浅谈呋喃树脂自硬砂的生产及应用
呋喃树脂自硬砂工艺的推广应用

2 )微 粉含 量
再生树脂砂的微粉 ( 指极细砂粒) 含景要求如表2
所示 。
裹 2 再 生 树 脂砂 的微 粉含 量
体的卷入 , 才能解决树脂 自硬砂易产生气孔缺陷的毛 病。同时由于树脂砂常温强度高 , 其砂铁比可控制在 31为宜 。 : 拨模 斜度 比粘 土砂放 大 14到 1 2 树脂 自 / /。 硬砂 生 产 的铸件 尺 寸 准确 , 近模 样 尺 寸 , 接 故其 加 工 余量可减少13 总之 , /。 铸造工艺参数的调整是一个长 期过 程 , 中牵 涉到工 人操 作 习惯 , 木模 的利 用 , 其 老 多 种 型砂工 艺 同时 使用 等 。
6
3 )粒度
混制 树脂 自硬 砂 时 , 新砂 按 占旧砂 5 ~1 的 O
比例 , 同加 入到混 砂 机 , 发现 再生砂 粒 度明显 细 一 在
( 转第 2 下 6页)
维普资讯
铸造 工程 触, 但通 过 培训使 他 们 顺利 地 掌握 了记 录方 法 , 成 完
2 铸 造 工艺参数 的调整 树 脂 自硬砂 工艺有 其 固有特 点 , 不能 完全沿 用 故 原 有粘 土砂工艺 参数 。 做 到 , 当提 高浇 注速 度 } 应 适 缩 短 浇注 时 间 , 保证 足够 的浇 注 压 力头 , 防止 紊 流与 气
旧砂残存的可燃性物质总量的百分数。 生产不 同 材质铸件时, 旧砂的灼减量要求如表 1 所示。
Ab ta t Thsp p rp its u h r ob o eb f r u u aiig n - a ef r n—a dt c n l g sr c i a e on o tt ewo k t ed n e o ep p lrzn o— k u a - n e h o o y b s a d as ei —a d p e a a in a d a pia in i y ia a t g . n lor sn s n r p r to n p l t t p c lc si s c o n n Ke wo d Re i a d Te h o ia a a t r Ap l a in y rs sn s n c n gc l r mee p p i to c
呋喃树脂砂在铸造生产中的应用及质量控制

呋喃树脂砂在铸造生产中的应用及质量控制摘要呋喃树脂砂是近20年来发展最快的铸造工艺之一,用呋喃树脂砂生产的铸件,尺寸精确、表面光洁、棱角清晰、废品率低,并能节约造型工时、提高生产效率、改善劳动条件和成产环境。
2007年,山东安信机械制造有限公司对铸造车间进行技术改造,建立了一条树脂砂生产线,再该条生产线正式投产前,通过对员工进行系统的技术培训,制定相关的规章制度和操作规范,顺利实现了由水玻璃砂生产工艺向树脂砂生产工艺的转变。
本文对铸造生产各工序的过程控制作一简单阐述。
关键词呋喃树脂砂;铸造;生产;质量控制1 铸造工艺的控制呋喃树脂砂的特点是瞬间发气量大,高温溃散性好,易产加成气孔、夹渣和冲砂缺陷,在设计浇注系统时,应坚持快速、平稳、分散的浇注原则,浇注系统的截面积要比粘土砂工艺稍大一些,内浇道要分散放置。
树脂砂强度高、刚性好,铸件不容易产生缩孔缺陷,故应采用相对较高的浇注温度,以避免出现气孔和夹渣缺陷,厚大铸铁件的浇注温度也不应低于1 320℃。
2 砂型质量的控制2.1 原材料的选择及要求2.1.1 原砂树脂砂工艺对原砂的要求很高,原砂的粒度应根据主要产品的壁厚来确定,由于我公司主要以生产薄壁铸件为主,且未配备原砂烘干设备,故选用了粒度为50/100目的烘干擦洗砂。
2.1.2 树脂、固化剂国内成产树脂、固化剂的厂家很多,但具有自主研发能力、具备完善的检测设备和严密可靠的质量保证体系的厂家屈指可数。
经检验、对比,我们选用了济南圣泉集团股份有限公司生产的环保型呋喃树脂和磺酸固化剂,树脂加入量一般为原砂重量的1.0%~1.2%。
3 型砂工艺参数的控制3.1 可使用时间在生产过程中,我们将型砂表面开始固化的时间作为型砂的可使用时间,一般情况下,型砂的可使用时间应控制在6~10min,对于大型铸型或砂芯,可使用时间可延长15min,通过调整固化剂的加入量来控制型砂的可使用时间。
3.2 型砂强度初强度:是指型砂在1h的抗拉强度,型砂的初强度应控制在0.1~0.4MPa。
自硬呋喃树脂热塑性的研究及应用

•
3)江苏某铸造厂利用热塑 性自硬呋喃树脂到目前为止, 已累计生产各类铸钢件36件, 铸件重量由400kg到12500kg, 壁厚由60mm到500mm,最大单 件浇注重量22000kg。铸件表面 光洁,无裂纹、微裂纹、表面 气孔和皮下针孔等铸造缺陷, 如图7和图8所示,大大减轻了 后道清理、修补工序的工作量, 同时也提高了劳动生产率,降 低了铸件生产的综合成本。铸 件以100%的优良率赢得用户的 一致好评。
2
10 秒
20 秒
30 秒
40 秒
50 秒
60 秒
70秒 70秒
80秒 80秒
100
100
100
98. 5
97. 6
95. 5
94.5
92.2
100 100 100 100
98. 6
97. 2
96.4
95.1
• 注:1:普通呋喃树脂,2:热 塑性呋喃树脂;加热温度 1000℃
• 3)工艺调控简单:型砂可使用时间和硬化速度可控制范围相对较大, 受温度、湿度等环境因素影响相对较小,流动性更好,造型紧实容易, 常温强度适中,完全能满足中、大型铸件对铸型或砂芯的质量要求。 • 4)无刺激性气味,优化环境。行标JB/T 7526—2008《铸造用自硬呋 喃树脂》中规定:一级呋喃树脂中游离甲醛含量须≤1%,而热塑性自 硬呋喃树脂中游离甲醛仅为一级品的1/3,操作现场基本无刺激性气 味,优化了生产环境。 • 5)降本增效成效显著:旧砂回用率≥95%,灼烧减量稳定可控, 5 ≥95% 可减少新砂加入量3%~5%;铸件表面质量优良,铸件修补、清理、 检验工作量减少将近1/2,劳动生产率大为提高,生产周期大为缩短, 工人劳动强度大为减轻,产品质量稳定可控。 •
铸造技术:自硬呋喃树脂砂性能及优缺点

铸造技术:自硬呋喃树脂砂性能及优缺点进群须知,供应商和业务员禁止入群表面稳定性将经 24小时硬化后的φ 50×50试样称重 W 1;然后放在 14目筛上振动 2分钟,再称重 W 2,则表面稳定性为:SSI=W 2/W 1 × 100%砂型(芯)表面稳定性不足会导致冲砂及砂眼、机械粘砂等缺陷,一般来说表面稳定性的好坏与型砂常温强度的高低是一致的。
增加树脂加入量,选择合适的固化剂品种及加入量,不超过可使用时间,造型时适当的紧实,芯盒填砂面用刮刀墁平等等都可提高表面稳定性。
生产上要求砂型(芯)的互作表面(即与铁水接触的表面)稳定性应大于 90%,现场经验判定方法是用手指摩擦硬化后的型(芯)表面,一般以摸不下砂粒为准。
透气性它与硬化速度无关,与砂的粒型和粒度组成有关,颗粒越小,粒度越分散,含微分越多则透气性越差,粘结剂加入量多也影响透气性。
透气性好是呋喃树脂砂的一个优点,他弥补了有机铸型发气量大的优点,但也不可忽视采用集中通气等方式解决砂型和型芯的通气。
发气量呋喃树脂是有机粘结剂,型砂发气量主要与树脂的成分和加入量有关。
脲醛的发起量大,而糠醇和甲醛的发气量低。
加入量大,发气量相应增大而且发气时间也延长,但与发气的增长率不成比例。
千方百计降低树脂加入量之所以成为树脂砂互艺最基本的问题之一,除了经济上的原因之外,也是为了尽量降低砂型发气量,以减少铸件的气孔、呛火等缺陷。
由于发气量与型砂灼减量成正比,为方便起见,生产厂常以测定型砂灼热减量的方法代替测定发气量。
溃散性其指标用高温残留强度高低来反映。
将试样经 24小时硬化后放在 100、 200、300℃的电炉中保持一定时间,取出冷却至室温,测定其抗压强度。
残留抗压强度越低,说明溃散性越好。
一般说呋喃砂溃散性比较好,500℃左右残留强度为零。
实际砂型浇注后,由于树脂砂导热性较差,靠近铁水部分的砂层经受高温显示出较好的溃散性,但离铁水稍远一些的砂层受到热作用较小,残留强度仍然很高。
【坛友分享】浅析呋喃树脂自硬砂铸造的生产技术和应用

【坛友分享】浅析呋喃树脂自硬砂铸造的生产技术和应用1、自硬呋喃树脂砂铸造中所需原材料的选用1) 铸造用砂的要求原砂对呋喃树脂砂的性能粘结剂用量以及铸件表面质量的影响很大,要求原砂中的SiO2含量要高,含泥量和酸耗值要低。
建议粒度:大件42或30组别,中件21组别,小件15或10组别。
2) 呋喃树脂呋喃树脂是由糠醇生产而成的树脂,其糠醇含量较高,树脂的存放性能得以改善,热强度高但增加了成本。
树脂中的游离甲醛是生产中产生刺激性气体的来源,也是恶化环境的因素之一,应加控制(如铸造厂效率较好建议选用低甲醛呋喃树脂,保护环境)。
铸铁件生产应选用低氮或无氮树脂,实际应用根据铸件的技术要求和结构来选择。
3) 固化剂一般采用有机磺酸溶液按其水溶液或醇溶液的浓度来调节固化速度,铸造厂可以根据自己的工艺要求进行固化时间的调节,十分方便。
4) 添加剂(硅烷作偶联剂)为改善呋喃树脂自硬砂的性能,配比中常加入一些添加剂。
加入少量的硅烷作偶联剂,可显著的提高树脂砂强度,但随着时间的延长作用逐渐减弱,一般两个月将消失。
因此在国内由用户在使用之前加入并搅拌均匀,应尽快用完,也有部分呋喃树脂生产厂家为了方便客户,出厂之前便已经添加了硅烷。
(因此使用的时候必须注意时效问题)2、旧砂的再生和回收利用(降低成本)旧砂能很好的回收与再生是呋喃树脂砂的一大优点之一。
如何控制好再生砂的质量,是生产出高质量树脂砂铸件的关键质量树脂砂铸件的关键。
1) 砂温调节稳定砂温是呋喃树脂自硬砂的关键,尤其是再生砂的砂温,因此砂温调节是必不可少的。
如果砂温能控制好的话,它即可提高生产效率,可减少数珠加入量,又可减少砂型损坏和铸造缺陷,降低成本。
2) 关于呋喃树脂再生砂的质量指标@再生砂的酸耗值和PH值对于用酸作固化剂的呋喃树脂,酸耗值通常取负值;PH值过高就较难确定酸固化剂合适的加入量,一般PH值控制在3~6的范围。
@再生砂的灼减量和发气量灼减量是衡量树脂砂型中硬化粘结剂的残留量的大致标准。
呋喃树脂砂的应用

呋喃树脂砂的应用武汉重型机床集团铸锻公司有机自硬性铸型的开发是非量产铸造生产方式的一大改革,其生产效率和尺寸精度大大高于原有各种造型工艺水平。
目前树脂自硬砂工艺的优越性已被国内许多厂家的生产实践所肯定,其工艺已用于浇注所有种类的金属铸件。
1呋喃树脂砂的特性呋喃树脂砂具有如下特性:1)毒性小、气味低、粘度低,型、芯强度高。
2)砂子流动性好,性能稳定,储存期长。
3)可使用时间和脱模时间可以控制。
4)浇注后包覆在砂粒表面的树脂膜易除去,旧砂易回收利用。
5)可浇注所有类型的金属铸件。
6)对原砂的酸碱性要求严格。
7)硬化过程受周围环境的温度、湿度影响大。
呋喃树脂的原材料和它的组成如下表:1.1 硬化特性一般情况下,铸造用树脂是有C、H、O、N等原子以不同的形式结合而形成的液态的有机化合物。
在树脂生产阶段,各种原材料分子在热和催化剂的作用下,初步聚合成具有两维空间的线形链状结构的初聚物分子。
而在铸造生产使用时,由于第二种催化剂(固化剂或硬化剂)的加入,促使分子间这种聚合反应继续进行并形成具有非常大的分子量的具有三维空间结构的不溶性的体形网状高分子聚合物。
当三维结构聚合反应发生在砂子之间时,所形成的网状树脂结构就将砂粒彼此粘结起来,形成坚硬的骨架结构。
也就是树脂产生固化反应而硬化了。
1.2 可使用时间与可脱模时间1)可使用时间:指混好的树脂砂可以用来造型制芯的时间。
树脂砂混好后不立即使用,而是停留一段时间后再制型或制芯,则硬化强度随砂的停留时间延长而降低。
树脂和催化剂混合物聚合反应速度越快,其可用时间越短。
测试树脂砂可使用时间方法通常有三种:1)测型砂的初抗压强度值。
2)测型砂的终抗压强度值。
3)经验判断法。
2)可脱模时间:指型、芯达到起模不致损坏的强度所需的硬化时间。
型、芯在起模前处在封闭硬化状态,水分不易蒸发,硬化较慢,起模后,水分易蒸发,硬化较快。
如环境的相对湿度低,硬化反应进行的较完全,硬化强度亦高;环境的相对湿度较高,则硬化强度低。
浅谈呋喃树脂自硬砂的生产及应用
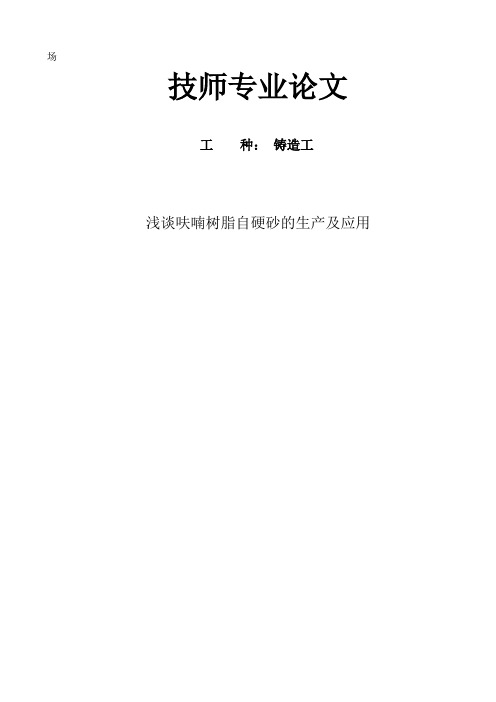
场技师专业论文工种:铸造工浅谈呋喃树脂自硬砂的生产及应用摘要 (2)引言 (2)1.呋喃树脂砂性能的优缺点 (2)2.呋喃树脂自硬砂的生产工艺技术 (3)3.工艺及现场控制 (6)4.呋喃自硬树脂砂铸件的缺陷分析及防止措施 (8)5.结论 (9)参考文献 (10)本论文针对呋喃树脂自硬砂的坭芯生产,阐述了呋喃树脂自硬砂的原材料配比、混制及硬化工艺。
结合作者多年在实际生产工作中的经验,就生产中出现的实际问题进行分析和讨论,通过采取文中提出的控制、解决措施,有效地解决了铸件出现的气孔、粘砂、热裂、冲/夹砂、脉纹等铸造缺陷。
关键词:呋喃树脂自硬砂、铸造缺陷、夹砂、热裂、脉纹引言呋喃树脂自硬砂工艺是指在呋喃树脂砂中加入一定量的酸性固化剂,使之在芯盒或砂箱内经历一定时间后,在常温条件下通过自行硬化成型(不需烘烤或吹入硬化气体)的一种造型制芯工艺。
呋喃树脂自硬砂硬化反应机理可简单描述为:涂敷在砂粒表面的树脂在酸性固化剂的催化作用下,呋喃树脂分子上的活性氢、羟甲基与羟甲基之间发生缩聚反应和呋喃环上的双键打开发生加成聚合反应,形成三维网状结构固体树脂,使型(芯)砂硬化成型。
1.呋喃树脂砂性能的优缺点1.1优点1)铸件的尺寸精度高、外部轮廓清晰、铸件表面光洁,外观质量好、组织致密、铸件综合品质高。
2)呋喃树脂自硬砂具有较好的流动性,容易紧实,脱模时间可调节,硬化后强度高,在其后的搬运及合箱过程中不变形,因树脂砂的强度高,在浇注和凝固过程中基本上不会出现位移现象,所以铸件的尺寸精度高。
3)不用烘干,缩短了生产周期、节省了能源、芯砂易紧实、溃散性好、容易清理、大幅度降低了劳动强度,为实现机械化生产创造了条件。
1.2 呋喃树脂自硬砂的不足之处1)对原砂质量要求高2)在生产过程中有刺激性气味3)采用树脂砂生产,成本较高2.呋喃树脂自硬砂的生产工艺技术2.1 原材料的选用1)铸造用砂的要求:原砂对呋喃树脂砂的性能、粘结剂用量、以及对铸件表面质量的影响很大,要求原砂中的SiO2含量要高、含泥量和酸耗值要低。
呋喃树脂自硬砂控制技术

呋喃树脂自硬砂控制技术摘要:本文主要从硅砂的性能要求、造型过程的控制和再生砂的回用等对呋喃树脂自硬砂技术进行了探讨,供广大铸造同行参考。
关键词:呋喃树脂自硬砂硅砂造型再生砂在线检测随着中国制造业近几年的长足发展,中国的铸造业也迎来了历史上最好的发展机遇。
目前,我国铸件的产量已连续多年位居世界之首。
呋喃树脂自硬砂工艺由于其生产周期短、铸件表面精度高、铸件质量容易控制、柔性化制造能力高等特点,已经被广泛的应用到机床铸件、耐磨铸件、工程机械铸件等产品中。
而铸造企业能否发挥呋喃树脂自硬砂的特点,有效的提高铸件的质量,这与型砂的控制技术有着密切的关系。
砂型铸造行业公认型砂控制技术、熔炼控制技术和管理水平三者决定了一个铸造厂在市场上的竞争能力,由此可见型砂的控制技术在铸造业中的重要性。
本文就呋喃树脂砂的一些控制技术提出一些个人的观点,希望同行提出批评指正。
1 硅砂的技术要求1.1 硅砂的粒度组成硅砂的粒度反映了硅砂的颗粒大小和分布状态。
由于自硬砂强度的获得是依靠呋喃树脂“包覆”硅砂表面形成的高分子链,所以硅砂的粒度越细,从理论上说获得同样强度的树脂消耗量就越大,型砂的成本也就越高,所以在保证铸件不发生粘砂缺陷的前提下,尽可能提高硅砂的粒度。
图1为自硬砂八字试样测得的抗拉强度(MPa)和砂型粒度组成的关系曲线:1.2 硅砂的角形系数硅砂的角形系数S=Sw/StSw---硅砂的实际比表面积(cm2/g)St----硅砂的理论比表面积(cm2/g)硅砂的角形系数越小,表面就越园整,同样体积的硅砂表面积越小,硅砂和呋喃树脂的物理和化学结合力就越强,获得同样的抗拉强度需要的树脂消耗量就越低。
作为自硬砂用的硅砂角性系数要求≤1.30,《1.51.3 硅砂的加工处理由于天然硅砂有大量直径小于0.02的泥分和一些污染物和一些有碱性的物资,泥分的存在极大的降低了硅砂的粒度组成,提高了树脂的消耗量,同时有碱性的物资在树脂砂硬化过程中消耗了大量的催化剂——对甲苯磺酸等物资,造成砂型硬化很慢甚至不硬化,所以硅砂必须经过擦洗和粒度分选处理。
呋喃树脂砂的使用方法

呋喃树脂砂的使用方法由于树脂自硬砂具有尺寸精度高、生产周期短、铸件质量高等特点,该工艺越来越多地用在机床、阀门、铸管、模具等众多领域,成为改善铸件质量、提高工艺水平的一种重要工艺方法。
本公司以其先进的技术和可靠的质量控制体系生产多种型号的自硬树脂,以适应铸钢、铸铁、有色金属及特殊要求的场合,其产品被越来越多的铸造企业采用。
呋喃树脂自硬砂工艺的一个特点就是固化速度、脱模时间受温度、湿度影响很大,最佳的温度范围是20℃~30℃,湿度则是越低越好,这时无论是固化剂用量、树脂砂强度还是固化速度都较理想。
随着冬季的到来,固化速度明显降低,每降低8℃,固化速度就降低一半。
许多客户尤其是新客户常发现2-3小时也不能脱箱,影响生产速度,所以用户必须掌握树脂砂工艺的特性,采取必要措施来解决这个问题。
常用的方法有:⒈更换固化剂公司有针对不同季节使用的固化剂,当冬季到来之前,注意及时更换使用G09固化剂或酸值更大的固化剂。
⒉ 增加固化剂的用量增加固化剂用量可以显著提高固化速度,这是生产中常用的方法,但加入量不宜过高,一方面增加成本,另一方面对终强度有害,且增加发气量,易产生气孔等缺陷。
⒊ 提高砂温通过增加砂温调节装置来提高砂温。
⒋ 增加环境温度很多铸造车间冬季无取暖设备,温度只有0℃左右,严重影响了固化速度,为此可以在造型现场设置几个取暖炉适当提高环境温度。
⒌ 提高模具、砂箱温度,保持干燥对金属模型、芯盒、砂箱可以适当加热以提高固化速度,对木模、木砂箱一定要保持其干燥。
另外,温度对树脂、固化剂粘度影响较大,因而波及定量泵流量,为保证加入量准确,每天生产前需校验树脂、固化剂量。
树脂砂的可使用时间随着树脂种类的不同有很大变化,它是供用户选择生产方法、工装、设备的重要依据,因此有必要介绍一下可使用时间的概念及其检测方法,以便于用户更好地控制生产。
⒈定义:树脂砂的可使用时间是指从混砂完毕至放置到不能制作出合格型芯的这段时间。
呋喃树脂自硬砂生产大型铸钢件
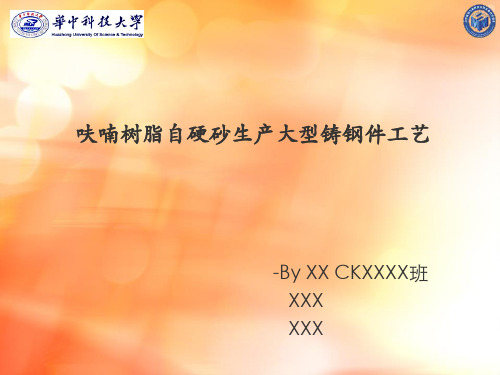
铬铁矿砂
Cr2O3>46% 粒度40/70目 细粉含量≤1.0% 酸耗值≤5ml 水分含量≤0.2% 灼减量≤0.5%
当然,再生砂性能指标与铸件质量也有直接关系!
呋喃树脂自硬砂生产大型铸钢件工艺▪树脂和固化剂的选择
树脂:无氮高糠醇呋喃树脂
固化剂:对甲苯磺酸或二甲苯磺酸
呋喃树脂自硬砂生产大型铸钢件工艺▪砂温控制
20℃~30℃
呋喃树脂自硬砂生产大型铸钢件工艺▪砂型强度
一般要求: 型砂终强度:0.6MPa~0.8MPa 芯砂终强度:0.8MPa~1.0MPa 复杂芯砂终强度:1.6~2.0MPa
呋喃树脂自硬砂生产大型铸钢件工艺▪树脂和固化剂加入量
实际树脂加入量:1.0%~1.2% 固化剂加入量:树脂加入量的30%~50%
参考文献
参考文献: [ 1 ]李远才 . 铸型材料基础 [M]. 北京:化学工业出版社, 2009 [ 2 ]于洪岩,周俊珍 . 呋喃树脂自硬砂生产大型铸钢件工 艺控制要点[J].铸造设备与工艺,2011(3):22-24 [ 3 ]李小军,江国栋,等 . 一种快速测定铸造用自硬呋喃 树脂含氮量的方法[J].铸造,2014,63(4):360-362
呋喃树脂自硬砂生产大型铸钢件工艺▪工艺设计原则
多组芯造型 朝铸件表面填砂 铬铁矿面砂
慎重铸造缩尺
冒口树脂自硬砂生产大型铸钢件工艺▪生产操作注意事项
严控生产操作
举措
型芯紧实
涂料涂刷
型芯排气
砂型芯退让
结论
合格大型铸 有毒气体 发气量大 钢件
不利因素 增碳
热裂倾向 大 退让性差
疏漏之处,恳请指正!
谢谢!
材控XXXX班 XX XXX XXX
呋喃树脂砂旧砂再生回用及质量控制

呋喃树脂砂旧砂再生回用及质量控制一、呋喃树脂自硬砂的特点:1、型(芯)强度高,溃散性好,能够保证铸件的尺寸精度和表面质量。
2、流动性好,能提高型(芯)的充填性,提高型(芯)质量和劳动生产率,减轻工人的劳动强度。
3、节约能耗,铸型(芯)只需低温烘烤,就满足浇注要求。
4、旧砂可再生回用,可进一步降低成本。
二、再生设备的几个主要技术指标:1、生产率3~15t/h2、回用率≥90%3、脱膜率≥18%~25%三、呋喃树脂自硬砂旧砂的再生工艺流程:落砂再生筛分破碎磁选风选砂库备用混砂铸型(芯)浇注后经冷却,符合开箱落砂工艺规程要求时,即可开箱。
经振动落砂机进行落砂后,砂子与铸件分开。
对落砂后混入旧砂中的铁刺、铁块、砂豆等金属杂物,通过磁选机进行清除,旧砂经过落砂、磁选即进入(S56系列)振动再生机,砂快在振动再生机通过互相搓擦、摩擦,最后基本形成砂粒和一小部分微小砂块。
破碎后在旧砂中存在的小砂块通过筛分去除,经筛分后的旧砂,基本以砂粒形成存在,然后进入(S52系列)转子再生机。
砂子在转子再生机中通过快速旋转的叶片,使刚进入再生机顶部的砂流,在离心力作用下,即刻被甩向耐磨筒壁,使旧砂在再生机里互相摩擦,撞击去除砂粒表面的残存粘结剂膜。
通过再生机再生的旧砂,存在大量的粉尘和微粒,这些物质的存在,会严重影响树脂性能,因此必须经风选进行清除。
风选后的再生砂既可输送到砂库中储存冷却备用。
四、再生砂的质量控制再生砂的质量直接影响到铸件质量和生产成本,故必须严格控制,对再生砂质量主要控制以下指标。
1、灼减量灼减量是指旧砂经过再生后,砂中残存的可燃性物质总量的百分数。
浇注落砂后的旧砂,砂粒表面覆盖着一层粘结剂膜,除靠近铸件表面的由于高温烧失外,大部分因远离铸件仍保持完整,这些仍保持完整粘结剂膜的旧砂,必须通过再生处理,才能达到工艺要求。
否则会使型砂发气量增加,从而引起铸件产生气孔等缺陷。
表1、不同材质的灼减量要求2、微粉含量微粉是指直径为0.106mm以下的颗粒,其表面积较大,再生时脱膜率低。
呋喃树脂自硬砂在纺织机械铸铁件上的应用
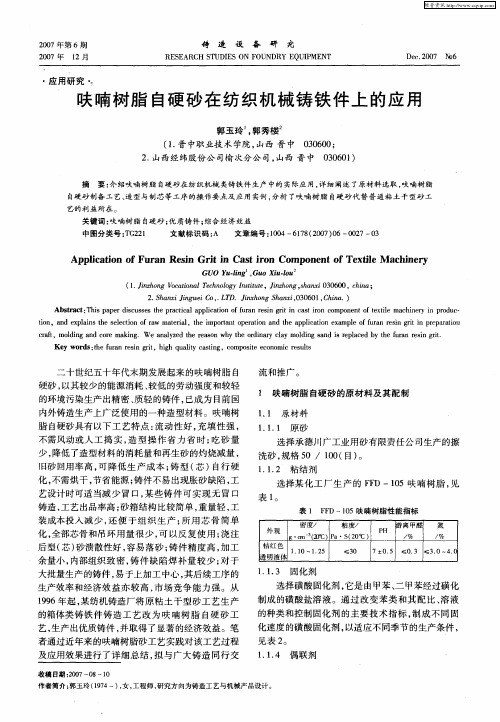
选择 某 化 工 厂 生 产 的 F D一15呋 喃树 脂 , F 0 见
表 1 。
表 1 F D一15呋 喃树 脂 性 能 指 标 F 0
外
观
密度/
粘 度/
化 , 部芯骨 和 吊环 用 量 很少 , 以 反 复使 用 ; 注 全 可 浇 后型( ) 芯 砂溃 散性好 , 易落 砂 ; 件 精度 高 , 工 容 铸 加 余 量小 , 内部组 织 致 密 , 件 缺 陷焊 补 量 较 少 ; 于 铸 对 大批量 生产 的铸件 , 于上加 工 中心 , 后续 工序 的 易 其 生产效率 和经 济 效 益亦 较高 , 场 竞 争 能 力 强 。从 市
c at r f,mo d n n o e ma i g l i g a d c r kn 。W e a ay e h e s n w y t e o d n r ly mod n a d i rp a e y t e f rn r sn g i n l z d t e r a o h h r ia y c a li g s n s e lc d b h u a e i r , t Ke r s te f r n r sn y wo d :h u a e i t i h q ai a t g,c mp s e e o o i e ut ,h g u t c s n l y i o o i c n m crs l t s
维普资讯
20 0 7年 第 6期
20 0 7年 l 2月
铸
造
设
备
研
究
D c20 N6 e。0 7 o
R S A C T D E N F U D Y E UP N E E R H S U ISO O N R Q IME T
铸钢用几种自硬砂综述

生产薄壁类铸钢件用几种自硬砂工艺综述生产铸钢件可供选择的型砂工艺有:呋喃树脂自硬砂工艺、碱性树脂自硬砂工艺、pepset 法自硬砂工艺、新型水玻璃自硬砂工艺。
这四种自硬砂工艺的基本情况如下:一、四种自硬砂工艺的概述(一)呋喃树脂自硬砂工艺1、工艺主要优势(1)铸件表面质量和尺寸精度高。
(2)型芯溃散性好,铸件落砂清理容易。
(3)旧砂干法再生回用容易,回用率高(≥90%)。
这些优点使该工艺在铸件生产中得到大面积推广应用,尤其是铸铁件的生产。
2、工艺缺点多年的理论研究和生产实践表明,用呋喃树脂砂工艺生产铸钢件有难以解决的技术难题。
(1)呋喃树脂砂热膨胀系数大,高温退让性差,铸件易产生裂纹,尤其是薄壁、壁厚差较大,结构复杂的铸钢件。
(2)粘结剂系统含S、N等有害元素,易造成铸件表面渗硫,造成表面微裂纹,以及N导致的气孔或皮下气孔。
(3)型砂发气量较大,铸件易出现气孔缺陷。
(4)混砂、造型、浇注、落砂、清理过程中产生SO2、CO等有害气体,污染作业环境。
正是由于上述一些原因,导致某些工厂不能把所有产品都使用呋喃树脂砂生产,而保持呋喃树脂砂、水玻璃砂(粘土砂、碱性树脂砂)并行的状态,造型管理、生产上的诸多不便。
呋喃树脂砂生产线有的因铸件废品率多、生产成本高已闲置,有的生产线已改造成新型水玻璃自硬砂生产线或碱性树脂砂生产线。
针对呋喃树脂砂工艺的不足,国内外专家进行了多年研究,推出改性呋喃树脂,并在生产过程中采取多项工艺措施(如冷铁等),但未收到明显实效。
综上所述,呋喃树脂砂工艺用于铸钢件的生产不是一种好的选择,生产薄壁、结构复杂、易产生裂纹、气孔类缺陷的泵、阀、机车类铸钢件则更不可取。
(二)碱性树脂自硬砂工艺1、工艺优势(1)铸件表面质量和尺寸精度高,铸件综合质量优良。
(2)粘结剂系统不含S、P、N等有害元素,可防止因这些元素引起的铸件缺陷。
(3)具有独特的高温硬化特性,可显著减少铸钢件的热裂缺陷。
(4)固化剂参与硬化反应,型砂硬化性能好,可调性强。
呋喃树脂自硬砂生产大型铸钢件工艺控制要点概要

2011年第3期Jun.2011№3铸造设备与工艺呋喃树脂自硬砂是指常温下呋喃树脂在固化剂的作用下发生化学反应,使铸型(芯获得固化成型的一种工艺方法。
它具有许多优点,如铸件尺寸精度高,表面粗糙度好,生产工艺简单,生产效率高,劳动强度低,尤其是铸型(芯溃散性好,铸件清砂容易,旧砂通过再生可反复回用,再生率在90%以上,且再生后的旧砂性能与新砂相似,有些性能指标甚至优于新砂,既可作背砂,也可作面砂。
采用呋喃树脂自硬砂工艺生产铸钢件时,由于呋喃树脂自硬砂发气量大且迅速、铸型导热性差、高温强度高、退让性差,造成铸钢件质量难以控制,表现在:易产生侵入性的皮下气孔;铸钢件的热裂倾向性大;浇注后砂型的导热性差,不利于形成铸件的顺序凝固。
但是,只要通过对造型原辅材料进行科学合理的控制,采用符合呋喃树脂自硬砂生产要求的铸造工艺方法,并严格控制生产操作过程,呋喃树脂自硬砂完全能够生产出满足使用要求的高质量铸钢件。
我厂2007年所上的呋喃树脂自硬砂生产线,目前已经形成规模性的生产。
1造型用原辅材料的合理控制1.1原砂的选择我厂生产大型铸钢件的原砂主要是石英砂和铬铁矿砂。
作为生产大型铸钢件用砂,要求原砂必须具有一定的耐火度和热稳定性,不与金属液发生反应,选择适合铸钢件生产的高品位擦洗烘干原砂,并控制好再生砂的相关指标。
通过我厂几年来的生产实践,石英砂的SiO 2含量应大于97%,粒度30/70目(集中度≥85%,含泥量≤0.3%,细粉含量≤1.0%,酸耗值≤5ml ,水分含量≤0.2%,酌减量≤0.5%,粒形:采用椭球形的天然石英砂或者多边形的人工破碎石英砂,避免使用尖角砂。
原砂应具有良好的抗破碎性,以便于进行再生。
铬铁矿砂中Cr 2O 3含量应大于46%,粒度40/70目,细粉含量≤1.0%,酸耗值≤5ml ,水分含量≤0.2%,酌减量≤0.5%。
在铸钢件的生产过程中,再生砂的性能指标与铸件质量有直接关系,特别是灼减量和微粉含量直呋喃树脂自硬砂生产大型铸钢件工艺控制要点于洪岩1,周俊珍2(1.天津市天重江天重工有限公司,天津300400;2.西北工业集团有限公司,陕西西安710043摘要:结合多年呋喃树脂自硬砂生产大型铸钢件的经验,针对常出现发气量大、退让性差、热裂倾向大的问题,摸索出合理的解决办法,实践证明通过科学控制造型原辅材料,采用符合呋喃树脂自硬砂生产要求的铸造工艺方法,并严格控制生产操作过程等措施,即可以生产出满足用户要求的合格产品。
呋喃树脂自硬砂的应用和旧砂的回用

( 3) 原砂的选用 大型铸件用硅砂 ( 28~ 55 目 ) , 小铸 件用硅 砂( 70 ~ 100 目 ) 以 及 型芯 砂 用硅 砂 ( 70 ~ 140 目) , 砂含泥量和含水量均应控制在 0. 5% 以下。 对砂粒形状要求应该是 : 表面圆滑、 颗粒成圆形 或椭圆形。这样的砂粒表面积小, 透气性能好, 树脂消耗量少, 经济效益好。 ( 4) 附加物 实验证明, 呋喃树脂自硬砂中, 添加少量的 硅烷偶联剂 , 可提高呋喃树脂砂的硬度 , 在相同 条件下, 加入 2% 左右的硅烷后, 其抗压强度可 提高 10kg/ cm , 甚至更多, 尤其在树脂加入量少 时更为突出。 ( 5) 型芯砂的配比及混制工艺 配比: 取型 砂 100% , 树脂 1. 4% ~ 1. 75% ( 砂重 ) , 固 化剂 50% ~ 65% ( 树 脂重 ) , 偶联 剂 0. 2% ( 砂重) 。 混制工艺: 先将型砂干混 1min, 加入固化剂 混匀约 1. 5min, 然后加入树 脂, 混搅 1. 5~ 2min 即可出砂。 为了达到铸型要求, 型砂中最好除去杂物, 水分控制在 1% 以下, PH 值不应大于 7. 0, 砂温 25 为 最佳。硬 化进度与 温度存在 密切联 系, 树脂加入后 , 混砂时间要适当控制, 造型时以树 脂砂发粘时即应停止使用。冬季要保温或对模 具预热处理 , 硬化时间一般为 10~ 15min 即可脱 模。砂层厚的型芯可设置通气和吊攀, 另外用自 硬砂的型芯和型腔, 必须适当增加出气 , 保证气 38
( 2) 干燥后的旧砂 85% ( 水份< 2% 、灰份不 控制) + 15% 新砂, 树脂加入量不变 , 固化剂加入 量增加原总量 4% 左右, 混制工艺不变。 ( 3) 造型工艺应对铸型、 型芯增加 2~ 3 道排 气或出气孔 , 由于树脂砂传递性减弱应增加夯实 程度。 此种办法可保证旧砂反复使用 , 在实践中树 脂砂的溃散性、 退让性稍有降低, 但铸件缺陷发 生率基本不变。
呋喃树脂自硬砂原砂
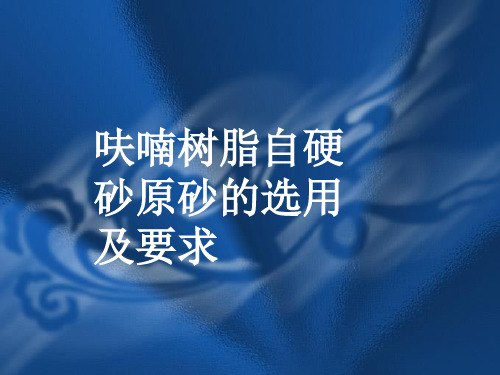
<5
硅砂
30
>97
<0.2
<0.1~0.2
<0.5~1
<5
硅砂
30
>96
<0.2
<0.1~0.2
<0.5~1
<5
材质 铸钢
适用范围 铸件类型
中大型及大型铸件
大、中型铸件
硅砂
21
>96
<0.2~0.3 <0.1~0.2 <0.5~1
<5
中、小型铸件
硅砂
30
硅砂
21
硅砂
21
硅砂
10
>90 >90 >90 >90
<0.5~1 <0.5~1
<5
有色
<5
合金
各类铸件
<0.2 <0.2~0.3 <0.2~0.3
<0.3
<0.1~0.2 <0.1~0.2 <0.1~0.2 <0.1~0.2
<0.5~1 <0.5~1 <0.5~1 <0.5~1
<5 中大型及大型铸件
<5 铸铁
<5 一般件
<5
硅砂
15
硅砂
10
>85 >85
<0.2~0.3 <0.3
<0.1~0.2 <0.1~0.2
呋喃树脂自硬 砂原砂的选用 及要求
一、呋喃树脂自硬砂
呋喃树脂自硬砂——是指常温下呋喃树脂粘结剂由 于催化剂的作用发生化学反应 而 固化的型(芯)砂
(一)呋喃树脂自硬砂原材料的选用
呋喃树脂砂由原砂、呋喃树脂、催化剂、添加剂组成
各种原材料很大
正确选用树脂砂的各种原材料非常重要
1.原砂 1)对原砂化学成分、需酸值、pH值的要求
(1)化学成分
铸钢件用原砂wSiO2>97% 铸铁件用原砂wSiO2>85%
呋喃树脂砂型砂性能及其控制
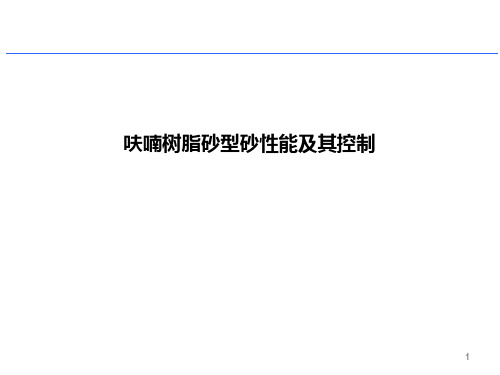
10
型砂性能及其控制
(六)灼烧减量(LOI):1.8-3.0% 1、灼烧减量就是再生砂经过高温灼烧后重量减少的数量,它是衡量再生砂 的脱膜率的重要指标,影响型砂的发气量。 2、灼烧减量越大,型砂的发气量就越大,铸件产生气孔的可能性就越大。 影响铸件的质量,造成废品偏高。 3、灼烧减量越低,需要增加再生成本,同时混砂时需要加入过多的树脂、 固化剂,增加生产成本。 4、在不增加成本的前提下降低灼烧减量的途径: (1)减少砂铁比:型砂重量/金属重量≤3,(使用合适的砂箱来进行生产, 浇冒口可单独加高) (2)重复利用砂块,减少铸型新型砂的加入。
12
型砂性能及其控制
(八) 细分含量(灰分含量):≤0.5% 1、混合砂中粒度小于140目的称为细分含量(灰分含量)。 2、砂细分含量高,产生以下不利: (1)消耗的树脂、固化剂多; (2)降低了型砂的透气性; (3)使铸件产生粘砂的可能性增加。 3、控制型砂的细分含量: (1)保持再生除尘系统始终处于良好的工作状态 (2)及时补加新砂 (3)打扫卫生时落地的型砂的最后部分不要放在落砂机上
2
型砂性能及其控制
2、型砂的分类:
浇注后铸型 落砂机落砂 旧砂
再生系统再生
(新砂库)
新砂
再生砂
(再生砂库)
(造型机砂库)
混合砂
固化剂
树脂
混砂机
造型用砂
3
型砂性能及其控制
二、型砂性能的要求及控制: (一)8小时抗拉强度:0.5-1.2MPa 1、铸铁生产线从模型准备完到浇注准备第一箱,共计140个工位,全线正
7
型砂性能及其控制
(二) 发气量: 12-17ml/g: 1、铸型浇注铁(钢)水后,型砂中的树脂、固化剂在作用下产生气。 2、影响因素 (1)型砂中树脂、固化剂的加入量。加入量越大,发气量就越大。 (2)造型用砂的灼烧减量。当型砂中树脂、固化剂的加入量一定时,灼烧 减量越大,发气量就越大。 3、型砂的发气量越大,铸件产生气孔(侵入性)的可能性就越大,因此在 满足型砂强度的前提下,型砂的树脂、固化剂加入量越少越好。
呋喃树脂砂铸造生产及应用实例
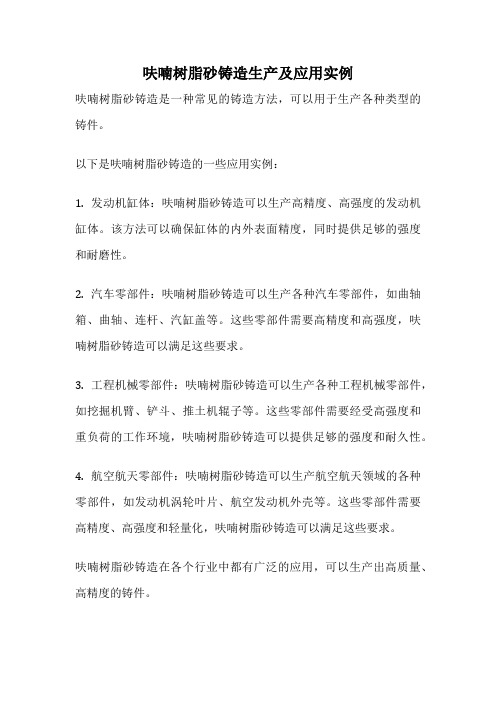
呋喃树脂砂铸造生产及应用实例
呋喃树脂砂铸造是一种常见的铸造方法,可以用于生产各种类型的铸件。
以下是呋喃树脂砂铸造的一些应用实例:
1. 发动机缸体:呋喃树脂砂铸造可以生产高精度、高强度的发动机缸体。
该方法可以确保缸体的内外表面精度,同时提供足够的强度和耐磨性。
2. 汽车零部件:呋喃树脂砂铸造可以生产各种汽车零部件,如曲轴箱、曲轴、连杆、汽缸盖等。
这些零部件需要高精度和高强度,呋喃树脂砂铸造可以满足这些要求。
3. 工程机械零部件:呋喃树脂砂铸造可以生产各种工程机械零部件,如挖掘机臂、铲斗、推土机辊子等。
这些零部件需要经受高强度和重负荷的工作环境,呋喃树脂砂铸造可以提供足够的强度和耐久性。
4. 航空航天零部件:呋喃树脂砂铸造可以生产航空航天领域的各种零部件,如发动机涡轮叶片、航空发动机外壳等。
这些零部件需要高精度、高强度和轻量化,呋喃树脂砂铸造可以满足这些要求。
呋喃树脂砂铸造在各个行业中都有广泛的应用,可以生产出高质量、高精度的铸件。
呋喃树脂自硬砂生产球铁的过程控制及问题探讨

冷自硬树脂砂用于球铁生产的过程控制及问题探讨高连国(荆州环宇汽车零部件有限公司湖北荆州4340000)【摘要】冷自硬树脂砂型除受树脂本身的性能影响外,还受气温、砂温、原砂的特性、固化剂的种类、酸度值、固化剂的加入量以及混砂方式,混砂时间长短等等方面的影响,在用于生产球墨铸铁件时,铸型表面的涂料特性以及球铁本身的固有特性等都将对球铁铸件产生影响。
本文针对以上方面,并结合生产实际就冷自硬树脂砂用于球铁生产的过程控制及问题进行一些探讨,求教于广大铸造同仁,以期对冷自硬树脂砂用于球铁生产有所帮助。
【关键词】冷自硬树脂砂固化剂涂料球墨铸铁随着铸件采购商对毛坯外观和铸件尺寸精度要求的提高,潮模砂生产铸件的方式显得越来越落伍了,特别是在较大型的机床、阀门类铸件的生产方面,无论是铸件的外观还是尺寸精度,尤其是铸件的内在质量甚至生产周期,树脂砂生产的优势变得越来越明显,并逐渐被广大铸造工作者和铸件采购商所认同。
虽然呋喃树脂并不是新东西,文献表明早在1873年就有了起源于玉米制品的呋喃乙醇树脂记载,但国内用呋喃树脂作为粘结剂用于铸造生产却只有二十多年的历史,并已有最新成果“碱性酚醛自硬树脂”等。
树脂砂在国内发展的这二十多年来,随着国内对树脂、固化剂等研究的深入和成熟,生产中的应用也越来越广泛,并且无论是造型还是制芯,无论是加热固化还是催化固化——即所谓自硬都被大量应用,本文仅对加酸硬化的冷自硬树脂砂在球墨铸铁生产中的运用过程及产生的一些影响产品质量的问题进行分析探讨并提出结合自己生产实际的解决办法,以求得到方家的指正。
一、树脂质量对球铁质量的影响及控制方法所谓冷自硬树脂砂就是用树脂作粘结剂用酸作催化剂,不用加热,常温下即能使砂型(芯)达到所要求的硬度的一种型(芯)砂。
要得到表面光洁、几何尺寸精确(相对而言)、内在质量高的铸件,铸型(芯)的表面必须光洁,铸型的几何尺寸必须符合金属液的凝固、收缩特点而精确;要得到内在质量高的铸件,在铸型(芯)上要做的文章更多,而树脂的质量则对铸型(芯)的质量起着决定性的作用,树脂就是通过影响铸型(芯)的质量从而影响到铸件的质量的。
浅谈呋喃树脂砂的生产与质量控制
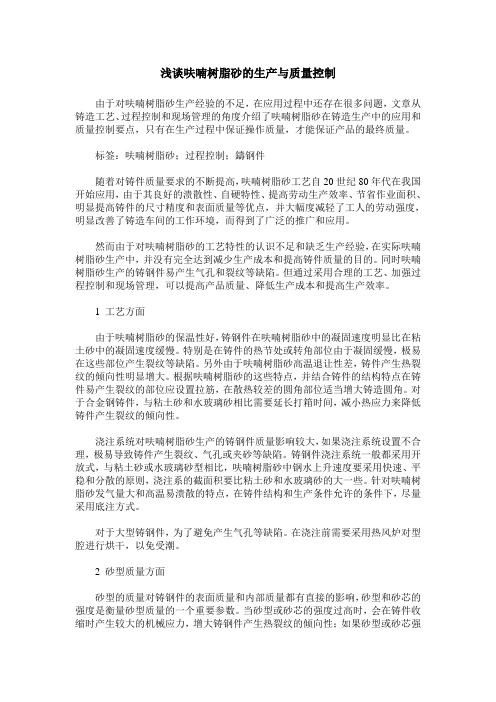
浅谈呋喃树脂砂的生产与质量控制由于对呋喃树脂砂生产经验的不足,在应用过程中还存在很多问题,文章从铸造工艺、过程控制和现场管理的角度介绍了呋喃树脂砂在铸造生产中的应用和质量控制要点,只有在生产过程中保证操作质量,才能保证产品的最终质量。
标签:呋喃树脂砂;过程控制;鑄钢件随着对铸件质量要求的不断提高,呋喃树脂砂工艺自20世纪80年代在我国开始应用,由于其良好的溃散性、自硬特性、提高劳动生产效率、节省作业面积、明显提高铸件的尺寸精度和表面质量等优点,并大幅度减轻了工人的劳动强度,明显改善了铸造车间的工作环境,而得到了广泛的推广和应用。
然而由于对呋喃树脂砂的工艺特性的认识不足和缺乏生产经验,在实际呋喃树脂砂生产中,并没有完全达到减少生产成本和提高铸件质量的目的。
同时呋喃树脂砂生产的铸钢件易产生气孔和裂纹等缺陷。
但通过采用合理的工艺、加强过程控制和现场管理,可以提高产品质量、降低生产成本和提高生产效率。
1 工艺方面由于呋喃树脂砂的保温性好,铸钢件在呋喃树脂砂中的凝固速度明显比在粘土砂中的凝固速度缓慢。
特别是在铸件的热节处或转角部位由于凝固缓慢,极易在这些部位产生裂纹等缺陷。
另外由于呋喃树脂砂高温退让性差,铸件产生热裂纹的倾向性明显增大。
根据呋喃树脂砂的这些特点,并结合铸件的结构特点在铸件易产生裂纹的部位应设置拉筋,在散热较差的圆角部位适当增大铸造圆角。
对于合金钢铸件,与粘土砂和水玻璃砂相比需要延长打箱时间,减小热应力来降低铸件产生裂纹的倾向性。
浇注系统对呋喃树脂砂生产的铸钢件质量影响较大,如果浇注系统设置不合理,极易导致铸件产生裂纹、气孔或夹砂等缺陷。
铸钢件浇注系统一般都采用开放式,与粘土砂或水玻璃砂型相比,呋喃树脂砂中钢水上升速度要采用快速、平稳和分散的原则,浇注系的截面积要比粘土砂和水玻璃砂的大一些。
针对呋喃树脂砂发气量大和高温易溃散的特点,在铸件结构和生产条件允许的条件下,尽量采用底注方式。
对于大型铸钢件,为了避免产生气孔等缺陷。
- 1、下载文档前请自行甄别文档内容的完整性,平台不提供额外的编辑、内容补充、找答案等附加服务。
- 2、"仅部分预览"的文档,不可在线预览部分如存在完整性等问题,可反馈申请退款(可完整预览的文档不适用该条件!)。
- 3、如文档侵犯您的权益,请联系客服反馈,我们会尽快为您处理(人工客服工作时间:9:00-18:30)。
场技师专业论文工种:铸造工浅谈呋喃树脂自硬砂的生产及应用摘要 (2)引言 (2)1.呋喃树脂砂性能的优缺点 (2)2.呋喃树脂自硬砂的生产工艺技术 (3)3.工艺及现场控制 (6)4.呋喃自硬树脂砂铸件的缺陷分析及防止措施 (8)5.结论 (9)参考文献 (10)本论文针对呋喃树脂自硬砂的坭芯生产,阐述了呋喃树脂自硬砂的原材料配比、混制及硬化工艺。
结合作者多年在实际生产工作中的经验,就生产中出现的实际问题进行分析和讨论,通过采取文中提出的控制、解决措施,有效地解决了铸件出现的气孔、粘砂、热裂、冲/夹砂、脉纹等铸造缺陷。
关键词:呋喃树脂自硬砂、铸造缺陷、夹砂、热裂、脉纹引言呋喃树脂自硬砂工艺是指在呋喃树脂砂中加入一定量的酸性固化剂,使之在芯盒或砂箱内经历一定时间后,在常温条件下通过自行硬化成型(不需烘烤或吹入硬化气体)的一种造型制芯工艺。
呋喃树脂自硬砂硬化反应机理可简单描述为:涂敷在砂粒表面的树脂在酸性固化剂的催化作用下,呋喃树脂分子上的活性氢、羟甲基与羟甲基之间发生缩聚反应和呋喃环上的双键打开发生加成聚合反应,形成三维网状结构固体树脂,使型(芯)砂硬化成型。
1.呋喃树脂砂性能的优缺点1.1优点1)铸件的尺寸精度高、外部轮廓清晰、铸件表面光洁,外观质量好、组织致密、铸件综合品质高。
2)呋喃树脂自硬砂具有较好的流动性,容易紧实,脱模时间可调节,硬化后强度高,在其后的搬运及合箱过程中不变形,因树脂砂的强度高,在浇注和凝固过程中基本上不会出现位移现象,所以铸件的尺寸精度高。
3)不用烘干,缩短了生产周期、节省了能源、芯砂易紧实、溃散性好、容易清理、大幅度降低了劳动强度,为实现机械化生产创造了条件。
1.2 呋喃树脂自硬砂的不足之处1)对原砂质量要求高2)在生产过程中有刺激性气味3)采用树脂砂生产,成本较高2.呋喃树脂自硬砂的生产工艺技术2.1 原材料的选用1)铸造用砂的要求:原砂对呋喃树脂砂的性能、粘结剂用量、以及对铸件表面质量的影响很大,要求原砂中的SiO2含量要高、含泥量和酸耗值要低。
2)呋喃树脂:含糠醇的树脂称为呋喃树脂,其糠醇含量较高,树脂的存放性能得以改善,热强度高但增加了成本,树脂中的游离甲醛是生产中产生刺激性气体的来源,也是恶化环境的因素之一,应加以控制。
3)固化剂:一般采用有机磺酸溶液按其水溶液的浓度来调节固化速度。
选用呋喃树脂自硬砂固化剂时,应注意以下问题:A、应根据室温的高低,合理选用固化剂夏季室温高时,选用酸度较低的固化剂;冬季室温较低时,应采用酸度较高的固化剂。
B、应根据呋喃树脂种类,合理选用固化剂磷酸是生产中常用的酸固化剂,但多用于高氮呋喃树脂,而很少用于低氮呋喃树脂。
这是因为低氮高糠醇树脂采用磷酸作固化剂时,硬化速度过慢,脱模时间过长;而高氮低糠醇树脂,使用磷酸作固化剂仍可获得必要的硬化速度;而且高氮低糠醇树脂采用磷酸作固化剂仍可获得很好的终强度,而低氮高糠醇用磷酸作固化剂时终强度较低。
C、应根据铸造合金种类和旧砂再生回用情况,合理选用固化剂呋喃树脂砂再生回用时,建议不采用磷酸作固化剂。
因为用磷酸作固化剂的砂型(芯)在浇注后,磷酸不能在金属液的热作用下分解破坏,而生成磷酸盐沉积在砂粒表面,较难通过再生去除,导致再生砂配制的树脂砂的强度下降很多,并且增加铸型膨胀量,使夹砂倾向增加。
D、应根据型砂的强度要求,合理确定固化剂加入量当固化剂加入量很少时,不足以使树脂的硬化反应完全,自硬砂的强度很低;随着固化剂加入量的增加,自硬砂的强度明显提高;强度达到最高值以后,如果继续增加固化剂,自硬砂的强度会急剧下降,这是因为硬化反应太强烈,树脂的交联结构不完整,导致树脂膜和黏结桥脆化。
由于固化剂加入量不同,加等量树脂的自硬砂的强度可以相差几倍之多。
值得注意的是:终强度达到最高时的固化剂用量不一定就是最佳的。
因为型砂终强度最高时,其硬化过程往往缓慢,甚至要等几个小时才能脱模,这在生产上是行不通的。
由此可见:采用呋喃树脂自硬砂时,对固化剂加入量的选定应非常慎重,切不可为追求硬化快而随意多加。
4)添加剂,为改善呋喃树脂自硬砂的性能,配比中常加入一些添加剂,一般加入少量的硅烷做偶联剂,可以明显的提高树脂砂的强度,但随着时间的延长,其作用逐渐减弱,一般情况下,其强度在两个月后将消失,因此,对于偶联剂硅烷应在使用之前加入并搅拌均匀,必须尽快用完。
2.2呋喃树脂自硬砂的再生回用:旧砂能很好的回收与再生是呋喃树脂砂的一大优点,如何控制好再生砂的质量,是生产出高质量树脂砂铸件的关键。
1)砂温调节、稳定砂温是呋喃树脂自硬砂的关键,因此,砂温调节控制是必不可少的,再生砂的砂温尤其重要,如果砂温能控制好的话,它既可提高生产效率,减少砂型损坏和铸造缺陷、降低成本。
2)再生砂的酸耗值和PH值:对于用酸作固化剂的呋喃树脂,酸耗值通常取负值、PH值过高就较难确定酸性固化剂合适的加入量,一般PH值控制在3-6的范围。
3)再生砂反复使用以后,砂粒容易变小,将会影响型砂的透气性,在实际生产过程中,应该多注意观察。
2.3混制工艺1)配比及混制:①混合料配比:呋喃树脂的加入量一般占砂量的0.8~1.5%,而固化剂的加入量占树脂重的20-70%,这可以依据季节的温度变化来调节。
②混制工艺:造型最好采用连续式混砂机混制,一般是将原砂、再生砂、固化剂,树脂依次快速混合而成,要做到随混随用,用间歇式混砂机时,应先加砂,开动混砂机后小心加入固化剂,混拌1-2min之后加入树脂,待混匀后即放砂,制芯采用碗形混砂机,按所制芯的重量大小来选择混砂量的多少。
在呋喃树脂自硬砂配制时,还应对以下几个问题予以足够的重视。
(1)添加剂为了改善酸自硬树脂砂的某些性能,有时在配比中加入一些添加剂。
(2)计量装置为了保证树脂砂性能一致,树脂砂的各种原材料称量要准确。
原砂、树脂及硬化剂的定量装置必须每天在运行生产前进行严格校验,以确保各种组分的计量准确无误。
(3)温度这里所说的温度包括车间环境温度、原砂或再生砂温度以及模具温度。
但是,目前国内生产过程中控制环境温度不容易实现,因此我们能够控制的实际上只有原砂或再生砂温度和模具温度。
(4)可使用时间和脱模时间树脂砂混制时,即开始了树脂的固化反应,如果混制好后停留一段时间再造型,则会将已经交联起来的部分树脂链重新破坏,使得终强度恶化。
所以刚混出的型砂做出的试样强度最高。
树脂砂造型制芯后,必须等型,芯砂建立一定强度后才可起模,否则型和芯将变形和破裂。
2)硬化工艺:树脂砂硬化速度与砂温、环境温度、空气湿度及固化剂的种类加入量的多少都有很大的关系。
①温度:原砂温度最好控制在20-35℃,原砂及工作环境过低,硬化速度会变得很慢,延缓了脱模时间,降低生产效率,而温度过高,可使用的时间过短,砂子的流动性变差,影响了型芯的紧实度,所以应控制好硬化速度,合理的控制好呋喃树脂砂的可使用时间与脱模时间。
3.工艺及现场控制3.1制芯工艺设计:起模斜度相比较而言应比粘土砂大,树脂砂的砂型在起模时,已经具有一定的硬化强度,几乎没有什么退让性,在起模的时候,摩擦力较大,生产现场可通过经验判定起模时间,一般手持钉子向砂型(芯)中扎不进去时,被认为是可以进行起模了,树脂自硬砂起模时不可太早,以免塌型;但也不可太晚,以免脱模阻力过大。
一般情况下不能采用敲击芯盒模样来起模,因此,在制作模样时,应适当增加拔模斜度,保证外观质量的同时也便于起模,除此之外,还应充分考虑自硬砂特性,尽量减少活块,能用砂芯的尽量取消活块,以提高生产效率。
3.2砂箱设计:利用树脂砂硬化后强度高这一特点,在满足有效吃砂量的前提下,减小砂箱尺寸,降低生产成本。
3.3浇冒系统设计:①设计浇冒口的原则是:少设补缩冒口,多设出气和溢流冒口,因为树脂砂型刚度好,浇注初期铸型强度高,有条件利用铸铁凝固过程的石墨化膨胀,有效地消除缩孔,缩松实现灰铸铁,球墨铸铁件的少冒口和无冒口铸造。
②尽量避免在冒口处集中开设浇口,应在提高挡渣和充型能力的前提条件之下,采用分散,径向引入加溢流的方式,横浇口端而开为高梯形,内浇口开设原则为短薄、宽。
③生产重量大的铸件时,浇注系统优先采用陶瓷管制作,防止出现因冲砂造成的砂眼缺陷。
4)与粘土砂相比可以适当的减小加工余量,提高机械加工效率。
3.4现场控制1)造型工序最好使用震实台提高铸型的坚实度,保证型腔的几何形状和铸件的尺寸精度。
2)加强型芯的排气、多设出气孔和气道,在浇注过程中要保证型芯内的气体及时排出型外。
3)应注意刚起模的型芯不能立刻上涂料,因为刚起模的型芯树脂硬化反映还处于初期阶段,如果遇到水基涂料中的水分会影响硬化的正常进行。
如果刷醇基涂料立刻点燃也会使未反应的树脂过烧,影响型芯的表面湿度性。
4)夏天潮湿季节生产的时候,树脂砂型及型芯最好要进行表干处理,以祛除潮气,防止出现因“呛火”引起的气孔缺陷,铸型存放半小时后方可合箱浇注。
5)树脂砂铸件的材质控制:应充分利用树脂砂的保温性,生产过程中应分别采取措施,以确保材质质量。
4.呋喃自硬树脂砂铸件的缺陷分析及防止措施呋喃树脂砂与其它砂型相比,具有铸件缺陷少、废品率低,尺寸精度高,表面光洁,轮廓清晰等优点,但是:如果现场使用不当,也会出现质量问题,有时甚至引起成批报废,主要废品类别及解决措施如下:4.1气孔主要有两种:一是因树脂发气量大,气体来不及排出形成的侵入性气孔。
二是树脂中含氮的化合物,浇注后分解出的原子氮和氢进入铁液,冷凝时溶入的气体来不及析出,形成针孔。
防止措施:在满足型砂(芯砂)使用强度的条件下,降低树脂加入量,再者加强型芯的排气,浇注时应点火引气。
4.2粘砂原因是:树脂在500℃左右时分解,树脂膜被烧蚀、砂与砂之间的间隙增大丧失粘结力,铁液渗入形成机械粘砂。
防止措施为:(1))增加型芯紧实度,(2)厚壁处可采用特殊原砂:如锆英砂、铬铁矿砂、及冷铁等。
(3)刷耐火涂料及适当降低浇注温度,(4) 提高树脂本身耐热性增加糠醇含量等。
(5)在树脂中加入附加物提高热强度如:氧化铁、硼砂等。
4.3热裂:浇注薄壁铸件时,树脂砂型不能被烧透,形成一层坚固的结焦残碳层,阻碍铸件收缩,产生热裂纹。
防止措施;生产时不能只追求高的砂型强度,型芯应采用中空结构,铸型中可填入砂块或埋入塑性好的材料,提高型砂的退让性。
4.4铸件冲砂、夹砂、砂眼铸件在浇注时由于行径内清砂不干净,浇注后形成铸件夹砂,砂眼,再就是浇注时金属液体对浇口的高温冲刷,把浇口壁上的砂冲进行径内,造成铸件夹砂、砂眼。
防止措施:(1)提高型砂强度。
(2)把型腔内散碎砂清除干净。
4.5脉纹脉纹(脉状凸起、飞刺、飞翅)树脂硅砂、型(芯)表层在液态金属的包围下,表面及里面产生很大的温差,石英受热相变热膨胀,与此同时,呋喃树脂受热后其粘结桥突然收缩而脆化破裂,在膨胀收缩应力下导致表层开裂,金属液从裂缝渗入砂层,在铸件上形成毛刺状凸起,称之为“脉纹”它是呋喃树脂自硬砂所特有的一种表面缺陷,多出现在型(芯)拐角处,高温热节处,严重的呈网状分布,轻的只有1-2条存在,而且容易铲去。