残余应力对表面质量的影响
习题三:机械加工表面质量

机械加工表面质量一、填空:1.表面质量的含义有两方面的内容,一是表面的几何特征,包括、表面波度、纹理方向;二是表面层的物理力学性能,主要表现在表面层、、。
2.机械加工表面质量将影响零件的耐磨性、耐蚀性、________强度和______质量。
3.表面层的残余应力对疲劳强度有影响,表面层内为残余应力可提高疲劳强度,表面层内为残余应力可降低疲劳强度。
4.工件表面粗糙度越小,在交变载荷的作用下,工件的疲劳强度就____________。
5.切削加工的表面粗糙度主要取决于_______ ,并与切削表面及积屑瘤、鳞刺的产生、切削液等有关。
6.磨削加工时,提高砂轮速度可使加工表面粗糙度数值_______,提高工件速度可使加工表面粗糙度数值_______,增大砂轮粒度号,可使加工表面粗糙度数值______。
7.精加工时,主要考虑加工质量,常利用较小的_____________和进给量,较高的_____________。
8.切削速度提高,冷硬层深度和硬度。
9.残余应力是金属内部的相邻组织发生了的体积变化而产生。
加工过程由表面层若以冷塑性变形为主,则表面层产生残余___ 应力;若以热塑性变形为主,则表面层产生残余_____应力。
10.表面强化工艺有:、、。
11.为了提高零件的使用可靠性,使表面产生残余压应力,有时采用滚压、喷丸等表面工艺。
12.对工件表面进行喷丸强化能使表面层产生冷作硬化和残余____应力。
二、单项选择:1.为减小零件加工表面硬化层深度和硬度,应使切削速度()A、减小B、中速C、增大D、保持不变2.磨削时磨削热传给较多的是()A、工件B、砂轮C、切屑D、空气3.当工件表面层温度超过相变温度,如果这时无冷却液,则造成。
A、淬火烧伤B、退火烧伤C、回火烧伤4.磨削淬火钢时,在重磨削条件下,如果使用冷却液,则可能造成的烧伤是。
A、淬火烧伤B、退火烧伤C、回火烧伤5.为减小切削残留面积高度,应。
A、减小主副偏角、减小进给量,增大刀尖圆孤半径。
影响机械加工表面质量的因素
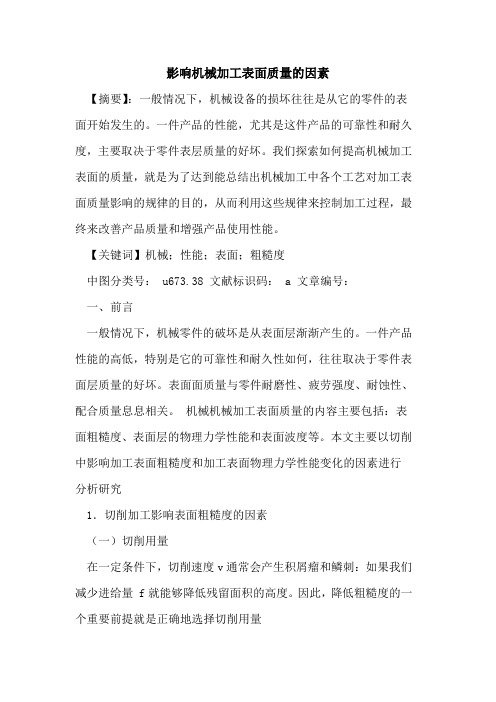
影响机械加工表面质量的因素【摘要】:一般情况下,机械设备的损坏往往是从它的零件的表面开始发生的。
一件产品的性能,尤其是这件产品的可靠性和耐久度,主要取决于零件表层质量的好坏。
我们探索如何提高机械加工表面的质量,就是为了达到能总结出机械加工中各个工艺对加工表面质量影响的规律的目的,从而利用这些规律来控制加工过程,最终来改善产品质量和增强产品使用性能。
【关键词】机械;性能;表面;粗糙度中图分类号: u673.38 文献标识码: a 文章编号:一、前言一般情况下,机械零件的破坏是从表面层渐渐产生的。
一件产品性能的高低,特别是它的可靠性和耐久性如何,往往取决于零件表面层质量的好坏。
表面面质量与零件耐磨性、疲劳强度、耐蚀性、配合质量息息相关。
机械机械加工表面质量的内容主要包括:表面粗糙度、表面层的物理力学性能和表面波度等。
本文主要以切削中影响加工表面粗糙度和加工表面物理力学性能变化的因素进行分析研究1.切削加工影响表面粗糙度的因素(一)切削用量在一定条件下,切削速度v通常会产生积屑瘤和鳞刺:如果我们减少进给量 f就能够降低残留面积的高度。
因此,降低粗糙度的一个重要前提就是正确地选择切削用量(二)刀具材料和几何参数无数的实践证明,如果切削条件相同,我们用高速钢刀具加工的表面粗糙度比用硬质合金刀具加工的表面粗糙度要高,使用金钢石车刀加工的话也很难形成积屑瘤,所以在这种情况下我们能够获得粗糙度比较低的机械加工表面。
刀类圆弧半径rs、主偏角k 和副偏角k 都会影响到残留面积的大小。
因此我们要想降低表面粗糙度的话就可以选择适当减少r8、k 和k 。
前角 l增大可抑制积屑瘤和鳞刺的生长帮有利于降低表面粗糙度。
(三)切削液切削液在机械加工过程能够冷却和润滑机械,其作用不言而喻。
为了使切削过程不易塑性变形,我们应当使切削区的温度不断降低,使刀刃与工件的摩擦不断减少。
2.影响切削加工表面层物理力学性能的因素在机械切削加工的过程中,工件很容易受到切削力和切削热的影响,从而导致机械表面层的金属在物理机械性能方面发生很多变化,而其中最主要的变化就是表面层金属显微硬度的变化、金相组织的变化和残余应力的产生(一)表面层冷作硬化a.加工表面冷作硬化因为切削力的影响,在机械加工的过程中,很容易出现机械塑性变形的情况,从而使得晶格扭曲,还有畸变。
金属加工表面质量的影响因素及改进措施

金属加工表面质量的影响因素及改进措施摘要:加工表面质量是加工后零件的粗糙度。
经处理金属的物理、化学和其他性质可直接由零件粗糙度决定。
因此,必须分析影响金属加工表面质量的因素,以便找到提高产品性能的方法。
本文分析了影响金属加工表面的因素,并提出了一些改进建议,以供参考。
关键词:金属加工表面质量;影响因素;改进措施前言在实际金属加工过程中,金属加工的表面质量要求因产品而异,产品越复杂,金属加工的表面质量要求越高。
在这种情况下,应根据实际需要选择不同的金属加工工具和不同的金属加工方法,并应根据影响金属加工表面质量的实际因素采取适当的改进措施,以提高金属加工表面的质量。
金属表面质量可以说是其功能和使用时间的基础。
只有不断改善影响因素,才能更好地促进金属工业发展。
1金属加工表面质量影响因素许多因素影响金属加工表面的质量。
本质上有三种主要类型:(1)切削强度和切削热。
加工是加工金属零件的极其重要和常见的过程。
零件经常会因切割过程中的拖曳约束而发生一系列变更,包括金相的排列方式以及表面层的硬度和完整性。
例如,平板硬化是指原始金属强度的增加、表面物理特性的变化、塑性的降低以及加工过程中硬度的增加。
但是,当切割过程产生的切割热量达到一定的水平时,金属零件表面的强度和硬度会降低。
(2)系统误差与工艺选择不符。
系统误差(也称为原始误差)是指流程调整中的原始误差和基本原理中的原始误差。
拟合误差是加工过程中由于加工设备、切割边和金属原材料不适当而引起的误差。
可以根据工作经验和产前检查减少这一误差。
例如,切割金属时,在金属表面留下的痕迹通常是刀具的原始形状。
如果未正确使用刀具,则金属的塑性变形会异常,摩擦产生的裂缝会增加,表面的粗糙度也会提高。
理论误差是由轮廓刀具或类似运动引起的间隙。
这主要是由于先进的金属加工技术、工艺和设备造成的。
(3)热塑性应变和残余应力。
在切削强度的作用下,金属零件表面的塑性变形会导致金属层的内外分层,而由于切削热而导致的内部和外部金属层比率的差异是产生残余应力的主要原因。
3.1表面质量概述及表面粗糙度的影响因素

谢谢大家!
②表面层金属的残余应力的影响
拉伸残余应力将使耐疲劳强度下降;压缩残余应力则使耐疲劳强度提高。
3. 表面质量对耐蚀性的影响 (1)表面粗糙度的影响 表面粗糙度值越大,加工表面与气体、液体接触的面积越大,腐蚀物 质越容易沉积于凹坑中,耐蚀性能就越差。 (2)表面层金属力学物理性质的影响 零件表面层有残余压应力时,能够阻止表面裂纹的进一步扩大,有利 于提高零件表面抵抗腐蚀的能力。 4. 表面质量对零件配合质量的影响 (1) 对于间隙配合表面 原有间隙将因急剧的初期磨损而改变,表面粗糙度越大,变化量就 越大,从而影响配合的稳定性。 (2) 对于过盈配合表面 表面粗糙度越大,两表面相配合时表面凸峰易被挤掉,这会使过盈量 减少,影响配合的可靠性。
(4)表面缺陷 加工表面上出现的缺陷,如砂眼、气孔、裂痕等。
2.表面层金属的力学物理性能和化学性能 由于机械加工中力因素和热因素的综合作用,加工表面层金属的力 学物理性能和化学性能将发生一定的变化,主要反映在以下几方面: (1)表面层金属的冷作硬化
机械加工过程中,工件表面层金属都会有一定程度的冷作硬化,使 表面层金属的显微硬度有所提高。
3.2 影响加工表面粗糙度的工艺因素及其改进措施
3.2.1 切削加工表面粗糙度 其值主要取决于切削残留面积的高度。影响切削残留面积高度的因素 主要有:刀尖圆弧半径r、主偏角kr、副偏角kr’及进给量f等。 车削、刨削时残留面积高 度的计算示意图如图3。其中图 a 是用尖刀切削的情况,切削 残留面积的高度为:
3.2.2 磨削加工后的表面粗糙度 1.几何因素的影响 单纯从几何因素考虑,可以认为:在单位面积上刻痕越多,即通过单位 面积的磨粒数越多,刻痕的等高性越好,则磨削表面的粗糙度值越小。 (1)磨削用量对表面粗糙度值的影响 砂轮的速度越高、工件速度越低、砂轮的纵向进给减小,工件表面的 每个部位被砂轮重复磨削的次数增加,被磨表面的粗糙度值将减小。
几何缺陷和残余应力

几何缺陷和残余应力全文共四篇示例,供读者参考第一篇示例:随着科技的进步和工业的发展,几何缺陷和残余应力已经成为工程设计和制造过程中需要重点关注的问题之一。
几何缺陷和残余应力对材料的性能和可靠性有着重要影响,因此需要认真分析和有效控制。
让我们先来了解一下什么是几何缺陷和残余应力。
几何缺陷是指材料或产品在制造过程中出现的形状、尺寸、表面质量不合格的问题。
几何缺陷可能是由于材料的选择、工艺参数的控制不当或者生产设备的失效等原因造成的。
几何缺陷会导致产品的性能下降,甚至在使用过程中出现故障,对产品的可靠性和安全性造成威胁。
而残余应力是指在材料制造或加工过程中,由于内部应力不完全释放所产生的残余应力。
残余应力的产生与材料的加工方式、工艺流程、热处理过程密切相关。
残余应力会导致材料的变形、开裂,甚至影响产品的使用寿命。
针对几何缺陷和残余应力,工程技术人员需要采取一系列有效的措施来进行分析和控制。
对于几何缺陷,工程技术人员应该加强对材料选择和工艺参数控制的重要性认识。
合理的材料选择和严格的工艺控制可以有效降低几何缺陷的发生率,提高产品的质量和可靠性。
建立完善的检测和检验制度也是很重要的,及时发现和解决几何缺陷问题。
对于残余应力,工程技术人员需要深入研究材料的物理性能和结构特点,合理调整材料加工工艺,降低残余应力的产生。
采用适当的热处理和应力释放技术也可以有效地降低残余应力的大小,提高材料的可靠性和稳定性。
在实际工程设计和制造中,我们应该密切关注几何缺陷和残余应力的问题,制定相应的分析和控制方案,确保产品的质量和性能符合要求。
只有不断改进和提高我们的技术水平,才能在激烈的市场竞争中立于不败之地。
【2000字】第二篇示例:几何缺陷和残余应力是固体材料中常见的两种问题,它们会对材料的性能和使用寿命产生影响。
几何缺陷指的是材料中存在的形状不规则或者尺寸不符合要求的问题,而残余应力则是由于材料加工或者热处理过程中所产生的内部应力。
残余应力 表面张力-概述说明以及解释

残余应力表面张力-概述说明以及解释1.引言1.1 概述概述:本文将详细探讨残余应力和表面张力这两个与材料性质和力学行为相关的重要概念。
残余应力是指在材料内部存在的一种应力状态,表征了物体负荷之后在去除载荷后剩余的应力。
而表面张力是液体表面处存在的一种特殊力,使得液体表面呈现出收缩的趋势,使液体分子聚集在一起形成液体的表面膜。
在本文中,我们将首先对残余应力进行详细的介绍。
残余应力可能源自材料制备过程中的热应力、冷却应力、加工应力等,它们会对材料的性能和稳定性产生重要影响。
我们将着重讨论残余应力的产生机制和对材料性能的影响,同时还会介绍一些常见的残余应力检测方法。
其次,我们将探讨表面张力的概念和作用。
表面张力是液体分子间相互作用力的结果,是造成液体表面紧缩的力。
我们将详细讨论表面张力的产生原理、表征方法以及在液体行为中的重要作用,如液体的凝聚现象、液体的形状和液滴的稳定性等。
最后,我们将探讨残余应力与表面张力之间的关系。
尽管它们是两个不同的概念,但从分子层面来看,它们都涉及到材料内部或表面分子间相互作用力的存在。
我们将探讨如何通过调控残余应力来影响表面张力,并且通过实例分析展示二者之间的关系。
通过对残余应力和表面张力的深入研究,我们可以更好地理解不同材料的行为和性能,从而指导材料的制备和应用。
同时,对于了解材料的疲劳性能、形变行为以及液体的稳定性等方面也具有重要意义。
因此,对于残余应力和表面张力的研究具有重要的理论和实践意义。
通过本文的研究,我们希望能够揭示残余应力和表面张力之间的关系,并为相关领域的研究和应用提供有益的启示。
1.2文章结构文章结构部分的内容可以写成如下形式:1.2 文章结构本篇长文主要分为三个部分:引言、正文和结论。
每个部分都有相应的小节,具体的内容安排如下:引言部分将对本文的主题进行概述,说明残余应力和表面张力的概念以及它们在材料科学中的重要性。
同时,引言部分将介绍本文的目的,即通过对残余应力与表面张力关系的探讨,揭示它们对材料性能的影响,并为相关研究提供启示。
金属加工表面质量的影响因素及改进措施
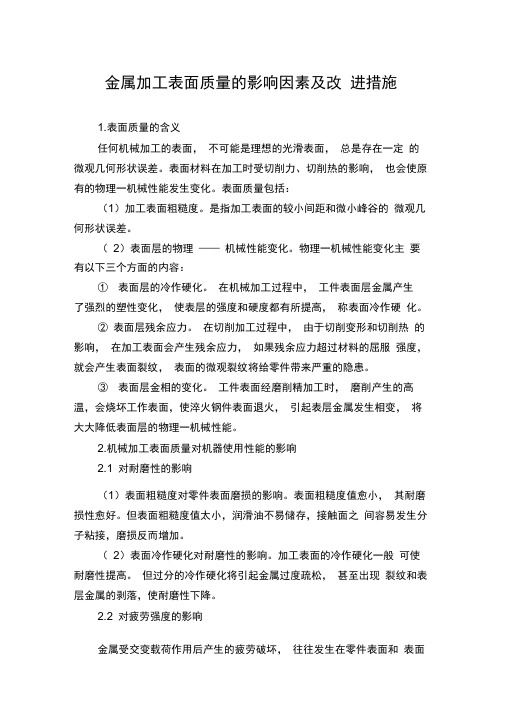
金属加工表面质量的影响因素及改进措施1.表面质量的含义任何机械加工的表面,不可能是理想的光滑表面,总是存在一定的微观几何形状误差。
表面材料在加工时受切削力、切削热的影响,也会使原有的物理一机械性能发生变化。
表面质量包括:(1)加工表面粗糙度。
是指加工表面的较小间距和微小峰谷的微观几何形状误差。
(2)表面层的物理——机械性能变化。
物理一机械性能变化主要有以下三个方面的内容:①表面层的冷作硬化。
在机械加工过程中,工件表面层金属产生了强烈的塑性变化,使表层的强度和硬度都有所提高,称表面冷作硬化。
②表面层残余应力。
在切削加工过程中,由于切削变形和切削热的影响,在加工表面会产生残余应力,如果残余应力超过材料的屈服强度,就会产生表面裂纹,表面的微观裂纹将给零件带来严重的隐患。
③表面层金相的变化。
工件表面经磨削精加工时,磨削产生的高温,会烧坏工作表面,使淬火钢件表面退火,引起表层金属发生相变,将大大降低表面层的物理一机械性能。
2.机械加工表面质量对机器使用性能的影响2.1 对耐磨性的影响(1)表面粗糙度对零件表面磨损的影响。
表面粗糙度值愈小,其耐磨损性愈好。
但表面粗糙度值太小,润滑油不易储存,接触面之间容易发生分子粘接,磨损反而增加。
(2)表面冷作硬化对耐磨性的影响。
加工表面的冷作硬化一般可使耐磨性提高。
但过分的冷作硬化将引起金属过度疏松,甚至出现裂纹和表层金属的剥落,使耐磨性下降。
2.2 对疲劳强度的影响金属受交变载荷作用后产生的疲劳破坏,往往发生在零件表面和表面冷硬层下面,因此零件的表面质量对疲劳强度影响很大。
(1)表面粗糙度对疲劳强度的影响。
在交变载荷作用下,表面粗糙度的凹谷部位容易引起应力集中,产生疲劳裂纹。
表面粗糙度值愈大,表面的纹痕愈深,纹底半径愈小,抗疲劳破坏的能力就愈差。
(2 )残余应力、冷作硬化对疲劳强度的影响。
表面层残余拉应力,将使疲劳裂纹扩大,加速疲劳破坏;而表面层残余压应力,能够阻止疲劳裂纹的扩展,延缓疲劳破坏的产生:表面冷硬化一般伴有残余压应力的产生,可以防止裂纹产生并阻止已有裂纹的扩展,对提高疲劳强度有利。
机械加工质量的影响因素及防治措施

机械加工质量的影响因素及防治措施摘要:在加工过程中,影响工件表面质量的因素很多,导致产品质量不合格,进而影响其使用寿命和性能。
因此,它是进一步提高加工质量水平和工作效率的有效手段,也是加工人员和相关管理人员在加工前必须面对和考虑的问题。
关键词:机械加工质量;影响因素;防治措施1机械加工质量对产品性能的影响加工质量直接影响到产品的实际性能,因此要注意具体的影响程度,采取合理的方法,适当避免干涉程度,以保证加工质量更好,产品性能得到保证。
1.1 耐磨性加工质量是影响零件磨损的决定性因素。
在零件的具体操作过程中,如果加工表面粗糙,势必影响零件的操作效果,也会产生更为严重的后果。
零件的磨损可分为不同的阶段,主要包括两个阶段,即初始磨损阶段和正常磨损阶段。
表面的基本粗糙度是一个不容忽视的重要问题。
它会直接影响零件的使用。
如果表面粗糙度控制得当,损伤越小,使用寿命越长,其他部件的干涉越小。
如果表面粗糙度值太小,润滑油就不易保存,这就增加了部件在运行过程中与其他部件的接触面,相应的磨损程度也就大大提高。
1.2 疲劳强度金属易受多种因素和载荷的影响。
在各种因素和载荷的影响下,金属能够反映变形,同时又呈现冷热交替的状态,加剧了金属本身的疲劳。
零件一旦受到影响,加工阶段的表面粗糙度会显著提高,抗疲劳效果较差。
1.3耐腐蚀性一般来说,零件往往表现出相应的耐腐蚀性因素,而外观的表面质量会严重影响零件的耐腐蚀性。
零件是否会发生严重腐蚀与表面质量的好坏密切相关[3]。
如果零件的实际粗糙度很明显,则表明其耐腐蚀性很低。
如果表面光滑,基本防腐效果极佳。
2 影响机械加工表面质量的因素根据机械加工原理以及实际生产经验,影响机械加工表面质量的因素可以分为以下几个方面:2.1影响表面粗糙度的因素2.1.1材料的性能影响粗糙度机械零件基体材料的性能是决定加工后表面性能的重要因素。
例如,发现合金材料在加工前经过热处理。
这种热处理可以改善合金材料在加工过程中的磨损机理,提高合金材料的耐磨性,获得表面耐磨性好的机械零件。
降低涂层残余应力的方法

降低涂层残余应力的方法
涂层残余应力是一种因为物理性质的原因,在表面涂层的过程中
造成的平面内的不均匀应力。
如果涂层残余应力得不到有效控制,会
对涂层结构的性能产生负面影响,包括涂层外观和表面质量、早期断
裂以及可靠性问题。
因此,涂层残余应力的控制是提高表面涂覆质量、延长产品使用寿命的关键所在。
为了减少或消除涂层残余应力,可以通过改变涂覆工艺、使用低
应力材料、降低温度、采用多层涂层、采用混合涂层等方法来实现。
降低涂层温度是消除涂层残余应力的有效方法之一。
涂层材料的
热膨胀系数不均衡,容易形成残余应力,而涂层和基体材料在高温时,热膨胀比例变大,残余应力增加,因此可通过降低温度来减少涂层残
余应力。
另外,采用多层涂层也是一种有效的减少涂层残余应力的方法。
多层涂层可以有效地减少残余应力,较单层涂层有更优的均衡性。
多
层涂层中可以添加低应力材料,以有效的削弱涂层结构的残余应力。
最后,采用混合涂层也可以消除涂层残余应力。
混合涂层是将多
种涂层材料混合涂布在基体上,使得不同材料之间的应力能相互抵消,从而实现消除残余应力的目的。
总而言之,通过改变涂覆工艺,使用低应力材料,降低温度,采
用多层涂层,采用混合涂层等方式,都可以有效的消除涂层中的残余
应力,提高表面涂覆质量,从而延长产品的使用寿命。
电镀的残余应力-概述说明以及解释
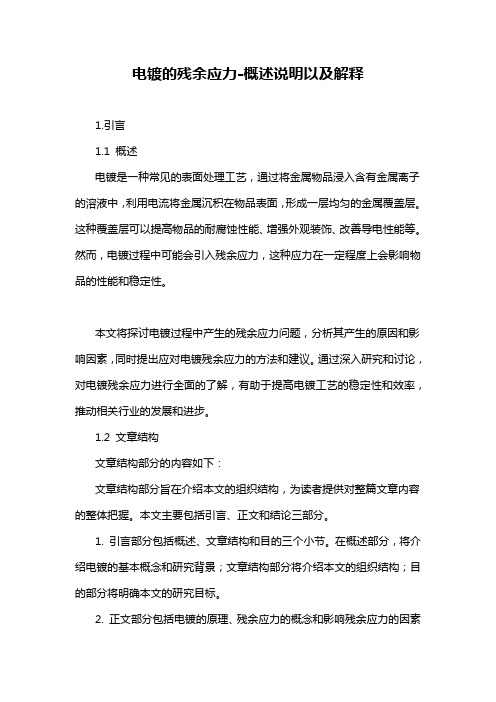
电镀的残余应力-概述说明以及解释1.引言1.1 概述电镀是一种常见的表面处理工艺,通过将金属物品浸入含有金属离子的溶液中,利用电流将金属沉积在物品表面,形成一层均匀的金属覆盖层。
这种覆盖层可以提高物品的耐腐蚀性能、增强外观装饰、改善导电性能等。
然而,电镀过程中可能会引入残余应力,这种应力在一定程度上会影响物品的性能和稳定性。
本文将探讨电镀过程中产生的残余应力问题,分析其产生的原因和影响因素,同时提出应对电镀残余应力的方法和建议。
通过深入研究和讨论,对电镀残余应力进行全面的了解,有助于提高电镀工艺的稳定性和效率,推动相关行业的发展和进步。
1.2 文章结构文章结构部分的内容如下:文章结构部分旨在介绍本文的组织结构,为读者提供对整篇文章内容的整体把握。
本文主要包括引言、正文和结论三部分。
1. 引言部分包括概述、文章结构和目的三个小节。
在概述部分,将介绍电镀的基本概念和研究背景;文章结构部分将介绍本文的组织结构;目的部分将明确本文的研究目标。
2. 正文部分包括电镀的原理、残余应力的概念和影响残余应力的因素三个小节。
将详细介绍电镀的工作原理,残余应力的概念以及影响残余应力的因素。
3. 结论部分包括总结电镀残余应力的重要性、应对电镀残余应力的方法和展望未来研究方向三个小节。
将总结本文的研究成果和对电镀残余应力的重要性进行归纳,提出应对电镀残余应力的方法,并展望未来研究的方向。
通过以上结构的安排,读者可以清晰地了解本文的内容和组织,方便其在阅读过程中更好地理解和把握文章的主要观点和结论。
1.3 目的文章的目的是探讨电镀过程中产生的残余应力对零件性能和质量的影响,以及如何有效应对这种残余应力。
通过深入分析电镀残余应力的形成机制、影响因素和表现形式,可以更好地理解电镀工艺中的问题,并提出相关的解决方法。
此外,通过对电镀残余应力的研究,可以为未来的电镀工艺改进和优化提供参考,推动该领域的发展。
因此,本文旨在从理论和实践的角度探讨电镀残余应力的问题,为相关研究和应用提供有益的参考和指导。
材料表面残余应力

材料表面残余应力
材料表面残余应力是指材料表面的应力状态,它不仅受到外界作用力的影响,还受到材料内部变形和温度变化等因素的影响。
通常情况下,材料的表面会存在着残余应力。
这种残余应力在材料使用过程中,可能会对材料的性能和寿命产生影响。
表面残余应力的产生原因比较多,主要包括材料的制备、加工、焊接等过程中受到的变形、温度变化等因素。
一般来说,材料经过加工或焊接等工艺过程中,会产生一定的塑性变形,从而导致表面残余应力的产生。
此外,材料在高温环境下的热膨胀也会导致表面残余应力的产生。
表面残余应力对材料的影响主要表现在以下几个方面。
首先,它可能会导致材料的疲劳寿命缩短,从而影响材料的使用寿命。
其次,它还可能会导致材料的强度和韧性降低,从而影响材料的性能。
此外,表面残余应力还可能会导致材料产生形变和裂纹等缺陷,从而影响材料的质量。
为了减小材料表面残余应力的影响,可以采取一些措施。
例如,在材料制备、加工和焊接等过程中,可以采用适当的工艺措施,减小塑性变形的程度,从而减小表面残余应力的产生。
此外,还可以采用热处理等方法,对材料进行退火或正火处理,从而消除表面残余应力。
- 1 -。
机械加工表面质量影响因素及改善

2、加工表面层的残余应力
2)表面层残余应力的影响因素 (1)刀具方面 ①刀具几何因素 前角对残余应力有很大影响。图p188 454 ②刀具磨损;图p189 4-55 (2)工件方面 工件材料塑性越大,切削加工后产生的残余拉应力越大。 (3)切削条件方面 切削用量三要素对残余应力影响较大。图p189 4-57 、4-58
高速钢、硬质合金或陶瓷刀具在切削低碳钢、中碳钢等塑
性金属,加工工序中都可能产生鳞刺。会使表面粗糙度加工。 成为塑性金属材料精加工的一个障碍。 在物理因素方面,降低表面粗糙度主要措施,即消除积 屑瘤和鳞刺的措施。
2、切削加工表面粗糙度的产生原因及其控制
4)切削机理的变化:
在挤裂切屑或单元切屑形成的过程中,由于单元切屑 周期性的断裂在切屑表面以下深入,在加工表面上留下挤 裂痕迹而呈现波浪形。在崩碎切屑形成过程中,从主切削 刃处开始的裂纹在接近主应力方向斜着向下延伸,造成加 工表面凹凸不平。p182图4-39 切削刃两侧的工件材料被挤压后因没有侧面的约束力
在精密磨削时不能判断试切时的吃
刀量,很不方便。
(3) 磨削用量的选择
1)提高工件速度和采用小的切深能够有效地减小残余拉应
力和消除烧伤、裂纹等磨削缺陷。
3、 磨削烧伤及磨削裂纹及其控制
2)降低砂轮速度也能得 3)提高砂轮速度的同时相应 提高工件速度,可以避免烧伤。
到残余压应力,但是会影响
生产效率,故一般不常采用。
2、切削加工表面粗糙度的产生原因及其控制
1)理论粗糙度P181:
刀具几何参数中的主偏角、副偏角和刀尖圆弧半径及切削
用量中的进给量是产生理论粗糙度的最基本因素。
Rmax
f cot cot '
影响表面质量的因素

2.采用表面强化工艺改善物理力学性能
滚压加工
滚压加工是利用经过淬硬 和精细研磨过、可自由旋 转的滚压工具(滚轮或滚 珠),在常温下对工件表 面进行挤压,以提高其表 面质量的一种机械强化加 工工艺方法。
喷丸强化
喷丸强化是利用压缩空 气或离心力将大量直径 细小(0.4~4 mm)的 珠丸高速向工件表面喷
切削加工中影响表面粗糙度的几何因素
2.磨削加工中影响表面粗糙度的因素 磨削加工是由砂轮的微刃切削形成的加工表面,单位面积上刻痕越
多且刻痕细密均匀,则表面粗糙度越小。磨削加工中影响表面粗糙度的 因素如下。 1)砂轮的影响
砂轮粒度越细,单位面积上的磨粒数越多,就越能保证加工表面刻 痕细密,使表面粗糙度减小。但砂轮粒度过细,容易堵塞砂轮,使砂轮 失去切削能力,增大摩擦热,使表面粗糙度增大。
切削液的冷却和润滑作用减少了磨削热和摩擦,可减小表面 粗糙度,且能防止磨削烧伤。
1.2 影响表面层金属物理力学性能的因素
1.表面层金属的加工硬化 1)加工硬化的产生及衡量指标
1
2
硬化层深度h。
指标
表面层金属的显微硬度 HV。
3
硬化程度。一般硬化程 度越大,硬化层深度也 越大。
2)影响表面层金属加工硬化的因素 影响表面层金属加工硬化的因素如下:
射的方法。
液体磨料强化
液体磨料强化是利用液体 和磨料的混合物高速喷射 到工件表面,以强化工件 表面,提高工件耐磨性、 抗蚀性和疲劳强度的一种 工艺方法。工件表面在高 速磨料的冲击作用下,表 面粗糙度波峰被磨平,并 产生几十微米厚的塑性变 形层,具有压应力。
机械制造工艺与设备
谢谢观看!
超精研磨
(3)珩磨。珩磨与超精
辊刷对热轧5052铝合金带材表面质量的影响
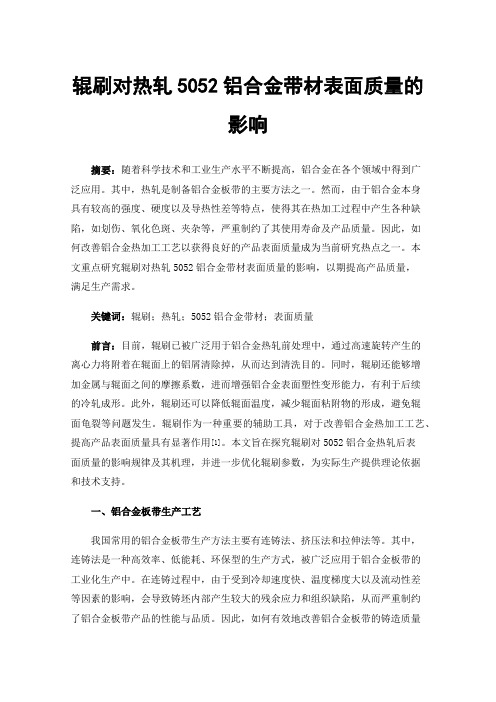
辊刷对热轧5052铝合金带材表面质量的影响摘要:随着科学技术和工业生产水平不断提高,铝合金在各个领域中得到广泛应用。
其中,热轧是制备铝合金板带的主要方法之一。
然而,由于铝合金本身具有较高的强度、硬度以及导热性差等特点,使得其在热加工过程中产生各种缺陷,如划伤、氧化色斑、夹杂等,严重制约了其使用寿命及产品质量。
因此,如何改善铝合金热加工工艺以获得良好的产品表面质量成为当前研究热点之一。
本文重点研究辊刷对热轧5052铝合金带材表面质量的影响,以期提高产品质量,满足生产需求。
关键词:辊刷;热轧;5052铝合金带材;表面质量前言:目前,辊刷已被广泛用于铝合金热轧前处理中,通过高速旋转产生的离心力将附着在辊面上的铝屑清除掉,从而达到清洗目的。
同时,辊刷还能够增加金属与辊面之间的摩擦系数,进而增强铝合金表面塑性变形能力,有利于后续的冷轧成形。
此外,辊刷还可以降低辊面温度,减少辊面粘附物的形成,避免辊面龟裂等问题发生。
辊刷作为一种重要的辅助工具,对于改善铝合金热加工工艺、提高产品表面质量具有显著作用[1]。
本文旨在探究辊刷对5052铝合金热轧后表面质量的影响规律及其机理,并进一步优化辊刷参数,为实际生产提供理论依据和技术支持。
一、铝合金板带生产工艺我国常用的铝合金板带生产方法主要有连铸法、挤压法和拉伸法等。
其中,连铸法是一种高效率、低能耗、环保型的生产方式,被广泛应用于铝合金板带的工业化生产中。
在连铸过程中,由于受到冷却速度快、温度梯度大以及流动性差等因素的影响,会导致铸坯内部产生较大的残余应力和组织缺陷,从而严重制约了铝合金板带产品的性能与品质。
因此,如何有效地改善铝合金板带的铸造质量成为当前研究热点之一。
针对上述问题,近年来,许多学者提出了采用辊压技术进行铝合金板带生产的方案。
该技术通过周期性地施加一定压力并配合相应的辊轮形状和运动轨迹,可以使熔融状态下的金属液沿着辊子表面形成均匀的薄层液体膜,进而实现固-液相变分离、结晶细化及致密化等目的,显著提高了合金的塑性成形能力和产品质量。
机械加工表面质量因素分析

5科技资讯科技资讯S I N &T NOLOGY I NFORM TI ON 2008N O .24SC I ENC E &TEC HN OLO GY I NFO RM ATI O N 工业技术1机械加工表面质量对机器使用性能的影响1.1表面质量对耐磨性的影响1.1.1表面粗糙度对耐磨性的影响一个刚加工好的摩擦副的两个接触表面之间,最初阶段只在表面粗糙的的峰部接触,实际接触面积远小于理论接触面积,在相互接触的峰部有非常大的单位应力,使实际接触面积处产生塑性变形、弹性变形和峰部之间的剪切破坏,引起严重磨损。
零件磨损一般可分为三个阶段,初期磨损阶段、正常磨损阶段和剧烈磨损阶段。
表面粗糙度对零件表面磨损的影响很大。
一般说表面粗糙度值愈小,其磨损性愈好。
但表面粗糙度值太小,润滑油不易储存,接触面之间容易发生分子粘接,磨损反而增加。
因此,接触面的粗糙度有一个最佳值,其值与零件的工作情况有关,工作载荷加大时,初期磨损量增大,表面粗糙度最佳值也加大。
1.1.2表面冷作硬化对耐磨性的影响加工表面的冷作硬化使摩擦副表面层金属的显微硬度提高,故一般可使耐磨性提高,但也不是冷作硬化程度愈高,耐磨性就愈高,这是因为过分的冷作硬化将引起金属组织过度疏松,甚至出现裂纹和表层金属的剥落,使耐磨性下降。
1.2表面质量对疲劳强度的影响金属受交变载荷作用后产生的疲劳破坏往往发生在零件表面和表面冷硬层下面,因此零件的表面质量对疲劳强度影响很大。
1.2.1表面粗糙度对疲劳强度的影响在交变载荷作用下,表面粗糙度的凹谷部位容易引起应力集中,产生疲劳裂纹,表面粗糙度值愈大,表面的纹痕愈深,纹底半径愈小,抗疲劳破坏底能力就愈差。
1.2.2残余应力、冷作硬化对疲劳强度的影响余应力对零件疲劳强度的影响很大,表面层残余拉应力将使疲劳裂纹扩大,加速疲劳破坏;而表面层残余应力能够阻止疲劳裂纹的扩展,延缓疲劳破坏的产生表面冷硬一般伴有残余应力的产生,可以防止裂纹产生并阻止已有裂纹的扩展,对提高疲劳强度有利。
注塑件 残余应力
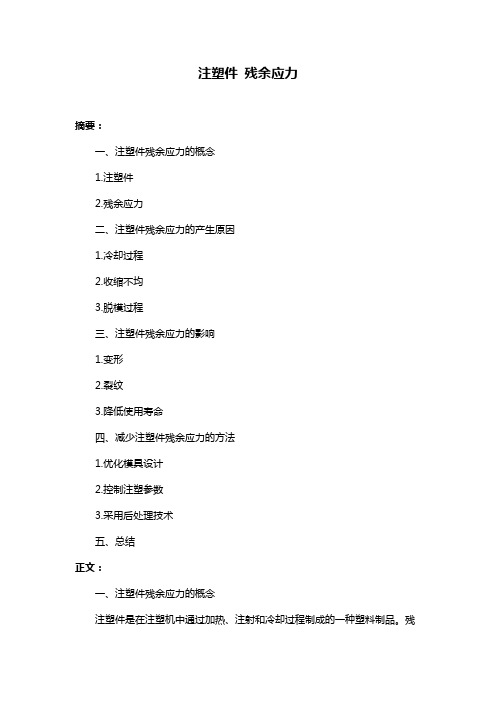
注塑件残余应力摘要:一、注塑件残余应力的概念1.注塑件2.残余应力二、注塑件残余应力的产生原因1.冷却过程2.收缩不均3.脱模过程三、注塑件残余应力的影响1.变形2.裂纹3.降低使用寿命四、减少注塑件残余应力的方法1.优化模具设计2.控制注塑参数3.采用后处理技术五、总结正文:一、注塑件残余应力的概念注塑件是在注塑机中通过加热、注射和冷却过程制成的一种塑料制品。
残余应力是指在注塑件生产过程中,由于冷却收缩、脱模等外力作用,使得塑料内部产生的一种潜在的应力。
这种应力在制品内部形成一个平衡状态,但如果受到外部因素的影响,可能会引发制品变形、裂纹等问题。
二、注塑件残余应力的产生原因1.冷却过程:在注塑件冷却过程中,由于塑料的热膨胀系数和冷却速度不同,容易产生收缩不均,从而导致内部应力的产生。
2.收缩不均:由于模具设计不合理、浇口位置不当等原因,使得塑料在冷却过程中收缩不均,从而形成残余应力。
3.脱模过程:在脱模过程中,如果脱模力过大或过小,都可能导致制品内部产生应力。
三、注塑件残余应力的影响1.变形:残余应力使制品在存放、使用过程中容易发生变形,影响制品的外观和使用性能。
2.裂纹:当残余应力超过制品的强度极限时,容易在制品表面形成裂纹,导致制品报废。
3.降低使用寿命:残余应力会降低制品的使用寿命,严重时可能导致制品在使用过程中突然损坏。
四、减少注塑件残余应力的方法1.优化模具设计:合理设置模具冷却水道,确保冷却速度均匀;选择合适的模具材料,提高模具刚性;合理设置浇口位置,减小收缩变形。
2.控制注塑参数:合理选择注射速度、压力、时间和温度等注塑参数,降低残余应力的产生。
3.采用后处理技术:通过热处理、时效处理等方法,消除或减小残余应力,提高制品的稳定性和使用寿命。
综上所述,注塑件残余应力对制品的质量、使用寿命和性能具有重要影响。
要减少残余应力,需要从模具设计、注塑参数控制和后处理技术等方面进行优化。
PVD法制备(Ti,Al)N涂层中残余应力对其质量的影响
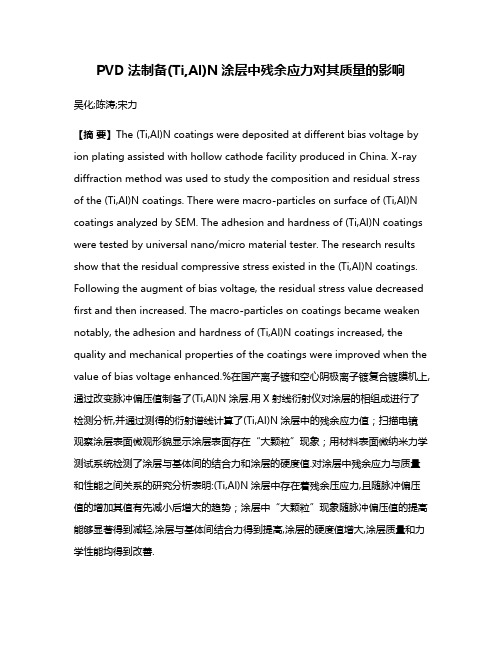
PVD法制备(Ti,Al)N涂层中残余应力对其质量的影响吴化;陈涛;宋力【摘要】The (Ti,Al)N coatings were deposited at different bias voltage by ion plating assisted with hollow cathode facility produced in China. X-ray diffraction method was used to study the composition and residual stress of the (Ti,Al)N coatings. There were macro-particles on surface of (Ti,Al)N coatings analyzed by SEM. The adhesion and hardness of (Ti,Al)N coatings were tested by universal nano/micro material tester. The research results show that the residual compressive stress existed in the (Ti,Al)N coatings. Following the augment of bias voltage, the residual stress value decreased first and then increased. The macro-particles on coatings became weaken notably, the adhesion and hardness of (Ti,Al)N coatings increased, the quality and mechanical properties of the coatings were improved when the value of bias voltage enhanced.%在国产离子镀和空心阴极离子镀复合镀膜机上,通过改变脉冲偏压值制备了(Ti,Al)N涂层.用X射线衍射仪对涂层的相组成进行了检测分析,并通过测得的衍射谱线计算了(Ti,Al)N涂层中的残余应力值;扫描电镜观察涂层表面微观形貌显示涂层表面存在“大颗粒”现象;用材料表面微纳米力学测试系统检测了涂层与基体间的结合力和涂层的硬度值.对涂层中残余应力与质量和性能之间关系的研究分析表明:(Ti,Al)N涂层中存在着残余压应力,且随脉冲偏压值的增加其值有先减小后增大的趋势;涂层中“大颗粒”现象随脉冲偏压值的提高能够显著得到减轻,涂层与基体间结合力得到提高,涂层的硬度值增大,涂层质量和力学性能均得到改善.【期刊名称】《材料工程》【年(卷),期】2013(000)002【总页数】6页(P60-64,92)【关键词】(Ti,Al)N涂层;残余应力;X射线衍射法;大颗粒【作者】吴化;陈涛;宋力【作者单位】长春工业大学先进结构材料教育部重点实验室,长春 130012;长春工业大学先进结构材料教育部重点实验室,长春 130012;长春工业大学先进结构材料教育部重点实验室,长春 130012【正文语种】中文【中图分类】TB302.1;TB333通过PVD方法在材料表面制备(Ti,Al)N涂层替代TiN涂层,将使材料表面获得更为优异的硬度、耐磨损和抗高温氧化等特性[1]。
残余应力对热处理的影响-概述说明以及解释

残余应力对热处理的影响-概述说明以及解释1.引言1.1 概述残余应力是指在材料内部存在的一种留存状态的应力,它可以在热处理过程中产生或减小。
残余应力的存在对材料的性能和稳定性有着重要的影响,因此研究残余应力与热处理的关系具有重要的理论和实际意义。
本文将首先介绍残余应力的概念以及其在材料中的形成机制,然后探讨热处理在材料加工过程中的作用,最后分析残余应力对热处理过程产生的影响。
通过深入探讨残余应力与热处理之间的关系,有助于更好地理解材料的行为,提高材料的性能和延长材料的使用寿命。
1.2 文章结构文章结构部分应包括对整篇文章的内容安排和组织方式进行详细说明,以引导读者对文章的整体结构有清晰的认识。
在这篇关于残余应力对热处理的影响的文章中,文章结构应该包括引言、正文和结论三个主要部分。
引言部分应该简要介绍文章的主题并概述文章的目的和重要性。
正文部分将详细阐述残余应力的概念、热处理的作用以及残余应力对热处理的影响。
最后结论部分将对文章的主要内容进行总结,并探讨残余应力与热处理之间的关系,实际应用中的意义,以及未来研究方向。
通过清晰的文章结构安排,读者可以快速了解整篇文章的内容,并更好地理解作者的观点和论述。
1.3 目的:本文旨在探讨残余应力对热处理的影响,探讨残余应力与热处理之间的相互关系。
我们将深入剖析残余应力的概念、热处理的作用以及残余应力对热处理的具体影响,以期为相关领域的研究和实践提供理论支撑和参考依据。
通过本文的研究,我们希望能够更好地理解残余应力与热处理之间的关系,为工程领域的实际生产提供一定的指导和帮助,促进相关领域的发展和进步。
2.正文2.1 残余应力的概念残余应力是指在材料内部的应力状态,在材料形成过程中产生或者在外部加载消失后保留在材料内部的应力。
在材料经历了各种加工过程,如焊接、锻造、冷却等后,内部会出现不均匀的温度和应变分布,导致产生残余应力。
这种应力不会通过外力作用而发生变化,会一直存在于材料内部,直到被外部力量释放。
渗碳淬硬层残余应力的分布特征
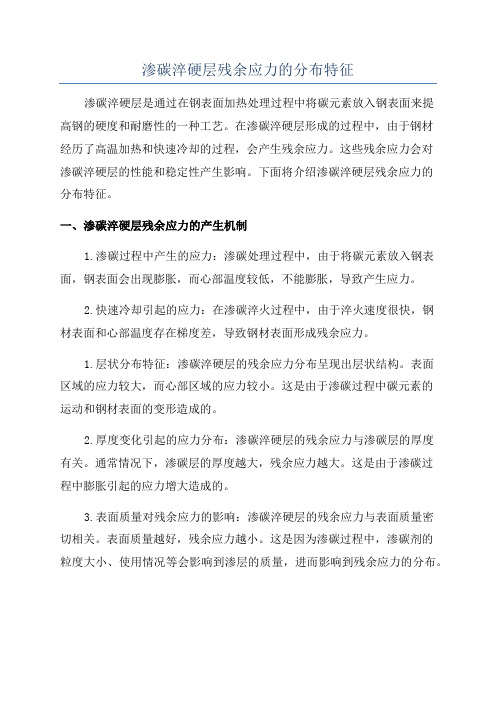
渗碳淬硬层残余应力的分布特征渗碳淬硬层是通过在钢表面加热处理过程中将碳元素放入钢表面来提高钢的硬度和耐磨性的一种工艺。
在渗碳淬硬层形成的过程中,由于钢材经历了高温加热和快速冷却的过程,会产生残余应力。
这些残余应力会对渗碳淬硬层的性能和稳定性产生影响。
下面将介绍渗碳淬硬层残余应力的分布特征。
一、渗碳淬硬层残余应力的产生机制1.渗碳过程中产生的应力:渗碳处理过程中,由于将碳元素放入钢表面,钢表面会出现膨胀,而心部温度较低,不能膨胀,导致产生应力。
2.快速冷却引起的应力:在渗碳淬火过程中,由于淬火速度很快,钢材表面和心部温度存在梯度差,导致钢材表面形成残余应力。
1.层状分布特征:渗碳淬硬层的残余应力分布呈现出层状结构。
表面区域的应力较大,而心部区域的应力较小。
这是由于渗碳过程中碳元素的运动和钢材表面的变形造成的。
2.厚度变化引起的应力分布:渗碳淬硬层的残余应力与渗碳层的厚度有关。
通常情况下,渗碳层的厚度越大,残余应力越大。
这是由于渗碳过程中膨胀引起的应力增大造成的。
3.表面质量对残余应力的影响:渗碳淬硬层的残余应力与表面质量密切相关。
表面质量越好,残余应力越小。
这是因为渗碳过程中,渗碳剂的粒度大小、使用情况等会影响到渗层的质量,进而影响到残余应力的分布。
4.温度梯度对应力的影响:温度梯度是渗碳淬硬过程中产生残余应力的主要因素之一、渗碳淬火过程中,由于表面和心部的温度梯度差异,会导致残余应力的产生。
温度梯度越大,残余应力越大。
三、渗碳淬硬层残余应力的控制方法为了控制渗碳淬硬层的残余应力,可以考虑以下方法:1.控制渗碳温度和时间:渗碳温度和时间的控制对渗碳淬硬层的残余应力有重要影响。
合理选择渗碳温度和时间,可以减小残余应力。
2.控制淬火速度:淬火速度对渗碳淬硬层的残余应力有显著影响。
合理选择淬火速度,可以减小残余应力。
3.提高硬化工艺控制精度:提高硬化工艺的控制精度,可以减小残余应力的产生。
4.优化渗碳剂和处理工艺:优化渗碳剂和处理工艺,可以改善渗碳淬硬层的质量,从而减小残余应力的产生。
- 1、下载文档前请自行甄别文档内容的完整性,平台不提供额外的编辑、内容补充、找答案等附加服务。
- 2、"仅部分预览"的文档,不可在线预览部分如存在完整性等问题,可反馈申请退款(可完整预览的文档不适用该条件!)。
- 3、如文档侵犯您的权益,请联系客服反馈,我们会尽快为您处理(人工客服工作时间:9:00-18:30)。
• 影响残余应力的工艺因素主要是刀具的前角、切削速度以及工件 材料的性质和冷却润滑液。但是,具体情形则视其对切削时的塑 性变形、切削温度和金相组织变化的影响程度而定。
冷态塑性变形
塑Байду номын сангаас变形
残余应力的产生 金相组织变化 热态塑性变形
冷态塑性变形和金相组织变化
• 冷态塑性变形 机械加工时,表层金属产生强烈的塑性变形。工件表面的晶粒 沿切削速度方向被拉长,密度减小,比容增大,而里层材料阻碍这 种变化。所以工件的表面层产生残余压应力,里层产生残余拉应力。 • 金相组织变化 切削时产生高温引起表面的相变,由于不同的金相组织有不 同的比容,表面层金相变化造成体积变化。表面层体积膨胀产生压 应力,体积缩小则产生拉应力。
热态塑性变形
加工时,温度与离表面深度
加工时,应力与离表面深度
开始冷却时,应力与离表面深度
最后冷却时,应力与离表面深度
三类磨削条件
轻磨削——塑性变形 中等磨削——金相组织变化 重磨削——热态塑性变形和金相组织变化
磨削裂纹的产生
• 当工件表面的残余拉应力超过材料的强度极限时,零件表面就会 出现裂纹,一般在0.25~0.50mm的深度,大多数垂直于磨削方 向或成网状。 磨削裂纹产生的主要原因是材料性 质及热处理工序。因此,在磨削前 先去除残余应力会比较好,渗碳、 渗氮时,如果工艺不当,也容易出 现网状裂纹。