五金模具常见十大问题及解决方案
五金模具拉伤的原因及解决措施
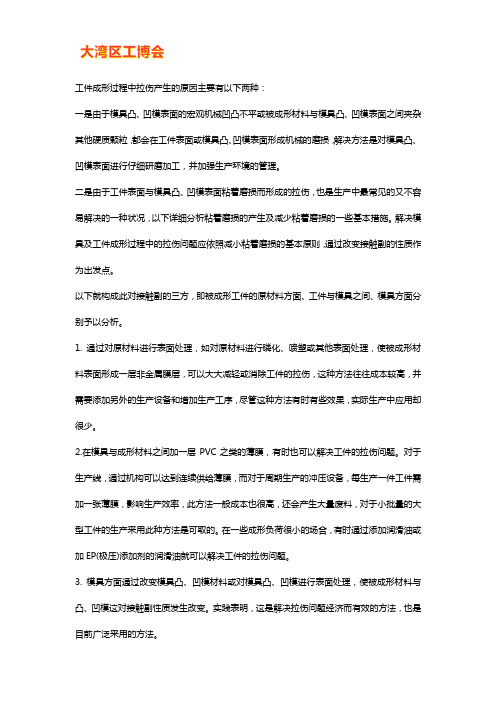
工件成形过程中拉伤产生的原因主要有以下两种:一是由于模具凸、凹模表面的宏观机械凹凸不平或被成形材料与模具凸、凹模表面之间夹杂其他硬质颗粒,都会在工件表面或模具凸、凹模表面形成机械的磨损,解决方法是对模具凸、凹模表面进行仔细研磨加工,并加强生产环境的管理。
二是由于工件表面与模具凸、凹模表面粘着磨损而形成的拉伤,也是生产中最常见的又不容易解决的一种状况,以下详细分析粘着磨损的产生及减少粘着磨损的一些基本措施。
解决模具及工件成形过程中的拉伤问题应依照减小粘着磨损的基本原则,通过改变接触副的性质作为出发点。
以下就构成此对接触副的三方,即被成形工件的原材料方面、工件与模具之间、模具方面分别予以分析。
1. 通过对原材料进行表面处理,如对原材料进行磷化、喷塑或其他表面处理,使被成形材料表面形成一层非金属膜层,可以大大减轻或消除工件的拉伤,这种方法往往成本较高,并需要添加另外的生产设备和增加生产工序,尽管这种方法有时有些效果,实际生产中应用却很少。
2.在模具与成形材料之间加一层PVC之类的薄膜,有时也可以解决工件的拉伤问题。
对于生产线,通过机构可以达到连续供给薄膜,而对于周期生产的冲压设备,每生产一件工件需加一张薄膜,影响生产效率,此方法一般成本也很高,还会产生大量废料,对于小批量的大型工件的生产采用此种方法是可取的。
在一些成形负荷很小的场合,有时通过添加润滑油或加EP(极压)添加剂的润滑油就可以解决工件的拉伤问题。
3. 模具方面通过改变模具凸、凹模材料或对模具凸、凹模进行表面处理,使被成形材料与凸、凹模这对接触副性质发生改变。
实践表明,这是解决拉伤问题经济而有效的方法,也是目前广泛采用的方法。
(1)从模具凸、凹模材料入手解决工件的拉伤问题,可以采用硬质合金,一般情况下,由这种材料制作的凸、凹模抗拉伤性能很高,存在的问题是材料成本高,不易加工,对于较大型的模具,由于烧制大型硬质合金块较困难,即使烧制成功,加工过程中也有可能出现开裂,成材率低,有些几乎难以成形。
五金冲压模具常见问题及处理方法汇总
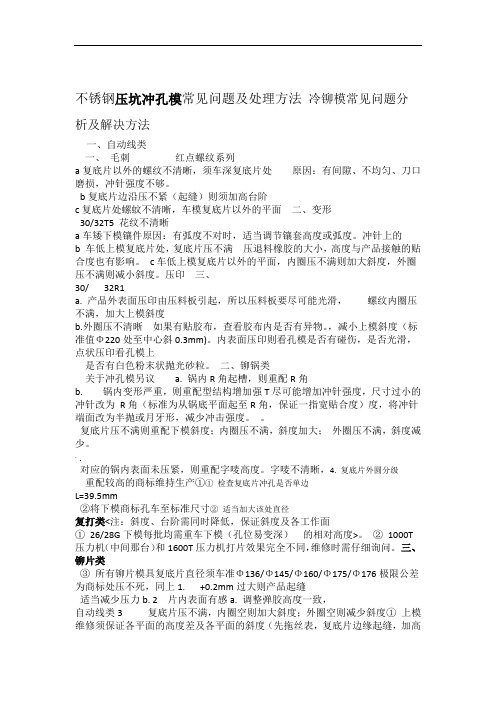
不锈钢压坑冲孔模常见问题及处理方法冷铆模常见问题分析及解决方法一、自动线类一、毛刺红点螺纹系列a复底片以外的螺纹不清晰,须车深复底片处原因:有间隙、不均匀、刀口磨损,冲针强度不够。
b复底片边沿压不紧(起缝)则须加高台阶c复底片处螺蚊不清晰,车模复底片以外的平面二、变形30/32T5 花纹不清晰a车矮下模镶件原因:有弧度不对时,适当调节镶套高度或弧度。
冲针上的b 车低上模复底片处,复底片压不满压退料橡胶的大小,高度与产品接触的贴合度也有影响。
c车低上模复底片以外的平面,内圈压不满则加大斜度,外圈压不满则减小斜度。
压印三、30/ 32R1a. 产品外表面压印由压料板引起,所以压料板要尽可能光滑,螺纹内圈压不满,加大上模斜度b.外圈压不清晰如果有贴胶布,查看胶布内是否有异物。
,减小上模斜度(标准值Φ220处至中心斜0.3mm)。
内表面压印则看孔模是否有碰伤,是否光滑,点状压印看孔模上是否有白色粉末状抛光砂粒。
二、铆锅类关于冲孔模另议 a. 锅内R角起槽,则重配R角b. 锅内变形严重,则重配型结构增加强T尽可能增加冲针强度,尺寸过小的冲针改为R角(标准为从锅底平面起至R角,保证一指宽贴合度)度,将冲针端面改为半抛或月牙形,减少冲击强度。
复底片压不满则重配下模斜度;内圈压不满,斜度加大;外圈压不满,斜度减少。
.对应的锅内表面未压紧,则重配字唛高度。
字唛不清晰,4.复底片外圆分级重配较高的商标维持生产①①检查复底片冲孔是否单边L=39.5mm②将下模商标孔车至标准尺寸②适当加大该处直径复打类<注:斜度、台阶需同时降低,保证斜度及各工作面①26/28G下模每批均需重车下模(孔位易变深)的相对高度>。
②1000T 压力机(中间那台)和1600T压力机打片效果完全不同,维修时需仔细询问。
三、铆片类③所有铆片模具复底片直径须车准Φ136/Φ145/Φ160/Φ175/Φ176极限公差为商标处压不死,同上1.+0.2mm过大则产品起缝适当减少压力b. 2 片内表面有感a. 调整弹胶高度一致,自动线类3 复底片压不满,内圈空则加大斜度;外圈空则减少斜度①上模维修须保证各平面的高度差及各平面的斜度(先拖丝表,复底片边缘起缝,加高边缘处台阶高度,保证台阶直径记录数据,0.1~0.15mm 和复底片直径相等或大再动平车)②配车复底片直径处须遵循以下步骤,11sΦ145片为例:a.车准斜度b.车直径Φ142-Φ143 具常见问题及处理办法冷铆模铝制品c.车准台阶高约0.3mmd.台阶直径Φ142处圆滑连接。
模具问题点总结及改善方法

模具问题点总结及改善方法嘿,大家好,今天咱们聊聊模具的问题。
模具在生产中可是个“核心角色”,没有它,产品就像缺了腿的蜈蚣,走不动。
可是,模具也不是总能顺风顺水,时不时地就会有点小麻烦。
这时候,咱们就得好好“琢磨琢磨”,找出问题的根源,想办法解决。
要知道,问题来了,咱们可不能慌张,得先冷静下来,看看是什么原因。
模具不合格,可能是材料不对劲,或者设计上出了岔子。
这就像做菜,食材不新鲜,出来的菜肴肯定没味道。
咱们得“深挖”一下这些问题。
比如说,模具的寿命短得吓人,真让人感到心累。
这时候,得好好看看使用的材料是不是够硬气,能不能撑得住频繁的使用。
模具的保养也非常重要,像小孩儿一样,要经常关心、维护。
这些看似简单的事情,往往会被大家忽视,结果就像是“竹篮打水一场空”。
所以啊,定期的检查和维护,绝对是必不可少的。
说到模具的设计,嘿,这可是个大工程。
很多时候,设计师一时“兴起”,搞出来的模具形状复杂得让人摸不着头脑。
这样一来,生产时就容易出现误差,真是得不偿失啊。
我们得明白,设计要简洁实用,像是“萝卜青菜,各有所爱”。
大多数情况下,简单的设计反而能提高生产效率。
为了避免问题,设计师和工程师之间得多沟通,多交流,把想法摊开来讨论,这样才能减少误解。
生产过程中的操作也得小心翼翼。
操作者的技术水平直接影响到模具的使用效果。
就像开车,技术好的人,车子开得稳,技术差的人,容易出事故。
所以,培训是必不可少的,得让每个人都知道该怎么用模具,注意事项有哪些。
就算再忙,也得把这个环节搞好,绝对不能草率。
如果模具在使用过程中出现了问题,大家一定要保持“冷静”。
要知道,有时候小问题不及时解决,最后可能会演变成大麻烦。
像是漏水的水龙头,初始只是小滴水,等你发现时,整个厨房都淹了。
所以,及时排查,及时处理,是王道。
这里的关键就是要建立一个完善的反馈机制,随时收集操作员的意见,及时了解模具的使用情况。
咱们还得考虑到模具的升级换代。
就像人一样,时间一长,总得更新换代,才能跟上时代的步伐。
模具常见问题分析及其解决方法

模具常见问题分析及其解决方法概述模具是工业生产中常用的一种工具,它在各个行业中被广泛应用。
然而,随着使用时间的增加,模具也会出现各种问题。
本文将详细分析模具常见问题,并提供相应的解决方法,以帮助读者更好地应对模具问题。
问题一:模具磨损严重模具磨损是使用寿命过程中常见的问题之一。
其主要表现为模具表面磨损或凹陷。
磨损的原因可能是: - 使用材料硬度较高 - 使用时间较长 - 模具润滑不足 - 模具设计不合理解决方法: - 使用耐磨性能更好的模具材料,如优质钢材 - 定期进行模具保养和维护,及时更换磨损严重的部件 - 在使用过程中保持适当的模具润滑,减少磨损 - 对模具进行优化设计,减少出现磨损的可能性问题二:模具尺寸偏差大模具尺寸偏差大是另一个常见问题。
这可能导致生产出的产品尺寸不准确,影响产品质量。
尺寸偏差大的原因包括: - 模具制造过程中的测量误差 - 模具材料膨胀或收缩不均匀 - 模具结构设计不合理解决方法: - 提高模具制造过程中的测量精度,并进行多次验证 - 选择合适的模具材料,控制材料膨胀或收缩的影响 - 对模具结构进行优化设计,避免尺寸偏差的产生问题三:模具易生锈模具易生锈是模具在使用过程中常见的问题之一。
模具生锈不仅影响外观,还可能导致模具损坏。
模具易生锈的原因可能是: - 环境湿度较高 - 模具存放不当 - 模具润滑不足解决方法: - 控制使用环境湿度,尽量保持干燥 - 对模具进行正确的存放,避免受潮或受酸碱腐蚀 - 在使用过程中,保持模具的适度润滑,防止生锈问题四:模具易断裂模具易断裂是一种严重的问题,可能导致模具报废,造成生产线停机。
模具易断裂的原因包括: - 模具结构设计不合理 - 模具材料不合格或强度低 - 模具使用过程中发生过载解决方法: - 对模具结构进行优化设计,提高其受力性能 - 选择合适的模具材料,确保其强度和韧性满足要求 - 在使用过程中,避免过载操作,及时发现并处理异常情况问题五:模具易堵塞模具易堵塞是模具在使用过程中常见的问题,特别是对于塑料注塑模具。
五金模具失效案例分析

五金模具失效案例分析
1、五金模具在冲压过程中,如果存在模具强度设计不够或受力不均,模具导向不良、倾斜,或模板间有异物等情况,就会导致具合模不灵活,甚至卡死。
这时就需要停止生产,找出卡模原因,排除故障,否则,就会扩大故障,导致模具损坏。
2、五金模具的制造材料及其热处理工艺是否适合,对模具质量影响很大,如果冲压模具的淬火温度过高,淬火方法和时间不合理,以及回火次数和温度、弯头管件,肘间选择不当,都会导致模具进入冲压生产后损坏,五金冲压件质量受损。
3、五金模具在加工过程中,如果有异物进入冲压模具、制件重叠、废料阻塞等情况出现,却没能未及时处理,模具还继续使用,就很容易导致模具的落料板、冲头、下模板和导柱损坏。
4、五金冲压模具落料孔尺寸或深度设计不够,容易使槽孔阻塞,造成落料板损坏。
弹簧力设计太小或等高套不等高,会使弹簧断裂、落料板倾斜,造成重叠冲打,损坏零件。
冲头固定不当或螺丝强度不够,会导致冲头掉落或折断,损坏模具。
5、五金模具在使用时,零件位置、方向等安装错误或螺栓紧固不好。
工作高度调整过低、导柱润滑不足,送料设备有故障,压力机异常等,都会造成冲压模具的损坏。
五金模具常见故障原因及处理对策

五金模具常见故障原因及处理对策在级进模的冲压生产中,针对冲压不良现象必须做到具体分析,采取行之有效的处理对策,从根本上解决所发生之问题,如此才能降低生产成本,达到生产顺畅。
以下就生产中常见的冲压不良现象其产生的原因及处理对策分析如下,供模具维修人员参考。
1.冲件毛边.(1)原因:a、刀口磨损;b、间隙过大研修刀口后效果不明显;c、刀口崩角; d、间隙不合理上下偏移或松动;e、模具上下错位。
(2)对策:a、研修刀口;b、控制凸凹模加工精度或修改设计间隙;c、研修刀口;d、调整冲裁间隙确认模板穴孔磨损或成型件加工精度等问题;e、更换导向件或重新组模。
2.跳屑压伤(1)原因:a、间隙偏大;b、送料不当;c、冲压油滴太快,油粘;d、模具未退磁;e、凸模磨损,屑料压附于凸模上;f、凸模太短,插入凹模长度不足;g、材质较硬,冲切形状简单;h、应急措施。
(2)对策:a、控制凸凹模加工精度或修改设计间隙;b、送至适当位置时修剪料带并及时清理模具;c、控制冲压油滴油量,或更换油种降低粘度;d、研修后必须退磁(冲铁料更须注意);e、研修凸模刀口;f、调整凸模刃入凹模长度;g、更换材料,修改设计。
凸模刃入端面装顶出或修出斜面或弧性(注意方向)。
减少凸模刃部端面与屑料之贴合面积;h、减小凹模刃口的锋利度,减小凹模刃口的研修量,增加凹模直刃部表面的粗糙度(被覆),采用吸尘器吸废料。
降低冲速,减缓跳屑。
3.屑料阻塞(1)原因:a、漏料孔偏小;b、漏料孔偏大,屑料翻滚;c、刀口磨损,毛边较大;d、冲压油滴太快,油粘;e、凹模直刃部表面粗糙,粉屑烧结附着于刃部;f、材质较软;g、应急措施。
(2)对策:a、修改漏料孔;b、修改漏料孔;c、刃修刀口;d、控制滴油量,更换油种;e、表面处理,抛光,加工时注意降低表面粗糙度;更改材料,f、修改冲裁间隙;g、凸模刃部端面修出斜度或弧形(注意方向),使用吸尘器,在垫板落料孔处加吹气。
4.下料偏位尺寸变异(1)原因:a、.凸凹模刀口磨损,产生毛边(外形偏大,内孔偏小);b、设计尺寸及间隙不当,加工精度差;c、下料位凸模及凹模镶块等偏位,间隙不均;d、导正销磨损,销径不足;e、导向件磨损;f、送料机送距、压料、放松调整不当;g、模具闭模高度调整不当;h、卸料镶块压料位磨损,无压料(强压)功能(材料牵引翻料引发冲孔小);i、卸料镶块强压太深,冲孔偏大;j、冲压材料机械性能变异(强度延伸率不稳定);k、冲切时,冲切力对材料牵引,引发尺寸变异。
五金模问题点

五金模问题点第一篇:五金模问题点连续冲模常见设计缺陷连续冲模常见设计缺陷一.冲裁中常见不良1.跳屑2.金属丝3.冲子蹦4.模仁裂与堵料5.接刀毛头6.尺寸超差7.压板断8.啃刀口9.接刀设计错(粗定位无效果)二.折弯成形常见不良1.违反先压料后成形原则2.冲子断差太大3.框口磨损4.拉毛5.两次折弯折弯线设计错6.折弯成形尺寸不稳定7.成形尺寸不到位8.浮动模仁定位段太短,晃动幅度大9.浮动模仁或Lifter,易跳出来(危险性大),或者设计强度太差10.KINK的成形问题11.尺寸不良的几个因素:1)角度2)圆角3)展开长度4)折弯线处之逃料三.整形机构1.斜面整形的适用范围及常见问题点2.摆块整形机构的适用范围及常见问题点3.斜面整形机构的适用范围及常见问题点4.一次折弯整形机构的局限性四.翻边打卡荀等起伏成形工站常见问题点1.翻边口部裂纹2.翻边高度小3.扭力不足4.翻边起皱5.卡荀断6.起伏成形对相邻已成形尺寸的影响7.撕破成形高度偏低五.下料时常见问题:(下料不畅)1.废料留在模面2.下料不畅,加吹气,顶杆3.混料4.下产品改为下废料(吹气方式)六.抽引中常见问题点1.毛坯太大2.毛坯太小3.抽引拉裂4.抽引起皱5.壁部拉毛6.Carry 相互挤压7.定位不可靠8.大肚子七.结构设计中常见问题:1.定位针固定在冲子固定板上2.剥料套设计不良3.料条定位不好(追加导板)4.压板,弹簧断裂(改冲子固定方式)5.背板螺丝太靠外6.抽引第一抽不分开7.缺少整形工站8.定位针太少,太细9.Lifter无爬坡(模仁太短)八.料条设计问题:1.刚性太差2.前后工序排配不合理3.粗定位无效4.定位针孔太靠后九.几种常见的典型机构十.其它常见问题:1.大平面的平面度问题2.SMT PAD的共面度问题3.铆合中的一些问题及解决措施4.料带式产品的扇形(波浪形)第一章冲裁中常见不良一.跳屑一)跳屑的几种情况:1.切边时的跳屑:原因:系不完整的冲孔废料难以有效卡在模仁里,故易跳屑改善措施:修边结构复杂化2.小方孔,小圆孔跳屑原因:1)间隙太大2)有较多的油3)料太薄改善措施:1)收紧间隙2)减少用油3)加向下吹气,在废料下面形成负压4)设变模仁加工方式(改为PG加工),提高刃口段光洁度5)对冲子结构作重新设计6)对铁材产品模具备品须退磁干凈)3.细小废屑:(常见于有撕破的模具,有重切时尤为时显)4.大片废屑的跳屑原因: 同2改善措施:1)加顶杆2)加吹气3)对其形状复杂化5.其它状况的跳屑:原因:工序排配设计不合理改善措施:重新调整工序排配(重新设计接刀)二)跳屑的危害:1.产生模痕,压伤等不良2.对间歇性跳屑,不易发现,极易流出不良品3.维修不易(常采用异形冲子,刃口披覆等有损备品寿命和产品断面质量的方式)致生产效率和稼动率低4.不良品产生时常需大量的人工进行挑选二.金属丝一)危害:1.组装成成品后,极易造成短路(SHORT),是要绝对禁止的严重一种不良2.脱落时易在产品上产生模痕3.当有发生时须耗费大量的人力对其重工二)产出原因:常见于有撕破的模具,比如:1.先向下撕破,后又被向上拍平,撕破切口处产生二次挤压,形成金属丝2.先向一个方向撕破后又向相反方向折弯成形3.一次撕破折弯不到位时,让设计不合理三)改善措施:1.撕破处后面工站闪开(放电)避免撕破和被反复拍打。
五金模具表面处理常见缺陷分析和消除措施
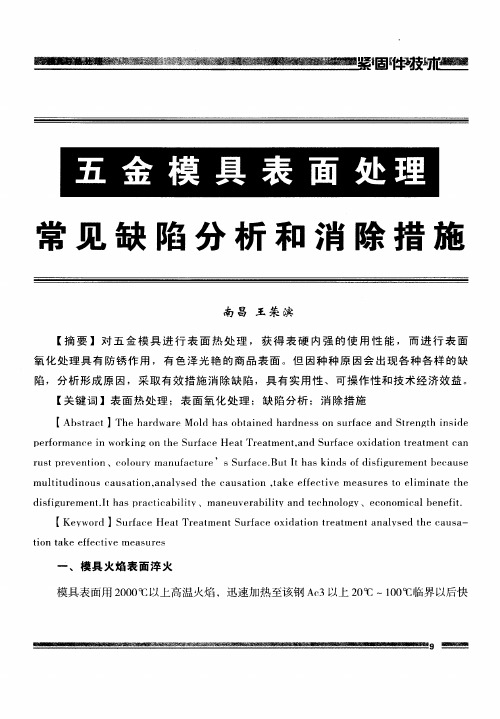
淬火模具不受体积大小 限制 ,可局部
淬硬 ; 淬火畸变小 , 淬火表面清洁无氧化 、 脱
碳;
成本低 、易上 马 、生产效率高 。
经验和最佳工艺参数后投产 ;
仔细观察火色 ,控制淬火加热温度 。 火焰表 面淬火后应及时在 2 0C± 1 0 ̄ 0 ℃ X1 h —2 低温 回火 , 消除淬火 内应力 , 避 免淬裂。
陷 , 分 析 形 成 原 因 , 采 取 有 效 措 施 消 除 缺 陷 ,具 有 实 用 ・ 可 操 作 性 和 技 术 经 济 效 益 。 性、 【 键 词 】表 面 热 处 理 ;表 面 氧 化 处 理 ;缺 陷 分 析 ; 消 除 措 施 关
【 bt c 】 h ad aeM l h s ban dh rn s o ufc n t n t is e A s a t T eh rw r od a o tie ad es nsr ea dSr gh n i r a e d
移 动速 度
1 65
/ m . i m m n
l5 4
1 25
11 0
10 O
9 0
8 0
到该钢 临界温度 A 3 t 以上 1 0 10 0℃ 5 ℃高
温奥 氏体 状 态 ,然 后 急速 冷却 淬火 ,实
模具感应 加热表面淬火 常见 缺陷及防
治措 施 :
2淬硬层 深度不易控制 、受热不均 . 匀、 硬度不均匀 , 主要靠实践经验控制淬 火质量。
防治措施 : 选用精炼钢 、电渣重熔钢或真空熔炼
钢。 它们具有纯度高 、 杂质少 、 晶粒细 、 碳
五金模具不良原因分析
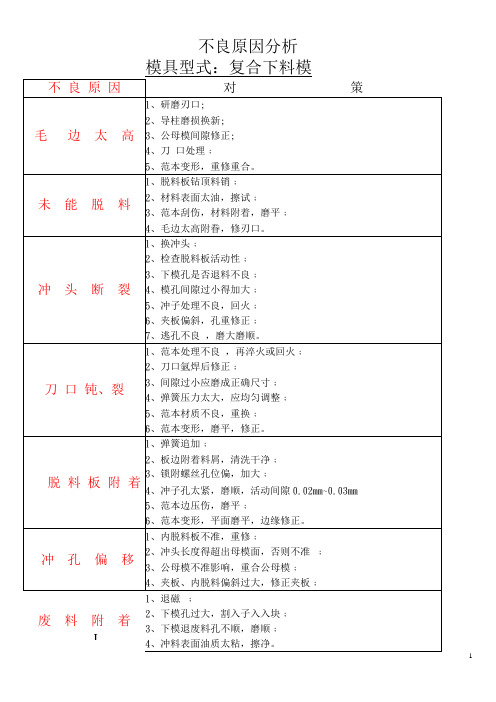
5、顶料太高,研短顶料﹔
6、顶料不平均,追加顶料销。
反批锋的产生是产品从凹模脱料出来的时候.产品与凹模直壁相对运动擦出来的.
分析原因如下:
1:冲裁间隙太小,造成产品卡在凹模里面太紧.
2:内脱力不均匀.造成偏向脱料.
3:产品外形附近有向外胀料之类的成形.造成产品卡在凹模里面太紧.且周边不一,还会造成脱料偏向.
7、范本变形,重研、重修、重合模﹔
平面不平
1、重磨不平范本﹔
2、脱料时顶料不均,修正﹔
3、脱板压力不足,追加弹簧﹔
4、架模深浅不足,调整冲床高低﹔
5、上下模间隙不均,脱料后变形,重修模具间隙﹔
6、加强范本厚度。
送料不顺
1、两用销与料宽不配,重剪料或研两用销﹔
2、折弯角卡住,把两用销升高﹔
3、滑块挡住,将滑块倒斜度﹔
4、案内高度,磨确实﹔
模具形式:卷圆模
不良原因
对 策
外观变形
1、排气不顺,铣沟十字槽,气孔钻大﹔
2、NC型腔不对,重新NC加工放大﹔
3、气压顶太弱,增强气压吨数﹔
4、铣槽相对深度不准,重新配模上下吻合。
圆卷不起
1、沟槽不顺,重打滑槽沟﹔
2、压皱板太小,产品向内弯曲,重换压皱板与产品紧滑配再研磨斜度好定位。
2、上下模不配合,修正﹔
3、下模孔太小,刮伤冲头﹔
4、导柱太短,刮伤,换新﹔
5、冲床剪切力不足,换大冲床﹔
刀口凹陷
1、处理不良,重处理﹔
2、冲压力不足,换校大冲床﹔
3、孔径不足,剪断力太大,加大孔﹔
4、下垫板逃孔过大,修正﹔
5、范本变形,修平。
脱料不易
1、追加顶料﹔
五金冲压模具常见问题解决方案

五金冲压模具常见问题解决方案1.冲头使用前应注意2.冲模的安装与调试3.冲压毛刺4.跳废料5.压伤、刮伤6.工件折弯后外表面擦伤7.漏冲孔8.脱料不正常9.折弯边不平直,尺寸不稳定10.弯曲表面挤压料变薄11.凹形件底部不平12.不锈钢翻边变形13.材料扭曲14.模具严重磨损15.防止冲压噪音1.冲头使用前应注意①用干净抹布清洁冲头。
②查看表面是否有刮、凹痕。
如有,则用油石去除。
③及时上油防锈。
④安装冲头时小心不能有任何倾斜,可用尼龙锤之类的软材料工具把它轻轻敲正,只有在冲头正确定位后才能旋紧螺栓。
2.冲模的安装与调试安装与调校冲模必须特别细心。
因为冲模尤其大中型冲模,不仅造价高昂,而且重量大微量移动困难,人身的安全应始终放在首位。
无限位装置的冲模在上下模之间应加一块垫木板,在冲床工作台清理干净后,将合模状态的待试模具置于台面合适位置。
按工艺文件和冲模设计要求选定的压机滑块行程,在模具搬上台面前调至下死点并大于模具闭合高度10~15mm的位置,调节滑块连杆,移动模具,确保模柄对准模柄孔并达到合适的装模高度。
一般冲裁模先固定下模(不拧紧)后再固定上模(拧紧),压板T型螺栓均宜使用合适扭矩扳手拧紧(下模),确保相同螺拴具有一致而理想的预加夹紧力。
可以有效防止手动拧紧螺纹出现的因体力、性别、手感误差造成的预紧力过大或过小、相同螺纹预紧力不等,从而引起冲压过程中上下模错移、间隙改变、啃剥刃口等故障发生。
试模前对模具进行全面润滑并准备正常生产用料,在空行程启动冲模3~5次确认模具运作正常后再试冲。
调整和控制凸模进入凹模深度、检查并验证冲模导向、送料、推卸、侧压与弹压等机构与装置的性能及运作灵活性,而后进行适当调节,使之达到最佳技术状态。
对大中小型冲模分别试冲3、5、10件进行停产初检,合格后再试冲10、15、30件进行复检。
经划线检测、冲切面与毛刺检验、一切尺寸与形位精度均符合图纸要求,才能交付生产。
3.冲压毛刺①模具间隙过大或不均匀,重新调整模具间隙。
五金冲压模具常见问题及处理方法汇总

五⾦冲压模具常见问题及处理⽅法汇总不锈钢压坑冲孔模常见问题及处理⽅法⼀、⽑刺原因:有间隙、不均匀、⼑⼝磨损,冲针强度不够。
⼆、变形原因:有弧度不对时,适当调节镶套⾼度或弧度。
冲针上的压退料橡胶的⼤⼩,⾼度与产品接触的贴合度也有影响。
三、压印产品外表⾯压印由压料板引起,所以压料板要尽可能光滑,如果有贴胶布,查看胶布内是否有异物。
内表⾯压印则看孔模是否有碰伤,是否光滑,点状压印看孔模上是否有⽩⾊粉末状抛光砂粒。
关于冲孔模另议尽可能增加冲针强度,尺⼨过⼩的冲针改为T型结构增加强度,将冲针端⾯改为半抛或⽉⽛形,减少冲击强度。
冷铆模常见问题分析及解决⽅法⼀、⾃动线类红点螺纹系列a复底⽚以外的螺纹不清晰,须车深复底⽚处b复底⽚边沿压不紧(起缝)则须加⾼台阶c复底⽚处螺蚊不清晰,车模复底⽚以外的平⾯30/32T5 花纹不清晰a车矮下模镶件b车低上模复底⽚处,复底⽚压不满c车低上模复底⽚以外的平⾯,内圈压不满则加⼤斜度,外圈压不满则减⼩斜度。
30/32R1a. 螺纹内圈压不满,加⼤上模斜度b.外圈压不清晰,减⼩上模斜度(标准值Φ220处⾄中⼼斜0.3mm)。
⼆、铆锅类a. 锅内R⾓起槽,则重配R⾓b. 锅内变形严重,则重配R⾓(标准为从锅底平⾯起⾄R⾓,保证⼀指宽贴合度)。
复底⽚压不满则重配下模斜度;内圈压不满,斜度加⼤;外圈压不满,斜度减少。
字唛不清晰,对应的锅内表⾯未压紧,则重配字唛⾼度。
①重配较⾼的商标维持⽣产②将下模商标孔车⾄标准尺⼨L=39.5mm<注:斜度、台阶需同时降低,保证斜度及各⼯作⾯的相对⾼度>。
三、铆⽚类1.商标处压不死,同上2 ⽚内表⾯有感a. 调整弹胶⾼度⼀致,b.适当减少压⼒3 复底⽚压不满,内圈空则加⼤斜度;外圈空则减少斜度复底⽚边缘起缝,加⾼边缘处台阶⾼度,保证台阶直径和复底⽚直径相等或⼤0.1~0.15mm铝制品冷铆模具常见问题及处理办法常见问题1.台阶变矮。
磨损,按原数据加深(约0.6~0.7mm)2.商标孔变深(39.5mm)按原数据重车/重配⾼商标3.内表⾯有平感①适当减⼩压⼒②检查弹胶⾼度是否⼀致③检查下⼯作台平⾏度(模具是否放平)④复打类须对正上/下模4.复底⽚外圆分级①检查复底⽚冲孔是否单边②适当加⼤该处直径复打类①26/28G下模每批均需重车下模(孔位易变深)②1000T压⼒机(中间那台)和1600T压⼒机打⽚效果完全不同,维修时需仔细询问。
17个模具典型问题及解决方案,每一个都很经典
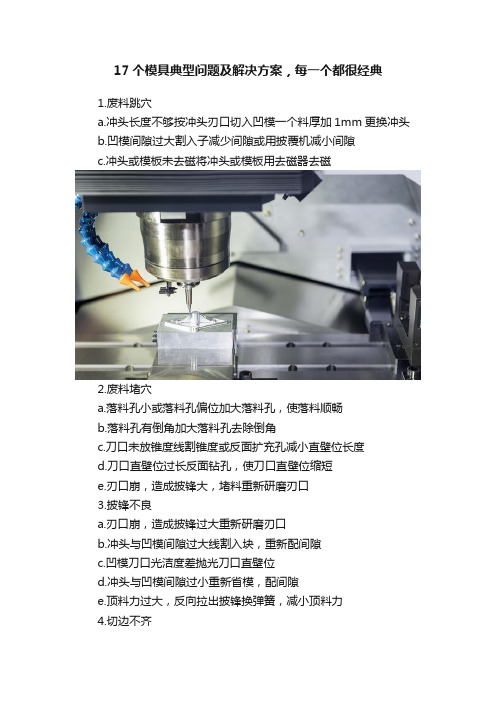
17个模具典型问题及解决方案,每一个都很经典1.废料跳穴a.冲头长度不够按冲头刃口切入凹模一个料厚加1mm更换冲头b.凹模间隙过大割入子减少间隙或用披覆机减小间隙c.冲头或模板未去磁将冲头或模板用去磁器去磁2.废料堵穴a.落料孔小或落料孔偏位加大落料孔,使落料顺畅b.落料孔有倒角加大落料孔去除倒角c.刀口未放锥度线割锥度或反面扩充孔减小直壁位长度d.刀口直壁位过长反面钻孔,使刀口直壁位缩短e.刃口崩,造成披锋大,堵料重新研磨刃口3.披锋不良a.刃口崩,造成披锋过大重新研磨刃口b.冲头与凹模间隙过大线割入块,重新配间隙c.凹模刀口光洁度差抛光刀口直壁位d.冲头与凹模间隙过小重新省模,配间隙e.顶料力过大,反向拉出披锋换弹簧,减小顶料力4.切边不齐a.定位偏移调整定位b.有单边成型,拉料加大压料力,调整定位c.设计错误,造成接刀不平重新线割切边刀口镶块d.送料不准调整送料器e.送料步距计算有误重新计算步距,重定接刀位5.冲头易断a.闭合高度过低,冲头切入刀口部位过长调整闭合高度b.材料定位不当,造成冲孔冲头切单边,调整定位或送料装置因受力不均断裂c.下模废料堵死刀口,造成冲头断重新钻大落料孔,使落料顺畅d.冲头的固定部位(夹板)与导向部位修配或重新线割入块使冲头上下顺畅(打板)偏移e.打板导向不良,造成冲头单边受力重新修配打板间隙f.冲头刀口太短,与打板干涉重换冲头,增长刀口部分长度g.冲头固定不好,上下窜动重新固定冲头使之不能上下窜动h.冲头刃口不锋利重新研磨刃口I.冲头表面拉伤,脱料时受力不均重新换冲头j.冲头过细,过长,强度不够重新换冲头类型k.冲头硬度过高,冲头材质不对更换冲头材质,调整热处理硬度6.铁屑a.压筋错位重新计算压筋位置或折弯位置b.折弯间隙过小,挤出铁屑重新调整间隙,或研磨成型块,或研磨成型冲头c.折弯凸模太锋利修R角d.接刀口材料太少重新接刀口e.压筋太窄重新研磨压筋7.抽芽不良a.抽芽底孔中心与抽芽冲子中心不重合造确定正确中心位置,或移动抽芽冲子位置,或移成抽芽-边高-边低甚至破裂动预冲孔位置,或调整定位b.凹模间隙不均匀,造成抽芽-边高-边修配抽芽间隙低甚至破裂c.抽芽底孔不符合要求,造成抽芽高度及重新计算底孔孔径,预冲孔增大或减少直径偏差,甚至破裂8.成型不良a.成型模凸模太锋利,造成材料拉裂成型凸模修R角,刀口处适当修R角b.成型冲头长度不够,造成未能成型计算冲头正确长度调整冲头实际长度以达成型要求c.成型冲头过长,成型处材料压变形,甚确定冲头正确长度,调整冲头实际长度以达到要求至冲头断裂d.成型处材料不够造成拉裂计算展开材料,或修R角,或降低成型高度e.定位不良,造成成型不良调整定位或送料装置f.成型间隙太小造成拉裂或变形调配间隙9.折弯尺寸a.模具没调到位造成角度误差导致尺寸偏调整闭合高度不良或角度差不良b.弹力不够造成角度不良导致尺寸偏差换弹簧c.材质不符合要求造成角度不良导致尺寸换材料或重新调整间隙偏差d.材料厚度偏差引起角度不良导致尺寸偏确定料厚,换材料或重新调整间隙差e.定位不当导致尺寸偏差调整定位使尺寸OKf.设计或加工错误造成折弯公拼块间有间補焊研磨,消除拼块间的间隙,导致折弯尺寸小值得关注的“模具人杂志微信~g.成型公无R角,在角度及其他正常情况成型公修R角下折弯高度偏小h.两边折弯尺寸偏大加压筋I.单边折弯拉料造成尺寸不稳定加大弹簧力,调整定位j.间隙不合理,引起角度不良和尺寸偏差修配间隙k.折刀高度不够,折弯冲头合入折刀太短增加折刀高度,使折弯冲头尽可能合入折刀部队位造成角度不良多一些l.折弯时速度太快,造成折弯根部变形调整速比控,选择合理转速m.结构不合理,折刀未镶入固定模板,重新铣槽,将折刀镶入模板冲压时,造成间隙变大n.成型公热处理硬度不够,造成压线崩或重制成型公压线打平10.不卸料a.定位不当或送料不当调整定位或送料装置b.避位不够修磨避位c.内导柱拉伤,造成打板活动不畅更换内导柱d.冲头拉伤或表面不光滑更换冲头e.顶料销摆布不合理重新摆布顶料销位置f.顶料力不够,或脱料力不够更换顶料弹簧或脱料弹簧g.冲头与夹板打板配合不顺畅修配打板和夹板使冲头配合顺畅h.成型滑块配合不畅修整滑块与导向槽使之配合顺畅I.打板热处理不适,冲压一段时间后变形重新研磨打板,矫正变形j.冲头过长或顶料销长度不够增加顶料销长度或换用长度合适之冲头k.冲头断更换冲头l.模板未云磁,工件往上带给模板去磁11.送料不顺a.模具没架正,导致料带与送料器及模具重架模具或调整送料器不在同一条直线上b.料带不平调整校平机或更换材料c.不卸料造成送料不顺参照不卸料解决对策。
五金拉深模具常见问题产生原因和解决方法
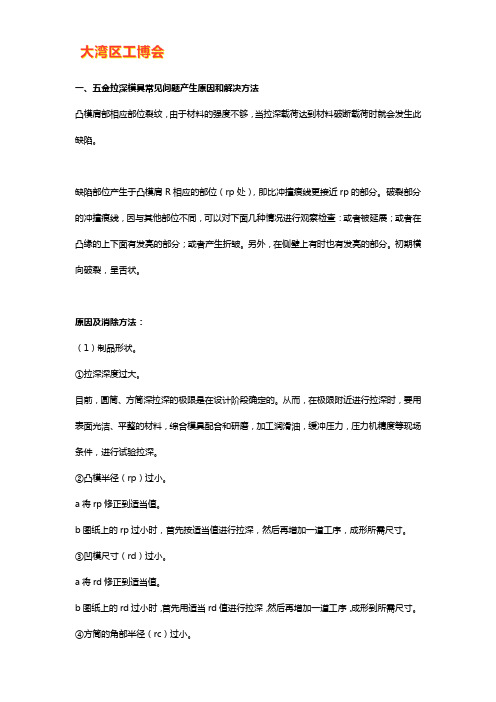
一、五金拉深模具常见问题产生原因和解决方法凸模肩部相应部位裂纹,由于材料的强度不够,当拉深载荷达到材料破断载荷时就会发生此缺陷。
缺陷部位产生于凸模肩R相应的部位(rp处),即比冲撞痕线更接近rp的部分。
破裂部分的冲撞痕线,因与其他部位不同,可以对下面几种情况进行观察检查:或者被延展;或者在凸缘的上下面有发亮的部分;或者产生折皱。
另外,在侧壁上有时也有发亮的部分。
初期横向破裂,呈舌状。
原因及消除方法:(1)制品形状。
①拉深深度过大。
目前,圆筒、方筒深拉深的极限是在设计阶段确定的。
从而,在极限附近进行拉深时,要用表面光洁、平整的材料,综合模具配合和研磨,加工润滑油,缓冲压力,压力机精度等现场条件,进行试验拉深。
②凸模半径(rp)过小。
a将rp修正到适当值。
b图纸上的rp过小时,首先按适当值进行拉深,然后再增加一道工序,成形所需尺寸。
③凹模尺寸(rd)过小。
a将rd修正到适当值。
b图纸上的rd过小时,首先用适当rd值进行拉深,然后再增加一道工序,成形到所需尺寸。
④方筒的角部半径(rc)过小。
a将拉深深度减小;b多增加一道拉深工序;c换成更高级的材料;d将板料厚度增加。
(2)冲压条件。
①压边力过大。
压边力过大时,在凸缘面上不会发生起皱。
防皱压板面粗糙度,模具配合,间隙,rp,rd,加工油的种类和涂敷条件,缓冲销造成的压边力分布等,都影响防皱压力。
如果有关拉深的上述这些条件都合适的话,压边力就会下降,在起皱之前,不会发生破裂。
压边力过大时,由于凸缘面会全面发亮,所以很容易判断。
②润滑不良。
拉深加工与润滑有极为密切的关系,特别是包含有减薄拉深加工时,必须控制制品温度的升高。
如果是条件好的拉深加工,润滑油的选择不成什么问题;条件不好的拉深加工,如果润滑油选择不当,就会引起破裂。
③毛坯形状不良。
在试拉深阶段,决定毛坯形状是重要的工作之一。
必须将毛坯形状限制在最小尺寸。
当用方形毛坯进行圆筒拉深时,极限拉深率为0.58左右。
五金连续冲模常见不良及其改善措施

五金连续冲模常见不良及其改善措施一、冲裁中常见不良(一)跳屑1.跳屑的几种情况:(1)切边时的跳屑:原因:系不完整的冲孔废料难以有效卡在模仁里,故易跳屑。
改善措施:修边结构复杂化。
(2)小方孔,小圆孔跳屑:原因:a、间隙太大b、有较多的油c、料太薄改善措施:a、收紧间隙b、减少用油c、加向下吹气,在废料下面形成负压d、设变模仁加工方式(改为PG加工),提高刃口段光洁度e、对冲子结构作重新设计f、对铁材产品模具备品须退磁干净(3)细小废屑:(常见于有撕破的模具,有重切时尤为时显,821-220模)(4)大片废屑的跳屑原因:同(2)改善措施:a、加顶杆b、加吹气c、对其形状复杂化(和carry相连一侧)(5)其他状况的跳屑:原因:工序排配设计不合理。
改善措施:重新调整工序排配(重新设计接刀)2.跳屑的危害(1)产生模痕,压伤等不良(2)对间歇性跳屑,不易发现,极易流出不良品。
(3)维修不易(常采用异性冲子,刃口披覆等有损备品寿命和产品断面质量的方式)致生产效率和稼动率低(4)不良品产生时常需要大量的人工进行挑选(二)金属丝危害1、组装成成品后,极易造成短路(short),是要绝对禁止的严重一种不良2、脱落时易在产品上产生模痕3、当有发生时须耗费大量的人力对其重工产生原因常见于有撕破的模具,比如:1、先向下撕破,后又被向上拍平,撕破切口处产生二次挤压,形成金属丝2、先向一个方向撕破后又向相反方向折弯成形3、一次撕破折弯不到位时,让设计不合理改善措施1、撕破处后面工站闪开(放电)避免撕破和被反复拍打。
(抽引毛坯的准备)2、对抽引,有撕破准备毛坯的后面各工站,均应闪开撕破缝隙处,或是重新对carry进行设计,以改善其变形,防止接缝段太长。
3、撕破方向应和后续**进行的成形方向一致,能采用一次撕破折弯成形方案的要尽可能采用。
4、在撕破处须进行二次forming,要合理设计穿过缝隙的冲子和模仁与撕破口间的间隙>0.02(三)冲子蹦根源:结构设计不合理1、直刀面太长为(大于10mm)2、该用PG加工(光学研磨)的未用,由于压板槽的影响,使用强度大大削弱(820-380N1)3、采用PG加工时结构设计不合理,PG槽对其削弱很多,822-173U形冲子4、弧量的部分太过细长5、太过细小冲子的导向段送样不合理(入子加工方式不好)改善措施:1、PG加工的冲子直刀面应小于10mm2、长*宽<3*3者应采用PG加工方式来设计和加工3、对大多数改U形结构冲子来讲,尽量采用PG加工,也应采用分体式结构,以尽量减小对其强度的削弱。
五金模具常见十大问题及解决方案
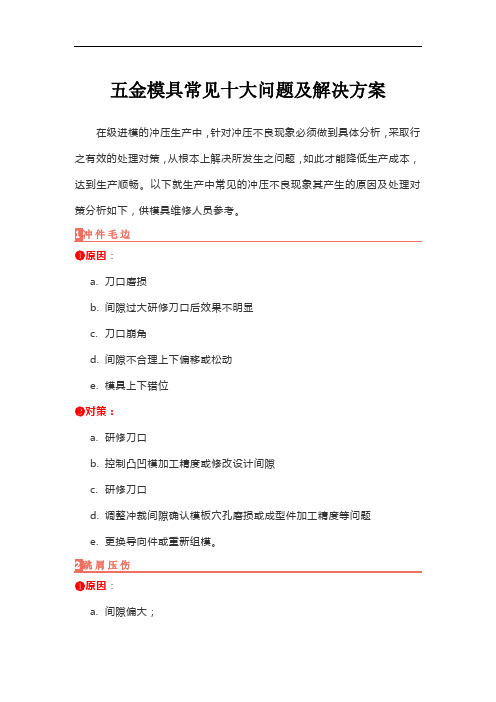
五金模具常见十大问题及解决方案在级进模的冲压生产中,针对冲压不良现象必须做到具体分析,采取行之有效的处理对策,从根本上解决所发生之问题,如此才能降低生产成本,达到生产顺畅。
以下就生产中常见的冲压不良现象其产生的原因及处理对策分析如下,供模具维修人员参考。
❶原因:a.刀口磨损b.间隙过大研修刀口后效果不明显c.刀口崩角d.间隙不合理上下偏移或松动e.模具上下错位❷对策:a.研修刀口b.控制凸凹模加工精度或修改设计间隙c.研修刀口d.调整冲裁间隙确认模板穴孔磨损或成型件加工精度等问题e.更换导向件或重新组模。
❶原因:a.间隙偏大;b.送料不当;c.冲压油滴太快,油粘;d.模具未退磁;e.凸模磨损,屑料压附于凸模上;f.凸模太短,插入凹模长度不足;g.材质较硬,冲切形状简单;h.应急措施。
❷对策:a.控制凸凹模加工精度或修改设计间隙;b.送至适当位置时修剪料带并及时清理模具;c.控制冲压油滴油量,或更换油种降低粘度;d.研修后必须退磁(冲铁料更须注意);e.研修凸模刀口;f.调整凸模刃入凹模长度;g.更换材料,修改设计。
凸模刃入端面装顶出或修出斜面或弧性(注意方向)。
减少凸模刃部端面与屑料之贴合面积;h.减小凹模刃口的锋利度,减小凹模刃口的研修量,增加凹模直刃部表面的粗糙度(被覆),采用吸尘器吸废料。
降低冲速,减缓跳屑3屑料阻塞❶原因:a.漏料孔偏小;b.漏料孔偏大,屑料翻滚;c.刀口磨损,毛边较大;d.冲压油滴太快,油粘;e.凹模直刃部表面粗糙,粉屑烧结附着于刃部;f.材质较软;g.应急措施。
❷对策:a.修改漏料孔;b.修改漏料孔;c.刃修刀口;d.控制滴油量,更换油种;e.表面处理,抛光,加工时注意降低表面粗糙度;更改材料,f.修改冲裁间隙;g.凸模刃部端面修出斜度或弧形(注意方向),使用吸尘器,在垫板落料孔处加吹气。
❶原因:a..凸凹模刀口磨损,产生毛边(外形偏大,内孔偏小);b.设计尺寸及间隙不当,加工精度差;c.下料位凸模及凹模镶块等偏位,间隙不均;d.导正销磨损,销径不足;e.导向件磨损;f.送料机送距、压料、放松调整不当;g.模具闭模高度调整不当;h.卸料镶块压料位磨损,无压料(强压)功能(材料牵引翻料引发冲孔小);i.卸料❷对策:a.研修刀口;b.修改设计,控制加工精度;c.调整其位置精度,冲裁间隙;d.更换导正销;e.更换导柱、导套;f.重新调整送料机;g.重新调整闭模高度;h.研磨或更换卸料镶块,增加强压功能,调整压料;i.减小强压深度;j.更换材料,控制进料质量;k.凸模刃部端面修出斜度或弧形(注意方向),以改善冲切时受力状况。
五金冲压模具常见问题点及不良原因与对策)

五金冲压模具常见问题点及不良原因与对策发布时间:2011-7-22 10:21:50 来源:本站原创作者:佚名冲件毛边不良原因:1.刀口或冲头磨损 2.间隙过大(研磨修刀口后效果不明显) 3.刀口崩角.4.导柱/导套磨损对策:1.研磨刀口. 2.依产品断面调整下料间隙. 3.研修刀口. 4. 调整站裁间隙(确保模板穴孔磨损或成形加工精度等问题. 5. 更换导向件或重新组装跳屑压伤不良原因:1. 间隙偏大. 2. 送料不当. 3. 五金冲压油滴太快,油粘 , 4.模具末退磁, 5.冲子磨损,屑料压附于冲子上. 6.冲子太短,刃入下模长度不足, 7.材质较硬,冲切形状简单.对策:1控制冲子及下模加工精度或修改设计间隙; 2送至适当位置时修剪料带并及时清理模具;3控制五金冲压油滴油量,或更换油种降低粘度;4零件研修后必须退磁;5研修冲刀口. 6调整冲子刃入子下模长度;7修改设计,冲子刃部端面装顶出或修出斜面或弧形(注意方向)减小冲子刃部端面与屑料之贴合面积,可防真空跳屑;8减小下模刃口的锋利度,减小下模刃口的研修量,增加下模刃部表面粗糙度,采用吸尘器吸屑料.降低冲速屑料阻塞不良原因:1.漏料孔偏小, 2.漏料孔偏大,屑料翻滚,3.刀口磨损,毛边较大, 4五金冲压油滴太快,油粘 5.下模直刃部表面粗糙,粉屑烧结附着于刃部. 6.材质较软. 对策:1.修改漏料孔,2.修改漏料孔 3.研修刀口, 4. 控制滴油量,更换油种, 5.表面处理抛光加工时注意降低表面粗糙度. 6.更改材料修改冲裁间隙, 7. 冲子刃部端面修出斜度或弧形,使用吸尘器下料偏位尺寸变异不良原因:1.冲子及下模刀口磨损,产生毛边(外形偏大,内孔偏小)2. 设计尺寸及间隙不当,加工精度差. 3.下料位冲子及下模镶块等偏位,间隙不均, 4.导料针磨损,定经不够. 5.导向件磨损. 6.送料机送距,压料,放松调整不当,7.模具合模深度不当, 8. 脱料镶块压料位磨损,无压料功能(材料牵引发翻料冲孔小), 9.脱料镶块强压太深,冲孔偏大. 10.五金冲压材质机械性能变异(强度延伸率等不稳定), 11.冲切时冲切力对材料牵引,引发尺寸变异.对策:1.研修刀口, 2.修改设计,控制加工精度, 3.调整其位置精度, 4.更换导料销, 5.更换导柱,导套, 6.重新调整送料机,7.重新调整合模深度, 8.重新研磨或更换脱料镶块,增加压功能调整压料. 9.减小强压深度, 10.更换材料,控制进料质量. 11.冲子端部修出斜面或弧形,以改善冲切时受力状况,许可时,下料部位于脱料镶块上加设导位功能卡模不良原因:1.送料送距,压料,放松,调整不当, 2.生产中送距产生变异, 3.送料机故障, 4.材料弧形,宽度超差,毛边较大, 5.模具五金冲压异常,镰刀弯引发, 6.导料孔经不足,上模拉料, 7.折弯或撕切位上下脱料不顺, 8.导料板之脱料功能设置不当,料带上带, 10.材料薄,送进中翘曲对策:1.重新调整,2.重新调整. 3.调整及维修, 4. 更换材料, 控制进料质量, 5.消除料带镰刀弯, 6.研修冲导孔冲子下模, 7.调整脱料弹簧力量等, 8.修改导料板,防料带上带, 9.送料机与模具间加设上下压料,加设上下挤料安全开关, 10.重新架设模具料带镰刀不良原因:1.五金冲压毛边, 2.材料毛边模具无切边. 3.冲床深度不当. 4.冲件压伤模内在屑料,5.局部压料太深或压至部局损伤对策:1.研修下料刀口,2. 更换材料,模具加设切边装置, 3.重调冲床深度. 4.清理模具,解决跳屑, 5.检查并调整各位脱料及下模镶块高度尺寸损伤位研修, 6.采用整弯机构调整冲子断裂崩刃不良原因:1.跳屑,屑料阻塞,卡模等倒致,2.送料不当,切半料, 3.冲子强度不足.4.大小冲子相距太近,冲切时材料牵引引发小冲断.5. 冲子及下模局部过于尖角, 6.冲裁间隙偏小, 7.无五金冲压油或使用的五金冲压油挥发性较强.8.冲裁间隙不均,偏移,冲子,上模发生干涉,9.脱料镶件精度差或磨损,失去精密导向功能,10.模具导向不准,磨损,11.冲子,下模材质选用不当,硬度不当,12.导料件(销)磨损,13.垫片加设不当,引发冲子与下模断裂,对策:1.解决跳屑,屑料阻塞,,卡模等问题,2.注意送料,及时修剪料带,及时清理模具,3.修改设计,增加冲子整体强度,减短下模直刃部尺寸,注意冲子刃部端面修出斜度,细小部后切, 4.小冲子长度磨短大冲子一个料厚以上, 5.修改设计, 6.控制冲子下模加工精度或修改设计间隙,细小部位冲切间隙适当加大,7.调整五金冲压油滴油量或更换油种,8.松查各成形悠扬精度,并施以调整或更换,控制加工精度,9.研修或更换,10.更换导柱,导套,注意日常保养,11.更换使用材质使用合适硬度,12.修正,垫片数画量少,尽可使用权用钢垫.且垫在漏料垫块之下面.折弯变形尺寸变异不良原因: 1.导料销尺寸不准,磨损, 2.折弯导位部精度差,磨损,3. 折弯冲子,下模磨损(压损), 4.模具让位不足, 5.材料滑移,折弯冲子,下模无导位功能,折弯时未施以预压, 6.模具结构及设计尺寸不良,7.冲件毛边引发折弯不良, 8.折率位冲子,下模加设垫片较多,造成尺寸不稳定, 9.材料厚度尺寸不变异, 10.材料机械性能变异对策:1.更换导料销, 2.重新研磨或更换, 3.重新研磨或更换. 4.检查,修正, 5.修改设计,增设导位功能,增设预压功能, 6.修改设计尺寸,分解折弯,增加折弯整形等, 7.研修下料位刀口, 8.调整,采用整体钢垫, 9.换料,控制进料质量, 10.换料控制进料质量冲件高低(一模多件)不良原因:1.冲件毛边. 2.冲件有压伤,模内有屑料,3.冲子,下模(折弯位)压损或损伤.4.冲剪时翻料, 5.相关压料部位磨损压损, 6.相关撕切位撕切尺寸不一致,刀口磨损,7.相关易断位,预切深度不一致,冲子下模有磨损事崩刃, 8.相关打凸部位冲子及下模有崩刃事磨损较为晋重, 9.模具设计缺陷,对策:1.研修下料刀口,2.清理模具,解决屑料上浮问题, 3.重新研修或更换新件, 4.研修冲切刀口,调整或增设强压功能, 5.检查实施维护或更换, 6.维修或更换保证切的状况一致辞, 7.检查预切之冲子,下模状况实施维护或更换. 8.检查冲子,下模状况实施维修或更换, 9.修改设计加设高低调整事增设整形工位维护不当不良原因:1.模具无防呆功能组模时疏忽导致装反向,错位(指不同工位)等已经偏移过间隙之镶件未按原状复原对策:1.修改模具,增防呆功能,采用模具上作记号等方法,并在组模后对照料带作必要的检查,确认等特别提醒:东莞禾聚塑胶五金有限公司是珠三角最专业的精密五金冲压件/贴片LED支架厂家,有绝对的优势!。
五金冲压模具的几种修复方法

五金冲压模具的几种修复方法
【答】:五金冲压模具经过长期的机械运作,大量冲切金属板材,即使有冲压油等起润滑保护作用,也难免会出现问题,需要及时拆卸修复,通常需要模具师参与。
当然,损坏的程度也分轻微和严重,要根据修复成本和生产周期的紧急情况决定,过于严重的直接要换模生产,下面就来分析几种轻微情况的修复方法。
1、五金冲压模具发生倾斜、松动、模板变形时可以逐一分析解决。
倾斜时会破坏冲压件的整体性,使冲裁不规范,产品发生变形等现象,首先分析问题,运动的角度不垂直,可能是模板间跳进废料,无法贴平,可以拆模重组,重新校正姿势;松动的问题则可通过微调模位的两边间隙,使其恰到好处;更换变形的模板。
2、此外,五金冲压模具还会出现冲裁偏斜、冲程干涉、模座变形等问题,可以
通过以下方法逐一修复。
造成冲压件半倾斜的问题可能是由冲头强度不够,大小头距离过近,从而使侧位力不平衡,此时可以将大小冲头磨短或者增加踵跟长度,还可以加强对引导板的保护作用来加强效果;受干涉的影响,检查冲模尺寸和位置的正确性,组合后的接洽程度,架模的正确性等;最简单的方法之一就是更换模座了,不然就研磨矫正不平衡的部位。
对生产工具的修复是以最大限度保持生产成本为前提,通过快速决策,制定维修方案,今尽量保持量产效率,是工程师一直追寻的方法。
五金模具维修经验

五金模具维修经验在电脑连接器上,端子(冲压件)越来越趋于细小、复杂及精密化,而端子在模具的冲压生产中,如何克服其翻转扭曲之变形,保证其尺寸及功能等要求,则必须采取行之有效的策。
1. 冲压时产生翻料、扭曲的原因在级进模中,通过冲切冲压件周边余料的方法,来形成冲件的外形。
冲件产生翻料、扭曲的主要原因为冲裁力的影响。
冲裁时,由于冲裁间隙的存在,材料在凹模的一侧受拉伸(材料向上翘曲),靠凸模侧受压缩。
当用卸料板时,利用卸料板压紧材料,防止凹模侧的材料向上翘曲,此时,材料的受力状况发生相应的改变。
随卸料板对其压料力的增加,靠凸模侧之材料受拉伸(压缩力趋于减小),而凹模面上材料受压缩(拉伸力趋于减小)。
冲压件的翻转即由于凹模面上的材料受拉伸而致。
所以冲裁时,压住且压紧材料是防止冲件产生翻料、扭曲的重点。
2. 抑制冲压件产生翻料、扭曲的方法(1). 合理的模具设计。
在级进模中,下料顺序的安排有可能影响到冲压件成形的精度。
针对冲压件细小部位的下料,一般先安排较大面积之冲切下料,再安排较小面积的冲切下料,以减轻冲裁力对冲压件成形的影响。
(2). 压住材料。
克服传统的克服传统的模具设计结构,在卸料板上开出容料间隙(即模具闭合时,卸料板与凹模贴合,而容纳材料处卸料板与凹模的间隙为材料厚t-0.03~0.05mm)。
如此,冲压中卸料板运动平稳,而材料又可被压紧。
关键成形部位,卸料板一定做成镶块式结构,以方便解决长时间冲压所导致卸料板压料部位产生的磨(压)损,而无法压紧材料。
(3). 增设强压功能。
即对卸料镶块压料部加厚尺寸(正常的卸料镶块厚H+0.03mm),以增加对凹模侧材料的压力,从而抑制冲切时冲压件产生翻料、扭曲变形。
(4). 凸模刃口端部修出斜面或弧形。
这是减缓冲裁力的有效方法。
减缓冲裁力,即可减轻对凹模侧材料的拉伸力,从而达到抑制冲压件产生翻料、扭曲的效果。
(5). 日常模具生产中,应注意维护冲切凸、凹模刃口的锋利度。
五金制造行业中存在的问题及改善建议
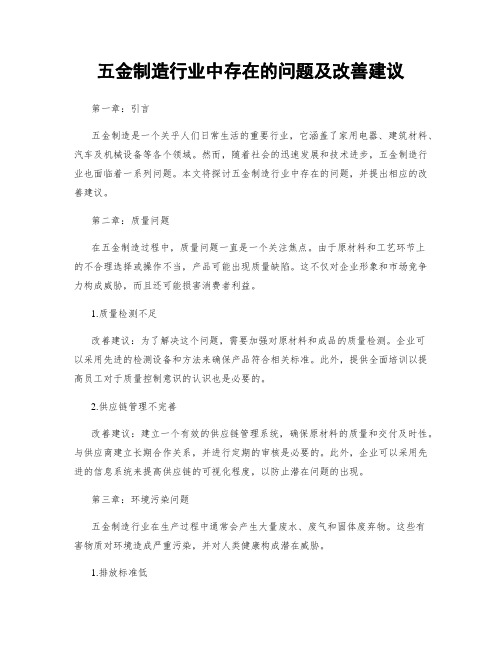
五金制造行业中存在的问题及改善建议第一章:引言五金制造是一个关乎人们日常生活的重要行业,它涵盖了家用电器、建筑材料、汽车及机械设备等各个领域。
然而,随着社会的迅速发展和技术进步,五金制造行业也面临着一系列问题。
本文将探讨五金制造行业中存在的问题,并提出相应的改善建议。
第二章:质量问题在五金制造过程中,质量问题一直是一个关注焦点。
由于原材料和工艺环节上的不合理选择或操作不当,产品可能出现质量缺陷。
这不仅对企业形象和市场竞争力构成威胁,而且还可能损害消费者利益。
1.质量检测不足改善建议:为了解决这个问题,需要加强对原材料和成品的质量检测。
企业可以采用先进的检测设备和方法来确保产品符合相关标准。
此外,提供全面培训以提高员工对于质量控制意识的认识也是必要的。
2.供应链管理不完善改善建议:建立一个有效的供应链管理系统,确保原材料的质量和交付及时性。
与供应商建立长期合作关系,并进行定期的审核是必要的。
此外,企业可以采用先进的信息系统来提高供应链的可视化程度,以防止潜在问题的出现。
第三章:环境污染问题五金制造行业在生产过程中通常会产生大量废水、废气和固体废弃物。
这些有害物质对环境造成严重污染,并对人类健康构成潜在威胁。
1.排放标准低改善建议:政府部门应加强对五金制造企业排放标准的监管,并严厉惩罚不符合标准的企业。
同时,鼓励企业使用清洁生产技术和设备,使其能够更好地达到环保要求。
2.缺乏节能措施改善建议:为了解决这个问题,可以推广节能设备和工艺、培训工作人员关于节能意识,以及鼓励企业投资可再生能源等。
此外,在政策和法规层面引导企业加大研发力度,推动环保技术的应用也是十分重要的。
第四章:人力资源问题五金制造行业对于高素质员工的需求逐渐增加,然而存在人才稀缺、劳动力成本上升等问题。
1.员工培训不足改善建议:企业应积极投资员工培训,提升其技能和专业知识。
通过举办内部培训课程、与高等院校合作开展实习项目等方式,吸引并留住优秀人才。
- 1、下载文档前请自行甄别文档内容的完整性,平台不提供额外的编辑、内容补充、找答案等附加服务。
- 2、"仅部分预览"的文档,不可在线预览部分如存在完整性等问题,可反馈申请退款(可完整预览的文档不适用该条件!)。
- 3、如文档侵犯您的权益,请联系客服反馈,我们会尽快为您处理(人工客服工作时间:9:00-18:30)。
五金模具常见十大问题及解决方案
在级进模的冲压生产中,针对冲压不良现象必须做到具体分析,采取行之有效的处理对策,从根本上解决所发生之问题,如此才能降低生产成本,达到生产顺畅。
以下就生产中常见的冲压不良现象其产生的原因及处理对策分析如下,供模具维修人员参考。
❶原因:
a.刀口磨损
b.间隙过大研修刀口后效果不明显
c.刀口崩角
d.间隙不合理上下偏移或松动
e.模具上下错位
❷对策:
a.研修刀口
b.控制凸凹模加工精度或修改设计间隙
c.研修刀口
d.调整冲裁间隙确认模板穴孔磨损或成型件加工精度等问题
e.更换导向件或重新组模。
❶原因:
a.间隙偏大;
b.送料不当;
c.冲压油滴太快,油粘;
d.模具未退磁;
e.凸模磨损,屑料压附于凸模上;
f.凸模太短,插入凹模长度不足;
g.材质较硬,冲切形状简单;
h.应急措施。
❷对策:
a.控制凸凹模加工精度或修改设计间隙;
b.送至适当位置时修剪料带并及时清理模具;
c.控制冲压油滴油量,或更换油种降低粘度;
d.研修后必须退磁(冲铁料更须注意);
e.研修凸模刀口;
f.调整凸模刃入凹模长度;
g.更换材料,修改设计。
凸模刃入端面装顶出或修出斜面或弧性(注意
方向)。
减少凸模刃部端面与屑料之贴合面积;
h.减小凹模刃口的锋利度,减小凹模刃口的研修量,增加凹模直刃部表
面的粗糙度(被覆),采用吸尘器吸废料。
降低冲速,减缓跳屑
3屑料阻塞
❶原因:
a.漏料孔偏小;
b.漏料孔偏大,屑料翻滚;
c.刀口磨损,毛边较大;
d.冲压油滴太快,油粘;
e.凹模直刃部表面粗糙,粉屑烧结附着于刃部;
f.材质较软;
g.应急措施。
❷对策:
a.修改漏料孔;
b.修改漏料孔;
c.刃修刀口;
d.控制滴油量,更换油种;
e.表面处理,抛光,加工时注意降低表面粗糙度;更改材料,
f.修改冲裁间隙;
g.凸模刃部端面修出斜度或弧形(注意方向),使用吸尘器,在垫板落
料孔处加吹气。
❶原因:
a..凸凹模刀口磨损,产生毛边(外形偏大,内孔偏小);
b.设计尺寸及间隙不当,加工精度差;
c.下料位凸模及凹模镶块等偏位,间隙不均;
d.导正销磨损,销径不足;
e.导向件磨损;
f.送料机送距、压料、放松调整不当;
g.模具闭模高度调整不当;
h.卸料镶块压料位磨损,无压料(强压)功能(材料牵引翻料引发冲孔
小);
i.卸料
❷对策:
a.研修刀口;
b.修改设计,控制加工精度;
c.调整其位置精度,冲裁间隙;
d.更换导正销;
e.更换导柱、导套;
f.重新调整送料机;
g.重新调整闭模高度;
h.研磨或更换卸料镶块,增加强压功能,调整压料;
i.减小强压深度;
j.更换材料,控制进料质量;
k.凸模刃部端面修出斜度或弧形(注意方向),以改善冲切时受力状况。
许可时下料部位于卸料镶块上加设导位功能。
5卡料
❶原因:
a.送料机送距、压料、放松调整不当;
b.生产中送距产生变异;
c.送料机故障;
d.材料弧形,宽度超差,毛边较大;
e.模具冲压异常,镰刀弯引发;
f.导料孔径不足,上模拉料;
g.折弯或撕切位上下脱料不顺;
h.导料板之脱料功能设置不当,料带上带;
i.材料薄,送进中翘曲;
j.模具架设不当,与送料机垂直度偏差较大。
❷对策:
a.重新调整;
b.重新调整;
c.调整及维修;
d.更换材料,控制进料质量;
e.消除料带镰刀弯;
f.研修冲导正孔凸、凹模;
g.调整脱料弹簧力量等;
h.修改导料板,防料带上带;
i.送料机与模具间加设上下压料,加设上下挤料安全开关;
j.重新架设模具。
❶原因:
a.冲压毛边(特别是载体上);
b.材料毛边,模具无切边;
c.冲床深度不当(太深或太浅);
d.冲件压伤,模内有屑料;
e.局部压料太深或压到部局部损伤;
f.模具设计。
❷对策:
a.研修下料刀口;
b.更换材料,模具加设切边装置;
c.重调冲床深度;
d.清理模具,解决跳屑和压伤问题;
e.检查并调整各位卸料及凹模镶块高度尺寸正确,损伤位研修
f.采用整弯机构调整。
7凸模断裂崩刃
❶原因:
a.跳屑、屑料阻塞、卡模等导致;
b.送料不当,切半料;
c.凸模强度不足;
d.大小凸模相距太近,冲切时材料牵引,引发小凸模断;
e.凸模及凹模局部过于尖角;
f.冲裁间隙偏小;
g.无冲压油或使用的冲压油挥发性较强;
h.冲裁间隙不均、偏移,凸、凹模发生干涉;
i.卸料镶块精度差或磨损,失去精密导向功能;
j.模具导向不准、磨损;
k.凸、凹模材质选用不当,硬度不当;
l.导料件(销)磨损;
m.垫片加设不当。
❷对策:
a.解决跳屑、屑料阻塞、卡模等问题;
b.注意送料,及时修剪料带,及时清理模具;
c.修改设计,增加凸模整体强度,减短凹模直刃部尺寸,注意凸模刃部
端面修出斜度或弧形,细小部后切;
d.小凸模长度磨短相对大凸模一个料厚以上;
e.修改设计;
f.控制凸凹模加工精度或修改设计间隙,细小部冲切间隙适当加大;
g.调整冲压油滴油量或更换油种;
h.检查各成形件精度,并施以调整或更换,控制加工精度;
i.研修或更换;
j.更换导柱、导套,注意日常保养;
k.更换使用材质,使用合适硬度;
l.更换导料件; m、修正,垫片数尽可少,且使用钢垫,凹模下垫片需垫在垫块下面。
❶原因:
a.导正销磨损,销径不足;
b.折弯导位部分精度差、磨损;
c.折弯凸、凹模磨损(压损);
d.模具让位不足;
e.材料滑移,折弯凸、凹模无导位功能,折弯时未施以预压;
f.模具结构及设计尺寸不良;
g.冲件毛边,引发折弯不良;
h.折弯部位凸模、凹模加设垫片较多,造成尺寸不稳定;
i.材料厚度尺寸变异;
j.材料机械形能变异。
❷对策:
a.更换导正销;
b.重新研磨或更换;
c.重新研磨或更换;
d.检查,修正;
e.修改设计,增设导位及预压功能;
f.修改设计尺寸,分解折弯,增加折弯整形等;
g.研修下料位刀口; h、调整,采用整体钢垫;
h.更换材料,控制进料质量;
i.更换材料,控制进料质量。
❶原因:
a.冲件毛边;
b.冲件有压伤,模内有屑料;
c.凸、凹模(折弯位)压损或损伤;
d.冲剪时翻料;
e.相关压料部位磨损、压损;
f.相关撕切位撕切尺寸不一致,刀口磨损;
g.相关易断位预切深度不一致,凸凹模有磨损或崩刃;
h.相关打凸部位凸凹模有崩刃或磨损较为严重;
i.模具设计缺陷。
❷对策:
a.研修下料位刀口;
b.清理模具,解决屑料上浮问题;
c.重新研修或更换新件;
d.研修冲切刀口,调整或增设强压功能;
e.检查,实施维护或更换;
f.维修或更换,保证撕切状况一致;
g.检查预切凸、凹模状况,实施维护或更换;
h.检查凸、凹模状况,实施维护或更换;
i.修改设计,加设高低调整或增设整形工位。
❶原因:
a.模具无防呆功能,组模时疏忽导致装反方向、错位(指不同工位)等;
b.已经偏移过间隙之镶件未按原状复原。
❷对策:
a.修改模具,增防呆功能;
b.采模具上做记号等方式,并在组模后对照料带做必要的检查、确认,
并做出书面记录,以便查询。
在冲压生产中,模具的日常维护作业至关重要,即日常注意检查冲压机及模具是否处于正常状态,如冲压油的供给导向部的加油。
模具上机前的检查,刃部的检查,各部位锁紧的确认等,如此可避免许多突发性事故的产生。
修模时一定要先想而后行,并认真做好记录积累经验。