金属表面处理 锆化 硅烷
锆化前处理工艺
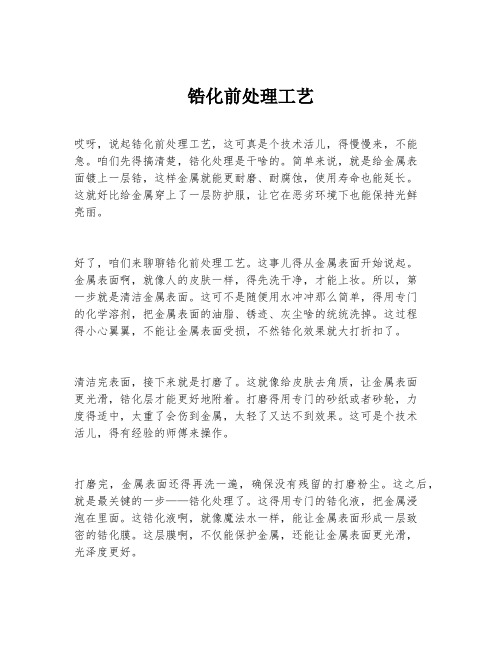
锆化前处理工艺哎呀,说起锆化前处理工艺,这可真是个技术活儿,得慢慢来,不能急。
咱们先得搞清楚,锆化处理是干啥的。
简单来说,就是给金属表面镀上一层锆,这样金属就能更耐磨、耐腐蚀,使用寿命也能延长。
这就好比给金属穿上了一层防护服,让它在恶劣环境下也能保持光鲜亮丽。
好了,咱们来聊聊锆化前处理工艺。
这事儿得从金属表面开始说起。
金属表面啊,就像人的皮肤一样,得先洗干净,才能上妆。
所以,第一步就是清洁金属表面。
这可不是随便用水冲冲那么简单,得用专门的化学溶剂,把金属表面的油脂、锈迹、灰尘啥的统统洗掉。
这过程得小心翼翼,不能让金属表面受损,不然锆化效果就大打折扣了。
清洁完表面,接下来就是打磨了。
这就像给皮肤去角质,让金属表面更光滑,锆化层才能更好地附着。
打磨得用专门的砂纸或者砂轮,力度得适中,太重了会伤到金属,太轻了又达不到效果。
这可是个技术活儿,得有经验的师傅来操作。
打磨完,金属表面还得再洗一遍,确保没有残留的打磨粉尘。
这之后,就是最关键的一步——锆化处理了。
这得用专门的锆化液,把金属浸泡在里面。
这锆化液啊,就像魔法水一样,能让金属表面形成一层致密的锆化膜。
这层膜啊,不仅能保护金属,还能让金属表面更光滑,光泽度更好。
锆化处理完,金属表面还得再洗一遍,把多余的锆化液洗掉。
最后,就是干燥了。
这得用专门的干燥设备,确保金属表面完全干燥,没有水分残留。
这样,锆化前处理工艺就算完成了。
整个过程啊,得严格按照操作规程来,一步都不能马虎。
这可是关系到金属使用寿命的大事儿,一点儿都不能马虎。
虽然听起来挺复杂的,但只要按照步骤来,其实也没那么难。
就像做饭一样,只要掌握了火候和调料,就能做出美味的菜肴。
锆化前处理工艺,也是一样的道理。
金属表面处理 锆化 硅烷

金属表面处理锆化硅烷1. 引言1.1 金属表面处理的重要性金属表面处理是指对金属表面进行改性处理,以提高其耐腐蚀性、耐磨性、耐疲劳性和美观性等性能。
金属制品在实际使用中常常会受到氧化、腐蚀、磨损等因素的影响,严重影响其使用寿命和效果。
而金属表面处理技术可以有效地解决这些问题,保护金属制品,延长其使用寿命,提高其性能表现。
金属表面处理的重要性主要体现在以下几个方面:金属表面处理可以有效防止金属制品因腐蚀而失效,延长其使用寿命,降低维护成本;金属表面处理可以提高金属制品的外观质量,提升其市场竞争力;金属表面处理可以改善金属制品的耐磨性和耐疲劳性,提高其使用效果;金属表面处理是实现金属材料功能多样化的重要手段,满足不同领域对金属制品性能的需求。
金属表面处理技术在工业生产和日常生活中具有重要意义,对于提高金属制品的质量、性能和使用寿命起着关键作用。
随着技术的发展和不断创新,金属表面处理技术将会迎来更加广阔的发展前景。
1.2 锆化和硅烷的介绍锆化是一种常用的金属表面处理技术,通过在金属表面形成一层锆化层,能够提高金属的耐腐蚀性和耐磨损性,同时提高金属的表面硬度。
锆化技术可以应用于各种金属材料,如铝、镁、钢铁等,广泛用于航空航天、汽车制造、电子等领域。
锆化和硅烷技术都是重要的金属表面处理方法,它们能够有效提升金属材料的性能和使用寿命,为各个行业提供优质的金属制品。
在金属表面处理领域,锆化和硅烷技术的应用和研究不断深入,为金属制品的品质提升和技术创新提供了有力支持。
2. 正文2.1 金属表面处理技术概述金属表面处理技术是一种通过特定的方法使金属表面获得特定性能的工艺。
金属在使用过程中会受到各种外界因素的影响,如氧化、腐蚀和磨损等,这些都会降低金属的使用寿命。
金属表面处理技术的应用变得至关重要。
金属表面处理技术有很多种,常见的包括镀层、涂覆、氧化、硝化等。
这些处理方法可以改善金属表面的耐腐蚀性、抗磨损性、导热性等性能,从而延长金属的使用寿命。
硅烷化处理及其在金属表面处理中的应用分析

通过硅烷化处理与传统磷化处理相比较,能够省去表调及磷 化前后的水洗工序,处理时间大大缩短,并减少了污水处理量。
1 硅烷化处理的原理 硅烷化处理是以有机硅烷为主要原料对金属或非金属材料
进行表面处理的过程,该过程通过引入硅烷基与基材形成共价 键连接,在金属表面形成高致密的保护膜。
硅烷是一类含硅基的有机/无机杂化物,其基本分子式为 X-R-SiY3,其中的Y指的是与硅原子连接的可水解基团,其中 R则是指非水解脂肪族链,其中的X指的是可以和有机材料实现 反应的基团,例如乙烯基以及氨基等[2]。
TECHNOLOGY AND INFORMATION
工业与信息化
硅烷化处理及其在金属表面处理中的应用分析
汪洋 包英俊 中国船舶重工集团第七一五研究所 浙江 杭州 311400
摘 要 工业生产中,将耐腐蚀的有机物涂覆在金属表面,经固化成膜后制备的有机涂层具有屏蔽、缓蚀及电化学 保护三方面的作用,防腐效果好。由于涂料具有选择性宽、可用范围广、节约能源、应用施工方便等优点,是现今 最有效、最经济和研究最多的表面防护方法之一。对工作表面进行强化热处理,可在不改变零件内部组织和性能的 前提下,达到工作心部与表层在组织结构、性能等的最佳配合。本文结合硅烷化处理剂的制备及金属表面处理方法 的对比,来分析硅烷化处理方法的优势和应用情况。 关键词 硅烷化;金属表面;处理工艺;应用分析
硅烷化处理相比传统的处理工艺有以下优势: (1)硅烷化金属表面处理工艺路线相比传统工艺省去了 表调和磷化前后两道水洗工序,减少了废水的排放量,减轻了 环境污染程度,降低了生产成本。 (2)在使用温度方面,由于硅烷成膜过程为常温化学反 应,因为在日常使用中槽液无须加热即可达到理想处理效果。 此方面相比较来说,为行业应用节省了大量能源并减少了燃料 废气排放。 (3)硅烷化反应中无沉淀反应,所以在日常处理中不产 生沉渣,消除了前处理工序中的固体废物处理问题并有效地延 长了槽液的倒槽周期。 (4)在配槽用量方面,硅烷化较磷化工艺也减少了 20%~50%,更关键的是在每平方米单耗方面硅烷化的消耗量 为传统磷化工艺的15%-20%。在处理时间上硅烷化较磷化也有 较大幅度的缩短,从而提高了生产率,降低了设备持续运作成 本。 (5)电沉积硅烷化金属表面处理工艺除具有硅烷化金属 表面处理工艺的优点外,还可以通过对沉积过程电化学参数的 调节,实现对硅烷化膜结构的可控制备。 (6)通过对现有磷化处理设备的简单改造,投入少量资 金,即可将磷化金属表面生产线改装成硅烷化和电沉积硅烷化
金属表面处理 锆化 硅烷

金属表面处理锆化硅烷全文共四篇示例,供读者参考第一篇示例:金属表面处理是一种常见的工艺,在制造金属产品时起着重要的作用。
金属表面处理的主要目的是提高金属产品的耐腐蚀性、耐磨损性和美观度。
锆化和硅烷是两种常见的金属表面处理方法。
一、锆化锆化是一种通过在金属表面形成一层锆化层来提高金属表面硬度、耐磨损性和耐腐蚀性的表面处理方法。
锆化的原理是将金属表面浸泡在含锆化剂的溶液中,通过化学反应在金属表面形成一层坚固的锆化层。
锆化层的形成可以提高金属表面的硬度和耐腐蚀性,延长金属产品的使用寿命。
锆化的主要优点包括:1. 提高金属表面的硬度和耐磨损性;2. 提高金属表面的耐腐蚀性;3. 降低金属表面的摩擦系数;4. 改善金属产品的外观。
锆化的主要应用领域包括汽车制造、航空航天、电子产品等各个领域。
在汽车制造领域,锆化可以提高汽车发动机的耐磨损性和耐腐蚀性;在航空航天领域,锆化可以提高飞机部件的抗氧化性能;在电子产品领域,锆化可以提高电子产品的耐磨损性和耐腐蚀性。
二、硅烷第二篇示例:金属表面处理是一种常见的工业加工技术,可以提高金属的表面性能和耐腐蚀性。
在金属表面处理中,锆化和硅烷处理是两种常见的方法,它们能够有效地改善金属的耐腐蚀性能,延长金属的使用寿命。
让我们来了解一下什么是锆化。
锆化是一种在金属表面形成一层锆化层的处理方法,通过在金属表面形成一种金属氧化物膜,从而提高金属的耐蚀性和耐磨性。
锆化处理可以应用于各种金属材料,如铁、铜、铝等,可以在金属表面形成一层致密的氧化层,有效地阻止金属材料与外界环境的接触,起到保护金属的作用。
在锆化处理中,通常会使用一种含锆元素的溶液进行处理,通过浸泡或涂覆的方式将锆元素与金属表面发生反应,形成致密的氧化层。
这种氧化层具有很高的硬度和耐腐蚀性能,可以有效地保护金属表面不受腐蚀和氧化的影响。
锆化处理后的金属表面不仅能够延长金属的使用寿命,还能够提高金属的外观质量,增强金属的抗磨损性能。
金属硅烷前处理技术

金属硅烷前处理技术
金属硅烷前处理技术是一种将金属表面处理成硅烷基化合物的技术。
该技术主要用于金属的防腐蚀和提高表面润滑性能。
金属硅烷前处理技术的主要步骤包括清洗、活化和硅烷基化处理。
清洗步骤主要是将金属表面的油脂、氧化物和污垢等污染物清除,以保证后续处理的有效性。
活化步骤是通过化学活化剂处理金属表面,增加表面活性,使硅烷化剂能够更好地与金属反应。
硅烷基化处理是使用硅烷化剂对金属表面进行处理,形成硅烷基化合物层。
硅烷基化合物具有较好的黏附性和耐腐蚀性,能够有效地防止金属被氧化、腐蚀和磨损,同时还能提高金属表面的润滑性能。
金属硅烷前处理技术广泛应用于航空航天、汽车制造、电子设备等领域,可以提高产品的质量和耐用性,延长使用寿命。
同时,该技术还能够减少对环境的污染,提高生产效率,具有较好的经济效益和社会效益。
金属表面硅烷处理技术的未来趋势

金属表面硅烷处理技术的未来趋势金属表面硅烷处理是近几年进展起来的一种有望代替铬酸钝化和磷化的环保型汽车车身前处理技术,该技术通过硅烷分子(通式为X-R-Si(OR)n)水解后产生的硅羟基与金属和金属氧化物反应,以及硅烷分子自身的缩合反应形成无机/有机膜层,以浸泡方式或电化学帮助沉积方式在金属表面制备这种具有疏水性能的膜层,该膜层能对金属基体供应爱护作用,而且能够提高金属和涂层之间的附着力。
成膜过程如下。
1、在使用过程中,水解后的OXSilane分子中的SiOH基团与基体金属表面的MeOH基团形成氢键,快速吸附于基体金属表面。
水解反应:OROHRO—Si—R1+3H2OHO—Si—R1+3ROHOROH2、在干燥过程中,SiOH基团和MeOH基团进一步分散,在界面上生成Si-O-Me共价键。
SiOH(溶液)+MeOH(金属表面)=SiOMe(界面)+H2O3、剩余的OXSilane分子则通过SiOH基团之间的分散反应在金属表面上形成具有Si-O-Si三维网状结构的有机膜。
缩合反应:OHOHOH2HO—Si—R1R1—Si—O—Si—R1+H2OOHOHOH关于硅烷与金属表面的反应机理,目前讨论者伞认为是硅醇与金属表面的氧气物或水化物层发生了反应(见图1)试验证明,不带有特征官能团的硅烷无论在固相或液相中都不具有电化学活性,既不能被氧化,也不能被还原。
经过硅烷处理的电极浸泡在电解质溶液中,硅烷膜能起到阻挡层的作用,阻挡电解质、水和氧分子向金属界面区域渗透。
尽管金属表面硅烷处理技术已经比较成熟,但硅烷膜的性能一一磷化膜相比还有一些差距,现在国内外各大金属表面处理剂生产公司都在全力进行有关的讨论开发工作,信任硅烷处理技术将会像磷化技术一样带给汽车车身涂装一次革命性的创新。
金属表面前处理液硅烷锆盐复合型陶化剂

金属表面前处理液硅烷 锆盐复合型陶化剂
硅烷锆盐复合型陶化剂
定义
CSF-801陶化剂是以硅烷、锆盐及硅烷锆盐复合为基 础的低能耗、高性能的新型环保产品,加入特殊的成 膜助剂后能在钢铁、锌板、铝材表面进行化学处理, 生成一种杂合难溶纳米级陶瓷转化膜。陶瓷转化膜具 有优良的耐腐蚀性,抗冲击力,能提高涂料的附着力。 转化膜生成过程中无需加热,槽液中也无渣产生。 CSF-801陶化剂中不含磷、锌、钙、镍、锰、铬等元 素,不含硝酸盐和亚硝酸盐等致癌物质,其废液经简 单中和处理后即可排放
陶化工作液的补加方法(以1吨槽 液计算
1、PH值的调整方法 (1)补加1kgCSF-801陶化剂,PH值下降0.1。 (2)补加1kgCSF-802碱性调整剂,PH值上升 0.2。
2、陶化点(F)的调整方法 补加1kgCSF-801陶化剂,F上升0.2,然后检 测PH值,调整PH值时对陶化点量小:是磷化的六分之一左右,污水处理量小,可节
约大量废水处理费用 6. 无需表调,简化工艺 7. 原磷化喷淋浅,做好磷化系统的清洁后可直接替换 8. 陶化膜与金属基体是通过化学键连接,陶化膜与涂料也是通过
化学键连接,因此通过陶化工艺的产品的附着力极强,为0级,陶 化膜厚度为20—30纳米,其正反冲击力均可达50KG,由于陶化膜 在含有锆盐下的高致密性,使其耐蚀性极强,完全超越磷化。
注意事项
1、各工作液尽量不要被污染。 2、按一般化学品进行储存和安全防护。
陶化与磷化的优势对比
1. 常温处理:无需加热设备,可节约大量能源(天然气、电源) 2. 无渣:喷淋管道和喷嘴不宜堵塞,工件不会挂灰 3. 环保:原液无磷,无锌、镍、锰、铬等元素,无硝酸盐和亚硝
金属表面硅烷化处理即非磷化转化
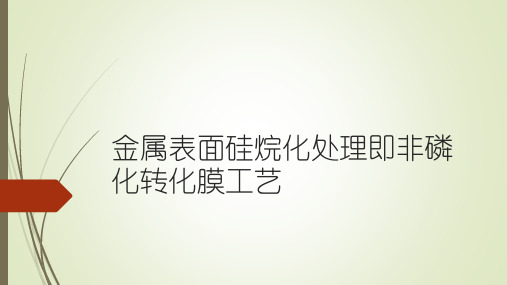
典型硅烷处理工艺介绍
硅烷处理剂浓度(5%) 处理方式:喷淋 PH值:5.0-6.8 温度:常温 处理时间:5-120秒 适用材料:钢铁件
工艺注意事项
工序间隔时间:各工序间的间隔时间如果太长,会造成工件在 运行过程中二次生銹,生锈泛黄泛绿的工件,严重影响硅烷化 效果,不能形成完整的硅烷膜,所以,应尽量缩短工序间的间 隔时间。工序间的间隔时间若太短,工件存水处的积水,不能 完全有效的沥干,产生串槽现象,特别在喷淋方式时,会产生 相互喷射串槽,使槽液成分不易控制,甚至槽液遭到破坏。因 此在考虑工序间隔时,应根据工件几何尺寸,形状选择一个恰 当的工序间隔时间。
金属表面硅烷化处理工艺的优点
该种处理工艺优点主要包括: 在处理过程中不使用磷、没有有害的重金属离子; 工艺处理程序简单,所需时间短,容易控制; 处理中不需要加温,并且不会产生沉渣,槽液可循环使用; 可有效提高油漆与基材结合力; 能够共线处理多种基材,如铁、锌、铝等; 当前,硅烷化处理技术已经在欧美国家的普通工业中得以广泛
பைடு நூலகம்烷膜的防腐蚀性
耐腐蚀性是直接体现硅烷膜性能的主要特征之一,大量试验结 果表明:硅烷表面处理后不仅可有效提高基材耐蚀性能,而且 也大大提高了基材和涂层的结合能力,金属表面硅烷化处理工 艺技术可取代涂装前磷化及铬钝化处理。
影响金属表面硅烷膜的性能的因素
影响金属表面硅烷膜的性能的因素主要有:硅烷液浓度、硅烷 液 PH 值、硅烷偶联剂水解时间、金属基体在硅烷液的浸渍时 间、处理后的老化温度以及老化时间等。
溢流水清洗:提倡溢流水清洗,以保证工件充分清洗干净,减 少串槽现象。
应用。大大地改善了传统金属表面处理方式的处理效果。
硅烷处理对基体的一些要求
在金属表面硅烷化处理工艺中,金属基体的前处理是很重要的, 其处理效果对硅烷膜的质量以及后期涂装都会造成非常大的影 响。通常,金属表面硅烷化处理过程中必须要使用无磷脱脂剂 来清洗金属表面的油污或者其他杂质。然后用含有氢氧化钠稀 碱液清洗除油后的金属基体,最后再使用清水进行浸洗;并使 用纯水清洗工件之后才能使用硅烷处理液来处理。
金属表面处理环保新技术——硅烷化处理

金属表面处理环保新技术——硅烷化处理[摘要] 硅烷化处理是以有机硅烷水溶液为主要成分对金属或非金属材料进行表面处理的过程。
在涂装行业,涂装前的表面处理以磷化为主,硅烷化处理与传统磷化相比具有节能、环保和降低成本的优点。
本文简述了硅烷化处理的特点、基本原理、施工工艺等。
[关键词] 硅烷;表面处理;磷化硅烷化处理是以有机硅烷为主要原料对金属或非金属材料进行表面处理的过程。
硅烷化处理与传统磷化相比具有以下多个优点:无有害重金属离子,不含磷,无需加温。
硅烷处理过程不产生沉渣,处理时间短,控制简便。
处理步骤少,可省去表调工序,槽液可重复使用。
有效提高油漆对基材的附着力。
可共线处理铁板、镀锌板、铝板等多种基材0 基本原理硅烷含有两种不同化学官能团,一端能与无机材料(如玻璃纤维、硅酸盐、金属及其氧化物)表面的羟基反应生成共价键;另一端能与树脂生成共价键,从而使两种性质差别很大的材料结合起来,起到提高复合材料性能的作用。
硅烷化处理可描述为四步反应模型,(1)与硅相连的3个Si-OR基水解成Si-OH;(2)Si-OH之间脱水缩合成含Si-OH的低聚硅氧烷;(3)低聚物中的Si-OH与基材表面上的OH形成氢键;(4)加热固化过程中伴随脱水反应而与基材形成共价键连接,但在界面上硅烷的硅羟基与基材表面只有一个键合,剩下两个Si-OH或者与其他硅烷中的Si-OH缩合,或者游离状态。
为缩短处理剂现场使用所需熟化时间,硅烷处理剂在使用之前第一步是进行一定浓度的预水解。
①水解反应:在水解过程中,避免不了在硅烷间会发生缩合反应,生成低聚硅氧烷。
低聚硅氧烷过少,硅烷处理剂现场的熟化时间延长,影响生产效率;低聚硅氧烷过多,则使处理剂浑浊甚至沉淀,降低处理剂稳定性及影响处理质量。
②缩合反应:成膜反应是影响硅烷化质量的关键步骤,成膜反应进行的好坏直接影响涂膜耐蚀性及对漆膜的附着力。
因此,对于处理剂的PH值等参数控制显的尤为重要。
并且对于硅烷化前的工件表面状态提出了更高的要求:1、除油完全;2、进入硅烷槽的工件不能带有金属碎屑或其他杂质;3、硅烷化前处理最好采用去离子水。
金属表面硅烷处理技术
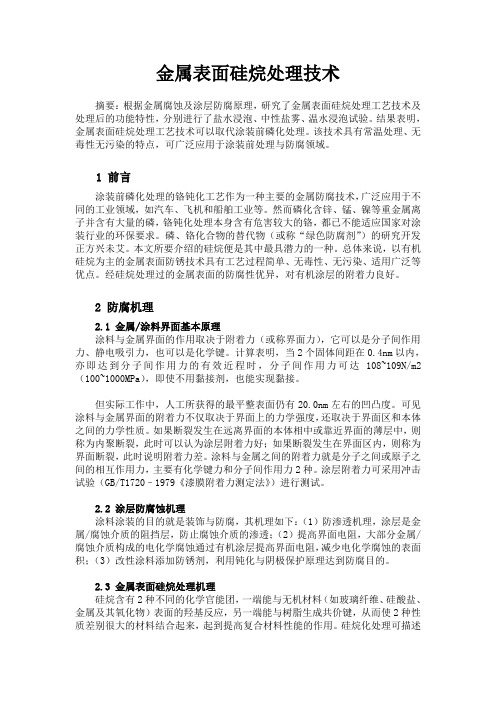
金属表面硅烷处理技术摘要:根据金属腐蚀及涂层防腐原理,研究了金属表面硅烷处理工艺技术及处理后的功能特性,分别进行了盐水浸泡、中性盐雾、温水浸泡试验。
结果表明,金属表面硅烷处理工艺技术可以取代涂装前磷化处理。
该技术具有常温处理、无毒性无污染的特点,可广泛应用于涂装前处理与防腐领域。
1 前言涂装前磷化处理的铬钝化工艺作为一种主要的金属防腐技术,广泛应用于不同的工业领域,如汽车、飞机和船舶工业等。
然而磷化含锌、锰、镍等重金属离子并含有大量的磷,铬钝化处理本身含有危害较大的铬,都已不能适应国家对涂装行业的环保要求。
磷、铬化合物的替代物(或称“绿色防腐剂”)的研究开发正方兴未艾。
本文所要介绍的硅烷便是其中最具潜力的一种。
总体来说,以有机硅烷为主的金属表面防锈技术具有工艺过程简单、无毒性、无污染、适用广泛等优点。
经硅烷处理过的金属表面的防腐性优异,对有机涂层的附着力良好。
2 防腐机理2.1 金属/涂料界面基本原理涂料与金属界面的作用取决于附着力(或称界面力),它可以是分子间作用力、静电吸引力,也可以是化学键。
计算表明,当2个固体间距在0.4nm以内,亦即达到分子间作用力的有效近程时,分子间作用力可达108~109N/m2(100~1000MPa),即使不用黏接剂,也能实现黏接。
但实际工作中,人工所获得的最平整表面仍有20.0nm左右的凹凸度。
可见涂料与金属界面的附着力不仅取决于界面上的力学强度,还取决于界面区和本体之间的力学性质。
如果断裂发生在远离界面的本体相中或靠近界面的薄层中,则称为内聚断裂,此时可以认为涂层附着力好;如果断裂发生在界面区内,则称为界面断裂,此时说明附着力差。
涂料与金属之间的附着力就是分子之间或原子之间的相互作用力,主要有化学键力和分子间作用力2种。
涂层附着力可采用冲击试验(GB/T1720–1979《漆膜附着力测定法》)进行测试。
2.2 涂层防腐蚀机理涂料涂装的目的就是装饰与防腐,其机理如下:(1)防渗透机理,涂层是金属/腐蚀介质的阻挡层,防止腐蚀介质的渗透;(2)提高界面电阻,大部分金属/腐蚀介质构成的电化学腐蚀通过有机涂层提高界面电阻,减少电化学腐蚀的表面积;(3)改性涂料添加防锈剂,利用钝化与阴极保护原理达到防腐目的。
zhongyao 胡吉明 金属表面硅烷化防护处理及其研究现状

定稿日期:2005204208基金项目:国家自然科学基金重大项目(50499336),国家自然科学基金(50571090)及浙江省自然科学基金(Y404295)作者简介:刘亻京,男,1986年生,在读研究生,研究方向为电化学与金属腐蚀与防护金属表面硅烷化防护处理及其研究现状刘 亻京1 胡吉明1 张鉴清1,2 曹楚南1,2(11浙江大学化学系杭州310027;21中国科学院金属研究所金属腐蚀与防护国家重点实验室沈阳110016)摘要:综述了一种新型的金属表面防护处理技术———硅烷化处理的研究现状.对硅烷膜的制备工艺、表征及膜覆盖电极的性能进行了详细介绍.文中也同时探讨了硅烷溶液的水解与失效问题,这两个基础问题的研究有助于了解金属表面硅烷膜的形成,并对制备工艺的优化起到决定性作用.最后还介绍了更具发展潜力的电沉积制备硅烷膜技术并提出了展望.关键词:硅烷 防腐蚀 工艺 水解与失效中图分类号:TG 178 文献标识码:A 文章编号:100524537(2006)01200592061前言传统的金属表面防护处理技术如铬酸盐钝化、磷酸盐转化等对环境并不友好,例如高价铬离子有很强的毒性、磷酸盐则是水体富营养化的元凶之一.随着环保呼声的高涨,迫切需要研发新型表面处理工艺,其中金属表面硅烷化处理所用试剂合成简单且对环境友好,是一种理想的表面防护处理技术.该技术利用硅烷试剂(通式为X -Si (OR )n ,其中X 代表官能团,R 为烷基,通常R 为-CH 3或-CH 2CH 3,n =2或3)水解生成硅醇(X -Si (OH )n ),硅醇与金属(Me )表面结合及自身交联在金属表面形成一层致密的保护膜,从而大幅度提高金属的耐蚀性.硅烷化处理过程主要经过以下反应[1,2]:硅烷水解:-Si —OR ′+H 2O →-Si -OH +R ′OH(1)硅醇在金属表面吸附:-Si —OH +Me -OH →Me —O —Si -+H 2O(2)硅醇在金属表面交联形成具有空间网状结构的保护膜:-Si —OH +HO —Si -→-Si —O -Si —+H 2O(3)表1列出了一些商用硅烷的结构及其用于金属表面防护处理技术的研究文献.可知,对不同硅烷处理各种不同金属及合金的工艺、一些工艺参数对处理件耐蚀性的影响[1~25]、金属表面硅烷膜的形成机理[26~30]和结构表征[1,4,6~11,19~21,26~32]等问题已有大量研究,而对硅烷试剂的水解与失效研究[2,31,33~42]虽已取得一些成果,但还有待于进一步探索.本文对上述问题及其研究现状将做详细介绍.2硅烷化处理工艺211常规制备工艺金属表面硅烷化处理的工艺流程较为简单.传统方法为配制一定浓度(硅烷、水、乙醇的比例)的硅烷溶液,在一定温度下水解数天后即可用于金属表面处理,处理时将金属片投入硅烷溶液,数秒后取出,然后再吹干、固化.近来文献报道的硅烷膜电沉积制备[12,13],是通过将金属片作为工作电极电解硅烷溶液从而实现硅烷在其表面吸附,其溶液制备和固化等工艺与传统方法相同.为获得单纯防护性的硅烷膜,一般选用无官能团的硅烷试剂(如B TSE 、B TSPS 等),而为了提高基体与有机涂层的结合力,常选用与涂层匹配的带特定官能团的硅烷(如对环氧系列涂层,一般选用γ-GPS 等),此功能性硅烷膜也可涂覆在非官能团硅烷膜上,该技术称为两步法成膜工艺(two -step ),得到的双层膜既有一定的耐蚀性,又与有机涂层有较好的结合力.近期又开发出了复合硅烷膜技术[11,14~16],实现一次性制备两类硅烷膜,结果显示复合膜的性能具有协同效应.此外,Que 等人[17,18]还研究了硅烷涂层与其他无机涂层的结合应用.值得一提的是,Van Ooij 研究组开发出在硅烷膜中复合纳米颗粒(SiO 2、Al 2O 3[25]等),以提高膜的耐蚀性与机械性能.第26卷第1期2006年2月 中国腐蚀与防护学报Journal of Chinese Society for Corrosion and ProtectionT able1Structure of some commercial silanessilane structure ref1 bis-1,2-[triethoxysilyl]ethane(BTSE)(H5C2O)3Si-CH2CH2-Si(OC2H5)3[1,3,4] bis-1,2-[trimethoxysilylpropyl]amine(BTSPA)(H5C2O)3Si-(CH2)3-NH-(CH2)3-Si(OC2H5)3[5] bis-1,2-[triethoxysilylpropyl]tetrasulfide(BTSPS)(H5C2O)3Si-(CH2)3-S4-(CH2)3-Si(OC2H5)3[5,6]γ-aminopropyltriethoxysilane(γ-APS)(H5C2O)3Si-(CH2)3-NH2[7]γ-ureidopropyltriethoxysilane(γ-U PS)(H5C2O)3Si-(CH2)3-NH-CO-NH2[8]γ-glycidoxypropyltrimethoxysilane(γ-GPS)CH2OCHCH2-O-(CH2)3-Si(OCH3)3[7,9] vinyltriethoxysilane(VS)(H5C2O)3Si-CH=CH2[8] methyltrimethoxysilane(MS)CH3-Si(OCH3)3[10] propyltrimethoxysilane(PS)CH3CH2CH2-Si(OCH3)3[11]21111制备工艺对硅烷膜性能的影响 从工艺流程看,影响金属表面硅烷化处理效果的主要因素包括硅烷种类、浓度、硅烷溶液p H值、溶剂成分、水解时间与温度,以及硅烷膜的固化温度、固化时间等.其中硅烷溶液p H值、溶剂成分、硅烷浓度、水解时间与温度主要与硅烷溶液的水解与失效反应有关,而固化温度和固化时间主要影响硅醇在金属表面的成膜.硅烷试剂的选择是金属表面硅烷化处理需要面对的首要问题,含不同官能团的硅烷处理金属可能.一般认为B TSE等无官能团硅烷膜对金属的保护效果较好,而APTMS等含有机官能团的硅烷膜能增强金属基体与有机涂层的结合力,适于和有机涂层结合使用[19].另外,同种硅烷试剂在不同金属表面的形成机制与性能也不尽相同.例如,研究发现B TSPS能显著提高铝及镁的耐蚀性,却不能用于镀锌钢铁的表面处理中[15].p H值主要通过影响硅烷溶液的水解与缩聚反应速率,进而影响硅烷膜的性能.较一致的认为酸性和碱性条件下均有利于硅烷的水解反应[33,35],而碱性条件似乎更能促进缩聚反应的进行[35].因此,合理的p H值选取应考虑抑制硅烷溶液缩聚反应的发生[3],同时使硅烷溶液有合适的水解速率.根据这一原则,摸索出了一些防护用硅烷溶液的最佳p H 值范围:B TSE(4~5)[4,19]、B TSPS(6~615)[24],对于功能性硅烷膜的制备p H值的适用范围则可以更宽一些,如γ-APS(4~11)[19],B TSPA(315~915)[5].另外在选取p H值时,还应考虑金属基体在溶液中的稳定性,例如对Al及Zn基金属而言,溶液p H值就不能太大.一般认为硅烷膜的厚度随硅烷溶液浓度升高而增大[20],从而提高处理件耐蚀性,然而硅烷浓度太高会促进硅烷溶液的絮凝而使其失效[21],因此需同时考虑处理件的耐蚀性和溶液的稳定性.水含量除了影响硅烷的水解与缩聚外,还影响其溶解性,而醇溶剂除了对硅烷分子起到助溶和分散作用外,还可抑制硅烷的水解,起到调节水解速率的作用.固化是金属表面硅烷处理工艺的一个重要环节,未经固化处理的硅烷膜几乎没有耐蚀性[1].与固化相关的工艺参数有固化温度和固化时间.一般认为固化温度太低所得硅烷膜结构疏松且含水较多,而固化温度过高则可能改变膜的交联状态,甚至导致在基体与硅烷膜间形成新的物相,使硅烷膜耐蚀性下降[21].Franquet等人[1]研究了固化时间对硅烷膜耐蚀性的影响,发现随着时间的延长,膜的厚度先减小后趋于不变,耐蚀性则先增加后趋于恒定.硅烷膜的性能是上述各因素共同作用的结果,研究各处理条件对硅烷膜结构性能的影响规律有助于得到更高效的硅烷化处理工艺,同时也为硅烷成膜机理和动力学研究提供有用的信息.21112硅烷膜的表征与防护机制 通过对硅烷膜进行表征得到膜的空间结构状态及硅醇分子在金属表面的吸附机制与成膜动力学,同时通过膜覆盖金属电极在腐蚀介质中耐蚀性及腐蚀行为的测试,进而得到硅烷膜的防护机制,是硅烷化处理中的重要研究内容.上述工作借助于一些表面分析与电化学测试来完成.Bertelsen等[9]测试了铝合金表面γ-GPS膜的反射红外光谱(RA IR)并对各谱峰对应的化学键进行了分析,指出硅烷膜中含有-OH、-CH2-、C=O、Si-OH、Si-O-Si等基团.徐溢等[32]也用同样方法研究了铝表面硅烷膜,提出硅烷与金属表面之间是以化学键结合,膜的厚度只在一定时间内增长,且膜的性能和固化温度有关.RA IR具有测试简06中国腐蚀与防护学报第26卷单、不破坏样品等优点,适于原位检测硅烷膜的变化,缺点是仅能给出某些化学键的半定量信息.通过X射线光电子能谱(XPS)谱峰对应的结合能可以确定一些基团,同时通过峰面积积分和相关计算又能定量得到硅醇在金属表面的表面分数(百分含量).Harun等[11]报道了经几种常用硅烷处理的钢材表面XPS测试中结合能与基团的关系并对峰面积作了积分.Abel等[7]研究了硅烷在铝表面的吸附,并根据XPS测量结果提出溶剂中水含量减少会降低硅烷在铝表面的有效吸附,以及各种硅烷膜漂洗方法对膜厚度的影响.Subramanian等[19]利用RA IR、XPS等方法研究了氨基对铁表面硅烷膜形成的影响,提出硅烷膜表面存在-N H+3会吸引具有侵蚀性的Cl-,且使膜的导电性增加,会降低膜的耐蚀性.椭圆光谱(SE)和红外椭圆光谱(IRSE)技术是研究硅烷膜厚度十分有效的方法.Franquet 等[1,4,20,32]分别利用SE和IRSE研究了硅烷溶液浓度、p H值、温度以及金属在硅烷溶液中的浸泡时间、固化等因素对硅烷膜厚度的影响并对两种方法的结果作了对比.IRSE的优点是能同时得到膜的化学结构和形态信息.飞行时间———二次离子质谱(TOF-SIMS)是一种新型表面分析技术,目前应用于硅醇与金属的吸附成膜研究.Bexell等[26]用该技术研究了B TSE 膜的表征,提出硅烷膜最外层结构取决于金属基体的种类,当有醇作溶剂时,醇上的烷氧基会与硅烷上的烷氧基发生相互取代,B TSE在金属表面形成一层连续的膜,-OH、-OC2H5基团朝外,其缩合主要经过1~3个Si-O-Si桥,也有分子内缩合发生.他们还研究了γ-MPS和B TSE两步处理Al、Zn 等金属和合金,发现两步处理后膜的厚度反而小于单一B TSE膜,且γ-MPS完全覆盖在B TSE表面[27].Quinton等[28~30]结合XPS和TOF-SIMS 测试发现了硅醇在Al、Fe表面的吸附不是单向过程,而是振荡变化的.他们提出了硅烷在金属表面可能的吸附机理,并观察到浸泡时间30s~35s时,γ-APS质子化的氨基在金属表面的吸附所占比例最高.TOF-SIMS能测量体系中各原子浓度随时间的变化,适于研究硅醇的吸附成膜动力学等.电化学方法是研究材料腐蚀和失效的最常用方法,目前研究硅烷膜的电化学方法主要有极化曲线和电化学阻抗谱等技术[6,10,21].极化曲线测试表明硅烷膜在金属表面仅起到物理阻挡层的作用而并未改变金属腐蚀的电极过程动力学[21,24].而电化学阻抗谱测试则可为研究硅烷膜耐腐蚀机理提供信息,同时还可为硅烷膜的耐蚀性提供无损、定量的评价方法.Van Ooij等[6]提出了硅烷膜在金属表面吸附的三种可能结构并提出了相应的电化学阻抗谱模型,认为硅醇可能在金属自身氧化膜表面形成多孔的膜,也可能在硅烷膜与金属氧化膜之间还存在一个“未知相(unknown phase)”.本研究组认为该未知相可能是测试介质中侵蚀性Cl-在多孔硅烷膜下与基体形成的盐膜层,并根据实验结果提出了相应的等效电路模型[21].212硅烷膜的电化学沉积制备传统的硅烷膜制备一般采用浸涂的方法,即将金属试样浸泡于经一定时间水解后的硅烷/水/醇溶液中,几十秒至几十分钟后取出吹干,再经一定温度一定时间固化即可.硅烷膜的电化学辅助制备则是金属试样在硅烷溶液浸泡过程中,在其表面施加一定的电位,从而提高硅烷膜的耐蚀性.1999年,Mandler等人[12]用电化学辅助技术在导电玻璃及金表面成功沉积了甲基三甲氧基硅烷(MS),2003年他们研究组又将该技术用于铝表面的防护处理[13],结果显示采用电化学辅助沉积制备的硅烷膜耐蚀性较传统浸涂法有显著提高.遗憾的是,上述工作中研究者们选取的硅烷种类[四甲氧基硅烷(TEOS)、苯基三甲氧基硅烷(PTMS)等]并不是常见的防护用硅烷试剂.最近,我们首次通过电化学辅助技术在铝合金表面制备了一系列金属表面防护常用的硅烷膜[22,23].Mandler等人[12,13]认为,在金属表面施加阴极电位后电极表面局部溶液的p H值升高,有利于硅醇缩聚反应的进行,从而促进硅醇在金属表面缩聚形成交联聚合产物[-Si-O-Si-]n,提高了金属的耐蚀性,由于其改变的只是金属表面小部分溶液的p H值,因而不会影响本体溶液的稳定性,克服了处理液p H值升高导致其产生絮凝而失效的缺点.最近,我们研究了电化学技术在铝合金表面制备B TSE硅烷膜工艺,发现在阴极电位下沉积得到该种膜的耐蚀性得到明显提高,而在阳极电位下沉积后合金的耐蚀性甚至比未沉积硅烷膜的裸基体还差.得到了B TSE在铝合金表面沉积的最佳电位为-018V(vs SCE),且在沉积过程中电极的电化学行为具有振荡现象[22].作为金属表面硅烷化处理的一种新技术,硅烷膜的电化学辅助制备具有重要的学术价值和应用前景.首先,通过对沉积过程电化学参数的在线监测及硅烷膜的表征,可以更深入的探讨电化学辅助沉积机理,如施加电位及改变电位波形对硅烷膜结构及耐蚀性的影响等.其次,通过膜耐蚀性测试及与有机涂层结合力测试,可以对制备工艺中溶液参数与电化学参数进行优化,得到性能更好的硅烷膜.此外,传统浸涂工艺很难对硅烷膜的结构性能进行控制,而通过对沉积过程电化学参数的调节,则可以实现硅烷膜的可控制备.目前对电化学辅助沉积硅烷膜的研究报道还较少.3硅烷试剂的水解与失效硅烷水解生成硅醇是其在金属表面成膜的前提,处理金属时溶液中硅醇的浓度将直接影响处理件的耐蚀性[20].硅烷的失效则是其应用的一大障碍,实验发现一般硅烷水溶液体系在数天内即发生肉眼能见的絮凝,某些甚至仅能稳定一天.促进水解并尽可能减少失效是研究者们所希望的.对硅烷的水解与失效机制研究主要集中在近些年,并取得了一些进展.311硅烷的水解用于金属表面防护处理的硅烷一般含有三个烷氧基(如γ-APS、B TSE),研究表明该类硅烷试剂的水解一般分步进行,其水解基元反应如下[33]: R-Si(OR′)3+H2O→R-Si(OH)(OR′)2(4)R-Si(OH)(OR′)2+H2O→R-Si(OH)2(OR′)(5)R-Si(OH)2(OR′)+H2O→R-Si(OH)3(6)Satoshi等[35]用量子计算的方法研究了三烷氧基硅烷的水解反应,提出了各水解产物的结构模型和结构参数.他们还提出了酸和碱对三烷氧基硅烷水解的影响机理及相应的水解产物结构的改变.由于硅烷的水解过程需要一定时间,围绕其动力学的研究便十分重要.而硅烷水解动力学研究的关键问题则是各中间产物的实时定量检测,对此人们尝试了一些现代仪器分析方法并取得了一些成果,表2列出了硅烷水解的一些研究方法.T able2S ome techniques used for silane hydrolysis investigation techniques silanes ref1 FTIR TEOS[36] FT-Raman Spectroscopyγ-GPS、γ-APS[37] NMRγ-GPS[9,34]γ-GPS、γ-APS、3-methacry2loxypropyltrimethoxy silane[2]LC-ICP-AESγ-GPS、γ-APS[33] 以上方法中,较为成功的是K ozerski等人采用的LC-ICP-AES联用技术[33].由于液相色谱C18反相柱能很好的分离硅烷水解的各中间产物,而等离子体原子发射光谱检测器则能对其进行良好的定量分析.他们测定了p H值在6197~9100、一定离子强度下γ-APS和γ-GPS水解中间产物浓度随时间的变化,并用非线性回归方法拟合得到了相应条件下各基元反应的反应速率常数(k).其结果证明硅烷的水解是单向连续反应且第一步反应为速度控制步骤(RDS).312硅烷的失效硅烷的失效是硅烷水解产生硅醇的副反应,它消耗了溶液中的硅醇,因此硅烷用于表面处理时应尽量避免失效的发生.一般认为硅烷的失效主要包含酯化、缩合和去质子化,其反应方程式如下[39]:酯化(esterification):-Si-OH+ROH→-Si-OR+H2O(7)缩合(condensation):-Si-OH+HO-Si-→-Si-O-Si-+H2O(8)去质子化(deprotonation):-Si-OH+OH-→SiO-+H2O(9)如何控制合理的水解时间使得硅烷溶液中-Si-OH含量最高,以及如何降低硅烷的失效以提高硅烷试剂的利用率受到了广泛关注.然而目前对硅烷失效的研究还只局限于单羟基硅醇及2~3个多羟基硅醇(表3).例如,Λef ík 等[39]用29Si-NMR的方法研究了Me3SiOH在碱性乙醇-水溶液中的酯化、缩合和去质子化反应并得到了Me3SiOH在该条件下的酯化、缩合反应平衡常数,且指出了它们随体系中水的摩尔分数的变化规律.Satoshi等[35]用量子计算的方法研究了三羟基硅醇的缩合机理,提出了一水缩合、二水缩合及相应的反应物和产物分子结构的变化.Britt等[38]则研究了硅烷在空气-水界面上的水解与缩合.Beari 等[2]研究了三烷氧基硅烷在稀的水溶液中的三分子缩合动力学.他们利用1H-NMR和29Si-NMR 的方法,根据化学位移不同对体系中各物质进行定性,根据峰面积计算出它们的相对含量并观察了各物质含量随时间的变化,但没有得到相关反应动力学参数.总体来看,对硅醇酯化、缩合等反应的热力学研究已较完善,而相应的动力学研究较少,对硅醇缩聚及其在空间的交联等方面的研究则几乎是空白.还应该看到,对硅烷的失效研究仅停留在理论阶段.正T able3Previous works on esterification,condensation and de2 protonation reactions of silanolsreaction type solutions ref1 esterification four-functional silanols+ethanol[40]monofunctional silanols+alcohols+dioxane[41] condensation monofunctional alkoxysilanes+alcohols+H+[42]monofunctional silanols+dioxane+H+/OH-[43] deprotonation triphenylsilanol+H2O[44]因为如此,还未提出抑制(或减缓)硅烷水溶液失效的有效办法.徐溢等[31]尝试采用在硅烷溶液中加入多羟基醇(如乙二醇、丙三醇等)以提高溶液的稳定性,但制得硅烷膜的性能如何却不得而知.4展望在硅烷化处理工艺方面,人们正在探索进一步提高处理效果的方法,新的处理方法如硅烷电沉积等将是未来研究的一个热点.另外在硅烷溶液中加入添加剂、硅烷复合涂层以及硅烷化处理与其他金属表面处理方法结合使用也是金属表面硅烷化处理研究的新方向.同时,硅烷的水解与失效等基础问题也受到人们的关注.在水解动力学研究方面,电化学分析是实现在线检测的最理想方法,其具有设备简单、数据采集方便、易实现与计算机的连接等优点.如果能建立一套硅烷水解的电化学检测方法,有望得到硅烷在各种条件下的水解动力学信息.另外高效的硅烷水解催化剂和失效抑制剂的开发也将是硅烷化处理走向工业应用的关键所在.参考文献:[1]Franquet A,Le Pen C,Terryn H.Effect of bath concentration andcuring time on the structure of non-functional thin organosilane layers on aluminium[J].Electrochim.Acta,2003,48:1245[2]Beari F,Brand M,Jenkner anofunctional alkoxysilanes in di2lute aqueous solution:new accounts on the dynamic structural muta2 bility[J]anomet.Chem.,2001,625:208[3]Subramanian V,Van Ooij W J.Silane based metal pretreatments asalternatives to chromating[J].Surf.Eng.,1999,15:168[4]Franquet A,J De Laet,Schram T.Determination of the thickness ofthin silane films on aluminium surfaces by means of spectroscopic ellipsometry[J].Thin Solid Films,2001,384:37[5]Sundararajan G P,Van Ooij W J.Silane based pretreatments for au2tomotive steels[J].Surf.Eng.,2000,16:315[6]Van Ooij W J,Zhu D.Electrochemical impedance spectroscopy ofbis-[triethoxysilylpropyl]tetrasulfide on Al2024-T3substrates [J].Corrosion,2001,57:413[7]Abel M,Watts J F,Digby R P.The adsorption of alkoxysilanes onoxidised aluminium substrates[J].Inter.J.Adhes.&Adhes., 1998,18:179[8]Van Ooij W J,Zhu D,Prasad G.Silane based chromate replace2ments for corrosion control,paint adhesion,and rubber bonding[J].Surf.Eng.,2000,16:386[9]Bertelsen C M,Boerio F J.Linking mechanical properties of silanesto their chemical structure:an analytical study ofγ-APS solutions and films[J].Coat.,2001,41:239[10]Tang N,Van Ooij W J,Górecki parative EIS study of pre2treatment performance in coated metals[J].Coat., 1997,30:255[11]Harun M K,Lyon S B,Marsh J A.Surface analytical study of func2tionalised mild steel for adhesion promotion of organic coatings[J]..Coat.,2003,46:21[12]Shacham R,Avnir D,Mandler D.Electrodeposition of methylatedsol-gel films on conducting surfaces[J].Adv.Mater.,1999,11: 384[13]Sheffer M,Groysman A,Mandler D.Electrodeposition of sol-gelfilms on Al for corrosion protection[J].Corros.Sci.,2003,45: 2893[14]Conde A,Durán A,De Damborenea J J.Polymeric sol-gel coat2ings as protective layers of aluminium alloys[J].Coat., 2003,46:288[15]Zhu D,Van Ooij W J.Enhanced corrosion resistance of AA2024-T3and hot-dip galvanized steel using a mixture of bis-[tri2 ethoxysilylpropyl]tetrasulfide and bis-[trimethoxysilylpropyl] amine[J].Electrochim.Acta,2004,49:1113[16]Zhu D,Van Ooij W J.Corrosion protection of metals by water-based silane mixtures of bis-[trimethoxysilylpropyl]amine and vinyltriacetoxysilane[J].Coat.,2004,49:42[17]Que W X,Sun Z,Zhou Y.Preparation of hard optical coatingsbased on an organic/inorganic composite by sol-gel method[J].Mater.Lett.,2000,42:326[18]Que W X,Zhang Q Y,Chan Y C.Sol-gel derived hard opticalcoatings via organic/inorganic composites[J].Compos.Sci.Tech2 nol.,2003,63:347[19]Subramanian V,Van Ooij W J.Effect of amine functional group oncorrosion rate of iron coated with films of organofunctional silanes [J].Corrosion,1998,54:204[20]Franquet A,Terryn H,Vereecken position and thickness ofnon-functional organosilane films coated on aluminium studied by means of infra-red spectroscopic ellipsometry[J].Thin Solid Films,2003,441:76[21]Hu J M,Liu L,Zhang J T.Studies of protective treatment on alu2minium alloys by BTSE silane agent[J].Acta Metall.Sin.,2004, 40:1189(胡吉明,刘亻京,张金涛.铝合金表面BTSE硅烷化处理研究[J].金属学报,2004,40:1189)[22]Hu J M,Liu L,Zhang J Q.Effects of electrodeposition potential onthe corrosion properties of bis-1,2-[triethoxysilyl]ethane films on aluminum alloy[J].Electrochim.Acta,in press[23]Hu J M,Liu L,Zhang J Q.Studies of electrodeposition and corro2361期刘 亻京等:金属表面硅烷化防护处理及其研究现状 sion protection of DTMS films on aluminum alloys[J].Chem.J.Chin.U.,in press(胡吉明,刘亻京,张鉴清.铝合金表面电化学沉积制备DTMS硅烷膜及其耐蚀性研究[J].高等学校化学学报,待发表)[24]Zhu D,Van Ooij W J.Corrosion protection of AA2024-T3by bis-[3-(triethoxysilyl)propyl]tetrasulfide in neutral sodium chlo2 ride solution.Part1:corrosion of AA2024-T3[J].Corros.Sci., 2003,45:2177[25]Palanivel V,Zhu D,Van Ooij W J.Nanoparticle-filled silane filmsas chromate replacements for aluminium alloys[J].Coat.,2003,47:384[26]Bexell U,Olsson M.Characterization of a non-organofunctionalsilane film deposited on Al,Zn and Al-43.4Zn-1.6Si alloy-coated steel[J].Surf.Interface Anal.,2001,31:212[27]Bexell U,Olsson M.Time-of-flight SIMS characterization ofhydrolysed organofunctional and non-organofunctional silanes de2 posited on Al,Zn and Al-43.4Zn-1.6Si alloy-coated steel[J].Surf.Interface Anal.,2003,35:880[28]Quinton J S,Dastoor P C.Modelling the observed oscillations inthe adsorption kinetics of propyltrimethoxysilane on iron and alu2 minium oxide surfaces[J].Surf.Interface Anal.,2000,30:25 [29]Quinton J S,Dastoor P C.Conformational dynamics ofγ-APS onthe iron oxide surface:an adsorption kinetic study using XPS and T of-SIMS[J].Surf.Interface Anal.,2000,30:21[30]Quinton J S,Thomsen L,Dastoor P C.Adsorption of organosilaneson iron and aluminium oxide surfaces[J].Surf.Interface Anal., 1997,25:931[31]Xu Y,Tang S Y,Teng Y.Hydrolysis and condensation of silane a2gent for metallic surface treatment[J].J.Chongqing University, 2002,25(10):72(徐溢,唐守渊,滕毅.金属表面处理用硅烷试剂的水解与缩聚[J].重庆大学学报,2002,25(10):72)[32]Franquet A,Terryn H,Bertrand e of optical methods to char2acterize thin silane films coated on aluminium[J].Surf.Interface Anal.,2002,34:25[33]K ozerski G E,G allavan R H,Z iemelis M J.Investigation of tri2alkoxysilane hydrolysis kinetics using liquid chromatography with inductively coupled plasma atomic emission spectrometric detection and non-linear regression modeling[J].Anal.Chim.Acta,2003, 489:103[34]Cunliffe A V,Evans S,Tod D A.Optimum preparation of silanesfor steel pre-treatment[J].Adhesion&Adhesives,2001,21:287 [35]Satoshi O,Naokatsu F.Theoretical study of hydrolysis and conden2sation of silicon alkoxides[J].J.Phys.Chem.A,1998,102:3991 [36]Tejedor-Tejedor M I,Paredes L,Anderson M A.Evaluation ofATR-FTIR spectroscopy as an”in situ”tool for following the hydrolysis and condensation of alkoxysilanes under rich H2O condi2 tions[J].Chem.Mater.,1998,10:3410[37]Riegel B,Blittersdorf S,K iefer W.K inetic investigations of hydrol2ysis and condensation of the glycidoxypropyltrimethoxysilane/ aminopropyltriethoxy-silane system by means of FT-Raman spectroscopy[J].J.Non-cryst.Solids,1998,226:76[38]Britt D W,Hlady V.Protonation,hydrolysis and condensation ofmono-and trifunctional silanes at the air/water interface[J].Langmuir,1999,15:1770[39]Λef ík J,Rankin S E,K irchner S J.Esterfication,condensation anddeprotonation equilibria of trimethylsilanol[J].J.Non-cryst.Solids,1999,258:187[40]Λef ík J,McCormick A V.K inetic and thermodynamic issues in theearly stages of sol-gel processes using silicon alkoxides[J].Catal.Today.,1997,35:205[41]K ohlheim I,Lange D,K elling H.On the reaction of silanols withalcohols[J].J.Prakt Chem.Chem.Z,1996,338:660[42]Grubb W T.Rate study of the silanol condensation reaction at25℃in alcoholic solvents[J].J.Am.Chem.Soc.,1954,76:3408 [43]Bilda S,Rohr G,Lange D.On the condensation behavior ofsilanols.Ⅴ.Base catalyzed condensation of organodimethylsilanols in dioxane/water[J].Z.Anorg.Allg.Chem.,1988,564:155 [44]West R,Baney R H.Hydrogen-bonding studiesⅡ.Acidity andbasicity of silanols compared to alcohols[J].J.Am.Chem.Soc., 1959,81:6145PR OGRESS IN ANTI-CORR OSIVE TREATMENT OF METALS B Y SI LANIZATIONL IU Liang1,HU Jiming1,ZHAN G Jianqing1,2,CAO Chu’nan1,2(1.Depart ment of Chemist ry,Zhejiang U niversity,Hangz hou310027;2.State Key L aboratory f or Corro sion and Protection,Institute of Metal Research,The Chinese Academy of Sciences,S henyang110016)Abstract:A novel protective surface treatment of metals by silanization is reviewed.Studies on preparation and characterization of silane films,the performance of silanized electrodes was presented.Two fundamental prob2 lems—hydrolysis and failure of silane solution,which can help us get insight in the properties of silane film on metal substrates and have crucial effect on optimizing the preparation of it,are discussed as well.The more promising electrodeposition of silane films and prospects are also presented.K ey w ords:silane,corrosion protection,processes,hydrolysis,failure46中国腐蚀与防护学报第26卷。
金属硅烷前处理技术
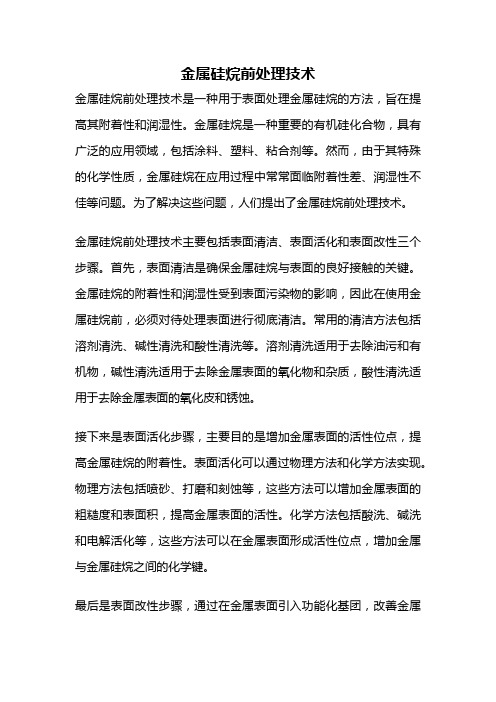
金属硅烷前处理技术金属硅烷前处理技术是一种用于表面处理金属硅烷的方法,旨在提高其附着性和润湿性。
金属硅烷是一种重要的有机硅化合物,具有广泛的应用领域,包括涂料、塑料、粘合剂等。
然而,由于其特殊的化学性质,金属硅烷在应用过程中常常面临附着性差、润湿性不佳等问题。
为了解决这些问题,人们提出了金属硅烷前处理技术。
金属硅烷前处理技术主要包括表面清洁、表面活化和表面改性三个步骤。
首先,表面清洁是确保金属硅烷与表面的良好接触的关键。
金属硅烷的附着性和润湿性受到表面污染物的影响,因此在使用金属硅烷前,必须对待处理表面进行彻底清洁。
常用的清洁方法包括溶剂清洗、碱性清洗和酸性清洗等。
溶剂清洗适用于去除油污和有机物,碱性清洗适用于去除金属表面的氧化物和杂质,酸性清洗适用于去除金属表面的氧化皮和锈蚀。
接下来是表面活化步骤,主要目的是增加金属表面的活性位点,提高金属硅烷的附着性。
表面活化可以通过物理方法和化学方法实现。
物理方法包括喷砂、打磨和刻蚀等,这些方法可以增加金属表面的粗糙度和表面积,提高金属表面的活性。
化学方法包括酸洗、碱洗和电解活化等,这些方法可以在金属表面形成活性位点,增加金属与金属硅烷之间的化学键。
最后是表面改性步骤,通过在金属表面引入功能化基团,改善金属硅烷的附着性和润湿性。
表面改性可以采用化学改性、物理改性和光化学改性等方法。
化学改性是将化学物质与金属表面反应,形成化学键,改善金属硅烷的附着性和润湿性。
物理改性是通过物理方法在金属表面形成微纳米结构,增加金属表面的粗糙度和表面积,提高金属硅烷的附着性和润湿性。
光化学改性是利用光化学反应在金属表面形成活性位点,提高金属硅烷的附着性和润湿性。
金属硅烷前处理技术是一种用于提高金属硅烷附着性和润湿性的方法。
通过表面清洁、表面活化和表面改性三个步骤,可以有效地改善金属硅烷的应用性能。
在实际应用中,根据具体的金属硅烷种类和应用需求,可以选择合适的前处理方法和工艺参数。
- 1、下载文档前请自行甄别文档内容的完整性,平台不提供额外的编辑、内容补充、找答案等附加服务。
- 2、"仅部分预览"的文档,不可在线预览部分如存在完整性等问题,可反馈申请退款(可完整预览的文档不适用该条件!)。
- 3、如文档侵犯您的权益,请联系客服反馈,我们会尽快为您处理(人工客服工作时间:9:00-18:30)。
金属表面处理锆化硅烷
全文共四篇示例,供读者参考
第一篇示例:
金属表面处理一直是工业生产中非常重要的一环。
金属产品在使用过程中,会因为各种原因容易受到腐蚀和氧化等影响,降低其使用寿命,影响产品的质量和美观度。
金属表面处理技术的发展就显得尤为重要。
在金属表面处理技术中,锆化和硅烷被广泛应用。
锆化是一种将锆与金属表面反应生成锆化合物的化学处理方法,通过锆化可以提高金属的耐蚀性和耐磨性,进而延长金属产品的使用寿命。
而硅烷是一种表面活性剂,可以在金属表面形成一层亲水薄膜,提高金属的防腐蚀能力和降低摩擦系数。
锆化和硅烷在金属表面处理中的应用,不仅可以提高金属产品的质量,延长其使用寿命,还可以降低生产成本,提高生产效率。
下面我们就来详细了解一下这两种金属表面处理技术的原理和应用。
锆化技术的应用范围很广泛,适用于各种金属产品,包括钢铁、铝合金、铜合金等。
通过锆化处理,可以降低金属产品的摩擦系数,改善表面光洁度,增加防腐蚀能力,提高产品的抗腐蚀性和耐磨性,减少产品的维护成本,延长使用寿命。
锆化和硅烷是金属表面处理中非常重要的两种技术。
它们可以有
效提高金属产品的质量,延长其使用寿命,降低生产成本,提高生产
效率。
在金属制造行业中,锆化和硅烷技术都具有非常重要的应用价值,值得进一步推广和研究。
希望通过本文的介绍,能够增加大家对
金属表面处理技术的了解,促进相关技术的进一步发展和应用。
【字数达到2004字】
第二篇示例:
金属表面处理是一种常见的工艺,可以提高金属材料的表面性能,延长金属材料的使用寿命。
在金属表面处理中,锆化和硅烷是两种常
用的处理方法。
本文将着重介绍这两种方法的原理、特点和应用。
一、锆化
锆化是一种将锆元素镀覆在金属表面的工艺。
锆元素具有很高的
化学稳定性和硬度,能够有效保护金属表面不受氧化、腐蚀和磨损。
锆化处理后的金属表面具有优良的耐蚀性、耐磨性和耐高温性能,能
够延长金属材料的使用寿命。
锆化的原理是利用锆元素与金属表面形成一层坚固的保护层,阻
止金属表面与外界物质接触,从而达到保护金属表面的作用。
锆化处
理一般通过电镀、喷涂、热浸等方法进行,根据不同金属材料的要求
选择不同的锆化工艺。
锆化处理适用于各种金属材料,如钢铁、铜、铝等。
在航空航天、汽车制造、电子器件等领域广泛应用。
锆化处理可以有效保护金属表
面不受氧化、腐蚀和磨损,提高金属材料的耐用性和稳定性。
二、硅烷
第三篇示例:
金属表面处理是一项重要的工艺,可以有效提高金属制品的表面
硬度、耐腐蚀性和耐磨性,延长其使用寿命。
在金属表面处理技术中,锆化和硅烷是常用的方法之一。
本文将重点介绍这两种金属表面处理
方法,并探讨其应用范围和优缺点。
一、锆化技术
锆化是一种将锆元素镀覆在金属表面形成保护膜的表面处理技术。
锆属于稀有金属,具有较高的化学稳定性和耐腐蚀性,可以有效保护
金属表面免受氧化、腐蚀和磨损的影响。
锆化技术广泛应用于航空航天、汽车、电子、化工等领域,可以提高金属制品的使用寿命和性
能。
锆化技术的优点有:
1. 耐高温:锆化膜可以在高温条件下保持稳定,不易被氧化、变
色或剥落。
2. 耐腐蚀:锆化膜具有良好的耐蚀性,可以有效防止金属表面遭
受化学腐蚀。
3. 提高硬度:锆化膜可以增加金属表面的硬度,提高耐磨性和耐刮擦性。
4. 环保:锆化过程中不会产生有害物质,对环境友好。
锆化技术的缺点是:
1. 费用较高:锆是一种稀有金属,锆化技术的成本较高。
2. 技术要求高:锆化技术需要严格控制温度、时间和溶液浓度等参数,操作难度较大。
二、硅烷技术
硅烷技术的优点有:
1. 耐磨性:硅烷膜具有较强的耐磨性,可以延长金属制品的使用寿命。
2. 耐蚀性:硅烷膜具有良好的耐蚀性,可以有效防止金属表面遭受化学腐蚀。
3. 防污性:硅烷膜具有一定的抗污染功能,可以减少金属表面的清洁频率。
4. 显色效果:硅烷膜可以提高金属表面的光泽度,使其具有更好的装饰效果。
硅烷技术的缺点是:
1. 耐温性差:硅烷膜在高温条件下容易失效,限制了其应用范围。
2. 涂覆厚度难控制:硅烷技术涂覆的薄膜厚度难以控制,影响了
其抗磨损性能。
锆化和硅烷是两种常用的金属表面处理技术,具有各自的优点和
缺点。
在选择金属表面处理方法时,应根据具体应用场景和要求进行
综合考虑,选择最适合的技术。
随着科技的不断发展,金属表面处理
技术也在不断创新和进步,相信未来会有更多更先进的技术出现,为
金属制品的表面处理提供更多选择。
第四篇示例:
金属表面处理是一种常见的工业技术,它可以改善金属的表面性能,增强其耐腐蚀性、耐磨性和美观度。
在金属表面处理技术中,锆
化和硅烷处理是两种常用的方法,它们在不同场合下发挥着重要作
用。
锆化是一种表面处理技术,它通过在金属表面形成锆化层来提高
金属的耐蚀性和耐磨性。
锆金属在常温下是一种具有良好耐腐蚀性的
金属,它可以与铁、铬等金属形成亲和力很大的合金。
在金属表面进
行锆化处理可以有效地提高金属的耐腐蚀性能。
锆化层的硬度也很高,可以增强金属的耐磨性,延长金属的使用寿命。
锆化还可以提高金属
的美观度,使金属表面更加光滑、均匀。
在一些对表面质量要求较高
的场合下,锆化处理是一种很有必要的金属表面处理方法。
硅烷是一种表面处理剂,它可以在金属表面形成一层硅含量较高的保护层,起到保护金属的作用。
硅烷主要是通过在金属表面生成硅氢键,形成硅氢键保护膜,从而降低金属的活性,抑制金属的腐蚀。
硅烷还可以提高金属表面的亲水性,减少水分子在金属表面的吸附,从而降低金属表面的腐蚀速度。
硅烷的保护层还可以起到减摩减磨的作用,延长金属的使用寿命。
在一些外界条件较恶劣的场合下,如高温、高湿、高盐等环境中,硅烷处理可以有效地提高金属的抗腐蚀性能,保护金属不受腐蚀损伤。
在实际应用中,锆化和硅烷处理通常结合使用,以达到更好的效果。
首先进行锆化处理,形成一层锆化层提高金属的耐腐蚀性和耐磨性,然后再进行硅烷处理,形成一层硅氢键保护膜,提高金属表面的抗腐蚀性能。
这样就可以同时起到保护金属、增强金属耐磨性和延长金属使用寿命的作用。
在一些对金属要求较高的领域,如航空航天、汽车制造、电子设备等行业中,锆化和硅烷处理已经成为一种不可或缺的金属表面处理技术。