宝钢炼钢工艺和设备-详细
宝钢高炉炼铁工艺介绍2016年
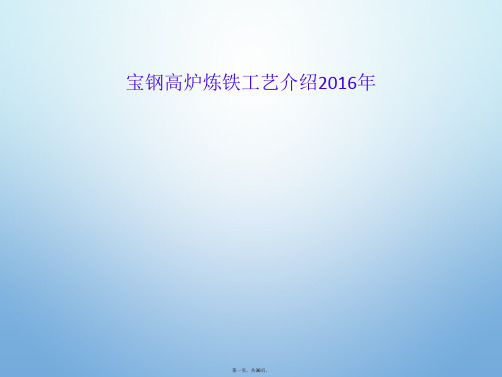
8、液压系统。
第二十三页,共36页。
2.6高炉炉前工艺流程
2、高炉工艺流程介绍
第二十四页,共36页。
2.7高炉炉渣处理流程
2、高炉工艺流程介绍
渣处理方式
水渣:熔渣经过冷却水急冷,产生细碎颗粒状水渣,用于制作水泥。
干渣:熔渣放入坑中,洒水冷却,冷却后挖掘清运出厂,用于铺路。
第十三页,共36页。
2、高炉工艺流程介绍
2.3高炉热风炉流程
宝钢高炉采用新日铁外燃式风炉,每座高炉配有4座热风炉,采用三孔陶瓷燃烧器,最高风温 :1310度,送风最高压力:0.51Mpa,拱顶温度:1450度,废气温度:350度。
拱顶连接管采用弹性结构。使用了混风室。
第十四页,共36页。
2.4高炉煤气清洗流程
4、均:粒度均匀
5、小:粒度小 6、稳:物理性能和化学成分稳定
7、少:杂志少
8、好:冶金性能好
第三十三页,共36页。
4、高炉操作基本知识
高炉操业管理
1、透气性管理 与炉型、原燃料强度粒度、气流分布、炉况等有关
2、炉温管理 与铁份、焦炭灰分、热量水平、顺行、冷却设备有无漏水等有关
3、操作炉型管理 与气流分布、热负荷和冷却强度等有关
水渣处理工艺
LASA法:粗粒分离槽与脱水槽脱水;电消耗大,管道易磨损,占地大。
INBA法:转鼓与成品槽脱水,水电消耗少,管道阀门寿命长,占地少。 新INBA法:较INBA法增加了蒸汽冷却装置,环保,耗电增多。
第二十五页,共36页。
2.7高炉炉渣处理流程
2、高炉工艺流程介绍
第二十六页,共36页。
2.7高炉炉渣处理流程
环缝洗涤塔:粉尘与水滴碰撞凝聚,同时,蒸汽促使粉尘集合。 干法除尘:通过滤袋将煤气中的粉尘除去并收集起来,具有除尘效率高,节约水的优点,同 时能提高TRT发电量。
宝钢炼焦工艺与设备

主要产品:1、荒煤气,可精制得到煤气和 焦油、粗苯等化产品;2、焦炭。
用户:煤气送往能中,供炼铁、热轧、冷 轧等处使用;焦油粗苯供化产工序深加工;焦 炭主要供高炉和烧结使用。
宝钢炼焦用煤一般有焦煤、肥煤 、气煤、瘦 煤和1/3焦煤及少量的无烟煤。配煤工艺是带预破 碎的分组粉碎工艺,凡是气煤、瘦煤以及未洗选的 原煤需经过预粉碎、各组煤的粉碎细度采用 78/85±2% (< 3mm)。
目录
一、宝钢炼焦生产规模 二、宝钢炼焦工艺流程 三、宝钢炼焦工艺设备概况 四、宝钢炼焦生产实绩
概况
炼焦工业是煤化工的一个重要组成部分,它 是以煤为原料,经过高温干馏生产焦炭,同时获 得煤气、煤焦油,并回收其他化工产品的一种工 业。
炼焦工业的主要产品是焦炭和煤气,其中焦 炭是冶金工业中的主要燃料,在焦化工业中有 90%的焦炭都是用来高炉炼铁的。焦炭在高炉中 既是燃料、还原剂及增碳剂,而且还起着贯穿炉 身上下的疏松骨架作用。
四期焦炉投产后、一期焦炉停产前的2012年, 焦炭产量创历史峰值,达573.69万吨。2014年计划 产量485万吨,实绩预计可达486.5万吨。
新建一期4座50孔7米焦炉计划于2015年4月30日 投产,届时二期焦炉将停止运营。
新一期焦炉稳定生产后,焦炭设计产能为553万 吨/年(上海市最高产量要求)。
处理能力:二期 40 t/h,三期 61 t/h(干基) 设备数量:二期 4台,三期 2台 成型辊尺寸:φ1400×1400 mm 回 转 数:二期 10.9 rpm(常用),12.1rpm(最大)
三期 9.4 rpm(常用),11.1rpm(最大) 辊 速:0.69 m/s(一般),0.81m/s(最高) 球碗容量:二期 约30ml,三期 约40ml(间隙5mm时) 球碗个数:二期 90个/列×24列=2160个
宝钢工程RH精炼炉设备与工艺技术介绍

•宝钢工程RH工艺特点及先进性(续)
多功能顶枪喷吹燃气加热功能,同时可 以保持高槽温,防止冷钢形成;
多功能顶枪供氧与铝粉剂放热反应,实 现钢水化学升温;
采用顶枪的提升,去除真空槽槽壁粘结 的冷钢;
强合金化能力; 吹氩喂丝功能;
•工艺特点及先进性综述
分类
功能 脱 氢
脱碳
加热
自然 强制 二次 化学 去冷 脱碳 脱碳 燃烧 加热 钢
RH简介
• 可实现脱气、脱氧、脱碳、合金化、及调整钢水成 分、调整钢水温度(升温)、去除杂净化钢液、喷 粉脱硫等多重功能。
• 具有大的钢液循环速度,缩短处理时间。 • 具有与炼钢、连铸之间较高的配合率,适应灵活多
变的生产。 • 通过先进的计算机控制系统,实现电气、仪表、计
算机的三电一体化。实现生产计划和生产命令接受 处理、以及与基础自动化通讯、冶金数学模型处理 及状态跟踪等功能。
一.采用转炉-LF/RH-连铸的工艺搭配。 二.采用新型的多功能顶枪,实现吹氧脱碳,化学处理和加 热升温等工艺要求。 三.采用大抽气量的真空泵,为提高抽气速率可在末级并 联水环泵。 四.开发了热弯管技术,提高处理工艺效果和热效率 五.浸渍管采用新型的大规格,大环流量设计,提高钢水循 环速度和工艺效果 六.合理分配环流管的根数,层数和规格,提高钢水循环工 艺效果 七.合理设定合金加料口高度和槽体高度的设计.
• 发展趋势
RH真空精炼设备正在向功能多样化、设备大型化、 操作自动化及可靠连续化方向发展,成为生产超低碳钢、 硅钢、高合金钢等高附加值钢种的主要手段。可以说, 现代工业所需要的几乎所有的超纯、超低C、S钢种,均 可以用RH工艺设备来生产。
BSEE-RH充分考虑了RH精炼中各项先进的设备技术和 工艺技术,满足现代产品对高质量和高附加值的要求。
宝钢炼钢厂简介

04
宝钢炼钢厂的技术创新与研 发实力
宝钢炼钢厂的技术创新与研发实力
• 宝钢炼钢厂作为中国钢铁行业的领军企业之一,拥有悠久的历史和丰富的经验 。该厂具备了较强的技术创新与研发实力,不断推出新的技术和产品,推动了 中国钢铁行业的发展。
05
宝钢炼钢厂的未来发展与展 望
产能扩张与产品升级
产能扩张
宝钢炼钢厂计划在未来几年内扩 大产能,以满足国内外市场对钢 铁产品的需求。
流程。
宝钢炼钢厂的组织架构与主要部门
01
02
03
轧钢车间是另一个重要的生产 部门,主要负责将铸坯加工成 各种规格的钢材产品。
质量检验部门负责对生产过程 中的产品质量进行检测和控制 ,确保产品符合客户要求。
研发部门致力于研发新技术和 新工艺,提高产品质量和降低 成本。
宝钢炼钢厂的组织架构与主要部门
产品升级
为提高产品质量和附加值,宝钢 炼钢厂将加大投入,研发新型钢 铁产品,拓展高端市场。
技术创新与绿色发展
技术创新
通过引进和自主研发新技术,宝钢炼 钢厂将提高生产效率和能源利用效率 ,降低生产成本。
绿色发展
宝钢炼钢厂将积极推进环保技术的应 用,减少污染物排放,实现可持续发 展。
国际竞争力与全球影响力
03
近年来,宝钢炼钢厂不断进行技术升级和产业 转型,提高了产品质量和竞争力。
宝钢炼钢厂的组织架构与主要部门
01
宝钢炼钢厂的组织架构 包括董事会、监事会和 管理层等,实行总经理
负责制。
02
主要部门包括炼钢车间 、轧钢车间、质量检验 部门、研发部门、销售 部门和行政部门等。
03
炼钢车间是宝钢炼钢厂 的核心生产部门,主要 负责炼钢和铸坯等工艺
宝钢工艺
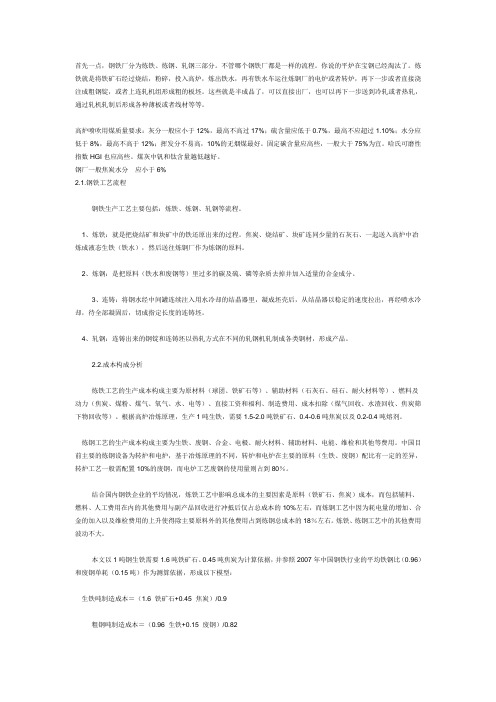
首先一点,钢铁厂分为炼铁、炼钢、轧钢三部分。
不管哪个钢铁厂都是一样的流程。
你说的平炉在宝钢已经淘汰了。
炼铁就是将铁矿石经过烧结,粉碎,投入高炉,炼出铁水,再有铁水车运往炼钢厂的电炉或者转炉,再下一步或者直接浇注成粗钢锭,或者上连轧机组形成粗的板坯。
这些就是半成品了,可以直接出厂,也可以再下一步送到冷轧或者热轧,通过轧机轧制后形成各种薄板或者线材等等。
高炉喷吹用煤质量要求:灰分一般应小于12%,最高不高过17%;硫含量应低于0.7%,最高不应超过1.10%;水分应低于8%,最高不高于12%;挥发分不易高,10%的无烟煤最好。
固定碳含量应高些,一般大于75%为宜。
哈氏可磨性指数HGI也应高些。
煤灰中钒和钛含量越低越好。
钢厂一般焦炭水分应小于6%2.1.钢铁工艺流程钢铁生产工艺主要包括:炼铁、炼钢、轧钢等流程。
1、炼铁:就是把烧结矿和块矿中的铁还原出来的过程。
焦炭、烧结矿、块矿连同少量的石灰石、一起送入高炉中冶炼成液态生铁(铁水),然后送往炼钢厂作为炼钢的原料。
2、炼钢:是把原料(铁水和废钢等)里过多的碳及硫、磷等杂质去掉并加入适量的合金成分。
3、连铸:将钢水经中间罐连续注入用水冷却的结晶器里,凝成坯壳后,从结晶器以稳定的速度拉出,再经喷水冷却,待全部凝固后,切成指定长度的连铸坯。
4、轧钢:连铸出来的钢锭和连铸坯以热轧方式在不同的轧钢机轧制成各类钢材,形成产品。
2.2.成本构成分析炼铁工艺的生产成本构成主要为原材料(球团、铁矿石等)、辅助材料(石灰石、硅石、耐火材料等)、燃料及动力(焦炭、煤粉、煤气、氧气、水、电等)、直接工资和福利、制造费用、成本扣除(煤气回收、水渣回收、焦炭筛下物回收等)。
根据高炉冶炼原理,生产1吨生铁,需要1.5-2.0吨铁矿石、0.4-0.6吨焦炭以及0.2-0.4吨熔剂。
炼钢工艺的生产成本构成主要为生铁、废钢、合金、电极、耐火材料、辅助材料、电能、维检和其他等费用。
中国目前主要的炼钢设备为转炉和电炉,基于冶炼原理的不同,转炉和电炉在主要的原料(生铁、废钢)配比有一定的差异,转炉工艺一般需配置10%的废钢,而电炉工艺废钢的使用量则占到80%。
宝钢炼钢工艺和设备_详细

二、铁水预处理
▪ 电石粉的特点:
▪ (1)分解出的钙离子与[S]有极强的亲和力,因此 CaC2有很强的脱硫能力,耗量少,渣量也较少。
▪ (2)生成物CaS熔点高,形成固体渣,防止回硫, 扒渣容易,对耐材侵蚀较轻。
▪ (3)脱硫生成的碳除饱和于铁水外,其余以石墨态 析出。同时还有少量CO、C2H2气体,以及少量电石 粉和石灰粉会污染环境,因此必须设置除尘设备。
升降装置由升降小车、横移台车、升降卷扬装 置及升降轨道组成。
三、转炉
(3)副枪装置 为了提高吹炼终点控制的命中率,在吹炼过程
中获得钢水温度、成分、炉内造渣情况等信息。 可装上不同的探头达到不同的检测目的,枪体采 用水冷,使用寿命较长,运行安全可靠,测定速 度快、精度高。副枪装置由旋转框架及其驱动装 置、副枪及升降小车、升降小车驱动装置、探头 供给及装着装置、探头提取及试样切断装置、刮 渣装置及副枪孔密封装置、副枪枪体矫直装置、 探头回收溜槽等。
▪ (4)电石粉极易吸潮劣化,在大气下与水分接触迅 速发生反应,生成C2H2(乙炔)气体易爆,应采取 安全措施。
▪ (5)电石粉价格昂贵。
二、铁水预处理
▪ 石灰粉的特点: ▪ (1)当铁水中的[Si]氧化后,生成Ca2SiO4和SiO2,
相应消耗有效CaO,降低了脱硫效率。 ▪ (2)脱硫渣为固体渣,对耐材侵蚀较轻微,扒渣方
▪ 宝钢现有的炉外精炼装置有:RH-OB(1#RH)、 RH-KTB(3#RH)、RH-MFB(2#RH)、VD、 CAS-OB、KIP、IR、UT、LF炉和喂丝等。
四、炉外精炼
(1)RH真空脱气的基本原理和工艺 为了减少钢中的有害气体和夹杂,净化钢水,提高钢
材的内在质量,改善机械性能,国内外各大钢厂均采用了 各种脱气方法,其中RH真空循环脱气法生产能力大,脱 气效果好,能使用于高生产率的氧气顶吹转炉。
宝钢股份高炉生产工艺与设备-yj上课讲义

小钟
溜槽 探尺
导料板
大钟
探尺
串罐式炉顶装料流程
Z-401BC
上部闸阀
上料罐
一次排压阀
二次排压阀
GAS N2
消音器
上部密封阀
一均
二均
Z-401BC驱动马达
旋转溜槽
FCG阀 下部密封阀
探尺
并罐式炉顶装料系统
并罐式炉顶装料系统 优点: 系统上料能力较强,具有 互为备份功能;
缺点: 炉料粒度偏析和轨迹偏析 较大,不易消除。
W .G
CB
AB
BB
H
CB
AB
BB
H
CB
AB
BB
H
CB
AB
BB
H
B
M
B
M
B
M
B
M
4HS
3HS
2HS
1HS
H
H
H
H
SII WS W E SI C SII WS W E SI C SII WS W E SI C SII WS W E SI C
高炉炉顶装料流程
项 目 单位 1BF 2BF 3BF
上部漏斗 m3 40 80 80
下料罐 m3 80 80 80
溜槽长度 mm
4500 4500
大钟直径 mm 7300
炉顶压力 MPa 0.25 0.25 0.25
探尺数量 把 4 3 3
Z-101BC
闸阀
No 1 No 2 No 3 No 4
No 1 No 2 No 3 No 4
原料工序是我国钢铁企业第一个现代化的大型原料处理厂,对全公司的 原燃料进行集中管理,以精料为宗旨向全公司各用户供料。具有以下特点: 大型化:料场占地面积1.02平方公里;年作业总量1亿吨。 现代化:计算机、PLC高效率集中分级控制,并实现三电一体化。 先进性:装备良好的环境保护设备;混匀矿堆积采用先进的数模智能控制。
宝钢炼钢工艺和设备详细

宝钢炼钢工艺和设备详细宝钢集团有限公司是中国最大的钢铁企业之一,拥有先进的炼钢工艺和设备。
炼钢是将生铁或废钢通过冶炼和精炼等工艺,制成合格的钢材的过程。
宝钢炼钢工艺和设备的先进性,直接影响到钢材的质量和生产效率。
下面我们来详细了解一下宝钢的炼钢工艺和设备。
首先是炼钢工艺。
宝钢采用了先进的转炉炼钢工艺,主要包括废钢预处理、炼钢冶炼、精炼和连铸等环节。
在废钢预处理环节,宝钢采用了先进的废钢分选技术,将不同种类的废钢进行分类处理,以保证炼钢过程中的原料质量。
在炼钢冶炼环节,宝钢主要采用转炉冶炼工艺,通过高温燃烧和氧气吹炼,将生铁或废钢中的杂质和不良元素去除,得到高质量的熔铁。
在精炼环节,宝钢采用了LF精炼炉和VD真空脱气设备,通过精确控制温度和气氛,进一步提高钢材的纯度和均匀性。
最后,在连铸环节,宝钢采用了连铸机组,将熔化的钢水连续浇铸成坯料,为后续的轧制和成品加工提供原料。
其次是炼钢设备。
宝钢拥有一批先进的炼钢设备,包括转炉、精炼炉、连铸机组等。
其中,转炉是炼钢的核心设备,宝钢拥有多台不同规格的转炉,能够满足不同种类钢材的生产需求。
精炼炉是提高钢材质量的关键设备,宝钢引进了国际先进的LF和VD设备,通过真空脱气和精确的合金添加,提高了钢材的纯度和均匀性。
连铸机组是将熔化的钢水浇铸成坯料的设备,宝钢的连铸机组采用了先进的直接结晶技术,能够生产高质量的连铸坯料。
除了上述的主要工艺和设备外,宝钢还在炼钢过程中引入了先进的自动化控制系统和在线检测设备,以确保生产过程的稳定性和钢材质量的可控性。
同时,宝钢还注重节能减排,采用了高效的热能回收设备和环保设施,实现了炼钢过程的清洁生产。
总的来说,宝钢的炼钢工艺和设备处于国际领先水平,能够满足不同种类钢材的生产需求,保证钢材质量和生产效率。
未来,宝钢还将继续引进先进的炼钢技术和设备,不断提升自身的竞争力和可持续发展能力。
宝钢的生产管理系统介绍(完整版)
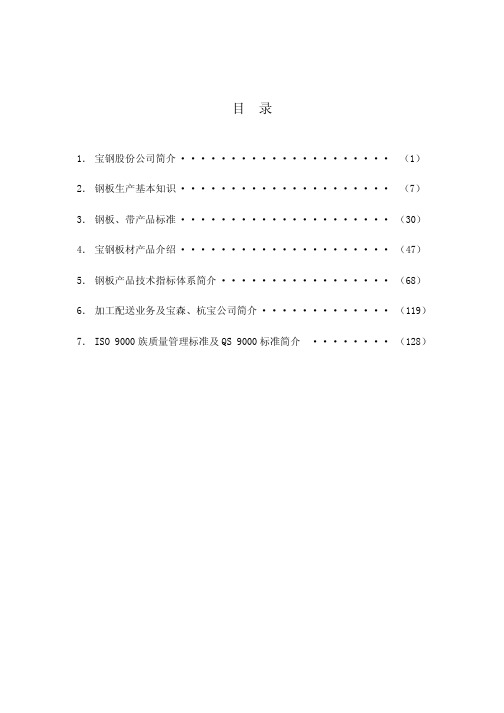
宝钢的质量管理与质量保证体系于 1994 年通过了由 BSI-QA(英国标准协 会质量保证部)进行的 ISO 9001-1994 认证,成为中国领先获得 ISO 9000 系 列标准认证的大型钢铁联合企业之一。1999 年又通过了美国三大汽车公司(通 用、福特、克莱斯勒)的 QS 9000 标准认证,进一步提升了宝钢的质量保证体 系层次。
电镀锌机组从奥地利引进,采用鲁斯纳重力法,钝化采用辊涂,这样锌层 及钝化层更均勾。机组电镀槽后采用全封闭保证了电镀锌卷表面的清洁,可生 产适于作汽车零件的厚镀层电镀锌及锌镍合金化产品,卷宽可达 1830mm。
热镀锌机组从德国西马克引进,可生产无铅零锌花及锌铁合金化产品,先 进的镀层厚度闭环自动控制系统保证了镀锌层重量均匀,入口段设置高级强化
2030 冷轧主体设备分别从德国、日本和美国成套引进,包括酸洗机组、 2030mm 五机架全连续冷轧机组、罩式退火炉、单机架四辊式平整机组、六段立 式连续退火机组(CAPL)、横切、纵切及重卷机组、连续热镀锌机组、连续电镀 锌机组、彩色涂层机组等。
先进的生产技术有:采用了盐酸浅槽酸洗,可有效地清除热轧来料表面氧 化铁皮;生产过程采用计算机控制;装有厚度自动控制 AGC 系统,确保轧后厚 度精度;轧机装有最新的板型检测调节装置和 CVC 轧辊凸度连续可变的调节技 术,保证了板型平直;计算机控制的罩式退火炉可按不同钢种及堆垛方式分别 采用不同的退火曲线;CAPL 连续退火机组可一次完成脱脂、再结晶退火和平整 工艺,使冷轧板(卷)获得良好的力学性能。
炼钢主要工艺设备表
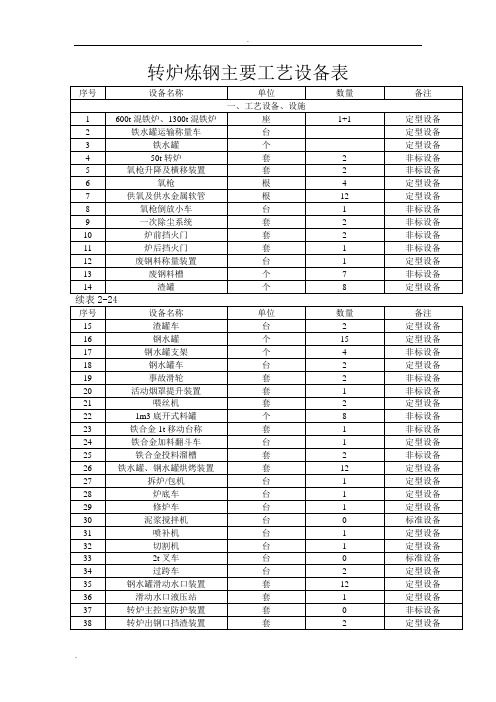
套
13
二冷喷水集管150x150
4
套
14
150 x150引锭头装配
2
套
表2-29 板坯连铸机主要设备表
序号
设备名称
数量
单位
备注
一
在线设备
1
操作平台
1
套
2
大包回转台(含加盖装置)
1
套
3
中间包
2
个
4
中间包盖
2
个
5
塞棒机构
4
个
6
浸入式水口夹持装置
4
套
7
中间包车
2
台
8
中间包预热站
2
套
9
浸入式水口烘烤装置
1
套
1
非标设备
21
喂丝机
套
2
定型设备
22
1m3底开式料罐
个
8
非标设备
23
铁合金1t移动台称
套
1
非标设备
24
铁合金加料翻斗车
台
1
定型设备
25
铁合金投料溜槽
套
2
非标设备
26
铁水罐、钢水罐烘烤装置
套
12
定型设备
27
拆炉/包机
台
1
定型设备
28
炉底车
台
1
定型设备
29
修炉车
台
1
定型设备
30
泥浆搅拌机
台
0
标准设备
31
序号
设备名称
数量
单位
备注
22
150×150引锭头装配
5
南通宝钢热轧产线工艺设备

南通宝钢热轧产线工艺设备基本情况1 总体情况说明1.1 生产规模热轧产线为生产规模年产50万t低合金钢棒材,考虑控制冷却技术及小规格切分轧制技术。
φ10为三切分工艺,φ12、φ14为两切分工艺,φ16为两切分和单线两种工艺,其余规格为单线轧制工艺。
1.2产品方案序号品种钢种代表规格年产量比例钢号(mm)(万吨) (%)1螺纹钢低合金钢HRB335、HRB335E、HRB400、HRB400E、HRB500、HRB500Eφ10~φ14 11.25 22.52 φ16~φ18 12 243 φ20~φ25 19.5 394 φ28~φ365 105 φ40 2.25 4.5合计50 100.00 注:连铸坯规格为:150mm×150mm×8000mm,加热炉能力要求不低于100t/h。
1.3生产工艺流程1.3.1 车间生产工艺流程框图1.3.2 生产工艺过程简述连铸 吊运至上料台辊道输送 推钢入炉 加 热出 炉(不合格坯剔除)粗 轧切 头中 轧控制冷却 切 头倍尺分段 冷床冷却 冷剪剪切定尺移送、检查、计数打 捆称重标志 收 集 入 库精 轧合格的连铸钢坯由炼钢连铸车间用电动平车运输至本车间,然后用吊车吊运至上料台架,坯料由上料台架推入坯料输送辊道,并输送到加热炉入炉端后由推钢机将其从加热炉的端部推到推钢式加热炉中加热。
根据钢种的要求,钢坯在加热炉内加热到1030~1130℃后,按轧制节奏由出钢机从加热炉侧面单根推出炉。
如果钢坯有缺陷,由剔除装置从出炉辊道上剔除。
出炉后的热坯,经辊道输送,钢坯开始进入连轧机组轧制。
钢坯首先在粗轧机组轧制6个道次,然后轧件由1#飞剪切头后,进入中轧机组轧制,轧成工艺规程要求的断面。
出中轧机组的轧件,再由2#飞剪切去头尾,继续进入精轧机组轧成最终要求的成品断面尺寸。
当轧制过程出现事故时,1#、2#飞剪手动启动,进行连续剪切,将轧件碎断,防止事故进一步扩大。
炼钢技术设备与工艺

炼钢工艺的未来发展方向:包括开发新的炼钢技术、优化现有工艺、提高自动化和智能 化水平等方面。 炼钢工艺的应用前景:随着科技的不断发展,炼钢工艺的应用前景非常广阔,未来将会 有更多的领域和行业应用炼钢工艺。
炼钢技术设备与工艺的结合应用
优缺点:电弧炉 炼钢具有生产效 率高、产品质量 好等优点,但也 存在耗能大、成 本高等缺点。
炉外精炼工艺
炉外精炼的必要性 炉外精炼的设备与工艺流程 炉外精炼的原理与操作要点 炉外精炼的优缺点及发展趋势
连铸工艺
连铸工艺的定义和原理
连铸工艺的优点和局限性
添加标题
添加标题
连铸工艺的流程和设备
添加标题
产品质量与稳定性:炼钢工艺需要生产高质量的钢材,以满足不同领域的需求。同 时,由于炼钢工艺的复杂性和不确定性,产品质量和稳定性也面临挑战。
生产效率与成本控制:炼钢工艺需要提高生产效率,降低成本,以提高企业的竞争 力。
技术创新与人才培养:随着科技的不断发展,炼钢工艺需要不断创新,提高技术水 平。同时,也需要培养高素质的人才,以满足炼钢工艺的需求。
提高炼钢技术设备与工艺的对策建议
加大技术研发力度,提高设备与工艺水平 加强人才培养,提高操作技能和素质 优化生产流程,降低能耗和排放 加强设备维护和保养,确保稳定运行 推广先进技术和经验,促进产业升级
加强技术创新和人才培养的措施
加大技术研发力度,提高炼钢 技术设备的性能和效率
加强人才培养,提高技术人员 的专业素质和创新能力
推动产学研合作,促进技术创 新和人才培养的有机结合
建立完善的技术创新和人才培 养机制,为炼钢技术的发展提 供有力保障
炼钢主要设备及其工艺参数

主要设备及其工艺参数混铁炉设备主要工艺参数公称容量: G 600t炉容铁量:G 526t熔池最大深度: h 3.122m炉体外形尺寸: L×B×H9545㎜×7897㎜×7520㎜炉壳重量: 113.475 t炉衬重量: 349t最大操作角度: +24.5°炉体向前倾动极限角度: + 47°炉体向后倾动极限角度:-5°炉顶燃烧温度: 1200℃铁水出炉温度: 1250℃转炉设备主要工艺参数:2.1 转炉炉体转炉公称容量: 60t炉体总高: 7000㎜炉壳高度: 6800㎜炉壳外径: 4700㎜炉壳内径: 4610㎜炉壳壁厚: 45㎜炉壳高度/炉壳外径: H/D=6800/4700=1.45炉膛内高/炉膛直径: H/D=6652/3480=1.91有效容积: 47 m3炉容比: V/t=0.78熔池深度: 900㎜炉口直径:Ф1440㎜出钢口直径:Ф125㎜出钢口与水平夹角: 10°炉衬厚度: 500㎜炉壳总重: 71000㎏炉衬总重: 153t(包括135.7t镁碳砖,17.3烧镁砖) 转炉净环冷却水:总给水量:70t/h 水压p≥0.3MPa T≤60℃2.2 托圈及倾动部分托圈结构:水冷箱型;托圈与炉壳间隙:100㎜,耳轴部位50㎜电机: 45KW×4台最大操作力矩:~1000N·m倾动转速: 0.1-1.22r/min倾动角度: ±360 °倾动减速机比:一次:98.821 二次:8.1176额定制动力矩: 1000N·m×42.3 氧枪系统a. 氧枪系统:氧枪总长度: 17.730m喷头:四孔拉瓦尔型枪直径Ф219㎜喉口Ф30.5㎜出口Ф39.5㎜马赫数 M=1.95 α= 11°50´~12°三层同心套管:内:Ф133㎜×5㎜中:Ф180㎜×5㎜外:Ф219㎜×7㎜供水压力>1.2MPa,进水温度≤35℃,出水温度≤50℃,供水量≥100t/h供氧压力: 0.7~0.9MPa氧枪总重: 2030㎏(包括枪内水量480㎏)b.提升机构提升能力: 55KW升降速度: V快=40m/min V慢=3.5m/min升降行程:工作行程:13900㎜c.横移装置:横移速度: 4m/min横移行程: 2500㎜连铸机设备主要设备工艺参数连铸机台数: 3台机型:2#机:四机四流R8m全弧形方坯连铸机3#机:五机五流R7m矩坯连铸机4#机:三机三流R6.5m直弧形板坯连铸机铸机流间距: 1.25m、 1.4m、 3.2m铸流断面: 2#机: 150×180 150×2203#机: 150×260 150×320 150×3304#机: 150×(330~650)中间包容量: 2#机: 18t 3#机:20t 4#机:25t引锭杆型式: 2#、3#机:钢性引锭杆 4#机:柔性引锭杆钢包转台:a) 钢包最大(单臂)承重:2#连铸机100t,3#连铸机90t,4#连铸机100tb) 钢包转台中心回转半径: 3.5 mc) 钢包回转速度: 1转/分中间包车:a) 行走速度: 2.9~13 m/minb)中间包车轨矩: 2#、3# 5670㎜ 4#6300㎜c)车长: 2#7600 ㎜、3#9200㎜、4#9800㎜结晶器振动装置:a) 型式:四连杆仿弧b) 振幅: 4~8㎜c)振动频率: 0~200次/min拉矫机:a) 型式: 2#、3#机双驱动五辊拉矫机4#机 7组拉矫机,4点矫直b) 辊子开口度: 2#、3#机最小106㎜,最大480㎜4#机 150㎜切割机:a) 型式:火焰切割b) 工作行程: 2#、3#机 2.1m,4#机4.65mc)切割速度: 0.3~0.4m/min4、 60t钢包尺寸包壳:上口2640㎜,下口2300㎜,全高3350㎜打结好钢包:上口2200㎜,下口1880㎜,内高2850㎜常用原材料基本技术要求(一)基本检测1、原材料计量入炉铁水必须经吊车电子秤称量。
宝钢高炉炼铁工艺介绍ppt课件
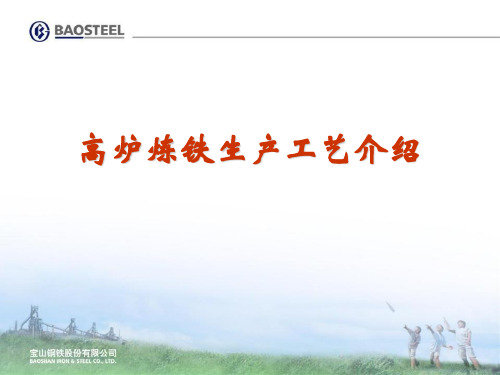
1 2 0 m /m i n
CC OO O
炉顶装料
BF
喷煤系统
重力 除尘器
热风
1VS 2VS
TRT
调压阀组
消音器
水封装置
冷风
HS HS
HS
HS
最高风温
1310℃
最高拱顶温度 1450℃
最高废气温度
350℃
混铁车
高炉脱硅装 置
2、高炉工艺流程介绍
高炉冶炼物流流程
原燃料 鼓风机
矿石 焦炭 辅料 煤粉
高温鼓风
1、行车、悬臂吊车等起重设备; 2、泥炮; 3、开口机; 4、移盖机; 5、摆动流嘴; 6、残铁开口机; 7、主沟、渣铁沟; 8、液压系统。
2.6高炉炉前工艺流程
2、高炉工艺流程介绍
2.7高炉炉渣处理流程
2、高炉工艺流程介绍
渣处理方式
水渣:熔渣经过冷却水急冷,产生细碎颗粒状水渣,用于制作水泥。 干渣:熔渣放入坑中,洒水冷却,冷却后挖掘清运出厂,用于铺路。
水渣处理工艺
LASA法:粗粒分离槽与脱水槽脱水;电消耗大,管道易磨损,占地大 。 INBA法:转鼓与成品槽脱水,水电消耗少,管道阀门寿命长,占地少。 新INBA法:较INBA法增加了蒸汽冷却装置,环保,耗电增多。
2.7高炉炉渣处理流程
压缩空气
烟囱
2、高炉工艺流程介绍
风扇
冷却 塔
炉渣
渣水槽
渣水沟
冲渣水
P 事故水
渣皮带
输送皮带
渣槽
转鼓
P
集水槽 温水槽
P
水渣
P
P
2.7高炉炉渣处理流程
2、高炉工艺流程介绍
2.8高炉除尘系统
宝钢1780热轧热轧工艺设备简介

➢ 新型主传动变频调速装置。(GTC) GTC为GTO的改进型,max6.0KV,6.0KA。功率
因素高(达1.0);响应速度快(max 60rad/s), 谐波少,效率高。 ➢ 主辅助传动全交流化,主传动采用凸极式交流同 步电动机;辅传动采用感应式交流变频调速电动 机和普通交流异步电动机。 ➢ 开放性的自动化控制系统。由三级自动化系统L1、 L2、L3组成。
15
560
7.8
0~1.4 齿形 2
14400
宝钢1780热轧热轧工艺设备简介
二、加热炉
• 加热炉区域机械设备 • 加热炉区域机械设备主要包括板坯称量辊道、连
接辊道(A7)与中间辊道(A9)、装炉辊道 (A8、A10)、返回辊道(B6)、连接辊道 (B7)、中间辊道(B9)、出炉辊道(B8、 B10)、装钢机、出钢机、炉底机械、进出料炉 门升降机构组成。
宝钢1780热轧热轧工艺设备简介
• 钢卷运输采用运输链和步进梁组合运输方式,快速运输链 将钢卷运输到步进梁运输机取卷位置,由步进梁运输机取 下钢卷向前继续运输,钢卷经称重、喷印,送到钢卷提升 机,钢卷提升机将钢卷托起到地面步进梁,根据下一工序 决定钢卷存放的跨间。对需要检查的钢卷由钢卷检查线的 钢卷小车取下,送到钢卷检查线进行检查和取样,检查后 的钢卷返回步进梁运输机。 热轧碳钢商品卷通过步进梁式运输机送到热轧商品钢卷跨 (D-F跨);热轧不锈钢商品卷和需平整分卷的碳钢钢 卷则送到不锈钢钢卷库和中间库存放(B-D跨);需平 整分卷的钢卷经冷却后,送到平整分卷机组进行处理,处 理后的钢卷进入平整分卷钢卷跨(A-B跨)。钢卷的运 输、冷却及堆放采用一卧到底的方式。 从板坯进入板坯库开始至成品发货为止,计算机通过物流 跟踪系统对板坯、轧件和钢卷进行全线跟踪,并确定其位 置,从而对相应设备进行设定和控制。
宝钢炼钢技术资料1

3
一炼钢连铸钢种组成(1986年初步设计)
钢种
碳素钢 其中深冲用钢 其中普碳钢 1 号 其中普碳钢 2 号
铸坯去向
热轧 热轧 热轧
年产量 (万吨/年)
224
154.8
生产比例 (%) 56
38.7
69.2
17.3
低铝铝镇静钢 (相当准沸腾钢)
热轧
68
17
结构钢
造船用钢 结构用钢 螺旋焊管钢 (API 标准)
2
宝钢一炼钢RH脱气处理计划
单位:万吨/年(基本设计审查后)
类品
油井管
锅炉钢管 条
高压锅炉管
钢 钢
普通钢管 外供钢管坯
计
焊条钢
方
钢轨钢
低合金钢
钢
普通碳素钢
计
锭 板
热轧普通钢 深冲用钢
低合金钢
用
螺旋焊管钢
钢
计
钢锭用钢水合计
普碳钢
Riband 钢
连
AL-K 钢
铸
低合金钢
造船用碳素钢低合金钢
坯
螺旋焊管钢
DX06
不烧成镁砖
永久层砖
F1
烧成镁砖
出钢口捣打料 炉底捣打料 接缝捣打料
B-MIXMA 相当品
R-4EU 相当 品
DOP2 相当品
重量 (吨)
~9 ~48 ~170 ~195 ~1.5 ~0.8 ~120 ~1.0 ~5 ~11.5
15
一炼钢氧枪升降及横移机构
氧枪升降及横移机构
1
提升荷重(常用最大)
5
一炼钢车间组成及厂房参数表
车间名称 号
1 主厂房 (1) 装料跨
跨度 (m)
- 1、下载文档前请自行甄别文档内容的完整性,平台不提供额外的编辑、内容补充、找答案等附加服务。
- 2、"仅部分预览"的文档,不可在线预览部分如存在完整性等问题,可反馈申请退款(可完整预览的文档不适用该条件!)。
- 3、如文档侵犯您的权益,请联系客服反馈,我们会尽快为您处理(人工客服工作时间:9:00-18:30)。
转炉操作室
转炉进废钢
转炉进铁水
三、转炉
▪ 3、炼钢原理:铁中的各种元素(也包括铁 本身)与氧结合(氧化),从铁中去除。 比铁与氧容易结合的元素,按照其结合能 力,从铁中去除。与氧结合比铁弱的元素, 则不能通过氧化去除。因此要在原料阶段 对不能氧化去除而又有害是元素进行处理 或不让其进入炉内。
三、转炉
(7)其他系统 转炉设备还包括蒸汽回收系统(锅炉汽包、
锅炉循环泵、蒸汽蓄热器等)、二次除尘 系统(除尘管道、风机、布袋除尘机等)、 挡渣棒投入装置、炉后测温取样装置等。
三、转炉
转炉顶底复吹LD—CB设施规格
项目
说明
项目
设置地点
转炉分厂
氧气流 量
公称能力×座数 300t×3座
氧气压 力
型式 炉底非对称
▪ 倾动装置主要由一次减速机、二次减 速机和扭力杆系统组成。
三、转炉
(2)氧枪及其升降装置 氧枪的工作环境恶劣--高温、多尘、易燃、
易爆,因此必须十分可靠。氧枪由三根钢管相套 而成,内管为氧气通道,内管与中管之间是冷却 水进水通道,中管与外管之间是冷却水的出水通 道。氧枪的端部是五孔拉瓦尔喷嘴,为脱氧铸铜 制作,具有良好的导热性。
三、转炉
▪ 4、炼钢反应 铁中主要元素:C、Si、Mn、P、S发生如下氧化 反应: [C]+[O]CO [Si]+2[O](SiO2) [Mn]+[O] (MnO) 2[P]+5[O] (p2O5) [FeS]+(CaO)(CaS)+(FeO)
“[ ]”表示铁水(或钢水)中溶解的 “( )”表示存在于渣中 “”表示变为气体逃掉
钢水的脱气就是溶解在钢中的气体向气相迁移的过程, 其步骤为: A、通过扩散,钢水中的气体原子逐渐迁移到钢水表面; B、原子由溶解状态转变为表面吸附状态; C、吸附在钢水表面的同类原子相互作用生产气体分子; D、吸附的气体分子进入气相后被真空泵吸走。
三、转炉
OG系统计算机控制画面
三、转炉
OG的主要设计指标:
▪ 工艺条件:炉容量300t ▪ 铁水比:89% ▪ 吹炼时间:16min ▪ 冶炼周期:36min,吹氧流量:70000Nm3/h,矿石:
45kg/t.s ▪ 烟尘排放浓度:≤100mg/Nm3 ▪ 煤气回收量:50~60Nm3/t.s ▪ CO浓度:55%~65% ▪ 蒸气回收量:35kg/t.s ▪ 氧化铁尘回收量:16kg/t.s ▪ 耗水量:2t/t.s ▪ 耗电量:3.3Kwh/t.s
▪ 脱P反应的有利条件归纳如下: A、(CaO)要多 B、 (FeO)要多 C、 (P2O5)要少 D、熔池温度低
三、转炉
(3)脱硫
S和P同样是有害元素。S对钢材的影响是在 热轧时造成表面裂纹(热脆)。由于FeS的 熔点低,当其在溶解状态下轧制,就产生 了缺陷。此外S同P一样易偏析。一般认为 炉内脱硫反应有三个:
升降装置由升降小车、横移台车、升降卷扬装 置及升降轨道组成。
三、转炉
(3)副枪装置 为了提高吹炼终点控制的命中率,在吹炼过程
中获得钢水温度、成分、炉内造渣情况等信息。 可装上不同的探头达到不同的检测目的,枪体采 用水冷,使用寿命较长,运行安全可靠,测定速 度快、精度高。副枪装置由旋转框架及其驱动装 置、副枪及升降小车、升降小车驱动装置、探头 供给及装着装置、探头提取及试样切断装置、刮 渣装置及副枪孔密封装置、副枪枪体矫直装置、 探头回收溜槽等。
三、转炉
▪ 冶炼时要注意以下几点,以取得满意的 结果:
A、应随着C的降低,把熔池温度正常的升 。
B、应在C低到钢种的目标值之前,先使P、 S降低到目标值以下。
C、吹炼终点各元素的含量应符合其钢种 的要求,钢水的温度也应调整到符合下 工序的要求。
三、转炉
(4)脱氧 加入比[C]更易与[O]结合的元素,如Al、Si 等使[O]去除的过程。 把氧脱到何种程度,根据钢的使用目的而 异,如沸腾钢,钢中的[O]是要利用的,而 镇静钢则要完全脱氧。但脱氧产物对钢的 性能有不良影响。
喷吹氮气压力
Max.200×104Pa
喷枪
尺寸 插入深度
250×8095mm 距铁水包包底350-450mm
数量
1×2
测温取样装置
型式
升降式
升降速度
10-30m/min
三、转炉
▪ 1、转炉冶炼流程 装入废钢和铁水副原料投入吹炼副 枪测定温度和成分出钢(脱氧及合金化) 倒渣
▪ 2、炼钢原料 (1)主原料(铁水和废钢):主要铁源。 (2)副原料:用于造渣去除P、S等杂质和调
▪ 宝钢现有的炉外精炼装置有:RH-OB(1#RH)、 RH-KTB(3#RH)、RH-MFB(2#RH)、VD、 CAS-OB、KIP、IR、UT、LF炉和喂丝等。
四、炉外精炼
(1)RH真空脱气的基本原理和工艺 为了减少钢中的有害气体和夹杂,净化钢水,提高钢
材的内在质量,改善机械性能,国内外各大钢厂均采用了 各种脱气方法,其中RH真空循环脱气法生产能力大,脱 气效果好,能使用于高生产率的氧气顶吹转炉。
三、转炉
公称容量(T)
300t
转炉炉壳高度(H) 11.5m
▪ 6、转炉设备 (1)转炉本体及倾动设备
转炉炉壳直径(D1) 8.5m
倾动速度
0.15~1.5cpm
倾动角度
±270°
由炉体、倾动装置、耳轴轴承座、托圈 及润滑装置组成,还有一套空气冷却系统。
炉体可分为炉帽、炉身、炉底三个部分, 炉体约重290吨。
A、钢液内脱硫:
[FeS]+[Mn][MnS]+[Fe]
B、钢液和炉渣之间的脱S
[FeS]+(MnO)(MnS)+(FeO)
三、转炉
C、熔池和炉气间的脱S 根据现场的经验,吹入大量氧时能脱S。通常认 为这是钢水中的S与氧气反应,生成SO2、SO3的 缘故。
▪ 脱硫反应的有利条件归纳如下: A、(CaO)要多 B、(FeO)要少 C、(CaS)要少 D、熔池温度要高 E、Mn要多
2[P]+5(FeO)5[Fe]+(P2O5) 2[P]+8(FeO)5[Fe]+(3FeO.P2O5) 当CaO足量时按下式进行: (P2O5)+4(CaO)(4CaO.P2O5) P2O5生成稳定的(4CaO.P2O5),防止回P反应。
三、转炉
▪ 脱P反应放出相当多的热,低温有利于放热 反应的进行。故脱P反应应在低温下进行。
三、转炉
(4)副原料系统 由进料、上料、加料等三个系统组成。 A、进料流程:原料场皮带机中转料仓1#皮
带机2#皮带机3#皮带机梭式皮带机地下 料仓 B、上料流程:地下料仓给料器1#皮带机2#皮 带机3#皮带机卸料小车炉顶料仓 C、加料流程:炉顶料仓给料器称量斗密封 阀中间料斗切断阀密封阀固定溜槽转 炉
(2)生成物CaS熔点高,形成固体渣,防止回硫,扒 渣容易,对耐材侵蚀较轻。
(3)脱硫生成的碳除饱和于铁水外,其余以石墨态析 出。同时还有少量CO、C2H2气体,以及少量电石粉 和石灰粉会污染环境,因此必须设置除尘设备。
(4)电石粉极易吸潮劣化,在大气下与水分接触迅速 发生反应,生成C2H2(乙炔)气体易爆,应采取安 全措施。
硅酸二钙,阻碍了硫向石灰粉颗粒中的扩散,故 脱硫效率仅为电石粉的1/3~1/4。 (5)价格低廉。
二、铁水预处理
▪ 脱硫剂的组成:为 了降低脱硫剂成本, 减少电石粉消耗, 脱硫剂的组成常根 据铁水条件、脱硫 要求作适当调整。 其原则是既满足脱 硫的要求,又要尽 量降低脱硫成本。
二、铁水预处理
▪ 3、铁水脱硫主要设备 喷吹法脱硫是把脱硫剂吹入铁水中以粉状料 的流态化气力输送技术为基础的。 (1)脱硫剂输送设备:受料设备、给料设备、 喷吹设备。 (2)脱硫喷枪及喷枪升降装置:喷枪工作时 必须插入混铁车的铁水内,喷枪底部为喷 口,两个喷口成一直线水平布置。 (3)混铁车测温取样装置。
三、转炉
(5)铁合金系统 分为输送系统和投料系统。
输送系统:自卸卡车地下料仓1#皮带机 2#皮带机3#皮带机卸料小车炉上 料仓
投料系统:炉上料仓称量斗卸料闸阀 皮带给料器中间料斗截止阀振动给 料器中间溜槽投料溜槽钢包
三、转炉
(6)OG系统
吹炼中从炉口大量冒出含有CO和氧化铁 的高温炉气,通过裙罩、烟罩等收集,经 过热交换(由锅炉系统收集蒸汽)冷却、 一次除尘和二次除尘,在IDF风机的吸引下, 将一定CO含量的转炉煤气回收到煤气罐中, 而达不到回收条件的炉气则由烟囱放散。
CaC2(固)+FeS=CaS(固)+Fe+2C CaC2+[S]=CaS+2C 2FeS+4CaO+[Si]=2Fe+2CaS+Ca2SiO4 2FeS+2CaO+[Si]=2Fe+2CaS+SiO2
二、铁水预处理
▪ 电石粉的特点:
(1)分解出的钙离子与[S]有极强的亲和力,因此 CaC2有很强的脱硫能力,耗量少,渣量也较少。
炼钢工艺和设备
2008年7月
一、炼钢概述
▪ 钢的定义:含碳量小于2%的铁合金。 ▪ 钢的分类:普碳钢和特殊钢(优质碳素钢、
合金钢、高合金钢(合金含量大于10%))。 ▪ 炼钢:将高炉生产出来的铁水炼成适合各
种用途的钢的过程。 ▪ 炼钢方法:平炉法、转炉法、电炉法。 ▪ 炼钢流程:高炉(铁水)铁水预处理
Ar:Max.l980(BRP脱磷 时3500)Nm3/h
N2:Max.1000(BRP脱磷 时3500)Nm3/h
N2,Ar,N2+02
四、炉外精炼
▪ 炉外精炼的定义:把粗精炼的钢水导入另一简便的 精炼装置,为得到比粗精炼更高的生产率、更高的 质量,而进行的冶金操作。