前处理硅烷处理
前处理硅烷处理
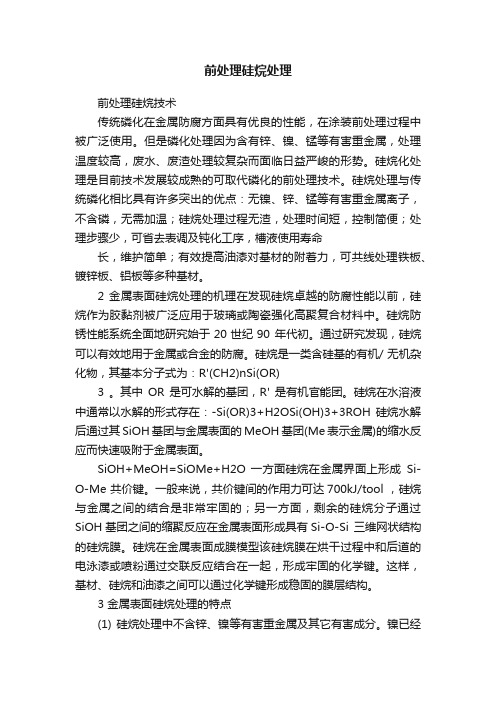
前处理硅烷处理前处理硅烷技术传统磷化在金属防腐方面具有优良的性能,在涂装前处理过程中被广泛使用。
但是磷化处理因为含有锌、镍、锰等有害重金属,处理温度较高,废水、废渣处理较复杂而面临日益严峻的形势。
硅烷化处理是目前技术发展较成熟的可取代磷化的前处理技术。
硅烷处理与传统磷化相比具有许多突出的优点:无镍、锌、锰等有害重金属离子,不含磷,无需加温;硅烷处理过程无渣,处理时间短,控制简便;处理步骤少,可省去表调及钝化工序,槽液使用寿命长,维护简单;有效提高油漆对基材的附着力,可共线处理铁板、镀锌板、铝板等多种基材。
2 金属表面硅烷处理的机理在发现硅烷卓越的防腐性能以前,硅烷作为胶黏剂被广泛应用于玻璃或陶瓷强化高聚复合材料中。
硅烷防锈性能系统全面地研究始于20世纪90 年代初。
通过研究发现,硅烷可以有效地用于金属或合金的防腐。
硅烷是一类含硅基的有机/ 无机杂化物,其基本分子式为:R'(CH2)nSi(OR)3 。
其中OR是可水解的基团,R' 是有机官能团。
硅烷在水溶液中通常以水解的形式存在:-Si(OR)3+H2OSi(OH)3+3ROH 硅烷水解后通过其SiOH基团与金属表面的MeOH基团(Me表示金属)的缩水反应而快速吸附于金属表面。
SiOH+MeOH=SiOMe+H2O 一方面硅烷在金属界面上形成Si-O-Me 共价键。
一般来说,共价键间的作用力可达700kJ/tool ,硅烷与金属之间的结合是非常牢固的;另一方面,剩余的硅烷分子通过SiOH基团之间的缩聚反应在金属表面形成具有Si-O-Si 三维网状结构的硅烷膜。
硅烷在金属表面成膜模型该硅烷膜在烘干过程中和后道的电泳漆或喷粉通过交联反应结合在一起,形成牢固的化学键。
这样,基材、硅烷和油漆之间可以通过化学键形成稳固的膜层结构。
3 金属表面硅烷处理的特点(1) 硅烷处理中不含锌、镍等有害重金属及其它有害成分。
镍已经被证实对人体危害较大,世界卫生组织(WHO规) 定,2016年后镍需达到零排放,要求磷化废水、磷化蒸气、磷化打磨粉尘中不得含镍。
硅烷-前处理2016

硅烷处理
硅烷处理
电泳涂装
电泳涂装后耐冲击性测试 中达到50kg.cm
电泳涂装
电泳涂装后在NSS(中性盐 雾)测试中达到800小时
优点
• 硅烷技术形成的超薄有机膜可以替代传统的磷化膜 • 磷化膜的重量通常为2-3g/㎡, OXSILAN涂层膜重仅仅
0.1 g/㎡,相差20倍左右。 • 单耗大大降低。
脱脂
水洗 纯水洗
硅烷
纯水洗
电泳
磷化与硅烷处理技术在使用条件方面的区别化与
项目 温度 时间 成渣量 换槽周期 耗水量/m2 膜层密度 膜重 膜厚 晶型 检测参数
磷化 35-55℃
3分 3-12g/m2
2-6个月 4升
1.5g/cm2 2-3g/m2 1-2µm
晶体 游离酸、总酸、促进剂、氟硅酸 含量、锌、镍、锰含量等
金属表面处理剂
Metal surface treatment
上海耀岩化学品有限公司
Shanghai yaoyan chemical Co., Ltd.
代替传统磷化-硅烷处理剂
传统磷化工艺的缺陷
含磷,废水 处理困难
需加热 能耗高
废水产生多, 费用高
缺陷
废渣多 处理难
含致 癌物
有害的重 金属离子
工序多,投 资成本高
废水处理的要求越来越高,成本也呈上升趋势 渣产出量小于0.1g/m2,而锌系磷化一般产渣量在1-5gm2 省却了对磷化槽和管路中磷化渣的定期清理和使用大量清洗化学品 避免了磷化废渣对环境的影响和污染,降低处理费用 废水量少,减轻了废水处理的压力 废水处理更容易,处理设备和占地更少 目前大多数磷化工艺使用亚硝酸钠作为促进剂 亚硝酸钠被证明是一种致癌物质
金属表面处理环保新技术——硅烷化处理

金属表面处理环保新技术——硅烷化处理[摘要] 硅烷化处理是以有机硅烷水溶液为主要成分对金属或非金属材料进行表面处理的过程。
在涂装行业,涂装前的表面处理以磷化为主,硅烷化处理与传统磷化相比具有节能、环保和降低成本的优点。
本文简述了硅烷化处理的特点、基本原理、施工工艺等。
[关键词] 硅烷;表面处理;磷化硅烷化处理是以有机硅烷为主要原料对金属或非金属材料进行表面处理的过程。
硅烷化处理与传统磷化相比具有以下多个优点:无有害重金属离子,不含磷,无需加温。
硅烷处理过程不产生沉渣,处理时间短,控制简便。
处理步骤少,可省去表调工序,槽液可重复使用。
有效提高油漆对基材的附着力。
可共线处理铁板、镀锌板、铝板等多种基材0 基本原理硅烷含有两种不同化学官能团,一端能与无机材料(如玻璃纤维、硅酸盐、金属及其氧化物)表面的羟基反应生成共价键;另一端能与树脂生成共价键,从而使两种性质差别很大的材料结合起来,起到提高复合材料性能的作用。
硅烷化处理可描述为四步反应模型,(1)与硅相连的3个Si-OR基水解成Si-OH;(2)Si-OH之间脱水缩合成含Si-OH的低聚硅氧烷;(3)低聚物中的Si-OH与基材表面上的OH形成氢键;(4)加热固化过程中伴随脱水反应而与基材形成共价键连接,但在界面上硅烷的硅羟基与基材表面只有一个键合,剩下两个Si-OH或者与其他硅烷中的Si-OH缩合,或者游离状态。
为缩短处理剂现场使用所需熟化时间,硅烷处理剂在使用之前第一步是进行一定浓度的预水解。
①水解反应:在水解过程中,避免不了在硅烷间会发生缩合反应,生成低聚硅氧烷。
低聚硅氧烷过少,硅烷处理剂现场的熟化时间延长,影响生产效率;低聚硅氧烷过多,则使处理剂浑浊甚至沉淀,降低处理剂稳定性及影响处理质量。
②缩合反应:成膜反应是影响硅烷化质量的关键步骤,成膜反应进行的好坏直接影响涂膜耐蚀性及对漆膜的附着力。
因此,对于处理剂的PH值等参数控制显的尤为重要。
并且对于硅烷化前的工件表面状态提出了更高的要求:1、除油完全;2、进入硅烷槽的工件不能带有金属碎屑或其他杂质;3、硅烷化前处理最好采用去离子水。
硅烷处理技术在铝及铝合金喷涂前处理中的应用

Lw2010铝型材技术(国际)论坛文集硅烷处理技术在铝及铝合金喷涂前处理中的应用余泉和(福建南平铝业有限公司,福建南平353000)摘要:介绍了~种新型的铬酸盐化学转化处理的替代技术——硅烷处理技术。
详细介绍了硅烷处理技术的防护机理、技术特点和硅烷处理技术存在的问题,对硅烷处理技术在铝及铝合金喷涂前处理中的应用前景进行展望。
关键词:硅烷;铝及铝合金;喷涂;前处理;前景或氟锆酸体系溶液),已经在工业上推广应用,尤1前言其在欧洲的铝罐、室内散热器和某些铝轮毂等方面目前,铝及铝合金表面处理工艺相对成熟,其已经广泛使用,但是在建筑铝门窗涂装前的化学转产品也丰富多彩。
与发达国家相比,我国铝及铝合化处理中用的并不多,其原因除了钛、锆转化处理金表面处理仍有较大差距,环境污染严重,能耗膜的耐腐蚀性还不如含铬体系之外,因为铝合金建高。
因此,未来一定时期内铝及铝合金表面处理的筑型材要求具有更高和更持久的耐候性和耐腐蚀发展趋势是开发并推广清洁环保,高效节能的性,还与钛、锆工艺处理后的化学转化膜没有颜技术。
色,造成工业控制的实际操作的判别困难有关。
因把铝置于铬酸盐、锰酸盐、钼酸盐等溶液中数此寻找工业操作容易、又具有相当于钛、锆化学转分钟,表面即可形成与铝基体表面结合良好的转化化膜的性能,甚至相当于铬化膜性能的新化学转化膜。
其中应用最广泛的是铬酸盐转化膜,但六价铬膜体系,已经刻不容缓。
有剧毒和致癌作用,在使用上受到严格限制。
硅烷转化膜正是适应当前环保的要求而受到研目前我国铝型材生产企业喷涂前的化学转化处究人员的关注。
作为新兴的铬酸盐替代技术,硅烷理基本上还是铬酸盐处理,喷涂层的品质如附着偶联剂对金属表面进行预处理具有无毒、无污染、性、耐候性和耐蚀性等都可以满足国家标准的技术处理工艺简单、适用范围广、对有机涂层和金属均指标。
问题是铬酸盐处理中六价铬的环境损害始终有良好的结合力等优点。
没有彻底解决,我国在技术上彻底告别铬酸盐处理硅烷偶联剂按其结构可分为两大类:单硅烷偶尚需时日。
硅烷化处理工艺流程
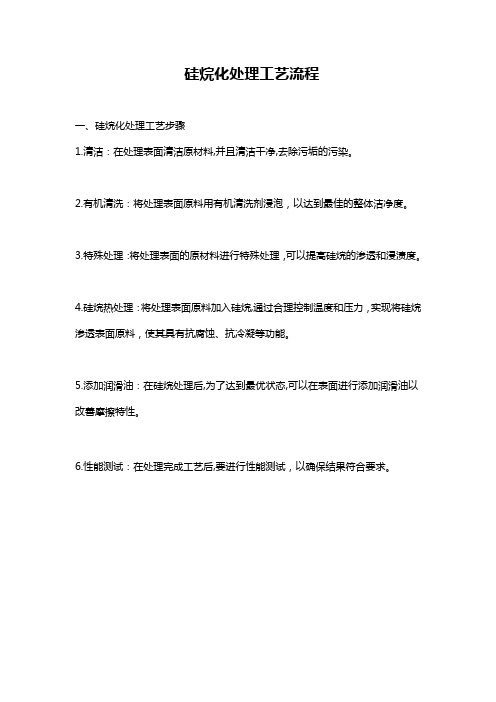
硅烷化处理工艺流程
一、硅烷化处理工艺步骤
1.清洁:在处理表面清洁原材料,并且清洁干净,去除污垢的污染。
2.有机清洗:将处理表面原料用有机清洗剂浸泡,以达到最佳的整体洁净度。
3.特殊处理:将处理表面的原材料进行特殊处理,可以提高硅烷的渗透和浸渍度。
4.硅烷热处理:将处理表面原料加入硅烷,通过合理控制温度和压力,实现将硅烷渗透表面原料,使其具有抗腐蚀、抗冷凝等功能。
5.添加润滑油:在硅烷处理后,为了达到最优状态,可以在表面进行添加润滑油以改善摩擦特性。
6.性能测试:在处理完成工艺后,要进行性能测试,以确保结果符合要求。
硅烷处理

硅烷处理序言引进国外最新转化膜技术,结合本研发中心的“水溶共聚结晶技术”,开发出的“硅烷处理剂”,可取代磷化产品,用于涂装前处理,本剂形成的转化膜是一种较为致密的均匀的微孔隙的微纳米结晶三维立体网型交联封闭膜,该膜厚度约为0.5µm,可提高涂装附着力“硅烷处理剂”是本科研中心“金五规划”的重点培育项目,详情见本说明书。
科学场合1、要求取代磷化,且要求环保的场合,可以使用本品有效取代;2、要求取代磷化,且要求杜绝酸性腐蚀的场合,可以使用本品有效取代;3、适用于碳钢、碳钢类合金钢、铸铁等黑色金属的涂装前处理、防锈;4、使用传统的水性防锈剂,影响附着力的场合,可使用本品有效替代;5、对于要求水性防锈后,后期配套喷漆、喷粉、喷塑、电泳涂装,增加附着力的场合。
选用本品为最佳选择;科学属性●无锈蚀现象。
在连续施工场合的工艺线上,不会出现腐蚀或返锈的现象;●无附着力缺陷。
与漆膜涂层具有极佳的附着力,克服了传统水性防锈剂影响附着力的缺点;涂装附着能力优于铁系磷化液,等同于锌系磷化的附着力。
●无磷、无铬、无亚硝酸盐、无镍、无铜、无氟、无锌、无锰、无重金属离子污染。
减轻了水处理负担,对操作工人及环境更友好;●无酸性腐蚀。
不含磷酸、硝酸、氢氟酸及有机酸。
本品呈中性范围,克服了传统磷化液的酸蚀性。
不会腐蚀金属,不会腐蚀人体;●无强氧化性。
杜绝了亚硝酸钠、六价铬等传统钝化防锈剂对人体的危害;●无繁琐的工艺程序。
直接浸泡、喷淋、涂刷均可。
施工后无需水洗,直接晾干、风干或烘干即可;●无色变现象。
可以杜绝传统磷化处理后,金属表面色变的现象。
传统磷化液,磷化后,表面出现灰色、黑色、蓝紫色、彩色等显色现象,使金属失去原色。
本剂处理后的金属表面呈原色,不影响金属的质感和色泽。
●无需表调。
只要工件表面洁净即可。
●无需经常添加促进剂。
体系性能稳定,不需额外添加其它助剂。
●无沉渣,无需经常维护。
本品长期使用不会出现大量沉渣。
●无需加热,低能耗。
硅烷前处理工艺应急控制策略的应用及研究
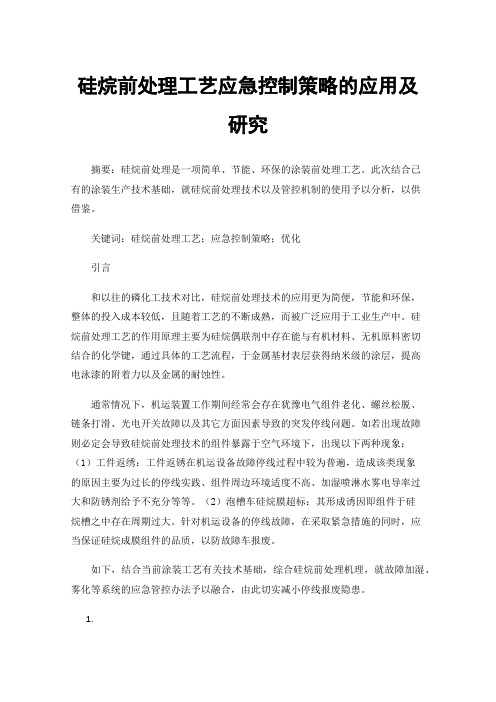
硅烷前处理工艺应急控制策略的应用及研究摘要:硅烷前处理是一项简单、节能、环保的涂装前处理工艺。
此次结合已有的涂装生产技术基础,就硅烷前处理技术以及管控机制的使用予以分析,以供借鉴。
关键词:硅烷前处理工艺;应急控制策略;优化引言和以往的磷化工技术对比,硅烷前处理技术的应用更为简便,节能和环保,整体的投入成本较低,且随着工艺的不断成熟,而被广泛应用于工业生产中。
硅烷前处理工艺的作用原理主要为硅烷偶联剂中存在能与有机材料、无机原料密切结合的化学键,通过具体的工艺流程,于金属基材表层获得纳米级的涂层,提高电泳漆的附着力以及金属的耐蚀性。
通常情况下,机运装置工作期间经常会存在犹豫电气组件老化、螺丝松脱、链条打滑、光电开关故障以及其它方面因素导致的突发停线问题。
如若出现故障则必定会导致硅烷前处理技术的组件暴露于空气环境下,出现以下两种现象:(1)工件返绣:工件返锈在机运设备故障停线过程中较为普遍,造成该类现象的原因主要为过长的停线实践、组件周边环境适度不高、加湿喷淋水雾电导率过大和防锈剂给予不充分等等。
(2)泡槽车硅烷膜超标:其形成诱因即组件于硅烷槽之中存在周期过大。
针对机运设备的停线故障,在采取紧急措施的同时,应当保证硅烷成膜组件的品质,以防故障车报废。
如下,结合当前涂装工艺有关技术基础,综合硅烷前处理机理,就故障加湿、雾化等系统的应急管控办法予以融合,由此切实减小停线报废隐患。
1.硅烷前处理工艺概述1.硅烷前处理原理硅烷槽溶液中主要为硅烷偶联剂,其包含了可水解基团,碳官能团和硅官能团。
可水解基团通过水解和组件的金属材料出现化学键合,水解基团彼此也存在缩聚反应键合,由此于其表面得到三维网状膜,促使电泳漆的附着力提升。
1.硅烷前处理工艺流程硅烷前处理技术对温度适应性较高,不要求表调以及钝化工艺,且整体产渣量较少,但是对槽液之中的杂质粒子含量、酸碱值、电导率、硅含量以及亚铁离子含量的要求较为严格,以确保硅烷成膜质量。
硅烷 前处理2016
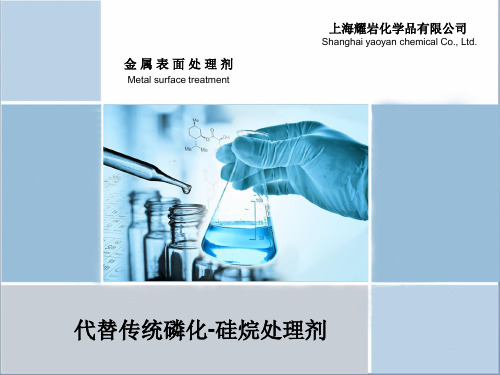
含致 癌物
危险化 学品
硅烷工艺的优势
不含磷, 对环境 友善
不含有危 害的重金 属离子
废渣大量 减少,便 于处理
无需加温, 节约能源
优势
可多种金属 混线处理
流程缩短, 设备投资 降低
工艺简单, 操作简便
非危险 化学品
化学机理学机理
超薄的类似磷化晶体的三 维网状 结构的有机涂层 吸附于金属表面 Si-O-Me共价键结合力很强 为涂料提供了很好的附着 力
间
硅烷处理后的膜层效果
冷轧钢板 镀锌钢板
硅烷处理
在冷轧钢板经过表面处理 后膜呈金黄色
硅烷处理
在镀锌钢板经过表面处 理后膜呈淡黄色或无色
硅烷处理后与涂料匹配性能优越
硅烷处理
硅烷处理
电泳涂装
电泳涂装后耐冲击性测试 中达到50kg.cm
电泳涂装
电泳涂装后在NSS(中性盐 雾)测试中达到800小时
优点
化学机理学机理
具无机物特性
膜层致密,可取代陶瓷或其他金属膜层性能
具有机/聚合物特性
耐折弯性能
隔离性
含阻断及抑制剂
多种聚合物
可溶于水
适用多种金属
CRS, HDG, EG, AL, SS, …
M
M
反应官能团
共价键结合
有极性
可提高结合力
与锌系磷化工艺对比锌系磷化对比
脱脂
水洗
表调
转化膜
水洗
钝化(可选 )
• 硅烷技术形成的超薄有机膜可以替代传统的磷化膜 • 磷化膜的重量通常为2-3g/㎡, OXSILAN涂层膜重仅仅 0.1 g/㎡,相差20倍左右。 • 单耗大大降低。
优点
• 使用方便,便于控制 • 槽液为双组分液体配成,仅需要控制PH值和电导率,无 须象磷化液那样,要控制游离酸、总酸、促进剂、锌、 镍、锰的含量和温度等许多参数。
硅烷前处理技术应用要点
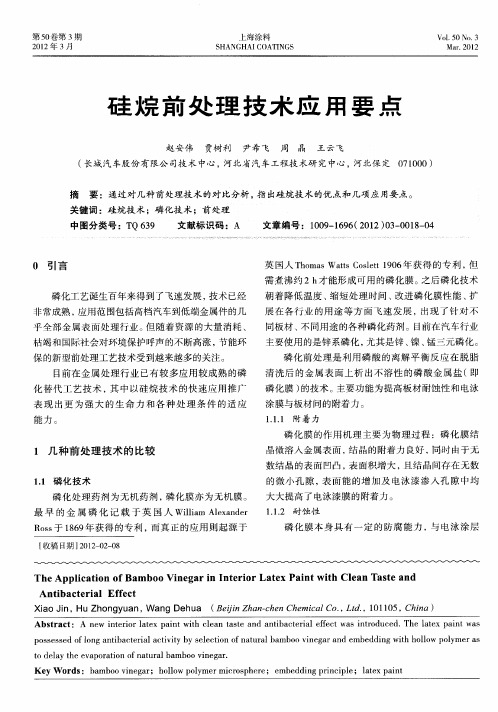
氧 化 锆本 身 是 一 种 矿 物 原 料 , 强 度 、 硬 度 、 高 高
耐高温性 、 耐磨损性 、 耐化学腐蚀性等极佳 , 在陶瓷 、
耐 火 材 料 、 械 、 子等 行 业 应 用 广泛 , 汽 车 行 业 机 电 在 主要 作 为 原 材 料 用 于 汽 车 氧 传 感 器 的制 作 。 化 锆 氧
为其 他 产 品 的原材 料 , 与石 材 混合 后烧 成 瓷 砖 , 如 用
作铸 钢铁 的原料或用 于铺 路等 , 由于各汽 车厂产 但
生 的 磷 化 废 渣 量 不 大 , 备 处 理 装 置 不 合 算 而 不 能 装 规模 化 利用 。
如 上 所 述 , 化 工 艺 替 代 技 术 的 研 究 应 用 成 为 磷
黻 氅 ’
3 nH2O42 Z( P ) z 3P ).H O +4 3 O n(O42 2 4 HP 4 ( 化 膜 H相 :Ho e e 磷 pi ) t F e+2 nH P 42 Z ( 2 O )— z 2eP 42 H2 +2 P nF (O ). o 4 H3O4 :P 。p 。 h lt ) h sh p yle i
历史 , 目前该技术 已发展至第 3 , 代 可有效应用于金
属表面处理及防腐工艺 , 对各种生产条件 、 工件材质
都 有 了更 广 泛 和成 熟 的应 用 。 硅 烷 是 代 替 传 统 磷 化 的一 种 前 处 理 剂 , 一 种 是 反 应 性 的前 处 理 药 剂 ,由于 在 成 分 中加 入 了特 殊 的 成 膜 助剂 , 以在钢 铁 、 可 镀锌 板 和 铝表 面 形成 类 似磷 化 膜 的转 化 膜 , 膜 物 质包 括 ZO 、 r O TO 、 成 r 。 Z ( H)、 i,
金属表面处理环保新技术——硅烷化处理

金属表面处理环保新技术——硅烷化处理[摘要] 硅烷化处理是以有机硅烷水溶液为主要成分对金属或非金属材料进行表面处理的过程。
在涂装行业,涂装前的表面处理以磷化为主,硅烷化处理与传统磷化相比具有节能、环保和降低成本的优点。
本文简述了硅烷化处理的特点、基本原理、施工工艺等。
[关键词] 硅烷;表面处理;磷化硅烷化处理是以有机硅烷为主要原料对金属或非金属材料进行表面处理的过程。
硅烷化处理与传统磷化相比具有以下多个优点:无有害重金属离子,不含磷,无需加温。
硅烷处理过程不产生沉渣,处理时间短,控制简便。
处理步骤少,可省去表调工序,槽液可重复使用。
有效提高油漆对基材的附着力。
可共线处理铁板、镀锌板、铝板等多种基材0 基本原理硅烷含有两种不同化学官能团,一端能与无机材料(如玻璃纤维、硅酸盐、金属及其氧化物)表面的羟基反应生成共价键;另一端能与树脂生成共价键,从而使两种性质差别很大的材料结合起来,起到提高复合材料性能的作用。
硅烷化处理可描述为四步反应模型,(1)与硅相连的3个Si-OR基水解成Si-OH;(2)Si-OH之间脱水缩合成含Si-OH的低聚硅氧烷;(3)低聚物中的Si-OH与基材表面上的OH形成氢键;(4)加热固化过程中伴随脱水反应而与基材形成共价键连接,但在界面上硅烷的硅羟基与基材表面只有一个键合,剩下两个Si-OH或者与其他硅烷中的Si-OH缩合,或者游离状态。
为缩短处理剂现场使用所需熟化时间,硅烷处理剂在使用之前第一步是进行一定浓度的预水解。
①水解反应:在水解过程中,避免不了在硅烷间会发生缩合反应,生成低聚硅氧烷。
低聚硅氧烷过少,硅烷处理剂现场的熟化时间延长,影响生产效率;低聚硅氧烷过多,则使处理剂浑浊甚至沉淀,降低处理剂稳定性及影响处理质量。
②缩合反应:成膜反应是影响硅烷化质量的关键步骤,成膜反应进行的好坏直接影响涂膜耐蚀性及对漆膜的附着力。
因此,对于处理剂的PH值等参数控制显的尤为重要。
并且对于硅烷化前的工件表面状态提出了更高的要求:1、除油完全;2、进入硅烷槽的工件不能带有金属碎屑或其他杂质;3、硅烷化前处理最好采用去离子水。
(完整word版)硅烷化处理

金属表面处理环保新技术—-硅烷化处理硅烷化处理是以有机硅烷水溶液为主要成分对金属或非金属材料进行表面处理的过程。
在涂装行业,涂装前的表面处理以磷化为主,硅烷化处理与传统磷化相比具有节能、环保和降低成本的优点。
本文简述了硅烷化处理的特点、基本原理、施工工艺等.[关键词]硅烷;表面处理;磷化硅烷化处理是以有机硅烷为主要原料对金属或非金属材料进行表面处理的过程.硅烷化处理与传统磷化相比具有以下多个优点:无有害重金属离子,不含磷,无需加温.硅烷处理过程不产生沉渣,处理时间短,控制简便。
处理步骤少,可省去表调工序,槽液可重复使用。
有效提高油漆对基材的附着力。
可共线处理铁板、镀锌板、铝板等多种基材0 基本原理硅烷含有两种不同化学官能团,一端能与无机材料(如玻璃纤维、硅酸盐、金属及其氧化物)表面的羟基反应生成共价键;另一端能与树脂生成共价键,从而使两种性质差别很大的材料结合起来,起到提高复合材料性能的作用。
硅烷化处理可描述为四步反应模型,(1)与硅相连的3个Si—OR基水解成Si-OH;(2)Si-OH之间脱水缩合成含Si-OH的低聚硅氧烷;(3)低聚物中的Si—OH与基材表面上的OH形成氢键;(4)加热固化过程中伴随脱水反应而与基材形成共价键连接,但在界面上硅烷的硅羟基与基材表面只有一个键合,剩下两个Si-OH或者与其他硅烷中的Si—OH缩合,或者游离状态.为缩短处理剂现场使用所需熟化时间,硅烷处理剂在使用之前第一步是进行一定浓度的预水解。
①水解反应:在水解过程中,避免不了在硅烷间会发生缩合反应,生成低聚硅氧烷.低聚硅氧烷过少,硅烷处理剂现场的熟化时间延长,影响生产效率;低聚硅氧烷过多,则使处理剂浑浊甚至沉淀,降低处理剂稳定性及影响处理质量.②缩合反应: 成膜反应是影响硅烷化质量的关键步骤,成膜反应进行的好坏直接影响涂膜耐蚀性及对漆膜的附着力.因此,对于处理剂的PH值等参数控制显的尤为重要。
并且对于硅烷化前的工件表面状态提出了更高的要求:1、除油完全;2、进入硅烷槽的工件不能带有金属碎屑或其他杂质;3、硅烷化前处理最好采用去离子水。
金属表面处理环保新技术——硅烷化处理

金属表面处理环保新技术——硅烷化处理[摘要] 硅烷化处理是以有机硅烷水溶液为主要成分对金属或非金属材料进行表面处理的过程。
在涂装行业,涂装前的表面处理以磷化为主,硅烷化处理与传统磷化相比具有节能、环保和降低成本的优点。
本文简述了硅烷化处理的特点、基本原理、施工工艺等。
[关键词] 硅烷;表面处理;磷化硅烷化处理是以有机硅烷为主要原料对金属或非金属材料进行表面处理的过程。
硅烷化处理与传统磷化相比具有以下多个优点:无有害重金属离子,不含磷,无需加温。
硅烷处理过程不产生沉渣,处理时间短,控制简便。
处理步骤少,可省去表调工序,槽液可重复使用。
有效提高油漆对基材的附着力。
可共线处理铁板、镀锌板、铝板等多种基材0 基本原理硅烷含有两种不同化学官能团,一端能与无机材料(如玻璃纤维、硅酸盐、金属及其氧化物)表面的羟基反应生成共价键;另一端能与树脂生成共价键,从而使两种性质差别很大的材料结合起来,起到提高复合材料性能的作用。
硅烷化处理可描述为四步反应模型,(1)与硅相连的3个Si-OR基水解成Si-OH;(2)Si-OH之间脱水缩合成含Si-OH的低聚硅氧烷;(3)低聚物中的Si-OH与基材表面上的OH形成氢键;(4)加热固化过程中伴随脱水反应而与基材形成共价键连接,但在界面上硅烷的硅羟基与基材表面只有一个键合,剩下两个Si-OH或者与其他硅烷中的Si-OH缩合,或者游离状态。
为缩短处理剂现场使用所需熟化时间,硅烷处理剂在使用之前第一步是进行一定浓度的预水解。
①水解反应:在水解过程中,避免不了在硅烷间会发生缩合反应,生成低聚硅氧烷。
低聚硅氧烷过少,硅烷处理剂现场的熟化时间延长,影响生产效率;低聚硅氧烷过多,则使处理剂浑浊甚至沉淀,降低处理剂稳定性及影响处理质量。
②缩合反应:成膜反应是影响硅烷化质量的关键步骤,成膜反应进行的好坏直接影响涂膜耐蚀性及对漆膜的附着力。
因此,对于处理剂的PH值等参数控制显的尤为重要。
并且对于硅烷化前的工件表面状态提出了更高的要求:1、除油完全;2、进入硅烷槽的工件不能带有金属碎屑或其他杂质;3、硅烷化前处理最好采用去离子水。
金属表面处理环保新技术硅烷化处理

金属表面处理环保新技术——硅烷化处理[摘要] 硅烷化处理是以有机硅烷水溶液为主要成分对金属或非金属材料进行表面处理的过程。
在涂装行业,涂装前的表面处理以磷化为主,硅烷化处理与传统磷化相比具有节能、环保和降低成本的优点。
本文简述了硅烷化处理的特点、基本原理、施工工艺等。
[关键词] 硅烷;表面处理;磷化硅烷化处理是以有机硅烷为主要原料对金属或非金属材料进行表面处理的过程。
硅烷化处理与传统磷化相比具有以下多个优点:无有害重金属离子,不含磷,无需加温。
硅烷处理过程不产生沉渣,处理时间短,控制简便。
处理步骤少,可省去表调工序,槽液可重复使用。
有效提高油漆对基材的附着力。
可共线处理铁板、镀锌板、铝板等多种基材0 基本原理硅烷含有两种不同化学官能团,一端能与无机材料(如玻璃纤维、硅酸盐、金属及其氧化物)表面的羟基反应生成共价键;另一端能与树脂生成共价键,从而使两种性质差别很大的材料结合起来,起到提高复合材料性能的作用。
硅烷化处理可描述为四步反应模型,(1)与硅相连的3个Si-OR基水解成Si-OH;(2)Si-OH之间脱水缩合成含Si-OH的低聚硅氧烷;(3)低聚物中的Si-OH与基材表面上的OH形成氢键;(4)加热固化过程中伴随脱水反应而与基材形成共价键连接,但在界面上硅烷的硅羟基与基材表面只有一个键合,剩下两个Si-OH或者与其他硅烷中的Si-OH缩合,或者游离状态。
为缩短处理剂现场使用所需熟化时间,硅烷处理剂在使用之前第一步是进行一定浓度的预水解。
①水解反应:在水解过程中,避免不了在硅烷间会发生缩合反应,生成低聚硅氧烷。
低聚硅氧烷过少,硅烷处理剂现场的熟化时间延长,影响生产效率;低聚硅氧烷过多,则使处理剂浑浊甚至沉淀,降低处理剂稳定性及影响处理质量。
②缩合反应:成膜反应是影响硅烷化质量的关键步骤,成膜反应进行的好坏直接影响涂膜耐蚀性及对漆膜的附着力。
因此,对于处理剂的PH值等参数控制显的尤为重要。
并且对于硅烷化前的工件表面状态提出了更高的要求:1、除油完全;2、进入硅烷槽的工件不能带有金属碎屑或其他杂质;3、硅烷化前处理最好采用去离子水。
涂装前处理的硅烷处理与传统磷化的比较

涂装前处理的硅烷处理与传统磷化的比较作者:安奕娜来源:《科学与财富》2016年第16期摘要:空调用压缩机的涂装前处理一直采用传统磷化技术,利用磷化反应成膜,起到提高被处理工件的耐腐蚀性,此种加工工艺存在一定弊端。
随着表面处理工业技术的发展和进步,硅烷技术逐步替代了传统磷化。
本文主要从反应原理、工艺流程、工艺参数等维度对磷化和硅烷技术进行比较说明。
关键词:空调压缩机;磷化;硅烷一、磷化处理与硅烷处理简介1、磷化处理所谓磷化处理,就是金属表面与磷化液接触发生化学反应,在金属表面生成稳定的不溶性的无机化合物膜层的化学处理方法,所生成的膜被称为磷化膜。
磷化膜的作用:1.1在充分脱脂的基础上能提供清洁、均一、无油的表面。
1.2由于物理与化学作用,增强曲轴本身的耐磨性。
2、硅烷处理硅烷化处理是以有机硅烷为主要原料对金属或非金属材料进行表面处理的过程。
是利用氟锆酸与硅烷的水解反应,在金属表面形成一种由氧化锆(ZrO2)和氧化硅(SiO2)组成的三维网状化合物,该化合物在被处理的金属物表面起到耐腐蚀并增加附着力的作用。
二、磷化处理与硅烷处理比对1、工艺流程1.1磷化工艺流程磷化的加工工艺流程:脱脂→水洗→新水洗→表调→磷化→水洗→水洗→纯水洗,共8道工序。
1.2硅烷工艺流程硅烷的加工工艺流程:脱脂→水洗→新水洗→表调→硅烷→水洗→水洗→纯水洗,共7道工序。
2、工艺技术3、皮膜组成对比4、原子力2D图三、磷化处理与硅烷处理的优劣势分析磷化反应机理可大致分为酸蚀反应和磷化反应。
其中磷化反应可简单定义为:压缩机金属表面与磷化液中的磷酸盐反应,最终以磷酸锌的形式在被处理物表面结晶,形成保护膜的化学过程。
在整个反应过程中,由于溶解下来的金属离子被氧化,所以会产生大量沉淀。
沉淀的产生是伴随磷化反应过程同步生成的,因此,无法消除。
最终大量的沉淀沉积在槽体内,覆盖在加热管路表面,导致磷化槽温度升高缓慢,磷化液温度控制异常,大量蒸汽损失产生浪费。
金属表面硅烷前处理技术的研究进展

,2018,32 ( 增刊) : 98 ~ 102 SILICONE MATERIAL
金属表面硅烷前处理技术的研究进展
高子茹,文宇佳,易生平,廖 俊,王晓玲* ,黄 驰,张先亮
( 武汉大学化学与分子科学学院,武汉 430072)
素 电化学辅助沉积技术是由 L . Shapiro 等人
提出的阴极电沉积局部碱化机理发展而来,其 基本原理为: 对体系施加一个阴极电位使溶液 局部 碱 化,较 高 浓 度 的—OH 催 化 硅 烷 缩 合, 从而促进硅烷沉积在阴极表 面,形 成 硅 烷 膜 层[18- 19]。
( 4) 甘油醚氧丙基三甲氧基硅烷 ( KH 560)1 ∶2 时膜层防腐效果最佳[16]。韩佳佳研究 发现,采用 KH 560 与 3 -氨基丙基三甲氧基硅 烷 ( PTMS) 体积 比 为 1 ∶2 的 处 理 液 制 得 的 硅 烷膜,其腐蚀电流密度比单一膜层下降 1 个数 量级[17]。 2. 2 电化学辅助沉积硅烷膜制备方法及影响因
增刊
高子茹等. 金属表面硅烷前处理技术的研究进展
· 99 ·
( 2) ( 3)
水、醇按一定比例配制成硅烷溶液,硅烷溶液 水解一定时间,再将金属基材在硅烷溶液中浸 渍约数分钟后取出。硅烷膜层的性能与硅烷种 类、硅烷 浓 度、硅 烷 溶 液 pH 值、 水 解 时 间、 浸渍 时 间、固 化 时 间、固 化 温 度 等 有 关[8-17]。 张琳琳等人探索了低乙醇含量的 γ-氨丙基三乙 氧基硅烷 ( KH 550) 改性铝合金的工艺,发现 处理液中 硅 烷、水、乙 醇 体 积 比 为 5 ∶55 ∶40, 涂膜后 在 180℃ 下 加 热 40 min, 能 得 到 完 整、 均匀、耐蚀性较好的硅烷膜,该工艺在保证膜 层性能的同时亦满足工业化生产中低成本、安 全 的 需 求[14]。 此 外 , 复 合 硅 烷 膜 层 也 被 广 泛 研 究。J. Song 等人在铝基材表面制备了 KH 550 / 1,2- 双 ( 三 乙 氧 基 硅 基) 乙 烷 ( BTSE) 复 合 膜层,该膜层能为铝基材提供 更 好 的 防 腐 保 护,同时提出防腐保护效果与在铝基材表面形 成 的 硅 氧 烷 薄 膜 的 疏 水 性 有 关[15]。 胡 巧 玲 探 究 了正硅酸乙酯 ( TEOS) 和硅烷偶联剂γ-缩水
硅烷前处理工艺技术怎么样

硅烷前处理工艺技术怎么样硅烷前处理工艺技术,是指对硅烷材料在应用前进行处理和改性的工艺技术。
本文将从硅烷前处理的目的、技术和应用等方面,对硅烷前处理工艺技术进行探讨。
硅烷前处理的目的是为了改善硅烷材料的性能,提高其适用范围和附着力。
硅烷材料具有很强的粘附性和耐化学腐蚀性,但其表面的有机污染物、氧化物以及其它杂质会影响其性能和使用寿命。
硅烷前处理的主要目的是去除这些污染物和杂质,并实现硅烷材料的表面特性改良。
硅烷前处理技术主要包括清洗、激活和改性等步骤。
清洗是首要步骤,可以使用溶剂或清洗剂对硅烷材料进行表面污染物的清除。
激活是指通过物理或化学方法提高硅烷材料表面的活性,增加其与底材的粘附力。
改性是指在激活的基础上,通过涂覆或浸渍的方式,将功能性物质引入硅烷材料表面,实现对其性能的改良。
常见的硅烷前处理技术包括氧化、干法脱脂、酸洗、溶剂清洗、等离子体活化等。
氧化是指将硅烷材料表面暴露在大气中或使用氧化剂进行处理,形成一层氧化层的方法。
干法脱脂是通过热脱脂、高温灭菌或在真空条件下将表面有机污染物脱除。
酸洗是将硅烷材料浸泡在酸性溶液中,去除有机物和氧化物。
溶剂清洗是使用有机溶剂溶解表面的污染物,并通过物理或化学吸附的方式去除。
等离子体活化是通过等离子体处理,使硅烷材料表面发生化学反应,改善其表面性质。
硅烷前处理工艺技术广泛应用于硅烷材料的清洗、防腐、涂覆以及粘接等方面。
在半导体、光学、医疗器械、航空航天等领域中,硅烷材料被广泛用于制备各类功能薄膜、涂层和粘接剂等。
而硅烷前处理技术则为这些应用提供了基础。
例如,在涂覆领域,硅烷前处理可以增加材料与底材之间的附着力,提高涂层的耐久性和防护性;在粘接领域,硅烷前处理则可以提高粘接界面的强度和稳定性,实现高效牢固的粘接。
综上所述,硅烷前处理工艺技术是一种重要的材料改性工艺,可以通过清洗、激活和改性等步骤,改善硅烷材料的性能和附着力。
该技术具有广泛的应用领域,并在各种领域中发挥着重要的作用。
硅烷处理

硅烷处理序言引进国外最新转化膜技术,结合本研发中心的“水溶共聚结晶技术”,开发出的“硅烷处理剂”,可取代磷化产品,用于涂装前处理,本剂形成的转化膜是一种较为致密的均匀的微孔隙的微纳米结晶三维立体网型交联封闭膜,该膜厚度约为0.5µm,可提高涂装附着力“硅烷处理剂”是本科研中心“金五规划”的重点培育项目,详情见本说明书。
科学场合1、要求取代磷化,且要求环保的场合,可以使用本品有效取代;2、要求取代磷化,且要求杜绝酸性腐蚀的场合,可以使用本品有效取代;3、适用于碳钢、碳钢类合金钢、铸铁等黑色金属的涂装前处理、防锈;4、使用传统的水性防锈剂,影响附着力的场合,可使用本品有效替代;5、对于要求水性防锈后,后期配套喷漆、喷粉、喷塑、电泳涂装,增加附着力的场合。
选用本品为最佳选择;科学属性●无锈蚀现象。
在连续施工场合的工艺线上,不会出现腐蚀或返锈的现象;●无附着力缺陷。
与漆膜涂层具有极佳的附着力,克服了传统水性防锈剂影响附着力的缺点;涂装附着能力优于铁系磷化液,等同于锌系磷化的附着力。
●无磷、无铬、无亚硝酸盐、无镍、无铜、无氟、无锌、无锰、无重金属离子污染。
减轻了水处理负担,对操作工人及环境更友好;●无酸性腐蚀。
不含磷酸、硝酸、氢氟酸及有机酸。
本品呈中性范围,克服了传统磷化液的酸蚀性。
不会腐蚀金属,不会腐蚀人体;●无强氧化性。
杜绝了亚硝酸钠、六价铬等传统钝化防锈剂对人体的危害;●无繁琐的工艺程序。
直接浸泡、喷淋、涂刷均可。
施工后无需水洗,直接晾干、风干或烘干即可;●无色变现象。
可以杜绝传统磷化处理后,金属表面色变的现象。
传统磷化液,磷化后,表面出现灰色、黑色、蓝紫色、彩色等显色现象,使金属失去原色。
本剂处理后的金属表面呈原色,不影响金属的质感和色泽。
●无需表调。
只要工件表面洁净即可。
●无需经常添加促进剂。
体系性能稳定,不需额外添加其它助剂。
●无沉渣,无需经常维护。
本品长期使用不会出现大量沉渣。
●无需加热,低能耗。
- 1、下载文档前请自行甄别文档内容的完整性,平台不提供额外的编辑、内容补充、找答案等附加服务。
- 2、"仅部分预览"的文档,不可在线预览部分如存在完整性等问题,可反馈申请退款(可完整预览的文档不适用该条件!)。
- 3、如文档侵犯您的权益,请联系客服反馈,我们会尽快为您处理(人工客服工作时间:9:00-18:30)。
2金属表面硅烷处理的机理在发现硅烷卓越的防腐性能以前,硅烷作为胶黏剂 被广泛应用于玻璃或陶瓷强化高聚复合材料中。硅烷防锈性能系统全面地研 究始于20世纪90年代初。通过研究发现,硅烷可以有效地用于金属或合金 的防腐。硅烷是一类含硅基的有机/无机杂化物,其基本分子式为:R'(CH2)nSi(OR)3。其中OR是可水解的基团,R'是有机官能团。硅烷在水溶液 中通常以水解的形式存在:-Si(OR)3+H2OSi(OH)3+3ROH
2000m2/kg
pH
3.8 4.5
5.5
。
5.3处理性能 该线使用硅烷处理,成品性能见表
3
。
5.4
综合成本 无表调,节约表调槽所需化学品
(
该线原本无钝化步骤
)
。
硅烷槽工作温度降低至室温,热能耗下降,节约成本计算如下: 磷化
(以磷化温度
40
~45℃计算
)
目前国内一般磷化线热能消耗在
80元
/km2
。 硅烷
1→水洗
2→表调→磷化→水洗
3→水洗
4→烘干→喷粉
在使用硅烷处理后,选用的处理工艺为:热水洗→预脱脂→主脱脂→水洗
1→水洗
2→纯水直喷→硅烷处理→水洗
3→水洗
4→烘干→喷粉。
表
2
磷化产品与硅烷产品成本方面的差异
5.2
处理条件 该线硅烷处理条件如下: 处理方式:喷淋; 温度:室温; 时间:
2min
槽液处理面积:
3金属表面硅烷处理的特点
(1)硅烷处理中不含锌、镍等有害重金属及其它有害成分。镍已经被证实对 人体危害较大,世界卫生组织(WHO规)定,2016年后镍需达到零排放,要求磷 化废水、磷化蒸气、磷化打磨粉尘中不得含镍。
(2)硅烷处理是无渣的。渣处理成本为零,减少设备维护成本。 磷化渣是传统磷化反应的必然伴生物。比如一条使用冷轧板的汽车 生产线,
5金属表面硅烷处理实例
随着硅烷技术的不断推广, 很多厂家都将原来的传统磷化前处理工艺改成了环保型的硅烷前处理工 艺。笔者曾参与了某空调机箱前处理工艺转换,该厂原来使用磷化处理时的 工艺如下:热水洗→预脱脂→主脱脂→水洗1→水洗2→表调→磷化→水洗3→水洗4→烘 干→喷粉在使用硅烷处理后,选用的处理工艺为:热水洗→预脱脂→主脱脂→水洗1→水洗2→纯水直喷→硅烷处理→水洗3→水洗4→烘干→喷粉。
(6)常温可行,节约 能源 。硅烷槽液不需要加温,传统磷化一般需要35~55℃。
(7)与现有设备工艺不冲突,无需设备改造而可直接替换磷化;与原有涂装 处理工艺相容,能与目前使用的各类油漆和粉末涂装相匹配。
4硅烷处理与磷化处理之间的区别
(1)磷化与硅烷处理技术在使用条件方面的区别。
(2)磷化产品与硅烷产品实际应用时在成本方面的差异。
(4)产品消耗量低,仅是磷化的5%
10%
。
(5)硅烷处理没有表调、钝化等工艺过程,较少的生产步骤和较短的处理时间有 助于提高工厂的产 能,可缩短新建生产线,节约设备投资和占地面积。
(6)常温可行,节约 能源 。硅烷槽液不需要加温,传统磷化一般需要
35~55℃。
(7)与现有设备工艺不冲突,无需设备改造而可直接替换磷化;与原有涂装处理工 艺相容,能与目 前使用的各类油漆和粉末涂装相匹配。
硅烷槽工作温度降低至室温,热能耗下降,节约成本计算如下: 磷化
(
以磷化温度
40
~45℃计算
)
目前国内一般磷化线热能消耗在
80元/km2
。 硅烷
(仅冬天加热到15℃以热能方面:磷化比硅烷贵了
100元/km2,节约热能约
0.07元/m2
。
(3)不需要亚 硝酸 盐促进剂,从而避免了亚硝酸盐及其分解产物对人体的危害
硅烷水解后通过其SiOH基团与金属表面的MeOH基团(Me表示金属)的缩水 反应而快速吸附于金属表面。
SiOH+MeOH=SiOMe+H2O一方面硅烷在金属界面上形成Si-O-Me共价键。一般来说,共价键间的 作用力可达700kJ/tool,硅烷与金属之间的结合是非常牢固的;另一方面, 剩余的硅烷分子通过SiOH基团之间的缩聚反应在金属表面形成具有Si-O-Si三维网状结构的硅烷膜。 硅烷在金属表面成膜模型 该硅烷膜在烘干过程中和后道的电泳漆或喷粉通过交联反应结合在一起, 形成牢固的化学键。这样,基材、硅烷和油漆之间可以通过化学键形成稳固 的膜层结构。
(仅冬天加热到
15℃以上
前处理硅烷技术
传统磷化在金属 防腐 方面具有优良的性能,在涂装前处理过程中被广泛使 用。但是磷化处理因为含有锌、镍、锰等有害重金属,处理温度较高,废水、 废渣处理较复杂而面临日益严峻的形势。硅烷化处理是目前技术发展较成熟 的可取代磷化的 前处理技术 。硅烷处理与传统磷化相比具有许多突出的优点: 无镍、锌、锰等有害重金属离子,不含磷,无需加温;硅烷处理过程无渣, 处理时间短,控制简便;处理步骤少,可省去表调及钝化 工序,槽液使用寿命
4硅烷处理与磷化处理之间的区别
(1)磷化与硅烷处理技术在使用条件方面的区别见表1
。
(2)磷化产品与硅烷产品实际应用时在成本方面的差异见表2
。
5
金属表面硅烷处理实例
5.1应用工艺 随着硅烷技术的不断推广, 很多厂家都将原来的传统磷化前处理工艺改成了环保型的硅烷前处理工 艺。笔者曾参与了某空调机箱前处理工艺转换,该厂原来使用磷化处理时的 工艺如下:热水洗→预脱脂→主脱脂→水洗
每处理1辆车(以100m2计),就会产生约600g含水率为50%的磷化渣,一条10万辆车的生产线每年产生的磷化渣就有60t。
(3)不需要亚 硝酸 盐促进剂,从而避免了亚硝酸盐及其分解产物对人体的危 害。
(4)产品消耗量低,仅是磷化的5%~10%。
(5)硅烷处理没有表调、钝化等工艺过程,较少的生产步骤和较短的处理时 间有助于提高工厂的产能,可缩短新建生产线,节约设备投资和占地面积。
磷化产品与硅烷产品成本方面的差异
5.2处理条件 该线硅烷处理条件如下: 处理方式:喷淋; 温度:室温; 时间:2min槽液处理面积:2000m2/kg pH:3.8~4.5~5.5。
5.3处理性能 该线使用硅烷处理,成品性能见表3
。
5.4综合成本 无表调,节约表调槽所需化学品
(
该线原本无钝化步骤
)
。