第1章铸造A详解
机械制造工艺基础第六版:第一章铸造教案讲义
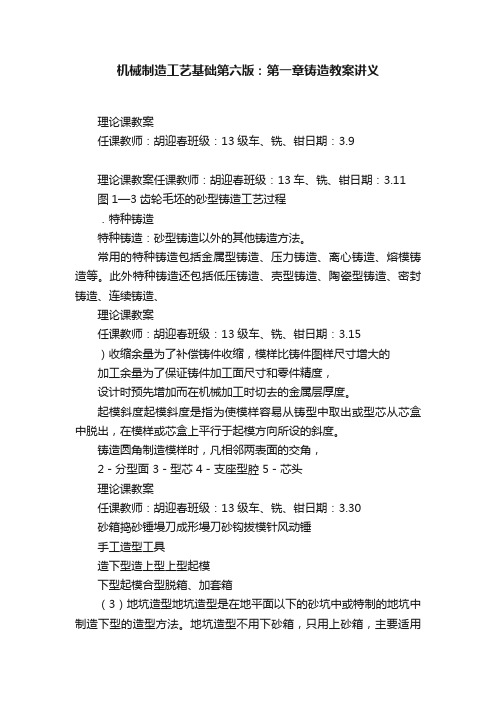
机械制造工艺基础第六版:第一章铸造教案讲义理论课教案任课教师:胡迎春班级:13级车、铣、钳日期:3.9理论课教案任课教师:胡迎春班级:13车、铣、钳日期:3.11 图1—3齿轮毛坯的砂型铸造工艺过程.特种铸造特种铸造:砂型铸造以外的其他铸造方法。
常用的特种铸造包括金属型铸造、压力铸造、离心铸造、熔模铸造等。
此外特种铸造还包括低压铸造、壳型铸造、陶瓷型铸造、密封铸造、连续铸造、理论课教案任课教师:胡迎春班级:13级车、铣、钳日期:3.15)收缩余量为了补偿铸件收缩,模样比铸件图样尺寸增大的加工余量为了保证铸件加工面尺寸和零件精度,设计时预先增加而在机械加工时切去的金属层厚度。
起模斜度起模斜度是指为使模样容易从铸型中取出或型芯从芯盒中脱出,在模样或芯盒上平行于起模方向所设的斜度。
铸造圆角制造模样时,凡相邻两表面的交角,2-分型面 3-型芯 4-支座型腔 5-芯头理论课教案任课教师:胡迎春班级:13级车、铣、钳日期:3.30砂箱捣砂锤墁刀成形墁刀砂钩拔模针风动锤手工造型工具造下型造上型上型起模下型起模合型脱箱、加套箱(3)地坑造型地坑造型是在地平面以下的砂坑中或特制的地坑中制造下型的造型方法。
地坑造型不用下砂箱,只用上砂箱,主要适用于大中型铸件的单件生产。
地坑造型操作较麻烦,劳动量大,1-通气管 2-型芯 3-冒口 4-铸型空腔 5-浇口 6-上箱 7-定位桩 8-焦炭1-下砂箱 2-刮板架 3-刮板 4-上砂箱 5-型砂2.机器造型机器造型:用机器完成紧砂和起模或至少完成紧砂操作的造型工序称为机器造型。
芯盒的装配取芯芯盒造芯刮板造芯.烘干与刷涂料烘芯:用适当温度和足够时间加热型芯,使其获得一定强度的过程。
芯骨:放入型芯中用以加强或支持型芯并有一定形状的金属构架。
烘芯的目的是提高烘芯的强度和透气性,减少型芯的发气量。
-直浇道 3-横浇道 4-内浇道冒口:铸型内存储供补缩铸件用熔融金属的空腔。
-直浇道 3-横浇道 4-内浇道合型:又称合箱,是将铸型的各个组元,如上型、下型、型芯、浇口盆等组合成一个完整铸型的操作过程。
铸造基础知识教程
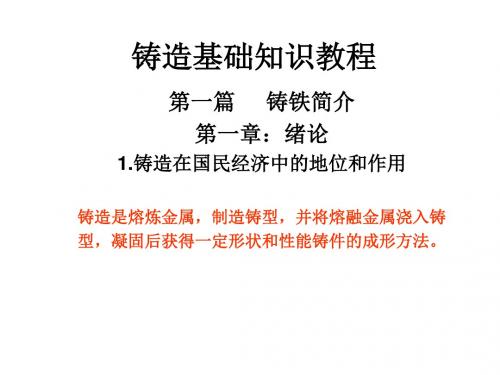
2.球铁的主要种类和应用:
1)珠光体球 典型牌号 性能特点 应用:曲轴、连杆
铁
(QT700-2) 强度为主 等
2)铁素体球 铁
典型牌号 (QT450-
10)
性能特点 韧性为主
应用:汽拖底盘零 件、铸管等
3)混合基体 典型牌号 性能特点 应用:齿轮、叶轮、
球铁
(QT500-7) 强韧结合 螺栓等
A体QT(阀门、电力金具)、A+B、B(齿 4)其他类型 轮、凸轮轴)、M、M+A、M+P+Cm(耐磨
杂 • 2.可制造各种合金铸件 • 3.铸件的尺寸精度高 • 4.成本低廉 • 铸件在一般机器生产中约占总质量的40 %~80%,而成
本只占机器总成本的25 %~30%。 • 成本低廉的原因是:①容易实现机械化生产;②可大量利
用废、旧金属料;③与锻件相比,其动力消耗小;④尺寸 精度高,加工余量小,节约加工工时和金属
2)、我国铸造技术的发展
• 我国的铸造技术已有6000年悠久的历史,是世界 上较早掌握铸造技术的文明古国,
• 1978年湖北省随县出土的曾侯乙墓青铜器重达1 0t。有64件的一套编钟,铸造时代是距今2400 年前的战国初期。湖北省随县出土的曾侯尊盘可 以看出铸工之精湛,铸于战国初期。
• 河北省沧州的大铁狮,高5m多,长近6m.重 19.3t,是公元9世纪五代后周时铸成的.
第二章 灰铸铁
• §2-1 灰铸铁的特点 • 1.金相组织与力学性能 • 组织:G片+P 或 • G片+P+F(间或有少量Cm) • 非金属夹杂物: 硫化物+磷共晶
• 2.牌号与成分
• 1)灰铸铁牌号:
• HT150、HT200、HT250、HT300、 HT350,共5个牌号
机械制造基础课堂习题(第一章 铸造)20120304

《机械制造基础》课堂习题(热加工工艺基础—第一章铸造)一、选择题1、滑动轴承生产时,采用的铸造方法应是()。
A、溶模铸造B、压力铸造C、金属型铸造D、离心铸造2、铸件缩孔常产生的部位是()。
A、冒口B、最后凝固区C、浇口3、合金液体的浇注温度越高,合金的流动性()。
A、愈好B、愈差C、愈小D、愈大4、在铸造生产的各种方法中,最基本的方法是()。
A、砂型铸造B、金属型铸造C、离心铸造D、熔模铸造5、在下列合金中,流动性最差的合金是()。
A、灰铸铁B、铸钢C、铜合金D、铝合金6、铸件的壁或肋的连接应采用()。
A、锐角连接B、直角连接C、圆角连接D、交叉连接7、在铸铁的熔炼设备中,应用最为广泛的是()。
A、电弧炉B、冲天炉C、工频炉D、反射炉8、影响铸铁性能最主要的因素是()。
A、石墨形状B、基体组织C、含碳量D、含硅量9、下列何种金属通常以糊状凝固方式结晶()。
A、纯金属B、结晶温度范围宽的合金C、共晶合金D、恒温下结晶的合金10、为防止铸件产生内应力,型砂应具有一定的()。
A、透气性B、耐火性C、强度D、退让性11、在型芯中安置芯骨的主要作用是()。
A、增加透气性B、激冷C、提高强度D、定位12、造型时,如果型砂的紧实度太高,铸件易产生()。
A、夹杂B、气孔C、缩孔D、冷隔13、铸件在固态收缩时,因受到铸型、型芯等外力阻碍而产生的应力一般称为()。
A、固态相变应力B、机械应力C、热应力14、球墨铸铁牌号为QT450-10,其中450代表何意。
()A、抗弯强度B、抗拉强度C、硬度D、冲击韧性15、如果铸铁在结晶过程中,各阶段石墨化都能充分进行,最后得到的组织为:()A、P+GB、F+PC、F+GD、G16、下列合金流动性最好的是哪一种。
()A、共晶合金B、亚共晶合金C、过共晶合金D、结晶温度范围宽的合金17、制造双金属滑动轴承时,内衬轴承合金通常是采用()铸造方法镶铸在钢制轴瓦上的。
A、压力铸造B、熔模铸造C、离心铸造D、砂型铸造18、芯头是型芯的重要组成部分,芯头一般()形成铸件的形状。
第一章铸造解析
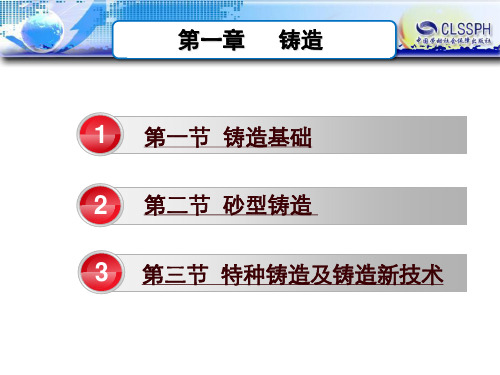
铸造分类:
第一章 铸造
砂型铸造: 制造砂型的基本原材料是铸造砂 和型砂粘结剂.最常用的铸造砂是硅 质砂.硅砂的高温性能不能满足使用 要求时则使用锆英砂,铬铁矿砂,刚玉 砂等特种砂.
第一章 铸造
金属型铸造又称硬模铸造,它是将液体金 属浇入金属铸型,以获得铸件的一种铸造 方法。铸型是用金属制成,可以反复使用 多次(几百次到几千次)。金属型铸造目 前所能生产的铸件,在重量和形状方面还 有一定的限制,如对黑色金属只能是形状 简单的铸件;铸件的重量不可太大;壁厚 也有限制,较小的铸件壁厚无法铸出。
第一章 铸造
1 第一节 铸造基础 2 第二节 砂型铸造 3 第三节 特种铸造及铸造新技术
第一章 铸造
铸造是人类掌握较早的一种金属热加工工艺,已有约6000年的历史。 公元前3200年,美索不达米亚出现铜青蛙铸件。公元前13~前10世 纪之间,中国已进入青铜铸件的全盛时期,工艺上已达到相当高的水 平,如商代的重875千克的司母戊方鼎、战国的曾侯乙尊盘和西汉的 透光镜等都是古代铸造的代表产品。早期的铸造受陶器的影响较大, 铸件大多为农业生产、宗教、生活等方面的工具或用具,艺术色彩较 浓。公元前513年,中国铸出了世界上最早见于文字记载的铸铁件— —晋国铸鼎(约270千克重)。公元8世纪前后,欧洲开始生产铸铁件 。18世纪的工业革命后,铸件进入为大工业服务的新时期。进入20世 纪,铸造的发展速度很快,先后开发出球墨铸铁,可锻铸铁,超低碳 不锈钢以及铝铜、铝硅、铝镁合金,钛基、镍基合金等铸造金属材料 ,并发明了对灰铸铁进行孕育处理的新工艺。50年代以后,出现了湿 砂高压造型,化学硬化砂造型和造芯、负压造型以及其他特种铸造、 抛丸清理等新工艺。
适用于铸件最大截面在一端且为平面的铸件
特种成型-熔模铸造工艺技术详解
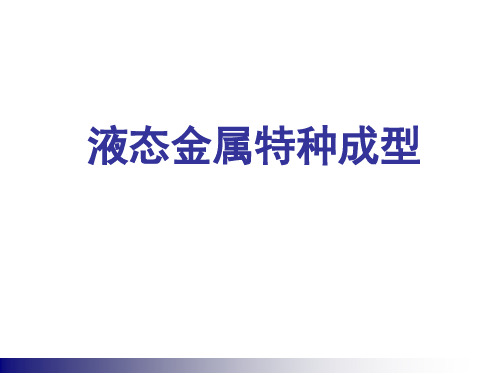
二是与醇发生脂化反应,生成脂肪酸脂和
水。
(3)酯蜡 ➢ 是高级脂肪酸和高级饱和一元醇进行脂化反应生
成酯的混合物,其分子式为RCOOR′。
➢ 主要包括川蜡C25H51COOC26H53和蜂蜡 C15H31COOC30H61 。
3、工艺性能 ➢可焊性:具有良好的焊接性能和焊接强度。 ➢流动性:获得形状准确和表面光洁的熔模。 ➢图挂性:模料应能很好的为耐火材料所润湿。 ➢灰分:要尽可能少,应低于0.05%。 4、其他性能
还要求模料的密度小,回收方便,复用 性好,无公害及来源丰富,价格低廉等。
二、模料的种类、组成和性能
1、蜡基模料(低温模料)
金属材料工程教研室
第二节 制壳原材料
对制壳用耐火材料提出相应的性能要求: (1)耐火材料的耐火度及最低共熔点
必须具有高于金属浇注温度的耐火度,耐火度 和熔点这两个概念的区别。 (2)耐火材料的热膨胀性
各种耐火材料的热膨胀性能主要取决于其化学 矿物组成和所处的温度。 (3)耐火材料的化学稳定性
耐火材料对于粘结剂和熔融金属应具有良好的 化学稳定性。
金属材料工程教研室
金属材料工程教研室
金属材料工程教研室
金属材料工程教研室
工艺流程: 熔模铸造的工艺过程包括:蜡模制造、
结壳、
熔模铸造的特点:
➢铸件的精度和表面质量较高(精度可达 CT4~7,Ra1.6~12.5)。
➢合金种类不受限制,钢铁及有色金属均可适 用。
➢ 石蜡的强度低,塑性好,硬度差(针入度为150)。
2)地蜡 ➢ n=35~53,主要由异构烷烃组成,是微晶型蜡。 ➢ 熔点比石蜡高,热稳定性好,能与石蜡互溶。 ➢ 有提纯地蜡和合成地蜡两种,地蜡价高。 (2)脂肪酸蜡 分子式CnH2n+1COOH,为晶体。 ➢ 酸性:固态时酸性不明显,熔融时随温度升高,
铸造课件论述可编辑全文
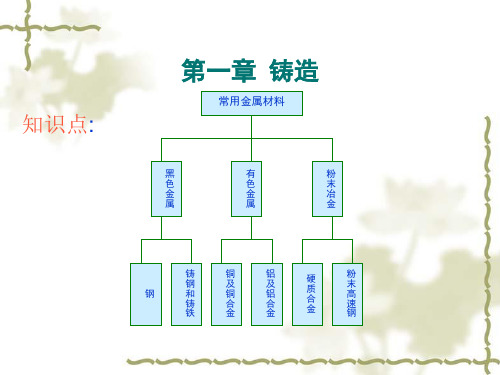
浇不足
冷隔
夹砂
气孔
夹渣
充型能力的决定因数
合金的流动性 铸型性质 浇注条件 铸件结构等
合金的充型能力
测试合金充型 能力的方法:
如右图,将合 金液浇入铸型中, 冷凝后测出充满型 腔的式样长度。浇 出的试样越长,合 金的流动性越好, 合金充型能力越好.
几种不同合金流动性的比较
比较下面几种合金流动性能 *铸钢的流动性
裂纹
当热应力大到一定程度会导致出现裂纹。
热应力的形成过程演示
热应力的消除方法
铸件的结构:铸件各部分能自由收缩
铸件的结构尽可能对称 铸件的壁厚尽可能均匀
工艺方面:采用同时凝固原则 时效处理:人工时效;自然时效
铸件的变形原因
结论: 厚部、心部受拉应力, 出现内凹变形。 薄部、表面受压应力, 出现外凸变形。
铸件的结构
凡能增加金属流动阻力和冷却速度,降低流速的因素,均能降低金属的流动性。 如型腔过窄,浇注系统结构复杂,直浇道过低,内浇道截面太小,型砂水分 过多或透气性不好,铸型材料热导性过大等,都会降低金属的流动性。
铸件结构对充型能力的影响
折算厚度:
复杂程度:
折算厚度也叫当量厚度 或模数,是铸件体积与铸件 表面积之比。折算厚度越大, 热量散失越慢,充型能力就 越好。
孕育铸铁应用:一般用于动载荷较小、静载荷较大, 对强度、硬度、和耐磨性要求较高的重要铸件,尤 其是厚大铸件,如床身、凸轮轴、汽缸体等
灰铸铁的铸造性能:流动性好、 收缩小,铸造性能好, 具有自身补缩的能力。
铸造工艺特点:冲天炉熔炼(金属炉料、燃料、熔剂) 砂型铸造 常采用同时凝固原则,高强度采用顺序凝固
成本低,原材料来源广泛, 价格低廉,一般不需要昂 贵的设备
电子课件——机械制造工艺基础(第七版) 1第一章 铸造

1 §1—1 概述 2 §1—2 砂型铸造 3 §1—3 特种铸造及铸造新技术
第一章 铸造
§1—1 铸造基础
一、 铸造及其分类
将熔融金属浇注、压射或吸入铸型型 腔中,凝固后获得具有一定形状、尺寸 和性能的毛坯或零件
砂型铸造
铸 造
特种铸造
熔模铸造 金属型铸造 压力铸造 离心铸造
§第1一—章1 铸铸造造基础
整模两箱造型
§第1—一2章 砂型铸铸造造
模样分成两 部分,分别 制造上型和 下型,型腔 则位于上型 和下型之间
分模两箱造型
§第1—一2章 砂型铸铸造造
2)脱箱造型 在可脱砂箱内造型,合型后浇注前脱去砂箱
§第1—一2章 砂型铸铸造造
3)挖沙造型 下型分型面挖成不平分型面(曲面、非平面)
§第1—一2章 砂型铸铸造造
气动微振压实造型机紧砂
§第1—一2章 砂型铸铸造造
3.造芯
制造型芯的过程称为造芯
手工造芯 机器造芯
芯盒造芯
§第1—一2章 砂型铸铸造造
4.合型
又称合箱,是将铸型的各个组元 组合成一个完整铸型的操作过程
5.熔炼
熔炼是使金属由固态转变为熔融状态的过程
§第1—一2章 砂型铸铸造造
6.浇注
(1)浇注工具
4.铸造圆角
相邻两表面的过渡圆角
§第1—一2章 砂型铸铸造造
5.芯头
在模样上:芯头是模样的凸出部分 在型芯上:芯头是型芯的外伸部分
§第1—一2章 砂型铸铸造造
6.浇注系统
(1)外浇口 (2)直浇道 (3)横浇道 (4)内浇道
7.冒口
§第1—一2章 砂型铸铸造造
三、砂型铸造的工艺过程
1.混砂
第一章 砂型铸造
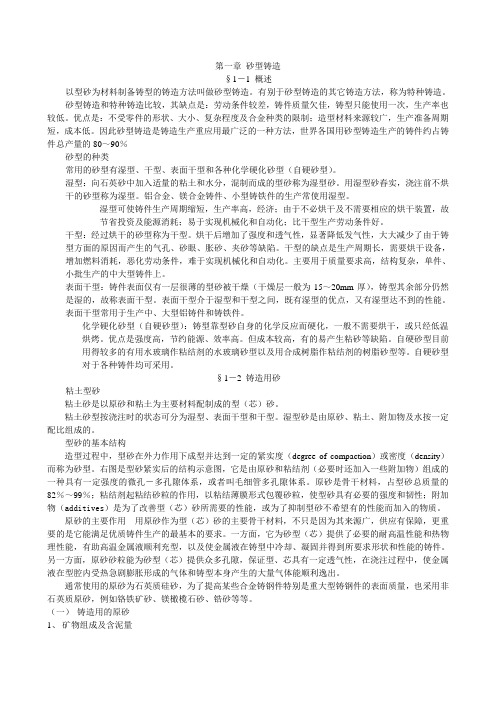
第一章砂型铸造§1-1 概述以型砂为材料制备铸型的铸造方法叫做砂型铸造。
有别于砂型铸造的其它铸造方法,称为特种铸造。
砂型铸造和特种铸造比较,其缺点是:劳动条件较差,铸件质量欠佳,铸型只能使用一次,生产率也较低。
优点是:不受零件的形状、大小、复杂程度及合金种类的限制;造型材料来源较广,生产准备周期短,成本低。
因此砂型铸造是铸造生产重应用最广泛的一种方法,世界各国用砂型铸造生产的铸件约占铸件总产量的80~90%砂型的种类常用的砂型有湿型、干型、表面干型和各种化学硬化砂型(自硬砂型)。
湿型:向石英砂中加入适量的粘土和水分,混制而成的型砂称为湿型砂。
用湿型砂舂实,浇注前不烘干的砂型称为湿型。
铝合金、镁合金铸件、小型铸铁件的生产常使用湿型。
湿型可使铸件生产周期缩短,生产率高,经济;由于不必烘干及不需要相应的烘干装置,故节省投资及能源消耗;易于实现机械化和自动化;比干型生产劳动条件好。
干型:经过烘干的砂型称为干型。
烘干后增加了强度和透气性,显著降低发气性,大大减少了由于铸型方面的原因而产生的气孔、砂眼、胀砂、夹砂等缺陷。
干型的缺点是生产周期长,需要烘干设备,增加燃料消耗,恶化劳动条件,难于实现机械化和自动化。
主要用于质量要求高,结构复杂,单件、小批生产的中大型铸件上。
表面干型:铸件表面仅有一层很薄的型砂被干燥(干燥层一般为15~20mm厚),铸型其余部分仍然是湿的,故称表面干型。
表面干型介于湿型和干型之间,既有湿型的优点,又有湿型达不到的性能。
表面干型常用于生产中、大型铝铸件和铸铁件。
化学硬化砂型(自硬砂型):铸型靠型砂自身的化学反应而硬化,一般不需要烘干,或只经低温烘烤。
优点是强度高,节约能源、效率高。
但成本较高,有的易产生粘砂等缺陷。
自硬砂型目前用得较多的有用水玻璃作粘结剂的水玻璃砂型以及用合成树脂作粘结剂的树脂砂型等。
自硬砂型对于各种铸件均可采用。
§1-2 铸造用砂粘土型砂粘土砂是以原砂和粘土为主要材料配制成的型(芯)砂。
铸造工艺学第一篇第一章讲解
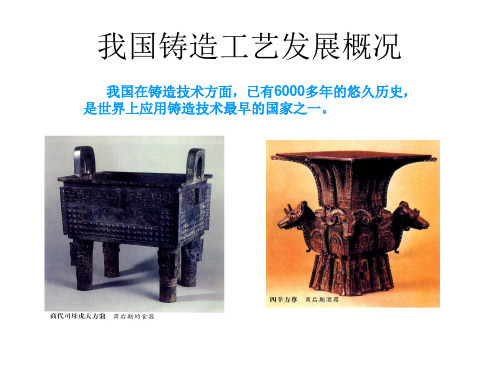
⑶ 重要性:
在机床、内燃机、重型机 器中,铸件约占70-90%;
铸造生产 的内容
在风机、压缩机中,约占
60-80%;在拖拉机中,约 占50-70%,农业机械中, 约占40-70%;汽车中约占 20-30%。
铸造合金 熔炼
铸造工艺
铸造过程 的机械化 及自动化
⑷铸造生产的内容:三个 方面。
工艺的含义及制定原则
永乐大钟
它重46.5吨,通高6.75米, 最大外径3.3米。永乐大钟距 今已有500多年历史,它是采 用地坑造型、表面陶范的泥 型法铸造的。钟体内外遍铸 经文,共22.7万字。铸造时, 几十座熔炉同时开炉,熔化 的铜汁沿着泥做的槽道注入 陶范,一次成形,工艺高超。
青龙偃月刀 重八十二斤
Hale Waihona Puke 现代铸件(2)型(芯)砂用原材料的基本性能的影响,型 (芯)砂性能及其对铸件质量影响的基本规律, 型(芯)砂的配制及其性能控制和检测的基本原 理。
(3)工艺设计的基本原则和方法以及浇冒口系统的 作用和基本原理,提高其效率的措施。
第一篇 金属—铸型的相互作用
Interface Reactions Between Metal and Mould
内应力 和变形
第一章 砂型结构及其工作条件
型砂的结构
砂型----造型过程中型砂在外力作用下成型 并达到所要求的密度(紧实度)而成为砂型。
型砂----由原砂、粘结剂、附加物等按一定 比例均匀混制而成的混合物。
1-原砂砂粒 2-粘结剂 3-附加物 4-微孔
原砂的主要作用
• 1、为砂型提供了必要的耐高温性能和热物理性能, 有助高温金属顺利充型,以及使金属液在铸型中冷 却、凝固并得到所要求形状和性能的铸件。
机械制造工艺基础课件第一章铸造

2.制造模样与芯盒的注意要点
(1)分型面——铸型组元间的接合面。
1—上型
2—分型面 3—型芯
4—支座型腔
5—芯头 6—下型
第十七页,共五十八页,2022年,8月28日
(2)收缩余量——为了补偿铸件收缩,模样比铸件图样尺 寸增大的数值。
(3)加工余量——为保证铸件加工面尺寸和零件精度, 在铸造工艺设计时预先增加而在机械加工时切去的金属层厚 度。
第十八页,共五十八页,2022年,8月28日
(4)起模斜度——为使模样容易从铸型中取出或型芯从芯盒
中脱出,在模样或芯盒上平行于起模方向所设的斜度。
一般α=0.5 ° ~3°
第十九页,共五十八页,2022年,8月28日
(5)铸造圆角——制造模样时,凡相邻两表面的交角,都 应做成圆角。
铸造圆角(r为铸造圆角半径)
第四十五页,共五十八页,2022年,8月28日
握包
抬包
吊包
第四十六页,共五十八页,2022年,8月28日
2.浇注温度与浇注速度
浇注温度(℃)——金属熔液浇入铸型时所测量到的温度 。
浇注速度(kg/s)——单位时间内浇入铸型中的金属熔液质量
。
第四十七页,共五十八页,2022年,8月28日
二、落砂和清理
四、 造芯 五、浇注系统及冒口 六、合型
第十页,共五十八页,2022年,8月28日
一、砂型和造型材料
1. 造型材料 2. 型砂和芯砂 3. 砂型
第十一页,共五十八页,2022年,8月28日
1.造型材料
造型材料——制造砂型和砂芯的材料。 1砂 2 黏土
3 黏结剂 4 附加物
第十二页,共五十八页,2022年,8月28日
第八页,共五十八页,2022年,8月28日
第一章 铸造PPT课件

二、铸造工艺参数确定(P11)
1、铸造收缩率:为补偿收缩,模样比铸件图样 尺寸增大的数值。其大小与铸件尺寸大小、结 构、壁厚,铸造合金的线收缩率及收缩时受阻 碍情况有关。常以铸件线收缩率表示。即
寸、形状、重量和数量的铸件都能生产; 3)成本较低。原材料来源广泛,价格低廉。
3
铸造成形的缺点(P1)
1)铸造组织疏松、晶粒粗大,内部易产生 缩孔、缩松、气孔等缺陷。
2)铸件的机械性能较低。 3)铸造工序多,难以精确控制,使得铸件
质量不够稳定。
4)劳动条件较差,劳动强度较大。
4
铸造的主要工序
零件图
13
二、分型面的选择( P30) Choose of Mold Joint
分型面是指分开铸型便于取模的接合面。 它决定了铸件在造型时的位置。通常造 型位置和浇注位置一致。分型面对铸件 质量及铸造工艺有很大影响。首先应保 证铸件质量要求,其次应使操作尽量简 化,再考虑具体生产条件。
14
浇注位置的选择原则( P29)
铸造工艺图
模样图、芯盒图、铸型装配图
制造模样及芯盒
混制型砂 预处理造型材料 混制芯砂
主
要
造型
制芯
工 序
演
烘干铸型
合型
烘干芯子
示
准备 炉料
熔炼 金属
化验
浇注 落砂、清理
检验
热处理
合格铸件
5
第三节 砂型(芯)制造(P16)
造型和制芯是砂型铸造最基本 的工序,按照紧实型砂和起模的方 法,可分为手工造型和机器造型两 大类。
1、震压造型 3、高压造型 5、空气冲击造型
2、微震压实造型 4、射压造型 6、抛砂造型
9
铝合金铸造基础知识.精品ppt资料
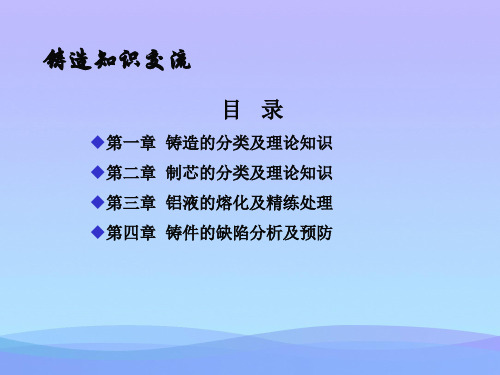
3.金属液〔铝液〕在压力作用下充型,流动性增加, 有利于生产复杂薄壁件,获得轮廓清晰的铸件;
低压铸造
低压铸造的缺点:在生产铝合金铸件时,坩埚和升液 管长期与铝液接触,易受侵蚀而报废;也会使金属液 〔铝液〕因增铁而性能恶化。 低压铸造目前主要用于生产铝合金,如汽车工业的汽 车轮毂、内燃发动机的气缸体、气缸盖、活塞等。
1-浇勺 2-压射活 塞 3-压室 4-铝 液 5-定型 6-动 型 7-顶杆机构
压力铸造
5
4 2
3
b〕压射铝液进入型 腔
压室3的左端局部设 在定型5之中,压室 活塞2向左移动,把 铝液4压入压铸型 〔压铸模〕。
压力铸造
76
c〕开型取下铸件
动型6左移,翻开铸 型〔模具〕,形成 的铸件连同浇注余 料8一起随动型6左 移,最后由顶杆机 构7把铸件顶离动型 6,完成一个压铸循 环。
金属型铸造
五菱B11/12D缸盖
金属型铸造
金属型铸造的优点:
1.金属型铸件具有较高的尺寸精度和较低的外表粗 糙度;
2.金属型铸件组织致密,具有较高强度、硬度和耐 磨蚀性;
3.金属型上可方便地采取较多工艺措施;
4.铸造生产中使用较少的坭芯,可节省造型材料 〔砂〕;
金属型铸造
金属型铸造的缺点:
1.金属型〔模具〕加工困难,制造和调整周期长, 一次性投资高;
件的方法。 〔二〕壳芯在浇注时破裂
别离夹杂和气泡,阻止其进入型腔; 高温时铝和水汽的反响: 另一方面原砂砂粒能为坭芯提供众多孔隙,保证坭芯具有一定的透气性。
高压力和高速度是压力铸造时金属液〔铝液〕充填成 金属型铸造:金属液〔铝液〕用重力浇注法浇入金属型,以获得铸件的一种铸造方法。
第二篇铸造第一章铸造工艺基础演示文稿

坑。动画演示。 ◆收缩率↑,浇注温度↑,铸件愈厚,则缩孔↑。
现在是16页\一共有20页\编辑于星期五
2)缩松:分散在铸件某区域内的细小缩孔,称为缩松。缩松分为宏 观缩松和纤维缩松。动画演示
(2)铸型温度: 铸型的温度↑ 充型能力↑∴铸型可先预热。
(3)铸型中气体: 砂型铸造产生大
量气体,排气能力差,型腔中气压↑流 动阻力↑充型能力↓,所以铸型要留出
排气口。
四、铸件结构条件
铸件结构对充型能力的影响。
折算厚度: 折算厚度也叫当量厚度或模数,是铸件体积与铸件表面积之比。折算厚度 越大,热量散失越慢,充型能力就越好。铸件壁厚相同时,垂直壁比水平壁更容
二、铸件合金的收缩 合金从浇注、凝固直至冷却到室温,其体积
或尺寸缩减的现象,称为收缩 - 收缩是多种铸造
缺陷产生的根源。(如:缩孔、缩松、裂纹、
变Байду номын сангаас等)。
◆合金的收缩经历有三个阶段:
1)液态收缩、2)凝固收缩 、3)固态收缩
现在是14页\一共有20页\编辑于星期五
◆合金的收缩过程: 液态合金冷却
合金收缩 固态合金冷却
越小,则流动性越好。铸件晶粒组织
◆由图亚共晶铸铁随含碳量的增加,结晶温度范围减小,流动性提高。
实验证明铸铁的流动性好,
铸钢的流动性差
。
现在是9页\一共有20页\编辑于星期五
◆合金流动性对充型能力的影响
合金流动性的决定因数:
1)合金种类: 合金不同,流动性不同
2)化学成分:同种合金中成分不同的合金具有不同的结晶特点, 流动性也不同。
铸造基本常识课件

2020/12/8
33
三、铸造合金的偏析和吸气性
1.偏析 铸件中出现化学成分不均匀的现象称为偏析。铸件的偏析可分为晶内偏析、区域偏析和体积质量偏析 三类。 (1)晶内偏析(又称枝晶偏析)是指晶粒内各部分化学成分不均匀的现 象,这种偏析出现在具有一定 凝固温度范围的合金铸件中。为防止和减少晶内偏析的产生,在生产中常采取缓慢冷却或孕育处理的 方 法。 (2)区域偏析是指铸件截面的整体上化学成分和组织的不均匀。避免区域偏析的发生,主要应该采取预 防措施,如控制浇注温度不要太高 ,采取快速冷却使偏析来不及发生,或采取工艺措施造成铸件断面 较低的温度梯度,使表层和中心部分接近同时凝固。 (3)比重偏析 铸件上、下部分化学成分不均匀的现象称为比重偏析。为防止 比重偏析,在浇注时应 充分搅拌金属液或加速合金液的冷却, 使液相和固相来不及分离,凝固即告结束。
2020/12/8
21
(3)中间凝固方式 大多数合金的凝固介于逐层凝固和糊状凝固之间,称为中间凝固方式。中碳钢、高锰钢、白口铸 铁等具有中间凝固方式。
图9-5 铸件的凝固方式
2020/12/8
22
2. 凝固方式的影响因素 (1)合金凝固温度范围的影响 合金的液相线和固相交叉在一起,或间距很小,则金属趋于逐层凝固;如两条相线之 间的距离很大,则趋于糊状凝固;如两条相线间距离较小,则趋于中间凝固方式。 (2)铸件温度梯度的影响 增大温度梯度,可以使合金的凝固方式向逐层凝固转化;反之,铸件的凝固方式向糊 状凝固转化。
缺点或者说适用范围有: 1、从尺寸大小看,不适宜做大型铸件。迪砂虽然不断地扩大可造型尺寸范围,但最大也就 850*1200*675。 2、砂芯太复杂的铸件操作不便,如汽缸体等,不如水平造型下芯方便。 3、砂芯较大的铸件不宜采用,如变速箱壳体。 4、拔模太深,即使在中间分型也不能应用,给春兰做的偏心轴基本已到极限。 5、需要放置冷铁的砂型也不宜采用。
第一节铸造基础知识(指导人员用)

铸造实习课件目录第一节铸造基础知识 (4)一、铸造生产概述 (4)二、铸造生产常规工艺流程 (4)第二节砂型铸造工艺 (5)一、型砂和芯砂的制备 (5)二、型砂的性能 (5)三、铸型的组成 (6)四、浇冒口系统 (6)五、模样和芯盒的制造 (7)第三节合金的熔炼 (9)一、铝合金的熔炼 (9)二、铸铁的熔炼 (10)第四节造型 (12)一、手工造型 (12)二、制芯 (15)三、合型 (16)四、造型的基本操作 (16)五、合金的浇注 (18)六、机器造型 (19)第五节铸造工艺设计 (21)一、分型面 (21)二、型芯 (22)三、铸造工艺参数 (22)四、模样的结构特点 (22)第六节铸件常见缺陷的分析 (24)铸工实习安全技术守则 (25)第七节铸工概论 (26)一、铸造的辉煌历史 (26)二、铸造的分类 (26)第八节特种铸造 (27)一、压力铸造 (27)二、实型铸造 (28)三、离心铸造 (28)四、低压铸造 (29)五、熔模铸造 (30)六、垂直分型无箱射压造型 (31)七、金属型铸造 (31)八、多触头高压造型 (32)九、真空密封造型 (33)第九节铸造工艺图的绘制 (34)一、铸造工艺图 (34)二、浇注位置 (34)三、分型面 (34)四、机械加工余量和铸孔 (34)五、拔模斜度 (35)六、铸造圆角 (35)七、型芯、芯头及芯座 (35)八、铸造收缩率 (35)九、铸造工艺图的绘制 (35)十、模样图的绘制 (35)十一、铸型装配图的绘制 (36)十二、铸件图的绘制 (37)十三、模样、型腔、铸件和零件之间的尺寸与空间的关系 (37)十四、铸造技术的发展趋势 (37)第一节铸造基础知识一、铸造生产概述铸造是熔炼金属,制造铸型,并将熔融金属浇入铸型,凝固后获得一定形状和性能铸件的成形方法。
铸件一般是毛坯,经切削加工等才成为零件。
零件精度要求较低和表面粗糙度,参数值允许较大的零件,或经过特种铸造的铸件也可直接使用。
铸造基础1解析
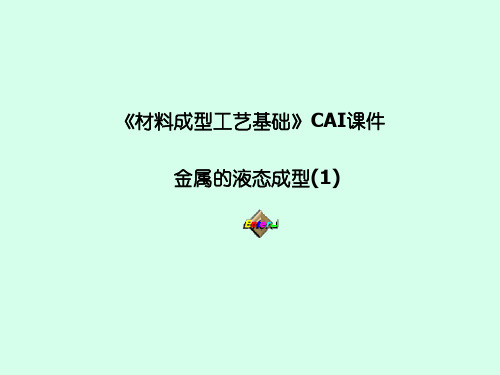
◆ 在同样浇铸温度下,共晶成分合金液体的过 热度大,在液态时间长
3)杂质 熔融合金中出现的固态夹杂物
9 2020年10月17日星期六
泥石流
(2)浇注条件
1)浇注温度t浇 t浇 原因: t浇 合金粘度
t浇 过热度
充型能力 内摩擦阻力 流动时间
2)充型压力 充型压力 充型能力
10 2020年10月17日星期六
同时凝固: 采用工艺方法尽量减少铸件各部位间的
温度差,使其均匀冷却。
21 2020年10月17日星期六
工艺措施: 浇口开在薄壁处;厚壁处安放冷铁;
22 2020年10月17日星期六
同时凝固原则之不足: 铸件心部容易产生缩孔或缩松
23 2020年10月17日星期六
4)机械应力的形成 动画10 机械应力: 合金的固态收缩受到铸型或型芯的机 械阻碍而形成的内应力
25 2020年10月17日星期六
5、残余应力的危害及消除
尽管变形后铸件的内应力有所减缓,但并未彻 底消除,它的存在不利于切削加工精度的提高
动画12
消除方法:时效处理
时效处理 自然时效 人工时效
26 2020年10月17日星期六
6、铸件的裂纹与防止
裂纹 热裂 冷裂
(1)热裂 在高温下产生的裂纹。其形 状特征是:裂纹短、缝隙宽、形状曲折、 缝内呈氧化色
2)合金的化学成分 影响规律:
共晶成分合金的流动性最好,远离 共晶成分合金的流动性最差
8 2020年10月17日星期六
理由: ◆ 共晶成分合金的结晶是在恒温下进行的,液 态合金从表层逐层向中心凝固,已结晶的固体层 内表面光滑,对金属液的流动阻力小;
非共晶成分合金有液、固两相共存区;已 结晶固体层内表面粗糙,流动阻力大;
- 1、下载文档前请自行甄别文档内容的完整性,平台不提供额外的编辑、内容补充、找答案等附加服务。
- 2、"仅部分预览"的文档,不可在线预览部分如存在完整性等问题,可反馈申请退款(可完整预览的文档不适用该条件!)。
- 3、如文档侵犯您的权益,请联系客服反馈,我们会尽快为您处理(人工客服工作时间:9:00-18:30)。
图1-6 整体模造型过程
a)造下型 b)刮平 c)造上型 d)起模 e)合型 e)带有浇口铸件 1-捣砂箱 2-砂箱 3-模底板 4-模样 5-刮板 6-记号 7-浇口棒 8-气孔针
图1-7 两箱分开模造型过程
a)铸件简图 b)模样 c)造下型 d)造上型、开浇冒口 e)下芯、合型并加压铁f )带有浇冒口的铸件 1-下半模样 2-下砂箱 3-模底板 4-浇田棒 5-冒口棒 6-上半模样 7-上砂箱 8-压铁
由于铸造具有上述优点,因此广泛应用于机械零 件的毛坯制造,在各种机械和设备中,铸件在整机重 量上占有很大的比例。
表2-1 各类机械工业中铸件重量比
机 械 类 别
%
机床、内燃机、重型机器 风机、压缩机 拖拉机 农业机械
汽车
70~90
60 ~ 80 50 ~ 70 40 ~ 70 20 ~ 30
铸造存在如下缺点:
(5)芯头 芯头是指模样上的突出部分,它在型内形成芯座(铸 型中专为放置型芯头的空腔),以放置芯头。对于型芯来说芯头是 型芯的外伸部分,不形成铸件轮廓,只是落入芯座内,用以定位和 支承型芯(图1-4)。
(6)分型面 分型面是指铸型组元间的接合面(图1-4)。选择 分型面时应考虑以下几个方面:使分型面具有最大水平投影尺寸; 尽量满足浇注位置的要求;造型方便;起模容易。
时要保证铸型型腔几何形状和尺寸的准确及型芯的稳固。合型后,
上、下型应夹紧或在铸型上放且压铁,以防浇注时上型被熔融金 属顶起,造成抬箱、射箱(熔融金属流出箱外)或跑火(着火的
五、造芯
制造型芯的过程称造芯。是为获得铸件的内孔或局部外形,用 芯砂或其他材料制成的安放在型腔内部的铸型组元。造芯可分手工 造芯和机器造芯。常用手工造芯的方法为芯盒造芯。芯盒通常由两 半组成,图1-8为芯盒造芯的示意图。手工造芯主要应用于单件、 小批量生产中。机器造芯是利用造芯机来完成填秒、紧砂和取芯的, 生产效率高,型芯质量好,适用于大批量生产。
有箱造型是用砂箱作为铸型组成 部分制造铸型的过程。砂箱是容纳和
图1-5 砂 箱
支承砂型的刚性框。
有箱造型分整体模造型和分开模造型。有分模面的模样称为 整体模。造型时,型腔全部在半个铸型(通常为下型)内,另外半 个铸型(上型)为平箱,分型面为一平面。整体模造型方法简单, 适用于形状简单的铸件。图1-6所示为整体模造型的过程示图。 有分模面的模样称为分开模。通常为一个分模面,模样被分成 两部分,分别制造上型和下型。型腔位于上型和下型之中。分开模 造型有两箱造型和三箱造型,其中两箱分开模造型是应用最广泛的 一种有箱造型方法。图1-7所示为法兰管铸件的两箱分开模造型的 过程示图。
(4)透气性 型砂透气性用紧实砂样的孔隙度表示。孔隙度越大,则透气性越好。 熔融金属浇入砂型后,在高温的作用下,砂型中会产生大量气体,熔融金属内部也会分 离出气体。如果透气性差,部分气体就会留在熔融金属内不能排出,导致铸件产生气孔 等缺陷。
(5)退让性 铸件冷却收缩时,砂型与型芯的体积可以被压缩的性能称为退让性。 退让性差时,铸件收缩时受到较大阻碍,会使铸件产生较大内应力,甚至产生变形或裂 纹等缺陷。 在铸造过程中,型芯被熔融金属包围,工作条件恶劣,因此,芯砂比型砂应具有更 高的强度、耐火性、透气性和退让性。
图1-1 砂型铸造工艺过程
2、特种铸造 一般称砂型铸造以外的其他铸造方法为特种铸 造。常用的特种铸造有:金属型铸造、压力铸造、 离心铸造、熔模铸造等。
§1-2 砂型的制作
一、砂型 用型砂、金属或其他耐火材料制成,包括形成铸件形状的空腔、 型芯和浇冒口系统的组合整体称为铸型。 用型砂制成的铸型称为砂型。砂型用砂箱支撑时,砂箱也是铸 型的组成部分。 砂型的制作是砂型铸造工艺过程中的主要工序。制造砂型即使 用造型材料,借助模样和芯盒造型造芯,以实现铸件的外形和内形 的要求。 二、造型材料
2、机器造型和自动化造型
用机器全部地完成或至少完成紧砂操作的造型工序称为机器 造型。紧砂是使砂箱(芯盒)内型(芯)砂提高紧实度的操作。 所有造型工序基本不需人力完成的造型过程称为自动化造型。机
器造型和自动化造型可提高生产率,改善劳动条件,提高铸件精
c a b
度和表面质量,但设备、工艺装备等投资较大,适用于大批量生 产和流水线生产。
成形后的型芯一般都需要烘干,烘芯的目的是提高型芯的强度 和透气性,减少型芯的发气量。若需要增加型芯的强度,则可在造 芯时在型芯内放置芯骨。芯骨是一种放入型芯中用以加强或支持型 芯并有一定形状的金属构架。若需要增加型芯的透气性,除对型芯 扎通气孔外,还可在型芯中埋放通气蜡线(蜡质线绳),型芯烘干 时焚化,成为排气通道。型芯表面一般都要刷上涂料,用以提高型 芯表层的耐火度、保温性、化学稳定性,使型芯表面光滑,并提高 其抵抗高温熔融金属的侵蚀能力。
图1-8 芯盒造芯示意图
a)芯盒的装配 b)取芯 1-型芯 2-芯盒 3-定位销 4-夹钳
六、浇注系统及冒口
1、浇注系统
浇注系统是为填充型腔和冒口而开设 于铸型中的一系列通道。通常由浇口杯、 直浇道、横浇道和内浇道组成(图1-9)。
浇注系统简称浇口,其作用是:保 证熔融金属平稳、均匀、连续地充满型腔; 阻止熔渣、气体和砂粒随熔融金属进人型 腔;控制铸件的凝固顺序;供给铸件冷凝 收缩时所需补充的金用熔液(补缩)。
图1-2起模斜度图
图1-3 铸造圆角
图1-4 支座的铸型
1-上型 2-分型面 3-型芯 4--支座 型腔 5-芯头 6-下型
2、芯盒
制造型芯或其他种类耐火材料芯所用的装备称为芯盒。芯盒的 内腔与型芯的形状和尺寸相同。
四、造型
用造型混合料及模样等工艺装备制造铸型的过程称为造型。造 型可分为手工造型、机器造型和自动化造型。
造型材料是制造砂型和砂芯的材料,包括砂、黏土、有机或无 机粘结剂和其他附加物。
按一定比例配合的造型材料,经过混制,符合造型要求的混合 料称为型秒。按一定比例配合的造型材料,经过混制,符合造芯要 求的混合料称为芯砂。
型砂的性能
砂型在浇注和凝固过程中要承受熔融金属的冲刷、静压力和高温的作用,并要排出 大量气体,型芯则要承受凝固时的收缩压力,因此型(芯)砂应有以下几方面的性能要 求: (1)可塑性 型(芯)砂在外力作用下可以成形,外力消除后仍能保持其形状的性 能称为可塑性。可塑性好,易于成形,能获得型腔清晰的砂型,从而保证铸件具有精确 的轮廓尺寸。 (2)强度 型秒、芯砂抵抗外力破坏的能力称为型砂强度。型砂应具有足够的强度, 在浇注时能承受熔融金属的冲击和压力而不致发生变形和毁坏(如冲秒、塌箱等),从 而避免铸件产生夹砂、结疤、砂眼等缺陷。 (3)耐火性 型砂在高温熔融金属的作用下不软化、不熔融烧结及不粘附在铸件表 面上的性能称为耐火性。耐火性差会造成铸件表面粘砂,使清理和切削困难,严重时铸 件报废。
图1-10 带有浇冒口的铸件
1-浇口杯 2-直浇道 3-横浇道 4-内浇道
七、合型
将铸型的各个组元如上型、下型、型芯、浇口盆等组合成一 个完整铸型的操作过程称为合型(又称合箱)。合型前应对砂型 和型芯的质量进行检查,若有损坏,需要进行修理;为检查型腔 顶面与芯子顶面之间的距离需要进行试合型(称为验型)。合型
1、手工造型图1-5砂箱
全部用手工或手动工具完成的造型工序称为手工造型。手工造 型方法简便,工艺装备简单,适应性强,因此在单件或小批量生产, 特别是大型铸件和复杂铸件生产中应用广泛。但手工造型生产率低, 劳动强度大,铸件质量不稳定。 手工造型的方法很多,常见的有: 有箱造型、脱箱造型、地坑造型和刮
板造型等。
L
模
三、模样扣芯盒
1、模样
由木材、金属或其他材料制成,用来形成铸型型腔的工艺装备称为模样。 制造砂型时,使用模样可以获得与零件外部轮廓相似的型腔。模样是按照 零件图样要求绘制的铸造工艺图的。制造模样时要注意以下几点: (1)加工余量 加工余量是指为保证铸件加工面尺寸和零件精度,在铸 件工艺设计时预先增加而在机械加工时切去的金属层厚度。加工余量的大 小根据铸件尺寸公差等级和加工余量来确定。一般小型铸件的加工余置为 2~6mm。 (2)收缩余量 收缩余量是指为了补偿铸件收缩,模样比铸件图样尺寸 增大的数值。收缩余量与铸件的线收缩率和模样尺寸有关,铸件的线收缩 率可用下式表示:
式中
L模 L铸件 L模
1000 0
——铸件线收缩率;
L模 、 L铸件——同一尺寸在模样与铸件上的长度,mm。
不同的铸造金属(或合金)其线收缩率不同。一般灰铸铁= 0.5~1%; 铸钢=1.6%~2.0%;青铜=1.4%;铝合金=1.0%~1.2%。
(3)起模斜度 起模斜度是指为使模样容易从铸型中取出或型芯 自芯盒中脱出,平行于起模方向在模样或芯盒壁上的斜度。起模斜 度可用倾斜角表示或用起模斜度使铸件增加或减少的尺寸表示(图1 0 -2)。起模斜度一般为 = 50 ~ 30 。 (4)铸造圆角 制造模样时,凡相邻两表面的交角,都应做成圆 角(图 1 - 3 )。铸造圆角的作用是:造型方便;浇注时防止铸型夹 角被冲坏而引起铸件粘砂;防止铸件因夹角处应力集中而产生裂纹。
第一章 铸 造
§ 3- 1 概 述
一、铸造的特点
将熔融金属浇注、压射或吸人铸型型腔中,待其凝固后而得到一定形 状和性能铸件的方法称为铸造。 铸造所得到的金屑工件或毛坯称为铸件。 铸造具有以下优点: (1)可获得复杂外形及内腔的铸件,如各种箱体、床身、机架、汽缸 体等。 (2)铸件尺寸与重量几乎不受限制,小至几毫米、几克,大至十几米、 几百吨的铸件均可铸造。 (3)可铸造任何金属和合金铸件。 (4)铸件成本低廉。铸造用的原材料来源广泛,还可利用报废零件和 废金属材料,且生产设备较简单,投资少。 (5)铸件的形状、尺寸与零件很接近,因而减小了切削加工的工作量, 可节省大量金属材料。
( 1 )铸造生产工序繁多,工艺过程较难控制, 因此铸件易产生缺陷。