第三代轮毂轴承设计实例
三代轮毂轴承内圈法兰孔组合钻床主轴箱设计

三代轮毂轴承内圈法兰孔组合钻床主轴箱设计1. 引言1.1 背景介绍三代轮毂轴承内圈法兰孔组合钻床主轴箱设计是针对现有轮毂轴承内圈法兰孔组合钻床存在的结构设计问题和性能瓶颈进行研究的。
随着工业自动化的发展,对机床的性能要求也越来越高,当前的轮毂轴承内圈法兰孔组合钻床存在着结构设计复杂、加工精度有限、安装调整不便等问题。
这些问题严重影响了轮毂轴承内圈的钻床的性能和稳定性,同时也限制了机床的生产效率和加工质量。
通过对轮毂轴承内圈法兰孔组合钻床主轴箱设计的研究,可以优化结构设计,提高加工精度和稳定性,从而提升机床的性能和效率。
这不仅对提升国内轮毂轴承内圈法兰孔组合钻床的技术水平具有重要意义,也对相关行业的发展具有积极推动作用。
1.2 研究意义轮毂轴承内圈法兰孔组合钻床主轴箱设计是当前机械加工领域中一项具有重要意义的研究课题。
其研究意义主要体现在以下几个方面:该设计能够提高轮毂轴承内圈法兰孔组合钻床的加工精度和效率,进一步提升产品质量,满足市场对高精度加工设备的需求。
这对于提升企业竞争力具有重要意义。
通过对主轴箱结构设计和轴承安装方案的研究,可以有效改善设备的稳定性和可靠性,减少设备故障率,降低维护成本,延长设备使用寿命。
内圈法兰孔组合钻床设计的优化将能够大幅提高加工效率,减少生产周期,加快产品上市速度,提高企业生产效率。
这将为企业节约成本,提高生产效率,带来显著的经济效益。
通过对轮毂轴承内圈法兰孔组合钻床主轴箱设计的研究,不仅可以提高加工设备的技术水平和性能指标,还能够促进相关产业的发展,推动制造业的转型升级,具有重要的理论和实践意义。
1.3 研究内容研究内容主要包括以下几个方面:通过对三代轮毂轴承内圈法兰孔组合钻床主轴箱设计的研究,探讨其在工业生产中的应用和价值。
分析主轴箱结构设计的要求和特点,以确保设计的主轴箱符合机床的使用需求。
接下来,设计内圈法兰孔组合钻床,考虑到工艺要求和性能参数的影响,以提高加工效率和精度。
轮毂单元技术发展演变
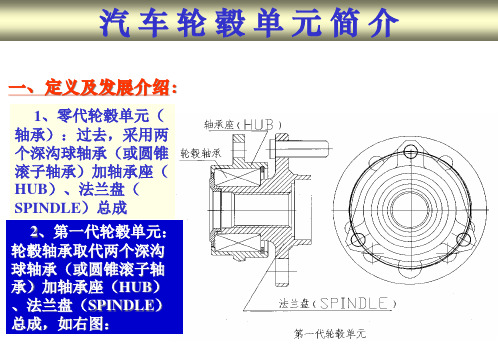
下图为法兰盘有限元分析网格 分布图例 :
下图为法兰盘有限元分析应力 ----应变分布图例:
2、有限元分析螺母拧紧力矩相关参数变化图关系
汽车轮毂单元简介
一、定义及发展介绍:
1、零代轮毂单元( 轴承):过去,采用两 个深沟球轴承(或圆锥 滚子轴承)加轴承座( HUB)、法兰盘( SPINDLE)总成
2、第一代轮毂单元: 轮毂轴承取代两个深沟 球轴承(或圆锥滚子轴 承)加轴承座(HUB) 、法兰盘(SPINDLE) 总成,如右图:
3、第二代轮毂单元:第一代轮毂单元的基础上 ,轮毂轴承外圈与轴承座为一体(HUB)、法兰 盘(SPINDLE)总成。如下图1、2:
第二代 内圈旋转 ++ 一般 高 ++ +++ ++(轻质合金的可能性) ++ +++ + ++ ++ ++ 轿车(客车)/跑车
第三代 内圈旋转 +++ 一般 高 ++++ ++++ ++(轻质合金的可能性) +++ +++ +++ ++ +++ +++ 轿车(客车)/跑车
Байду номын сангаас
圆锥滚 子类
汽车轮毂轴承的研发介绍
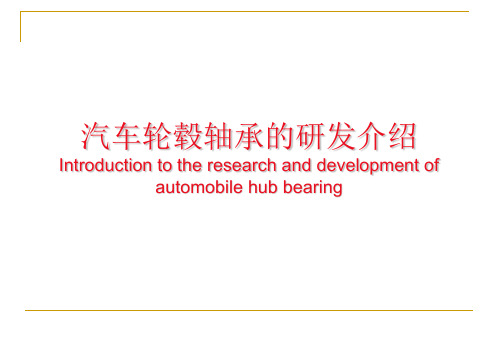
100 q1,% q2,% q3,%
L L L L com,km Lcom,h average _ speed (km/ h)
2.3.4、系统的寿命计算
1/ e
Lsystem
1 Le
com,inside
1 1e
Lcom,outside
e :指数 球轴承 e=10/9; 滚子轴承e=9/8
1.3 轮毂轴承的特性和功能 ◎很好 ○好 △较差
1代
2代
3代
特性
项目
球
球
滚子
滚子
球
滚子
球
外圈旋转
内圈旋转
外圈旋转
内圈旋转
承载能力
○
◎
○
○
◎
◎
○
功能性
轴承刚性
△
◎
△
△
◎
◎
○
旋转力矩
○
△
◎
○
△
△
◎
抗阻滞性
◎
△
◎
◎
△
△
◎
减轻轴重
△
△
○
○
○
○
◎
紧凑性
径向空间
△
△
△
△
◎
◎
◎
宽度空间
○
△
◎
◎
○
○
◎
无密封
无密封
3、轴承失效的分析
海宁奥通汽车零件有限公司常年对试验件及售后三包件进行分析时,发现了多种原因,会导 致轴承提前失效,常见的失效模式及原因:
1、预紧不足导致 轴承失效:
预紧不足的原因有很 多,除轴承自身设计 时要保证安装后有一 定的预紧力之外,(该 预紧力要求在车厂, 制动器总成厂和轴承 厂之间有时得不到完 全传递),还要要求轴 承在使用过程中,除 轴承自身磨损导致预 紧力轻微降低之外, 对轴承进行预紧的相 关零件不得发生过大 的变化,导致轴承的 预紧消失,常见的原 因见右图。
(整理)轮毂轴承单元结构图
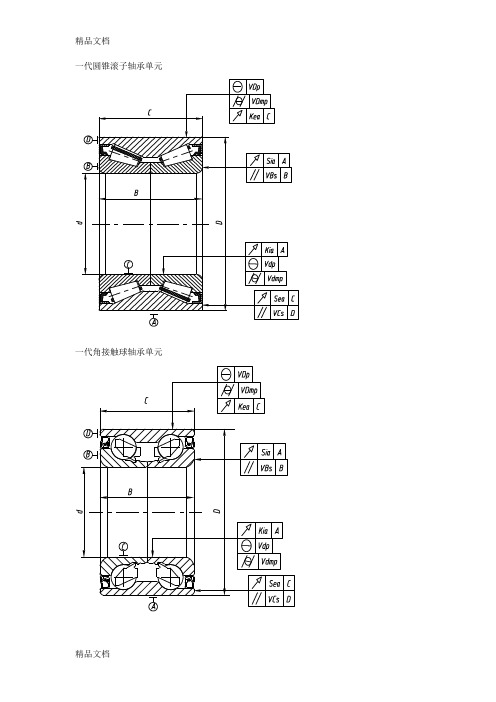
(五)建设项目环境影响评价文件的审批
1)地方环境标准是对国家环境标准的补充和完善。在执行上,地方环境标准优先于国家环境标准。
三代角接触球轴承单元(非驱动轮用) Nhomakorabea1.法律
(3)环境影响评价中应用环境标准的原则。
一、环境影响评价的发展与管理体系、相关法律法规体系和技术导则的应用
三代角接触球轴承单元(驱动轮用带传感器)
一代圆锥滚子轴承单元
一代角接触球轴承单元
二代双列圆锥滚子轴承单元
二代角接触球轴承单元(外圈旋转型)
二代角接触球轴承单元(内圈旋转型)
三代角接触球轴承单元(驱动轮用)
2.环境影响报告表的内容三代角接触球轴承单元(非驱动轮用)
(2)安全验收评价。
(四)安全预评价内容
1)按类型分。环境标准按类型分为环境质量标准、污染物排放标准(或控制标准)、环境基础标准、环境检测方法标准、环境标准样品标准。
第三代轮毂轴承单元密封件的设计与性能验证_周旭

第三代轮毂轴承单元在结构上集成了轴承座 和凸缘, 使得其在旋转精度、 可靠性、 可装配性、 易 维修性方面有了很大提高。 由于汽车轴承耐久性 所以避免出现滚道疲劳失效 和高可靠度的要求, 以外的失效也是第三代轮毂轴承单元设计的一个 重点。密封件失效就是其中一种比较常见的失效 它会导致: ( 1 ) 外界的泥沙、 粉尘和水汽等污 形式, 使轴承产生异响, 加速沟道和钢 染物侵入轴承中, 球的磨损, 使钢球、 沟道表面出现疲劳剥落
5
结束语
介绍了几种常用的密封件结构和常用的橡胶 材料, 通过示例提出密封件的配合设计要求, 给出 并对密封件的试验进行了介绍。 了相关参数, 参考文献:
[ 1] 李婉, 吴振东. 汽车轮毂轴承密封结构现状及发展 [ J] . 轴承, 2008 ( 7 ) : 47 - 51 , 53. [ 2] Harris T A. Rolling Bearing Analysis[ M] . 5 ed. Boca Raton: CRC Press Inc. , 2007. [ 3] 机械设计手册编委会. 机械设计手册: 第 2 卷[ M] . 2004. 3 版. 北京: 机械工业出版社 , [ 4] 余志生. 汽车理论[ M] . 3 版. 北京: 机械工业出版 2000. 社, ( 编辑: 赵金库)
NSK第三代轮毂轴承的开发_蒋兴奇

- 2/ 3
由赫兹接触理பைடு நூலகம்可知 [2 ]
(1 (1 δ= δ3 [ 3 Q ( + ρ 2∑ E1 E2 δ 式中 赫兹接触变形 δ3 接触变形常数 Q
2 v1 ) 2 v2 )
]2/ 3
∑ ρ ( 1) 2
ρ ∑
v E
赫兹接触载荷 两接触体接触点曲率和 两接触体泊松比 两接触体弹性模量
足密封性能要求的密封圈 。
表1 不同密封圈的性能比较
密封圈型式 轴密封 密封圈 双唇密封 低摩擦整体式密封 具有侧密封唇的轴密封 具有侧密封唇的密封圈 整体式密封 耐泥浆性能 一般 良 优 极优 极优 极优 极优 摩擦力矩 极优 优 极优 优 优 优 一般 成本 极优 优 优 良 优 良 一般
・48 ・
式中 KL — — — 第 L 个钢球与沟道的赫兹接触刚 度 K — — — 轮毂轴承轴向刚度 Z— — — 单列钢球数 α— — — 接触角
i,o— — — 分别代表钢球与内沟道和外沟道的
图2 预紧载荷测量原理及频率响应曲线
2 轮毂轴承密封技术
汽车对轮毂轴承的密封性能有非常苛刻的要 求 。不仅要求轮毂轴承具有良好的防漏脂性能 , 还要有良好的防尘 、 防水及防泥浆性能 。轮毂轴 承的密封性能与密封圈设计有关 , 与轮毂轴承周 围的结构设计也有密切的关系 。为此 ,NSK 开发 了一系列轮毂轴承密封圈 , 可根据不同的密封性 能要求进行选择 。不同密封圈的耐泥浆寿命试验 结果见图 3 。不同密封圈的性能比较列于表 1 。 可以根据轮毂轴承周围结构 , 选择既经济又能满
接触变形常数q赫兹接触载荷jd两接触体接触点曲率和两接触体泊松比e两接触体弹性模量由1式可得轮毂轴承轴向刚度鼠第个钢球与滚道的赫兹接触刚度k轮毂轴承轴向刚度z单列钢球数口接触角i0分别代表钢球与内滚道和外滚道的接触预紧状态下赫兹接触载荷q与预紧载荷之间的关系凡恐sine由2一4式可知当轮毂轴承设计参数已知时轴向刚度与预紧载荷成正比因此只要测量出轮毂轴承的轴向刚度就能确定预紧载荷的大小
第三代轮毂轴承设计实例

第三代轮毂轴承设计实例DACF2126A轮毂单元设计DACF2126A的结构设计属于双列⾓接触球轴承,第三代轿车轮毂轴承,配装在吉利GL型轿车上,适⽤于汽车在恶劣的环境使⽤。
因此,该轴承的设计及检测与常规的双列⾓接触球轴承⼤不相同,轴承的设计既要符合常规轴承的设计原理与⽅法,⼜要考虑结构的特殊性。
本⽂对DACF2126A轮毂轴承的设计进⾏分析。
简图如下:1、轴承的结构外圈带凸缘且有4个安装⼩孔,可分离式半内圈,另⼀个半内圈与轴肩、法兰盘连体,其结构紧凑,安装⽅便。
轴向游隙装配时已调好,安装时⽆需调整2、轴承主要参数设计2.1接触⾓a⾓接触球轴承的接触⾓15°---40°,承受轴向载荷⼤时,a取⼤些,根据轴承的载荷特点与装配性能要求,取a=36°。
2.2轴向游隙根据轴承的安装及所承受的载荷情况,按以往轴承的设计经验,选取游隙0~0.017,检测游隙载荷±200N2.3钢球直径Dw根据轴承设计理论,钢球直径⼤⼩与所承受的额定载荷成正⽐关系,⼀般Dw取⼤些,根据轴承设计理论公式:0.3(D-d)≤Dw≤0.33(D-d)式中D和d,由于外圈和内法兰均选⽤材料65Mn,热外理采⽤中频感应淬⽕,受淬硬层深度的影响取D=?70,取d= ?28,代⼊公式0.3(70-28)≤Dw≤0.33(70-28)12.6≤Dw≤13.86根据轴承结构除考虑径向尺⼨外,还要考虑轴承的轴向尺⼨、装配空间、装ABS空间、两列钢球互不⼲涉、合理放置保持架等因素。
取Dw=12.7更为合适。
2.4钢球中⼼圆直径Dpw的确定按轴承设计理论公式:0.5(D+d)≤Dpw≤0.515(D+d)代⼊数据得49≤Dpw≤50.47取Dpw=492.5钢球数量Z的确定钢球数量由下列条件约束Z≤(πDpw)/(K2Dw) 常数K2=0.91+1.5/12.7算得Z≤11.79,取Z=112.6径向加载作⽤中⼼位置Pi的确定径向加载作⽤中⼼位置的确定通常由整车数据确定或按提供的样件检测得出按样件检测得出Pi =41.45,同时求得两列钢球中⼼间距Pi2=25.1243、轴承主要尺⼨的设计3.1内、外沟沟曲率Ri、Re的确定内沟沟曲率Ri=0.515Dw=0.515*12.7=6.54取Ri=6.57公差为±0.03外沟沟曲率Re=0.525Dw=0.525*12.7=6.67取Ri=6.7公差为±0.033.2内、外沟径di、De内沟径di=Dpw-2Ri+(2Ri-Dw)COS a=49-2*6.57+(2*6.57-12.7)COS36°=36.216外沟径di=Dpw+2Re-(2Re-Dw)COS a=49+2*6.7-(2*6.7-12.7)COS36°=61.8343.3内圈⼤档边外径d2、外圈中档边内径D2d2=0.85Dw+di=0.85*12.7+36.216=47.011 取d2=47.1D2=De-0.85Dw=61.834-0.85*12.7=51.039 取D23.4外圈两滚道的中⼼距离Pe的确定Pe= Pi2+[Dpw-(De-2Re)]tga=25.124+[49-(61.834-2*6.7)]tg36°=25.5354、密封结构的设计根据本公司以往的设计经验,此结构例轴承均采⽤三唇⼝接触式密封结构,技术标准采⽤JBT/6639-1993.5、基本额定动载荷的计算理论计算公式Cr=bm fc(iCOSa)7.0Z3/2Dw8.1= 1.3*59.9*(2COS36°)7.0*113/2*12.78.1=52.3KNi—滚动体列数2a—接触⾓z-- 滚动体个数Dw-- 钢球直径bm-- 系数取1.3fc-- 系数取59.96、修正寿命Lna的计算根据Bundberg和Palmgren的理论计算公式基本额定寿命L10=(Cr/P)3=(53200/9160)3=195.91(*106) 即旋转总转数为195910000 如以公⾥数加以表达如下:195.91*106*2πr*103 =38.2*104(千⽶)修正寿命L1a3L10=98%*0.33*38.2*104=12.3*104(千⽶) Lna—修正寿命L10—基本额定寿命Cr—基本额定动载荷P —径向载荷a1—可靠度修正系数取98%a3—运转条件修正系数0.33r—车轮半径(⽶)设计:余祖辉审核:⽇期:2007/10/30。
带有ABS传感器的新型轮毂轴承单元的设计_张钢
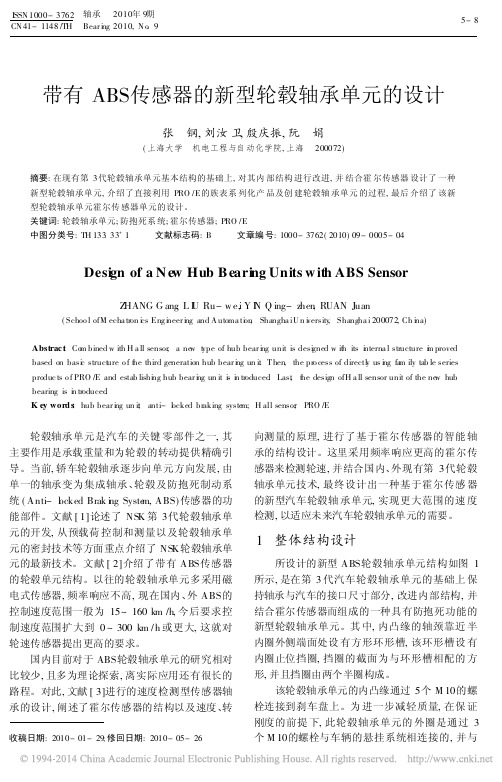
带有ABS传感器的新型轮毂轴承单元的设计张钢,刘汝卫,殷庆振,阮娟(上海大学机电工程与自动化学院,上海200072)摘要:在现有第3代轮毂轴承单元基本结构的基础上,对其内部结构进行改进,并结合霍尔传感器设计了一种新型轮毂轴承单元,介绍了直接利用PRO/E的族表系列化产品及创建轮毂轴承单元的过程,最后介绍了该新型轮毂轴承单元霍尔传感器单元的设计。
关键词:轮毂轴承单元;防抱死系统;霍尔传感器;PRO/E中图分类号:TH133.33+1文献标志码:B文章编号:1000-3762(2010)09-0005-04Desi gn of a N e w Hub B eari ng Units w ith ABS SensorZ HANG G ang,L I U Ru-w e,i Y I N Q ing-zhen,RUAN Juan(Schoo l ofM echa tron i cs Eng i neer i ng and A utoma ti on,Shangha iU n i versity,Shangha i200072,Ch i na)Abstrac t:Co m bined w ith H a ll sensor,a ne w t ype of hub bear i ng unit is desi gned w it h its i nterna l structure i m proved based on basi c struct ure o f t he third generation hub bear i ng un it.T hen,the pro cess of directl y us i ng fa m ily tab le series produc ts o f PRO/E and estab lishi ng hub bear i ng un it i s i n st,t he design ofH a ll sensor unit of the ne w hub bearing is i n troduced.K ey word s:hub bear i ng un it;anti-l ocked braking syste m;H all sensor;PRO/E轮毂轴承单元是汽车的关键零部件之一,其主要作用是承载重量和为轮毂的转动提供精确引导。
前轮毂轴承DFMEA分析范例

系统FMEA 编号:子系统第 页共 页零部件
设计责任人:编制日期: 车
关键日期:
修订日期:
核心小组:
潜在设计失效模式和后果分析(DFMEA)
底盘 制动前轮毂轴承
系统FMEA 编号:子系统第 页共 页零部件
设计责任人:编制日期: 车
关键日期:
修订日期:
核心小组:
潜在设计失效模式和后果分析(DFMEA)
底盘
制动前轮毂轴承
承早期失效
内不能正常运行,甚至引起其他部件的功能,车辆异响,顾客
不满意
统共 页零部件
设计责任人:编制日期: 车
关键日期:
修订日期:
核心小组:
制动前轮毂轴承
统共 页零部件
设计责任人:编制日期: 车
关键日期:
修订日期:
核心小组:
制动前轮毂轴承
统共 页零部件
设计责任人:编制日期: 车
关键日期:
修订日期:
核心小组:
制动前轮毂轴承
统共 页零部件
设计责任人:编制日期: 车
关键日期:
修订日期:
核心小组:
制动前轮毂轴承
统共 页零部件
设计责任人:编制日期: 车
关键日期:
修订日期:
核心小组:
制动前轮毂轴承
统共 页零部件
设计责任人:编制日期: 车
关键日期:
修订日期:
核心小组:
制动前轮毂轴承。
第三代轿车轮毂双列角接触球轴承的设计_黄雪华

· 15 ·
综合两种工艺的后续加工特点和加工量可以 看到 :温锻件的后续加工仅增加了窜磨环带和双 端面磨削两道初磨工序 , 而这两道工序安排在淬 火前进行 , 又采用通用设备 , 自动化程度和生产效 率都较高 , 对温锻滚动体成本的影响有限 。
4 结束语
采用温锻成形工艺取代车削成形工艺生产轴
承球面 滚子 , 可 以使 材料 利用
钢球数量用下列条件约束 Z ≤(πDpw )/(KzDw), 常取 Kz =1 .01 +1 .9/ 13 .494 =1 .150 8 。算得 Z ≤12 .35 , 取 Z =12 。
3 套圈主要尺寸的设计
3 .1 内 、外沟半径 Ri 、Re 的确定 Ri =0 .515 Dw =0 .515 ×13 .494 =6 .949 mm ,
(下转第 15 页)
徐新成等 :球面滚子塑性成形及后续加工工艺
少 。 前两道工序完成后 , 在淬火前还要进行一道
初磨工序 , 即软磨球形工作面 。 该工序实际上是 将原车削件淬火后进行的初磨工序改为温锻件的 软磨工序(见图 1c)。 其作用是磨去工件精磨前 的余量 , 为淬火后的精磨工序作准备 。 软磨后的 尺寸为零件尺寸加上精磨余量 。精磨余量的大小 应保证能去除淬火后新增的脱碳层 。
双半内圈双列角接触球轴承 TGB, 适用于汽车在恶劣的环境下使用 。因此 , 该类轴 承的设计及检测与第二代双列角接触球轴承大不 相同 , 轴承设计既要符合常规轴承设计原理与方 法 , 又要考虑结构的特殊性 。 本文对 TGB10872 轴 承的设计进行探讨分析 。
·7 ·
根据轴承特殊结构 , 由于轮毂轴承为双列角 接触球轴承 , 除了考虑径向尺寸外 , 还要考虑轴承 的轴向尺寸 , 考虑装配空间 , 如装密封圈空间 、两 列钢球之间不发生干涉 、合理放置保持架等因素 。 必须满足 Dw <Bi -b -h -s -y -x(图 2)。
三代轮毂轴承内圈法兰孔组合钻床主轴箱设计

三代轮毂轴承内圈法兰孔组合钻床主轴箱设计【摘要】本文主要研究了三代轮毂轴承内圈法兰孔组合钻床主轴箱的设计。
在分析了研究背景和研究意义。
设计需求分析部分讨论了主轴箱的功能和性能要求,主轴箱结构设计中考虑了轴承承载和旋转精度。
轴承内圈法兰孔组合设计中提出了相应的设计方案及优化措施。
主轴箱加工工艺部分介绍了制造过程中需考虑的工艺技术要点。
在性能测试与优化中对设计方案进行评价和调整。
结论部分评价了设计效果,并展望了未来研究方向。
通过本研究,可以更好地提高主轴箱的精度和稳定性,对相关领域的发展具有一定的参考意义。
【关键词】三代轮毂轴承、内圈法兰孔、组合钻床、主轴箱设计、设计需求分析、结构设计、加工工艺、性能测试、优化、设计效果评价、未来研究方向。
1. 引言1.1 研究背景研究背景:轮毂轴承作为汽车的重要部件之一,承载着车轮的重量和转动力。
在汽车行驶过程中,轮毂轴承承受着来自路面不平、车速变化等因素的作用,因此其性能对汽车的安全性和行驶平稳性有着重要影响。
随着汽车制造技术的不断发展,要求轮毂轴承具有更高的负荷承载能力、更好的耐磨性和更长的使用寿命。
而轮毂轴承内圈法兰孔组合设计是影响轮毂轴承性能的关键因素之一。
目前,针对轮毂轴承内圈法兰孔组合设计的研究还比较有限,尤其是在三代轮毂轴承内圈法兰孔组合设计方面的研究较少。
本文旨在针对三代轮毂轴承内圈法兰孔组合设计进行深入研究,以提高轮毂轴承的性能和寿命,为汽车行驶安全提供技术支持。
1.2 研究意义轮毂轴承内圈法兰孔组合钻床主轴箱设计是工程领域中一项重要的技术研究,具有较高的实用价值和广泛的应用前景。
该研究旨在通过对主轴箱结构和内圈法兰孔组合的设计优化,提高轮毂轴承内圈法兰孔组合钻床主轴箱的加工精度和效率,进而提升整个钻床设备的性能和稳定性。
研究意义主要体现在以下几个方面:优化设计主轴箱结构和轴承内圈法兰孔组合,可以有效提高主轴箱的稳定性和刚性,减少设备的振动和噪音,提高加工精度和效率。
轮毂轴承介绍

四、轮毂轴承特点介绍
2 代 轮 毂 轴 承 特 点
外圈
保持架
内圈
滚子
三、轮毂轴承组成结构介绍 1代轮毂轴承(双列角接触球轴承、双列圆锥滚子轴承)
橡胶密封圈
保持架 外圈 钢球
防尘盖
内圈
防尘盖 橡胶密封圈
保持架
圆锥滚子 外圈 内圈
三、轮毂轴承组成结构介绍 2代轮毂轴承(2代球轮毂轴承单元)
外法兰盘
防尘盖
ABS齿圈
车轮螺栓
保持架
橡胶密封圈 钢球
内圈
三、轮毂轴承组成结构介绍 2代轮毂轴承(2代锥轮毂轴承单元)
异径轴承
• 实现高刚性
四、轮毂轴承特点介绍
现代汽车轮毂轴承的主要技术方向
高精度的法兰盘端面跳动
降低法兰盘端面轴 向跳动,减小制动 盘的振动,提高制 动效能和舒适度。
密封技术
提高密封性能,降低水份、盐分、 灰尘等侵入轴承内部的几率,提高 轴承寿命。
旋铆工艺
・不需要装配厂商 控制预压。
传感器技术
・内置轮速度传感器,为 ABS,ESP,ASR等提供轮 速信号。
五、轮毂轴承安装介绍
2代轮毂轴承安装简图(驱动轮)
二代轮毂轴承单元 内圈紧配合于轮毂轴承法 兰盘3之上,轮毂轴承法 兰盘3通过轮毂螺栓1与 制动盘4(盘式制动器) 轮辋连接。轮毂轴承法兰 盘3通过花键与带花键传 动轴的等速万向节7相连, 同时通过螺母2轮毂轴承 法兰盘3通过花键与带花 键传动轴的等速万向节7 在轴向得以固定。轮毂轴 承外圈6通过转向节5 (或后轴分头)与悬架系 统通过螺栓相连接。在汽 车行驶时,带花键传动轴 的 等速万向节7轮毂轴承 法兰盘3 、二代轮毂轴承 单元内圈、制动盘4以及 轮辋旋转,而轮毂轴承外 圈6与转向节通过悬架系 统保持静止。
乘用车第三代轮毂轴承单元制造关键技术及应用

乘用车第三代轮毂轴承单元制造关键技术及应用1. 背景介绍在乘用车行业中,轮毂轴承单元是车辆传动系统中的重要部件之一。
它承担着支撑车辆重量、传递动力和减少摩擦的重要作用,直接关系到车辆的性能和安全性。
随着乘用车制造技术的不断发展和创新,第三代轮毂轴承单元已成为当今乘用车制造行业的主流选择。
本文将从制造关键技术和应用两个方面探讨乘用车第三代轮毂轴承单元的相关内容。
2. 制造关键技术第三代轮毂轴承单元制造关键技术是保证产品性能和品质的关键。
在轮毂轴承单元的制造过程中,需要借助复杂的工艺和先进的设备,确保其在高速旋转、重载和恶劣环境下的可靠性和持久性。
以下是第三代轮毂轴承单元制造关键技术的主要内容:2.1 材料选择第三代轮毂轴承单元的材料选择至关重要。
通常采用滚动轴承钢、不锈钢或其他特殊合金材料,以提高其耐磨损、耐腐蚀和耐高温的性能。
2.2 制造工艺制造工艺包括冷态成型、热态成型、热成型和精密锻造等多种工艺。
其中,精密锻造技术可以提高产品的密实度和硬度,减少表面裂纹和疲劳寿命。
2.3 精密加工精密加工是保证轮毂轴承单元尺寸精度和表面质量的关键。
采用数控机床、磨床和其他高精度设备进行外圆、内孔、滚道和轴肩的加工,确保轴承的匹配性和可靠性。
2.4 装配技术装配技术是保证轮毂轴承单元完整性和一致性的关键。
采用自动装配线和检测设备进行组装和检测,确保产品的质量和稳定性。
3. 应用领域第三代轮毂轴承单元已经广泛应用于乘用车行业,并逐渐成为主流产品。
它在提高车辆性能、降低燃油消耗、减少维护成本等方面具有显著的优势。
以下是第三代轮毂轴承单元的主要应用领域:3.1 高速旋转第三代轮毂轴承单元可以承受高速旋转和高温环境,适用于高速公路和竞速赛车等领域。
3.2 重载传动第三代轮毂轴承单元可以承受重载和冲击负荷,适用于越野车辆和卡车等领域。
3.3 高精度传动第三代轮毂轴承单元具有高精度和高刚性,适用于高速列车和豪华轿车等领域。
- 1、下载文档前请自行甄别文档内容的完整性,平台不提供额外的编辑、内容补充、找答案等附加服务。
- 2、"仅部分预览"的文档,不可在线预览部分如存在完整性等问题,可反馈申请退款(可完整预览的文档不适用该条件!)。
- 3、如文档侵犯您的权益,请联系客服反馈,我们会尽快为您处理(人工客服工作时间:9:00-18:30)。
DACF2126A轮毂单元设计DACF2126A的结构设计属于双列角接触球轴承,第三代轿车轮毂轴承,
配装在吉利GL型轿车上,适用于汽车在恶劣的环境使用。
因此,该轴承的设计及检测与常规的双列角接触球轴承大不相同,轴承的设计既要符合常规轴承的设计原理与方法,又要考虑结构的特殊性。
本文对DACF2126A轮毂轴承的设计进行分析。
简图如下:
1、轴承的结构
外圈带凸缘且有4个安装小孔,可分离式半内圈,另一个半内圈与轴肩、法兰盘连体,其结构紧凑,安装方便。
轴向游隙装配时已调好,安装时无需调整
2、轴承主要参数设计
2.1接触角a
角接触球轴承的接触角15°---40°,承受轴向载荷大时,a取大些,根据轴承的载荷特点与装配性能要求,取a=36°。
2.2轴向游隙
根据轴承的安装及所承受的载荷情况,按以往轴承的设计经验,选取游隙0~0.017,检测游隙载荷±200N
2.3钢球直径Dw
根据轴承设计理论,钢球直径大小与所承受的额定载荷成正比关系,一般Dw取大些,根据轴承设计理论公式:
0.3(D-d)≤Dw≤0.33(D-d)
式中D和d,由于外圈和内法兰均选用材料65Mn,热外理采用中频感应淬火,受淬硬层深度的影响取D=Ø70,取d= Ø28,代入公式
0.3(70-28)≤Dw≤0.33(70-28)
12.6≤Dw≤13.86
根据轴承结构除考虑径向尺寸外,还要考虑轴承的轴向尺寸、装配空间、装ABS空间、两列钢球互不干涉、合理放置保持架等因素。
取Dw=12.7更为合适。
2.4钢球中心圆直径Dpw的确定
按轴承设计理论公式:0.5(D+d)≤Dpw≤0.515(D+d)代入数据得
49≤Dpw≤50.47取Dpw=49
2.5钢球数量Z的确定
钢球数量由下列条件约束
Z≤(πDpw)/(K
2Dw) 常数K
2
=0.91+1.5/12.7
算得Z≤11.79,取Z=11
2.6径向加载作用中心位置Pi的确定
径向加载作用中心位置的确定通常由整车数据确定或按提供的样件检测得出
按样件检测得出Pi =41.45,同时求得两列钢球中心间距Pi
2
=25.124
3、轴承主要尺寸的设计
3.1内、外沟沟曲率Ri、Re的确定
内沟沟曲率Ri=0.515Dw=0.515*12.7=6.54取Ri=6.57公差为±0.03
外沟沟曲率Re=0.525Dw=0.525*12.7=6.67取Ri=6.7公差为±0.03
3.2内、外沟径di、De
内沟径di=Dpw-2Ri+(2Ri-Dw)COS a
=49-2*6.57+(2*6.57-12.7)COS36°
=36.216
外沟径di=Dpw+2Re-(2Re-Dw)COS a
=49+2*6.7-(2*6.7-12.7)COS36°
=61.834
3.3内圈大档边外径d
2、外圈中档边内径D
2
d
2=0.85Dw+di=0.85*12.7+36.216=47.011 取d
2
=47.1
D
2=De-0.85Dw=61.834-0.85*12.7=51.039 取D
2
=51
3.4外圈两滚道的中心距离Pe的确定
Pe= Pi
2
+[Dpw-(De-2Re)]tga
=25.124+[49-(61.834-2*6.7)]tg36°
=25.535
4、密封结构的设计
根据本公司以往的设计经验,此结构例轴承均采用三唇口接触式密封结
构,技术标准采用JBT/6639-1993.
5、基本额定动载荷的计算
理论计算公式Cr=b
m f
c
(iCOSa)7.0Z3/2Dw8.1
= 1.3*59.9*(2COS36°)7.0*113/2*12.78.1
=52.3KN
i—滚动体列数2
a—接触角
z-- 滚动体个数
Dw-- 钢球直径
b
m
-- 系数取1.3
f
c
-- 系数取59.9
6、修正寿命L
na
的计算
根据Bundberg和Palmgren的理论计算公式
基本额定寿命L
10
=(Cr/P)3=(53200/9160)3=195.91(*106) 即旋转总转数为195910000 如以公里数加以表达如下:195.91*106*2πr*103 =38.2*104(千米)
修正寿命L
na =a
1
a
3
L
10
=98%*0.33*38.2*104=12.3*104(千米)
L
na
—修正寿命
L
10
—基本额定寿命
Cr—基本额定动载荷
P —径向载荷
a
1
—可靠度修正系数取98%
a
3
—运转条件修正系数0.33
r—车轮半径(米)
设计:余祖辉
审核:
日期:2007/10/30。