浅议铣削力对铣削过程的影响
浅议铣削力对铣削过程的影响

浅议铣削力对铣削过程的影响摘要铣削力大小和变化对加工过程的稳定性、工件表面质量及刀具的磨损和破损均有着重要影响。
关键词铣削力加工过程稳定性在铣工生产实习教学课题练习中,学生经常会遇到虽然都按照合理的加工工艺进行操作,但工件在铣削过程中仍出现尺寸精度不一致、表面质量不稳定、刀具磨损状况不同等普遍问题,这其中很大因素是由于加工过程中铣削力的变化造成的。
一、铣削力及其分解1.铣削力是铣刀在切除工件上的材料余量时受到的一种阻力。
它是同时工作的各个刀齿上受到切削力的总和。
总的铣削力主要来自三个方面:a在铣削过程中克服工件材料变形的抗力。
b克服切屑形成过程中工件材料对塑性变形的抗力。
c克服切屑与前刀面的摩擦力和铣刀后刀面与工件已加工表面及过度表面之间的摩擦力。
2.铣削力的分解。
为了对机床、刀具、夹具之间的作用力进行科学分析和研究,我们可将铣削力分解到所研究的方向上,这样就得到如图示的铣削力示意图:圆周分力(主切削力)Fc:铣刀外圆切线方向上的分力。
轴向分力Fa:沿铣刀轴线方向上的分力。
径向分力(垂直切削力)Fp:沿铣刀半径方向上的分力。
如果把主切削力Fc和垂直切削力Fp合成就是切削力R,把切削力R1可以分解成水平分力Fh和垂直分力Fv。
从而可以看出,主切削力Fc消耗机床的主要功率,轴向分力Fa作用在机床的主轴上,垂直分力Fv作用在机床工作面或者是工件上,而水平分力Fh是作用在机床的进给机构上。
切削力作用在主轴轴心上,会影响刀杆的弯曲。
二、铣削力对铣削过程中的影响1.铣削力对铣削平稳性的影响铣削加工过程是非连续切削,铣削加工过程中由于切削面积是随着刀具的移动而变化的,所以引起的切削力及力矩也是变化的,是一个动态的数值。
尤其是当同时参加切削得刀齿数量越少时,这种切削力和切削力矩的变化也就越大。
切削力和切削力矩的变化,会引起工艺系统的受力变形、震动、冲击。
这些都会使加工精度、表面质量、机床的寿命和刀具的寿命下降。
铣削过程的动态切削厚度与动态铣削力模型

铣削过程的动态切削厚度与动态铣削力模型铣削是常见的金属加工方法,它通过旋转刀具将工件表面的金属材料削除,从而实现形状和尺寸的加工。
在铣削过程中,动态切削厚度和动态铣削力是两个重要的参数,它们对加工效率和工件表面质量有着重要的影响。
本文将分别介绍动态切削厚度和动态铣削力模型,以帮助读者更好地理解铣削过程。
1.动态切削厚度模型动态切削厚度是指工件表面上金属材料被刀具削除的厚度,它随着时间的推移而变化。
在铣削过程中,动态切削厚度的变化主要与刀具进给速度、切削速度和切削深度有关。
(1)刀具进给速度:刀具进给速度是指刀具在单位时间内沿工件表面移动的距离。
当刀具进给速度增加时,每单位时间内切削的金属材料体积也会增加,因此动态切削厚度也会增加。
(2)切削速度:切削速度是指刀具在单位时间内相对于工件表面的线速度。
切削速度增加时,切削时刀具与工件之间的相对速度增加,因此动态切削厚度也会增加。
(3)切削深度:切削深度是指刀具在切削过程中进入工件表面的深度。
切削深度增加时,刀具与工件之间的接触面积增加,切削力会增加,从而动态切削厚度也会增加。
通过以上的分析,可以得到动态切削厚度与刀具进给速度、切削速度和切削深度之间的关系模型。
该模型可以用于预测和优化铣削过程中的动态切削厚度。
动态铣削力是指在铣削过程中刀具对工件施加的力,它主要由切削力和进给力组成。
切削力是指刀具在切削过程中削除工件的力,它与刀具的几何形状、切削材料的特性和切削参数有关。
进给力是指刀具推动工件运动的力,它与刀具的进给速度、切削深度和切削宽度相关。
在铣削过程中,切削力是最主要的力。
它的大小和方向决定了刀具与工件之间的相互作用力和金属材料的削除情况。
切削力的大小和变化与切削参数、刀具结构和工件材料的性质有关。
动态铣削力的模型可以分为经验型和理论型两种。
(1)经验型模型:经验型模型是通过实验测量获得的经验公式,它根据不同的切削参数和工件材料的性质建立了切削力与这些参数之间的关系。
铣削加工中的切削力

铣削加工中的切削力铣削加工是机械制造领域中常见的加工方式之一,而铣削加工中的切削力则是影响加工质量的重要因素之一。
本文将从切削力的概念、影响切削力的因素、切削力的测量和切削力的控制等方面进行分析。
一、切削力的概念切削力指铣刀在加工过程中对工件作用的力。
在铣削加工中,切削力的大小会影响工件的表面质量、加工精度和刀具的使用寿命等方面。
切削力的大小受到多种因素的影响,如切削条件、材料力学性质、铣刀几何参数和铣刀的运动状态等。
二、影响切削力的因素1.切削参数切削参数包括切削速度、进给速度和切削深度。
在相同切削条件下,当切削速度增加或进给速度增加,切削力也会增加。
而当切削深度增加时,切削力的变化则较为复杂,通常会出现先增加后减小的趋势。
2.材料力学性质材料力学性质对切削力的影响很大,如硬度、切削性和韧性等。
当切削硬度增加时,切削力也会增加。
而当材料的切削性和韧性提高时,切削力则会减小。
3.铣刀几何参数铣刀的几何参数对切削力的影响也很大。
如铣刀的齿数、刃角和刃磨度等参数均会对切削力产生影响。
当铣刀齿数增加时,每个齿的切削深度和切削速度就会减小,因此切削力也会减小。
而当刃角增大时,切削力则会增大。
4.铣刀的运动状态铣刀的运动状态也会对切削力产生影响。
如切削液的使用和冷却剂的使用等均可以影响铣刀的运动状态,从而影响切削力的大小。
三、切削力的测量在铣削加工中,测量切削力对于保证加工质量和刀具的使用寿命有着重要作用。
目前常用的切削力测量方法有间隙传感器法、压电传感器法和片式传感器法等。
间隙传感器法是指将铣刀的副切口设置成斜向切口,然后在铣削过程中测量副切口的间隙变化来计算切削力大小。
这种方法需要将铣刀进行加工和改造,因此应用较少。
压电传感器法是指将压电传感器安装在夹具上并接收由工件产生的力来计算切削力的大小。
这种方法不需要对铣刀进行改造,测量精度较高,但会受到振动干扰的影响。
片式传感器法是指将张力传感器安装在夹具上,测量夹具或工件受力的大小来计算切削力的大小。
铣削力计算公式详解

铣削力计算公式详解铣削力是指铣削过程中刀具对工件所施加的力,它是铣削加工过程中重要的参数之一。
铣削力大小的计算对于工件的加工质量、工具的寿命以及加工效率都有着重要的影响。
铣削力的计算公式通常是根据铣削的工艺参数以及材料的性质来推导,下面我们将详细解释铣削力的计算公式。
一、铣削力的基本概念为了更好地理解铣削力的计算公式,首先我们需要了解铣削力的基本概念。
在铣削加工过程中,刀具在与工件接触时会产生力的作用。
这些力包括主轴的进给力、切削力和阻力等。
其中,切削力是指刀具在切削过程中与工件发生力的作用,它是决定加工质量和加工效率的重要因素。
铣削力的大小与工件的材料性质、切削刀具的材料和几何形状、切削速度、进给速度、切削深度等因素密切相关。
因此,在进行铣削加工时,需要对铣削力进行精确地计算和控制,以保证加工质量和工具寿命。
二、铣削力的计算公式在铣削加工中,刀具施加在工件上的切削力可以用力学原理进行计算,一般来说,可以参考以下的铣削力计算公式:1.切削力Fc的计算公式切削力Fc是铣削中最常见的力。
在进行铣削加工时,切削力的大小直接影响着刀具的磨损情况和加工表面的加工质量。
切削力Fc的计算公式通常如下:Fc = kc * ae * ap * f //(1)其中,Fc为切削力,单位为牛顿(N);kc为切削力系数,其大小与材料性质、切削条件和刀具类型等有关;ae为轴向切削深度,单位为毫米(mm);ap为径向切削深度,单位为毫米(mm);f为给进量,单位为毫米/刀齿(mm/tooth)。
切削力Fc的大小与刀具材料、刀具的结构和铣削参数等因素有关。
在实际的工程中,我们需要根据具体的加工情况和工件材料来确定切削力系数kc的数值,然后通过公式(1)来计算切削力Fc的大小。
2.主轴的进给力Fr的计算公式除了切削力之外,铣削加工中还存在着主轴的进给力Fr。
主轴的进给力是指主轴在刀具与工件接触时所施加的力,它也是影响加工质量和加工效率的重要因素。
铣床及加工中心铣削力计算

铣床及加工中心铣削力计算铣床及加工中心是现代机械加工中不可或缺的设备,广泛应用于各个行业的加工生产线中。
铣床及加工中心的铣削力计算是机械加工过程中的重要参数,对于加工件的质量和刀具的寿命都有着直接的影响。
下面将对铣床及加工中心的铣削力计算进行详细介绍。
首先,铣削力是指在铣削过程中切削刃对工件单位长度表面上的摩擦力。
它是描述切削刃与工件之间相互作用能量大小及其空间分布的物理量,通常用力矩的大小和方向来表示。
铣床及加工中心的铣削力计算需要考虑多种因素,如刀具材料、工件材料、切削参数、切削速度等。
刀具材料是铣削力计算的重要因素之一、刀具材料的硬度、抗磨性和热稳定性都会影响铣削力的大小。
刀具材料越硬、抗磨性越好,铣削力越小。
常用的刀具材料有高速钢、硬质合金和陶瓷等。
工件材料也是铣削力计算的重要因素之一、工件材料的硬度、韧性和热导率都会影响铣削力的大小。
工件材料越硬、韧性越差、热导率越低,铣削力越大。
常用的工件材料有铸铁、钢材、铝合金和高温合金等。
切削参数是铣削力计算中最直接影响铣削力大小的因素。
主要包括切削速度、进给量和切削深度三个参数。
切削速度越高,铣削力越大;进给量越大,铣削力越大;切削深度越大,铣削力越大。
切削速度是指切削刃在单位时间内与工件接触的次数,单位是米/分钟。
切削速度越高,铣削力越大,因为切削刃与工件接触时间越短,摩擦力越大。
进给量是指切削刃在单位时间内对工件进行切削的量,单位是毫米/转。
进给量越大,铣削力越大,因为切削刃与工件之间的切削面积越大,摩擦力越大。
切削深度是指切削刃在铣削过程中从工件表面到切削层顶部的距离,单位是毫米。
切削深度越大,铣削力越大,因为切削刃与工件接触的切削面积越大,摩擦力越大。
在实际应用中,铣床及加工中心的铣削力计算可以通过经验公式、实验测量和有限元分析等多种方法来进行。
比较常用的经验公式有帕斯卡公式和柯蒂斯公式。
帕斯卡公式是最为常用的铣削力计算公式之一,可以用来计算瞬时铣削力以及稳态铣削力。
机械制造考试问答题
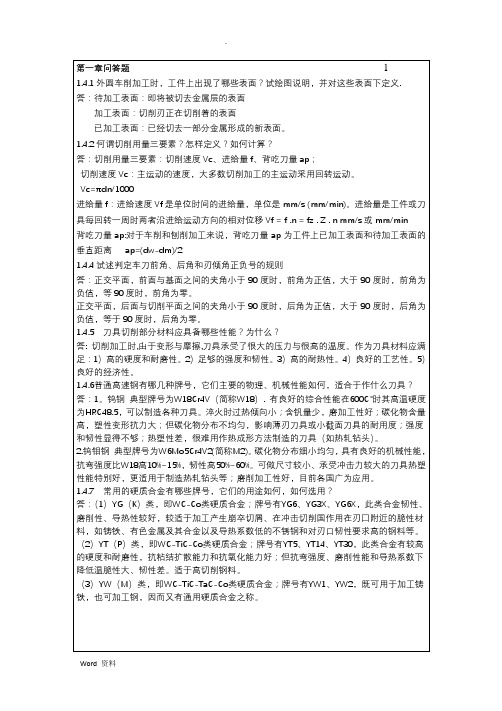
2.5.1 如何表示切屑变形程度?两种表示方法的区别与联系?答:1.相对滑移ε(剪切角越小,剪切变形量越大)Λ(变形系数越大,剪切角越小)2. 变形系数hΛ与相对滑移ε的关系:变形系数h当0γ= 0~30°,hΛ≥1.5时,hΛ的数值与ε相近。
当0γ<0°或hΛ<1.5时,不能用hΛ表示切屑的变形程度。
2.5.2 影响切削变形有哪些因素?各因素如何影响切削变形?答:前角、工件材料、切削速度、进给量、v c在低速围提高,积屑瘤高度随着增加,刀具实际前角增大,使剪切角φ增大,故变形系数Λh减小;v c在中速围提高,积屑瘤逐渐消失,刀具实际前角减小,使φ减小,Λh 增大。
高速,由于切削温度继续增高,致使摩擦系数μ下降,故变形系数Λh减小。
增大前角,使剪切角φ增大,变形系数Λh减小,切屑变形减小。
进给量f 增大,使变形系数Λh减小。
工件材料的机械性能不同,切屑变形也不同。
材料的强度、硬度提高,正压力Fn 增大,平均正应力σav增大,因此,摩擦系数μ下降,剪切角φ增大,切屑变形减小。
2.5.3 三个切削分力是如何定义的?各分力对加工有何影响?答:(1)主切削力F z 主运动切削速度方向的分力;切深抗力F y切深方向的分力;进给抗力F x进给方向的分力。
(2)1.主切削力Fz是最大的一个分力,它消耗了切削总功率的95%左右,是设计与使用刀具的主要依据,并用于验算机床、夹具主要零部件的强度和刚度以及机床电动机功率。
2.切深抗力Fy不消耗功率,但在机床—工件—夹具—刀具所组成的工艺系统刚性不足时,是造成振动的主要因素。
3.进给抗力Fx消耗了总功率5%左右,它是验算机床进给系统主要零、部件强度和刚性的依据。
2.5.4 刀具磨损过程有哪几个阶段?为何出现这种规律?答:1.初期磨损阶段(在开始切削的短时间,磨损较快。
这是由于刀具表面粗糙不平或表层组织不耐磨引起的。
)2.正常磨损阶段(随着切削时间增加,磨损量以较均匀的速度加大。
机械制造技术基础(高教版,吉卫喜主编)复习题

第2章金属切削过程及其控制一、选择题1.车床上镗内孔时,刀尖安装高于工件回转中心,则刀具工作角度与标注角度相比,后角。
…………………………………………………………………()(A)增大(B)减小(C)不变2.纵车外圆时,不消耗功率但影响工件精度的切削分力是()(A)进给力(B)背向力(C)主切削力(D)总切削力4.在车削细长轴时,为了减小工件的变形和振动,故采用较大的车刀进行切削,以减小径向切削分力。
…………………………………………………………………()(A)主偏角(B)副偏角(C)后角5.在车削加工铸铁工件外圆时,应选用的硬质合金刀具材料种类为……………()(A)YT类(B)YT或YG类(C)YG类6.刃倾角的功用之一是控制切屑流向,若刃倾角为负,则切屑流向为……………()(A)流向已加工面(B)流向待加工面(C)沿切削刃的法线方向流出7.粗加工时,前角应取();加工材料塑性越大,前角应取()的值。
(A)相对较大(B)相对较小(C)任意取8.车45钢调质工件外圆时,产生表面粗糙度主要原因是残留面积、塑性变形和等因素引起的。
…………………………………………………()(A)切屑崩碎(B)鳞刺(C)积屑瘤9.刀具磨损到一定的限度就不能再继续使用,这个磨损限度称为()。
(A)磨钝标准(B)磨损极限(C)耐用度(D)刀具寿命10.在基面内测量的角度有()(A)前角和后角(B)主偏角和副偏角(C)刃倾角11.前刀面与基面间的夹角是( )。
12.切削用量中对切削力影响最大的是()。
(A)切削速度Vc (B)进给量f (C)切削深度a p(D)三者一样13.在切削平面内测量的角度有()。
(A)前角(B)后角(C)主偏角(D)刃倾角14.下列哪种刀具不适宜进行沟槽的铣削()。
(A) 立铣刀(B)圆柱形铣刀(C)锯片铣刀(D)三面刃铣刀15.YT 类硬质合金适用于加工钢材,其中()适合于精加工。
(A)YT1 (B)YT5 (C)YT15 (D)YT3016.()切削液主要起冷却作用。
浅议铣削力对铣削过程的影响

1 . 书店 。城 区学 校 , 着 天 时 、 凭 地利 等 优 势 , 近 水 楼 台 “ 先 得 月” 新华 书店 , 书 中心 , 大 超 市 , 要 想读 绘 本 , 。 购 各 只 是
一
走进“ 文本 ” 才 能领 着 学 生走 进 “ , 文本 ” 。比如 《 母鸡 萝 丝 去 散 步》 本 绘 本 需提 取 出两 个字 “ 闲” 才 能让 学 生深 深地 这 悠 , 感 受 到母 鸡 萝 丝 的悠 闲和 狐狸 倒 霉 的一 天 。
不 动 摇 。农 村 小学 领 导也 只 能“ 随波 逐 流” 对 成绩 “ 睐 有 , 青
力进行科 学分析和研究 , 我们可将铣削力分解到所研究 的
方 向上 , 样 就 得 到 如 图 示 的铣 削 力 示 意 图 : 这 展 低年 级绘 本 阅读教 学 , 农村 学校 现有 设施 在支 持 上大 有压
企 及 的 。 且绘 本 阅读 是最 好 的亲 子 方 式 , 而 家长 更容 易 与 孩 子 建立 亲 密 、 谐 的关 系 。 和
五、 远水 难 救近 火
点 且渗 透 语 言 、 语 、 维方 式等 训 练 的绘 本 , 《 里 最漂 词 思 如 城
亮 的 巨人 》 。其次 , 需要 潜 下心 来 , 钻 文 本 。教 师 自己先要 深
不 能一 刀 切 。必 须 慎重 选 择 , 充分 考虑 学 生 不 同年龄 、 要 心
查 , 百名 学 生 家长 , 有初 中 以上 学 历 不足 1 , 多数 上 具 O人 大 只 有 小学 或毫 无 学历 , 说是 实 实在 在 的 文盲 。 可 而与 农 村相 比, 城镇 学 生家 长 有文 化 , 触 面广 , 目 的 “ 本热 ” 接 对 前 绘 知 晓、 理解 、 同 , 能积 极 响应 。 赞 并 我认 为 , 绘本 虽 贵 , 物 超所 但
《铣削加工工艺》课件

铣削加工适用于各种金属材料的加工,如钢铁、有色金属等,尤其适用于加工平面、沟 槽、齿形等复杂形状。在航空制造业中,铣削加工广泛应用于机翼、机身和发动机部件 的制造;在汽车制造业中,铣削加工用于发动机、变速器和底盘部件的制造;在模具制
造业中,铣削加工用于模具型腔和型芯的加工。
铣削加工的发展趋势
总结词
工件表面质量不佳是铣削加工中常见的问题 之一,它可能影响工件的外观和使用性能。
详细描述
工件表面质量不佳的原因可能包括机床精度 不足、刀具磨损、切削参数选择不当等。为 了提高工件表面质量,可以采取一系列措施 ,如提高机床精度、定期检查和更换刀具、
优化切削参数等。
THANKS
感谢观看
02
切削速度是指铣刀在单位时间内所转过的弧长,通常以米/分钟为单 位。
03
进给速度是指铣刀在进给系统中每分钟所移动的距离,通常以毫米/ 分钟为单位。
04
铣削深度是指铣刀在工件表面上所切削的深度,通常以毫米为单位。
铣削深度与进给速度的确定
铣削深度的确定应根据工件的材料、硬度、铣刀的材质和规格以及加工要求等因素 综合考虑。
02
CATALOGUE
铣削加工的基本原理
铣削力的产生与影响
总结词
了解铣削力的产生原因及其对铣削加工的影响
详细描述
铣削力是铣削加工过程中的主要作用力,其产生与切削层的形成和切屑的排出 有关。铣削力的方向、大小和变化直接影响铣削加工的效率、刀具的磨损和加 工质量。
铣削加工的切屑形成与控制
总结词
掌握切屑的形成机理及切屑控制的方法
齿轮铣削是一种针对齿轮的铣削 工艺,主要用于加工各种齿轮。
齿轮铣削工艺主要采用指状铣刀 进行加工,通过调整刀具的角度 和切削参数,可以获得较好的加
铣削加工精度影响因素分析及控制措施

铣削加工精度影响因素分析及控制措施工业制造是一个国家发展的基础,机械加工制造是工业制造中的一个极为重要的分支,其中在机械加工制造中车削、铣削、刨、磨是其中最为基础的机械加工制造形式,确保工件的机械加工制造精度是工业加工制造质量的重要基础。
铣削加工在机械加工中的应用极多,在铣削加工的过程中其铣削加工精度会受到各种因素的影响,做好铣削加工中的各影响因素的分析并在此基础上采取相应的措施予以解决是提高工件铣削加工精度的举措。
文章将在分析铣削加工过程中影响铣削加工精度因素的基础上提出提高铣削加工精度的方法与举措。
标签:铣削加工;加工精度;影响因素;方法举措前言铣削加工是在机械加工中应用较多的一种加工形式,其多应用于平面加工中,相较于磨削加工,铣削加工的加工效率高且能够完成更为复杂结构的加工。
但是在铣削加工的过程中其会受到机床自身、工件材质、刀具等多种因素的影响从而造成工件铣削加工的加工精度无法满足精度要求,做好铣削加工中的影响加工精度的各影响因素的分析并采取相应的应对措施是机械加工中需要注意的问题。
1 影响工件铣削加工精度的因素分析1.1 铣削加工中工件振动对加工精度所造成的影响铣削加工中的振动主要是由于铣削加工过程中的断续加工的加工特点以及铣削加工方式和机床的刚性等方面的原因所导致的,铣削加工过程中的振动将会对铣削加工的加工精度及加工表面的光洁度产生极大的影响。
在铣削加工的过程中由于铣刀是多刃刀具,其在铣削的过程中各刃会断续的切入到待加工工件的表面从而导致在铣削的过程中工件所承受的铣削力在不断的变化进而引起工艺系统的周期性的振动。
当逆铣时铣刀在切入工件表面时会产生一段滑移的距离,会使得铣刀的刀杆在移动的过程中受到周期性的铣削振动。
此外在铣削加工的过程中,机床的主轴、工作台导轨、传动副等都是导致铣削振动产生的重要因素之一。
此外,工件夹具的刚性是否到位也是铣削振动产生的原因之一。
1.2 机床自身精度对于铣削加工精度的影响机床是对工件进行铣削加工的主要的设备,在铣削加工的过程中如果机床自身的精度存在问题将会对工件铣削加工的加工精度造成严重的影响。
机械加工中铣削加工精度的影响因素分析

机械加工中铣削加工精度的影响因素分析在国家发展的过程中,工业制造发挥基础性作用,机械加工制造是工业制造的重要组成部分。
在机械加工的过程中,车削、铣削、刨、磨是其中基础的方式,保证机械加工的进度能够有效保证机械加工的质量。
铣削加工作为其最为重要的加工制造方式,铣削加工的精确度控制非常重要。
在机械加工的过程中,铣削加工精度受到内部和外部环境的影响。
在铣削加工精度控制的过程中,需要了解影响精度的因素,采取针对性的控制措施。
标签:铣削加工;精度控制;影响因素;控制措施在机械加工的过程中,铣削加工作为其常见的加工形式,主要在平面加工的过程中应用。
相对于磨削加工来说,铣削加工的效果更高,在铣削加工的过程中,能够减少由于零部件复杂的原因带来加工困难。
在工业制造铣削加工的过程中,由于机床自身或者其他因素的影响,造成铣削加工的精度降低,达不到机械加工的质量标准。
文章中分析铣削加工精度的影响因素,提出几点铣削加工精度控制的措施,提高我国机械加工的效率和质量。
1 铣削加工精度的影响因素(1)工件振动影响加工精度。
在铣削加工的过程中,振动是影响加工精度的重要因素,主要是由于铣削加工中断续加工、铣削加工方式和机床的刚性造成的,在铣削加工的过程中,由于振动因素对加工精度和加工表面的光洁度影响很大。
铣刀大多数是多刃刀具,加工的过程中,各个刀刃断续的切入到加工工件的表面,导致铣削加工中,工件承受的铣削力切入工件表面时产生一定的振动。
在逆铣的过程中,铣刀在切入表面时出现一定的滑移,使得铣刀的刀杆移动时出现周期性的铣削振动。
另外,在铣削加工中,机床的主轴、工作台导轨等都会造成一定的铣削振动。
(2)机床自身精度的影响。
在工件铣削加工的过程中,机床是主要的机械设备,如果机床自身精度存在问题,对铣削加工的精度造成影响。
如机床的X、Y、Z的轴定位不够精确,影响加工的工件尺寸,主轴的振动也会造成工件表面粗糙度较大。
铣床的工作台面精度也会影响工件的加工精度,工作台面的进度对安装在工作台的夹具以及工件安装进度具有一定影响,同时在加工过程中,尺寸链对机床的铣削加工精度有着一定影响。
数控机床铣削切削力的计算与优化
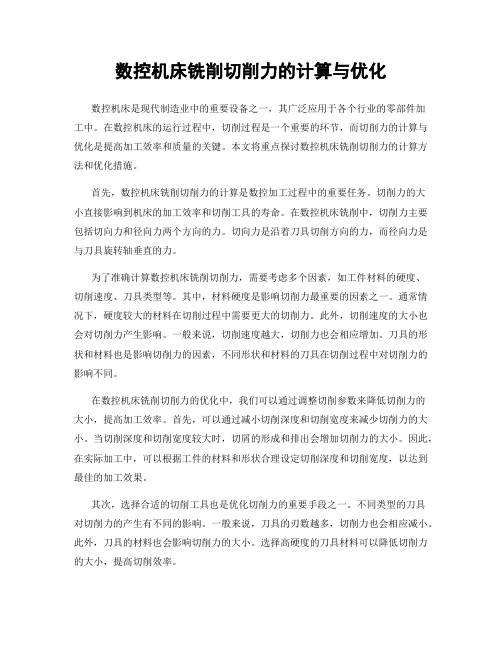
数控机床铣削切削力的计算与优化数控机床是现代制造业中的重要设备之一,其广泛应用于各个行业的零部件加工中。
在数控机床的运行过程中,切削过程是一个重要的环节,而切削力的计算与优化是提高加工效率和质量的关键。
本文将重点探讨数控机床铣削切削力的计算方法和优化措施。
首先,数控机床铣削切削力的计算是数控加工过程中的重要任务。
切削力的大小直接影响到机床的加工效率和切削工具的寿命。
在数控机床铣削中,切削力主要包括切向力和径向力两个方向的力。
切向力是沿着刀具切削方向的力,而径向力是与刀具旋转轴垂直的力。
为了准确计算数控机床铣削切削力,需要考虑多个因素,如工件材料的硬度、切削速度、刀具类型等。
其中,材料硬度是影响切削力最重要的因素之一。
通常情况下,硬度较大的材料在切削过程中需要更大的切削力。
此外,切削速度的大小也会对切削力产生影响。
一般来说,切削速度越大,切削力也会相应增加。
刀具的形状和材料也是影响切削力的因素,不同形状和材料的刀具在切削过程中对切削力的影响不同。
在数控机床铣削切削力的优化中,我们可以通过调整切削参数来降低切削力的大小,提高加工效率。
首先,可以通过减小切削深度和切削宽度来减少切削力的大小。
当切削深度和切削宽度较大时,切屑的形成和排出会增加切削力的大小。
因此,在实际加工中,可以根据工件的材料和形状合理设定切削深度和切削宽度,以达到最佳的加工效果。
其次,选择合适的切削工具也是优化切削力的重要手段之一。
不同类型的刀具对切削力的产生有不同的影响。
一般来说,刀具的刃数越多,切削力也会相应减小。
此外,刀具的材料也会影响切削力的大小。
选择高硬度的刀具材料可以降低切削力的大小,提高切削效率。
最后,数控机床铣削切削力的优化还可以通过提高机床的刚性和减小机床的振动来实现。
刚性越大,机床的抗变形能力越强,切削力产生的变形也会减小。
另外,减小机床的振动可以有效地降低切削力的大小,提高加工质量。
总之,数控机床铣削切削力的计算与优化是提高加工效率和质量的重要任务。
铣削加工中的加工变形机理

铣削加工中的加工变形机理随着制造业的发展,铣削加工成为了重要的加工方法之一。
在铣削加工中,加工变形是一种不可避免的机理,会影响加工质量,造成加工精度不高或者零件变形。
因此,深入了解铣削加工中的加工变形机理是非常必要的。
一、铣削加工中的加工变形机理铣削加工中的加工变形是由多种因素共同作用产生的。
其中,切削力是影响铣削加工变形的主要因素。
在铣削加工中,刀具切削材料时会受到切削力的作用,使工件发生变形。
在切削力的作用下,工件会产生弹性变形和塑性变形两种形式。
其次,材料的物理力学性能也是影响铣削加工变形的重要因素。
材料的强度、韧性和塑性等性质会影响加工变形的程度和形式。
通常来说,材料的韧性和塑性越高,加工变形的程度也就越大。
此外,机床的刚度和精度也会影响铣削加工的加工变形。
机床的刚度越高,承受的切削力就越大,加工变形也就越小。
机床的精度越高,对加工变形的控制就越精准。
因此,在进行铣削加工时,必须选择适合加工工件的机床以及合适的刀具。
最后,切削液的选择和使用也会对加工变形产生影响。
如果使用的切削液不合适,会使刀具与工件之间的摩擦增大,导致加工变形加剧。
二、解决铣削加工中的加工变形问题针对铣削加工中的加工变形问题,有很多的解决方法。
其中,一些常用的方法如下:1. 选择合适的刀具。
选择合适的刀具可以有效降低切削力,控制加工变形。
在选择刀具时,应注意刀具的材料、形状和齿数等因素。
2. 增加机床刚度。
增加机床刚度可以有效减少机床振动,保证加工精度。
3. 优化加工工艺。
针对不同的工件,需要制定不同的加工工艺,包括切削参数、加工顺序、加工表面形状等。
4. 使用适合的切削液。
使用适合的切削液可以减轻切削力,降低工件和刀具的摩擦,有效控制加工变形。
5. 加工中加强测量。
在加工过程中加强测量可以及时发现加工变形的问题,采取相应的调整措施。
三、总结铣削加工中的加工变形是一种普遍存在的机理,可以通过合适的刀具、机床、工艺和切削液等多种因素来控制。
铣削加工中的加工参数优化
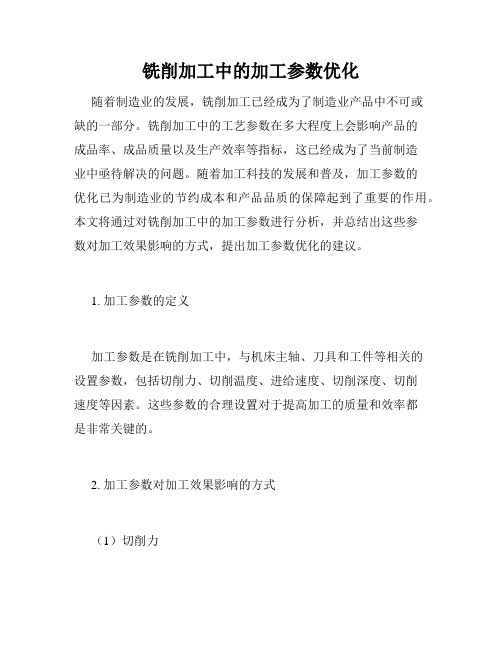
铣削加工中的加工参数优化随着制造业的发展,铣削加工已经成为了制造业产品中不可或缺的一部分。
铣削加工中的工艺参数在多大程度上会影响产品的成品率、成品质量以及生产效率等指标,这已经成为了当前制造业中亟待解决的问题。
随着加工科技的发展和普及,加工参数的优化已为制造业的节约成本和产品品质的保障起到了重要的作用。
本文将通过对铣削加工中的加工参数进行分析,并总结出这些参数对加工效果影响的方式,提出加工参数优化的建议。
1. 加工参数的定义加工参数是在铣削加工中,与机床主轴、刀具和工件等相关的设置参数,包括切削力、切削温度、进给速度、切削深度、切削速度等因素。
这些参数的合理设置对于提高加工的质量和效率都是非常关键的。
2. 加工参数对加工效果影响的方式(1)切削力切削力是指铣削刀具在加工过程中所产生的力。
在铣削加工中,切削力是影响加工精度和表面光洁度的重要因素。
一般来说,理想的切削力应该尽量小,并且保证在加工过程中较为平稳,以减少加工过程中所带来的振动影响。
(2)切削温度切削温度是指在加工过程中所产生的切削界面的温度。
太高的切削温度会导致刀具和工件的表面硬度降低,并且增加了刀具的磨损。
因此,良好的加工参数应该能够保证切削温度在一定的范围内,这可以通过改变切削液的流量和稀释度等措施实现。
(3)进给速度进给速度是指在加工过程中刀具沿着工件表面运动的速度。
与切削速度一样,进给速度也是影响加工效率和产品质量的一个非常关键的因素。
当进给速度太慢时,加工效率低下,并可能导致加工后的表面不光滑;当进给速度太快时,切削力和切削温度会迅速升高,降低铣削刀具的寿命。
(4)切削深度切削深度是指在铣削加工中刀具切削到工件中的深度。
对于深度大于切削刀具半径的工件而言,切削深度是影响加工的关键因素,其影响表现在表面粗糙度、切削时甚至有可能出现切削振动等方面。
(5)切削速度切削速度是指铣削加工中刀具沿着工件表面快速移动的速度。
良好的切削速度应该能够保证加工的精度和表面质量,而且还应该与进给速度等参数进行协调。
铣削实验报告
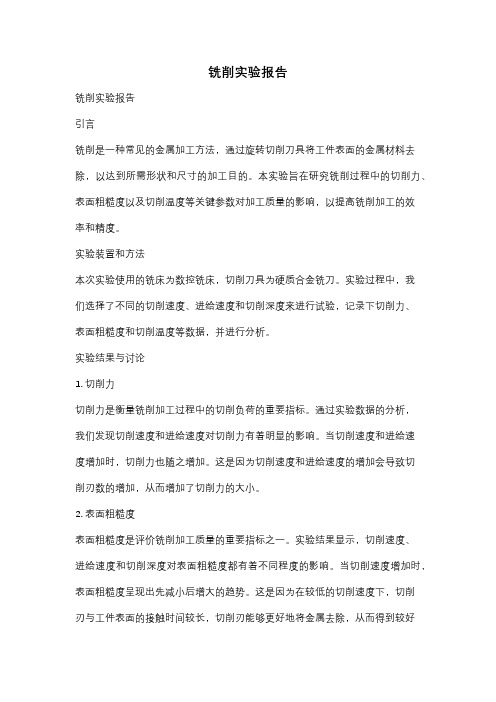
铣削实验报告铣削实验报告引言铣削是一种常见的金属加工方法,通过旋转切削刀具将工件表面的金属材料去除,以达到所需形状和尺寸的加工目的。
本实验旨在研究铣削过程中的切削力、表面粗糙度以及切削温度等关键参数对加工质量的影响,以提高铣削加工的效率和精度。
实验装置和方法本次实验使用的铣床为数控铣床,切削刀具为硬质合金铣刀。
实验过程中,我们选择了不同的切削速度、进给速度和切削深度来进行试验,记录下切削力、表面粗糙度和切削温度等数据,并进行分析。
实验结果与讨论1. 切削力切削力是衡量铣削加工过程中的切削负荷的重要指标。
通过实验数据的分析,我们发现切削速度和进给速度对切削力有着明显的影响。
当切削速度和进给速度增加时,切削力也随之增加。
这是因为切削速度和进给速度的增加会导致切削刃数的增加,从而增加了切削力的大小。
2. 表面粗糙度表面粗糙度是评价铣削加工质量的重要指标之一。
实验结果显示,切削速度、进给速度和切削深度对表面粗糙度都有着不同程度的影响。
当切削速度增加时,表面粗糙度呈现出先减小后增大的趋势。
这是因为在较低的切削速度下,切削刃与工件表面的接触时间较长,切削刃能够更好地将金属去除,从而得到较好的表面质量。
然而,当切削速度过高时,切削刃与工件表面的接触时间变短,导致表面粗糙度增加。
进给速度和切削深度对表面粗糙度的影响与切削速度类似。
3. 切削温度切削温度是铣削加工过程中的另一个重要参数。
实验结果显示,切削速度、进给速度和切削深度对切削温度都有着显著的影响。
当切削速度和进给速度增加时,切削温度也随之增加。
这是因为切削速度和进给速度的增加会导致切削刃与工件之间的摩擦增加,从而产生更多的热量。
切削深度对切削温度的影响也是类似的。
结论通过本次实验,我们研究了铣削过程中的切削力、表面粗糙度和切削温度等关键参数对加工质量的影响。
实验结果表明,切削速度、进给速度和切削深度对这些参数都有着明显的影响。
在实际应用中,我们可以根据需求和要求来选择合适的切削参数,以提高铣削加工的效率和精度。
高速铣削过程铣削力建模与仿真及实验研究的开题报告

高速铣削过程铣削力建模与仿真及实验研究的开题报告一、研究背景及意义高速铣削技术是在高速数控机床上进行的,其主要特点是:切削速度较高,工具进给速度也较高,铣削精度高,加工效率高等。
高速铣削加工技术的出现,不仅极大提高了工件的质量和生产效率,还有望进一步推动制造业的发展。
因此,高速铣削技术的研究和应用具有重要意义。
随着机械加工技术的进步与发展,对于高速铣削过程中铣削力、表面粗糙度、切屑形态、刀具寿命等一系列问题的研究已成为机械工程领域重要的研究方向之一。
铣削加工中的铣削力是一个非常重要的加工参数,具有直接影响到加工效率、加工质量的特点。
因此,研究铣削力的变化规律及其控制方法是提高高速铣削加工质量和效率的必要条件。
而表面粗糙度则是体现工件表面光洁度的重要指标,是直接影响到工件的功能性能的因素之一。
在高速铣削加工过程中,如何有效地预测铣削过程中的铣削力及表面粗糙度,对提高高速铣削加工质量和效率具有非常重要的意义。
因此,铣削力和表面粗糙度的预测是高速铣削加工研究的重要领域之一。
二、研究内容及方法1. 研究内容本研究的主要研究内容包括:(1) 高速铣削过程中刀具与工件的接触状态建模和仿真。
(2) 基于接触状态的铣削力计算与分析。
(3) 高速铣削加工表面粗糙度的预测与控制方法研究。
(4) 高速铣削加工过程中切削刃面磨损的分析及刀具寿命的预测。
2. 研究方法本研究的研究方法主要包括:(1) 基于有限元仿真的高速铣削加工过程建模和仿真。
(2) 基于实验测试数据的高速铣削加工过程力学特性分析。
(3) 基于人工神经网络的高速铣削加工表面粗糙度预测模型的建立。
(4) 组合多种方法,实现高速铣削加工过程中切削刃面磨损的分析及刀具寿命的预测。
三、研究计划及进度1. 研究计划(1) 第一年:建立高速铣削加工过程的有限元仿真模型,分析铣削力的变化规律。
(2) 第二年:基于实验测试数据,分析高速铣削加工过程中的力学特性,并建立高速铣削加工表面粗糙度预测模型。
铣削力计算公式详解

铣削力计算公式详解铣削力是在铣削加工过程中切削刀具对工件所产生的力。
在进行铣削加工时,切削力的大小和刀工的功率直接关系到加工的效率和质量。
因此,对铣削力的计算和分析对于选用合适的切削参数和刀具具有很大的意义。
铣削力的计算是一个复杂的工程问题,涉及到材料力学、切削力学、热力学等多个领域的知识。
通常情况下,我们可以通过经验公式或者专业软件来计算和预测铣削力的大小。
下面将详细介绍铣削力的计算公式及其相关知识。
一、切削力的大小与刀具的进给量、转速、切削深度、切削速度等因素有关。
为了能够有针对性地确定切削参数,我们必须首先了解切削力的计算公式及其影响因素。
铣削力的计算公式通常可以通过以下几种方法进行估算:1.经验公式2.力矩平衡法3.数值模拟下面将分别对这三种方法进行详细介绍。
1.经验公式经验公式是根据大量的实验数据总结得出的,它可以简单、直观地估算切削力的大小。
通常情况下,经验公式需要根据不同的刀具和工件材料来选择不同的参数。
最常用的经验公式之一是菲利普公式,其计算公式为:F_c = K_c * D * d * f其中,F_c为切削力,K_c为切削力系数,D为刀具直径,d为切削深度,f为进给量。
菲利普公式是最简单、最常用的切削力计算公式之一。
但是,它只适用于一定范围内的切削参数和材料。
在实际应用中,由于不同的材料、刀具和加工条件的不同,菲利普公式可能会存在一定的误差。
因此,在进行铣削力计算时,还需要结合实际情况来选择合适的切削力计算公式。
2.力矩平衡法力矩平衡法是一种比较常见的精确计算切削力大小的方法。
它是基于切削力与切削热量之间的平衡关系来进行计算的。
通过分析刀具与工件之间的瞬时力平衡状态,可以得到切削力的大小。
这种方法对于复杂工件和刀具的铣削力计算特别有效。
力矩平衡法的基本思想是:对于切削过程中的每一小段切削刀具,刀具上的切削力与切屑推力之间存在一个平衡关系。
因此,我们可以通过对切屑推力的测量来间接测得切削力的大小。
- 1、下载文档前请自行甄别文档内容的完整性,平台不提供额外的编辑、内容补充、找答案等附加服务。
- 2、"仅部分预览"的文档,不可在线预览部分如存在完整性等问题,可反馈申请退款(可完整预览的文档不适用该条件!)。
- 3、如文档侵犯您的权益,请联系客服反馈,我们会尽快为您处理(人工客服工作时间:9:00-18:30)。
浅议铣削力对铣削过程的影响
摘要铣削力大小和变化对加工过程的稳定性、工件表面质量及刀具的磨损和破损均有着重要影响。
关键词铣削力加工过程稳定性在铣工生产实习教学课题练习中,学生经常会遇到虽然都按照合理的加工工艺进行操作,但工件在铣削过程中仍出现尺寸精度不一致、表面质量不稳定、刀具磨损状况不同等普遍问题,这其中很大因素是由于加工过程中铣削力的变化造成的。
一、铣削力及其分解
1.铣削力是铣刀在切除工件上的材料余量时受到的一种阻力。
它是同时工作的各个刀齿上受到切削力的总和。
总的铣削力主要来自三个方面:a在铣削过程中克服工件材料变形的抗力。
b克服切屑形成过程中工件材料对塑性变形的抗力。
c克服切屑与前刀面的摩擦力和铣刀后刀面与工件已加工表面及过度表面之间的摩擦力。
2.铣削力的分解。
为了对机床、刀具、夹具之间的作用力进行科学分析和研究,我们可将铣削力分解到所研究的方向上,这样就得到如图示的铣削力示意图:圆周分力(主切削力)Fc:铣刀外圆切线方向上的分力。
轴向分力Fa:沿铣刀轴线方向上的分力。
径向分力(垂直切削力)Fp:沿铣刀半径方向上的分力。
如果把主切削力Fc和垂直切削力Fp合成就是切削力R,把切削力R1可以分解成水平分力Fh和垂直分力Fv。
从而可以看出,主切削力Fc消耗机床的主要功率,轴向分力Fa作用在机床的主轴上,垂直分力Fv作用在机床工作面或者是工件上,而水平分力Fh是作用在机床的进给机构上。
切削力作用在主轴轴心上,会影响刀杆的弯曲。
二、铣削力对铣削过程中的影响
1.铣削力对铣削平稳性的影响
铣削加工过程是非连续切削,铣削加工过程中由于切削面积是随着刀具的移动而变化的,所以引起的切削力及力矩也是变化的,是一个动态的数值。
尤其是当同时参加切削得刀齿数量越少时,这种切削力和切削力矩的变化也就越大。
切削力和切削力矩的变化,会引起工艺系统的受力变形、震动、冲击。
这些都会使加工精度、表面质量、机床的寿命和刀具的寿命下降。
如果采用螺旋铣刀、细齿铣刀及多齿铣刀(如多齿飞刀),可以增加同时工作的刀齿数量,从而减小切削过程中切削力和切削力矩的变化,使切削变的平稳。
但要根据不同的加工材料来选择不同的刀具,不是所有的材料在加工过程中都优先选择刀齿数量多的。
例如:在加工有些有色金属(典型如铝件、铜件)时,由于塑性强,使用刀具刀齿过多会使加工过程中产生积屑瘤,易导致加工表面质量下降。
所以,在选择加工刀具时要根据实际的情况而定。
2.铣削力对加工过程中的影响
铣削中的径向分力是通过铣刀作用在刀轴上,易使刀轴产生弯曲变形,增大了铣刀的径向跳动,会影响铣削的加工质量和铣刀刀具的寿命。
因此,在铣刀安装时应尽量靠近主轴,以减小刀轴的变形。
轴向分力Fa会使机床主轴受到轴向拉力或者轴向推力,若铣刀安装不当,会使刀具从主轴中拔出发生安全事故。
故
使用螺旋铣刀铣削时,应使轴向力指向主轴。
a逆铣分析
在逆铣加工中,铣削力R1的垂直分力Fv将工件连同工作台有一个抬起的作用力(如逆铣分析图),而垂直分力Fv亦随着刀齿的切人增大,切出消失。
所以在逆铣加工中,刀齿的频繁切出和切人,会引起工作台和工件的振动,影响了工件加工的表面质量。
例如:用立铣刀铣平面,该力横向作用在工件上,对于狭长的工件,在较大横向力作用下易产生弯曲变形,造成铣削振动,影响加工质量。
另外,切削力R1的水平分力Fh方向与工件的进给方向相反,所以逆铣时需要的进给功率较大。
对于卧式机床逆铣时,垂直分力方向向上,会把工件连同工作台一起向上抬。
因此,易使工作台产生跳动。
对于加工长而薄,刚性差的工件是不适合的。
而在卧式机床上用顺铣,垂直分力Fv方向向下压着工件,所以,适合加工薄而长的工件。
b.顺铣分析
铣削力R1的水平分力Fh通过工件作用在进给机构上,顺铣时水平分力Fh 与工作台的移动方向相同(如顺铣分析图),当丝杆和螺母之间存在间隙时而没有消除间隙时,若水平分力较小,工作台的进给机构仍由丝杆驱动,当水平分力Fh变的足够大时,工作台便会由水平分力Fh驱动,这样在铣削时会使工作台产生窜动,易导致铣刀的刀齿因受到窜动冲击而损坏。
因此,顺铣时首先要消除机床丝杆与螺母的间隙。
普通铣床大多采用滑动导轨,并且之间的间隙不易调整,所以在生产加工中采用顺铣会产生以上缺点。
总之,铣削力对铣削过程中的影响因素是很多的,因此在铣削加工时应充分考虑铣削力大小对加工质量的影响,从而寻求最优化的加工方法和铣削刀具,来保证零件精度、机床寿命及生组织的要求。
参考文献:
[1]周泽华.金属切削原理[M].上海:上海科学技术出版社,1984.
[2]顾熙棠.金属切削机床[M].上海:上海科学技术出版社,1994.
[3]陈海魁.铣工工艺学[M].北京:中国劳动社会保障出版社,2006.。