氮化工艺内容
氮化工艺的工艺流程与注意事项

氮化工艺的工艺流程与注意事项下载温馨提示:该文档是我店铺精心编制而成,希望大家下载以后,能够帮助大家解决实际的问题。
文档下载后可定制随意修改,请根据实际需要进行相应的调整和使用,谢谢!并且,本店铺为大家提供各种各样类型的实用资料,如教育随笔、日记赏析、句子摘抄、古诗大全、经典美文、话题作文、工作总结、词语解析、文案摘录、其他资料等等,如想了解不同资料格式和写法,敬请关注!Download tips: This document is carefully compiled by theeditor. I hope that after you download them,they can help yousolve practical problems. The document can be customized andmodified after downloading,please adjust and use it according toactual needs, thank you!In addition, our shop provides you with various types ofpractical materials,such as educational essays, diaryappreciation,sentence excerpts,ancient poems,classic articles,topic composition,work summary,word parsing,copy excerpts,other materials and so on,want to know different data formats andwriting methods,please pay attention!氮化工艺是一种重要的化学工程,广泛应用于金属材料的表面处理和硬化。
氮化炉的氮化工艺

氮化炉的氮化工艺
1氮化工艺简介
氮化工艺是一种利用催化剂氮化物在暴露于加热的一定温度和气压环境下,使物料(包括金属)表面产生一层氮化膜的重要过程,可使金属表面的性能及寿命极大的提高。
氮化工艺广泛应用于日常生活中的许多产品,由于其具有良好的防锈性能,耐磨性和耐腐蚀性,因而被广泛应用在食品加工、石油化工、医药卫生、精密仪器、汽车制造等行业中。
2氮化炉的使用
氮化炉是一种便携式设备,主要用于对金属表面氮化处理,可把金属表面贴上一层氮化表面层。
氮化炉通常用于多种金属材料的氮化处理,其中包括各种金属合金、钣金件、碳钢件、易切削金属和非金属材料。
氮化炉采用可控温设计,具有定时和定温功能,氮化处理程序可自动完成,可有效地降低劳动强度,保证处理质量。
3氮化炉的氮化工艺
1.启动炉子,调节回气口和氮气口的门到位,根据各种金属材料选择相应门比,调节门比后将气体杂质除去。
2.将要氮化处理的零件放入氮化炉中。
3.选择合适的温度,根据不同的金属和处理目的选择合适的温度设置,将氮化炉整体加热至设定温度,保持温度一段时间,完成氮化处理。
4.将氮化炉内的零件清除出来,打开门,取出零件,完成氮化处理,氮化工艺完成。
氮化工艺流程

氮化工艺流程
《氮化工艺流程》
氮化工艺是一种常用的表面处理工艺,能够提高材料的硬度、耐磨性和耐腐蚀性。
氮化工艺流程通常包括以下步骤:
1. 预处理:在氮化之前,需要对待处理的材料进行清洗和除油处理。
这一步骤的目的是确保表面干净,并且可以提高氮的渗透性。
2. 氮化:在经过预处理的材料表面加温,然后暴露在氮气环境中,使氮原子渗透到材料表面。
氮原子将会在材料表面形成氮化层,提高材料的硬度和耐磨性。
3. 后处理:氮化完成后,材料需要进行后处理工艺,通常包括淬火、回火等热处理,以使材料达到期望的强度和硬度。
4. 表面处理:为了提高材料表面的光泽度和耐腐蚀性,可以进行抛光、打磨等表面处理工艺。
氮化工艺流程可以应用于各种材料,包括钢铁、铝合金、不锈钢等。
氮化后的材料不仅表面硬度和耐磨性提高,还具有优异的耐腐蚀性能。
氮化工艺流程的优点是工艺简单、成本低廉、效果明显,因此得到广泛应用。
在汽车零部件、机械制造、航空航天等行业中都有着重要的应用价值。
随着科学技术的不断发展,氮化工艺
流程也在不断完善和提高,为材料提供了更加优质的表面处理解决方案。
氮化处理的工艺
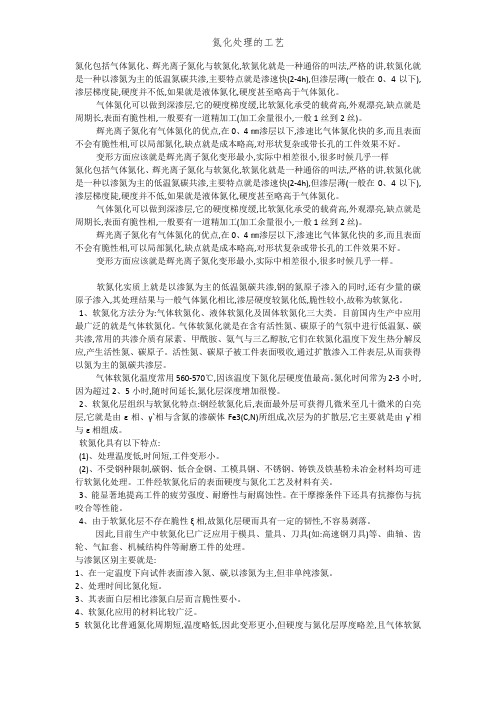
氮化包括气体氮化、辉光离子氮化与软氮化,软氮化就是一种通俗的叫法,严格的讲,软氮化就是一种以渗氮为主的低温氮碳共渗,主要特点就是渗速快(2-4h),但渗层薄(一般在0、4以下),渗层梯度陡,硬度并不低,如果就是液体氮化,硬度甚至略高于气体氮化。
气体氮化可以做到深渗层,它的硬度梯度缓,比软氮化承受的载荷高,外观漂亮,缺点就是周期长,表面有脆性相,一般要有一道精加工(加工余量很小,一般1丝到2丝)。
辉光离子氮化有气体氮化的优点,在0、4㎜渗层以下,渗速比气体氮化快的多,而且表面不会有脆性相,可以局部氮化,缺点就是成本略高,对形状复杂或带长孔的工件效果不好。
变形方面应该就是辉光离子氮化变形最小,实际中相差很小,很多时候几乎一样氮化包括气体氮化、辉光离子氮化与软氮化,软氮化就是一种通俗的叫法,严格的讲,软氮化就是一种以渗氮为主的低温氮碳共渗,主要特点就是渗速快(2-4h),但渗层薄(一般在0、4以下),渗层梯度陡,硬度并不低,如果就是液体氮化,硬度甚至略高于气体氮化。
气体氮化可以做到深渗层,它的硬度梯度缓,比软氮化承受的载荷高,外观漂亮,缺点就是周期长,表面有脆性相,一般要有一道精加工(加工余量很小,一般1丝到2丝)。
辉光离子氮化有气体氮化的优点,在0、4㎜渗层以下,渗速比气体氮化快的多,而且表面不会有脆性相,可以局部氮化,缺点就是成本略高,对形状复杂或带长孔的工件效果不好。
变形方面应该就是辉光离子氮化变形最小,实际中相差很小,很多时候几乎一样。
软氮化实质上就是以渗氮为主的低温氮碳共渗,钢的氮原子渗入的同时,还有少量的碳原子渗入,其处理结果与一般气体氮化相比,渗层硬度较氮化低,脆性较小,故称为软氮化。
1、软氮化方法分为:气体软氮化、液体软氮化及固体软氮化三大类。
目前国内生产中应用最广泛的就是气体软氮化。
气体软氮化就是在含有活性氮、碳原子的气氛中进行低温氮、碳共渗,常用的共渗介质有尿素、甲酰胺、氨气与三乙醇胺,它们在软氮化温度下发生热分解反应,产生活性氮、碳原子。
氮化工艺及操作方法

氮化工艺及操作方法
氮化工艺是一种通过在材料表面上形成氮化层的方法,常用于增加材料的硬度、耐磨性和耐腐蚀能力。
下面是氮化工艺的一般操作方法:
1. 准备工作:将需要进行氮化处理的材料进行清洗和去油处理,确保表面干净。
2. 装载材料:将清洗过的材料放入氮化炉中,注意避免材料之间的接触。
3. 创建氮化气氛:将氮化炉加热至适当温度,同时通入氮气或氨气,以产生合适的氮化气氛。
4. 加热处理:将材料在氮化气氛中加热至适当温度,使其表面发生化学反应形成氮化层。
加热时间和温度根据材料类型和所需的氮化层厚度而定。
5. 性能调节:根据需要,可以在氮化过程中进行一些特殊处理,如控制温度变化、添加特殊气体等,以调节氮化层的性能。
6. 冷却:在氮化过程结束后,将材料逐渐冷却到室温。
7. 检测和分析:对氮化后的材料进行检查和分析,以确保氮化层的质量和性能满足要求。
需要注意的是,氮化工艺的操作方法会根据具体的材料和氮化要求而有所不同,以上是一般的操作流程。
在实际操作中,应根据具体情况采取恰当的措施和控制参数,以确保氮化效果的稳定和一致性。
不锈钢氮化处理工艺

不锈钢氮化处理工艺一、前期准备1.确定氮化处理的目的和要求,包括硬度、耐磨性、抗腐蚀性等。
2.选择适合的不锈钢材料,如SUS304、SUS316L等。
3.进行表面清洁,去除油污、锈蚀等杂质。
4.进行表面抛光,使表面光滑。
二、氮化处理工艺流程1.真空干燥处理将不锈钢制品放入真空干燥室中,在高温高真空条件下进行预处理。
该过程主要是为了去除制品表面的水分和氧化物,以保证后续处理的效果。
2.氮化处理将预处理后的不锈钢制品放入氮化炉中,在一定温度下与氨气反应生成氮化层。
根据不同要求可分为浅层氮化和深层氮化两种方式。
浅层氮化可提高制品表面硬度和耐磨性;深层氮化则可提高整体强度和耐腐蚀性。
3.冷却将经过氮化处理后的不锈钢制品从炉内取出,进行自然冷却或水冷却。
自然冷却时间较长,但能避免由于快速冷却导致的变形和裂纹;水冷却则能更快地降温,但容易引起变形和裂纹。
4.后处理将经过氮化处理和冷却的不锈钢制品进行后处理,包括磨光、清洗、防锈等。
此过程有助于保证制品表面光滑度和整体质量。
三、工艺参数1.氮化温度:一般在500℃-600℃之间。
2.氮化时间:根据不同要求可在2-8小时之间。
3.气氛成分:主要为氨气和氮气混合物。
4.真空度:在真空干燥处理时应维持高真空状态。
5.冷却方式:可选择自然冷却或水冷却。
四、注意事项1.不锈钢材料必须进行表面清洁和抛光,否则会影响后续处理效果。
2.在进行氮化处理时应严格控制温度、时间和气氛成分等参数,以保证处理效果。
3.在进行冷却时应注意避免变形和裂纹的发生。
4.后处理过程中应注意防止制品表面受到损伤和污染。
5.在整个处理过程中应注意安全,避免发生意外事故。
五、总结不锈钢氮化处理是一种有效提高不锈钢材料性能的方法。
通过严格控制工艺参数和注意事项,可获得理想的氮化层厚度和性能。
在实际应用中,应根据具体要求选择不同的氮化方式和工艺参数,以达到最佳效果。
气体氮化的工艺流程
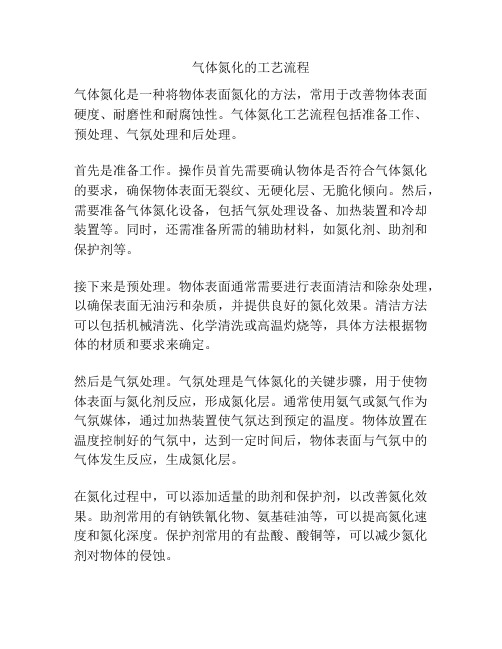
气体氮化的工艺流程气体氮化是一种将物体表面氮化的方法,常用于改善物体表面硬度、耐磨性和耐腐蚀性。
气体氮化工艺流程包括准备工作、预处理、气氛处理和后处理。
首先是准备工作。
操作员首先需要确认物体是否符合气体氮化的要求,确保物体表面无裂纹、无硬化层、无脆化倾向。
然后,需要准备气体氮化设备,包括气氛处理设备、加热装置和冷却装置等。
同时,还需准备所需的辅助材料,如氮化剂、助剂和保护剂等。
接下来是预处理。
物体表面通常需要进行表面清洁和除杂处理,以确保表面无油污和杂质,并提供良好的氮化效果。
清洁方法可以包括机械清洗、化学清洗或高温灼烧等,具体方法根据物体的材质和要求来确定。
然后是气氛处理。
气氛处理是气体氮化的关键步骤,用于使物体表面与氮化剂反应,形成氮化层。
通常使用氨气或氮气作为气氛媒体,通过加热装置使气氛达到预定的温度。
物体放置在温度控制好的气氛中,达到一定时间后,物体表面与气氛中的气体发生反应,生成氮化层。
在氮化过程中,可以添加适量的助剂和保护剂,以改善氮化效果。
助剂常用的有钠铁氰化物、氨基硅油等,可以提高氮化速度和氮化深度。
保护剂常用的有盐酸、酸铜等,可以减少氮化剂对物体的侵蚀。
最后是后处理。
气体氮化后,物体需进行退火处理或淬火处理,以消除氮化过程中产生的应力和提高材料性能。
退火处理可以采用氮化前的热处理方法,根据材料的要求和氮化条件来确定。
淬火处理可通过快速冷却的方法,使物体表面形成高硬度的氮化层。
总而言之,气体氮化工艺流程包括准备工作、预处理、气氛处理和后处理。
通过这些步骤,可以对物体表面进行氮化,提高物体的硬度、耐磨性和耐腐蚀性。
气体氮化在汽车零部件、工具钢、模具材料等领域得到广泛应用,为各行各业的发展提供了有力支持。
金属氮化工艺

金属氮化工艺金属氮化工艺是一种重要的表面处理方法,通过在金属表面形成氮化层,提高了金属的硬度、耐磨性和耐腐蚀性。
这种工艺广泛应用于航空航天、汽车制造、机械制造等领域,为提高产品性能和延长使用寿命起到了关键作用。
在金属氮化工艺中,最常用的方法是气体氮化和离子氮化。
气体氮化是将金属置于氨气或氮气气氛中,在高温下进行处理,使氮原子渗透到金属表面形成氮化层。
离子氮化则是通过离子束轰击金属表面,使氮原子在金属表面形成氮化层。
这两种方法各有优缺点,需要根据具体情况选择合适的工艺。
金属氮化工艺可以显著提高金属的硬度。
通过形成氮化层,金属的表面硬度可以提高几倍甚至几十倍,大大增强了金属的耐磨性。
这对于需要承受高强度摩擦的零部件尤为重要,可以延长使用寿命,减少维护成本。
此外,氮化层还可以提高金属的耐腐蚀性,增强其抗氧化能力,使其在恶劣环境下仍能保持良好的性能。
除了提高金属的性能,金属氮化工艺还可以改善金属的外观。
氮化层通常具有金属光泽,使金属表面看起来更加美观。
这对于一些需要外观精美的产品尤为重要,如高档手表、珠宝等。
同时,氮化层还可以增加金属的抗刮擦能力,使其表面更加光滑,不易受到损伤。
在实际应用中,金属氮化工艺还可以根据需要进行进一步的改进和优化。
例如,可以通过控制氮化工艺参数,调整氮化层的厚度和组织结构,以满足不同的使用要求。
同时,还可以将金属氮化工艺与其他表面处理方法结合,如涂层、喷涂等,进一步提高金属的性能和功能。
总的来说,金属氮化工艺是一种重要的表面处理方法,可以显著提高金属的硬度、耐磨性和耐腐蚀性,改善金属的外观,延长使用寿命。
随着技术的不断进步和应用领域的不断拓展,金属氮化工艺将在更多领域发挥重要作用,为推动工业发展和提升产品品质做出贡献。
金属氮化工艺

金属氮化工艺引言金属氮化工艺是一种将金属与氮气反应形成金属氮化物薄膜的技术。
金属氮化物具有高硬度、优异的耐磨、耐腐蚀和高温稳定性等特性,广泛应用于硬质涂层、陶瓷刀具、光学薄膜和电子器件等领域。
本文将对金属氮化工艺进行全面、详细、完整且深入地探讨。
金属氮化工艺的分类金属氮化工艺可以根据反应方式和工艺条件的不同而分为几种不同类型,包括:氨气氮化法氨气氮化法是最常用的金属氮化工艺。
在这种方法中,金属材料在氨气氛中加热反应,通过反应生成金属氮化物。
该方法简单、经济,并且可以得到均匀的薄膜。
离子氮化法离子氮化法利用离子束轰击金属材料表面,使其表面发生化学反应,生成金属氮化薄膜。
这种方法可以在较低的温度下实现金属氮化,对基材的损伤较小。
等离子体氮化法等离子体氮化法是一种利用等离子体反应进行金属氮化的方法。
在等离子体氛围中,金属材料表面发生离子反应,生成金属氮化物薄膜。
这种方法形成的氮化薄膜致密、均匀,并且具有较高的附着力。
金属氮化工艺的优势和应用金属氮化工艺具有许多优势,使其在多个领域得到广泛应用。
以下是金属氮化工艺的几个优势和应用示例:高硬度通过金属氮化工艺制备的金属氮化物薄膜具有很高的硬度,可达到几千至几万兆帕。
这使得金属氮化物薄膜非常适用于硬质涂层、陶瓷刀具等领域,提高其耐磨性和使用寿命。
优异的耐腐蚀性金属氮化物具有较好的耐腐蚀性,能够抵抗许多化学腐蚀介质的侵蚀。
因此,金属氮化物薄膜广泛应用于防腐蚀涂层、管道材料等领域。
高温稳定性金属氮化物薄膜具有较好的高温稳定性,能够在高温环境下保持其性能。
这使得金属氮化物薄膜在航空航天、汽车发动机等高温领域得到广泛应用。
光学应用某些金属氮化物薄膜具有良好的光学性能,如低反射、高透过率等特性。
这使得金属氮化物薄膜被广泛应用于光学镀膜、太阳能电池等领域。
金属氮化工艺的研究进展金属氮化工艺的研究一直在不断进展,以提高工艺效率和薄膜性能。
以下是几个金属氮化工艺的研究方向:气相沉积技术改进气相沉积技术是金属氮化工艺中常用的一种方法。
氮化处理工艺 -回复

氮化处理工艺 -回复
氮化处理工艺是指将材料表面暴露在氮气环境中,通过热处理使氮原子渗透到材料表层形成氮化层的一种表面处理技术。
氮化处理可以提高材料的硬度、耐磨性、耐腐蚀性和高温性能,同时还可以改善材料的表面光洁度和抗氧化性能。
常见的氮化处理工艺包括气体氮化、盐浴氮化和离子氮化等。
气体氮化是将材料置于高温高氮气氛中进行处理,通过热扩散使氮原子渗透到材料表层形成氮化层。
盐浴氮化是将材料浸泡在含有氮化剂的盐浴中加热处理,使氮原子渗透到材料表层。
离子氮化则是通过在真空中向材料表面轰击氮离子,使氮原子从离子束中沉积到材料表面。
氮化处理可以应用于各种材料,包括金属、陶瓷和塑料等。
它被广泛应用于工业领域,如航空航天、汽车、机械制造等。
氮化处理可以提高材料的硬度和耐磨性,延长材料的使用寿命,同时还可以改善材料的表面品质和耐蚀性能。
需要指出的是,氮化处理是一项复杂的工艺,需要控制好处理温度、氮气浓度和处理时间等参数,以确保处理效果的稳定性和一致性。
氮化曲轴工艺流程加工工艺
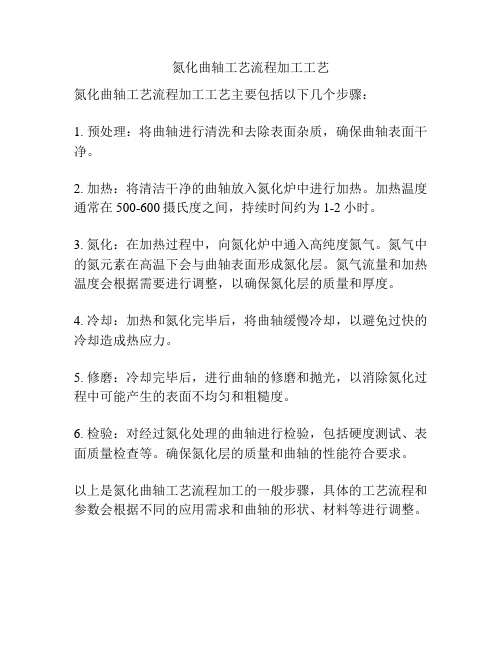
氮化曲轴工艺流程加工工艺
氮化曲轴工艺流程加工工艺主要包括以下几个步骤:
1. 预处理:将曲轴进行清洗和去除表面杂质,确保曲轴表面干净。
2. 加热:将清洁干净的曲轴放入氮化炉中进行加热。
加热温度通常在500-600摄氏度之间,持续时间约为1-2小时。
3. 氮化:在加热过程中,向氮化炉中通入高纯度氮气。
氮气中的氮元素在高温下会与曲轴表面形成氮化层。
氮气流量和加热温度会根据需要进行调整,以确保氮化层的质量和厚度。
4. 冷却:加热和氮化完毕后,将曲轴缓慢冷却,以避免过快的冷却造成热应力。
5. 修磨:冷却完毕后,进行曲轴的修磨和抛光,以消除氮化过程中可能产生的表面不均匀和粗糙度。
6. 检验:对经过氮化处理的曲轴进行检验,包括硬度测试、表面质量检查等。
确保氮化层的质量和曲轴的性能符合要求。
以上是氮化曲轴工艺流程加工的一般步骤,具体的工艺流程和参数会根据不同的应用需求和曲轴的形状、材料等进行调整。
氮化处理的工艺
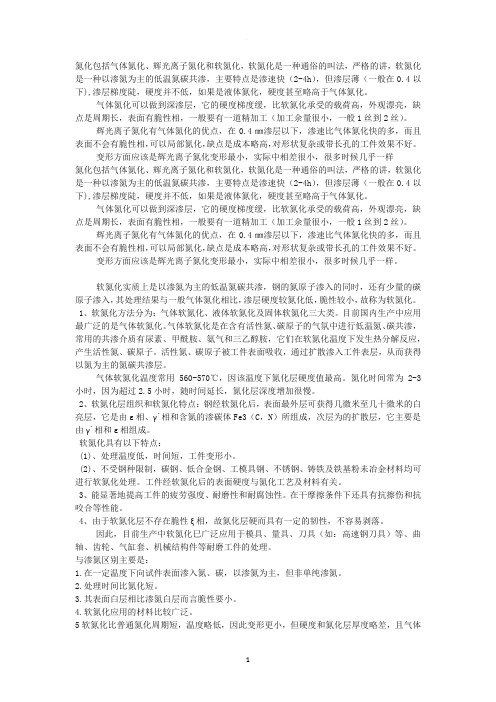
氮化包括气体氮化、辉光离子氮化和软氮化,软氮化是一种通俗的叫法,严格的讲,软氮化是一种以渗氮为主的低温氮碳共渗,主要特点是渗速快(2-4h),但渗层薄(一般在0.4以下),渗层梯度陡,硬度并不低,如果是液体氮化,硬度甚至略高于气体氮化。
气体氮化可以做到深渗层,它的硬度梯度缓,比软氮化承受的载荷高,外观漂亮,缺点是周期长,表面有脆性相,一般要有一道精加工(加工余量很小,一般1丝到2丝)。
辉光离子氮化有气体氮化的优点,在0.4㎜渗层以下,渗速比气体氮化快的多,而且表面不会有脆性相,可以局部氮化,缺点是成本略高,对形状复杂或带长孔的工件效果不好。
变形方面应该是辉光离子氮化变形最小,实际中相差很小,很多时候几乎一样氮化包括气体氮化、辉光离子氮化和软氮化,软氮化是一种通俗的叫法,严格的讲,软氮化是一种以渗氮为主的低温氮碳共渗,主要特点是渗速快(2-4h),但渗层薄(一般在0.4以下),渗层梯度陡,硬度并不低,如果是液体氮化,硬度甚至略高于气体氮化。
气体氮化可以做到深渗层,它的硬度梯度缓,比软氮化承受的载荷高,外观漂亮,缺点是周期长,表面有脆性相,一般要有一道精加工(加工余量很小,一般1丝到2丝)。
辉光离子氮化有气体氮化的优点,在0.4㎜渗层以下,渗速比气体氮化快的多,而且表面不会有脆性相,可以局部氮化,缺点是成本略高,对形状复杂或带长孔的工件效果不好。
变形方面应该是辉光离子氮化变形最小,实际中相差很小,很多时候几乎一样。
软氮化实质上是以渗氮为主的低温氮碳共渗,钢的氮原子渗入的同时,还有少量的碳原子渗入,其处理结果与一般气体氮化相比,渗层硬度较氮化低,脆性较小,故称为软氮化。
1、软氮化方法分为:气体软氮化、液体软氮化及固体软氮化三大类。
目前国内生产中应用最广泛的是气体软氮化。
气体软氮化是在含有活性氮、碳原子的气氛中进行低温氮、碳共渗,常用的共渗介质有尿素、甲酰胺、氨气和三乙醇胺,它们在软氮化温度下发生热分解反应,产生活性氮、碳原子。
氮化处理的工艺
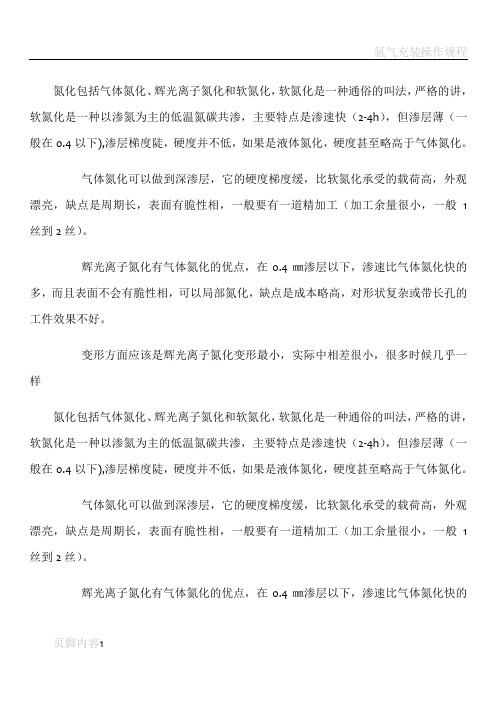
氮化包括气体氮化、辉光离子氮化和软氮化,软氮化是一种通俗的叫法,严格的讲,软氮化是一种以渗氮为主的低温氮碳共渗,主要特点是渗速快(2-4h),但渗层薄(一般在0.4以下),渗层梯度陡,硬度并不低,如果是液体氮化,硬度甚至略高于气体氮化。
气体氮化可以做到深渗层,它的硬度梯度缓,比软氮化承受的载荷高,外观漂亮,缺点是周期长,表面有脆性相,一般要有一道精加工(加工余量很小,一般1丝到2丝)。
辉光离子氮化有气体氮化的优点,在0.4㎜渗层以下,渗速比气体氮化快的多,而且表面不会有脆性相,可以局部氮化,缺点是成本略高,对形状复杂或带长孔的工件效果不好。
变形方面应该是辉光离子氮化变形最小,实际中相差很小,很多时候几乎一样氮化包括气体氮化、辉光离子氮化和软氮化,软氮化是一种通俗的叫法,严格的讲,软氮化是一种以渗氮为主的低温氮碳共渗,主要特点是渗速快(2-4h),但渗层薄(一般在0.4以下),渗层梯度陡,硬度并不低,如果是液体氮化,硬度甚至略高于气体氮化。
气体氮化可以做到深渗层,它的硬度梯度缓,比软氮化承受的载荷高,外观漂亮,缺点是周期长,表面有脆性相,一般要有一道精加工(加工余量很小,一般1丝到2丝)。
辉光离子氮化有气体氮化的优点,在0.4㎜渗层以下,渗速比气体氮化快的多,而且表面不会有脆性相,可以局部氮化,缺点是成本略高,对形状复杂或带长孔的工件效果不好。
变形方面应该是辉光离子氮化变形最小,实际中相差很小,很多时候几乎一样。
软氮化实质上是以渗氮为主的低温氮碳共渗,钢的氮原子渗入的同时,还有少量的碳原子渗入,其处理结果与一般气体氮化相比,渗层硬度较氮化低,脆性较小,故称为软氮化。
1、软氮化方法分为:气体软氮化、液体软氮化及固体软氮化三大类。
目前国内生产中应用最广泛的是气体软氮化。
气体软氮化是在含有活性氮、碳原子的气氛中进行低温氮、碳共渗,常用的共渗介质有尿素、甲酰胺、氨气和三乙醇胺,它们在软氮化温度下发生热分解反应,产生活性氮、碳原子。
氮化工艺流程

氮化工艺流程氮化工艺流程简介氮化是一种将氮气引入材料中,使其具备氮化物层的工艺。
氮化工艺通常用于提高材料的硬度、耐磨性和抗腐蚀性能。
这种工艺在许多工业领域中得到广泛应用,如刀具制造、汽车零部件和航空航天工业等。
本文将介绍一个氮化工艺的流程。
氮化工艺流程1. 材料准备:首先是选择适合氮化的材料。
常见的材料包括钢、不锈钢、高速钢和硬质合金等。
要确保材料的表面没有油脂和污垢,这可以通过清洁和去脂的方法来实现。
2. 预处理:在进行氮化之前,材料需要进行预处理。
预处理的目的是去除材料表面的氧化物和碳氮化物,以确保氮气能够进入材料内部。
预处理可以通过砂轮研磨、电解抛光和酸洗等方法来实现。
3. 氮化:氮化是将氮气注入材料中的过程。
有许多不同的氮化方法可供选择,如盐浴氮化、气氮化和等离子氮化等。
其中,盐浴氮化是最常见的方法之一。
在盐浴氮化中,材料被浸泡在含有氮化盐和氮化剂的盐浴中,然后加热到适当的温度。
热盐浴会产生一定的氰化物气气氛,氮气会在高温下扩散到材料表面,并在材料表面形成氮化物层。
4. 淬火和固溶处理:在完成氮化后,材料可能需要进行淬火和固溶处理来增强其性能。
淬火是将高温材料迅速冷却的过程,可以提高材料的硬度和强度。
固溶处理是将经过淬火的材料加热到中等温度,然后在恒温下保持一段时间,以改善材料的内部结构。
5. 表面处理:在氮化完成后,还可以进行表面处理,以改变氮化层的外观和性能。
表面处理可以包括抛光、磨削、研磨和电镀等方法。
6. 检测和质量控制:最后一步是对氮化材料进行检测和质量控制。
检测方法可以包括金相显微镜观察、显微硬度测试和抗腐蚀测试等。
质量控制的目的是确保氮化材料符合规定的要求和标准。
总结氮化是一种提高材料性能的重要工艺。
氮化工艺流程包括材料准备、预处理、氮化、淬火和固溶处理、表面处理以及检测和质量控制等步骤。
通过仔细选择材料和正确执行工艺流程,可以获得具有良好耐磨性、高硬度和抗腐蚀性能的氮化材料。
氮化工艺的详细讲解

氮化工艺的详细讲解#热处理基础知识氮原子序数为7,比碳大1,原子结构与碳不同,因此氮元素与铁元素的化学作用和金属晶体学作用完全不同于碳与铁的相互作用。
渗氮温度比渗碳温度低得多,渗氮层的结构也比渗碳层复杂得多。
本期分别简要介绍渗氮和氮碳共渗的原理、工艺方法、作用及渗层检查。
一、渗氮钟罩式氮化炉出炉场景1.1渗氮原理渗氮,也叫氮化,有时候为了区别软氮化,也称硬氮化,但就渗氮层硬度来讲,并无软硬之分。
渗氮工艺过程和其它化学热处理一样,包括渗剂反应、溶剂中扩散、相界面反应、氮元素在铁中扩散,以及扩散过程中氮化物的形成。
渗剂中的反应主要指渗剂中分解出含有活性氮原子的过程,该物质通过渗剂中的扩散输送至铁表面,参与界面反应,在界面反应中产生的活性氮原子被铁表面吸收,进而向内部扩散。
渗氮使用最多的介质是氨气,在渗氮温度下,氨是亚稳定的,它发生如下分解反应:2NH3<=>3H2+2[N]当活性氮原子遇到铁原子时,则发生下列反应:Fe+[N]<=>Fe(N)4Fe+[N]<=>Fe4(N)2~3Fe+[N]<=>Fe2~3(N)2Fe+[N]<=>Fe2(N)Fe-N系中存在的相如表1所示。
除表中所列各项外,Fe-N 系中可能出现含氮马氏体α´和介稳定相α〞。
前者是渗氮后快冷的产物,呈体心正方点阵,硬度较高可达650HV左右;α〞氮化物的分子式为Fe16N2,或Fe8N呈体心正方点阵。
▼表1渗氮层中各相的性质(纯铁渗氮)氮的渗入过程不同于渗碳,它是一个典型的反应扩散过程,依照Fe-N相图,不同温度下,随着渗氮时间的延长,依次形成的相各有不同。
详见表2。
▼表2纯铁渗氮层中各相的形成顺序及平衡状态下各层的相组成物渗氮层的形成过程详见图1。
在渗氮初期,表层的α固溶体未被N所饱和,渗氮层的深度可随时间的增加而增加。
随着气相中氮的不断渗入,使α达到饱和氮含量Cmax,即τ1时刻。
在τ1~τ2时间内,气相中的氮继续向工件内扩散而使α过饱和,引发α→γ´反应,产生γ´相。
氮化的作用和工艺要求

氮化的作用和工艺要求
氮化是一种工艺过程,通过在材料表面引入氮元素来改变其表面性质。
氮化常用于金属和合金的处理,其作用和工艺要求如下:
作用:
1.硬度增加:氮化可以显著提高材料表面的硬度和耐磨性,使其更耐用和耐磨损。
2.耐腐蚀性提高:经过氮化处理后的材料表面通常具有更好的抗腐蚀性能,更耐高温、耐腐蚀。
3.改善表面摩擦性能:氮化可以改善材料的表面润滑性能,降低摩擦系数。
4.提高导热性和电性能:在某些情况下,氮化处理可以提高材料的导热性和电性能。
工艺要求:
1.温度和时间控制:氮化过程通常需要在高温下进行,要求温度和时间能够精确控制。
常见的氮化方法包括气体氮化和盐浴氮化,它们的工艺条件略有不同。
2.氮气气氛:在气体氮化过程中,氮气气氛的控制是至关重要的。
材料暴露在氮气中,氮原子渗透到材料表面形成氮化层。
3.材料表面准备:在进行氮化处理之前,材料的表面通常需要经过清洁和抛光等处理,以确保氮原子能够充分渗透并均匀分布在表面。
4.冷却和处理后工艺:氮化完成后,通常需要适当的冷却和后续处理,如淬火、回火等,以保证材料具有理想的性能和结构。
5.工艺环境控制:控制氮化过程的工艺环境,包括气氛、压力、温度和处理时间等,对于确保氮化效果至关重要。
氮化是一种有效的材料表面处理方法,可以显著改善材料的性能,但需要在合适的工艺条件下进行,以确保所需的性能提升。
气体氮化的工艺流程
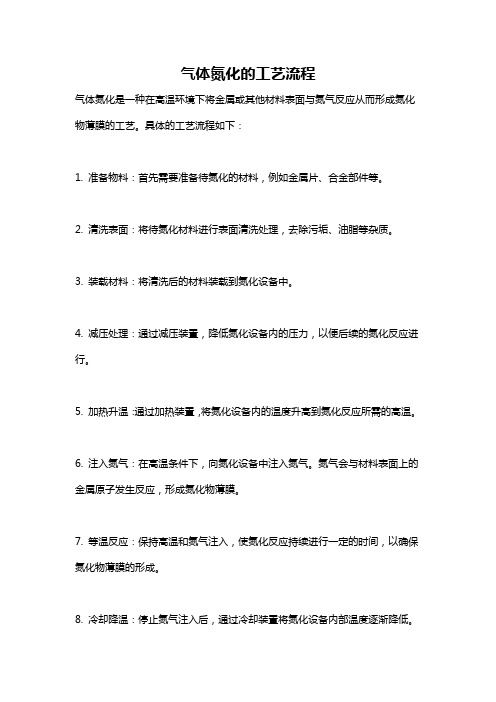
气体氮化的工艺流程
气体氮化是一种在高温环境下将金属或其他材料表面与氮气反应从而形成氮化物薄膜的工艺。
具体的工艺流程如下:
1. 准备物料:首先需要准备待氮化的材料,例如金属片、合金部件等。
2. 清洗表面:将待氮化材料进行表面清洗处理,去除污垢、油脂等杂质。
3. 装载材料:将清洗后的材料装载到氮化设备中。
4. 减压处理:通过减压装置,降低氮化设备内的压力,以便后续的氮化反应进行。
5. 加热升温:通过加热装置,将氮化设备内的温度升高到氮化反应所需的高温。
6. 注入氮气:在高温条件下,向氮化设备中注入氮气。
氮气会与材料表面上的金属原子发生反应,形成氮化物薄膜。
7. 等温反应:保持高温和氮气注入,使氮化反应持续进行一定的时间,以确保氮化物薄膜的形成。
8. 冷却降温:停止氮气注入后,通过冷却装置将氮化设备内部温度逐渐降低。
9. 取出材料:待氮化的材料经冷却后,可从氮化设备中取出,氮化过程完成。
需要注意的是,具体的氮化工艺流程会根据材料的类型、形状和要求的氮化层厚度等因素而有所不同。
此外,氮化过程中的温度、压力和氮气流量等参数也需要根据具体情况进行控制和调整。
氮化工艺技术

氮化工艺技术氮化工艺技术是一种利用高温气氛中的氮气与固体或液体材料发生反应,形成氮化物薄膜或氮化物材料的技术。
该技术具有独特的优点,广泛应用于材料加工、电子器件制备、表面改性等领域。
氮化工艺技术主要分为两种类型:气氛氮化和离子氮化。
气氛氮化是在高温氮气气氛下,通过氮化源或氨气在材料表面形成氮化物薄膜的过程。
这种方法具有操作简单、适用性广、成本低的优点。
离子氮化是将待处理物体放置在低压辉光放电等离子体中,通过离子轰击和表面反应形成氮化物薄膜。
这种方法具有薄膜质量优良、成膜速率快的优点。
氮化工艺技术在材料加工领域具有重要应用。
一方面,氮化工艺可用于制备高硬度和高氮含量的刀具涂层。
这种涂层具有优异的耐磨性和高温性能,可以显著提高刀具寿命和切削加工质量。
另一方面,氮化工艺还可用于金属、陶瓷、玻璃等材料的表面改性。
通过氮化处理,可在表面形成致密、高硬度的氮化物层,显著提高材料的抗磨损、耐腐蚀和绝缘性能。
氮化工艺技术在电子器件制备领域也有广泛应用。
一方面,氮化工艺可用于制备氮化硅(Si3N4)绝缘层。
这种绝缘层具有优异的耐电压和绝缘性能,可用于封装电子元器件,提高器件的可靠性和稳定性。
另一方面,氮化工艺还可用于制备氮化硼(BN)材料。
氮化硼具有高热导率和良好的绝缘性能,可用于制备高功率电子器件的散热材料。
除了以上应用,氮化工艺技术也被广泛应用于太阳能电池、光学薄膜等领域。
例如,氮化硅材料可用于制备太阳能电池的抗反射膜,提高光电转换效率。
氮化硼材料可用于制备光学薄膜的硬度保护层,延长薄膜的使用寿命。
总之,氮化工艺技术是一种重要的表面工艺技术,具有广泛的应用前景。
随着材料科学和制备技术的不断发展,氮化工艺技术将进一步完善和推广,为各领域的材料加工和器件制备提供更多可能性。
氮化处理的工艺知识分享
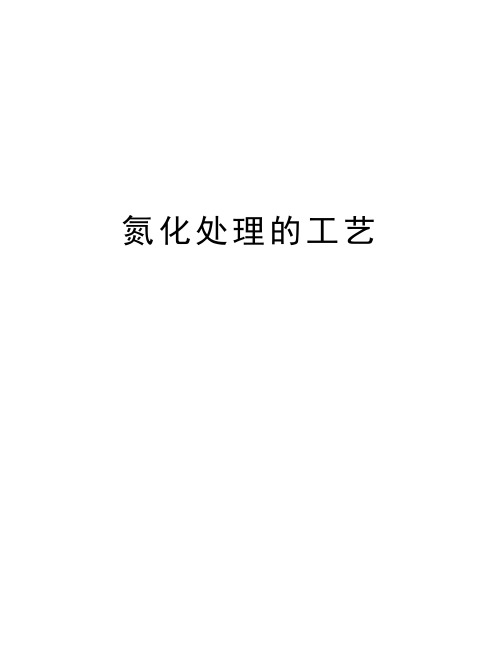
氮化处理的工艺氮化包括气体氮化、辉光离子氮化和软氮化,软氮化是一种通俗的叫法,严格的讲,软氮化是一种以渗氮为主的低温氮碳共渗,主要特点是渗速快(2-4h),但渗层薄(一般在0.4以下),渗层梯度陡,硬度并不低,如果是液体氮化,硬度甚至略高于气体氮化。
气体氮化可以做到深渗层,它的硬度梯度缓,比软氮化承受的载荷高,外观漂亮,缺点是周期长,表面有脆性相,一般要有一道精加工(加工余量很小,一般1丝到2丝)。
辉光离子氮化有气体氮化的优点,在0.4㎜渗层以下,渗速比气体氮化快的多,而且表面不会有脆性相,可以局部氮化,缺点是成本略高,对形状复杂或带长孔的工件效果不好。
变形方面应该是辉光离子氮化变形最小,实际中相差很小,很多时候几乎一样氮化包括气体氮化、辉光离子氮化和软氮化,软氮化是一种通俗的叫法,严格的讲,软氮化是一种以渗氮为主的低温氮碳共渗,主要特点是渗速快(2-4h),但渗层薄(一般在0.4以下),渗层梯度陡,硬度并不低,如果是液体氮化,硬度甚至略高于气体氮化。
气体氮化可以做到深渗层,它的硬度梯度缓,比软氮化承受的载荷高,外观漂亮,缺点是周期长,表面有脆性相,一般要有一道精加工(加工余量很小,一般1丝到2丝)。
辉光离子氮化有气体氮化的优点,在0.4㎜渗层以下,渗速比气体氮化快的多,而且表面不会有脆性相,可以局部氮化,缺点是成本略高,对形状复杂或带长孔的工件效果不好。
变形方面应该是辉光离子氮化变形最小,实际中相差很小,很多时候几乎一样。
软氮化实质上是以渗氮为主的低温氮碳共渗,钢的氮原子渗入的同时,还有少量的碳原子渗入,其处理结果与一般气体氮化相比,渗层硬度较氮化低,脆性较小,故称为软氮化。
1、软氮化方法分为:气体软氮化、液体软氮化及固体软氮化三大类。
目前国内生产中应用最广泛的是气体软氮化。
气体软氮化是在含有活性氮、碳原子的气氛中进行低温氮、碳共渗,常用的共渗介质有尿素、甲酰胺、氨气和三乙醇胺,它们在软氮化温度下发生热分解反应,产生活性氮、碳原子。
- 1、下载文档前请自行甄别文档内容的完整性,平台不提供额外的编辑、内容补充、找答案等附加服务。
- 2、"仅部分预览"的文档,不可在线预览部分如存在完整性等问题,可反馈申请退款(可完整预览的文档不适用该条件!)。
- 3、如文档侵犯您的权益,请联系客服反馈,我们会尽快为您处理(人工客服工作时间:9:00-18:30)。
渗氮、渗碳、碳氮共渗工艺专利技术大全1 CN02136610.1 高温气体渗氮淬火时效或等温淬火工艺高温气体渗氮淬火时效或等温淬火工艺属于钢铁化学热处理领域。
钢铁高温气体渗氮时,选择适当的温度、时间、氮势和冷却方法,在只含氮无碳的介质进行渗氮,表面形成ε-Fe<sub>2-3</sub>N化合物层,次表层为高氮奥氏体,渗后采用水基或油基淬火介质直接淬火,后在180~300℃时效或在奥氏体渗氮后直接于180~300℃等温。
本发明具有实质性特点和显著进步,能获得高的硬度,心部好的塑性和韧性。
可进一步减少热处理畸变,畸变程度与铁素体氮碳共渗相当。
用此工艺来代替奥氏体氮碳共渗,可以根除产生氢氰酸的根源,用来代替铁素体氮碳共渗,不仅根除氢氰酸的污染,还能提高有效硬化层的深度。
2 CN96110008.7 钢的渗氮方法一种用氮原子与钢表面反应形成一层硬质渗氮化层的钢的渗氮方法,在渗氮处理之前,将钢置于含氟化物气体或含氟气和占总体积0.5—20%的空气或占总体积0.1—4%的氧气组成的气氛中加热因此防止发生非均匀渗氮,同时可以节省昂贵的含氟化物或含氟气体的消耗。
3 CN96107326.8 高渗氮性能弹簧及其制备方法一种形成弹簧的方法,当弹簧渗氮时,当方法能降低其表面硬度和硬化层厚度的变化。
在该弹簧渗氮前,用电抛光或其它适宜的方法将其表面上形成的氧化厚度减至1.5μm或更小,以使弹簧靠近其表面的残余应力为-5kg/mm<sup>2</sup>—5kg/mm<sup>2</sup>。
用这种方法,通过渗氮提高所得弹簧的表面硬度和渗氮层厚度是可能的。
4 CN96190898.X 成型性与渗氮特性优良的渗氮钢及其冲压成型制品一种成型性和渗氮特性优良的渗氮钢,它含有(以重量为基础):C:0.0002~0.08%以下、Si:0.005~1.00%、Mn:0.010~3.00%、P:0.001~0.150%、N:0.0002~0.0100%、Cr:0.15以上~5.00%、Al:0.060以上~2.00%(当C含量为0.0002—0.0100%以下时,Al成为0.10以上~2.00%范围内的选择性元素)以及选自Ti:0.010~1.00%和V:0.010~1.00%中的1种或2种元素,其余是Fe和不可避免的杂质,该冲压成型制品是钢制品,至少在其一侧上具有硬质氮化物层。
5 CN85101602 长管内壁离子渗氮装置一种离子轰击化学热处理炉用长管内壁离子渗氮装置,它主要由自动定位的密封接头、内阳极管和定位器组成.采用钛管作为内阳极,可加速渗氮过程,改善长管内孔壁硬化的均匀性.用熔铸云母制造定位器,制作方便,寿命长,成本低.本发明的渗氮装置不仅结构简单使用方便,改进了内阳极管的安装和定位技术,而且解决了长内孔渗氮不均的质量问题.6 CN85100540 最优扩散条件动态可控渗氮技术最优扩散条件动态可控渗氮技术.本发明属黑色金属材料表面化学热处理可控渗氮新方法.解决可控渗氮所存在的渗氮速度慢和重现性差两个问题.本发明主要技术特征是在渗氮过程中使氮势跟踪最优扩散条件动态控制曲线由高而低地逐渐变化,既能控制渗氮层组织、降低渗氮层脆性,又能保持高的渗氮速度,重现性良好.本发明兼有普通渗氮和已有的可控渗氮的优点而克服了两者各自的缺点.用于38CrMoAl、3Cr<sub>2</sub>W8、Cr<sub>2</sub>、25Cr<sub>2</sub>MoV等钢种的渗氮处理.7 CN85107162 深层可控离子渗氮法本发明是关于深层可控辉光离子渗氮方法。
$为了提高合金结构钢制零件的耐疲劳性能,应尽可能地增加其渗氮层深度和抑制表面脆性化合物的产生。
本发明通过使用含氮5-50%的N<sub>2</sub>+H<sub>2</sub>混合气,经450-550℃、550-650℃、450-550℃三段共45-65小时的辉光离子渗氮,得到0.7-1.0mm的渗氮层,表面相成分为γ单相化合物或无化合物的纯扩散层。
8 CN86105732 铝及铝合金渗氮法本工艺采用两种方法:一是气体渗氮时添加洁净剂氯化铵和活化剂稀土,使铝及铝合金渗氮;另一是离子渗氮时采用交流辉光放电使渗氮气氛电离,用直流电场使离子定向运动,解决了铅及铝合金的渗氮问题。
$采用本工艺可在铝及铝合金上获得0.1到几毫米的渗氮层,渗氮层硬度纯铝HV64,铝合金HV170,可提高铝制品的强度和耐磨性,扩大铝及铝合金的用途。
9 CN87106444.8 钢制品的低温渗氮方法钢制品的低温渗氮方法是在密闭容器中用含氮物料一聚酰胺的气态产物气氛处理钢制品。
10 CN90101529.6 钢渗氮方法本发明形成均匀渗氮层,其中在渗氮前用含氟或氟化物的主体清洗钢工件表面以去除表面上的杂质,氧化层和/或类似物质,同时使表面活化而促使渗氮时N原子渗透和扩散。
钢渗氮方法包括在炉中加热到约300-500℃后向炉中引入含氟或氟化物的气体以将表面氧化层等转化成含氟层,最后进行渗氮处理。
渗氮时含氟层分解并被去除,从而在去除杂质后露出活化表面。
氮原子即可迅速渗透过活化表面并向内扩散而形成均匀渗氮层。
11 CN90108276.7 钢渗氮的方法及所用热处理炉本发明涉及一种对钢件渗氮的方法,钢件在第一热处理炉进行氟化处理后,就在第二热处理炉进行渗氮处理,而得到深而均匀的氮化层。
根据氟化处理和渗氮处理所需要的时间(这两种处理的时间是不同的),确定上述两种处理用的热处理炉的台数配比,以保持钢件渗氮处理连续进行。
12 CN91111528.5 钢铁工件渗氮的快速熏渗方法本发明属金属表面化学热处理技术。
本发明的方法是把某种高氮化合物作为熏渗剂,将工件和熏渗剂同时装入熏渗箱,在加热时熏渗剂升华并包覆工件,其催化分解产生的活性氮原子被工件吸收并形成渗层的方法。
本方法优于常规气体渗氮,时间短、渗剂省、效果好。
一般在500-900℃熏渗10-60分钟可获得化合物层厚度达35-210μm。
本方法可利用常规热处理设备,可用于连续化生产线和真空渗氮,亦可和常规固体、气体渗氮或碳氮共渗等工艺结合使用。
13 CN91106880.5 一种无氮化物层(白亮层)气体渗氮工艺一种无氮化物层(白层)气体渗氮工艺,特别适用经固溶,时效的17-4PH类不锈钢制件,其特征是将制件装罐交向罐内撒放少量卤化铵晶粒后入炉,在下述条件下进行两段处理:$a)350±5℃,35~45h,氨分解率30~40%;$b)550±5℃,6~10h,氨流量维持炉内正压。
$实践证明,按本发明工艺处理相应制件后,可保证获得深0.12~0.25mm的渗氮层,渗层表面硬度HR<sub>N15</sub>≥91,且表面无氮化物层。
14 CN91107932.7 稀土催渗离子渗氮新技术本发明公开了一种添加稀土催渗剂的离子渗氮新技术,适用于金属表面的化学热处理。
催渗剂为含镧和铈的混合稀土。
由于稀土无素具有强烈的化学活性,可与氧、氢、氮作用形成相应的化合物,并能加快氮、氢化合物的分解,因此,在将工件装入离子渗氮炉内的同时,加入混合稀土催渗剂,即可实现稀土催渗离子渗氮。
本发明与常规离子渗氮比较,渗速明显加快,一般可提高25~40%,渗层硬度分布平缓,渗层脆性降低。
同时,本发明工艺方法简单,易于掌握,稀土原料来源广泛,因此,经济效益显著。
15 CN92114647.7 电离渗氮不锈钢板及其制造和使用方法本发明涉及使用电离渗氮技术硬化生产含有氧化铝颗粒的耐磨装饰层压板的压板,同时提高压板使用寿命的方法和装置。
由于参数调整和预期效果之间相互依存关系的确定,上述方法应用于压板,使压板能满足严格的微观表面光洁度要求。
上述相互依存关系包括工件几何形状,表面和表面下的结构和要求的效果,处理温度,压力,加热时间,热负载,反射性辐射和热效应,冷却系统,以及气体混合物组成。
16 CN93119998.0 带有渗氮的硬化表面的织机导纱梳栉筘片一种用于自动纺织机械例如,喷气织机导纱梳节筘片(其表面接触纱线),渗氮形成一个渗氮硬化层,以防止近来自动高速纺织机械上与纱线接触点的磨损等,结果因磨损后引起接触表面粗糙不平,使与其接触的纱线毛。
因此,本发明的织机导纱梳节筘片能完全适应目前自动化高速织造机械。
17 CN94118641.5 不锈钢中形成高强度奥氏体表面层的表面渗氮方法经在1000与1200℃之间温度下渗氮,使接近成品形状的不锈钢零件表面部分富集溶解氮。
借此使表面部分的铁素体及马氏体组织成分转化成奥氏体。
氮通过固溶强化使所形成的表面层强度得以提高,同时,该表面层以奥氏体组织的高韧性为特征。
强度与韧性的结合,导致尤其在冲击磨损、气蚀及空蚀情况下显著提高的耐磨性。
与碳相反,渗氮并不会使表面层的耐腐蚀性能变差,而是有所提高。
该热处理方法适合用来延长料流机械中不锈钢零部件的寿命。
18 CN98110936.5 钢制模具顶杆均匀平直的离子渗氮技术本发明在于通过设置辅助阴极、采取合理的装炉方式和适当的处理温度及热分解氨气压等工艺参数,使模具顶杆渗氮达到均匀而有效硬化的同时,根据顶杆外径膨胀(变形)较小和外表层硬度分布存在较宽的高硬度平台的特点,把渗氮后的顶杆再精磨至规定外径尺寸而表面仍保持技术要求的高硬度,从而解决了此类顶杆大批量渗氮处理中表面硬度不均(或不足)和直线度大量超差的难题,使渗件合格率几乎达到100%。
19 CN97114434.6 稀土在气体渗氮及氮碳共渗工艺中的应用方法本发明提出了气体硬氮化及气体软氮化工艺中应用稀土催渗剂的三种方法,即固体包装法、机械化自动加料法及液体滴注法。
加入稀土催渗剂可将硬氮化纯渗入时间缩短50~100%,软氮化缩短30~50%;表面硬度相对提高HV50~200,耐磨性,抗腐蚀能力,金相组织和脆性均有不同程度改善,可使模具和零件寿命提高1~2倍。
20 CN98108741.8 渗氮钢渗氮钢,尤其适用于制造易磨损的结构件的钢,它具有以下组成(%重量):$C0.10—0.20,Si≤0.50,Mn0.65—1.20,Cr1.50—4.00,Mo0.40—0.70,Al≤0.50,余量为Fe及杂质。
21 CN99124182.7 渗氮废气排放与残余氨回收的装置及其方法本发明渗氮废气排放与残余氨回收的装置,主要由缓冲器第一级吸收器、氨水贮存槽、第二级吸收器和废液中和槽构成,缓冲器通过管道与第一级吸收器相联,第一级吸收器又通过管道与第二级吸收器相联,第一级吸收器的一侧所设的溢流槽与氨水贮存槽相通,第二级吸收器通过管道可由开关控制与外界相通,第二级吸收器底部可由开关控制与废液中和槽相通。