高炉冶炼物料平衡计算
《高炉炼铁技术》项目11任务11.2物料平衡

另外,H2参加还原反应,即相当于同体积的CO参加反应,所以C02生成量中应减去 55.59米3。 总计间接还原生成C02量:139.58+208.98+0.05—55.59=293.O2米3 石灰石分解出C02量:16.85×0.4543×22.4/44=3.90米3 焦炭挥发分的C02量:450×0.0033×22.4/44=0.76米3 混合矿分解出C02量:1808.11×0.0115×22.4/44=10.59米3 煤气中总C02量:
1107.63+1.98+0.21+0.25=1110.07米3
根据计算,列出煤气成分表如下:
四、编制物料平衡表 1.计算鼓风重量 1米3鼓风重量: 全部鼓风重量:1423.41×1.28=1821.96公斤
2.计算煤气重量 1米3煤气重量:
全部煤气重量: 20O2.08×1.321=2644.75公斤
[评价观测点]
1.能否正确的进行物料平衡计算,并编制物料平衡表。 2.给定酒钢原料成分和冶炼焦比、配矿比、喷煤比等已知条件,
进行物料平衡计算。
谢谢!
二、根据碳平衡计算风量
1.风口前燃烧的碳量 焦炭带入固定碳量:450×0.8563=385.34公斤 煤粉带人固定碳量:75×0.6784=50.88公斤 重油带入固定碳量:46×0.86=39.56公斤 共计燃料碳量:385.34+50.88+39.56=475.78公斤
二、根据碳平衡计算风量
293.O2+3.90+0.76+10.59=308.27米3
4.CO
炼钢物料平衡热平衡计算概述
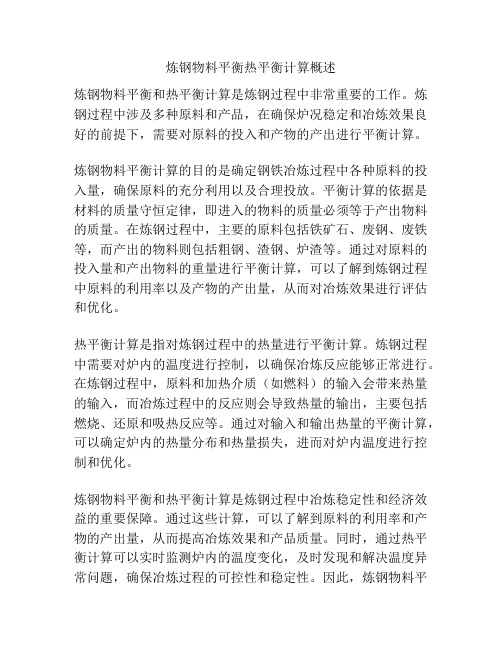
炼钢物料平衡热平衡计算概述炼钢物料平衡和热平衡计算是炼钢过程中非常重要的工作。
炼钢过程中涉及多种原料和产品,在确保炉况稳定和冶炼效果良好的前提下,需要对原料的投入和产物的产出进行平衡计算。
炼钢物料平衡计算的目的是确定钢铁冶炼过程中各种原料的投入量,确保原料的充分利用以及合理投放。
平衡计算的依据是材料的质量守恒定律,即进入的物料的质量必须等于产出物料的质量。
在炼钢过程中,主要的原料包括铁矿石、废钢、废铁等,而产出的物料则包括粗钢、渣钢、炉渣等。
通过对原料的投入量和产出物料的重量进行平衡计算,可以了解到炼钢过程中原料的利用率以及产物的产出量,从而对冶炼效果进行评估和优化。
热平衡计算是指对炼钢过程中的热量进行平衡计算。
炼钢过程中需要对炉内的温度进行控制,以确保冶炼反应能够正常进行。
在炼钢过程中,原料和加热介质(如燃料)的输入会带来热量的输入,而冶炼过程中的反应则会导致热量的输出,主要包括燃烧、还原和吸热反应等。
通过对输入和输出热量的平衡计算,可以确定炉内的热量分布和热量损失,进而对炉内温度进行控制和优化。
炼钢物料平衡和热平衡计算是炼钢过程中冶炼稳定性和经济效益的重要保障。
通过这些计算,可以了解到原料的利用率和产物的产出量,从而提高冶炼效果和产品质量。
同时,通过热平衡计算可以实时监测炉内的温度变化,及时发现和解决温度异常问题,确保冶炼过程的可控性和稳定性。
因此,炼钢物料平衡和热平衡计算是炼钢过程中不可或缺的重要环节。
炼钢物料平衡和热平衡计算在炼钢过程中起着非常重要的作用。
通过这些计算,冶炼厂可以更好地了解和控制物料的投入和产物的产出,实现冶炼过程的稳定运行和优化效果。
首先,炼钢物料平衡计算能够确保原料的充分利用和合理投放。
在炼钢过程中,钢厂会使用不同的原料,如铁矿石、废钢、废铁等。
这些原料的投入量需要经过平衡计算来确定,以确保原料的利用率最大化。
通过平衡计算,可以了解到每种原料的投入量,避免过量或不足的情况发生。
《高炉炼铁技术》项目11任务11.2物料平衡
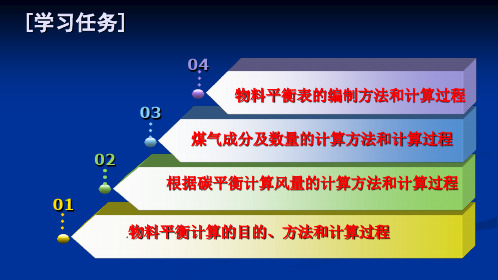
04
物料平衡表的编制方法和计算过程 03
煤气成分及数量的计算方法和计算过程 02
根据碳平衡计算风量的计算方法和计算过程 01
.物料平衡计算的目的、方法和计算过程
一、原始条件
本例取大自然湿度为12克/米3(f=1.5%) 3.假定焦炭和喷吹物总碳量1.2%的碳与H2反响生 成CH4(纯焦炭冶炼时可取0.5%~1.0%)
[评价观测点]
1.能否正确的进行物料平衡计算,并编制物料 平衡表。
2.给定酒钢原料成分和冶炼焦比、配矿比、喷 煤比等条件,进行物料平衡计算。
谢谢!
重油分解出的H2量: 煤粉分解出H2量:
入炉总H2量: 在喷吹条件下一般有40%的H2参加复原,所以参加复原的H2量为:
生成CH4的H2量: 进人煤气的H2量:
3.C02
由Fe2O3复原FeO所生成的C02:
由FeO复原成Fe所生成的C02:
由MnO2复原成Байду номын сангаасnO生成的C02:
另外,H2参加复原反响,即相当于同体积的CO参加反响,所以C023。 总计间接复原生成C02量: 石灰石分解出C02量: 焦炭挥发分的C02量: 混合矿分解出C02量: 煤气中总C02量: 293.O2+3.90+0.76+10.59=308.27米3
C风 文字式:C风=∑C燃-[C]×103-∑C直-CCH4
C风占总人炉炭量: 330.40/475.78=69.46%
2.计算风量 3/米3 风口前燃烧碳素需要氧量:
三、计算煤气成分及数量
1.CH4 由燃料碳索生成CH43 焦炭挥发分含CH43 进人煤气的CH43
2.H2
由鼓风中水分分解出H2:3 焦炭挥发分及有机物的H2量:
3 高炉物料平衡计算
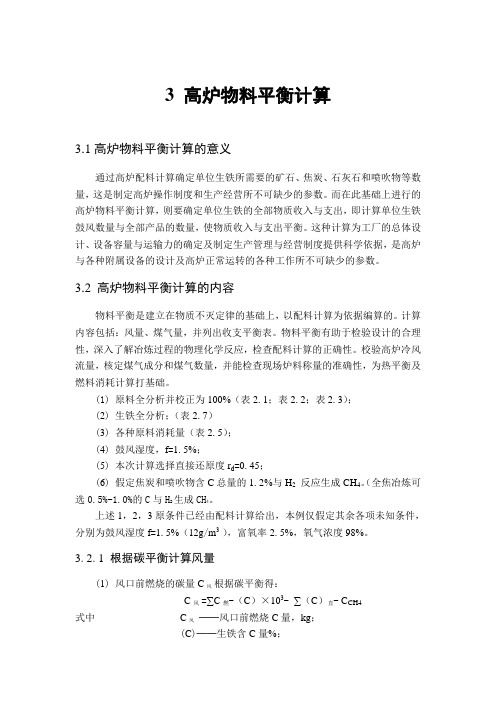
3 高炉物料平衡计算3.1高炉物料平衡计算的意义通过高炉配料计算确定单位生铁所需要的矿石、焦炭、石灰石和喷吹物等数量,这是制定高炉操作制度和生产经营所不可缺少的参数。
而在此基础上进行的高炉物料平衡计算,则要确定单位生铁的全部物质收入与支出,即计算单位生铁鼓风数量与全部产品的数量,使物质收入与支出平衡。
这种计算为工厂的总体设计、设备容量与运输力的确定及制定生产管理与经营制度提供科学依据,是高炉与各种附属设备的设计及高炉正常运转的各种工作所不可缺少的参数。
3.2高炉物料平衡计算的内容物料平衡是建立在物质不灭定律的基础上,以配料计算为依据编算的。
计算内容包括:风量、煤气量,并列出收支平衡表。
物料平衡有助于检验设计的合理性,深入了解冶炼过程的物理化学反应,检查配料计算的正确性。
校验高炉冷风流量,核定煤气成分和煤气数量,并能检查现场炉料称量的准确性,为热平衡及燃料消耗计算打基础。
(1) 原料全分析并校正为100%(表2.1;表2.2;表2.3);(2) 生铁全分析;(表2.7)(3) 各种原料消耗量(表2.5);(4) 鼓风湿度,f=1.5%;(5) 本次计算选择直接还原度r d=0.45;(6) 假定焦炭和喷吹物含C总量的1.2%与H2反应生成CH4。
(全焦冶炼可选0.5%-1.0%的C与H2生成CH4。
上述1,2,3原条件已经由配料计算给出,本例仅假定其余各项未知条件,分别为鼓风湿度f=1.5%(12g/m3),富氧率2.5%,氧气浓度98%。
3.2.1根据碳平衡计算风量(1) 风口前燃烧的碳量C风根据碳平衡得:C风=∑C燃-(C)×103- ∑(C)直- C CH4式中C风──风口前燃烧C量,kg;(C)──生铁含C量%;∑C 燃 ,∑C 直 ,C CH4 ──分别为燃料带入C 量,直接还原耗C 和生成CH 4的C 量,㎏[2];按上式分别进行计算:燃料带入的C=m (C )J +m (C )M =360×0.8672+160×0.7624=434.17kg 溶于生铁的C =44.8kg直接还原耗碳=m (C )Mn+m (C )Si+m (C )P+m (C )Fe=0.7×5512+3.5×2824+0.7×6260+950×0.45×5612=0.15+3+0.68+91.60=95.43kg生成CH 4耗碳=434.17×0.012=5.21 kg风口前燃烧的C 量=434.17-44.8-95.43-5.21=288.73(290.97) kg ,占入炉总碳量的67.01%。
高炉冶炼物料平衡计算

高炉冶炼综合计算概述组建炼铁车间(厂)或新建高炉,都必须依据产量以及原料和燃料条件作为高炉冶炼综合计算包括配料计算、物料平衡计算和热平衡计算。
从计算中得到原料、燃料消耗量及鼓风消耗量等,得到冶炼主要产品(除生铁以外)煤气及炉渣产生量等基本参数。
以这些参数为基础作炼铁车间(厂)或高炉设计。
计算之前,首先必须确定主要工艺技术参数。
对于一种新的工业生产装置,应通过实验室研究、半工业性试验、以致于工业性试验等一系列研究来确定基本工艺技术参数。
高炉炼铁工艺已有200余年的历史,技术基本成熟,计算用基本工艺技术参数的确定,除特殊矿源应作冶炼基础研究外,一般情况下都是结合地区条件、地区高炉冶炼情况予以分析确定。
例如冶炼强度、焦比、有效容积利用系数等。
计算用的各种原料、燃料以及辅助材料等必须作工业全分析,而且将各种成分之总和换算成100%,元素含量和化合物含量要相吻合。
将依据确定的工艺技术参数、原燃料成分计算出单位产品的原料、燃料以及辅助材料的消耗量,以及主、副产品成分和产量等,供车间设计使用。
配料计算也是物料平衡和热平衡计算的基础。
依据质量守恒定律,投入高炉物料的质量总和应等于高炉排出物料的质量总和。
物料平衡计算可以验证配料计算是否准确无误,也是热平衡计算的基础。
物料平衡计算结果的相对误差不应大于%。
常用的热平衡计算方法有两种。
第一种是根据热化学的盖斯定律,即按入炉物料的初态和出炉物料的终态计算,而不考虑炉内实际反应过程。
此法又称总热平衡法。
它的不足是没有反应出高炉冶炼过程中放热反应和吸热反应所发生的具体空间位置,这种方法比较简便,计算结果可以判断高炉冶炼热工效果,检查配料计算各工艺技术参数选取是否合理,它是经常采用的一种计算方法。
第二种是区域热平衡法。
这种方法以高炉局部区域为研究对象,常将高炉下部直接还原区域进行热平衡计算,计算其中热量的产生和消耗项目,这比较准确地反应高炉下部实际情况,可判断炉内下部热量利用情况,以便采取相应的技术措施。
炼铁高炉物料平衡
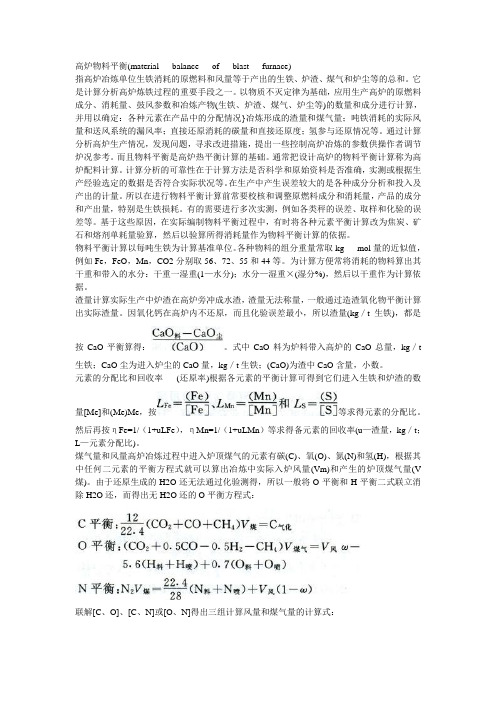
高炉物料平衡(material balance of blast furnace)指高炉冶炼单位生铁消耗的原燃料和风量等于产出的生铁、炉渣、煤气和炉尘等的总和。
它是计算分析高炉炼铁过程的重要手段之一。
以物质不灭定律为基础,应用生产高炉的原燃料成分、消耗量、鼓风参数和冶炼产物(生铁、炉渣、煤气、炉尘等)的数量和成分进行计算,并用以确定:各种元素在产品中的分配情况}冶炼形成的渣量和煤气量;吨铁消耗的实际风量和送风系统的漏风率;直接还原消耗的碳量和直接还原度;氢参与还原情况等。
通过计算分析高炉生产情况,发现问题,寻求改进措施,提出一些控制高炉冶炼的参数供操作者调节炉况参考。
而且物料平衡是高炉热平衡计算的基础。
通常把设计高炉的物料平衡计算称为高炉配料计算。
计算分析的可靠性在于计算方法是否科学和原始资料是否准确,实测或根据生产经验选定的数据是否符合实际状况等。
在生产中产生误差较大的是各种成分分析和投入及产出的计量。
所以在进行物料平衡计算前常要校核和调整原燃料成分和消耗量,产品的成分和产出量,特别是生铁损耗。
有的需要进行多次实测,例如各类秤的误差、取样和化验的误差等。
基于这些原因,在实际编制物料平衡过程中,有时将各种元素平衡计算改为焦炭、矿石和熔剂单耗量验算,然后以验算所得消耗量作为物料平衡计算的依据。
物料平衡计算以每吨生铁为计算基准单位。
各种物料的组分重量常取kg mol量的近似值,例如Fe,FeO,Mn,CO2分别取56、72、55和44等。
为计算方便常将消耗的物料算出其干重和带入的水分:干重一湿重(1—水分);水分—湿重×(湿分%),然后以干重作为计算依据。
渣量计算实际生产中炉渣在高炉旁冲成水渣,渣量无法称量,一般通过造渣氧化物平衡计算出实际渣量。
因氧化钙在高炉内不还原,而且化验误差最小,所以渣量(kg/t生铁),都是按CaO平衡算得:。
式中CaO料为炉料带入高炉的CaO总量,kg/t生铁;CaO尘为进入炉尘的CaO量,kg/t生铁;(CaO)为渣中CaO含量,小数。
高炉物料平衡和热平衡的计算
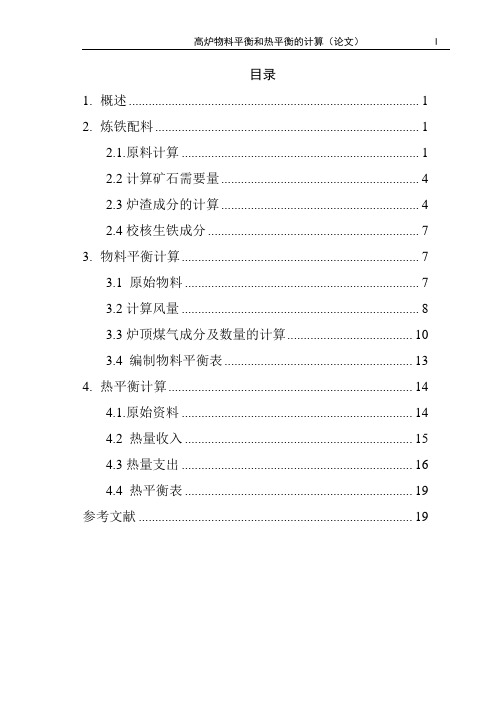
目录1.概述 (1)2.炼铁配料 (1)2.1.原料计算 (1)2.2计算矿石需要量 (4)2.3炉渣成分的计算 (4)2.4校核生铁成分 (7)3.物料平衡计算 (7)3.1 原始物料 (7)3.2计算风量 (8)3.3炉顶煤气成分及数量的计算 (10)3.4 编制物料平衡表 (13)4.热平衡计算 (14)4.1.原始资料 (14)4.2 热量收入 (15)4.3热量支出 (16)4.4 热平衡表 (19)参考文献 (19)高炉物料平衡和及平衡的计算1.概述在计算物料平衡和热平衡之前,首先必须确定主要工艺技术参数。
对于一种新的工业生产装置,应通过实验室研究、半工业性试验、以致于工业性试验等一系列研究来确定基本工艺技术参数。
高炉炼铁工艺已有200余年的历史,技术基本成熟,计算用基本工艺技术参数的确定,除特殊矿源应作冶炼基础研究外,一般情况下都是结合地区条件、地区高炉冶炼情况予以分析确定。
例如冶炼强度、焦比、有效容积利用系数等。
计算用的各种原料、燃料以及辅助材料等必须作工业全分析,而且将各种成分之总和换算成100%,元素含量和化合物含量要相吻合。
配料计算是高炉操作的重要依据,也是检查能量利用状况的计算基础。
配料计算的目的,在于根据已知的原料条件和冶炼要求来决定矿石和溶剂的用量,以配置合适的炉渣成分和获得合格的生铁。
通常以一吨生铁的原料用量为基础进行计算。
物料平衡是建立在物质不灭定律的基础上,以配料计算为依据编算的。
计算内容包括风量、煤气量、并列出收支平衡表。
物料平衡有助于检验设计的合理性,深入了解冶炼过程的物理化学反应,检查配料计算的正确性,校核高炉冷风流量,核定煤气成分和煤气数量,并能检查现场炉料称量的准确性,为热平衡及燃料消耗计算打基础。
热平衡计算的基础是能量守恒定律,即供应高炉的热量应等于各项热量的消耗;而依据是配料计算和物料平衡计算所得的有关数据。
热平衡计算采用差值法,即热量损失是以总的热量收入,减去各项热量消耗而得到的,即把热量损失作为平衡项,所以热平衡表面上没有误差,因为一切误差都集中掩盖在热损失之重。
炼钢过程中的物料平衡与热平衡计算

炼钢过程的物料平衡与热平衡计算炼钢过程的物料平衡与热平衡计算是建立在物质与能量守恒的基础上.其主要目的是比较整个冶炼过程中物料、能量的收入项和支出项,为改进操作工艺制度,确定合理的设计参数和提高炼钢技术经济指标提供某些定量依据.应当指出,由于炼钢系复杂的高温物理化学过程,加上测试手段有限,目前尚难以做到精确取值和计算。
尽管如此,它对指导炼钢生产和设计仍有重要的意义。
本章主要结合实例阐述氧气顶吹转炉和电弧炉氧化法炼钢过程物料平衡和热平衡计算的基本步骤和方法,同时列出一些供计算用的原始参考数据。
1.1 物料平衡计算(1)计算所需原始数据。
基本原始数据有:冶炼钢种及其成分(表1);金属料—铁水和废钢的成分(表1);终点钢水成分(表1);造渣用溶剂及炉衬等原材料的成分(表2);脱氧和合金化用铁合金的成分及其回收率(表3);其它工艺参数(表4).①本计算设定的冶炼钢种为H15Mn。
②[C]和[Si]按实际生产情况选取;[Mn]、[P]和[S]分别按铁水中相应成分含量的30%、10%和60%留在钢水中设定。
表2 原材料成分①10%C与氧生产CO2收入项有:铁水、废钢、溶剂(石灰、萤石、轻烧白云石)、氧气、炉衬蚀损、铁合金。
支出项有:钢水、炉渣、烟尘、渣中铁珠、炉气、喷溅。
(3)计算步骤。
以100kg铁水为基础进行计算.第一步:计算脱氧和合金化前的总渣量及其成分.总渣量包括铁水中元素氧化、炉衬蚀损和加入溶剂的成渣量.其各项成渣量分别列于表5、6和7。
总渣量及其成分如表8所示.第二步:计算氧气消耗量。
氧气实际消耗量系消耗项目与供入项目之差,详见表9。
表7 加入溶剂的成渣量(SiO2)=0。
857+0.009+0.028+0.022=0。
914kg。
因设定的终渣碱度R=3.5;故石灰加入量为:[R∑w(SiO2)-∑w(CaO)]/[w(CaO石灰)-R×w(SiO2石灰)]= 2。
738/(88。
00%-3.5×2.50%)=3。
高炉炼铁计算
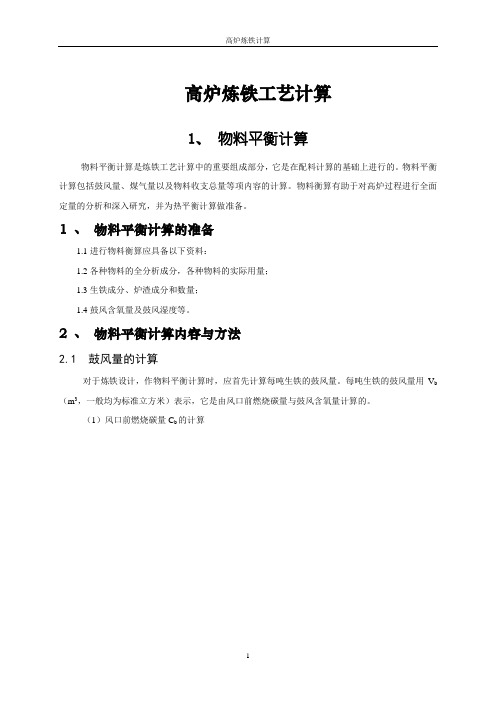
高炉炼铁工艺计算1、物料平衡计算物料平衡计算是炼铁工艺计算中的重要组成部分,它是在配料计算的基础上进行的。
物料平衡计算包括鼓风量、煤气量以及物料收支总量等项内容的计算。
物料衡算有助于对高炉过程进行全面定量的分析和深入研究,并为热平衡计算做准备。
1 、物料平衡计算的准备1.1进行物料衡算应具备以下资料:1.2各种物料的全分析成分,各种物料的实际用量;1.3生铁成分、炉渣成分和数量;1.4鼓风含氧量及鼓风湿度等。
2 、物料平衡计算内容与方法2.1 鼓风量的计算对于炼铁设计,作物料平衡计算时,应首先计算每吨生铁的鼓风量。
每吨生铁的鼓风量用V b (m3,一般均为标准立方米)表示,它是由风口前燃烧碳量与鼓风含氧量计算的。
(1)风口前燃烧碳量C b的计算由碳素平衡图(图2-4)可知b O da dFe C C C C =-- (kg/t ,下同) (2-1)式中 C O ——氧化碳量,kg/t ;C da ——合金元素还原耗碳,kg/t ;C dFe ——铁的直接还原耗碳,kg/t 。
要计算风口前燃烧碳量b C ,则需先计算式中其他各项碳量,它们的计算是1)氧化碳量O C 计算4O f C CH C C C C =--[]410K M CH K C M C C C =⨯+⨯-- (2-2)式中,C C 为生铁渗碳量,由生铁成分计算;4CH C 为生成CH 4碳量,按燃料带入碳量f C 的0.5% ~ 1.2%取值计算;在作炼铁设计时,选定的焦比K 是参加炉内冶炼过程的实际数值,进入炉尘的碳量不包括在内。
2)合金元素还原耗碳da C 的计算()[][][][][])(375.0273.0882.55677.9182.2571.832/)(1244/12102/60][48/24][62/60][55/12][28/24][1022S U CO V Ti P Mn Si S U CO V Ti P Mn Si C da ⨯⨯+⨯⨯Φ⨯+++++=⨯⨯+⨯⨯Φ⨯+⨯+⨯+⨯+⨯+⨯⨯=ΦΦαα式中 []Si ,[]Mn ,[]P ,[]Ti ,[]V ——生铁中相应元素含量,%;Φ ——每吨生铁的石灰石用量,kg ;2CO φ——石灰石中CO 2含量;α——石灰石在高温区分解率,通常取α = 0.5;U —— 每吨生铁的渣量,kg ;()S ——渣中硫含量。
炼铁物料平衡及能量平衡计算
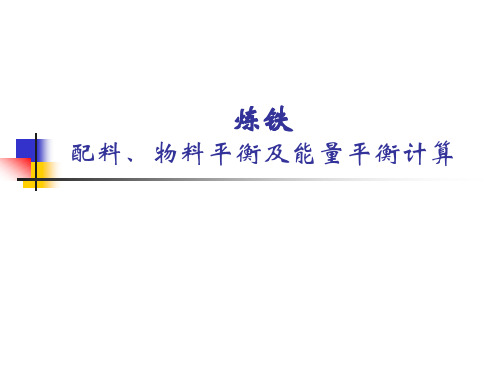
1
23456 7
8 9 10
产 品 Fe Mn V Nb Ti Cr Cu K,Na P S
生 铁 0.9975 0.70 0.8 0.70 0.10 0.85 1.00
1.00
炉 渣 0.0025 0.30 0.2 0.30 0.90 0.15
0.95 0.00
炉渣粘度以1450~1500℃(炉缸温度)时,0.2~0.6Pas为好。
炉渣性能和脱硫能力验算
脱硫能力:
按拉姆教授的最低碱性氧化物经验公式:
(RO)min
ቤተ መጻሕፍቲ ባይዱ
50 0.25(Al2O3) 3(S)
0.3[Si] 30[S] u
要求:实际(RO) = (CaO)+(MgO)+(MnO)+(FeO) (RO)min 。
元素和化合物的存在状态
焦炭:
工业分析:CF、S(有机硫为主)、灰分、挥发分、
Moist
化学分析:
以Fe2O3给出,需折算
灰分: CaO、SiO2、MgO、Al2O3、P2O5、FeO、FeS 挥发分:CO、CO2、CH4、H2、N2
煤粉:
工业分析:CF、S、灰分、挥发分、H2O 化学分析:
Q
R0
SiO 2矿 SiO 2尘
SiO 2废 SiO 2焦 60 28 10 [Si]
SiO
2喷
CaO 矿 CaO
喷
CaO废 CaO尘
CaO 焦
CaO%熔 R 0 SiO 2 %熔
SiO2矿 = 矿石量 SiO2%矿 SiO2废 = 废铁量 SiO2%废 SiO2焦 = 干焦比 SiO2%焦灰 SiO2喷 = 喷吹量 SiO2%喷 SiO2尘 = 炉尘量 SiO2%尘
炼钢过程中的物料平衡与热平衡计算
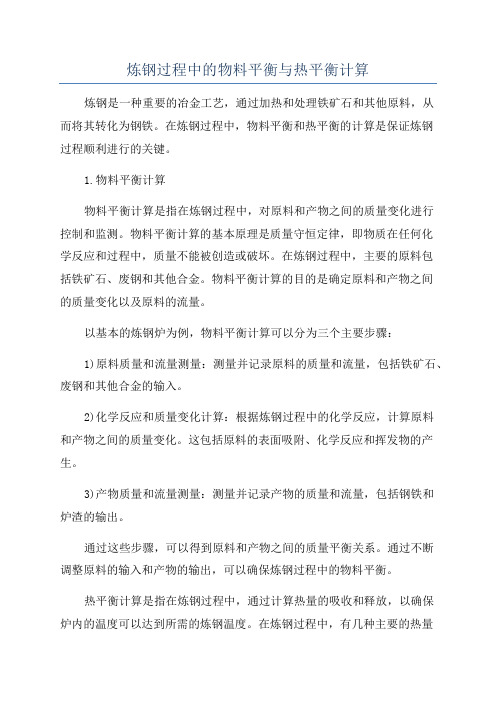
炼钢过程中的物料平衡与热平衡计算炼钢是一种重要的冶金工艺,通过加热和处理铁矿石和其他原料,从而将其转化为钢铁。
在炼钢过程中,物料平衡和热平衡的计算是保证炼钢过程顺利进行的关键。
1.物料平衡计算物料平衡计算是指在炼钢过程中,对原料和产物之间的质量变化进行控制和监测。
物料平衡计算的基本原理是质量守恒定律,即物质在任何化学反应和过程中,质量不能被创造或破坏。
在炼钢过程中,主要的原料包括铁矿石、废钢和其他合金。
物料平衡计算的目的是确定原料和产物之间的质量变化以及原料的流量。
以基本的炼钢炉为例,物料平衡计算可以分为三个主要步骤:1)原料质量和流量测量:测量并记录原料的质量和流量,包括铁矿石、废钢和其他合金的输入。
2)化学反应和质量变化计算:根据炼钢过程中的化学反应,计算原料和产物之间的质量变化。
这包括原料的表面吸附、化学反应和挥发物的产生。
3)产物质量和流量测量:测量并记录产物的质量和流量,包括钢铁和炉渣的输出。
通过这些步骤,可以得到原料和产物之间的质量平衡关系。
通过不断调整原料的输入和产物的输出,可以确保炼钢过程中的物料平衡。
热平衡计算是指在炼钢过程中,通过计算热量的吸收和释放,以确保炉内的温度可以达到所需的炼钢温度。
在炼钢过程中,有几种主要的热量转移方式,包括辐射、传导、对流和蒸发。
热平衡计算的基本原理是能量守恒定律,即能量不能被创造或破坏。
热平衡计算可以分为以下几个步骤:1)炉内温度测量:通过在炉内安装温度传感器,可以测量和记录炉内的温度分布。
2)热量输入和输出计算:通过测量原料的热量输入和产物的热量输出,可以计算总的热量平衡。
热量输入包括燃料燃烧生成的热量和化学反应产生的热量。
热量输出包括炉渣的热量、废气的热量以及钢铁的热量。
3)热量转移计算:通过计算炉内热量的传导、辐射、对流和蒸发,可以确定炉内的热量分布。
这可以通过数学模型和计算方法进行计算。
通过热平衡计算,可以确定炉内的温度分布,并根据需要进行调整。
高炉冶炼物料平衡计算

热风炉系统:冷风管、热风管、冷风阀、热风阀、混风阀、倒流阀、空气燃烧阀、煤气燃烧阀、均压阀、废气阀、烟道阀、热风炉本体及各人孔和连接法兰。
人员准备:检漏试压必须有专人指挥,分区域检漏和监视。
施工方、技改部、监理、动力、安环处等有关部门必须到位。
4.3配备充足的通讯设备、肥皂水、红墨水、安全带、记号笔。
4.4在检漏过程中,发现一般泄漏只需作上记号和记录,以便统一处理和复查;如发现严重泄漏或易引发事故的险情时,应立即终止试压和检漏,待险情排除后再重新检漏和试压。
检漏时要避开人孔和堵头正面。
4.5检漏、试压应分段进行,从50KPa开始,每次升压不得超过50KPa,每升一次压最少稳压30min钟,压力到200KPa时关闭所有干法箱体的进口盲板阀和蝶阀,然后再升压到250KPa,计划稳压时间和区域见表9,具体时间可根据检漏情况确定。
4.6检漏、试压前所有波纹补偿器和相关管道的定位螺栓应解开,拉紧螺栓应紧固。
表9试压、试漏方案表
检漏试压程序:
关闭热风炉所有燃烧阀、烟道阀、废气阀、倒流阀、冷风阀、热风阀。
送风支管盲板堵好后,重新送风对热风炉、热风围管试压至350KPa,同时进一步检漏。
5.11当压力升至350KPa时,三座热风炉逐个关均压阀,开废气阀,对热风阀、冷风阀、燃烧阀、烟道阀、均压阀进行观察,检查泄漏情况。
6 以上程序全部完毕,即高炉热风炉检漏试压完成。
2000m3高炉炉型设计及物料平衡计算1

2000m3高炉炉型设计及物料平衡计算摘要:本设计要求建2000m3炼铁高炉。
设计主要内容包括高炉炉型设计计算及高炉本体立剖图,同时对所设计高炉的特点进行简述。
设计高炉有效容积为2000m3,高径比取 2.3,高炉利用系数取值为 2.0,据此设计高炉炉型。
设计本着优质、高产、低耗和对环境污染小的宗旨,为日产生铁4000t的高炉提供高炉内型设计。
并对2000m3炼铁高炉进行物料平衡计算,物料平衡计算是炼铁工艺计算中重要组成部分,它是在配料计算的基础上进行的。
整个物料平衡计算有配料计算和物料衡算两部分构成。
在配料计算过程中,进行了原料和燃料的全分析,渣铁成分及含量分析;在物料衡算过程中计算了包括鼓风量、煤气量以及物料收支总量等项内容的计算,并制作物料平衡表。
关键词:高炉发展;高炉炉型;炉型计算;物料平衡配料计算物料衡算物料平衡表绪论最近二十年来,日本和欧盟区的在役高炉座数由1990年的65座和92座下降到28座和58座,下降幅度分别为56.9%和37%,但是高炉的平均容积却分别由1558m3和1690m3上升到4157m3和2063m3,上升幅度为166.8%和22%,这基本代表了国外高炉大型化的发展状况。
高冶炼强度、高富氧喷煤比和长寿命化作为大型高炉操作的主要优势受到大家越来越高的关注和青睐,但是高炉大型化作为一项系统工程,它在立足自身条件的基础上仍须匹配的炼钢、烧结和炼焦能力。
我国近年推出的《钢铁产业发展政策》中规定高炉炉容在300m3以下归并为淘汰落后产能项目,且仍存在扩大小高炉容积的淘汰范围的趋势。
同时国内钢铁产业的快速发展均加速了世界和我国高炉大型化的发展进程。
由于大型化高炉具备的单位投资省、效能高和成本低等特点,从而有效地增强了其竞争力。
20世纪高炉容积增长非常快。
20世纪初,高炉炉缸直径4-5m,年产铁水约100000吨左右,原料主要是块矿和焦炭。
20世纪末,最大高炉的炉缸直径达到14-15m,年产铁水300-400万吨。
炼钢物料平衡热平衡计算

烟尘中:FeO=77%;Fe2O3=20%
(做课程设计时可改为:烟尘为铁水量的1.16%)
O2(烟尘中)=1.6×(77%× +20%× )
=0.37[㎏]
三、炉气成分及重量的计算
表1-14
炉气成分
重量,㎏
体积(Nm3)
%
CO
8.663
8.663× =6.925
79.4
CO2
3.235
0.15
—
0.17
0.015
0.025
实测
氧化量
4.19
0.37
0.41
0.135
0.012
转入表1-7
说明:
[Si]——碱性渣操作时终点[Si]量为痕迹;
[P]——单渣发去磷约90%(±5%);
[Mn]——终点余锰量约30~40%,这里实测为30%;
[S]——转炉去硫约30~50%,这里取40%;
烧碱**
1.0×10%=0.2
S
1.0×0.03%=0.0003
1.0×0.03%=0.0003
Al2O3
1.0×0.4%=0.004
共计
3.0
*加入生白云石后经经炉渣成分计算,应满足MgO=6~8%范围(见表1—13),目的是可以提高炉衬抗熔渣的侵蚀能力,提高炉龄。
* *烧碱是指生白云石或石灰中未分解的CO2及其重量。
0.445
3.28
CaS
0.018
0.0045
0.002
0.025
0.22
FeO
0.757
0.757
10.00
Fe2O3
0.378
0.378
5.00
高炉物料平衡计算课程设计
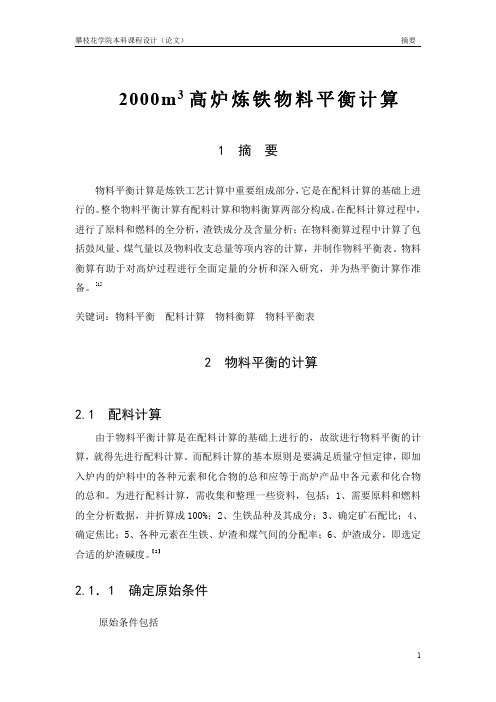
2.1 配料计算
由于物料平衡计算是在配料计算的基础上进行的,故欲进行物料平衡的计 算,就得先进行配料计算。而配料计算的基本原则是要满足质量守恒定律,即加 入炉内的炉料中的各种元素和化合物的总和应等于高炉产品中各元素和化合物 的总和。为进行配料计算,需收集和整理一些资料,包括:1、需要原料和燃料 的全分析数据,并折算成 100%;2、生铁品种及其成分;3、确定矿石配比;4、 确定焦比;5、各种元素在生铁、炉渣和煤气间的分配率;6、炉渣成分,即选定 合适的炉渣碱度。【2】
2.2.1 原始条件的确定
原始条件为:[7] (1)选择确定直接还原度:可根据煤气成分来计算,但较复杂,故这里直 接选定直接还原度 rd = 0.45 。 (2)鼓风湿度 f:这里取大自然湿度为 0.012 Kg/ m3 ,f =1.5% 。 (3)假定入炉碳量 0.5%的碳与 H2 反应生成 CH4(纯焦冶炼可取 0.5%~1.0%, 喷吹燃料时可取 1.2%)。
MgO
2.02 0.12 0.52 1.49 0.37
Al2O3
1.70 0.43 1.18 1.39 0.27
MnO S
P
Fe2O3
0.62 0.023 0.041 2.39 0.010 0.035 1.05 0.210 0.023 1.02 0.039 0.038 66.20
0.01 0.004
(2)根据碱度平衡求石灰石用量: 混合矿带入的 CaO 量:1694.47×0.0859 = 145.55 ㎏ 焦炭带入的 CaO 量:450×0.1350×0.0434 =2.64 ㎏ 煤粉带入的 CaO 量:90×0.0062 = 0.57 ㎏ 共带入的 CaO 量:145.55 + 2.64 +0.57 =148.76 ㎏ 混合矿带入的 SiO2 量:1694.47×0.0745 = 126.24 ㎏ 焦炭带入的 SiO2 量:450×0.1350×0.5400 = 32.81 ㎏ 煤粉带入的 SiO2 量: 90×0.0876 = 7.88 ㎏ 共带入的 SiO2 量:126.24 + 32.81 + 7.88 = 166.93 ㎏ 还原 Si 消耗的 SiO2 量:3×(60÷28)= 6.43 ㎏ 石灰石用量:[(166.93-6.43)×1.04-148.76]/(0.5402-0.0138× 1.04)=34.53 ㎏ 考虑到机械损失及水分,则每吨生铁的原料实际用量列于表 8
炼钢过程物料平衡和热平衡计算

炼钢过程物料平衡和热平衡计算炼钢过程是将生铁或者其他铁合金通过熔炼等一系列工艺操作得到所需成分和性能的钢的过程。
在炼钢过程中,物料平衡和热平衡计算是非常重要的。
物料平衡计算是炼钢过程中的一项重要工作,其目的是通过计算物料的进出量,确定每个工序中原料和产物的平衡情况,以便控制和优化炼钢过程。
炼钢过程中常用的物料平衡计算方法有材料平衡和元素平衡两种。
材料平衡计算主要是根据原料的进出量和成分,以及每个工序中材料的变化情况,来计算各种物料的平衡情况。
以炼钢高炉为例,其主要原料是铁矿石、焦炭和空气,通过冶金反应得到生铁和炉渣。
在材料平衡计算中,需要考虑到进料的质量和数量,以及冶金反应中矿石的还原程度、焦炭的燃烧程度等因素。
通过对每个工序中原料和产物的物料平衡计算,可以确定炉内各种物料的流动情况和变化规律,以便优化炼钢过程,提高钢的质量和产量。
元素平衡计算是针对炼钢过程中的元素进行的平衡计算。
炼钢过程中,除了铁、碳、硅、锰等主要元素外,还有许多杂质元素,如磷、硫、氧等。
元素平衡计算需要考虑每个工序中元素的进出量,以及元素在冶金反应中的分配情况。
通过元素平衡计算,可以确定炼钢过程中每个工序的杂质元素的分布情况,以便进行相应的处理和控制,保证钢的质量符合要求。
热平衡计算是炼钢过程中的另一个重要工作,其目的是通过计算炼钢过程中的热量进出量,了解各个工序的热平衡情况,以便合理利用热能,优化炼钢过程。
炼钢过程中产生的热量主要有焦炭燃烧产生的热量、冶金反应放热产生的热量、热风和燃料的预热热量等。
热平衡计算中需要考虑的因素有炉内热量的进出量、热量的耗散和损失等。
通过热平衡计算,可以确定每个工序中热量的平衡情况,以便根据热量的分布和变化,进行相应的热能利用优化。
在炼钢过程中进行物料平衡和热平衡计算,可以帮助把握炼钢过程中材料和热量的变化规律,从而更好地控制和优化整个过程。
这对于提高炼钢质量、降低成本具有重要意义。
同时,物料平衡和热平衡计算也为炼钢过程的模拟和仿真提供了基础数据,为炼钢工艺的改进和创新提供了理论依据。
高炉冶炼物料平衡计算
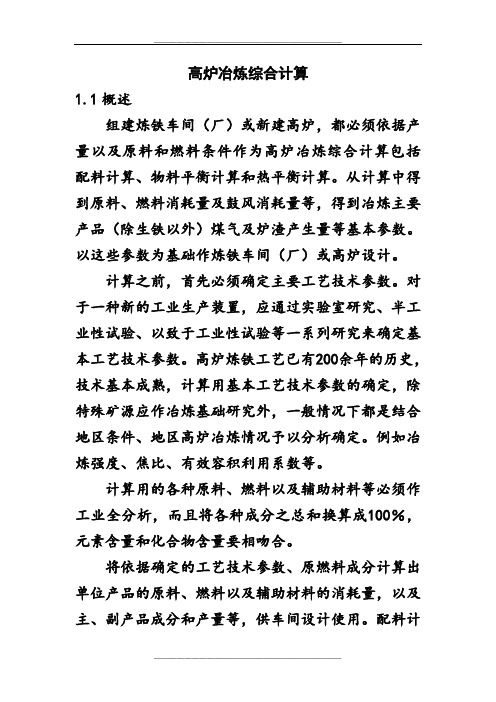
高炉冶炼综合计算1.1概述组建炼铁车间(厂)或新建高炉,都必须依据产量以及原料和燃料条件作为高炉冶炼综合计算包括配料计算、物料平衡计算和热平衡计算。
从计算中得到原料、燃料消耗量及鼓风消耗量等,得到冶炼主要产品(除生铁以外)煤气及炉渣产生量等基本参数。
以这些参数为基础作炼铁车间(厂)或高炉设计。
计算之前,首先必须确定主要工艺技术参数。
对于一种新的工业生产装置,应通过实验室研究、半工业性试验、以致于工业性试验等一系列研究来确定基本工艺技术参数。
高炉炼铁工艺已有200余年的历史,技术基本成熟,计算用基本工艺技术参数的确定,除特殊矿源应作冶炼基础研究外,一般情况下都是结合地区条件、地区高炉冶炼情况予以分析确定。
例如冶炼强度、焦比、有效容积利用系数等。
计算用的各种原料、燃料以及辅助材料等必须作工业全分析,而且将各种成分之总和换算成100%,元素含量和化合物含量要相吻合。
将依据确定的工艺技术参数、原燃料成分计算出单位产品的原料、燃料以及辅助材料的消耗量,以及主、副产品成分和产量等,供车间设计使用。
配料计算也是物料平衡和热平衡计算的基础。
依据质量守恒定律,投入高炉物料的质量总和应等于高炉排出物料的质量总和。
物料平衡计算可以验证配料计算是否准确无误,也是热平衡计算的基础。
物料平衡计算结果的相对误差不应大于0.25%。
常用的热平衡计算方法有两种。
第一种是根据热化学的盖斯定律,即按入炉物料的初态和出炉物料的终态计算,而不考虑炉内实际反应过程。
此法又称总热平衡法。
它的不足是没有反应出高炉冶炼过程中放热反应和吸热反应所发生的具体空间位置,这种方法比较简便,计算结果可以判断高炉冶炼热工效果,检查配料计算各工艺技术参数选取是否合理,它是经常采用的一种计算方法。
第二种是区域热平衡法。
这种方法以高炉局部区域为研究对象,常将高炉下部直接还原区域进行热平衡计算,计算其中热量的产生和消耗项目,这比较准确地反应高炉下部实际情况,可判断炉内下部热量利用情况,以便采取相应的技术措施。
3高炉物料平衡计算

3高炉物料平衡计算3 高炉物料平衡计算3.1高炉物料平衡计算的意义通过高炉配料计算确定单位生铁所需要的矿石、焦炭、石灰石和喷吹物等数量,这是制定高炉操作制度和生产经营所不可缺少的参数。
而在此基础上进行的高炉物料平衡计算,则要确定单位生铁的全部物质收入与支出,即计算单位生铁鼓风数量与全部产品的数量,使物质收入与支出平衡。
这种计算为工厂的总体设计、设备容量与运输力的确定及制定生产管理与经营制度提供科学依据,是高炉与各种附属设备的设计及高炉正常运转的各种工作所不可缺少的参数。
3.2高炉物料平衡计算的内容物料平衡是建立在物质不灭定律的基础上,以配料计算为依据编算的。
计算内容包括:风量、煤气量,并列出收支平衡表。
物料平衡有助于检验设计的合理性,深入了解冶炼过程的物理化学反应,检查配料计算的正确性。
校验高炉冷风流量,核定煤气成分和煤气数量,并能检查现场炉料称量的准确性,为热平衡及燃料消耗计算打基础。
(1) 原料全分析并校正为100%(表2.1;表2.2;表2.3);(2) 生铁全分析;(表2.7)(3) 各种原料消耗量(表2.5);(4) 鼓风湿度,f=1.5%;(5) 本次计算选择直接还原度r d=0.45;(6) 假定焦炭和喷吹物含C总量的1.2%与H2反应生成CH4。
(全焦冶炼可选0.5%-1.0%的C与H2生成CH4。
上述1,2,3原条件已经由配料计算给出,本例仅假定其余各项未知条件,分别为鼓风湿度f=1.5%(12g/m3),富氧率2.5%,氧气浓度98%。
3.2.1根据碳平衡计算风量(1) 风口前燃烧的碳量C风根据碳平衡得:C风=∑C燃-(C)×103- ∑(C)直- C CH4式中C风──风口前燃烧C量,kg;(C)──生铁含C量%;∑C 燃,∑C 直,C CH4 ──分别为燃料带入C 量,直接还原耗C 和生成CH 4的C 量,㎏[2];按上式分别进行计算:燃料带入的C=m (C )J +m (C )M =360×0.8672+160×0.7624=434.17kg 溶于生铁的C =44.8kg 直接还原耗碳=m (C )Mn+m (C )Si+m (C )P+m (C )Fe=0.7×5512+3.5×2824+0.7×6260+950×0.45×5612=0.15+3+0.68+91.60=95.43kg生成CH 4耗碳=434.17×0.012=5.21 kg风口前燃烧的C 量=434.17-44.8-95.43-5.21=288.73(290.97) kg ,占入炉总碳量的67.01%。
- 1、下载文档前请自行甄别文档内容的完整性,平台不提供额外的编辑、内容补充、找答案等附加服务。
- 2、"仅部分预览"的文档,不可在线预览部分如存在完整性等问题,可反馈申请退款(可完整预览的文档不适用该条件!)。
- 3、如文档侵犯您的权益,请联系客服反馈,我们会尽快为您处理(人工客服工作时间:9:00-18:30)。
高炉冶炼综合计算1.1概述组建炼铁车间(厂)或新建高炉,都必须依据产量以及原料和燃料条件作为高炉冶炼综合计算包括配料计算、物料平衡计算和热平衡计算。
从计算中得到原料、燃料消耗量及鼓风消耗量等,得到冶炼主要产品(除生铁以外)煤气及炉渣产生量等基本参数。
以这些参数为基础作炼铁车间(厂)或高炉设计。
计算之前,首先必须确定主要工艺技术参数。
对于一种新的工业生产装置,应通过实验室研究、半工业性试验、以致于工业性试验等一系列研究来确定基本工艺技术参数。
高炉炼铁工艺已有200余年的历史,技术基本成熟,计算用基本工艺技术参数的确定,除特殊矿源应作冶炼基础研究外,一般情况下都是结合地区条件、地区高炉冶炼情况予以分析确定。
例如冶炼强度、焦比、有效容积利用系数等。
计算用的各种原料、燃料以及辅助材料等必须作工业全分析,而且将各种成分之总和换算成100%,元素含量和化合物含量要相吻合。
将依据确定的工艺技术参数、原燃料成分计算出单位产品的原料、燃料以及辅助材料的消耗量,以及主、副产品成分和产量等,供车间设计使用。
配料计算也是物料平衡和热平衡计算的基础。
依据质量守恒定律,投入高炉物料的质量总和应等于高炉排出物料的质量总和。
物料平衡计算可以验证配料计算是否准确无误,也是热平衡计算的基础。
物料平衡计算结果的相对误差不应大于0.25%。
常用的热平衡计算方法有两种。
第一种是根据热化学的盖斯定律,即按入炉物料的初态和出炉物料的终态计算,而不考虑炉内实际反应过程。
此法又称总热平衡法。
它的不足是没有反应出高炉冶炼过程中放热反应和吸热反应所发生的具体空间位置,这种方法比较简便,计算结果可以判断高炉冶炼热工效果,检查配料计算各工艺技术参数选取是否合理,它是经常采用的一种计算方法。
第二种是区域热平衡法。
这种方法以高炉局部区域为研究对象,常将高炉下部直接还原区域进行热平衡计算,计算其中热量的产生和消耗项目,这比较准确地反应高炉下部实际情况,可判断炉内下部热量利用情况,以便采取相应的技术措施。
该计算比较复杂。
要从冶炼现场测取大量工艺数据方可进行。
1.2配料计算一.设定原料条件1、矿石成分:表1-1原料成分,%2、焦炭成分:表1-2焦炭成分 ,%表1-4预定生铁成分 ,%为Fe 。
C=4.3-0.27Si-0.329P-0.032S+0.3Mn某元素在生铁、炉渣、炉气中的分配率(%)见表1-5表1-5元素分配率分 ,%燃料消耗量(kg/t 生铁):焦炭 360(干) 375(湿) 煤粉 150 kg/t 生铁 鼓风湿度 12g/ m 3相对湿度 φ=100012×184.22=1.493%风温 1100℃炉尘量 20 kg/t 生铁入炉熟料温度80℃炉顶煤气温度200℃焦炭冶炼强度0.98 t/(m3·d)高炉有效容积利用系数 2.7t/(m3·d)炉渣碱度R=1.10(1)燃料带入的铁量G燃Fe首先计算20kg炉尘中的焦粉量:G焦粉=G尘C%尘/C%焦=20×11.95/85.36=2.80kg高炉内参加反应的焦炭量为:G焦=360- G焦粉=360-2.80=357.2kg故G燃Fe = G焦FeO%焦7256+ G煤FeO%煤7256=357.2×0.43%×7256+150×0.92%×7256 =2.27kg(2)进入炉渣中的铁量G渣Fe =1000Fe%生铁×%7.99%3.0=952.3×7.993.0=2.865kg式中0.3%、99.7%——分别为铁在炉渣和生铁中的分配比(3)需要由铁矿石带入的铁量为:G矿Fe =1000 Fe%生铁+ G渣Fe- G燃Fe =952.3+2.856-2.27=952.9kg(4)冶炼1t生铁的铁矿石需要量:G矿= G矿Fe/ Fe%矿=%59.599.952=1599.09kg考虑到炉尘吹出量,入炉铁矿石量为:G/矿= G矿+ G尘- G焦粉=1599.09+20-2.80=1616.29kg(1)设定炉渣碱度R=CaO/SiO2=1.10 (2)石灰石的有效溶剂性CaO有效= CaO%熔剂-R SiO2%熔剂=(51.03-1.10×1.96)% =48.87%(3)原料、燃料带有的CaO量GCaO 铁矿石带入的CaO量为:G矿CaO =G矿CaO%矿=1599.09×7.10%=113.54kg焦炭带入的CaO量为:G焦CaO = G焦CaO%焦=357.2×0.51%=1.82kg煤粉带入的CaO量为:G煤CaO =G煤CaO%煤=150×0.73%=1.10kg故GCaO = G矿CaO+ G焦CaO+ G煤CaO=113.54+1.82+1.10=116.46kg(4)原料、燃料带入的SiO2量GSiO2铁矿石带入的SiO2量为:G矿SiO2= G矿SiO2%矿=1599.09×5.68%=90.83kg焦炭带入的SiO2量为:G焦SiO2= G焦SiO2%焦=357.2×7.32%=26.15kg煤粉带入的SiO2量为:G煤SiO2= G煤SiO2%煤=150×7.31%=10.97kg硅素还原消耗的SiO2量为:G还SiO2=1000Si%生铁2860=11.79kg故GSiO2= G矿SiO2+G焦SiO2+G煤SiO2-G还SiO290.83+26.15+10.97-11.79=116.16kg熔剂(石灰石)需要量为:G熔=(R GSiO2- GCaO)/ CaO有效=(1.10×116.16-116.46)/48.87% =23.16kg原料、燃料带入的成分见下表1-6表1-6 每吨生铁带入的有关物质的量(1)炉渣中CaO的量G渣CaO由上表:G渣CaO=128.28kg(2)炉渣中SiO2的量G渣SiO2由上表:G渣SiO2=128.40- G还SiO2=128.40-11.79=116.61kg(3)炉渣中Al2O3的量G渣Al2O3由上表:G渣Al2O3=49.44kg(4)炉渣中MgO的量G渣MgO由上表:G渣MgO=28.62kg(5)炉渣中MnO的量G渣MnOG渣MnO=0.66×50%=0.33kg50%——锰元素在炉渣中的分配率(6)炉渣中FeO的量G渣FeO进入渣中的铁量为:Fe渣=2.865kg ,并以FeO形式存在故G渣FeO =2.865×5672=3.68kg(7)炉渣中S的量G渣S原燃料带入的总S量为:GS=3.138kg (见表3-6)进入生铁的S量为:G生铁S =1000S%生铁=1000×0.026%=0.26kg进入煤气中的S量为:G煤气S = GS5%=3.138×0.05=0.157kg故G渣S = GS-G生铁S-G煤气S=3.138-0.26-0.157 =2.72kg炉渣成分见下表1-7铁矿石带入的P 量为:G 矿P = G 矿P%矿=1599.09×0.032%=0.51kg 石灰石带入的P 量为:G 熔P = G 熔P%熔=23.16×0.001%=0.0002kg故 [P]=(0.51+0.0002)×10001=0.051% (2)生铁含[Mn] 按原料带入的锰有50%进入生铁计算故 [Mn]=0.66×50%×7155×10001=0.026%(3)生铁含[C][C]=[100-(95.23+0.55+0.026+0.051+0.026)]%=4.117% 校核后的生铁成分(%)见下表1-81.3物料平衡计算(1)风口前燃烧的碳量G 燃C 1)G 总C = G 焦C%焦+ G 煤C%煤 =357.2×85.36%+150×77.75% =421.53kg2)溶入生铁中的碳量为:G 生铁C =1000[C]%=1000×4.117%=41.17kg3)生成甲烷的碳量为:燃料带入的总碳量有1%~1.5%与氢化合生成甲烷,本例去1%。
G 甲烷C =1% G 总C =0.01×421.53=4.22kg 4)直接还原消耗的碳量G 直C 锰还原消耗的碳量:G 锰C =1000[Mn]%5512=1000×0.026%×5512=0.06kg硅还原消耗的碳量:G 硅C 1000[Si]%2824=1000×0.55%×2824=4.71kg 磷还原消耗的碳量:G 磷C 1000[P]%6260=1000×0.051%×6260=0.49kg-铁直接还原消耗的碳量:G 铁直C =1000[Fe]% 5612r d /r d /= r d -r H2r d 一般为0.4~0.5,本计算取0.45。
r H2= 256[ G 焦( H 2%焦挥发+ H 2%焦有机)+ G 煤H 2%煤+182(V /风φ4.2218+ G 煤H 2O %煤)]×ηH2α/(1000[Fe]%)=256[ 357.2(0.037%+ 0.36%)+ 150×2.28%+182 (1200×1.493%×4.2218+ 150×0.85 %)]×0.35×0.9/(100095.23%) =0.06式中 ηH2——氢在高炉内的利用率,一般为0.3~0.5,本计算取0.35;α——被利用氢气量中,参加还原FeO 的百分量,一般为0.85~1.0,取0.9;V /风——设定的每吨生铁耗风量,本计算取1200m 3。
G 铁直C =1000×95.23%×5612×0.39=79.59kg 故 G 直C = G 锰C + G 硅C +G 磷C +G 铁直C =0.06+4.71+0.49+79.59 =84.85kg风口前燃烧的碳量为: G 燃C = G 总C -G 生铁C -G 甲烷C -G 直C=421.53-41.17-4.22-84.85 =291.29kg (2)计算鼓风量V 风1)鼓风中氧的浓度:N=21%(1-φ)+0.5φ=21%(1-1.493%)+0.5×1.493% =21.43% 2) G 燃C 燃烧需要氧的体积为: V O2= G 燃C 1224.22=291.29×1224.22 =271.87 m 33)煤粉带入氧的体积为: V 煤O2=G 煤(O%煤+ H 2 O %煤1816)324.22 =150(2.32%+ 0.85 %1816)×324.22=3.23 m 34)需鼓风供给氧的体积为: V 风O2= V O2-V 煤O2271.87-3.23=268.64 m 3 故 V 风= V 风O2/N=21.43%64.268=1253.57 m 3(1)甲烷的体积V CH41)由燃料碳素生成的甲烷量为:V 碳CH4= G 甲烷C 124.22=4.22×124.22=7.88 m 32)焦炭挥发分中的甲烷量为:V 焦CH4=G 焦CH 4%焦164.22=357.2×0.025%×164.22=0.125 m 3故 V CH4= V 碳CH4+V 焦CH47.88+0.125=8.01 m 3 (2)氢气的体积V H21)由鼓风中水分分解产生的氢量为: V 分H2= V 风φ=1253.57×1.493%=18.72 m 3 2)焦炭挥发分及有机物中的氢量为:V 焦H2= G 焦(H 2%焦挥发+ H 2%焦有机)24.22=357.2(0.037%+0.36%)24.22=15.88 m 33)煤粉分解产生的氢量为:OV 煤H2= G 煤(H 2%煤+ H 2 O %煤182)24.22=150(2.28%+0.85%×182)24.22=39.89 m 34)炉缸煤气中氢的总产量为:V总H2= V分H2+V焦H2+V煤H2=18.72+15.88+39.89 =74.04 m35)生成甲烷消耗的氢量为:V烷H2=2VCH4=2×8.10=16.02 m36)参加间接反应消耗的氢量为:V间H2=V总H2ηH2=74.04×0.35=25.91 m3故VH2=V总H2-V烷H2-V间H2=74.04-16.02-25.91 =32.11 m3(3)二氧化碳的体积VCO21)由CO还原Fe2O3为FeO生成的CO2 V/2还COG32OFe = G矿Fe2O3%矿=1599.09×72.53% =1159.82kg参加还原Fe2O3为FeO的氢气量为:G还H2= V总H2ηH2(1-α)4.222=74.04×0.35×(1-0.9)×4.222 =0.23kg由氢气还原Fe2O3的质量为:G/32OFe = G还H22160=0.23×2160=18.4kg由CO还原Fe2O3的质量为:G//32OFe = G32OFe- G/32OFe =1159.82-18.4 =1141.42kg故V/2还CO = G//32OFe1604.22=1141.42×1604.22=159.80 m32)由CO还原FeO为Fe生成的CO2量为:V//2还CO =1000[Fe]%[1- r d/-rH2]564.22=1000×95.23%(1-0.39-0.06)564.22 =209.51 m33)石灰石分解产生的CO2量为:V分CO2=G熔CO2%熔444.22=23.16×42.43%×444.22 =5.00 m34)焦炭挥发分中的CO2量为:V挥CO2= G焦CO2%焦444.22=357.2×0.91%×444.22 =0.35 m3故VCO2= V/2还CO+V//2还CO+V分CO2+V挥CO2 =159.80+209.51+5.00+0.35 374.66 m3(4)一氧化碳的体积VCO1)风口前碳素燃烧生成的CO量为:V燃CO =G燃C124.22=291.29×124.22=543.74 m32)直接还原生成的CO量为:V直CO = G直C124.22=84.85×124.22=158.39 m33)焦炭挥发分中的CO量为:V挥CO = G焦CO%焦284.22=357.2×0.21%×284.22=0.60 m34)间接还原消耗的CO量为:V间CO = V/2还CO+V//2还CO=159.80+209.51=369.31 m3故VCO =V燃CO+V直CO+V挥CO-V间CO=334.42 m3(5)氮气的体积V2N1)鼓风带入的氮气量为:V风2N = V风(1-φ)N2%风=1253.57(1-1.493%)79%=975.53 m32)焦炭带入的氮气量为:V焦2N =G焦(N2%焦挥发+ N2%焦有机)284.22=357.2(0.118%+0.27%)284.22=1.11 m33)煤粉带入的氮气量为:V煤2N =G煤N2%煤284.22=150×0.52%×284.22 =0.62 m3故V2N =V风2N+V焦2N+V煤2N=975.53+1.11+0.62=977.26 m3煤气成分见下表1-9表1-9煤气量及成分1 m3鼓风的质量为:r风=[0.21(1-φ)32+0.79(1-φ)28+18φ]/22.4=[0.21×0.985×32+0.79×0.985×28+18×0.01493]/22.4 =1.28kg/ m3鼓风的质量为:G风=V风r风=1253.57×1.28=1604.57kg(2)煤气质量的计算1 m3煤气的质量为:r气=(44 CO2%+28 CO %+28 N2%+2 H2%+16 CH4%)/22.4=(44×0.217+28×0.1937+28×0.566+2×0.0186+16×0.0047)/22.41.381 kg/ m3煤气的质量为:G气=V气r气=1726.46×1.381=2384.24kg(3)煤气中的水分1)焦炭带入的水分G焦OH2=G焦H2O%焦=357.2×4.17%=14.90kg2)石灰石带入的水分G熔OH2=G熔H2O%熔23.16×1.06%=0.25kg3)氢气参加还原生成的水分为:G还OH2= V间H24.222×218=25.91×4.222×218 20.82kg故GOH2= G焦OH2+G熔OH2+G还OH2=14.90+0.25+20.82=35.97kg物料平衡列表1-10所以计算结果符合要求。