硅烷化处理
橡胶硅烷化处理

橡胶硅烷化处理橡胶硅烷化处理是一种常见的橡胶表面改性方法,通过在橡胶表面引入硅烷基团,可以改善橡胶的表面性能和界面亲和性。
本文将从橡胶硅烷化处理的原理、方法和应用等方面进行探讨。
一、橡胶硅烷化处理的原理橡胶硅烷化处理的原理是通过将含有硅烷基团的硅烷化剂与橡胶表面发生反应,形成化学键连接。
硅烷化剂通常包括有机硅化合物,如氨基硅烷、甲基硅烷等。
这些硅烷化剂具有活性氨基、羟基或甲基等官能团,能够与橡胶表面的活性基团发生反应,形成硅烷键。
橡胶硅烷化处理的方法主要包括溶液法、热固化法和辐射法等。
其中,溶液法是最常用的方法。
具体操作步骤如下:1. 将硅烷化剂与溶剂按一定比例混合,并加热搅拌使其溶解均匀;2. 将橡胶制品浸泡在硅烷化剂溶液中,保持一定的时间,使硅烷化剂能够与橡胶表面反应;3. 取出橡胶制品,进行干燥和固化处理,使硅烷化剂与橡胶表面形成牢固的化学键。
三、橡胶硅烷化处理的应用橡胶硅烷化处理可以改善橡胶的表面性能和界面亲和性,使其在各种应用领域中发挥更好的性能。
具体应用如下:1. 橡胶粘接剂:橡胶硅烷化处理可以提高橡胶与其他材料的粘接强度,使橡胶粘接剂在汽车、航空航天等领域中得到广泛应用。
2. 橡胶填料:橡胶硅烷化处理可以增强橡胶填料与基体材料的界面结合力,提高填料的分散性和增强效果。
3. 橡胶改性剂:橡胶硅烷化处理可以改善橡胶的热稳定性、耐磨性和耐候性,提高其机械性能和使用寿命。
4. 橡胶涂层:橡胶硅烷化处理可以提高橡胶涂层的附着力和耐化学品性能,广泛应用于建筑、船舶、家电等领域。
5. 橡胶填充剂:橡胶硅烷化处理可以提高橡胶填充剂的分散性和增强效果,使其在橡胶制品中得到更好的应用。
橡胶硅烷化处理是一种有效的橡胶表面改性方法,通过引入硅烷基团,可以改善橡胶的表面性能和界面亲和性。
其原理是通过硅烷化剂与橡胶表面发生化学键连接,方法主要包括溶液法、热固化法和辐射法等。
橡胶硅烷化处理的应用广泛,包括橡胶粘接剂、橡胶填料、橡胶改性剂、橡胶涂层和橡胶填充剂等。
硅烷化处理

金属表面处理环保新技术——硅烷化处理硅烷化处理是以有机硅烷水溶液为主要成分对金属或非金属材料进行表面处理的过程。
在涂装行业,涂装前的表面处理以磷化为主,硅烷化处理与传统磷化相比具有节能、环保和降低成本的优点。
本文简述了硅烷化处理的特点、基本原理、施工工艺等。
[关键词] 硅烷;表面处理;磷化硅烷化处理是以有机硅烷为主要原料对金属或非金属材料进行表面处理的过程。
硅烷化处理与传统磷化相比具有以下多个优点:无有害重金属离子,不含磷,无需加温。
硅烷处理过程不产生沉渣,处理时间短,控制简便。
处理步骤少,可省去表调工序,槽液可重复使用。
有效提高油漆对基材的附着力。
可共线处理铁板、镀锌板、铝板等多种基材0 基本原理硅烷含有两种不同化学官能团,一端能与无机材料(如玻璃纤维、硅酸盐、金属及其氧化物)表面的羟基反应生成共价键;另一端能与树脂生成共价键,从而使两种性质差别很大的材料结合起来,起到提高复合材料性能的作用。
硅烷化处理可描述为四步反应模型,(1)与硅相连的3个Si-OR基水解成Si-OH;(2)Si-OH之间脱水缩合成含Si-OH的低聚硅氧烷;(3)低聚物中的Si-OH与基材表面上的OH 形成氢键;(4)加热固化过程中伴随脱水反应而与基材形成共价键连接,但在界面上硅烷的硅羟基与基材表面只有一个键合,剩下两个Si-OH或者与其他硅烷中的Si-OH缩合,或者游离状态。
为缩短处理剂现场使用所需熟化时间,硅烷处理剂在使用之前第一步是进行一定浓度的预水解。
①水解反应:在水解过程中,避免不了在硅烷间会发生缩合反应,生成低聚硅氧烷。
低聚硅氧烷过少,硅烷处理剂现场的熟化时间延长,影响生产效率;低聚硅氧烷过多,则使处理剂浑浊甚至沉淀,降低处理剂稳定性及影响处理质量。
②缩合反应:成膜反应是影响硅烷化质量的关键步骤,成膜反应进行的好坏直接影响涂膜耐蚀性及对漆膜的附着力。
因此,对于处理剂的PH值等参数控制显的尤为重要。
并且对于硅烷化前的工件表面状态提出了更高的要求:1、除油完全;2、进入硅烷槽的工件不能带有金属碎屑或其他杂质;3、硅烷化前处理最好采用去离子水。
玻璃表面硅烷化处理

玻璃表面硅烷化处理
玻璃表面硅烷化处理是一种常用的表面改性技术,通过在玻璃表面形成一层硅烷化薄膜,以改善玻璃的性能和特性。
硅烷化处理主要有以下几个步骤:
1.清洗玻璃表面:使用去离子水或特定的清洁剂对玻璃表面
进行清洗,以去除灰尘、污垢和油脂等污染物。
2.表面活化:将清洗后的玻璃表面通过酸洗或等离子体处理
等方式进行表面活化,以增加表面的反应性和接纳性。
3.硅烷溶液制备:制备硅烷处理液,通常是将有机硅化合物
(如三氯甲基硅烷、甲基硅烷醇等)溶解在合适的溶剂中。
4.硅烷涂覆:将硅烷处理液均匀涂覆在玻璃表面上,可以使
用喷涂、浸渍、刷涂等方式进行涂覆。
5.硅烷化反应:处理过的玻璃样品需要在特定条件下进行硅
烷化反应。
反应条件可根据硅烷化剂和具体应用要求进行
调整。
6.干燥和固化:经过硅烷化反应后,将样品进行干燥和固化,
使硅烷化薄膜形成稳定的玻璃表面保护层。
硅烷化处理可以提供一些优良的性能,包括:
•水和油的抗附着性:硅烷化薄膜可以阻止水和油等液体的附着,使其在玻璃表面形成滴状,易于清洁。
•抗污染性:硅烷化薄膜能减少灰尘、污垢和污染物的附着,使玻璃表面保持清洁。
•耐磨性:硅烷化薄膜能增加玻璃的硬度和耐磨性。
•耐化学性:硅烷化薄膜能提高玻璃的耐酸性和耐碱性,减少化学腐蚀。
硅烷化处理被广泛应用于建筑玻璃、光学器件、太阳能电池板等领域,以改善材料的性能和延长使用寿命。
硅烷吸水烘干

硅烷吸水烘干是一种表面处理技术,主要用于提高材料表面的附着力、耐腐蚀性和耐磨性。
这种技术主要应用于金属、塑料、陶瓷等材料的表面处理。
硅烷吸水烘干的过程包括硅烷化处理、水洗和烘干三个步骤。
下面详细介绍这三个步骤及其作用。
1.硅烷化处理:硅烷化处理是将硅烷偶联剂与材料表面进行化学反应,形成一层稳定的硅烷膜。
硅烷偶联剂是一种具有两种不同化学性质的有机硅化合物,一端能与材料表面的羟基发生化学反应,另一端能与涂料、胶粘剂等有机物质发生化学反应。
硅烷化处理的目的是提高材料表面与涂层之间的附着力,从而提高涂层的耐久性和防护性能。
硅烷化处理方法有喷涂法、浸涂法和刷涂法等。
喷涂法是将硅烷偶联剂喷洒在材料表面,适用于大面积、形状复杂的材料表面处理。
浸涂法是将材料浸泡在硅烷偶联剂溶液中,适用于小型、形状简单的材料表面处理。
刷涂法是用刷子将硅烷偶联剂涂抹在材料表面,适用于局部、小面积的材料表面处理。
2.水洗:硅烷化处理后,材料表面可能会有多余的硅烷偶联剂残留,需要进行水洗以去除这些残留物。
水洗可以采用喷淋、浸泡或超声波清洗等方法。
喷淋法是用喷头将水喷洒在材料表面,将多余的硅烷偶联剂冲洗干净。
浸泡法是将材料浸泡在水中,通过水的渗透作用将多余的硅烷偶联剂溶解掉。
超声波清洗法是利用超声波的振动作用,将多余的硅烷偶联剂从材料表面剥离。
3.烘干:水洗后,材料表面会残留一定的水分,需要进行烘干处理。
烘干的目的是去除材料表面的水分,使硅烷膜更加稳定和牢固。
烘干方法有自然晾干、热风烘干和红外线烘干等。
自然晾干是将材料放置在通风良好的环境中,让水分自然蒸发。
热风烘干是利用热风将材料表面的水分迅速吹干。
红外线烘干是利用红外线的辐射作用,将材料表面的水分迅速蒸发。
总之,硅烷吸水烘干是一种有效的表面处理技术,可以提高材料表面的附着力、耐腐蚀性和耐磨性。
这种技术广泛应用于金属、塑料、陶瓷等材料的表面处理,为各种工业产品提供了良好的防护性能。
硅烷化处理工艺流程
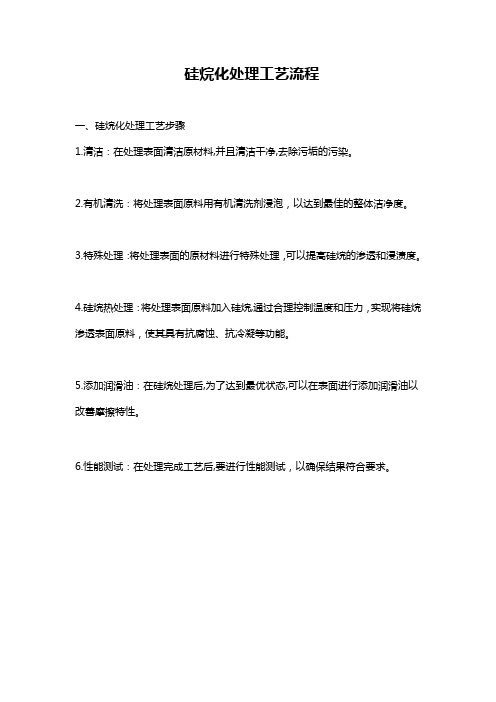
硅烷化处理工艺流程
一、硅烷化处理工艺步骤
1.清洁:在处理表面清洁原材料,并且清洁干净,去除污垢的污染。
2.有机清洗:将处理表面原料用有机清洗剂浸泡,以达到最佳的整体洁净度。
3.特殊处理:将处理表面的原材料进行特殊处理,可以提高硅烷的渗透和浸渍度。
4.硅烷热处理:将处理表面原料加入硅烷,通过合理控制温度和压力,实现将硅烷渗透表面原料,使其具有抗腐蚀、抗冷凝等功能。
5.添加润滑油:在硅烷处理后,为了达到最优状态,可以在表面进行添加润滑油以改善摩擦特性。
6.性能测试:在处理完成工艺后,要进行性能测试,以确保结果符合要求。
硅烷化处理

金属表面办理环保新技术——硅烷化办理硅烷化办理是以有机硅烷水溶液为主要成分对金属或非金属资料进行表面办理的过程。
在涂装行业,涂装前的表面办理以磷化为主,硅烷化处理与传统磷化对比拥有节能、环保和降低成本的长处。
本文简述了硅烷化办理的特色、基来源理、施工工艺等。
[ 重点词 ]硅烷;表面办理;磷化硅烷化办理是以有机硅烷为主要原料对金属或非金属资料进行表面办理的过程。
硅烷化办理与传统磷化对比拥有以下多个长处:无有害重金属离子,不含磷,无需加温。
硅烷办理过程不产生沉渣,办理时间短,控制简易。
办理步骤少,可省去表调工序,槽液可重复使用。
有效提升油漆对基材的附着力。
可共线办理铁板、镀锌板、铝板等多种基材0基来源理硅烷含有两种不一样化学官能团,一端能与无机资料(如玻璃纤维、硅酸盐、金属及其氧化物)表面的羟基反响生成共价键;另一端能与树脂生成共价键,进而使两种性质差异很大的资料联合起来,起到提升复合资料性能的作用。
硅烷化办理可描绘为四步反响模型,(1)与硅相连的 3 个 Si-OR 基水解成 Si-OH;(2)Si-OH 之间脱水缩合成含Si-OH 的低聚硅氧烷;(3)低聚物中的 Si-OH 与基材表面上的OH形成氢键;(4)加热固化过程中伴随脱水反响而与基材形成共价键连结,但在界面上硅烷的硅羟基与基材表面只有一个键合,剩下两个Si-OH 或许与其余硅烷中的Si-OH 缩合,或许游离状态。
为缩短办理剂现场使用所需熟化时间,硅烷办理剂在使用以前第一步是进行必定浓度的预水解。
① 水解反响:在水解过程中,防止不了在硅烷间会发生缩合反响,生成低聚硅氧烷。
低聚硅氧烷过少,硅烷办理剂现场的熟化时间延伸,影响生产效率;低聚硅氧烷过多,则使办理剂污浊甚至积淀,降低办理剂稳固性及影响办理质量。
②缩合反响:成膜反响是影响硅烷化质量的重点步骤,成膜反响进行的利害直接影响涂膜耐蚀性及对漆膜的附着力。
所以,关于办理剂的PH值等参数控制显的尤其重要。
实验中硅烷化的处理过程
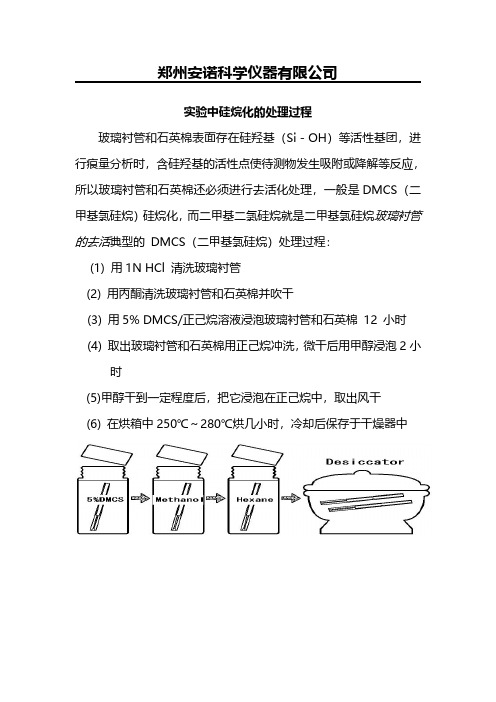
郑州安诺科学仪器有限公司
实验中硅烷化的处理过程
玻璃衬管和石英棉表面存在硅羟基(Si-OH)等活性基团,进行痕量分析时,含硅羟基的活性点使待测物发生吸附或降解等反应,所以玻璃衬管和石英棉还必须进行去活化处理,一般是DMCS(二甲基氯硅烷)硅烷化,而二甲基二氯硅烷就是二甲基氯硅烷玻璃衬管的去活典型的DMCS(二甲基氯硅烷)处理过程:
(1)用1N HCl清洗玻璃衬管
(2)用丙酮清洗玻璃衬管和石英棉并吹干
(3)用5%DMCS/正己烷溶液浸泡玻璃衬管和石英棉12小时
(4)取出玻璃衬管和石英棉用正己烷冲洗,微干后用甲醇浸泡2小
时
(5)甲醇干到一定程度后,把它浸泡在正己烷中,取出风干
(6)在烘箱中250℃~280℃烘几小时,冷却后保存于干燥器中。
金属表面硅烷化处理即非磷化转化
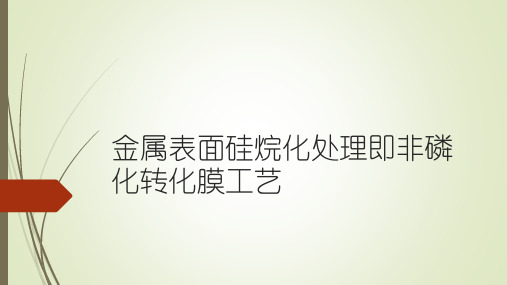
典型硅烷处理工艺介绍
硅烷处理剂浓度(5%) 处理方式:喷淋 PH值:5.0-6.8 温度:常温 处理时间:5-120秒 适用材料:钢铁件
工艺注意事项
工序间隔时间:各工序间的间隔时间如果太长,会造成工件在 运行过程中二次生銹,生锈泛黄泛绿的工件,严重影响硅烷化 效果,不能形成完整的硅烷膜,所以,应尽量缩短工序间的间 隔时间。工序间的间隔时间若太短,工件存水处的积水,不能 完全有效的沥干,产生串槽现象,特别在喷淋方式时,会产生 相互喷射串槽,使槽液成分不易控制,甚至槽液遭到破坏。因 此在考虑工序间隔时,应根据工件几何尺寸,形状选择一个恰 当的工序间隔时间。
金属表面硅烷化处理工艺的优点
该种处理工艺优点主要包括: 在处理过程中不使用磷、没有有害的重金属离子; 工艺处理程序简单,所需时间短,容易控制; 处理中不需要加温,并且不会产生沉渣,槽液可循环使用; 可有效提高油漆与基材结合力; 能够共线处理多种基材,如铁、锌、铝等; 当前,硅烷化处理技术已经在欧美国家的普通工业中得以广泛
பைடு நூலகம்烷膜的防腐蚀性
耐腐蚀性是直接体现硅烷膜性能的主要特征之一,大量试验结 果表明:硅烷表面处理后不仅可有效提高基材耐蚀性能,而且 也大大提高了基材和涂层的结合能力,金属表面硅烷化处理工 艺技术可取代涂装前磷化及铬钝化处理。
影响金属表面硅烷膜的性能的因素
影响金属表面硅烷膜的性能的因素主要有:硅烷液浓度、硅烷 液 PH 值、硅烷偶联剂水解时间、金属基体在硅烷液的浸渍时 间、处理后的老化温度以及老化时间等。
溢流水清洗:提倡溢流水清洗,以保证工件充分清洗干净,减 少串槽现象。
应用。大大地改善了传统金属表面处理方式的处理效果。
硅烷处理对基体的一些要求
在金属表面硅烷化处理工艺中,金属基体的前处理是很重要的, 其处理效果对硅烷膜的质量以及后期涂装都会造成非常大的影 响。通常,金属表面硅烷化处理过程中必须要使用无磷脱脂剂 来清洗金属表面的油污或者其他杂质。然后用含有氢氧化钠稀 碱液清洗除油后的金属基体,最后再使用清水进行浸洗;并使 用纯水清洗工件之后才能使用硅烷处理液来处理。
硅烷化处理
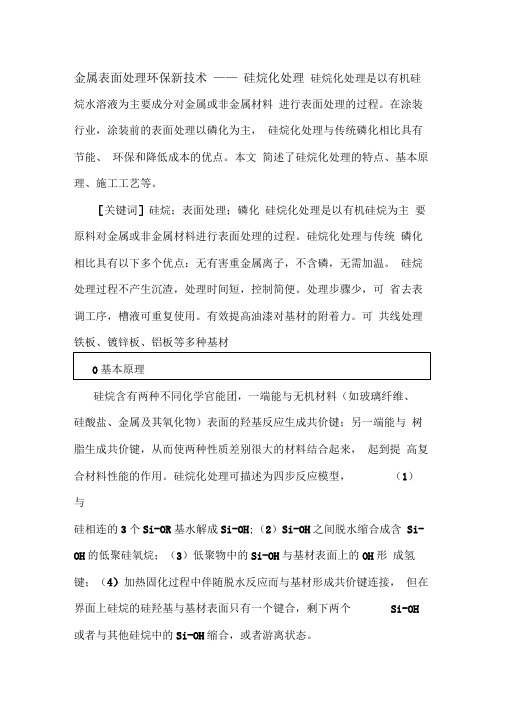
金属表面处理环保新技术——硅烷化处理硅烷化处理是以有机硅烷水溶液为主要成分对金属或非金属材料进行表面处理的过程。
在涂装行业,涂装前的表面处理以磷化为主,硅烷化处理与传统磷化相比具有节能、环保和降低成本的优点。
本文简述了硅烷化处理的特点、基本原理、施工工艺等。
[关键词]硅烷;表面处理;磷化硅烷化处理是以有机硅烷为主要原料对金属或非金属材料进行表面处理的过程。
硅烷化处理与传统磷化相比具有以下多个优点:无有害重金属离子,不含磷,无需加温。
硅烷处理过程不产生沉渣,处理时间短,控制简便。
处理步骤少,可省去表调工序,槽液可重复使用。
有效提高油漆对基材的附着力。
可共线处理铁板、镀锌板、铝板等多种基材硅烷含有两种不同化学官能团,一端能与无机材料(如玻璃纤维、硅酸盐、金属及其氧化物)表面的羟基反应生成共价键;另一端能与树脂生成共价键,从而使两种性质差别很大的材料结合起来,起到提高复合材料性能的作用。
硅烷化处理可描述为四步反应模型,(1)与硅相连的3个Si-OR基水解成Si-OH;(2)Si-OH之间脱水缩合成含Si-OH的低聚硅氧烷;(3)低聚物中的Si-OH与基材表面上的OH形成氢键;(4)加热固化过程中伴随脱水反应而与基材形成共价键连接,但在界面上硅烷的硅羟基与基材表面只有一个键合,剩下两个Si-OH 或者与其他硅烷中的Si-OH缩合,或者游离状态。
为缩短处理剂现场使用所需熟化时间,硅烷处理剂在使用之前第步是进行一定浓度的预水解①水解反应:在水解过程中,避免不了在硅烷间会发生缩合反应,生成低聚硅氧烷。
低聚硅氧烷过少,硅烷处理剂现场的熟化时间延长,影响生产效率;低聚硅氧烷过多,则使处理剂浑浊甚至沉淀,降低处理剂稳定性及影响处理质量。
②缩合反应:成膜反应是影响硅烷化质量的关键步骤,成膜反应进行的好坏直接影响涂膜耐蚀性及对漆膜的附着力。
因此,对于处理剂的PH值等参数控制显的尤为重要。
并且对于硅烷化前的工件表面状态提出了更高的要求:1、除油完全;2、进入硅烷槽的工件不能带有金属碎屑或其他杂质;3、硅烷化前处理最好采用去离子水。
铝合金硅烷化处理工艺

铝合金硅烷化处理工艺铝合金在现代制造业中被广泛应用于航空、汽车、建筑和电子等领域。
然而,铝合金在高温、潮湿的环境中易腐蚀,这限制了其使用寿命和功能。
硅烷化处理是一种有效的方法,可以增强铝合金的耐腐蚀性和耐热性。
硅烷化处理是一种将铝合金表面涂覆一层化学反应产生的硅烷化物的工艺。
这一工艺的基本原理是将表面活性较高的铝合金表面与硅烷分子发生化学反应,从而形成一层无机硅烷化物保护层。
该层具有良好的防蚀性和耐热性,可大幅度提高铝合金的使用寿命和功能。
硅烷化处理可以应用于各种铝合金材料,包括铝硅合金、铝镁合金、铝锰合金、铝铜合金和铝锌合金等。
不同材料的处理条件和涂层性质也有所不同。
一般来说,需要对不同合金材料进行定制化的处理工艺,以达到最佳的效果。
硅烷化处理的工艺流程包括表面处理、化学涂覆和热处理三个步骤。
首先,需要将铝合金表面进行清洁处理,去除表面杂质和氧化物。
清洁方式可以通过化学浸泡和机械刷洗等方式进行,确保表面的平整和光洁度。
接着,通过化学反应将铝合金表面与硅烷分子交联,形成硅烷化层。
硅烷分子的选取以及反应过程的控制是保证硅烷化层质量的关键点。
最后,使用热处理进行固化,提高涂层与基材结合的牢固度和耐热性。
硅烷化处理可以大幅度提高铝合金材料的防蚀性和耐热性。
一些研究表明,硅烷化层可以在高温和潮湿的环境下保护铝合金材料,并且能够在600℃的高温下保持长时间的稳定性。
这使得铝合金材料可以应用于更复杂和严峻的环境中。
除此之外,硅烷化处理还可用于增强材料表面的润滑性、耐磨性和抗粘附性等性能。
硅烷化层可以起到减少摩擦和磨损的作用,从而提高铝合金材料的性能。
总之,硅烷化处理是一种有效的铝合金表面处理工艺,能够提高铝合金材料的耐腐蚀性和耐热性。
其应用广泛,不仅在飞机、汽车、建筑和电子等领域有着广泛的应用,还可应用于其他种类的材料表面处理,具有广泛的应用前景。
玻璃表面硅烷化处理

玻璃表面硅烷化处理
玻璃表面硅烷化处理是一种对玻璃表面进行改性的方法,通过在玻璃表面引入硅烷基团,改变玻璃表面的化学成分和结构,从而改善其性能。
硅烷化处理可以提高玻璃表面的润湿性、粘附性、耐磨性、抗腐蚀性等性能。
玻璃表面硅烷化处理的过程通常包括以下几个步骤:
1. 准备玻璃样本:首先,需要对玻璃表面进行清洁,去除表面的油污、灰尘等杂质。
然后,对玻璃表面进行一定的预处理,如打磨、抛光等,以提高表面粗糙度,有利于硅烷化处理的效果。
2. 硅烷化处理:将玻璃样本放入硅烷化处理设备中,通过涂抹或喷涂的方式,将硅烷化试剂均匀地覆盖在玻璃表面。
硅烷化试剂中的硅烷基团可以与玻璃发生化学反应,形成硅烷化玻璃表面。
3. 固化:在硅烷化处理后,需要对玻璃表面进行固化处理,使其具有稳定的性能。
固化处理方法包括烘干、加热、紫外线照射等。
4. 分析与表征:通过各种分析方法(如扫描电子显微镜(SEM)、红外光谱(FTIR)、X射线衍射(XRD)等)对硅烷化处理后的玻璃表面进行表面形貌、粗糙度、化学结构等
方面的观察和表征,以评估硅烷化处理的效果。
玻璃表面硅烷化处理的应用领域广泛,包括建筑、家居、汽车、电子、生物医学等。
通过硅烷化处理,可以提高玻璃表面的性能,降低表面污染、粘附、磨损等问题,从而满足不同领域的需求。
需要注意的是,在玻璃表面硅烷化处理过程中,一些因素如处理温度、电源频率、电极间隙等会影响处理效果。
因此,在实际应用中,需要根据具体需求和条件,优化处理工艺,以获得理想的硅烷化效果。
硅烷化处理的作用(二)
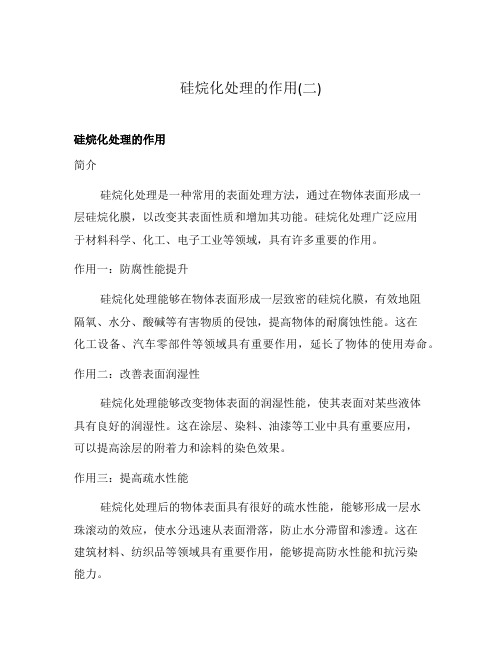
硅烷化处理的作用(二)硅烷化处理的作用简介硅烷化处理是一种常用的表面处理方法,通过在物体表面形成一层硅烷化膜,以改变其表面性质和增加其功能。
硅烷化处理广泛应用于材料科学、化工、电子工业等领域,具有许多重要的作用。
作用一:防腐性能提升硅烷化处理能够在物体表面形成一层致密的硅烷化膜,有效地阻隔氧、水分、酸碱等有害物质的侵蚀,提高物体的耐腐蚀性能。
这在化工设备、汽车零部件等领域具有重要作用,延长了物体的使用寿命。
作用二:改善表面润湿性硅烷化处理能够改变物体表面的润湿性能,使其表面对某些液体具有良好的润湿性。
这在涂层、染料、油漆等工业中具有重要应用,可以提高涂层的附着力和涂料的染色效果。
作用三:提高疏水性能硅烷化处理后的物体表面具有很好的疏水性能,能够形成一层水珠滚动的效应,使水分迅速从表面滑落,防止水分滞留和渗透。
这在建筑材料、纺织品等领域具有重要作用,能够提高防水性能和抗污染能力。
作用四:增加电绝缘性能硅烷化处理能够在物体表面形成一层具有良好绝缘性能的硅烷化膜,提高物体的电绝缘能力。
这在电子工业、电力传输等领域具有重要作用,能够提高电子器件的可靠性和安全性。
作用五:增加耐磨性能硅烷化处理能够增加物体表面的硬度和耐磨性能,形成一层具有优异耐磨性的硅烷化膜。
这在汽车制造、机械加工等领域具有重要作用,可以提高零件的使用寿命和耐磨性能。
总结硅烷化处理通过在物体表面形成一层硅烷化膜,能够改变物体的表面性质,提高其防腐性能、润湿性、疏水性、电绝缘性和耐磨性能等。
这种表面处理方法在不同领域具有广泛应用,为材料科学和工业生产带来了许多优势和便利。
金属表面处理环保新技术——硅烷化处理

金属表面处理环保新技术——硅烷化处理[摘要] 硅烷化处理是以有机硅烷水溶液为主要成分对金属或非金属材料进行表面处理的过程。
在涂装行业,涂装前的表面处理以磷化为主,硅烷化处理与传统磷化相比具有节能、环保和降低成本的优点。
本文简述了硅烷化处理的特点、基本原理、施工工艺等。
[关键词] 硅烷;表面处理;磷化硅烷化处理是以有机硅烷为主要原料对金属或非金属材料进行表面处理的过程。
硅烷化处理与传统磷化相比具有以下多个优点:无有害重金属离子,不含磷,无需加温。
硅烷处理过程不产生沉渣,处理时间短,控制简便。
处理步骤少,可省去表调工序,槽液可重复使用。
有效提高油漆对基材的附着力。
可共线处理铁板、镀锌板、铝板等多种基材0 基本原理硅烷含有两种不同化学官能团,一端能与无机材料(如玻璃纤维、硅酸盐、金属及其氧化物)表面的羟基反应生成共价键;另一端能与树脂生成共价键,从而使两种性质差别很大的材料结合起来,起到提高复合材料性能的作用。
硅烷化处理可描述为四步反应模型,(1)与硅相连的3个Si-OR基水解成Si-OH;(2)Si-OH之间脱水缩合成含Si-OH的低聚硅氧烷;(3)低聚物中的Si-OH与基材表面上的OH形成氢键;(4)加热固化过程中伴随脱水反应而与基材形成共价键连接,但在界面上硅烷的硅羟基与基材表面只有一个键合,剩下两个Si-OH或者与其他硅烷中的Si-OH缩合,或者游离状态。
为缩短处理剂现场使用所需熟化时间,硅烷处理剂在使用之前第一步是进行一定浓度的预水解。
①水解反应:在水解过程中,避免不了在硅烷间会发生缩合反应,生成低聚硅氧烷。
低聚硅氧烷过少,硅烷处理剂现场的熟化时间延长,影响生产效率;低聚硅氧烷过多,则使处理剂浑浊甚至沉淀,降低处理剂稳定性及影响处理质量。
②缩合反应:成膜反应是影响硅烷化质量的关键步骤,成膜反应进行的好坏直接影响涂膜耐蚀性及对漆膜的附着力。
因此,对于处理剂的PH值等参数控制显的尤为重要。
并且对于硅烷化前的工件表面状态提出了更高的要求:1、除油完全;2、进入硅烷槽的工件不能带有金属碎屑或其他杂质;3、硅烷化前处理最好采用去离子水。
金属表面处理环保新技术硅烷化处理

金属表面处理环保新技术——硅烷化处理[摘要] 硅烷化处理是以有机硅烷水溶液为主要成分对金属或非金属材料进行表面处理的过程。
在涂装行业,涂装前的表面处理以磷化为主,硅烷化处理与传统磷化相比具有节能、环保和降低成本的优点。
本文简述了硅烷化处理的特点、基本原理、施工工艺等。
[关键词] 硅烷;表面处理;磷化硅烷化处理是以有机硅烷为主要原料对金属或非金属材料进行表面处理的过程。
硅烷化处理与传统磷化相比具有以下多个优点:无有害重金属离子,不含磷,无需加温。
硅烷处理过程不产生沉渣,处理时间短,控制简便。
处理步骤少,可省去表调工序,槽液可重复使用。
有效提高油漆对基材的附着力。
可共线处理铁板、镀锌板、铝板等多种基材0 基本原理硅烷含有两种不同化学官能团,一端能与无机材料(如玻璃纤维、硅酸盐、金属及其氧化物)表面的羟基反应生成共价键;另一端能与树脂生成共价键,从而使两种性质差别很大的材料结合起来,起到提高复合材料性能的作用。
硅烷化处理可描述为四步反应模型,(1)与硅相连的3个Si-OR基水解成Si-OH;(2)Si-OH之间脱水缩合成含Si-OH的低聚硅氧烷;(3)低聚物中的Si-OH与基材表面上的OH形成氢键;(4)加热固化过程中伴随脱水反应而与基材形成共价键连接,但在界面上硅烷的硅羟基与基材表面只有一个键合,剩下两个Si-OH或者与其他硅烷中的Si-OH缩合,或者游离状态。
为缩短处理剂现场使用所需熟化时间,硅烷处理剂在使用之前第一步是进行一定浓度的预水解。
①水解反应:在水解过程中,避免不了在硅烷间会发生缩合反应,生成低聚硅氧烷。
低聚硅氧烷过少,硅烷处理剂现场的熟化时间延长,影响生产效率;低聚硅氧烷过多,则使处理剂浑浊甚至沉淀,降低处理剂稳定性及影响处理质量。
②缩合反应:成膜反应是影响硅烷化质量的关键步骤,成膜反应进行的好坏直接影响涂膜耐蚀性及对漆膜的附着力。
因此,对于处理剂的PH值等参数控制显的尤为重要。
并且对于硅烷化前的工件表面状态提出了更高的要求:1、除油完全;2、进入硅烷槽的工件不能带有金属碎屑或其他杂质;3、硅烷化前处理最好采用去离子水。
硅烷化处理

硅烷化处理硅烷化处理硅烷化处理是以有机硅烷水溶液为主要成分对金属或非金属材料进行表面处理的过程。
硅烷化处理与传统磷化相比具有以下多个优点:无有害重金属离子,不含磷,无需加温。
硅烷处理过程不产生沉渣,处理时间短,控制简便。
处理步骤少,可省去表调工序,槽液可重复使用。
有效提高油漆对基材的附着力。
可共线处理铁板、镀锌板、铝板等多种基材。
但就目前的国内技术来说,不是十分成熟,有待提高!尤其是硅烷和助剂的选型上,得很下功夫!一、金属表面硅烷化处理的机理:硅烷是一类含硅基的有机/无机杂化物,其基本分子式为:R'(CH2)nSi(OR)3。
其中OR是可水解的基团,R'是有机官能团。
硅烷在水溶液中通常以水解的形式存在:-Si(OR)3+H2OSi(OH)3+3ROH硅烷水解后通过其SiOH基团与金属表面的MeOH基团(Me表示金属)的缩水反应而快速吸附于金属表面。
SiOH+MeOH=SiOMe+H2O一方面硅烷在金属界面上形成Si-O-Me共价键。
一般来说,共价键间的作用力可达700kJ/tool,硅烷与金属之间的结合是非常牢固的;另一方面,剩余的硅烷分子通过SiOH基团之间的缩聚反应在金属表面形成具有Si-O-Si三维网状结构的硅烷膜[2]。
该硅烷膜在烘干过程中和后道的电泳漆或喷粉通过交联反应结合在一起,形成牢固的化学键。
这样,基材、硅烷和油漆之间可以通过化学键形成稳固的膜层结构。
二、金属表面硅烷处理的特点(1)硅烷处理中不含锌、镍等有害重金属及其它有害成分。
镍已经被证实对人体危害较大,世界卫生组织(WHO)规定,2016年后镍需达到零排放,要求磷化废水、磷化蒸气、磷化打磨粉尘中不得含镍。
(2)硅烷处理是无渣的。
渣处理成本为零,减少设备维护成本。
磷化渣是传统磷化反应的必然伴生物。
比如一条使用冷轧板的汽车生产线,每处理1辆车(以100m2计),就会产生约600g含水率为50%的磷化渣,一条10万辆车的生产线每年产生的磷化渣就有60t。
硅烷化处理与二氧化硅涂层

前言:温馨小提示:本篇文档是通过查阅资料精心整理编制的,希望能帮助大家解决实际问题,文档内容不一定完美契合各位的需求,请各位根据需求进行下载。
文档下载后可自己根据实际情况对内容进行任意改写,确保能够帮助到大家。
除此之外,本店铺还提供各种文档材料,涉及多个领域例如活动文案、工作方案、读后感、读书笔记等,大家按需搜索查看!Warm tip:This document is prepared by consulting information carefully. Hope to help you solve practical problems. The content of the document is not necessarily perfect to match your needs. Please download according to your needs. Then you can rewrite the content according to the actualsituation to ensure that we can help. In addition, the store also provides a variety of documents and materials, covering areas such as copywriting for activities, work plans, reflections, reading notes, etc.正文如下:硅烷化处理与二氧化硅涂层硅烷化及二氧化硅包覆硅烷化及二氧化硅包覆一、硅烷化处理硅烷化处理是一种独特的表面改性策略,其核心机制是通过在目标材料表面嵌入硅烷官能团,从而成功地生成一层稳固的化学键合硅烷层。
该关键技术的基础在于通过硅烷分子与材料表面原生基团的化学结合作用,实现了表面的改性和强化。
硅烷化处理在众多领域展现出广泛的实用价值。
二甲基二氯硅烷 硅烷化处理时间

二甲基二氯硅烷硅烷化处理时间一、硅烷化处理的概念和作用硅烷化处理是指将有机硅化合物与基底表面反应,形成稳定的硅-碳键,从而改善基底表面的润湿性、粘附性和耐久性。
硅烷化处理通常用于金属、陶瓷、玻璃等材料表面的改性,以提高其性能和应用范围。
二、二甲基二氯硅烷的硅烷化处理过程二甲基二氯硅烷在硅烷化处理中起到硅源的作用。
其硅烷化处理过程主要包括以下几个步骤:1. 表面预处理:在进行硅烷化处理之前,需要对基底表面进行预处理,以去除表面的杂质和氧化物。
常见的预处理方法包括机械研磨、溶剂清洗和酸洗等。
2. 硅烷化剂的施加:将二甲基二氯硅烷以适当的方法施加到基底表面上。
常见的施加方法包括浸渍法、喷涂法和浸涂法等。
3. 反应时间控制:硅烷化处理时间是影响硅烷化反应效果的重要因素之一。
一般情况下,硅烷化反应的时间范围从几分钟到几小时不等,具体时间取决于基底材料的性质、硅烷化剂的浓度和反应温度等因素。
4. 反应温度控制:硅烷化反应的温度也是影响反应效果的关键因素之一。
一般情况下,反应温度在室温到100摄氏度之间,具体温度取决于基底材料和硅烷化剂的特性。
5. 后处理:硅烷化反应完成后,需要对基底表面进行后处理,以去除未反应的硅烷化剂和产生的副产物。
常见的后处理方法包括溶剂洗涤、热处理和氧化等。
三、硅烷化处理时间的影响因素硅烷化处理时间的长短对反应效果有直接影响。
以下是几个影响硅烷化处理时间的主要因素:1. 基底材料的性质:不同的基底材料对硅烷化剂的反应速率有不同的影响。
一些基底材料表面的活性位点较多,更容易与硅烷化剂发生反应,反应时间相对较短。
2. 硅烷化剂的浓度:硅烷化剂的浓度越高,与基底表面发生反应的速率越快,反应时间相对较短。
3. 反应温度:反应温度的升高可以加快硅烷化反应的速率,从而缩短反应时间。
但是温度过高可能导致副反应的发生,影响反应效果。
4. 硅烷化剂的性质:不同类型的硅烷化剂具有不同的反应活性。
一些硅烷化剂的反应速率较快,反应时间相对较短。
硅烷化金属表面处理技术
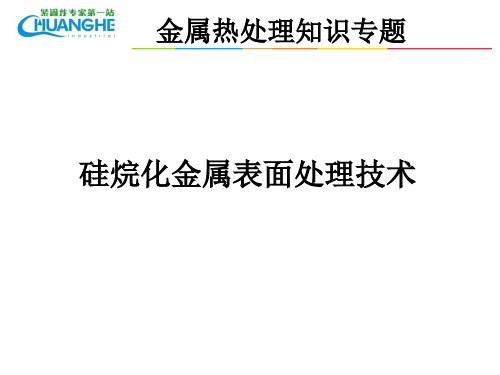
金属热处理知识专题
硅烷化处理优点 硅烷化处理是以有机硅烷为主要原料对金 属或非金属材料进行表面处理的过程。硅烷 化处理与传统磷化相比具有以下多个优点: 无有害重金属离子,不含磷,无需加温。硅烷 处理过程不产生沉渣,处理时间短,控制简便。 处理步骤少,可省去表调工序,槽液可重复使 用。有效提高油漆对基材的附着力。可共线 处理铁板、镀锌板、铝板等多种基材
金属热处理知识专题
②缩合反应 成膜反应是影响硅烷化质量的关键步骤, 成膜反应进行的好坏直接影响涂膜耐蚀性及 对漆膜的附着力。因此,对于处理剂的PH值 等参数控制显的尤为重要。并且对于硅烷化 前的工件表面状态提出了更高的要求:1、除 油完全;2、进入硅烷槽的工件不能带有金属 碎屑或其他杂质;3、硅烷化前处理最好采用 去离子水。
4加热固化过程中伴随脱水反应而与基材形成共价键连接但在界面上硅烷的硅羟基与基材表面只有一个键合剩下两个sioh或者与其他硅烷中的sioh缩合或者游离状一定浓度的预水解为缩短处理剂现场使用所需熟化时间硅烷处理剂在使用之前第一步是进行一定浓度的预水解
金属热处理知识专题
硅烷化金属表面处理技术
金属热处理知识专题
③成膜反应 其中R为烷基取代基,Me为金属基材 成膜后的金属硅烷化膜层主要由两部分构成:其一即在金属 表面,硅烷处理剂通过成膜反应形成反应③产物,二是通过缩合 反应形成大量反应②产物,从而形成完整硅烷膜,金属表面成膜 状态微观模型可描述为图1所示结构。 硅烷处理与磷化的相比较,环保型涂装前处理产品以代替传 统磷化如今显的尤为重要。硅烷前处理技术做为磷化替代技术 之一,目前已引起了世界涂装行业的广泛关注。与传统磷化相比, 硅烷处理技术具有环保性(无有毒重金属离子)、低能耗(常温使 用)、低使用成本(每公斤处理量为普通磷化的5-8倍),无渣等优 点。
金属表面处理环保新技术——硅烷化处理

金属表面处理环保新技术——硅烷化处理[摘要] 硅烷化处理是以有机硅烷水溶液为主要成分对金属或非金属材料进行表面处理的过程。
在涂装行业,涂装前的表面处理以磷化为主,硅烷化处理与传统磷化相比具有节能、环保和降低成本的优点。
本文简述了硅烷化处理的特点、基本原理、施工工艺等。
[关键词] 硅烷;表面处理;磷化硅烷化处理是以有机硅烷为主要原料对金属或非金属材料进行表面处理的过程。
硅烷化处理与传统磷化相比具有以下多个优点:无有害重金属离子,不含磷,无需加温。
硅烷处理过程不产生沉渣,处理时间短,控制简便。
处理步骤少,可省去表调工序,槽液可重复使用。
有效提高油漆对基材的附着力。
可共线处理铁板、镀锌板、铝板等多种基材0 基本原理硅烷含有两种不同化学官能团,一端能与无机材料(如玻璃纤维、硅酸盐、金属及其氧化物)表面的羟基反应生成共价键;另一端能与树脂生成共价键,从而使两种性质差别很大的材料结合起来,起到提高复合材料性能的作用。
硅烷化处理可描述为四步反应模型,(1)与硅相连的3个Si-OR基水解成Si-OH;(2)Si-OH之间脱水缩合成含Si-OH的低聚硅氧烷;(3)低聚物中的Si-OH与基材表面上的OH形成氢键;(4)加热固化过程中伴随脱水反应而与基材形成共价键连接,但在界面上硅烷的硅羟基与基材表面只有一个键合,剩下两个Si-OH或者与其他硅烷中的Si-OH缩合,或者游离状态。
为缩短处理剂现场使用所需熟化时间,硅烷处理剂在使用之前第一步是进行一定浓度的预水解。
①水解反应:在水解过程中,避免不了在硅烷间会发生缩合反应,生成低聚硅氧烷。
低聚硅氧烷过少,硅烷处理剂现场的熟化时间延长,影响生产效率;低聚硅氧烷过多,则使处理剂浑浊甚至沉淀,降低处理剂稳定性及影响处理质量。
②缩合反应:成膜反应是影响硅烷化质量的关键步骤,成膜反应进行的好坏直接影响涂膜耐蚀性及对漆膜的附着力。
因此,对于处理剂的PH值等参数控制显的尤为重要。
并且对于硅烷化前的工件表面状态提出了更高的要求:1、除油完全;2、进入硅烷槽的工件不能带有金属碎屑或其他杂质;3、硅烷化前处理最好采用去离子水。
- 1、下载文档前请自行甄别文档内容的完整性,平台不提供额外的编辑、内容补充、找答案等附加服务。
- 2、"仅部分预览"的文档,不可在线预览部分如存在完整性等问题,可反馈申请退款(可完整预览的文档不适用该条件!)。
- 3、如文档侵犯您的权益,请联系客服反馈,我们会尽快为您处理(人工客服工作时间:9:00-18:30)。
金属表面处理环保新技术——硅烷化处理硅烷化处理是以有机硅烷水溶液为主要成分对金属或非金属材料进行表面处理的过程。
在涂装行业,涂装前的表面处理以磷化为主,硅烷化处理与传统磷化相比具有节能、环保和降低成本的优点。
本文简述了硅烷化处理的特点、基本原理、施工工艺等。
Si-OH的低聚硅氧烷;(3)低聚物中的Si-OH与基材表面上的OH形成氢键;(4)加热固化过程中伴随脱水反应而与基材形成共价键连接,但在界面上硅烷的硅羟基与基材表面只有一个键合,剩下两个Si-OH 或者与其他硅烷中的Si-OH缩合,或者游离状态。
为缩短处理剂现场使用所需熟化时间,硅烷处理剂在使用之前第
一步是进行一定浓度的预水解。
①水解反应:在水解过程中,避免不了在硅烷间会发生缩合反
应,生成低聚硅氧烷。
低聚硅氧烷过少,硅烷处理剂现场的熟
化时间延长,影响生产效率;低聚硅氧烷过多,则使处理剂浑
浊甚至沉淀,降低处理剂稳定性及影响处理质量。
随着涂装行业中环保压力的逐渐增大,环保型涂装前处理产品以代替传统磷化如今显的尤为重要。
硅烷前处理技术做为磷化替代技术之一,目前已引起了世界涂装行业的广泛关注。
与传统磷化相比,硅烷处理技术具有环保性(无有毒重金属离子)、低能耗(常温使用)、低使用成本(每公斤处理量为普通磷化的5-8倍),无渣等优点。
美国已于上世纪90年代就开始对金属硅烷前处理技术进行理论研究,欧洲于上世纪90年代中期也开始着手对于硅烷进行试探性研究。
我国在本世纪初迫于环保方面的巨大压力,各大研究机构及生产企业也着手对硅烷进行研究。
1.1工位工序方面比较
备用。
在改换槽位功能的同时提高链速进行生产,以加快前处理生产节拍,提高生产率。
1.2处理条件方面比较
传统磷化处理因沉渣、含磷及磷化后废水等环保问题,一直是各涂装生产企业为之困扰的问题。
随着国家对环保及节能减排的重视程
度不断提高,在未来时间里,涂装行业的环保及能耗问题会越来突出。
硅烷技术的推出,对于整个涂装行业的前处理环保及节能降耗问题,进行了革命性的改善。
表2将传统磷化与硅烷化处理的使用条件进行比较。
传统磷化硅烷化使用温度 35-40℃常温处理过程是否产生沉
烷化相比较磷化也有着明显的优势。
表3在使用成本方面将硅烷化与磷化相比较。
传统磷化
配槽用量60-70kg/吨30-50kg/吨每公斤浓缩液处理面积30-40m2 200-300m2 处理时间 4-5min 0.5-2min 是否需要除渣槽是
否表3 磷化与硅烷化使用成本比较使用硅烷化工艺能省去磷化加温设备、除渣槽、板框压滤机及磷化污水处理等设备,节省设备初期投入。
在配槽用量方面硅烷化较磷化也减少20%-50%,更关键的是在每平方单耗方面硅烷化的消耗量为传统磷化的15%-20%。
在减少单位面积消耗量的同时,在处理时间上硅烷化较磷化也有较大幅度的缩
H2PO4-、H3PO4以及其它一些添加物。
磷化膜主体组成(钢铁工件):Fe5H2(PO4)4•4H2O,磷化膜厚度大,磷化温度高,处理时间长,膜孔隙较多,磷化晶粒呈颗粒状。
硅烷化处理为有机硅烷与金属反应形成共价键反应原理,硅烷本身状态不发生改变,因此在成膜后,金属表面无明显膜层物质生成。
通过电镜放大观察,金属表面已形成一层均
匀膜层,该膜层较锌系磷化膜薄,较铁系磷化膜均匀性有很大提高此膜层即为硅烷膜。
1.4盐水浸泡试验比较比较
冷轧板是目前用途最为广泛的金属材料,在每个行业都有大规模的应用,但冷轧板没有镀锌板那样的镀锌层、热轧板的氧化皮及铝板
和硅烷化处理与漆膜附着力相当,同时两者附着力明显优于铁系磷化。
采用硅烷化处理效果与锌系磷化效果在耐盐水及附着力方面相当。
1.5盐雾试验比较镀锌板目前因其本身具有较高耐腐蚀性能
已被广大高质量家电及汽车企业所采用。
为检验硅烷化处理对
于镀锌板的耐腐蚀性能以及附着力表现,设计试验对镀锌试片采用各种前处理工艺,并对其喷涂相同厚度的粉末涂料进行涂装,通过500小时盐雾试验对其进行附着力比较。
根据GB/T10125-1997人造气氛腐蚀试验--盐雾试验对试验镀锌试片进行500小时中性盐雾试验。
试片漆膜平均厚度为70±2μm。
油桶类工件在液体中不易沉入,因而不适合于浸泡方式。
2.1 全浸泡方式将工件完全浸泡在槽液中,待处理一段时间后取出,完成除油或硅烷化等目的的一种常见处理方式,工件的几何形状繁简各异,只要液体能够到达的地方,都能实现处理目标,这是浸泡方式的独特优点,是喷淋、刷涂所不能比拟的。
其不足之处,是没
有机械冲刷的辅助使用。
并且象连续悬挂输送工件时,除工件在槽内运行时间外,还有工件上下坡时间,因而使设备增长,场地面积和投资增大,并且工序间停留时间较长,易引起工序间返锈,影响硅烷化质量。
2.2 全喷淋方式用泵将液体加压,并以0.1~0.2Mpa的压力使液
化学处理的目的,这种方式一般不易获得很好的处理效果,在工厂应用较少。
对于某些大型、形状较简单的工件,可以考虑用这种方式。
3 工艺流程根据硅烷化的用途及处理板材不同,分为不同的工艺流程。
3.1 铁件、镀锌件预脱脂——脱脂——水清洗——水清洗——
硅烷化——烘干或晾干——后处理
3.2 铝件预脱脂——脱脂——水洗——水洗——出光——水洗——硅烷化——烘干或晾干——后处理
3.3 磷化后钝化有锈工件:预脱脂——水清洗——脱脂除锈“二合一”¬——水清洗——中和——表调——磷化——水洗——硅
控制参数 PH值 5.0-6.8 5.5-6.8 5.5-6.8 5.5-6.8 温度常温常温常温常温
处理时间(秒) 5-120 5-120 5-120 5-60
适用材料钢铁件镀锌件、铝件不锈钢件磷化后钝化
表4 典型的硅烷处理工艺
5 工艺设计上几点注意事项
在工艺设计中有些小地方应该十分注意,即使有些是与设备设计有关的,如果考虑不周,将会对生产线的运行及工人操作产生很多不利的影响,如工序间隔时间,溢流水洗,工件的工艺孔,槽体及加热管材料等。
5.3 工件工艺孔
对于某些管形件或易形成死角存水的工件,必须选择适当的位置钻好工艺孔,保证水能在较短的时间内充分流尽。
否则会造成串槽或者要在空中长时间沥干,产生二次生锈,影响硅烷化效果。
6 硅烷化性能检测
1 漆膜耐蚀性
GB/T14293-1998 人造气氛腐蚀试验一般要求
GB/T10125-1997 人造气氛腐蚀试验盐雾试验
2漆膜附着力
GB9286-1998&ASTMD3359 色漆和清漆漆膜的划格试验。