二切分轧钢生产
轧钢切分工艺流程

轧钢切分工艺流程轧钢切分工艺是将钢板按照客户要求的尺寸进行切割的工艺过程。
本文将详细描述轧钢切分工艺流程的步骤和流程。
1. 准备工作在进行轧钢切分工艺之前,需要做一些准备工作,包括: - 检查设备:确保设备正常运转,刀片锋利。
- 检查原材料:检查钢板是否符合质量要求,排除瑕疵。
- 调整设备:根据要求调整设备的刀片间距、送料速度等参数。
2. 设定切割尺寸根据客户的要求和生产订单,设定切割尺寸。
通常情况下,可以通过计算机控制设备来设定切割尺寸,确保准确性和一致性。
3. 上料将原材料钢板放置在切割设备上,通常是在滚轮或切割平台上进行。
确保钢板平整、稳固,并进行固定,以避免在切割过程中产生误差。
4. 切割4.1 切割方式根据要求和设备类型,选择合适的切割方式。
常见的切割方式包括: - 刀片切割:使用钢刀片进行切割,可以通过水冷却刀片来降低温度。
- 激光切割:使用激光束进行切割,高精度高速。
- 火焰切割:使用火焰进行切割,适合厚板材。
4.2 切割操作根据设备的操作面板或计算机控制软件,进行切割操作。
按下切割按钮后,设备将自动进行切割,同时切割刀片或激光束将沿着预设的切割尺寸进行移动。
4.3 切割质量控制切割过程中需要对切割质量进行控制,确保切割尺寸的准确性和切割表面的质量。
常见的切割质量控制方法包括: - 视觉检测:使用相机或传感器进行实时的切割质量检测,如表面平整度、边缘质量等。
- 尺寸测量:使用测量仪器对切割尺寸进行检测,如激光测距仪、坐标测量机等。
5. 分料在切割完成后,将切割好的钢板进行分料。
根据客户要求和生产订单,将钢板按照指定的尺寸和数量进行分堆、码放,以便后续加工或发货。
6. 清理和保养切割完毕后,需要对设备进行清理和保养,以确保设备的正常运行和延长设备的使用寿命。
主要包括: - 清理钢板碎屑等杂物。
- 清理切割设备,如刃口、切割床、导轨等。
- 对刀片进行检查和磨削,保持刀片的锋利度。
棒材20螺2线切分轧制技术的开发与应用
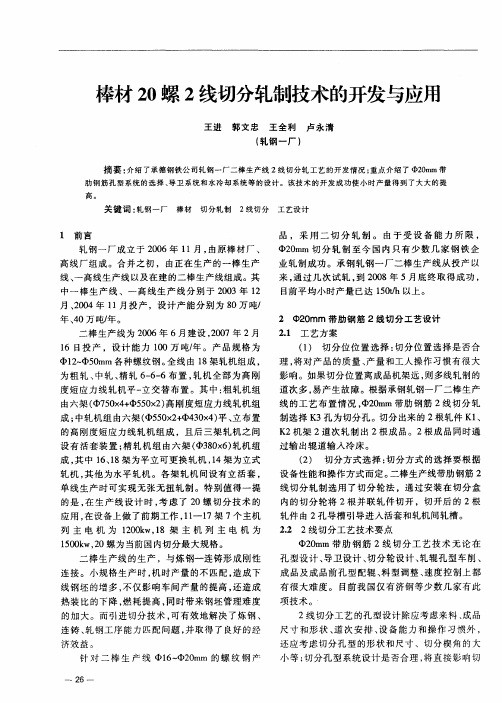
关键 词 : 轧钢一厂 棒材 切分轧制 2 线切分 工艺设计
பைடு நூலகம்1 前 言
品 ,采 用 二 切 分 轧 制 。 由 于 受 设 备 能 力 所 限 ,  ̄2 mm 切 分 轧 制 至 今 国 内 只有 少 数几 家 钢 铁 企 0 业 轧 制 成 功 。承 钢 轧 钢一 厂 二 棒 生产 线 从 投产 以
的高 刚 度短 应力 线 轧 机组 成 ,且后 三 架 轧机 之 间
设 有 活 套装 置 ; 轧机 组 由六 架 ( 8 x ) 机 组 精  ̄3 0 6 轧
道次多 , 易产 生故 障。根 据 承钢 轧钢 一厂 二棒 生产
线 的工 艺 布 置 情 况 , 0 m 带肋 钢 筋 2线 切 分 轧  ̄2 m 制 选 择 K3孔 为切 分 孔 。切 分 出来 的 2根 轧件 Kl 、 K 2机架 2道 次轧 制 出 2根 成 品 。2根成 品 同时通 过 输 出辊 道输 入 冷床 。 ( ) 切分 方 式选 择 : 分 方式 的选 择 要 根据 2 切 设 备 性 能 和操作 方 式而 定 。 二棒 生产线 带肋 钢筋 2 线 切分 轧制 选 用 了 切分 轮 法 ,通 过 安装 在 切 分 盒 内的切 分 轮 将 2根 并 联 轧 件切 开 ,切开 后 的 2根 轧件 由 2孔 导槽 引导进 入 活套 和轧 机 间轧槽 。 22 2线切 分 工艺 技 术要 点 .  ̄2 m 带 肋 钢 筋 2线 切 分 工 艺 技 术 无 论 在 0m
21 工艺 方 案 .
( ) 切 分 位 位 置选 择 : 分位 置选 择是 否 合 1 切 理 , 对 产 品的 质量 、 量 和工 人操 作 习惯 有 很 大 将 产
影 响 。如 果切 分 位 置离 成 品机架 远 , 多线 轧 制 的 则
Φ16mm热轧带肋钢筋两切分技术的开发与应用
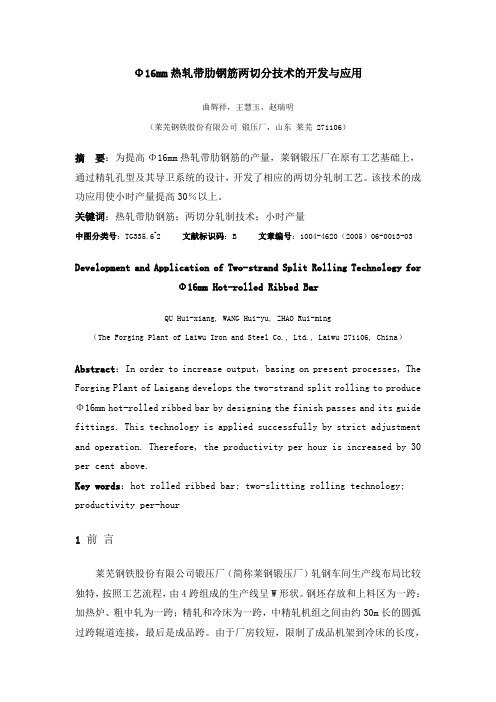
Φ16mm热轧带肋钢筋两切分技术的开发与应用曲辉祥,王慧玉,赵瑞明(莱芜钢铁股份有限公司锻压厂,山东莱芜 271106)摘要:为提高Φ16mm热轧带肋钢筋的产量,莱钢锻压厂在原有工艺基础上,通过精轧孔型及其导卫系统的设计,开发了相应的两切分轧制工艺。
该技术的成功应用使小时产量提高30%以上。
关键词:热轧带肋钢筋;两切分轧制技术;小时产量中图分类号:TG335.6+2 文献标识码:B 文章编号:1004-4620(2005)06-0013-03Development and Application of Two-strand Split Rolling Technology forΦ16mm Hot-rolled Ribbed BarQU Hui-xiang, WANG Hui-yu, ZHAO Rui-ming(The Forging Plant of Laiwu Iron and Steel Co., Ltd., Laiwu 271106, China)Abstract:In order to increase output, basing on present processes, The Forging Plant of Laigang develops the two-strand split rolling to produce Φ16mm hot-rolled ribbed bar by designing the finish passes and its guide fittings. This technology is applied successfully by strict adjustment and operation. Therefore, the productivity per hour is increased by 30 per cent above.Key words:hot rolled ribbed bar; two-slitting rolling technology; productivity per-hour1前言莱芜钢铁股份有限公司锻压厂(简称莱钢锻压厂)轧钢车间生产线布局比较独特,按照工艺流程,由4跨组成的生产线呈W形状。
Ф22mm规格热轧带肋钢筋二切分轧制生产实践
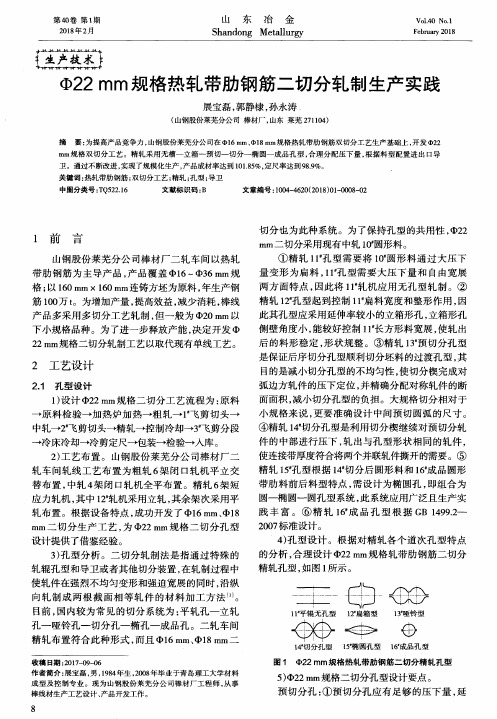
图 1 @22 mm 规 格 热 轧 带 肋 钢 筋 二 切 分 精 轧 孔 型
5)022 mm规 格 二切 分 孔 型设 计要 点 。 预切分孑L:①预切分孔应有足够 的压下量 ,延
8
展宝 磊等
022 mm规格热轧带肋钢筋二切分轧制生产实践
2018年第 1期
伸系数应 为 1.1~1.2;②强迫宽展 系数 为 1.1左右 , 使轧件得到较充分变形 ;③为减小切分楔尖所承受 的轧制力 ,预切分楔尖半径设计为 3.8 mm。
— , 1 —\
. ::
1 切 分 孔 型 l5 i圆孔 型 16 成 品孔 型
收稿 日期 :2017—09—06 作者简 介 :展宝磊 ,男 ,1984年 生 ,2008年毕业于青 岛理工大学材料 成型及 控制 专业 。现为 山钢股 份莱芜分 公司棒 材厂 工程师 ,从事 棒线 材生产工艺设计 、产品开发工作 。
展宝 磊 ,郭 静棣 ,孙永涛
(山钢股份莱 芜分公 司 棒材厂 ,山东 莱芜 27110 4 )
摘 要 :为提高产品竞争力 ,山钢股份莱芜分公 司在 016 mm、018 inm规格 热轧带肋钢筋双切分 工艺生产基础上 ,开发 022
mm规格 双切 分工艺 。精轧 采用无槽 一立 箱一预 切一切 分一椭 圆一 成品孔 型 ,合 理分 配压下 量 ,根 据料 型配置进 出 口导
2 工艺设计
切分也为此种 系统 。为了保持孑L型的共用性 ,022 mm--"切 分 采用 现有 中轧 10"圆形 料 。
①精 轧 1 l 孔型需要 将 10"圆形料 通过大压 下 量 变 形 为扁 料 ,l1 孔 型 需 要 大 压 下 量 和 自由 宽 展 两方面特点 ,因此将 l1 轧机应用无孑L型轧制 。② 精 轧 12"孔 型 起 到 控 制 1 1 扁 料 宽 度 和 整形 作 用 ,因 此其孔型应采用延伸率较小的立箱形孔 ,立箱形孔 侧壁角度小 ,能较好控制 11 长方形料宽展 ,使轧出 后 的料形稳定 ,形状规整 。③精轧 13 预切分孔 型 是保证后序切分孑L型顺利切分坯料的过渡孑L型 ,其 目的是减小切分孔型的不均匀性 ,使切分楔完成对
两线切分轧制技术在阳春新钢铁轧钢厂的应用
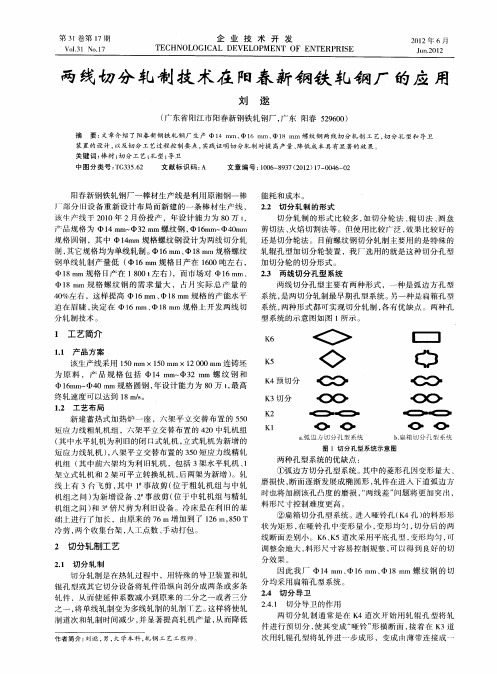
刀处易粘钢 , 从而导致堆钢事故的发生 , 其原因大部分是 前端靠近轧辊处有“ 鼻尖 ” 起引导作用 , 一对切分轮处于 因 为 导 卫 横 梁 标 高 问题 导 致 轧 件 与 导 卫 内 孔 壁 摩 擦 所 中间段 来 撕 开 轧件 , 分 轮后 有 一 把 切 分 刀 , 切 当切 分 轮 未 致 , 因此对导卫对中的安装提出了更高度 的要求 。
12 工 艺布 局 .
K5
◇
.: _ = .: 一 | _ =’ |
C= : l
. I c <
.==I.: . _ = 1 =: | 一| _
K 预切分 4 K 切分 3
K 2
新建蓄热式加热 炉一座 ,六架平立交替 布置 的 50 5 短 应 力线 粗 轧 机 组 ,六 架 平 立交 替 布 置 的 40中轧机 组 2
更 换 成 双通 道 过 渡导 槽 。
从切分道次( 3 出来 的两根并联 圆轧件之 间的连接 K) 3 实际生产控制措施 带 厚度 一 般 为 1m 楔 形 的切 分 轮 边缘 宽度 为 1 m, m, .m 5 而轧件最后是靠切分轮撕开 ,因此切分轮的角度与轧辊
孔 型切 分 楔 的 角度 必 须 严 格 配合 才 能 保 证撕 开 的正 常 完 成 。 型 切分 楔 角 须满 足 轧 件变 形 的要 求 , 切 分轮 的 角 孔 而 度 则直 接 对 能否 将 轧 件 “ 开 ” 切 分 导 卫 的寿 命 产 生 影 撕 及
将 轧件 彻 底撕 开时 , 可通 过 切 分 刀切 开 。 8 1H进 口为滑 动
⑥对于 1H出口扭转导卫扭转辊的角度易跑偏难 紧 8 导 卫 , 口为 R O O * 出 T — B 2型扭 转 导卫 。1H进 口为滚 动 导 固 的问 题 ,采 用 调 整好 角 度 后 再 直 接焊 接 死 的办 法来 得 9 卫 , 口为 方 形滑 动 导卫 。详 细情 况 如 表 1 示 。 出 所 到 了解 决 , 少 了堆 钢 事 故 的发 生 。 减 25 切 分 孔型 的 布 置 . ⑦针对机架及活套 间双通道导槽设计不合理导致频 切分孔型一般布置在精轧道次 ,结合我厂精轧机组 繁堆钢事故 的问题 ,通过优化导槽设计最终得到了很好 的布置形式 ,将 1#和 2#立式轧机 空过 ,7 6 0 1#和 1#平 的解 决 。 8 立可转换轧机全部水平使用 ,9 轧机为终轧道次。孔型 1# 4 效 果 在各 个 机 架 问 的布 置情 况 如 表 2 示 。 所 2 活套 的使 用 及 导槽 的改 进 . 6 自 2 1 年 6月份 开 始 , 步 在 中1 m 、 l m、 00 逐 6m 4m
敬业集团轧钢厂(一、二车间)概况
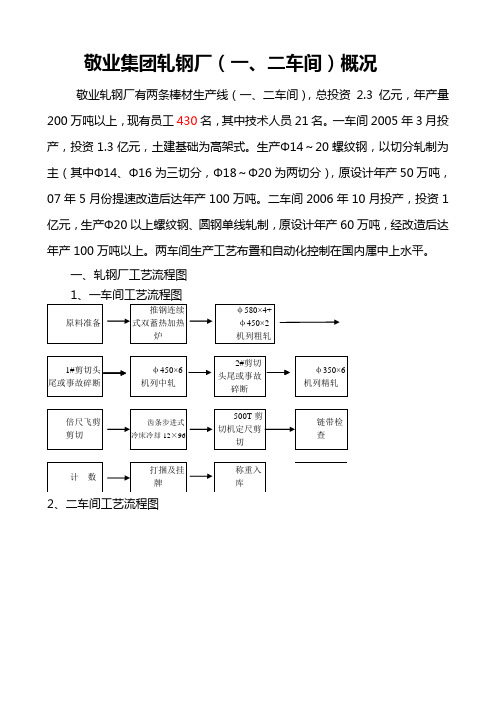
敬业集团轧钢厂(一、二车间)概况敬业轧钢厂有两条棒材生产线(一、二车间),总投资2.3亿元,年产量200万吨以上,现有员工430名,其中技术人员21名。
一车间2005年3月投产,投资1.3亿元,土建基础为高架式。
生产Φ14~20螺纹钢,以切分轧制为主(其中Φ14、Φ16为三切分,Φ18~Φ20为两切分),原设计年产50万吨,07年5月份提速改造后达年产100万吨。
二车间2006年10月投产,投资1亿元,生产Φ20以上螺纹钢、圆钢单线轧制,原设计年产60万吨,经改造后达年产100万吨以上。
两车间生产工艺布置和自动化控制在国内属中上水平。
一、轧钢厂工艺流程图2、二车间工艺流程图二、轧线主要工艺设备及性能:1、两车间加热炉均为端进侧出蓄热式加热炉,一车间加热炉有效尺寸为21 m ×10.6 m ,加热能力120t /h (冷坯),二车间加热炉有效尺寸为29m ×10.6 m ,加热能力150t /h (冷坯)。
燃料是本集团炼铁厂供应的副产品高炉煤气,坯料为150方×10米,由本集团炼钢厂热送。
蓄热式加热和钢坯热送热装两项技术在提高加热质量的同时,又具有显著的经济、节能、减排、环保特色。
2、主轧机:一车间轧机共18架,二车间轧机共16架,均为全平立交替布置。
两车间粗中轧轧机均为Ф580×4+Ф450×8二辊闭口式轧机,一车间精轧机为Ф350×6短应力线轧机,设有5个立活套,二车间精轧机为Ф350×4短应力线轧机,设有3个立活套。
平立交替和活套可实现无扭无张轧制。
3、飞剪:一车间共3台飞剪,1#剪、2#剪分别位于粗、中轧机组之后,用以切头尾或事故碎断,3#剪是倍尺飞剪,位于精轧机组之后;二车间共2台飞剪,1#剪位于粗轧8架之后,用以切头尾或事故碎断,2#剪是倍尺飞剪,位于精轧机组之后4、精整系统由冷床系统、冷剪定尺系统、分捡打捆包装系统及称重标识系统组成。
轧钢切分工艺流程

轧钢切分工艺流程轧钢切分工艺流程是钢铁生产中非常重要的一个环节,它的主要作用是将大块的钢材切割成所需的规格和尺寸,以满足不同客户的需求。
下面将详细介绍轧钢切分工艺流程。
一、原材料准备在轧钢切分工艺流程中,首先需要准备好原材料。
一般来说,原材料是钢板或钢卷,其厚度和宽度根据客户的要求而定。
在准备原材料的过程中,需要对其进行检查,确保其质量符合要求。
二、钢板切割钢板切割是轧钢切分工艺流程中的第一步。
在这一步中,需要将大块的钢板切割成所需的规格和尺寸。
切割的方式有多种,常见的有火焰切割、等离子切割和激光切割等。
不同的切割方式适用于不同的厚度和材质。
三、钢卷切割钢卷切割是轧钢切分工艺流程中的第二步。
在这一步中,需要将大块的钢卷切割成所需的规格和尺寸。
切割的方式有多种,常见的有剪切切割和卷曲切割等。
不同的切割方式适用于不同的厚度和材质。
四、边切割边切割是轧钢切分工艺流程中的第三步。
在这一步中,需要将钢板或钢卷的边缘进行切割,以去除不规则的边缘和毛刺。
这一步的目的是为了使钢材的边缘更加平整,以便后续的加工和使用。
五、定尺切割定尺切割是轧钢切分工艺流程中的第四步。
在这一步中,需要将钢板或钢卷按照客户的要求进行切割,以得到所需的长度和宽度。
这一步的目的是为了使钢材的尺寸更加精确,以满足客户的需求。
六、打标记打标记是轧钢切分工艺流程中的最后一步。
在这一步中,需要在钢材的表面打上标记,以标识钢材的规格、尺寸和批次等信息。
这一步的目的是为了方便后续的追溯和管理。
综上所述,轧钢切分工艺流程是一个非常重要的环节,它直接影响到钢材的质量和使用效果。
在进行轧钢切分工艺流程时,需要严格按照操作规程进行,确保每一步都符合要求,以得到高质量的钢材产品。
22螺两切分改造4页
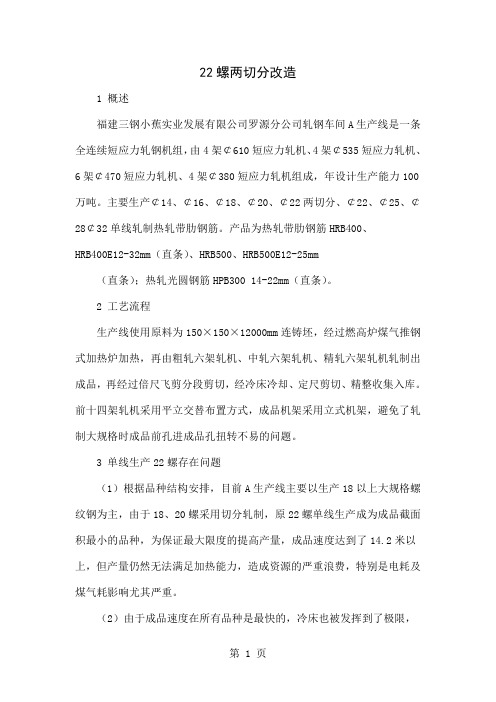
22螺两切分改造1 概述福建三钢小蕉实业发展有限公司罗源分公司轧钢车间A生产线是一条全连续短应力轧钢机组,由4架¢610短应力轧机、4架¢535短应力轧机、6架¢470短应力轧机、4架¢380短应力轧机组成,年设计生产能力100万吨。
主要生产¢14、¢16、¢18、¢20、¢22两切分、¢22、¢25、¢28¢32单线轧制热轧带肋钢筋。
产品为热轧带肋钢筋HRB400、HRB400E12-32mm(直条)、HRB500、HRB500E12-25mm(直条);热轧光圆钢筋HPB300 14-22mm(直条)。
2 工艺流程生产线使用原料为150×150×12000mm连铸坯,经过燃高炉煤气推钢式加热炉加热,再由粗轧六架轧机、中轧六架轧机、精轧六架轧机轧制出成品,再经过倍尺飞剪分段剪切,经冷床冷却、定尺剪切、精整收集入库。
前十四架轧机采用平立交替布置方式,成品机架采用立式机架,避免了轧制大规格时成品前孔进成品孔扭转不易的问题。
3 单线生产22螺存在问题(1)根据品种结构安排,目前A生产线主要以生产18以上大规格螺纹钢为主,由于18、20螺采用切分轧制,原22螺单线生产成为成品截面积最小的品种,为保证最大限度的提高产量,成品速度达到了14.2米以上,但产量仍然无法满足加热能力,造成资源的严重浪费,特别是电耗及煤气耗影响尤其严重。
(2)由于成品速度在所有品种是最快的,冷床也被发挥到了极限,造成冷床上钢故障是所有品种中最多的,严重制约了产能的提升,而成品在冷床停留的时间是最短的,又造成成品还没有完全冷却就到了定尺剪切,很容易造成成品的弯曲,既影响产品表面质量,又不利于负偏差的控制。
4 ¢22螺两切分设计思路(1)充分利用¢20螺两切分的工艺基础进行修改设计:1#用箱形孔、2-5#用平辊轧制,6#采用圆孔进行轧件的收尾,防止开花尾的产生,7-11#采用平辊轧制,取消12#,13、14#采用平辊轧制,15#预切,16#切分同,经过17、18#轧出成品。
Φ25mm螺纹钢筋两线切分新工艺的应用与实践

Φ25mm螺纹钢筋两线切分新工艺的应用与实践摘要:本文介绍了陕西龙门钢铁有限责任公司轧钢厂棒二线25mm规格螺纹钢筋两切分工艺技术的生产实践,在一年多的生产实践中通过孔型,导卫,轧制参数的不断改进和优化,生产逐渐稳定顺行,产量的经济指标全面达标。
关键词:Φ25规格;两线切分;应用;实践前言切分轧制是在轧机上利用特殊的轧辊孔型和导卫或者其他切分装置,将原来的一根坯料纵向切成两根或以上的轧件,进而轧制多根成品或中间坯的轧制工艺。
目前切分轧制技术已发展到五切分轧制,且两线切分、三线切分轧制技术和四线切分轧制技术作为成熟技术已经普遍应用在小规格螺纹钢的生产中,但是像Φ25这种大规格切分工艺国内是不不常见。
1.Φ25规格两切分工艺概况龙钢公司轧钢厂棒二线2014年投产,成品架次设计速度最高16米/秒,全线采用高刚度短应力轧机,年产120万t钢材,产品规格Φ12—25mm热轧带肋钢筋和热轧直条光圆钢筋,全线使用18架轧机,平立交替,轧机工艺布局6—6—6三段式布局,即粗轧6架,中轧6架,精轧6架,轧制的坯料为170mmx170mm,轧制速度设计为10米/s,钢材的生产流程是:原料准备—上料—加热—粗轧—1#飞剪切头—中轧—2#飞剪切头切尾—精轧—3#倍尺飞剪—冷穿冷却—定尺剪切—检查、分选—计数—打捆—称重—挂牌—入库。
1.1工艺布局龙钢公司开2016年底开发出的Φ25规格两切分工艺,全线使用全线使用15架轧机,其中粗中轧使用1#-9#架,9#为无孔型轧辊,精轧使用13#—18#共6架轧机,K6为无孔型轧机,K5为箱型孔,K4为预切孔型,K3为切分孔型,。
实际生产中精轧共使用了3个活套,布局为14#—15#之间1个,15#—16#中间1个,17#—18#中间1个。
精轧孔型布置图见图1.切分原理图见图2。
图1精轧孔型图图2切分装置示意图1.2导卫选择切分轧制对导卫的要求高,生产普通品种时,只采用单导轮导卫即可,而切分轧制从第16#架进口开始就要采用双轮导卫,即每个导卫要4个导轮,以保证能稳定地夹持钢料。
二切分轧制技术在涟钢棒材一厂的应用
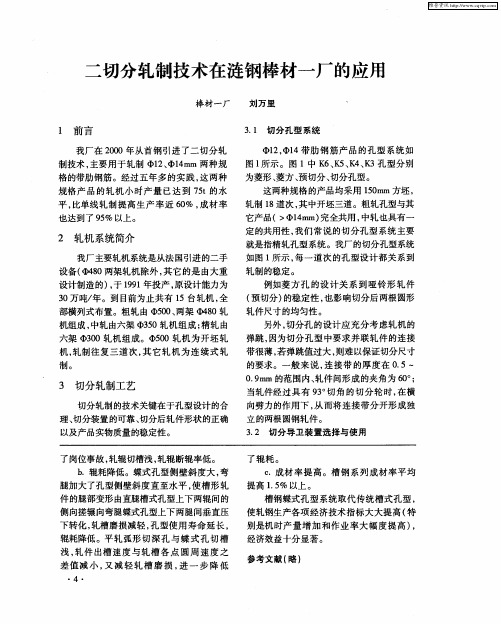
3 O万吨/ 年。到 目前为止共有 1 5台轧机 , 全
部横列式布置。粗轧 由 5o 两架 8 o、 O轧 机组成 , 中轧 由六架 3O轧机组 成 ; 5 精轧 由
六架 3 o轧机组成。 5o轧机为开坯轧 o o 机, 轧制往 复三道次 , 它轧 机为连 续式轧 其
制。
规格产 品的轧机小 时产量 已达 到 7 t 5 的水
平, 比单线轧制提高生产率 近 6 % , 0 成材率
也 达到 了 9 % 以上 。 5
2 轧 机系统简介
我厂 主要 轧机 系统是 从法 国引进 的二 手
设备( 8 两架轧机除外 , O 其它 的是 由大重
设计 制造 的) 于 19 年 投产 , , 91 原设 计 能力 为
利 的通过活套进入下一道次 。
中。扭转导卫的使用要特别注意轧件尺寸的 变化和扭转辊的磨损程度。
32 3 切 分导 卫装 置 的选择 .. 我厂 轧 制 qlm qlm 两 种 小 规 格 b2 m、 4 m b
4 需注 意的问题
采用切分轧制 , 切分 孔道次 由切分装 置
审
图1 1 、 4带肋 钢筋产品的孔型 系统 2 1
扭转导卫装置 由扭转管、 导辊 和导 卫盒 组成。轧件通过扭转管进入两个导辊之 间 ,
按照工艺要求调整好 导辊的开 口度 , 使轧件 绕心形翻转, 从而正确进入下一机架 的导卫
最平稳 的状态 ; 在切分体 的后部安装 了分 料 盒 以及分料管 , 用来保证分 开的两 根轧件顺
322 扭转 出 口导 卫 的选 择 ..
由于我厂使用 的全部 是横列式轧机 , 故 在双数轧机 的出 口必须使用扭转导卫才可以 保证轧件的均匀变形 ( 在单 数轧机上使用 简 单 的无缝钢管就可 以满足了) 。
Φ22螺纹两切分轧制生产实践

Φ22螺纹两切分轧制生产实践作者:温健来源:《中国科技纵横》2014年第10期【摘要】简要介绍福建三安钢铁有限公司轧钢厂Φ22螺纹两切分轧制工艺,轧制过程中温度、轧机张力、料型等工艺控制要点,两线差调整方法,导卫安装的关键性,并针对在Φ22螺纹两切分轧制中发现的工艺故障、产品质量不稳定等现象,提出解决的办法和各个环节应注意的问题。
【关键词】两切分工艺控制要点改进措施1 引言所谓切分轧制技术,即采用特殊的切分孔型或辅助切分手段,在轧制过程中使轧件在强烈的不均匀变形和强迫宽展的同时,沿纵向轧制成两根或两根以上截面相同或不等的轧件的材料加工新方法[1]。
我国切分技术近年发展较快,日趋成熟,连轧棒材生产线已普遍采用切分轧制技术。
采用切分轧制技术有如下优点:(1)提高生产效率,与单线轧制工艺相比,生产同样的产品,机时产量较单线轧制可以提高50%-80%;(2)由于生产效率的提高,进一步提升了经济技术指标、降低产品成本、减少能耗,吨钢煤气耗减少30%至40%,吨钢电耗可以节约20%以上;(3)单线轧制的轧制速度越高,越容易出现红钢轧后穿水冷却不均匀,倍尺弯曲,冷床上钢位置相差太大,倍尺长度不稳定等缺陷,相应的工艺故障也越多,使用切分轧制后,部分规格由于轧制速度降低,实际生产过程中的吨钢工艺故障率更低。
2 概述三安轧钢厂棒材生产线2008年11月份底正式投产,设计年产100万吨材,为提高Φ22螺纹机时产量,降低消耗,2011年开发了Φ22螺两线切分轧制工艺,并从11月开始使用两切分轧制工艺正常生产,三安轧钢厂棒材生产线成为福建省内第一条成功开发Φ22螺两线切分轧制工艺的生产线。
三安轧钢厂棒材生产线主要的工艺装备有:步进梁双蓄热式加热炉;18架单独传动的短应力轧机(粗轧、中轧、精轧各6架,呈平立交替布置,其中第16、18架为平立可转换短应力线轧机,最大轧制速度:15m/s)。
成品机架后设有三段穿水冷却装置、倍尺飞剪、裙板、冷床,自动计数系统及自动成型打捆机等。
我厂二切分轧制生产实践

我厂二切分轧制生产实践陈爱平卢平安钟海清杨世平何水金(新余钢铁有限责任公司棒材厂江西新余338001)摘要:本文主要介绍了我厂切分轧制工艺生产的过程及生产过程中出现的一些问题和改进效果。
关键词:二切分,轧制,生产,问题,改进效果1 前言新余钢铁有限责任公司棒材厂是一条年设计能力为40万吨的棒材半连续生产线,它是在利用现行可靠工艺技术和生产设备设施的基础上建成投产的。
原料:124方、130方、150方主要产品规格:螺纹钢:Φ12—36园钢:Φ16--Φ36其中:Φ12- Φ14螺纹钢轧制总量占20%左右。
由于Φ12- Φ14若单线生产产量太低,能耗高,机架数目多,场地受限,而采用切分轧制,产量可提高至少50%,且能耗低,机架数量少,因而决定Φ12- Φ14采用二切分轧制。
2 切分轧制工艺概述2.1 设备简介我厂是一条半连轧生产线,全线共布置13架水平轧机。
其中粗轧是一架530三辊开坯机,中轧为6架Φ400×4+Φ350×2闭式水平轧机,精轧为6架Φ300×6闭式水平轧机,K7-K2间均设立式活套,K1,K2间不起套。
Φ12,Φ14切分轧制均不甩机架,采用切分轮法。
精轧孔型使用如下:K6为菱形孔,K5为弧边方孔,K4为哑铃预切孔型,K2为椭圆孔,K1为成品孔。
2.2工艺平面布置图3 切分轧轧制生产情况3.1 生产准备3.1.1 车削预切分孔,切分孔轧辊车削精度要高,成品孔,成品前孔轧槽配辊两线间的中心距要保证。
3.1.2 导卫1)导卫安装首先要求检查导卫备件的质量,尺寸公差,表面质量是否符合工艺要求,禁止不合格品进行安装,导卫的开口度每架次用专用样棒进行安装与检测,确保导卫安装质量,即导卫的内腔尺寸,导轮的开口度尺寸符合要求。
2)K6出口DU65为带扭转的滚动导卫,K6轧件进K5孔能自动找正,K5进口导轮尺寸不要将K6轧件夹持很紧,K5出口CTR45度扭转。
3)K4轧件的形状控制对切分轧制的顺利很关键,2个亚铃形的面积要基本一样,防止切分不均匀,K4、K3进口为0930B四辊滚动导卫,导轮间距要合适,以防止料形发生扭转,K4出口为滑动导卫,滑动导板的头部一定要与亚铃形孔相吻合。
_18mm螺纹钢筋二线切分轧制工艺开发实践

1 切分轧制对轧机设备负荷的要求
由于 实 现 了 “一 切 二 ”, 采 用 切 分 轧 制 工 艺 后 , 生 产同一规格产品较单线相比道次变形量增加很大, 这就 必然要求现有设备轧机负荷足够大, 否则会出现轧机电机 跳闸或烧损轧辊轴承等事故。为了预测现实生产线中是否 能实现切分轧制, 必须根据现场的实际情况计算出轧机 的负荷。根据金属变形抗力模型 [3], 计算出材料的变形 抗力, 然后通过现场轧制参数表计算出各项轧制力能参 数 , 最 终 得 出 开 轧 温 度 为 1050℃时 , Φ18mm 螺 纹 钢 筋 切分轧制过程中的轧机负荷如图 1 所示。
轧孔型系统采用与其它产品共用的孔型系统, 以减少轧
辊数量、增大效率; 精轧孔型系统则采用专用的切分孔
型系统, 需
K6
K6
要精确计算
K5
K5
设计如图 3
所示。
K4
K4
这两种
K3
K3
孔型系统的
区别主要在
K2
K2
K6、K5 道 次
上。每种方
K1
K1
案都有各自
( a) 小规格产品孔型
( b) 大规格产品孔型
( 四川省有色冶金研究院, 四川 成都 610081)
摘 要: 棒材连轧生产线可应用切分轧制工艺实现提高产量、节约成本。本文结合某钢铁厂棒材生产线 的实际情况, 设计开发了 Φ18mm 大规格螺纹钢筋二线切分轧制工艺, 对切分轧制孔型系统和 导卫装置的选择和设计进行了较为详细的分析。
关键词: 切分轧制; 螺纹钢筋; 孔型系统; 导卫设计 中图分类号: TG335 文献标识码: A 文章编号: 1002- 6673 ( 2007) 04- 055- 03
切分轧制技术

一、切分轧制切分轧制是在轧机上利用特殊的轧辊孔型和导卫或者其他切分装置,将原来的一根坯料纵向切成两根以上的轧件,进而轧制多根成品或中间坯的轧制工艺。
采用切分轧制技术可缩短轧制节奏,提高机时产量,显著提高生产效率,降低能耗和成本。
目前切分轧制技术已发展到五切分轧制,且两线切分轧制技术和三线切分轧制技术作为成熟技术已经普遍应用在小规格螺纹钢的生产中。
1.1切分轧制的特点切分轧制有如下的优点:(1)在轧钢主要设备相同的条件下,可以采用较大断面的原料或相同原料断面下,减少轧制道次。
进而可以减少新建或改建的厂房面积,减少设备投资。
(2)减少坯料规格,提高小断面轧件产量。
简化坯料规格和孔型设计。
并使轧机生产不同规格时负荷均匀,产量达到最大。
(3)提高轧机生产率。
由于采用切分轧制可以使坯料尺寸增加时不增加轧制道次和节奏时间。
(4)节约能源。
获得同样断面轧件切分时道次少,温降小,变形功少,消耗的电能大幅降低。
温降小,可降低开轧温度,节省燃料。
(5)使电机负荷分配合理,在多品种生产的轧机上,电机功率一般按大规格设计,小规格身材时电机处于轻负荷运行状态,采用切分轧制,可加大轧制小规格时电机负荷,使其效率趋于最佳。
(6)提高经济效益。
(7)改变孔型结构,变不对称产品为对称产品。
切分轧制的缺点是:(1)切分部位带毛刺,切口不规则,轧后易形成折叠,影响轧材表面质量。
因此,切分轧制多用于轧制螺纹钢和开坯道次。
(2)钢锭、连铸坯的缩孔、夹杂和偏析多位于中心部位,经切分后易暴漏于表面,形成缺陷。
(3)当剪切方法分开并联轧件时,轧件易扭转,影响轧件质量。
1.2切分方法切分轧制的切分方法可分为两大类:纵切法和辊切法。
纵切法:在轧制过程中把一根轧件利用孔型切分成两根以上的并联轧件,再利用切分设备将并联轧件分成单根轧件。
根据所用切分设备不同,可进一步分为几种方法。
(1)切分轮切分法。
切分轮是一对从动轮安装在轧机的出口处,靠轧件剩余摩擦力剪切轧件。
谢韦尔钢厂切分轧制改造的设计及应用
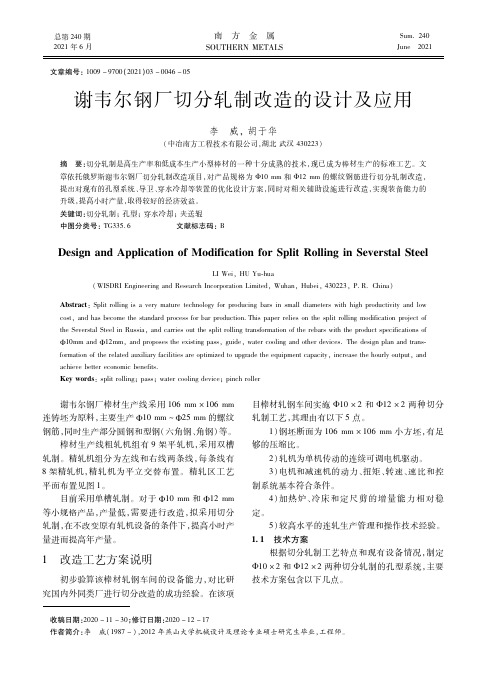
总第240期2021年6月 南 方 金 属SOUTHERNMETALSSum.240June 2021 收稿日期:2020-11-30;修订日期:2020-12-17 作者简介:李 威(1987-),2012年燕山大学机械设计及理论专业硕士研究生毕业,工程师。
文章编号:1009-9700(2021)03-0046-05谢韦尔钢厂切分轧制改造的设计及应用李 威,胡于华(中冶南方工程技术有限公司,湖北武汉430223)摘 要:切分轧制是高生产率和低成本生产小型棒材的一种十分成熟的技术,现已成为棒材生产的标准工艺。
文章依托俄罗斯谢韦尔钢厂切分轧制改造项目,对产品规格为Φ10mm和Φ12mm的螺纹钢筋进行切分轧制改造,提出对现有的孔型系统、导卫、穿水冷却等装置的优化设计方案,同时对相关辅助设施进行改造,实现装备能力的升级,提高小时产量,取得较好的经济效益。
关键词:切分轧制;孔型;穿水冷却;夹送辊中图分类号:TG335.6 文献标志码:BDesignandApplicationofModificationforSplitRollinginSeverstalSteelLIWei,HUYu hua(WISDRIEngineeringandResearchIncorporationLimited,Wuhan,Hubei,430223,P.R.China)Abstract:Splitrollingisaverymaturetechnologyforproducingbarsinsmalldiameterswithhighproductivityandlowcost,andhasbecomethestandardprocessforbarproduction.ThispaperreliesonthesplitrollingmodificationprojectoftheSeverstalSteelinRussia,andcarriesoutthesplitrollingtransformationoftherebarswiththeproductspecificationsofΦ10mmandΦ12mm,andproposestheexistingpass,guide,watercoolingandotherdevices.Thedesignplanandtrans formationoftherelatedauxiliaryfacilitiesareoptimizedtoupgradetheequipmentcapacity,increasethehourlyoutput,andachievebettereconomicbenefits.Keywords:splitrolling;pass;watercoolingdevice;pinchroller 谢韦尔钢厂棒材生产线采用106mm×106mm连铸坯为原料,主要生产Φ10mm~Φ25mm的螺纹钢筋,同时生产部分圆钢和型钢(六角钢、角钢)等。
双道箱形孔切分轧制项目探究
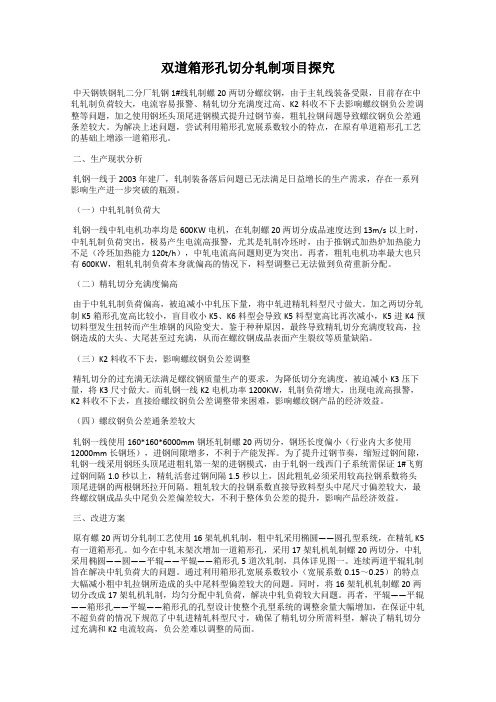
双道箱形孔切分轧制项目探究中天钢铁钢轧二分厂轧钢1#线轧制螺20两切分螺纹钢,由于主轧线装备受限,目前存在中轧轧制负荷较大,电流容易报警、精轧切分充满度过高、K2料收不下去影响螺纹钢负公差调整等问题,加之使用钢坯头顶尾进钢模式提升过钢节奏,粗轧拉钢问题导致螺纹钢负公差通条差较大。
为解决上述问题,尝试利用箱形孔宽展系数较小的特点,在原有单道箱形孔工艺的基础上增添一道箱形孔。
二、生产现状分析轧钢一线于2003年建厂,轧制装备落后问题已无法满足日益增长的生产需求,存在一系列影响生产进一步突破的瓶颈。
(一)中轧轧制负荷大轧钢一线中轧电机功率均是600KW电机,在轧制螺20两切分成品速度达到13m/s以上时,中轧轧制负荷突出,极易产生电流高报警,尤其是轧制冷坯时,由于推钢式加热炉加热能力不足(冷坯加热能力120t/h),中轧电流高问题则更为突出。
再者,粗轧电机功率最大也只有600KW,粗轧轧制负荷本身就偏高的情况下,料型调整已无法做到负荷重新分配。
(二)精轧切分充满度偏高由于中轧轧制负荷偏高,被迫减小中轧压下量,将中轧进精轧料型尺寸做大。
加之两切分轧制K5箱形孔宽高比较小,盲目收小K5、K6料型会导致K5料型宽高比再次减小,K5进K4预切料型发生扭转而产生堆钢的风险变大。
鉴于种种原因,最终导致精轧切分充满度较高,拉钢造成的大头、大尾甚至过充满,从而在螺纹钢成品表面产生裂纹等质量缺陷。
(三)K2料收不下去,影响螺纹钢负公差调整精轧切分的过充满无法满足螺纹钢质量生产的要求,为降低切分充满度,被迫减小K3压下量,将K3尺寸做大。
而轧钢一线K2电机功率1200KW,轧制负荷增大,出现电流高报警,K2料收不下去,直接给螺纹钢负公差调整带来困难,影响螺纹钢产品的经济效益。
(四)螺纹钢负公差通条差较大轧钢一线使用160*160*6000mm钢坯轧制螺20两切分,钢坯长度偏小(行业内大多使用12000mm长钢坯),进钢间隙增多,不利于产能发挥。
- 1、下载文档前请自行甄别文档内容的完整性,平台不提供额外的编辑、内容补充、找答案等附加服务。
- 2、"仅部分预览"的文档,不可在线预览部分如存在完整性等问题,可反馈申请退款(可完整预览的文档不适用该条件!)。
- 3、如文档侵犯您的权益,请联系客服反馈,我们会尽快为您处理(人工客服工作时间:9:00-18:30)。
切分轧制生产实践
摘要:本文对轧厂切分轧制技术做了总结,对生产操作中孔型设计、导卫装置等做了详细分析,为提高产品的成材率及各种规格质量进行了深入探讨。
关键词:螺纹钢生产;二切分;轧制技术要求
1 前言
轧钢厂2002年引进的小型棒材轧机,对Ф12、Φ14、Φ16mm三种规格带肋钢筋采用二切分轧制,轧机小时产量达到70t,接近其它规格平均85t的水平,且与其它产品共用150mm方连铸坯,经Ф500×1/Ф400×2/Ф350×4/Ф300×6十三架轧机15道次轧出成品。
粗轧和中轧道次孔型具有共用性,缩短更换规格停机时间,提高了轧机作业率。
目前,轧厂φ16mm以下规格的建筑用带肋钢筋都采用切分工艺轧制,既保证了轧制小规格具备的条件,又保证了产品质量和产量,更好地满足市场的要求,取得了明显的经济效益。
2切分轧制技术特点
切分轧制是国家推广的新技术,也是今后发展方向。
据不完全统计,在小型棒材的产品中,直径小于φ16mm规格的钢筋约占总量的60%。
而棒材生产率随产品直径的减小而降低,因此要使各种规格产品的生产率基本相等,必须采用切分轧制,从而导致了棒材切分轧制技术的广泛应用。
切分轧制的技术关键在于切分设备的可靠性、孔型设计的合理性、切分后轧件形状的正确性以及产品质量的稳定性。
切分轧制具有以下明显的技术特点:
2.1 均衡不同规格产品的生产能力
使现有加热炉、轧机、冷床及其它辅助设备的生产能力有效利用和充分发挥。
因此,减少了厂房面积,减少了设备投资。
2.2 大幅度提高轧制小规格产品的机时产量
采用切分轧制由于缩短了轧件长度,从而缩短了轧制周期,提高了轧机生产率。
2.3 节约能源、降低成本
采用切分轧制变形量小,电机负荷分配均衡,电机效率趋于最佳状态,电量消耗趋于最低。
节约大量能源,且由于轧制成品长度减短,钢坯的出炉温度可适当降低。
但切分轧制也存在一些问题,主要表现在:棒材切分带容易产生毛刺,如调整不当有可能形成折叠,影响产品质量;对坯料的质量要求较严格,切分后坯料中心部位的缩孔、疏松等易暴露在轧件表面;对导卫、切分装置精度要求很高,在操作上应调整好进、出口导卫及切分轮间距,确保轧件对称地切分。
3切分工艺
3.1切分工艺布置
2×Ф12~16mm带肋钢筋产品的孔型系统如图1所示。
图1中k6、k5、k4、k3孔型分别为菱形、菱方、预切分、切分孔型。
该产品采用150mm方坯,轧制15道次。
粗轧孔型与中轧孔型具有共用性,精轧为切分孔型系统。
图1 2×Ф12—16mm带肋钢筋产品的孔型系统
3.2 轧辊孔型、导卫装置的控制
切分孔型在设计时应充分考虑轧机的弹跳,在预切分、切分孔型中要求并联轧件的连接带很薄,若弹跳值过大,则难以保证切分尺寸的要求。
同时,切分孔楔角应大于预切分的楔角,以保证楔子侧壁有足够的压下量和水平分力。
楔角一般取60°左右,楔子角度和顶部的设计要满足楔子头部耐冲击、抗磨损;在切分孔型中楔子尖部应高于辊面0.2mm左右,保证顶部不被冲坏。
在加工轧辊时,由于菱方孔、预切孔、切分孔形状复杂,车刀不易手工磨出,用数控线切割机加工成型刀具。
轧件在切分孔后被导卫分成两根,即最后两道次分开的轧件同时在两个轧槽中轧制,因此具有两个通道的导卫中心距与该两个轧槽中心距应很好的对正,导卫的制作安装要精确,且同时使用的两道轧槽的间距要准确。
为此在轧槽加工时,使用长跨样板,这样为导卫的调整创造了条件。
由于切分轧制主要是小规格产品,在轧槽加工时,还要保证轧辊上、下轧槽、孔型开口圆角的对称度。
上线前再进行轴向、径向的微调,以消除轴错等偏差。
轧制时,对于菱方孔要认真检查磨损情况,若该道次磨损不均、磨损严重要及时更换,防止轧件形状不对称、不正确,在经出口扭转导卫后不能以正确的角度进入预切孔,而产生堆钢。
该孔型的轧制量应限制在一定的范围内,轧到额定吨位时必须及时更换。
预切孔、切分孔因孔型较相似,都有楔角,由于强迫宽展,楔角顶部极易磨损,使得切分带厚度增大,从而增加切分刀片、切分轮的负荷,且因其受冲击较大易缺损,所以应及时换槽。
导卫方面要注意调整好K3出口切分导卫和K5出口扭转导卫。
切分导卫上、下切分轮间隙十分关键,过小、过大都易造成事故。
一般该间隙应控制在0.4mm左右。
扭转导卫的作用是将菱方形轧件扭转45°导入预切孔型,即导辊孔型,因此要保证扭转角度,否则会在K2—K3、K3—K4、K4--K5之间易产生堆钢,K5进口导卫要设计合理,以确保轧件能够轧出基本对称的菱方形状。
这三个导卫在使用时,还要注意观察切分轮、扭转辊的磨损情况及润滑、冷却状况,并要求及时调整更换。
3.3 轧件尺寸及活套的控制
由于切分轧制,轧件进入精轧后就进入切分的实质性阶段,因此精轧来料的尺寸应符合工艺技术要求。
通过调整K7轧机使轧件尺寸形状准确,保证轧件经扭转导卫以要求的角度进入预切孔。
预切孔、切分孔的辊缝值要及时调整以补偿孔型的磨损量,使切分带厚度控制在一定范围。
活套的控制要设置合适的高度,并通过前、后轧机速度的调整,消除张力,特别是当轧件切分开后,由于单支轧件断面变小,活套控制不当,易产生拉钢或堆钢,造成轧件长短不一,上冷床后难以齐头,甚至将会造成废品或事故。
当切分后的两支轧件起套高度相差较大时,应调整预切孔或切分孔的入口导卫(最好入口导卫横梁为可移动横梁,保证导卫在轧制过程中能够及时得到调整),
使轧件被均匀的切分,保证两根成品的尺寸满足标准要求。
4 需要注意的问题
采用切分轧制,切分孔道次由切分装置配合孔型最终分开两根并联轧件,如果工艺尺寸控制不当在轧件表面被切分部位将产生毛刺,影响成品表面质量;同时导卫在使用时易粘连氧化铁皮而导致生产事故。
并且因切分不均易造成两根轧件的尺寸偏差。
针对这些问题,必须在生产过程中严格控制工艺尺寸、及时调整、更换轧槽和导卫,才能保证良好的产品质量,提高轧机作业率,降低材料消耗。
5 结束语
棒材已成功地进行了二切分轧制生产,产品质量完全符合技术要求。