冲压工艺与冲压模设计-ch06
冲压工艺及冲模设计
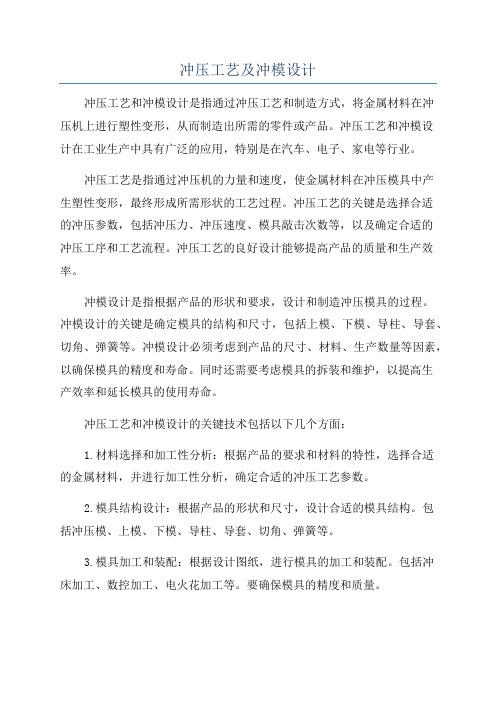
冲压工艺及冲模设计冲压工艺和冲模设计是指通过冲压工艺和制造方式,将金属材料在冲压机上进行塑性变形,从而制造出所需的零件或产品。
冲压工艺和冲模设计在工业生产中具有广泛的应用,特别是在汽车、电子、家电等行业。
冲压工艺是指通过冲压机的力量和速度,使金属材料在冲压模具中产生塑性变形,最终形成所需形状的工艺过程。
冲压工艺的关键是选择合适的冲压参数,包括冲压力、冲压速度、模具敲击次数等,以及确定合适的冲压工序和工艺流程。
冲压工艺的良好设计能够提高产品的质量和生产效率。
冲模设计是指根据产品的形状和要求,设计和制造冲压模具的过程。
冲模设计的关键是确定模具的结构和尺寸,包括上模、下模、导柱、导套、切角、弹簧等。
冲模设计必须考虑到产品的尺寸、材料、生产数量等因素,以确保模具的精度和寿命。
同时还需要考虑模具的拆装和维护,以提高生产效率和延长模具的使用寿命。
冲压工艺和冲模设计的关键技术包括以下几个方面:1.材料选择和加工性分析:根据产品的要求和材料的特性,选择合适的金属材料,并进行加工性分析,确定合适的冲压工艺参数。
2.模具结构设计:根据产品的形状和尺寸,设计合适的模具结构。
包括冲压模、上模、下模、导柱、导套、切角、弹簧等。
3.模具加工和装配:根据设计图纸,进行模具的加工和装配。
包括冲床加工、数控加工、电火花加工等。
要确保模具的精度和质量。
4.冲压工艺参数设计:根据产品的要求和材料的特性,确定合适的冲压工艺参数。
包括冲压力、冲压速度、模具敲击次数等。
5.冲压工艺的优化:通过实验和计算分析,优化冲压工艺,提高产品的质量和生产效率。
包括模具结构的改进、冲压工序的优化等。
冲压工艺和冲模设计的优点包括以下几个方面:1.生产效率高:冲压工艺可以实现高效的批量生产,提高生产效率。
2.产品质量好:冲压工艺可以保证产品的尺寸精度和外观质量,提高产品的质量。
3.材料利用率高:冲压工艺可以实现材料的最大利用,减少材料的浪费。
4.设计灵活性高:冲压工艺和冲模设计可以根据产品的要求,进行灵活的设计和调整,满足不同客户的需求。
冲压工艺与模具设计的内容及步骤

冲压工艺与模具设计的内容及步骤冲压工艺是利用机械设备将金属板材冲压成所需形状的一种生产方法,广泛应用于制造汽车、电器、通信设备等工业产品中。
模具设计是冲压工艺的重要环节,它决定了冲压件的质量和成本。
下面将详细介绍冲压工艺和模具设计的内容及步骤。
一、冲压工艺步骤:1.确定冲压工艺参数:包括材料的选择、厚度、韧性、硬化指数等;成形件的形状、尺寸、公差要求等;冲床的选型和工作速度等。
2.设计冲压模具:根据成形件的形状和尺寸,设计出合适的冲压模具。
冲压模具一般包括上模、下模、冲子、顶针和导向装置等。
冲床是冲压操作的设备,通过上下模具的间隙来进行材料的冲压。
3.制作冲压模具:根据冲压模具设计的要求,进行模具零件的加工和装配。
模具材料通常选择高硬度、高耐磨、高强度的工具钢。
4.进行冲压加工:根据工艺参数和模具设计要求,将金属板材装夹在冲床上,通过冲床的动力系统进行冲压加工,将金属板材冲压成成形件。
5.进行后续加工:对冲压成形的零件进行必要的后续加工,如去毛刺、油污清洗、焊接等。
6.进行检验和质量控制:对成形件进行尺寸、公差、表面质量等方面的检验。
根据质量控制要求,对生产过程进行控制和调整,以保证成形件的质量。
二、模具设计步骤:1.确定产品的设计要求:根据成形件的形状和尺寸要求,确定模具结构、材料和工艺要求。
同时还要考虑到模具制造的成本和生产周期等因素。
2.进行产品结构的分析和仿真:运用CAD和CAM软件进行产品结构的分析和仿真,确定冲压工艺和模具设计的合理性。
通过仿真,可以预测模具在使用过程中可能出现的问题,并进行相应的优化。
3.进行模具结构设计:根据产品的形状和尺寸要求,设计模具的结构,包括上下模板的大小和形状、导向装置的位置和尺寸、冲子的形状和尺寸等。
同时还要合理布置冷却系统和润滑系统,以保证模具的使用寿命和成形件的质量。
4.进行模具零件的设计:将模具结构划分为各个零件,并进行分析和计算,确定各个零件的形状、尺寸和工艺要求,包括上下模板、导向装置、冲子、顶针等。
冲压工艺及模具设计六

第六章冲压工艺规程内容简介:ﻫ掌握冲压工艺过程设计步骤、一般冲压工艺方案的确定以及相应的模具结构设计。
章节内容:6.1 冲压工艺过程设计步骤6.2冲压工艺方案的确定6.3 冲压工艺过程设计实例学习目的与要求:ﻫ1.了解冲压工艺过程设计步骤;2.了解冲压工艺方案的确定方法。
重点内容:冲压工艺方案的确定ﻫﻫ难点内容:ﻫ冲压工艺方案的确定以及相应的模具结构设计。
ﻫ主要参考书:ﻫ[1]王同海.实用冲压设计技术.北京:机械工业出版社,2000[2] 冯炳尧.模具设计与制造简明手册.上海:上海科学技术出版社,2000ﻫﻫ复习思考题:ﻫ6-1简述冲压工艺过程设计的一般流程?6-2 分析图6.1零件的工艺性?6-3 详细分析图6.9汽车空调前端盖的冲压工艺设计过程? ﻫﻫ例题与解答:[1]冲压工艺设计过程应用举例电子教材6.1 冲压工艺过程设计步骤冲压工艺过程是冲压件各加工工序的总和。
加工工序不仅包括冲压所用到的冲压加工基本工序,而且包括基本工序之前的准备工序、基本工序之间的辅助工序和基本工序之后的后续工序。
工艺过程设计的任务就是根据生产条件,对这些工序的先后次序做出合理安排(协调组合),其基本要求是技术上可行、经济上合算,还要考虑操作方便与安全。
冲压工艺过程的优劣,决定了冲压件的质量和成本,所以,冲压工艺过程设计是一项十分重要的工作。
1.分析冲压件零件图产品零件图是制订冲压工艺方案和模具设计的重要依据,制订冲压工艺方案要从产品的零件图入手。
分析零件图包括技术和经济两个方面:⑴冲压加工的经济性分析根据冲压件的生产纲领,分析产品成本,阐明采用冲压生产可以取得的经济效益。
⑵冲压件的工艺性分析冲压件的工艺性是指该零件冲压加工的难易程度。
技术方面,主要分析该零件的形状特点,尺寸大小,精度要求和材料性能等因素是否符合冲压工艺的要求。
如果发现冲压工艺性差,则需要对冲压件产品提出修改意见,经产品设计者同意后方可修改。
2.制定冲压工艺方案⑴在分析了冲压件的工艺性之后,通常在对工序性质、工序数目、工序顺序及组合方式的分析基础上,制定几种不同的冲压工艺方案。
冲压工艺与冲压模设计-ch06

第6章冲压工艺过程设计冲压工艺过程是冲压件各加工工序的总和。
加工工序不仅包括冲压件所用到的冲压加工基本工序,而且包括基本工序之前的准备工序、基本工序之间的辅助工序和基本工序之后的后续工序。
工艺过程设计的任务就是根据生产条件,对这些工序的先后次序做出合理安排(协调组合),其基本要求是技术上可行、经济上合算,还要考虑操作方便与安全。
冲压工艺过程的优劣,决定了冲压件的质量和成本,所以,冲压工艺过程设计是一项十分重要的工作。
6.1 冲压工艺过程设计步骤冲压工艺过程设计涉及的内容很多很广,所以应分步进行,其步骤现已大体形成规律,可依据程序进行。
一般步骤如下。
1. 熟悉原始资料在接到冲压件设计任务之后,首先应熟悉以下原始资料:(1) 产品图及技术条件或实物样品;(2) 原材料的牌号、尺寸规格、冲压性能;(3) 生产纲领或生产批量;(4) 可提供的冲压设备种类、型号、规格、技术参数及使用说明;(5) 可提供的模具制造能力与技术水平;(6) 相关技术标准和资料。
2. 冲压件的工艺性分析按上述原始资料对冲压件的结构形状、尺寸、精度要求、材料性能等进行分析。
判断该冲压件用冲压工艺成形能不能达到规定的技术要求,需要哪几种性质的工序和工步,各道中间工序件/半成品的形状和尺寸由哪道工序完成,然后按前几章分别阐述的冲压工艺性要求逐个分析,裁定该冲压件加工难易程度,裁定是否需要采取特殊工艺措施。
由于生产条件(工艺装备及生产的传统习惯)不同,工艺性的涵义也会有一些差异。
若存在冲压工艺性不好、冲压加工困难,则应在不影响其使用性能的前提下提出修改意见,经与产品设计人员协商同意后对冲压件图样作出适合工艺性的修改。
3. 确定最佳工艺方案通过工艺性分析,结合工艺计算,并经分析比较确定最佳方案,这是冲压工艺过程设计中十分重要的环节。
其内容包括工艺性质、工序数目、工序顺序、工序件/半成品件的形状尺寸以及其他辅助工序的安排,6.2节将专题叙述。
冲压工艺及模具设计

冲压工艺及模具设计冲压工艺及模具设计是现代工业制造中常用的一种技术,它通过将金属板材或者其他形状的金属件置于模具中,然后通过冲压机的动作使得金属材料发生塑性变形以得到所需的形状和尺寸。
冲压工艺及模具设计是一门综合性强的工艺技术,以下将介绍其包括冲压工艺流程、模具设计原则、模具结构设计、模具构件选用等相关内容。
一、冲压工艺流程冲压工艺分为单道冲压和多道冲压两种。
单道冲压是指在一个冲压过程中完成产品的全体造型,多道冲压是指通过多次冲压工艺来完成产品的全体造型。
下面将以多道冲压为例介绍冲压工艺流程。
1.材料准备:选择合适的板材材料,进行剪切、铺料等准备工作。
2.模具设计:根据产品的形状和尺寸要求,设计合适的冲压模具。
3.上料:将材料板厚按照模具规格要求剪切成对应尺寸,然后放置在模具上。
4.开模:通过冲压机的动作,使得模具上的凸模与凹模对压,使材料发生塑性变形。
5.去杂及模具保养:在冲压过程中会产生一些杂质,需要及时清理,并对模具进行保养和维护。
二、模具设计原则模具设计是冲压工艺的核心环节,它直接影响着产品的质量和成本。
在进行模具设计时,需要遵循以下原则:1.合理性原则:模具结构要合理,能够满足产品的形状和尺寸要求,并且易于加工和调整。
2.稳定性原则:模具要具有足够的刚性和稳定性,能够承受冲压机的冲击力和振动。
3.高效原则:模具设计要考虑工作效率,设计出能够实现快速冲压的模具结构。
4.经济原则:模具的设计和制造成本要较低,以降低产品的制造成本。
三、模具结构设计模具的结构设计是模具设计的重要环节,它包括模具的整体结构、分段结构、导向结构等。
下面将介绍常用的模具结构设计方法:1.整体结构设计:将模具设计为一个整体结构,具有较好的刚性和稳定性。
2.分段结构设计:根据产品的形状和尺寸要求,将模具分为多个部分,通过连接件进行连接。
3.导向结构设计:模具需要具有良好的导向性,避免材料在冲压过程中发生歪斜和偏移。
4.其他辅助结构设计:模具还需要考虑各种辅助结构,如剪断边缘结构、定位结构、脱模结构等。
冲压工艺及模具设计方案

冲压工艺及模具设计方案冲压工艺是一种常用的金属成形工艺,适用于大批量生产,具有高效、精确、稳定的特点。
模具是冲压工艺的核心部件,其设计方案直接影响产品的质量和生产效率。
本文将就冲压工艺及模具设计方案进行探讨。
一、冲压工艺分析冲压工艺的核心是模具设计,其主要过程包括:材料选择、冲剪线设计、工序计算、模具设计、模具制造和装配等。
在模具设计过程中,需要考虑产品的尺寸、形状、材料及生产批量等因素。
1.材料选择:根据产品的要求,选择适宜的材料进行冲压。
常见的材料有冷轧钢板、不锈钢板、铝板等。
材料的选择应考虑产品的应用环境、强度、耐磨性等因素。
2.冲剪线设计:冲剪线是产品的外形轮廓线,在模具设计中,需要绘制出产品的冲剪线。
冲剪线的设计应合理,保证产品的精度和质量。
3.工序计算:根据产品的结构和尺寸,进行工序计算。
工序计算主要包括模具开数、冲头设计、压力计算等。
通过合理的工序计算,可以提高生产效率和降低生产成本。
4.模具设计:模具设计是冲压工艺的核心。
在模具设计中,需要考虑产品的形状、尺寸、材料、模具材料、模具开数、冲头设计等因素。
模具设计应以满足产品要求为主要目标,同时考虑制造成本和交货周期。
5.模具制造和装配:根据模具设计方案进行模具制造和装配。
模具的制造应严格按照模具设计要求进行,保证模具的精度和质量。
模具装配时,需要注意各组件之间的配合和调试,确保模具能够正常运行。
在模具设计方案中,需要考虑以下几个方面:1.产品的形状和尺寸:根据产品的形状和尺寸,确定模具的结构和尺寸。
模具的结构应简单、合理,并能够满足产品的要求。
2.模具材料:模具的材料应具有良好的切削性能、硬度和耐磨性。
常见的模具材料有合金工具钢、硬质合金等。
模具的材料选择应根据产品的要求和生产批量来确定。
3.模具开数:模具开数是指一次生产中所需要的模具的数量。
模具开数的选择应根据产品的生产批量和生产效率来确定。
开数过多不利于模具制造和管理,开数过少会降低生产效率。
冲压工艺与冲压模具设计

冲压工艺过程设计与冲压模具设计
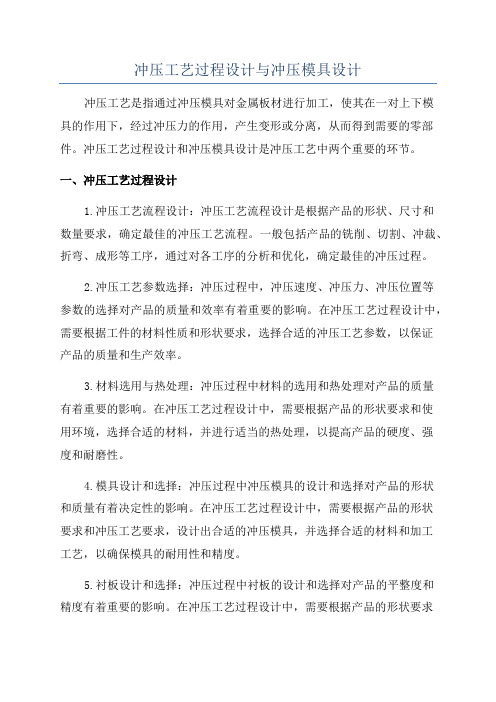
冲压工艺过程设计与冲压模具设计冲压工艺是指通过冲压模具对金属板材进行加工,使其在一对上下模具的作用下,经过冲压力的作用,产生变形或分离,从而得到需要的零部件。
冲压工艺过程设计和冲压模具设计是冲压工艺中两个重要的环节。
一、冲压工艺过程设计1.冲压工艺流程设计:冲压工艺流程设计是根据产品的形状、尺寸和数量要求,确定最佳的冲压工艺流程。
一般包括产品的铣削、切割、冲裁、折弯、成形等工序,通过对各工序的分析和优化,确定最佳的冲压过程。
2.冲压工艺参数选择:冲压过程中,冲压速度、冲压力、冲压位置等参数的选择对产品的质量和效率有着重要的影响。
在冲压工艺过程设计中,需要根据工件的材料性质和形状要求,选择合适的冲压工艺参数,以保证产品的质量和生产效率。
3.材料选用与热处理:冲压过程中材料的选用和热处理对产品的质量有着重要的影响。
在冲压工艺过程设计中,需要根据产品的形状要求和使用环境,选择合适的材料,并进行适当的热处理,以提高产品的硬度、强度和耐磨性。
4.模具设计和选择:冲压过程中冲压模具的设计和选择对产品的形状和质量有着决定性的影响。
在冲压工艺过程设计中,需要根据产品的形状要求和冲压工艺要求,设计出合适的冲压模具,并选择合适的材料和加工工艺,以确保模具的耐用性和精度。
5.衬板设计和选择:冲压过程中衬板的设计和选择对产品的平整度和精度有着重要的影响。
在冲压工艺过程设计中,需要根据产品的形状要求和冲压工艺要求,设计出合适的衬板,并选择合适的材料和工艺,以确保衬板的平整度和精度。
1.冲压模具结构设计:冲压模具的结构设计是根据产品的形状要求和冲压工艺要求,设计出合适的模具结构。
一般包括上模、下模、导柱、导套、导向件等部分,通过对这些部分的设计,实现产品的冲裁、折弯、成形等工艺要求。
2.冲压模具材料选择:冲压模具的材料选择对模具的寿命和精度有着重要的影响。
在冲压模具设计中,需要根据模具的使用环境和要求,选择合适的材料,并进行适当的热处理,以提高模具的硬度、强度和耐磨性。
冲压工艺与冲压模具设计
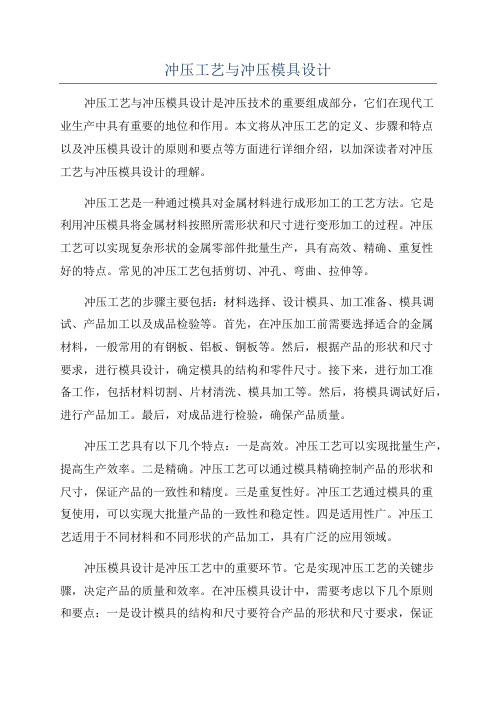
冲压工艺与冲压模具设计冲压工艺与冲压模具设计是冲压技术的重要组成部分,它们在现代工业生产中具有重要的地位和作用。
本文将从冲压工艺的定义、步骤和特点以及冲压模具设计的原则和要点等方面进行详细介绍,以加深读者对冲压工艺与冲压模具设计的理解。
冲压工艺是一种通过模具对金属材料进行成形加工的工艺方法。
它是利用冲压模具将金属材料按照所需形状和尺寸进行变形加工的过程。
冲压工艺可以实现复杂形状的金属零部件批量生产,具有高效、精确、重复性好的特点。
常见的冲压工艺包括剪切、冲孔、弯曲、拉伸等。
冲压工艺的步骤主要包括:材料选择、设计模具、加工准备、模具调试、产品加工以及成品检验等。
首先,在冲压加工前需要选择适合的金属材料,一般常用的有钢板、铝板、铜板等。
然后,根据产品的形状和尺寸要求,进行模具设计,确定模具的结构和零件尺寸。
接下来,进行加工准备工作,包括材料切割、片材清洗、模具加工等。
然后,将模具调试好后,进行产品加工。
最后,对成品进行检验,确保产品质量。
冲压工艺具有以下几个特点:一是高效。
冲压工艺可以实现批量生产,提高生产效率。
二是精确。
冲压工艺可以通过模具精确控制产品的形状和尺寸,保证产品的一致性和精度。
三是重复性好。
冲压工艺通过模具的重复使用,可以实现大批量产品的一致性和稳定性。
四是适用性广。
冲压工艺适用于不同材料和不同形状的产品加工,具有广泛的应用领域。
冲压模具设计是冲压工艺中的重要环节。
它是实现冲压工艺的关键步骤,决定产品的质量和效率。
在冲压模具设计中,需要考虑以下几个原则和要点:一是设计模具的结构和尺寸要符合产品的形状和尺寸要求,保证加工精度和产品质量。
二是选择合适的材料和热处理方式,以提高模具的耐磨性和使用寿命。
三是合理布局模具的零部件和附件,便于加工和调试。
四是考虑模具的易制造性和可维修性,方便模具的加工和维护。
在冲压模具设计中,还需要注意以下几个关键点:一是合理确定冲程和压力,以满足产品的成形要求。
冲压工艺与模具设计

冲压工艺与模具设计冲压工艺是一种通过对金属板材进行压制或冲剪,以改变其形状和尺寸的制造工艺。
在冲压过程中,需要使用模具来对金属板材施加确定的压力,使其发生塑性变形。
模具设计是冲压工艺的关键环节,合理的模具设计可以保证冲压过程的精度和效率。
一、金属材料的选择冲压工艺中常用的金属材料有钢板、铝板、铜板等。
不同金属材料的机械性能和加工性能不同,选择合适的金属材料对冲压工艺的成功至关重要。
二、冲压工艺的确定冲压工艺主要包括件的外形确定、孔位置的布置、切缘的设计等。
通过工艺确定,可以确定冲压工序的顺序、模具的需求以及操作要求。
三、模具设计要点1.模具结构的设计:模具结构设计要满足零件的加工要求,并在生产中方便拆卸、更换。
2.模具材料的选择:模具材料需要具有较高的硬度、强度和耐磨性,常用的模具材料有合金工具钢、硬质合金等。
3.模具配套设备的选择:根据冲压工艺的要求,选择合适的配套设备,如冲压机等。
4.压力分布的设计:模具在冲压过程中需要对板材施加一定的压力,合理的压力分布可以避免产生变形和裂纹。
5.模具的预紧力设计:预紧力是指模具在冲压过程中需承受的力量,需要合理设置预紧力以保证冲压过程的稳定性和精度。
6.附件的设计:模具附件是模具的辅助部件,如导向柱、定位销等,合理的设计可以提高模具的使用寿命和加工效率。
7.考虑模具的便于制造性和可维护性:在模具设计中,需要考虑到模具的制造难度和维护难度,合理的设计可以降低成本和提高效率。
总之,冲压工艺与模具设计是密不可分的,合理的模具设计可以保证冲压过程的精度和效率,最终提高产品的质量和生产效益。
在进行冲压工艺与模具设计时,需要考虑金属材料的选择、工艺的确定以及模具结构、材料等方面的要点。
只有全面考虑这些因素,才能设计出合理、高效的模具,实现优质的冲压加工。
《冲压工艺与模具设计(第4版)》电子教案 模 块 六 其 他 冲 压 成 形 工 艺
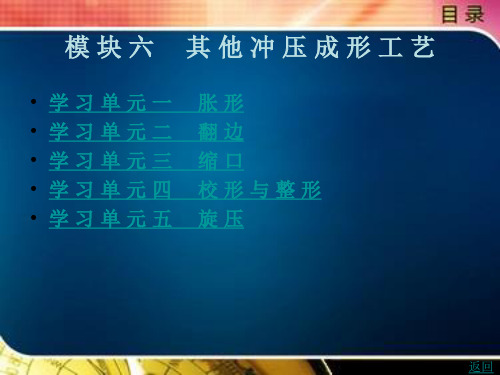
下式估算:
上一 曲 柄 压 力 机 上 对 板 厚 小 于 1.5 mm、 成 形 面 积 小 于 2 00 mm 2 的 小 件 压 加 强 筋 时 , 如 在成 形 后 进 行 校 形 , 所需冲压力F按下式计算:
上一页 下一页 返回
学习单元一 胀形
• 3) 润 滑 情 况 • 胀形时进行良好的润滑,也有使变形趋于均匀化的作
用 , 使 胀 形 深 度 能 够 增 加 。 但 润 滑的 部 位 应 与 拉 深 不 同,在凹模圆角区进行润滑是没有意义的,润滑面应 选 在 凸 模 与 板 料 的 接触 部 分 , 这 是 由 胀 形 的 变 形 特 点 所 决定的。 • 采用平头凸模对塑性较好的低碳钢板、软铝板进行胀 形 所 能 达 到 的 深 度 h 见 表 6-1。 采用 球 头 凸 模 胀 形 能 达 到 的 深 度 h 为 : h≈d/3, d 为 胀 形 件 的 直 径 。 在 平 板 上 压 加 强 筋 时 , 如果 截 面 形 状 为 圆 弧 形 , 可 能 达 到 的 压 筋 深 度 h 为 压 筋 宽 度 b 的 30%左 右 , 即 h≤0.3b。
点 , 应 力 -应 变 状 态 也 相 同 。 但 对 空 心 毛 坯 的 胀 形 , 如 • 图 6-3 所 示 对 一 段 管 子 的 凸 肚 胀 形 , 如 果 管 子 的 长 度
不 是很 长 , 胀 形 时 管 子 的 长 度 就 会 缩 短 。 这 表 明 胀 形 区 以 外 的材 料 向 胀 形 区 内 补 充 , 使 胀 形 区 的 径 向 拉 伸 变 形 得 到 缓 和 ,而 使 切 向 的 拉 伸 变 形 成 为 最 主 要 的 变 形 , 胀 破 就 是 由 于 切向 拉 应 变 过 大 引 起 的 。 • 为 了 不 胀 破 , 需 限 制 切 向 最 大 拉 应 变 ε θmax 不 超 过 材 料 的 许 用 伸 长 率 [ δ]
冲压工艺与模具设计

模具设计原则与要求
模具设计应遵循结构简单、易于 制造和使用维护方便的原则,同 时要考虑到生产批量、生产效率
和经济性等因素。
模具设计应满足冲压件的使用要 求和质量标准,确保冲压件具有 良好的外观、尺寸精度和力学性
能。
模具设计应考虑到制造周期、制 造成本和使用寿命等因素,力求
提高生产效率和降低成本。
模具设计流程及方法
发展阶段
随着工业技术的发展,冲压设备不断 更新换代,模具设计制造技术也不断 提高,冲压工艺逐渐实现自动化和规 模化。
冲压工艺应用领域
汽车制造
汽车车身、底盘、发动 机等部件的制造都离不
开冲压工艺。
家用电器
冰箱、洗衣机、空调等 家用电器中的金属部件 大多采用冲压工艺制造
。
电子行业
电子元器件、电路板等 产品的制造也广泛应用
冲压工艺与模具设计
汇报人: 日期:
目录
• 冲压工艺概述 • 冲压模具设计基础 • 冲压模具设计原理 • 冲压模具结构优化设计 • 冲压模具材料选择与制造工艺
优化 • 冲压模具设计发展趋势与挑战
01
冲压工艺概述
冲压工艺定义与特点
定义
冲压工艺是一种金属加工方法, 通过模具和冲压设备对金属材料 施加压力,使其发生变形,从而 获得所需形状和尺寸的零件。
材料准备
选择合适的材料,进行切割、打磨等预处理。
粗加工
根据图纸进行粗加工,形成大致形状和尺寸。
热处理
进行淬火、回火等热处理,提高材料硬度和韧性。
精加工
进行精磨、抛光等处理,达到要求的精度和表面 质量。
组装调试
将各部件组装在一起,进行调试和试模,确保模具正常 工作并达到预期效果。
冲压工艺与模具设计

冲压工艺与模具设计
一、冲压工艺
冲压工艺是一种通过利用模具来对金属板材进行冷热压制成型的工艺。
冲压工艺具有高效、高精度、高一致性、低成本等特点,被广泛应用于汽
车制造、航空航天、电子电器等领域。
冲压工艺的步骤包括材料准备、模具设计、冲孔冲裁、弯曲、折边、
拉伸等。
冲压工艺的关键是模具设计,良好的模具设计能够提高冲压效率
和产品质量。
二、模具设计
模具是冲压工艺中不可或缺的一环,其设计需要考虑材料性能、产品
形状、工艺要求等多个因素。
1.材料性能
模具设计首先需要考虑冲压材料的性能,如材料的硬度、可塑性等。
不同材料对模具的磨损程度不同,需要根据具体情况选择合适的材料和表
面处理方式。
2.产品形状
根据产品的形状和尺寸要求,设计合适的模具结构。
模具的结构分为
上模和下模,同时还需要考虑产品的分模方式、冲切方式等。
3.工艺要求
在模具设计中还需要考虑产品的工艺要求,如冲孔孔径、孔距、冲压
力度等。
良好的模具设计能够确保产品的质量和生产效率。
在设计模具时还需要考虑模具的使用寿命和维修性,良好的模具设计能够减少模具的磨损和尺寸误差,提高模具的使用寿命。
冲压工艺和模具设计的发展趋势是向着高效、高精度、高一致性和自动化方向发展。
随着科技的进步,模具设计越来越注重材料技术、加工技术和模具制造技术的综合应用,通过不断提高模具的精度和耐用性,实现产品质量的提高和生产效率的提升。
总之,冲压工艺和模具设计在工业生产中起着重要的作用,合理的设计和应用能够提高产品质量和生产效率,推动工业制造向高效、高精度和自动化方向发展。
冲压工艺及模具设计

冲压工艺及模具设计冲压工艺及模具设计是一种应用广泛的金属加工方法,它通过将金属材料置于模具中,施加外力使其产生塑性变形来实现加工目的。
冲压工艺及模具设计在日常生活中被广泛应用于汽车制造、家电制造、建筑结构等领域。
本文将详细介绍冲压工艺及模具设计的基本原理、流程以及注意事项。
一、冲压工艺的基本原理冲压工艺是利用模具的上下凸模与下模的活套孔进行压力传递,从而给金属材料施加一定的压力,使其发生塑性变形,最终获得所需形状的零件。
冲压工艺的基本原理包括:所需零部件的模具设计、材料的选用、设备的调整和操作、冲压力的控制等。
二、冲压工艺的流程1.设计模具:根据所需加工的零件形状和尺寸,设计相应的冲压模具。
模具的设计考虑要点包括:模具结构、零件加工顺序、模具寿命等。
2.材料选用:根据所需加工的零件的要求,选择合适的金属材料。
常用的金属材料有冷轧钢板、不锈钢板、铝合金板等。
3.材料切割:将金属材料按照所需零件的形状和尺寸切割成相应的板料。
4.模具调整:将上下模具安装在冲床上,并进行调整,使得上下模具对齐、平衡。
5.进料:将切割好的板料放置在模具上,通过上模的压力传递给下模,使金属材料发生塑性变形。
6.成型:通过上下模具的周期性运动,使金属材料依次进行冲击、拉伸、弯曲等工艺,最终获得所需形状的零件。
7.完成零件:将成型好的零件从模具中取出,并进行后续处理,如清洗、打磨、表面处理等。
三、冲压工艺及模具设计的注意事项1.模具的设计:模具的设计应符合所需零件的形状和尺寸要求,且要考虑模具的寿命和成本问题。
模具设计时,需注意加工顺序的合理性,以提高生产效率。
2.材料的选用:选择合适的金属材料是冲压工艺的关键,需考虑零件的材质要求、成本和加工性能等因素。
3.设备的调整和操作:正确调整冲床的压力、速度和行程等参数,保证冲压工艺的稳定进行。
操作时,需注意安全,确保操作人员的人身安全。
4.增加冲压辅助工艺:根据所需零件的形状和要求,可以增加冲压辅助工艺,如冲孔、拉伸、弯曲、压花等,以提高零件的加工质量和寿命。
冲压工艺及模具设计(3篇)

第1篇一、引言冲压工艺是一种常见的金属成形工艺,广泛应用于汽车、家电、电子、航空等行业。
冲压工艺具有生产效率高、成本低、精度高、尺寸稳定性好等优点。
模具是冲压工艺中的关键设备,其设计质量直接影响到冲压产品的质量和生产效率。
本文将对冲压工艺及模具设计进行简要介绍。
二、冲压工艺概述1. 冲压工艺原理冲压工艺是利用模具对金属板材施加压力,使其产生塑性变形,从而获得所需形状、尺寸和性能的零件。
冲压工艺的基本原理是金属的塑性变形,即金属在受到外力作用时,产生塑性变形而不破坏其连续性的过程。
2. 冲压工艺分类(1)拉深:将平板金属沿模具凹模形状变形,形成空心或实心零件的过程。
(2)成形:将平板金属沿模具凸模形状变形,形成具有一定形状的零件的过程。
(3)剪切:将平板金属沿剪切线剪切成一定形状和尺寸的零件的过程。
(4)弯曲:将平板金属沿模具凸模形状弯曲,形成具有一定角度的零件的过程。
三、模具设计概述1. 模具设计原则(1)满足产品精度和尺寸要求:模具设计应保证冲压产品具有高精度和尺寸稳定性。
(2)提高生产效率:模具设计应优化工艺流程,减少不必要的加工步骤,提高生产效率。
(3)降低生产成本:模具设计应选用合适的材料,降低模具成本。
(4)确保模具寿命:模具设计应考虑模具的耐磨性、耐腐蚀性等性能,延长模具使用寿命。
2. 模具设计步骤(1)产品分析:分析产品的形状、尺寸、材料等,确定模具设计的基本要求。
(2)工艺分析:根据产品形状和尺寸,确定冲压工艺类型,如拉深、成形、剪切、弯曲等。
(3)模具结构设计:根据工艺要求,设计模具结构,包括凸模、凹模、导向装置、压边装置等。
(4)模具零件设计:根据模具结构,设计模具零件,如凸模、凹模、导向装置、压边装置等。
(5)模具加工:根据模具零件设计,进行模具加工。
(6)模具调试:完成模具加工后,进行模具调试,确保模具性能符合要求。
四、冲压工艺及模具设计要点1. 冲压工艺要点(1)合理选择材料:根据产品形状、尺寸、性能要求,选择合适的金属材料。
- 1、下载文档前请自行甄别文档内容的完整性,平台不提供额外的编辑、内容补充、找答案等附加服务。
- 2、"仅部分预览"的文档,不可在线预览部分如存在完整性等问题,可反馈申请退款(可完整预览的文档不适用该条件!)。
- 3、如文档侵犯您的权益,请联系客服反馈,我们会尽快为您处理(人工客服工作时间:9:00-18:30)。
第6章冲压工艺过程设计冲压工艺过程是冲压件各加工工序的总和。
加工工序不仅包括冲压件所用到的冲压加工基本工序,而且包括基本工序之前的准备工序、基本工序之间的辅助工序和基本工序之后的后续工序。
工艺过程设计的任务就是根据生产条件,对这些工序的先后次序做出合理安排(协调组合),其基本要求是技术上可行、经济上合算,还要考虑操作方便与安全。
冲压工艺过程的优劣,决定了冲压件的质量和成本,所以,冲压工艺过程设计是一项十分重要的工作。
6.1 冲压工艺过程设计步骤冲压工艺过程设计涉及的内容很多很广,所以应分步进行,其步骤现已大体形成规律,可依据程序进行。
一般步骤如下。
1. 熟悉原始资料在接到冲压件设计任务之后,首先应熟悉以下原始资料:(1) 产品图及技术条件或实物样品;(2) 原材料的牌号、尺寸规格、冲压性能;(3) 生产纲领或生产批量;(4) 可提供的冲压设备种类、型号、规格、技术参数及使用说明;(5) 可提供的模具制造能力与技术水平;(6) 相关技术标准和资料。
2. 冲压件的工艺性分析按上述原始资料对冲压件的结构形状、尺寸、精度要求、材料性能等进行分析。
判断该冲压件用冲压工艺成形能不能达到规定的技术要求,需要哪几种性质的工序和工步,各道中间工序件/半成品的形状和尺寸由哪道工序完成,然后按前几章分别阐述的冲压工艺性要求逐个分析,裁定该冲压件加工难易程度,裁定是否需要采取特殊工艺措施。
由于生产条件(工艺装备及生产的传统习惯)不同,工艺性的涵义也会有一些差异。
若存在冲压工艺性不好、冲压加工困难,则应在不影响其使用性能的前提下提出修改意见,经与产品设计人员协商同意后对冲压件图样作出适合工艺性的修改。
3. 确定最佳工艺方案通过工艺性分析,结合工艺计算,并经分析比较确定最佳方案,这是冲压工艺过程设计中十分重要的环节。
其内容包括工艺性质、工序数目、工序顺序、工序件/半成品件的形状尺寸以及其他辅助工序的安排,6.2节将专题叙述。
4. 完成工艺计算工艺方案确定后,对各道冲压工序进行工艺计算,其内容主要包括:(1) 排样及计算材料消耗定额;(2) 计算冲压所需的力、所消耗的功;(3) 计算凸、凹模工作部分尺寸。
5. 选择模具类型及结构形式根据确定的工艺方案和冲压件形状特点、精度要求、生产批量、模具加工条件、操作方便与安全等要求,选定冲模类型及结构形式。
一般而言,用复合模冲出的制件精度高于级进模,而级进模又高于单工序模。
这是因为用单工序模冲压多工序的冲压件时,要经过多次定位和变形,产生积累误差大,冲压件精度较低。
复合模是在同一位置一次冲出,不存在定位误差。
因此,厚料、低精度、小批量、大尺寸的冲压件宜单工序生产,用简单模;薄料、小尺寸、大批量的产品宜用级进模连续生产;而形位精度高的产品,可用复合模加工相关尺寸。
详细内容见第7章。
6. 选择冲压设备根据工艺计算结果和模具空间尺寸的估算值,结合可提供的冲压设备情况,合理确定设备类型和标称压力。
7. 编写工艺过程卡冲压工艺过程设计的归宿是编制出冲压工艺过程卡,它是针对具体冲压产品,对其生产方式、方法、数量、质量等作出的全部决定和记载,其内容主要包括工序名称、工序内容、工序说明(工序件/半成品形状和尺寸)、模具类型、选用设备、检验要求等(参见表6.1、表6.2)。
应该说明的是,上述各项内容难免互相联系、互相制约,因而各设计步骤应前后兼顾和呼应,有时要互相穿插进行。
6.2 冲压工艺方案的确定在分析冲压件加工工艺性的基础上,提出各种可能的冲压工艺方案,经过综合分析、比较,最后确定适合生产条件的最佳方案,其内容主要包括工序性质、工序数目、工序顺序以及其他辅助工艺(热处理等)的安排。
6.2.1 工序性质的确定工序性质是由冲压件的结构形状、尺寸精度、弱区的变形性质所决定。
一般冲压件的加工过程由表 1.1、表 1.2中所列的各基本工序中的一个或几个组成,即可完成冲压成形。
简单冲压件的形状能很直观地反映出冲压加工的工序性质类别,如图 6.1所示弯曲件,需经落料、弯曲、冲孔等工序完成。
但有些冲压件工序性质类别并不能直观地反映出来,其弱区和强区是相对的,必须通过计算和比较才能确定,如图 1.13所示“环形坯料的变形趋向”,改变坯料各部分的相对尺寸、改变模具工作部分的几何形状和尺寸,甚至改变坯料和模具之间的摩擦阻力,都会使坯料某部分由弱区转化为强区,或由强区转化为弱区,从而改变冲压工序的性质。
为了使每道工序都能顺利完成任务,必须使该道工序中应该变形的部分处于弱区,并保证需要变形的先变形,不需要变形的部分不变形,为此,应采取措施对冲压变形加以控制(详见1.4.4节)。
为了改善弱区的变形条件,有时要增加一些附加工序。
如图6.2所示的轴承盖零件,其拉深系数为0.43,已超过极限拉深系数,不能一次拉深成形,该件的一种工艺方案为落料——第1次拉深——第2次拉深——冲23mm孔,但若在落料同时,在坯料中心预冲11mm孔,则在拉深时凸缘仍然是弱区,但底部也可以产生一定的变形量,拉深时11mm孔扩大,底部的部分材料转向侧壁,从而使成形高度得到增加,而坯料直径则可适当减小,因此可一次拉深成形,此时该件的工艺方案变为冲孔(11)落料复合——拉深——冲孔(23)。
显然,后一方案更好。
此外,冲裁件如果平面度要求较高,应增加校平工序;弯曲件弯曲半径太小时,应增加整形工序,使之达到要求;各类空心件若采用拉深工序,拉深件圆角半径太小时,也要增加整形工序。
图6.1 弯曲件图6.2 轴承盖零件图6.2.2 工序数目的确定冲压件基本工序确定后,工序数目主要根据材料的极限变形参数(如拉深系数、翻边系数、缩口系数、胀形系数等)来确定,此外,下列因素也对工序数目的确定产生影响。
1. 冲压件的形状、尺寸要求的影响对于复杂的冲裁件,由于受模具结构或强度限制,常常将其内外轮廓分成几个部分,用几道冲压工序或在级进模中分几个工步进行冲裁。
非常靠近的孔,不能同时冲出,也要分步冲裁。
弯曲件的工序数目决定于弯角的多少、相对位置和弯曲方向。
2. 工序合并情况的影响对于多工序的冲压件,应尽可能把冲压基本工序合并起来,采用复合工序或级进工序,以提高生产效率。
料薄、尺寸小的冲压件,宜通过工序合并,用级进工序进行冲压;形位精度高的冲压件,宜通过工序合并,用复合工序加工相关尺寸,反之宜采用单工序分散冲压。
工序合并与否,还需考虑冲压设备能力、模具制造能力、模具造价及使用的可靠性。
3. 冲压件的尺寸精度及形位公差要求如图6.3所示的某锁圈,因为内孔 00.122 是配合尺寸,有精度要求,所以其工艺方案为落料——成形——冲孔。
如果其内孔22没有精度要求,则其工艺方案可以是落料冲孔复合——成形。
这样工序少、效率高。
图6.3 有精度要求的锁圈弯曲件弯曲角度公差要求较高时,需增加校正弯曲;有凸缘拉深件底部和凸缘有平面度要求时,要增加整形工序。
拉深件的口部、翻边件的边缘等都难以直接做到规则而平齐,因而一般情况下,拉深件、翻边件等最后都有一道修边工序。
若对周边口部没有较高要求时,修边工序可省略。
4. 坯料类型的影响如图5.24所示,该制件如用板料加工,从落料到最后冲孔共需6道工序,改为用管料则只需切断、缩口、第2次缩口共3道工序。
当然,这种替代只有对细长的管类制件才有效。
5. 操作安全与方便方面的要求工人操作是否安全、方便也是在确定工艺方案时要考虑的一个十分重要的问题。
例如,对于一些形状复杂、需要进行多道工序冲压的小型件,如果用单工序模分步冲压,需用手钳放置或取出坯料/工序件/制件,多次进出危险区域,很不安全。
还可能出现定位困难。
为此,有时即使批量不大,也采用比较安全的级进模进行冲压。
图 6.4和图6.5所示即为一实例。
图6.4 形状复杂的小冲压件图6.5 形状复杂的小冲压件在级进模上连续冲压的排样1—冲废Ⅰ;2—冲废Ⅱ;3—切边、冲工艺孔;4—压包;5—压弯Ⅰ;6—压弯Ⅱ;7—切断图6.6所示制件,第1道工序拉深出的 00.460 是以后冲侧孔和翻边两道工序的定位尺寸,为了防止工序件转动,还需增加周向定位,所以,冲裁两个 5.5工艺孔。
图6.6 增加定位工艺孔的制件又如图6.7(a)所示冲裁件,3个槽与3个小孔之间有相对位置要求。
图6.7(b)、(c)所示为用单工序模进行冲裁的两种工艺方案。
工艺方案1先冲出带槽的型孔,再以型孔定位冲出3个小孔。
该方案定位较复杂,操作不方便,效率低而且不安全。
工艺方案2先冲大圆孔,再以大圆孔定位冲3个槽和3个小孔,这样定位简单可靠,操作方便安全,效率高。
图6.7 冲裁工艺方案的比较6.2.3 工序顺序的安排各冲压工序的先后顺序,主要根据冲压件的形状、工序性质、材料的变形规律及冲压件的精度和定位要求来安排。
安排的一般原则为:(1) 所有的孔,只要其形状和尺寸不受后续工序的变形影响,都应在平板坯料上冲出。
因为在立体冲压件上冲孔时操作不方便,定位困难,模具结构复杂。
另外,先冲的孔还可以作为后续工序的定位孔。
(2) 对于带孔(缺)的平板冲裁件,如果采用单工序模,一般先落料再冲孔(缺);若选用级进工序,则先冲孔(缺)后落料。
(3) 对于带孔的弯曲件,应参照弯曲件的工艺性分析安排冲孔工序,当孔径与变形区或孔与基准面有较高要求时,应先弯曲后冲孔。
除此之外,一般情况下都应先冲孔后压弯。
(4) 对于带孔(缺)的拉深件,一般先拉深后冲孔(缺)。
对于带底孔的拉深件,当孔径要求不高时,可先冲孔后拉深。
即使孔径要求较高(如图 6.3所示),为使确定的工序顺序有利于发挥材料的塑性,以减少工序数量,也可采取先冲孔后拉深,最后修边达到要求。
(5) 对于多角弯曲件,应从材料变形区的相互影响和弯曲时坯料偏移走向两方面安排先后弯曲的顺序。
一般先弯外角后弯内角。
(6) 对于复杂旋转体拉深件,一般按由大到小顺序进行拉深(先拉出大尺寸的外形,后拉深小尺寸的圆筒)。
对于非旋转体复杂形状的拉深件,为便于材料的变形流动,应先成形内部形状再拉深外部形状。
(7) 附加的整形工序、校平工序,应安排在基本成形之后。
热处理及酸洗工序,一般安排在多次拉深工序中间或压弯工序之前。
6.2.4 工序件/半成品形状与尺寸工序件/半成品是坯料和成品制件之间的过渡件。
每个工序件/半成品都可分为两个组成部分:已成形部分——形状和尺寸与成品制件相同;待成形部分——形状和尺寸与成品制件不同(是过渡性的)。
这些过渡性的尺寸和形状,虽然在冲压加工完成后会完全消失,但对每道工序的成形及整个冲压件的质量却有重要的影响。
因此,工序件/半成品形状尺寸的确定是冲压工艺方案确定的重点内容之一。
图6.8所示为气阀罩的冲压工艺过程。
第2次拉深工序之后,形成了直径为16.5的圆筒形部分,这部分形状和尺寸在以后的加工过程中不再发生变化。