端弯矩比转矩小,取C=106。
≥=⨯=min d 10622.93Cmm由于考虑到轴的最小直径处要安装大带轮,会有键槽存在,故将其扩大5%,得min d 1.0524.07k d mm ≥⨯=,按标准GB2822-81的10R 圆整后取125=d mm 。
轴系结构设计实验报告

轴系结构设计实验报告轴系结构设计实验报告引言轴系结构是机械工程中的一个重要概念,它涉及到机械装置中的轴、轴承和传动装置等元件。
轴系结构的设计对于机械装置的稳定性和性能有着重要的影响。
本实验旨在通过设计和测试不同轴系结构的性能,探索轴系结构的设计原则和优化方法。
实验目的本实验的目的是研究不同轴系结构的设计对于机械装置性能的影响,具体包括以下几个方面:1. 了解不同轴系结构的基本原理和特点;2. 掌握轴系结构的设计方法和步骤;3. 测试和分析不同轴系结构的性能差异;4. 探索轴系结构的优化方法。
实验装置和方法本实验使用了一台模拟机械装置,包括轴、轴承和传动装置等元件。
实验过程如下:1. 选择不同类型的轴承,包括滚动轴承和滑动轴承,并安装在不同的轴上;2. 设计和制造不同类型的轴系结构,包括单支撑轴系、双支撑轴系和悬臂轴系等;3. 测试不同轴系结构的转动摩擦力、刚度和振动等性能指标;4. 分析和比较不同轴系结构的性能差异;5. 根据实验结果,进行轴系结构的优化设计。
实验结果和讨论通过实验测试和数据分析,我们得到了以下结果和讨论:1. 不同类型的轴承对轴系结构的性能有着显著的影响。
滚动轴承具有较小的摩擦力和较高的刚度,适用于高速和高负荷的工况;而滑动轴承具有较大的摩擦力和较低的刚度,适用于低速和低负荷的工况。
2. 不同类型的轴系结构对机械装置的性能也有着显著的影响。
单支撑轴系具有较大的刚度和较小的振动,适用于要求较高精度和稳定性的工况;双支撑轴系具有较小的刚度和较大的振动,适用于要求较高速度和动态响应的工况;悬臂轴系则适用于较小负荷和较简单的工况。
3. 轴系结构的优化设计需要综合考虑不同性能指标之间的矛盾和平衡。
例如,在追求较大刚度的同时,需要注意振动的控制和减小摩擦力的影响。
结论通过本实验,我们深入了解了轴系结构的设计原理和方法,并通过实验测试和数据分析,探索了不同轴系结构的性能差异和优化设计。
我们发现不同类型的轴承和轴系结构对机械装置的性能有着重要的影响,需要根据具体工况和要求进行选择和设计。
机械设计:轴系设计方案

7.参考文献------------------------------------------------------8
1.设计题目及要求
图示二级斜齿圆柱齿轮减速器,已知中间轴Ⅱ的输入功率P=40kW,转速nⅠ=100r/min,齿轮2的分度圆直径d2=688mm,螺旋角β2=12°50′,齿轮3的分度圆直径d3=170mm,螺旋角β3=10°29′。本设计报告要求完成:
3.4.3.校核薄弱截面---------------------------------------6
3.5.轴的安全系数校核计算-----------------------------------6
4.轴承的选型与校核---------------------------------------------7
传递到轴系部件上的转矩为:
计算齿轮2有关系数:
圆周力:
径向力:
轴向力:
计算齿轮3有关系数:
圆周力:
径向力:
轴向力:
3.4.2绘制轴受力图
我们可以根据上一步的齿轮受力结果绘制节点受力简图,后根据节点受力简图即可方便得到轴的分段弯矩公式,最后利用Excel表格的x-y坐标图工具由弯矩公式求得水平与垂直两方向的弯矩图,如下图4.2.1,4.2.2。
[2]机械设计手册/闻邦椿主编-机械工业出版社
[3]机械工程师设计手册-电子版/北京英科宇科技开发中心
本例中轴键主要用于在扭转方向固定齿轮与轴,考虑到减速器需要良好的对中性,并且应该能够适应变载荷受力情况,普通型平键可以满足设计需求。参阅GB/T 1096-2003标准,为保证键连接的强度,选用尺寸为28×16的键较为适宜,最终得到初步设计结果。
哈工大机械设计大作业轴系部件设计完美版

(4)轴段1和轴段7:
轴段1和7分别安装大带轮和小齿轮,故根据大作业3、4可知轴段1长度 ,轴段7长度 。
(5)计算
, ,
, ,
4、轴的受力分析
4.1画轴的受力简图
轴的受力简图见图3。
4.2计算支承反力
传递到轴系部压轴力
带初次装在带轮上时,所需初拉力比正常工作时大得多,故计算轴和轴承时,将其扩大50%,按 计算。
图2
3.2选择滚动轴承类型
因轴承所受轴向力很小,选用深沟球轴承,因为齿轮的线速度小于2m/s,齿轮转动时飞溅的润滑油不足于润滑轴承,采用油脂对轴承润滑,由于该减速器的工作环境有尘,脂润滑,密封处轴颈的线速度较低,故滚动轴承采用唇形圈密封,由于是悬臂布置所以不用轴上安置挡油板。
3.3键连接设计
齿轮及带轮与轴的周向连接均采用A型普通平键连接,齿轮、带轮所在轴径相等,两处键的型号均为12 8GB/T 1096—1990。
4.4画转矩图……………………………………………………………6
五、校核轴的弯扭合成强度……………………………………………………8
六、轴的安全系数校核计算……………………………………………………9七、键的强度校核………………………………………………………………10
八、校核轴承寿命………………………………………………………………11
在水平面上:
在垂直平面上
轴承1的总支承反力
轴承2的总支承反力
4.3画弯矩图
竖直面上,II-II截面处弯矩最大, ;
水平面上,I-I截面处弯矩最大, ;
合成弯矩,I-I截面:
II-II截面: ;
竖直面上和水平面上的弯矩图,及合成弯矩图如图5.4所示
4.4画转矩图
哈工大 机械设计 大作业 轴系部件设计说明书

Harbin Institute of Technology机械设计大作业设计题目: 院 班 姓 学 时 系: 级: 名: 号: 间:轴系部件设计 英才学院2012.12.05哈尔滨工业大学方案 5.2.2 3nm (r / min)710nw (r / min)80i12.4轴承座中 心高 H/mm 200最短工作 年限 5年2班工作环境 室内潮湿一、选择轴的材料因传递功率小,扭矩小,机器工作平稳,单向回转,可选择 45 号钢并调质处理。
二初算轴径对于转轴,按扭转强度初算直径式中P——轴传递的功率; C——由许用扭转切应力确定的系数; n——轴的转速,r/min。
, 因弯矩比转矩小, 且齿轮装在悬伸端, 应取较小值, C由[1] 中表 9.4 查得 可取。
输出轴所传递的功率:输出轴的转速:代入数据,得考虑键的影响,将轴径扩大 5%,。
三结构设计1. 确定轴承部件机体结构形式及主要尺寸为方便轴承部件的装拆,机体采用剖分式结构。
取机体的铸造壁厚 δ=9mm,机体上轴 承旁连接螺栓直径 ,装拆螺栓所需要的扳手空间 ,故轴承座内壁至座孔外端面距离 ,取 L=49 mm。
2.确定轴的轴向固定方式因为轴的跨度不大,且工作温度变化不大,故轴的轴向固定采用两端固定方式。
3.选择滚动轴承类型,并确定其润滑与密封方式因为轴受轴向力作用,故选用角接触球轴承支承。
因为齿轮在机体外侧,无油滴飞溅, 故滚动轴承采用脂润滑。
因采用脂润滑,故选用毛毡圈密封。
4.轴的结构设计本方案有 7 个轴段的阶梯轴。
由最小直径得 带轮、齿轮倒角为 1.5mm,所以 因此 ,取要 和 轴 承 配 合 , 查 [2] 中 表 12.2 , 初 选 轴 承 7208C , 其 基 本 尺 寸 是 :。
因此采用凸缘式轴承盖,其凸缘厚度,。
为避免齿轮轮毂端面与轴承盖连接螺栓头相碰,并便于轴承盖上螺栓的装拆,齿轮轮毂端面与轴承盖间应有足够的 间距 K,取轴段①的长度。
轴系部件结构设计

轴系部件结构设计本文介绍了轴系部件结构设计的重要性,以及本文的目的和结构安排。
轴系部件结构设计是机械工程领域中重要的设计任务之一。
轴系部件是指连接和传递动力的轴、轴承、联轴器等部件。
它们的结构设计直接影响到机械设备的性能、寿命和可靠性。
良好的轴系部件结构设计能够保证机械设备的正常运转。
首先,合理设计的轴可以实现传递动力和承载负荷的功能;其次,优化设计的轴承能够减少能量损失和机械设备的故障率;还有,恰当选择的联轴器可以实现动力传递的可靠性和高效性。
本文的目的在于深入探讨轴系部件结构设计的关键要素和原则,并提供相关的设计指导。
首先,我们将介绍轴系部件结构设计的基本原则和考虑因素;然后,我们将详细讨论轴的设计要点和注意事项;接着,我们将重点介绍轴承的选择和安装方法;最后,我们将讨论联轴器的选型和安装步骤。
通过阅读本文,读者将了解到轴系部件结构设计的重要性,并可以获得实用的设计指导,以提升机械设备的性能和可靠性。
参考文献请注意,本文引言部分未引用任何内容,其信息为创造性生成)本部分将介绍轴系部件的不同分类和各自的功能。
轴系部件包括轴承、齿轮、连接件等,它们在机械系统中起着重要的作用。
1.轴承轴承是轴系部件中的重要组成部分,它用于支撑轴的旋转运动并减少摩擦。
根据结构和用途的不同,轴承可以分为滚动轴承和滑动轴承。
滚动轴承采用滚动体(如球、柱体、圆锥体)和轴承座的结构,适用于高速转动、小摩擦、高精度要求的场景。
滑动轴承则采用润滑剂在轴和轴承之间形成薄膜,减少摩擦力,适用于低速大负荷的场景。
2.齿轮齿轮是一种通过齿的啮合传递力和运动的机构,常用于机械传动系统中。
齿轮根据齿的形状和用途可以分为直齿轮、斜齿轮、蜗杆齿轮等。
直齿轮是最常见的齿轮形式,它的齿面与轴线平行,适用于传递旋转运动和转矩的工况。
斜齿轮的齿面与轴线倾斜,可以传递更大的力和转矩。
蜗杆齿轮用于角度传动,具有较高的传动比和安全性。
3.连接件连接件用于连接轴系部件和其他机械部件,保证它们协同工作。
轴的设计知识范文

轴的设计知识范文轴是一种用于传递和转动动力的机械元件,广泛应用于各个行业和领域。
在轴的设计中,需要考虑到材料的选择、尺寸的确定、结构的设计等因素。
本文将介绍轴的设计知识,并详细讨论这些因素。
首先,材料的选择对轴的设计至关重要。
常见的轴材料有钢、铜、铝等。
钢材具有优异的机械性能,强度高、刚性好,因此常被用于制作轴。
在选择材料时,不仅需要考虑到材料的机械性能,还需要考虑到材料的耐磨性、耐腐蚀性等特性,以满足实际应用的需求。
其次,尺寸的确定也是轴设计的关键。
轴的尺寸设计包括直径、长度、轴颈位置等方面。
首先,轴的直径应根据承载力和刚度要求进行确定。
一般来说,轴的直径越大,其承载能力越高,但同时也会增加轴的重量和制造成本。
此外,轴的长度也需要根据应用需求进行合理设计。
如果轴过长,容易发生挠曲和变形;如果轴过短,会影响其刚度和承载能力。
轴颈位置的确定则与安装和传动装置的设计相关,需要综合考虑到传递力矩和受力平衡等因素。
结构的设计也是轴设计的关键。
具体而言,结构设计包括轴上的各种传动部件(如键槽、轴肩等)和连接方式(如销轴、铆接、焊接等)。
为了确保轴与其他零件的连接可靠性,需要选用合适的连接方式。
例如,大型机械设备通常采用销轴连接,而小型机械设备则常采用铆接或焊接连接。
此外,为了提高轴的刚度和耐疲劳性能,设计者还可以采用加强筋、斜槽等措施。
另外,轴的表面处理也是轴设计的一个重要环节。
轴的表面处理可以改善其表面质量、硬度和耐磨性。
常见的轴表面处理方法包括热处理、渗碳、表面镀层等。
其中,最常用的是热处理,通过控制轴的加热温度和冷却方式,可以改变轴的组织结构,提高其硬度和耐磨性。
除了上述基本的设计知识外,还有一些注意事项需要考虑。
首先,轴与轴承的配合是轴设计中的一个重要环节。
轴与轴承的配合直接影响轴的运转和使用寿命。
其次,需要注意轴的平衡性。
由于轴承的存在,轴在运转时会产生一定的离心力。
如果轴的质量分布不均匀,会导致轴的弯曲和振动,从而影响轴的运转稳定性。
机械设计课程设计轴系部件设计说明书

轴磨削加工时的表面质量系数,由参考文献[1]附表10.1和附表10.2,得 。
由此,安全系数计算如下:
由参考文献[1]附表10.5,查得许用安全系数 。
显然 ,故a—a剖面安全。
对于一般用途的转轴,也可按弯扭合成强度进行校核计算。
对于单向转动的转轴,通常转矩按脉动循环处理,取折合系数 ,当量应力为
轴承Ⅰ的总支承反力:
轴承Ⅱ的总支承反力:
3.轴弯矩计算
在水平面上
a—a剖面左侧:
a—a剖面右侧:
在垂直平面
合成弯矩
a—a剖面左侧:
a—a剖面右侧:
4.轴转矩算
5.轴的受力简图(b)、弯矩图(c、d、e)和转矩图(f)
五校核轴的强度
此轴几乎为对称布置,但a—a剖面左侧使用套筒固定齿轮,轴径比右侧小,故a—a剖面左侧为危险剖面。
已知轴的材料为45钢,调质处理,查得 。
二初算轴径
对于转轴,按扭转强度初算直径
式中P——轴传递的功率;
C——由许用扭转剪应力确定的系数;
n——轴的转速,r/min。
由参考文献[1]表10.2查得 ,考虑轴端弯矩比转矩小,故取 。
输出轴所传递的功率:
输出轴的转速:
代入数据,得
考虑键的影响,将轴径扩大5%, 。
三结构设计
1.轴承部件机体结构形式及主要尺寸
(1)联轴器及轴段①和轴段⑧
本设计中,轴段①和轴段⑧为轴的最小尺寸 。因此,轴段①和轴段⑧与联轴器的设计同时进行。
为了补偿联轴器所连接的两轴的安装误差,隔离振动,选用弹性柱销联轴器。
由参考文献[1]表13.1查得 ,则计算转矩
由参考文献[2]表13.1可以查得GB/T 5014-2003中的LX3型弹性柱销联轴器符合要求。
(完整版)轴系布局与设计
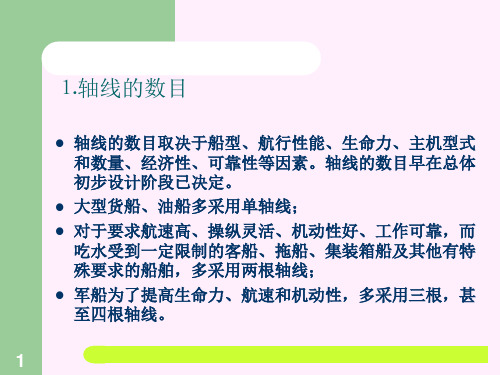
⑴主机位置布置原则如下
①对称布置:考虑到设备重量的平衡以及布置和操作的便利。 单轴系的轴线一般布置在船舶的纵中剖面上; 双轴系的轴线一般对称布置于船舶纵中剖面两侧,即对称布
置在船舶两舷; 三根轴系的船舶,一根布置在船舶的纵中剖面上,其余两根
对称布置在左右两舷。多轴系的间距由船舶总体设计确定。
当轴线出现倾角和偏角时,将使螺旋桨的推力受到损失,因此必须对倾 角和偏角加以控制。
一般将倾角控制在0°~5°之内,高速快艇轴线的倾角可放大到12°~ 16°;偏角则控制在0°~3°之内。
③主机应尽量靠近机舱后舱壁布置,以缩短轴线长度。
④应考虑主机左、右、前、底与上部空间是否满足船舶规范, 另外还需要考虑拆装与维修要求以及吊缸的高度是否足够等 因素。比如高度方向,一般应使主机的油底壳不碰到船的双 层底或肋骨,并使它们之间留有向隙,还应留出油底壳放油 所需的操作高度。
7
⒉轴承的间距
⑴中间轴承最小间距:lmin=24.9d2/3 (cm) 式中:d—轴径,cm
缘由:中间轴承底座通过螺栓与船体刚性连接, 船体因受水压、装载等因素影响而产生变形 (尤其垂向),轴承随之变位,从而产生附加 负荷。当变位量△一定时,轴承间距愈小,当 轴承变位时,它对轴线的牵制作用愈大,其附 加负荷也愈大,故轴承的间距太小是不利的, 应对它有所限制。
4
⑵螺旋桨的布置与定位
螺旋桨的布置与定位由船体总体设计决定,其原则是保证螺 旋桨可靠而有效地工作。
①螺旋桨应有一定的浸没深度。单桨船的浸没深度e=(0.250.30)D,双桨船的浸没深度e=(0.4-0.5)D。D为螺旋桨直 径;
②螺旋桨不应超出船体中部轮廓之外; ③叶梢应尽量高于船体基线以避免螺旋桨在浅水区域航行时
概述轴系的结构方案设计

概述轴系的结构方案设计轴系的结构方案设计和机器的整体质量息息相关,一旦发生轴失效,将导致严重后果。
轴系的结构方案设计和一般零部件的设计存在很大的差异,不仅包括强度设计,还包括结构设计。
1 基于功能元的结构方案设计分析机械产品概念设计内容主要包括下列三个部分:功能抽象化、功能分解、功能结构图设计。
机器可被视作一个大系统,在这个系统中,各种零件按照某种关系组合在一起,以满足客户的特定需求,其基本功能要素如下:(1)轴承集——支撑功能的功能元;(2)齿轮副集——传递运动的功能元;(3)螺栓集——紧固功能元。
在每一类功能元中,又可根据功能特性的差异而做进一步的细分。
以图1所示的单级减速器为例,扭矩通过轴、键、齿轮、轴承、轴承座进行传递,力的传递过程可以用图2表示。
2 轴系主要功能元的特征属性分析2.1 轴的属性轴发挥着支撑以及传递转矩的功能,其决定性能的因素主要有两个:一是刚度,二是强度。
在轴的设计过程中,不仅要以工作能力准则为基础,而且要兼顾如下要求:(1)轴向定位方法的运用;(2)周向固定轴上的各类零件,使其符合转矩传递的要求;(3)轴和其他部分存在相对滑动的表面要具有良好的耐磨性;(4)符合实际工艺生产要求。
2.2 传动类结构功能元两轴间的运动通常依靠齿轮传动来完成。
齿轮传动不仅效率高,而且持续稳定,因而具有很强的适应性。
齿轮副有以下分类:(1)平面齿轮——直齿/斜齿圆柱齿轮传动;(2)空间齿轮——传递相交轴/交错轴运动。
结合齿轮的特点及使用条件,采用功能元划分的方法将齿轮副的十大特征总结如下:(1)传动比;(2)传动平稳性;(3)传动效率;(4)耐磨性;(5)结构紧凑性;(6)轴向力;(7)承载能力;(8)转速要求;(9)两轴线方向;(10)制造成本。
2.3 支撑类结构功能元在机器中,轴承装置是一种应用广泛且相当关键的部件,其设计质量关系着机器是否能够正常运转。
轴承装置的设计涉及多种知识与技术,表现出了一定的复杂性和灵活性。
轴系的结构设计

四、轴上零件的周向定位
运转时,为了传递转矩或避免与轴发生相对转动, 零件在轴上必须周向固定。
轴上零件的周向定位方法主要有键联接(平键、 半圆键、楔键等)、花键联接、弹性环联接、过 盈配合联接、销联接、成型联接等等。
a)平键
制造简单、装拆方便。用 于传递转矩较大,对中性 要求一般的场合
b)花键
锥顶重合于轴承回转 轴线
七、轴的结构工艺性
1、关于轴的形状:阶梯轴
• 由于阶梯轴接近于等强度,而且便于加工和轴 上零件的定位和拆装,所以实际上的轴多为阶 梯形.
2、关于轴的有关尺寸
➢ 为了能选用合适的圆钢和减少切削用量,阶梯轴 各轴段的直径不宜相差过大,一般取为5~10MM。
➢ 为了便于切削加工,一根轴上的圆角应尽可能取 相同的半径;
轴系结构的设计
第一节 轴 一、轴的功用和分类
1、功用:支承其他回转件,承受转矩与弯矩, 并传递运动和动力。
2.轴的分类
1)按所受载荷特点分三种: 心轴: 只承受弯矩;如 传动轴:只承受转矩;如 转轴:同时承受弯矩和转矩;如
2)按轴的结构形状分:
直轴,曲轴; 光轴,阶梯轴; 空心轴,实心轴; 刚性轴,挠性轴。
3、用带螺纹的端盖调整;
4、用圆螺母调整轴承内圈调整游隙。
预紧的定义:
对某些可调游隙的轴承,为提高旋转精度和 刚度,常在安装时施加一定的轴向作用力(预紧 力)消除轴承游隙,并使内、外圈和滚动体接触 处产生微小弹性变形。
预紧的方法有:
一般采用移动轴承套圈的方法;对一些支承 的轴承组合,还可用金属垫片或磨窄外圈等方法 获得预紧。
内圈滚道、滚子和外圈滚道这三个圆锥面的锥顶必须重合于轴承回 转轴线上——说着玩的!
轴系设计 说明书
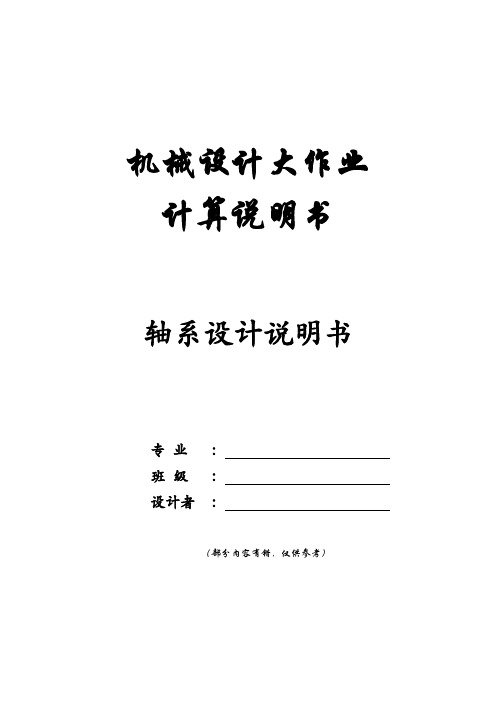
机械设计大作业计算说明书轴系设计说明书专业:班级:设计者:(部分内容有错,仅供参考)设计题目:已知数据:转速1/480/m in m n n i r == P=3.65kw T=72610.24 N ·mm轴上小齿轮: 齿数Z1=17,模数5m =,齿宽b=17mm ,分度圆直径d=85mm ,压力角 20=α 圆周力1510/2t a T F Nd ==径向力×tan 550r t F F N α== 法向力F n =F t ÷cos20=1607N 轴上大带轮:压轴力:F Q =1481.68N=1490N一、选择轴的材料因传递功率不大,且对质量及结构尺寸无特殊要求,故选用常用材料45号钢,调质处理。
二、初算轴径d min对于转轴,按扭转强度初算轴径,由机械设计教材得C=106~118,考虑轴端弯矩比转矩小,故取C=106,则d =C PN3=20.84mm考虑键槽的影响,取d min =d ×1.05=21.88mm ,取轴径为d=40mm 。
三、结构设计1.确定轴承部件机体的结构形式及主要尺寸为方便轴承部件的装拆,铸造机体采用剖分式结构,取机体的铸造壁厚δ=8mm ,机体上轴承旁连接螺栓直径d 2=12mm ,装拆螺栓所需要的扳手空间C 1=18mm ,C 2=16mm ,故轴承座内壁到座孔外壁面距离L=δ+C 1+C 2+5~8mm=47~50mm ,取L=50mm 。
2.确定轴的轴向固定方式因为一级齿轮减速器输出轴的跨距不大,且工作温度变化不大,故轴的轴向固定采用两端固定方式。
3.选择滚动轴承类型,并确定其润滑与密封方式因为没有轴向力作用,故选用深沟球支承。
因为齿轮的线速度v =πdn 60×1000=π×85×10060×1000m/s =0.45m/s ,齿轮为开式,故滚动轴承采用脂润滑。
因为该减速器采用脂润滑,密封处轴颈的线速度较低,故滚动轴承采用毡圈密封。
滚动轴承轴系结构设计

9—3 滚动轴承轴系结构设计滚动轴承轴系的结构设计,主要是解决轴承在机器中的固定、调整、预紧、配合、装拆、润滑与密封等问题。
一、支承部分的刚度和同轴度轴承在载荷的作用下应具有一定的旋转精度和寿命,这就要求轴承以及与轴承相配的轴、轴承座或箱体都应具有足够的刚度。
一般外壳及轴承座孔壁均应有足够的厚度,壁板上的轴承座的悬臂应尽可能地缩短,并用加强筋来增强支承部位的刚度 ( 图 9 - 12) 。
如果外壳是用轻合金或非金属制成的,安装轴承处应采用钢或铸铁制的套杯 ( 图 9 - 13) 。
对于一根轴上两个支承的座孔,必须尽可能地保持同心,以免轴承内外圈间产生过大的偏斜。
最好的办法是采用整体结构的外壳,并把安装轴承的两个孔一次镗出。
如在一根轴上装有不同尺寸的轴承时,外壳上的轴承孔仍应一次镗出,这时可利用衬筒来安装尺寸较小的轴承。
当两个轴承孔分在两个外壳上时,则应把两个外壳组合在一起进行镗孔。
图 9—12 用加强筋增强轴承座孔刚度图 9—13 利用套杯安装轴承二、滚动轴承的轴向固定滚动轴承的轴向固定,包括轴承外圈与机座的固定和轴承内圈与轴的固定。
对这两种固定的要求取决于轴系 ( 轴、轴上零件、轴承与机座的组合 ) 的使用和布置情况。
一方面,轴和轴承相对于机座应有确定的位置,以保证轴上零件能正常地传递力和运动;另一方面,由于工作中轴和机座的温度不相等 ( 通常轴的温度高于机座的温度 ) ,而温差可能产生较大的温度应力。
为保证轴系中不致产生过大的温度应力,应在适当的部位设置足够大的间隙,使轴可以自由伸缩。
常见的滚动轴承的轴向固定形式有如下几种。
1 . 两端固定支承如图 9 - 14 所示,轴两端的轴承各限制轴在一个方向的轴向移动,合起来就限制轴的双向移动。
为补偿轴的受热伸长,轴承盖与外圈端面之间应留有 0.25 ~0.4mm 的补偿间隙 c (图 9 — 14b )。
间隙值可用改变轴承盖和箱体之间的垫片厚度进行调整。
轴系设计

轴的强度计算:
1. 按扭转强度计算
2. 按弯扭合成强度计算
机械设计基础
分 目 录
上 一 页
下 一 页
回返
一. 按扭转强度计算
按扭转强度计算时,只考虑轴所受的转 矩,如果轴还受不大的弯矩,则用降低许用 扭转切应力的方法加以解决。 按扭转强度计算适应下列情况: 1)以传递转矩为主的传动轴;
2)对转轴进行结构设计时,初步估算轴径;
返 回
一单级齿轮减速器,已知:
输出轴通过弹性柱销联轴器与工
W
作机相联,单向转动。传递功率 P=4.95 kW,转速 n= 71.64
r/min,试设计该输出轴。
Ⅰ
0
机械设计基础
一、选择轴的材料、估算最小轴径 45钢 调质处理
A=118~107
最小轴径:
[-1]=60 MPa
dmin A
3
P 9.41 (107 ~ 118) 3 44 ~ 48 n 93.61
机械设计基础
ห้องสมุดไป่ตู้系结构改错
图中有一处错误, 请改正。
错误原因 r >c 使得轴上零件与轴肩 的配合不够紧密。
r
机械设计基础
分 目 录
上 一 页
下 一 页
返 回
轴系结构改错
图中有三处错误, 请改正。 错误原因 1.轴肩太高,滚动 轴承无法拆卸。
2.轴上未留退刀槽,不便于 螺纹加工。 3.轴左段直径过大,圆螺 母无法装入。
轴的设计例题
一圆锥-圆柱齿轮减速器, 已知:输出轴通过弹性柱销联轴 器与工作机相联,单向转动。传 递功率 P=9.41 kW,转速 n= 93.61 r/min,试设计该输出轴。
S=8 分 目 录
机械基础——轴的类型、材料和结构设计

P368:3、4
课题
轴的类型、材料和结构设计
教学目的
1、熟悉轴的功用熟悉轴的材料的选择;
3、掌握轴结构设计的基本因素和基本方法。
教学安排
组织教学
讲述新课
第二十二单元轴
轴是组成机器的主要零件之一。轴的功用在于支承作回转运动的零件(如齿轮、带轮、链轮等),使其具有确定的工作位置,并传递运动与动力。
一、轴上零件的定位和固定
1、轴上零件的轴向定位和固定轴上零件的轴向定位和固定以轴肩、轴环、套筒、锁紧挡圈、圆螺母、弹性挡圈、轴端挡圈、轴承端盖及圆锥面等来实现。
2、轴上零件的周向定位和固定为使零件和轴一起转动并可靠地传递运动和动力,周向固定可以用普通平键或花键联接。当要求对中性好,在振动条件下工作时,可用轴孔间的过盈配合;也可两者同时采用。在载荷很小时,也可以采用紧定螺钉或销钉。
合金钢比碳钢有更好的力学性能和淬火性能。通常用于重载、高速的重要轴或有特殊要求的轴。
对于形状复杂、尺寸大的轴,球墨铸铁有成形容易,且价格低,吸振、耐磨,对应力敏感性小等优点。但可靠性差些。
三、轴设计的主要问题和一般步骤
1、轴设计的主要问题具有合理的结构和足够的承载能力是轴设计时必须解决的两个主要问题。
2、轴设计的一般步骤①确定许用应力;②估算最小直径、③轴的结构设计;④轴的强度校核计算。
第二节轴的结构设计
轴结构设计应遵循的一般原则:(1)轴和装在轴上的零件要有准确的工作位置;(2)轴上零件应便于拆卸和调整;(3)轴应具有良好的加工工艺性;(4)尽量减小应力集中;(5)受力合理,有利于节约材料,减轻轴的重量。
二、各段轴径和长度的确定
1、轴径的确定原则确定各段直径时应遵循如下原则:
1)有配合要求的轴段应取标准直径。
- 1、下载文档前请自行甄别文档内容的完整性,平台不提供额外的编辑、内容补充、找答案等附加服务。
- 2、"仅部分预览"的文档,不可在线预览部分如存在完整性等问题,可反馈申请退款(可完整预览的文档不适用该条件!)。
- 3、如文档侵犯您的权益,请联系客服反馈,我们会尽快为您处理(人工客服工作时间:9:00-18:30)。
目录
轴系部件的选择与设计 (1)
1.轴系设计的基本要求 (1)
(1)旋转精度、刚度、抗振性、热变形 (1)
(2)机床主轴传动齿轮空间布置比较 (1)
2.轴系(主轴)用轴承的类型与选择 (2)
(1)标准滚动轴承; (2)
(2)深沟球轴承; (2)
(3)双列向心短圆柱滚子轴承; (2)
(4)圆锥滚子轴承; (2)
(5)推力轴承。
(2)
3.提高轴系性能的措施 (5)
(1)提高轴系的旋转精度 (5)
(2)提高轴系组件的抗振性 (5)
轴系部件的选择与设计
1.轴系设计的基本要求
轴系由轴及安装在轴上的齿轮、带轮等传动部件组成,有主轴轴系和中间传动轴轴系。
轴系的主要作用是传递转矩及精确的回转运动,它直接承受外力(力矩)。
对于中间传动轴系一般要求不高。
而对于完成主要作用的主轴轴系的旋转精度、刚度、热变形及抗振性等的要求较高。
(1 )旋转精度、刚度、抗振性、热变形
旋转精度是指在装配之后,在无负载、低速旋转的条件下轴前端的径向跳动和轴向窜动量。
轴系的刚度反映了轴系组件抵抗静、动载荷变形的能力。
轴系的振动表现为受迫振动和自激振动两种形式。
其振动原因有轴系组件质量不匀引起
的动不平衡、轴的刚度及单向受力等;它们直接影响旋转精度和轴承寿命。
轴系的受热会使轴伸长或使轴系零件间隙发生变化,影响整个传动系统的传动精度、旋
转精度及位置精度。
又由于温度的上升会使润滑油的粘度发生变化,使滑动或滚动轴承的承载能力降低。
(2)机床主轴传动齿轮空间布置比较
机床主轴传动齿轮空间布置比较
机床主轴不仅受切削力还受传功齿轮的凰罔力(均可等效为辘心线上的屁向力}的作冃. 如採丄卧布豈■当犢功齿轮1和2的国周力总与作卑在轴端的切削力厂同向时、铀歸弯曲变形屋2二E ■込)较<N而丽釉離的支承力F弄暈大.技图b布置时,其骂与时反也釉3R变形坨W = 务[为最夫,晅前轴承的支承反力f 翠和.说计中賽综合考总这些因重的影响.
2.轴系(主轴)用轴承的类型与选择
(1 )标准滚动轴承;
(2)深沟球轴承;
(3)双列向心短圆柱滚子轴承;
(4)圆锥滚子轴承;
(5 )推力轴承。
双列向心短圆柱滚子轴承、
圆锥滚子轴承、双列推力球轴承图
1)配套应用例
: EH栉: iJU- .JM J - H >
上图为其配套应用实例,双列向心短圆柱滚子轴承的径向间隙调整,是先将螺母6松开、转动螺母1,拉主轴7向左推动轴承内圈,利用内圈胀大以消除间隙或预紧。
这种轴承只能承受径向载荷。
轴向载荷由双列推力球轴承2承受,用螺母1调整间隙。
轴向力的传递见图中箭头所示,轴向刚度较高。
这种推力轴承的制造精度已达B级,适用于各种精度的主轴轴系。
其预紧力和间隙大小调整用隔套3来实现。
外围开有油槽和油孔4,以利于润滑油进入轴承。
2)微型滚动轴承
3)精密分度头主轴系统
I i -rnEHii*; a t
上图为一精密分度头主轴系统。
它采用的是密珠轴承,主轴由止推密珠轴承2、4和径向密珠轴承1、3组成。
这种轴承所用滚珠数量多且接近于多头螺旋排列。
由于密集的钢珠有误差平均效应,减小了局部误差对主轴轴心位置的影响,故主轴回转精度有所提高;每个
钢珠公转时沿着自己的滚道滚动而不相重复,减小了滚道的磨损,主轴回转精度可长期保持。
实践证明,提高钢珠的密集度有利于主轴回转精度的提高,但过多地增加钢珠会增大摩擦力矩。
因此,应在保证主轴运转灵活的前提下,尽量增多钢珠数量。
图b为推力密珠轴承保持
架孔分布情况,图c为径向密珠轴承保持架孔的分布情况。
4 )液体静压轴承工作原理
液体静压轴承工作原理
1、2、3、4-油腔;5-金属薄膜;6-圆盒;7-回油槽;8-轴套
静压轴承是利田外韶供油(气)装置将具有一定压尢的液(5)体通过油OfLffi人轴誉油(气烂.椅轴淳起而形成压力油(气潭,以承受嶷荷-其承戟能力写滑动裏面的绥逮度无关,故
厂泛应用于低、中迄大載荷,高清度的机親它具有别度大、精度高、抗振性好、摩麋阻力屮等优点.上閤为浪際静压轴弟工作原理圈'
開中油腔1育轴套&内面r的凹入部分;包圉油膛时四周称沖封油面I封油面与运胡表面枸成的闱隙称为曲狽厚度.叛r慕辄需要超补偿-补偿克星的机构称为4卜偿兀件,也称节箭
器,如團b所示.压力躍节流器第一次节流石流入油腔,又经过封油面第二诙节流所从轴向歸面
湘周向㈣袖糟?颍入油箱.
在不的至量.且皿牛P張爲的嚴組押蓦(即1. 53.4的压力相割即鮎・衍"“形= */*主樹■一宗油®無幵•釉■岸度为尙.・中右勻端拿申心It合。
苹瑚轴的评向亂荷F”【辅的畫■[柞闿时,o移至6.也移曲“善十油晚伍力秋址屮克忧血脏1的何廉塔丸展敲阻船』K小.■豐压力兀徘赴邀翌2却扣应.抽腔Md圧力跑尊u苦帖展L、2曲釉压愛代前产生曲庄力差皑精
尼沖a = 为犀吓科胆有戎承氧
面枳,世囚牛袖腔面段相部).主抽便赴于牺的平存荷■,即轴向下忖科崔小的雨高,绸远小干巾I WJ9X A和射
仍秋处亦藏体克承狀25下戏转,
因为就腔每牛釉胆的itlt Q垃辱予潦竪节沈I!的fltlt Q^.RU Q K-Q.-Q O A节flE幕进口翦的垂秋油压用为鲁抽腔的權蹴离
Q- p」R产2广2%林槁畫匪力为
* 八
联■ 1厂和瓦
时干袖腔W;讣订佥萤巧FT瓷丙?
如累岡亍节流爲的權鼠悬億■艮柄等.则P*irA^?仪产IV話瓦"只因为油腔阿甜敲阴Ktj>恐一枚着腔压力九〉曲“半节S[舒穢龜同时发生变业.即Rv丈眄I •这时的p a>p tli向上的推力很大'輛的也棒即吐!6小.甚至为
零•即團厦峪向无甥大。
节d輕的作用是■节支韋屮备前曲的墜力,以适应备自的于同戟柿;使柚豪具昔一定的刖艮•以适应軌荷的住代“由就可知,it暫节渡1T權量载圻價不繼#隹来匚
5 )磁悬浮轴承工作原理i
磁悬浮轴承是利用磁场力将轴无机械摩擦、无润滑地悬浮在空间的一种新型轴承。
其工作原理如下图所示。
径向磁悬浮轴承由转子(转动部件)6和定子(固定部件)5两部分组成。
定子部分装上电磁体,保持转子悬浮在磁场中。
转子转动时,由位移传感器4检测转子的偏心,并通过反馈与基准信号1(转子的理想位置)进行比较,调节器2根据偏差信号进行调节,并把调节信号送到功率放大器3以改变电磁体(定子)的电流,从而改变磁悬浮力的大小,使转子恢复到理想位置。
径向磁悬浮轴承的转轴(如主轴)一般要配备辅助轴承,工作时辅助轴承不与转轴接触,当断电或磁悬浮失控时能托住高速旋转的转轴,起到完全保护作用。
辅助轴承与转子之间的
间隙一般等于转子与电磁体气隙的一半。
轴向悬浮轴承的工作原理与径向磁悬浮轴承相同。
磁悬浮轴承工作原理
1—信号输入;2—调节器;3—功率放大器;4—位移传感器;5—定子;6—转子
3.提高轴系性能的措施
(1)提高轴系的旋转精度
轴承(如主轴)的旋转精度中的径向跳动主要由
1)被测表面的几何形状误差;
2)被测表面对旋转轴线的偏心;
3)旋转轴线在旋转过程中的径向漂移。
等因素引起。
轴系轴端的轴向窜动主要由
1)被测端面的几何形状误差;
2)被测端面对轴心线的不垂直度;
3)旋转轴线的轴向窜动。
等三项误差引起。
提高其旋转精度的主要措施有:
1)提高轴颈与架体(或箱体)支承的加工精度;
2)用选配法提高轴承装配与预紧精度;
3)轴系组件装配后对输出端轴的外径、端面及内孔通过互为基准进行精加工。
(2 )提高轴系组件的抗振性
轴系组件有受迫振动和自激振动,前者是由轴系组件的不平衡、齿轮及带轮质量分布不
均匀以及负载变化引起的,后者是由传动系统本身的失稳引起的。
提高其抗振性的主要措施有:
1)提高轴系组件的固有振动频率、刚度和阻尼,通过计算或试验来预测其固有振动频率,当阻尼很小时,应使其固有振动频率远离受迫振动频率,以防止共振。
一般讲,刚度越高、阻尼越大,则激起的振幅越小。
2)消除或减少受迫振动振源的干扰作用。
构成轴系的主要零部件均应进行静态和动态平衡,选用传动平稳的传动件、对轴承进行合理预紧等。
3)采用吸振、隔振和消振装置。
注:摘自张建民《机电一体化系统设计》第四版。