国内外氮化工艺新进展
氮化处理技术在汽车制造领域中的应用前景展望
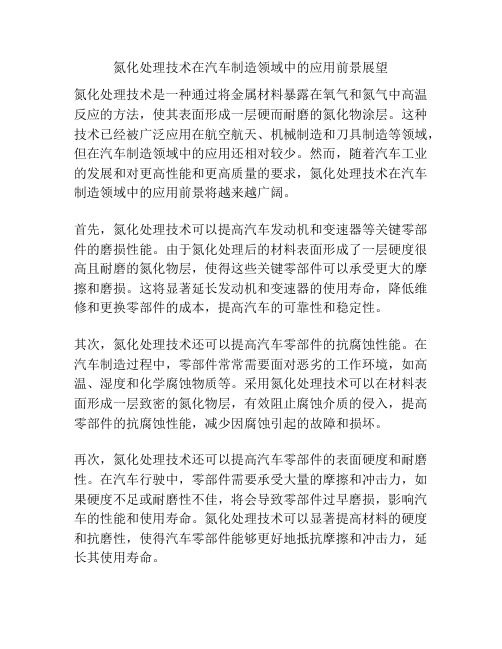
氮化处理技术在汽车制造领域中的应用前景展望氮化处理技术是一种通过将金属材料暴露在氧气和氮气中高温反应的方法,使其表面形成一层硬而耐磨的氮化物涂层。
这种技术已经被广泛应用在航空航天、机械制造和刀具制造等领域,但在汽车制造领域中的应用还相对较少。
然而,随着汽车工业的发展和对更高性能和更高质量的要求,氮化处理技术在汽车制造领域中的应用前景将越来越广阔。
首先,氮化处理技术可以提高汽车发动机和变速器等关键零部件的磨损性能。
由于氮化处理后的材料表面形成了一层硬度很高且耐磨的氮化物层,使得这些关键零部件可以承受更大的摩擦和磨损。
这将显著延长发动机和变速器的使用寿命,降低维修和更换零部件的成本,提高汽车的可靠性和稳定性。
其次,氮化处理技术还可以提高汽车零部件的抗腐蚀性能。
在汽车制造过程中,零部件常常需要面对恶劣的工作环境,如高温、湿度和化学腐蚀物质等。
采用氮化处理技术可以在材料表面形成一层致密的氮化物层,有效阻止腐蚀介质的侵入,提高零部件的抗腐蚀性能,减少因腐蚀引起的故障和损坏。
再次,氮化处理技术还可以提高汽车零部件的表面硬度和耐磨性。
在汽车行驶中,零部件需要承受大量的摩擦和冲击力,如果硬度不足或耐磨性不佳,将会导致零部件过早磨损,影响汽车的性能和使用寿命。
氮化处理技术可以显著提高材料的硬度和抗磨性,使得汽车零部件能够更好地抵抗摩擦和冲击力,延长其使用寿命。
另外,氮化处理技术还可以提高汽车零部件的热稳定性。
在高温环境中,材料容易发生热膨胀、变形和软化等现象,从而影响汽车的性能和安全性。
采用氮化处理技术可以提高材料的热稳定性,降低材料的热膨胀系数,使得零部件能够在高温环境中保持稳定的尺寸和形状。
综上所述,氮化处理技术在汽车制造领域中的应用前景非常广阔。
通过提高汽车零部件的磨损性能、抗腐蚀性能、表面硬度和耐磨性以及热稳定性,氮化处理技术可以显著提高汽车的性能和质量,降低维修和更换零部件的成本,提高汽车的可靠性和稳定性,进而推动汽车工业的发展。
钐铁合金氮化新工艺

钐铁合金氮化新工艺王黎光;王书桓;宋春燕;赵定国;蔡爽【摘要】自SmFeN系稀土永磁材料于1990年在实验室发现以来,20年间国内外科研工作者对其开展了一系列的研究工作,并取得了一定的科研成果.目前限制钐铁合金发展的主要因素是合金渗氮,渗氮工艺主要围绕钐铁合金粉体的固态渗氯,固态渗氮会造成合金渗氮速率慢、渗氮不均匀等一系列问题.钐铁合金渗氮方面的这些问题严重影响着钐铁氮的磁性能.由于受渗氮工艺限制,对钐铁氮的研制还处于实验室研究阶段.该项研究提出液态钐铁合金高压底吹渗氮工艺,旨在解决当前存在的渗氮慢、渗氮不均匀等问题.【期刊名称】《河北联合大学学报(自然科学版)》【年(卷),期】2016(038)003【总页数】5页(P20-24)【关键词】钐铁氮;渗氮;渗氮速率【作者】王黎光;王书桓;宋春燕;赵定国;蔡爽【作者单位】华北理工大学冶金与能源学院,河北唐山063009;华北理工大学冶金与能源学院,河北唐山063009;华北理工大学冶金与能源学院,河北唐山063009;华北理工大学冶金与能源学院,河北唐山063009;华北理工大学冶金与能源学院,河北唐山063009【正文语种】中文【中图分类】TF7461990年Coey和Sun Hong[1] 利用气—固反应法成功的将N原子引入到Sm2Fe17中合成了Sm2Fe17NX化合物。
作为新一代的稀土永磁材料。
Sm2Fe17NX相比于NdFeB具有较高的居里温度(476 ℃,高出Nd2Fe14B近160 ℃[2,3])、更高的内禀磁性,且具有良好的热稳定性、耐蚀性和抗氧化性。
目前钐铁合金氮化工艺主要集中于气固渗氮方面,由于固态渗氮不均匀且渗氮效果差,因此迄今为止Sm2Fe17NX依然处于实验室研究阶段,工业化生产技术仍不成熟。
如今永磁研究领域依然以第3代永磁材料(Nd2Fe14B)为主。
针对上述问题,该项研究提出液态钐铁合金高压渗氮工艺,旨在解决钐铁合金渗氮方面的问题。
金属材料表面离子轰击(离子氮化)新技术

离子氮化本技术是我国70年代新兴的表面强化技术学科。
自1978年以来,我院从事钛合金的离子氮化和离子复合处理研究。
对热挤压铝型材模具钢3Cr2W8V 、进口(仿)H13钢。
不锈钢、日本P20、38CrMoAl 、40Cr 、35CrMo 、40CrNiMo 和30CrMnSi 等钢制零部件进行离子氮化和离子复合处理研究。
近年来,又开展对长轴类工件施行离子处理表面强化工作,诸如,高精度大型瓦楞辊和生产淀粉刮刀进行表面强化处理研究。
使工件表面既提高硬度,又保持基体强度。
耐腐蚀性能和耐磨性能也十分显著。
为社会创造了较大的经济效益。
多次获得国家科委“七五”攻关奖、中国有色金属总公司和省市级有关部门的奖励。
1. 离子轰击氮化法的基本原理离子氮化是利用辉光放电这一物理现象对金属材料表面强化的氮化法。
在低压的氮气或氨气等气氛中,炉体和被处理工件之间加以直流电压,使产生辉光放电,在被处理表面数毫米处出现急剧的电压降,气体中的离子,朝着图1箭头所示方向向阴极移动(如图1)。
当接近工件表面时,由于电压剧降而被强烈加速,轰击工件表面,离子具有的动能转变为热能,加热了被处理工件,同时一部分离子直接注入工件表面,一部分离子引起阴极溅射,从工件表面“溅出”电子和原子,“溅出”的铁原子和由于电子作用而形成的原子态氮相结合,形成FeN 。
FeN 由于吸附和在表面上蒸发,因受到高温和离子轰击而很快地分解为低价氮化物而放出氮。
一部分失去氮的铁又被溅射到辉光等离子气体中与新的氮原子相结合,促进氮化。
图1 离子氮化的表面反应图阴极下降电压降等离子区工件处理表面炉壁离子Fe + NFe 2N N FeNFe 3N N Fe 4N N ε相 γ‘相 αFe电子吸附图2 H13钢试样离子复合处理渗层与普通离子氮化渗层的X 射线衍射曲线对比 2. 离子轰击(氮化)处理工艺特点2.1采用本工艺能够在同一工件上获得基体性能与表面性能的良好配合,渗层表面既硬以韧。
氮化处理在工业制造中的应用与发展前景
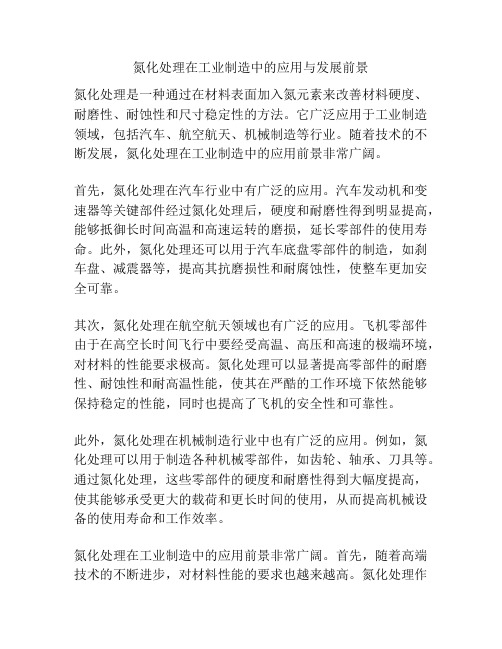
氮化处理在工业制造中的应用与发展前景氮化处理是一种通过在材料表面加入氮元素来改善材料硬度、耐磨性、耐蚀性和尺寸稳定性的方法。
它广泛应用于工业制造领域,包括汽车、航空航天、机械制造等行业。
随着技术的不断发展,氮化处理在工业制造中的应用前景非常广阔。
首先,氮化处理在汽车行业中有广泛的应用。
汽车发动机和变速器等关键部件经过氮化处理后,硬度和耐磨性得到明显提高,能够抵御长时间高温和高速运转的磨损,延长零部件的使用寿命。
此外,氮化处理还可以用于汽车底盘零部件的制造,如刹车盘、减震器等,提高其抗磨损性和耐腐蚀性,使整车更加安全可靠。
其次,氮化处理在航空航天领域也有广泛的应用。
飞机零部件由于在高空长时间飞行中要经受高温、高压和高速的极端环境,对材料的性能要求极高。
氮化处理可以显著提高零部件的耐磨性、耐蚀性和耐高温性能,使其在严酷的工作环境下依然能够保持稳定的性能,同时也提高了飞机的安全性和可靠性。
此外,氮化处理在机械制造行业中也有广泛的应用。
例如,氮化处理可以用于制造各种机械零部件,如齿轮、轴承、刀具等。
通过氮化处理,这些零部件的硬度和耐磨性得到大幅度提高,使其能够承受更大的载荷和更长时间的使用,从而提高机械设备的使用寿命和工作效率。
氮化处理在工业制造中的应用前景非常广阔。
首先,随着高端技术的不断进步,对材料性能的要求也越来越高。
氮化处理作为一种有效的表面改性方法,能够使材料在满足高强度、高耐磨性、高耐腐蚀性等要求的同时,保持材料原有的韧性和塑性,满足不同行业的需求。
其次,随着工业化生产的不断推进,对产品的质量和效率要求也越来越高。
氮化处理可以通过表面改性来提高材料的性能,从而延长产品的使用寿命,减少产品的维修和更换次数,降低生产成本。
因此,氮化处理在提高产品质量和降低生产成本方面具有很大的潜力。
此外,氮化处理在环保方面也有着积极的作用。
由于氮化处理能够提高材料的耐磨性和耐腐蚀性,减少了材料的损耗和废弃物的产生。
微电子器件中氮化处理技术的应用与前景展望
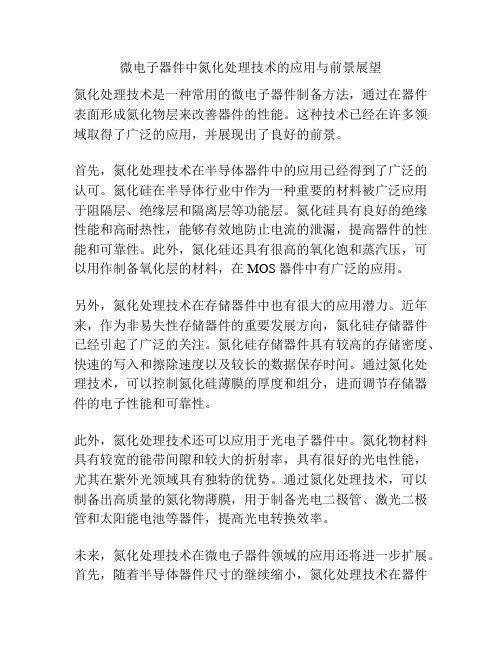
微电子器件中氮化处理技术的应用与前景展望氮化处理技术是一种常用的微电子器件制备方法,通过在器件表面形成氮化物层来改善器件的性能。
这种技术已经在许多领域取得了广泛的应用,并展现出了良好的前景。
首先,氮化处理技术在半导体器件中的应用已经得到了广泛的认可。
氮化硅在半导体行业中作为一种重要的材料被广泛应用于阻隔层、绝缘层和隔离层等功能层。
氮化硅具有良好的绝缘性能和高耐热性,能够有效地防止电流的泄漏,提高器件的性能和可靠性。
此外,氮化硅还具有很高的氧化饱和蒸汽压,可以用作制备氧化层的材料,在MOS器件中有广泛的应用。
另外,氮化处理技术在存储器件中也有很大的应用潜力。
近年来,作为非易失性存储器件的重要发展方向,氮化硅存储器件已经引起了广泛的关注。
氮化硅存储器件具有较高的存储密度、快速的写入和擦除速度以及较长的数据保存时间。
通过氮化处理技术,可以控制氮化硅薄膜的厚度和组分,进而调节存储器件的电子性能和可靠性。
此外,氮化处理技术还可以应用于光电子器件中。
氮化物材料具有较宽的能带间隙和较大的折射率,具有很好的光电性能,尤其在紫外光领域具有独特的优势。
通过氮化处理技术,可以制备出高质量的氮化物薄膜,用于制备光电二极管、激光二极管和太阳能电池等器件,提高光电转换效率。
未来,氮化处理技术在微电子器件领域的应用还将进一步扩展。
首先,随着半导体器件尺寸的继续缩小,氮化处理技术在器件隔离和绝缘方面的应用将更加重要。
其次,氮化物材料在功率器件领域具有广阔的应用前景。
由于氮化物材料具有较高的击穿电场强度和热传导性能,可以制备出高效率、高功率的功率器件,具有很高的市场潜力。
此外,氮化处理技术还可以应用于柔性电子器件和传感器等领域,推动微电子器件的多样化和智能化发展。
总之,氮化处理技术是一种重要的微电子器件制备方法,具有广泛的应用前景。
在半导体器件、存储器件和光电子器件等领域,氮化处理技术的发展将推动微电子器件的性能提升和功能扩展。
热处理与氮化处理联合应用在钢材制造中的最新研究进展

热处理与氮化处理联合应用在钢材制造中的最新研究进展热处理和氮化处理是钢材制造中常用的两种改性技术。
热处理通过加热和冷却的方式改变钢材的组织结构和力学性能,以增强材料的硬度、强度和耐磨性等特性。
而氮化处理则是将氮气或氨气浸渍到钢材表层,使其形成一层硬度很高的表面层,提高钢材的耐磨性、耐蚀性和疲劳寿命等。
最近,研究人员开始探索将热处理和氮化处理联合应用在钢材制造中的潜力。
这种联合应用可以进一步提高钢材的性能,并且通常比单独应用某一种处理技术更有效。
下面将介绍最新的研究进展。
首先,研究人员发现,对钢材进行热处理后再进行氮化处理,可以显著提高钢材的表面硬度和耐磨性。
热处理会改变钢材的晶粒结构和残余应力分布,为后续的氮化处理创造了更好的条件。
而氮化处理则能够在钢材表面形成一层硬度很高的氮化物层,进一步增强钢材的硬度和耐磨性。
研究人员通过优化热处理和氮化处理的工艺参数,成功制备出了表面硬度超过1000 HV的高硬度钢材。
其次,研究人员还发现,利用热处理和氮化处理的联合应用,可以提高钢材的耐腐蚀性能。
热处理可以消除钢材内部的缺陷和氧化物,改善钢材的耐腐蚀性。
而氮化处理可以在钢材表面形成一层紧密的氮化物层,阻止腐蚀介质的进一步侵蚀。
研究人员通过对不同工艺参数进行优化,成功制备出了耐腐蚀性能优异的氮化钢材。
最后,研究人员还开始研究将热处理和氮化处理联合应用于提高钢材的疲劳寿命。
热处理可以改变钢材的组织结构和残余应力分布,减少疲劳裂纹的产生和扩展,提高钢材的疲劳寿命。
而氮化处理则可以在钢材表面形成一层硬度很高的氮化物层,阻止裂纹的扩展,进一步延长钢材的使用寿命。
研究人员通过对热处理和氮化处理工艺参数的细致调控,成功制备出了疲劳寿命超过500万循环的高耐久性钢材。
综上所述,热处理和氮化处理联合应用在钢材制造中具有广阔的应用前景。
通过对热处理和氮化处理工艺参数的优化,可以进一步提高钢材的硬度、强度、耐磨性、耐腐蚀性和疲劳寿命等性能。
氮化处理技术在塑料制品中的应用研究与展望

氮化处理技术在塑料制品中的应用研究与展望氮化处理技术是一种通过在材料表面形成氮化物层的方法,可以显著提高材料的硬度、耐热性、耐磨损性和耐腐蚀性。
在塑料制品领域,氮化处理技术的应用得到了广泛关注和研究。
本文将对氮化处理技术在塑料制品中的应用研究进行探讨,并展望未来的发展方向。
首先,氮化处理技术可以克服塑料制品在硬度和耐磨损性方面的缺陷。
由于塑料制品的相对软性和易磨损性,其在一些应用中容易出现磨损和损坏的情况。
而通过氮化处理,可以在塑料表面形成硬度较高的氮化物层,从而显著提高塑料制品的硬度和耐磨损性。
这使得塑料制品可以在更为恶劣的工作环境下使用,延长使用寿命,降低维修和更换成本。
其次,氮化处理技术也可以提高塑料制品的耐热性。
由于塑料制品的热稳定性较差,常常在高温环境下发生软化甚至熔化的现象。
而氮化处理技术可以通过形成氮化物层来提高塑料制品的耐热性。
氮化物具有较高的熔点和热导率,可以有效地改善塑料制品在高温下的使用性能。
此外,氮化处理技术还可以增强塑料制品的耐腐蚀性。
常见的塑料材料如聚氯乙烯(PVC)、聚乙烯(PE)等在一些酸、碱等腐蚀性介质下容易发生腐蚀,导致材料性能下降。
而通过氮化处理技术,可以在塑料表面形成氮化物层,起到一定的防腐蚀作用,提高塑料制品的耐腐蚀性,延长使用寿命。
尽管氮化处理技术在塑料制品中的应用前景广阔,但仍存在一些挑战和局限性。
首先,目前氮化处理技术仍处于发展阶段,对于不同类型的塑料材料和工艺参数的氮化处理效果仍需要进一步研究和优化。
其次,氮化处理技术在大规模应用时可能面临成本高、加工周期长、设备复杂等问题。
此外,氮化处理技术对于塑料制品的应用范围仍存在一定限制,不同类型的塑料材料在氮化处理中的适应性可能存在差异。
在未来的发展中,可以通过以下途径进一步推动氮化处理技术在塑料制品中的应用。
首先,可以加大对于不同类型塑料材料的氮化处理研究和优化,以提高处理效果和适用范围。
其次,可以探索和优化氮化处理技术的工艺参数,以缩短加工周期、降低成本并提高生产效率。
新型氮化处理方法研究与应用现状分析
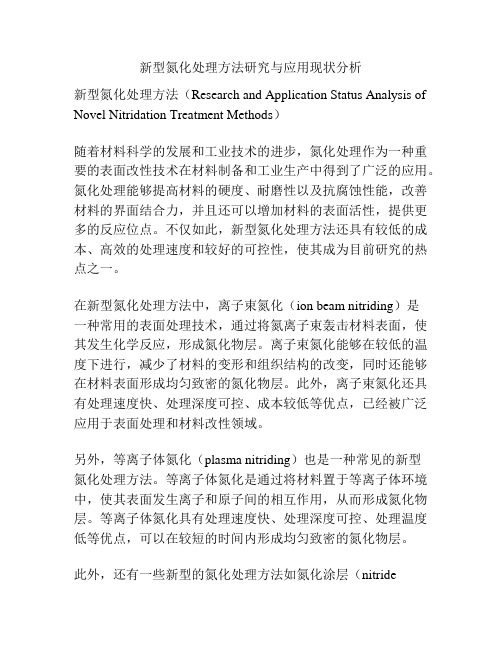
新型氮化处理方法研究与应用现状分析新型氮化处理方法(Research and Application Status Analysis of Novel Nitridation Treatment Methods)随着材料科学的发展和工业技术的进步,氮化处理作为一种重要的表面改性技术在材料制备和工业生产中得到了广泛的应用。
氮化处理能够提高材料的硬度、耐磨性以及抗腐蚀性能,改善材料的界面结合力,并且还可以增加材料的表面活性,提供更多的反应位点。
不仅如此,新型氮化处理方法还具有较低的成本、高效的处理速度和较好的可控性,使其成为目前研究的热点之一。
在新型氮化处理方法中,离子束氮化(ion beam nitriding)是一种常用的表面处理技术,通过将氮离子束轰击材料表面,使其发生化学反应,形成氮化物层。
离子束氮化能够在较低的温度下进行,减少了材料的变形和组织结构的改变,同时还能够在材料表面形成均匀致密的氮化物层。
此外,离子束氮化还具有处理速度快、处理深度可控、成本较低等优点,已经被广泛应用于表面处理和材料改性领域。
另外,等离子体氮化(plasma nitriding)也是一种常见的新型氮化处理方法。
等离子体氮化是通过将材料置于等离子体环境中,使其表面发生离子和原子间的相互作用,从而形成氮化物层。
等离子体氮化具有处理速度快、处理深度可控、处理温度低等优点,可以在较短的时间内形成均匀致密的氮化物层。
此外,还有一些新型的氮化处理方法如氮化涂层(nitridecoating)、氮离子注入(nitrogen ion implantation)等也得到了广泛的研究和应用。
氮化涂层是通过在材料表面涂覆含氮化合物的涂层,然后通过热处理使其与材料基体发生反应,形成氮化物层。
氮离子注入是将氮离子注入到材料内部,通过原子间的相互作用形成氮化物层。
这些新型氮化处理方法不仅可以弥补传统氮化处理方法的不足,而且能够实现对材料性能的进一步调控,提高材料的综合性能。
国内外氮化工艺新进展
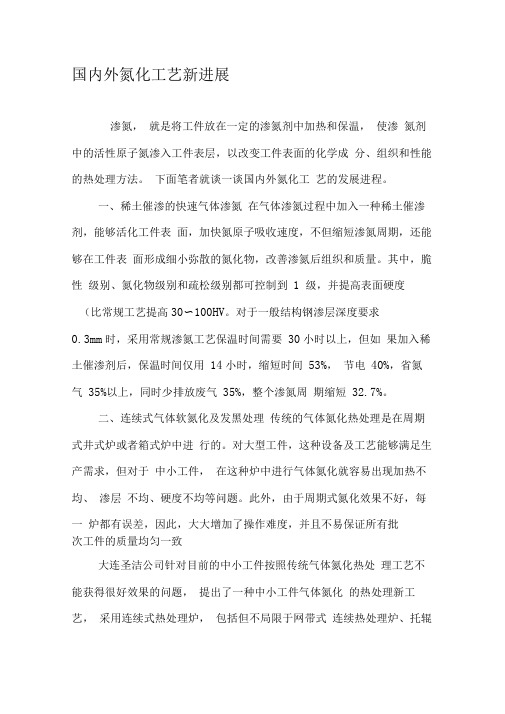
国内外氮化工艺新进展渗氮,就是将工件放在一定的渗氮剂中加热和保温,使渗氮剂中的活性原子氮渗入工件表层,以改变工件表面的化学成分、组织和性能的热处理方法。
下面笔者就谈一谈国内外氮化工艺的发展进程。
一、稀土催渗的快速气体渗氮在气体渗氮过程中加入一种稀土催渗剂,能够活化工件表面,加快氮原子吸收速度,不但缩短渗氮周期,还能够在工件表面形成细小弥散的氮化物,改善渗氮后组织和质量。
其中,脆性级别、氮化物级别和疏松级别都可控制到1 级,并提高表面硬度(比常规工艺提高30〜100HV。
对于一般结构钢渗层深度要求0.3mm时,采用常规渗氮工艺保温时间需要30小时以上,但如果加入稀土催渗剂后,保温时间仅用14小时,缩短时间53%,节电40%,省氮气35%以上,同时少排放废气35%,整个渗氮周期缩短32.7%。
二、连续式气体软氮化及发黑处理传统的气体氮化热处理是在周期式井式炉或者箱式炉中进行的。
对大型工件,这种设备及工艺能够满足生产需求,但对于中小工件,在这种炉中进行气体氮化就容易出现加热不均、渗层不均、硬度不均等问题。
此外,由于周期式氮化效果不好,每一炉都有误差,因此,大大增加了操作难度,并且不易保证所有批次工件的质量均匀一致大连圣洁公司针对目前的中小工件按照传统气体氮化热处理工艺不能获得很好效果的问题,提出了一种中小工件气体氮化的热处理新工艺,采用连续式热处理炉,包括但不局限于网带式连续热处理炉、托辊式连续热处理炉、滚动底式连续热处理炉、推杆炉等,通过调整通入气体流量和氨分解率可控制渗层深度及表面化合物层的深度。
冷却方式有水冷、油冷或空冷(专利申请号:200910012783.4)。
该发明突破了传统思维的缺点,创造性地将中小工件在连续炉中进行气体氮化,解决了传统周期式炉中气体渗氮的诸多缺点,不但大大提高了产品渗氮后的质量和热处理过程的一致性,且由于温度和时间均可连续调整,使操作简单易行并可成倍提高生产效率。
三、集5 项专利于一身的脉冲电源辉光离子氮化炉由大连圣洁公司研制的辉光离子氮化炉集5 项专利于一身,并根据客户的实际需要而量身定做,为大连开发区盘起工业公司(日本独资企业)制作的一台100kW①lOOOmrK2000mm的^离子氮化炉,用于处理①2mm 400mm的模具顶杆及其他模具配件。
佛山真空离子氮化工艺
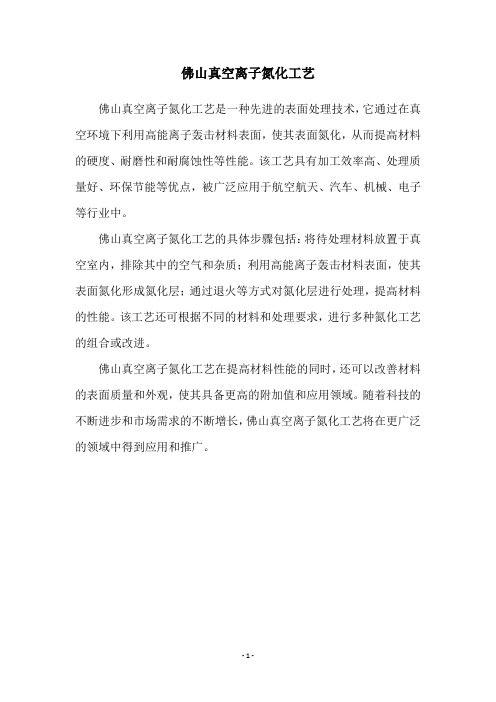
佛山真空离子氮化工艺
佛山真空离子氮化工艺是一种先进的表面处理技术,它通过在真空环境下利用高能离子轰击材料表面,使其表面氮化,从而提高材料的硬度、耐磨性和耐腐蚀性等性能。
该工艺具有加工效率高、处理质量好、环保节能等优点,被广泛应用于航空航天、汽车、机械、电子等行业中。
佛山真空离子氮化工艺的具体步骤包括:将待处理材料放置于真空室内,排除其中的空气和杂质;利用高能离子轰击材料表面,使其表面氮化形成氮化层;通过退火等方式对氮化层进行处理,提高材料的性能。
该工艺还可根据不同的材料和处理要求,进行多种氮化工艺的组合或改进。
佛山真空离子氮化工艺在提高材料性能的同时,还可以改善材料的表面质量和外观,使其具备更高的附加值和应用领域。
随着科技的不断进步和市场需求的不断增长,佛山真空离子氮化工艺将在更广泛的领域中得到应用和推广。
- 1 -。
国内外渗碳和渗氮热处理工艺的新进展_三_朱祖昌

围于整个装满处理工件支架平 源装置④; 活性屏⑤, 台; ( 4 ) 位于炉体和活性屏之间的炉气输入管路 ⑥, 上有均匀分布的喷口, 确保渗氮气氛的均匀平缓流 动; ( 5 ) 工件支架平台 ⑧, 被保持处于浮动电位; ( 6 ) 在处理室顶部安装真空密闭电机和风扇以便对渗氮 工件的强制冷却( 图 18 ( a) 中未画出) ; ( 7 ) 辅助电源 11 , ○ 以供处理不锈钢工件时去除表面的钝化膜 ( 图 18 ( a) 中未画出) 。 设备的关键部件是活性金属屏, 脉冲或直流电 源的电流直接加于活性屏上, 其产生的热依靠辐射 同时由喷口 ⑥ 喷入的气体 均匀加热渗氮处理工件, 产生等离子体, 按精心设计的流动方向均匀平缓地 与处理工件接触, 实现均匀的渗氮。 工件进行渗氮
1400 1200
硬度 /HV
(a)
1000 800 600 400 200 0 0 1400 1200 50 (a) d/μm 100 150 ) 的平衡常数: 5 5 k N = a N / P0. % N]/ P0. N2 = f N[ N2
( 2)
硬度 /HV
2. Shanghai Machine Building
3. Shanghai Engineering Research
Center of Metal Materials Modification, Shanghai 200070 )
5
活性屏离子的渗氮技术 钢铁工件渗氮的典型处理温度为 450 ~ 590 ℃ , 一般工件处于铁素体或铁素体 + 渗碳体状态。 依靠
[28 - 29 ]
[27 ]
= Δ H0 - T Δ S 0 Δ H0 Δ S 0 + RT R ( 5)
曲轴的离子氮化工艺现状
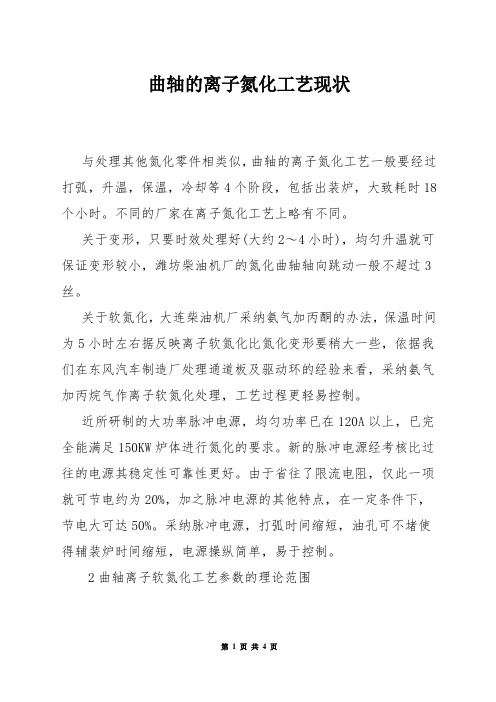
曲轴的离子氮化工艺现状与处理其他氮化零件相类似,曲轴的离子氮化工艺一般要经过打弧,升温,保温,冷却等4个阶段,包括出装炉,大致耗时18个小时。
不同的厂家在离子氮化工艺上略有不同。
关于变形,只要时效处理好(大约2~4小时),均匀升温就可保证变形较小,潍坊柴油机厂的氮化曲轴轴向跳动一般不超过3丝。
关于软氮化,大连柴油机厂采纳氨气加丙酮的办法,保温时间为5小时左右据反映离子软氮化比氮化变形要稍大一些,依据我们在东风汽车制造厂处理通道板及驱动环的经验来看,采纳氨气加丙烷气作离子软氮化处理,工艺过程更轻易控制。
近所研制的大功率脉冲电源,均匀功率已在120A以上,已完全能满足150KW炉体进行氮化的要求。
新的脉冲电源经考核比过往的电源其稳定性可靠性更好。
由于省往了限流电阻,仅此一项就可节电约为20%,加之脉冲电源的其他特点,在一定条件下,节电大可达50%。
采纳脉冲电源,打弧时间缩短,油孔可不堵使得辅装炉时间缩短,电源操纵简单,易于控制。
2曲轴离子软氮化工艺参数的理论范围就曲轴等离子体氮化技术而言,大多数厂家采纳了离子软氮化技术,其工艺参数的制定一般应遵循以下几项原则:1. 氮化温度的选择范围等离子体氮化就是利用真空辉光放电的方法把氮渗透金属表面形成FeN 的一种化学热处理方法。
在铁氮相图中,580℃为同素异晶转变点,低于580℃其组织为铁,高于580℃其组织转变为铁。
通常,进步处理温度有助于氮化物的形成和获得较深的渗层(在相同时间内),这是由于扩散系数与温度的指数变化成正比。
但是,由于在铁中氮的扩散系数仅为铁中的1/4 ,当处理温度高于580℃时,渗层的增长反而减慢,因此,离子氮化的控制温度范围为520℃至580℃。
2. 软氮化温度的选择范围关于碳钢或铸铁或低合金钢,人们常采纳离子软氮化(低温碳、氮共渗)技术。
就大量的施行说明:氮化层的硬度和渗层与温度、时间、浓度有极值关系。
通常在氨气与丙酮之比为10:1,温度在560℃至580℃,时间在3至4小时之间,获得的硬度和渗层。
关注│国内外氮化工艺新进展
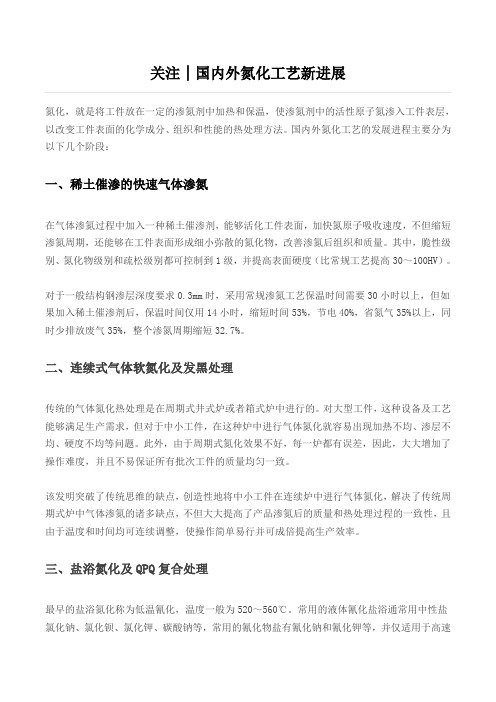
关注│国内外氮化工艺新进展氮化,就是将工件放在一定的渗氮剂中加热和保温,使渗氮剂中的活性原子氮渗入工件表层,以改变工件表面的化学成分、组织和性能的热处理方法。
国内外氮化工艺的发展进程主要分为以下几个阶段:一、稀土催渗的快速气体渗氮在气体渗氮过程中加入一种稀土催渗剂,能够活化工件表面,加快氮原子吸收速度,不但缩短渗氮周期,还能够在工件表面形成细小弥散的氮化物,改善渗氮后组织和质量。
其中,脆性级别、氮化物级别和疏松级别都可控制到1级,并提高表面硬度(比常规工艺提高30~100HV)。
对于一般结构钢渗层深度要求0.3mm时,采用常规渗氮工艺保温时间需要30小时以上,但如果加入稀土催渗剂后,保温时间仅用14小时,缩短时间53%,节电40%,省氮气35%以上,同时少排放废气35%,整个渗氮周期缩短32.7%。
二、连续式气体软氮化及发黑处理传统的气体氮化热处理是在周期式井式炉或者箱式炉中进行的。
对大型工件,这种设备及工艺能够满足生产需求,但对于中小工件,在这种炉中进行气体氮化就容易出现加热不均、渗层不均、硬度不均等问题。
此外,由于周期式氮化效果不好,每一炉都有误差,因此,大大增加了操作难度,并且不易保证所有批次工件的质量均匀一致。
该发明突破了传统思维的缺点,创造性地将中小工件在连续炉中进行气体氮化,解决了传统周期式炉中气体渗氮的诸多缺点,不但大大提高了产品渗氮后的质量和热处理过程的一致性,且由于温度和时间均可连续调整,使操作简单易行并可成倍提高生产效率。
三、盐浴氮化及QPQ复合处理最早的盐浴氮化称为低温氰化,温度一般为520~560℃。
常用的液体氰化盐浴通常用中性盐氯化钠、氯化钡、氯化钾、碳酸钠等,常用的氰化物盐有氰化钠和氰化钾等,并仅适用于高速钢工具。
另外,还有称作液体硫氮共渗的盐浴氮化,配方为氯化钡30%、氯化钠20%、氯化钙50%,另加5%~10%(中性盐总重量),成粉末状的硫化亚铁,其盐浴含硫量不低于0.2%,再通入一定量的氨气(NH3),促使盐浴翻动。
国内外氮化碳改性的研究进展
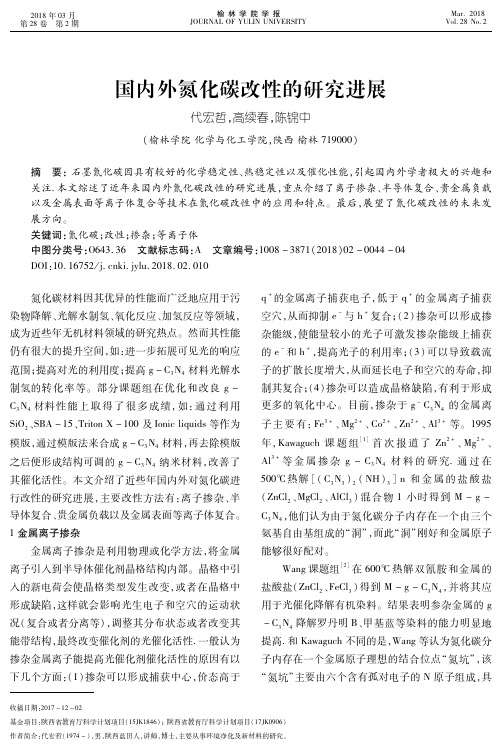
Zhang等[6]通过热解二氰胺和 1-丁基 -3-甲 基咪唑六氟磷酸盐 (BmimPF6)的混合物通过缩聚 反应成功地制备了 P掺杂的石墨状氮化碳(P-g- C3N4),经 过 表 征,其 光 电 特 性 发 生 了 很 大 的 变 化, 较 g-C3N4而言,电导率提高了大约 4倍,光生电流 提升了 5倍,可见光吸收范围更宽,其光催化能力更 加强劲。和 B掺杂相类似,Wang等[7]通过热解二 氰胺和 NH4F的 混 合 物 也 成 功 地 制 备 了 F-g- C3N4,并将其 用 于 光 解 水 制 氢 和 光 氧 化 反 应,分 析 发现氟元素很好地进入到 g-C3N4 结构中,并形成 了 F-C键,改变了 g-C3N4 的光电特性,增强了 g -C3N4的光解水和光氧化的能力.Liu等[8]在 H2S 气氛下于 450℃加热 g-C3N4成功制得 CN4-xSx,并 应用于光解水制氢.与氟掺杂相似的是,也形成了 S
金属离子掺杂是利用物理或化学方法,将金属 离子引入到半导体催化剂晶格结构内部。晶格中引 入的新电荷会使晶格类型发生改变,或者在晶格中 形成缺陷,这样就会影响光生电子和空穴的运动状 况(复合或者分离等),调整其分布状态或者改变其 能带结构,最终改变催化剂的光催化活性.一般认为 掺杂金属离子能提高光催化剂催化活性的原因有以 下几个方面:(1)掺杂可以形成捕获中心,价态高于
根据半导体能带理论,半导体的导带能级主要 取决于半导体中金属离子空的 d轨道能级,而半导 体的价带能级主要取决于非金属离子充满的 p轨道 能级。与金属元素不同的是,非金属元素一般具有 能量相对较高的 p轨道,掺杂进入 g-C3N4 晶格相 对困难一些。因此,在 g-C3N4晶格形成之前,最好 把非金 属 杂 原 子 配 位 于 其 晶 体 当 中。 目 前 硼、氟、 硫、磷、氧等非金属元素被成功引入 g-C3N4中形成 较为理 想 的 复 合 物 (nonmetal-g-C3N4 nanocom plexes),增强了 g-C3N4材料的催化活性。
氮化处理技术在刀具制造中的应用及发展方向
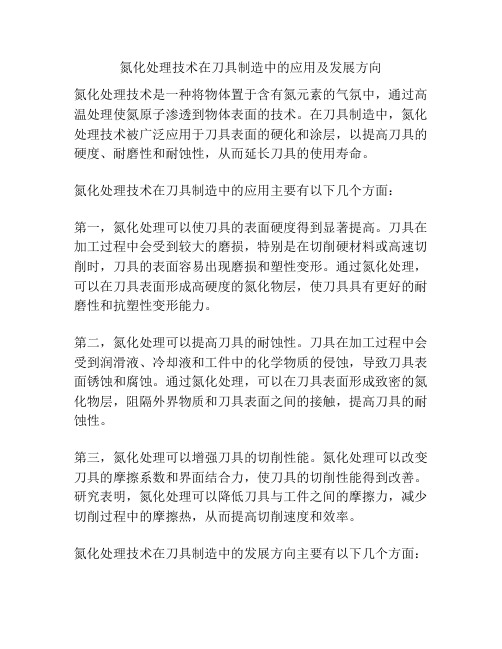
氮化处理技术在刀具制造中的应用及发展方向氮化处理技术是一种将物体置于含有氮元素的气氛中,通过高温处理使氮原子渗透到物体表面的技术。
在刀具制造中,氮化处理技术被广泛应用于刀具表面的硬化和涂层,以提高刀具的硬度、耐磨性和耐蚀性,从而延长刀具的使用寿命。
氮化处理技术在刀具制造中的应用主要有以下几个方面:第一,氮化处理可以使刀具的表面硬度得到显著提高。
刀具在加工过程中会受到较大的磨损,特别是在切削硬材料或高速切削时,刀具的表面容易出现磨损和塑性变形。
通过氮化处理,可以在刀具表面形成高硬度的氮化物层,使刀具具有更好的耐磨性和抗塑性变形能力。
第二,氮化处理可以提高刀具的耐蚀性。
刀具在加工过程中会受到润滑液、冷却液和工件中的化学物质的侵蚀,导致刀具表面锈蚀和腐蚀。
通过氮化处理,可以在刀具表面形成致密的氮化物层,阻隔外界物质和刀具表面之间的接触,提高刀具的耐蚀性。
第三,氮化处理可以增强刀具的切削性能。
氮化处理可以改变刀具的摩擦系数和界面结合力,使刀具的切削性能得到改善。
研究表明,氮化处理可以降低刀具与工件之间的摩擦力,减少切削过程中的摩擦热,从而提高切削速度和效率。
氮化处理技术在刀具制造中的发展方向主要有以下几个方面:第一,开发新型氮化处理工艺。
目前,氮化处理技术主要包括气氛氮化、盐浴氮化和离子氮化等多种方法。
但这些方法存在一些问题,如工艺复杂、能耗大、生产效率低等。
未来的发展方向是开发出更简便、高效的氮化处理工艺,以满足刀具制造业的需求。
第二,优化氮化处理参数。
氮化处理的效果与处理温度、处理时间、氮气氛浓度等参数密切相关。
通过优化处理参数,可以进一步提高刀具的硬度和耐磨性,降低刀具的变形和失效。
第三,应用先进的氮化处理设备。
随着科技的进步,氮化处理设备也在不断发展和更新。
未来的氮化处理设备应更加智能化和自动化,能够实现在线监测和控制,提高刀具的质量和生产效率。
总之,氮化处理技术在刀具制造中具有重要的应用价值和广阔的发展前景。
东莞金属氮化处理工艺
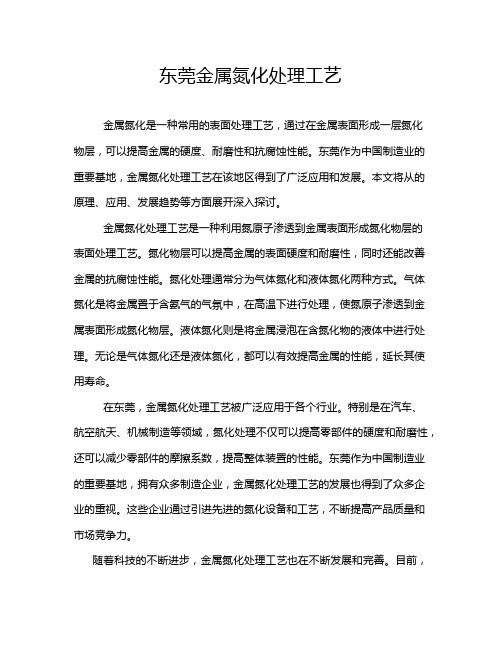
东莞金属氮化处理工艺金属氮化是一种常用的表面处理工艺,通过在金属表面形成一层氮化物层,可以提高金属的硬度、耐磨性和抗腐蚀性能。
东莞作为中国制造业的重要基地,金属氮化处理工艺在该地区得到了广泛应用和发展。
本文将从的原理、应用、发展趋势等方面展开深入探讨。
金属氮化处理工艺是一种利用氮原子渗透到金属表面形成氮化物层的表面处理工艺。
氮化物层可以提高金属的表面硬度和耐磨性,同时还能改善金属的抗腐蚀性能。
氮化处理通常分为气体氮化和液体氮化两种方式。
气体氮化是将金属置于含氨气的气氛中,在高温下进行处理,使氮原子渗透到金属表面形成氮化物层。
液体氮化则是将金属浸泡在含氮化物的液体中进行处理。
无论是气体氮化还是液体氮化,都可以有效提高金属的性能,延长其使用寿命。
在东莞,金属氮化处理工艺被广泛应用于各个行业。
特别是在汽车、航空航天、机械制造等领域,氮化处理不仅可以提高零部件的硬度和耐磨性,还可以减少零部件的摩擦系数,提高整体装置的性能。
东莞作为中国制造业的重要基地,拥有众多制造企业,金属氮化处理工艺的发展也得到了众多企业的重视。
这些企业通过引进先进的氮化设备和工艺,不断提高产品质量和市场竞争力。
随着科技的不断进步,金属氮化处理工艺也在不断发展和完善。
目前,一些新型的氮化工艺已经被引入到东莞地区。
比如等离子体氮化、扩散氮化等高端氮化工艺,可以实现更高的氮化深度和氮化均匀性,提高金属的整体性能。
同时,一些绿色环保的氮化工艺也逐渐得到应用,减少了对环境的污染,符合可持续发展的要求。
在未来,随着东莞制造业的不断发展,金属氮化处理工艺将会继续发挥重要作用。
企业应该不断引进新技术,推动氮化工艺的创新和升级,提高产品质量和工艺水平。
同时,相关部门和企业应该加强合作,制定相关标准和规范,推动金属氮化处理工艺的健康发展。
相信在大家的共同努力下,东莞金属氮化处理工艺将会迎来更加美好的未来。
佛山真空离子氮化工艺
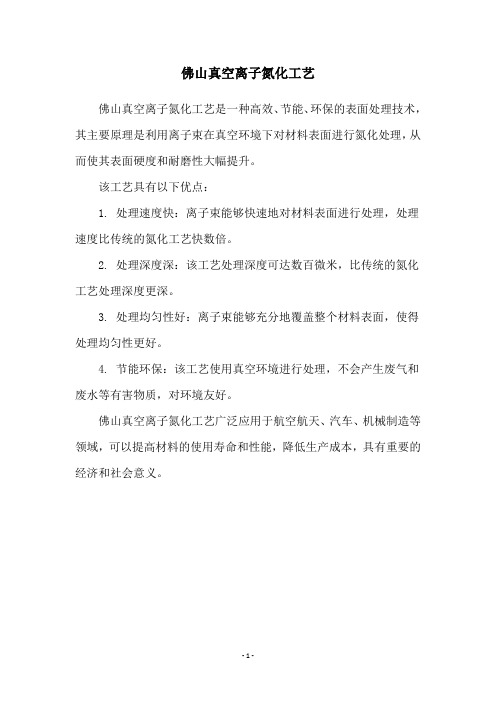
佛山真空离子氮化工艺
佛山真空离子氮化工艺是一种高效、节能、环保的表面处理技术,其主要原理是利用离子束在真空环境下对材料表面进行氮化处理,从而使其表面硬度和耐磨性大幅提升。
该工艺具有以下优点:
1. 处理速度快:离子束能够快速地对材料表面进行处理,处理速度比传统的氮化工艺快数倍。
2. 处理深度深:该工艺处理深度可达数百微米,比传统的氮化工艺处理深度更深。
3. 处理均匀性好:离子束能够充分地覆盖整个材料表面,使得处理均匀性更好。
4. 节能环保:该工艺使用真空环境进行处理,不会产生废气和废水等有害物质,对环境友好。
佛山真空离子氮化工艺广泛应用于航空航天、汽车、机械制造等领域,可以提高材料的使用寿命和性能,降低生产成本,具有重要的经济和社会意义。
- 1 -。
中科院金属材料表面氮化技术获成功

中科院金属材料表面氮化技术获成功
佚名
【期刊名称】《电镀与涂饰》
【年(卷),期】2005(24)3
【摘要】日前,中科院金属材料科学国家实验室采用表面氮化技术,在300℃的温度环境中成功实现纯铁块的表面氮化,突破了长期以来金属表面氮化应用中的技术“瓶颈”,被两院院士评为中国十大科技进展之一。
【总页数】1页(P53-53)
【关键词】表面氮化技术;金属材料;金属表面;纯铁;中国;“瓶颈”;成功;中科院;突破;国家实验室
【正文语种】中文
【中图分类】TQ342;TG174.4
【相关文献】
1.我国金属材料表面纳米化技术获重大进展 [J],
2.我国金属材料表面纳米化技术重要进展在300℃下获得的表面氮化层具有很高的硬度、耐磨性和耐腐蚀性 [J],
3.中科院在铝合金表面防护技术研究方面获进展 [J], 佳工
4.中科院氮化硼表面制备石墨烯单晶研究获突破 [J], 科苑
5.“金属材料表面纳米化技术和机理”获2009年度辽宁省自然科学一等奖 [J],因版权原因,仅展示原文概要,查看原文内容请购买。
- 1、下载文档前请自行甄别文档内容的完整性,平台不提供额外的编辑、内容补充、找答案等附加服务。
- 2、"仅部分预览"的文档,不可在线预览部分如存在完整性等问题,可反馈申请退款(可完整预览的文档不适用该条件!)。
- 3、如文档侵犯您的权益,请联系客服反馈,我们会尽快为您处理(人工客服工作时间:9:00-18:30)。
国内外氮化工艺新进展作者:张耀军来源:《职业·中旬》2011年第09期渗氮,就是将工件放在一定的渗氮剂中加热和保温,使渗氮剂中的活性原子氮渗入工件表层,以改变工件表面的化学成分、组织和性能的热处理方法。
下面笔者就谈一谈国内外氮化工艺的发展进程。
一、稀土催渗的快速气体渗氮在气体渗氮过程中加入一种稀土催渗剂,能够活化工件表面,加快氮原子吸收速度,不但缩短渗氮周期,还能够在工件表面形成细小弥散的氮化物,改善渗氮后组织和质量。
其中,脆性级别、氮化物级别和疏松级别都可控制到1级,并提高表面硬度(比常规工艺提高30~100HV)。
对于一般结构钢渗层深度要求0.3mm时,采用常规渗氮工艺保温时间需要30小时以上,但如果加入稀土催渗剂后,保温时间仅用14小时,缩短时间53%,节电40%,省氮气35%以上,同时少排放废气35%,整个渗氮周期缩短32.7%。
二、连续式气体软氮化及发黑处理传统的气体氮化热处理是在周期式井式炉或者箱式炉中进行的。
对大型工件,这种设备及工艺能够满足生产需求,但对于中小工件,在这种炉中进行气体氮化就容易出现加热不均、渗层不均、硬度不均等问题。
此外,由于周期式氮化效果不好,每一炉都有误差,因此,大大增加了操作难度,并且不易保证所有批次工件的质量均匀一致。
大连圣洁公司针对目前的中小工件按照传统气体氮化热处理工艺不能获得很好效果的问题,提出了一种中小工件气体氮化的热处理新工艺,采用连续式热处理炉,包括但不局限于网带式连续热处理炉、托辊式连续热处理炉、滚动底式连续热处理炉、推杆炉等,通过调整通入气体流量和氨分解率可控制渗层深度及表面化合物层的深度。
冷却方式有水冷、油冷或空冷(专利申请号:200910012783.4)。
该发明突破了传统思维的缺点,创造性地将中小工件在连续炉中进行气体氮化,解决了传统周期式炉中气体渗氮的诸多缺点,不但大大提高了产品渗氮后的质量和热处理过程的一致性,且由于温度和时间均可连续调整,使操作简单易行并可成倍提高生产效率。
三、集5项专利于一身的脉冲电源辉光离子氮化炉由大连圣洁公司研制的辉光离子氮化炉集5项专利于一身,并根据客户的实际需要而量身定做,为大连开发区盘起工业公司(日本独资企业)制作的一台100kW Φ1000mm×2000mm的离子氮化炉,用于处理Φ2mm×400mm的模具顶杆及其他模具配件。
由于专利技术的炉体结构设计,氮化后的顶杆不仅性能及组织全部合格,且变形程度也达到了日本标准的要求。
离子渗氮作为一种有效的钢铁及合金表面强化技术,在工业领域已得到了广泛的应用。
离子渗氮取代传统的气体渗氮已成为一种必然趋势。
随着离子渗氮技术应用范围的日益拓展,传统的直流电源离子渗氮设备在某些应用领域已不能很好地满足工艺生产的需求,带脉冲电源的辉光离子氮化炉正是在这种需求下应运而生的。
与传统的直流电源相比,脉冲电源具有如下优点:第一,能更可靠迅速灭弧,散弧清理速度快;第二,脉冲电源有抑制空心阴极效应的作用,解决了具有深孔或沟槽的复杂零件的氮化问题,有效提高了氮化工件温度的均匀性及氮化层组织的均匀性;第三,脉冲电源将放电的物理参数(气压、电压、电流)与控温参数(即占空比)分开,增加了工艺的可调性,易于选择最佳工艺参数;第四,脉冲电源更节能;第五,与同功率的直流电源相比,脉冲电源可提高设备的有效功率输出。
四、盐浴氮化及QPQ复合处理最早的盐浴氮化称为低温氰化,温度一般为520~560℃。
常用的液体氰化盐浴通常用中性盐氯化钠、氯化钡、氯化钾、碳酸钠等,常用的氰化物盐有氰化钠和氰化钾等,并仅适用于高速钢工具。
另外,还有称作液体硫氮共渗的盐浴氮化,配方为氯化钡30%、氯化钠20%、氯化钙50%,另加5%~10%(中性盐总重量),成粉末状的硫化亚铁,其盐浴含硫量不低于0.2%,再通入一定量的氨气(NH3),促使盐浴翻动。
工艺参数是:温度540℃~560℃,时间90~120分钟。
1.盐浴氮碳共渗方法国外提出了盐浴氮碳共渗的方法,包括软氮化、Tenifer法;Tufftriding、新Tenifer法、Melonizing、Sulfinuz法、Sur-Sulf法等。
国外的盐浴碳氮共渗在含氰化物和氰酸盐的熔盐中进行,熔盐中氰酸盐的热分解以及其他化学反应产生有扩散能力的氮,置于熔盐中的铁质工件表面和在气体渗氮时一样,起催化剂的作用。
2.QPQ盐浴复合处理技术中国的QPQ盐浴复合处理技术,是“九五”期间国家级重点推广项目。
QPQ一词来源于英文Quench-Polish-Quench一词的字头缩写,原意为淬火(快冷)—抛光—淬火(快冷),后有些专家学者把不加抛光工序的盐浴复合处理和增加了抛光工序的QPQ技术结合起来,统称为QPQ盐浴复合处理技术。
QPQ盐浴复合处理技术有以下特点:(1)良好的耐磨性、耐疲劳性能。
大量生产应用及试验证明,该技术可以提高工模具寿命2倍以上。
严格的滚动和滑动磨损试验说明,45钢、40Cr钢经QPQ盐浴复合处理后,其耐磨性比高频淬火高15倍以上,比20钢渗碳淬火高10倍以上,比镀硬铬和离子渗氮高2倍以上。
调质的45钢经QPQ盐浴复合处理以后疲劳强度提高40%。
(2)极好的抗蚀性。
45钢经QPQ盐浴复合处理以后,在大气和盐雾试验中的抗蚀性比发黑高70倍以上,比镀硬铬高16倍以上,甚至比1Cr18Ni9Ti奥氏体不锈钢还高几倍。
(3)极小的变形。
QPQ盐浴复合处理以后工件的尺寸和形状几乎无变化。
在最佳工艺状态下,工件尺寸的胀缩量仅仅为0.005mm。
工件形状的变化也极小,如可以成功地使(508mm×457mm×1.5mm)2Cr13不锈钢薄板处理后平面度保证在0.5mm以下。
因此,该技术可以用来解决常规热处理方法无法解决的硬化变形难题。
(4)大幅度节能。
与常规热处理技术相比,该技术处理温度低、保温时间短,可以大幅度节能。
与渗碳淬火相比,可以节能50%以上。
(5)无公害。
该技术在大量生产条件下,经各地环保部门在生产现场实地检测,各项环保指标均低于国家环保排放标准允许值。
迪高沙公司曾因这项技术获德国环保奖。
QPQ盐浴复合处理技术的“复合”一词说明它不是一种单一的技术。
“复合”的概念首先体现在它是渗氮(氮碳共渗)和氧化工序的复合;在性能上,它是高耐磨性与高抗蚀性的复合;在工艺上,它是热处理技术与防腐技术的复合。
五、盐浴钛氮化大连圣洁公司的工程师深入细致地研究了在盐浴氮化时钛的催渗机理,成功地申报了两项发明专利(专利申请号:99112897.4;专利申请号:200910012783.4)。
早在20世纪70年代,为了改变气体渗氮时间长、硬度不均等缺点,广大的工程技术人员和车间工人投入了大量的精力和时间,研究了在氮化时加入电解钛而使渗速加快、渗层加深的工艺,当时叫做镀钛氮化,并在一些产品上进行了试用,还对钛氮化和普通气体氮化、盐浴氮化进行了对比试验。
实际生产表明,钛氮化能大大加快渗速,并使工件的硬度大大提高,从而大大提高了钻头、刀具、工具、模具的使用寿命。
特别对于高速钢制造的钻头和刀具等,既克服了其他氮化造成刀口脆性而降低使用寿命的缺点,又使寿命大大提高。
试验结果还指出,对于PVD镀膜的钻头,钛氮化后也能提高寿命14.5倍。
为了进一步查明钛氮化的实质,还将预先抛光的38CrMoAl钢金相试样进行普通氮化和钛氮化,随后再进行抛光(约抛出0.02mm)制取二次碳复型,在国产DX-301电子显微镜下观察获得的氮化层电子显微组织。
比较上述结果可以看出,与普通氮化一样,钛氮化除在α铁基底上分布弥散小粒外,还存在白色条块状亮相,钛-扩钛氮化后的这种亮相的数量比钛氮化大大增加,估计这种亮相与钛有关。
当年的实践证明,钛氮化有以下特点:第一,钛氮化能在较短的时间内获得较厚和较硬的氮化层。
8小时钛氮化的深度较60小时普通氮化的要深,表面硬度没有差别;12小时钛氮化有效硬化层(HV>900)较60小时普通氮化层厚,表面硬度也高得多。
尤其是40Cr钢,8小时的钛氮化,其硬度、深度和有效硬化层都超过60小时的普通氮化。
第二,钛氮化工艺可用于任何钢铁零件,不仅限于氮化钢。
除了38CrMoAl、42CrMo、40Cr、20Cr、20号钢外,各种型号的不锈钢、高速钢、合金工具钢、弹簧钢及10号钢、Y12钢和球墨铸铁均可进行钛氮化,并能获得较满意的结果。
第三,钛氮化件有良好的耐冲击性能和疲劳强度,耐热性、耐腐蚀性能也好。
经氮化处理的3Cr2W8钢的热锻模、冲头等,其使用寿命比用其他方法热处理的要长。
第四,钛氮化处理所需时间短,并可在较低的温度下处理,工件变形小,可节约加工费用,适于大量生产。
近十年来,大连圣洁公司的工作人员继续努力进一步试验总结了钛氮化的工艺,并在钻头、工具、模具等产品上进行了批量试验,取得了较好的结果,并申报了两项发明专利。
六、英国BODYCOTE和预抽真空气体软氮化处理鲍迪克(宁波)热处理有限公司是总部在英国的鲍迪克国际PLC()的子公司。
该公司是从事热处理加工和检测的世界第一品牌。
鲍迪克集团无锡工厂的卧式预抽真空气体软氮化炉,在世界上也属于领先的设备,该设备克服了传统井式气体氮化炉的各种缺点,不但可以降低成本,而且炉子的均匀性、稳定性、可控性和可调性都特别好,因此,加工出的产品能够很好地达到汽车、航空工业高精技术标准要求,且一炉多用,氮化后还可以进行发黑处理。
七、法国HEF及舍舍夫(SURSULF)盐浴表面渗氮处理技术1.舍舍夫的优越性舍舍夫(SURSULF)过程是HEF公司开发的一种先进表面处理技术,与其他渗氮工艺相比,它具有如下优越性:(1)无公害。
整个过程几乎无污染,舍舍夫(SURSULF)炉中的氰根浓度低于0.8%,多数情况下,就像在Perkins,氰根浓度在0.4%~0.5%,目前在世界上是最低的。
其他相应过程,氰根浓度在2%~5%。
因此,舍舍夫(SURSULF)过程在世界上被认为Environmental Friendly Process”or“Environmental Acceptable process”(“与环境友好的过程”或“环境可接受的过程”)。
(2)高性能。
与其他表面方法相比,工件有更高的耐疲劳强度、耐磨性、表面硬度和耐腐蚀性,以及更低的表面摩擦系数。
与其他渗氮表面处理相比,其具有更好的工件表面外观质量。
原因之一是采用了连续自动滤渣、除渣系统,使得盐浴炉始终保持高度的纯净。
工件表面化合层厚度和结构可根据K2S的量进行调节,满足不同场合的要求,如解决磨损、点蚀和疲劳的问题,或解决咬合、粘着和拉伤问题。
所以,具有极好的性能价格比。
(3)高效率。
由于在盐浴炉中加入了锂(Li)等元素,使渗氮的潜力大幅度提高,在达到相同化合物厚度和扩散层厚度的条件下,其处理时间要大大减少,一般处理时间在30分钟至120分钟,化合层厚度可达10~30μm。