MSA数据收集表
计数型msa表单

计数型msa表单
计数型MSA表单是一种用于收集和统计数据的表单。
该表单可以用于各种目的,例如调查、评估和跟踪进展等。
创建计数型MSA表单的第一步是确定需要收集的数据类型。
这可以包括定量数据(例如数量、百分比等)或分类数据(例如选择项、评级等)。
然后,根据数据类型创建相应的字段或问题。
对于定量数据,可以使用数字输入框或滑动条,而对于分类数据可以使用单选框或复选框。
接下来,为每个字段或问题添加适当的标签,以便参与者能够理解并回答正确。
这些标签应该简洁明了,并且没有歧义。
此外,还可以添加一些说明或提示,以帮助参与者理解问题的背景或如何回答。
在表单的设计过程中,应该考虑到数据的一致性和完整性。
为此,可以添加验证规则,例如确保数字输入在指定范围内,或者至少选择一个选项。
这些验证规则可以减少错误数据的输入,并提高数据的质量。
一旦表单创建完成,可以通过多种方式进行分发。
例如,可以通过电子邮件发送给参与者,或者将表单链接分享给他们。
此外,还可以将表单嵌入到网站或应用程序中,以方便参与者的访问和填写。
当参与者开始填写表单时,数据将自动收集和存储。
可以使用表单工具提供的分析功能来对数据进行统计和可视化。
这些功能可以帮助识别趋势、展示结果,并为后续的决策提供支持。
总而言之,计数型MSA表单是一种强大的工具,可以帮助收集和统计数据。
通过合理的设计和分发,可以提高数据的质量和可靠性,并为各种应用场景提供有价值的信息和见解。
KAPPA【MSA】

Minitab工具
Kappa计算也可以通过软件Minitab来实现 路径: 打开Minitab 软件-打开工作表- 统计-质量工具-属性一致性分析.下表为 范例.
范例
1.打开工作表,选择kappa test excl.
2. 点击统计-质量工具-属性一致性分析
3.输入数据:属性列(T)为“判定值”,样本(L)为“样品”,检验 员(A)为“检验员”
下表代表上表的数据,其中每个单元格 用总数的百分比来表示
Rater A First Measure Good Bad Rater A Second Measure
检验员A比例
代表10/20
Good Bad
0.5 0.05 0.55
0.1 0.35 0.45
0.6 0.4
由行和列的总和计算而得
计算检验员A的Kappa值
◆测试样品收集
在选择测试样品时,要考虑以下几方面:
如果只有两个类别:良品和次品,
◆至少应该选择20个良品和20个次品
最多可选择 50个良品和50个次品
尽量保持大约50%的良品和50%的次品
选择不同程度的良品和次品
如果样品类别超过2种,其中一类是优良,其它类别是不同 种类的缺陷方式 ◆至少应该选择大约50%的良品和每种缺陷方式最少为10%的
3第二格代表检验员a在第一次测量中判定一个样品为次品在第二次测量中判定为良品的次数第四格代表检验a在第一次测量和第二次测量中判定一个样品为次品的次数第三格代表检验员a在第一次测量中判定一个样品为良品在第二次测量中判定为次品的次数交叉表边格的数字代表行和列的总和交叉表比例检验员a比例下表代表上表的数据其中每个单元格用总数的百分比来表示代表1020由行和列的总和计算而得对kappa的定义将有所不同取决于我们是在定义检验员内部kappa还是在定义检验员之间的kappa计算检验员a的kappa值pobserved检验员两次判断一致比率检验员a两次一致判定为良品
MSA分析报告总结归纳

XX/840-004B 公司XX:L2017003№分析报告计量型MSA日期:日2月232017年人:施实陈秋凤、雷丽花、欧阳丽敏评价人:张志超仪器名称:数显卡尺(中间检验)XXX仪器编号:分析结论:合格不合格审核:批准:计量型MSA分析报告目录1 稳定性………………………………………………………………………………………4 ………………………………………………………………………………………偏倚7 线性...................................................................................................重复性和 (9)再现性.对于有条件接收的项目应阐述接受原因: 备注.第一节稳定性分析1.1 稳定性概述在经过一段长时间下,用相同的测量系统对同一基准或零件的同一特性进行测量所获得的总变差,即稳定性是整个时间的偏倚变化。
1.2 试验方案2017 年 02 月份,随机抽取一常见印制板样品,让中间检验员工每天的早上及晚上分别使用数显卡尺对样品外形尺寸测量5次/组,共测量25组数据,并将每次测量的数据记录在表1。
1.3 数据收集表1 稳定性分析数据收集记录表1.4 测量系统稳定性可接受判定标准1.4.1 不允许有超出控制限的点;1.4.2 连续7点位于中心线同一侧;1.4.3 连续6点上升或下降;1.4.4 连续14点交替上下变化;1.4.5 连续3点有2点距中心的距离大于两个标准差;1.4.6 连续5点中有4点距离中心线的距离大于一个标准差;1.4.7 连续15点排列在中心线的一个标准差范围内;1.4.8 连续8点距中心线的距离大于一个标准差。
1.5 数据分析图1 中间检验_数显卡尺 Xbar-R控制图从图1 Minitab生成Xbar-R控制图可知,没有控制点超出稳定性可接受判定标准,表明该测量系统稳定性可接受。
MSA分析报告样本

量器规 格:
AX-114N
测定日: 报告者:
工序位 置:
温 度: 24.3℃
湿 度:
48
%
从 数据收 集表:
R=
0.0960
Xdiff = 0.0463
测量单元分析
Rp= 7.0578
总变差%(TV)
第 8 页,共 18 页
1. 重复性 -装置 变差 (EV)
2. 再現性 -測定 者变差 (AV)
0.100
0.050
0.000
1
2
3
4
5
6
7
8
9
10
评价人C UCL CL
评价者
评价人A
评价人B
评价人C
样 品 1 2 3 4 5 6 7 8 9 10
1 2 3 4 5 6 7 8 9 10
1 2 3 4 5 6 7 8 9 10
第 16 页,共 18 页
读
1
12. 19. 12. 15. 12. 12. 12. 12. 12. 12. 980 840 780 550 850 930 790 860 890 850
极差
0.070 0.010 0.090 0.230 0.100 0.070 0.090 0.100 0.080 0.060 Rb=
13.891
13.913 13.876 0.090
11
C
1 12.970 19.880 12.700 15.810 12.780 12.900 12.740 12.810 12.860 12.840
n=样品 数量 r=测量 次数
3. 重复性 和再现 性 (GRR )
4. 样品变 差 (PV)
MSA分析报告
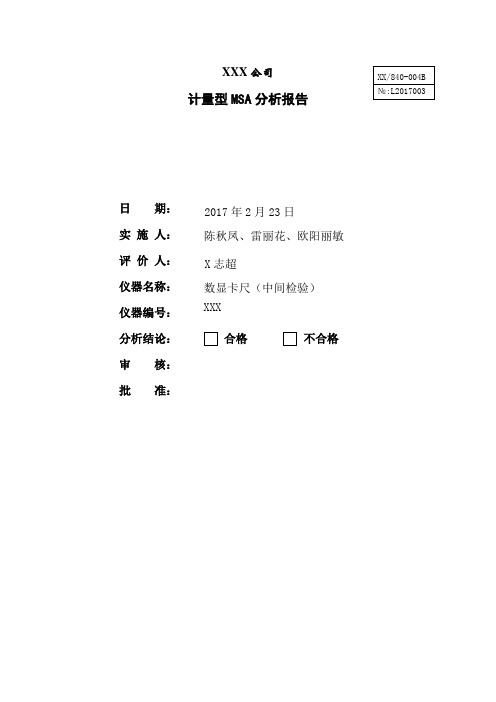
XXX 公司计量型MSA 分析报告日 期:实 施 人: 评 价 人:仪器名称: 仪器编号: 分析结论: 合格 不合格 审 核:批 准:2017年2月23日陈秋凤、雷丽花、欧阳丽敏 X 志超数显卡尺(中间检验) XXX计量型MSA分析报告目录稳定性 (1)偏倚 (4)线性 (7)重复性和 (9)再现性备注: 对于有条件接收的项目应阐述接受原因.第一节稳定性分析1.1 稳定性概述在经过一段长时间下,用相同的测量系统对同一基准或零件的同一特性进行测量所获得的总变差,即稳定性是整个时间的偏倚变化。
1.2试验方案2017年02月份,随机抽取一常见印制板样品,让中间检验员工每天的早上与晚上分别使用数显卡尺对样品外形尺寸测量5次/组,共测量25组数据,并将每次测量的数据记录在表1。
1.3数据收集表1 稳定性分析数据收集记录表1.4 测量系统稳定性可接受判定标准1.4.1 不允许有超出控制限的点;1.4.2 连续7点位于中心线同一侧;1.4.3 连续6点上升或下降;1.4.4 连续14点交替上下变化;1.4.5 连续3点有2点距中心的距离大于两个标准差;1.4.6 连续5点中有4点距离中心线的距离大于一个标准差;1.4.7 连续15点排列在中心线的一个标准差X围内;1.4.8 连续8点距中心线的距离大于一个标准差。
1.5数据分析图1中间检验_数显卡尺Xbar-R控制图从图1 Minitab生成Xbar-R控制图可知,没有控制点超出稳定性可接受判定标准,表明该测量系统稳定性可接受。
1.6测量系统稳定性分析结果判定对中间检验_数显卡尺进行稳定性分析,分析结果表明该测量系统稳定性可接受。
第二节偏倚分析2.1 偏倚分析概述对相同零件上同一特性的观测值与真值(参考值)的差异。
2.2 试样方案2.2.1选择一个被测样品,确定样品的外形尺寸基准值x,样品外形尺寸基准值通过__铣边工序所使用的泛用型尺寸测量机重复测量10次取测量均值获得。
MSA报告(卡尺)

=100[ 0.00358
重复性和再现性(GRR )
GRR =
=
EV ²+AV ²
1.71032E-05 + 1E-05 零件 K3
%GRR= 100[GRR /TV ] =100[ 0.00547 = 6 7 0.3742 %PV= 0.3534 0.3375 0.3249 0.3146 =100[ = 0.058 ]
量具重复性和再现性数据收集表
评价人/ 试验
部品 1 165.16 165.15 165.16 165.16 0.01 165.16 165.17 165.16 165.16 0.01 165.15 165.16 165.15 165.15 0.01 165.16 2 165.18 165.19 165.18 165.18 0.01 165.19 165.19 165.18 165.19 0.01 165.19 165.18 165.19 165.19 0.01 165.19 3 165.19 165.19 165.18 165.19 0.01 165.18 165.19 165.18 165.18 0.01 165.19 165.20 165.18 165.19 0.01 165.19 4 165.18 165.19 165.19 165.19 0.01 165.19 165.18 165.19 165.19 0.01 165.18 165.18 165.19 165.18 0.01 165.19 5 165.21 165.22 165.21 165.21 0.01 165.21 165.22 165.21 165.21 0.01 165.22 165.22 165.21 165.22 0.01 165.21 6 165.25 165.25 165.25 165.25 0.00 165.25 165.25 165.25 165.25 0.00 165.25 165.25 165.25 165.25 0.00 165.25 7 165.24 165.24 165.24 165.24 0.00 165.24 165.24 165.24 165.24 0.00 165.24 165.24 165.24 165.24 0.00 165.24 8 165.27 165.26 165.26 165.26 0.01 165.27 165.27 165.26 165.27 0.01 165.26 165.26 165.27 165.26 0.01 165.26 9 165.33 165.32 165.33 165.33 0.01 165.32 165.33 165.33 165.33 0.01 165.33 165.33 165.32 165.33 0.01 165.33 10 165.34 165.34 165.34 165.34 0.00 165.34 165.34 165.34 165.34 0.00 165.34 165.34 165.34 165.34 0.00 165.34 均值 165.235 165.235 165.234 Xa= 165.2347 Ra= 0.007 165.235 165.238 165.234 Xb= 165.2357 Rb= 0.007 165.235 165.236 165.234 Xc= 165.235 Rc= 0.007 X= 165.235 Rp= 0.1822 0.007 )+( Rb= MinX= D4= 0.007 )+( 165.235 )=X DIFF= 2.58 )= 0.01806 Rc= 0.007 )]/评
MSA管理程序(含表格)
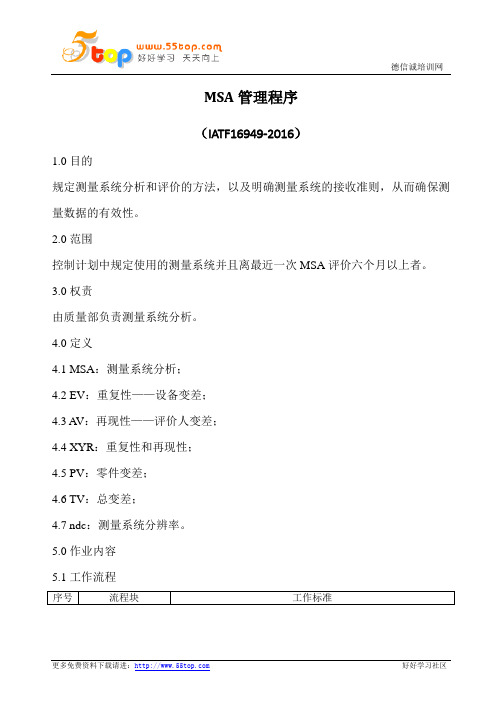
(
1.0目的
规定测量系统分析和评价的方法,以及明确测量系统的接收准则,从而确保测量数据的有效性。
2.0范围
控制计划中规定使用的测量系统并且离最近一次MSA评价六个月以上者。
3.0权责
由质量部负责测量系统分析。
4.0定义
4.1 MSA:测量系统分析;
4.2 EV:重复性——设备变差;
4.3 AV:再现性——评价人变差;
5、确定每个曲线的控制限并按标准曲线图判断系统失控或不
稳定状态。
稳定性判定接受准则:
a)若控制图中无超差点,证明该系统的稳定性适于应用;
b)控制图中出现下列情况者,表明该测量系统不稳定:
·控制图中出现超差点;
·连续7点在平均值一侧;
·7点连续上升或下降。
6、填写《稳定性分析报告》。
7、如通过控制图判断测量系统不稳定,其原因可能是量具松动、磨损或仪器故障。需采取纠正措施:对量具进行修理、校准、缩短检定周期。合格后应重新对量具进行稳定性分析。
B)当再现性大于重复性时,可采取下列措施:
a)再明确订定或修改作业标准,加强评价人对量具
的操作方法和数据读取方式的技能培训。
b)可能需要采用某些夹具协助操作员,以提高操作量具的一致性。c)量源自经维修校准合格后再进行%R&R分析。
9、量具的重复性和再现性的接受准则:
a)%R&R小于10%时,测量系统可接受;
4.2偏移分析
1、取一样件,在计量室或全尺寸检验设备上对其进行精度测量,将其值作为基准.
2、让一位评价人用正被评价的量具测量基准件或零件至少10次。
3、计算n次读数的平均值。
4、计算偏倚值,并填写《偏倚分析报告》:
偏倚=观测测量平均值-基准值
MSA表格

量具重复性和再现性报告
零件号名称: 特性: 规范: 量具名称: 量具编号: 量具类型: ABC 均值极差 X DIFF =R
X
日期: 执行人:
从数据表得到:总平均极差 R =0.342
=0.44
零件均值极差 RP=3.51
测量单元分析 重复性-测量设备变差(EV) EV= R × 1 K =0.342×0.5908 =0.202 试验次数 2 3 再现性-评价人变差(AV) AV= K1 0.8862 0.5908
%GRR=100[GRR/TV]
2 2
( EV ) ( AV )
2 2
=100[(0.306) / (1.146)] K3 2 3 4 5 6 0.7071 0.5231 0.4467 0.4030 0.3742 测量系统可靠地辨别过程的分级数 ndc=1.41(PV/GRR) =1.41((1.105) / (0.306)) =5.094 %PV=100[PV/TV] =100[(1.105)/ (1.146)] =96.38 % =26.68 %
-0.56 -0.49 -0.503
1.45 1.87 1.697
-1.77 -2.16 -1.807
X C 2=-0.256 X C 3=-0.284
X C =-0.254
RC =0.328
C 测量数据 的均值
极差
0.19
0.42
0.42
0.09
0.39
0.38
0.20
0.10
0.42
0.67
C 测量数据 的平均极差
零 件 均 值
0.169
-0.851
1.099
0.367
-1.064
MSA及过程能力分析

评 价 人
序号 A B C
1
2
3
4
5
6
7
8
9
10
第3页共5页
重复性极差控制图
零件编号/名称 尺寸规格 执行者 R = UCLR 公差值 样本容量/频率 = 日期 10/3/人 LCLR =
评 价 人
序号 A B C
1
2
3
4
5
6第4页共5页
测量系统GRR分析结果报告
零件编号和名称 尺寸规格 公差值 样本容量/频率 10/3/人 量具名称 量具编号 量具类型 量具精度 执 行 者 测量日期
表中所有的有关理论和常数的资料参见MSA参考手册第三版 0.707 0.523 0.447 0.403 0.374 0.353 0.338 0.325 0.315
量具名称 量具编号 量具类型 RP=
日期 执 行 者 %总变差(TV) %EV= 100*(EV/TV) K1
0.8862
=
%
0.59
%AV= 100*(AV/TV)
测量系统GRR分析结果
计量工程师:
质量工程师:
第5页共5页
= n=零件数量 2 3 r=实验次数
%
0.707 0.523
%GRR=100*(GRR/TV) = %
%PV= 100*(PV/TV) = %
10
第2页共5页
零件评价人平均值控制图
零件编号/名称 尺寸规格 执行者 X = UCLX 公差值 样本容量/频率 = 操作日期 10/3/人 LCLX =
占总次数的百分比 = % 占总次数的百分比 = % A2 D3 实验次数 2 1.880 0 3 1.023 0
《MSA表单填写》课件

1 2
了解MSA表单的用途和要求
在开始填写之前,确保你清楚MSA表单的用途、 目的和要求,以便有针对性地填写。
收集必要的信息
为了确保填写的准确性,你需要收集所有必要的 信息,如设备规格、操作员姓名和工号等。
3
准备相关工具
确保你有笔、计算器和任何其他必要的工具,以 便顺利填写MSA表单。
填写MSA表单的步骤
MSA表单的用途
1 2
3
识别制造过程中的变异来源
通过收集和分析数据,MSA表单可以帮助识别制造过程中可 能导致产品变异的因素。
评估过程能力
通过分析MSA表单中的数据,可以评估制造过程的稳定性和 一致性,以及过程能力指数,如Cpk和Ppk。
改进制造过程
通过识别制造过程中的变异和偏差,MSA表单可以帮助确定 改进措施,以降低产品不合格率并提高生产效率。
示例三:表单填写错误纠正
总结词:错误处理
详细描述:介绍如何发现和纠正填写MSA表单时可能出现的常见错误,包括格式错误、逻辑错误和数据不一致等问题。
04
MSA表单填写常见问题解 答
问题一
总结词
解决数据不一致问题
详细描述
在填写MSA表单时,如果发现数据不一致,应立即核对原始数据源,确认正确 的数据后进行修改。同时,要检查数据不一致的原因,防止类似问题再次出现 。
《msa表单填写》PPT课件
$number {01}
目录
• MSA表单概述 • 如何填写MSA表单 • MSA表单填写示例 • MSA表单填写常见问题解答 • 单的定义
01
MSA表单是一种用于测量系统分 析的记录表,用于评估制造过程 的一致性和稳定性。
02
它是一种标准化的表格,用于收 集和分析过程数据,以确定制造 过程中是否存在变异和偏差。
计数型 MSA数据记录用表

项目名称:测量人:测量工具:测量地点:测量次数:温湿度:1234567891011121314151617181920212223242526272829303132333435363738394041424344454647484950项目名称:测量人:测量工具:测量地点:测量次数:温湿度:1234567891011121314151617181920212223242526272829303132333435363738394041424344454647484950结果样品编号结果样品编号3.每次请注意按产品编号对应填写。
4.在检验过程中发现新问题请在备注栏填写。
结果备注2.如果有要求写明不良原因﹐请写出不良原因代码(A .划痕 B.脏污 C. 缺料 D .色差 E .金属丝 F.其它 )可以根据产品特点﹐由主导者自行加减不良原因。
计数型MSA 数据记录用表样品编号结果样品编号结果样品编号备注1.样品可接受请填写"1",不可接受请填写"0"﹔2.如果有要求写明不良原因﹐请写出不良原因代码(A .划痕 B.脏污 C. 缺料 D .色差 E .金属丝 F.其它 )可以根据产品特点﹐由主导者自行加减不良原因。
3.每次请注意按产品编号对应填写。
4.在检验过程中发现新问题请在备注栏填写。
ZB.W-PB-02-0006-04 (A)样品编号结果样品编号结果样品编号结果ZB.W-PB-02-0006-04 (A)计数型MSA 数据记录用表样品编号结果样品编号结果JOINSYS ELECTRONIC TECHNOLOGY CO., LTD 嘉力讯电子科技有限公司。
测量系统分析MSA程序(含表格)
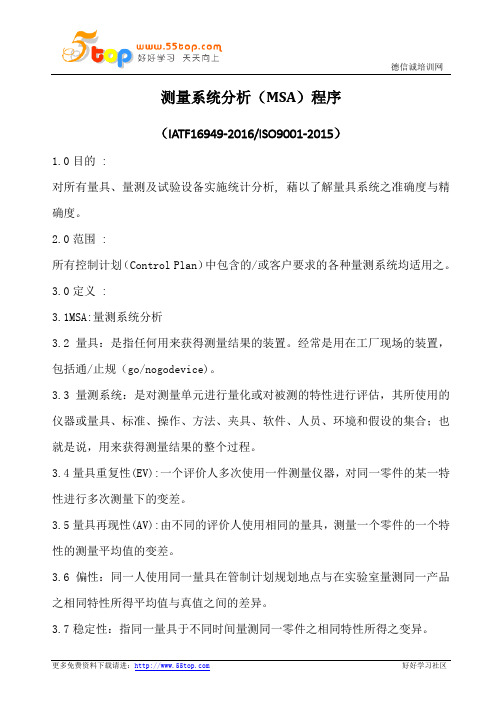
测量系统分析(MSA)程序(IATF16949-2016/ISO9001-2015)1.0目的 :对所有量具、量测及试验设备实施统计分析, 藉以了解量具系统之准确度与精确度。
2.0范围 :所有控制计划(Control Plan)中包含的/或客户要求的各种量测系统均适用之。
3.0定义 :3.1MSA:量测系统分析3.2量具:是指任何用来获得测量结果的装置。
经常是用在工厂现场的装置,包括通/止规(go/nogodevice)。
3.3量测系统:是对测量单元进行量化或对被测的特性进行评估,其所使用的仪器或量具、标准、操作、方法、夹具、软件、人员、环境和假设的集合;也就是说,用来获得测量结果的整个过程。
3.4量具重复性(EV):一个评价人多次使用一件测量仪器,对同一零件的某一特性进行多次测量下的变差。
3.5量具再现性(AV):由不同的评价人使用相同的量具,测量一个零件的一个特性的测量平均值的变差。
3.6偏性:同一人使用同一量具在管制计划规划地点与在实验室量测同一产品之相同特性所得平均值与真值之间的差异。
3.7稳定性:指同一量具于不同时间量测同一零件之相同特性所得之变异。
3.8线性:指量具在预期内之偏性表现。
4.0权责:4.1量测系统测试的排定、数据分析、仪器操作人员的选择:品保部4.2测试执行:各相关单位4.3MSA操作人员的培训:品保部5.0执行方法5.1QA工程师人员依公司PCP文件建立《xx年MSA实施计划表》或客户要求,并依据计划表之排程进行对仪器做量测系统分析。
5.2取样方法:5.2.1计量型取样:从代表整个工作范围的过程中随机抽取10件样品,但所抽取的10件样品其数值必须涵盖该产品的公差带。
5.2.2计数型取样:取50PCS样品,其中包含临近值,不良品与合格品。
5.2.3.需要2或3个测量者随机抽取对每个产品各测量取一定数量样品.5.3计数型:5.3.1被评价的零件的选定随机抽取50个零件,把零件编号,由研究小组给出该50个零件的标准,必须含合格,不合格,模糊品,条件允许的情况下最好各占1/3。
- 1、下载文档前请自行甄别文档内容的完整性,平台不提供额外的编辑、内容补充、找答案等附加服务。
- 2、"仅部分预览"的文档,不可在线预览部分如存在完整性等问题,可反馈申请退款(可完整预览的文档不适用该条件!)。
- 3、如文档侵犯您的权益,请联系客服反馈,我们会尽快为您处理(人工客服工作时间:9:00-18:30)。
测量人 测量次数 第一次 聂江宜 第二次 第三次 第一次 田美娟 第二次 第三次 第一次 苏芸 第二次 第三次 第一次 喻忠顺 第二次 第三次 测量人 测量次数 第一次 聂江宜 第二次 第三次 第一次 田美娟 第二次 第三次 第一次 苏芸 第二次 第三次 第一次 喻忠顺 第二次 第三次 测量人 测量次数 第一次 聂江宜 第二次 第三次 第一次 田美娟 第二次 第三次 第一次 苏芸 第二次 第三次 第一次 喻忠顺 第二次 第三次 1 2 零件序号(测量对象:信泰倒角刀,小后角) 3 4 5 6 7 8 9 10 1 2 零件序号(测量对象:信泰倒角刀,干涉高度) 3 4 5 6 7 8 9 10 1 2 零件序号(测量对象:信泰倒角刀,崩尖高度) 3 4 5 6 7 8 9 10
ቤተ መጻሕፍቲ ባይዱ