生产组织方式的演变
【一周一案】全球生产方式演变:福特制、丰田制与温特制
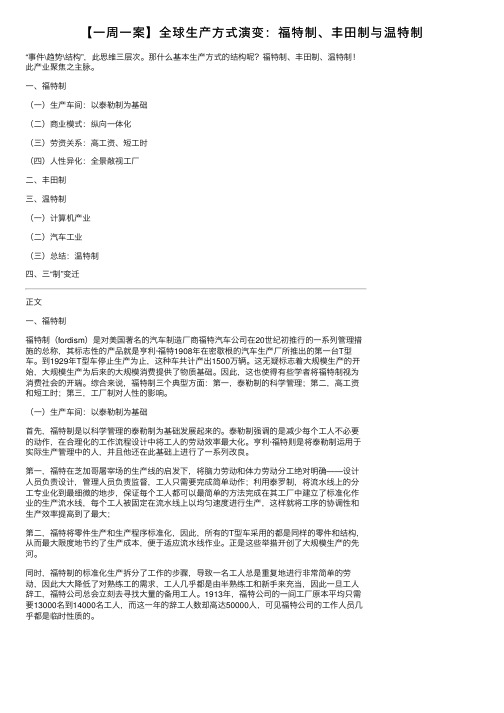
【⼀周⼀案】全球⽣产⽅式演变:福特制、丰⽥制与温特制“事件\趋势\结构”,此思维三层次。
那什么基本⽣产⽅式的结构呢?福特制、丰⽥制、温特制!此产业聚焦之主脉。
⼀、福特制(⼀)⽣产车间:以泰勒制为基础(⼆)商业模式:纵向⼀体化(三)劳资关系:⾼⼯资、短⼯时(四)⼈性异化:全景敞视⼯⼚⼆、丰⽥制三、温特制(⼀)计算机产业(⼆)汽车⼯业(三)总结:温特制四、三“制”变迁正⽂⼀、福特制福特制(fordism)是对美国著名的汽车制造⼚商福特汽车公司在20世纪初推⾏的⼀系列管理措施的总称,其标志性的产品就是亨利·福特1908年在密歇根的汽车⽣产⼚所推出的第⼀台T型车。
到1929年T型车停⽌⽣产为⽌,这种车共计产出1500万辆。
这⽆疑标志着⼤规模⽣产的开始,⼤规模⽣产为后来的⼤规模消费提供了物质基础。
因此,这也使得有些学者将福特制视为消费社会的开端。
综合来说,福特制三个典型⽅⾯:第⼀,泰勒制的科学管理;第⼆,⾼⼯资和短⼯时;第三,⼯⼚制对⼈性的影响。
(⼀)⽣产车间:以泰勒制为基础⾸先,福特制是以科学管理的泰勒制为基础发展起来的。
泰勒制强调的是减少每个⼯⼈不必要的动作,在合理化的⼯作流程设计中将⼯⼈的劳动效率最⼤化。
亨利·福特则是将泰勒制运⽤于实际⽣产管理中的⼈,并且他还在此基础上进⾏了⼀系列改良。
第⼀,福特在芝加哥屠宰场的⽣产线的启发下,将脑⼒劳动和体⼒劳动分⼯绝对明确——设计⼈员负责设计,管理⼈员负责监督,⼯⼈只需要完成简单动作;利⽤泰罗制,将流⽔线上的分⼯专业化到最细微的地步,保证每个⼯⼈都可以最简单的⽅法完成在其⼯⼚中建⽴了标准化作业的⽣产流⽔线,每个⼯⼈被固定在流⽔线上以均匀速度进⾏⽣产,这样就将⼯序的协调性和⽣产效率提⾼到了最⼤;第⼆,福特将零件⽣产和⽣产程序标准化,因此,所有的T型车采⽤的都是同样的零件和结构,从⽽最⼤限度地节约了⽣产成本,便于适应流⽔线作业。
正是这些举措开创了⼤规模⽣产的先河。
几种生产模式的区别

多品种小批量生产生产模式
成组生产 准时化生产(JIT) 精益生产(LP) 敏捷制造 (AM) CIMS
一、 准时化生产方式
“准时化”(JUST IN TIME)——“在必要的时刻生产 必要数量的必要产品或零部件。” “三及时生产系统”——需要的时候,按需要的时间,
零件分 类编码
4-2
成
成
图
组
组
加 工
工
成
艺
组 技
术
的
原
理
提高生产效率、产 品质量、降低成本
2.成组技术的作用——通向CIMS的必由之路
1)简化了生产技术准备工作。 2)为中小批量生产广泛采用高效率设备,为实现自动化
创造了条件。 3)缩短了产品生产周期,提高了按期交货率。 4)促进产品结构及零部件的标准化。
二、 成组生产方式
成组技术为改变多品种小批量生产的传统生产方 式开辟了一条重要的途径,并在工业生产中推广应用, 取得了良好的经济效益。
1.成组技术原理
成组技术将具有相似性的零件汇集成组,实现 成组加工、成组工艺编制,以扩大批量、减少调整 时间,使工序间的搬运和等待时间接近大量生产的 效果,从而大幅度的提高生产效率的一种合理化组 织生产的科学方法。如图4-2所示。
按需要的数量及时进行生产。
消除浪费、减少库存、制止过量、适应市场
1.JIT发展历程 1953年丰田汽车公司首创
2.JIT生产方式的目标
—— 消除生产过程中的浪费
日本人定义7种浪费 (1) 过量生产的浪费 (2) 等待时间造成的浪费 (3)搬运造成的浪费 (4)工艺流程造成的浪费 (5)库存造成的浪费 (6)寻找操作工具造成的浪费 (7)产品缺陷造成的浪费
产业生产组织方式演变的历史进程讲稿
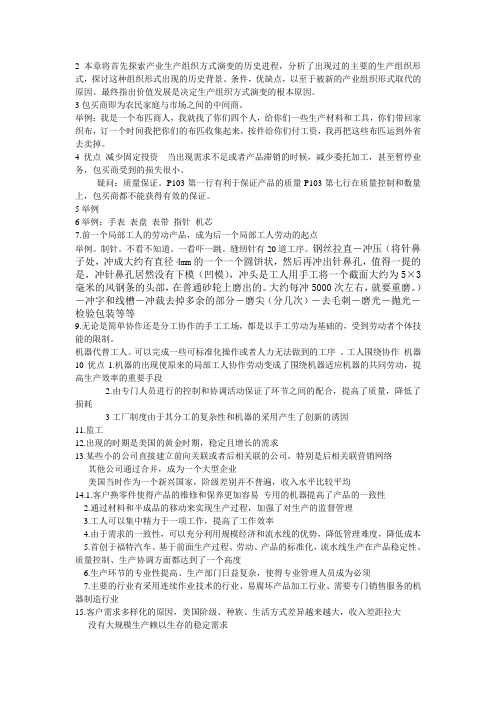
2本章将首先探索产业生产组织方式演变的历史进程,分析了出现过的主要的生产组织形式,探讨这种组织形式出现的历史背景、条件,优缺点,以至于被新的产业组织形式取代的原因。
最终指出价值发展是决定生产组织方式演变的根本原因。
3包买商即为农民家庭与市场之间的中间商。
举例:我是一个布匹商人,我就找了你们四个人,给你们一些生产材料和工具,你们带回家织布,订一个时间我把你们的布匹收集起来,按件给你们付工资,我再把这些布匹运到外省去卖掉。
4优点减少固定投资当出现需求不足或者产品滞销的时候,减少委托加工,甚至暂停业务,包买商受到的损失很小。
疑问:质量保证。
P103第一行有利于保证产品的质量P103第七行在质量控制和数量上,包买商都不能获得有效的保证。
5举例6举例:手表表盘表带指针机芯7.前一个局部工人的劳动产品,成为后一个局部工人劳动的起点举例。
制针。
不看不知道。
一看吓一跳。
缝纫针有20道工序。
钢丝拉直-冲压(将针鼻子处,冲成大约有直径4mm的一个一个圆饼状,然后再冲出针鼻孔,值得一提的是,冲针鼻孔居然没有下模(凹模),冲头是工人用手工将一个截面大约为5×3毫米的风钢条的头部,在普通砂轮上磨出的。
大约每冲5000次左右,就要重磨。
)-冲字和线槽-冲裁去掉多余的部分-磨尖(分几次)-去毛刺-磨光-抛光-检验包装等等9.无论是简单协作还是分工协作的手工工场,都是以手工劳动为基础的,受到劳动者个体技能的限制。
机器代替工人。
可以完成一些可标准化操作或者人力无法做到的工序。
工人围绕协作机器10优点1.机器的出现使原来的局部工人协作劳动变成了围绕机器适应机器的共同劳动,提高生产效率的重要手段2.由专门人员进行的控制和协调活动保证了环节之间的配合,提高了质量,降低了损耗3工厂制度由于其分工的复杂性和机器的采用产生了创新的诱因11.监工12.出现的时期是美国的黄金时期,稳定且增长的需求13.某些小的公司直接建立前向关联或者后相关联的公司,特别是后相关联营销网络其他公司通过合并,成为一个大型企业美国当时作为一个新兴国家,阶级差别并不普遍,收入水平比较平均14.1.客户换零件使得产品的维修和保养更加容易专用的机器提高了产品的一致性2.通过材料和半成品的移动来实现生产过程,加强了对生产的监督管理3.工人可以集中精力于一项工作,提高了工作效率4.由于需求的一致性,可以充分利用规模经济和流水线的优势,降低管理难度,降低成本5.首创于福特汽车、基于前面生产过程、劳动、产品的标准化,流水线生产在产品稳定性、质量控制、生产协调方面都达到了一个高度6.生产环节的专业性提高、生产部门日益复杂,使得专业管理人员成为必须7.主要的行业有采用连续作业技术的行业、易腐坏产品加工行业、需要专门销售服务的机器制造行业15.客户需求多样化的原因,美国阶级、种族、生活方式差异越来越大,收入差距拉大没有大规模生产赖以生存的稳定需求16 演员(英国、美国、日本)剧本(工厂制度大规模生产模式大规模定制)技术创新扮演了重要的角色是一家造纸厂兼并了另一家因为经营不善濒临破产的造纸厂,这是规模经济;要是兼并对象是一家印刷厂,这就是范围经济。
第一次工业革命 第二次工业革命 资本主义世界市场

第7课第一次工业革命一、工业革命——“蒸汽时代”1、前提与条件⑴前提:18世纪时,随着资本主义制度的进一步发展,社会稳定,英国经济迅速发展。
⑵条件:①市场:殖民地提供广阔的海外市场,资本主义的发展,迫切需求技术创新(根本)②劳动力:圈地运动使得很多农民被迫离开土地,去工场做工。
③技术:手工工场日益兴旺,生产技术进一步发展。
④资本:殖民贸易和掠夺。
2、进程:⑴开始——时间:18世纪60年代地点:英国部门:棉纺织业———冶金—采煤①生产:18世纪60年代,哈格里夫斯发明“珍妮纺纱机”②动力:1785年,瓦特改良蒸汽机,工业革命进入新阶段③运输:1807年美国人富尔敦发明汽船,1814年英国人史蒂芬孙发明火车机车⑵扩展:欧洲大陆和美国⑶完成:1840年前后,英法美相继完成。
标志:机器生产取代手工劳动(机器制造机器)二、影响A、对资本主义国家的影响⑴经济:①生产力:极大提高社会生产力,英国成为“世界工厂”。
②生产组织形式:传统的手工工场被工厂所取代,成为工业生产的主要组织形式。
③经济结构:工业文明取代农业文明。
④生活方式:城市化进程明显加快⑤阶级关系:工业资产阶级和工业无产阶级成为社会的两大阶级。
⑵政治:工业资产阶级获得更多的政治权利,各国通过改革,巩固了资产阶级的统治。
⑶思想:自由经营、自由竞争和自由贸易。
重商主义被自由放任政策所取代。
⑷世界市场:殖民扩张和殖民掠夺的加快,世界市场基本形成。
B、对世界市场的影响——世界市场基本形成1、原因条件⑴经济:资产阶级竭力在全世界拓展市场,抢占原料产地,使世界贸易的范围和规模迅速扩大⑵交通:蒸汽机车和轮船的出现,改变了交通运输条件,世界各地间的联系更为便捷。
⑶政治:资产阶级凭借着强大经济和军事实力,把亚非拉纳入资本主义世界市场之中。
2、基本形成:19世纪中后期,英国成为世界工厂和贸易中心。
以欧美资本主义国家为主导的世界市场基本形成。
C、对世界的影响1)工业革命大大提高了社会生产力,使人类进入到了“蒸汽时代”2)工业革命改变了人类的生产方式和生存状态,传播了先进的思想和生产方式,开始改变世界的面貌3)工业革命还带来社会经济结构形式的变化,世界市场基本形成,工业文明逐渐成为社会的主导。
生产方式演变及发展趋势

八种生产方式形态
作坊生产 工场式生产
批量生产 流水生产
&1820年奥斯特发现电流磁效应 &安培提出电流相互作用定律 &1831年法拉第提出电磁感应定律 &1864年麦克斯韦尔电磁场理论的建立 &电气化改变了机器结构 &机器在动力学、运动学上的无可比拟 优越性 &产品的批量也得到了提高 &企业也从批量生产中获得了“规模效益 &“造得多”取代“能制造”开始成为最重 要策略。
八种生产方式形态
大量生产 高质量生产
快速生产 大规模定制
& 微电子、计算机技术的发展,为设计、制造和 营销过程的信息管理与计算机辅助设计制造创造 了前所未有的条件 & 近代制造技术及其自动化的发展,为先进制造 技术积累了现代工艺和管理文明 & 运筹学、专家系统、仿真技术和人工智能等发 展,为制造技术走向智能化创造了技术前提 & 先进的工艺如精密成型,超精密加工、精细焊 接、表面技术和在线检测技术的发展为制造技术 提供了新的工艺基础。 & 通过企业严格的内部分工和高度专业化操作、 塔形多层次的垂直领导以及严格的生产节拍控制 &“有人要”已成为新的生产策略
精益生产模式的发展和特征
在以福特公司为代表的福特制生产组织市场份额下 降、利润率减少时, 日本汽车公司的生产率、市场占 率和利润水平却在不断上升, 并在1980年突破1000万 大关, 成为世界汽车第一制造大国。
1985年美国麻省理工学院的Danie l Ross教授等 资500万美元, 用了近5年的时间对90多家汽车厂进行 考察, 将福特制与丰田生产方式进行了对比分析, 提 精益生产的生产组织概念 。
精益生产与日本制造业的兴盛
从“福特制”到“丰田制”的演变
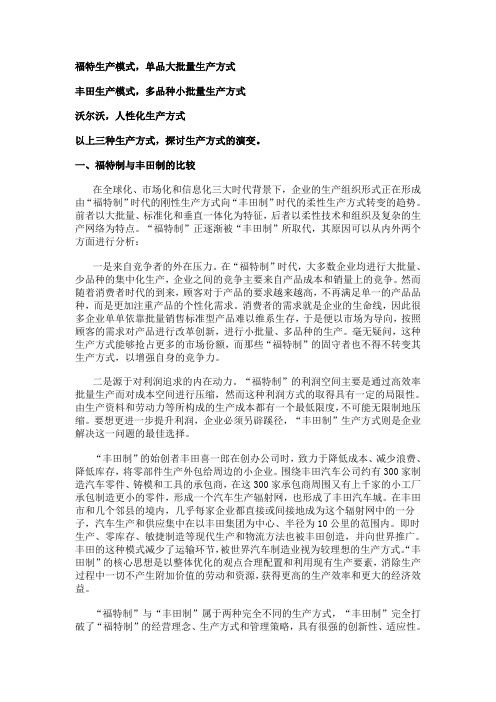
福特生产模式,单品大批量生产方式丰田生产模式,多品种小批量生产方式沃尔沃,人性化生产方式以上三种生产方式,探讨生产方式的演变。
一、福特制与丰田制的比较在全球化、市场化和信息化三大时代背景下,企业的生产组织形式正在形成由“福特制”时代的刚性生产方式向“丰田制”时代的柔性生产方式转变的趋势。
前者以大批量、标准化和垂直一体化为特征,后者以柔性技术和组织及复杂的生产网络为特点。
“福特制”正逐渐被“丰田制”所取代,其原因可以从内外两个方面进行分析:一是来自竞争者的外在压力。
在“福特制”时代,大多数企业均进行大批量、少品种的集中化生产,企业之间的竞争主要来自产品成本和销量上的竞争。
然而随着消费者时代的到来,顾客对于产品的要求越来越高,不再满足单一的产品品种,而是更加注重产品的个性化需求。
消费者的需求就是企业的生命线,因此很多企业单单依靠批量销售标准型产品难以维系生存,于是便以市场为导向,按照顾客的需求对产品进行改革创新,进行小批量、多品种的生产。
毫无疑问,这种生产方式能够抢占更多的市场份额,而那些“福特制”的固守者也不得不转变其生产方式,以增强自身的竞争力。
二是源于对利润追求的内在动力。
“福特制”的利润空间主要是通过高效率批量生产而对成本空间进行压缩,然而这种利润方式的取得具有一定的局限性。
由生产资料和劳动力等所构成的生产成本都有一个最低限度,不可能无限制地压缩。
要想更进一步提升利润,企业必须另辟蹊径,“丰田制”生产方式则是企业解决这一问题的最佳选择。
“丰田制”的始创者丰田喜一郎在创办公司时,致力于降低成本、减少浪费、降低库存,将零部件生产外包给周边的小企业。
围绕丰田汽车公司约有300家制造汽车零件、铸模和工具的承包商,在这300家承包商周围又有上千家的小工厂承包制造更小的零件,形成一个汽车生产辐射网,也形成了丰田汽车城。
在丰田市和几个邻县的境内,几乎每家企业都直接或间接地成为这个辐射网中的一分子,汽车生产和供应集中在以丰田集团为中心、半径为10公里的范围内。
历史上的生产组织形式
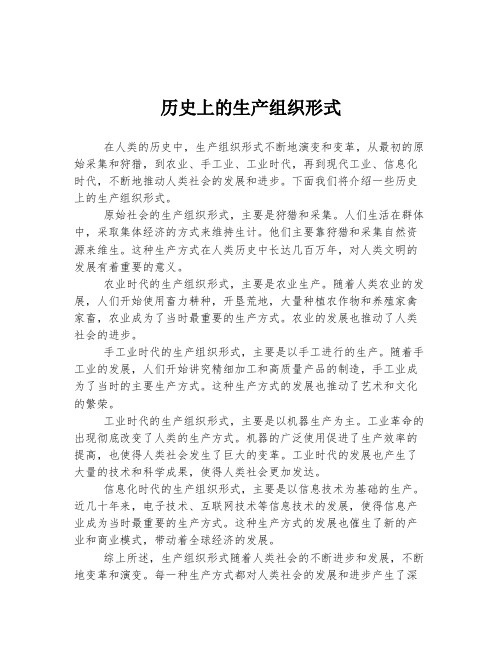
历史上的生产组织形式在人类的历史中,生产组织形式不断地演变和变革,从最初的原始采集和狩猎,到农业、手工业、工业时代,再到现代工业、信息化时代,不断地推动人类社会的发展和进步。
下面我们将介绍一些历史上的生产组织形式。
原始社会的生产组织形式,主要是狩猎和采集。
人们生活在群体中,采取集体经济的方式来维持生计。
他们主要靠狩猎和采集自然资源来维生。
这种生产方式在人类历史中长达几百万年,对人类文明的发展有着重要的意义。
农业时代的生产组织形式,主要是农业生产。
随着人类农业的发展,人们开始使用畜力耕种,开垦荒地,大量种植农作物和养殖家禽家畜,农业成为了当时最重要的生产方式。
农业的发展也推动了人类社会的进步。
手工业时代的生产组织形式,主要是以手工进行的生产。
随着手工业的发展,人们开始讲究精细加工和高质量产品的制造,手工业成为了当时的主要生产方式。
这种生产方式的发展也推动了艺术和文化的繁荣。
工业时代的生产组织形式,主要是以机器生产为主。
工业革命的出现彻底改变了人类的生产方式。
机器的广泛使用促进了生产效率的提高,也使得人类社会发生了巨大的变革。
工业时代的发展也产生了大量的技术和科学成果,使得人类社会更加发达。
信息化时代的生产组织形式,主要是以信息技术为基础的生产。
近几十年来,电子技术、互联网技术等信息技术的发展,使得信息产业成为当时最重要的生产方式。
这种生产方式的发展也催生了新的产业和商业模式,带动着全球经济的发展。
综上所述,生产组织形式随着人类社会的不断进步和发展,不断地变革和演变。
每一种生产方式都对人类社会的发展和进步产生了深远的影响。
未来,我们能否创造出更为先进、高效和可持续的生产方式,是人类社会需要不断探索的重要课题。
生产方式演变及发展趋势

2013年6月 哈尔滨
李凤霄
硕士研究生 研究员级高工
生产业6S管理审核员
六西格玛黑带大师(MBB)
全国六西格玛管理推进委员会委员
卓越绩效模式(质量奖)评审员
6S、精益现场管理资深咨询师
技术创新理论(TRIZ)培训师
质量体系(AS9100、TS16949、IRIS等)咨询师
生产方式形态四分法
手工单件生产
典型的手工生产
大批量生产 多品种小批量生产
大规模定制
福特流水线 丰田生产方式
?
柔性生产 刚性生产 手工生产
生产方式变迁
生产方式变迁
大规模定制
多品种小 批量生产
大批量生产
手工单件生产
农业经济
工业经济
知识经济
1
2
3
生产方式演变的一般规律
4
5
6
新型生产方式具备的特征
顺应经济发展 的客观规律, 适应市场需求
精益生产模式的发展和特征
在以福特公司为代表的福特制生产组织市场份额下 降、利润率减少时, 日本汽车公司的生产率、市场占 率和利润水平却在不断上升, 并在1980年突破1000万 大关, 成为世界汽车第一制造大国。
1985年美国麻省理工学院的Danie l Ross教授等 资500万美元, 用了近5年的时间对90多家汽车厂进行 考察, 将福特制与丰田生产方式进行了对比分析, 提 精益生产的生产组织概念 。
八种生产方式形态
大量生产 高质量生产
快速生产 大规模定制
& 20世纪80年代,世界上发生了严重的债务危机 & 发达国家积极在国外开设工厂 & 竞争环境激化,对质量的要求不断提高 & 超大规模集成电路的发展,电子计算机的出现 & 以人机一体智能化为特征的后发展时期 & 机电学(Mechtronics)和机电一体化(NC、CAD 、CAM)的时代
马克思主 义生产方式的历史演变

马克思主义生产方式的历史演变生产方式是人类社会赖以生存和发展的基础,它决定着社会的性质和面貌。
马克思主义认为,生产方式包括生产力和生产关系两个方面,生产力是生产方式的物质内容,生产关系则是生产方式的社会形式。
在人类社会的发展进程中,马克思主义生产方式经历了一系列的历史演变。
在原始社会,生产力水平极其低下,人们主要依靠简单的石器工具和集体劳动来获取生活资料。
生产关系是以原始公有制为基础的,人们共同劳动、平均分配,没有剥削和压迫。
由于生产力的限制,人们的生产活动仅仅是为了满足最基本的生存需求。
随着生产力的发展,特别是金属工具的出现和农业的兴起,人类社会进入了奴隶社会。
在奴隶社会,奴隶主占有生产资料和奴隶本身,奴隶完全没有人身自由,被强制劳动,劳动成果全部归奴隶主所有。
这种生产关系适应了当时生产力的发展水平,使得社会分工进一步细化,农业、手工业和商业都有了一定的发展。
封建社会取代奴隶社会是生产方式发展的必然结果。
在封建社会,地主占有土地等生产资料,农民租种地主的土地,向地主缴纳地租,并在一定程度上拥有自己的生产工具和劳动成果。
封建社会的生产力有了较大的提高,铁制农具得到广泛应用,水利灌溉技术不断改进,农业生产得到进一步发展。
同时,手工业和商业也逐渐繁荣起来。
资本主义生产方式的出现是人类社会发展的一个重大转折。
资本主义生产方式以机器大工业为基础,以资本家占有生产资料、雇佣工人劳动并获取剩余价值为特征。
资本主义极大地推动了生产力的发展,创造了巨大的物质财富。
工业革命使得生产技术和生产组织方式发生了根本性变革,工厂制度取代了手工工场,机器生产取代了手工劳动,生产效率大幅提高。
同时,资本主义的市场经济体制促进了资源的优化配置和商品的流通。
然而,资本主义生产方式也存在着内在的矛盾和弊端。
生产的社会化与生产资料的私人占有之间的矛盾是资本主义的基本矛盾,这一矛盾导致了经济危机的周期性爆发,给社会带来了巨大的破坏。
同时,资本主义社会存在着严重的贫富分化和阶级对立,工人阶级受到资本家的剥削和压迫。
(生产管理知识)全球生产组织方式发生重大变化

全球生产组织方式发生重大变化对可口可乐生产过程的研究表明,从铝矾土的采掘开始到制成易拉罐,制造可口可乐的原汁,加水,再把它装到罐里,销售出去,直到顾客把它放到家中的冰箱,一共要花费319天,而实际创造价值,即加工制造所花的时间只有3小时。
其余318天21小时干什么了?答案是用于为交易而运输和储存原材料和成品。
这就是说,在整个生产过程中,产品加工制造所需的时间大大少于产品和原材料交易所需的时间。
据调查,在西欧制造业企业,纯粹的加工制造时间只占整个生产过程所需时间的2%,原材料、零部件和制成品的运输时间占5%,其余93%的时间是生产准备和产品交易的时间。
显然,要节约成本,在只有2%的加工制造时间上下工夫,难度已经相当大,在其余93%的时间上下工夫的余地则很大,即节约交易成本对增加企业利润的作用更大。
价值链与全球生产体系的形成工业革命以来,根据技术进步的特点改善生产组织方式是推动经济发展的动力。
技术进步催生了流水线生产方法,企业的生产组织方式发生了根本变化,由此产生的大规模生产方式刺激了美国经济的增长,也推动了二次战后西欧和日本的经济复苏和发展。
这种方式使企业变得越来越大。
一个企业囊括了生产价值链的所有过程,即产品研发、加工制造、生产和财务管理、市场营销和售后服务。
20世纪80年代以来,世界经济进入网络化的新阶段。
说起网络,有人认为它不过是一个虚拟的世界。
其实不然,所谓世界经济网络化,不仅指互联网的应用,也指全球生产体系的形成。
生产组织方式的变化不是局限在一个企业之内,也没有拘泥于一个国家之内。
原来存在于一个企业的生产价值链的不同过程分布到全球不同国家的不同企业,它们密切合作,形成了相互协调的网络。
第一,企业摆脱了大而全的困扰,使单个企业的能力集中于核心能力。
例如,耐克制鞋公司在美国的总部把业务集中在研究和开发,把制鞋生产转移给其他企业。
它选择合作对象的标准是生产能力。
瑞士航空公司把票务中心转移到印度,它看中的是印度的软件开发和管理能力。
资本主义生产组织演变的整体性解读与反思
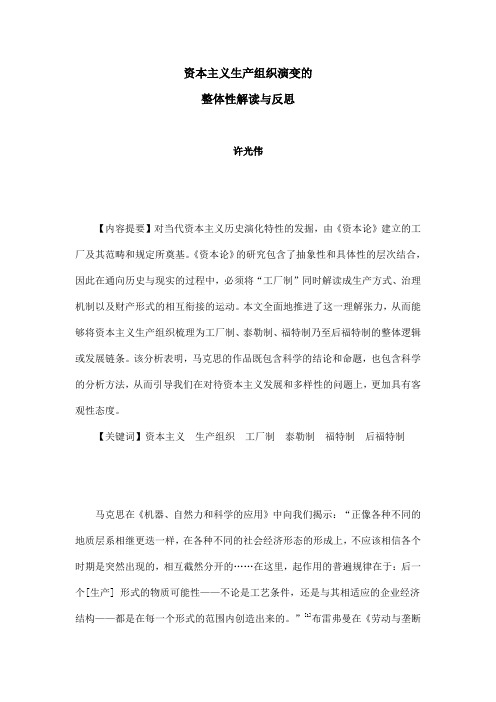
资本主义生产组织演变的整体性解读与反思许光伟【内容提要】对当代资本主义历史演化特性的发掘,由《资本论》建立的工厂及其范畴和规定所奠基。
《资本论》的研究包含了抽象性和具体性的层次结合,因此在通向历史与现实的过程中,必须将“工厂制”同时解读成生产方式、治理机制以及财产形式的相互衔接的运动。
本文全面地推进了这一理解张力,从而能够将资本主义生产组织梳理为工厂制、泰勒制、福特制乃至后福特制的整体逻辑或发展链条。
该分析表明,马克思的作品既包含科学的结论和命题,也包含科学的分析方法,从而引导我们在对待资本主义发展和多样性的问题上,更加具有客观性态度。
【关键词】资本主义生产组织工厂制泰勒制福特制后福特制马克思在《机器、自然力和科学的应用》中向我们揭示:“正像各种不同的地质层系相继更迭一样,在各种不同的社会经济形态的形成上,不应该相信各个时期是突然出现的,相互截然分开的……在这里,起作用的普遍规律在于:后一个[生产] 形式的物质可能性——不论是工艺条件,还是与其相适应的企业经济结构——都是在每一个形式的范围内创造出来的。
”[1]布雷弗曼在《劳动与垄断资本》的导言中强调:马克思从来不对历史研究采取一种公式主义的态度,从来不随意玩弄无遮无盖的相互关系,“一对一的关系”,也不愚蠢地打算通过极度简单化的做法来掌握历史。
因此,社会的确定性并不具备化学反应的固定性,而是一种历史过程;就是说,社会的具体而确定的形式确实是“确定的”,不是偶然的,但这是一条线、一条线把历史这块织物编织起来的那种确定性,决不是硬塞进一些外来的公式[2]。
这是一种正确对待历史发展和进行研究的方法。
本文试图运用由这一方法所确定的分析体式,具体完成对于资本主义生产组织的考察,重构资本主义发展的真实图景。
一、工厂制在考察18世纪的产业革命时,法国史学家芒图说:“所谓大工业,首先必须将其理解成一种组织、一种生产制度。
但是,它的作用却影响到整个经济制度,从而也影响到社会制度,而社会制度则是由财富的增殖条件和分配条件所统治的。
企业组织结构模式类型及历史演变

企业组织结构模式类型及历史演变1、U型组织结构19世纪末20世纪初,西方大企业普遍采用的是一种按职能划分部门的纵向一体化的职能结构,即U型结构。
特点是企业内部按职能(如生产、销售、开发等)划分成若干部门,各部门独立性很小,均由企业高层领导直接进行管理,即企业实行集中控制和统一指挥。
U型结构保持了直线制的集中统一指挥的优点,并吸收了职能制发挥专业管理职能作用的长处。
适用于市场稳定、产品品种少、需求价格弹性较大的环境。
但是,从20世纪初开始,西方企业的外部环境发生了很大的变化,如原有市场利润率出现下降、新的技术发明不断产生等,同时企业规模不断扩大,使这种结构的缺陷日渐暴露:高层领导们由于陷入了日常生产经营活动,缺乏精力考虑长远的战略发展,且行政机构越来越庞大,各部门协调越来越难,造成信息和管理成本上升。
到20世纪初,通用汽车公司针对这种结构的缺陷,首先在公司内部进行组织结构的变革,采用M型组织结构,此后,许多大公司都仿效。
2、M型组织结构M型组织结构,又称事业部门型组织结构。
这种结构的基本特征是,战略决策和经营决策分离。
根据业务按产品、服务、客户、地区等设立半自主性的经营事业部,公司的战略决策和经营决策由不同的部门和人员负责,使高层领导从繁重的日常经营业务中解脱出来,集中精力致力于企业的长期经营决策,并监督、协调各事业部的活动和评价各部门的绩效。
与U型结构相比较,M型结构具有治理方面的优势,且适合现代企业经营发展的要求。
M型组织结构是一种多单位的企业体制,但各个单位不是独立的法人实体,仍然是企业的内部经营机构,如分公司。
3、矩阵制结构在组织结构上,把既有按职能划分的垂直领导系统,又有按产品(项目)划分的横向领导关系的结构,称为矩阵组织结构。
矩阵制组织是为了改进直线职能制横向联系差,缺乏弹性的缺点而形成的一种组织形式。
它把按职能划分的部门与按项目划分的小组结合起来组成矩阵,使小组成员接受小组和职能部门的双重领导。
历次工业革命与组织模式演进
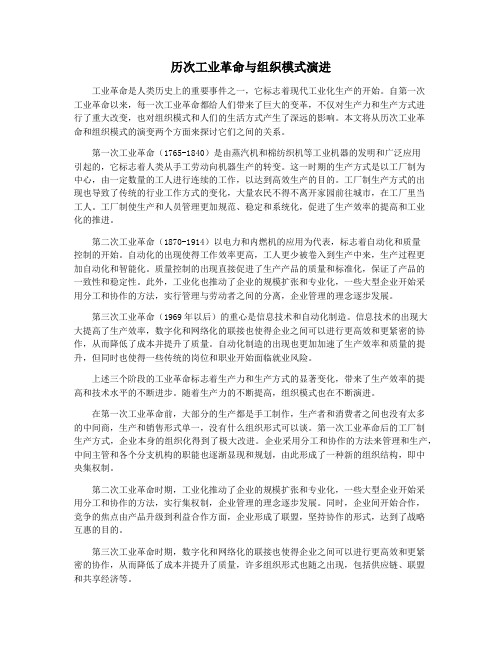
历次工业革命与组织模式演进工业革命是人类历史上的重要事件之一,它标志着现代工业化生产的开始。
自第一次工业革命以来,每一次工业革命都给人们带来了巨大的变革,不仅对生产力和生产方式进行了重大改变,也对组织模式和人们的生活方式产生了深远的影响。
本文将从历次工业革命和组织模式的演变两个方面来探讨它们之间的关系。
第一次工业革命(1765-1840)是由蒸汽机和棉纺织机等工业机器的发明和广泛应用引起的,它标志着人类从手工劳动向机器生产的转变。
这一时期的生产方式是以工厂制为中心,由一定数量的工人进行连续的工作,以达到高效生产的目的。
工厂制生产方式的出现也导致了传统的行业工作方式的变化,大量农民不得不离开家园前往城市,在工厂里当工人。
工厂制使生产和人员管理更加规范、稳定和系统化,促进了生产效率的提高和工业化的推进。
第二次工业革命(1870-1914)以电力和内燃机的应用为代表,标志着自动化和质量控制的开始。
自动化的出现使得工作效率更高,工人更少被卷入到生产中来,生产过程更加自动化和智能化。
质量控制的出现直接促进了生产产品的质量和标准化,保证了产品的一致性和稳定性。
此外,工业化也推动了企业的规模扩张和专业化,一些大型企业开始采用分工和协作的方法,实行管理与劳动者之间的分离,企业管理的理念逐步发展。
第三次工业革命(1969年以后)的重心是信息技术和自动化制造。
信息技术的出现大大提高了生产效率,数字化和网络化的联接也使得企业之间可以进行更高效和更紧密的协作,从而降低了成本并提升了质量。
自动化制造的出现也更加加速了生产效率和质量的提升,但同时也使得一些传统的岗位和职业开始面临就业风险。
上述三个阶段的工业革命标志着生产力和生产方式的显著变化,带来了生产效率的提高和技术水平的不断进步。
随着生产力的不断提高,组织模式也在不断演进。
在第一次工业革命前,大部分的生产都是手工制作,生产者和消费者之间也没有太多的中间商,生产和销售形式单一,没有什么组织形式可以谈。
资本主义经济发展阶段及生产组织形式的变化

资本主义经济发展阶段及生产组织形式的变化Capitalism, as an economic system, has gone throughdifferent stages of development and witnessed various changes in its modes of production. Throughout history, capitalism has evolved in response to changing social and technological factors, leading to shifts in theorganization of production and the dynamics of the economy.资本主义作为一个经济体系,在其发展的过程中经历了不同的阶段,并且见证了生产组织形式的各种变化。
在整个历史中,资本主义系统根据社会和技术因素的变化而不断演进,导致了生产组织方式和经济动态的转变。
One significant landmark in the development of capitalismis the transition from early merchant capitalism toindustrial capitalism. In the late 18th century, the Industrial Revolution brought about significant advancements in technology and machinery, such as steam power and mechanization. This led to a profound shift away from an economy dominated by small-scale artisan workshopsand guilds towards large-scale factory production. The emergence of factories marked a change in the mode of production, where capitalists now owned means of production and hired workers to operate machines.资本主义发展中的一个重要里程碑是从早期商业资本主义向工业资本主义的转变。
生产方式
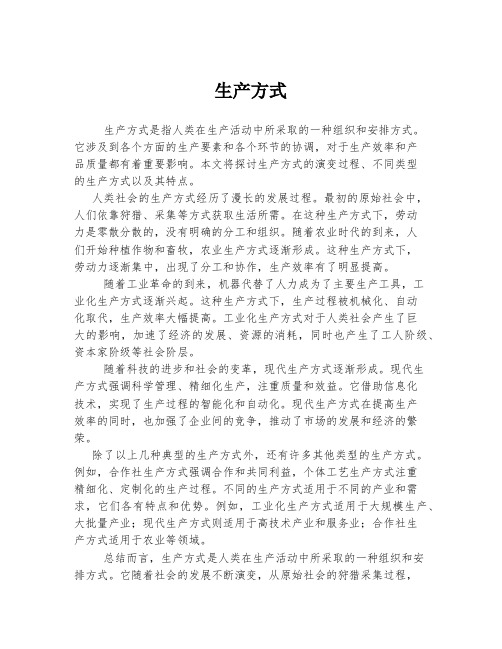
生产方式生产方式是指人类在生产活动中所采取的一种组织和安排方式。
它涉及到各个方面的生产要素和各个环节的协调,对于生产效率和产品质量都有着重要影响。
本文将探讨生产方式的演变过程、不同类型的生产方式以及其特点。
人类社会的生产方式经历了漫长的发展过程。
最初的原始社会中,人们依靠狩猎、采集等方式获取生活所需。
在这种生产方式下,劳动力是零散分散的,没有明确的分工和组织。
随着农业时代的到来,人们开始种植作物和畜牧,农业生产方式逐渐形成。
这种生产方式下,劳动力逐渐集中,出现了分工和协作,生产效率有了明显提高。
随着工业革命的到来,机器代替了人力成为了主要生产工具,工业化生产方式逐渐兴起。
这种生产方式下,生产过程被机械化、自动化取代,生产效率大幅提高。
工业化生产方式对于人类社会产生了巨大的影响,加速了经济的发展、资源的消耗,同时也产生了工人阶级、资本家阶级等社会阶层。
随着科技的进步和社会的变革,现代生产方式逐渐形成。
现代生产方式强调科学管理、精细化生产,注重质量和效益。
它借助信息化技术,实现了生产过程的智能化和自动化。
现代生产方式在提高生产效率的同时,也加强了企业间的竞争,推动了市场的发展和经济的繁荣。
除了以上几种典型的生产方式外,还有许多其他类型的生产方式。
例如,合作社生产方式强调合作和共同利益,个体工艺生产方式注重精细化、定制化的生产过程。
不同的生产方式适用于不同的产业和需求,它们各有特点和优势。
例如,工业化生产方式适用于大规模生产、大批量产业;现代生产方式则适用于高技术产业和服务业;合作社生产方式适用于农业等领域。
总结而言,生产方式是人类在生产活动中所采取的一种组织和安排方式。
它随着社会的发展不断演变,从原始社会的狩猎采集过程,到农业时代的种植畜牧,再到工业化和现代化的生产方式,每一种生产方式都带来了不同的社会和经济效果。
各种不同的生产方式存在着不同的特点和优势,应根据不同的产业和需求加以选择和应用。
只有合理选择和科学运用生产方式,才能进一步提高生产效率,实现经济的可持续发展。
生产方式的演变过程
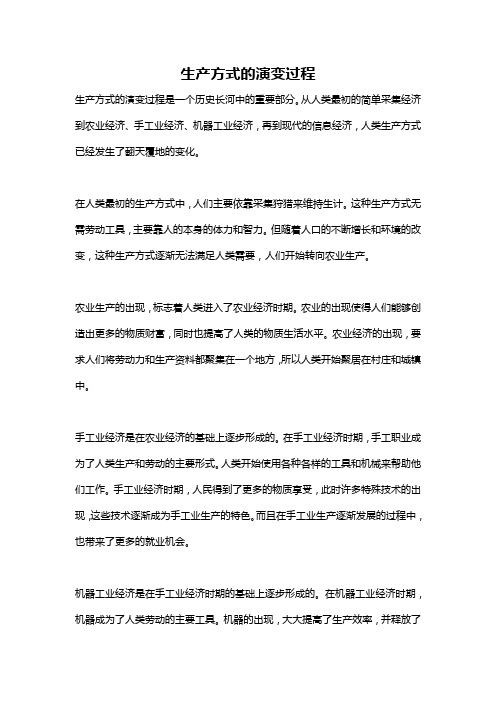
生产方式的演变过程生产方式的演变过程是一个历史长河中的重要部分。
从人类最初的简单采集经济到农业经济、手工业经济、机器工业经济,再到现代的信息经济,人类生产方式已经发生了翻天覆地的变化。
在人类最初的生产方式中,人们主要依靠采集狩猎来维持生计。
这种生产方式无需劳动工具,主要靠人的本身的体力和智力。
但随着人口的不断增长和环境的改变,这种生产方式逐渐无法满足人类需要,人们开始转向农业生产。
农业生产的出现,标志着人类进入了农业经济时期。
农业的出现使得人们能够创造出更多的物质财富,同时也提高了人类的物质生活水平。
农业经济的出现,要求人们将劳动力和生产资料都聚集在一个地方,所以人类开始聚居在村庄和城镇中。
手工业经济是在农业经济的基础上逐步形成的。
在手工业经济时期,手工职业成为了人类生产和劳动的主要形式。
人类开始使用各种各样的工具和机械来帮助他们工作。
手工业经济时期,人民得到了更多的物质享受,此时许多特殊技术的出现,这些技术逐渐成为手工业生产的特色。
而且在手工业生产逐渐发展的过程中,也带来了更多的就业机会。
机器工业经济是在手工业经济时期的基础上逐步形成的。
在机器工业经济时期,机器成为了人类劳动的主要工具。
机器的出现,大大提高了生产效率,并释放了更多的人力资源。
这一时期,印刷、化学、电力和交通的发明,使得经济和文化都得到了前所未有的发展。
此外,在机器工业的时代中工人开始组织工会,争取工人的权益,这也成为了现代劳工运动的基础。
现代的信息经济是在机器工业经济的基础上建立的经济模式。
在这个时代,信息传递和高科技产品成为了经济发展的主要驱动力。
计算机和网络技术的使用,使得生产、销售和分配这些经济活动变得更加高效和便捷。
此时,人们可以通过远程办公、视频会议和电子支付等实现全球交流。
现代信息经济的建立,使得人类经济和文化发展更加快速和全面。
总之,人类生产方式的演变告诉我们,人类社会是在不断发展的。
生产方式的演变,反映了社会生产和生活水平的提高,同时也将影响到日后的社会发展。
- 1、下载文档前请自行甄别文档内容的完整性,平台不提供额外的编辑、内容补充、找答案等附加服务。
- 2、"仅部分预览"的文档,不可在线预览部分如存在完整性等问题,可反馈申请退款(可完整预览的文档不适用该条件!)。
- 3、如文档侵犯您的权益,请联系客服反馈,我们会尽快为您处理(人工客服工作时间:9:00-18:30)。
生产组织方式的演变
人类对生产的组织最早可以追溯到古代手工作坊式的生产。
近代,产业革命的兴起和科学管理理念的发展为生产系统组织形式的创新创造了条件。
20世纪初,福特汽车公司创立了大量流水生产方式,使得创造物质财富的能力大大增强。
第二次世界大战后,大批量流水线的专业化生产系统和成批生产系统以及单件小批生产系统,是人们生产制造过程中的主要生产组织形式。
到了20世纪60年代,随着顾客对于产品要求的多元化和个性化程度的不断提高,对生产系统的适应性和集成性提出了新的要求,数控机床和加工中心的产生为生产组织形式的变革提供了技术支持,柔性制造系统应运而生。
同时,丰田汽车公司的大野耐一和丰田英二在研究了以往汽车制造的经验和日本自身国情的基础上,创立了丰田生产方式TPS(Toyota production system)。
20世纪70年代计算机技术的发展使得MRP(material requirement planning)实施成为现实,而后人们不断地改进和完善,逐步使其发展为MRPⅡ(manufacturing resource planning)和ERP(enterprise resource planning)系统。
进入80年代,生产领域的效益依赖于管理水平的提高,追求系统的综合管理效益并配有自动化、现代化、信息化的计算机辅助管理系统,CIMS正是应科技与生产的发展需要而产生的。
下面对上述生产方式作一一介绍。
1.福特的大量流水生产方式
在福特公司创立大量流水生产方式之前,汽车行业的生产都是以单件小批量生产方式进行的。
单件小批量生产对工人的技术有很高的要求,供应商提供的零件不规范不统一,这样使得每一辆车都不能做到标准化和统一化,并且高成本使得当时的汽车成为贵族显示尊贵的工具,而不能为普通百姓带来便利。
亨利.福特于1903年创立福特汽车公司,他认为影响汽车业生产效率的原因主要来自三个方面:产品结构的复杂性、零件之间的通用性和工人之间技术水平的差异性。
并由此提出了汽车制造行业的所谓“3S”,即标准化、简单化、专门化。
在产品标准化的前提下,进一步发展为零部件的标准化。
同时引入传送带式流水生产线,使得工人的作业得到细分,降低了对于工人技术水平的要求,使其工作也得到标准化。
到1920年,T型福特车的成本降到了1908年刚开始生产时的三分之一,使得福特公司成为当时汽车领域的主宰。
事务总是有其两面性,大量流水生产也有其致命的弱点,它不能适应市场需求的变化,产品品种过于单一,员工的技术含量要求过低且重复性过高,从而极大地影响了员工的积极性和创新性。
在1921年创造了年产210万辆的辉煌后,福特汽车公司逐渐在与通用汽车等其他公司的竞争中处于下风,到1930年甚至跌倒了破产的边缘。
2.丰田生产方式
战后的日本汽车工业刚刚起步,丰田汽车公司的管理者充分考虑到当时国内国外的情况,与美国相比,日本没有如此巨大的市场需求,并且当时的日本企业也没有足够的资金来投入大规模的厂房设备建设和进行大规模的批量生产,这就使丰田的领导者下决心探索出一条适合于自己企业发展的新路子。
丰田公司的大野耐一和丰田英二在研究了美国大规模生产之后,发明出了一种与福特的大规模生产大相径庭的生产方式。
这种生产方式以小批量的灵活性生产来满足市场的需求变化,同时彻底地杜绝一切浪费,丰田生产方式由此产生。
随着世界石油危机的到来,日本的汽车以其对市场的灵活应变生产出了成本低、质量高、耗油少的经济型汽车,一举打进了美国市场,从此丰田生产方式也在世界范围内开始普及。
丰田人在不断地摸索和探求中,发明了一系列新型的管理理念和管理方法,如JIT、看板管理、生产的标准化、均衡化、快速换模、全面生产维护、标准作业等,极大地丰富了生产管理的内容。
3.MRP和ERP
物料需求计划MRP(material requirement planning)于20世纪60年代在美国首先提出,70年代开始流行。
由于MRP的成效显著,美国生产和库存管理委员会(APICS)为此曾在美国各大城市进行巡回组织推广,使用MRP的企业从60年代末的20多家猛增至70年代末的1000多家。
物料需求计划是一种基于相关需求编制的,在综合考虑了主生产计划(MPS)、物料清单(BOM)和实际库存量后定制的计算机辅助生产计划管理系统。
从MRP到闭环MRP 再到MRPⅡ和ERP的发展历程。
4.柔性制造系统FMS(flexible manufacturing system)
随着顾客对产品需求的多样化和个性化,原来单一产品的生产模式已经越来越不能适应现代社会顾客的口味,激烈的市场竞争使得企业必须加快产品的更新速度,不断地推出新产品,同时提高生产系统对市场需求变化的适应能力,比便更快地对市场做出反应,企业的生产类型逐渐向多品种小批量的方向转移。
同时,科学技术的发展特别是数控技术、计算机技术的发展为柔性制造系统的产生提供了技术支持,在这样的背景下,柔性制造系统应运而生。
所谓柔性制造系统(FMS),是指由数台至几十台数控机床(MC)、数控加工中心(NC)和自动检测装置,用一套自动物料搬运装置连接起来的,由计算机进行程序控制的、具有很高柔性的自动化生产加工系统。
一个柔性制造系统一般由加工系统、物料搬运系统(MHS)和计算机控制系统组成。
一个柔性制造系统一般加工零件的品种数都在数十种以上,最多的时候可达5000种,它改变了传统的多品种小批量生产的落后状态,解决了“柔性大”和“效率低”之间的矛盾,使生产效率大幅度提高,成本下降,经济效益十分显著。
5.计算机集成制造系统CIMS(comuter integrated manufacturing system)
1974年,美国约瑟夫.哈林顿博士首先提出了计算机集成制造的概念。
哈林顿提出的CIM 概念中主要包括两个方面:
(1)企业经营生产活动的各个环节是一个不可分割的整体,要紧密连接,统一考虑。
(2)整个生产过程实际上是一个数据采集、传递和加工的过程,最终的产品可以看做是数据的物质表现。
从上面两点可以看出,CIM是生产技术和信息技术的结合,从而使得企业能够快速地响应市场需求,提高生产效率。
我国863/CIMS主题专家组通过近十年来的研究和实践,根据中国国情,把CIM和CIMS定义为:CIM是一种组织、管理与运行企业生产的哲理,它借助计算机硬件及软件,综合运用现代管理技术、制造技术、信息技术、自动化技术、系统工程技术,将企业生产全过程中的有关人/组织、技术、经营管理三要素及其信息流、物流有机地集成并优化运行,实现企业整体优化,以达到产品高质、低耗、上市快、服务好,从而使得企业赢得市场竞争。
CIMS是基于CIM哲理的系统。