03_项目三__轮廓加工.pptx
合集下载
数控车床外轮廓加工课件
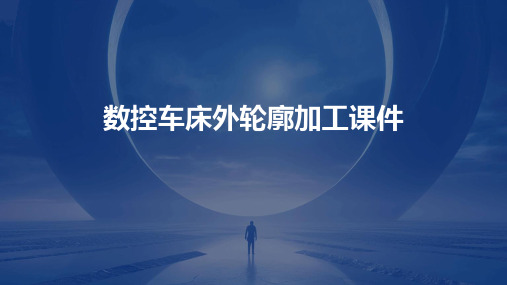
总结
数控车床在加工复杂外轮廓零件方面具有显著优势,可以大大提高生产效率和产品质量。
案例二:不锈钢零件的加工
总结词
材料硬度高、加工难度大
详细描述
该案例以一个不锈钢零件为例,说明了数控车床在加工高硬度材料方面的优越性。不锈钢的硬度较高,加工难度较大 ,需要使用特殊的刀具和加工参数。在数控车床上,通过精确控制刀具的速度和深度,可以实现对不锈钢的高效加工 。
加工效率高
数控车床可以连续进行加工,能够有效提高 生产效率。
技术含量高
数控车床需要专业的技术人员进行编程、操 作和维护,技术含量较高。
数控车床外轮廓加工的工艺流程
装夹
将工件固定在数控车床上,确 保工件位置准确、稳定。
加工
按照程序进行加工,注意控制 加工速度和进给速度。
编程
根据零件图纸和技术要求,编 写数控程序。
加工精度概述
数控车床外轮廓加工的精度是指加工后零件的实际几何参数与理想几何参数的符 合程度,包括尺寸精度、形状精度和位置精度。
影响因素分析
影响数控车床外轮廓加工精度的因素主要包括机床误差、刀具误差、夹具误差、 测量误差、工件误差等。
表面质量及影响因素
表面质量概述
数控车床外轮廓加工的表面质量是指加工后零件表面微观几何形状误差和物理力学性能的总和,包括表面粗糙度 、表面波纹度、表面加工硬化等。
冷却方式选择
根据加工要求和刀具材料选择合 适的冷却方式,如喷雾冷却、切
削液冷却等。
润滑方式选择
根据加工要求和工件材料选择合适 的润滑方式,如切削液润滑、固体 润滑等。
冷却润滑剂选用
根据加工要求和刀具、工件材料选 用合适的冷却润滑剂,如切削液、 润滑油等。
05
数控车床在加工复杂外轮廓零件方面具有显著优势,可以大大提高生产效率和产品质量。
案例二:不锈钢零件的加工
总结词
材料硬度高、加工难度大
详细描述
该案例以一个不锈钢零件为例,说明了数控车床在加工高硬度材料方面的优越性。不锈钢的硬度较高,加工难度较大 ,需要使用特殊的刀具和加工参数。在数控车床上,通过精确控制刀具的速度和深度,可以实现对不锈钢的高效加工 。
加工效率高
数控车床可以连续进行加工,能够有效提高 生产效率。
技术含量高
数控车床需要专业的技术人员进行编程、操 作和维护,技术含量较高。
数控车床外轮廓加工的工艺流程
装夹
将工件固定在数控车床上,确 保工件位置准确、稳定。
加工
按照程序进行加工,注意控制 加工速度和进给速度。
编程
根据零件图纸和技术要求,编 写数控程序。
加工精度概述
数控车床外轮廓加工的精度是指加工后零件的实际几何参数与理想几何参数的符 合程度,包括尺寸精度、形状精度和位置精度。
影响因素分析
影响数控车床外轮廓加工精度的因素主要包括机床误差、刀具误差、夹具误差、 测量误差、工件误差等。
表面质量及影响因素
表面质量概述
数控车床外轮廓加工的表面质量是指加工后零件表面微观几何形状误差和物理力学性能的总和,包括表面粗糙度 、表面波纹度、表面加工硬化等。
冷却方式选择
根据加工要求和刀具材料选择合 适的冷却方式,如喷雾冷却、切
削液冷却等。
润滑方式选择
根据加工要求和工件材料选择合适 的润滑方式,如切削液润滑、固体 润滑等。
冷却润滑剂选用
根据加工要求和刀具、工件材料选 用合适的冷却润滑剂,如切削液、 润滑油等。
05
项目三内轮廓的加工

3.内圆锥的检测方法
图3.18 内圆锥加工的轨迹示意图
任务实施 ◆ 工艺分析
1.零件几何特点
零件加工面主要为端面、内台阶、内 圆锥面和倒角。 尺寸如图3.17所示,棒料伸出卡盘长 度为10mm。
2.选择工具、量具和刀具
(1)工具选择。 (2)量具选择。 (3)刀具选择。 (4)粗、精车内圆锥面至尺寸。
4.常见的内圆检测方法
可采用内卡钳、游标卡尺、塞规和内 径百分表检测内圆,如图3.13所示。
图3.13 内圆的检测方法
用内径表测量时,要注意以下两方面。
(1)长指针和短指针应结合观察, 以防指针多转一圈。 (2)短指针位置基本符合,长指针 转动至“零”位线附近时,应防止 “+”、“−”数值搞错。
3.程序模拟加工 4.自动加工及尺寸控制
◆ 检测评分 零件加工结束后,检测结果按表3.5要 求填写。
◆ 任务反馈
(1)装夹钻头时,钻头轴心线和工 件轴心线要一致,否则钻头容易折断。 (2)在装夹钻头锪锥形套前,必须 把钻头锥柄、尾座套筒和锥形套擦拭 干净。否则会由于锥面接触不好,使 钻头在尾座锥孔内打滑旋转。
4.切削用量选择
内圆的加工工艺分析如表3.1所示。
◆ 加工操作
1.加工准备
(1)检查毛坯尺寸。 (2)开机、回参考点。 (3)装夹工件和刀具。 (4)程序输入。
2.对刀
(1)X方向对刀。 (2)Z方向对刀。
图3.15 内圆车刀对刀示意图
3.程序模拟加工 4.自动加工及尺寸控制
◆ 检测评分 零件加工结束后,检测结果按表3.2要 求填写。
图3.23 主偏角不同内圆弧面加工刀具示意图
2.内圆弧加工工艺设计技巧
图3.24 内腔轴向进刀加工示意图
项目三轮廓加工ppt

四、刀具半径补偿功能
为保证轮廓的加工精度和生产效率,要求粗加 工时尽量选择直径较大的铣刀进行铣削,便于 多余材料的快速去除;精加工则选择相对较小 直径的铣刀,从而保证轮廓的尺寸精度及表面 粗糙度。编写程序时,需考虑铣刀进刀与退刀 的位置,尽量选在轮廓的节点处或沿着轮廓的 切向进行;为简化程序,将轮廓铣削程序作为 子程序进行编写,通过给定不同的刀具半径补 偿,用于粗精加工中。
在进行数控编程时,都是根据刀具中心轨迹进 行编程。而在进行二维轮廓铣削时,由于刀具 存在一定的直径,使刀具中心轨迹与零件轮廓 不重合,如图3-7所示。
图3-7 刀具半径补偿功能
若不采用刀具半径自动补偿功能,编程员必须 依据图样尺寸要求结合刀具半径计算刀具中心 坐标位置,根据这个坐标进行编程。如果运用 进给控制指令,结合刀具补偿功能加工如图 3-7所示的外形轮廓零件时,刀具中心坐标计 算工作就可以省去,编程时直接按照工件轮廓 尺寸进行编程即可。
图3-3 内圆铣削
图3-4有交点内轮廓加工刀具的切入切出
2、铣削封闭的内轮廓表面
铣削封闭的内轮廓表面时,若内轮廓曲线允许 外延,则应沿切线方向切入切出。
铣削封闭的内轮廓表面时,若内轮廓曲线不允 许外延,则刀具只能沿内轮廓曲线的法向切入 切出,并将其切入、切出点选在零件轮廓两几 何元素的交点处,如图3-4所示。
(a)人工预刀补编程
(b)刀具半径补偿的功能
图3-8 人工预刀补编程
在加工运行时,控制系统将根据程序中的刀补 指令自动进行相应的刀具偏置,确保刀具切削 出符合要求的轮廓。
利用机床自动进行刀补计算的方法,可大大简 化计算及编程工作,并且还可以利用同一个程 序、同一把刀具,通过设置不同大小的刀具半 径偏置值而逐步减少切削余量的方法来达到粗、 精加工的目的,如图3-9 所示。
数控铣工实训课件-轮廓加工

图4-1-4
轮廓加工
4.1.2任务实施
一、工艺分析
1.技术要求分析 该零件为模具镶件,其120*120尺寸及公差由坯料制造时保证。成 形部分即台阶尺寸精度要求较高,且成形尺寸只许正差,这是为后续 工序钳工修正和抛光留量。因此,在编程、加工或机床调整时保证本 工序加工出工件的最大极限尺寸 2.确定加工方案 工件的铣削过程分为三个阶段进行,即加工工艺路线为:粗铣——半 精铣——精铣。
第 8 / 30页
轮廓加工
2.坐标系的确定 编程时选择G54作为工件坐标系,坐标系原点设在工件上 表面几何中心处,即,Φ80圆台圆心。如图4-1-5 b所示。 3.数值计算 由确定的进给路线可知,以刀具中心为基准按轮廓编程, 起刀点均设在X-120.0,Y-120.0,Z100.0处。则三个铣削 过程在XY平面内的有关节点计算如下: 铣平面:行切,每刀沿X方向的切削宽度设为20mm。 切入点坐标:X-40.0 -X=60.0-20.0=40.0
第 18 / 30页
轮廓加工
2.刀具长度补偿指令G43、G44、G49
G43、G44指令是指令机床数控系统在刀具长度的方向的坐标轴上加一个刀 具长度差值或减一个刀具长度差值,编程时使用G43、G44指令必须与具有 直线运动指令配合使用,G43、G44指令才能有效。 指令编程格式: (G17/G18/G19) G01/G00 G43 X Y Z H ; (G17/G18/G19) G01/G00 G44 X Y Z H ; 在G17后的刀具长度补偿指令,只能将刀具长度的补偿值补偿到Z轴。 在G18后的刀具长度补偿指令,只能将刀具长度的补偿值补偿到Y轴。 在G19后的刀具长度补偿指令,只能将刀具长度的补偿值补偿到X轴。
精铣方台轮廓;
轮廓加工
4.1.2任务实施
一、工艺分析
1.技术要求分析 该零件为模具镶件,其120*120尺寸及公差由坯料制造时保证。成 形部分即台阶尺寸精度要求较高,且成形尺寸只许正差,这是为后续 工序钳工修正和抛光留量。因此,在编程、加工或机床调整时保证本 工序加工出工件的最大极限尺寸 2.确定加工方案 工件的铣削过程分为三个阶段进行,即加工工艺路线为:粗铣——半 精铣——精铣。
第 8 / 30页
轮廓加工
2.坐标系的确定 编程时选择G54作为工件坐标系,坐标系原点设在工件上 表面几何中心处,即,Φ80圆台圆心。如图4-1-5 b所示。 3.数值计算 由确定的进给路线可知,以刀具中心为基准按轮廓编程, 起刀点均设在X-120.0,Y-120.0,Z100.0处。则三个铣削 过程在XY平面内的有关节点计算如下: 铣平面:行切,每刀沿X方向的切削宽度设为20mm。 切入点坐标:X-40.0 -X=60.0-20.0=40.0
第 18 / 30页
轮廓加工
2.刀具长度补偿指令G43、G44、G49
G43、G44指令是指令机床数控系统在刀具长度的方向的坐标轴上加一个刀 具长度差值或减一个刀具长度差值,编程时使用G43、G44指令必须与具有 直线运动指令配合使用,G43、G44指令才能有效。 指令编程格式: (G17/G18/G19) G01/G00 G43 X Y Z H ; (G17/G18/G19) G01/G00 G44 X Y Z H ; 在G17后的刀具长度补偿指令,只能将刀具长度的补偿值补偿到Z轴。 在G18后的刀具长度补偿指令,只能将刀具长度的补偿值补偿到Y轴。 在G19后的刀具长度补偿指令,只能将刀具长度的补偿值补偿到X轴。
精铣方台轮廓;
中职教育-加工中心操作项目训练教程:项目三 加工二维内轮廓训练(一).ppt

高等教育出版社
Higher Education Press
高等教育出版社
Higher Education Press
O17 G40 G80;
N3 G90 G54 G00 X0 Y0 S300 M03;
(从参考点到X、Y向起点,启动主轴)
N4 G43 Z20 H01 M08;
(从参考点到Z向安全高度,建立长度补偿)
高等教育出版社
Higher Education Press
子程序和主程序的区别是:主程序结束标记是用M30或 M02表示程序结束,而子程序的结束标记则是使用M99结 束,并返回主程序,子程序在使用过程中还可以让子程 序调用另外的子程序,这种功能叫子程序嵌套,如3-2所 示。这样在应用当中可以大大简化程序。在FANUC0i系统, 一般可以嵌套四级。
高等教育出版社
Higher Education Press
【学习目标】
二、技能目标 1.熟练掌握机床的操作,能快速进行程序的编制、模 拟仿真和加工。 2.能正确运用工量具,掌握测量的方式方法,保证高 的测量精度。。
高等教育出版社
Higher Education Press
【项目简介】
如图3-1所示,零件材料为硬铝,切削性能较好,加工部分由内轮廓 构成,厚度为20mm,零件毛坯为100 mm×100 mm的方料,12课时。
高等教育出版社
Higher Education Press
【相关知识】
一、子程序 在一个加工程序中,如果其中有些加工内容完全相同或 相似,为了简化程序,可以把这些重复的程序段单独列 出,并按一定的格式编写成子程序。主程序在执行过程 中如果需要某一子程序,通过调用指令来调用该子程序, 子程序执行完后又返回到主程序,继续执行后面的程序 段。
Higher Education Press
高等教育出版社
Higher Education Press
O17 G40 G80;
N3 G90 G54 G00 X0 Y0 S300 M03;
(从参考点到X、Y向起点,启动主轴)
N4 G43 Z20 H01 M08;
(从参考点到Z向安全高度,建立长度补偿)
高等教育出版社
Higher Education Press
子程序和主程序的区别是:主程序结束标记是用M30或 M02表示程序结束,而子程序的结束标记则是使用M99结 束,并返回主程序,子程序在使用过程中还可以让子程 序调用另外的子程序,这种功能叫子程序嵌套,如3-2所 示。这样在应用当中可以大大简化程序。在FANUC0i系统, 一般可以嵌套四级。
高等教育出版社
Higher Education Press
【学习目标】
二、技能目标 1.熟练掌握机床的操作,能快速进行程序的编制、模 拟仿真和加工。 2.能正确运用工量具,掌握测量的方式方法,保证高 的测量精度。。
高等教育出版社
Higher Education Press
【项目简介】
如图3-1所示,零件材料为硬铝,切削性能较好,加工部分由内轮廓 构成,厚度为20mm,零件毛坯为100 mm×100 mm的方料,12课时。
高等教育出版社
Higher Education Press
【相关知识】
一、子程序 在一个加工程序中,如果其中有些加工内容完全相同或 相似,为了简化程序,可以把这些重复的程序段单独列 出,并按一定的格式编写成子程序。主程序在执行过程 中如果需要某一子程序,通过调用指令来调用该子程序, 子程序执行完后又返回到主程序,继续执行后面的程序 段。
项目三:轮廓铣削加工
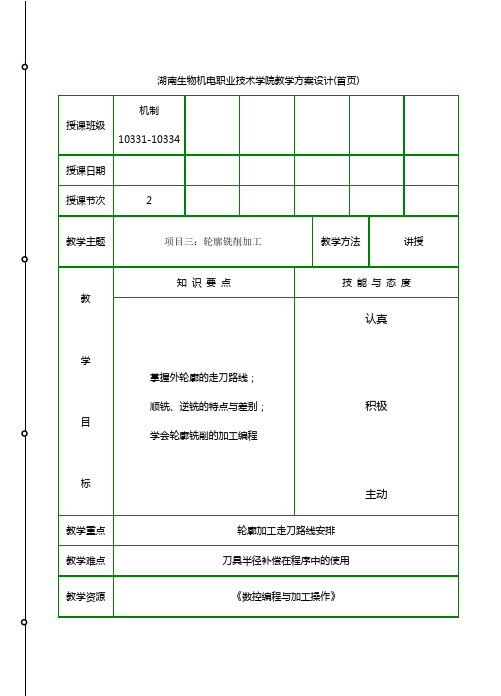
④ 在刀补建立或取消时,注意由于程序轨迹方向不当而发生过切。
⑤ 当刀补数据为负值时,则G41、G42功效互换。
⑥G41、G42指令不要重复规定,否则会产生一种特殊的补偿。
⑦G40、G41、G42都是模态代码,可相互注销。
(5)刀具半径补偿应用实例
已知某零件如下图所示,工件材料为5mm厚的铝板,编写工件精加工程序。加工刀具:直径φ10的立铣刀;安全高度10mm;切削用量:主轴转速600r/min,进给速度300mm/min;采用顺铣,上平面为Z0。
产品名称
零件名称
材料
零件图号
工序号
程序编号
夹具名称
夹具编号
设备名称
编制
审核
工步号
工步内容
刀具号
刀具规格
主轴转速
/(r/min)
进给速度
/(mm/min)
背吃刀量
/mm
1
粗铣高度为16mm凸台
T01
Φ20mm
立铣刀
320
80
4
2
粗铣高度为8mm凸台
T01
Φ20mm
立铣刀
320
80
4
3
精铣高度为8mm凸台
教学资源
《数控编程与加工操作》
教学后记
任课教师
曹新明
教研室主任或课程负责人
廉良冲
湖南生物机电职业技术学院教学方案设计
教学步骤、内容与时间分配
重点、难点诠释或分解目标等
项目3轮廓铣削加工
3.2.1轮廓铣削的工艺知识
1.轮廓铣削的走刀路线
当铣削平面零件轮廓时,一般采用立铣刀侧刃切削。刀具切入工件时,应避免沿零件轮廓的法向切入,而应沿外轮廓曲线延长线的切向切入,以避免在切入处产生刀具的切痕而影响表面质量,保证零件外轮廓曲线平滑过渡。同理,在切出工件时,也应避免在零件的轮廓处直接退刀,而应沿零件轮廓延长线的切向逐渐切离工件。
⑤ 当刀补数据为负值时,则G41、G42功效互换。
⑥G41、G42指令不要重复规定,否则会产生一种特殊的补偿。
⑦G40、G41、G42都是模态代码,可相互注销。
(5)刀具半径补偿应用实例
已知某零件如下图所示,工件材料为5mm厚的铝板,编写工件精加工程序。加工刀具:直径φ10的立铣刀;安全高度10mm;切削用量:主轴转速600r/min,进给速度300mm/min;采用顺铣,上平面为Z0。
产品名称
零件名称
材料
零件图号
工序号
程序编号
夹具名称
夹具编号
设备名称
编制
审核
工步号
工步内容
刀具号
刀具规格
主轴转速
/(r/min)
进给速度
/(mm/min)
背吃刀量
/mm
1
粗铣高度为16mm凸台
T01
Φ20mm
立铣刀
320
80
4
2
粗铣高度为8mm凸台
T01
Φ20mm
立铣刀
320
80
4
3
精铣高度为8mm凸台
教学资源
《数控编程与加工操作》
教学后记
任课教师
曹新明
教研室主任或课程负责人
廉良冲
湖南生物机电职业技术学院教学方案设计
教学步骤、内容与时间分配
重点、难点诠释或分解目标等
项目3轮廓铣削加工
3.2.1轮廓铣削的工艺知识
1.轮廓铣削的走刀路线
当铣削平面零件轮廓时,一般采用立铣刀侧刃切削。刀具切入工件时,应避免沿零件轮廓的法向切入,而应沿外轮廓曲线延长线的切向切入,以避免在切入处产生刀具的切痕而影响表面质量,保证零件外轮廓曲线平滑过渡。同理,在切出工件时,也应避免在零件的轮廓处直接退刀,而应沿零件轮廓延长线的切向逐渐切离工件。
中职教育-加工中心操作项目训练教程:项目三 加工二维内轮廓训练(二).ppt

粗铣内轮廓
T4
φ12
2300
100
10
4
精铣内轮廓
T4
φ12
3200
320
0.5
注意事项:①起动机床回零后,检查机床零点位置是否正 确。
②正确操作机床,注意安全,文明生产。
高等教育出版社
Higher Education Press
表3-2 数控加工刀具及其补偿
编号
刀具名称
刀具规格 数量 用途
刀具材料
高等教育出版社
Higher Education Press
【项目评价】
表3-4评分表
高等教育出版社
Higher Education Press
时限 2h
开始时间
考核项目 序号
坚定内容
1 100(2处)
2 32
3 Ø 50
4 48工件评分 5 Nhomakorabea73
(80)
6
29
7 R8(2处)
8 20
9 平行度
10 MRR Ra3.2(6处)
程序不完整扣5~20
否定项 (扣分
)
不规范每次扣2 误操作每次扣2 不合理每次扣2 不符合要求每次扣2
否定项 (扣分
)
扣2~10/次
否定项 (扣分
)
扣5~20/次
扣分
【知识拓展】
坐标系旋转 对于某些围绕中心旋转得到的特殊的轮廓加工,如
果根据旋转后的实际加工轨迹进行编程,就可能使坐标 计算的工作量大大增加,而通过图形旋转功能,可以大 大简化编程的工作量。
⑤准备刀具。共使用3把刀具,安装时要严格按照步骤执行, 并要检查刀具安装的牢固 程度。
高等教育出版社
零件外轮廓加工ppt课件
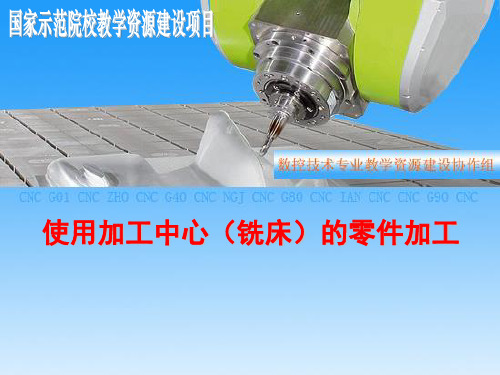
指令格式:
刀具半径补偿的建立:
X Y __ X Z __ Y Z __
D __
刀具补偿起刀时必须为G00或G01 左、右刀补的设置
刀具半径补偿(G41、G42、G40 Z __ Y Z __
刀具半径补偿(G41、G42、G40)
(1)刀补的建立
当刀具从起点接近工件时, 刀具中心从与编程轨迹重合 过渡到与编程轨迹偏离一个 偏置量的过程。 如图,OA段 为建立刀补段, 必须用直线 G01编程,示例程序段如下: G41G01X50.0Y40.0F100 D01;
G00 Z50. M9; G28 G91 Z0; G28 G91 X0 Y0;
M30; %
程序结束。
加工中心(铣)的编程基础
注意! 1.工件坐标系在编制加工程序时使用。 2.不同工件的工件坐标系不同。 3.工件坐标系是建立在机床坐标系中的。
轮廓零件的数控铣削加工
5、加工实施:
(1)输入并校验各程序。 (2)设定工件坐标系及各刀长补正。 (3)保持机床正常状态开始加工。 (4)注意观察加工过程中的现象和声音。
#2=2; WHILE [#2 LE 6] DO2;
G1 Z-#2 F150; #3=1;
WHILE [#3 LE 2] DO3; G1 G41 X20. Y-50. F200
D#3; G3 X0 Y-30. R20.;
G1 X-27.; G2 X-32.Y-16.R8.; G3 X-32.Y16. R20; G2 X-27.Y30. R8.;
2.可使粗加工的程序简化,如 图,通过有意识地改变刀具半 径补偿量,则可以用同一把刀 具、同一程序、不同的切削余 量完成切削。
刀具
工件
刀具半径补偿(G41、G42、G40)
03课件-单元三——零件的内轮廓加工

程序号 公制单位设定\设定G54作为加工坐标 工作平面设定\取消半径补偿\取消长度补偿\取消
固定循环\绝对坐标设定 直线快速移动\主轴正转 Z轴直线快速移动至安全平面 \开启切削液 变量初始值 WHILE循环语句条件设置
建立半径补偿D01=4.5 轮廓起始
N130 G2 X30. Y-5. R5.; N132 G3 X5. Y-30. R25.; N134 G2 X-5. Y-30. R5.; N136 G3 X-12.322 Y-12.322 R25.;
(1)、分析图纸,指导制订加工工艺;
(2)、根据工艺编写加工程序;
(3)、指导工件、刀具的装夹、对刀和工件坐标系的 确定;
(4)、程序的输入、调试;
(5)、指导零件的检验,评价方法。
(1) 分析图纸,指导制订加工工艺;
根据内轮廓1的零件特点,外轮廓使用¢20平铣刀进行 加工,内轮廓使用¢8平铣刀进行加工。粗加工需要分 层铣削,并且在零件轮廓的周边及底面留有精加工余量 。精加工在提高切削进给速度的同时,根据实际测量值 确定精加工的刀具半径补偿。在刀具的切削过程中,注 意首切时降低刀具进给速度。
O0004; N100 G21 G54; N102 G17 G40 G49 G80 G90;
N104 G00 X0 Y0.S1000 M03; N106 Z20.; N108 M08; N110 #1=1; N112 WHILE [#1 LE 3] DO1; N114 G1 Z-#1 F150; N116 G42 G1 Y-13.74 F200 D1; N118 G02 X-12.322 Y-12.322 R10.; N120 G03 X-30. Y-5. R25.; N122 G02 X-30. Y5. R5.; N124 G3 X-5. Y30. R25.; N126 G2 X5. Y30. R5.; N128 G3 X30. Y5. R25.;
数控铣床加工中心加工工艺编程与操作轮廓型腔类零件加工PPT课件

半精铣台阶面 精铣台阶面
刀具号
T01
T02 T02 T02 T02
使用设备 主轴转速 n(r/min
)
650 800 800 800 1000
夹具名称 机用虎钳
进给速度 f(mm/min)
切削深 度 ap(
mm)
80
1
100
3
100
3
100
3
80
1
任务1 平面加工
2、程序编制
O1; G90 G54 G40 G21 F100; M03 S800; G00 X-20. Y-20.; G00 Z10.; G01 Z0.; G91 G01 Z-5. F50; M00; G91 G01 X11. F100; Y100.; X9.; Y-100.; X-20.; M30;
式按指定的进给速度作任意斜率的直线运动。
格式:G01 X- Y- Z- F-;
式中X、Y、Z与G00相同,F表示进给速度。
注意:
①G01只能为直线轨迹。
②G01之前必须有F定速度。
任务1 平面加工
例题讲解
绝对(O-A-B-C)
G90 G00 X10. Y10.;(A) G00 X20. Y20.;(A-B) G00 X20. Y30.;(B-C)
(2)刀心轨迹与工件边缘重合——刀齿冲击大,易蹦刃 (3)刀心轨迹在工件边缘外——冲击大,易破损或产生缺口 (4)刀心轨迹在工件边缘与中心线间——最合适
注意:刀心在工件内时铣刀直径选择要适当,避免全齿切削。
任务1 平面加工
5、平面铣削用量
粗加工:刚性、功率、效率
精加工:精度
6、大平面铣削时的走刀路线
注意:
①G00移动速度由参数定。 ②G00有两种轨迹,直线型和折线形。 直线型:各轴移动速度不同,但同时到达终点。 折线形:各轴移动速度相同,不能同时到达终点。 (注意撞刀) ③G00应留有安全余量。
刀具号
T01
T02 T02 T02 T02
使用设备 主轴转速 n(r/min
)
650 800 800 800 1000
夹具名称 机用虎钳
进给速度 f(mm/min)
切削深 度 ap(
mm)
80
1
100
3
100
3
100
3
80
1
任务1 平面加工
2、程序编制
O1; G90 G54 G40 G21 F100; M03 S800; G00 X-20. Y-20.; G00 Z10.; G01 Z0.; G91 G01 Z-5. F50; M00; G91 G01 X11. F100; Y100.; X9.; Y-100.; X-20.; M30;
式按指定的进给速度作任意斜率的直线运动。
格式:G01 X- Y- Z- F-;
式中X、Y、Z与G00相同,F表示进给速度。
注意:
①G01只能为直线轨迹。
②G01之前必须有F定速度。
任务1 平面加工
例题讲解
绝对(O-A-B-C)
G90 G00 X10. Y10.;(A) G00 X20. Y20.;(A-B) G00 X20. Y30.;(B-C)
(2)刀心轨迹与工件边缘重合——刀齿冲击大,易蹦刃 (3)刀心轨迹在工件边缘外——冲击大,易破损或产生缺口 (4)刀心轨迹在工件边缘与中心线间——最合适
注意:刀心在工件内时铣刀直径选择要适当,避免全齿切削。
任务1 平面加工
5、平面铣削用量
粗加工:刚性、功率、效率
精加工:精度
6、大平面铣削时的走刀路线
注意:
①G00移动速度由参数定。 ②G00有两种轨迹,直线型和折线形。 直线型:各轴移动速度不同,但同时到达终点。 折线形:各轴移动速度相同,不能同时到达终点。 (注意撞刀) ③G00应留有安全余量。
《复合轮廓的加工》说课课件
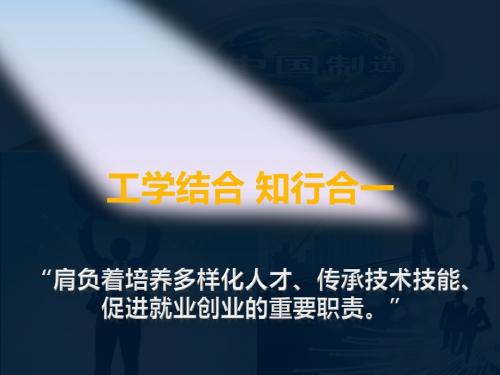
PART 5
教学反思
浙江省中等职业学校教师 “创新杯”说课大赛
设计意图:实现空间结合 验证工艺正确 提高教学实效 符合中职特点
浙江省中等职业学校教师 “创新杯”说课大赛
谢 谢 大 家!
2015-6-14
说明:请同学们结合任务的实施情况,完成任务评价的内容 设计意图: 充分体验成功的快乐与满足
发放聘用书
任务评价
浙江省中等职业学校教师 “创新杯”说课大赛
课前
表扬
课中
指出不足
课后
鼓励
设计意图: 学生真正成为教学主体
任务拓展
浙江省中等职业学校教师 “创新杯”说课大赛
思考:能否根据轮廓特点, 用其他方法简化程序?
各个击破 “做中教,做中学”
课前准备
浙江省中等职业学校教师 “创新杯”说课大赛
设计意图: 扫描二维码 学习微视频 复习预习
课前准备
浙江省中等职业学校教师 “创新杯”说课大赛
数控铣床 6 台 计算机 6台
(预装宇龙仿真系统)
任务书及游标卡尺等工量具 多媒体 课件 微课视频
游戏激趣
浙江省中等职业学校教师 “创新杯”说课大赛
教材选用
浙江省中等职业学校教师 “创新杯”说课大赛
项目四 平面轮廓的加工
目录
XXX XXX XXX
任务三 复合轮廓的加工 (3课时)
作用地位
浙江省中等职业学校教师 “创新杯”说课大赛
外轮廓 加工
型腔的 加工
复合轮 廓加工
学情分析
浙江省中等职业学校教师 “创新杯”说课大赛
热情爱表现 自制力不够
思维活跃 热爱 新鲜事物 任性 乐于动手探究 初步具备加工 工艺基础知识
第四章轮廓加工的数学基础演示文档
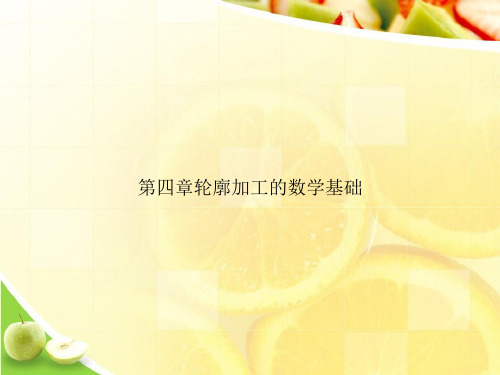
▪ 逐点比较法既可作为直线插补,又可作圆弧插补。这种算法的特点 是:运算直观,插补误差小于一个脉冲当量,输出脉冲均匀,而且 输出脉冲的速度变化小,调节方便。因此,在两坐标联动的数控机 床中应用较为广泛。
1.直线插补 (1)偏差计算 第一象限直线OE,起点O为坐标原点,直线的终点坐标 E(Xe,Ye),直线方程为:
(3)终点判断
判别方法: 设置一个长度计数器, 刀具沿X轴应走的步数为X e ,沿Y 轴走的步数为Ye ,计数器中存入X和Y两坐标进给步数总和∑=∣Xe∣+ ∣Ye∣,当X或Y坐标进给时,计数器做减1运算,当计数器减到零时,即∑=
0时,到达终点,停止插补 .
(4)直线插补软件流程图
开始
Xe , Ye , F←0, Σ=∣Xe∣+ ∣Ye ∣
F >0时,表示刀具在OE上方,如点P1,应向+X向进给. F <0时,表示刀具在OE下方,如点P2,应向+Y向进给.
这里将F =0的情况归入F >0的情况一同考虑. 下面将F 的运算采用递推算法予以简化,动点 Pi(Xi,Yi)的Fi值为
Fi YiXeXiYe
若Fi≥0,表明Pi(Xi,Yi)点在OE直线上方或在直线上,应沿+X 向 走一步,假设坐标值的单位为脉冲当量,进给后新的坐标值为(Xi+1, Yi+1),且Xi+1=Xi+1,Yi+1=Yi , 新点偏差为:
插补时间采用12ms、8ms、4ms、2ms等,对于运行速度较快的计 算机,有的选用的更小。插补时间越短,机床的进给速度越快。现代 数据机床的进给速度已超过15m/min~30m/min,有些达到60m/min。 它适用于直流伺服电动机和交流伺服电动机的闭环或半闭环控制系统。
第四章轮廓加工的数学基础幻灯片

插补时间采用12ms、8ms、4ms、2ms等,对于运行速度较快的计 算机,有的选用的更小。插补时间越短,机床的进给速度越快。现代 数据机床的进给速度已超过15m/min~30m/min,有些达到60m/min。 它适用于直流伺服电动机和交流伺服电动机的闭环或半闭环控制系统。
第二节 脉冲增量插补
脉冲增量插补就是分配脉冲的计算,在插补过得中不断向各坐标轴 发出相互协调的进给脉冲,控制机床坐标作相应的移动。
(3)终点判断
判别方法: 设置一个长度计数器, 刀具沿X轴应走的步数为X e ,沿Y 轴走的步数为Ye ,计数器中存入X和Y两坐标进给步数总和∑=∣Xe∣+ ∣Ye∣,当X或Y坐标进给时,计数器做减1运算,当计数器减到零时,即∑=
0时,到达终点,停止插补 .
(4)直线插补软件流程图
开始
Xe , Ye , F←0, Σ=∣Xe∣+ ∣Ye ∣
主要介绍: 逐点比较法 数字积分法
一、逐点比较法插补原理
基本原理:数控装置在控制刀具按要求的轨迹移动过程中,不断比 较刀具与给定轮廓误差,由此误差决定下一步刀具移动方向,使刀 具向减少误差的方向移动,且只有一个方向移动。
一、逐点比较法插补原理
逐点比较法插补过程可按以下4个步骤(节拍)进行:
第1节拍:偏差判别: 判别刀具当前位置相对给定
▪ 逐点比较法既可作为直线插补,又可作圆弧插补。这种算法的特点 是:运算直观,插补误差小于一个脉冲当量,输出脉冲均匀,而且 输出脉冲的速度变化小,调节方便。因此,在两坐标联动的数控机 床中应用较为广泛。
1.直线插补 (1)偏差计算 第一象限直线OE,起点O为坐标原点,直线的终点坐标 E(Xe,Ye),直线方程为:
YXe-XYe=0
第二节 脉冲增量插补
脉冲增量插补就是分配脉冲的计算,在插补过得中不断向各坐标轴 发出相互协调的进给脉冲,控制机床坐标作相应的移动。
(3)终点判断
判别方法: 设置一个长度计数器, 刀具沿X轴应走的步数为X e ,沿Y 轴走的步数为Ye ,计数器中存入X和Y两坐标进给步数总和∑=∣Xe∣+ ∣Ye∣,当X或Y坐标进给时,计数器做减1运算,当计数器减到零时,即∑=
0时,到达终点,停止插补 .
(4)直线插补软件流程图
开始
Xe , Ye , F←0, Σ=∣Xe∣+ ∣Ye ∣
主要介绍: 逐点比较法 数字积分法
一、逐点比较法插补原理
基本原理:数控装置在控制刀具按要求的轨迹移动过程中,不断比 较刀具与给定轮廓误差,由此误差决定下一步刀具移动方向,使刀 具向减少误差的方向移动,且只有一个方向移动。
一、逐点比较法插补原理
逐点比较法插补过程可按以下4个步骤(节拍)进行:
第1节拍:偏差判别: 判别刀具当前位置相对给定
▪ 逐点比较法既可作为直线插补,又可作圆弧插补。这种算法的特点 是:运算直观,插补误差小于一个脉冲当量,输出脉冲均匀,而且 输出脉冲的速度变化小,调节方便。因此,在两坐标联动的数控机 床中应用较为广泛。
1.直线插补 (1)偏差计算 第一象限直线OE,起点O为坐标原点,直线的终点坐标 E(Xe,Ye),直线方程为:
YXe-XYe=0
- 1、下载文档前请自行甄别文档内容的完整性,平台不提供额外的编辑、内容补充、找答案等附加服务。
- 2、"仅部分预览"的文档,不可在线预览部分如存在完整性等问题,可反馈申请退款(可完整预览的文档不适用该条件!)。
- 3、如文档侵犯您的权益,请联系客服反馈,我们会尽快为您处理(人工客服工作时间:9:00-18:30)。
四、手工编程中基点的计算
12
任务一 【知识准备】
五、指令介绍
1.圆弧插补 (1)圆弧程序的一般书写格式 (2)通过中间点进行圆弧插补 (3)切线和过渡圆弧 2.圆弧进给率修正
13
任务一 【知识准备】
六、刀具半径补偿
1.刀位点
2.刀具补偿功能的概念 (1)刀具半径补偿定义 (2)刀具半径补偿指令 (3)刀具半径补偿过程 (4)刀具半径补偿注意事项
一、数控铣削加工工序的划分
1.加工阶段 (1)粗加工阶段 (2)半精加工阶段 (3)精加工阶段 (4)光整加工阶段
2.数控铣削加工工序的划分原则 (1)按所用刀具划分 (2)按安装次数划分 (3)按粗、精加工划分 (4)按加工部位划分
9
任务一 【知识准备】
3.工步的划分 4.数控铣削加工顺序的安排
(1)基面先行原则 (2)先粗后精原则 (3)先主后次原则 (4)先面后孔原则 5.数控加工工序与普通工序的衔接
平口钳
10
任务一 【知识准备】
二、铣削内外轮廓的进给路线
三、数控加工工艺文件
1.数控加工编程任务书 2.工序卡 3.工件安装和零点设定卡 4.数控加工进给路线图 5.数控加工程序单
11
任务一 【知识准备】
4
任务一 外轮廓加工
技能目标
任务描述
知识准备 任务实施
拓展训练
5
任务一 【任务描述】
图示零件,轮廓较为复杂,如果直接计算刀具刀位点的轨迹进行编程, 则计算复杂,容易出错,编程效率低,而采用刀具半径补偿方式进行编程,则较 为简便。零件毛坯为80mm×80mm×20mm的45钢,四周与上下表面已经加工好了, 只进行外轮廓加工。。
14
任务一 【知识准备】
3.刀具补偿D (1)编程举例 (2)补偿存储器的 (3)刀具半径补偿中的几个特殊情况 4.拐角特性 5.刀具半径补偿编程示例
15
任务一 【知识准备】
七、循环
1.轮廓铣削CYCLE72
(1)功能
1)循环运行可选择使用或不使用刀具半径补偿。
2)轮廓可以封闭也可以不封闭.
3)轮廓的定义方向必须是它的加工方向
31
任务二 【任务实施】
● 加工准备 ● 编写加工程序 ● 能熟练运用刀具半径补偿进行编程 ● 了解数控铣削加工阶段的划分方法
32
任务二 【任务实施】
◆加工准备 1.选择数控机床 本任务选用的机床为TK7650型SIEMENS802D系统数控铣床。 2.选择刀具及切削用量 加工本任务工件时,选择如图3.58所示键槽铣刀(Z向垂直进刀)或立铣刀(Z 向螺旋线进刀)进行加工,根据内轮廓的形状,选择刀具直径为φ16mm。切削 用量推荐值如下:主轴转速n=500~700 r/min;XY平面内进给速度取f=100~ 200 mm/min,Z向进给速度取f=50~100 mm/min;背吃刀量的取值等于型腔高 度,取ap=8 mm。
2.矩形外轮廓(凸台)铣削
18
任务一 【知识准备】
3.圆形凸台铣削
19
任务一 【任务实施】★加工源自备★工件检验★
检测评分
★
任务反馈
20
任务一 【任务实施】
◆加工准备
1.材料准备 2.设备准备 3.量具与刀具 4.识读零件图 5.工艺分析 6.程序编制
21
任务一 【任务实施】
◆工件检验
1.长度尺寸测量 2.圆弧的测量 3.表面粗糙度的测量
28
任务二 【知识准备】
2.平面切削
29
任务二 【知识准备】
二、螺旋类加工
30
任务二 【知识准备】
图示螺旋槽由两个螺旋面组成,前半圆AmB为左旋螺旋面,后 半圆AnB右旋螺旋面。螺旋槽最深处为A点,最浅处为B点。要求用 φ8mm的立铣刀进行加工该螺旋槽,编制数控加工程序。刀具半径 补偿号为D01,长度补偿号为D01。
项目三 轮廓加工
典型平面
二维轮廓零件 a)齿轮 b)链轮 c)凸轮 d)离合器 e)花键轴
2
典型平面
3
学习目标
● 掌握数控铣床/加工中心铣削轮廓的工艺设计 ● 掌握数控铣床/加工中心铣削外轮廓的方法 ● 掌握数控铣床/加工中心铣削内轮廓的方法 ● 掌握数控铣床/加工中心铣削复杂轮廓的方法 ● 掌握数控铣床/加工中心铣削轮廓的编程方法
◆检测评分 ◆任务反馈——造成尺寸精度降低的常见原因
22
任务一 【拓展训练 】
1.试简要叙述刀具半径补偿的过程。 2.采用刀具半径补偿编程时,应注意哪些问题? 3.试采用刀具半径补偿指令编写
23
任务二 内轮廓铣削
技能目标
任务描述
知识准备 任务实施
拓展训练
24
任务二 【任务描述】
图示零件,为封闭内轮廓。因此,如何进行刀具的Z向进给是加 工本工件的关键。另外,对于侧面轮廓,需将工件竖起来重新装夹校正 后再进行加工。该零件的毛坯为100mm×100mm×20mm的45钢。
4)循环可选择粗加工或精加工
(2)刀具动作顺序
1)粗加工时循环形成以下动作顺序
2)精加工时循环形成以下动作顺序
(3)参数说明
1)KNAME(名称)
2)LP1、LP2(长度、半径)
3)AS1、AS2(接近方向/路径,.返回方向/返回路径)
4)FF3(返回进给倍率)
16
任务一 【知识准备】
17
任务一 【知识准备】
任务二 【技能目标】
★
★
★
掌握内轮廓铣 削的编程方法
掌握内轮廓铣 削时刀具的进 刀方式
掌握内轮廓铣 削的加工工艺 的设计方法
26
任务二【知识准备】
一
内轮廓的加工工艺
二
螺旋类加工
三
子程序
27
任务二 【知识准备】
一、内轮廓的加工工艺
1.加工内轮廓时的Z向进刀方式 (1)垂直切深进刀 (2)在工艺孔中进刀 (3)三轴联动斜线进刀 (4)三轴联动螺旋线进刀
6
任务一 【技能目标】
● 掌握外轮廓铣削的编程方法 ● 掌握刀具半径补偿的基本概念 ● 能熟练运用刀具半径补偿进行编程 ● 了解数控铣削加工阶段的划分方法
7
任务一【知识准备】
一
数控铣削加工工序的划分
二
铣削内外轮廓的进给路线
三
数控加工工艺文件
四
手工编程中基点的计算
五
指令介绍
六
刀具半径补偿
七
循环
8
任务一 【知识准备】
33
任务二 【任务实施】
◆编写加工程序 1.设计加工路线 2.分析基点坐标 3.编制加工程序
34
任务二 【任务实施】
◆任务反馈——轮廓加工精度及误差分析
轮廓铣削精度主要包括尺寸精度、形状和位置精度及表面粗糙度。数控铣削加工过程中产生精度降 低的原因是多方面的,在实际加工过程中,造成形状和位置精度降低的常见原因见表3.20,造成表 面粗糙度降低的常见原因见表3.21。 表3.20 数控铣形位精度误差降低原因分析
12
任务一 【知识准备】
五、指令介绍
1.圆弧插补 (1)圆弧程序的一般书写格式 (2)通过中间点进行圆弧插补 (3)切线和过渡圆弧 2.圆弧进给率修正
13
任务一 【知识准备】
六、刀具半径补偿
1.刀位点
2.刀具补偿功能的概念 (1)刀具半径补偿定义 (2)刀具半径补偿指令 (3)刀具半径补偿过程 (4)刀具半径补偿注意事项
一、数控铣削加工工序的划分
1.加工阶段 (1)粗加工阶段 (2)半精加工阶段 (3)精加工阶段 (4)光整加工阶段
2.数控铣削加工工序的划分原则 (1)按所用刀具划分 (2)按安装次数划分 (3)按粗、精加工划分 (4)按加工部位划分
9
任务一 【知识准备】
3.工步的划分 4.数控铣削加工顺序的安排
(1)基面先行原则 (2)先粗后精原则 (3)先主后次原则 (4)先面后孔原则 5.数控加工工序与普通工序的衔接
平口钳
10
任务一 【知识准备】
二、铣削内外轮廓的进给路线
三、数控加工工艺文件
1.数控加工编程任务书 2.工序卡 3.工件安装和零点设定卡 4.数控加工进给路线图 5.数控加工程序单
11
任务一 【知识准备】
4
任务一 外轮廓加工
技能目标
任务描述
知识准备 任务实施
拓展训练
5
任务一 【任务描述】
图示零件,轮廓较为复杂,如果直接计算刀具刀位点的轨迹进行编程, 则计算复杂,容易出错,编程效率低,而采用刀具半径补偿方式进行编程,则较 为简便。零件毛坯为80mm×80mm×20mm的45钢,四周与上下表面已经加工好了, 只进行外轮廓加工。。
14
任务一 【知识准备】
3.刀具补偿D (1)编程举例 (2)补偿存储器的 (3)刀具半径补偿中的几个特殊情况 4.拐角特性 5.刀具半径补偿编程示例
15
任务一 【知识准备】
七、循环
1.轮廓铣削CYCLE72
(1)功能
1)循环运行可选择使用或不使用刀具半径补偿。
2)轮廓可以封闭也可以不封闭.
3)轮廓的定义方向必须是它的加工方向
31
任务二 【任务实施】
● 加工准备 ● 编写加工程序 ● 能熟练运用刀具半径补偿进行编程 ● 了解数控铣削加工阶段的划分方法
32
任务二 【任务实施】
◆加工准备 1.选择数控机床 本任务选用的机床为TK7650型SIEMENS802D系统数控铣床。 2.选择刀具及切削用量 加工本任务工件时,选择如图3.58所示键槽铣刀(Z向垂直进刀)或立铣刀(Z 向螺旋线进刀)进行加工,根据内轮廓的形状,选择刀具直径为φ16mm。切削 用量推荐值如下:主轴转速n=500~700 r/min;XY平面内进给速度取f=100~ 200 mm/min,Z向进给速度取f=50~100 mm/min;背吃刀量的取值等于型腔高 度,取ap=8 mm。
2.矩形外轮廓(凸台)铣削
18
任务一 【知识准备】
3.圆形凸台铣削
19
任务一 【任务实施】★加工源自备★工件检验★
检测评分
★
任务反馈
20
任务一 【任务实施】
◆加工准备
1.材料准备 2.设备准备 3.量具与刀具 4.识读零件图 5.工艺分析 6.程序编制
21
任务一 【任务实施】
◆工件检验
1.长度尺寸测量 2.圆弧的测量 3.表面粗糙度的测量
28
任务二 【知识准备】
2.平面切削
29
任务二 【知识准备】
二、螺旋类加工
30
任务二 【知识准备】
图示螺旋槽由两个螺旋面组成,前半圆AmB为左旋螺旋面,后 半圆AnB右旋螺旋面。螺旋槽最深处为A点,最浅处为B点。要求用 φ8mm的立铣刀进行加工该螺旋槽,编制数控加工程序。刀具半径 补偿号为D01,长度补偿号为D01。
项目三 轮廓加工
典型平面
二维轮廓零件 a)齿轮 b)链轮 c)凸轮 d)离合器 e)花键轴
2
典型平面
3
学习目标
● 掌握数控铣床/加工中心铣削轮廓的工艺设计 ● 掌握数控铣床/加工中心铣削外轮廓的方法 ● 掌握数控铣床/加工中心铣削内轮廓的方法 ● 掌握数控铣床/加工中心铣削复杂轮廓的方法 ● 掌握数控铣床/加工中心铣削轮廓的编程方法
◆检测评分 ◆任务反馈——造成尺寸精度降低的常见原因
22
任务一 【拓展训练 】
1.试简要叙述刀具半径补偿的过程。 2.采用刀具半径补偿编程时,应注意哪些问题? 3.试采用刀具半径补偿指令编写
23
任务二 内轮廓铣削
技能目标
任务描述
知识准备 任务实施
拓展训练
24
任务二 【任务描述】
图示零件,为封闭内轮廓。因此,如何进行刀具的Z向进给是加 工本工件的关键。另外,对于侧面轮廓,需将工件竖起来重新装夹校正 后再进行加工。该零件的毛坯为100mm×100mm×20mm的45钢。
4)循环可选择粗加工或精加工
(2)刀具动作顺序
1)粗加工时循环形成以下动作顺序
2)精加工时循环形成以下动作顺序
(3)参数说明
1)KNAME(名称)
2)LP1、LP2(长度、半径)
3)AS1、AS2(接近方向/路径,.返回方向/返回路径)
4)FF3(返回进给倍率)
16
任务一 【知识准备】
17
任务一 【知识准备】
任务二 【技能目标】
★
★
★
掌握内轮廓铣 削的编程方法
掌握内轮廓铣 削时刀具的进 刀方式
掌握内轮廓铣 削的加工工艺 的设计方法
26
任务二【知识准备】
一
内轮廓的加工工艺
二
螺旋类加工
三
子程序
27
任务二 【知识准备】
一、内轮廓的加工工艺
1.加工内轮廓时的Z向进刀方式 (1)垂直切深进刀 (2)在工艺孔中进刀 (3)三轴联动斜线进刀 (4)三轴联动螺旋线进刀
6
任务一 【技能目标】
● 掌握外轮廓铣削的编程方法 ● 掌握刀具半径补偿的基本概念 ● 能熟练运用刀具半径补偿进行编程 ● 了解数控铣削加工阶段的划分方法
7
任务一【知识准备】
一
数控铣削加工工序的划分
二
铣削内外轮廓的进给路线
三
数控加工工艺文件
四
手工编程中基点的计算
五
指令介绍
六
刀具半径补偿
七
循环
8
任务一 【知识准备】
33
任务二 【任务实施】
◆编写加工程序 1.设计加工路线 2.分析基点坐标 3.编制加工程序
34
任务二 【任务实施】
◆任务反馈——轮廓加工精度及误差分析
轮廓铣削精度主要包括尺寸精度、形状和位置精度及表面粗糙度。数控铣削加工过程中产生精度降 低的原因是多方面的,在实际加工过程中,造成形状和位置精度降低的常见原因见表3.20,造成表 面粗糙度降低的常见原因见表3.21。 表3.20 数控铣形位精度误差降低原因分析