硫酸生产新工艺研究进展
硫酸生产总结报告范文(3篇)

第1篇一、前言随着我国经济的快速发展,硫酸作为重要的基础化工原料,在化肥、农药、染料、石油、冶金等行业中发挥着不可替代的作用。
本报告旨在对2022年度硫酸生产工作进行总结,分析存在的问题,提出改进措施,以促进硫酸生产工作的持续改进和发展。
二、2022年度硫酸生产工作回顾1. 生产任务完成情况2022年,我公司在硫酸生产方面,紧紧围绕公司年度目标,充分发挥生产设备潜力,加大生产力度,确保了生产任务的顺利完成。
全年硫酸产量达到XX万吨,同比增长XX%,创历史新高。
2. 技术改造与设备维护为提高硫酸生产效率和产品质量,我们积极开展技术改造和设备维护工作。
一是对关键设备进行升级改造,提高了设备运行稳定性;二是对生产流程进行优化,降低了生产成本;三是加强设备点检和维护,确保设备安全运行。
3. 产品质量与安全环保在产品质量方面,我们严格执行国家标准,加强生产过程质量控制,全年硫酸产品合格率达到XX%,高于行业平均水平。
在安全环保方面,我们持续加强安全管理,严格落实环保措施,确保了生产过程安全环保。
4. 人员培训与团队建设为提高员工素质,我们积极开展各类培训活动,提高员工的专业技能和综合素质。
同时,加强团队建设,培养一支高素质、高效率的生产团队。
三、存在的问题与不足1. 生产成本较高尽管我们采取了一系列措施降低生产成本,但与同行业先进企业相比,我公司在生产成本方面仍有较大差距。
主要原因是原材料价格波动较大,设备老化,部分生产工艺落后等。
2. 产品质量稳定性有待提高虽然全年硫酸产品合格率较高,但仍有部分批次产品质量不稳定,主要表现在硫酸含量、杂质含量等方面。
这需要我们进一步加强对生产过程的质量控制。
3. 安全环保压力依然较大虽然我们加强了安全环保管理,但仍存在一定压力。
主要表现在环保设施投入不足,部分员工安全意识薄弱等方面。
四、改进措施及建议1. 降低生产成本(1)优化采购策略,降低原材料采购成本;(2)加强设备管理,提高设备利用率,降低设备折旧费用;(3)改进生产工艺,提高生产效率,降低单位产品能耗。
硫酸烧渣提金新工艺和新设备

硫酸烧渣提金新工艺和新设备一.硫酸烧渣提金技术现状与研究方向目前我国黄金资源的利用明显出现勘探跟不上生产要求的局面,制约着我国黄金产量的提高,与此同时,从含金废料中和难选矿石中回收金的技术和扶持政策却不够理想,这部分金资源尚未得到充分的利用.含金硫酸烧渣回收金技术急待开发.我国每年产生含金硫酸烧渣几十万吨,目前仅大于3克/吨的烧渣得以利用.每年仅有7.5万吨的处理能力,其余烧渣或废崐弃或以十几元/吨的价格出售给水泥厂做原料,•所含黄金白白流失,十分可惜.从国内外的技术文献看,从烧渣中回收金的技术也只限于氰化工艺,重选、浮选、磁选、硫脲工艺等均处于研究阶段.现时的氰化工艺仅适合处理金品位高于2.5克/•吨的硫酸烧渣,品位再低则利润太低,投资难以在短期内收回,因此尽管具有较好的社会效益,但经济效益不明显而无建提金厂的积极性;堆浸法虽然能使生产成本降低,•但不能连续生产而且冬季无法生产,因此这种工艺也难以推广;重选、•磁选和浮选均能崐回收烧渣中的一部分金,但回收率不如氰化法高而且从产生的精矿中再回收金时回收率不理想,也难以推广.•硫脲法药剂成本高且浸出条件不易控制,溶液中金的回收尚满意的方法,•还处在探索阶段,距工业应用尚远.我们认为,影响从烧渣中提金的主要因素有两个,•一是投资过大、二是生产成本过高.如果能解决这两个问题,•低品位硫酸烧渣提金技术将被顺利推广.通过对我国推广使用的氰化法工艺进行研究,发现该工艺存在如下问题:1.长春黄金研究院的多年研究证明,硫酸烧渣不须再磨氰化浸出率就能保证,采用磨矿工段的目的仅仅是为了保证氰化反应时矿浆被搅拌均匀,不沉槽.磨矿工段投资达40余万元,生产成本高达15元/吨,如果能通过其它办法砍掉该工段,氰化法的崐投资和生产成本会大幅度下降.2.由于靠排放磨矿后浓密机溢流进行洗矿--•除去烧渣中溶出的铁铜等杂质,在磨矿过程中就不能加氰化物,•因此贫液也不能全部循环使用,贫液处理后排放不但使生产成本提高,•还产生环境污染问题,在一些环境质量要求高的地区,•环保部门就不会批准建氰化厂.3.不少硫酸厂建在城市内•,无足够的场地建较大的尾矿库.采用现在的氰化工艺时,无论用锌粉置换还是用炭浆法,•都必须过滤氰尾分离出废渣,用机动车把渣运到它处.•过滤工段增加了投资,又因磨矿使渣粒度变细增加了过滤难度、增加了生产成本.4.采用锌粉置换将使贫液中锌浓度不断增加,恶化浸出条件,造成金回收率降低;由于烧渣硬度大,用炭浆法炭磨损大,金流失多,生产成本增高.5.氰化法的最大不足不在于反应时间太长,一般至少要16小时,这就要求建很大体积的浸出槽,投资增大、电耗增加,厂房面积增加.综上所述,从低品位硫酸烧渣中提金必须开发新的浸出技术或新的工艺,降低投资和成本.•其具体研究内容包括以下几个途径:1.使用新的浸出设备,不磨矿即可保证浸出反应顺利进行.•而且浸出电耗不增加或增加较少.2.使用浸出速度快的浸出方法,浸出时间仅几小时或更短.•可增加搅拌强度来保证浸出效果,由于反应时间短,•单位电耗也不会增加很多.3.采用贫液全循环工艺,不外排废水,节约废水处理费用,节约浸出药剂.4.用固定床吸附法从贵液中回收金,不设洗涤工段或炭浆工段,浸后直接过滤,提高贵液金浓度以使吸附剂上金品位提高,•减少设备投资和生产成本.通过大量的研究和试验,选择了水氯法工艺.•小试结果表明,浸出率比氰化法高,•其原因是氰化过程中烧渣颗粒上金表面产生阻碍金浸出和扩散的膜.均由烧渣的性质决定--氰尾渣制酸时的焙烧温度致关重要.二.新工艺和新设备的技术经济指标1.技术工艺指标金回收率: 55%浸出时间: 3min •石灰耗量: 3kg/t电耗: 15kwh/t水耗: 0.15m3•/t 液氯耗量: 3kg/t投资: 80万元生产成本: 38.6元•/t 生产人员: 35人2.黄金产量和产值、利润按每年生产300天,处理能力为•100m3•/d,烧渣金品位1.5g/t,回收率55%计,产金量如下:每吨烧产金量: 1×1.5×55%=0.825g日产黄金: 100×0.825=82.5g年产金量: 300×82.5=24750g每吨烧渣产值: 0.825×96=79.2元日产值: 100×79.2=0.792万元年产值: 300×0.792=237.6万元年利润: 300×100×(79.2-38.6)=120万元按100万元投资计算,返还期为10个月.用本工艺提金的最低经济品位为0.75g/t.3.新工艺与常规氰化工艺比较新工艺:4.新式固液分离设备的特点常规固液分离设备有板框压滤机、带式过滤机、浓密机,板框压滤机的配套高压泵易损不易防腐,而且在压滤前要设搅拌槽平衡流量,设备投资达150万元,电耗大;带式真空过滤机过滤带易损,不易防止氯的腐蚀,投资达200万元;浓密机不易处理大颗粒物料.而且防腐也不易,占地大,投资达150万元.新式固液分离设备类似池浸用的浸出池,多池串联,上部设溢液口,下部设分布板,矿浆进入后,大颗粒物料很快沉降到池下部,水颗粒物料将通过溢液口向后面的池中流去,经过较长时间的沉降,较清的贵液从固液分离设备中流出,进入吸附工段.待前面的池中充满浸渣后,打开分布板下面的排液阀并从池上部加水洗涤,从分布板下液出的贵液也进入吸附工段.新设备用混凝土制成,涂以防腐材料即可.投资仅30万元.三.新工艺和设备的优点浸出方法的优点:1.本浸出方法使用工业上广泛使用的氯气(开始使用少量食盐)做浸出药剂及少量助剂,避免了氰化物的污染,使用的助剂降低氯气的消耗,使其药剂成本低于氰化法.2.本方法浸出时间仅3分钟,因此浸出设备有效容积仅为氰化法的0.2%~0.4%,以处理能力100t/d的工厂为例,浸出设备有效容积仅0.3立米.不但投资可减少20%,浸出的电耗也可降低4~5kwh/t.新式浸出设备的优点:采用新式反应器,适应大颗粒物料的浸出.常规浸出设备只适用于处理200目以下的矿浆,否则就会出现"沉槽"、压搅拌浆等故障.本设备容积很小,采用其它方法解决反应器问题,避免搅拌不均.新式固液分离设备具有投资少、生产成本低、易防腐等特点.现有的过滤设备不能解防腐问题,而且价格很高,大约需要投资100万元,新式固液分离设备投资仅30万元.新工艺的优点:1.省去了磨矿及相应的分级、浓密设备,减少投资40%左右;节省占地400平米;减少材料消耗10元/t;减少电费5元/t;减少操作工3--6人.2.不磨的烧渣本身粒度较大,一般在-80目占70%以上,40-80目占25%左右,其余5%在20-40目之间,沉降速度快.特别适合用新式固液分离设备进行液固分离.这种设备易于操作.与氰化工艺相比,省去了浓密机和压滤机,易于控制浸出液物量平衡.3.选用活性炭吸附法回收浸出液中的金,考虑到在吸附过程中可能产生沉淀物,采用我单位已获专利的吸附槽.吸附装置投资仅2万元.4.由于在酸性含氯溶液中吸附金氯络合物,并使金离子最终转变为单质金.因此载金炭上金品位至少可富集到10kg/t,采用焚烧—王水溶解—还原的联合工艺即可生产出纯金.冶炼工艺设备简单,仅使用常规药剂,与氰化法比,冶炼工段节约设备投资30万元,冶炼成本也低于常规工艺.5.贫液中杂质主要是铁、锌和铜,可用石灰沉淀,分离掉杂质的溶液可循环使用;由于不断加氯,浸出液的酸度将不断增加,加石灰除杂的过程还会起到调节酸度的作用.6.与常规氰化工艺相比,采用本工艺建设100t/d处理能力的提金厂,可节约设备投资80万元,降低生产成本30元/t.使那些用氰化法处理没有利润的低品位烧渣提金成为可能,换句话说,使烧渣的提金经济品位大幅度降低.以处理能力100t/d的工厂为例,投资60~80万元,供电不超过50kw,处理成本约40元/t,即使烧渣品位低至1.5g/t,浸出率为55%,年利润也可达到100万元.我国有这类烧渣的工厂至少10座,金品位都在2g/t以下,如果推广本工艺,每年至少回收金250kg.利润1000万元以上.硫酸烧渣提金工艺设计一.工艺数据1.处理能力: 100t/d2.浸出液浓度: 氯气1.5kg/M3 PH=1.5-2.5 Cl-4kg/M33.液固比: 2~5:14.反应时间: 3 分钟5.反应类型: 全返混6.液固分离方法:新式固液分离设备7.贵液中金回收方法:活性炭固定床吸附法8.贫液循环措施:石灰中和沉淀杂质后再循环9.金浸出率:55%10.废气处理方法: 烧碱液吸附再利用二.原料1.烧渣金品位:1.67克/t2.液氯3.石灰4.活性炭:木质炭或果核炭5.自来水6.烧碱三.物料流量1.硫酸烧渣: 4.17t/h2.浸出液流量: 8.34~20M3/h3.活性炭吸附剂用量: 1t4.废气处理排气量: >500M3/h收液流量: 2-4M3/h 四.工艺流程。
硫酸法生产碳酸锂工业代码

硫酸法生产碳酸锂工业代码摘要:一、背景与意义二、硫酸法生产碳酸锂的原理三、硫酸法生产碳酸锂的工艺流程四、硫酸法生产碳酸锂的优缺点五、我国在该领域的现状与展望正文:一、背景与意义随着新能源产业的快速发展,特别是电动汽车和储能领域的广泛应用,碳酸锂市场需求持续旺盛。
硫酸法生产碳酸锂作为一种重要的生产方法,具有较高的经济价值和环保意义。
本文将详细介绍硫酸法生产碳酸锂的原理、工艺流程以及优缺点,并探讨我国在该领域的现状与展望。
二、硫酸法生产碳酸锂的原理硫酸法生产碳酸锂主要利用硫酸锂与碳酸钠反应生成碳酸锂的原理。
首先将含锂矿石粉碎、混合、溶解,得到硫酸锂溶液。
然后将硫酸锂溶液与碳酸钠溶液混合,通过过滤、洗涤、干燥等步骤,得到碳酸锂产品。
三、硫酸法生产碳酸锂的工艺流程1.含锂矿石的粉碎与混合:将含锂矿石进行粉碎,使其达到一定的细度,然后与适量的硫酸混合均匀。
2.硫酸锂溶液的制备:将混合物加入水中,搅拌均匀,得到硫酸锂溶液。
3.碳酸钠溶液的制备:将碳酸钠溶解在水中,得到碳酸钠溶液。
4.反应与分离:将硫酸锂溶液与碳酸钠溶液混合,充分搅拌,使硫酸锂与碳酸钠发生反应,生成碳酸锂沉淀。
5.过滤、洗涤与干燥:将反应混合物进行过滤,得到碳酸锂沉淀。
将沉淀物洗涤干净,然后进行干燥,得到碳酸锂产品。
6.产品质量检测与分级:对碳酸锂产品进行质量检测,根据不同品质要求进行分级。
四、硫酸法生产碳酸锂的优缺点优点:1.原料成本较低,利用含锂矿石资源丰富。
2.生产工艺相对简单,易于实现自动化控制。
3.产品纯度较高,有利于后续深加工。
缺点:1.生产过程中产生一定量的硫酸钠废水,环保处理成本较高。
2.对含锂矿石的品质要求较高,部分低品位矿石难以利用。
3.设备腐蚀较严重,影响设备使用寿命。
五、我国在该领域的现状与展望近年来,我国硫酸法生产碳酸锂技术取得了显著进展,产业规模不断扩大。
然而,在面对国际市场激烈竞争的背景下,我国仍需加强以下方面:1.提高生产效率,降低生产成本。
硫酸工艺和设备选择中的节能问题研究
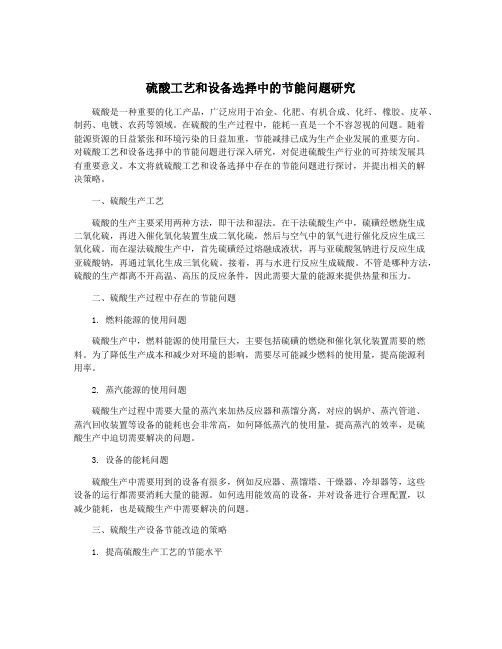
硫酸工艺和设备选择中的节能问题研究硫酸是一种重要的化工产品,广泛应用于冶金、化肥、有机合成、化纤、橡胶、皮革、制药、电镀、农药等领域。
在硫酸的生产过程中,能耗一直是一个不容忽视的问题。
随着能源资源的日益紧张和环境污染的日益加重,节能减排已成为生产企业发展的重要方向。
对硫酸工艺和设备选择中的节能问题进行深入研究,对促进硫酸生产行业的可持续发展具有重要意义。
本文将就硫酸工艺和设备选择中存在的节能问题进行探讨,并提出相关的解决策略。
一、硫酸生产工艺硫酸的生产主要采用两种方法,即干法和湿法。
在干法硫酸生产中,硫磺经燃烧生成二氧化硫,再进入催化氧化装置生成二氧化硫,然后与空气中的氧气进行催化反应生成三氧化硫。
而在湿法硫酸生产中,首先硫磺经过熔融成液状,再与亚硫酸氢钠进行反应生成亚硫酸钠,再通过氧化生成三氧化硫。
接着,再与水进行反应生成硫酸。
不管是哪种方法,硫酸的生产都离不开高温、高压的反应条件,因此需要大量的能源来提供热量和压力。
二、硫酸生产过程中存在的节能问题1. 燃料能源的使用问题硫酸生产中,燃料能源的使用量巨大,主要包括硫磺的燃烧和催化氧化装置需要的燃料。
为了降低生产成本和减少对环境的影响,需要尽可能减少燃料的使用量,提高能源利用率。
2. 蒸汽能源的使用问题硫酸生产过程中需要大量的蒸汽来加热反应器和蒸馏分离,对应的锅炉、蒸汽管道、蒸汽回收装置等设备的能耗也会非常高,如何降低蒸汽的使用量,提高蒸汽的效率,是硫酸生产中迫切需要解决的问题。
3. 设备的能耗问题硫酸生产中需要用到的设备有很多,例如反应器、蒸馏塔、干燥器、冷却器等,这些设备的运行都需要消耗大量的能源。
如何选用能效高的设备,并对设备进行合理配置,以减少能耗,也是硫酸生产中需要解决的问题。
三、硫酸生产设备节能改造的策略1. 提高硫酸生产工艺的节能水平对于干法和湿法硫酸生产工艺,可以采用新型催化剂、反应器的优化设计等方式来提高反应效率,从而减少能源和原料消耗。
利用硫酸渣生产铁精粉的新工艺研究

利用硫酸渣生产铁精粉的新工艺研究
利用硫酸渣生产铁精粉是一种新型工艺,它可以将废弃的硫酸渣转化为有用的铁精粉。
以下是对该工艺的研究内容:
1. 硫酸渣特性研究:对不同来源的硫酸渣进行化学分析和物理性质测试,了解其成分、含铁量、颗粒大小和形态等特性。
2. 硫酸渣预处理:对硫酸渣进行预处理,包括破碎、磨细、磁选等步骤,以提高铁含量和改善颗粒形态,使其更适合后续的铁精粉生产工艺。
3. 铁精粉生产工艺优化:根据硫酸渣的特性和预处理结果,设计出适宜的铁精粉生产工艺。
可能包括浸出、还原、沉淀、过滤、干燥等步骤,以得到高品质的铁精粉。
4. 工艺参数研究:对铁精粉生产过程中的关键参数进行研究,如浸出温度、还原剂种类和用量、沉淀pH值等,以确定最佳
工艺条件,提高产率和产品质量。
5. 产品性能评价:对产生的铁精粉进行性能评价,包括化学成分分析、颗粒大小和形态分析、磁性测试等,以确定产品是否符合相关标准和应用要求。
6. 应用研究:探索不同领域中利用铁精粉的应用,如钢铁生产、磁性材料制备、催化剂等,并进行性能测试和效果评估,以确定其实际应用价值。
综上所述,利用硫酸渣生产铁精粉的新工艺研究涉及硫酸渣特性分析、预处理、铁精粉生产工艺优化、工艺参数研究、产品性能评价和应用研究等方面。
通过对这些研究内容的深入探究,可以开发出高效、节能、环保的铁精粉生产工艺,实现废弃物资源化利用和循环经济的目标。
硫酸的生产工艺原理原材料

硫酸的生产工艺原理原材料硫酸是一种非常重要的化工原料,在工业生产中有着广泛的用途。
其生产工艺可以使用多种方法,其中较为常见的是铁铜法、硫铁矿法和沸腾床法。
1. 铁铜法铁铜法是硫酸的传统生产方法,主要原料有硫矿石、空气和水。
具体步骤如下:(1)将硫矿石(FeS2)粉碎成适当的颗粒,并与石灰石(CaCO3)混合,然后放入焙烧炉中进行煅烧。
(2)煅烧过程中,硫矿石中的硫形成二氧化硫(SO2),并与空气中的氧气反应生成二氧化硫气体。
(3)二氧化硫进入冷却器后与一定浓度的硫酸接触,生成浓硫酸。
冷却器中有装有铜制的塔板,用于增加反应表面积和提高反应效果。
(4)煅烧产生的副产物熔渣和尾气中的污染物经过处理,可以得到硫酸和其他有用的工业原料。
2. 硫铁矿法硫铁矿法是较为常用的硫酸生产工艺,其原料主要包括硫矿石、石灰石和空气。
具体步骤如下:(1)将硫矿石和石灰石按一定比例混合,并经过破碎和煅烧过程,形成熔池。
(2)空气通过熔池中的熔渣,与硫矿石中的硫反应生成二氧化硫气体。
(3)二氧化硫气体进一步氧化生成三氧化硫(SO3),并通过冷却器与水接触,生成浓硫酸。
(4)熔渣经过处理和回收后,可用于再次煅烧。
3. 沸腾床法沸腾床法是一种相对较新的硫酸生产工艺,其基本原理是通过气固两相流在反应器中进行反应。
主要原料为硫矿石粉和空气。
具体步骤如下:(1)将硫矿石粉碎成适当颗粒,并与催化剂(如氧化铈或氧化锆)混合,然后放入沸腾床反应器中。
(2)反应器中加热床层的空气通过中央喷管喷入,床层中的硫矿石粒子被悬浮并与空气中的氧气发生反应,生成二氧化硫。
(3)二氧化硫通过床层顶部的乙醚洗涤塔,与乙醚溶液接触,生成硫酸。
乙醚洗涤塔中的乙醚会被硫酸溶解,生成稀硫酸。
(4)沸腾床反应器中的煤气经过处理和回收后,可用于再次循环使用。
综上所述,硫酸的生产工艺原理中常用的方法有铁铜法、硫铁矿法和沸腾床法。
不同的方法在原料和反应步骤上略有差异,但基本原理都是利用硫矿石与空气反应生成二氧化硫,再通过氧化和冷却与水接触,生成硫酸。
硫酸生产工艺工作总结

硫酸生产工艺工作总结
硫酸是一种重要的化工产品,广泛应用于冶金、电镀、化肥、医药等领域。
硫
酸的生产工艺是一个复杂的过程,需要严格控制各个环节,以确保产品质量和生产效率。
在硫酸生产工艺中,主要包括硫磺燃烧、吸收、转化和结晶等环节。
首先,硫磺燃烧是硫酸生产的第一步。
硫磺燃烧产生的二氧化硫气体通过冷却
和净化后,进入吸收塔进行吸收。
在吸收塔中,二氧化硫气体与稀硫酸溶液接触,发生化学反应生成浓硫酸。
吸收过程需要控制吸收塔的温度、压力和流速,以确保吸收效果和产品质量。
接下来是硫酸的转化过程。
吸收后的浓硫酸溶液经过蒸馏、氧化等工艺步骤,
转化成浓硫酸。
在转化过程中,需要严格控制反应温度、压力和反应时间,以保证反应的完全和产品的纯度。
最后是硫酸的结晶过程。
浓硫酸溶液经过结晶器结晶,生成硫酸晶体。
结晶过
程需要控制结晶温度、搅拌速度和结晶时间,以确保产品的结晶度和颗粒大小。
在硫酸生产工艺中,需要严格遵守操作规程,严格控制生产过程中的各项参数,确保产品质量和生产安全。
同时,还需要加强设备维护和管理,确保设备的正常运行和生产效率。
通过不断优化工艺流程和技术手段,提高生产效率和产品质量,降低生产成本,实现可持续发展。
总之,硫酸生产工艺是一个复杂的过程,需要严格控制各个环节,确保产品质
量和生产效率。
通过不断优化工艺流程和技术手段,提高生产效率和产品质量,降低生产成本,实现可持续发展。
尿素硫酸复肥生产新工艺研究

摘 要 : 对 尿 素 硫 酸 复 肥 生 产 工 艺 现 状 及 研 究 进 展 分 析 的 基 础 上 , 用 开 阳 矿 进 行 了 优 惠 工 艺 条 件 选 择 的 实 验 在 利 可 得 到 N—P O5为 1 . 2 8 5—8 5的 产 品 , 矿 转 化 率 在 8 % 以 上 , 可 一 步 制 得 复 合 肥 。 . 磷 5 并 关 键 词 : 矿 ; 混 肥 ; 素 ; 酸 硫 酸 脲 磷 复 尿 硫
到 适 应 我 国 特 有磷 矿 的 尿 素 一过 磷 酸 钙 系 肥料 工
收 稿 日 期 :0 2—0 20 2—0 9
・
酸 解 液 和 磷 矿 反 应 、 应 液 中 和 及 喷 浆 造 粒 、 成 反 半
品的 加 工 。这 种 工 艺 为 满 足 喷 浆 造 粒 的 要 求 , 酸 解 液 的 水 分 量 较 文 献 [ ] 5 6倍 , 此 后 续 处 1高 ~ 为
维普资讯
・
试验 研究 ・
文章 编号 : 0 8—7 2 2 0 0 10 5 4(0 2)9~0 1 0 4—0 3
I &P 化 I 矿 物 与 加 I M
20 0 2年 第 9期
尿 素 硫 酸 复 肥 生 产 新 工 艺研 究
侯 翠 红 , 宝林 , 光龙 , 登 高 张 王 蒋
硫酸 尿 素 溶 液 ( 称 酸 解 液 ) 制 备 , 酸 解 液 与 简 的 和 磷 矿一步反 应并成 粒 。为 使成粒 能 够均 匀进行, 加 入 相 当于 磷 矿 处 理 量 2 % ~5 %的 成 品 返 料 。 0 0
由 于 颗粒 的 硬 化 以 及 反 应 完 全 需 要 1 0~2 h 因 0, 而 工 业 上 , 将 反 应 和 造 粒 分 成 两 步 进 行 。 文 献 又 [] 出 的 工 艺 原 则 上 分 为 四 步 , 酸 解 液 制 备 、 3提 即
总结硫酸生产工艺

总结硫酸生产工艺硫酸是一种广泛应用于化工、冶金、环保等行业的重要化工原料。
目前,硫酸的生产主要在工业规模上存在两种工艺:硫磺制酸法和硫氧化制酸法。
以下是对这两种工艺的简要总结。
一、硫磺制酸法:硫磺制酸法是一种传统的硫酸生产工艺,其主要步骤包括硫磺的燃烧、氧化产生二氧化硫、氧化反应生成三氧化硫、与水反应生成硫酸的吸收过程。
硫磺燃烧:硫磺通过燃烧产生二氧化硫。
传统的硫磺制酸法采用炉窑燃烧硫磺,炉温控制在1200-1300℃,燃烧后产生硫磺氧化物。
氧化反应:氧化反应是硫磺制酸的关键步骤,其中的氧化反应主要有两步:硫磺氧化生成二氧化硫,二氧化硫进一步氧化生成三氧化硫。
这两个反应是通过催化剂的存在来加速进行的。
硫酸吸收:三氧化硫与吸收剂(通常为浓硫酸)进行反应,生成硫酸。
反应发生在吸收塔中,通过吸收器的设置,将吸收剂花洒在塔上,与上方从塔底部喷出的三氧化硫气体进行接触,吸收生成硫酸的气体。
二、硫氧化制酸法:硫氧化制酸法是一种比较新的硫酸生产工艺,主要步骤包括硫的含氧化物的形成、催化剂催化转化、尾气净化和吸收生成硫酸的过程。
硫化物氧化:硫化物氧化是硫氧化制酸的关键步骤,其中的硫化物可以来自于石油加工过程产生的硫化氢和石膏、矿石中的硫酸盐等。
硫化物在反应器中通过氧化剂(如空气或氧气)氧化生成硫的含氧化物。
催化剂催化转化:在氧化反应中,硫的含氧化物通过催化剂的作用进行催化转化,生成二氧化硫。
尾气净化:硫氧化制酸法中产生的尾气中含有二氧化硫和少量的氧化副产物,需要通过脱硫、脱氮等净化工艺进行处理,以达到环保要求。
吸收生成硫酸:净化后的气体进入吸收器,与硫酸或硫酸溶液进行接触,吸收生成硫酸的气体。
总结:目前,硫磺制酸法和硫氧化制酸法是较为常用的硫酸生产工艺。
硫磺制酸法是传统的工艺,流程较为简单,但存在炉温高、能源消耗大等缺点。
而硫氧化制酸法相对较新,流程中采用催化剂催化转化,在尾气净化方面更加环保,但在硫化物氧化和脱硫等方面存在一定的技术难度。
硫酸锰生产新工艺的研究_田宗平

析 , 做到了对生产过程科学 、准确 、及时地控制 ; 4)设计了隔绝空气的快速冷却方式 , 在使用二
氧化锰[ MnO2 ≥25 %(质量分数)] 矿粉的生产中 , 确 保了焙烧还原率 93 %以上 ;
5)优化采用了热能的循环利用方式 , 大大降低 了生产过程中的能源消耗 ;
现了矿粉中二氧化锰的综合利用率在 85 %以上的 工业生产效果 ;但渣量较大 、能耗偏高 、工艺控制难 度大和渣中硫 含量高不便综合利用等 是该法的弊 端 ;随着二氧化锰和硫铁矿等原材料价格的攀升 , 硫 酸锰生产成本急剧上涨 , 工厂生产利润率越来越少 。
针对上述状况 , 本文结合工业实践 , 分析与研究 了各种老式窑炉焙烧还原法和两矿加酸法生产硫酸 锰工艺 , 通过对资源利用 、能源消耗和环境保护等 3 方面的研究 , 找到了工艺研究的突破口 。
粉碎是将焙烧砂粉碎至 150 μm 以下的工序 , 其目的是确保能迅速 、有效地将矿粉中的一氧化锰 被硫酸浸出和后续工序高效进行 。 为确保工业生产 的最佳效果 , 粉碎设备我们使用了能最有效控制粉 碎产品粒度和便于粉尘收集和处理的雷磨机 。 2.4.3 酸浸与除杂
酸浸与除杂是提高资源利用效益 、降低成本和 生产优质产品的重 要工序 。 经 过长期的研究 与实 践 , 制定了本工序的操作规程 :第 1 , 根据焙 烧砂中 锰含量计算出单桶所需投加的矿粉量 , 并做到准确 计量 ;第 2 , 根据试验获取的酸矿比数据加入适量的 硫酸 ;第 3 , 控制固液比 、浸取温度 、搅拌强度和反应 时间 ;第 4 , 以分析渣中锰的含量和反应液中游离硫 酸含量为依据 , 决定酸浸工序是否合格与终止 。
6)根据受热温度和部位不同 , 选择窑炉材料和 科学砌筑 , 确保热能的充分利用和窑炉长时间使用 。
硫磺法硫酸生产工艺设计

2
硫酸是最重要的无机强酸之一,浓硫酸具有强酸性、强氧化性、强的吸水性、强的磺化性等。当加热到30℃以上放出蒸气,加热到200℃以上,散发出三氧化硫。
⒈硫酸是一种强酸,具有酸的特性,它的化学性质非常活泼,根据硫酸的浓度和温度及金属的种类不同,而生成H2、H2S、SO2、S及金属的硫化物和硫酸盐。
1
1.
以硫铁矿为原料生产硫酸,共有九种流程,他们的共同特点是均采用沸腾焙烧,干法除尘,酸洗净化,两转两吸,回收高低温位余热技术方案。设计采用的流程为:焙烧炉→ 废热锅炉→ 旋风除尘器→电除尘器→Swemco洗涤塔→电除雾器→干燥塔→主鼓风机 (2+2两转两吸。该流程首先对硫铁矿进行预处理,对于块状硫铁矿则要粉碎加工成粉矿,对于硫精砂则要进行干燥。若矿的品种较多,入炉前还要按杂质含量要求进行掺配。其主要工序有:硫铁矿焙烧、炉气净化、二氧化硫转化及三氧化硫吸收。
分子量:64.06比重:1.43(液体)
熔 点:-12.7℃沸点:-10℃
蒸汽密度:2.92蒸汽压力:337.5×103Pa(21℃时)
易溶解于水,溶解于有机溶剂及硫酸,无色且不燃烧气体,有刺激性酸味;容易及水化合,生成亚硫酸(H2SO3),并且因氧化而慢慢转化成硫酸(H2SO4)7
2
SO3在硫酸生产过程中来源于两个工段:一是焚硫工段焚硫炉内,二是转化工段转化器内。
3.2.1.2 所管范围
精硫泵槽、精硫泵、焚硫炉、升温风机、油槽、油泵以及所属电气、仪表、设备管线等。
0.001
20.0
0.03
0.010
0.0001
0.10
0.010
3.
主要工艺技术以固体硫磺为原料,采用湿式搅拌快速熔硫、液硫石灰中和、叶片式机械过滤机过滤精制液硫、机械雾化焚烧、III、II—IV、I3+1两次转化两次吸收,接触法制造硫酸。中压余热锅炉回收高、中温热能,副产过热蒸汽供动力车间。
“矿石提锂”的工艺革新——锂辉石-硫酸法生产碳酸锂的工艺革新
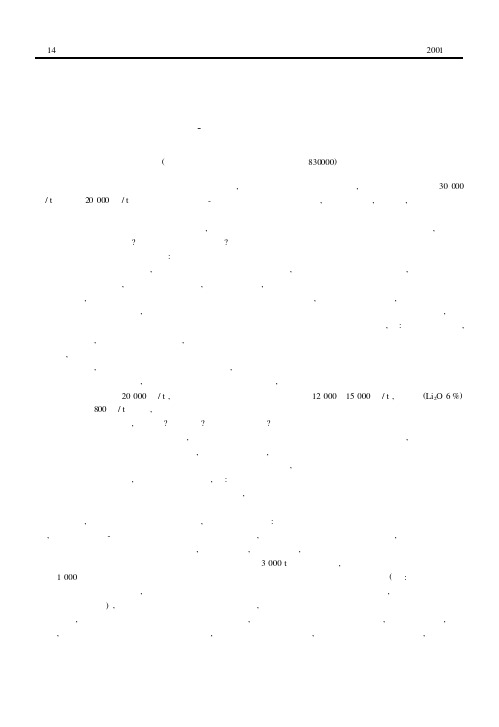
41 第十届全国锂铷铯学术会议论文 2001年“矿石提锂”的工艺革新———锂辉石-硫酸法生产碳酸锂的工艺革新石 颖(新疆有色金属工业公司 乌鲁木齐830000)智利“卤水提锂”的低价碳酸锂进入中国之后,对中国锂盐市场的冲击很大,使碳酸锂的价格从30000元/t降低到20000元/t左右。
国内锂辉石-硫酸法生产碳酸锂的工艺,由于流程长,成本高,因而许多锂盐生产厂家纷纷倒闭或转产。
现在智利“卤水提锂”的冲击即将过去,青海、西藏“卤水提锂”的冲击又要到来。
在这种情况下,中国锂盐的“矿石提锂”怎么办?能不能继续生存下去?已经成了当前突出重要的问题。
仅对此问题谈谈个人的看法:智利“卤水提锂”的冲击,到现在已经过去了四、五年的时间,现在市场已经逐渐稳定下来,碳酸锂商品的价格已经降到了低谷,并且现在稍有回升,在这种情况下,我们应该认真思索中国锂盐的“矿石提锂”问题了。
我认为,对于已经存在并有多年生产经验的“矿石提锂”流程来讲,只要能做到不亏损,就没有理由现在就把它淘汰掉。
经过考察,看到新疆锂盐厂碳酸锂流程的生产成本就基本上做到了不亏损。
这个事实,说明了现在中国的“矿石提锂”还有继续生存下去的希望。
而且中国锂矿石的资源还有很多,如:四川的锂辉石,宜春的锂云母,新疆大红柳滩锂辉石,而且又能买到澳大利亚的锂辉石。
我们不能把中国这么多的锂矿石丢掉不管,全都去研究“卤水提锂”。
中国锂盐,应该既要抓紧“卤水提锂”的研究,也要考虑“矿石提锂”的问题。
要想使“矿石提锂”能够与“卤水提锂”实现长期并存,必须进行“矿石提锂”的工艺革新,要在现在的基础上大幅度降低生产成本。
现在碳酸锂的市场价格是20000元/t,在这个基础上要使生产成本降低到12000~15000元/t,锂辉石(Li2O6%)的价格要降到800元/t左右,以此目标来考虑工艺技术革新。
要搞工艺技术革新,怎么搞?搞什么?资金从哪里来?企业要走“自力更生”的创新之路,一般要求不花钱或少花钱。
硫酸法制备磷酸二氢钾新工艺研究

摘要硫酸法制备磷酸二氢钾新工艺研究摘要磷酸二氢钾作为食品添加剂,饲料添加剂和高效无氯磷钾复合肥,应用广泛。
目前,磷酸二氢钾生产主要采用中和法,因原料磷酸和氢氧化钾价格太高,难以大规模在农业上进行推广和应用。
另外,随着国内工业发展,大量的废硫酸处理和排放已成为严重的环境问题。
本文针对上述问题,提出以氯化钾、硫酸和磷酸氢钙为原料制备磷酸二氢钾的新工艺,其关键点是整个反应过程控制在80℃以下,从而即克服了传统曼海姆法高温(600-800℃)合成反应条件以及对设备的严重腐蚀(硫酸和盐酸)的根本缺点,又解决了传统中和法以磷酸、氢氧化钾为原料的高成本缺点。
研究表明:本新工艺钾和磷的总回收率分别为99% 和95%,每制一吨磷酸二氢钾的原料成本约为3100-3500元,大大低于现有的以氢氧化钾、磷酸为原料的中和法原料成本(约6000元/吨),原料成本降低了35-45%。
本新工艺优化的工艺条件是:(1)氯化钾和硫酸反应制硫酸氢钾的最适工艺条件为:氯化钾初始质量浓度为50%,反应温度为80℃,氯化钾和硫酸的摩尔配比在1:1.2,反应时间12min。
(2)经单因素和正交试验得到,磷酸氢钙和硫酸氢钾反应制磷酸二氢钾的最优工艺组合为:反应时间为120min,反应温度为60℃,液固比为4.5,钾磷比为1.3。
各因素对磷酸二氢钾制备中母液磷收率的影响顺序:反应温度>液固比>磷钾比>反应时间。
(3)磷酸二氢钾母液结晶实验,控制蒸发水量在70%,所得到的磷酸二氢钾产品纯度在96%以上,符合国家农业级一等品标准。
关键词:磷酸二氢钾;硫酸氢钾;废硫酸;新工艺Study on the New Technology ofPotassium Dihydrogen Phosphate with Sulfuric AcidAbstractPotassium dihydrogen phosphate is widely used as food additives, feed additives and efficient chlorine-free phosphorus and potassium compound fertilizer. At present, the main method of producing potassium dihydrogen phosphate is the neutralization method. Because the raw material price of phosphoric acid and potassium hydroxide is too expensive, neutral method is difficult to be popularized and widely applied in agriculture. In addition, a large quantity of waste sulfuric acid treatment and emissions has become a serious environmental problem with the rapid development of domestic industry.In view of the above problems, a new process has been proposed in the paper that is we prepare potassium dihydrogen phosphate with potassium chloride, sulfuric acid and calcium hydrogen phosphate as raw materials. The key point is that the whole reaction process is controlled below 80℃, which can overcome the traditional Mannheim method of high temperature (600-800℃) synthesis reaction conditions and the fundamental shortcomings of the serious corrosion of equipment (sulfuric acid and hydrochloric acid). This process can also solve the shortcoming that is high cost of traditional neutralization method to phosphoric acid, potassium hydroxide as raw material. The results showed that the total recoveries of potassium and phosphorus were 99% and 95%. The cost of raw materials for the production of one ton of potassium dihydrogen phosphate is about 3100-3500 yuan, which was significantly lower than the existing raw materials with potassium hydroxide and phosphoric acid as raw materials (about 6,000 yuan /ton). The cost of raw materials is reduced by 35-45%. The new process optimization process conditions are:(1) Potassium chloride and sulfuric acid were used to prepare potassium hydrogen sulfate. The optimum conditions were as follows: the initial mass concentration of potassium chloride was 50%, the reaction temperature was 80 ℃, the molar ratio of potassium chloride and sulfuric acid was 1: 1.2, the reaction time wasAbstract(2) In the experiment we use calcium hydrogen phosphate and potassium hydrogen sulfate as raw materials to prepare potassium dihydrogen phosphate. And through single factor experiments and orthogonal test, this paper gives the following optimal combination of processes: the reaction time was 120min, the reaction temperature was 60℃, the ratio of liquid to solid was 4.5, and the ratio of potassium to phosphorus was 1.3. The effect of various factors on the yield of phosphorus in the preparation of potassium dihydrogen phosphate: reaction temperature > liquid to solid ratio > phosphorus and potassium ratio > reaction time.(3) Through the mother liquor evaporation and crystallization experiments, we got the result that the purity of potassium dihydrogen phosphate can be 96% when the amount of evaporated water is 70%. And the products can meet the national agricultural grade first-class standards.Key words: potassium dihydrogen phosphate; potassium hydrogen sulfate; waste sulfuric acid; new process目录摘要 (I)Abstract (II)第1章引言 (1)1.1 磷酸二氢钾的性质及其用途 (1)1.2 国内外研究现状 (2)1.2.1 磷酸二氢钾研究现状 (2)1.2.2 硫酸制钾盐现状及工业废酸的利用 (10)1.2.3 现有技术存在的问题 (10)1.2.4 国内外市场现状 (11)1.3 本论文主要研究意义、目的及内容 (11)1.3.1 研究意义 (11)1.3.2 研究目的 (12)1.3.3 研究内容 (12)第2章实验仪器、药品及分析方法 (13)2.1 实验仪器 (13)2.2 实验药品 (14)2.3 实验分析方法 (15)2.3.1 钾离子的测定 (15)2.3.2 氯离子的测定 (15)2.3.3 硫酸根含量的测定 (16)2.3.4 磷含量的测定 (17)2.3.5 氢离子含量的测定 (18)2.4 表征方法 (18)2.5 工艺流程图 (19)第3章KCL制备KHSO4的实验研究 (20)3.1 理论基础 (20)3.2 硫酸氢钾的制备 (20)3.2.1 实验装置与方法 (20)3.2.2 分析方法 (21)3.2.3 单因素实验结果及讨论 (21)3.2.4循环可行性试验 (26)3.3 本章小结 (28)目录4.1 研究的理论基础 (29)4.1.1 磷酸氢钙转化的化学基础 (29)4.1.2 硫酸钙的结晶 (31)4.2动力学基础 (32)4.3 磷酸二氢钾的制备 (34)4.3.1 实验的反应体系 (34)4.3.2 实验装置 (35)4.3.3 单因素实验结果及讨论 (35)4.3.4 正交实验结果及讨论 (40)4.3.5 重复实验 (42)4.4 母液的蒸发结晶 (43)4.4.1母液的蒸发水量 (43)4.4.2磷酸二氢钾的结晶 (45)4.4.3小结 (46)第5章经济性评价 (47)结论 (49)致谢 (50)参考文献 (51)攻读学位期间取得学术成果 (55)第1章引言第1章引言作为高效无氯磷钾复合肥,食品添加剂和饲料添加剂,磷酸二氢钾的制备工艺早在十八世纪初就已经开始研究,但由于设备条件简陋、科研实力不足等多方面因素并没有对其生产过程理论基础和工艺进行深入研究。
硫酸生产装置低温位热能回收技术研究进展

硫酸生产装置低温位热能回收技术研究进展低温位余热是指常规硫酸生产装置中经转化工序回收高、中温位热能后, 降级转入干吸工序的热量, 以及在干吸工序内产生的硫酸生成热、蒸汽冷凝热、硫酸稀释热的总和,合理开发利用低温位余热, 具有重大的现实意义。
本文简要介绍了硫酸生产装置热能回收利用现状及与热能回收技术,重点叙述了国内外开发硫酸生产装置低温位热能回收技术的原理、工艺技术和主要设备,综述硫酸生产装置低温位热能回收技术。
关键字:低温位余热回收技术研究进展1.概述硫酸生产主要包括含硫原料的燃烧、二氧化硫的氧化及三氧化硫的吸收三个过程, 这些过程均伴有释放大量的化学能。
硫磺制酸三个过程的理论反应热分别约占总反应热的56% 、19% 和25% 。
大部分硫酸生产装置对含硫原料燃烧和二氧化硫氧化产生的高、中温位热能尽可能地进行了回收利用, 而对于干燥和吸收系统中的低温位热能, 长期以来除了少数生产企业用于加热工业用水和生活用水外, 一般都是用循环冷却水移走而白白浪费。
传统的硫磺制酸装置, 只回收了产生的总热量的60%-70% , 而硫铁矿制酸装置, 只回收了产生的总热量的50%-60% 。
低温位余热在硫酸生产过程中占有很大的比重, 这里所称的低温位余热是指常规硫酸生产装置中经转化工序回收高、中温位热能后, 降级转入干吸工序的热量, 以及在干吸工序内产生的硫酸生成热、蒸汽冷凝热、硫酸稀释热的总和。
在满足产品酸储存所要求的温度的前提下, 这些热量必须移去, 以维持酸循环系统酸温的稳定。
除散热损失、产品酸和放空尾气带走少量热量以外,其他的低温位余热都可以考虑回收利用。
硫酸生产中废热的回收利用程度已成为衡量硫酸工业技术的一项重要指标,在高、中温位热能普遍得到回收利用的情况下,合理开发利用低温位余热, 具有重大的现实意义。
2.低温位热能回收技术的开发硫酸生产装置低温位余热的利用大体来说有三种形式: 加热其他物料, 如预热锅炉给水、加热生活用水和工业用水, 加热造纸液, 浓缩硫酸、磷酸等;以低沸点物料做载体, 带动透平发电机组发电;采用高温吸收, 生产低压蒸汽, 增加发电量。
硫酸生产新建项目可研报告

一、项目名称及承办单位1、项目名称:硫酸生产项目2、项目建设性质:新建3、项目承办单位:XX硫酸生产有限公司4、注册资金:80万元人民币二、可行性研究报告编制原则和范围(一)项目可行性报告编制依据(1)《中华人民共和国国民经济和社会发展“十二五”规划纲要》;(2)《建设项目经济评价方法与参数及使用手册》(第三版);(3)《工业可行性研究编制手册》;(4)《现代财务会计》;(5)《工业投资项目评价与决策》;(6)国家及XX有关政策、法规、规划;(7)项目公司提供的有关材料及相关数据;(8)国家公布的相关设备及施工标准(二)可行性研究报告编制原则在该想开幕可行性研究报告中,以节约资源保护环境为原则,遵循“创新、先进、可靠、实用、效益”的指导方针,严格按照技术先进、低能耗、低污染、控制投资的要求,确保该硫酸项目技术先进、质量优良、保证进度、节省投资、提高效益。
树立和落实科学发展观,构建节约型和谐社会,秉着工艺技术达到国际先进水平,提高劳动生产率,节约消耗,环保安全的原则,认真分析市场要求,了解市场的区域性差别,针对产品的差异化要求、区域化的特点,寻求经济效益最大化,提高企业在国内外的知名度。
认真贯彻执行国家建设项目有关消防、安全、卫生、劳动保护和环境保护管理规定、规范,本着“三同时”原则,设计上充分考虑生产设施在上述各方面投资,使得环境保护、安全生产及消防工作贯穿于项目的全过程。
在总体布局中,力求做到功能分区明确、生产流程顺、交通组织合理,环境保护良好,空间处理协调,厂容厂貌整洁,有利于生产管理和工程分区建设。
(三)可行性研究报告编制范围本可行性研究报告的内容和深度依照国家发展和改革委员会《工业建设项目可行性研究报告编制内容深度规定》的要求进行,依据国家产业发展政策和有关部门的行业发展规划以及项目承办单位的实际情况,按照项目的建设要求,对项目的实施在技术、经济、社会和环境保护等领域的科学性、合理性和可行性进行研究论证。
硫酸生产工艺的发展状况

硫酸生产工艺的发展状况摘要:硫酸对于我国工业生产而言具有很大作用,其应用范围广泛,尤其是化学工业中的地位较高,不仅能生产无机化学肥料,还能作为基础工业原料,因此其生产工艺将会直接决定我国农业经济及工业经济发展进程,工作人员需要充分了解硫酸生产各工艺的特性,进而为我国硫酸生产工艺稳定长远发展奠定基础。
为此,本文就以硫酸生产工艺为例,对其发展状况进行深入分析。
关键字:硫酸;生产工艺;发展状况引言:随着我国工业经济的快速发展,目前我国硫酸工业得到了大幅度提升,硫酸工程无论其质量还是水平都发展良好,对我国国民经济发展起到了推波助澜的作用,因此我国对于硫酸生产工艺格外重视并引入了先进的技术以及装备,其目的就是为了提高我国硫酸工艺水平。
硫酸生产原料较为多元化,不同生产原料制作工艺以及应用要点就具有一定需求,因此工作人员需要充分掌握各原材料特性,合理选择生产工艺开展作业,进而提高硫酸生产水平,同时还需要从不同角度开展综合考虑,在优化硫酸生产体系的同时做好生态环境保护工作,控制硫酸生产成本。
一、硫酸生产工艺概述目前我国硫酸生产工艺主要是包括硫铁矿制酸以及硫磺制酸,其中硫铁矿制酸主要是通过沸腾燃烧方式提炼出硫铁矿中硫元素,再通过气体净化吸收的方式生产出硫酸,而硫磺制酸主要是以硫磺为主,通过不同方式提高液体硫磺温度,如快速熔流、液体硫酸燃烧等,通过设备将其转化为固体硫酸。
其次,我国硫酸生产原料多元化,不同生产原料特性以及化学反应都具有很大不同,工作人员需要了解各生产原料特性,根据其特性选择相应的方式进行生产,进而提高硫酸生产质量,如冶炼烟气制酸、硫磺制酸、硫酸盐制酸、硫铁矿制酸等,工作人员需要掌握各生产方式特性,根据实际生产需求选择不同的技术开展制作,保证硫酸生产符合工业生产需求,为我国工业发展奠定基础。
二、硫酸生产工艺的发展状况分析1、硫铁矿生产硫铁矿作为我国的特有资源,可以保持一定规模的硫铁矿制酸能力,有效提高我国经济发展,并且工作人员利用硫铁矿开展硫酸制作可以弥补国外硫资源,节约硫酸制作成本,因此相关学者要以国际市场以及我国发展现状为依据,为我国硫酸生产工艺争取有利条件,做好调节与平衡。
- 1、下载文档前请自行甄别文档内容的完整性,平台不提供额外的编辑、内容补充、找答案等附加服务。
- 2、"仅部分预览"的文档,不可在线预览部分如存在完整性等问题,可反馈申请退款(可完整预览的文档不适用该条件!)。
- 3、如文档侵犯您的权益,请联系客服反馈,我们会尽快为您处理(人工客服工作时间:9:00-18:30)。
硫酸生产新工艺研究进展
摘要:硫酸工业是一个古老的行业,至今已有250多年的历史,其工艺发展经历了铅室法、塔式法、接触法(包括一转一吸和两转两吸)等阶段。
本文介绍国内外近期开发的几种硫酸生产工艺Cansolv SO2循环工艺、Regesox工艺、SAPNE 工艺、Poseidon尾气循环工艺、Notrosyl工艺、Waterloo工艺,以纯氧作为氧化剂、采用三转三吸生产硫酸的新工艺。
关键字:硫酸工业工艺技术进展
硫酸生产排放尾气中的二氧化硫、三氧化硫(硫酸雾)是对大气的污染物,现代硫酸生产技术就此已作了很多改进,大大降低了污染物的排放量。
硫酸工业不属于技术密集型行业,自20世纪60年代开发两转两吸工艺以来,工艺上没有什么重大的突破。
两转两吸工艺的最大特点是SO2转化率高,含铯低温催化剂的应用,进一步降低了其尾气SO2排放浓度。
然而,任何工艺都有其固有的局限性,由于在现有的催化剂条件下依然存在着极限SO2平衡转化率,两转两吸工艺无法满足过于苛刻的环保要求;由于受热平衡、水平衡的限制,该工艺也不适宜处理较低浓度的SO2原料气。
为此,近年来国内外在硫酸生产工艺的改革方面做了大量的工作。
1.纯氧作为氧化剂、采用三转三吸生产硫酸工艺
使用纯氧(浓度高于95.5%或更高)作为氧化剂的硫酸生产新工艺,该工艺采用三转三吸以获得更高的SO2转化率。
超过85%的尾气循环进人转化器, 这样可以大幅度减少尾气的排放量。
该新工艺由熔硫、焚硫、SO2转化和SO3吸收四部分组成,其中熔硫工序与传统工艺一样。
2.Cansolv SO2循环工艺
Cansolv SO2循环工艺循环工艺为加拿大Cansolv工艺公司开发。
它在一转一吸装置后增设1套SO2吸收系统,采用二胺溶液吸收尾气中的SO2,然后通过加热气提,解吸出纯净的SO2,返回干燥塔循环使用。
二胺吸收剂对SO2浓度不敏感,选择性好、吸收速度快而SO2平衡分压低,装置的最终SO2排放浓度甚至可低于50mg/m3。
Cansolv循环工艺的最大特点是尾气吸收系统具有很强的吸收、缓冲能力,所以不仅SO2排放浓度极低,而且简化了前面一转一吸装置的配置,
降低了对其转化率的要求(约85%即可),工艺控制条件较为宽松。
与两转两吸装置相比,Cansolv SO2循环装置用1 座较小的吸收塔代替中间吸收塔,用1 座比吸收塔小得多的再生塔和1台溶剂净化设备代替3 台气体换热器和2段催化剂床,所以装置的投资较低。
此外,由于工艺简单阻力较小,主鼓风机的费用和电耗也大大降低。
尾气吸收装置消耗的低压再生蒸汽可由装置的废热回收提供,其费用可通过主鼓风机费用的减少而抵消,所以总的运行费用具有竞争性。
3.Regesox工艺
Regesox工艺工艺由丹麦托普索公司开发。
该工艺在一转一吸装置后设置1套非稳态催化氧化装置,以质量分率50%-80%形式回收吸收塔排气中94%以上的含硫化合物。
出SO3吸收塔的气体进入Regesox非稳态氧化系统。
该系统包括2台串联的绝热反应器,上部装有VK系列SO2氧化催化剂,下部装有惰性换热材料(HEM)。
入口气体以3-8min的周期交替改变流向,依次通过第一、第二或第二、第一反应器。
气体从下部进入第一台反应器后,与HEM层换热升温至大约400℃,SO2在VK催化剂层中氧化成SO3并放出热量。
高温气体从上部进入第二台反应器,继续反应后与HEM层换热进行冷却,同时HEM层升温蓄热,为下一个周期加热气体做好准备。
冷却后的SO3与工艺气体中的水结合生成H2SO4蒸气并冷凝成质量分率70%的H2SO4从底部排出。
4.SAPNE工艺
1998年11月在美国塔克森国际硫会议上,工艺工程协会(PEA)提出一种想法,将古老的塔式法与现代接触法制酸工艺相结合,以同时利用接触法产品酸浓度高(H2SO4)和塔式法SO2转化率极高(≥99.9%)的优点。
LocKwood Greene Petersen公司成功地将这一想法付诸于实践并获得专利权。
该工艺命名为SAPNE,意即“接近于零排放的硫酸生产工艺。
5.Poseidon尾气循环工艺
尾气循环工艺是印度Poseidon工程咨询公司开发的,它将一部分SO3吸收塔排出的尾气送回SO2转化器,代替空气作为冷激气。
该工艺可用于一转一吸和两转两吸装置的改造。
出吸收塔的气体由1台风机加压返回转化器二、三段出口。
用尾气冷激不同于用空气冷激。
用空气冷激相当于用空气稀释尾气;而用尾气冷激,烟囱排气量减少了,在相同的表观转化率下,排入大气的SO2与SO3量也相
应减少了。
6.Notrosyl工艺
Notrosyl工艺工艺由加拿大Expatriate Resources公司的全资子公司Notrosyl 工艺公司开发。
Notrosyl工艺是一种液相均相催化工艺,用含有HNO3的H2SO4氧化并加以吸收。
由于该法每立方米反应器容积的H2SO4生成量为1t/h氧化速度较接触法约快10倍,并且尾气排放SO2浓度很低。
该工艺可处理SO2气体,改进后也可处理各种含硫气体,如硫化氢、硫醇、多硫化物和含胺硫等。
Notrosyl工艺是一种液相工艺,所以由硫铁矿或硫精矿焙烧、硫磺或硫化铁焚烧获得的SO2体无需干燥或除雾直接进入反应器。
反应器内装有H2SO4和HNO3的强氧化性混合物,混酸浓度为5-16mol/L,其中HNO3浓度至少为0.1mol/L。
气体通过溶液后被氧化并形成H2SO4,而HNO3则被还原并立即重新氧化。
因为反应在液相进行,速度很快,所以反应器大小仅为接触装置的1/10。
鼓泡试验证实了Notrosyl法极高的反应速率,在工艺参数尚未优化的情况下,转化率可达88%。
7.Waterloo工艺活性炭H2SO4生产工艺
用活性炭吸附并氧化SO2成SO3,然后用水冲洗生成稀H2SO4是一个很老的方法。
SO2在活性炭上的反应非常迅速,在25℃下,时空产率可达到3g/gh,为传统钒催化氧化的几百倍,而且反应非常完全。
但由于活性炭法生产的H2SO4浓度较低,所以一直仅限用于电厂烟气脱硫。
从这个意义上来说,传统活性炭法实际上不是一种真正的H2SO4生产工艺,而是一项环保措施。
最近,加拿大Waterloo大学提出了一种新型活性炭H2SO4生产工艺。
Waterloo工艺活性炭H2SO4生产工艺基于这样的原理:H2SO4在一些有机溶剂中是可溶的,采用特定的有机溶剂冲洗活性炭表面形成的SO3,有可能生产浓H2SO4及其他工业产品,如硫酸酯或磺酸盐。
研究发现,有机溶剂可选自丙酮、醚、十氢萘、四氢甲酰胺等,可同时含有超临界流体,如二氧化碳、乙烷、三氟甲烷等,以强化催化氧化效果;活性炭采用经无机或有机化合物改性以增强催化活性的产品。
Waterloo工艺活性炭H2SO4生产工艺目前尚在试验阶段。
在过去的10年内,随着改革开放的不断深入,我国硫酸工业的技术装备水平有了显著的提高,大批以合资、引进技术或设备、引进工艺设计软件等形式建
设的硫酸装置使我国硫酸工业步入了一个全新的发展阶段。
但是,回顾过去,我们走的基本上还是一条技术模仿的道路,缺乏技术上的创新。
而从知识经济的角度来看,国与国之间的竞争,归根结底是技术创新能力的竞争。
所以,在对国外先进技术消化吸收的基础上,积极开发拥有自主知识产权的新技术,是我国跻身于世界硫酸强国之林的必经之路。
参考文献:
[1]郭景芝.国外硫酸工艺技术进展[J].化工生产与技术,2003,(3):25一29.
[2]M.LEHNERW.GEIPEL.SeParationofSulPhurTrioxideAerosolswiththeNewElectrostaticPreciPit ator“CAROLA”[Jl.SulPhur,2003,(9):l一7.
[31KarlH.Daum.应对高浓度50:烟气的挑战[J],硫酸工业,2006,(l):l一10.
[4]胡伟生.高浓度50:转化技术[J1.有色冶金设计与研究,2001,(12):26一30.
[51应燮堂.两种高浓度502制酸工艺的评述[J1.硫酸工业,20仍,(6):13一17.
[6]陈南洋.我国有色冶炼低浓度二氧化硫烟气制酸技术进展[J].硫酸工业,2005,(2):15一18.。