《粉末冶金》结课论文
粉末冶金个人总结

粉末冶金个人总结概述粉末冶金是一种以粉末为原料,通过加工、成型和烧结等工艺,制备出具有特定形状和性质的金属件的技术方法。
粉末冶金具有高效、节约资源和环保等优势,在各个行业中广泛应用。
本文将对粉末冶金的基本原理、工艺流程、应用领域以及发展趋势进行总结。
基本原理粉末冶金的基本原理是将金属或合金加工成粉末状,通过加压成型、烧结等工艺,使粉末颗粒在热力条件下结合,并得到所需形状的金属件。
粉末冶金的基本原理包括以下几个方面:1.粉末制备:粉末冶金中的原料是金属或合金的粉末,可以通过多种方法进行制备,如机械研磨、溅射、化学方法等。
2.加压成型:将粉末装入模具中,施加一定的压力,使其形成所需形状的绿坯。
3.烧结:绿坯经过高温处理,粒间相互扩散,颗粒结合成为致密的金属件。
4.后续加工:对烧结后的金属件进行热处理、机械加工等工艺,使其达到所需的性能。
工艺流程粉末冶金的主要工艺流程包括粉末制备、加压成型、烧结和后续加工等步骤。
粉末制备粉末制备是粉末冶金的关键步骤,直接影响到最终制品的质量和性能。
常用的粉末制备方法有:•机械研磨法:将块状金属或合金材料放入球磨机中,通过磨球的撞击和摩擦作用,将其研磨成粉末。
•溅射法:将金属材料置于溅射靶中,通过电弧、高能束流等方法,使金属材料蒸发并沉积在基底上,形成粉末。
•化学法:利用化学反应使金属溶液中的金属原子析出形成粉末。
加压成型加压成型是将粉末装入模具中,并施加一定的压力,使其形成所需形状的绿坯。
加压成型可以分为冷压成型和热压成型两种方式。
•冷压成型:在常温下进行,常用的冷压成型方法有压块、压片和挤压等。
•热压成型:在高温下进行,通常使用等静压、热等静压、热挤压、热等挤压等方法。
烧结经过加压成型后的绿坯需要进行烧结。
烧结过程中,绿坯在高温下经历几个阶段:弥散阶段、颗粒结合阶段和致密化阶段。
在烧结过程中,颗粒之间发生扩散,逐渐形成致密的金属件。
后续加工烧结后的金属件可能需要进行后续加工,包括热处理、机械加工等工艺。
粉末冶金实训报告(3篇)
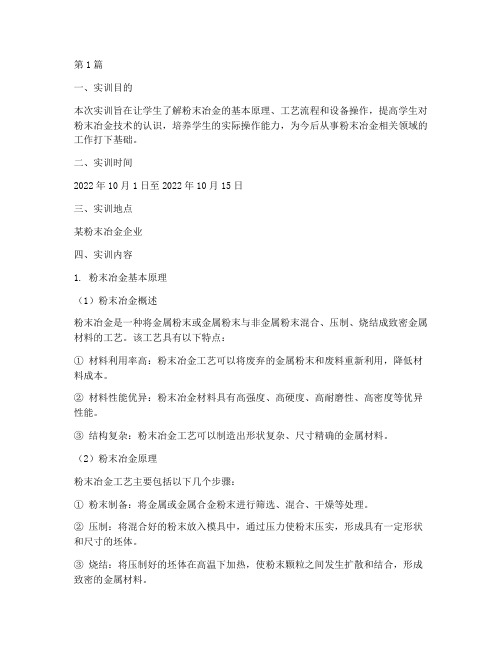
第1篇一、实训目的本次实训旨在让学生了解粉末冶金的基本原理、工艺流程和设备操作,提高学生对粉末冶金技术的认识,培养学生的实际操作能力,为今后从事粉末冶金相关领域的工作打下基础。
二、实训时间2022年10月1日至2022年10月15日三、实训地点某粉末冶金企业四、实训内容1. 粉末冶金基本原理(1)粉末冶金概述粉末冶金是一种将金属粉末或金属粉末与非金属粉末混合、压制、烧结成致密金属材料的工艺。
该工艺具有以下特点:① 材料利用率高:粉末冶金工艺可以将废弃的金属粉末和废料重新利用,降低材料成本。
② 材料性能优异:粉末冶金材料具有高强度、高硬度、高耐磨性、高密度等优异性能。
③ 结构复杂:粉末冶金工艺可以制造出形状复杂、尺寸精确的金属材料。
(2)粉末冶金原理粉末冶金工艺主要包括以下几个步骤:① 粉末制备:将金属或金属合金粉末进行筛选、混合、干燥等处理。
② 压制:将混合好的粉末放入模具中,通过压力使粉末压实,形成具有一定形状和尺寸的坯体。
③ 烧结:将压制好的坯体在高温下加热,使粉末颗粒之间发生扩散和结合,形成致密的金属材料。
2. 粉末冶金工艺流程(1)粉末制备① 粉末筛选:将金属粉末通过筛网进行筛选,去除杂质和粉末团。
② 混合:将不同成分的粉末进行混合,确保成分均匀。
③ 干燥:将混合好的粉末进行干燥处理,去除水分。
(2)压制① 模具设计:根据产品要求设计模具,包括模具形状、尺寸、孔径等。
② 压制:将干燥好的粉末放入模具中,通过压力机进行压制。
(3)烧结① 烧结炉:根据材料种类和性能要求选择合适的烧结炉。
② 烧结工艺:确定烧结温度、保温时间、冷却速度等工艺参数。
3. 设备操作(1)粉末筛选机:了解粉末筛选机的结构、原理和操作方法。
(2)混合机:了解混合机的结构、原理和操作方法。
(3)干燥机:了解干燥机的结构、原理和操作方法。
(4)压力机:了解压力机的结构、原理和操作方法。
(5)烧结炉:了解烧结炉的结构、原理和操作方法。
粉末冶金学习总结

粉末冶金学习总结
Hale Waihona Puke 2013年参加粉末冶金小组的学习,回顾整个一年的学习过程,收获颇多,对 粉末冶金工艺有了一定深度的了解,在组长王金强(工)的带领下,小组各 人进行分模块学习,最终我选定的模块是粉末冶金的后处理工艺。整个小组 进行了11次交流会,2次到首钢东星现场学习,2次粉末冶金供应商到DYPT培 训。 学习内容:了解粉末冶金工艺的原理,分为四大步:混粉、压制、烧结、后 处理。对粉末冶金后处理有较为深刻的学习,后处理主要分为:热处理、机 加工、熔渗及浸渍、喷丸处理等方式。不同的处理方式会对零件产生不同的 影响以及效果。 对工作的帮助:通过学习粉末冶金知道生产现场哪些是经过粉末冶金工艺制 成的,并且对于现场质量问题的处理也有一定的帮助,通过分析零件本体的 缺陷,大致知道缺陷来源于粉末冶金哪一个环节,从而可以确认问题的严重 性,采取最有效的遏制措施。 心得体会:在粉末冶金小组一年的学习中,组员之间的交流、现场学习、供 应商培训等活动非常丰富,给我带来了很多新鲜的东西,包括工艺、学习方 法等,让我认识到在面对一门工艺的时候该怎么学习,需要了解哪些相关信 息,怎么发现问题,怎么解决问题。在后续的工作中继续加强粉末冶金工艺 的学习,并且将学习方法以及成果运用到工作的各个方面中。
粉末冶金综述论文
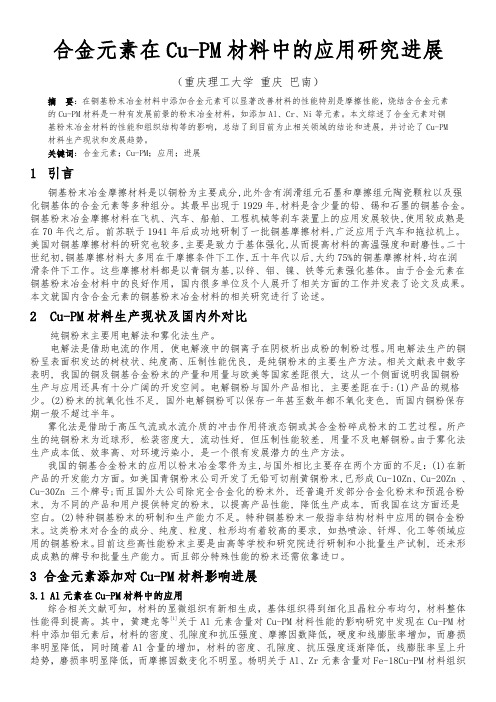
合金元素在Cu-PM材料中的应用研究进展(重庆理工大学重庆巴南)摘要:在铜基粉末冶金材料中添加合金元素可以显著改善材料的性能特别是摩擦性能,烧结含合金元素的Cu-PM材料是一种有发展前景的粉末冶金材料,如添加Al、Cr、Ni等元素。
本文综述了合金元素对铜基粉末冶金材料的性能和组织结构等的影响,总结了到目前为止相关领域的结论和进展,并讨论了Cu-PM 材料生产现状和发展趋势。
关键词:合金元素;Cu-PM;应用;进展1 引言铜基粉末冶金摩擦材料是以铜粉为主要成分,此外含有润滑组元石墨和摩擦组元陶瓷颗粒以及强化铜基体的合金元素等多种组分。
其最早出现于1929年,材料是含少量的铅、锡和石墨的铜基合金。
铜基粉末冶金摩擦材料在飞机、汽车、船舶、工程机械等刹车装置上的应用发展较快,使用较成熟是在70年代之后。
前苏联于1941年后成功地研制了一批铜基摩擦材料,广泛应用于汽车和拖拉机上。
美国对铜基摩擦材料的研究也较多,主要是致力于基体强化,从而提高材料的高温强度和耐磨性。
二十世纪初,铜基摩擦材料大多用在干摩擦条件下工作,五十年代以后,大约75%的铜基摩擦材料,均在润滑条件下工作。
这些摩擦材料都是以青铜为基,以锌、铝、镍、铁等元素强化基体。
由于合金元素在铜基粉末冶金材料中的良好作用,国内很多单位及个人展开了相关方面的工作并发表了论文及成果。
本文就国内含合金元素的铜基粉末冶金材料的相关研究进行了论述。
2 Cu-PM材料生产现状及国内外对比纯铜粉末主要用电解法和雾化法生产。
电解法是借助电流的作用, 使电解液中的铜离子在阴极析出成粉的制粉过程。
用电解法生产的铜粉呈表面积发达的树枝状、纯度高、压制性能优良, 是纯铜粉末的主要生产方法。
相关文献表中数字表明, 我国的铜及铜基合金粉末的产量和用量与欧美等国家差距很大, 这从一个侧面说明我国铜粉生产与应用还具有十分广阔的开发空间。
电解铜粉与国外产品相比, 主要差距在于:(1)产品的规格少。
粉末冶金的个人年度总结

粉末冶金的个人年度总结
尊敬的领导、同事:
大家好!时光荏苒,转眼间又到了一年的尾声。
在这一年中,我在粉末冶金领域中发展进步,积累了不少经验和知识。
现在,我想向大家分享一下我在这一年中的个人总结。
首先,我完成了多个粉末冶金项目,包括材料的选择、工艺的确定以及实验的设计与实施。
通过这些项目的实践,我对粉末冶金的原理和技术有了更深入的理解,并掌握了一些常用的材料制备和加工工艺。
在实验中,我注重细致的观察与记录,并及时总结分析。
通过不断的试验和反复的实践,我逐渐提高了自己的实验能力和技术水平。
其次,我积极参加各类学术会议和研讨会,并与同行们进行交流和合作。
这些学术交流活动为我提供了一个广阔的学习平台,我向别人学习和借鉴了许多宝贵的经验和技巧。
同时,我也有幸能和一些优秀的研究者共同合作,他们的思维方式和工作态度让我受益匪浅。
第三,我不断提高自己的学习能力和专业知识。
除了参加各类学术活动,我还积极阅读相关的学术文献和专业书籍,努力保持对行业前沿的了解,并不断拓展自己的知识面。
同时,我也加强了对于技术设备的学习和掌握,提高了自己的实验操作技巧。
最后,我还注重个人素质的提升。
在这一年中,我积极参与团队合作,提升了自己的团队意识和沟通能力。
同时,我也注重锻炼自己的逻辑思维和问题解决能力,以便更好地应对各种挑战和问题。
综上所述,这一年来我在粉末冶金领域中积极进取,不断学习和成长。
我相信,在未来的工作中,我会继续努力,不断学习和提高,为公司带来更多的价值。
谢谢大家!
个人签名。
《粉末冶金CoCrFeNiMn高熵合金的显微组织和强化策略研究》范文
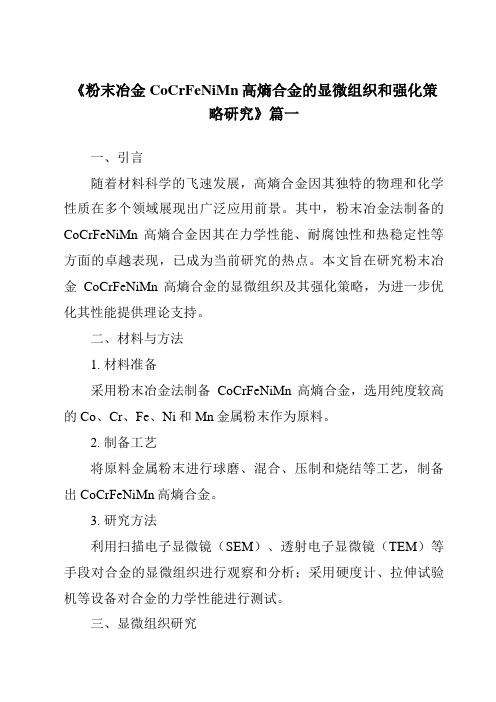
《粉末冶金CoCrFeNiMn高熵合金的显微组织和强化策略研究》篇一一、引言随着材料科学的飞速发展,高熵合金因其独特的物理和化学性质在多个领域展现出广泛应用前景。
其中,粉末冶金法制备的CoCrFeNiMn高熵合金因其在力学性能、耐腐蚀性和热稳定性等方面的卓越表现,已成为当前研究的热点。
本文旨在研究粉末冶金CoCrFeNiMn高熵合金的显微组织及其强化策略,为进一步优化其性能提供理论支持。
二、材料与方法1. 材料准备采用粉末冶金法制备CoCrFeNiMn高熵合金,选用纯度较高的Co、Cr、Fe、Ni和Mn金属粉末作为原料。
2. 制备工艺将原料金属粉末进行球磨、混合、压制和烧结等工艺,制备出CoCrFeNiMn高熵合金。
3. 研究方法利用扫描电子显微镜(SEM)、透射电子显微镜(TEM)等手段对合金的显微组织进行观察和分析;采用硬度计、拉伸试验机等设备对合金的力学性能进行测试。
三、显微组织研究1. 显微组织观察通过SEM和TEM观察,发现CoCrFeNiMn高熵合金具有典型的树枝晶结构,晶界清晰,晶内存在大量纳米尺度的析出相。
这些析出相可能是合金强化的关键因素。
2. 成分分析通过对合金进行成分分析,发现各元素在合金中分布均匀,无明显偏析现象。
这有利于提高合金的力学性能和耐腐蚀性。
四、强化策略研究1. 固溶强化通过调整合金中各元素的含量,可以有效地提高合金的固溶强化效果。
适量的Mn元素可以增加合金的固溶度,从而提高合金的强度和硬度。
2. 析出相强化纳米尺度的析出相可以有效地阻碍位错运动,提高合金的强度和韧性。
通过调整热处理工艺,可以控制析出相的种类、数量和分布,进一步提高合金的性能。
3. 晶界强化晶界是合金中的薄弱环节,通过优化烧结工艺,可以改善晶界的结构,提高其强度和韧性。
此外,晶界处形成的纳米尺度析出相也可以对晶界起到强化作用。
五、结论本研究通过粉末冶金法制备了CoCrFeNiMn高熵合金,对其显微组织和强化策略进行了深入研究。
粉末冶金论文 7、液相还原法制备超细Ni粉1

液相还原法制备超细Ni粉摘要以硫酸镍为原料,水合肼为还原剂,通过液相还原法,制备出了超细Ni粉。
采用X射线衍射分析(XRD)、扫描电镜分析(SEM)等对制备出粉末的物相、粒度以及形貌进行了表征。
实验结果表明:通过液相还原法成功的制备出了粒度为100nm的超细Ni粉;最佳的反应温度为90℃,温度过高会使镍颗粒发生团聚,温度低则会反应进行的速度;反应在碱性条件下发生,最佳反应的溶液pH值为11, pH值大于11时会使Ni粉产率降低;水合肼的最佳加入摩尔量n(N2H4)/n(NiSO4)为3.5。
关键词超细镍粉;水合肼;液相还原1 引言超细镍粉由于具有极大的表面效应和体积效应[1],在催化剂、烧结活化剂、导电浆料、电池、硬质合金等方面有广泛的应用前景[2-4]。
目前制备超细镍粉的方法主要有物理法,以及羰基物热离解法、电解法、高压氢还原法、真空热分解法等化学方法[5-12]。
这些方法都各有优点,但也存在一定的局限性。
其中物理法所需设备昂贵、产量低;羰基热分解法存在一定的污染问题;电解法能耗较高;加氢还原法需要高压反应釜;真空分解法则对设备要求较高。
液相还原法因具有工艺简单、成本低、粉末粒度及表面易于控制等优点,成为目前制备超细镍粉是研究热点之一[13-15]。
本文以水合肼为还原剂,系统研究了液相还原法制备超细镍粉工艺过程中反应温度,pH值和还原剂用量等对粉末性能的影响。
2实验实验所用的主要原料包括分析纯的硫酸镍(NiSO4•6H2O)、水合肼(N2H4•H2O)、氢氧化钠(NaOH)、无水乙醇(C2H5OH)、聚乙烯吡咯烷酮(PVP)等。
实验时,首先配制一定浓度的硫酸镍溶液,加入表面活性剂(PVP),用超声分散器混合成均匀的悬浮液。
然后往均匀悬浮液中缓慢滴加水合肼溶液,用恒温水浴锅控制反应温度,氢氧化钠溶液控制反应pH值,反应过程中用电动搅拌器不断搅拌。
反应约6h后,将混合液离心分离,得到的粉末采用去离子水洗涤4次,无水乙醇洗涤3次,置于60℃恒温烘箱中干燥30min。
粉末冶金年度总结回报(3篇)

第1篇尊敬的领导、各位同事:转眼间,一年又即将过去,我在粉末冶金这个充满挑战与机遇的岗位上,已经度过了充实而难忘的一年。
在此,我向领导和同事们表示衷心的感谢,现将本年度工作总结如下:一、工作回顾1. 技术提升过去的一年,我积极学习粉末冶金相关知识,努力提高自身技能。
通过参加各类培训、阅读专业书籍和与同事交流,我对粉末冶金的生产工艺、设备操作及质量控制等方面有了更深入的了解。
在此基础上,成功解决了多项生产难题,提高了产品质量。
2. 生产管理在日常工作中,我严格执行生产计划,确保生产进度和质量。
针对生产过程中的问题,及时与同事沟通,共同探讨解决方案。
此外,我还积极参与车间设备维护,降低设备故障率,保障生产顺利进行。
3. 团队协作在过去的一年里,我注重与同事的沟通交流,积极参与团队活动,增进彼此了解。
在遇到困难时,主动寻求同事帮助,共同克服困难。
在团队协作中,我充分发挥自己的优势,为团队的整体发展贡献力量。
二、工作亮点1. 优化生产工艺针对某款粉末冶金产品,我通过优化生产工艺,降低了生产成本,提高了产品合格率。
经过实践验证,该方法已广泛应用于生产,取得了显著成效。
2. 提高产品质量在质量控制方面,我严格执行各项检验标准,确保产品合格率。
同时,针对不合格品,及时分析原因,采取措施,防止问题再次发生。
3. 获得荣誉在本年度工作中,我因表现突出,荣获“优秀员工”称号。
这是对我过去一年工作的肯定,也是对我今后工作的鼓励。
三、不足与展望1. 不足在过去的一年里,我在工作中还存在一些不足,如:对某些新技术的掌握不够熟练,有时处理问题不够果断等。
2. 展望在新的一年里,我将继续努力,克服自身不足,不断提升自身能力。
具体如下:(1)深入学习粉末冶金相关知识,提高自身技术水平;(2)加强与同事的沟通交流,提高团队协作能力;(3)针对工作中存在的问题,及时采取措施,提高工作效率;(4)积极参与公司各项活动,为公司发展贡献自己的力量。
粉末冶金论文
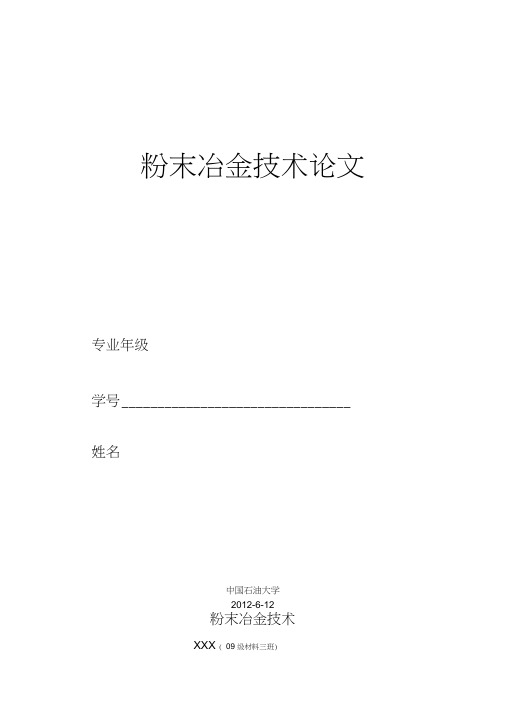
粉末冶金技术论文专业年级学号________________________________ 姓名中国石油大学2012-6-12粉末冶金技术XXX ( 09 级材料三班)摘要:粉末冶金是制取金属或用金属粉末(或金属粉末与非金属粉末的混合物)作为原料,经过成形和烧结,制造金属材料、复合以及各种类型制品的工艺技术。
粉末冶金法与生产陶瓷有相似的地方,因此,一系列粉末冶金新技术也可用于陶瓷材料的制备。
粉末冶金材料是指用几种金属粉末或金属与非金属粉末作原料,通过配料、压制成形、烧结等工艺过程而制成的材料。
这种工艺过程成为粉末冶金法,是一种不同于熔炼和铸造的方法。
其生产过程与陶瓷制品相类似,所以又称金属陶瓷法。
粉末冶金法不仅是制取具有某些特殊性能材料的方法,也是一种无切削或少切削的加工方法。
它具有生产率高、材料利用率高、节省机床和生产占地面积等优点。
但金属粉末和模具费用高,制品大小和形状受到一定限制,制品的韧性较差。
粉末冶金法常用于制作硬质合金、减摩材料、结构材料、摩擦材料、难熔金属材料、过滤材料、金属陶瓷、无偏析高速工具钢、磁性材料、耐热材料等。
关键词:粉末冶金、基本工序、应用、发展方向、问题及机遇Powder metallurgy technologyXXX(09 grade material class three)Abstract: Powder metallurgy is used for preparing metal or metal powder (or metal powder and metal powder mixture) as raw material, after forming and sintering, manufacture of metal materials, composite and various types of products technology.Powder metallurgy method and the production of ceramic have similar place, therefore, a series of new powder metallurgy technologies can also be used for preparing ceramic material. Powder metallurgy materials refers to the use of several kinds of metal powder or metal and non metal powder as raw material, through mixing, pressing, sintering process and made of materials.The process to become powder metallurgy method, is different from the melting and casting method.Its production process and ceramic products are similar, so called ceramic metal.Powder metallurgy method not only has some special properties of material preparation method, is also a kind of without cutting or less cutting processing method. It has high productivity, high material utilization rate, saving machine tools and production area etc..But the metal powderand high mold cost, product size and shape are subject to certain restrictions, flexibility is poor.Powder metallurgy method often used for the production of hard alloy, antifriction material, structural material, friction material, refractory metal materials, filter materials, metal ceramic, no segregation in high speed tool steel, magnetic materials, heat resistant materials.Key words: powder metallurgy, basic process, application, development trend, problems and opportunities一、世界粉末冶金工业概况2003 年全球粉末货运总量约为88 万吨,其中美国占51%,欧洲18%,日本13%,其它国家和地区18%。
粉末冶金的研究及应用毕业设计(论文)[管理资料]
![粉末冶金的研究及应用毕业设计(论文)[管理资料]](https://img.taocdn.com/s3/m/4bbe280dc8d376eeafaa317e.png)
毕业设计(论文)题目: 粉末冶金的研究及应用专业:数控技术及应用班级:04421班学号:34号姓名:唐宇指导老师:李华志成都电子机械高等专科学校二〇〇七年六月绪论粉末冶金方法起源于公元前三千多年。
制造铁的第一个方法实质上采用的就是粉末冶金方法。
而现代粉末冶金技术的发展中共有三个重要标志:1、克服了难熔金属熔铸过程中产生的困难。
1909年制造电灯钨丝,推动了粉末冶金的发展;1923年粉末冶金硬质合金的出现被誉为机械加工中的革命。
2、三十年代成功制取多孔含油轴承;继而粉末冶金铁基机械零件的发展,充分发挥了粉末冶金少切削甚至无切削的优点。
3、向更高级的新材料、新工艺发展。
四十年代,出现金属陶瓷、弥散强化等材料,六十年代末至七十年代初,粉末高速钢、粉末高温合金相继出现;利用粉末冶金锻造及热等静压已能制造高强度的零件。
什么是粉末冶金呢? 粉末冶金是制取金属或用金属粉末(或金属粉末与非金属粉末的混合物)作为原料,经过成形和烧结,制造金属材料、复合以及各种类型制品的工艺技术。
粉末冶金法与生产陶瓷有相似的地方,因此,一系列粉末冶金新技术也可用于陶瓷材料的制备。
由于粉末冶金技术的优点,它已成为解决新材料问题的钥匙,在新材料的发展中起着举足轻重的作用。
粉末冶金技术可以最大限度地减少合金成分偏聚,消除粗大、不均匀的铸造组织。
在制备高性能稀土永磁材料、稀土储氢材料、稀土发光材料、稀土催化剂、高温超导材料、新型金属材料(如Al-Li合金、耐热Al合金、超合金、粉末耐蚀不锈钢、粉末高速钢、金属间化合物高温结构材料等)具有重要的作用。
可以制备非晶、微晶、准晶、纳米晶和超饱和固溶体等一系列高性能非平衡材料,这些材料具有优异的电学、磁学、光学和力学性能。
可以容易地实现多种类型的复合,充分发挥各组元材料各自的特性,是一种低成本生产高性能金属基和陶瓷复合材料的工艺技术。
可以生产普通熔炼法无法生产的具有特殊结构和性能的材料和制品,如新型多孔生物材料,多孔分离膜材料、高性能结构陶瓷和功能陶瓷材料等。
粉末冶金技术论文
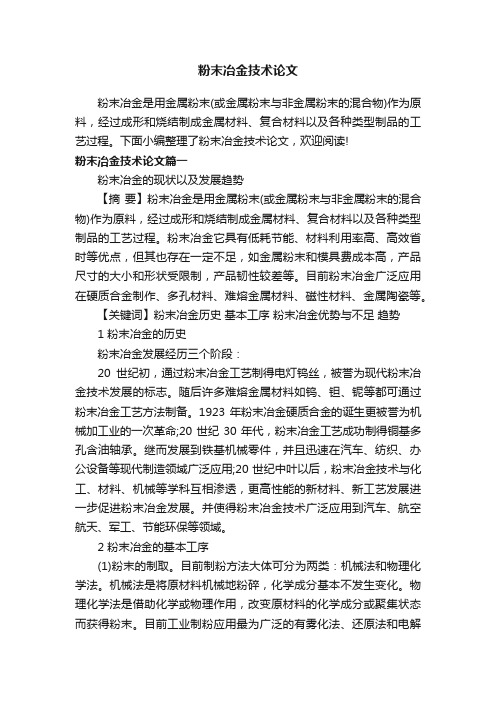
粉末冶金技术论文粉末冶金是用金属粉末(或金属粉末与非金属粉末的混合物)作为原料,经过成形和烧结制成金属材料、复合材料以及各种类型制品的工艺过程。
下面小编整理了粉末冶金技术论文,欢迎阅读!粉末冶金技术论文篇一粉末冶金的现状以及发展趋势【摘要】粉末冶金是用金属粉末(或金属粉末与非金属粉末的混合物)作为原料,经过成形和烧结制成金属材料、复合材料以及各种类型制品的工艺过程。
粉末冶金它具有低耗节能、材料利用率高、高效省时等优点,但其也存在一定不足,如金属粉末和模具费成本高,产品尺寸的大小和形状受限制,产品韧性较差等。
目前粉末冶金广泛应用在硬质合金制作、多孔材料、难熔金属材料、磁性材料、金属陶瓷等。
【关键词】粉末冶金历史基本工序粉末冶金优势与不足趋势1 粉末冶金的历史粉末冶金发展经历三个阶段:20世纪初,通过粉末冶金工艺制得电灯钨丝,被誉为现代粉末冶金技术发展的标志。
随后许多难熔金属材料如钨、钽、铌等都可通过粉末冶金工艺方法制备。
1923年粉末冶金硬质合金的诞生更被誉为机械加工业的一次革命;20世纪30年代,粉末冶金工艺成功制得铜基多孔含油轴承。
继而发展到铁基机械零件,并且迅速在汽车、纺织、办公设备等现代制造领域广泛应用;20世纪中叶以后,粉末冶金技术与化工、材料、机械等学科互相渗透,更高性能的新材料、新工艺发展进一步促进粉末冶金发展。
并使得粉末冶金技术广泛应用到汽车、航空航天、军工、节能环保等领域。
2 粉末冶金的基本工序(1)粉末的制取。
目前制粉方法大体可分为两类:机械法和物理化学法。
机械法是将原材料机械地粉碎,化学成分基本不发生变化。
物理化学法是借助化学或物理作用,改变原材料的化学成分或聚集状态而获得粉末。
目前工业制粉应用最为广泛的有雾化法、还原法和电解法;而沉积法(气相或液相)在特殊应用时也很重要。
(2)粉末成型。
成型是使金属粉末密实成具有一定形状、尺寸、孔隙度和强度坯块的工艺过程。
成型分普通模压成型和特殊成型两类。
粉末冶金及模具设计论文
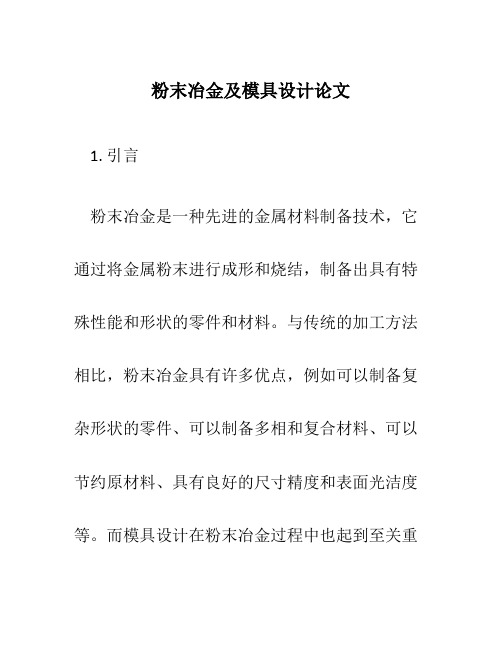
粉末冶金及模具设计论文1. 引言粉末冶金是一种先进的金属材料制备技术,它通过将金属粉末进行成形和烧结,制备出具有特殊性能和形状的零件和材料。
与传统的加工方法相比,粉末冶金具有许多优点,例如可以制备复杂形状的零件、可以制备多相和复合材料、可以节约原材料、具有良好的尺寸精度和表面光洁度等。
而模具设计在粉末冶金过程中也起到至关重要的作用,它直接影响着成形零件的质量和性能。
因此,研究粉末冶金及模具设计对于提高金属材料的制备效率和性能具有重要的意义。
2. 粉末冶金的工艺过程粉末冶金的工艺过程包括粉末的选择和处理、粉末成形和烧结等步骤。
2.1 粉末的选择和处理粉末的选择和处理是粉末冶金过程的第一步。
在粉末的选择中,需要考虑金属粉末的纯度、粒度和形状等因素。
高纯度的金属粉末可以得到高质量的成品,而合适的粒度和形状可以提高成形性能和烧结性能。
在粉末的处理中,通常包括混合、干燥和筛分等步骤。
混合是将所需金属粉末按一定比例混合以获得所需的合金成分,干燥则是去除粉末中的水分,筛分则是按照所需粒度进行筛选。
2.2 粉末成形粉末成形是指将混合并处理好的粉末以一定的压力加工成形。
常见的粉末成形方法包括压制、注射成形和挤压成形等。
压制是将粉末放置于模具中,然后施加压力使其形成一定形状的零件。
注射成形则是将粉末加入模具中,然后通过注射机将粉末充填模腔,最后再施加压力形成零件。
挤压成形是将粉末放置于模具中,然后通过挤压机施加压力使其在模腔中流动并形成零件。
2.3 烧结烧结是粉末冶金过程中的关键步骤,它是指将成形好的粉末在一定条件下进行加热处理,使其颗粒之间产生扩散和结合从而形成致密的固体材料。
烧结温度、时间和气氛都会影响烧结过程的质量和性能。
3. 模具设计在粉末冶金中的应用模具设计在粉末冶金中起到至关重要的作用,它直接影响着成形零件的质量和性能。
模具设计主要包括模具材料的选择、模腔设计和模具加工工艺的确定。
3.1 模具材料的选择模具材料的选择对于模具的寿命和成形零件的质量都有很大的影响。
《粉末冶金》结课论文

粉末冶金高速压制技术的研究现状及发展摘要:介绍一种低成本高密度粉末冶金零件成形技术一高速压制技术,通过阐述该技术的特点、原理、关键技术分析,指出其材料性能和应用前景以及高速压制技术目前存在的问题。
关键词:粉末冶金;高速压制;高密度粉末冶金技术以其低成本、近净形等加工特点在许多领域得到广泛应用。
密度对粉末冶金材料至关重要,它显著影响结构材料的力学性能,尤其是疲劳性能。
因此提高材料密度是粉末冶金的主要研究内容之一。
近年来粉末冶金新技术、新工艺层出不穷,温压技术、表面致密技术、高速压制技术等新技术的出现,使得粉末冶金技术不断取得突破性进展。
高速压制技术(high velocity compaction,简称HVC)是瑞典Hoganas公司在2001年6月主持召开的专门会议所推介的一种新技术,它所使用的重锤能产生强烈的冲击波,能在0.02s内将能量通过压模传给粉末进行致密化,间隔0.3s 的一个个附加的冲击波可将密度不断提高,使材料的性能更加优异,成本更加低廉,采用该技术可利用比传统压制小的设备生产超大零件。
HVC可能是粉末冶金工业寻求低成本高密度材料加工技术的又一次新突破。
1 高速压制技术的特点1.1高密度高性能HVC技术通过强烈的冲击波进行压制,使P/M零件达到高密度,它不仅可以使零件高致密化,而且可以使其密度均匀化。
与传统压制相比,HVC技术可使压坯密度提高0.3 g/cm3以上,如右图1所示。
典型的齿轮冲击试验表明其密度变化小于0.01 g/cm3。
将高速压制与其它工艺相结合,可使粉末压坯密度更高。
以铁基压坯为例,HVC技术与模壁润滑相结合,压坯密度可达7.6 g/cm3,与模壁润滑和温压结合的压坯密度达7.7g/cm3,若采用高速复压复烧工艺,压坯密度可达7.8g/cm3,接近全致密。
密度对提高材料性能的影响显而易见,如基于D.AE和Astaloy CrM的、采用HVC技术制备的材料与传统压制技术制备的材料相比,抗拉强度和屈服强度均提高20%~25%,其他各项性能指标也均有较大提高。
粉末冶金论文
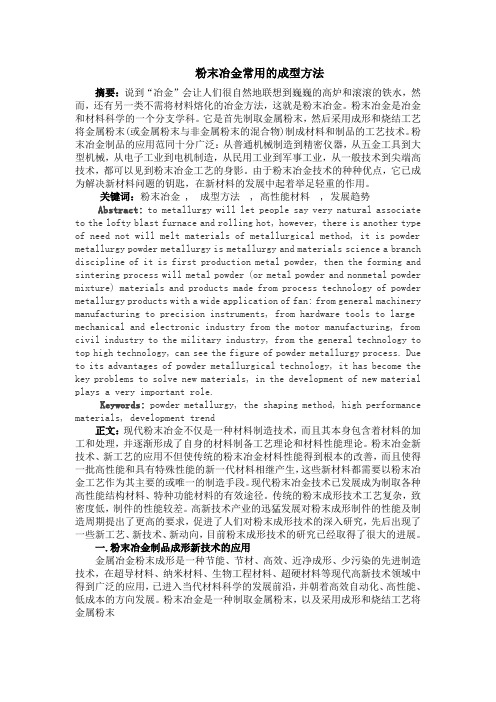
粉末冶金常用的成型方法摘要:说到“冶金”会让人们很自然地联想到巍巍的高炉和滚滚的铁水,然而,还有另一类不需将材料熔化的冶金方法,这就是粉末冶金。
粉末冶金是冶金和材料科学的一个分支学科。
它是首先制取金属粉末,然后采用成形和烧结工艺将金属粉末(或金属粉末与非金属粉末的混合物)制成材料和制品的工艺技术。
粉末冶金制品的应用范同十分广泛:从普通机械制造到精密仪器,从五金工具到大型机械,从电子工业到电机制造,从民用工业到军事工业,从一般技术到尖端高技术,都可以见到粉末冶金工艺的身影。
由于粉末冶金技术的种种优点,它已成为解决新材料问题的钥匙,在新材料的发展中起着举足轻重的作用。
关键词:粉末冶金 , 成型方法 , 高性能材料 , 发展趋势Abstract: to metallurgy will let people say very natural associate to the lofty blast furnace and rolling hot, however, there is another type of need not will melt materials of metallurgical method, it is powder metallurgy powder metallurgy is metallurgy and materials science a branch discipline of it is first production metal powder, then the forming and sintering process will metal powder (or metal powder and nonmetal powder mixture) materials and products made from process technology of powder metallurgy products with a wide application of fan: from general machinery manufacturing to precision instruments, from hardware tools to large mechanical and electronic industry from the motor manufacturing, from civil industry to the military industry, from the general technology to top high technology, can see the figure of powder metallurgy process. Due to its advantages of powder metallurgical technology, it has become the key problems to solve new materials, in the development of new material plays a very important role.Keywords: powder metallurgy, the shaping method, high performance materials, development trend正文:现代粉末冶金不仅是一种材料制造技术,而且其本身包含着材料的加工和处理,并逐渐形成了自身的材料制备工艺理论和材料性能理论。
粉末冶金件成型技术论文(2)
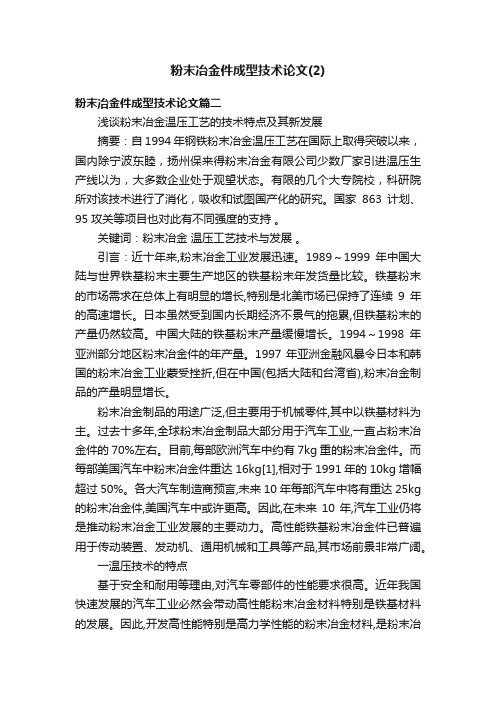
粉末冶金件成型技术论文(2)粉末冶金件成型技术论文篇二浅谈粉末冶金温压工艺的技术特点及其新发展摘要:自1994年钢铁粉末冶金温压工艺在国际上取得突破以来,国内除宁波东睦,扬州保来得粉末冶金有限公司少数厂家引进温压生产线以为,大多数企业处于观望状态。
有限的几个大专院校,科研院所对该技术进行了消化,吸收和试图国产化的研究。
国家863计划、95攻关等项目也对此有不同强度的支持。
关键词:粉末冶金温压工艺技术与发展。
引言:近十年来,粉末冶金工业发展迅速。
1989~1999年中国大陆与世界铁基粉末主要生产地区的铁基粉末年发货量比较。
铁基粉末的市场需求在总体上有明显的增长,特别是北美市场已保持了连续9年的高速增长。
日本虽然受到国内长期经济不景气的拖累,但铁基粉末的产量仍然较高。
中国大陆的铁基粉末产量缓慢增长。
1994~1998年亚洲部分地区粉末冶金件的年产量。
1997年亚洲金融风暴令日本和韩国的粉末冶金工业蒙受挫折,但在中国(包括大陆和台湾省),粉末冶金制品的产量明显增长。
粉末冶金制品的用途广泛,但主要用于机械零件,其中以铁基材料为主。
过去十多年,全球粉末冶金制品大部分用于汽车工业,一直占粉末冶金件的70%左右。
目前,每部欧洲汽车中约有7kg重的粉末冶金件。
而每部美国汽车中粉末冶金件重达16kg[1],相对于1991年的10kg增幅超过50%。
各大汽车制造商预言,未来10年每部汽车中将有重达25kg 的粉末冶金件,美国汽车中或许更高。
因此,在未来10年,汽车工业仍将是推动粉末冶金工业发展的主要动力。
高性能铁基粉末冶金件已普遍用于传动装置、发动机、通用机械和工具等产品,其市场前景非常广阔。
一温压技术的特点基于安全和耐用等理由,对汽车零部件的性能要求很高。
近年我国快速发展的汽车工业必然会带动高性能粉末冶金材料特别是铁基材料的发展。
因此,开发高性能特别是高力学性能的粉末冶金材料,是粉末冶金的发展方向和研究重点。
提高粉末冶金材料的密度,是实现这一目的的最有效途径。
粉末冶金发展方向论文
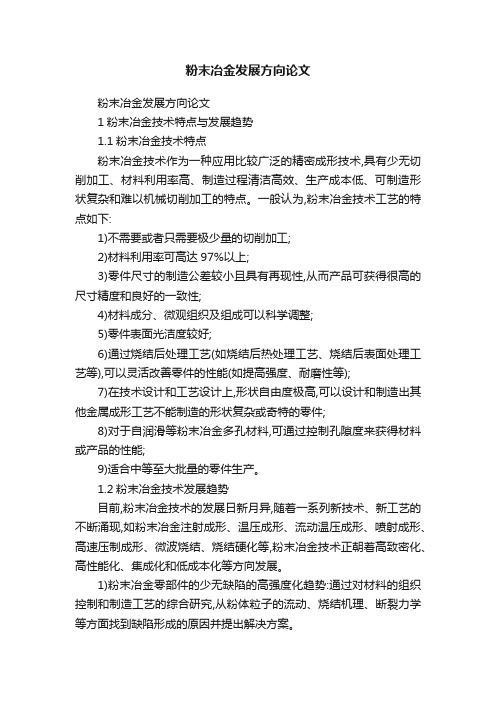
粉末冶金发展方向论文粉末冶金发展方向论文1粉末冶金技术特点与发展趋势1.1粉末冶金技术特点粉末冶金技术作为一种应用比较广泛的精密成形技术,具有少无切削加工、材料利用率高、制造过程清洁高效、生产成本低、可制造形状复杂和难以机械切削加工的特点。
一般认为,粉末冶金技术工艺的特点如下:1)不需要或者只需要极少量的切削加工;2)材料利用率可高达97%以上;3)零件尺寸的制造公差较小且具有再现性,从而产品可获得很高的尺寸精度和良好的一致性;4)材料成分、微观组织及组成可以科学调整;5)零件表面光洁度较好;6)通过烧结后处理工艺(如烧结后热处理工艺、烧结后表面处理工艺等),可以灵活改善零件的性能(如提高强度、耐磨性等);7)在技术设计和工艺设计上,形状自由度极高,可以设计和制造出其他金属成形工艺不能制造的形状复杂或奇特的零件;8)对于自润滑等粉末冶金多孔材料,可通过控制孔隙度来获得材料或产品的性能;9)适合中等至大批量的零件生产。
1.2粉末冶金技术发展趋势目前,粉末冶金技术的发展日新月异,随着一系列新技术、新工艺的不断涌现,如粉末冶金注射成形、温压成形、流动温压成形、喷射成形、高速压制成形、微波烧结、烧结硬化等,粉末冶金技术正朝着高致密化、高性能化、集成化和低成本化等方向发展。
1)粉末冶金零部件的少无缺陷的高强度化趋势:通过对材料的组织控制和制造工艺的综合研究,从粉体粒子的流动、烧结机理、断裂力学等方面找到缺陷形成的原因并提出解决方案。
2)粉末冶金成形技术的近净成形和近终成形趋势:着眼于粉体流动、充填成形、烧结过程粉末特性控制、粘结剂等角度,大力发展近净成形和近终成形的高致密化工艺技术,是降低竞争成本、减少制造工序、适应国际化市场的必然要求。
3)粉末冶金零部件的`高精度化趋势:通过对粉末冶金工模具、粉末冶金设备、粉末冶金工艺过程的精确设计和控制,实现粉末冶金零部件宏观尺寸的更高精度;通过对粉体特性、粉末冶金过程显微组织、粉末冶金工艺过程的精确设计和控制,实现粉末冶金零部件微观领域的显微精度。
粉末冶金课程心得体会(2篇)

第1篇作为一名对材料科学充满好奇心的学生,我有幸在大学期间选修了粉末冶金这门课程。
通过这门课程的学习,我对粉末冶金这一独特的材料加工技术有了更加深入的了解,以下是我对这门课程的心得体会。
一、粉末冶金的基本概念粉末冶金是一种将金属粉末或金属与非金属粉末混合、压制、烧结成制品的工艺技术。
它具有许多独特的优点,如材料利用率高、加工精度高、产品性能好等。
在学习这门课程之前,我对粉末冶金的基本概念和工艺流程并不了解,但通过课程的学习,我对粉末冶金有了全新的认识。
二、粉末冶金的发展历程粉末冶金技术的发展历史悠久,最早可以追溯到古代的陶瓷制作工艺。
随着科学技术的不断发展,粉末冶金技术逐渐从陶瓷领域扩展到金属领域。
从传统的粉末冶金工艺到现代的粉末冶金技术,我国粉末冶金行业取得了举世瞩目的成就。
通过学习这门课程,我了解了粉末冶金的发展历程,对这一领域的发展前景充满了信心。
三、粉末冶金的基本工艺粉末冶金的基本工艺包括粉末制备、压制、烧结和后处理等环节。
在学习这门课程的过程中,我了解了粉末制备的方法、压制工艺、烧结技术以及后处理工艺。
这些基本工艺对粉末冶金产品的质量起着决定性的作用。
以下是我对每个环节的心得体会:1. 粉末制备:粉末制备是粉末冶金工艺的第一步,也是至关重要的一步。
通过学习,我了解到粉末制备的方法有机械研磨、球磨、气流磨等。
粉末的粒度、形状、分布等参数对粉末冶金产品的性能有着重要影响。
2. 压制:压制是将粉末制成具有一定形状和尺寸的坯体的过程。
压制工艺包括干压、湿压、冷压等。
压制过程中的压力、模具、粉末流动等参数对压制质量有着直接影响。
3. 烧结:烧结是将压制好的坯体加热到一定温度,使粉末颗粒之间发生化学反应,形成具有致密组织和良好性能的金属材料的工艺。
烧结过程中的温度、时间、气氛等参数对烧结质量有着重要影响。
4. 后处理:后处理是对烧结后的产品进行表面处理、热处理等工艺,以提高产品的性能和加工精度。
后处理工艺包括表面处理、热处理、机械加工等。
粉末冶金材料论文
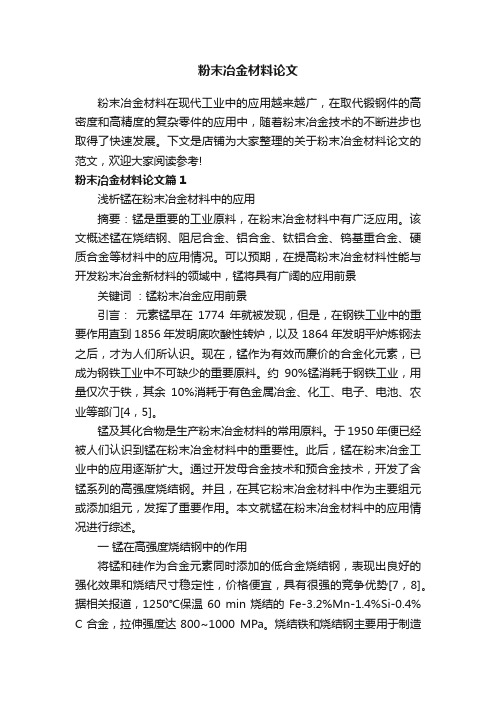
粉末冶金材料论文粉末冶金材料在现代工业中的应用越来越广,在取代锻钢件的高密度和高精度的复杂零件的应用中,随着粉末冶金技术的不断进步也取得了快速发展。
下文是店铺为大家整理的关于粉末冶金材料论文的范文,欢迎大家阅读参考!粉末冶金材料论文篇1浅析锰在粉末冶金材料中的应用摘要:锰是重要的工业原料,在粉末冶金材料中有广泛应用。
该文概述锰在烧结钢、阻尼合金、铝合金、钛铝合金、钨基重合金、硬质合金等材料中的应用情况。
可以预期,在提高粉末冶金材料性能与开发粉末冶金新材料的领域中,锰将具有广阔的应用前景关键词:锰粉末冶金应用前景引言:元素锰早在1774年就被发现,但是,在钢铁工业中的重要作用直到1856年发明底吹酸性转炉,以及1864年发明平炉炼钢法之后,才为人们所认识。
现在,锰作为有效而廉价的合金化元素,已成为钢铁工业中不可缺少的重要原料。
约90%锰消耗于钢铁工业,用量仅次于铁,其余10%消耗于有色金属冶金、化工、电子、电池、农业等部门[4,5]。
锰及其化合物是生产粉末冶金材料的常用原料。
于1950年便已经被人们认识到锰在粉末冶金材料中的重要性。
此后,锰在粉末冶金工业中的应用逐渐扩大。
通过开发母合金技术和预合金技术,开发了含锰系列的高强度烧结钢。
并且,在其它粉末冶金材料中作为主要组元或添加组元,发挥了重要作用。
本文就锰在粉末冶金材料中的应用情况进行综述。
一锰在高强度烧结钢中的作用将锰和硅作为合金元素同时添加的低合金烧结钢,表现出良好的强化效果和烧结尺寸稳定性,价格便宜,具有很强的竞争优势[7,8]。
据相关报道,1250℃保温60 min烧结的Fe-3.2%Mn-1.4%Si-0.4% C合金,拉伸强度达800~1000 MPa。
烧结铁和烧结钢主要用于制造机械零件,在选择合金元素时,必须注意到其对尺寸稳定性的影响。
在一般情况下,加入硅会引起压坯在烧结时收缩,而加入锰则会引起压坯膨胀。
同时加入锰和硅,能够较好控制烧结体的外观形状和尺寸[9]。
粉末冶金论文
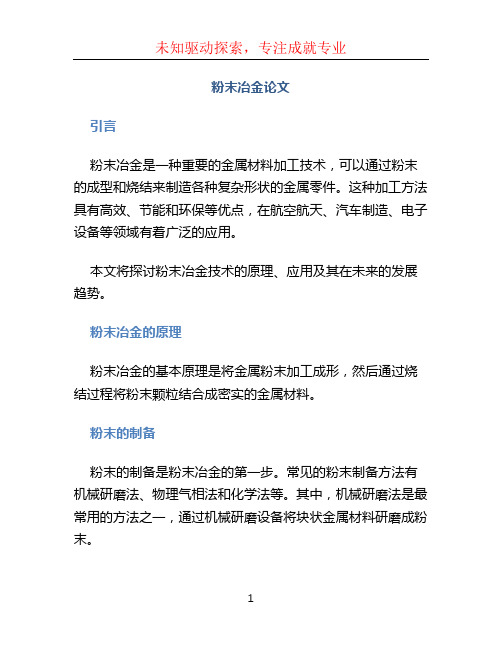
粉末冶金论文引言粉末冶金是一种重要的金属材料加工技术,可以通过粉末的成型和烧结来制造各种复杂形状的金属零件。
这种加工方法具有高效、节能和环保等优点,在航空航天、汽车制造、电子设备等领域有着广泛的应用。
本文将探讨粉末冶金技术的原理、应用及其在未来的发展趋势。
粉末冶金的原理粉末冶金的基本原理是将金属粉末加工成形,然后通过烧结过程将粉末颗粒结合成密实的金属材料。
粉末的制备粉末的制备是粉末冶金的第一步。
常见的粉末制备方法有机械研磨法、物理气相法和化学法等。
其中,机械研磨法是最常用的方法之一,通过机械研磨设备将块状金属材料研磨成粉末。
粉末成型粉末成型是将粉末按照所需形状进行加工的过程。
常见的粉末成型方法有压制、注射成型和挤压成型等。
其中,压制是最常用的方法之一,在压制过程中,粉末经过一定的压力使其紧密结合。
烧结过程烧结是粉末冶金的核心工艺环节。
在烧结过程中,经过高温和一定的时间作用,粉末颗粒之间发生结晶增长,形成坚固的结合。
粉末冶金的应用航空航天领域粉末冶金技术在航空航天领域有着广泛的应用。
通过粉末冶金技术,可以制造出复杂形状的零件,如涡轮叶片、火箭发动机喷嘴等。
这些零件具有高强度、耐高温和耐腐蚀等特点,能够适应极端环境下的工作条件。
汽车制造在汽车制造过程中,粉末冶金技术可以用于制造发动机零件、传动系统零件以及制动系统零件等。
通过粉末冶金技术,可以提高零件的性能,如减轻重量、提高强度和耐磨性等,从而提高整车的性能和经济性。
电子设备粉末冶金技术在电子设备制造中也有着重要的应用。
通过粉末冶金技术,可以制造出高导电性和磁性的材料,如电子封装材料、磁性存储器件等。
这些材料具有良好的热传导性和电磁性能,能够满足高性能电子设备的需求。
粉末冶金的发展趋势随着科学技术的进步和需求的不断增加,粉末冶金技术也在不断发展和创新。
3D打印技术与粉末冶金的结合粉末冶金技术与3D打印技术的结合,可以实现更加复杂、精密的零件制造。
通过3D打印技术,可以直接控制粉末的成型过程,制造出各种复杂形状的零件。
粉末冶金材料论文参考
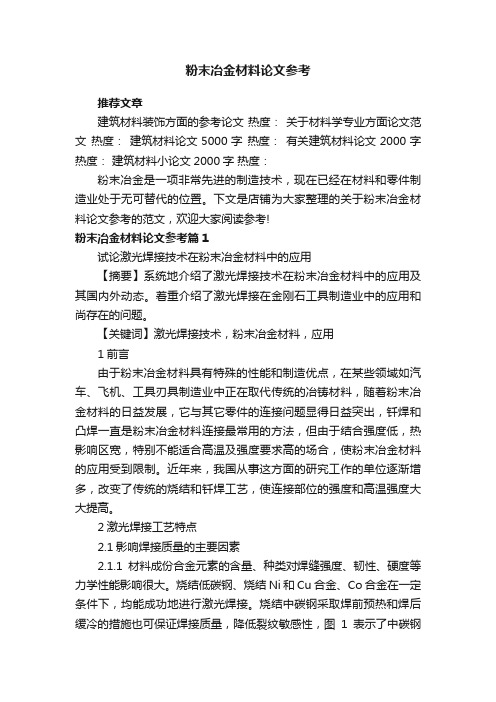
粉末冶金材料论文参考推荐文章建筑材料装饰方面的参考论文热度:关于材料学专业方面论文范文热度:建筑材料论文5000字热度:有关建筑材料论文2000字热度:建筑材料小论文2000字热度:粉末冶金是一项非常先进的制造技术,现在已经在材料和零件制造业处于无可替代的位置。
下文是店铺为大家整理的关于粉末冶金材料论文参考的范文,欢迎大家阅读参考!粉末冶金材料论文参考篇1试论激光焊接技术在粉末冶金材料中的应用【摘要】系统地介绍了激光焊接技术在粉末冶金材料中的应用及其国内外动态。
着重介绍了激光焊接在金刚石工具制造业中的应用和尚存在的问题。
【关键词】激光焊接技术,粉末冶金材料,应用1前言由于粉末冶金材料具有特殊的性能和制造优点,在某些领域如汽车、飞机、工具刃具制造业中正在取代传统的冶铸材料,随着粉末冶金材料的日益发展,它与其它零件的连接问题显得日益突出,钎焊和凸焊一直是粉末冶金材料连接最常用的方法,但由于结合强度低,热影响区宽,特别不能适合高温及强度要求高的场合,使粉末冶金材料的应用受到限制。
近年来,我国从事这方面的研究工作的单位逐渐增多,改变了传统的烧结和钎焊工艺,使连接部位的强度和高温强度大大提高。
2激光焊接工艺特点2.1影响焊接质量的主要因素2.1.1材料成份合金元素的含量、种类对焊缝强度、韧性、硬度等力学性能影响很大。
烧结低碳钢、烧结Ni和Cu合金、Co合金在一定条件下,均能成功地进行激光焊接。
烧结中碳钢采取焊前预热和焊后缓冷的措施也可保证焊接质量,降低裂纹敏感性,图1表示了中碳钢预热和不预热条件下焊缝区的显微硬度分布,预热时硬度降低,接头韧性增加,因为组织由贝氏体和少量的珠光体代替了针状马氏体。
2.1.2烧结条件在氢气、分解氨和真空中烧结的材料均能成功的进行激光焊接,在干净的还原性气氛中烧结的材料焊后出现的气孔、孔洞、夹杂和氧化物较小;此外,合适的烧结温度、保温时间、压力及温度-压力曲线也是焊接成功的重要保证。
- 1、下载文档前请自行甄别文档内容的完整性,平台不提供额外的编辑、内容补充、找答案等附加服务。
- 2、"仅部分预览"的文档,不可在线预览部分如存在完整性等问题,可反馈申请退款(可完整预览的文档不适用该条件!)。
- 3、如文档侵犯您的权益,请联系客服反馈,我们会尽快为您处理(人工客服工作时间:9:00-18:30)。
粉末冶金高速压制技术的研究现状及发展摘要:介绍一种低成本高密度粉末冶金零件成形技术一高速压制技术,通过阐述该技术的特点、原理、关键技术分析,指出其材料性能和应用前景以及高速压制技术目前存在的问题。
关键词:粉末冶金;高速压制;高密度粉末冶金技术以其低成本、近净形等加工特点在许多领域得到广泛应用。
密度对粉末冶金材料至关重要,它显著影响结构材料的力学性能,尤其是疲劳性能。
因此提高材料密度是粉末冶金的主要研究内容之一。
近年来粉末冶金新技术、新工艺层出不穷,温压技术、表面致密技术、高速压制技术等新技术的出现,使得粉末冶金技术不断取得突破性进展。
高速压制技术(high velocity compaction,简称HVC)是瑞典Hoganas公司在2001年6月主持召开的专门会议所推介的一种新技术,它所使用的重锤能产生强烈的冲击波,能在0.02s内将能量通过压模传给粉末进行致密化,间隔0.3s 的一个个附加的冲击波可将密度不断提高,使材料的性能更加优异,成本更加低廉,采用该技术可利用比传统压制小的设备生产超大零件。
HVC可能是粉末冶金工业寻求低成本高密度材料加工技术的又一次新突破。
1 高速压制技术的特点1.1高密度高性能HVC技术通过强烈的冲击波进行压制,使P/M零件达到高密度,它不仅可以使零件高致密化,而且可以使其密度均匀化。
与传统压制相比,HVC技术可使压坯密度提高0.3 g/cm3以上,如右图1所示。
典型的齿轮冲击试验表明其密度变化小于0.01 g/cm3。
将高速压制与其它工艺相结合,可使粉末压坯密度更高。
以铁基压坯为例,HVC技术与模壁润滑相结合,压坯密度可达7.6 g/cm3,与模壁润滑和温压结合的压坯密度达7.7g/cm3,若采用高速复压复烧工艺,压坯密度可达7.8g/cm3,接近全致密。
密度对提高材料性能的影响显而易见,如基于D.AE和Astaloy CrM的、采用HVC技术制备的材料与传统压制技术制备的材料相比,抗拉强度和屈服强度均提高20%~25%,其他各项性能指标也均有较大提高。
1.2弹性后效低用HVC技术成形的压坯,其径向弹性后效比传统压制低。
研究表明,对于水雾化普通铁基粉末ASCl00.29,高速压制成形的直径为31mm的圆柱体生坯径向弹性后效比传统压制的减少40%[1]。
弹性后效与压坯几何形状和粉末材料有关,北京科技大学王建忠等[2]发现,对于电解铜粉,多次高速压制的弹性后效比单次高速压制的小,从而减小了试样的脱模力。
1.3生产成本低P/M零部件在小轿车中的用量不断增加,探索出一个既能提高材料性能又不增加成本的生产方法,对于汽车生产厂家尤为重要。
以传统的一次压制为参考,几种粉末冶金工艺的相对生产成本如图2所示。
由此可见,采用高速压制技术制备的密度、高性能P/M零部件,具有良好的性价比,在成本与性能之间找到了最佳结合点。
图2几种不同制备工艺材料密度与成本比较Ⅱ1.4高生产率HVC的压制速度比传统压制快500~1000倍,其压制工序与传统压制工序相同,可用于大批量生产。
1.5 低经济成形大零件HVC可以通过连续不断的高频冲击迅速提高密度,密度和冲击能量之间的关系可以叠加,而在传统压制中采用重复压制密度提高不明显。
这种快速多重压实的特点在成形大型零件时具有实用性,且可通过较小型设备生产超大型零件,并使成本更低。
例如,HVC要获得相同的密度,用4kJ的能量冲击一次和2kJ的能量冲击两次都可以实现。
多重冲击致密的优点就是可以用比传统压制小的设备制备重达5kg的零部件,如用一次冲击能量为4~6kJ的HVC机来生产某一零件,可以用2×3kJ或3×2kJ的HVC机来制造而不需要用很大的设备。
多重冲击可由高速循环(冲击间隔小于0.3s)来实现。
通过对重锤冲击行程的控制,冲击能量控制已实现计算机操作,可以通过任意选择的冲击能量来安排冲击次序。
2 HVC技术基本原理高速压制生产零件的过程和传统的压制过程工序相同。
混合粉末加进送料斗中,粉末通过送粉靴自动填充模腔压制成形,之后零件被顶出并转入烧结工序。
所不同的是高速压制的压制速度比传统压制高500~1000倍,压机锤头速度高达2~30 rn/s,液压驱动的锤头重达5~1200kg,粉末在0.02s 之内通过高能量冲击进行压制,压制时产生强烈的冲击波。
通过附加间隔。
0.3s的多重冲击能达到更高的密度。
锤头的质量和它在冲击瞬间的速度决定了压制能量的大小和材料致密的程度。
图3为HVC的基本原理示意图。
图3 HVC基本原理示意图[3]3关键技术分析作为一种新型的粉末成形技术,HVC技术已成为目前粉末冶金界的研究热点,其关键技术受到严格的保护。
HVC关键技术主要包括几下几个方面:1)高速压制设备高速压制关键技术之一是如何获得瞬间的冲击速度,很多研究者通过各种不同的方法来驱动冲锤产生很高的速度,如压缩空气、爆炸混合气,磁力驱动、机械弹簧掣。
但爆炸成形由于生产效率低,可控制性差,并不适合工业化生产。
而电磁压制是利用感应电流和磁场的相互作用产生电磁力来压缩粉末,使粉末在非常短的时间内达到致密,但由于趋肤效应,中心部分可能压制不足,故主要适合于加工外形复杂或中空的零件,例如各种齿轮、齿环、轮毂等。
瑞典Hydropulsor公司利用其独创的液压阀门和控制系统,使冲击速度达到普通液压机的50倍,这一安全、高效技术的出现,极大地促进了动态压制技术的发展。
目前世界上这种高速压制成形机只有7台,国内也只有南京东部希顿精密机械有限公司能制造高速压机,因此研究具有自主知识产权的高速压机很有必要。
2)粉末及模具系统。
目前高速压制的生坯密度和性能均高于常规压制,但是在高速压制状态下,可能会造成粉末与模壁之间的焊合,使粉末压坯难于从阴模中脱出。
因此,成功开发润滑系统是实现高速压制的关键技术之一。
在模压过程中,致密化存在一个颗粒重排主导阶段向塑形变形主导阶段的转变[4-5],在高压制力下颗粒重排不占主要地位,模壁润滑能比粉末润滑更加有效地降低粉末与模壁的摩擦力。
为了获得更高的压坯密度,模壁润滑技术有望在高速压制中得到应用。
而且相对于不采用润滑剂或采用粉末润滑的高速压制,模壁润滑对减小压坯的脱模力显得尤为重要。
另外,模具的设计和选材是HVC技术推广和应用的关键[6-7]。
HVC技术与粉末冶金单向压制的模具很相似,但模具要承受剧烈的冲击波作用,因此必须设计为耐冲击震荡,且模具寿命在10万次以上。
所以模具通常使用韧性很高的材料如锻造合金钢和粉末冶金合金钢。
3)致密化机制。
果世驹教授[8]提出“热软化剪切致密化机制”,认为颗粒接合处在预压过程中形成“缺口”,当预成形的压坯进行高速压制时,“缺口”附近的颗粒表面形成高温剪切带并迅速蔓延,使颗粒容易发生塑性变形甚至局部焊合,从而达到高度致密化。
同时通过实验和理论分析,以黄培云双对数压制方程为参照,推导出HVC通用的压制方程,该方程合理解释了粉末压坯的致密化行为和特征。
对于铁粉,试验证明HVC方程有一定的精度,能够很好地指导速压制技术在铁粉上的应用。
4、HVC技术的应用目前,国内对高速压制技术的研究还处于起步阶段,国外对该技术的研究主要集中于铁粉,不锈钢粉和聚合物等。
各种重要几何形状的零部件都进行过高速压制试验,用来确定高速压制的可行性范围及其局限性,并指导此领域内的发展趋势。
诸如圆柱体、环形、棒体和凸轮等单层高度的零件制造已获得成功;内、外齿轮,齿条,花键也制备出来;另外一些几何形状的零件,典型的如阀门座,带轮毂的圆筒或齿轮正在研究评估之中,且很有希望。
高速压制的潜在应用不仅仅只局限在汽车工业,并且在现有的P/M领域也会有很大利用。
大量抗磨,较高疲劳寿命或者高强度的零件都可以采用高速压制来生产。
高速压制的能力能够满足很多工业上传动类零部件的要求。
具有潜在应用前景的结构零件包括阀座、法兰、导向阀、连杆、链轮、凸轮凸角机构、轴承盖、衬套、齿轮轴、轴承座圈等。
高速压制还将扩展P/M软磁复合材料的应用空间,该类零件包括磁芯和电动马达的定子与转子。
目前正在继续研究生产更复杂的多级部件。
图4是HVC压制的零件图。
图4 HVC技术制备的多阶和齿零件5、结束语HVC技术是传统粉末压制成形技术的极限式外延,为制备“三高一低”(高密度、高强度、高精度和低成本)的粉末冶金零件提供了一种新的成形方法。
国外已广泛开展成形金属、陶瓷和聚合物等材料的研究,目前已进人生产应用。
但HVC也存在一些问题,比如基于HVC瞬间冲击成形的特性,压制压力不适合表征其成形能力,如何评价HVC的技术优势是需进一步解决的问题。
此外,多次重复压制虽能达到更高的压坯密度,但压坯内部易出现缺陷,脱模时易分层或压坯烧结后出现肿胀等缺陷。
国内对HVC技术的研究刚刚起步。
充分利用国内已有的HVC试验平台,迅速开展该项目的研究,不仅具有重要的学术价值,而且能为提高我国粉末冶金零件的制造能力及其在国际市场的竞争力创造良好的条件。
参考文献[1] SKOGLUND P.High density P/M components by high velocity compaction[J].PM,2001,44(3):15—17.[2] 王建忠,曲选辉,尹海清,等.电解铜粉高速压制成形.中国有色金属学报,2008,18(8):1498—1503.[3] S kogIund P.High-deisity PM components by high velocity compaction.HOganas AB,HOganas ,Sweden,2002[4] SIMCHI A.Effects of lubrication procedure 011 theconsolidation,sintering and microstructural features of powdercompacts[J].Materials and Design,2003,24(8):585—594[5] BABAKHANI A,HAERIAN A,GHAMBARI M.On thecombined effect of lubrication and compaction temperature onproperties of iron—based P/M parts[J].Materials Science andEngineering,2006,437(2):360-365.[6] GEND H,STERl(ENBURG D.Hjgll一density multilevel PMcomponents by high velocity compaction:HERBERT D,RAIMUND R:Euro PM2004 Conference Proceedings.Shrewsbury UK:EPMA,2004:541—546.[7]CHRISTER A.High velocity compaction(Hvc)of stainlesssteel gas atomized powder:HERBERT D,RAIMUND R.EuroPM2004 Conference Proceedings.Shrewsbury UK:EPMA,2004:533-564.[8] 果世驹,迟悦,孟飞,等.粉末冶金高速压制成形的压制方程.粉末冶金材料科学与工程,2006,1 l(1):24—27.。