基于Autodesk Inventor的共轭凸轮设计与运动仿真
毕业论文-凸轮机构建摸,受力分析和运动仿真与分析研究

摘要凸轮是一具有曲面轮廓的构件,一般多为原动件(有时为机架);当凸轮为原动件时,通常作等速连续转动或移动,而从动件则按预期输出特性要求作连续或间隙的往复运动、移动或平面复杂运动。
本文主要介绍凸轮的大体概念与凸轮廓线的设计计算,以及后期使用Pro/E软件仿真其廓线。
凸轮轮廓曲线是凸轮机构设计的关键,常用的设计方法有解析法和图解法。
本文将对这两这种方法进行大致分析与应用设计,利用Pro/E软件绘制凸轮机构实体模型,并用Pro/E软件自带的Pro/MECHANICA Motion插件设计凸轮机构运动模型,进行机构运动学仿真分析,可以较准确掌握机械产品零部件的位移、速度和加速度等动力学参数,进而可分析机构动作的可靠性。
主要技术要求为:熟悉凸轮设计基本原理及相关理论计算;凸轮机构运动仿真及受力分析;指定内容的翻译和Pro/E软件的熟练应用。
本文将重点研究凸轮机构建摸,受力分析和运动仿真与分析。
通过理论上的计算和研究,结合图解以及解析的方法,算出凸轮廓线的大致数据,用Pro/E软件将其绘制出,进行运动仿真,记录和研究其位移、速度和加速度等动力参数,最后分析出机构动作的可靠性。
使以后工作中,可以更准确掌握机械产品零部件的动力方面个参数,减少事故的发生,降低设计的难度。
关键词:凸轮;廓线设计;Pro/E;三维造型;仿真。
AbstractCam is a component with a surface profile is generally more dynamic pieces of the original (sometimes for the rack), when the cam piece to its original form, it is usually in a row for the constant rotation or move, and the follower output characteristics according to the requirements expected for continuous or reciprocating motion of the space, move, or the complexity of sports plane. This paper mainly introduces the general concept of the cam and cam profile design and calculation, and the latter the use of Pro / E software simulation of its profile.Cam cam curve design is the key to the design of methods commonly used analytical method and graphical method. In this paper, two such methods will be more or less analysis and application design, use of Pro/E software cam solid model rendering, and Pro / E software comes with the Pro/MECHANICA Motion cam plug design movement model, the kinematics Simulation can b a more accurate knowledge of machinery parts and components of displacement, velocity and acceleration, such as kinetic parameters, which can analyze the reliability of body movement.The main technical requirements are:familiar with the basic principles of cam design and related theoretical calculation; cam mechanism motion simulation and stress analysis; specify the contents of the translation and Pro/e application software proficiency.This article will focus on cam modeling, stress analysis and motion simulation and analysis. Through theoretical calculations and research, combined with graphical and analytical methods, calculate the approximate convex contour data, using Pro/E software to draw, simulation exercise, record and study the displacement, velocity and acceleration and other dynamic parameters, Finally, the reliability of the agency action. So after work, can be more accurate machinery parts and components of the dynamic parameters, to reduce accidents, reduce the difficulty of design.Keywords:Cam, Profile Design ,Pro/E, Three-dimensional shape,Simulation.目录1绪论 (1)1.1选题意义 (1)1.2 仿真技术的发展 (3)1.3 Pro/Engineer在机械制造中的应用 (5)1.3.1 Pro/Engineer软件介绍 (5)1.3.2Pro/E在我国机械行业中的应用 (8)2凸轮轮廓线的设计 (10)2.1绪论 (10)2.2 凸轮机构的分类 (11)2.2.1 按两活动构件之间的相对运动特性分类 (11)2.2.2 按从动件运动副元素形状分类 (11)2.2.3 按凸轮高副的锁合方式分类 (11)2.3从动件运动规律 (12)2.3.1 基本运动规律 (12)2.4 凸轮轮廓线的设计 (14)2.4.1凸轮轮廓曲线的计算 (14)2.5凸轮机构基本尺寸的确定 (17)2.5.1凸轮机构的压力角及许用值 (17)2.6.2凸轮理论轮廓的外凸部分。
基于Autodesk Inventor的轮腿式行走机构的三维结构设计
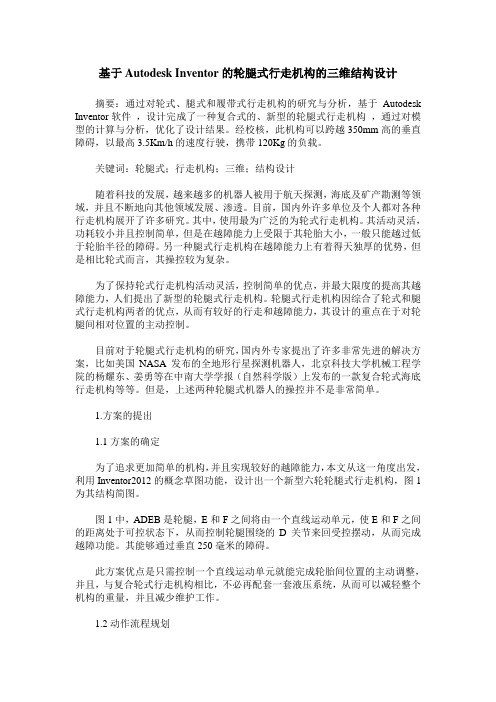
基于Autodesk Inventor的轮腿式行走机构的三维结构设计摘要:通过对轮式、腿式和履带式行走机构的研究与分析,基于Autodesk Inventor软件,设计完成了一种复合式的、新型的轮腿式行走机构,通过对模型的计算与分析,优化了设计结果。
经校核,此机构可以跨越350mm高的垂直障碍,以最高3.5Km/h的速度行驶,携带120Kg的负载。
关键词:轮腿式;行走机构;三维;结构设计随着科技的发展,越来越多的机器人被用于航天探测,海底及矿产勘测等领域,并且不断地向其他领域发展、渗透。
目前,国内外许多单位及个人都对各种行走机构展开了许多研究。
其中,使用最为广泛的为轮式行走机构。
其活动灵活,功耗较小并且控制简单,但是在越障能力上受限于其轮胎大小,一般只能越过低于轮胎半径的障碍。
另一种腿式行走机构在越障能力上有着得天独厚的优势,但是相比轮式而言,其操控较为复杂。
为了保持轮式行走机构活动灵活,控制简单的优点,并最大限度的提高其越障能力,人们提出了新型的轮腿式行走机构。
轮腿式行走机构因综合了轮式和腿式行走机构两者的优点,从而有较好的行走和越障能力,其设计的重点在于对轮腿间相对位置的主动控制。
目前对于轮腿式行走机构的研究,国内外专家提出了许多非常先进的解决方案,比如美国NASA发布的全地形行星探测机器人,北京科技大学机械工程学院的杨耀东、姜勇等在中南大学学报(自然科学版)上发布的一款复合轮式海底行走机构等等。
但是,上述两种轮腿式机器人的操控并不是非常简单。
1.方案的提出1.1方案的确定为了追求更加简单的机构,并且实现较好的越障能力,本文从这一角度出发,利用Inventor2012的概念草图功能,设计出一个新型六轮轮腿式行走机构,图1为其结构简图。
图1中,ADEB是轮腿,E和F之间将由一个直线运动单元,使E和F之间的距离处于可控状态下,从而控制轮腿围绕的D关节来回受控摆动,从而完成越障功能。
其能够通过垂直250毫米的障碍。
基于Autodesk Inventor的共轭凸轮设计与运动仿真
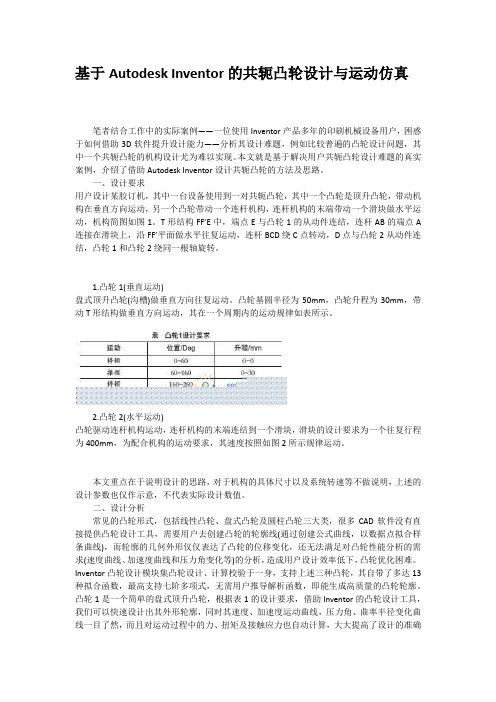
基于Autodesk Inventor的共轭凸轮设计与运动仿真笔者结合工作中的实际案例——一位使用Inventor产品多年的印刷机械设备用户,困惑于如何借助3D软件提升设计能力——分析其设计难题,例如比较普遍的凸轮设计问题,其中一个共轭凸轮的机构设计尤为难以实现。
本文就是基于解决用户共轭凸轮设计难题的真实案例,介绍了借助Autodesk Inventor设计共轭凸轮的方法及思路。
一、设计要求用户设计某胶订机,其中一台设备使用到一对共轭凸轮,其中一个凸轮是顶升凸轮,带动机构在垂直方向运动,另一个凸轮带动一个连杆机构,连杆机构的末端带动一个滑块做水平运动,机构简图如图1。
T形结构FF’E中,端点E与凸轮1的从动件连结,连杆AB的端点A 连接在滑块上,沿FF’平面做水平往复运动,连杆BCD绕C点转动,D点与凸轮2从动件连结,凸轮1和凸轮2绕同一根轴旋转。
1.凸轮1(垂直运动)盘式顶升凸轮(沟槽)做垂直方向往复运动。
凸轮基圆半径为50mm,凸轮升程为30mm,带动T形结构做垂直方向运动,其在一个周期内的运动规律如表所示。
2.凸轮2(水平运动)凸轮驱动连杆机构运动,连杆机构的末端连结到一个滑块,滑块的设计要求为一个往复行程为400mm,为配合机构的运动要求,其速度按照如图2所示规律运动。
本文重点在于说明设计的思路,对于机构的具体尺寸以及系统转速等不做说明,上述的设计参数也仅作示意,不代表实际设计数值。
二、设计分析常见的凸轮形式,包括线性凸轮、盘式凸轮及圆柱凸轮三大类,很多CAD软件没有直接提供凸轮设计工具,需要用户去创建凸轮的轮廓线(通过创建公式曲线,以数据点拟合样条曲线),而轮廓的几何外形仅仅表达了凸轮的位移变化,还无法满足对凸轮性能分析的需求(速度曲线、加速度曲线和压力角变化等)的分析,造成用户设计效率低下,凸轮优化困难。
Inventor凸轮设计模块集凸轮设计、计算校验于一身,支持上述三种凸轮,其自带了多达13种拟合函数,最高支持七阶多项式,无需用户推导解析函数,即能生成高质量的凸轮轮廓。
Inventor机械设计实战教程16 运动仿真

必须有一个运动约束确定两者的基本位置,例如例子中的“平面运动”;大多数情况下需要使 用“滚动+相切”的方式,否则另加相切约束。
6
AIP2008 实战教程 – 16
其中,名字前缀 Rl 是 Rolling(滚动)的意思。
♦ 与Inventor的装配约束相关:
不能继承 Inventor 中“运动约束”下的“转动-平动”装配约束,虽然两者应当是完全对应的。 否则出现图 16-14 的提示。所以,只好在运动仿真中重新添加。
1
AIP2008 实战教程 – 16
图 16-2 运动仿真设置
3. 基本运动约束
在运动仿真中, Inventor 默认情况下会自动将 装配中的约束转换成基本运动约束,但却不能再添加 基本运动约束。因此读者在看这节时,可以把运动仿 真设置中的“自动更新已转换的连接”禁用,这样就 可以手动添加基本运动约束。
♦ 非柔性子部件被视为单个刚体。包含子部件的单个零件也是刚体,不能在非柔性子部件的
零件之间定义运动连接。
♦ 因为零件是刚体,且在连接中处于空闲状态,所以可以对机械装置
进行过约束。例如,如果指定约束一个自由度,而该自由度已经受
到另一个现有连接需作如下操作:打开一个需要进行运动仿真
的装配文件,在 “应用程序”菜单下选择“运动仿真”,即可进入Inventor
运动仿真界面。参见图16-1所示。
图 16-1 进入界面
2. 基础参数
在切换到运动仿真环境中之后,一般要设置一些基础参数。先点击工具面板上的 “运动仿 真设置”按钮,会弹出对话框,参见图16-2。
当“自动更新已转换的连接”处于激活状态时,Inventor会在进入运动仿真模块后,自动把装 配约束转换为标准连接,但同时用户也不能再添加标准连接了,也就是不能添加后面所讲的“基本 运动约束”。如果通过清除该框来禁用“自动更新已转换的连接”,系统会显示一条消息警告用户将 删除所有已转换的连接,此后用户可以添加标准连接,如果有装配约束,也可以通过“转换装配约 束”手动转换装配约束。
用仿真生成凸轮轮廓线的步骤

用仿真生成凸轮轮廓线的步骤一、引言凸轮是机械传动中常用的一种元件,用于控制机械运动。
通过凸轮的运动,可以实现对其他机械元件的运动轨迹和速度的控制。
为了设计和制造高效可靠的凸轮,需要对凸轮的轮廓线进行仿真和优化。
本文将介绍使用仿真方法生成凸轮轮廓线的步骤。
二、建立凸轮模型需要在计算机软件中建立凸轮的三维模型。
可以使用CAD软件或者仿真软件来完成这一步骤。
在建立凸轮模型时,需要考虑凸轮的形状、轴向和径向尺寸以及凸轮上的凸起部分。
三、确定凸轮运动规律凸轮的轮廓线是根据凸轮的运动规律来确定的。
凸轮运动规律可以通过数学方法建立,也可以通过运动学仿真来确定。
在确定凸轮运动规律时,需要考虑凸轮的转动角度和运动速度。
四、进行凸轮仿真在进行凸轮仿真之前,需要确定仿真软件和仿真参数。
常用的凸轮仿真软件有ADAMS、CATIA、SolidWorks等。
在进行凸轮仿真时,需要输入凸轮模型和凸轮运动规律,并设置仿真参数,如仿真时间、时间步长等。
然后,通过仿真软件进行凸轮的运动仿真,得到凸轮的轨迹数据。
五、生成凸轮轮廓线通过凸轮仿真得到的凸轮轨迹数据,可以用来生成凸轮的轮廓线。
常用的方法有两种:一种是将凸轮轨迹数据导入CAD软件中,然后根据轨迹数据绘制凸轮轮廓线;另一种是使用数学方法,根据凸轮运动规律和凸轮轨迹数据,通过插值和拟合等方法生成凸轮轮廓线。
六、优化凸轮轮廓线生成凸轮轮廓线后,还可以对凸轮轮廓线进行优化。
通过调整凸轮轮廓线的形状和尺寸,可以改变凸轮的运动规律和运动速度,从而满足实际需求。
常用的优化方法有形状优化和参数优化。
形状优化是通过改变凸轮的形状来优化凸轮的运动规律;参数优化是通过改变凸轮的尺寸和凸起部分的位置来优化凸轮的运动速度。
七、验证凸轮轮廓线在生成和优化凸轮轮廓线之后,需要对其进行验证。
可以通过数学方法和实验方法进行验证。
数学方法是通过计算凸轮轮廓线的数学模型来验证凸轮的运动规律和运动速度;实验方法是通过实际的凸轮测试来验证凸轮的运动轨迹和速度。
基于ADAMS的凸轮机构设计及运动仿真分析_徐芳

!!!!!!!!!!!!!!"
!!!!!!!!!!!!!!!!!!!!!!!!!!!!!!!!!!!!!!!!!!!" 【摘 要】 用大型运动学和动力学分析软件 ADAMS 完成尖顶直动从动件盘形凸轮机构设计和 !!!!!!!!!!!!!!"
实体造型 , 并对其进行运动分析和仿真 , 缩短了凸轮的设计周期并提高了设计质量 , 为凸轮机构的设 计分析提供一种有效的新方法。 关键词 : ADAMS ; 凸轮机构 ; 运动仿真 【Abstr act】 The design and modeling of dish cam with straight moving follower is given by the kinetics
转副之上创建一个每秒钟逆时钟旋转 360 度的旋转驱动。 这样 , 一个完整的凸轮机构仿真模型建立起来 , 如图 4 所示 , 从而可以 进行下一步的运动仿真分析。
20* (1 - cos (6/5*360d*time)),40,IF(time - 7/12:40,40,IF (time - 11/12: 40* (2.75 - 3*time +1/(2*pi)*sin (3*2*pi*time - 3.5*pi)),0,IF (time - 1: 0,0,0))))" 。
在模型上施加一定的运动约束副、 力或力矩的运动激仿真实例分析
利用 ADAMS 进行凸轮机构设计仿真的过程大致可分为凸 轮机构几何建模、 施加约束和载荷、 凸轮机构样机模型检验和 仿真结果后处理、 仿真结果比较分析, 多次仿真及优化设计等
2.1 已知条件
已知尖顶直动从动件盘形凸轮机构的凸 轮 基 圆 半 径 r0=60, 从动件行程 h=40, 推程运动角为 !0=150!, 远休止角 !s=60!, 回程运 动 角 !0' =120!, 近 休 止 角 为 !s' =30! ; 从 动 件 推 程 、 回程分别采用余 弦加速度和正弦加速度运动规律, 对该凸轮机构进行模拟仿 真 , 各阶段的运动规律如下 : ( 1) 从动件推程 运 动 方 程 。 推 程 段 采 用 余 弦 加 速 度 运 动 规 律 , 故将已知条件 !0=150!=5!/6 、 h=40mm 代入余弦加 速 度 运 动 规律的推程段方程式中 , 推演得到 :
基于Inventor的凸轮轮廓参数化设计及性能分析
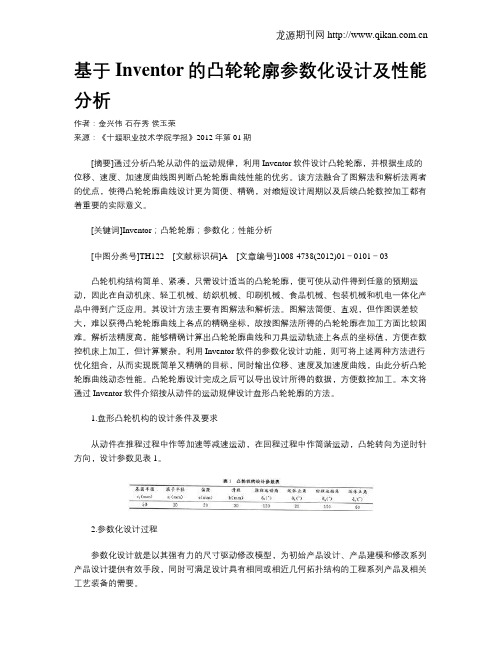
基于Inventor的凸轮轮廓参数化设计及性能分析作者:金兴伟石存秀侯玉荣来源:《十堰职业技术学院学报》2012年第01期[摘要]通过分析凸轮从动件的运动规律,利用Inventor软件设计凸轮轮廓,并根据生成的位移、速度、加速度曲线图判断凸轮轮廓曲线性能的优劣。
该方法融合了图解法和解析法两者的优点,使得凸轮轮廓曲线设计更为简便、精确,对缩短设计周期以及后续凸轮数控加工都有着重要的实际意义。
[关键词]Inventor;凸轮轮廓;参数化;性能分析[中图分类号]TH122[文献标识码]A[文章编号]1008-4738(2012)01-0101-03凸轮机构结构简单、紧凑,只需设计适当的凸轮轮廓,便可使从动件得到任意的预期运动,因此在自动机床、轻工机械、纺织机械、印刷机械、食品机械、包装机械和机电一体化产品中得到广泛应用。
其设计方法主要有图解法和解析法。
图解法简便、直观,但作图误差较大,难以获得凸轮轮廓曲线上各点的精确坐标,故按图解法所得的凸轮轮廓在加工方面比较困难。
解析法精度高,能够精确计算出凸轮轮廓曲线和刀具运动轨迹上各点的坐标值,方便在数控机床上加工,但计算繁杂。
利用Inventor软件的参数化设计功能,则可将上述两种方法进行优化组合,从而实现既简单又精确的目标,同时输出位移、速度及加速度曲线,由此分析凸轮轮廓曲线动态性能。
凸轮轮廓设计完成之后可以导出设计所得的数据,方便数控加工。
本文将通过Inventor软件介绍按从动件的运动规律设计盘形凸轮轮廓的方法。
1.盘形凸轮机构的设计条件及要求从动件在推程过程中作等加速等减速运动,在回程过程中作简谐运动,凸轮转向为逆时针方向,设计参数见表1。
2.参数化设计过程参数化设计就是以其强有力的尺寸驱动修改模型,为初始产品设计、产品建模和修改系列产品设计提供有效手段,同时可满足设计具有相同或相近几何拓扑结构的工程系列产品及相关工艺装备的需要。
2.1基本参数的输入打开Inventor软件,新建零部件后进入“设计”界面,选择“盘形凸轮生成器”,在相应的对话框中输入凸轮设计的基本参数,如图1所示。
凸轮机构廓线精确设计与运动仿真
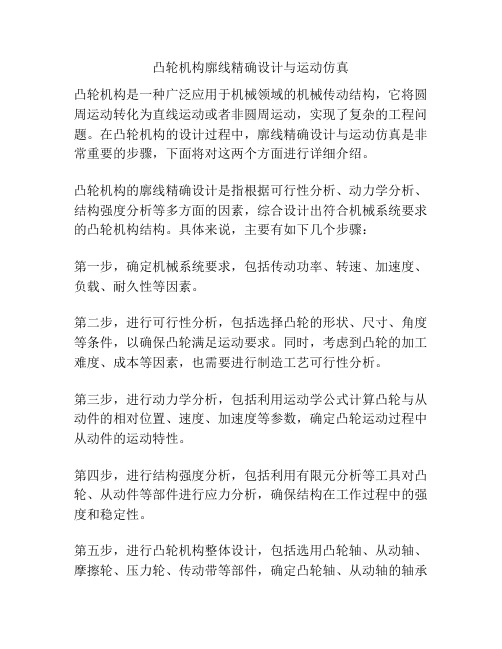
凸轮机构廓线精确设计与运动仿真凸轮机构是一种广泛应用于机械领域的机械传动结构,它将圆周运动转化为直线运动或者非圆周运动,实现了复杂的工程问题。
在凸轮机构的设计过程中,廓线精确设计与运动仿真是非常重要的步骤,下面将对这两个方面进行详细介绍。
凸轮机构的廓线精确设计是指根据可行性分析、动力学分析、结构强度分析等多方面的因素,综合设计出符合机械系统要求的凸轮机构结构。
具体来说,主要有如下几个步骤:第一步,确定机械系统要求,包括传动功率、转速、加速度、负载、耐久性等因素。
第二步,进行可行性分析,包括选择凸轮的形状、尺寸、角度等条件,以确保凸轮满足运动要求。
同时,考虑到凸轮的加工难度、成本等因素,也需要进行制造工艺可行性分析。
第三步,进行动力学分析,包括利用运动学公式计算凸轮与从动件的相对位置、速度、加速度等参数,确定凸轮运动过程中从动件的运动特性。
第四步,进行结构强度分析,包括利用有限元分析等工具对凸轮、从动件等部件进行应力分析,确保结构在工作过程中的强度和稳定性。
第五步,进行凸轮机构整体设计,包括选用凸轮轴、从动轴、摩擦轮、压力轮、传动带等部件,确定凸轮轴、从动轴的轴承结构、固定方式等。
以上五个步骤的精确设计,可以确保凸轮机构在机械领域能够稳定可靠地工作,满足机械系统要求,实现有效的运动传递。
同时,为了更直观地了解凸轮机构的运动特性,还需要进行运动仿真。
凸轮机构的运动仿真,主要是对凸轮轮廓、从动件运动轨迹、运动速度、加速度等参数进行模拟和分析。
在进行运动仿真时,需要用到相应的仿真软件,如ADAMS,SIEMENS NX等。
具体来说,主要有如下几个步骤:第一步,通过CAD软件,绘制凸轮轮廓图,并将图形导入仿真软件中。
第二步,模拟凸轮的运动过程,将凸轮的运动参数输入到仿真软件中,包括凸轮角速度、位移、角度等。
第三步,设定从动件的初始位置及在凸轮运动过程中的运动方式,并进行仿真计算。
第四步,观察仿真结果,分析凸轮机构的稳定性、精度、寿命等参数,进行运动特性分析。
凸轮机构的虚拟设计与运动仿真

2019年第5期凸轮机构的虚拟设计与运动仿真曹勇,邓岭(湖南人文科技学院能源与机电工程学院,湖南娄底417000)摘要:凸轮机构结构简单紧凑,只需设计出适当的轮廓曲线,就能得到推杆预期的运动规律,因此凸轮机构在机械领域中应用广泛。
随着机械工业的快速发展,对于凸轮机构的性能要求也越来越高,所以在凸轮机构设计、制造等方面的工作也越来越困难。
为了探索凸轮机构设计、仿真、分析方法,本文以内燃机的配气凸轮机构为例,综合利用MATLAB 与UG NX 软件,实现了配气凸轮机构的虚拟设计与运动仿真,该方法充分结合了MATLAB 与UG NX 软件的优点,可扩展性和可维护性强,在凸轮机构的计算机辅助设计应用中具有一定的实用价值。
关键词:凸轮机构;虚拟设计;轮廓曲线;运动仿真作者简介:曹勇(1997-),男,湖南永州人。
通讯作者:邓岭(1985-),女,湖南娄底人,硕士研究生,主要研究方向:机械设计理论。
凸轮机构是工程中用以实现机械化和自动化的一种重要驱动和控制机构,在轻工、纺织、食品、医药、印刷、交通运输等领域运行的工作机械中均有应用[1]。
汽车内燃机的配气机构往往采用凸轮机构,由于配气机构配合活塞运动进行吸气和排气,配气机构设计合理与否将直接关系到发动机运行的稳定性,噪音,效率及寿命等问题,因此配气机构的设计非常关键[2]。
而配气机构的运动是由凸轮轮廓控制,因此凸轮轮廓曲线设计是配气机构设计的中心环节。
凸轮轮廓曲线设计一般可分为图解法和解析法,其中图解法绘制轮廓曲线有很大的弊端,工作量大,精度不高。
解析法则可精确地计算出轮廓线上各点的坐标,实现凸轮的高精度设计。
Matlab 是一种科学计算软件,利用Matlab 编程可进行凸轮机构的解析法设计,并对从动件的运动规律(位移、速度、加速度和轮廓线)进行仿真绘制,以达到凸轮轮廓线的精确设计[3]。
UG NX 具有强大的曲线建模功能,将MATLAB 生成的凸轮轮廓线上点的坐标导人UG NX 中,建立配气凸轮机构模型再进行运动仿真从而得到气门运动规律并验证其凸轮结构的合理性,实现凸轮结构的优化设计。
AUTOLISP凸轮设计及仿真

key="key_alf1"; width=20; } :edit_box{ label="近休止角 alf2:"; key="key_alf2"; width=20; } :edit_box{ label="回程运动角 alf3:"; key="key_alf3"; width=20; } :edit_box{ label="远休止角 alf4:"; key="key_alf4"; width=20; } :button{ label="绘制理论轮廓"; key="draw_lilun"; }
一、对话框的设计
AutoCAD 为用户提供的可编程对话框技术是由专用的对话框 描述语言(DCL)和 AutoLISP 驱动函数两部分内容组成的。 对话框由框架和包含在框架内的控件组成。一个对话框由位 于其中的按钮(单选框、复选框、图像、动作) 、文本编辑框、弹出 式列表框和滑动条等控件组成。
1.控件的定义方式 2.
(defun c:My-circle() (setq pt (list 100 100)) ;;; 得到圆心坐标 (setq r 50) ;;; 得到半径
(command “circle” pt r) ;;; 绘制圆 ) 规则 1:以括号组成表达式,左右括号“ (”&“)”一定要配对。 表达式是 AutoLISP 的基本语句, 所有表达式都具有以下形式: (函数 [参数表]) 即由一个函数名和调用这个函数所需的参数表组成。 参数表中的 参数也可以是表达式,即 AutoLISP 的表达式可以嵌套。 规则 2:注释以分号“;”开头,它可以单独位于一行,也可以位于某 一程序语句的后面。 编写 AutoLISP 程序时,应添加必要的注释,以说明程序的功能、 规则 3:“前缀表示法”。 AutoLISP 语 言 的 结 构 与 常 用 高 级 结 构 有 所 区 别 。 像 BASIC 、 PASCAL、C 等语言均采用“中缀表示法”。当给变量 a 赋值 12.0 时, 通常为下面的形式: a=12.0; 即赋值运算符“=”位于中间。 AutoLISP 则采用,即把运算符放在参数表的第一个元素的位置,后 面为其参数。 例如,通常用到的表达式 X=(A+B)×C 在 AutoLISP 中表示为: (setq X (* (+ A B) C) )
SolidWorks三维设计及运动仿真实例教程 实例23 凸轮机构运动仿真

添加马达 仿真参数设置 曲线接触运动仿真 实体接触动力学仿真
工作原理 零件造型 装配 仿真
在MotkmManager界面中,拖动键 码将时间的长度拉到1s,单击工具栏上的 “运动算例属性”按钮,在弹出的“运动 算例属性”管理器中的【Motion分析】 栏内将每秒帧数设为“100”,选中【3D 接触分辨率】下的【使用精确接触】复选 框,其余参数采用默认设置,如图所示, 单击“确定”按钮,完成仿真参数的设置。
工作原理 零件造型 装配 仿真
创建凸轮
坐标数据将显示在“曲线文件”中;单击【确定】,
创建滚子、摆杆和机架 凸轮理论廓线被绘制出来,如图所示。
工作原理 零件造型 装配 仿真
创建凸轮 创建滚子、摆杆和机架
点击【草图】【草图绘制】 命令,选择【前视基准面】;点 击【等距实体】命令,单击前面 绘制好的曲线,输入摆杆滚子半 径12mm,点击【反向】,点击 【确定】,将曲线转换成草图曲 线,得到凸轮实际轮廓曲线,如 图所示。
右击 FeatureManager设 计树中的“材质<未指定>”, 在弹出的菜单中选择 “普通碳 钢”。最后以文件名“凸轮”保 存该零件。
工作原理 零件造型 装配 仿真
创建凸轮
根据已知条件:滚子半径=12mm,摆杆长度=
创建滚子、摆杆和机架
120mm,凸轮与摆杆转动中心距离= 150mm,根据以下 三个草图,以距离10mm两侧对称拉伸草图轮廓,得到
入,单击布局选项卡中的【运动算例1】, 在 MotionManager工具栏中的【算例类型】下拉列表中 选择“Motion分析”。
实体接触动力学仿真
单击MotionManager 工具栏中的“马达”按钮 ,为 凸轮添加一逆时针等速旋转 马达,如图所示,凸轮转速 n=72RPM = 432° /s,马达 位置为凸轮轴孔处。
inventor学习资料运动仿真简介CAD系列
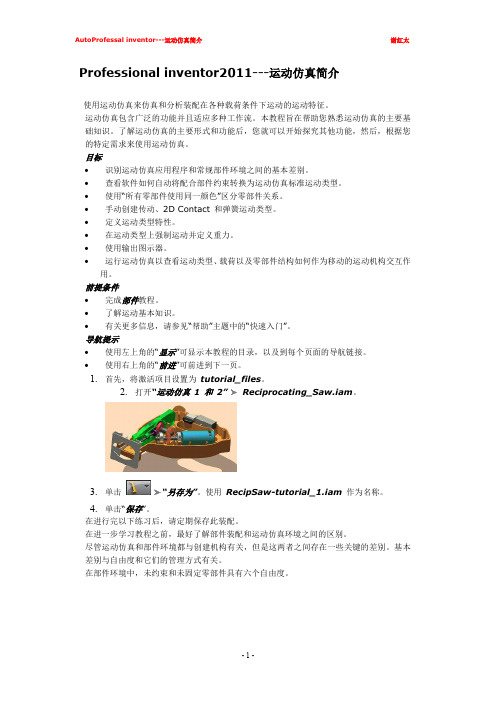
3. 单击
“另存为”。使用 RecipSaw-tutorial_1.iam 作为名称。
4. 单击“保存”。
在进行完以下练习后,请定期保存此装配。 在进一步学习教程之前,最好了解部件装配和运动仿真环境之间的区别。 尽管运动仿真和部件环境都与创建机构有关,但是这两者之间存在一些关键的差别。基本 差别与自由度和它们的管理方式有关。 在部件环境中,未约束和未固定零部件具有六个自由度。
具有自由度的零部 件,自由度允许它们 在应用力时参与仿
-2-
AutoProfessal inventor---运动仿真简介
谢红太
真。
每个移动组都指定了特定 颜色。在“移动组”文件夹 上单击鼠标右键,并单击 “所有零部件使用同一颜 色”来可视决定零部件所 在的移动组。
“标准 类型” 文件 夹来自当进入运动仿真环境 时由自动约束转换创 建的运动类型。起作 用的约束显示为子节 点。
1. 在功能区上,单击
“环境”选项卡 “开始”面板 “运动仿真”。
注意如果系统提示您运行“运动仿真”教程,请单击“否”。 随即激活运动仿真环境。您将注意到浏览器和其节点为仿真环境而更改。 在仿真浏览器中,有多个仿真对象的文件夹。它们与仿真的关系如下所示:
“固 定”文 件夹
没有自由度的零部件
“移动 组”文 件夹
各种 运动 类型 文件 夹
创建的所有非标准运 动类型都位于这些特 定运动类型的文件夹 中。起作用的约束显 示为子节点。
“外部 载荷” 文件 夹
您定义的载荷(包括 重力)显示在该文件 夹中。
2.
注意包括 Inventor 2008 以前的旧运动仿真对象的部件在进入仿真环境时不会自 动转换约束。
3. 展开“标准运动类型”文件夹。
凸轮机构的计算机辅助设计与运动仿真分析
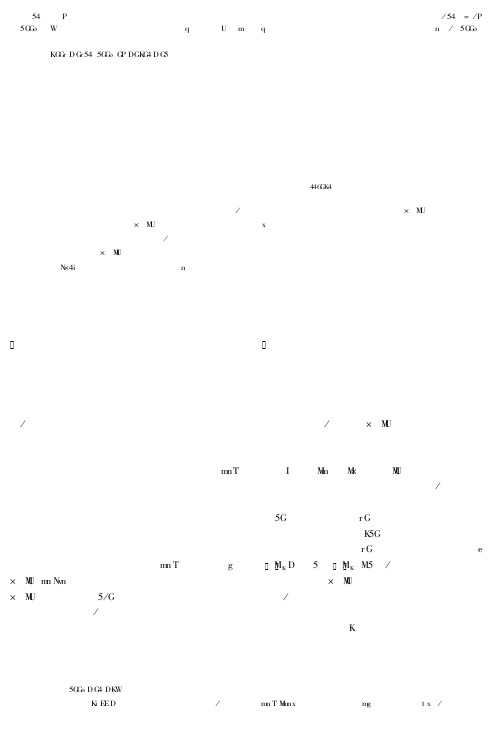
首先确定零件的形状、 结构、 尺寸和公差等, 并在计 算机上进行二维绘图和三维实体造型, 然后通过装 配模块完成零 件组装, 形成整机 . 装配是动态仿真 的前提, 装配关系的正确与否直接影响动态仿真的
足要求, 在此我们以其运动轨迹为例来说明分析运 效果 . 装配前, 先确定运动构件及构件间的运动副, 动机构和获取分析结果的过程 . 最后由各机构构成整机, 并为仿真做准备 . � � � � � � � � � � � � 单击特征操作按钮区的分析 ( A ) 凸轮机构的装配并不复杂, 在装入机架零件之 按钮通过相应的对话框定义分析名称, 后单击特征操作区的增加组件 (A 单击特征操 作按钮区的测量 (G � � � � � � � � � � � � � � ) 按钮装入凸轮, 在此要注意的是应该选择 ) 定义测量名 称、 测量类型、 测量对 元件放置 (C ) 对话框的连接 (C 象、 评估方式等, 在这里 我们选择测量从动件末 点 ) 按钮, 打开连接面板, 并在连接类型中选择销 位移, 接受系统的每时间步距 (E ) 的评 � � � � � � � � � � � 钉 ( ) 连接, 按照系统提示选取相应的对象从而完 估方法, 在按照要求完成了所有的参数定义之后就 成连接方式的建立 . 凸轮机构其他零部件的连接方 可以得到分析结果, 对于改点的位置变化我们可以 式可按照此方法依次完成, 其装配模型如图 2 所示 . 通过产生其轨迹线的方法来直接观察, 也可以输出 � . � 设置运动环境 位移—时间图 表来记录, 还可以通过产 生 E 表 � � � � 凸轮的运 动环境主要应 该完成弹簧、 阻尼器、 来对数据进行存储 . 这几种情况分别如图 4 所示: 驱动器等的设置 . 首先在装配模型的环境下通过菜 当然对于以上的运动模型 不仅可以观察 其运 单栏择应用程序 (A ) 进入 M 工作环 动情况, 还可以完成相应的速度分 析、 加速度分 析 境, 按照一定的方法建立凸轮随动连接以及槽随动 以及受力分析, 同样的我们可以得到不同形式的分 连接 . 接下来单击特征操作区的弹簧 ( ) 按钮, 打开弹簧对话框, 设置其属性: “ =15 , =3 7. 6 , 83 ” 并设置好弹簧图标的显示直径, 同样的 法单击特 征操作按 钮区的阻尼器 (D D ) 打开其对 话框设置好基准点以及阻尼系 , 最后单击特征操 作区的伺服电动机 (D M ) 按 钮, 按照 析结果 . (下转第 118 页)
基于AutoCAD, VB,Mathematica和Working model的凸轮设计与仿真

基于AutoCAD, VB,Mathematica和Working model的凸轮设计与仿真目录摘要 (1)引言 (1)凸轮设计要求 (2)Excel软件辅助设计 (2)AutoCAD凸轮轮廓线设计 (3)VB编程作凸轮轮廓线并仿真 (4)Mathematica编程作凸轮轮廓线 (9)Working Model凸轮仿真 (13)各个软件比较 (15)课题研究收获 (15)参考文献 (16)摘要凸轮是具有曲面轮廓的构件,一般多为原动件。
当凸轮为原动件时,通常做等速的转动或移动,而从动件就按照预期的输出特性要求做连续或间隙的往复运动,移动或平面复杂运动。
本文主要介绍用Excel 计算凸轮轮廓线坐标数据,然后导入AutoCAD和Working model中生成凸轮轮廓线。
还介绍了用VB和Mathematica编程来设计凸轮轮廓线并对凸轮进行仿真。
主要技术要求是熟悉凸轮设计基本原理及相关理论计算,能熟练使用Excel,AutoCAD和Working model等软件,熟悉VB和Mathematica编程语言,能将他们相结合起来应用到设计仿真中。
关键词:凸轮,Excel,AutoCAD,Working model,VB和Mathematica,设计,仿真。
引言盘形凸轮设计的主要任务是绘制凸轮的轮廓曲线, 传统设计方法分为图解法和解析法两种。
其中图解法是根据从动件的位移曲线, 按“反转法”原理, 做出从动件在反转过程中所占据的一系列位置, 从而求得凸轮轮廓曲线。
图解法可用手工法和计算机辅助设计的方法进行。
手工图解法设计凸轮的轮廓曲线误差较大, 故对于精度要求高的高速凸轮往往不能满足要求。
计算机辅助作图的方法来作凸轮曲线需要足够多的轨迹上的点的坐标才能达到高的精度要求。
但是求解大量点的坐标计算繁琐,所以我们就利用Excel强大的的表格数据处理功能来准确便捷的计算出足够多的点的坐标数据,然后将这些数据导入AutoCAD中生成凸轮轮廓线,我们还将数据导入Working Model中,这就可以对凸轮的运动做直观地观察。
- 1、下载文档前请自行甄别文档内容的完整性,平台不提供额外的编辑、内容补充、找答案等附加服务。
- 2、"仅部分预览"的文档,不可在线预览部分如存在完整性等问题,可反馈申请退款(可完整预览的文档不适用该条件!)。
- 3、如文档侵犯您的权益,请联系客服反馈,我们会尽快为您处理(人工客服工作时间:9:00-18:30)。
基于Autodesk Inventor的共轭凸轮设计与运动仿真
笔者结合工作中的实际案例——一位使用Inventor产品多年的印刷机械设备用户,困惑于如何借助3D软件提升设计能力——分析其设计难题,例如比较普遍的凸轮设计问题,其中一个共轭凸轮的机构设计尤为难以实现。
本文就是基于解决用户共轭凸轮设计难题的真实案例,介绍了借助Autodesk Inventor设计共轭凸轮的方法及思路。
一、设计要求
用户设计某胶订机,其中一台设备使用到一对共轭凸轮,其中一个凸轮是顶升凸轮,带动机构在垂直方向运动,另一个凸轮带动一个连杆机构,连杆机构的末端带动一个滑块做水平运动,机构简图如图1。
T形结构FF’E中,端点E与凸轮1的从动件连结,连杆AB的端点A 连接在滑块上,沿FF’平面做水平往复运动,连杆BCD绕C点转动,D点与凸轮2从动件连结,凸轮1和凸轮2绕同一根轴旋转。
1.凸轮1(垂直运动)
盘式顶升凸轮(沟槽)做垂直方向往复运动。
凸轮基圆半径为50mm,凸轮升程为30mm,带动T形结构做垂直方向运动,其在一个周期内的运动规律如表所示。
2.凸轮2(水平运动)
凸轮驱动连杆机构运动,连杆机构的末端连结到一个滑块,滑块的设计要求为一个往复行程为400mm,为配合机构的运动要求,其速度按照如图2所示规律运动。
本文重点在于说明设计的思路,对于机构的具体尺寸以及系统转速等不做说明,上述的设计参数也仅作示意,不代表实际设计数值。
二、设计分析
常见的凸轮形式,包括线性凸轮、盘式凸轮及圆柱凸轮三大类,很多CAD软件没有直接提供凸轮设计工具,需要用户去创建凸轮的轮廓线(通过创建公式曲线,以数据点拟合样条曲线),而轮廓的几何外形仅仅表达了凸轮的位移变化,还无法满足对凸轮性能分析的需求(速度曲线、加速度曲线和压力角变化等)的分析,造成用户设计效率低下,凸轮优化困难。
Inventor凸轮设计模块集凸轮设计、计算校验于一身,支持上述三种凸轮,其自带了多达13种拟合函数,最高支持七阶多项式,无需用户推导解析函数,即能生成高质量的凸轮轮廓。
凸轮1是一个简单的盘式顶升凸轮,根据表1的设计要求,借助Inventor的凸轮设计工具,我们可以快速设计出其外形轮廓,同时其速度、加速度运动曲线,压力角、曲率半径变化曲线一目了然,而且对运动过程中的力、扭矩及接触应力也自动计算,大大提高了设计的准确
性和设计效率。
图3Inventor盘式凸轮设计
对于凸轮2,由于无法直接描述其运动规律(位移或速度、加速度),因此无法直接借助Inventor的凸轮设计功能来进行设置。
在一些案例中,往往根据连杆机构的机械原理,建立凸轮2、连杆机构、滑块之间的运动解析方程,借助Matlab求解出凸轮2上的运动轨迹点,从而得到凸轮2的轮廓。
这种方法,对设计人员的要求高,适合院校研究,但很难在企业中应用推广。
因此,设计凸轮2的凸轮轮廓是整个产品设计的最大难点。
三、设计思路
Inventor的Professional版本中,提供了运动仿真(DynamicSimulation)模块,通过定义构件之间的运动副(连接类型),定义构件的运动特性(力、力矩、位移、速度、加速度以及刚度、阻尼等),将几何关系模型转换为具有运动关系的模型,从而让几何模型按照给定的要求运动,达到动态模拟、仿真机构运动的目的。
基于上面的分析,尽管凸轮2的运动规律我们很难描述,但是由其驱动连杆机构而产生水平运动的滑块,其设计运动规律是整个系统设计的性能要求,我们可以视为滑块的运动规律,从而反向推导(模拟)连杆机构的端点D的运动轨迹,也就是我们所要设计的凸轮2的外形轮廓。
1.建立几何模型
几何模型的准备,重点在于清晰表达出构件之间的几何位置关系,模型可以基于2D草图,或者基于3D模型,甚至也可以2D/3D混合建模,这为设计人员在设计前期做方案设计及验证提供了很大的便利性。
图4是创建的概念几何模型,其中凸轮1是采用Inventor的凸轮设计工具完成的3D模型,连杆机构仅用2D草图表达出其几何关系。
2.建立运动仿真模型
Inventor的运动仿真模块集成于产品内,能够很好地将几何模型的几何约束(装配约束)转换为运动副(运动关系)。
Inventor运动仿真模块具有丰富的运动副定义,节省了用户耗费在模型准备和运动副定义上的时间。
在本文中,定义仿真运动模型时我们使用了以下几类运动副(图5)。
◎滑块与T形结构上平面的水平运动;
◎凸轮1与T形结构顶端圆弧面的接触;
◎连杆机构的各杆件之间的转动关系;
◎T形结构只能在平面内上下运动。
3.定义驱动条件
参考图2,设计要求中对滑块的速度及位移相应的要求。
按照这些要求,定义出滑块的运动规律,作为机构的驱动条件,如图6所示。
4.执行运动仿真
在完成前面的定义之后,输入模拟仿真的时间(时间≥凸轮周期时间)及模拟步数,定义输出连杆的端点D的运动轨迹,执行仿真分析,凸轮2的运动轨迹即可生成,如图7所示。
5.设计调整
仔细观察滑块的运动轨迹,和设计要求不太吻合,主要反映在凸轮2带动滑块做匀速运动的时间段,凸轮1带动的T形结构不在最上端位置时,分析其原因是由于没有调整好凸轮1与凸轮2的相位差。
从Inventor的运动仿真结果中,我们可以很容易查看到滑块的运动位置及相应的运动时间,从而可以计算出凸轮1需要调整的相位值,和需要调整的角度值(角度=时间×凸轮转动角速度)。
根据计算结果修订凸轮1的初始位置,如图8所示。
调整后再次执行运动仿真,模拟输出的运动轨迹如图9所示,完全符合期望的设计要求。
图9调整后运动仿真结果
四、结语
本文借助运动仿真软件进行复杂机构的设计和分析,大幅提高了设计的准确性和设计效率。
在本设计中,通过和传统解析法的对比,无论是在设计周期还是在最终设计产品的质量上,新的方法都体现出其优势。