机床夹具设计步骤和实例
机床专用夹具及其设计方法
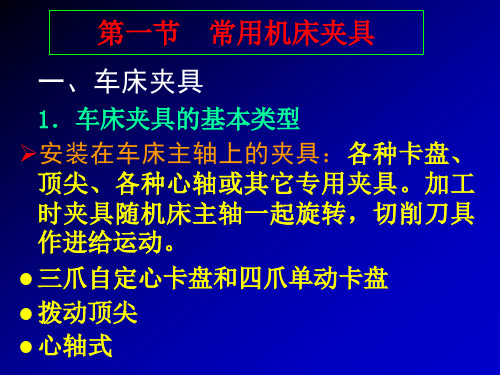
要有快速对刀元件
2、铣床夹 具的构造 主要由夹 具体、定 位板、夹 紧机构、 对刀块、 定向键等 组成
3.铣床夹具的设计
铣床夹具的安装:主要依靠定向键和
百分表校正来提高安装精度。定位键 的结构尺寸已标准化,应按铣床工作 台的T形槽尺寸选定,它和夹具底座 以及工作台T形槽的配合为H7/h6、 H8/h8。两定位键的距离应力求最大
• • • •
1、分度盘锁紧螺母 2、分度盘 3、定位轴 4、压紧螺母
移动式钻模
• 移动式钻模用在立式钻床上,先后钻销 工件同一表面上的多个孔,属于小型夹 具。移动的方法有两种:一种式自由移 动,另一种是定向移动,用专门设计的 轨道和定程机构来控制移动的方向和距 离。
滑柱式钻模
滑柱式钻模是一种标准化,规格化的 通用钻模。钻模体可以通用于较大范围 的不同工件。设计时,只需根据不同的 加工对象设计相应的定位。夹紧元件。 因此,可以简化设计工作。另外,这种 钻模不需另行设计专门的夹紧装置,夹 紧工件方便,迅速,适用于不同类型的 各种中小型零件的孔加工,生产中,尤 其是大批量生产中应用较广。
4、钻套的材料
性能要求:高硬度,耐磨 常用材料:T10A T12A CrMn 或20渗 碳淬火 D≤10mm CrMn D<25mm T10A T12A HRC58~64 D≥25mm 20渗碳淬火 HRC58~64
镗模
(一)镗模的特点及其组成 1、特点:镗床夹具称镗模,主要用于加工 箱体类零件上的孔或孔系通过布置镗套, 可加工出较高精度要求的孔或孔系。 与 钻模相比,它有相同之处,但箱体孔系 的加工精度一般要求较高,其本身精度 比钻模高。
l—台肩销 2—快换垫圈 3—螺母
机床夹具的设计步骤

机床夹具的设计步骤一、夹具的设计步骤1.设计准备工作——研究原始资料,明确设计要求和生产条件(1)生产纲领(生产类型)——了解生产批量和对夹具的需用情况;(2)零件图及工序图——了解工件情况、工序要求和加工状态;(3)零件的工艺规程——了解所用机床、刀具等的情况;(4)夹具制造能力——了解夹具制造车间的生产条件和技术现状(5)典型夹具结构及标准——同类型产品的夹具结构、有关夹具标准。
2.确定夹具的结构方案(总体方案)主要包括:(1)确定工件的定位方案,设计定位装置。
根据六点定位原理,确定工件的定位方式,选择和设计定位元件,计算定位误差。
(2)确定工件的夹紧方案,设计夹紧装置。
确定夹紧力、夹紧机构及动力装置。
(3)确定对刀或导向方案,设计对刀或导向装置。
对刀块或钻套、镗套等的设计。
(4)确定其它元件或装置的结构形式。
定位键、分度装置、连接元件等。
(5)协调各装置、元件的布局,确定夹具在机床上的安装方式以及夹具体的结构型式。
3.绘制夹具装配图按照国家制图标准绘制,应清楚表达出夹具的结构及各装置、元件之间的位置关系。
主视图应取操作者实际工作时的位置。
具体方法和步骤如下:(1)在装配图上,工件看作透明体,用双点划线将工件的外形轮廓、定位基面、夹紧表面及加工表面绘制在各个视图的合适位置上。
(2)依次绘出定位元件或装置、夹紧元件或装置、对刀或导向元件、其它元件、夹具体及连接元件。
(3)标注必要的尺寸、公差和技术要求。
(4)编制夹具明细表及标题栏。
图5-69 实例(改错:图中的错误——①心轴;②开口垫;③辅助支承;④V形块移动手柄;⑤技术要求)4.绘制夹具零件图。
画出夹具中非标零件图,并按夹具装配图的要求确定零件的尺寸、公差及技术要求。
——尺寸及公差、形位公差、表面粗糙度等标注要完整、正确。
二、夹具精度校核使用专用夹具加工工件时,影响加工精度的误差因素主要有三个方面:①工件在夹具中的安装误差,包括定位误差、夹紧误差(工件及夹具的夹紧变形)、夹具制造误差、导向误差等;②对定误差,即夹具在机床上的安装误差;③加工过程误差,与切削过程有关的误差。
机床夹具设计步骤和实例

机床夹具设计步骤和实例机床夹具是用于在机床上夹持工件或刀具的装置,用于保持工件的位置稳定,使其能够被加工。
机床夹具设计的步骤主要包括需求分析、夹具类型选择、夹具基础结构设计、夹具强度计算、夹具定位系统设计、夹具操作系统设计、夹具零件设计和夹具组装等。
以下为机床夹具设计步骤和一个实例:步骤1:需求分析首先,需要了解加工工件的要求和工艺流程。
通过与工艺人员或工程师的交流,了解工件的形状、材料、尺寸等特性,以及工件的精度要求、加工工艺和工时要求等。
根据需求分析,明确夹具的基本功能、定位方式和操作方式。
步骤2:夹具类型选择根据加工工件的特性和加工工艺的要求,通过参考手册或专业书籍选择合适的夹具类型。
常见的夹具类型包括平板夹具、顶升夹具、转角夹具、滑块夹具、气垫夹具等。
根据不同的工件形状和加工要求,选择适合的夹具类型。
步骤3:夹具基础结构设计根据工件的形状和夹持要求,设计夹具的基础结构。
夹具的基础结构通常由夹紧装置、支撑装置和定位装置组成。
夹紧装置主要用于夹持工件,支撑装置用于保持工件的平衡和稳定,定位装置用于确保工件的位置准确。
步骤4:夹具强度计算根据夹具类型和加工工件的特性,计算夹具的强度。
夹具的强度计算包括静态强度和动态强度两个方面。
静态强度主要考虑夹具在夹持工件时的受力情况,包括切削力、惯性力等;动态强度主要考虑夹具在工件加工过程中的振动和冲击力,保证夹具结构能够承受夹持工件时的各种力。
步骤5:夹具定位系统设计根据工件的定位要求,设计夹具的定位系统。
夹具的定位系统应能够满足工件的精度要求,并确保工件的位置准确。
定位系统常采用定位销、定位块等形式,根据工件的形状和加工特点选择合适的定位方式。
步骤6:夹具操作系统设计根据夹具的使用要求,设计夹具的操作系统。
夹具的操作系统主要包括夹紧装置的控制方式和操作机构的设计。
根据夹紧力的大小和控制精度的要求,选择合适的液压夹紧系统或气动夹紧系统。
步骤7:夹具零件设计根据夹具的基础结构、定位系统和操作系统的设计要求,设计夹具的各个零件。
补充:机床夹具设计步骤
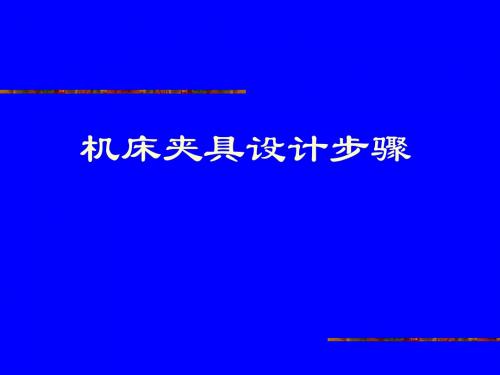
夹具的设计步骤:
一、设计准备
1、研究被加工零件,明确夹具设计任务。 2、分析零件的加工工艺过程。 3、了解所使用机床的性能、规格和运动情况。 4、了解零件的生产纲领等情况。 5、收集有关设计资料。
二、总体设计
1、拟定夹具的结构方案,绘制结构草图
确定工件的定位方案,设计定位装置 确定工件的夹紧方案,设计夹紧装置和引导方案 确定其他元件或装置的结构型式,如定向键,分度装置等 合理布置各元件或装置,确定夹具体的结构形式及在机
车床夹具的主要类型
(2)卡盘类车床夹具
用卡盘类车床夹具加工的零件,大都是回转体或对称 零件,因而卡盘类车床夹具的结构基本上是对称的,回转 时的不平衡影响较小。 角铁式夹具主要使用于以下两种情况: 工件的主要定位基准是平面,要求被加工表面的轴线 对定位基准面保持一定的位置关系。 工件定位基准虽然不是与被加工表面的轴线平行或成 一定角度的平面,但由于工件外形的限制,不适宜采用卡 盘式夹具,而必须采用半圆孔或V形块定位件的情况。
这类钻模是一种小型夹具,在操作过程中,需要用人工进 行翻动,为了减轻工人的劳动强度,这类钻模的总质量最好 不要超过10KG,且工件加工孔直径小于8~10mm。
支柱式钻模是这类钻模的典型结构之一,他用于钻同方向 上的孔系。结构特点是用四个支脚来支撑钻模。
三、回转式钻模
回转式钻模的结构形式按其转轴的位置可分为立轴式,卧轴 式和斜轴式三种。这类钻模的引导元件(钻套),一般是固定 不动的,为了实现工件在一次安装中进行多工位加工的目的, 钻模一般采用回转式分度装置。
回转式钻模主要适用于加工围绕回转轴线而分布的轴向或 径向的孔系。特别是对无法采用翻转式钻模的大型多孔零件 宜使用回转式钻模。既可保证加工精度,又可以提高生产效 率。
第二章 2.3典型机床夹具及设计步骤

特点:铣削中和工作台一起运动;结构主要取决于铣 削方式(直线进给、圆周进给)。 (一)主要类型 根据加工件数可分为 1.单件加工铣床夹具:如图2-78铣槽夹具。 2.多件加工铣床夹具:如图2-79多件铣槽夹具。 3.双工位铣床夹具:如图2-80双工位铣端面夹具。 (二)定位键 确定夹具在工作台上的位置与相对机床进给方向的正 确位置。结构如图2-81所示。
§ 2-7 典型机床夹具
3.钻套相关尺寸
1)钻套高度:H/d=1~1.25
2)钻套与工件间的排屑间隙: C=(1/3~1)d 脆性材料取小值;塑性材料取大值。 3)钻套内径与刀具的配合:采用间隙 配合。尺寸及偏差据刀具种类和被 加工孔的尺寸精度确定。一般钻套 内径基本尺寸应为刀具最大极限尺 寸。钻孔、扩孔可按F7;粗铰按G7, 精铰用G6。
3.滑柱式:钻模板安装在可升降滑柱上,兼起夹紧作用。
§ 2-7 典型机床夹具
(二)钻套 钻套是引导孔加工刀具的元件。
1.主要作用
1)确定刀具相对定位元件的位置; 2)引导钻头等孔加工刀具;
3)提高其刚性,防止刀具加工偏斜和摆动;
4)夹具在机床上定位安装。
§ 2-7 典型机床夹具
2.钻套的结构
§2-7 典型机床夹具
一、钻床夹具(钻模) 用于孔加工:钻、扩、铰孔;
特点:钻套,引导刀具。 (一)钻床夹具的主要类型 根据加工要求的不同,可分为: 1.固定式:钻模板与夹具体固 定连接,通常用于立式钻床 加工单孔,或在摇臂钻床上 加工平行孔系。
2.回转式:
与回转台联合使 用组成多工位, 用于圆周上孔 系加工。
§ 2-7 典型机床夹具
(三)对刀元件
确定刀具相对于夹具的正确位置。通常由对刀块与塞 尺组成。主要结构形式如图2-82所示。
机床夹具设计方法及步骤

第四章 机床夹具的设计方法及步骤
§4-2 机床夹具设计实例
三、绘制夹具总图
1.应标注的尺寸及配合
⑴最大轮廓尺寸 ⑵定位元件尺寸 ⑶对刀元件与定位元件定 位面之间的位置尺寸
第29次课
教学课型:理论课
机床夹具设计
第四章 机床夹具的设计方法及步骤
§4-2 机床夹具设计实例
三、绘制夹具总图
1.应标注的尺寸及配合
机床夹具设计
一、研究原始资料、分析设计任务 夹具的设计任务由工艺人员提出,夹具设计人 为保证设计质量,设计前应搜集和研究下列资
员应根据设计任务书进行结构设计。
料:
生产纲领
机床夹具设计
生产纲领决定了批量: 大量生产时,宜采用气动或其它机动夹具,以提高 生产率和自动化程度,但结构较复杂; 小批生产时,宜采用结构简单、成本低的手动夹具, 以尽快投产。
机床夹具设计
四、确定并标注有关尺寸、配合和技术条件 1.应标注的尺寸与配合
尺寸公差的确定有两种情况: 定位元件之间,对刀、导引元件之间的尺寸公差,直 接对工件上相应的尺寸产生影响,故一般取相应尺寸公 差的1/3~1/5;
其它尺寸按一般极限与配合原则确定。
机床夹具设计
2.应标注的技术条件(位置要求)
教学课型:理论课
机床夹具设计
第四章 机床夹具的设计方法及步骤
§4-2 机床夹具设计实例
四、确定夹具的主要尺寸、配合及技术条件
1.应标注的尺寸及配合
⑴最大轮廓尺寸
据实际尺寸确定。
第29次课
教学课型:理论课
机床夹具设计
第四章 机床夹具的设计方法及步骤
§4-2 机床夹具设计实例
四、确定夹具的主要尺寸、配合及技术条件 1.应标注的尺寸及配合
机床夹具设计实例
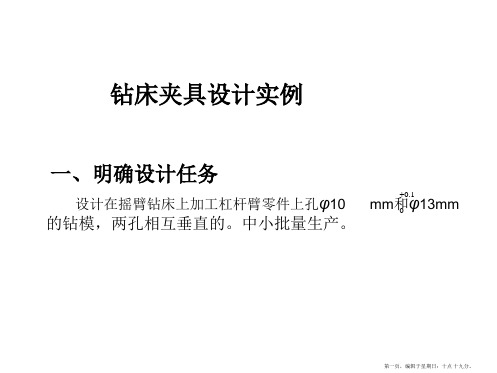
一、明确设计任务
设计在摇臂钻床上加工杠杆臂零件上孔φ10 mm和00.φ1 13mm 的钻模,两孔相互垂直的。中小批量生产。
第一页,编辑于星期日:十点 十九分。
一、明确设计任务
1.杠杆臂零件图
第二页,编辑于星期日:十点 十九分。
一、明确设计任务
2.杠杆臂加工工艺分析
(1)加工要求: 加工φ10 和0.1 φ13两孔;孔距为78±0.5; φ13与Φ22轴线的水平尺寸
度要求,两个支承钉在夹具体上安装到位后(见装配图),随夹 具体在车床上加工(车支承钉端面),以保证它们伸出的长度等 高允差不大于0.01mm。
第四十七页,编辑于星期日:十点 十九分。
2.夹紧装置
(1)夹紧机构
夹紧机构采用螺旋夹紧机构,为使机构简单 ,直接在定位心轴上加工螺纹。并根据类比法, 选用M20螺纹以满足强度要求。
公差: Φ10G7、 Φ13F7(公差带查表确定) • 影响夹具精度的尺寸及公差(公差按零件公差的1/2至1/5):
78±0.15、 15±0.15、 12.5±0.05、相对于基准F的垂
直度Φ0.05、相对于基准F的垂直度Φ0.03、相对于基准E 的垂直度Φ0.05 • 其它重要尺寸和公差:Φ18H7/r6、 Φ22H7/n6以及定位 销与夹具体的配合尺寸(图中遗漏,应补上)
– ΔT=(0.028+0.036)mm=0.064mm
• 安装误差ΔA:
– ΔA=0
第二十页,编辑于星期日:十点 十九分。
工件加工精度分析
• 夹具误差ΔJ:
78±0.5的夹具误差为:0.3 15±0.5的夹具误差为:0.3 12.5的夹具误差为:0.1 平行度0.1的夹具误差为:0.05 垂直度0.1的夹具误差为:0.05
机床夹具设计步骤和实例

机床夹具设计步骤和实例Company Document number:WUUT-WUUY-WBBGB-BWYTT-1982GT第2节机床夹具设计实例一、钻夹具的设计实例图2-2-20所示为杠杆类零件图样。
图2-2-21所示为本零件工序图。
1.零件本工序的加工要求分析①钻、扩、铰φ10H9孔及φ11孔。
②φ10H9孔与φ28H7孔的距离为(80±0.2)mm;平行度为。
③φ11孔与φ28H7孔的距离为(15±0.25)mm。
④φ11孔与端面K距离为14mm。
本工序前已加工的表面如下。
①φ28H7孔及两端面。
②φ10H9两端面。
本工序使用机床为Z5125立钻,刀具为通用标准工具。
2.确定夹具类型本工序所加工两孔(φ10H9和φ11),位于互成90°的两平面内,孔径不大,工件质量较小、轮廓尺寸以及生产量不是很大,因此采用翻转式钻模。
3.拟定定位方案和选择定位元件(1)定位方案。
根据工件结构特点,其定位方案如下。
①以φ28H7孔及一组合面(端面K和φ10H9一端面组合而成)为定位面,以φ10H9孔端外缘毛坯面一侧为防转定位面,限制六个自由度。
这一定位方案,由于尺寸885.0mm公差大,定位不可靠,会引起较大的定位误差。
如图2-2-22(a)所示。
②以孔φ28H7孔及端面K 定位,以φ11孔外缘毛坯一侧为防转定位面,限制工件六个自由度。
为增加刚性,在φ10H9的端面增设一辅助支承,如图2-2-22 (b)所示。
比较上述两种定位方案,初步确定选用图2-2-22(b)所示的方案。
(2)选择定位元件。
①选择带台阶面的定位销,作为以φ28H7孔及其端面的定位元件,如图2-2-23所示。
定位副配合取6728g H φ。
②选择可调支承钉为φ11孔外缘毛坯一侧防转定位面的定位元件,如图2-2-24(a)所示。
也可选择如图2-2-24 (b)所示移动V 形块。
考虑结构简单,现选用图2-2-24(a)所示结构。
夹具设计步骤

一、机床夹具设计要求1.保证工件加工的各项技术要求要求正确确定定位方案、夹紧方案,正确确定刀具的导向方式,合理制定夹具的技术要求,必要时要进行误差分析与计算。
2.具有较高的生产效率和较低的制造成本为提高生产效率,应尽量采用多件夹紧、联动夹紧等高效夹具,但结构应尽量简单,造价要低廉。
3.尽量选用标准化零部件尽量选用标准夹具元件和标准件,这样可以缩短夹具的设计制造周期,提高夹具设计质量和降低夹具制造成本。
4.夹具操作方便安全、省力为便于操作,操作手柄一般应放在右边或前面;为便于夹紧工件,操纵夹紧件的手柄或扳手在操作范围内应有足够的活动空间;为减轻工人劳动强度,在条件允许的情况下,应尽量采用气动、液压等机械化夹紧装置。
5.夹具应具有良好的结构工艺性所设计的夹具应便于制造、检验、装配、调整和维修。
二、机床夹具设计的内容及步骤1.明确设计要求,收集和研究有关资料在接到夹具设计任务书后,首先要仔细阅读加工件的零件图和与之有关的部件装配图,了解零件的作用、结构特点和技术要求;其次,要认真研究加工件的工艺规程,充分了解本工序的加工内容和加工要求,了解本工序使用的机床和刀具,研究分析夹具设计任务书上所选用的定位基准和工序尺寸。
2.确定夹具的结构方案1)确定定位方案,选择定位元件,计算定位误差。
2)确定对刀或导向方式,选择对刀块或导向元件。
3)确定夹紧方案,选择夹紧机构。
4)确定夹具其他组成部分的结构形式,例如分度装置、夹具和机床的连接方式等。
5)确定夹具体的形式和夹具的总体结构。
在确定夹具结构方案的过程中,应提出几种不同的方案进行比较分析,选取其中最为合理的结构方案。
3.绘制夹具的装配草图和装配图夹具总图绘制比例除特殊情况外,一般均应按1:1绘制,以使所设计夹具有良好的直观性。
总图上的主视图,应尽量选取与操作者正对的位置。
绘制夹具装配图可按如下顺序进行:用双点划线画出工件的外形轮廓和定位面、加工面;画出定位元件和导向元件;按夹紧状态画出夹紧装置;画出其他元件或机构;最后画出夹具体,把上述各组成部分联结成一体,形成完整的夹具。
机床夹具设计实例

机床夹具设计实例机床夹具是用于固定和定位工件的装置,用于加工过程中保证工件的稳定性和精确性。
下面介绍一个机床夹具设计的实例。
设计背景:工厂需要生产一种特殊型号的零件,该零件具有复杂的形状和尺寸要求。
为了满足零件的加工需求,设计了一款多功能机床夹具。
设计思路:1.确定工件特点:首先,需要对待加工的零件进行分析,了解其特点。
该零件较长,且具有多个复杂的曲面和孔洞,同时需要保证加工的精度和效率。
2.设计夹具结构:根据对工件的分析,制定夹具结构设计方案。
考虑到零件的形状复杂,需要设计一个多功能的夹具,可以在同一个夹具上完成多道工序的加工,提高加工效率。
夹具结构包括底座、夹持部件和定位部件。
3.设计固定夹持部件:设计固定夹持部件来夹持工件,保证工件的稳定性。
根据零件的形状和尺寸要求,设计了多个夹持点,分布在不同的夹持面上。
夹持部件采用可调式夹持方式,根据工件尺寸进行调节,确保夹持力均匀分布,避免工件变形。
4.设计定位部件:设计定位部件用来确保工件在夹持过程中的正确定位,以保证加工精度。
根据零件的特点,设计了多个定位销和定位块,与工件上的定位孔和定位台配合使用,确保工件的位置和姿态准确无误。
5.考虑工艺要求:考虑到零件加工的要求,设计了适合加工该零件的加工工艺。
在夹具上加装刀具支撑和冷却装置,以确保加工过程中的稳定性和切削效果。
6.进行夹具的综合性能检验:对设计出的机床夹具进行综合性能检验。
测试夹具对工件的夹持力和定位精度,检测夹具的刚性和稳定性。
根据测试结果对夹具进行调整和改进,以达到设计要求。
该机床夹具设计实例充分考虑了工件的特点和加工要求,通过综合运用夹持和定位原理,设计了满足复杂形状零件加工需求的多功能机床夹具。
设计过程中注重夹持力的均匀分布和定位的准确性,以满足零件加工的精度和效率要求。
在设计完成后进行了综合性能检验,确保夹具的稳定性和可靠性。
机床夹具设计步骤和实例[2]
![机床夹具设计步骤和实例[2]](https://img.taocdn.com/s3/m/852c558bcc22bcd126ff0ccf.png)
第2章机床夹具设计步骤和实例2.1机床夹具设计的基本要求和一般设计步骤一、机床夹具设计的基本要求1.保证工件的加工精度专用夹具应有合理的定位方案,合适的尺寸、公差和技术要求,并进行必要的精度分析,确保夹具能满足工件的加工精度要求。
2.提高生产效率专用夹具的复杂程度要与工件的生产纲领相适应。
应根据工件生产批量的大小选用不同复杂程度的快速高效夹紧装置,以缩短辅助时间,提高生产效率。
3.工艺性好专用夹具的结构应简单、合理、便于加工、装配、检验和维修。
专用夹具的生产属于单件生产。
当最终精度由调整或修配保证时,夹具上应设置调整或修配结构,如适当的调整间隙、可修磨的垫片等。
4.使用性好专用夹具的操作应简便、省力、安全可靠,排屑应方便,必要时可设置排屑结构。
5经济性好除考虑专用夹具本身结构简单、标准化程度高、成本低廉外,还应根据生产纲领对夹具方案进行必要的经济分析,以提高夹具在生产中的经济效益。
二、机床夹具设计的一般步骤1.研究原始资料在明确设计任务(通常在生产厂根据夹具设计任务书)后,应对以下几方面的原始资料进行研究。
(1)研究加工工件图样。
了解该工件的结构形状、尺寸、材料、热处理要求,主要表面的加工精度、表面粗糙度及其他技术要求。
(2)熟悉工艺文件,明确以下内容。
①毛坯的种类、形状、加工余量及其精度。
②工件的加工工艺过程、工序图、本工序所处的地位,本工序前已加工表面的精度及表面粗糙度,基准面的状况。
③本工序所使用的机床、刀具及其他辅具的规格。
④本工序所采用的切削用量。
2.拟定夹具的结构方案拟定夹具的结构方案包括以下几个内容。
(1)确定夹具的类型。
各类机床夹具均有多种不同的类型,如车床夹具可有角铁式、圆盘式等,钻床夹其有固定式、翻转式、盖板式等,应根据工件的形状.尺寸、加工要求及重量确定合适的夹具类型。
(2)确定工件的定位方案,设计定位装置。
根据六点定位原则,分析工序图上所规定的定位方案是否可取,否则应提出修改意见或提出新的方案,与有关工艺人员协商后确定。
专用机床夹具设计的全过程
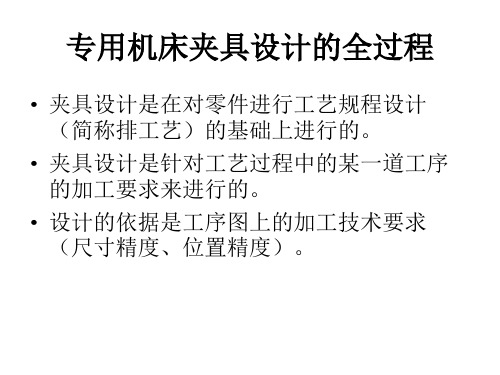
2.3.3
夹具的其它要求:
• 如夹具的平衡与密封,装配性能要求,有 关机构的调整参数、主要零件的磨损范围 和极限以及使用中的注意事项。 • 这些应在夹具设计总图上标注清楚。
夹具体的设计
1、夹具体的作用及基本要求:
夹具体是夹具的基本元件。夹具的基面与机床连接,其它工 作表面则装配各种元件和装置,以组成夹具的总体。 基本要求: 1)夹具体的结构形式一般由机床的有关参数和加工方式而定。 2)有一定的精度和良好的结构工艺性。 夹具体有三个重要表面:夹具体在机床上的安装面、装配 定位元件表面和装配对刀或导向元件的表面。一般应以夹 具体的基面为主要设计基准及工艺基准。这样有利于制造、 装配、使用和维修。 3)要有足够的强度和刚度。 对于铸件夹具体其壁厚一般取15—30mm。焊接夹具体的壁 厚取8—15 mm。若需用加强肋的则厚度取为壁厚的0.7— 0.9倍。 4)在机床工作台上安装的夹具,应使其重心尽量低,夹具体 的高度尺寸要小。
• 定位装置的方案设计:
应限制几个自由度,定位方案的布置、有多个 方案时还应注意方案的比较、筛选,定位元件的 确定。
夹紧方案的设计:
• 夹紧装置、机构的考虑,要能满足生产率 要求。 • ①、夹紧过程中,不改变工件定位后所占 据的正确位置。 • ②、夹紧力的大小要可靠适当,即要稳固, 又要不产生过大的夹紧变形。 • ③、在保证生产率的前提下,其结构力求 简单,便于加工、维修。 • ④、夹紧装置应操作方便、安全、省力。
夹具的设计步骤:
• 工件的定位方案设计,要注意满足: • 定位设计应遵循的3项基本原则: • 1)依循基准重合原则。使定位基准与工 序基准重合。 • 2)合理选择主要定位基准。 • 3)便于工件的装夹和加工,并使夹具的 结构简单。
工装夹具设计图解及实例

效率低,找正精度 较高;适用单件小 批量中形状简单的 工件.
通用性好,但效率 低,精度不高;适 用于单件小批量中 形状复杂的铸件.
操作简单,效率高, 容易保证加工精度, 适用于各种生产类型 .
9
1直接找正装夹
将工件装在机床上,然后按工件的某个或某些 表面,用划针或用百分表等量具进行找正,以获 得工件在机床上的正确位置.
32
3 对刀、引导元件或装置
这些元件的作用是保证工件与刀具之间的正确位置. 用于确定刀具在加工前正确位置的元件,称为对刀元
件,如对刀块. 用于确定刀具位置并导引刀具进行加工的元件,称为
导引元件. 如图中的快换钻套1.
2006-2
33
4 连接元件
使夹具与机床相连接的元件,保证机床与夹具之间的 相互位置关系.
2006-2
38
二、基准及其分类
基准
用于确定零件上 其它点、线、面 位置所依据的那 些点、线、面.
设计图样上所采 用的基准就是设 计基准.图
在加工时用于工件 定位的基准,称为
定位基准.图
设计基准 工艺基准
定位基准 测量基准
1、粗基准 2、精基准 3、辅助基准 4、主要基准 5、附加基准
在加工中或加工
如果工件的定位面经过了机械加工,并且定位面 和定位元件的尺寸、形状和位置都做得比较准确,比 较光整,则过定位不但对工件加工面的位置尺寸影响 不大,反而可以增强加工时的刚性,这时过定位是允
14
2006-2
15
2专用夹具
专用夹具是指专为某一工件的某道工序而专门设计 的夹具.
其特点是结构紧凑,操作迅速、方便、省力,可以保 证较高的加工精度和生产效率,但设计制造周期较长、 制造费用也较高.
机床夹具设计步骤和实例
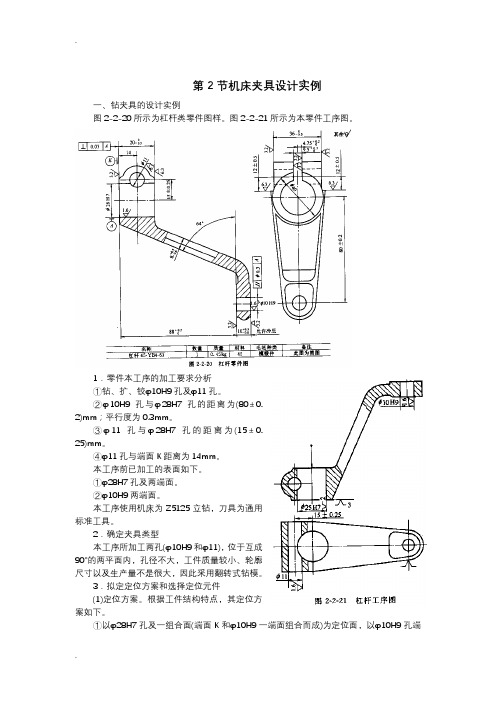
第2节机床夹具设计实例一、钻夹具的设计实例图2-2-20所示为杠杆类零件图样。
图2-2-21所示为本零件工序图。
1.零件本工序的加工要求分析①钻、扩、铰φ10H9孔及φ11孔。
②φ10H9孔与φ28H7孔的距离为(80±0.2)mm;平行度为0.3mm。
③φ11孔与φ28H7孔的距离为(15±0.25)mm。
④φ11孔与端面K距离为14mm。
本工序前已加工的表面如下。
①φ28H7孔及两端面。
②φ10H9两端面。
本工序使用机床为Z5125立钻,刀具为通用标准工具。
2.确定夹具类型本工序所加工两孔(φ10H9和φ11),位于互成90°的两平面内,孔径不大,工件质量较小、轮廓尺寸以及生产量不是很大,因此采用翻转式钻模。
3.拟定定位方案和选择定位元件(1)定位方案。
根据工件结构特点,其定位方案如下。
①以φ28H7孔及一组合面(端面K 和φ10H9一端面组合而成)为定位面,以φ10H9孔端外缘毛坯面一侧为防转定位面,限制六个自由度。
这一定位方案,由于尺寸885.00+mm 公差大,定位不可靠,会引起较大的定位误差。
如图2-2-22(a)所示。
②以孔φ28H7孔及端面K 定位,以φ11孔外缘毛坯一侧为防转定位面,限制工件六个自由度。
为增加刚性,在φ10H9的端面增设一辅助支承,如图2-2-22 (b)所示。
比较上述两种定位方案,初步确定选用图2-2-22(b)所示的方案。
(2)选择定位元件。
①选择带台阶面的定位销,作为以φ28H7孔及其端面的定位元件,如图2-2-23所示。
定位副配合取6728g H φ。
②选择可调支承钉为φ11孔外缘毛坯一侧防转定位面的定位元件,如图2-2-24(a)所考虑结构简单,现选用图2-2-24(a)所示结构。
(3)定位误差计算①加工φ10H9孔时孔距尺寸(80±0.2)mm的定位误差计算。
由于基准重合,故ΔB=0。
基准位移误差为定位孔(φ38021.00+mm)与定位销(φ38007.0002.0--mm)的最大间隙,故ΔY =(0.021+0. 007+0.013)mm =0.041rnm 。
5机床夹具设计步骤与方法

5.6 机床夹具设计步骤与方法本节着重介绍专用机床夹具的设计步骤与方法,并讨论与此有关的一些问题。
5.6.1 专用夹具设计的基本要求机床专用夹具设计的基本要求可概括为以下几方面:1.保证工件的加工精度这是夹具设计的最基本要求,其关键是正确地确定定位方案、夹紧方案、刀具导向方式及合理制定夹具的技术要求,必要时应进行误差分析与计算。
2.夹具总体方案应与生产纲领相适应在大批量生产时,应尽量采用各种快速、高效结构,如多件夹紧、联动夹紧等,以缩短辅助时间,提高生产率;在中小批量生产中,则要求在满足夹具功能的前题下,尽量使夹具结构简单、容易制造、以降低夹具制造成本。
3.操作方便,使用安全所设计的夹具应能减轻工人劳动强度,如采用气功、液压等机械化夹紧装置,以减轻工人的劳动强度,并可较好地控制夹紧力。
夹具操作位置应符合操作工人的习惯,必要时应有安全保护装置,以确保使用安全。
4.便于排屑切屑积聚在夹具中,会破坏工件正确的定位;切屑带来的大量热量会引起夹具和工件的热变形,影响加工质量;切屑的清扫又会增加辅助时间,降低工作效率;切屑积聚严重时,还会损伤刀具或造成工伤事故。
因此排屑问题在夹具设计时必须给予充分的注意,在设计高效机床夹具时尤为重要。
5.有良好的结构工艺性所设计的夹具应便于制造、检验、装配、调整、维修等。
5.6.2 专用夹具设计的一般步骤专用夹具设计的一般步骤如下:1.研究原始资料,明确设计要求,收集设计资料在接到夹具设计任务书后,首先要仔细地阅读被加工零件的零件图和装配图,清楚地了解零件的作用、结构特点、材料及技术要求。
其次要认真地研究零件的工艺规程,充分了解本工序的加工内容和加工要求、加工余量、定位基准及所使用的工艺装备。
收集有关资料,如机床的技术参数,夹具部件的国家标准、部颁标准、企业标准和厂定标准,典型夹具结构图册,夹具设计指导资料等。
必要时还应了解同类零件所用过的夹具及其使用情况,作为设计时的参考。
典型机床夹具设计

典型机床夹具设计引言:机床夹具设计是机械加工中重要的一部分,它的设计质量直接影响到加工产品的质量和生产效率。
典型机床夹具设计包括夹具的选择、夹具的结构设计和夹具的加工制造等方面。
本文将就典型机床夹具设计的一般步骤进行分析,并以五轴加工中心的夹具设计为例进行详细说明。
一、典型机床夹具设计的步骤:1、确定加工要求:首先根据产品的加工要求确定夹具的使用条件,包括工件的形状、尺寸和材料等方面的要求。
2、选择夹具类型:根据加工要求选择合适的夹具类型,例如,对于平面加工,通常可以选择钳工钳或万能钳等;对于多工序加工,可以选择支承式夹具或分度式夹具等。
3、进行夹具结构设计:基于夹具类型和加工要求,进行夹具的结构设计。
夹具结构设计的关键点包括夹紧方式的选择、定位方式的选择和夹紧行程的设计等。
4、进行夹具零件设计:根据夹具的结构设计将其分解为各个零件,并对各个夹具零件进行详细设计。
夹具零件设计的要求包括零件的强度、刚度和耐磨性等方面。
5、进行夹具装配设计:根据夹具零件设计的结果对夹具进行装配设计,包括各个零件的位置和安装方式等。
工制造。
加工工艺的选择和机械设备的使用对夹具的加工质量和加工效率都有影响。
7、进行夹具试用和调整:在夹具制造完成后,对夹具进行试用和调整。
通过试用和调整可以获得夹具的工作性能和使用效果等信息。
二、五轴加工中心夹具设计的实例分析:五轴加工中心用于加工一种具有复杂曲面的零件,加工要求为高精度、高效率和高稳定性。
根据加工要求,选择采用分度式夹具。
具体步骤如下:1、确定加工要求:产品要求加工精度达到0.02mm,加工速度达到60m/min。
2、选择夹具类型:根据加工要求选择分度式夹具,该夹具可以实现对产品进行分度加工,满足产品的加工精度要求。
3、进行夹具结构设计:夹具结构设计应包括基座、夹紧装置、定位装置和支撑装置等。
其中,基座用于将夹具固定在加工中心上,夹紧装置用于固定工件,定位装置用于确定工件在加工中心上的位置,支撑装置用于支撑和稳定工件。
机床夹具设计步骤
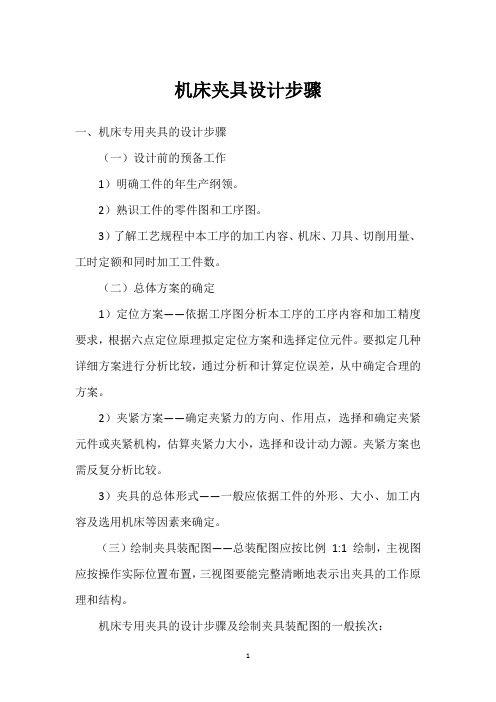
机床夹具设计步骤
一、机床专用夹具的设计步骤
(一)设计前的预备工作
1)明确工件的年生产纲领。
2)熟识工件的零件图和工序图。
3)了解工艺规程中本工序的加工内容、机床、刀具、切削用量、工时定额和同时加工工件数。
(二)总体方案的确定
1)定位方案——依据工序图分析本工序的工序内容和加工精度要求,根据六点定位原理拟定定位方案和选择定位元件。
要拟定几种详细方案进行分析比较,通过分析和计算定位误差,从中确定合理的方案。
2)夹紧方案——确定夹紧力的方向、作用点,选择和确定夹紧元件或夹紧机构,估算夹紧力大小,选择和设计动力源。
夹紧方案也需反复分析比较。
3)夹具的总体形式——一般应依据工件的外形、大小、加工内容及选用机床等因素来确定。
(三)绘制夹具装配图——总装配图应按比例1:1 绘制,主视图应按操作实际位置布置,三视图要能完整清晰地表示出夹具的工作原理和结构。
机床专用夹具的设计步骤及绘制夹具装配图的一般挨次:
(四)绘制夹具零件图
装配图中的非标准零件均应绘制零件图,视图尽可能与装配图上的位置全都,尺寸及公差、形位公差、协作精度及表面粗糙度等要标注完整。
二、夹具精度的验算
1)工件在夹具中的定位误差和夹紧误差。
2)夹具在机床上的对定误差。
3)加工过程中的其他误差。
夹具设计方法及步骤

夹具设计方法及步骤一、设计前的准备工作1.生产纲领;(中批生产)--手动专用夹具2.零件图及工序图;(工艺卡上的工序简图)3.工序内容;(1)工序的具体内容(2)工序的精度要求(3)已加工的表面二、夹具总体方案的确定1.定位方案根椐定位基准面的形状与尺寸,首先选用标准定位元件,若无合适的,可参照标准定位元件自行设计。
(参考夹具设计手册)2.夹紧方案首先选用典型的夹紧机构,若无合适的,可参照典型的夹紧机构自行设计。
(参考夹具设计手册)3.夹具的型式在满足要求的前提下,选用的标准件越多越好,夹具越简单越好。
例:车床支架三、夹具装配草图的绘制1.绘制工件图:在可能的情况下,应该按1:1的比例绘出工件的三面投影图。
线型用细的双点划线,表示工件的假想位置。
工件应该是“透明”的,不遮挡夹具有关部分。
同时工件图只需绘出外形轮廓,以及与定位、夹紧有关部分,其他细部均可略去。
2.绘制定位元件:在绘制好工件轮廓图后,就可以按预定的定位方案,选用合适的标准定位元件,或是设计特殊定位元件,并合理布置,绘制成图。
3. 绘制导向元件及其他元件:画好定位元件后,便可进行导向元件、对刀元件、分度元件及有关装置的设计及绘图。
钻套与工件间距离:钢h =(0.7∼1.5)d铁h =(0.6∼0.7)d4. 设计夹紧机构:根据确定的夹紧方案,参考有关资料,按照夹紧力的大小,决定夹紧机构的尺寸及具体结构。
5. 绘制夹具体:当夹具的有关元件、机构、装置设计好了之后,最后用夹具体把它们联接起来,形成一个有机的整体。
夹具体有铸造及焊结两大类。
四、绘制夹具的装配图及零件图夹具草图画好后,应该经过审定修改,然后便可绘制正式的装配图,并拆出零件图。
在夹具装配图上,应该标注下列尺寸、偏差及配合。
1.轮廓尺寸,及夹具的长、宽、高尺寸。
2.配合尺寸及配合种类。
夹具上有配合要求的部位,均应标注其公称尺寸及配合种类。
3.联系尺寸及偏差。
夹具上各个定位元件之间,定位元件与导向元件、对刀元件、定向键之间,各导向元件之间等等,一般都有严格的尺寸要求,应该标注出它们的尺寸及偏差。
- 1、下载文档前请自行甄别文档内容的完整性,平台不提供额外的编辑、内容补充、找答案等附加服务。
- 2、"仅部分预览"的文档,不可在线预览部分如存在完整性等问题,可反馈申请退款(可完整预览的文档不适用该条件!)。
- 3、如文档侵犯您的权益,请联系客服反馈,我们会尽快为您处理(人工客服工作时间:9:00-18:30)。
第2节机床夹具设计实例一、钻夹具的设计实例图2-2-20所示为杠杆类零件图样。
图2-2-21所示为本零件工序图。
1.零件本工序的加工要求分析①钻、扩、铰φ10H9孔及φ11孔。
②φ10H9孔与φ28H7孔的距离为(80±0.2)mm;平行度为0.3mm。
③φ11孔与φ28H7孔的距离为(15±0.25)mm。
④φ11孔与端面K距离为14mm。
本工序前已加工的表面如下。
①φ28H7孔及两端面。
②φ10H9两端面。
本工序使用机床为Z5125立钻,刀具为通用标准工具。
2.确定夹具类型本工序所加工两孔(φ10H9和φ11),位于互成90°的两平面内,孔径不大,工件质量较小、轮廓尺寸以及生产量不是很大,因此采用翻转式钻模。
3.拟定定位方案和选择定位元件(1)定位方案。
根据工件结构特点,其定位方案如下。
①以φ28H7孔及一组合面(端面K 和φ10H9一端面组合而成)为定位面,以φ10H9孔端外缘毛坯面一侧为防转定位面,限制六个自由度。
这一定位方案,由于尺寸885.00+mm 公差大,定位不可靠,会引起较大的定位误差。
如图2-2-22(a)所示。
②以孔φ28H7孔及端面K 定位,以φ11孔外缘毛坯一侧为防转定位面,限制工件六个自由度。
为增加刚性,在φ10H9的端面增设一辅助支承,如图2-2-22 (b)所示。
比较上述两种定位方案,初步确定选用图2-2-22(b)所示的方案。
(2)选择定位元件。
①选择带台阶面的定位销,作为以φ28H7孔及其端面的定位元件,如图2-2-23所示。
定位副配合取6728g H φ。
②选择可调支承钉为φ11孔外缘毛坯一侧防转定位面的定位元件,如图2-2-24(a)所示。
也可选择如图2-2-24 (b)所示移动V形块。
考虑结构简单,现选用图2-2-24(a)所示结构。
(3)定位误差计算①加工φ10H9孔时孔距尺寸(80±0.2)mm的定位误差计算。
由于基准重合,故ΔB=0。
基准位移误差为定位孔(φ38021.00+mm)与定位销(φ38007.0002.0--mm)的最大间隙,故ΔY =(0.021+0. 007+0.013)mm =0.041rnm 。
由此可知此定位方案能满足尺寸(80±0.2)mm 的定位要求。
②加工φ10H9孔时轴线平行度0.3mm 的定位误差计算。
由于基准重合,故ΔB =0。
基准位移误差是定位孔φ28H7与定位面K 间的垂直度误差。
故ΔY =0. 03mm 。
此方案能满足平行度0. 3mm 的定位要求。
③加工φ11孔时孔距尺寸(15±0.25)mm 。
加工φ11孔时与加工φ10H9孔时相同。
此方案能满足孔距(15±0.25) mm 的定位要求。
4.确定夹紧方案参考夹具资料,采用M12螺杆在φ28H7孔上端面夹紧工件。
5.确定引导元件(钻套的类型及结构尺寸) ⑴对φH9孔,为适应钻、铰选用快换钻套。
主要尺寸由《机床夹具零、部件》国家标准GB/T2263-80, GB/T2265-80选取。
钻孔时钻套内径φ10028.0013.0++mm 、外径φ15012.0001.0++mm ;衬套内径φ15034.0014.0++mm ,衬套外径φ22028.0015.0++mm 。
钻套端面至加工面的距离取8mm 。
麻花钻选用φ9. 80022.0-mm 。
(2)对φ11孔,钻套采用快换钻套。
钻孔时钻套内径φ11034.0016.0++mm 、外径φ18012.0001.0++mm ,衬套内径φ18034.0016.0++mm ,外径φ26028.0015.0++mm ;钻套端面至加工面间的距离取12mm 。
麻花钻选用φ10. 80027.0-mm 。
各引导元件至定位元件间的位置尺寸分别为(15±0.03)mm 和(18±0. 05)mm ,各钻套轴线对基面的直线度允差为0.02mm 。
6.夹具精度分析与计算由图2-2-22可知,所设计夹具需保证的加工要求有:尺寸(15±0.25)mm ;尺寸(80±0.2)mm ;尺寸14mm 及φ10H9孔和φ28H7孔轴线间平行度允差0.3mm 等四项。
除尺寸14mm ,因精度要求较低不必进行验算外,其余三项精度分别验算如下。
(1)尺寸(80±0.2)mm 的精度校核。
定位误差ΔD ,由前已计算,已知Δ=0.041mm 。
定位元件对底面的垂直度误差ΔA =0.03mm 。
钻套与衬套间的最大配合间隙ΔT1=0. 033mm 。
衬套孔的距离公差ΔT2=0.1mm 。
麻花钻与钻套内孔的间隙X 2=0.050mm 。
衬套轴线对底面(F)的垂直度误差ΔT3=0. 05mm 。
因而该夹具能保证尺寸(80±0. 2)mm 的加工要求。
(2)尺寸(15±0. 25)mm 的精度校核。
ΔD =0. 041mm ,ΔA =0. 03mm ,ΔT1=0. 033mm 。
衬套孔与定位元件的距离误差ΔT2=0.06mm 。
麻花钻与钻套内孔的间隙X =0.061mm 。
因而尺寸(15±0.25)mm 能够保证。
(3)φ10H9轴线对φ25H7轴线的平行度0.3mm 的精度校核。
ΔD =0. 03mm ,ΔA =0. 03mm 。
衬套对底面(F)的垂直度误差ΔT =0. 05mm 。
因而此夹具能保证两孔轴线的平行度要求。
7.绘制夹具总图根据已完成的夹具结构草图,进一步修改结构,完善视图后,绘制正式夹具总装图,如图2-2-23所示。
8.绘制夹具零件图样 从略。
9.编写设计说明书 从略。
二、铣床夹具设计实例图2-2-25所示为轴套类零件的零件图样。
现需设计铣两槽52.00+mm 的铣夹具。
1.零件本工序的加工要求分析本工序的加工要求,在实体上铣出两通槽,槽宽为52.00+mm ,槽深为2703.0-mm ,两槽在圆周方向互成60°±30′角度,表面粗糙度为Ra1. 25μm 。
本工序之前,外圆φ60021.0002.0++mm 、内孔φ32039.00+mm 及两端面均已加工完毕。
本工序采用φ5mm 标准键槽铣刀在X5l 立式铣床上,一次装夹六件进行加工。
2.确定夹具类型本工序所加工的是两条在圆周互成60°角的纵向槽,因此宜采用直线进给带分度装置的铣夹具。
3.拟定定位方案和选择定位元件 (1)定位方案。
①以φ32039.00+mm 内孔作为定位基准,再选孔端面为定位基准,限制工件五个自由度。
如图2-2-26(a)所示。
②以φ60021.0002.0++mm 外圆为定位基准 (以长V 形块为定位元件),限制4个自由度。
如图2-2-26 (b)所示。
方案②由于V 形块的特性,所以较易保证槽的对称度要求,但对于实现多件夹紧和分度较困难。
方案①的不足之处是由于心轴与孔之间有间隙、不易保证槽的对称度,且有过定位现象。
但本工序加工要求井不高,而工件孔和两端面垂直精度又较高,故过定位现象影响不大。
经上述分析比较,确定采用方案①。
(2)选择定位元件。
根据定位方式,采用带台肩的心轴。
心轴安装工件部分的直径为φ32g6(009.0025.0--)mm ,考虑同时安装6个工件,所以这部分长度取112mm ,由于分度精度不高,为简化结构,在心轴上做出六方头,其相对两面间的距离尺寸取28g6(007.0020.0+-)mm ,与固定在支座上的卡块槽28H7(021.00+)mm 相配合;加工完毕一个槽后,松开并取下心轴,转过相邻的一面再嵌入卡块槽内即实现分度。
心轴通过两端φ25H6mm 柱部分安装在支座的V 形槽上,并通过M16螺栓钩形压板及锥面压紧,压紧力的方向与心轴轴线成45°角。
(3)定位误差计算。
工序尺寸2705.0-mm 定位误差分析如下。
由于基准重合ΔB =0由于定位孔与心轴为任意边接触,则因此定位精度足够。
由于加工要求不高,其他精度可不必计算。
4.确定夹紧方案根据图2-2-26所示心轴结构,用M30螺母把工件轴向夹紧在心轴上。
心轴的具体结构如图2-2-27所示。
5.确定对刀装置 (1)根据加工要求,采用GB/T2242-80直角对刀块;塞尺符合GB/T2244-80,基本尺寸及偏差20014.0-mm 。
(2)计算对刀尺寸H 和B 如图2-2-28所示,计算时应把尺寸化为双向对称偏差,即6.夹具精度分析和计算本夹具总图上与工件加工精度直接有关的技术要求如下。
定位心轴表面尺寸φ32g6。
定位件与对刀间的位置尺寸(24.75±0.08)mm ,(4.575±0.05)mm 。
定位心轴安装表面尺寸φ25h6。
对刀塞尺厚度尺寸20014.0-mm 。
分度角度60°±10′。
定位心轴轴线与夹具安装面、定位键侧平面间的平行度公差为0. lmm。
分度装置工作表面对定位表面的对称度公差为0. 07mm。
分度装置工作表面对夹具安装面垂直度公差为0.07mm。
对刀装置工作表面对夹具安装面的平行度和垂直度公差为0. 07mm。
mm的精度分析。
(1)尺寸2705.0-ΔD=0. 064mm(定位误差前已计算)。
ΔT=0. 16mm(定位件至对刀块间的尺寸公差)。
1.0×20mm=0.0086mm(定位心轴轴线与夹具底面平行度公差对工件尺寸的影ΔA=233响)。
mm尺寸。
故此夹具能保证2705.0-(2)对60°±30′的精度分析。
分度装置的转角误差可按下式计算。
故此分度装置能满足加工精度要求。
7.绘制夹具总图图2-2-27所示为本夹具的总装图样。
8.绘制夹具零件图样从略。
9.编写设计说明书从略。