金属材料的扭转实验-庞玉
09_金属扭转试验_TortionTest
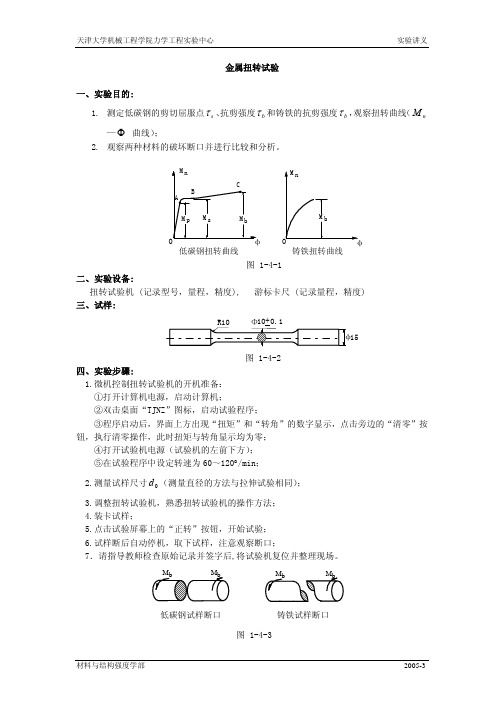
金属扭转试验一、实验目的:1. 测定低碳钢的剪切屈服点s τ、抗剪强度b τ和铸铁的抗剪强度b τ,观察扭转曲线(—曲线);nM Φ2. 观察两种材料的破坏断口并进行比较和分析。
低碳钢扭转曲线图 1-4-1二、实验设备:扭转试验机 (记录型号,量程,精度), 游标卡尺 (记录量程,精度)三、试样:15图 1-4-2四、实验步骤:1.微机控制扭转试验机的开机准备: ①打开计算机电源,启动计算机;②双击桌面“TJNZ”图标,启动试验程序;③程序启动后,界面上方出现“扭矩”和“转角”的数字显示,点击旁边的“清零”按钮,执行清零操作,此时扭矩与转角显示均为零;④打开试验机电源(试验机的左前下方);⑤在试验程序中设定转速为60~120°/min;2.测量试样尺寸(测量直径的方法与拉伸试验相同);0d 3.调整扭转试验机,熟悉扭转试验机的操作方法;4.装卡试样;5.点击试验屏幕上的“正转”按钮,开始试验;6.试样断后自动停机,取下试样,注意观察断口;7.请指导教师检查原始记录并签字后,将试验机复位并整理现场。
低碳钢试样断口铸铁试样断口图 1-4-3五、数据处理: nns s W M =τ, -----屈服扭矩 ns M nnb b W M =τ, -----最大破坏扭矩 nb M 1630d W n π=, -----抗扭截面模量n W六、说明:由于在弹性阶段时切应力在试样的圆截面上沿半径线性分布,当试样最外层进入屈服时,整个截面的绝大部分区域仍处于弹性范围。
试验机测量出的屈服扭矩实际上是横截面上相当一部分区域屈服时的扭矩值(如图中所示)。
所测到的破坏扭矩值也是这样。
因此,按前面公式计算得到的剪切屈服点s τ和抗剪强度b τ匀比实际值偏大。
若按全面屈服考虑,可得到以下关系:S S ττ43=实际 (S τ为实心圆截面试样的测试值)图1-4-4 切应力在不同阶段的分布图弹性阶段部分屈服全面屈服注意事项:低碳钢试样在屈服阶段及以前,需用手动加载,强化阶段用电动加载。
金属扭转实验报告

金属扭转实验报告金属扭转实验报告引言:金属材料是工业生产中最常用的材料之一,其力学性能对于产品的质量和可靠性至关重要。
在金属材料力学性能研究中,扭转实验是一种常用的实验方法,通过对金属试样进行扭转加载,可以获取材料的扭转强度、塑性变形能力和疲劳性能等重要参数。
本实验旨在通过对不同金属试样的扭转实验,探究金属材料的力学性能特点。
实验方法:1. 实验材料选择:本次实验选用了三种不同类型的金属材料,分别为铝合金、钢材和铜材。
这三种材料在工业中应用广泛,具有不同的力学性能特点。
每种材料都制备了10个相同尺寸的试样。
2. 实验装置:扭转实验使用扭转试验机进行,试验机具有精确的力和位移测量系统,能够准确记录试样在加载过程中的力学性能变化。
试样通过夹具固定在试验机上,然后扭转加载。
3. 实验步骤:(1) 将试样固定在夹具上,确保试样的中心轴与扭转试验机的转轴一致。
(2) 设置试验机的加载速度和加载范围,确保实验过程的可控性。
(3) 开始加载,记录试样的扭转力和位移数据。
(4) 当试样发生破坏或达到预设的加载条件时,停止加载,并记录试样的破坏形态。
实验结果与分析:1. 铝合金试样的扭转强度较低,破坏形态为断裂。
铝合金具有较好的塑性变形能力,在扭转过程中能够发生较大的变形,但其强度较低,容易发生断裂。
2. 钢材试样的扭转强度较高,破坏形态为塑性变形。
钢材具有较高的强度和较好的塑性变形能力,在扭转过程中能够承受较大的载荷而不发生断裂。
3. 铜材试样的扭转强度介于铝合金和钢材之间,破坏形态为塑性变形。
铜材具有较好的强度和塑性变形能力,但相对于钢材而言,其强度较低。
结论:通过本次实验,我们对铝合金、钢材和铜材的扭转性能进行了研究。
实验结果表明,不同类型的金属材料具有不同的力学性能特点。
铝合金具有较好的塑性变形能力,但强度较低;钢材具有较高的强度和塑性变形能力;铜材介于两者之间。
这些实验结果对于金属材料的选择和应用具有重要的指导意义,有助于提高产品的质量和可靠性。
材料力学金属扭转实验报告
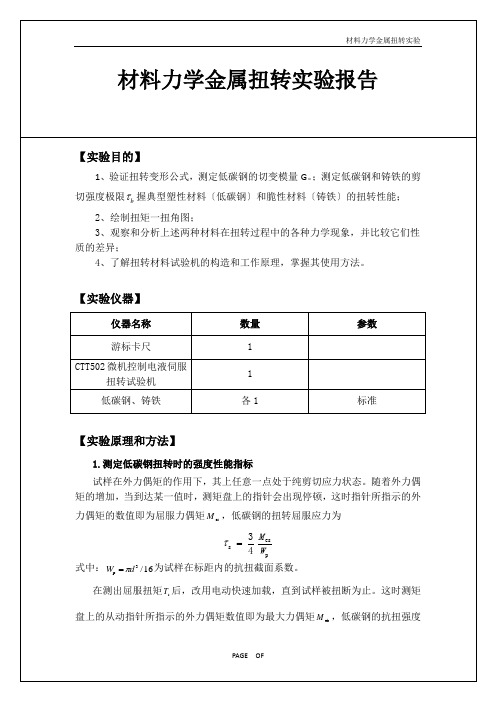
材料力学金属扭转实验报告
【实验目的】
1、验证扭转变形公式,测定低碳钢的切变模量 G。;测定低碳钢和铸铁的剪
切强度极限 b 握典型塑性材料〔低碳钢〕和脆性材料〔铸铁〕的扭转性能;
2、绘制扭矩一扭角图;
3、观察和分析上述两种材料在扭转过程中的各种力学现象,并比较它们性
质的差异;
4、了解扭转材料试验机的构造和工作原理,掌握其使用方法。
s
3 M es
4 Wp
式中: Wp d 3 / 16 为试样在标距内的抗扭截面系数。
在测出屈服扭矩 Ts 后,改用电动快速加载,直到试样被扭断为止。这时测矩
盘上的从动指针所指示的外力偶矩数值即为最大力偶矩 M eb ,低碳钢的抗扭强度
PAGE
OF
材料力学金属扭转实验
为
b
3 M eb
4 Wp
PAGE
OF
d 3
12
4
3
s Wp s
材料力学金属扭转实验
无论从测矩盘上指针前进的情况,还是从自动绘图装置所绘出的曲线来看,
A 点的位置不易精确判定,而 B 点的位置则较为明显。因此,一般均根据由 B 点
测定的 M es 来求扭转切应力 s 。当然这种计算方法也有缺陷,只有当实际的应力
分布与图 1-7c 完全相符合时才是正确的,对塑性较小的材料差异是比较大的。
从图 1-6 可以看出,当外力偶矩超过 M es 后,扭转角 增加很快,而外力偶矩 M e
增加很小, BC 近似于一条直线。因此,可认为横截面上的切应力分布如图 1-7c
所示,只是切应力值比 s 大。根据测定的试样在断裂时的外力偶矩 M eb ,可求得
4 实验四金属材料扭转实验

4 实验四金属材料扭转实验
一、实验目的
研究实验材料进行扭转变形后其力学性能。
二、实验原理
扭转变形是指在无限长假想杆材料横截面仅施加弯曲力的完全变形,其中应力均匀分
布于断面,杆材料的截面形状由圆形变成椭圆形。
三、实验环境
良好的室内环境,无电磁干扰,无固体颗粒,提供适当的实验操作场所,如实验室、
实验台等。
四、实验内容
1. 收集相关实验物料:金属标样、变形设备、实验软件等。
2. 安装变形设备,调试设备,使金属标样处于位置稳定性状态;
3. 按照实验计划,在变形设备上,施加一定大小的拉力,观察金属标样形变情况;
4. 在实验软件中,记录金属标样变形、错断、最终变形等信息;
5.根据实验数据对实验结果进行测试,分析实验结果,计算实验结果的重要力学参数;
6. 总结本次实验;
五、实验结果
在实验过程中,金属标样的形状出现变形,横截面形状由圆形变成椭圆形。
另外,通
过计算,可以得出实验材料的断裂应力为450MPa,变形能为385J,变形塑性指数为0.87。
材料的扭转实验实验报告
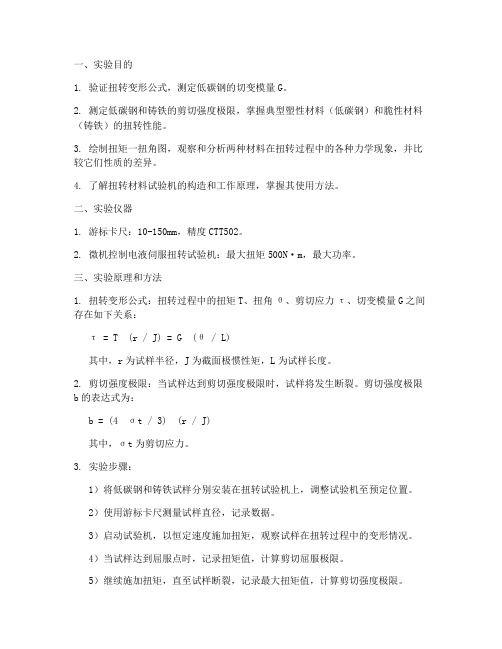
一、实验目的1. 验证扭转变形公式,测定低碳钢的切变模量G。
2. 测定低碳钢和铸铁的剪切强度极限,掌握典型塑性材料(低碳钢)和脆性材料(铸铁)的扭转性能。
3. 绘制扭矩一扭角图,观察和分析两种材料在扭转过程中的各种力学现象,并比较它们性质的差异。
4. 了解扭转材料试验机的构造和工作原理,掌握其使用方法。
二、实验仪器1. 游标卡尺:10-150mm,精度CTT502。
2. 微机控制电液伺服扭转试验机:最大扭矩500N·m,最大功率。
三、实验原理和方法1. 扭转变形公式:扭转过程中的扭矩T、扭角θ、剪切应力τ、切变模量G之间存在如下关系:τ = T (r / J) = G (θ / L)其中,r为试样半径,J为截面极惯性矩,L为试样长度。
2. 剪切强度极限:当试样达到剪切强度极限时,试样将发生断裂。
剪切强度极限b的表达式为:b = (4 σt / 3) (r / J)其中,σt为剪切应力。
3. 实验步骤:1)将低碳钢和铸铁试样分别安装在扭转试验机上,调整试验机至预定位置。
2)使用游标卡尺测量试样直径,记录数据。
3)启动试验机,以恒定速度施加扭矩,观察试样在扭转过程中的变形情况。
4)当试样达到屈服点时,记录扭矩值,计算剪切屈服极限。
5)继续施加扭矩,直至试样断裂,记录最大扭矩值,计算剪切强度极限。
6)绘制扭矩一扭角图,分析两种材料在扭转过程中的力学现象。
四、实验结果与分析1. 实验数据:低碳钢:- 直径:d = 10mm- 屈服扭矩:T屈服= 200N·m- 最大扭矩:T最大= 300N·m铸铁:- 直径:d = 10mm- 屈服扭矩:T屈服= 100N·m- 最大扭矩:T最大= 150N·m2. 分析:通过实验结果,可以看出低碳钢和铸铁在扭转过程中的力学性能存在明显差异。
低碳钢的屈服扭矩和最大扭矩均高于铸铁,说明低碳钢的扭转性能优于铸铁。
这是由于低碳钢具有良好的塑性变形能力,而铸铁属于脆性材料,抗扭性能较差。
金属材料的扭转实验-庞玉
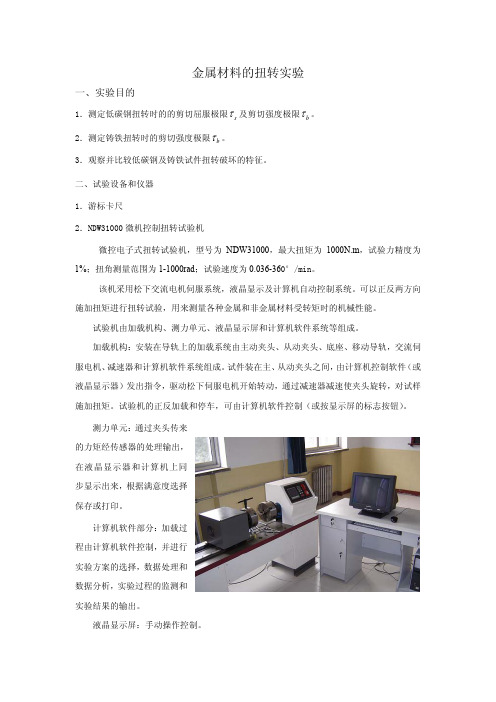
金属材料的扭转实验一、实验目的1.测定低碳钢扭转时的的剪切屈服极限s τ及剪切强度极限b τ。
2.测定铸铁扭转时的剪切强度极限b τ。
3.观察并比较低碳钢及铸铁试件扭转破坏的特征。
二、试验设备和仪器 1.游标卡尺2.NDW31000微机控制扭转试验机微控电子式扭转试验机,型号为NDW31000,最大扭矩为1000N.m ,试验力精度为1%;扭角测量范围为1-1000rad ;试验速度为0.036-360°/min。
该机采用松下交流电机伺服系统,液晶显示及计算机自动控制系统。
可以正反两方向施加扭矩进行扭转试验,用来测量各种金属和非金属材料受转矩时的机械性能。
试验机由加载机构、测力单元、液晶显示屏和计算机软件系统等组成。
加载机构:安装在导轨上的加载系统由主动夹头、从动夹头、底座、移动导轨,交流伺服电机、减速器和计算机软件系统组成。
试件装在主、从动夹头之间,由计算机控制软件(或液晶显示器)发出指令,驱动松下伺服电机开始转动,通过减速器减速使夹头旋转,对试样施加扭矩。
试验机的正反加载和停车,可由计算机软件控制(或按显示屏的标志按钮)。
测力单元:通过夹头传来的力矩经传感器的处理输出,在液晶显示器和计算机上同步显示出来,根据满意度选择保存或打印。
计算机软件部分:加载过程由计算机软件控制,并进行实验方案的选择,数据处理和数据分析,实验过程的监测和实验结果的输出。
液晶显示屏:手动操作控制。
三、试样NDW31000扭转试验机的试样夹持直径在8~40mm 。
本试验使用标距L=100mm,标距部分直径d=10mm 的圆形截面标准试件。
四、实验原理很多传动零件都在扭转条件下工作。
测定扭转条件下的机械性能,对零件的设计计算和选材有实际意义。
纯扭转时,圆试样表面为纯剪应力状态(如图1)其最大剪应力和正应力绝对值相等,夹角成450,因此扭转实验可以明显区分材料的断裂方式—拉断或剪断。
如果材料的抗剪强度小于抗拉强度,破坏形式为剪断,断口应与其轴线垂直;如果材料的抗拉强度小于抗剪强度,破坏原因为拉应力。
金属材料扭转实验-实验指导

金属材料扭转实验扭转问题是工程中经常遇到的一类问题。
金属材料的室温扭转实验通过对试样(低碳钢和铸铁)施加扭矩,测量扭矩及其相应的扭角(一般扭至断裂),来测定一些材料的扭转力学性能指标。
国家标准GB/T 10128-2007《金属材料室温扭转试验方法》是本试验的依据。
一、实验目的1了解GB/T 10128-2007《金属材料室温扭转试验方法》所规定的定义和符号、试样、实验要求、性能测定方法。
2了解扭转试验机的基本构造和工作原理,掌握其使用方法。
3测定金属材料扭转时的上下屈服强度、抗扭强度和相应的扭角。
4比较不同材料在扭转时的机械性能及其破坏情况。
二、实验设备扭转试验机(介绍参看附录),游标卡尺。
扭转试样采用圆柱形试样,材料为低碳钢和铸铁。
三、实验原理使直杆发生扭转的外力,是一对大小相等、转向相反、作用面垂直于杆轴线的外力偶。
在这种外力偶作用下,杆表面的纵向线将变成螺旋线,即发生扭转变形。
当发生扭转的杆是等直圆杆时,杆的物性和横截面几何形状具有极对称性,杆的变形满足平面假设(横截面像刚性平面一样绕轴线转动),这是扭转问题中最简单的情况。
标准中定义了多种可测的扭转性能指标,表1列出了扭转破坏实验常用的几种指标的符号、名称和单位。
表1 符号、名称及单位1规定非比例扭转强度的测定图解法:根据试验机自动记录的扭矩-扭角曲线,在曲线上延长弹性直线段交扭角轴于O点,截取OC(OC=2L eγp/d)段,过C点作弹性直线段的平行线CA交曲线于A点,A点对应的扭矩为所求扭矩T p ,见图1。
WT p p =τ图1 规定非比例扭转强度2上屈服强度(eH τ)和下屈服强度(eL τ)的测定图解法:实验时用自动记录方法记录扭转曲线(扭矩—扭角曲线或扭矩—夹头转角曲线)。
首次下降前的最大扭矩为上屈服扭矩;屈服阶段中不计初始瞬时效应的最小扭矩为下屈服扭矩,见图2。
按下式分别计算上屈服强度和下屈服强度。
W T eHeH =τ WT eLeL =τ图2 上、下屈服强度3 抗扭强度(m τ)的测定对试样连续施加扭矩,直至扭断。
《2024年高压扭转工艺对Al-Zn-Mg-Cu合金组织与性能的研究》范文
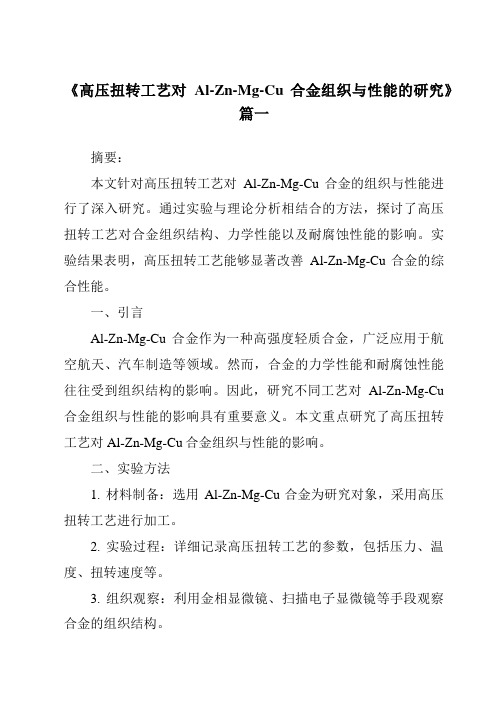
《高压扭转工艺对Al-Zn-Mg-Cu合金组织与性能的研究》篇一摘要:本文针对高压扭转工艺对Al-Zn-Mg-Cu合金的组织与性能进行了深入研究。
通过实验与理论分析相结合的方法,探讨了高压扭转工艺对合金组织结构、力学性能以及耐腐蚀性能的影响。
实验结果表明,高压扭转工艺能够显著改善Al-Zn-Mg-Cu合金的综合性能。
一、引言Al-Zn-Mg-Cu合金作为一种高强度轻质合金,广泛应用于航空航天、汽车制造等领域。
然而,合金的力学性能和耐腐蚀性能往往受到组织结构的影响。
因此,研究不同工艺对Al-Zn-Mg-Cu合金组织与性能的影响具有重要意义。
本文重点研究了高压扭转工艺对Al-Zn-Mg-Cu合金组织与性能的影响。
二、实验方法1. 材料制备:选用Al-Zn-Mg-Cu合金为研究对象,采用高压扭转工艺进行加工。
2. 实验过程:详细记录高压扭转工艺的参数,包括压力、温度、扭转速度等。
3. 组织观察:利用金相显微镜、扫描电子显微镜等手段观察合金的组织结构。
4. 性能测试:进行硬度测试、拉伸试验、耐腐蚀性测试等,评估合金的力学性能和耐腐蚀性能。
三、高压扭转工艺对Al-Zn-Mg-Cu合金组织的影响1. 晶粒细化:高压扭转工艺能够使Al-Zn-Mg-Cu合金的晶粒得到显著细化,从而提高合金的力学性能。
2. 第二相粒子分布:高压扭转工艺能够改善第二相粒子的分布,使其更加均匀地分布在基体中,从而提高合金的耐腐蚀性能。
3. 织构变化:高压扭转工艺能够改变合金的织构,使合金具有更好的塑性变形能力。
四、高压扭转工艺对Al-Zn-Mg-Cu合金性能的影响1. 力学性能:高压扭转工艺能够显著提高Al-Zn-Mg-Cu合金的硬度、屈服强度和抗拉强度,同时保持较好的延伸率。
2. 耐腐蚀性能:高压扭转工艺能够改善Al-Zn-Mg-Cu合金的耐腐蚀性能,提高其在恶劣环境下的使用寿命。
五、结论本文通过实验与理论分析相结合的方法,研究了高压扭转工艺对Al-Zn-Mg-Cu合金组织与性能的影响。
金属材料扭转实验及弹性模量的测量

中那么明显。由于强化阶段的过程很长,图中只绘出其开始阶段和最后阶段,破坏时实 验段的扭角可达 10π以上
图所示的铸铁试样扭转曲线可近似的视为直线 (与拉伸曲线相似, 没有明显的直线段) , 试样破环时的扭转形变比拉伸时的形变要明显的多。 从扭转试验机上可读取的试样的屈服扭矩 Ts 和破环扭矩 Tb。由 计算材料的屈服剪切点和抗剪切强度。 需要指出的是,对于塑形材料,采用实心圆截面试样测量得到的屈服点和抗剪强度,高 于薄壁圆环截面试样的测量值, 这是因为实心园截面试样扭转时横截面切应力分布不均 匀所致。 当园截面试样横截面的最外层切应力达到剪切强度屈服点时, 占横截面绝大部分的内层 应力仍低于弹性极限,因此此时试样仍表现为弹性行为,没有明显的屈服现象。当扭矩 继续增加使横截面大部分区域的切应力均达到剪切屈服点时, 试样会表现出明显的屈服 现象,此时的扭矩比真实的屈服扭矩要大一点,对于破环扭矩也会有同样的情况。低碳 钢试样和铸铁试样的扭转破环断口形貌有很大的差别断面是最大切应力作用面, 断口较 为平齐,可知剪切破坏,图 2 所示为铸铁试样的断面是与试样轴成 45 度角的螺旋面断 面是最大拉应力作用面,断口较为粗糙,因而是最大拉应力造成的拉伸断裂破坏 。 和
低碳钢扭转
铸铁扭转
T l =15.4GPa I p
E = 2(1 )
六、思考题 1.为什么低碳钢试样扭转破坏断面与横截面重合,而铸铁试样是与 试样轴线成 450 螺旋断裂面?
答:在圆杆扭转实验中,低碳钢属于剪切强度低于拉伸强度的材料, 破坏是由横截面上的最大切应力引起, 并从杆的最外层沿横截面发生 剪断产生的,而铸铁是属于拉伸强度低于剪切强度的材料, 它的破坏 是由 -45 °斜截面上最大拉应力引起,并从杆的最外层沿着轴线约 45°倾角的螺旋形曲面发生拉断而产生的, 故低碳钢试样扭转破坏断 面与横截面重合,而铸铁试样是与试样轴线成 450 螺旋断裂面。
《2024年高压扭转工艺对Al-Zn-Mg-Cu合金组织与性能的研究》范文
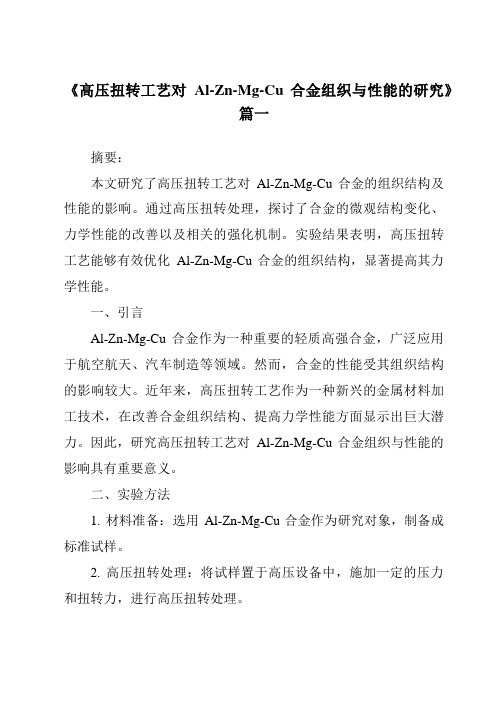
《高压扭转工艺对Al-Zn-Mg-Cu合金组织与性能的研究》篇一摘要:本文研究了高压扭转工艺对Al-Zn-Mg-Cu合金的组织结构及性能的影响。
通过高压扭转处理,探讨了合金的微观结构变化、力学性能的改善以及相关的强化机制。
实验结果表明,高压扭转工艺能够有效优化Al-Zn-Mg-Cu合金的组织结构,显著提高其力学性能。
一、引言Al-Zn-Mg-Cu合金作为一种重要的轻质高强合金,广泛应用于航空航天、汽车制造等领域。
然而,合金的性能受其组织结构的影响较大。
近年来,高压扭转工艺作为一种新兴的金属材料加工技术,在改善合金组织结构、提高力学性能方面显示出巨大潜力。
因此,研究高压扭转工艺对Al-Zn-Mg-Cu合金组织与性能的影响具有重要意义。
二、实验方法1. 材料准备:选用Al-Zn-Mg-Cu合金作为研究对象,制备成标准试样。
2. 高压扭转处理:将试样置于高压设备中,施加一定的压力和扭转力,进行高压扭转处理。
3. 性能测试与组织观察:通过拉伸试验、硬度测试等方法,测定合金的力学性能;利用金相显微镜、扫描电镜和透射电镜等手段,观察合金的微观组织结构。
三、实验结果与分析1. 微观组织结构变化(1)晶粒细化:经过高压扭转处理后,Al-Zn-Mg-Cu合金的晶粒得到显著细化,晶界清晰可见,有利于提高合金的力学性能。
(2)第二相分布:高压扭转处理使得合金中的第二相颗粒更加均匀地分布在基体中,提高了合金的均匀性。
2. 力学性能改善(1)屈服强度和抗拉强度:经过高压扭转处理后,Al-Zn-Mg-Cu合金的屈服强度和抗拉强度均得到显著提高,表明合金的力学性能得到优化。
(2)延伸率:虽然高压扭转处理会降低合金的延伸率,但仍然保持在较高水平,满足一般应用需求。
3. 强化机制探讨(1)晶界强化:晶粒细化使得晶界数量增加,晶界对位错运动的阻碍作用增强,从而提高合金的强度。
(2)第二相强化:第二相颗粒的存在能够有效地阻碍位错运动,提高合金的强度和硬度。
金属材料扭转实验

金属材料扭转实验在实际工程机械中,有很多传动是在扭转情况下工作。
设计扭转轴所用的许用剪应力,是根据材料在扭转破坏试验时,所测出的扭转剪切屈服极限τS 或剪切强度极限τb 而求得的。
在扭转试验时,即使韧性极好的金属也能在扭转时发生断裂,由于扭转断裂后外形无明显变化,从而可以精确地计算应力和应变情况。
一、实验目的1. 测定低碳钢的剪切屈服极限τs ,剪切强度及极限τb 。
2. 测定铸铁的剪切强度极限τb 。
3. 比较低碳钢和铸铁在扭转时的变形和破坏特征。
二、实验设备ND-500C 扭转试验三、实验原理1. 试件:根据国家标准,一般采用圆截面试件,标距mm 100=L ,标距部分直径mm 10=d 。
如图2-6所示。
图2-62. 实验原理:材料的扭转破坏过程可用扭转曲线即T -ϕ曲线来描述。
T 表示施加在试件上的扭距,ϕ表示试件的相对扭转角度。
现分别讨论低碳钢和铸铁扭转时力学性质,如图2-7所示。
图2-7图中起始直线段OA 表明试件在这阶段中的T 与ϕ成比例, 截面上的剪应力呈线性分布,如图 2-8(a)。
在 A 点处,T 与ϕ的比例关系开始破坏,此时截面周边上的剪应力达到了材料的剪切屈服极限s τ,相应的扭矩记为P T 。
由于这时截面内部的剪应力尚小于s τ,故试件仍具有承载能力,T -ϕ曲线呈继续上升的趋势。
扭矩超过P T 后,截面上的剪应力分布发生变化,如图2-8(b)。
在截面上出现了一个环状塑性区,并随着P T 的增长,塑性区逐步向中心扩展,T -ϕ曲线稍微上升,直到B 点趋于平坦,截面上各点材料完全达到屈服。
试件整体屈服后, T -ϕ曲线上出现屈服平台。
根据国家试验标准规定,这时的示值为材料扭转屈服扭矩,记作S T 。
而剪切屈服极限s τ由下式表 tS S W T ⋅=43τ 其中163d W t π=是试件的抗扭截面系数。
P T T ≤时的剪应力分布 P S T T T >>时的剪应力分布 ST T =时的剪应力分布 图2-8 截面上剪应力分布图继续给试件加载,试件再继续变形,材料进一步强化。
4.实验四 金属材料扭转实验

金属材料扭转实验一、 实验目的1. 测定低碳钢材料的剪切屈服极限s τ及剪切强度极限b τ。
2. 测定铸铁材料的剪切强度极限b τ。
3. 观察低碳钢和铸铁扭转变形过程中各种现象,比较两种材料试样断口破坏特性。
二、 实验仪器设备CTT500 微机控制扭转试验机、游标卡尺、低碳钢扭转试样和铸铁扭转试样 三、 实验原理将材料试样装夹在扭转试验机的夹头上,实验时,扭转试验机的一个夹头固定不转,另一个夹头绕轴转动,从而对材料试样施加扭转载荷,使试样发生扭转变形,同时绘制出试样承受的扭矩T 与发生的变形扭转角φ的关系曲线(T –φ曲线)。
1. 低碳钢扭转实验图 2-1-2 所示为低碳钢试样在扭转变形过程中的 T –φ关系曲线。
由该曲线可得到低碳钢材料在整个扭转过程中所表现出来的力学性能,其主要特征如下:在弹性变形的OA直线段。
试样截面上扭矩T与扭转角φ成正比例关系,材料服从切变虎克定律,在该阶段可测定材料的切变模量G,试样横截面上剪应力沿半径线性分布如图 2-1-3(a)所示。
拉伸时有明显屈服现象的金属材料在扭转时同样存在屈服现象,只是由于扭转时试样截面上的应力分布不均匀,当试样表面材料屈服时,内部材料并未出现屈服,因此载荷的下降不是突然发生,故无拉伸时的初始瞬时效应。
当扭矩保持恒定或在小范围内波动,而扭转角仍持续增加(曲线出现平台)时的扭矩称为屈服扭矩。
上屈服扭矩:屈服阶段中扭矩首次下降前的最大扭矩,称为上屈服扭T,如图 2-2-2 中所示。
矩,记为suT,如下屈服扭矩:屈服阶段中的最小扭矩称为下屈服扭矩,记为sL图 2-2-2中所示。
本次实验中测定下屈服扭矩作为低碳钢扭转时的屈服扭矩 Ts,根据τ。
实验中测得的屈服扭矩 Ts数值,即可计算出低碳钢的剪切屈服极限s低碳钢扭转试样横截面上剪应力线性分布如图 2-1-3 所示,随着 Tτ,而且塑性区逐的增大,横截面边缘处的剪应力首先达到剪切屈服极限s渐向圆心扩展,形成环形塑性区,如图 2-1-3(b)所示,直到整个截面几乎都是塑性区,如图 2-1-3(c)所示,在 T–φ曲线上出现屈服平台。
金属材料的扭转试验
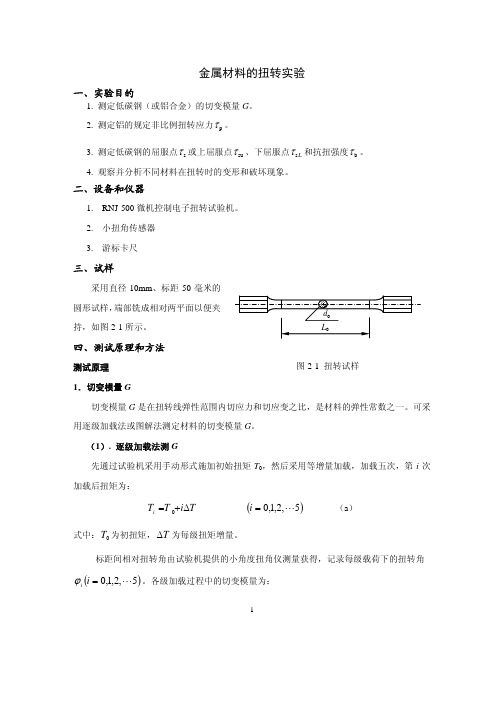
将(a)式代入,上式化为
∑ G = L0∆T ∑ IP
i2
i (ϕi −ϕ G
通过试验机配备的扭矩传感器以及小角度扭角仪,可自动
记录扭矩-扭转角(T-ϕ )曲线,如图 2-2 所示。 在所记录的曲线的弹性直线段上,选取扭矩增量 ∆T 和相
∆T ∆ϕ
2. 点击测试软样运行窗口,正式测试,直至试件变形开始急剧增加时,停止实验,取
7
下试样。保存实验数据。打印 T − ϕ 试验曲线。
(3) 测屈服点及抗扭强度 点击运行按钮,按预先设定的测试程序对试件进行加载,直至试件断裂。保存实验数据, 同时输出试验数据。 在测屈服点及抗扭强度时,应注意观察试样变形及破坏情况。取下试样,观察并分析断 口形貌和形成原因。
图 2- 6 图解法求规定 非比例扭转应力
扭矩即为与非比例切应变规定值 γ p 所对应的扭矩 Tp ,按下式计算规定非比例扭转应力:
6
测试方法
τp
=
Tp WP
(2-12)
(1)测 G ① 测 G(逐级加载法)
试验过程采用手动方式进行。先施加 3N.m 的初始扭矩,记下初始角度ϕ 0 ;然后采用等
增量( ∆T =5N.m)分五级加载,记录每次对应的角度值(在对应显示窗口显示)。重复测试
5
到规定数值时,按弹性扭转公式计算得到的切应力称为“规定非比例扭转应力”。相应应力附
以下标说明非比例切应变规定值
γ
p
τ ,如 p 0.015
和τ
p 0.3
分别表示规定的非比例切应变
γ
p
为
0.015%和 0.3%时的应力。
一般把τ p0.015 称为条件扭转比例极限,τ p0.3 称为扭转屈服强度。
材料力学金属扭转实验报告

材料力学金属扭转实验报告实验报告标题:材料力学金属扭转实验摘要:本实验旨在探究金属材料在扭转加载下的力学性能,并通过实际测量数据分析验证材料力学的相关理论。
实验通过制备试样、设计测试装置、施加扭转力、测量材料的应变和转动角度等步骤完成。
实验结果表明,金属材料在扭转过程中呈现出线性弹性行为,并根据实测数据计算得到了杨氏模量和剪切模量等材料力学参数。
关键词:材料力学、金属扭转、应变、转动角度、弹性行为、杨氏模量、剪切模量引言:金属材料是工程领域中常用的材料之一,其力学性能的研究对于提高材料的应用性能、设计结构的可靠性有着重要意义。
材料力学的研究主要包括拉伸、压缩、扭转等,本实验主要关注金属材料在扭转加载下的力学性能。
扭转是指通过对材料施加扭转矩,使其绕轴转动一定角度的过程。
通过测量应变和转动角度等参数,可以计算得到杨氏模量和剪切模量等材料力学性质的参数。
实验目的:1.了解金属材料在扭转加载下的力学性能。
2.掌握金属材料力学实验的基本操作流程。
3.熟悉测量应变和转动角度的相关方法。
4.计算得到金属材料的杨氏模量和剪切模量。
实验原理:金属材料在扭转加载下的力学行为可以用材料力学的相关理论进行描述。
杨氏模量是指材料的拉伸应力和应变之间的比值,可以用来衡量材料的刚度。
剪切模量是指材料在剪切应力作用下所表现出的抗剪切性能。
实验装置及试样制备:本实验采用扭转仪作为实验装置,配有测力传感器和角度测量装置。
所用试样为金属圆管,长度为L,外径为D,厚度为δ,可以通过所施加的扭转角度的测量反映材料的力学性能。
实验步骤:1.制备金属圆管试样:根据要求切割金属圆管,并记录其几何参数。
2.安装试样:将金属圆管试样安装在扭转仪上,并保证试样与仪器的接触面完全平行。
3.调整扭转仪:调整扭转仪使其垂直于试样轴线,并调节扭转仪的零位。
4.校准测力传感器:根据实验装置的要求对测力传感器进行校准。
5.施加扭转力:根据实验设计的负荷标准和实验要求,施加扭转力,并记录施加扭转力的数值。
金属材料圆轴扭转实验分析

金属材料圆轴扭转实验分析篇一:金属材料扭转实验及弹性模量的测量南昌大学工程力学实验报告姓名:钟燕平学号:5902411050 专业班级:本硕111班班级编号:S088 实验时间14时00分第9 星期三座位号:教师编号:成绩:金属扭转破坏实验、剪切弹性模量的测定中那么明显。
由于强化阶段的过程很长,图中只绘出其开始阶段和最后阶段,破坏时实验段的扭角可达10π以上图所示的铸铁试样扭转曲线可近似的视为直线(与拉伸曲线相似,没有明显的直线段),试样破环时的扭转形变比拉伸时的形变要明显的多。
从扭转试验机上可读取的试样的屈服扭矩Ts和破环扭矩Tb。
由计算材料的屈服剪切点和抗剪切强度。
需要指出的是,对于塑形材料,采用实心圆截面试样测量得到的屈服点和抗剪强度,高于薄壁圆环截面试样的测量值,这是因为实心园截面试样扭转时横截面切应力分布不均匀所致。
当园截面试样横截面的最外层切应力达到剪切强度屈服点时,占横截面绝大部分的内层应力仍低于弹性极限,因此此时试样仍表现为弹性行为,没有明显的屈服现象。
当扭矩继续增加使横截面大部分区域的切应力均达到剪切屈服点时,试样会表现出明显的屈服现象,此时的扭矩比真实的屈服扭矩要大一点,对于破环扭矩也会有同样的情况。
低碳钢试样和铸铁试样的扭转破环断口形貌有很大的差别断面是最大切应力作用面,断口较和为平齐,可知剪切破坏,图2所示为铸铁试样的断面是与试样轴成45度角的螺旋面断面是最大拉应力作用面,断口较为粗糙,因而是最大拉应力造成的拉伸断裂破坏。
四、实验步骤(1)低碳钢的扭转实验步骤首先测量试样直径d在试样上安装扭角测试样装置,将一个定位环套在试样的一端,装上卡盘,将螺钉拧紧。
再将另一个定位环套在试样的另一端,装上另一个卡盘,根据不同的试样标距要求将试样搁放在相应的V型块上,使卡盘与V型块两端紧贴,保证卡盘与试样垂直,将卡盘上的螺钉拧紧。
接着将试样机两端夹头对正。
将已装扭角测试实验装置的试样的一端放入从动夹头的夹口间,将试样加紧,进行扭矩清零操作,推动移动支座,使试样的另一端进入主动夹头间,进行试样保护,从而消除夹持扭矩,并清零扭角。
(2023)金属材料的扭转实验报告(一)

(2023)金属材料的扭转实验报告(一)(2023)金属材料的扭转实验报告实验目的•了解金属材料的扭转性能•掌握扭转实验的基本操作和流程•探究金属材料的力学性质对其扭转性能的影响实验原理金属材料的扭转性能与其抗扭转强度、剪切模量等力学性质密切相关。
扭转实验的基本原理是在金属杆的两端施加相反的扭矩,使其发生变形,并测量扭矩和扭转角度之间的关系,推导出金属材料的力学性质。
实验器材•扭转实验机•金属杆样品实验步骤1.将金属杆样品固定在扭转实验机上,确定扭转轴。
2.根据实验要求,在样品的两端施加相反的扭矩,使其发生扭转变形。
3.测量扭矩和扭转角度,记录数据。
4.根据测量的数据,计算出金属材料的扭转模量、抗扭转强度等参数。
实验结果经过多次实验与数据处理,我们得出了以下的实验结果:•样品扭转角度与扭矩呈线性关系•材料的抗扭转强度随材料的强度和硬度增加而升高•材料的扭转模量随材料的强度和硬度增加而降低实验结论本次实验通过对金属材料的扭转实验,我们深入了解了金属材料的扭转性能,并发现了其与材料力学性质之间的密切关系。
同时,我们也掌握了扭转实验的基本操作和流程,为以后的实验提供了很大的帮助。
实验分析从实验结果可以看出,金属材料的扭转性能受到多个因素的影响。
抗扭转强度是材料的一种重要性能指标,其大小决定了材料在实际应用中最大可承受的扭转力矩。
与此同时,材料的硬度和强度也影响其扭转性能,硬度大的材料对扭转的抵抗力相对较大,但其扭转变形程度可能随之降低。
因此,在选择材料时,需要综合考虑多个因素,以保证材料在实际应用中具有较好的性能表现。
实验不足本次实验还存在着一些不足之处。
首先,实验数据量较少,其可靠性有待进一步提高。
其次,我们并没有对不同材料的扭转性能进行对比分析,这可能导致实验结果的局限性。
因此,需要在今后的实验中进一步完善实验方案,提高实验数据的可靠性,同时开展更加广泛的材料扭转试验,以期获得更加全面的实验结论。
金属材料扭转实验
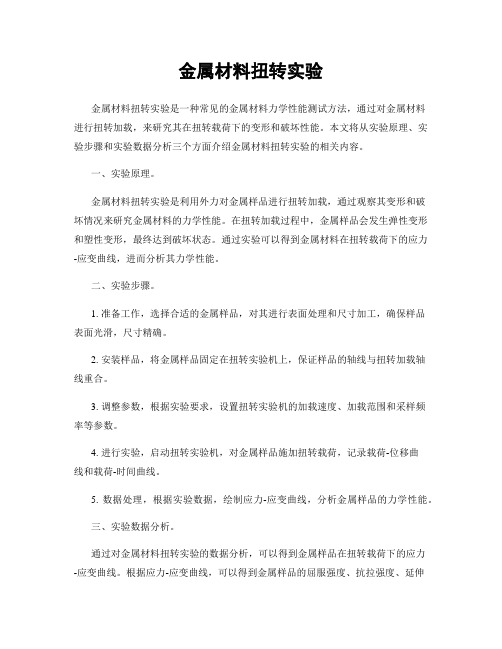
金属材料扭转实验金属材料扭转实验是一种常见的金属材料力学性能测试方法,通过对金属材料进行扭转加载,来研究其在扭转载荷下的变形和破坏性能。
本文将从实验原理、实验步骤和实验数据分析三个方面介绍金属材料扭转实验的相关内容。
一、实验原理。
金属材料扭转实验是利用外力对金属样品进行扭转加载,通过观察其变形和破坏情况来研究金属材料的力学性能。
在扭转加载过程中,金属样品会发生弹性变形和塑性变形,最终达到破坏状态。
通过实验可以得到金属材料在扭转载荷下的应力-应变曲线,进而分析其力学性能。
二、实验步骤。
1. 准备工作,选择合适的金属样品,对其进行表面处理和尺寸加工,确保样品表面光滑,尺寸精确。
2. 安装样品,将金属样品固定在扭转实验机上,保证样品的轴线与扭转加载轴线重合。
3. 调整参数,根据实验要求,设置扭转实验机的加载速度、加载范围和采样频率等参数。
4. 进行实验,启动扭转实验机,对金属样品施加扭转载荷,记录载荷-位移曲线和载荷-时间曲线。
5. 数据处理,根据实验数据,绘制应力-应变曲线,分析金属样品的力学性能。
三、实验数据分析。
通过对金属材料扭转实验的数据分析,可以得到金属样品在扭转载荷下的应力-应变曲线。
根据应力-应变曲线,可以得到金属样品的屈服强度、抗拉强度、延伸率等力学性能指标。
同时,还可以观察金属样品的变形和破坏情况,分析其力学性能表现。
在实验数据分析过程中,需要注意对数据的准确性和可靠性进行评估,排除实验误差对结果的影响。
同时,还需要将实验结果与金属材料的实际工程应用进行比较,评估其在实际工程中的性能表现。
综上所述,金属材料扭转实验是一种重要的力学性能测试方法,通过对金属样品进行扭转加载,可以得到其在扭转载荷下的力学性能指标和变形破坏情况。
通过实验原理、实验步骤和实验数据分析的介绍,相信读者对金属材料扭转实验有了更深入的了解,对相关领域的研究和应用具有一定的参考价值。
压缩和扭转实验(08.2)

实验报告要求
1.计算两种材料压缩、扭转强度指标及低碳钢扭转剪切弹性模量G。 计算两种材料压缩、扭转强度指标及低碳钢扭转剪切弹性模量G 计算两种材料压缩 及低碳钢扭转剪切弹性模量 描述两种材料压缩、 2.描述两种材料压缩、扭转破坏后断口特点,分析断口破坏原因。 描述两种材料压缩 扭转破坏后断口特点,分析断口破坏原因。 通过实验, 材料在拉伸、 3.通过实验,综合比较材料在拉伸、压缩、扭转时的力学性能。 通过实验 综合比较材料在拉伸 压缩、扭转时的力学性能。
低碳钢、铸铁扭转力学性能: 低碳钢、铸铁扭转力学性能:
低碳钢仍然有弹性阶段、屈服阶段和强化阶段。 低碳钢仍然有弹性阶段、屈服阶段和强化阶段。 仍然有弹性阶段
O
Ts
低碳钢扭转曲线
∆ϕ
铸铁没有明显直线部分,没有屈服变形。 铸铁没有明显直线部分,没有屈服变形。 没有明显直线部分 T
T 屈服强度 τs = s (强度指标) 强度指标) W p
二、实验仪器 液压电子万能材料试验机。 1、液压电子万能材料试验机。 电子扭转试验机。 2、电子扭转试验机。 0.02mm游标卡尺 游标卡尺。 3、0.02mm游标卡尺。
金属材料压缩和扭转实验
实验试样
采用标准圆形试样 1.扭转试样 — 采用标准圆形试样 扭转试样 长试样 l0=10d0 短试样 l0= 5d0 l0
m 4.强度指标以MPa为单位(1M 强度指标以MPa为单位( Pa=1N / m ),并保留3位有效数字。 并保留 位有效数字。 强度指标以MPa为单位 位有效数字
2
F
压缩
Fsc
O
拉伸
F 强度指标) σsc = sc(强度指标) A 0
低碳钢压缩曲线
∆l
思考: 思考:能否得到低碳钢压缩时的强度极限σbc ?
《2024年高压扭转工艺对Al-Zn-Mg-Cu合金组织与性能的研究》范文
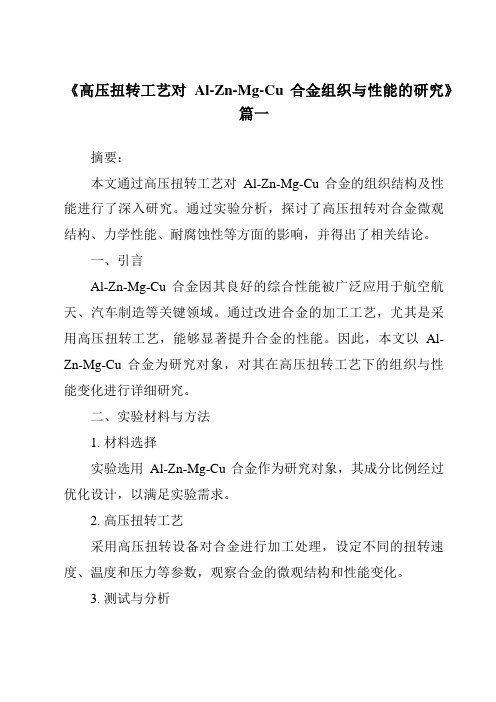
《高压扭转工艺对Al-Zn-Mg-Cu合金组织与性能的研究》篇一摘要:本文通过高压扭转工艺对Al-Zn-Mg-Cu合金的组织结构及性能进行了深入研究。
通过实验分析,探讨了高压扭转对合金微观结构、力学性能、耐腐蚀性等方面的影响,并得出了相关结论。
一、引言Al-Zn-Mg-Cu合金因其良好的综合性能被广泛应用于航空航天、汽车制造等关键领域。
通过改进合金的加工工艺,尤其是采用高压扭转工艺,能够显著提升合金的性能。
因此,本文以Al-Zn-Mg-Cu合金为研究对象,对其在高压扭转工艺下的组织与性能变化进行详细研究。
二、实验材料与方法1. 材料选择实验选用Al-Zn-Mg-Cu合金作为研究对象,其成分比例经过优化设计,以满足实验需求。
2. 高压扭转工艺采用高压扭转设备对合金进行加工处理,设定不同的扭转速度、温度和压力等参数,观察合金的微观结构和性能变化。
3. 测试与分析通过金相显微镜、扫描电子显微镜(SEM)、X射线衍射仪等设备对合金的微观结构进行观察和分析;同时,对合金的力学性能和耐腐蚀性进行测试。
三、实验结果与分析1. 微观组织结构分析(1)晶粒形态:经过高压扭转处理后,Al-Zn-Mg-Cu合金的晶粒明显细化,晶界更加清晰。
随着扭转程度的增加,晶粒尺寸逐渐减小,合金的晶界强化效果显著。
(2)相组成:高压扭转处理后,合金中的第二相粒子分布更加均匀,有利于提高合金的力学性能和耐腐蚀性。
2. 力学性能分析(1)硬度:随着高压扭转程度的增加,Al-Zn-Mg-Cu合金的硬度逐渐提高,表现出良好的强化效果。
(2)拉伸性能:经过高压扭转处理后,合金的抗拉强度和延伸率均有所提高,表明其具有良好的塑性和韧性。
3. 耐腐蚀性分析(1)电化学腐蚀测试:通过电化学腐蚀测试发现,经过高压扭转处理的Al-Zn-Mg-Cu合金的耐腐蚀性得到显著提高。
(2)腐蚀形貌观察:利用SEM观察腐蚀后的合金表面形貌,发现高压扭转处理后合金表面的腐蚀坑点明显减少,说明其耐腐蚀性得到提升。
- 1、下载文档前请自行甄别文档内容的完整性,平台不提供额外的编辑、内容补充、找答案等附加服务。
- 2、"仅部分预览"的文档,不可在线预览部分如存在完整性等问题,可反馈申请退款(可完整预览的文档不适用该条件!)。
- 3、如文档侵犯您的权益,请联系客服反馈,我们会尽快为您处理(人工客服工作时间:9:00-18:30)。
金属材料的扭转实验一、实验目的1.测定低碳钢扭转时的的剪切屈服极限s τ及剪切强度极限b τ。
2.测定铸铁扭转时的剪切强度极限b τ。
3.观察并比较低碳钢及铸铁试件扭转破坏的特征。
二、试验设备和仪器 1.游标卡尺2.NDW31000微机控制扭转试验机微控电子式扭转试验机,型号为NDW31000,最大扭矩为1000N.m ,试验力精度为1%;扭角测量范围为1-1000rad ;试验速度为0.036-360°/min。
该机采用松下交流电机伺服系统,液晶显示及计算机自动控制系统。
可以正反两方向施加扭矩进行扭转试验,用来测量各种金属和非金属材料受转矩时的机械性能。
试验机由加载机构、测力单元、液晶显示屏和计算机软件系统等组成。
加载机构:安装在导轨上的加载系统由主动夹头、从动夹头、底座、移动导轨,交流伺服电机、减速器和计算机软件系统组成。
试件装在主、从动夹头之间,由计算机控制软件(或液晶显示器)发出指令,驱动松下伺服电机开始转动,通过减速器减速使夹头旋转,对试样施加扭矩。
试验机的正反加载和停车,可由计算机软件控制(或按显示屏的标志按钮)。
测力单元:通过夹头传来的力矩经传感器的处理输出,在液晶显示器和计算机上同步显示出来,根据满意度选择保存或打印。
计算机软件部分:加载过程由计算机软件控制,并进行实验方案的选择,数据处理和数据分析,实验过程的监测和实验结果的输出。
液晶显示屏:手动操作控制。
三、试样NDW31000扭转试验机的试样夹持直径在8~40mm 。
本试验使用标距L=100mm,标距部分直径d=10mm 的圆形截面标准试件。
四、实验原理很多传动零件都在扭转条件下工作。
测定扭转条件下的机械性能,对零件的设计计算和选材有实际意义。
纯扭转时,圆试样表面为纯剪应力状态(如图1)其最大剪应力和正应力绝对值相等,夹角成450,因此扭转实验可以明显区分材料的断裂方式—拉断或剪断。
如果材料的抗剪强度小于抗拉强度,破坏形式为剪断,断口应与其轴线垂直;如果材料的抗拉强度小于抗剪强度,破坏原因为拉应力。
破坏面应是沿450方向。
材料的扭转过程可用M n —Φ曲线来描述。
M n —Φ曲线也叫扭转图。
低碳钢试件的M n —Φ曲线,如图2所示。
图1 圆轴扭转时的表面应力图中起始直线段OA 表明试件在这阶 段中的M n 与ϕ成比例, 截面上的剪应力 呈线性分布,如图 3(a)。
在 A 点处, M n 与ϕ的比例关系开始破坏,此时截面周 图2 低碳钢试件扭转图边上的剪应力达到了材料的剪切屈服极限s τ,相应的扭矩记为M P 。
由于这时截面内部的剪应力尚小于s τ,故试件仍具有承载能力,M n —ϕ曲线呈继续上升的趋势。
扭矩超过 M P 后,截面上的剪应力分布发生变化,如图 3(b)。
在截面上出现了一个环状塑性区,并随着M n 的增长,塑性区逐步向中心扩展,M n —ϕ曲线稍微上升,直到B 点趋于平坦,截面上各材料完全达到屈服,扭矩数值几乎不再变化,甚至出现微小的减小现象。
,此时的扭矩的最小值即为屈服扭矩M s 。
如图3(C),根据静力平衡条件,可以求得s τ与M s 的关系为:∫=As s dA M ρτ将式中dA 用环状面积元素ρπρd 2表示,则有/22423d s s os p M d πτρρ==∫W (1)故剪切屈服极限34s s pM W τ=,式中316p d W π=是试件的抗扭截面模量。
继续给试件加载,试件再继续变形,材料进一步强化。
当达到M n 一ϕ曲线上的C 点时,试件被剪断。
扭矩数值为最大扭矩M b ,与公式(1)相似,可得剪切强度极限34bb pM W τ=(2) 铸铁的M n 一ϕ曲线如图4所示。
铸铁的扭转曲线虽然较明显地偏离直线,但仍可近似地看作一条直线, 没有屈服过程, 故可按弹性应力公式计算出材料的剪切强度极限:即bb pM W τ=(3) 由于低碳钢的抗拉能力高于抗剪能力,故试件沿横截面剪断,而铸铁的抗拉能力低于抗剪能力, 故试件从表面上某一最弱处,沿与轴线成45º方向拉断成一螺旋面。
五、实验步骤1、试样准备在试样标距段的两端及中间截面处,沿两相互垂直方向测量直径各一次,并计算各截面直径的算术平均值。
选用三个截面中平均直径的最小值计算试样截面的扭转截面系数。
2、实验机准备①估计载荷,确定载荷在试验机量程范围之内。
②打开试验机开关;打开计算机主机及显示屏。
③打开控制主程序,联机。
3、装夹试样①将试样轻夹于两夹头上,使试样的纵轴线与试验机夹头的轴线要重合。
②松开被动夹头,拧紧主动夹头。
在控制程序的试验界面中选“扭矩清零”。
③拧紧两夹头,将试样夹好,并用粉笔在试样轴线方向画一条细线,以观察扭转变形。
4、录入试验参数①选择“参数录入”,单击“增加”,录入试验组编号、形状、日期等数据后保存。
②选中相应试验编号的文件夹,单击“增加”,录入试样序号、尺寸后保存。
③选择试验曲线(扭矩-扭角曲线)、试验方向(逆时针加载保证曲线显示于坐标平面上)、试验速度(低碳钢完全屈服前36°/min,屈服后360°/min;铸铁由于变形较小,采用缓慢加载36°/min)和断裂控制条件(断裂百分比:低碳钢为60%,铸铁为80%)。
5、进行实验单击实验开始开启试验机,当试验力达到断裂百分比(低碳钢为60%,铸铁为80%)自动停止试验,并计算结果。
6、结束工作试验结束后,取出试样。
退出试验主程序,关闭计算机。
断开试验机电源。
六、数据处理1、原始数据原始直径d(mm)材料试样截面(Ⅰ)截面(Ⅱ)截面(Ⅲ)低碳钢铸铁2、 实验结果试样 屈服扭矩M s (kNm ) 破坏扭矩M b (kNm )真实剪切屈服极限τts (MPa)剪切强度极限τb (MPa)真实剪切强度极限τtb (MPa)低碳钢 铸铁其中,对铸铁材料只需计算剪切强度极限pbb W M =τ对低碳钢应计算真实剪切屈服极限和真实剪切强度极限,表达式分别为为psts W M 43=τpb tb W M 43=τ七、注意事项1、实验前,要仔细阅读实验机操作规程,实验时严格按操作规程进行操作。
2、低碳钢试件在弹性和屈服阶段,加载速度要尽量缓慢,试样进入强化阶段后可加快试验速度;铸铁试样扭转试验始终采用慢速加载。
3、实验中如果出现异常,应马上停机。
八、思考题1、为什么低碳钢试样扭转破坏断面与横截面重合,而铸铁试样是与试样轴线成45度螺旋断裂面。
2、低碳钢拉伸和扭转的断裂方式是否一样?破坏原因是否相同?3、铸铁在压缩和扭转时,断口外缘都与轴线成450,破坏原因是否相同?4、试样受扭时,表层的材料处于什么应力状态?5、安装试样时,为什么试样的纵轴线与试验机夹头的轴线要重合?6、根据低碳钢和铸铁拉伸、压缩、扭转试验的载荷-变形曲线、强度指标、断口形貌以及试件上一点的应力状态图等方面,综合分析两类材料的机械性质。
7、圆截面试样拉伸试验屈服点和扭转试样剪切屈服点有什么区别和联系。
8、铸铁扭转破坏断口的倾斜方向与外加扭矩的方向有无直接联系,为什么?剪切模量G 的测定一、实验目的1.测定低碳钢材料的切变模量G,并验证剪切虎克定律 2.学习扭角仪的原理和使用方法。
二、实验原理圆轴受扭时,材料处于纯剪切应力状态。
在比例极限以内,材料的剪应力τ与剪应变γ成正比,即满足剪切虎克定律:γτG = (1)由此可得出圆轴受扭时的虎克定律表达式:n pM L GI Φ=(2) 式中M n 为扭矩L 0是试件的标距长度I p 为圆截面的极惯性矩,G 为低碳钢剪切弹性模量。
通过扭角仪,对试件逐级增加同样大小的扭矩n M +,相应地由百分表测出相距为L 0的两个截面之间的相对扭转角增量i ϕΔ。
如果每一级扭矩增量所引起的扭转角增量i ϕΔ基本相同,这就验证了剪切虎克定律。
根据测得的各级扭转角增量的平均值ϕΔ,可用下式算出剪切弹性模量0n pM L G I ϕΔ=Δ (3) 实验按照等间隔分级加扭矩n M Δ的方法进行,由扭角仪测得相应的扭转角增量ϕΔ,即可求得G。
图1为JY-2型扭角仪。
试件1装在支架6的AB 间,其标矩为0200L mm =,直径10d mm =,在B 端支架外侧装有加荷臂2,其长度为L ,内侧装有测量臂3,其长度为R,在R 端支架上装有百分表架及百分表5。
每次加载时由百分表读出的是δ+,而n M PL =++,Rδϕ=++,将此二式代入(3)式,得到 0432LL R PG d πδ=++ (4) 三、实验设备 1.扭角仪扭角仪结构如图1所示。
2.百分表百分表是一种精度较高的比较量具,主要用于检测工件的形状和位置误差(如圆度、平面度、垂直度、跳动等),也可在机床上用于工件的安装找正。
百分表的测量准确度为0.01mm。
百分表的结构及其传动原理如图2所示。
当测量杆1向上或向下移动1mm 时,通过齿轮传动系统带动大指针5转一圈,同时小指针7转一格。
大指针每转动一格读数值为0.01mm,小指针每转动一格读数为1mm。
小指针处的刻度范围为百分表的测量范围。
测量时大小指针读数之和即为测量尺寸的变动量。
刻度盘可以转动,以便测量时大指针对准零刻度线。
此实验所用的百分表的量程为0-5mm,精度为0.01mm,此次实验只读大指针的读数值即可。
四、实验步骤1、把扭角仪夹具套在试件标距为0200L mm =的A、B 两截面处,并拧紧固定螺钉(实验室已安装好)。
2、将安装好扭角仪的试件一端安装在固定支座上,另一端安装在可转动支座上,安装好加荷臂及百分表,安装时注意百分表套筒松紧是否适度(过紧,不能与试件一起变形,过松,固定不住,实验室安装好)。
3、测量试件直径()、标距(10d m =m 0200L mm =),百分表触头到试件轴线的距离()以及力臂长度(150R m =m m 150L m =)。
4、百分表调零。
用手轻轻压砝码盘,使百分表指针能够转动且松开手后,百分表指针能够回到原来位置,然后转动表盘使指针对准零。
5、挂砝码逐级加载(每个砝码质量为1Kg),采用3级加载,并记录百分表的读数。
重复做3次,实验完后砝码放回原处。
6、检查实验数据,整理好实验仪器。
六、实验数据列表表格中的为砝码质量的增量。
P +P(kg) △P(kg)δ(mm)×10-2△δ(mm) ×10-21 2 3七、实验数据处理每一次加载读出百分表下降的位移δ+,共加3级。
卸载后再重复前面的操作,共做3次,按下式算出平均值,即inδδ=∑++平, R δϕ=++平, n 00432p M L LL R G I d Pϕπδ==++++平再算出各级载荷下的平均值,即为试件材料的剪切弹性模量,式中的为砝码重量的增量。