07-曲轴常见锻造缺陷及对策
07-曲轴常见锻造缺陷及对策

曲轴常见锻造缺陷及对策[摘要] 本文主要讲述了我公司多年曲轴生产中曾经发生的质量缺陷、缺陷产生部位、产生的原因及解决的措施。
1前言发动机曲轴是发动机中最重要的、结构和受力情况最复杂的零件之一。
曲轴作为我公司的主要营利产品,生产有二十多年的历史,工艺已趋于成熟稳定,解决现场问题的经验日益渐丰。
但在这几年,人员流动较快,为防止新工艺及生产人员走弯路,预防曾经发生过的质量缺陷再次出现,笔者将从事现场工作中遇到的曲轴各类常见缺陷及解决方法归类如下,作为曲轴设计和生产中处理质量的参考。
2曲轴常见缺陷及对策2.1充不满2.1.1平衡块充不满法兰小头平衡块连杆颈外侧平衡块内侧曲柄外侧特征:该类缺陷主要产生在平衡块既高又薄且平衡块尖点离中心较远的曲轴上。
对于8个平衡块的六缸曲轴,中间的第六、七平衡块容易出现。
形成原因:平衡块高宽比大,平衡块内金属的温度下降快,塑性下降;其流动距离较长,模具表面阻力大。
8个平衡块的六缸曲轴,中间的四个平衡块处发生“抢料”现象,六七平衡块成形所需的金属无法补给,所以容易充不满。
对策:1、坯料规格的合理选取。
此方面要注意三个问题:l一是通常按最密集平衡块部分的材料利用率为80%来初选坯料直径;l二是要考虑平衡块配重部分占整个曲柄总面积的比例。
坯料面积/(2*配重块面积)≥0.6l三是要兼顾国内钢厂能够提供的规格,小规格的料比较好选,大规格的料,国内通常是10mm一个规格,时常会发生选上一个规格的较过大,选下一个规格的料又过小。
在有辊锻的情况下,尽量选用大一些的规格的料。
2、选用适当的压挤工艺及合理分布预锻储料:对于一些大型曲轴,由于平衡块较厚,再加上压挤工位没有顶料,压挤通常采用平面压挤的方式,此时就要注意不要压的太扁,使压挤后的坯料宽度不要超过预锻型腔边缘,以防止金属势能的流失,从而导致锻件充不满;预锻设计时,在常规设计的基础上,另外将平衡块与主轴径处设计一个较大的三角锥体形的存料区,与连杆颈之间的梯形区域做成一个存料区,即为终锻存储足够的用于填充的金属,此方面运用成功的例子为康C曲轴。
锻造过程冲孔和扩孔常见的缺陷和对策

锻造过程冲孔和扩孔常见的缺陷和对策1、冲孔过程中常见的缺陷和对策在坯料上锻制出透孔或不透孔的工序称为冲孔。
冲孔分为开式冲孔和闭式冲孔。
开式冲孔又分为实心冲子冲孔和空心冲子冲孔。
本节介绍实心冲子开式冲孔过程中常见的缺陷和对策。
冲孔过程中的主要缺陷是“走样”(图4-29)、侧表面裂纹、内孔圆角处裂纹(图4-30)和孔冲偏等。
所谓“走样”是指开式冲孔时坯料高度减小,外径上小下大,而且下端面突出,上端面凹进等现象。
“走样”和裂纹等缺陷是与冲孔时的受力和变形情况有关的。
冲孔时冲头下部的A区金属是直接受力区(图4-31),其周围的B区金属是间接受力区A区金属的的变形可看做是环形金属包围下的镦粗,A区金属被压缩后高度减小,横截面积增大,向四周径向外流,但受到环壁的限制,故处于三向受压的应力状态,其应力应变简图如图4-31所示。
B区之受力和变形主要是由于A区的变形引起的。
A区金属径向外流时,使B区金属径向受压,切向受拉,在高度方向,A区金属向下流动时,借助剪切应力对B区金属有一个拉缩作用。
愈靠近内侧受拉缩愈严重。
冲孔时D/d愈小,即B区愈薄时,拉缩和走样愈显著。
但是,如果B区很厚,即D/d很大时,B区外侧的σ1、σ2、σ3均很小,可能处于弹性状态,仅内侧发生塑性变形,这时B区的内侧金属径向被压缩,高度可能增大,犹如打硬度一样,“走样”很小。
低塑性材料开式冲孔时,外侧表面裂纹的产生就是由于A区金属向外流动时B区的外径被迫地扩大,使外侧金属受到切向拉应力,当超过金属当时的强度极限时,便产生裂纹破坏。
冲孔时D/d愈小,即B区愈薄时,最外层金属受到的切向拉应力和拉应变愈大,故愈易产生裂纹。
图4-29 冲孔时的“走样”现象图4-30 冲孔时的裂纹由以上分析可见,开式冲孔时D/d太小是不好的,会产生“走样”过大和裂纹,故生产中常取D/d=3,也有些厂取D/d≥(2.5~3)。
图4-31 开式冲孔时的应力应变简图冲孔时内孔圆角处的裂纹是由于此处温度降低较多,塑性较低,加之冲子一般都有锥度,当冲子往下运动时,此处便被胀裂。
锻造过程中常见的失效形式与防止措施
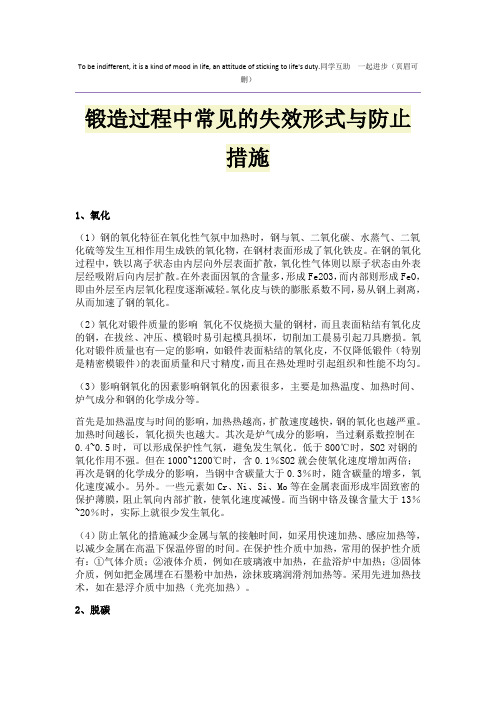
To be indifferent, it is a kind of mood in life, an attitude of sticking to life's duty.同学互助一起进步(页眉可删)锻造过程中常见的失效形式与防止措施1、氧化(1)钢的氧化特征在氧化性气氛中加热时,钢与氧、二氧化碳、水蒸气、二氧化硫等发生互相作用生成铁的氧化物,在钢材表面形成了氧化铁皮。
在钢的氧化过程中,铁以离子状态由内层向外层表面扩散,氧化性气体则以原子状态由外表层经吸附后向内层扩散。
在外表面因氧的含量多,形成Fe2O3,而内部则形成FeO,即由外层至内层氧化程度逐渐减轻。
氧化皮与铁的膨胀系数不同,易从钢上剥离,从而加速了钢的氧化。
(2)氧化对锻件质量的影响氧化不仅烧损大量的钢材,而且表面粘结有氧化皮的钢,在拔丝、冲压、模锻时易引起模具损坏,切削加工晨易引起刀具磨损。
氧化对锻件质量也有—定的影响,如锻件表面粘结的氧化皮,不仅降低锻件(特别是精密模锻件)的表面质量和尺寸精度,而且在热处理时引起组织和性能不均匀。
(3)影响钢氧化的因素影响钢氧化的因素很多,主要是加热温度、加热时间、炉气成分和钢的化学成分等。
首先是加热温度与时间的影响,加热热越高,扩散速度越快,钢的氧化也越严重。
加热时间越长,氧化损失也越大。
其次是炉气成分的影响,当过剩系数控制在0.4~0.5时,可以形成保护性气氛,避免发生氧化。
低于800℃时,SO2对钢的氧化作用不强。
但在1000~1200℃时,含0.1%SO2就会使氧化速度增加两倍;再次是钢的化学成分的影响,当钢中含碳量大于0.3%时,随含碳量的增多,氧化速度减小。
另外。
一些元素如Cr、Ni、Si、Mo等在金属表面形成牢固致密的保护薄膜,阻止氧向内部扩散,使氧化速度减慢。
而当钢中铬及镍含量大于13%~20%时,实际上就很少发生氧化。
(4)防止氧化的措施减少金属与氧的接触时间,如采用快速加热、感应加热等,以减少金属在高温下保温停留的时间。
曲轴常见损伤及预防措施

曲轴常见损伤及预防措施曲轴是柴油机最重要的机件之一,曲轴主要由前端、主轴颈、曲柄、连杆轴颈和尾部构成。
曲轴的前端装有曲轴正时齿轮,尾部安装飞轮的圆锥面。
主轴颈支承在机体主轴承中,并在其中旋转,是整个曲轴的支承部分。
在主轴颈上钻有通往连杆轴颈的油道。
由于主轴颈与主轴承之间的相对滑动速度通常很高,故除了必须采用压力供油润滑之外,主轴颈表面常经淬火处理提高硬度,以提高其耐磨性。
柴油发动机在工作中,曲轴由于受力和工作条件复杂,各摩擦表面滑动速度很高,散热条件又差,因此,曲轴不仅轴颈容易磨损,而且还会出现弯曲和扭曲变形,甚至产生裂纹或折断等。
所以检修时要进行仔细检查,根据查出的损伤部位和损伤程度,采取相应的修理措施。
一、曲轴常见损伤产生的原因1.曲轴颈表面磨损曲轴在长期运转中,会产生主轴颈和连杆轴颈尺寸的减小,以及因磨损不均匀产生圆度(椭圆)、圆柱度(锥度),由于连杆弯曲,缸套偏斜等,使作用在连杆轴颈的力分布不均而出现椭圆;由于油道中杂质在轴颈上偏积而磨成锥形。
因工作中气体压力,活塞连杆运动惯性力及连杆大头离心力所形成的合力,作用在连杆轴颈内侧,致使连杆轴颈偏磨。
2.曲轴颈损伤曲轴轴颈表面往往会出现烧伤、裂纹及划痕等缺陷。
其原因是由于润滑油不清洁或轴承上的缺陷,使轴颈表面上产生划痕。
曲轴烧瓦时轴颈表面也会烧伤,并易造成油道口周围裂纹,曲柄与轴颈过渡处的圆弧半径太小,也常因应力集中而产生裂纹。
一种裂纹为横向裂纹,是曲轴断裂的先兆,即从出现微细裂纹逐渐延伸,最后在特定条件下发生断裂;一种裂纹为纵向裂纹,由油孔处往轴向展开。
3.曲轴的弯曲、扭曲和断裂曲轴产生弯曲和扭曲变形,往往是由于曲轴受到过大的冲击负荷所造成的。
当拖拉机在使用中出现严重的爆燃或起步过猛等,都将使曲轴受到较大的冲击负荷,尤其是发动机出现烧瓦、抱轴等事故时,容易使曲轴产生弯曲及扭曲。
当曲轴、飞轮、活塞连杆组等联动机件的相互位置关系不正确,工作不协调,不平稳时,使曲轴受力不均,也会引起曲轴的变形。
锻造工艺常见缺陷

锻造工艺不当产生的缺陷通常有以下几种:1.大晶粒大晶粒通常是由于始锻温度过高和变形程度不足、或终锻温度过高、或变形程度落人临界变形区引起的。
铝合金变形程度过大,形成织构;高温合金变形温度过低,形成混合变形组织时也可能引起粗大晶粒,晶粒粗大将使锻件的塑性和韧性降低,疲劳性能明显下降。
2.晶粒不均匀晶粒不均匀是指锻件某些部位的晶粒特别粗大,某些部位却较小。
产生晶粒不均匀的主要原因是坯料各处的变形不均匀使晶粒破碎程度不一,或局部区域的变形程度落人临界变形区,或高温合金局部加工硬化,或淬火加热时局部晶粒粗大。
耐热钢及高温合金对晶粒不均匀特别敏感。
晶粒不均匀将使锻件的持久性能、疲劳性能明显下降。
3.冷硬现象变形时由于温度偏低或变形速度太快,以及锻后冷却过快,均可能使再结晶引起的软化跟不上变形引起的强化(硬化),从而使热锻后锻件内部仍部分保留冷变形组织。
这种组织的存在提高了锻件的强度和硬度,但降低了塑性和韧性。
严重的冷硬现象可能引起锻裂。
4.裂纹裂纹通常是锻造时存在较大的拉应力、切应力或附加拉应力引起的。
裂纹发生的部位通常是在坯料应力最大、厚度最薄的部位。
如果坯料表面和内部有微裂纹、或坯料内存在组织缺陷,或热加工温度不当使材料塑性降低,或变形速度过快、变形程度过大,超过材料允许的塑性指针等,则在撤粗、拔长、冲孔、扩孔、弯曲和挤压等工序中都可能产生裂纹。
5.龟裂龟裂是在锻件表面呈现较浅的龟状裂纹。
在锻件成形中受拉应力的表面(例如,未充满的凸出部分或受弯曲的部分)最容易产生这种缺陷。
引起龟裂的内因可能是多方面的:①原材料合Cu、Sn等易熔元素过多。
②高温长时间加热时,钢料表面有铜析出、表面晶粒粗大、脱碳、或经过多次加热的表面。
③燃料含硫量过高,有硫渗人钢料表面。
6.飞边裂纹飞边裂纹是模锻及切边时在分模面处产生的裂纹。
飞边裂纹产生的原因可能是:①在模锻操作中由于重击使金属强烈流动产生穿筋现象。
②镁合金模锻件切边温度过低;铜合金模锻件切边温度过高。
轴承零件锻造常见的加热缺陷及解决方法

内燃机与配件0引言中大型轴承零件制造工艺一般要经过钢材下料→锻造→去应力退火→金属切削加工→热处理→磨削加工→零件检验→成品装配→成品检测试验等工序。
而锻造是轴承零件加工的首道工序,也是所有后工序基础。
锻造质量的好坏,直接影响后工序加工和成品轴承的综合机械性能和轴承使用寿命。
轴承钢(常用GCr15、GCr15SiMn )锻造始锻温度为1050~1100℃之间、终锻温度为800~850℃之间。
在这一区域温度范围内,轴承钢塑性、锻造工艺性、获得的内部组织等关键性技术指标都较好。
由于是在高温状态下加工,轴承套圈热锻件在加热过程中不可避免地会产生氧化皮、脱碳、过热、过烧、加热裂开(内部裂纹)、折叠等缺陷,从而导致金属材料损耗过多,甚至废品。
也为后工序加工留下的质量隐患,且某些隐患在后工序加工过程中是不可完全修复的或者是不可逆的。
因此,理解上述加热缺陷产生的机理,掌握正确的加热工艺方法,尽最大可能减少或防止这些缺陷的产生,是提高锻件质量和锻造水平重要的有效途径之一,也是衡量锻造水平高低的重要技术指标之一。
本文从生产实践中总结出几种常见的轴承钢加热缺陷及防止办法如下:1氧化皮轴承钢锻件在加热过程中很容易产生氧化皮,产生的氧化皮极有可能会随着辗扩过程卷入到零件表面的辗扩流线方向,有的粗大,有的细如发丝,深浅不一,深度较深时,后工序不易及时发现,只有到成品零件才能看见。
氧化皮的产生同时造成锻件原材料的损耗,锻件每加热一次,便有1.5~3%的金属被氧化烧损。
另外氧化皮的产生降低了锻件表面的质量,被压入锻件内部时表面形成了凹陷并影响锻件的精度,如果氧化皮不处理,直接进行锻打还会导致锻件组织和性能的不均匀;如果氧化皮过硬就变相地降低了模具的使用寿命。
严重影响锻件的表面质量、锻模的精度和寿命,特别是对轴承寿命危害极大。
产生氧化皮的主要原因是因为金属表面的元素与炉气中O 2、CO 2、H 2O 及SO 2发生化学反应所致。
球墨铸铁曲轴的铸造缺陷分析及对策

一、铸造工艺设计方案
我们考虑到滑枕的精度要求、运动方向和受力情况, 铸造工艺采取了立浇方案。 滑枕属于细长类铸件,此前大型滑枕类铸件通常采 用平浇方式,造型方案简便,充型平稳,但铸件的上表 面质量难以保证,缩孔、缩松多,无法满足使用性能要 求。滑枕采用立浇方案,可以保证铸件整体的质量,工 艺出品率高。即总高 #,*:44 分成 % 段模样制造,分段 造型后,逐段垒起,使滑枕的浇注状态与工作状态一致, 保证铸件质量。
%’ 模样的分段、定位
滑枕确定为立浇工艺后,就要考虑对模样分段。但 分段后各截模样的起模斜度就成了难点,对铸造而言, 起模斜度是必须的,而分段后 : 截模样合到一起的铸型 无法实现,因此工艺对中箱模样设计了抽芯式。
二、铸造工艺设计要点
滑枕整体模样分为 : 段造型( 冒口单独一段) ,中箱
’’’’’’’’’’’’’’’ ( # ) 适当降低浇注温度。 %’ 形成原因
$’ 形成原因
( # ) $% 含量过高。残留 $% 量越多,夹渣层越厚。 ( & ) 原铁液 ’ 含量过高。原铁液 ’ 含量越高,曲轴 的夹渣缺陷越多。 ( ( ) 球化剂、孕育剂过多,使 ’) 量过高,形成氧化 夹渣。 ( * ) 浇注温度过低,一次渣、二次渣来不及逸出铸 件而形成夹渣。
!’ 防止措施
!’ 防止措施
( # ) 严 格 控 制 ( @ + (- 3. / (- >. , ( ’) + #- ?. / &- &. 。大断面曲轴可取下限。 ( & ) 采用低硅原铁液, ( ’) + #- #. / #- (. ,以及加 强延后孕育处理工艺。 ( ( ) 在保证球化的前提下,严格 控 制 球 化 剂 加 入 量,特别是 ( $%残留 = ,- ,0. 。
浅谈锻造过程中常见问题及解决对策

浅谈锻造过程中常见问题及解决对策浅谈锻造过程中常见问题及解决对策【摘要】:本文主要结合作者自身的多年工作经验,分析了锻造过程中常见的问题以及对应的解决措施,望对锻造行业工作者具有借鉴作用。
【关键词】:锻造;过程;问题;对策1.锻造操作的技巧和体会1.1“铜铁不同炉”的分析及解决方法铁匠行里的规矩“铜铁不同炉”是什么道理呢?例如,在煤气炉里加热一种小型模锻件,材质为40#钢碳,锻后表面有一些龟裂,经金相观察表明,裂纹是沿晶界扩展的,在晶界上出现了淡黄色的普碳,铜异相-铜相。
这就是“铜脆”现象,其实质是渗铜。
经了解,该加热炉加热过铜坯料。
如果在炉内加热铜,因氧化作用会造成氧化铜。
不清除炉内的氧化铜屑,再用同一个炉子去加热钢,氧化铜就可能在高温下还原成熔融状态的铜,渗透到钢的表面,沿奥氏体晶界扩展开。
因为铜的强度和熔点都比钢低很多,所以铜的渗扩消弱了钢晶粒间的联系,使被加热的钢在锻造时出现裂纹或报废,故有“铜铁不同炉”的说法。
如何消除此现象呢?笔者建议两种方法:(1)加热铜时,在炉底放置一铁皮,加热后抽走,易清理。
(2)在加热铜后的炉膛内撒一层食盐(NaCl),待食盐与铜发生反应挥发后,即可使用。
1.2简便快捷的坯料计算从事锻造专业,计算坯料是一项基本工作。
现在算料有人用金属盘,大部分人用计算器(用计算器先是算出体积,再乘以密度,然后数位数,较麻烦、易出错。
笔者是这样简便快捷计算的:G圆=6.165d2H.其中:d-直径,cm;H-高度,mm;G-质量,kg。
G扁或方=7.85ABL.其中:宽、高、长度,A、B、L-,cm;G-质量,kg。
若密度与7.85有差异,可换算。
1.3用螺帽代替顶尖孔轴类零件加工,本身成品不需要保留顶尖孔,有时若锻造工艺未考虑到此情怎么办呢?笔者曾遇到过一批轴类零件60多件,锻造毛坯在长度上只加了锻造余量,未加顶尖孔长度。
经过考虑,找了一些与机床顶尖相符的螺帽,焊在锻件端部,即刻解决了此事,挽救了一批零件。
曲轴常见的锻造缺陷及解析

曲轴常见的锻造缺陷及解析曲轴是一种重要的机械零件,它经常用于内燃机、柴油机、发电机和飞机发动机等的传动装置中。
在曲轴的制造过程中,锻造是一种常用的加工方法。
然而,锻造过程中可能会产生一些缺陷,以下是曲轴常见的锻造缺陷及解析:
1. 晶界氧化物缺陷:这种缺陷是由于锻造过程中钢材表面被氧化而产生的。
这种缺陷通常出现在曲轴的表层,不仅影响曲轴的强度和韧性,而且还会导致曲轴的疲劳寿命缩短。
解决方法是通过增加锻造温度、减少加工速度或采用防氧化剂来减少这种缺陷。
2. 折叠缺陷:这种缺陷是曲轴锻件中最常见的缺陷之一。
折叠缺陷通常是在锤击或挤压中产生的。
这种缺陷会形成各种类型的裂纹,从而降低曲轴的强度和耐久性。
解决方法是通过变换锤击或挤压的方向,以减少折叠的风险。
3. 空洞缺陷:在曲轴的锻造过程中,可能会出现由气体或其他不稳定物质引起的空洞缺陷。
这种缺陷不仅会对曲轴的强度和刚度产生影响,而且还会导致曲轴表面的裂纹。
解决方法包括在制造过程中使用更好的防气体措施,并在生产前进行更彻底的金属质量检查。
4. 脆性缺陷:脆性缺陷产生的原因是当钢材在高温下变形时,钢材中的晶粒晶界会发生断裂。
脆性缺陷会导致曲轴易于断裂和损坏。
解决方法包括在锻造过程中加热和冷却的更准确控制及表面硬度测试的改进。
综上所述,锻造曲轴时需要采取多项措施来避免这些缺陷的发生,其中包括正确控制温度、锤击或挤压方向的变换、使用更好的防气体
措施以及在生产前进行更完善的金属质量检查。
锻件缺陷的原因及处理

锻件缺陷的主要原因及处理一、原材料的主要缺陷及其引起的锻件缺陷锻造用的原材料为铸锭、轧材、挤材及锻坯。
而轧材、挤材及锻坯分别是铸锭经轧制、挤压及锻造加工成的半成品。
一般情况下,铸锭的内部缺陷或表面缺陷的出现有时是不可避免的。
例如,内部的成分与组织偏析等。
原材料存在的各种缺陷,不仅会影响锻件的成形,而且将影响锻件的最终质量。
根据不完全的统计,在航空工业系统中,导致航空锻件报废的诸多原因中,由于原材料固有缺陷引起的约占一半左右。
因此,千万不可忽视原材料的质量控制工作。
由于原材料的缺陷造成的锻件缺陷通常有:1.表面裂纹表面裂纹多发生在轧制棒材和锻制棒材上,一般呈直线形状,和轧制或锻造的主变形方向一致。
造成这种缺陷的原因很多,例如钢锭内的皮下气泡在轧制时一面沿变形方向伸长,一面暴露到表面上和向内部深处发展。
又如在轧制时,坯料的表面如被划伤,冷却时将造成应力集中,从而可能沿划痕开裂等等。
这种裂纹若在锻造前不去掉,锻造时便可能扩展引起锻件裂纹。
2.折叠折叠形成的原因是当金属坯料在轧制过程中,由于轧辊上的型槽定径不正确,或因型槽磨损面产生的毛刺在轧制时被卷入,形成和材料表面成一定倾角的折缝。
对钢材,折缝内有氧化铁夹杂,四周有脱碳。
折叠若在锻造前不去掉,可能引起锻件折叠或开裂。
3.结疤结疤是在轧材表面局部区域的一层可剥落的薄膜。
结疤的形成是由于浇铸时钢液飞溅而凝结在钢锭表面,轧制时被压成薄膜,贴附在轧材的表面,即为结疤。
锻后锻件经酸洗清理,薄膜将会剥落而成为锻件表面缺陷。
4.层状断口层状断口的特征是其断口或断面与折断了的石板、树皮很相似。
层状断口多发生在合金钢(铬镍钢、铬镍钨钢等),碳钢中也有发现。
这种缺陷的产生是由于钢中存在的非金属夹杂物、枝晶偏析以及气孔疏松等缺陷,在锻、轧过程中沿轧制方向被拉长,使钢材呈片层状。
如果杂质过多,锻造就有分层破裂的危险。
层状断口越严重,钢的塑性、韧性越差,尤其是横向力学性能很低,所以钢材如具有明显的层片状缺陷是不合格的。
曲轴常见缺陷及对策
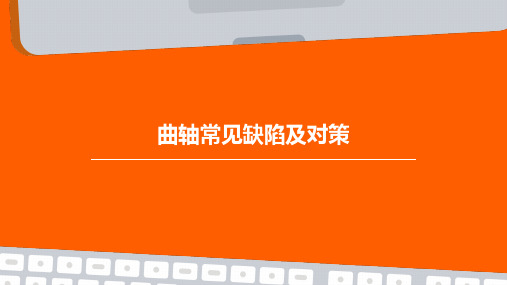
谢谢观看
磨损
总结词
磨损是曲轴常见的另一种缺陷,通常是由于润滑不良或发动机长时间高负荷运 行引起的。
详细描述
曲轴的磨损通常发生在轴颈和轴承接触区域。如果润滑不良或发动机长时间高 负荷运行,轴承和轴颈之间的摩擦就会加剧,导致轴颈磨损。磨损严重时,曲 轴的动平衡会被破坏,影响发动机的性能和寿命。
疲劳断裂
总结词
润滑油的作用是减少摩擦和磨损,如 果未按时更换,会导致曲轴的磨损加 剧。
未定期检查紧固件
未及时修复损坏零件
曲轴上的损坏零件如果不及时修复, 会导致其工作状态恶化,甚至引发更 大的故障。
曲轴的紧固件如果松动,会导致曲轴 的振动和位移,从而影响其正常工作。
03
对策与解决方案
制造工艺改进
01
02
03
曲轴材料选择
采用高强度、耐磨损的材 料,如合金钢、钛合金等, 以提高曲轴的机械性能和 抗疲劳强度。
热处理工艺优化
通过改进热处理工艺,如 淬火、回火等,提高曲轴 的硬度和耐磨性,同时增 强其抗疲劳性能。
加工工艺改进
优化曲轴的加工工艺,减 少加工过程中的残余应力, 降低曲轴开裂的风险。
使用环境优化
工作温度控制
保持曲轴工作在适宜的温 度范围内,避免因过热而 导致材料疲劳和开裂。
劳断裂是一种突发性的破坏形式,一旦发生就会造成严重机械事故。
02
曲轴缺陷产生原因
制造工艺问题
铸造缺陷
01
如气孔、缩孔、夹渣等,这些缺陷会影响曲轴的强度和疲劳寿
命。
热处理问题
02
如淬火不均、回火不当等,会导致曲轴内部组织结构不均匀,
降低其力学性能。
加工误差
03
锻件缺陷分析
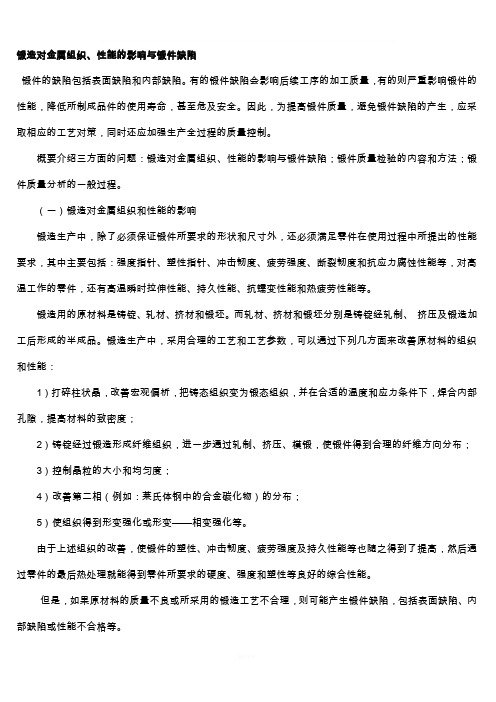
锻造对金属组织、性能的影响与锻件缺陷锻件的缺陷包括表面缺陷和内部缺陷。
有的锻件缺陷会影响后续工序的加工质量,有的则严重影响锻件的性能,降低所制成品件的使用寿命,甚至危及安全。
因此,为提高锻件质量,避免锻件缺陷的产生,应采取相应的工艺对策,同时还应加强生产全过程的质量控制。
概要介绍三方面的问题:锻造对金属组织、性能的影响与锻件缺陷;锻件质量检验的内容和方法;锻件质量分析的一般过程。
(一)锻造对金属组织和性能的影响锻造生产中,除了必须保证锻件所要求的形状和尺寸外,还必须满足零件在使用过程中所提出的性能要求,其中主要包括:强度指针、塑性指针、冲击韧度、疲劳强度、断裂韧度和抗应力腐蚀性能等,对高温工作的零件,还有高温瞬时拉伸性能、持久性能、抗蠕变性能和热疲劳性能等。
锻造用的原材料是铸锭、轧材、挤材和锻坯。
而轧材、挤材和锻坯分别是铸锭经轧制、挤压及锻造加工后形成的半成品。
锻造生产中,采用合理的工艺和工艺参数,可以通过下列几方面来改善原材料的组织和性能:1)打碎柱状晶,改善宏观偏析,把铸态组织变为锻态组织,并在合适的温度和应力条件下,焊合内部孔隙,提高材料的致密度;2)铸锭经过锻造形成纤维组织,进一步通过轧制、挤压、模锻,使锻件得到合理的纤维方向分布;3)控制晶粒的大小和均匀度;4)改善第二相(例如:莱氏体钢中的合金碳化物)的分布;5)使组织得到形变强化或形变——相变强化等。
由于上述组织的改善,使锻件的塑性、冲击韧度、疲劳强度及持久性能等也随之得到了提高,然后通过零件的最后热处理就能得到零件所要求的硬度、强度和塑性等良好的综合性能。
但是,如果原材料的质量不良或所采用的锻造工艺不合理,则可能产生锻件缺陷,包括表面缺陷、内部缺陷或性能不合格等。
(二)原材料对锻件质量的影响原材料的良好质量是保证锻件质量的先决条件,如原材料存在缺陷,将影响锻件的成形过程及锻件的最终质量。
如原材料的化学元素超出规定的范围或杂质元素含量过高,对锻件的成形和质量都会带来较大的影响,例如:S、B、Cu、Sn等元素易形成低熔点相,使锻件易出现热脆。
锻件的瑕疵原因及检验方法
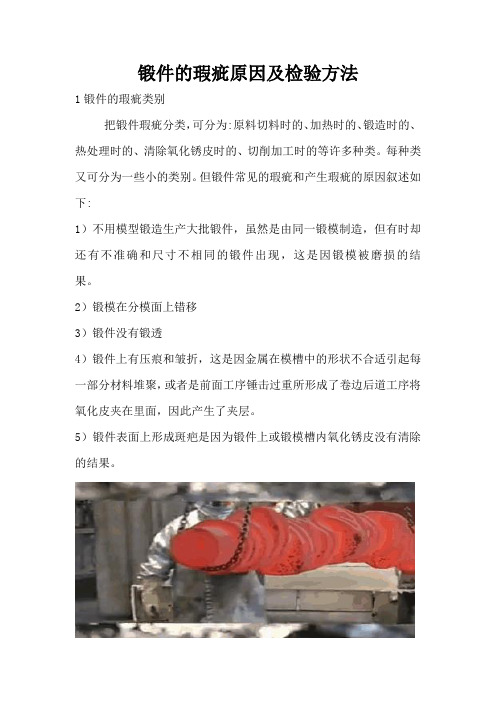
锻件的瑕疵原因及检验方法1锻件的瑕疵类别把锻件瑕疵分类,可分为:原料切料时的、加热时的、锻造时的、热处理时的、清除氧化锈皮时的、切削加工时的等许多种类。
每种类又可分为一些小的类别。
但锻件常见的瑕疵和产生瑕疵的原因叙述如下:1)不用模型锻造生产大批锻件,虽然是由同一锻模制造,但有时却还有不准确和尺寸不相同的锻件出现,这是因锻模被磨损的结果。
2)锻模在分模面上错移3)锻件没有锻透4)锻件上有压痕和皱折,这是因金属在模槽中的形状不合适引起每一部分材料堆聚,或者是前面工序锤击过重所形成了卷边后道工序将氧化皮夹在里面,因此产生了夹层。
5)锻件表面上形成斑疤是因为锻件上或锻模槽内氧化锈皮没有清除的结果。
2锻件几何外观质量检验几何尺寸的检查法要点如下:1)检查高度和直径:抽查时用普通卡尺,全查时用极限量规。
2)检查,抽查时用带千分表的卡,全查时用极限卡钳。
3)孔径:用极限量规。
4)检查大孔径,用样板测量。
5)检查长度:如只测量一个尺寸,可用杆状样板以槽宽的公差检查,如同时测量几个尺寸,可用成形样板检查。
6)检查弯曲度:将锻件放置在元宝铁或磙子上旋转,检查脉动,如大量检查曲轴或其他截面有变化的件,可同时检查几处脉动。
7)检查表面翘曲度:将大面积锻件放置在三个支点上,用深度仪检查。
8)检查表面平行度:将锻件放置在基准面上,用深度仪检查。
9)检查表面垂直度:将锻件放置在元宝铁上,用深度仪检查,大量检查时,用电接触仪,尺寸误差超过公差,红灯就亮,合格的锻件,绿灯就亮。
10)检查角度:用量角器或专门的量角仪。
3锻件表面质量检验1)目视检查这是检验锻件表面质量最普遍、最常用的方法,凭肉眼观察锻件表面是否有折叠、裂纹、压伤、疤痕、表面过烧等缺陷。
锻件表面隐藏较深的缺陷,常在酸洗、喷沙或滚筒清除表面氧化皮后进行目视检查。
3)磁力探伤也称磁粉探伤或磁粉检验,可用来发现锻件肉眼不能检查出的表面层中微小缺陷,如微小裂纹、折纹、夹杂等。
锻件的常见缺陷及原因分析

锻件的常见缺陷及原因分析(2007/07/05 10:58)锻件的缺陷很多,产生的原因也多种多样,有锻造工艺不良造成的,有原材料的原因,有模具设计不合理所致等等。
尤其是少无切削加工的精密锻件,更是难以做到完全控制。
1.大晶粒大晶粒通常是由于始锻温度过高和变形程度不足、或终锻温度过高、或变形程度落人临界变形区引起的。
铝合金变形程度过大,形成织构;高温合金变形温度过低,形成混合变形组织时也可能引起粗大晶粒,晶粒粗大将使锻件的塑性和韧性降低,疲劳性能明显下降。
2.晶粒不均匀晶粒不均匀是指锻件某些部位的晶粒特别粗大,某些部位却较小。
产生晶粒不均匀的主要原因是坯料各处的变形不均匀使晶粒破碎程度不一,或局部区域的变形程度落人临界变形区,或高温合金局部加工硬化,或淬火加热时局部晶粒粗大。
耐热钢及高温合金对晶粒不均匀特别敏感。
晶粒不均匀将使锻件的持久性能、疲劳性能明显下降。
3.冷硬现象变形时由于温度偏低或变形速度太快,以及锻后冷却过快,均可能使再结晶引起的软化跟不上变形引起的强化(硬化),从而使热锻后锻件内部仍部分保留冷变形组织。
这种组织的存在提高了锻件的强度和硬度,但降低了塑性和韧性。
严重的冷硬现象可能引起锻裂。
4.裂纹裂纹通常是锻造时存在较大的拉应力、切应力或附加拉应力引起的。
裂纹发生的部位通常是在坯料应力最大、厚度最薄的部位。
如果坯料表面和内部有微裂纹、或坯料内存在组织缺陷,或热加工温度不当使材料塑性降低,或变形速度过快、变形程度过大,超过材料允许的塑性指针等,则在镦粗、拔长、冲孔、扩孔、弯曲和挤压等工序中都可能产生裂纹。
5.龟裂龟裂是在锻件表面呈现较浅的龟状裂纹。
在锻件成形中受拉应力的表面(例如,未充满的凸出部分或受弯曲的部分)最容易产生这种缺陷。
引起龟裂的内因可能是多方面的:①原材料合Cu、Sn等易熔元素过多。
②高温长时间加热时,钢料表面有铜析出、表面晶粒粗大、脱碳、或经过多次加热的表面。
③燃料含硫量过高,有硫渗人钢料表面。
曲轴常见的锻造缺陷及解析

曲轴常见的锻造缺陷及解析
曲轴是发动机的核心零部件之一。
在锻造过程中,曲轴会出现一些常见的缺陷,本文将介绍这些缺陷及解析。
1. 割缝:割缝是曲轴表面的裂缝。
它通常是由于轧制或冷却过程中曲轴表面的应力过大造成的。
割缝对曲轴的强度和耐久性造成严重影响。
2. 裂纹:裂纹是曲轴内部或表面的裂缝。
裂纹通常是由于过高的锻造温度或过快的冷却速度造成的。
裂纹对曲轴的强度和使用寿命造成严重影响。
3. 粗糙表面:粗糙表面是指曲轴表面的不平整。
这通常是由于锻造工艺不完善或锻造温度不合适造成的。
粗糙表面会导致曲轴在运转时产生额外摩擦力,加速磨损。
4. 异物:异物是指曲轴表面或内部的没有完全融入的杂质。
这通常是由于原材料不干净或炉子没有彻底清理造成的。
异物可导致局部应力集中,可能引发裂纹,影响曲轴的强度和使用寿命。
以上是曲轴常见的锻造缺陷及解析。
为了保证曲轴的质量,需要在锻造过程中注意这些缺陷的预防和排除,确保曲轴的稳定性和可靠性。
锻件缺陷的主要特征及产生的原因

绪论国家的装备制造能力的整体能力和发展水平决定着国家的经济实力、国防实力、综合国力和全球经济形势的竞争力与合作能力,决定着国家实现现代化和民族复兴的过程。
制造业是国民经济建设的基础,锻造在现代制造业中占有举足轻重的地位。
锻造在机床、重型机械、矿山机械、石油机械、水电设备、汽车、航空航天、核能及军工产品中占有比较大的比重。
由于锻压生产具有生产效率高、材料利用率和改善制件的内部组织及机械性能等显著特点,因此采用锻压生产零件的制造方法在各行各业中所占的比例很大。
随着精密成型、少无切削技术的发展,降低生产成本、减少产品质量、提高产品性能和质量要求的不断提高,锻压生产在工业、国防、航空航天以及其他各种装备制造业中的作用会越来越大。
锻件缺陷的主要特征及产生的原因制造业是国民经济建设的基础,锻造在现代制造业中占有举足轻重的地位。
锻造在机床、重型机械、矿山机械、石油机械、水电设备、汽车、航空、核能及军工产品中占有比较大的比重。
国家的装备制造能力的整体能力和发展水平决定着国家的经济实力、国防实力、综合国力和全球经济形势的竞争力与合作能力,决定着国家实现现代化和民族复兴的过程。
由于锻压生产具有生产效率高、材料利用率和改善制件的内部组织及机械性能等显著特点,因此采用锻压生产零件的制造方法在各行各业中所占的比例很大。
随着精密成型、少无切削技术的发展,降低生产成本、减少产品质量、提高产品性能和质量要求的不断提高,锻压生产在工业、国防、航空航天以及其他各种装备制造业中的作用会越来越大。
一锻造概述锻造利用冲击力或静压力使加热后的坯料在锻压设备上、下砧之间产生塑性变形,以获得所需尺寸、形状和质量的锻件加工方法称为锻造。
常用的锻造方法为自由锻、模锻及胎模锻。
自由锻利用冲击力或静压力使经过加热的金属在锻压设备的上、下砧间向四周自由流动产生塑性变形,获得所需锻件的加工方法称为自由锻。
自由锻分为手工锻造和机器锻造两种。
手工锻造只能生产小型锻件,机器锻造是自由锻锻造特点自由锻造所用工具和设备简单,通用性好,成本低。
壳型铸造曲轴常见缺陷与对策浅析

当铁水表面形成的液态渣进入型腔时后,曲轴在凝固时,渣中所含的FeO就会同铁水中的C发 生反应生成CO气体。
2.2防止渣气孑L缺陷对策
2.2.1合理确定浇注工艺温度范围 温度的降低是铁水氧化的根本原因,为此我们把浇注温度由以前的1360‘C左右提高到目前的 1390"--1450℃,冬季控制在上限,有效地防止了铁水在低浇注温度时的快速氧化。 2.2.2合理选用过滤网 我厂生产曲轴时为了降低渣孔缺陷一直使用直孔陶瓷过滤网。小型曲轴一般采用孔径为
球墨铸铁在浇注前用硅铁进行孕育处理时,如果孕育不庭,将导致铁水凝固时析出大量渗碳体,
从而使凝固收缩增加,产生缩孔或者缩松。
1 1
5浇注系统及冒口设计不合理 内浇口的位置及尺寸不正确可能会造成铁水在凝固时发生石墨化膨胀,铁水经内浇口倒流回直
浇道,从而使曲轴产生缩孔和缩松。冒口尺寸及冒口颈尺寸设计不当造成曲轴不能实现顺序凝固, 可能导致曲轴产生缩孔和缩松。
3.1曲轴动平衡不合格成因分析
3.1 3 1 3 3 1 1
1曲轴在制造过程中产生较大的变形量.导致曲轴不平衡量太大。 2曲轴由于涨壳造成连杆颈及主轴颈粗细不一。影响加工定位。 3曲轴清理不到位.定位点和夹紧点有凸起物引起定位偏差。 4加工厂设备平衡能力不足及缺乏动平衡经验。
3.2防止曲轴动平衡不合格对策
1.缩孔、缩松
缩孔、缩松是球墨铸铁特有的废品现象,也是曲轴常见缺陷之一,其产生原因与凝固方式、凝 固顺序、铁水的碳当量和冒口补缩等因素有很大关系。我厂壳型工艺生产的曲轴采用的立式浇注工 艺,曲轴的法兰端朝上,所以法兰盘中部和第五主轴径处最后凝固,比较容易出现缩孔、缩松缺陷。 其在曲轴上的主要表现形式为大头孔洞、大头内部缩松和五主轴缩陷(如图l、2)。它严重影响曲 轴内部的致密性和外部的无缺陷要求,尤其像大头内部缩松此类缺陷在加工过程不容易被发现,最
大型锻件中常见的缺陷与对策

大型锻件中常见的缺陷与对策大型锻件中常见的缺陷与对策大型锻件中的缺陷,从性质上分为化学成分、组织性能不合格,第二相析出,类孔隙性缺陷和裂纹五大类。
从缺陷的产生方面可分为,在冶炼、出钢、注锭、脱模冷却或热送过程中产生的原材料缺陷及在加热、锻压、锻后冷却和热处理过程中产生的锻件缺陷两大类。
大型锻造中,由于锻件截面尺寸大,加热、冷却时,温度的变化和分布不均匀性大,锻压变形时,金属塑性流动差别大,加上钢锭大冶金缺陷多,因而容易形成一些不同于中小型锻造的缺陷。
如严重偏析和疏松,密集性夹杂物,发达的柱状晶及粗大不均匀结晶,敏感开裂与白点倾向,晶粒遗传性与回火脆性,组织性能的严重不均匀性,形状尺寸超差等等。
大型锻件中常见的主要缺陷有:1.偏析钢中化学成分与杂质分布的不均匀现象,称为偏析。
一般将高于平均成分者,称为正偏析,低于平均成分者,称为负偏析。
尚有宏观偏析,如区域偏析与微观偏析,如枝晶偏析,晶间偏析之分。
大锻件中的偏析与钢锭偏析密切相关,而钢锭偏析程度又与钢种、锭型、冶炼质量及浇注条件等有关。
合金元素、杂质含量、钢中气体均加剧偏析的发展。
钢锭愈大,浇注温度愈高,浇注速度愈快,偏析程度愈严重。
(1)区域偏析它属于宏观偏析,是由钢液在凝固过程中选择结晶,溶解度变化和比重差异引起的。
如钢中气体在上浮过程中带动富集杂质的钢液上升的条状轨迹,形成须状∧形偏析。
顶部先结晶的晶体和高熔点的杂质下沉,仿佛结晶雨下落形成的轴心∨形偏析。
沉淀于锭底形成负偏析沉积锥。
最后凝固上部区域,碳、硫、磷等偏析元素富集,成为缺陷较多的正偏析区。
图1为我国解剖的55t34CrMolA钢锭纵剖面硫印低倍图片及区域偏析示意图。
图1 钢锭区域偏析硫印示意图①“∧”型偏析带②“∨”型偏析带③负偏析区防止区域偏析的对策是:1)降低钢中硫、磷等偏析元素和气体的含量,如采用炉外精炼,真空碳脱氧(VCD)处理及锭底吹氩工艺。
2)采用多炉合浇、冒口补浇、振动浇注及发热绝热冒口,增强冒口补缩能力等措施。
造成锻件质量缺陷的因素探讨

造成锻件质量缺陷的因素探讨摘要:本文综合剖析了影响锻件质量的各种原因,以机车山连杆产品为例简要分析了原材料缺陷、备料问题和锻造工艺不当所造成的锻件质量缺陷,并提出了防止和克服质量问题的具体措施。
关键词:锻件;质量缺陷;影响因素引言:锻件质量缺陷是由于金属在塑性变形过程中受到多种因素影响,进而在锻造完成之后呈现出表面氧化、裂纹、折叠等表现。
锻件质量缺陷在实际当中并不少见,而加强对锻件质量缺陷的影响因素研究和分析,对于进一步提高锻件质量,保证锻件实用价值,降低锻造成本有着一定的现实意义。
一、原材料缺陷长轴类零件的锻造成型过程是一个受诸多因素影响的复杂变形过程,此类零件形状都较复杂,锻造所使用的原材料种类丰富,其中铸锭为基本的锻件原材料形式,而其他原材料则均是在铸锭基础上给予不同初加工方式所获取的半成品。
造成原材料缺陷通常有以下几方面原因:1.表面裂纹引发表面裂纹的因素众多,尤其是在原料中含有一定量气泡时,气泡会随着操作的深入而向特定的方向进行延伸,并同时会向上下两个方面持续发展,发展至表面时即为表面裂纹。
表面裂纹对于锻件加工的影响较大,若在未处理表面裂纹的情况下就开展锻件加工,则可能会进一步发展为锻件裂纹,其一般以轴向裂纹的形式而存在。
[1](二)非金属杂质非金属杂质是由于金属材料熔炼和浇铸操作不当所引发的,尤其是在耐火材料混入钢液时,最容易出现非金属杂质。
非金属杂质在锻件中的形状表现多样化,包括点状、团状等。
非金属杂质对于锻件质量的危害性取决于杂质总量的多少以及锻件的结构形式,当非金属杂质含量较高时,会直接导致锻件开裂或者材料性能下降。
[2]1.备料不当(一)坯料弯曲、毛刺备料不当导致钢锭在切断之前就存在弯曲的状况,而在钢锭弯曲状态下进行切割,会导致钢锭的部分被挤入模具的间隙当中,进行形成毛刺的形态。
毛刺的存在对于后续锻造加工环节会造成直接的影响,包括局部过热、过烧等,锻件容易出现折叠和开裂的情况。
- 1、下载文档前请自行甄别文档内容的完整性,平台不提供额外的编辑、内容补充、找答案等附加服务。
- 2、"仅部分预览"的文档,不可在线预览部分如存在完整性等问题,可反馈申请退款(可完整预览的文档不适用该条件!)。
- 3、如文档侵犯您的权益,请联系客服反馈,我们会尽快为您处理(人工客服工作时间:9:00-18:30)。
曲轴常见锻造缺陷及对策[摘要] 本文主要讲述了我公司多年曲轴生产中曾经发生的质量缺陷、缺陷产生部位、产生的原因及解决的措施。
1前言发动机曲轴是发动机中最重要的、结构和受力情况最复杂的零件之一。
曲轴作为我公司的主要营利产品,生产有二十多年的历史,工艺已趋于成熟稳定,解决现场问题的经验日益渐丰。
但在这几年,人员流动较快,为防止新工艺及生产人员走弯路,预防曾经发生过的质量缺陷再次出现,笔者将从事现场工作中遇到的曲轴各类常见缺陷及解决方法归类如下,作为曲轴设计和生产中处理质量的参考。
2曲轴常见缺陷及对策2.1充不满2.1.1平衡块充不满法兰小头平衡块连杆颈外侧平衡块内侧曲柄外侧特征:该类缺陷主要产生在平衡块既高又薄且平衡块尖点离中心较远的曲轴上。
对于8个平衡块的六缸曲轴,中间的第六、七平衡块容易出现。
形成原因:平衡块高宽比大,平衡块内金属的温度下降快,塑性下降;其流动距离较长,模具表面阻力大。
8个平衡块的六缸曲轴,中间的四个平衡块处发生“抢料”现象,六七平衡块成形所需的金属无法补给,所以容易充不满。
对策:1、坯料规格的合理选取。
此方面要注意三个问题:l一是通常按最密集平衡块部分的材料利用率为80%来初选坯料直径;l二是要考虑平衡块配重部分占整个曲柄总面积的比例。
坯料面积/(2*配重块面积)≥0.6l三是要兼顾国内钢厂能够提供的规格,小规格的料比较好选,大规格的料,国内通常是10mm一个规格,时常会发生选上一个规格的较过大,选下一个规格的料又过小。
在有辊锻的情况下,尽量选用大一些的规格的料。
2、选用适当的压挤工艺及合理分布预锻储料:对于一些大型曲轴,由于平衡块较厚,再加上压挤工位没有顶料,压挤通常采用平面压挤的方式,此时就要注意不要压的太扁,使压挤后的坯料宽度不要超过预锻型腔边缘,以防止金属势能的流失,从而导致锻件充不满;预锻设计时,在常规设计的基础上,另外将平衡块与主轴径处设计一个较大的三角锥体形的存料区,与连杆颈之间的梯形区域做成一个存料区,即为终锻存储足够的用于填充的金属,此方面运用成功的例子为康C曲轴。
对于小型曲轴,压挤设计的思路一般为比预锻厚2-3mm,全桥部设计。
3、在实际生产中,由于种种原因,有时常采用将预锻模整体下落,桥部宽度加宽,降封闭高度锻打的方法,即将曲轴锻打得比以前更薄的方法以解决充不满。
此种情况对于料规格较大(但仍充不满)时作用甚微;对于料比较紧张的,采用此种方案较为有效,充分利用预锻的大圆角作用。
4、要控制加热温度及均匀性。
在高温段,金属塑性受温度影响较大。
低温锻打,不仅恶化模具的工作条件,而且引起锻件充不满。
2.1.2止推环处充不满特征:该类缺陷主要产生在第四主轴径两侧的止推环上,不易察觉,但发生几率较高。
产生原因:一是氧化皮过厚,喷丸后显现;二是模具型腔内堆积了石墨。
对策:l该处属于非辊锻区,但仍可利用辊锻轻微变形来达到去除氧化皮的目的;而且在锻打过程中利用风管吹除;l由于该处型腔较窄,对此我们不但要严格按工艺要求对石墨进行配比,每件润滑一次,并要定期对模具用尖锐的工具对该处进行清理,每班至少清理一次;l型腔设计时增加补偿量。
2.1.3曲柄臂充不满特征:该类缺陷主要产生在连杆颈处型腔较深的下模,发生几率相对不太高,但每年都会发生,而且一发生锻件就只能报废,无法挽救。
产生原因:机械手送料不到位,或者在生产中有时为了保证平衡块充满,有意将坯料摆偏。
但若摆放的过偏,虽然平衡块充满得到保证,但相应的造成曲柄臂处缺料充不满。
04年湖锻生产D6114曲轴就发生过一次该位置批量的充不满。
对策:解决此类缺陷,主要是要保证将压挤后坯料送到型腔中心位置。
2.2 折(裂)纹2.2.1 端面折(裂)纹A 类 产生原因特征:端面折纹主要发生在小头,通常有两种情况,一种为上图的A 类折纹,在圆周360º都可能发生;另一种为上图的B 类折纹,发生在小头,位置相对固定,为竖向折纹。
产生原因:A 类主要由于材料端面开裂造成。
原材料硬度较高,塑性不足或应力没有释放干净均会造成材料剪切开裂。
B 类产生的原因为辊锻过程中坯料表面的金属变形快,心部的金属变形难、流动慢,辊锻后端面形成大凹陷。
锻打时坯料截面流动速度的差异,加剧了凹陷的负面影响,从而形成折纹,。
对策:A 类折纹,解决措施为适当提高原材料的塑性指标,和控制坯料硬度,并且将坯料加热到蓝脆区进行剪切。
B 类折纹,解决措施为将凹陷区近可能摆放在A 类折纹 原因:材料端面开裂B 类折纹 原因:端面凹陷小头型腔外锻打。
2.2.2 二、五连杆颈折纹特征:该类折纹通常位于第三四九十曲柄外侧面。
产生原因:主要为预锻该处抬高较大,料多,终锻时曲柄镦粗宽度变宽后,发生边缘啃料现象产生折纹。
对策:通过减小预锻该处曲柄横向宽度(即减小该处金属量),常规设计是预锻比终锻宽度小1mm 左右,对此建议再减小1-2mm 左右,如上图康C 曲轴折纹,我们通过将预锻该处曲柄宽度由118.8减小到117(终锻为119.8mm),比终锻小2.8mm ,成功地消除了折纹(见上图)。
另外可适当将终锻该处斜面桥部的R 加大(利于多余金属排出),更利于折纹的消除。
2.2.3 平衡块分模面处折纹特征:该类折纹通常位于平衡块内侧分模面附近,其方向与分模面方向一致。
产生原因:预锻预留连皮中心线与终锻分模导面形状不匹配,相差较多引起。
二者相差过大,终锻锻打时上下模不能同时接触预留的连皮,先接触一侧势必会推动金属向另一侧移动,导致圆角锐化,与上模向分模面处流动的金属汇流形成折纹。
对策:解决方法为控制预、终锻分模落差,控制在10(约为预锻此处R 角的一半)毫米以内。
哪一侧有折纹,修磨预锻模相应一侧。
2.2.4 连杆颈外侧折纹特征:该类折纹通常位于1、3、4、6连杆颈外侧的分模面附近,在型腔深的一侧。
产生原因:由于连杆颈与主轴颈的分模面不在一个水平方向上,有一定的落差,而连杆颈与主轴颈在宽度方向上也不平齐;而主轴颈的有限长度,在模具相应型腔的桥部处二者之间形成了一个斜面过渡形式的连接面,在锻打的过程中,主轴颈的金属外流极易受到该处斜面的阻挡从而侧向流动,而由于连杆颈型腔边缘距离坯料中心较主轴颈远得多,从而在两处金属充填型腔的时间有差异的情况下,从连接斜面侧向流动的金属向连杆颈型腔流动,形成折纹。
对策:此类折纹解决方法是疏导,将三角斜面开通,并将三面汇交处做成SR25 ̄30的球面,使主轴颈一侧多余的金属作纵向流动,补给金属填充连杆颈,从而消除折纹。
2.2.5 校正折纹特征:该类裂纹,发生的数量较少,但是我们在加工厂处理废品时,每个月都有,产生的位置在曲轴两头的主轴径和曲柄的过渡处,产生原因:为锻件弯曲变形大,冷校正一次压下量太大造成。
对策:l产生原因为曲轴冷校正时压下量太大造成。
冷校正后应力难以消除,只能进行时效。
放置至少两个月后再进行探伤检查,以防裂纹件流出厂。
l取消冷校工艺的使用。
冷校的负面影响较大,虽然在表面上达到了消除变形的目的,却给冷加工带来了负面影响。
曲轴加工后应力得到释放,引起曲轴轴径跳动,当跳动量超过磨削量的要求时,曲轴只能报废。
2.3变形2.3.1小端变形特征:该类弯曲变形一般从第二主轴颈处开始变化,弯曲几乎都是向上模弯曲。
产生的原因:随着曲轴越来越长,曲轴小头部分受校正模装模所限,无法全部包容进行校正,以前我们生产的曲轴都用1、7主轴颈作为定位基准,此类问题还可以通过机加工进行弥补,现随着加工厂为解决动平衡问题,纷纷用2、6主轴颈为基准,此问题就充分暴露出来。
对策:l解决办法为想办法将校正模加长,如康C、D6114曲轴就是将校正模端头悬空加长;l若是实在无法加长,可适当将余量加大进行补偿,并定期对切边模进行检查、及时更换。
2.3.2平衡块变形特征:该类变形主要发生在平衡块比较薄的轿车曲轴上,反映的典型特征为平衡块切边后的上下“八”字变形。
该类变形不仅对加工定位带来负面影响,而且去重孔易钻豁。
产生原因:l 凹模与锻件轮廓间隙太小,存在切肉现象;l 凸凹模间隙间隙大宜造成间隙不均匀,从而造成平衡块两侧剪切力不等。
对策:l 在切边凹模的设计上,凹模与锻件轮廓之间的间隙,应在0.3-0.5mm 之间,在保证锻件不切肉的条件下,不致使切边力增大,切边变形问题严重。
l 凸凹模间隙取值在0.8毫米以内。
2.3.3 平衡块镦粗变形特征:平衡块凸模边宽度较另一侧宽度大,在平衡块比较薄的小曲轴上较为明显。
产生原因:凹模刃口老化或者终锻桥部磨损,造成切边力量加大,平衡块发生镦粗变形而展宽,该类缺陷影响到产品最终的动平衡(表现为凸模重)。
对策:l 对此问题的解决方法为在设计时有意将平衡块的上模减薄0.2mm 左右或将拔模角减小0.5度,进行工艺补偿。
l 优化成形工艺,增加精锻工序,减小桥部磨损,减小切边力。
2.4 凹坑2.4.1 氧化坑特征:主要分布在曲轴的型腔较窄、深处,凹凸不平滑。
产生原因:型腔较窄深,又在下模,极易堆积氧化皮等残渣。
对策:坚持按工艺要求对模具进行吹风、润滑,并及时对该类位置用尖锐的工具进行清理。
2.4.2 异物压入氧化坑处特征:此类缺陷出现在下模,位置不定,深度较深。
产生原因:模具顶杆孔内钻有小飞边,飞边脱落后掉入型腔打入下一支锻件上。
对策:1、坚持每生产一件就对模具吹风清理一次,保证及时将异物清出型腔。
2、保证顶杆和顶杆的配合精度,发现顶杆缺损后及时更换,以防止顶杆孔内钻有小飞边。
[结束语]曲轴锻造工艺和生产过程比较复杂,生产中碰到的质量问题很多,以上所列均是相对比较多的一些质量缺陷。
对于质量缺陷的处理方法,在本文中作了比较详细的说明。
但对于具体的工艺参数(如抬高量、轴向间隙、劈料角度等)及局部的形状设计,要根据曲轴的形状,大小及机加工要求不同而区分对待。
相信通过对未知领域(如动平衡性能研究)不断的探索实践及计算机三维模拟的有效运用,曲轴成形还可以进一步的优化,从设计的源头达到提高曲轴质量水平的目的。