轻压下技术在高碳钢方坯连铸生产应用中的参数选取
轻压下技术在连铸中的应用及研究
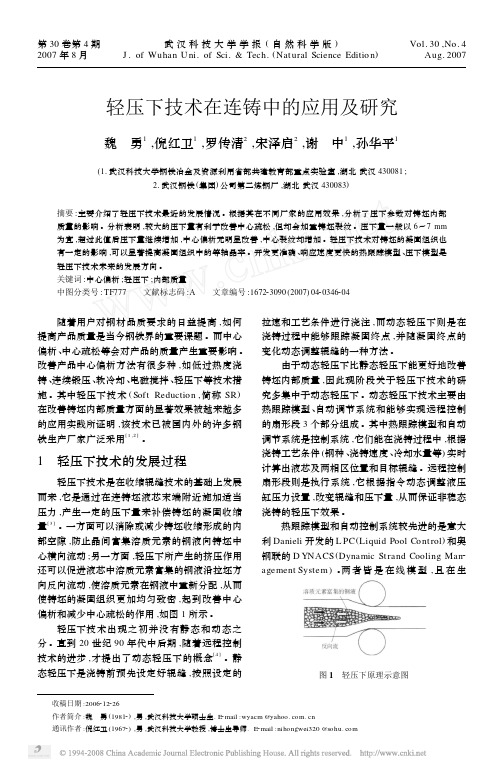
T H EMAL TRAC KIN G[6 ] ,它们也能模拟连铸过 好[8 ,9 ] 。
程中的非稳态情况 ,实时地给出液相穴末端位置 和液相穴的形状 ,但只是离线模型 。
2 轻压下技术的应用效果
扇形段技术最先进的是奥钢联的 SMA R T
轻压下技术在板坯连铸中应用非常普遍 ,在
扇形段和西马克公司的 Cyberlink 扇形段 。其中 方坯连铸中特别是大方坯连铸中的应用也得到了
由于动态轻压下比静态轻压下能更好地改善 铸坯内部质量 ,因此现阶段关于轻压下技术的研 究多集中于动态轻压下 。动态轻压下技术主要由 热跟踪模型 、自动调节系统和能够实现远程控制 的扇形段 3 个部分组成 。其中热跟踪模型和自动 调节系统是控制系统 ,它们能在浇铸过程中 ,根据 浇铸工艺条件 (钢种 、浇铸速度 、冷却水量等) 实时 计算出液芯及两相区位置和目标辊缝 。远程控制 扇形段则是执行系统 ,它根据指令动态调整液压 缸压力设置 ,改变辊缝和压下量 ,从而保证非稳态 浇铸的轻压下效果 。
1 轻压下技术的发展过程
轻压下技术是在收缩辊缝技术的基础上发展 而来 ,它是通过在连铸坯液芯末端附近施加适当 压力 ,产生一定的压下量来补偿铸坯的凝固收缩 量[3] 。一方面可以消除或减少铸坯收缩形成的内 部空隙 ,防止晶间富集溶质元素的钢液向铸坯中 心横向流动 ;另一方面 ,轻压下所产生的挤压作用 还可以促进液芯中溶质元素富集的钢液沿拉坯方 向反向流动 ,使溶质元素在钢液中重新分配 ,从而 使铸坯的凝固组织更加均匀致密 ,起到改善中心 偏析和减少中心疏松的作用 ,如图 1 所示 。
轻压下 技 术 出 现 之 初 并 没 有 静 态 和 动 态 之 分 。直到 20 世纪 90 年代中后期 ,随着远程控制 技术的进步 ,才提出了动态轻压下的概念[4] 。静 态轻压下是浇铸前预先设定好辊缝 ,按照设定的
连铸方坯动态轻压下位置

连铸方坯动态轻压下位置张松;杨彦宏【摘要】为准确确定铸坯凝固末端的位置,合理选择压下区域,为实施动态轻压下提供有效技术手段,利用数值模拟方法计算某炼钢厂2#铸机连铸方坯中温度场,用传热模型分析了45#钢在某工艺下的铸坯温度分布图.固相率0.3为轻压下初始点,压下区间总长度为10 m且拉速0.76 m/min时的压下量为0.7 mm/m.【期刊名称】《辽宁科技大学学报》【年(卷),期】2010(033)002【总页数】4页(P132-135)【关键词】连铸方坯;温度场;动态轻压下【作者】张松;杨彦宏【作者单位】辽宁科技大学,材料科学与冶金学院,辽宁,鞍山,114051;辽宁科技大学,机械工程与自动化学院,辽宁,鞍山,114051【正文语种】中文【中图分类】TF777在连铸生产中,板坯内部一般都会存在中心偏析、中心疏松及内裂等缺陷,影响了铸坯内部质量。
抑制内部缺陷问题最有效且经济的方法是采用轻压下技术[1]。
凝固末端的轻压下技术始于20世纪70年代末,是在辊缝收缩的基础上发展起来的。
在铸坯凝固末端,对铸坯施以2%-3%的压下量,以阻止凝固末端富集偏析元素的钢液向下流动,减少中心偏析[2]。
动态轻压下技术已成为现代连铸机关键技术的重要组成部分[3]。
在铸坯凝固过程中,坯壳至中心分为固态、固-液态、液-固态和液态四个区域。
由于选分结晶,在铸坯凝固末端的残余液相中含有的溶质浓度很高,当这些残余液相在铸坯中心部位凝固时,会产生很严重的中心偏析[4]。
在铸坯凝固过程中,如果柱状晶发达,会在凝固末端形成“搭桥”,阻碍上游钢液向下游动,凝固末端的残余液相不能被上游溶质浓度低的钢液稀释,就会在铸坯中心形成一条偏析带。
同时,残余液相在凝固末端急速凝固时,会急剧收缩,产生缝隙,如不能得到钢液的补充,就会产生疏松[5]。
轻压下的目的,就是要通过机械压下来补偿铸坯凝固后期体收缩,抑制枝晶间浓化钢水向中心富集,减轻或焊和中心疏松,减轻中心偏析。
试析炼钢—精炼—连铸工艺生产高碳钢的质量控制
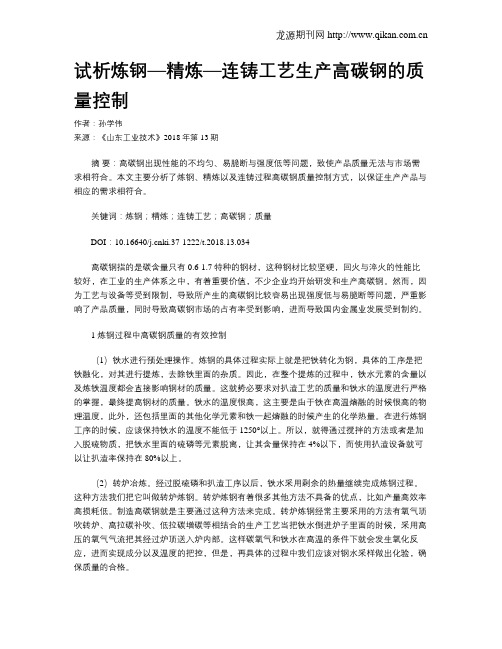
试析炼钢—精炼—连铸工艺生产高碳钢的质量控制作者:孙学伟来源:《山东工业技术》2018年第13期摘要:高碳钢出现性能的不均匀、易脆断与强度低等问题,致使产品质量无法与市场需求相符合。
本文主要分析了炼钢、精炼以及连铸过程高碳钢质量控制方式,以保证生产产品与相应的需求相符合。
关键词:炼钢;精炼;连铸工艺;高碳钢;质量DOI:10.16640/ki.37-1222/t.2018.13.034高碳钢指的是碳含量只有0.6-1.7特种的钢材,这种钢材比较坚硬,回火与淬火的性能比较好,在工业的生产体系之中,有着重要价值,不少企业均开始研发和生产高碳钢。
然而,因为工艺与设备等受到限制,导致所产生的高碳钢比较容易出现强度低与易脆断等问题,严重影响了产品质量,同时导致高碳钢市场的占有率受到影响,进而导致国内金属业发展受到制约。
1 炼钢过程中高碳钢质量的有效控制(1)铁水进行预处理操作。
炼钢的具体过程实际上就是把铁转化为钢,具体的工序是把铁融化,对其进行提炼,去除铁里面的杂质。
因此,在整个提炼的过程中,铁水元素的含量以及炼铁温度都会直接影响钢材的质量。
这就势必要求对扒渣工艺的质量和铁水的温度进行严格的掌握,最终提高钢材的质量。
铁水的温度很高,这主要是由于铁在高温熔融的时候很高的物理温度,此外,还包括里面的其他化学元素和铁一起熔融的时候产生的化学热量。
在进行炼钢工序的时候,应该保持铁水的温度不能低于1250°以上。
所以,就得通过搅拌的方法或者是加入脱硫物质,把铁水里面的硫磷等元素脱离,让其含量保持在4%以下,而使用扒渣设备就可以让扒渣率保持在80%以上。
(2)转炉冶炼。
经过脱硫磷和扒渣工序以后,铁水采用剩余的热量继续完成炼钢过程。
这种方法我们把它叫做转炉炼钢。
转炉炼钢有着很多其他方法不具备的优点,比如产量高效率高损耗低。
制造高碳钢就是主要通过这种方法来完成。
转炉炼钢经常主要采用的方法有氧气顶吹转炉、高拉碳补吹、低拉碳增碳等相结合的生产工艺当把铁水倒进炉子里面的时候,采用高压的氧气气流把其经过炉顶送入炉内部。
高碳钢连铸方坯质量控制

高碳钢连铸方坯质量控制蔡开科1.前言高碳钢制品入钢轨,硬线,钢丝等广泛应用于国民经济各个部门。
对高碳钢制品要求是:抗拉强度高,可承载较重的震动载荷承载能力大,使用安全可靠在高速条件下工作,运转平稳有良好的抗压性,耐磨性,耐腐蚀性等目前高碳钢生产有两件工艺:BOF(EAF)-LF(VD)-bloom大方坯BOF(EAF)-LF-Billet小方坯不管那种工艺,为获得高质量的产品,必须得到高质量的连铸坯。
(1)高的洁净度,非金属夹杂物类型,数量,尺寸分布如表1表1 洁净度要求硬线钢由于夹杂易造成的冷拔断裂如图1图1 夹杂物所致冷拔断裂重轨钢,滚珠钢由于脆性夹杂产生疲劳裂纹而断裂(2)铸坯良好的低倍结构要紧是指中心缺陷(锻孔,疏松,中心偏析)。
硬线钢的杯锥状断裂(图2)是由中心偏析所致图2 杯锥状断口硬线钢劈裂状断口(图3)要紧是由中心疏松缩孔引起的。
图3 劈裂状断口重轨钢由于中心偏析(C.S)而产生轨腰的断裂(图4)图4 钢轨形貌2.铸坯中夹杂物操纵当钢水凝固成固体后,铸坯中夹杂物数量就无法改变了。
因此铸坯中夹杂物决定于炼钢-精炼-连铸的全过程。
炼钢是一个氧化过程,钢中夹杂物可用总氧T[O]来评判:T[O] = [O]D + [O]I出钢时:钢水中[O]I→O T[O] = [O]D=a[O]脱氧合金化后:[O]D(a[O])→O T[O] = [O]I由此,可用总氧T[O]来表示钢的洁净度,也确实是夹杂物水平。
为使钢中夹杂物少,必须操纵钢T[O],为此(1)降低[O]D,转炉终点a[O](2)降低[O]I,脱氧(夹杂物工程),精炼(3)防止钢水再污染:连铸过程2.1转炉终点氧操纵转炉终点a[O]是产生夹杂物的源头。
重点a[O]决定于:[C]终渣中(FeO)钢水温度图5 转炉终点钢中[C]与a[O]关系关于中高碳钢转炉终点操纵方法:低拉碳增碳法高拉碳补吹法两种方法结果比较于表2表2 低拉碳与高拉碳结果比较由表可知高拉碳法特点:增C量小,成品C波动小终点a[O]低对铁水S,P要求研低拉碳法特点:对铁水S,P要求可放宽些有利于脱S,P终点a[O]高增C量大,碳粉收得率不稳,成品C波动在±0.05%以上两种方法各有优缺点,各厂依照具体条件决定采纳哪种方法。
连铸坯动态轻压下的压下参数分析

第3卷第4期材 料 与 冶 金 学 报V o l .3N o .4 收稿日期:2004-06-18. 作者简介:林启勇(1980-),男,重庆梁平人,硕士研究生,E -m a i l :s y q i y o n g@s i n a .c o m ;朱苗勇(1965-),男,浙江诸暨人,东北大学教授,博士生导师.2004年12月J o u r n a l o fM a t e r i a l s a n d M e t a l l u r g yD e c .2004连铸坯动态轻压下的压下参数分析林启勇,蒋欢杰,朱苗勇(东北大学 材料与冶金学院,辽宁沈阳110004)摘 要:简述了连铸坯动态轻压下技术,介绍了该技术的关键工艺参数即压下区间、压下量和压下速率。
通过对近年来国内外对压下模型研究结果的分析和讨论,预测了动态轻压下压下模型的研究方向.关键词:连铸;中心偏析;轻压下;压下参数中图分类号:T F777 文献标识码:A 文章编号:1671-6620(2004)04-0261-05A n a l y s i s o f r e d u c t i o n p a r a m e t e r s o f d yn a m i c s o f t r e d u c t i o n i n c o n t i n u o u s c a s t i n gL I N Q i -y o n g ,J I A N G H u a n -j i e ,Z HU M i a o -y o n g(S c h o o l o fM a t e r i a l s a n d M e t a l l u r g y ,N o r t h e a s t e r nU n i v e r s i t y ,S h e n y a n g 110004,C h i n a )A b s t r a c t :T h e d y n a m i c s o f t r e d u c t i o n t e c h n o l o g y a n d t h e k e y t e c h n i c a l p a r a m e t e r s o f s o f t r e d u c t i o n f o r c o n t i n u o u s c a s t i n g w e r e p r e s e n t e di nt h i s p a p e r .B y r e v i e w i n g a n da n a l y z i n g t h ev a r i a b l e s ,t h es o f t r e d u c t i o n m o d e l sa c h i e v e di n r e c e n t y e a r s ,t h et r e n df o ri n v e s t i g a t i n g t h er e d u c t i o n m o d e l w a s d i s c u s s e d .K e y wo r d s :c o n t i n u o u s c a s t i n g ;c e n t e r s e g r e g a t i o n ;s o f t r e d u c t i o n ;r e d u c t i o n p a r a m e t e r s 中心偏析和疏松是连铸坯的主要缺陷之一,它严重影响了钢材的性能,如焊接性能、拉拔性能.铸坯轻压下就是针对消除该缺陷的一种新技术,如图1所示.其机理为[1]:在连铸坯液芯末端附近施加压力产生一定的压下量来补偿铸坯的凝固收缩量.轻压下一方面可以消除或减少铸坯收缩形成的内部空隙,防止晶间富集溶质元素的钢液向铸坯中心横向流动;另一方面,轻压下所产生的挤压作用可促进钢液中的溶质元素进行重新分配,从而使铸坯的凝固组织更加均匀致密,起到改善中心偏析和减少中心疏松的作用.在实际生产过程中,浇铸速度和浇铸温度等条件的不稳定会引起凝固末端位置的变化,轻压下位置也随之改变.随着控制和液压技术的发展和应用,实现了跟踪凝固末端进行适时轻压下,即所谓的动态轻压下.图1 辊式轻压下示意图F i g .1 S c h e m a t i cd i a g r a mo f s o f t r e d u c t i o nb y r o I I i n g动态轻压下技术的主要工艺参数有压下区间、压下量和压下速率.只有合理确定这些参数值才能达到消除或减少铸坯中心偏析与疏松的目的.对此,已有大量的研究报道.本文将对有代表性的最新研究进行评述与分析.1 压下区间对压下区间的研究已经多年,目前一致认为,中心偏析和疏松发生在凝固末端的液固两相区内[2].凝固末端两相区如图2所示.在液相线温度(固相率f s =0)和固相线温度(f s =1)之间的区域为两相区.图2 凝固末端两相区示意图F i g .2 S c h e m a t i cd i a g r a mo fm u s h y zo n e i n t h ee n do f s o I i d i f i c a t i o n由图2可知,从f s =0到f s =1处,钢液中杂质元素含量越来越大.q 2区内的凝固收缩可以通过左端非浓化钢液的流动来补偿;q 1区内的凝固收缩时得到q 2区内的浓化钢液的补充.由于相邻柱状晶的二次晶臂开始并完成相互联结,补充钢液较困难.在p 区内残余浓缩钢液被枝晶网封闭起来,凝固收缩时将得不到前沿钢液的补充.因此,q 2区流动将不会造成中心偏析的形成,反而均匀了该区内的溶质分布;q 1区的收缩则将导致富集杂质元素钢液的集中,从而促进中心偏析的形成.p 区的凝固收缩因没有钢液的补充将形成疏松.T a k a h a s h i 和S u z u k i [3]等的研究指出q 1和q 2相分界处的固相率为0.3~0.4,而q 1和p 分界处的固相率为0.6~0.7,因此,最佳轻压下实施区间应在铸坯中心固相率0.3~0.7的位置(图2中的q 1区).但钢种不同,所要求的固相率也不同.一般来说,中碳钢为0.3~0.7;高碳钢为0.4~0.7.按美国专利4687047所述,铸坯实行轻压下的适宜部位,相当于从铸坯中心固相率为0.1~0.3之间到铸坯中心固相率达到流动极限固相率f s c (f s c 是指钢液达到流动极限时的固相率,一般的经验,普通碳素钢的f s c =0.6,低合金钢的f s c=0.65~0.75)之间的一段铸坯,当f s >f s c 时,钢液粘性很大,基本不会流动,若此时进行压下,很可能对内部质量产生有害影响.从生产实践来看,济南钢铁公司新引进奥钢联的新中厚板坯在压下区间为0.5~0.95,铸坯质量良好[4].芬兰的R a u t a r u u k k i 钢铁公司6号板坯上进行生产试验[5],钢种为w [C ]=0.088%的微合金钢,得出在浇铸210m m×(1250~1475)m m 尺寸时的最佳压下区间为0.3~0.9;在浇铸尺寸为210m m×1825m m 的最佳压下区间为0.15~0.8.台湾省中钢的大方坯连铸机生产表明,在0.55~0.75的区域进行压下能取得很好的效果[6].韩国浦项对S 82尺寸为250m m×330m m 的方坯实施压下的压下位置为f s =0.3~0.7的区域[7].对于压下区间目前没有一个定值,一般企业都是根据试验修正后取得最佳值.很显然该值和钢的成分、铸坯断面及生产设备有关.从生产实践得出的数据可以看出,板坯比大方坯的压下区间大,而且开始压下(f s 值大时开始,值小时结束)所对应的f s 值比方坯要大.这是由于p 区间如果也能轻微压下,则可以减少因凝固时未能得到补充的凝固收缩所形成的中心疏松.板坯的窄边坯壳较薄,温度较高,变形抗力较小,易实现轻压下;而方坯压下时坯壳较厚,温度较低,变形抗力大,压下难以实现.2 压下量与压下速率压下量要完全补偿压下区间内钢液在凝固过程中的体积收缩量,才能防止富集溶质钢液的流动.但是压下量过大会使铸坯内部产生裂纹,并使轻压下区夹辊受损.压下量过小,对中心偏析和疏松改善不明显.压下量大小必须满足三个要求:①能够补偿压下区间内的凝固收缩,减少中心偏析和中心疏松;②避免铸坯产生内裂;③压下时产生的反作用力要在铸机扇形段许可载荷范围内.压下速率是单位时间的压下量(m m /s ),最佳压下速率应和凝固速率一致,如果压下速率小于凝固速率,压下将不及时,凝固补偿不充分,仍出现中心偏析.同时,压下量对应于应变,压下速率对应于应变率,压下量和压下速率过大,将会导致铸坯的应变和应变率过大,一旦超过其许可范围就会形成裂纹.目前主要从铸坯高温物性、压下效率、压下量和压下速率等几方面开展研究.262材料与冶金学报 第3卷2.1铸坯高温物性铸坯高温物性包括随温度变化的弹性模量E、塑性模量、屈服极限σs、瞬时热膨胀系数α,以及铸坯在不同温度和变形条件下的临界应变值和临界应力值.它们是计算铸坯轻压下过程中位移、应力应变及判定内裂纹形成的基础.铸坯的受力来自两个方面:由自身温度不均匀产生的热应力和外加载荷产生的机械力.热应力的计算关键要了解铸坯在不同温度下的瞬时膨胀系数.只有明确了铸坯随温度变化的弹性模量和与温度和应变率相关的屈服应力,才能进行铸坯的应力应变计算.瞬时膨胀系数主要和含碳量有关,由实验测定.文献[8]中给出了在w[C]= 0.1%(参考温度t r e f=1495℃)和w[C]=0.7%(参考温度tr e f=1406℃)时的膨胀系数,如图3所示.图3碳质量分数为0.1%和0.7%时的平均热膨胀系数F i g.3T h e r m a I e x p a n s i v i t y v s t e m p e r a t u r ef o r0.1p c t a n d0.7p c t c a r b o n s t e e I s由图3可以看出,w[C]=0.1%的钢在发生包晶相变时体积发生明显变化,而w[C]=0.7%的钢的体积变化随温度变化不明显.许多研究者用实验所得数据回归出高温下钢的强度极限σB和弹性模量E随温度和化学成分的变化规律.一般情况下,钢的σB和E是随温度升高而降低的.它们与化学成分和温度t(℃)的关系表示如下[9]:σB=40140+640w[C]2-880w[S i]+170w[M n]-7680w[P]-1260w[S]-25.94t+0.0001726t2k P a(1) E=30230080+4209560w[C]-14120080w[C]2+ 2012890w[S i]-518690w[M n]-1176840w[P]-17064180w[S]-508950t+1.3524k P a(2)以上两式中的w[C]、w[S i]、w[M n]、w[P]、w[S]的单位为%.当铸坯超过弹性变形范围,将发生塑性变形.H a n等研究出了温度和应变率两个变量与应力的本构方程[10]:˙εP=A e x p(-Q/R T)[s i n h(βK)]1/m(3)σ=Kεn P(4)式中A、β、m为常数,εP为有效塑性应变,σ为应力,K为强度系数,n为变形强化系数,Q为变形能,R为摩尔气体常数.该公式和实际塑性变形测量结果很吻合.内裂纹敏感区在Z S T(Z e r o S t r e n g t h T e m p e r a t u r e)和Z D T(Z e r o D u c t i b i l i t y T e m p e r a t u r e)之间[11].在该区域(对应的两相区固相率约为0.99和0.8)内,铸坯的受力或变形超过一定程度时,将会产生内裂纹[12].常用临界应变作为裂纹形成的判据.不少学者研究了临界应变和一些相关变量(成分、应变率等)的关系[13].应变率和临界应变的关系如图4所示[12],临界应变和含碳量的关系如图5所示[14].图4应变率和临界应变的关系F i g.4I n f I u e n c e s o f s t r a i na n d s t r a i n r a t eo n f o r m a t i o no f i n t e r n a I c r a c k s从图4可以看出,对同一钢种质量分数分别为:C0.15%,M n0.6%,P0.02%,S0.012%)进行不同应变率实验,可以看出应变率越小,临界应变值越大,这可能与钢的变形太慢发生高温蠕变效应有关;随着应变率的增大,临界应变值急剧下降;当应变率下降到约3×10-4/s时,临界应变变化很小.图5中虚线为理论计算值[14],其余为实验值[13].可以看出,在w[C]=0~0.1%和0.17%~0.65%之间,临界应变是下降的;当w[C]=0.1%~0.17%之间,临界应变上升,这可能与发生包晶相变有关.2.2压下效率为了更好地确定压下量,使铸坯内部液芯的压缩量能满足凝固的收缩量,解决铸坯表面的压362第4期林启勇等:连铸坯动态轻压下的压下参数分析图5 含碳量和临界应变关系的计算值与实验值(在应变率为5×10-4/s 时)F i g.5 T h ec a I c u I a t e dc r i t i c a I s t r a i na s a f u n c t i o n o f c a r b o n c o n t e n t a t t h es t r a i n r a t eo f 5×10-4/s a I o n g wi t h t h em e a s u r e d f r a c t u r es t r a i n 下量不能全部传递到内部凝固末端的问题,提出压下效率概念,即:η=液芯厚度的减少量铸坯表面压下量(5)I t o 等[15]经过对不同形状的铸坯的轻压下试验,拟合出压下效率公式:η=e x p (2.36λ+3.73)×(R 420)0.587(6)式中R 为压下辊辊径,λ为铸坯形状指数.2.3 压下量和压下速率Y o k o y a m a [16]等对钢液凝固时的体积收缩率进行了研究,得出体积收缩率为4%.Z e z e [17]等人对液芯厚度与压下量、压下速率与压下量的相互作用对铸坯的质量的影响作了系统的实验研究,图6和图7是他们的研究结果.由图6可以看出,在压下量减少时,由于凝固收缩得不到充分补偿,仍有残存V 偏析.随着压下量增加,V 偏析不断减少.液芯厚度越大,所需压下量越大.当压下量大时,发生白亮带负偏析和逆V 偏析.当压下量过大时,将产生裂纹.同时可以看出液芯厚度过大(对应位置的两相区固相率很小或在液相区),压下已不起消除V 偏析作用,反而形成内部裂纹.由图7可知,在压下速率小于0.02m m /s 时,无论怎么增加压下量,也不能防止V 偏析,这是因为压下速率小于凝固收缩速率,来不及充分补充凝固收缩的缘故.同时,由于压下速率的增大导致应变率增加,相应的临界应变变小,从而上临界压下量减少.此外还可以看出,随着压下速率的增加,为防止V 偏析的必要压下量增加,但压下量区间变窄.图6 压下量和液芯厚度对V 偏析的影响(压下速率0.35m m /s)F i g .6 E f f e c t o f r e d u c t i o no nV -s e g r e ga t i o n a t r e d u c t i o n r a t eo f 0.35m m /s图7 压下速率和压下量对V 偏析的影响(液芯厚度32m m )F i g .7 E f f e c t o f r e d u c t i o n r a t eo nV -s e g r e ga t i o n a t I i qu i dc o r e t h i c k n e s s o f 32m m 从实际生产来看,芬兰的R a u t a r u u k k i 钢铁公司[5]在浇铸尺寸为210m m ×(1625~1825)m m 的低合金钢时的最佳压下量为1.5m m ,而且得出在压下率为1.00m m /m 以下,压下不会对铸坯表面质量产生影响.韩国浦项[7](大方坯)发现,随着压下量的增加,中心偏析不断降低,但压下量超过6m m 之后,中心偏析并无进一步改善.铸坯内部裂纹也是随着压下量的增加而增加,但在总压下量低于6m m 时,铸坯内部裂纹极其微小.综合这两方面的因素,合理的总压下量为6m m.具体的压下量和压下速率与钢种、铸坯断面及生产条件有关.462材料与冶金学报 第3卷3存在问题及讨论要很好应用或改进轻压下技术,必须要有相当的技术支持.虽然许多冶金工作者对此已进行了大量研究,但仍需在以下几方面作进一步的研究.3.1宏观偏析形成机理铸坯和钢锭凝固过程中,所有类型的宏观偏析只在固液混合区存在,而不是存在于固液共存区前端.绝大多数情况是因收缩、铸坯的几何形状、固体变形或者重力能引起枝晶间钢液的缓慢流动[2].在某些情况下,它可能是凝固前期固体运动的结果.但是,在实践中仍存在着如何理解宏观偏析和控制宏观偏析的问题.在这方面仍有更深入细致的工作要做.3.2两相区的本构关系钢在固态的应力和应变本构关系研究比较成熟.但对连铸过程中的凝固末端固液共存区(固相率fs从0到1所对应的区域)的应变与应力的关系研究很少.中心裂纹就是在该区域形成的,只有明晰了应力和应变的本构关系,才能精确地计算出凝固前沿的应力和应变,从而有效地控制其在临界范围内,不形成裂纹.3.3临界应力应变测定虽然众多的研究者测定了铸坯的临界应力和应变值,但由于实验方法和条件的差异,结果相差较大.为了能使测得的临界值成为评价裂纹敏感性及预测裂纹的判据,应当统一实验标准.要充分考虑实际连铸工况,尽可能地模拟凝固前沿的组织、温度分布及受力状态,使测得的临界值能够较真实地反映铸坯内裂纹的形成.3.4铸坯内部应力应变计算只有知道铸坯在实际复杂工况下的应力应变值,才能预测裂纹的形成.以前大多用经验或半经验公式进行计算,对铸坯断面和材料性质作了很多假设,这往往会忽略某些特殊而且很关键的局部应力与应变,这就需要用更准确的计算方法.有限元法在这方面有明显优势,以后须用该方法进行数值模拟,得出更准确的铸坯内部应力应变分布.4结语在改善产品中心疏松和偏析的诸多方法之中,动态轻压下技术将会占据重要地位.为了更好地应用和改进该技术,需对如下几个方面作进一步研究:宏观偏析形成的机理;两相区的本构关系;临界应力应变的准确测定;铸坯内部应力应变的计算.参考文献:[1]B y r n e C,T e r c e l l i C.M e c h a n i c a ls o f tr e d u c t i o ni n b i l l e tc a s t i n g[J].S t e e lT i m e sI n t e r n a t i o n a l,2002,26(9):33-35.[2]F l e m i n g sM C.O u r u n d e r s t a n d i n g o fm a c r o s e g r e g a t i o n:p a s ta n d p r e s e n t[J].I S I J i n t e r n a t i o n a l,2000,40(9):833-841.[3]S u z u k i K,T a k a h a s h i K.M e c h a n i c a l p r o p e r t i e s o f t h es l a b b i n g m i l l r o l l m a t e r i a l s a t r o o m a n d e l e v a t e d t e m p e r a t u r e s[J].T r a n s.I r o na n dS t e e l I n s t i t u t eo f J a p a n, 1975,61(3):371-387.[4]赵培建,韩洪龙.轻压下技术在济钢新板坯连铸机上的应用[J].工艺技术,2002,6:11-12.[5]武金波译.板坯动态软压下的最新成果[J].世界钢铁,2001,6:5-7,18.[6]董珍编译.关于高碳大方坯中心偏析的改善[J].冶金译丛,1998,1:44-48.[7]K u y n g S h i k O h.D e v e l o p m e n to f S o f t R e d u c t i o nf o rt h eB l o o mC a s t e ra tP o h a n g W o r k so fP o s c o[J].S t e e l m a k i n gC o n f e r e n c eP r o c e e d i n g,1995:301-308.[8]K e l l y J E,M i c h a l e k K P,O'c o n n o r T G,e ta l.I n i t i a ld e v e l o p m e n t o f t h e r m a l a n d s t r e s s f i e l d s i n c o n t i n u o u s l y c a s ts t e e l b i l l e t s[J].M e t a l l u r g i c a lT r a n s a c t i o n sA,1988,19A: 2589-2602.[9]闫小林.连铸过程原理及数值模拟[M].石家庄:河北科学技术出版社,2001.152-153.[10]H a n H N,L e e Y G,O h K H,e ta l.A n a l y s i so fh o tf o rg i n g o f p o r o u s m e t a l s[J].M a t e r i a l s S c i e n c e&E n g i n e e r i n g A,1996,206:81-89.[11]Y a m a n a k a A,N a k a j i m a K,Y a s u m o t o K,e ta l.N e we v a l u a t i o no fc r i t i c a l s t r a i nf o r i n t e r n a l c r a c kf o r m a t i o ni nc o n t i n u o u s c a s t i n g[J].L aR e v u ed eMe t a l l u r g i e,1992,89(7-8):627-633.[12]Y a m a n a k a A,N a k a j i m a K,O k a m u r a K,e ta l.C r i t i c a ls t r a i nf o ri n t e r n a lc r a c kf o r m a t i o ni n c o n t i n u o u sc a s t i n g [J].I r o n m a k i n g a n d S t e e l m a k i n g,1995,22(6):508-512.[13]M a t s u m i y aT,I t o M,K a j i o k a H,e t a l.A ne v a l u a t i o no fc r i t i c a l s t r a i nf o r i n t e r n a lc r a c kf o r m a t i o ni nc o n t i n u o u s l yc a s t s l a b s[J].T r a n sI r o na nd S te e lI n s t i t u t eo fJ a p a n,1986,26:540-546.[14]Y o u n g M W,T a e-J u n g Y,D o n g J S,e t a l.An e wc r i t e r i o nf o r i n t e r n a l c r a c k f o r m a t i o n i n c o n t i n u o u s l y c a s t s t e e l s[J].M e t a l l u r g i c a l a n dM a t e r i a l sT r a n s a c t i o n s B,2000,31B:779 -794.[15]I t oY,Y a m a n a k aA,W a t a n a b eT,e t a l.I n t e r n a l r e d u c t i o ne f f i c i e n c y o f c o n t i n u o u s l y c a s t s t r a n dw i t h l i q u i dc o r e[J].L aR e v u e d eM e t a l l u r g i e,2000,O c t o b r e:1171-1176.[16]Y o k o y a m aT,U e s h i m a Y,M i z u k a m iY,e t a l.E f f e c to fC r,Pa n dT i o nd e n s i t y a n d s o l i d i f i c a t i o ns h r i n k a g eo f i r o n[J].T e t s u-t o-H a g a n e,1997,83:557-562.[17]Z e z eM,M i s u m iH,N a g a t aS,e t a l.S e g r e g a t i o nb e h a v i o ra n d d e f o r m a t i o nb e h a v i o r d u r i n g s o f t-r e d uc t i o n o fu n s o l i d i f i e ds t e e l i n g o t[J].T e t s u-t o-H a g a n e,2001,87(2):71-76.562第4期林启勇等:连铸坯动态轻压下的压下参数分析。
动态轻压下技术在连铸中的应用
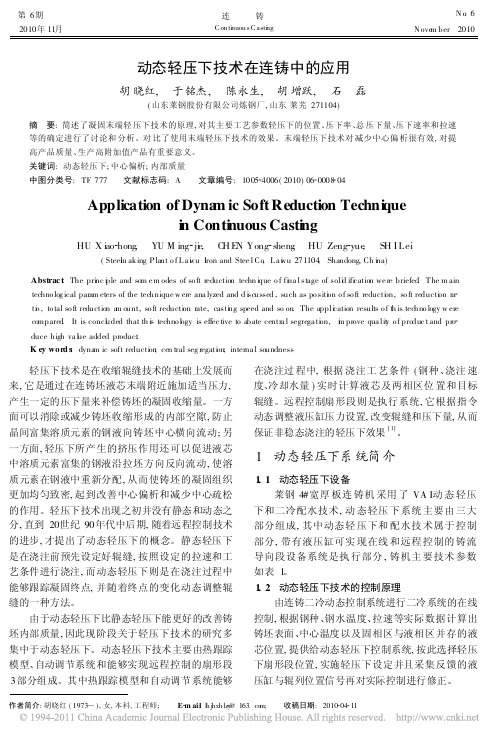
Abstrac t: The princ iple and som e m odes of so ft reduction techn ique o f fina l stage of solid ification we re briefed. T he m ain techno log ical param eters of the technique w ere ana lyzed and d iscussed , such as po sition o f so ft reduction, so ft reduction ra tio , to tal so ft reduction am ount, so ft reduction rate, casting speed and so on. The application results o f th is techno logy w ere compared. It is concluded that th is techno logy is effec tive to abate centra l segrega tion, im prove qua lity o f produc t and pro duce high va lue added product. K ey word s: dynam ic soft reduction; cen tral seg regation; interna l soundness
202. 00
a 50%
b 95%
10
辊缝值 结晶器上口 结晶器下口 垂直段入口 垂直段出口 矫直一段入口 水平一段入口 水平末段出口 压下量 /mm 出口实际辊缝值 压下位置固相率
连铸
表 3 250mm 厚辊缝及压下参数值 Table 3 Param eters of 250mm th ick roll gap and redu ction
关于连铸板坯轻压下位置的分析与研究

关于连铸板坯轻压下位置的分析与研究王国君,杜家恩(江西新余钢铁集团公司,江西 新余 338001)摘 要:轻压下技术对于提升板坯质量有着重要作用,位置的选择是轻压下技术的关键。
基于此,本文通过分析轻压下技术相关原理,展开了实验分析,通过实验计算和专家系统进行对比,在计算之后得出轻压下的位置。
在该位置上轻压板坯,对连铸坯的质量进行分析,发现板坯质量有明显的提升。
关键词:连铸板坯;轻压下技术;轻压下位置;实验研究中图分类号:TF777 文献标识码:A 文章编号:11-5004(2018)06-0261-2在连铸板坯的生产环节中,板坯出现中心偏析以及中心疏松问题十分常见,将会影响到钢材质量以及性能。
要想保证钢材的质量,必须要采取一些手段对疏松、偏析等问题进行控制和消除,最常使用的技术就是轻压下技术,轻压下技术需要使用在最佳位置上,才能保证技术的使用能够达到良好的效果,让钢材质量得到提升。
1轻压下技术1.1 概述在连续铸钢的过程中,钢坯使用液芯进行矫直的时候,为了能够得到没有缺陷的铸坯,需要使用对铸坯施加一定的压力。
这样能够避免凝固前出现搭桥,避免影响到钢水的输送,从而产生中心偏析的问题。
这项技术最早在二十世纪八十年代,在板坯支撑辊道从上至下收缩辊缝,从而避免板坯出现鼓肚,造成中心偏析问题的出现。
轻压下技术主要包括三种类型,第一种是轻压下技术,主要被应用在板坯以及大方板坯的铸坯液相穴的凝固末端;第二种是液芯压下技术,常被应用在薄板坯的连轧工艺中;第三种是铸轧技术,同样适合在薄板坯中使用。
从位置方面分类,轻压下技术分成全程和局部;从控制方式方面分类,轻压下技术分成动态压下和静态压下。
1.2 轻压下技术原理根据板坯中疏松、偏析以及缩孔的形成原理,在板坯凝固的最末端区域施加一定的压力,使得向下的压量让坯壳出现变形对两相区的凝固收缩量进行补偿。
一方面能够对中心孔隙进行消除,避免溶质液体向着铸坯出现横向的流动。
另一方面在轻压下作用下,积压作用能够破坏掉搭桥,让液相穴和凝固末端可以连通,实现补偿。
连铸板坯轻压下过程压下率参数的理论分析

图 1 铸坯横截面由液相区A、 中, , 两相区A . 2
单位时间的压下量, 等于压下率与拉速的乘积) , 以平均压下率、 平均压下速率来衡量轻压下的大
小和快慢程度。 22 模型求解 由式6 要确定压下率, 可知, 就必须首先确定
固相区A 组成; 〕 横坐标x 表示宽面方向, 纵坐标y 表示厚度方向, 垂直于纸面方向为: 方向, 即拉坯
d/z P p 整理后可得: M d= 汤= 拢+流, 0
J 静 警 d+ 0 o" P )y r .( ,、 J o x鄂Y d .
(z + JP),二 户)x d V,、。 U.、z. s, s一 : ‘ , z一 ( . ‘
() 3
P a` +k) () 。 二k) y“ c g au 。 c xa y> ・ 7 a (x ( T s a
板坯轻压下过程的基础上, 推出了压下 率理论模 型, 并结合实际条件, 研究了拉速和铸坯断面对连
铸板坯压下率的影响。
术 一 ’〕 其 动 轻 下 术, 成 现 之 〔’尤 是 态 压 技 已 为 代 一, 连 机重 铸 要标志之一〔‘ 压 “」 下率( 拉 一。 即 坯方向
单位长度的压下量,m m 是轻压下技术的核心 r/) t a 参数之一, 压下率过大将导致中心裂纹等缺陷, 过 小对改善中心偏析与疏松的效果不明显。目前, 有关压下率的研究主要集中 在工业试验和实验研
和凝固收缩的铸坯轻压下的必要压下率, 即:
液相区A ,
y
图 1 连铸坯 1 横截面内凝固区 / 4 域分布示意图
0} x 0器d ` f d _d, 2 " ( d ( ) H二 2 二 1 o ,y 6 Y
山 山
j }x x Op ,_ . 一d ,
连铸轻压下工艺优化与实践

连铸轻压下工艺优化与实践杨文清,陈迪庆,白静,潘金保(武钢股份条材总厂,武汉,430083)摘要:本文介绍了轻压下对改善铸坯中心偏析和中心疏松的作用,通过对液芯长度计算,确定压下位置,进行多次试验,并对试验结果进行分析对比,选择最适合的压下方式。
关键字:轻压下;中心偏析;中心疏松1 前言连铸钢水在冷凝过程中,低熔点的物质被推向铸坯中心部位,形成了C、S、P、Mn 等元素的偏析带,该偏析带在液相穴终端存在于底部,形成了中心偏析和中心疏松缺陷。
轻压下技术是连铸坯拉矫时,对带液芯的铸坯施加小的压力的工艺方法。
即在铸坯凝固终端附近,对铸坯施加一定的压下量,使铸坯凝固终端形成的液相穴被破坏,以打断枝晶搭桥。
轻压下工艺能够改善中心偏析和中心疏松,但如果工艺不当,会产生压下裂纹,严重影响连铸坯质量。
武钢条材总厂一炼钢分厂(以下简称“一炼钢”)1#连铸机主要生产高碳钢。
对高碳钢来说,由于碳含量较高造成导热性差、凝固区间大,连铸坯本身容易产生偏析、疏松和缩孔等缺陷,在拉丝和扭转过程中容易引起断裂 [1] 。
受铸机断面大小等条件的制约,铸坯中心碳偏析一直是一炼钢控制难点。
该厂通过对拉矫机设备进行改造,使设备具备更大压下功能,并通过计算液芯长度,调整压下方式,找出最适合的压下量及压下方式。
2 浇注工艺现状一炼钢1#连铸机是五机五流弧形连铸机,主要生产高碳钢,铸机主要工艺参数见下表:目前,高碳钢轻压下压下量为 9mm,从低倍检验看,铸坯存在一定程度中心疏松,铸坯中心碳偏析也一直徘徊在 1.15 左右,与其他炼钢厂相比有很大差距,难以满足日益增长的客户需求。
3 凝固末端计算对高碳钢发生纵裂漏钢的坯壳进行分析,将漏钢坯壳横向切开,测量切开点的坯壳厚度,根据坯壳厚度计算凝固系数,漏钢时浇注工艺如下:漏钢坯壳示意图如下:坯壳厚度测量结果及凝固系数计算如下:注:凝固系数:K=D*(V/L) 1/2 D 为凝固坯壳厚度,V 为拉速,L 为到液面距离取两点的平均凝固系数作为综合凝固系数K,则可计算出液芯长度 L。
高碳钢方坯连铸中心缩孔去除
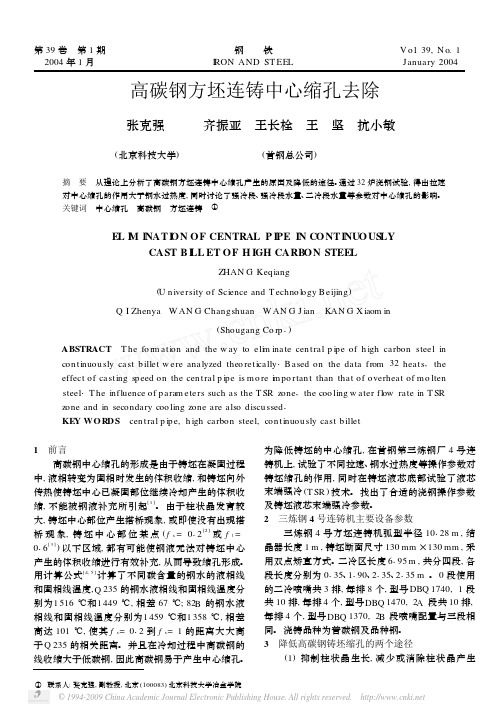
第39卷 第1期2004年1月钢 铁I RON AND ST EELV o l.39,N o.1January2004高碳钢方坯连铸中心缩孔去除 张克强 齐振亚 王长栓 王 坚 抗小敏(北京科技大学) (首钢总公司)摘 要 从理论上分析了高碳钢方坯连铸中心缩孔产生的原因及降低的途径。
通过32炉浇钢试验,得出拉速对中心缩孔的作用大于钢水过热度,同时讨论了强冷段、强冷段水量、二冷段水量等参数对中心缩孔的影响。
关键词 中心缩孔 高碳钢 方坯连铸 ①EL I M INAT I ON OF CENTRAL P IPE IN CONT INUOUS LYCAST B I LL ET OF H IGH CARB ON STEELZHAN G Keqiang(U n iversity of Science and T echno logy B eijing)Q I Zhenya W AN G Changshuan W AN G J ian KAN G X iaom in(Shougang Co rp1)ABSTRACT T he fo r m ati on and the w ay to eli m inate cen tral p i pe of h igh carbon steel in con tinuou sly cast b illet w ere analyzed theo retically1B ased on the data from32heats,the effect of casting sp eed on the cen tral p i pe is m o re i m po rtan t than that of overheat of m o lten steel1T he influence of p aram eters such as the T SR zone,the coo ling w ater flow rate in T SR zone and in secondary coo ling zone are also discu ssed1KEY WOR D S cen tral p i pe,h igh carbon steel,con tinuou sly cast b illet1 前言高碳钢中心缩孔的形成是由于铸坯在凝固过程中,液相转变为固相时发生的体积收缩,和铸坯向外传热使铸坯中心已凝固部位继续冷却产生的体积收缩,不能被钢液补充所引起[1]。
应用轻压下技术提高连铸坯质量的研究
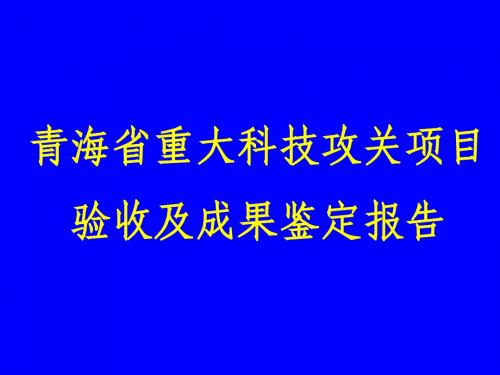
压下量,mm; L—辊距,mm;ε许用应变,≤0.15% 由公式(1)可以看出,对一定的辊列布置情况,附加 应变与压下量成正比,与凝固坯固坯壳的厚度成正比。 (2).物理模拟 (3).数值模拟
轻压下工艺的应用
• Danieli公司在试验中证实,在相同液芯率的 条件下,枝晶间的内部横向裂纹随着压下量 的增加成正比增加。曼内斯曼—德马克公司 的ISP工艺在二冷区扇形段液芯铸坯下拉速为 常数时,认为带液芯铸坯减薄是由逆向挤出 液芯实现的,坯壳宽面的纵向变形很小。 • 日本福山钢厂1986年4月在4号板坯连铸机上 安装了由分段辊组成的小间隙的轻压下扇形 段,最佳轻压下率0.9mm/min,试验的结果表 明不但可以减少大的宏观偏析,而且半宏观 偏析级别也明显地减少。
采用优化的连铸轻压下工艺生产的试验轴承钢连铸坯中心碳 偏析指数平均达到1.09级,中心疏松平均0.94级,一般疏松 平均0.87级,缩孔平均0.47级。与攻关前的指标相比:中心 碳偏析平均降低0.11,中心疏松平均降低1.86级,缩孔平均 降低1.53级。各项指标达到项目考核技术指标。
2 技术报告
青海省重大科技攻关项目 验收及成果鉴定报告
应用轻压下技术 提高连铸坯质量的研究
项目编号:2004-G-110 管理部门:青海省科学技术厅 承担单位:西宁特殊钢股份有限公司 协作单位:青海博世冶金研究所
1.1 项目简介 高碳的轴承钢、弹簧钢、碳素工具钢是西宁特钢的主导产品, 其年产量约占西钢年总产量的20%,在国内占有较大的市场份额。 长期以来,西钢一直采用模注工艺生产这些钢。模注工艺生产的钢 成材率低,生产成本高,表面质量差;采用连铸工艺生产的特殊钢 表面质量好,成材率显著提高,极大地节约生产成本,因此,连铸 成为当今特殊钢生产的主流。 西宁特钢于1997年引进美国康卡斯特的合金钢大方坯连铸机, 经过调试、试生产于1999年开始生产轴承钢、弹簧钢、碳素工具钢 等高碳的特殊钢。虽然连铸钢的表面质量较模注钢有了很大的改善 ,但因高碳钢固液两相区较其它钢种宽,在连铸坯的凝固过程中由 于选分结晶和凝固收缩导致富集溶质的钢液向中心的宏观流动而引 起中心偏析,同时由于枝晶“搭桥”,下部钢液在凝固收缩过程中 得不到上部钢液的补充,形成残余缩孔和中心疏松等缺陷,并伴随 产生中心的正或负偏析。
轻压下关键技术的研究及应用
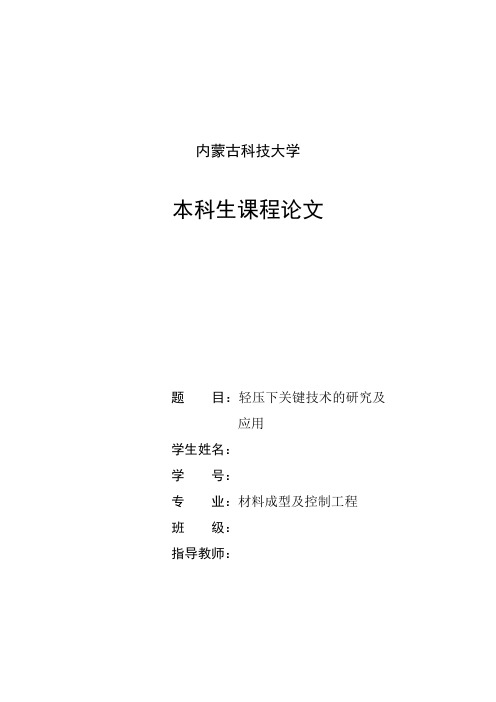
内蒙古科技大学本科生课程论文题目:轻压下关键技术的研究及应用学生姓名:学号:专业:材料成型及控制工程班级:指导教师:轻压下关键技术的研究及应用姓名(内蒙古科技大学材料与冶金学院成型班 014010)摘要:铸坯在连铸生产过程中比较容易产生中心偏析和中心疏松缺陷,其质量会对后续的轧材质量产生直接的影响。
近年来,人们在不断的摸索研究中,得出了许多在连铸坯方面改善铸坯质量的新技术,凝固末端轻压下技术,凝固末端强冷技术,低温浇注技术,电磁搅拌技术等,其中最为有效的是轻压下技术。
本文综述了轻压下技术基本原理及其关键技术的研究与运用。
关键词:连铸;中心偏析、疏松;轻压下;关键技术The research and application of keytechnology of soft reductionYuan Lu(Inner Mongolia University of Science and Technology,school of Materials andMetallurgy,class of chengxing09-2 014010)Abstaract:It is very easy to produce center segregation and center porosity defects in continuous casting process,the quality of the followed products is impacted by the slab or billet.As more research in the field in recent years,a number of methods to improve the quality of products are proposed in the continuous casting,the most effective one is the soft reduction technology.This paper reviews the basic principles of soft reduction technology,this article reviews the research and application of soft reduction technology of basic principles and key technology.Key words:continuous casting;center segregation and center porosity;soft reduction;key technology随着人们对钢铁产品质量的要求越来越高,连铸坯中心偏析和中心疏松等缺陷越来越成为影响钢材质量的主要因素之一。
连铸轻压下过程极限压下量及工艺参数分析
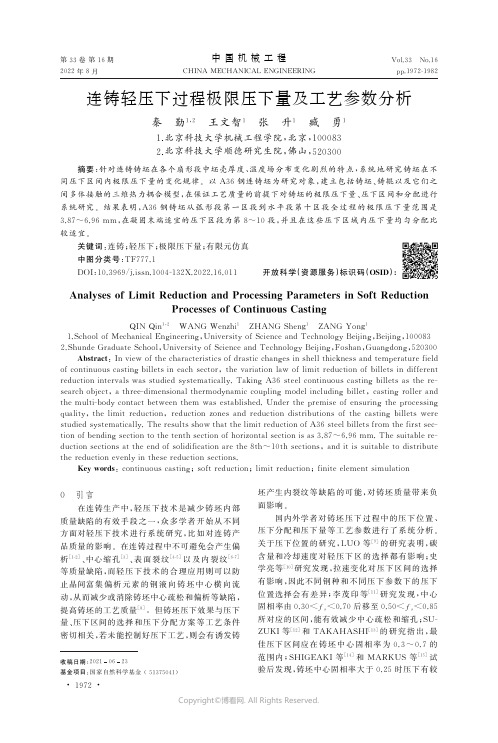
第33卷第16期中国机械工程V o l .33㊀N o .162022年8月C H I N A M E C HA N I C A LE N G I N E E R I N Gp p.1972G1982连铸轻压下过程极限压下量及工艺参数分析秦㊀勤1,2㊀王文智1㊀张㊀升1㊀臧㊀勇11.北京科技大学机械工程学院,北京,1000832.北京科技大学顺德研究生院,佛山,520300摘要:针对连铸铸坯在各个扇形段中坯壳厚度㊁温度场分布变化剧烈的特点,系统地研究铸坯在不同压下区间内极限压下量的变化规律.以A 36钢连铸坯为研究对象,建立包括铸坯㊁铸辊以及它们之间多体接触的三维热力耦合模型,在保证工艺质量的前提下对铸坯的极限压下量㊁压下区间和分配进行系统研究.结果表明,A 36钢铸坯从弧形段第一区段到水平段第十区段全过程的极限压下量范围是3.87~6.96mm ,在凝固末端适宜的压下区段为第8~10段,并且在这些压下区域内压下量均匀分配比较适宜.关键词:连铸;轻压下;极限压下量;有限元仿真中图分类号:T F 777.1D O I :10.3969/j .i s s n .1004 132X.2022.16.011开放科学(资源服务)标识码(O S I D ):A n a l y s e s o fL i m i tR e d u c t i o na n dP r o c e s s i n g P a r a m e t e r s i nS o f tR e d u c t i o n P r o c e s s e s o fC o n t i n u o u sC a s t i n gQ I N Q i n 1,2㊀WA N G W e n z h i 1㊀Z H A N GS h e n g 1㊀Z A N G Y o n g11.S c h o o l o fM e c h a n i c a l E n g i n e e r i n g ,U n i v e r s i t y o f S c i e n c e a n dT e c h n o l o g y B e i j i n g ,B e i j i n g,1000832.S h u n d eG r a d u a t eS c h o o l ,U n i v e r s i t y o f S c i e n c e a n dT e c h n o l o g y B e i j i n g ,F o s h a n ,G u a n g d o n g,520300A b s t r a c t :I nv i e wo f t h e c h a r a c t e r i s t i c s o f d r a s t i c c h a n g e s i n s h e l l t h i c k n e s s a n d t e m pe r a t u r ef i e l d o f c o n t i n u o u s c a s t i ng bi l l e t s i ne a c hs e c t o r ,t h ev a r i a t i o n l a wo f l i m i t r e d u c t i o no f b i l l e t s i nd i f f e r e n t r e d u c t i o n i n t e r v a l sw a s s t u d i e ds y s t e m a t i c a l l y .T a k i n g A 36s t e e l c o n t i n u o u s c a s t i n g bi l l e t s a s t h e r e Gs e a r c ho b j e c t ,a t h r e e Gd i m e n s i o n a l t h e r m o d y n a m i c c o u p l i n g m o d e l i n c l u d i n g b i l l e t ,c a s t i n g ro l l e r a n d t h em u l t i Gb o d y c o n t a c t b e t w e e nt h e m w a se s t a b l i s h e d .U n d e r t h e p r e m i s eo f e n s u r i n g t h e p r o c e s s i n gq u a l i t y ,t h e l i m i tr e d u c t i o n ,r e d u c t i o nz o n e sa n dr e d u c t i o nd i s t r i b u t i o n so f t h ec a s t i n g bi l l e t sw e r e s t u d i e ds y s t e m a t i c a l l y .T h e r e s u l t s s h o wt h a t t h e l i m i t r e d u c t i o n o fA 36s t e e l b i l l e t s f r o mt h e f i r s t s e c Gt i o no f b e n d i n g se c t i o n t o t h e t e n t h s e c t i o nof h o r i z o n t a l s e c t i o n i s a s 3.87~6.96mm.T h e s u i t a b l e r e Gd u c t i o n s e c t i o n s a t t h e e n do f s o l i d i f i c a t i o na r e t h e 8t h ~10t hs e c t i o n s ,a n d i t i s s u i t a b l e t od i s t r i b u t et h e r e d u c t i o ne v e n l yi n t h e s e r e d u c t i o n s e c t i o n s .K e y wo r d s :c o n t i n u o u s c a s t i n g ;s o f t r e d u c t i o n ;l i m i t r e d u c t i o n ;f i n i t e e l e m e n t s i m u l a t i o n 收稿日期:20210623基金项目:国家自然科学基金(51375041)0㊀引言在连铸生产中,轻压下技术是减少铸坯内部质量缺陷的有效手段之一,众多学者开始从不同方面对轻压下技术进行系统研究,比如对连铸产品质量的影响.在连铸过程中不可避免会产生偏析[1G2]㊁中心缩孔[3]㊁表面裂纹[4G5]以及内裂纹[6G7]等质量缺陷,而轻压下技术的合理应用则可以防止晶间富集偏析元素的钢液向铸坯中心横向流动,从而减少或消除铸坯中心疏松和偏析等缺陷,提高铸坯的工艺质量[8].但铸坯压下效果与压下量㊁压下区间的选择和压下分配方案等工艺条件密切相关,若未能控制好压下工艺,则会有诱发铸坯产生内裂纹等缺陷的可能,对铸坯质量带来负面影响.国内外学者对铸坯压下过程中的压下位置㊁压下分配和压下量等工艺参数进行了系统分析.关于压下位置的研究,L U O 等[9]的研究表明,碳含量和冷却速度对轻压下区的选择都有影响;史学亮等[10]研究发现,拉速变化对压下区间的选择有影响,因此不同钢种和不同压下参数下的压下位置选择会有差异;李茂印等[11]研究发现,中心固相率由0.30<f s <0.70后移至0.50<f s <0.85所对应的区间,能有效减少中心疏松和缩孔;S U GZ U K I 等[12]和T A K A H A S H I [13]的研究指出,最佳压下区间应在铸坯中心固相率为0.3~0.7的范围内;S H I G E A K I 等[14]和MA R K U S 等[15]试验后发现,铸坯中心固相率大于0.25时压下有较2791 Copyright ©博看网. All Rights Reserved.好效果,小于0.25时中心偏析会随着压下量的增大而恶化;罗森等[16]认为轻压下区间应在中心固相率为0.3~0.7的范围内;WA N G等[17]发现最佳压下位置大致在铸坯中心固相率为0.9处.由于连铸条件和铸坯材质不同,以中心固相率来确定的最佳压下位置会有差异且选择范围较大,铸坯的宽窄面温差与坯壳厚度在不同的位置亦会不同,则压下量会随连铸过程的位置变化而改变,因此需要对压下区间的选择进行进一步的系统研究.以各区段上铸坯的应力应变变化及变形情况作为侧重点进行研究,同时结合前人对压下位置的研究结果,可以较为细致地选择适宜区间,从而优化压下效果.在保证连铸工艺质量的前提下,压下过程还要避免内裂纹的产生,内裂纹的形成不仅受连铸机设备㊁冷却条件和钢种等因素影响,还受工艺操作的影响[18],因此需要对铸坯的压下量和分配方式进行研究.日本八蟠制钢发现凸形辊压下采用6mm压下量可获得中心质量良好的铸坯[19].台湾中钢发现在中心固相率0.55~0.75区域的压下总量为4~5mm[20].罗传清等[21]建议在中心固相率0.55~0.95区域采用6mm压下量进行压下.王少伟等[22]发现在扇形段9和10段分别压下2.9mm㊁2.8mm较为合理.Z H A O等[23]研究发现压下量与宽展量之比由2.0提高到4.4后压下效率显著提高,但该研究只针对凝固末端的合理压下量进行讨论,而未涉及其他扇形段中的压下量.L I U等[24]发现中心固相率为0.3~0.9时,轻压下量宜为12.2~4.0mm.刘珂等[25]对凝固末端糊状区体积收缩进行分析后认为,中心固相率为0.7~0.3时,合理轻压下量应为2.95~4.65mm,对铸坯体积收缩与压缩变形量进行分析来确定合理压下量的方法没有考虑是否会在压下过程中有产生裂纹缺陷的可能.Z O N G等[26]研究发现最大拉应力出现在脆性温度区间的边界处,因此压下量对铸坯脆性温度区间力学性能的影响尤为重要.罗仁辉等[27]分析了压下量分配对铸坯各节点应力和应变的影响,发现均匀的压下量更有利于降低铸坯表面的应力.虽然许多学者对压下量及分配方式进行了研究,但系统地探究其对铸坯内部力学性能的影响研究较少,且多为局部位置的压下量调整,缺少连铸全程极限压下量的研究.由于压下区间的选择范围较大,铸坯在各区间上温度与坯壳厚度有所变化,可施加的最大压下量也会不同,故需要在铸坯不产生内裂纹的前提下对连铸全过程的极限压下量进行探究.确定极限压下量的范围和适宜的分配方式,就可以根据情况动态选择各个区间上的压下量大小,既能最大化减少偏析与疏松等内部缺陷,又能防止内裂纹的产生.铸坯压下效果与合适的压下工艺密切相关,由于连铸生产工艺的复杂性和工艺参数的多样性,通过实验和生产线调试的方法对压下参数进行调试较为复杂且成本较高,故采用数值模拟的方法进行研究.许多学者采用有限元分析,建立了凝固传热[28]和热力耦合[29]等模型来研究连铸过程温度场变化及应力与变形行为演变规律.本文通过建立连铸热力耦合模型,考虑铸坯的温度场变化与弹塑性变形,并施加合理的钢水静压力以尽可能真实准确地模拟连铸压下的全过程,对连铸重要压下工艺参数进行了研究.以A36钢连铸坯为研究对象,基于A B A Q U S商业有限元软件建立铸坯三维压下模型,在临界应力与临界应变准则的基础上,探究连铸全程的极限压下量,并研究不同的压下区间和压下分配工艺参数对铸坯内部力学性能和极限压下量的影响,为连铸动态压下工艺的开发提供理论依据,以指导实际生产.1㊀分析模型本文建立了在辊列中运动的三维热力耦合有限元模型,首先根据材料的物性参数建立凝固传热模型,获得铸坯的温度场分布和凝固末端位置,然后根据铸坯的温度场数据和力学性能参数,建立热力耦合模型,并合理施加钢水静压力,最后结合内裂纹判定准则分析铸坯的极限压下量范围和不同的工艺参数下的应力应变分布及变形演变历程.具体研究思路如图1所示.图1㊀研究思路F i g.1㊀R e s e a r c h i d e a1.1㊀铸坯压下模型的建立连铸机模型采用湘潭钢铁厂5号直弧形板坯3791连铸轻压下过程极限压下量及工艺参数分析 秦㊀勤㊀王文智㊀张㊀升等Copyright©博看网. All Rights Reserved.连铸机,如图2所示.整个连铸机包括s e g0~ s e g12扇形段,其中s e g0为弯曲段,s e g1~6为弧形段,s e g7㊁8为连续矫直段,s e g9~12为水平段.其主要技术参数见表1.图2㊀连铸机辊列图F i g.2㊀R o l l l a y o u t o f c o n t i n u o u s c a s t e r表1㊀湘钢5号板坯连铸机的主要技术参数T a b.1㊀T h em a i n t e c h n i c a l p a r a m e t e r s o fN o.5b i l l e tc a s t e r i nX i a n g t a n I r o na n dS t e e l C o r p机型直弧型二次冷却方式水冷和气雾冷却铸机流数1矫直方式多点矫直结晶器实际长度(mm)900结晶器有效长度(mm)800铸坯断面厚度(mm)200铸坯断面宽度(mm)1500~3200连铸机基本半径(m)10正常浇铸速度(m/m i n)0.8~1.25㊀㊀为了探究不同压下工艺参数对铸坯内部力学行为的影响,根据所研究的连铸机实际生产规格建立了铸坯在辊列中运动的热力耦合有限元模型,如图3所示.其中,铸坯材料为A36钢,其化学成分见表2.考虑到铸坯左右部分的传热和边界条件具有对称性,使用1/2铸坯建立压下模型,铸坯尺寸为862mmˑ226mmˑ1100mm,使用C3D8R八节点线性六面体减缩积分单元,铸辊半图3㊀铸坯凝固变形三维几何模型和凝固末端压下模型F i g.3㊀T h r e eGd i m e n s i o n a l g e o m e t r i cm o d e l o f s o l i d i f i c a t i o nd e f o r m a t i o no f c a s t i n g b i l l e t a n d e n d s o l i d i f i c a t i o np r e s sGd o w nm o d e l表2㊀A36钢的化学成分(质量分数)T a b.2㊀C h e m i c a l c o m p o s i t i o no fA36s t e e l(m a s s f r a c t i o n)元素含量(%)元素含量(%)C0.157A l0.0289S i0.2489C r0.0375M n1.4143C u0.0284P0.0162N i0.0177S0.0044径R分别为75mm㊁115mm㊁125mm和150mm,共188个,拉速为1.15m/m i n.由于铸坯左右部分传热和边界条件具有对称性,故建立1/2铸坯模型,对三维铸坯模型宽面中部施加对称约束,作用于整个连铸过程中.在三维铸坯模型的外表面和解析刚性铸辊之间建立法向硬接触㊁切向罚函数法摩擦的接触关系.闫小林[30]研究表明热坯滚动摩擦因数为0.3,铸辊在热坯上的滚动摩擦因数受铸坯表面情况的影响,根据从动辊所用轴承类型摩擦因数设置为0.001,驱动辊摩擦因数设置为0.3.各驱动辊分别绕其中心轴旋转,在铸坯动态过程中对每个驱动辊施加角速度为0.2174r a d/s,并约束从动辊的全部自由度与驱动辊在U1和U2方向上的自由度.在预定义场部分导入铸坯凝固过程的温度场计算结果来模拟铸坯在拉坯运行过程中的实时温度变化的影响.钢水静压力的施加方法是通过计算铸坯单元以拉坯速度运行时每一时刻到结晶器弯月面的垂直距离h,由此得到坯壳单元在每一时刻所受钢水静压力的大小,利用温度分析时得到的坯壳厚度数据选取铸坯固液交界面,对固液交界面处的单元表面施加均布压应力,实现了钢水静压力的实时变化,更符合实际情况.1.2㊀铸坯内裂纹判定标准的确定1.2.1㊀临界应力应变判据的确定为了判断铸坯凝固前沿是否产生内裂纹,采用临界应力应变准则作为判断标准.为了获得钢种的临界应力,采用文献[31]中临界应力与碳含量的关系,如图4所示.当研究对象为A36㊁碳质量分数为0.157%时,该钢种在凝固末端所能承受的临界应力为3.3M P a.根据文献[32]中临界应变与碳含量的关系,如图5所示,该钢种的临界应变为2.5%.为了进行对比验证,采用高温拉伸变形试验的方法对上述内裂纹判定标准进行确定.具体试验方法如下:将试样均温区以T =10ħ/s的升温速率快速加热到1400ħ,保温60s,使其充分奥氏体化,再以升温速率T =1ħ/s缓慢加热至试验温度,最后在恒温下使试样拉断或者到指定应4791中国机械工程第33卷第16期2022年8月下半月Copyright©博看网. All Rights Reserved.图4㊀临界应力与碳含量的关系F i g .4㊀R e l a t i o n s h i p be t w e e n c r i t i c a l s t r e s s a n d c a r b o n c o n t e nt图5㊀临界应变与碳含量的关系F i g .5㊀R e l a t i o n s h i p be t w e e n c r i t i c a l s t r a i na n d c a r b o n c o n t e n t变从而完成高温拉伸试验.试样应力应变随温度变化情况如图6所示.在1460ħ温度下,当应变为2.88%㊁应力为3.72M P a 时,铸坯试样出现断裂,据断口形貌可判断为脆性断裂,所以该钢种的铸坯在凝固末端压下的临界应变为2.88%左右,临界应力为3.72M P a左右.随着温度的降低,断面收缩率迅速增大,试样已具有良好的塑性,在应变为4%㊁应力在图6㊀试样应力应变曲线F i g .6㊀S t r e s s s t r a i n c u r v e s o f s pe c i m e n 7M P a范围内,铸坯试样不会出现断裂.因此在连铸过程中,为避免出现内裂纹,出铸机前铸坯温度应避开温度脆性区间,并且在凝固末端压下过程中,铸坯凝固前沿的应变不应大于2.88%,应力不应大于3.72M P a .综上可得,铸坯的临界应力为3.72M P a ,临界应变为2.88%.1.2.2㊀高温脆性区间的确定铸坯的内裂纹多产生于凝固前沿处,需要确定其具体的位置.有学者把铸坯的固液两相区分为液相补充区和高温脆性区,液相不渗透温度和零塑性温度的区间范围即为高温脆性区间的温度范围.根据文献[33],零塑性温度对应的固相率大约是0.99,液相不渗透温度对应的固相率大约是0.9,零强度温度对应的固相率大约是0.75.采用G l e e b l e G3500热力模拟试验机进行高温拉伸测试,获得了钢种在不同测试温度下的热力塑性曲线㊁零强度温度和零塑性温度等高温力学性能参数.试验取样的位置㊁所用设备及试样断口形貌如图7所示.试样采用标准热拉伸圆柱状试样,尺寸为ϕ10mmˑ120mm .根据试验,当温度达到1460ħ时,据断口形貌可判断为脆性断裂,故将1460ħ作为A 36钢种的零塑性温度;当温度达到1485ħ时,试样的抗拉强度极限接近0,故将1485ħ作为A 36钢种的零强度温度.图7㊀试验取样位置㊁设备及结果F i g .7㊀T e s t s a m p l i n g l o c a t i o n ,e q u i pm e n t a n d r e s u l t 根据测得A 36钢的零强度温度和零塑性温度(分别为1485ħ和1460ħ),采用文献[33G34]的固相率公式计算零强度和零塑性温度对应的固相率如下:f s =(11-2ΩK )[1-(T f -T T f -T L)(1-2ΩK )(K -1)](1)Ω=α[1-e x p (-1/α)]-0.5e x p (-1/(2α))(2)α=33.7T-0.244(3)式中,f s 为固相率;T f 为纯铁熔点1536ħ;T L 为液相线温度1513ħ;T 为温度;K 为溶质再分配系数0.287;T为冷却速率,取5ħ/s ;α㊁Ω为表征溶质反扩散程度的参数.5791 连铸轻压下过程极限压下量及工艺参数分析秦㊀勤㊀王文智㊀张㊀升等Copyright ©博看网. All Rights Reserved.零强度和零塑性温度对应的固相率分别为0.99和0.75,与前文理论概述吻合.将液相不渗透温度对应的固相率代入回归公式中,计算得到液相不渗透温度为1468ħ.因此,A 36钢的高温脆性区间为1460~1468ħ,分析铸坯此位置在不同工况下的应力与变形情况.1.3㊀模型验证提取铸坯宽面中心和窄面中心节点在整个连铸过程中沿铸流方向的温度变化曲线,并与工厂生产现场相应位置测量的温度数据进行对比,如图8所示.仿真温度与测试温度基本一致,温度误差最大值为20ħ,最大相对误差在5%以内.(a)铸坯宽面中心节点(b)铸坯窄面中心节点图8㊀铸坯温度实测与仿真结果对比F i g .8㊀C o m pa r i s o nb e t w e e nm e a s u r e da n d s i m u l a t e d r e s u l t s o f b i l l e t t e m pe r a t u r e 模拟了扇形段5㊁6两段铸坯凝固前沿位置处的应力变化,压下量为5mm .由图9可知,铸坯凝固前沿处的应力值出现周期性变化,当铸坯位于压下辊之间时,由于钢水静压力的作用,铸坯凝固前沿受到拉应力,应力值为正值.当铸坯位于压下辊下方位置时,由于辊子的压下作用,凝固前沿受到压应力,应力值为负值,故铸坯在前进过程中应力呈现周期性波动变化.根据临界应力判据,当应力最大值不超过临界应力值时,铸坯不会产生内裂纹,因此在扇形段第5㊁6两段实施5mm的压下量时不会有内裂纹产生.为了验证压下模型的正确性与可行性,将模拟结果与文献[31]建立的连铸板坯三维有限元模型的模拟结果进行对比.所用材料为A 36钢,碳质量分数为0.157%,在凝固前沿所能承受的临界应力值为3.72M P a .文献[31]的模型计算对象为Q 345R ,碳质量分数为0.16%,临界应力值为3.31M P a .选取压下量为5mm 的工况进行对比,其中扇形段位置与铸辊数量与文献相同,提取同位置铸坯内弧侧凝固前沿应力值如图9所示,铸坯凝固前沿的应力在-2.85~1.79M P a 之间呈周期性变化,文献[31]应力在-5.5~2M P a 之间呈周期性变化.由于铸坯材料㊁模型建立以及工艺参数与文献[31]有所不同,故应力极值会略有差异,根据临界应力判据,应力最大值是主要的研究对象,其值与文献[31]相差10.5%.在相同工况下铸坯的应力变化原理及变化趋势相同,应力最大值相近.温度数据的实测对比和文献[31]仿真对比证明了压下模型的正确性.(a)本文结果(b )文献[31]结果图9㊀凝固前沿的应力值对比F i g .9㊀C o m pa r i s o no f s t r e s s v a l u e s a t t h e s o l i d i f i c a t i o n f r o n t运用上述压下模型对连铸过程进行模拟可以得到凝固前沿位置在不同区段的应力和应变变化情况,选取不同的压下量方案进行研究,结合临界应力应变准则进行力学性能分析,得到压下过程的极限压下量,进而探究压下区间及分配方式的选取对铸坯内部力学性能和极限压下量的影响.6791 中国机械工程第33卷第16期2022年8月下半月Copyright ©博看网. All Rights Reserved.2㊀铸坯极限压下量分析及工艺参数影响2.1㊀连铸过程的极限压下量压下量要完全补偿压下区间内钢液在凝固过程中的体积收缩量才能防止富集溶质钢液的流动,压下量必须满足3个要求:①能够补偿压下区间内的凝固收缩,减少中心偏析和中心疏松;②避免铸坯产生内裂纹;③压下时产生的反作用力要在铸机扇形段许可载荷范围内.首先讨论连铸凝固末端压下,本模型保证压下区间和压下分配不变,对4种不同压下量的应力应变㊁窄面鼓肚和宽面间隙进行了对比,探究凝固末端的极限压下量.压下方案分为4种,方案1~4的压下区间均为水平段的第8㊁9和10段,压下量分别为3mm㊁6mm㊁9mm和12mm,均匀分配压下量.提取铸坯高温脆性区内关键点内的应力最大值,如图10所示.统计铸坯不同区间的应力最大值可以看到,随着压下总量的增加,铸坯高温脆性区应力最大值增大.方案1压下3mm时主应力最大值出现在水平第9段,为2.41M P a;方案2压下6mm时主应力最大值出现在水平第10段,为3.28M P a;方案3压下9mm时主应力最大值出现在水平第10段,为6.09M P a;方案4压下12mm时主应力最大值出现在水平第10段,为6.70M P a.压下3mm和6mm时,铸坯主应力最大值未超过其临界应力3.72M P a,铸坯不会出现内裂纹缺陷;而压下9mm和12mm时,铸坯主应力最大值远超过临界应力值,容易产生内裂纹,压下量应小于9mm .图10㊀不同压下总量下的应力最大值F i g.10㊀M a x i m u ms t r e s s o f d i f f e r e n t t o t a l r e d u c t i o n铸坯高温脆性区的压下应变值如图11所示.压下应变值在不同的压下区段内呈现范围式波动,随着压下总量的增加,铸坯高温脆性区压下应变最大值增大.4种方案的应变最大值分别为1.58%㊁1.75%㊁5.27%和8.21%,最大应变值出现在水平第10段,不同压下量对铸坯高温脆性区的应变影响很大.压下3mm和6mm时,铸坯的应变最大值未超过其临界应变2.88%,铸坯不会出现内裂纹缺陷;而压下总量超过9mm,应变最大值远超过临界值,因此应将压下总量控制在9mm以内.图11㊀不同压下总量下的应变F i g.11㊀S t r a i no f d i f f e r e n t t o t a l r e d u c t i o n铸坯在压下过程中窄面会发生鼓肚变形,对铸坯力学性能产生影响,提取铸坯不同压下量的窄面鼓肚变形量如图12所示.铸坯每进入一个压下区段,窄面鼓肚变形量会增大,整体呈现增长趋势.压下3mm和6mm时,铸坯在完成压下前后窄面鼓肚变形量变化不大,增量保持在2mm 以下;压下9mm和12mm时,压下之后的窄面鼓肚变形量较之前增量更大,分别增加了4.1mm 和6.4mm,在控制窄面鼓肚方面,压下量控制在6mm以下较好.铸坯的角部应变随压下过程的进行呈现阶梯式增加,不同压下总量下的角部应变如图13所示.角部应变随着压下总量的增加而增加,方案1压下时角部应变在三个压下区间内分别为0.3%㊁1.2%和2%,方案2角部应变分别为0.5%㊁3.3%和5.5%;方案3角部应变分别为1.5%㊁5.5%和8.7%;方案4角部应变分别为图12㊀不同压下总量下的窄面鼓肚F i g.12㊀N a r r o wb u l g e s i z e o f d i f f e r e n t t o t a l r e d u c t i o n7791连铸轻压下过程极限压下量及工艺参数分析 秦㊀勤㊀王文智㊀张㊀升等Copyright©博看网. All Rights Reserved.图13㊀不同压下总量下的角部应变F i g.13㊀C o r n e r s t r a i no f d i f f e r e n t t o t a l r e d u c t i o n 2.5%㊁7.5%和11.5%,其中方案3和4在第9段的角部应变就已经超过了方案1和2的角部应变最大值,考虑到控制角部应变方面,压下总量不宜过大.将不同压下量的应变值进行线性拟合,如图14所示,铸坯在水平段上临界应变值为2.88%时的压下量为其极限压下量6.96mm.考虑到控制窄面鼓肚变形和角部应变以及合理分配压下量的情况下,较为适宜的压下量为6mm .图14㊀不同压下总量下的最大应变值F i g.14㊀M a x i m u ms t r a i no f d i f f e r e n t t o t a l r e d u c t i o n铸坯在各区间的温度不同,坯壳厚度逐渐增加,因此抵抗变形和压下的能力会有差别,不同区间的极限压下量亦会有所不同.在研究凝固末端区间的极限压下量的情况下,进一步探究连铸从弧形段到水平段全过程的极限压下量范围.选取弧形段第一区段s e g1,分析压下量为0㊁3mm㊁4mm和5mm四种不同情况下的铸坯应变变化,如图15所示.随着压下过程的进行,铸坯应变值总体呈增大趋势,在经过压下辊时应变值会有突变,此时应变容易超过临界应变值从而产生内裂纹.无压下时应变最大值为0.82%,压下3mm㊁4mm和5mm时应变最大值分别为2.28%㊁2.97%和3.29%.在压下后期应变范围波动很大,将不同压下量的应变值进行线性拟合可得,临界应变为2.88%时的铸坯压下量为其s e g1区段的极限压下量(大小为3.87mm).图15㊀s e g1段不同压下量下的应变F i g.15㊀S t r a i no f s e g m e n t1w i t hd i f f e r e n t r e d u c t i o n铸坯在弧形段s e g1区段的极限压下量为3.87mm,水平区段为6.96mm.随着连铸过程的进行,坯壳厚度逐渐增加,极限压下量逐渐增大,s e g1~s e g10段的极限压下量范围是3.87~6.96mm.2.2㊀不同压下区间对压下结果的影响压下区间是动态压下技术的重要参数之一,对于压下区间目前没有一个定值,一般企业都是根据实验修正后取得最佳值,该值与钢的成分㊁铸坯断面及生产设备都有关.本节保证上述合理压下量和压下分配不变,选取水平末端压下区间为研究对象,通过改变不同的压下区间,得到压下区间的变化对铸坯内部力学性能的影响,其中不同压下区间的压下方案见表3.表3㊀不同压下区间的压下方案T a b.3㊀R e d u c t i o n s c h e m e sw i t hd i f f e r e n t r e d u c t i o n z o n emm s e g8s e g9s e g10s e g11方案12220方案20222方案30330㊀㊀铸坯的压下区间分别是第8㊁9㊁10和11段,选取上节得到的适宜压下量6mm.提取铸坯高温脆性区内关键点的应力最大值,如图16所示.虽然总压下量相同且未超过极限压下量,但是不同压下区间的主应力变化范围差距较大,无压下时铸坯的主应力最大值为1.99M P a,方案1的主应力最大值为3.08M P a,方案2为2.97M P a,方案3为4.96M P a.方案1和方案2压下量平均分布在3个区间内,其主应力最大值大小相近,均未超过临界应力值3.72M P a,而方案3压下量平均分布在两个区间内,其主应力最大值大于前两种方案,且超过了临界应力值.8791中国机械工程第33卷第16期2022年8月下半月Copyright©博看网. All Rights Reserved.图16㊀不同压下区间的应变与应力最大值F i g.16㊀S t r a i na n dm a x i m u ms t r e s s o f d i f f e r e n tr e d u c t i o n z o n e无压下时铸坯的应变最大值为1.71%,方案1~3的应变最大值分别为1.75%㊁1.76%和2.53%.方案1和方案2应变最大值大小相近,远小于临界应变值2.88%,方案3应变最大值接近临界值,且比方案1大44.57%,采用方案3的压下方案可减小铸坯此区段的极限压下量.铸坯不同压下区间的窄面鼓肚变形量如图17所示.无压下时铸坯的窄面鼓肚变形量会随着时间不断减小,有压下时方案1的变形量最小,每个压下区段的变形增量也最小,方案3的变形量最大,变形量最大值比方案1大1.3mm .图17㊀不同压下区间的窄面鼓肚F i g.17㊀N a r r o wb u l g e s i z e o f d i f f e r e n t r e d u c t i o n z o n e在压下量相同的情况下,若压下区段较后,则坯壳较厚,变形抗力大,压下困难;减少压下区段的方案会减小铸坯的极限压下量,因为压下区段少,每段分配的压下量会增加,使得铸坯压下时变形抗力增大,高温脆性区所受应力应变增大,应力最大值4.96M P a超过了临界值.因此在凝固末端适宜的压下区间为第8~10段.2.3㊀不同压下分配对压下结果的影响从上节可以看出,不同的压下分配会对铸坯的压下结果产生影响,本节保证压下区间和压下量不变,通过改变不同的压下分配(均布压下量,大压下量分别置于压下区域前中后位置)时对铸坯内部力学性能的影响,探究压下量的适宜分配方式,其中,不同压下分配的压下方案见表4.表4㊀不同压下分配的压下方案T a b.4㊀R e d u c t i o n s c h e m e sw i t hd i f f e r e n t r e d u c t i o nd i s t r i b u t i o n mms e g8s e g9s e g10方案1222方案2114方案3141方案4411方案5123方案6321㊀㊀采用6m m的压下方案,选取压下区间为第8㊁9㊁10段.提取铸坯高温脆性区内关键点的主应力最大值和应变最大值见表5.关于主应力最大值,方案1压下时为3.28M P a,方案2为4.41M P a,方案3为5.04M P a,方案4为5.04M P a,方案5为4.64M P a,方案6为4.72M P a.采用平均分配压下量的方案时主应力最大值最小,未超过其临界应力值,而不均匀的分配方案主应力最大值较均匀分配的方案有所增大,且超过了临界应力值.在应变方面可以看到,方案1均匀分配方案的应变最大值为1.75%,是所有方案中最小的,其他不均匀分配的最大应变值均超过了临界应变值,会减小铸坯的极限压下量.铸坯不同压下分配的窄面鼓肚变形量如图18所示.方案1和方案2的鼓肚变形量最大值比其他方案小,方案4与方案6由于首段压下量分配太大,从开始压下便保持在很高的数值,会影响铸坯的压下质量.表5㊀不同压下分配的应力应变最值T a b.5㊀T h em a x i m u mv a l u e o f s t r e s s a n d s t r a i nw i t hd i f fe r e n t r e d u c t i o nd i s t r i b u t i o n方案主应力最大值(M P a)应变最大值(10-2)13.281.7524.413.1935.044.1645.043.7154.643.4164.723.45㊀㊀在压下量相同的情况下,均匀分配压下量的方案使铸坯在压下过程中所受应力应变缓慢增加,变形抗力较小,未超过内裂纹生成的临界应力应变值,压下效果最好.非均匀分配压下量的方案使铸坯在大压下量区段产生应变突变和较大的鼓肚变形,应力应变的变化范围大,若超过临界应力应变值,则会有产生裂纹的可能性.因此采用均布压下方式有利于改善压下质量.9791连铸轻压下过程极限压下量及工艺参数分析 秦㊀勤㊀王文智㊀张㊀升等Copyright©博看网. All Rights Reserved.。
大方坯连铸动态轻压下位置的确定

在热传导计算的基础上,对连铸大方坯进行了热应力计算。为进一步将凝固传热 模型和轻压下模型耦合在一起,分析连铸坯在轻压下过程中的应力-应变关系提供理 论基础。
Abstract
The soft reduction technique at the solidifying terminal is one of the effective methods to decrease the center segregation and center porosity, and it has been widely used in many plants abroad and achieved obvious metallurgical effect. The VAI’s soft reduction technique were introduced in the new bloom caster at Panzhihua Iron&Steel Company, Panzhihua commissioned successfully in September 2003, Pan-steel is the first plant to use soft reduction in bloom caster(280 mm×380mm) to produce the heavy rail steel in china. The parameters and the mathematical model of soft reduction are a ‘black box’ because of technique secrecy. The aim of this study is to definite the position of continuous casting bloom on the soft reduction so as to provide theory basis to detect the soft reduction.
轻压下控制系统在小方坯连铸机上的应用

旁. 拉 矫 机 液压 缸 上 安 装 内置 式 位
置 传 感 器控 制 压 下 的距 离 . 液 压 系 统 采 用 闭环 伺 服 控制 . 能够 根 据 拉 矫 机 液 压缸 的位 置 . 迅 速地 调 节 液 压 流量 . 闭环控制压下精 度 , 保 证
监视 设定 值
在 常规 压
统 包括 一 级 H MI 系统 、 二级 计算 机
系 统 、与 铸 流 P L C通 讯 、轻 压 下 P L C、 网络 系统 组成 , 轻压下 P L C采
通 过 对过 热 度 、 拉 速 和二 冷 条
1 轻 压 下 控 制技 术
轻压 下 技术 是 集 设 备 、液 压 、
地 在线 调整 拉矫 机 的辊缝 值 。拉矫 机 轻 压 下 控 制 系 统 由 以 下 硬 件 和 软件 系 统组 成 ( 见图 1 ) 。主要 组 成 有: 拉矫机液压 油缸 ; 拉 矫 机 液 压
轻 压 下控 制 系统在 小 方坯 连铸 机上 的应 用
陈 良 华
( 中冶连铸 技 术工程 股份 有 限公 司 湖北 武 汉 4 3 0 0 7 3 )
摘 要 : 介 绍一 种轻 压下 控制 系统 。 为提 高小方坯 连铸 机 生产 高碳 钢 的产 品质 量 , 配置 了轻 压 下控 制 系统 通 过在 1 5 0 mm ̄ 1 5 O m m 断 面和 1 6 5 m mx 1 6 5 mm 断 面 小方 坯 连铸 机 上 的应 用证
3 控 制 系统 配 置
轻 压 下 控 制 系 统 配 置
S I E ME N S S 7 —4 o 0 P L C ( 每流 1
动态轻压下技术在莱钢厚板连铸机上的应用
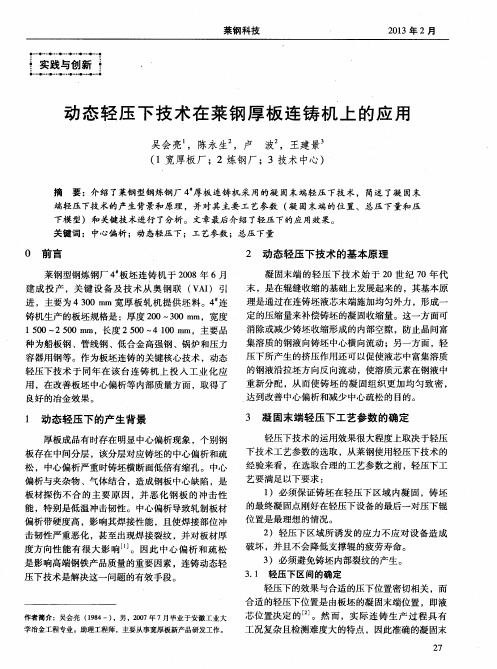
1 动态 轻压 下的产生背景
厚板成品有时存在明显中心偏析现象 ,个别钢 板存在中间分层 ,该分层对应铸坯的中心偏析和疏
松 ,中心 偏 析严 重 时铸 坯横 断 面低倍 有 缩孔 。 中心 偏析 与夹 杂 物 、气 体结 合 ,造成 钢板 中心缺 陷 ,是 板材 探伤 不 合 的 主 要 原 因 ,并 恶 化 钢 板 的 冲击 性 能 ,特别 是低 温 冲击韧 性 。 中心偏析 导 致轧制 板 材
合适的轻压下位置是由板坯 的凝 固末端位置 ,即液 芯位置决定 的 。然而 ,实际连铸 生产过程 具有
工况 复杂 且检测 难 度大 的特 点 ,因此 准确 的凝 固末
2 7
吴会 亮 ,等 :动 态轻 压 下技 术在 莱钢 厚板 连铸 机 上的应 用 端位 置 预测是 动 态轻 压下 实现 的必 要 条件 。压 下位 置是 根据 中心凝 固率 确定 的。 目前 ,对于 压下 区间 没有 一个 定值 ,一般 企业 都是 根据 试 验修 正后 取得 最佳 值 ,它 与 钢 的成 分 、铸 坯 断 面 及 生 产 设 备 有 关 。济 南钢铁 公 司 引进奥 钢联 的中厚 板铸 机压 下 区 间为 f s = 0 . 5~ 0 . 9 5 mm,铸坯 质量 良好 。考 虑到 连 铸机 本 身 的设 计 ,莱 钢 4 铸 机压 下 区 间设 定 为 f s =
是影响高端钢铁产品质量的重要因素 ,连铸动态轻
压下技术是解决这一问题 的有效手段 。
3 )必须避免铸坯 内部裂纹的产生。
3 . 1 轻 压下 区 间的确 定
轻压下的效果与合适的压下位置密切相关 ,而
作者简介 :吴会亮 ( 1 9 8 4 一) ,男 , 2 0 0 7 年7 月毕业 于安徽工业 大 学冶金工程专业。助理工程师 ,主要从事宽厚板新产品研 发工作。