磨削力及磨削
磨削机理

δ——单颗工作磨粒顶面积,即工件与工作磨粒的实际接触面积;
p ——磨粒实际磨损表面与工件间的平均接触压强;
因此,可以得到单位宽度法向磨削力F’n,单位宽度切向磨削力F’t公式:
F 'n
1 1 v w P An vw Ce a p 2 d se 2 Fp a p vs 1 vs
1 2
l l q
1
Fn l F p Al N d l dl
0
整个接触弧长度上的法向磨削力大小:
Fn F p C e
,
vw v s
2 1
a d
p se
1
1 1 n 1 n 2
有效磨刃数, 为砂轮以工件的接触弧长度,b为磨削宽度。
Ls
砂轮接触面上的动态磨刃数的磨削力计算公式
关于磨削力计算公式的建立,目前国内外有不少 论述。在这里重点介绍G.Wener等建立的磨削力计算 公式,该公式考虑了磨削力与磨削过程的动态参数关 系。
建立磨削力计算公式时,需要两项参数:
(1)单位砂轮表面上参与工作的磨刃数; (2)砂轮与工件相对接触长度内的平均切削截面积A。
单位砂轮表面上参与工作的磨刃数:N d An Ce
vw v s
ap d se
2
如图,对于弧任意接触长度ι范围内的动态磨刃数Nd(ι)为:
l N d (l ) N d l s
vw A C n e v s
磨削原理
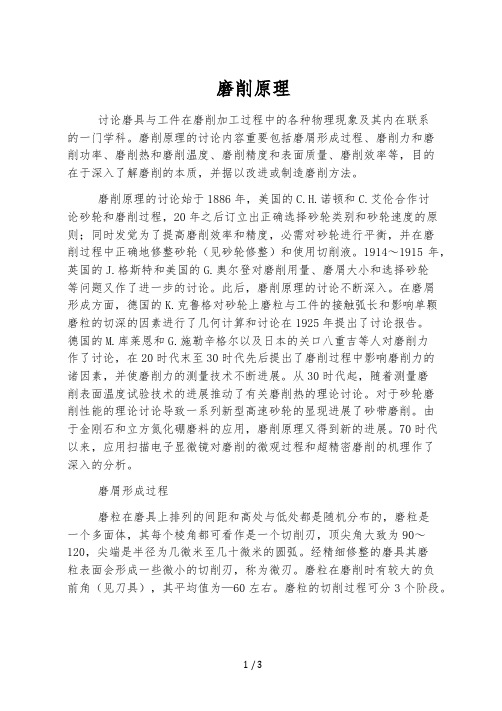
磨削原理讨论磨具与工件在磨削加工过程中的各种物理现象及其内在联系的一门学科。
磨削原理的讨论内容重要包括磨屑形成过程、磨削力和磨削功率、磨削热和磨削温度、磨削精度和表面质量、磨削效率等,目的在于深入了解磨削的本质,并据以改进或制造磨削方法。
磨削原理的讨论始于1886年,美国的C.H.诺顿和C.艾伦合作讨论砂轮和磨削过程,20年之后订立出正确选择砂轮类别和砂轮速度的原则;同时发觉为了提高磨削效率和精度,必需对砂轮进行平衡,并在磨削过程中正确地修整砂轮(见砂轮修整)和使用切削液。
1914~1915年,英国的J.格斯特和美国的G.奥尔登对磨削用量、磨屑大小和选择砂轮等问题又作了进一步的讨论。
此后,磨削原理的讨论不断深入。
在磨屑形成方面,德国的K.克鲁格对砂轮上磨粒与工件的接触弧长和影响单颗磨粒的切深的因素进行了几何计算和讨论在1925年提出了讨论报告。
德国的M.库莱恩和G.施勒辛格尔以及日本的关口八重吉等人对磨削力作了讨论,在20时代末至30时代先后提出了磨削过程中影响磨削力的诸因素,并使磨削力的测量技术不断进展。
从30时代起,随着测量磨削表面温度试验技术的进展推动了有关磨削热的理论讨论。
对于砂轮磨削性能的理论讨论导致一系列新型高速砂轮的显现进展了砂带磨削。
由于金刚石和立方氮化硼磨料的应用,磨削原理又得到新的进展。
70时代以来,应用扫描电子显微镜对磨削的微观过程和超精密磨削的机理作了深入的分析。
磨屑形成过程磨粒在磨具上排列的间距和高处与低处都是随机分布的,磨粒是一个多面体,其每个棱角都可看作是一个切削刃,顶尖角大致为90~120,尖端是半径为几微米至几十微米的圆弧。
经精细修整的磨具其磨粒表面会形成一些微小的切削刃,称为微刃。
磨粒在磨削时有较大的负前角(见刀具),其平均值为—60左右。
磨粒的切削过程可分3个阶段。
①滑擦阶段:磨粒开始挤入工件,滑擦而过,工件表面产生弹性变形而无切屑。
②耕犁阶段:磨粒挤入深度加大,工件产生塑性变形,耕犁成沟槽,磨粒两侧和前端堆高隆起;③切削阶段:切入深度连续增大,温度达到或超过工件材料的临界温度,工件材料明显地沿剪切面滑移而形成磨屑。
磨削加工中的磨削力监测
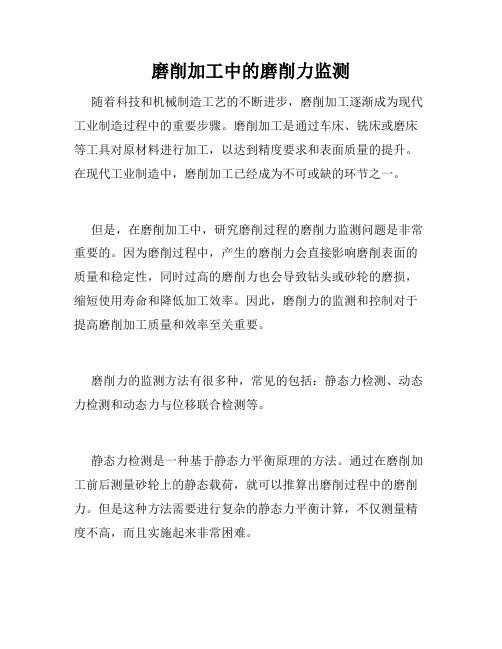
磨削加工中的磨削力监测随着科技和机械制造工艺的不断进步,磨削加工逐渐成为现代工业制造过程中的重要步骤。
磨削加工是通过车床、铣床或磨床等工具对原材料进行加工,以达到精度要求和表面质量的提升。
在现代工业制造中,磨削加工已经成为不可或缺的环节之一。
但是,在磨削加工中,研究磨削过程的磨削力监测问题是非常重要的。
因为磨削过程中,产生的磨削力会直接影响磨削表面的质量和稳定性,同时过高的磨削力也会导致钻头或砂轮的磨损,缩短使用寿命和降低加工效率。
因此,磨削力的监测和控制对于提高磨削加工质量和效率至关重要。
磨削力的监测方法有很多种,常见的包括:静态力检测、动态力检测和动态力与位移联合检测等。
静态力检测是一种基于静态力平衡原理的方法。
通过在磨削加工前后测量砂轮上的静态载荷,就可以推算出磨削过程中的磨削力。
但是这种方法需要进行复杂的静态力平衡计算,不仅测量精度不高,而且实施起来非常困难。
动态力检测是一种直接测量磨削过程中动态力变化的方法。
通过在磨削过程中实时监测磨具上的动态载荷,就可以推算出磨削力的大小和变化趋势。
这种方法可以实现高精度的测量,同时也比较简单易行。
但是,动态力检测只能测量磨削力的大小和变化趋势,对磨削过程中的位移和振动等其他因素无法进行检测。
动态力与位移联合检测是一种综合了动态力和位移测量的方法。
通过在磨削过程中实时监测磨具上的动态载荷和磨具的位移变化,就可以更加精确地推算出磨削力的大小和变化趋势,同时还能够检测磨削过程中的位移和振动。
这种方法可以实现非常高精度的测量,但是相对于动态力检测,它的实施难度和成本也会有所提高。
在磨削加工中,磨削力监测技术的应用已经变得非常普遍。
通过精确的磨削力监测,对磨削过程中的如量切削深度、磨削速度等要素进行优化和管理,就可以有效地提高磨削加工质量和效率,同时也可以有效地保护磨具的使用寿命,降低成本和存储开支。
总之,在现代机械制造领域中,磨削加工监测技术的发展已经成为了行业趋势,同时也为未来的机械制造提供了更广阔的空间和发展机遇。
机械加工中的磨削力分析与优化

机械加工中的磨削力分析与优化引言:机械加工是一种常见的制造工艺,磨削作为机械加工的重要环节之一,对于提高零件加工精度和表面质量至关重要。
然而,磨削过程中的磨削力对机械系统的稳定性和加工效果有着重要影响。
因此,磨削力的分析与优化成为了广大研究者关注的焦点。
一、机械加工中的磨削力分析1. 磨削力的来源磨削力主要由三个方面的因素共同作用产生:磨料与工件之间的相互作用力、磨料与磨削机构之间的相互作用力以及磨削过程中引起的摩擦力。
其中,磨料与工件之间的相互作用力又分为磨削力与进给力两个分力。
2. 磨削力的计算方法磨削力的计算方法主要有经验公式法、静力学法和有限元法等。
经验公式法根据实际生产中的经验数据和统计学方法得出,简单易行,但精度相对较低。
静力学法基于力平衡原理,将磨削力的计算转化为切削力的计算,适用于刀具磨削。
有限元法则是一种仿真方法,通过建立复杂的力学模型和各种约束条件,对磨削力进行精确的计算和预测。
二、磨削力的影响因素分析1. 材料特性被加工材料的硬度、韧性和热导率等物理特性直接影响着磨削力的大小。
一般来说,材料越硬、韧性越高、热导率越低,磨削力越大。
2. 磨料特性磨料的颗粒尺寸、形状和硬度等特性对磨削力有着重要影响。
磨削力随着磨料颗粒尺寸的增加而增加,而随着磨料颗粒硬度的增加而减小。
3. 加工参数磨削过程中的进给速度、切削速度和进给深度等加工参数对磨削力起重要作用。
一般来说,切削速度越大,进给速度越小,磨削力越大。
同时,进给深度的增加也会导致磨削力的增加。
三、磨削力的优化措施1. 选用合适的磨料根据被加工材料的特性选择合适的磨料是降低磨削力的有效措施之一。
对于硬度较高的材料,应选择颗粒较细、形状较锐利的磨料进行磨削,以降低磨削力。
2. 优化加工参数调节磨削过程中的进给速度、切削速度和进给深度等加工参数,是降低磨削力的重要手段。
通过合理选择这些参数,可以使磨削力保持在合适的范围内,同时提高加工效率和加工质量。
磨削过程及磨削原理
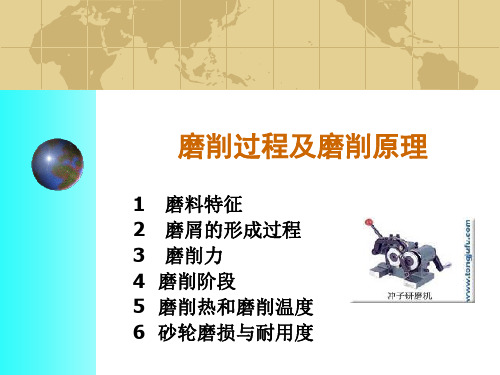
六、砂轮的磨损与耐用度
形态:磨耗磨损(A)、磨粒破碎(B-B) 和脱落磨损(C-C)。 砂轮耐用度:砂轮钝化、变形后加工 质量和效率降低。~用砂轮在两次修 整之间的实际磨削时间度时,工件将发 生颤振,表面粗糙度突然增大,或出 现表面烧伤现象。
由图可知,缩 短初磨阶段和稳定 阶段可提高生产效 率,而保持适当清 磨进给次数和清磨 时间可提高表面质 量。
五 磨削热和磨削温度
1. 磨削温度的基本概念 2. 影响磨削温度的主要因素
砂轮速度V: V ↑→θ↑ 工件速度Vw : Vw ↑→θ↓ 径向进给量fr: fr↑→θ↑ 工件材料: 导热性↓→θ↑ 砂轮硬度与粒度:硬度↓→θ↓ 磨粒大小↑→θ↓
二 磨屑的形成过程
滑擦阶段:磨粒切削厚度非常小,在 工件表面上滑擦而过,工件仅产生弹 性变形。
刻划阶段:工件材料开始产生塑性变 形,磨粒切入金属表面,磨粒的前方 及两侧出现表面隆起现象,在工件表 面刻划成沟纹。磨粒与工件间挤压摩 擦加剧,磨削热显著增加。
切削阶段:随着切削厚度的增加,在 达到临界值时,被磨粒推挤的金属明 显的滑移而形成切屑。
磨削过程及磨削原理
1 磨料特征 2 磨屑的形成过程 3 磨削力 4 磨削阶段 5 磨削热和磨削温度 6 砂轮磨损与耐用度
一 磨料特征
很不规则,大多数呈菱形八面体; 顶尖角大多数为90度~120度,以很大的负前角进行切 削; 磨粒切削刃几乎都存在切削刃钝圆半径; 在砂轮表面分布不均匀,高低也不同。
磨粒常见形状
三 磨削力
➢磨削力的的来源:工件材料产生变形时的抗力和 磨粒与工件间的摩擦力。
➢磨削力的特征: (1) 单位磨削力很大 (2) 径向分力很大---径向力虽不做工,但会使
工件产生水平方向的弯曲,直接影响加工精度。
磨削加工中的磨削力分析

磨削加工中的磨削力分析磨削加工是一种高精度的加工方式,可以用于加工各种材料的零部件。
其原理是使用磨料与加工物体之间的相对运动来去除材料表面的毛刺和瑕疵,制造出精密的表面和形状。
磨削加工的质量和效率与磨削力大小有着密切关系,因此对磨削力的分析和计算是磨削加工过程中极为重要的一环。
一、磨削加工的基本原理磨削加工是利用磨料与工件之间的相对运动,在压力的作用下,去除工件表面的毛刺和瑕疵,进而达到加工目的的过程。
在磨削加工中,磨料既是一个加工工具,也是一种加工介质。
其磨削力主要由切削力、磨合力和磨料轴向力三部分组成。
其中,切削力是主要作用力,因其大小和方向对于磨削加工的影响最为显著。
二、磨削力分析的原则磨削力是磨削加工过程中产生的一种重要力,其大小和方向对于成形精度、加工效率和工件表面质量等方面都有着显著的影响。
因此,了解磨削力的大小和方向,对于进行磨削加工质量的保证和高效率的实现都具有非常重要的作用。
在磨削力分析中,我们需要掌握以下几个基本原则:1.磨削力的大小和方向是磨削加工过程中的重要指标之一,需要进行精确的测量和分析。
2.在磨削加工过程中,应尽量降低磨削力的大小,实现高效率、高精度的加工目标。
3.在磨削力分析中,需要考虑到各个因素的综合影响,不能简单地直接计算或估算。
4.针对不同的磨削加工过程和实际需要,需要采用不同的磨削力分析方法和手段。
三、磨削力的计算方法磨削力的计算方法可以分为两种:经验计算法和基于力学原理的计算方法。
在实际应用中,一般采用经验计算和力学原理相结合的方法进行磨削力的估算。
一般情况下,磨削力的计算方法根据材料的硬度和材料的粘合程度分为两种:理论计算法和实验计算法。
其中,理论计算法以理论分析为基础,通过分析材料硬度和材料粘合程度之间的关系,计算出磨削力的大小和方向。
而实验计算法则以实验结果为依据,通过不同实验条件下的测量结果,计算出磨削力的大小和方向。
在实际应用中,常采用理论计算法和实验计算法相结合的方法,进行磨削力的估算。
4磨削
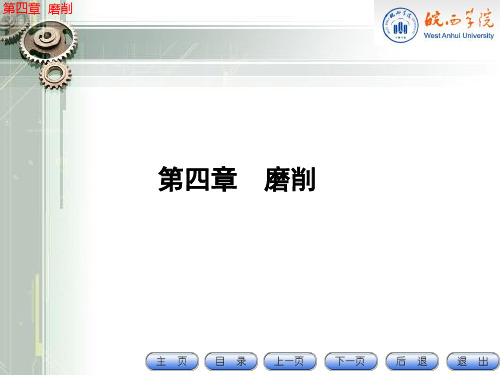
第四章 磨削
二、磨削温度
磨粒磨削点温度θdot 磨粒切削刃与切屑接触部分的温度,是磨削中温度 最高的部位,也是磨削热的热源。它不但影响工件 表面质量,且与磨粒的磨损以及切屑的熔着现象有 密切关系。
f v v
0 . 240 . 26 0 . 13 dot w r
v、vw——分别为砂轮及工件的线速度(m/s); fr——径向进给量(mm)。
工件干磨时常发生这种情况 。
第四章 磨削
二、磨削温度
(2)淬火烧伤 磨削时,工件表面层温度超过相变温度 Ac3 ,如果此时冷 却充分,则表层将急冷形成二次淬火马氏体组织。工件 表层硬度较原来的回火马氏体高,但很薄,其下层因冷 却速度慢仍为硬度较低的回火索氏体和屈氏体。这种情 况称为淬火烧伤。
⑷砂轮的磨损会使磨削力增大。
第四章 磨削
一、磨削力和磨削功率
主运动所消耗的功率定义为磨削功率。
磨削功率:
Pm Fz 1000
第四章 磨削
二、磨削温度
(一)磨削温度的概念 磨削时由于速度很高,且单位切削功率也大(约为车 削的10~20倍)。因此磨削温度很高。 磨削温度 :砂轮与工件接触面的平均温度 磨削温度区分为: 砂轮磨削区温度θA和磨粒磨削点温度θdot。
第四章 磨削
二、磨削温度
烧伤表面的硬度变化
第四章 磨削
二、磨削温度
磨削烧伤的表现形式
磨削烧伤会破坏工件表面层组织,严重的会出现裂纹, 从而影响工件的耐磨性和使用寿命。
(1)退火烧伤
(2)淬火烧伤 (3)回火烧伤
第四章 磨削
二、磨削温度
(1)退火烧伤 在磨削时,如工件表面层温度超过相变温度Ac3,则马 氏体转变为奥氏体,如果此时无冷却液,则表面层硬度 急剧下降,工件表面层被退火,故这种烧伤称退火烧伤。
磨边机的磨削过程的数学模型的研究
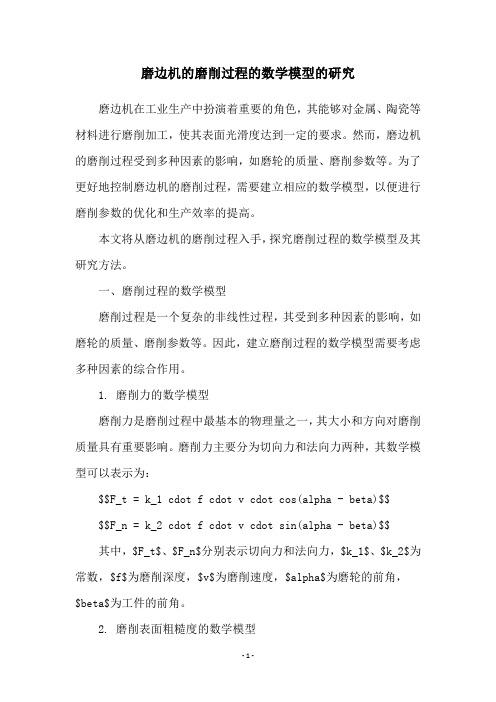
磨边机的磨削过程的数学模型的研究磨边机在工业生产中扮演着重要的角色,其能够对金属、陶瓷等材料进行磨削加工,使其表面光滑度达到一定的要求。
然而,磨边机的磨削过程受到多种因素的影响,如磨轮的质量、磨削参数等。
为了更好地控制磨边机的磨削过程,需要建立相应的数学模型,以便进行磨削参数的优化和生产效率的提高。
本文将从磨边机的磨削过程入手,探究磨削过程的数学模型及其研究方法。
一、磨削过程的数学模型磨削过程是一个复杂的非线性过程,其受到多种因素的影响,如磨轮的质量、磨削参数等。
因此,建立磨削过程的数学模型需要考虑多种因素的综合作用。
1. 磨削力的数学模型磨削力是磨削过程中最基本的物理量之一,其大小和方向对磨削质量具有重要影响。
磨削力主要分为切向力和法向力两种,其数学模型可以表示为:$$F_t = k_1 cdot f cdot v cdot cos(alpha - beta)$$$$F_n = k_2 cdot f cdot v cdot sin(alpha - beta)$$ 其中,$F_t$、$F_n$分别表示切向力和法向力,$k_1$、$k_2$为常数,$f$为磨削深度,$v$为磨削速度,$alpha$为磨轮的前角,$beta$为工件的前角。
2. 磨削表面粗糙度的数学模型磨削表面粗糙度是衡量磨削质量的重要指标之一,其数学模型可以表示为:$$R_a = frac{1}{2pi} int_0^{2pi} h(x) cdot cos(x) dx$$ 其中,$R_a$为磨削表面粗糙度,$h(x)$为表面高度函数。
3. 磨削温度的数学模型磨削过程中会产生大量的热量,磨削温度对磨削质量具有重要影响。
磨削温度的数学模型可以表示为:$$T = T_0 + k_3 cdot f cdot v cdot ln(frac{t}{t_0})$$ 其中,$T$为磨削温度,$T_0$为初始温度,$k_3$为常数,$t$为磨削时间,$t_0$为初始时间。
2.4磨削机理
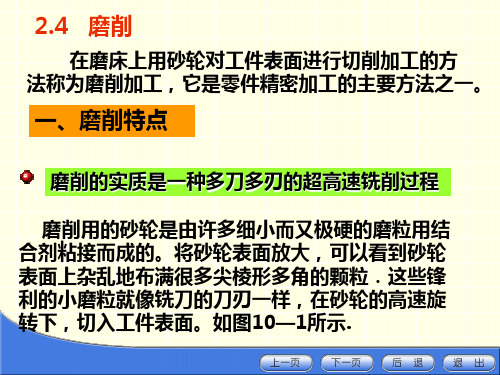
1)车削修整法
以单颗粒金刚石(或以细碎金刚石制成 的金刚笔、金刚石修整块) 作为刀具车 削砂轮是应用最普遍的修整方法。安装 在刀架上的金刚石刀具通常在垂直和水 平两个方向各倾斜约5°~15°;金刚 石与砂轮的接触点应低于砂轮轴线 0.5~2mm,修整时金刚石作均匀的低速 进给移动。要求磨削后的表面粗糙度越 小,则进给速度应越低,如要达到 Ra0.16~0.04µm的表面粗糙度,修整进 给速度应低于50mm/min。修整总量一般 为单面0.1mm左右,往复修整多次。粗 修的切深每次为0.01~0.03mm,精修则 小于0.01mm。
当砂轮硬度较低,修整较粗,磨削载荷较 重时。易出现脱落型。这时,砂轮廓形失真, 严重影响磨削表面质量及加工精度。 在磨削碳钢时由于切屑在磨削高温下发生 软化,嵌塞在砂轮空隙处,形成嵌入式堵塞, 在磨削钛合金时,由于切屑与磨粒的亲合力强, 使切屑熔结粘附于磨粒上,形成粘附式堵塞。 砂轮堵塞后即丧失切削能力,磨削力及温度剧 增,表面质量明显下降。
根据条件不同,磨粒的切削过程的3个阶段可以全部存 在,也可以部分存在 。
典型磨屑有带状、挤裂状、 球状及灰烬等(图10— 7).
三、磨削力及磨削功率 尽管单个磨粒切除的材料很少,但一个砂轮表层 有大量磨粒同时工作,而且磨粒的工作角度很不合理, 因此总的磨削力相当大。总磨削力可分解为三个分力: Rz——主磨削力(切向磨削力);
根据表面颜色,可以推断磨削温度及烧伤程度。如淡黄色 约为400℃~500℃,烧伤深度较浅;紫色为800℃~900℃, 烧伤层较深。 5、磨削表面裂纹 磨削过程中,当形成的残余拉应力超过工件材料的强 度极限时,工件表面就会出现裂纹。 磨削裂纹极浅,呈网状或垂直于磨削方向。有时不在表层, 而存在于表层之下。有时在研磨或使用过程中,由于去除 了表面极薄金属层后,残余应力失去平衡,形成微细裂纹。 这些微小裂纹,在交变载荷作用下,会迅速扩展,并造成 工件的破坏。
简述精密磨削机理
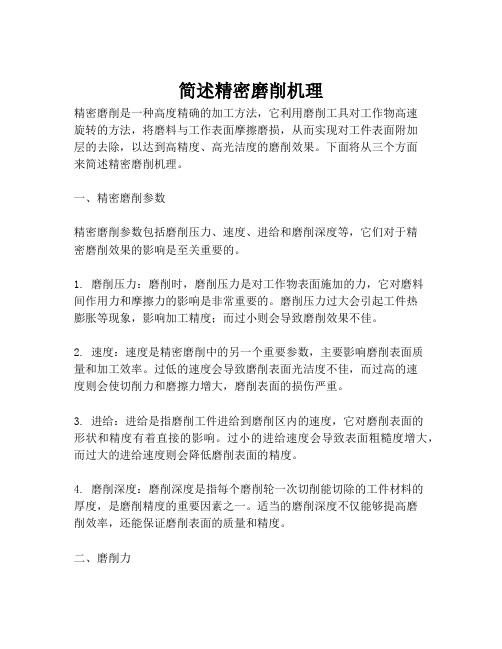
简述精密磨削机理精密磨削是一种高度精确的加工方法,它利用磨削工具对工作物高速旋转的方法,将磨料与工作表面摩擦磨损,从而实现对工件表面附加层的去除,以达到高精度、高光洁度的磨削效果。
下面将从三个方面来简述精密磨削机理。
一、精密磨削参数精密磨削参数包括磨削压力、速度、进给和磨削深度等,它们对于精密磨削效果的影响是至关重要的。
1. 磨削压力:磨削时,磨削压力是对工作物表面施加的力,它对磨料间作用力和摩擦力的影响是非常重要的。
磨削压力过大会引起工件热膨胀等现象,影响加工精度;而过小则会导致磨削效果不佳。
2. 速度:速度是精密磨削中的另一个重要参数,主要影响磨削表面质量和加工效率。
过低的速度会导致磨削表面光洁度不佳,而过高的速度则会使切削力和磨擦力增大,磨削表面的损伤严重。
3. 进给:进给是指磨削工件进给到磨削区内的速度,它对磨削表面的形状和精度有着直接的影响。
过小的进给速度会导致表面粗糙度增大,而过大的进给速度则会降低磨削表面的精度。
4. 磨削深度:磨削深度是指每个磨削轮一次切削能切除的工件材料的厚度,是磨削精度的重要因素之一。
适当的磨削深度不仅能够提高磨削效率,还能保证磨削表面的质量和精度。
二、磨削力在精密磨削中,磨削力起着关键的作用。
磨削力包括切削力和法向力两个方向的力。
切削力是沿着工件表面的力,是磨削过程中摩擦力和切削力的总和。
法向力是垂直于工件表面的力,作用于磨削轮和工件之间的接触面。
法向力的大小和方向对于精密磨削过程中的磨削力影响极大。
三、磨削热在高速磨削过程中,由于磨削面与切削刃瞬间之间的摩擦和接触,会引起加工界面的热变形和变色。
因此,控制磨削热的积累是保证精密磨削效果的关键。
合适的工作液和降低磨削温度的措施(如降低表面温度、改善切削液的散热、提高磨削速度等)都可以在一定程度上减少磨削热对加工质量的影响。
总之,了解各种精密磨削参数与机理的相互关系,才能够更好地运用磨削工艺,提高精密磨削的效率和质量。
【金属切削原理】第12章:磨削详解
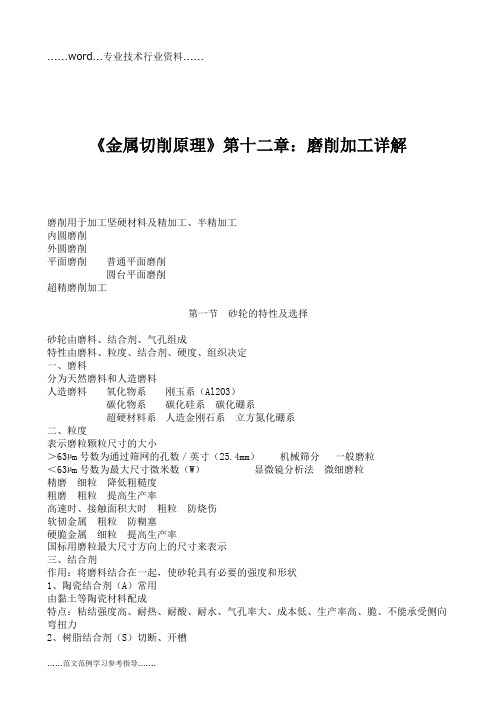
《金属切削原理》第十二章:磨削加工详解磨削用于加工坚硬材料及精加工、半精加工内圆磨削外圆磨削平面磨削普通平面磨削圆台平面磨削超精磨削加工第一节砂轮的特性及选择砂轮由磨料、结合剂、气孔组成特性由磨料、粒度、结合剂、硬度、组织决定一、磨料分为天然磨料和人造磨料人造磨料氧化物系刚玉系(Al2O3)碳化物系碳化硅系碳化硼系超硬材料系人造金刚石系立方氮化硼系二、粒度表示磨粒颗粒尺寸的大小>63µm号数为通过筛网的孔数/英寸(25.4mm)机械筛分一般磨粒<63µm号数为最大尺寸微米数(W)显微镜分析法微细磨粒精磨细粒降低粗糙度粗磨粗粒提高生产率高速时、接触面积大时粗粒防烧伤软韧金属粗粒防糊塞硬脆金属细粒提高生产率国标用磨粒最大尺寸方向上的尺寸来表示三、结合剂作用:将磨料结合在一起,使砂轮具有必要的强度和形状1、陶瓷结合剂(A)常用由黏土等陶瓷材料配成特点:粘结强度高、耐热、耐酸、耐水、气孔率大、成本低、生产率高、脆、不能承受侧向弯扭力2、树脂结合剂(S)切断、开槽酚醛树脂、环氧树脂特点:强度高、弹性好、耐热性差、易自砺、气孔率小、易糊塞、磨损快、易失廓形、与碱性物质易反应、不易长期存放3、橡胶结合剂(X)薄砂轮、切断、开槽、无心磨导轮人造橡胶特点:弹性好、强度好、气孔小、耐热性差、生产率低4、金属结合剂(Q)磨硬质合金、玻璃、宝石、半导体材料青铜结合剂(制作金刚石砂轮)特点:强度高、自砺性差、形面成型性好、有一定韧性四、硬度在磨削力作用下,磨粒从砂轮表面脱落的难易程度分为超软、软、中软、中、中硬、硬、超硬工件材料硬砂轮软些防烧伤工件材料软砂轮硬些充分发挥磨粒作用接触面积大软砂轮精度、成形磨削硬砂轮保持廓形粒度号大软砂轮防糊塞有色金属、橡胶、树脂软砂轮防糊塞五、组织磨粒、气孔、结合剂体积的比例关系分为:紧密(0~3)、中等(4~7)、疏松(8~14)(磨粒占砂轮体积%↘)气孔、孔穴开式(与大气连通)占大部分,影响较大闭式(与大气不连通)尺寸小、影响小开式空洞型蜂窝型前两种构成砂轮内部主要的冷却通道管道型5~50µm六、砂轮的型号标注形状、尺寸、磨料、粒度号、硬度、组织号、结合剂、允许最高圆周线速度P300x30x75WA60L6V35外径300,厚30,内径75第二节磨削运动一、磨削运动1、主运动砂轮外圆线速度 m/s2、径向进给运动进给量fr 工件相对砂轮径向移动的距离间歇进给 mm/st 单行程mm/dst 双行程连续进给 mm/s3、轴向进给运动进给量fa 工件相对砂轮轴向的进给运动圆磨 mm/r平磨 mm/行程4、工件速度vw线速度 m/s二、磨削金属切除率ZQ=Q/B=1000·vw·fr·fa/B mm^3/(s·mm)ZQ:单位砂轮宽度切除率Q:每秒金属切除量用以表示生产率B:砂轮宽度三、砂轮与工件加工表面接触弧长lc=sqrt(fr·d0)影响参加磨削磨粒数目及磨粒负荷,容屑,冷却条件四、砂轮等效直径将外圆(内圆)砂轮直径换算成接触弧长相等的假想平面磨削的砂轮直径结论:对砂轮耐用度影响内圆>平面>外圆第三节磨削的过程一、单个磨粒的磨削过程磨粒的模型锐利120°圆锥钝化半球实际磨粒:大的负前角,大的切削刃钝圆半径滑擦、耕犁、切削滑擦:(不切削,不刻划)产生高温,引起烧伤裂纹耕犁:(划出痕迹)磨粒钝或切削厚度小于临界厚度,工件材料挤向两侧隆起切削:切削厚度大于临界厚度,形成切屑v↑→隆起↓(线性)塑性变形速度<磨削速度二、磨削的特点1、精度高、表面粗糙度小高速、小切深、机床刚性2、径向分力Fn较大多磨粒切削3、磨削温度高磨粒角度差、挤压和摩擦、砂轮导热差4、砂轮的自砺作用三、磨削的阶段1、初磨阶段实际磨深小于径向进给量2、稳定阶段实际磨深等于径向进给量3、清磨阶段实际磨深趋向于0提高生产率缩短1、2提高质量保证3第四节磨削力及磨削功率一、磨削力的特征分解成三个分力Ft切向力 Fn法向力 Fa轴向力特征:1、单位切削力k很大磨粒几何形状的随机性和参数的不合理性7000~20000kgf/mm^2 其他切削方式k<700kgf/mm^22、Fn值最大Fn/Ft 通常2.0~2.5工件塑性↓、硬度↑→Fn/Ft↑切深小,砂轮严重磨损 Fn/Ft 可达5~103、磨削力随磨削阶段变化初磨、稳定、光磨二、磨削力及磨削功率摩擦耗能占相当大的比例(70~80%)切向力(N):Ft=9.81·(CF·(vw·fr·B/v)+µ·Fn)径向力(N):Fn=9.81·CF·(vw·fr·B/v)·tan(α)·(π/2) vw:工件速度v:砂轮速度fr:径向进给量B:磨削宽度CF:切除单位体积切屑所需的能 kgf/mm^2µ:工件-砂轮摩擦系数α:假设粒度为圆锥时的锥顶半角磨削功率P=Ft·v/1000 Kw理论公式精度不高,常用实验测定(顶尖上安装应变片)第五节磨削温度耕犁、滑擦和形成切屑的能量全部转化成热,大部分传入工件一、磨削温度砂轮磨削区温度θA:砂轮与工件接触区的平均温度影响:烧伤、裂纹的产生磨粒磨削点温度θdot:磨粒切削刃与切屑接触部分的温度温度最高处,是磨削热的主要来源影响:表面质量、磨粒磨损、切屑熔着工件温升:影响:工件尺寸、形状精度受影响二、影响磨削温度的因素切削液为降温的主要途径1、工件速度对磨粒磨削点温度的影响大于砂轮速度vw↑→acgmax↑→F↑→θdot↑大v↑→acgmax↓→θdot↑小→摩擦热↑↗acgmax:单个磨粒最大切削厚度 mm假设:磨粒前后对齐,均匀分不在砂轮表面平面磨:acgmax=(2·vw·fa/(v·m·B))sqrt(fr/dt)外圆磨:acgmax=(2·vw·fa/(v·m·B))sqrt((fr/dt)+(fr/dw))dt:砂轮直径m:每毫米周长磨粒数用于定性分析2、径向进给量Frfr↑→acgmax↑→θdot↑fr↑→接触区↑→同时参加切削磨粒数↑→θA↑3、其他因素fa↑→θdot↑、θA↑工件材料硬度↑、强度、↑韧性↑→θdot↑、θA↑θA↑→工件温升↑vw↑→被磨削点与砂轮接触时间↓→工件温升↗三、磨削温度的测量(热电偶)第六节砂轮的磨损及表面形貌一、砂轮的磨损类型磨耗磨损磨粒磨损破碎磨损磨粒或结合剂破碎(取决于磨削力与磨粒、结合剂强度)破碎磨损消耗砂轮多磨耗磨损通过磨削力影响破碎磨损阶段初期磨损磨粒破碎磨损(个别磨粒受力大,磨粒内部应力与裂纹)二期磨损磨耗磨损三期磨损结合剂破碎磨损二、砂轮的耐用度T砂轮相邻两次修整期间的加工时间 s各因素通过平均切削厚度来影响T经验公式:T=6.67·(dw^0.6)·km·kt/(10000·(vw·fa·fr)^2)dw:工件直径kt:砂轮直径修正系数km:工件材料修正系数粗磨时间常用单位时间内磨除金属体积与砂轮磨耗体积之比来选择砂轮三、砂轮的修整作用去除钝化磨粒或糊塞住的磨粒,使新磨粒露出来增加有效切削刃,提高加工表面质量工具单颗金刚石、单排金刚石、碳化硅修整轮、电镀人造金刚石滚轮、硬质合金挤压轮等使用单颗金刚石:导程小于等于磨粒平均直径,每颗磨粒都能修整深度小于等于磨粒平均直径,提高砂轮寿命四、表面形貌单位面积上磨粒数目越多→acgmax↓→磨粒受力↓→磨粒寿命↑→T↑磨粒高度分布越均匀→粗糙度↓磨粒间距均匀性越好→粗糙度↓第七节磨削表面质量与磨削精度一、表面粗糙度比普通切削小小于 Ra2~4µmvw↓、v↑、R工↑、R砂↑、细粒度→粗糙度↓细粒度→m↑→粗糙度↓B↑→acgmax↓→粗糙度↓磨粒等高性好→粗糙度↓二、机械性能1、金相组织变化烧伤:C↑、合金元素↑→导热性↓→易烧伤高温合金↑→磨削功率↑→θA↑→易烧伤影响:破坏工件表层组织,产生裂纹,影响耐磨性和寿命2、残余应力原因:相变引起金相组织体积变化温度引起热胀冷缩和塑性变形的综合结果光磨10次残余应力减少2~3倍光磨15次残余应力减少4~5倍fa↓、fr↓→拉应力↓3、磨削裂纹磨削速度垂直方向上的裂纹(局部高温急冷造成热应力)三、磨削精度1、磨床与工件的弹性变形2、磨床与工件的热变形3、砂轮磨损导致形状尺寸变化3、磨床与工件振动研磨加工是应用较广的一种光整加工。
第四章 磨削力

砂 轮 再生效应 位移 砂 轮 接触刚性 某一切深u 某一切深 0 工 件 再生效应 磨床刚性
砂 轮 磨损特性
磨削力 工 件 可磨削性
磨削中的自激振动原理 磨削中的自激振动原理 磨削中的颤振产生的主要原因是:磨具的硬度特性 砂轮若过软,则磨削过程中的扰动会使砂轮表面上的磨损不均匀, 砂轮若过软,则磨削过程中的扰动会使砂轮表面上的磨损不均匀, 使砂轮表面也出现了波纹;若砂轮过硬, 使砂轮表面也出现了波纹;若砂轮过硬,扰动则会使砂轮表面的 堵塞不均匀,以这两种砂轮磨削工件必将在工件表面形成波纹, 堵塞不均匀,以这两种砂轮磨削工件必将在工件表面形成波纹, 而工件表面的波纹反过来会促使砂轮的不均匀的磨损和堵塞更加 严重。如此相互影响相互促进,使振动越来越激烈 严重。如此相互影响相互促进,
PE ⋅η E Ft = π ⋅ ns ⋅ Ds
式中ηR--电动机传动效率; nS--砂轮转速(r/s); DS--砂轮直径(mm)。
PE--磨头电动机实测输入功率(kW);
(2)电阻应变测力法 )
(3)电容式测力仪 电容式测力仪 (4)压电原理的平面磨削测力仪 压电原理的平面磨削测力仪
第二节 磨削中的振动
3、影响磨削力的因素 、 1)磨具条件:磨料、粒度、结合剂、组织、硬度、磨具修整 )磨具条件:磨料、粒度、结合剂、组织、硬度、 2)工件条件:工件材料的硬度、强度、塑性、 )工件条件:工件材料的硬度、强度、塑性、 3)工艺参数条件: )工艺参数条件: 单位时间内参与切削的磨粒数量↑ 每个 砂轮速度v砂↑ →单位时间内参与切削的磨粒数量 →每个 单位时间内参与切削的磨粒数量 磨粒的切削厚度↓ 磨削力 磨削力↓ 磨粒的切削厚度 →磨削力 单位时间内磨去的金属量↑ 每个磨 工件速度vω、fa ↑ →单位时间内磨去的金属量 →每个磨 单位时间内磨去的金属量 粒的切削厚度↑→磨削力 磨削力↑ 粒的切削厚度 磨削力 径向进给量f 每个磨粒的切削厚度↑、 径向进给量 r ↑ →每个磨粒的切削厚度 、砂轮与工件的磨 每个磨粒的切削厚度 削接触弧长↑ 同时参与磨削的磨粒数 同时参与磨削的磨粒数↑ 磨削力 磨削力↑ 削接触弧长 →同时参与磨削的磨粒数 →磨削力 砂轮磨损↑磨削力 砂轮磨损 磨削力↑ 磨削力 4)磨削液条件:液体成分、润滑冷却性能、供液压力 )磨削液条件:液体成分、润滑冷却性能、 5)机床工艺系统的刚性和机床的精度 )
第十二章 磨削
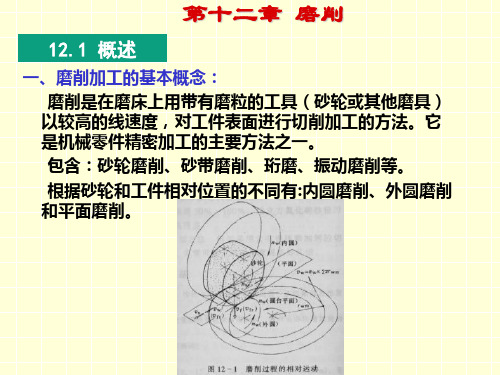
12.3 砂轮表面形貌图
有效磨粒切削刃,无效磨粒切削刃。 测量砂轮表面形貌目前主要用接触法: 1、静态法 2、动态法 3、工件复印法
12.4 磨削过程
一、磨削运动 磨削时,一般有四个运动。 1、主运动 砂轮的旋转运动,主运动的速度 就是砂轮外圆的线速度。 vs=πdsns/1000 2、径向进给运动:砂轮切入工件的运动,其 大小用径向进给量fr表示。又称磨削深度。
• • • •
天然金刚石 人造金刚石 CBN 普通磨料
二、粒度
粒度:磨粒颗粒的尺寸大小。
粗磨粒粒度(颗粒最大尺寸大于40μm ):用机械筛分法,
每平方英寸筛网上孔的数量,如60#,80#。粒度号数越大,
颗粒尺寸越细。
微粉磨粒粒度(颗粒尺寸小于40μm ):用显微镜分析法, 粒度号数即该颗粒最大尺寸的μm数。如W5,W3,W0.5
• 普通磨料固结磨具的标志按国标GB2484-84规定,其书写 顺序为:磨具形状、尺寸、磨料、粒度、组织、结合剂、 最高工作线速度。
国标GB2484-84
国际标准ISO
• 超硬磨料磨具的标志书写顺序为:形状、尺寸、 磨料、粒度、结合剂和浓度等。平行砂轮标志 示例如下:
超硬磨料磨具的结构
• 超硬磨料砂轮一般由磨料层、过渡层和基体组成。
四、磨削循环 一、磨削力的特征 磨削力的来源:一是各个磨粒的切削刃挤压切入工件后,工 件材料发生弹性、塑性变形时所产生的阻力;二是磨粒和结 合剂与工件表面之间的摩擦力。 以外圆纵磨为例,磨削力分解为切向力、法向力和轴向力。
由于磨粒上的切削刃为负前角,所以法向分力Fn远大于 切向分力Ft。轴向分力Fa最小。
以磨粒率表示的磨具组织及其应用范围
组织号 磨粒率 (%) 0 62 1 60 2 58 3 56 4 54 5 52 6 50 7 48 8 46
磨削力比的计算公式

磨削力比的计算公式磨削力比是磨削加工中的一个重要参数,它可以用来评估磨削过程中的磨削效率和磨损情况。
磨削力比的计算公式是磨削力比=磨削力/切削力。
在磨削加工中,磨削力比的数值越大,说明磨削效率越高,磨损情况越小,反之则说明磨削效率低,磨损情况严重。
本文将介绍磨削力比的计算公式及其在磨削加工中的应用。
磨削力比的计算公式是磨削力比=磨削力/切削力。
其中,磨削力是指在磨削过程中对工件表面进行磨削所需的力,它包括了磨粒与工件之间的摩擦力、磨粒与砂轮之间的摩擦力以及砂轮的切削力等。
切削力是指在切削过程中对工件表面进行切削所需的力,它包括了刀具与工件之间的摩擦力、刀具的切削力以及切屑的形成力等。
磨削力比的计算公式可以直观地反映出磨削力与切削力之间的关系,从而评估磨削过程中的磨削效率和磨损情况。
在磨削加工中,磨削力比的数值越大,说明磨削效率越高,磨损情况越小。
这是因为磨削力比的增大意味着相同的磨削力可以产生更大的切削力,从而达到更高的磨削效率。
另外,磨削力比的增大也意味着相同的切削力可以产生更小的磨削力,从而减小磨损情况。
因此,磨削力比的计算公式可以帮助工程师们在磨削加工中选择合适的磨削参数,从而提高磨削效率,减小磨损情况。
除了在磨削加工中的应用,磨削力比的计算公式还可以用于磨削工艺的优化。
通过对磨削力比的计算,工程师们可以评估不同磨削参数对磨削效率和磨损情况的影响,从而选择最优的磨削参数。
比如,在磨削过程中,可以通过调整磨削速度、磨削深度、磨削宽度等参数来改变磨削力比的数值,从而达到更好的磨削效果。
此外,磨削力比的计算公式还可以用于磨削工艺的监控。
通过实时监测磨削力和切削力的大小,可以及时发现磨削过程中的异常情况,从而采取相应的措施,保证磨削加工的质量和效率。
总之,磨削力比的计算公式是磨削加工中的重要参数,它可以用来评估磨削效率和磨损情况。
磨削力比的计算公式可以帮助工程师们在磨削加工中选择合适的磨削参数,优化磨削工艺,监控磨削过程。
磨削机理精选全文

为随着磨粒的钝化,将引起F的急剧增大,使砂轮磨损加快,系统振动增加,
噪声加大,工件表面粗糙度上升和表面质量恶化等。所以,它也可作为砂轮
耐用度的判断依据之一 。
磨削普通钢
料
磨削淬硬钢
1.6-1.8
1.9-2.6
磨削铸铁
硬脆
2.7-3.2
研究磨削力,主要在于了解清楚磨削过程的一些基本情况,
是机床设计和工艺改进的基础,是磨削研究中的主要问题,
磨削力几乎与所有的磨削有关系。
磨削力与砂轮耐用度、磨削表面粗糙度以及磨削比能等均有
直接的关系,且由于磨削力比较容易测量与控制,通常用磨
削力判断磨削状态。因此,磨削力是磨削加工中重要的参数
之一。
磨削力分析
(2)砂轮与工件相对接触长度内的平均切削截面积A。
单位砂轮表面上参与工作的磨刃数:N d An Ce
vw
vs
ap
d se
2
如图,对于弧任意接触长度ι范围内的动态磨刃数Nd(ι)为:
l
N d (l ) N d
ls
v
2
se
1
2
F’nc-由磨削变形引起的法向力;
F’ns-由摩擦引起的法向力;
F’tc-由磨削变形引起的切向力;
F’ts-由摩擦,即工件与工作磨粒的实际接触面积;
p ——磨粒实际磨损表面与工件间的平均接触压强;
因此,可以得到单位宽度法向磨削力F’n,单位宽度切向磨削力F’t公式:
磨削陶瓷
3.5-22
磨削力的理论公式
砂轮磨削力计算

磨削力、磨削功率及磨削温度一、磨削力和磨削功率(一)磨削力的主要特征及计算砂轮上单个磨粒的切削厚度固然很小,但是大量的磨粒同时对被磨金属层进行挤压、刻划和滑擦,加之磨粒的工作角度又很不合理,因此总的磨削力很大。
为便于测量和计算,将总磨削力分解为三个相互垂直的分力F x (轴向磨削力)、F y (径向磨削力)、F z (切向磨削力),如图4-4所示,和切削力相比,磨削力有如下特征:1.径向磨削力F y 最大。
这是因为磨粒的刃棱大都以负前角工作,而且刃棱钝化后,形成小的棱面增大了与工件的实际接触面积,从而使F y 增大。
通常F y =(1.6~3.2)F z 。
2.轴向磨削力F x 很小,一般可以不必考虑。
3.磨削力随不同的磨削阶段而变化。
在初磨阶段,磨削力由小至大变化较大;进入稳定阶段,工艺系统的弹性变形达到一定程度,此时磨削力较为稳定;光磨阶段实际磨削深度近趋于零,此时磨削力渐小。
磨削力的计算公式如下:(4-5)(4-6)式中F z ,F y ——分别为切向和径向磨削力( N );v w ,v ——分别为工件和砂轮的速度( m/s );f r ——径向进给量( mm );B ——磨削宽度( mm );α——假设磨粒为圆锥时的锥顶半角;C F ——切除单位体积的切屑所需的能( KJ/mm 2 );μ——工件和砂轮间的摩擦系数。
磨削过程很复杂,影响磨削力的因素也很多,上述理论公式的精确度不高。
目前一般采用实验方法来测定磨削力的大小。
(二)磨削功率的计算磨削时,由于砂轮速度很高,功率消耗很大。
主运动所消耗的功率定义为磨削功率。
其计算公式如下:(kW) ( 4-7 )式中F z ——砂轮的切向力( N );v——砂轮的线速度( mm/s )。
二、磨削温度由于磨削的线速度很高,功率消耗较大,所以磨削温度很高。
这样高的温度会直接影响工件的精度及表面质量。
因此,控制磨削温度是提高工件表面质量和保证加工精度的重要途径。
磨削原理
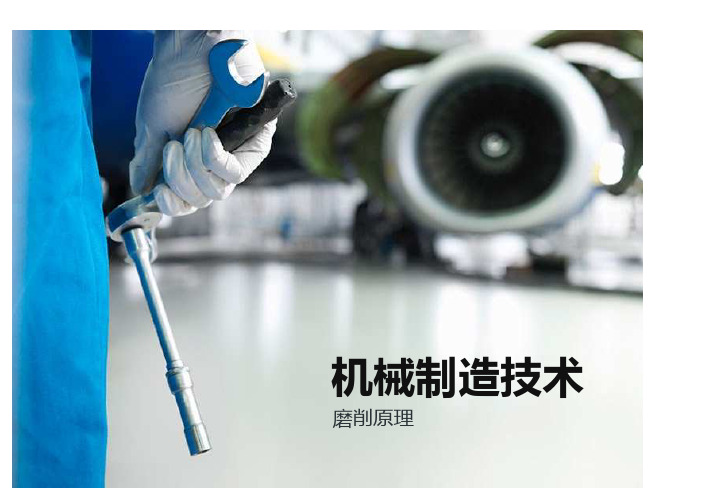
磨削原理3.7 磨削原理磨削是用砂轮作刀具磨削工件的主要方法之一。
它不仅能加工一可以加工一般刀具难以加工的材料磨削加工的精度可以达到IT60.02~1.25μm。
磨削加工不适合软的材料。
削工件的加工过程,是零件精加工加工一般材料(如钢、铸铁等),还的材料(如淬火钢、硬质合金等)。
~IT4,表面粗糙度Ra值可达适合磨削铝、铜等有色金属及较1.磨料:即砂轮中的硬质颗粒。
2.粒度粒度是指磨料颗粒的大小。
粒度号小的磨粒称为微粉,其号数越小,表示微粉从粗到细依次为W63、W50、W W7、W5、W3.5、W2.5、W1.5、W 度,粒度号W表示微粉,阿拉伯数字表示表示颗粒的大小为40~28μm。
砂轮的粒度对工件表面的粗糙度和磨削深度可以增加,磨削效率高,但表工作标表面上单位面积内的磨粒多,好的表面质量,但磨削效率比较低。
摩擦大,发热量大,易引起工件烧伤。
度号越大,表示磨料颗粒越小。
颗粒更表示磨料的颗粒也越小,亦即粒度越细W40、W28、W20、W14、W10、W1.0、W0.5。
微粉用显微镜测量其粒字表示磨粒的实际宽度尺寸。
例如W40度和磨削效率有较大的影响。
磨粒大,但表面质量差。
反之,磨粒小,在砂轮,磨粒切削刃的等高性好,可以获得较。
另外,粒度细砂轮与工件表面之间的。
3.结合剂结合剂用来将磨料粘合起来,使之影响砂轮的硬度、强度。
结合剂的名称及由于砂轮在高速旋转中进行磨削加击载荷以及强腐蚀性切削液的条件下工合剂本身的耐热、耐蚀性能,就成为结合使之成为砂轮。
结合剂的种类及其性质名称及其代号见表3-13。
削加工,而且又是在高温、高压、强冲下工作,所以磨料粘接的牢固程度,结为结合剂的重要要求。
4.硬度硬度是指砂轮表面上的磨粒在外力易脱落,表明砂轮的硬度低,反之,轮的硬度与磨料的硬度是两个不同的概成不同硬度的砂轮,它主要取决于结合艺。
根据GB/T2484—94标准,砂轮的硬、D、E、F、G、H、J、K、L、M、外力作用下脱落的难易程度。
砂轮磨削力计算

磨削力、磨削功率及磨削温度一、磨削力和磨削功率(一)磨削力的主要特征及计算砂轮上单个磨粒的切削厚度固然很小,但是大量的磨粒同时对被磨金属层进行挤压、刻划和滑擦,加之磨粒的工作角度又很不合理,因此总的磨削力很大。
为便于测量和计算,将总磨削力分解为三个相互垂直的分力F x (轴向磨削力)、F y (径向磨削力)、F z (切向磨削力),如图4-4所示,和切削力相比,磨削力有如下特征:1.径向磨削力F y 最大。
这是因为磨粒的刃棱大都以负前角工作,而且刃棱钝化后,形成小的棱面增大了与工件的实际接触面积,从而使F y 增大。
通常F y =(1.6~3.2)F z 。
2.轴向磨削力F x 很小,一般可以不必考虑。
3.磨削力随不同的磨削阶段而变化。
在初磨阶段,磨削力由小至大变化较大;进入稳定阶段,工艺系统的弹性变形达到一定程度,此时磨削力较为稳定;光磨阶段实际磨削深度近趋于零,此时磨削力渐小。
磨削力的计算公式如下:(4-5)(4-6)式中F z ,F y ——分别为切向和径向磨削力( N );v w ,v ——分别为工件和砂轮的速度( m/s );f r ——径向进给量( mm );B ——磨削宽度( mm );α——假设磨粒为圆锥时的锥顶半角;C F ——切除单位体积的切屑所需的能( KJ/mm 2 );μ——工件和砂轮间的摩擦系数。
磨削过程很复杂,影响磨削力的因素也很多,上述理论公式的精确度不高。
目前一般采用实验方法来测定磨削力的大小。
(二)磨削功率的计算磨削时,由于砂轮速度很高,功率消耗很大。
主运动所消耗的功率定义为磨削功率。
其计算公式如下:(kW) ( 4-7 )式中F z ——砂轮的切向力( N );v——砂轮的线速度( mm/s )。
二、磨削温度由于磨削的线速度很高,功率消耗较大,所以磨削温度很高。
这样高的温度会直接影响工件的精度及表面质量。
因此,控制磨削温度是提高工件表面质量和保证加工精度的重要途径。
外圆和平面磨削时磨削力的计算公式

外圆和平面磨削时磨削力的计算公式磨削过程中的磨削力是指砂轮与工件之间的相互作用力,它是砂轮将工件材料去除的力量。
在外圆和平面磨削中,磨削力的计算涉及到很多因素,如切削速度、进给速度、切削深度、切削宽度、砂轮特性等,因此并没有一种普适的公式可以适用于所有情况。
下面将针对外圆和平面磨削中常见的一些情况进行力的计算和估算。
1.外圆内径磨削在外圆磨削中,砂轮与工件接触的长度为πd,其中d为工件直径。
当切削深度为a时,可将磨削力分解为切向力和径向力两个方向。
切向力的计算可以使用下面的公式:Ft = Kt ×ae × ν其中Kt为切向力系数,ae为切向力系数的修正值,ν为切削速度。
对于径向力的计算可以使用下面的公式:Fr = Kr × ae × ae × ν其中Kr为径向力系数,ae为于径向力系数的修正值,ν为切削速度。
2.平面磨削在平面磨削中,工件的尺寸通常为L×W×H,L和W分别为工件的长度和宽度,H为磨削后的高度。
切削深度为a时,磨削力可以分解为切向力和径向力两个方向。
切向力的计算可以使用下面的公式:Ft=Kt×a×W×ν其中Kt为切向力系数,a为切削深度,W为工件的宽度,ν为切削速度。
对于径向力的计算可以使用下面的公式:Fr=Kr×a×L×ν其中Kr为径向力系数,a为切削深度,L为工件的长度,ν为切削速度。
需要注意的是,上述公式中的切削力系数Kt和Kr以及修正值ae的具体数值需要根据具体的工艺条件和机械设备来确定,一般需要通过试验和经验来进行估算和调整。
此外,还有一些其他因素也会对磨削力产生影响,比如刃口形状、切削液的使用以及砂轮磨损等。
因此,在实际应用中,还需要综合考虑这些因素来准确计算磨削力。
- 1、下载文档前请自行甄别文档内容的完整性,平台不提供额外的编辑、内容补充、找答案等附加服务。
- 2、"仅部分预览"的文档,不可在线预览部分如存在完整性等问题,可反馈申请退款(可完整预览的文档不适用该条件!)。
- 3、如文档侵犯您的权益,请联系客服反馈,我们会尽快为您处理(人工客服工作时间:9:00-18:30)。
§14—4 磨削力及磨削功率
14-1砂轮的特性和砂轮选择
14-2磨削加工类型和磨削运动
14-3磨削加工表面形成机理和磨削要素
14-4磨削力及磨削功率
一、磨削力的特征
二、磨削力及磨削功率
三、磨削力的测试方法
14-5磨削温度
14-6砂轮的磨损及砂轮表面形貌
14-7磨削表面质量与磨削精度
14-8几种高效和小粗糙度的磨削方法
一、磨削力的特征
尽管砂轮单个磨粒切除的材料很少,但因砂轮表层有大量的磨粒同时工作,而且磨粒的工作角度很不合理,因此总的磨削力仍相当大。
同其他切削加工一样,总磨削力可分解为三个分力:Fc—主磨削力(切向磨削力);Fp—切深抗力(径向磨削力);Ff——进给抗力(轴向磨削力)。
几种不同类型磨削加工的三向分力示如图14—15。
磨削力的主要特征有以下三点:
(1)单位磨削力kc值很大:由于磨粒几何形状的随机性和几何参数不合理,磨削时的单位磨削力kc值很大;根据不同的磨削用量,kc值约在7—20KN/mm2之间,而其他切削加工的单位切削力kc值均在7KN/mm2以下。
(2)三向分力中切深为Fp值最大:原因同上。
在正常磨削条件下,Fp/Fc的比值约为2.0—2.5,而且工件材料的塑性越小,硬度越大时,Fp/Fc的比值越大(见表14—7)。
在磨削深度(切深)很小和砂轮严重磨损致使磨粒刃区圆弧半径增大时,Fp/Fc的比值可能加大到5—10。
(3)磨削力随不同的磨削阶段而变化:由于Fp较大,使机床、工件和夹具产生弹性变形。
在开始的几次进给中,实际径向进给量frac远远小于名义径向进给量frap,即frac<frap。
随着进给次数的增加,工艺系统的变形抗力也逐渐增大,这时实际的径向进给也逐渐增大,直至变形抗力增大到等于名义的径向磨削力Fpap时,实际径向进给量才会等于名义值。
这一过程可用图14—16中的0A一段曲线来表示,称为初磨阶段。
在初磨阶段中,frac<frap。
若机床、工件和夹具的刚度越低,则此阶段越长。
此后,当frac=frap时,即进入稳定阶段AB。
当余量即将磨完时,就可停止进给进行光磨,以提高表面质量,图中BC一段称为光磨阶段。
由上述可知,要提高生产率,就必须缩短韧磨阶段及稳定阶段的时间,即在保证质量的前提下,可适当增加径向进给fr;要提高已加工表面质量,则必须保持适当的光磨进给次数。
二、磨削力及磨削功率
前已述及,磨削过程是磨粒在工件表面上进行滑擦、耕犁和切屑形成的过程。
由于磨削速度很高,所以摩擦在磨削过程中所消耗的能量占的比例相当大。
试验表明:干磨退火碳素钢时,材料剪切所消耗的能量占20%—30%,摩擦所消耗的能量占70%—80%。
所以在磨削力的公式中应能反映出滑擦力的影响。
磨削力的公式表示如下:
(14—9)
(14—l0)
式中Fc、Fp——分别为切向和径向磨削力,N;
Vw—工件速度,m/s;
Vc—砂轮速度,m/s;
fr—径向进给量,mm;
B——磨削宽度,mm;
CF—切除单位面积的切屑所需的力,N/mm2(表14—8);
α—假设磨粒为圆锥形时的锥顶半角;
μ—工件和砂轮间摩擦系数(表14—9)。
磨削功率Pm为:
Pm=Fc•Vc/1000KW(14—11)
式中Fc—一切向磨削力,N;
Vc—砂轮线速度,m/s。
三、磨削力的测试方法
磨削过程很复杂,影响磨削力因素很多,而对磨削的机理研究向有待深入,目前的磨削力计算理论公式精确度不高,所以一般都用实验方法来测定磨削力。
测定磨削力的方法很多,下面只介绍其中的一种。
图14—17所示为测定外圆磨削力的测定装置原理图。
此法是把工件支持在顶尖上。
由于顶尖的圆周上粘有电阻应变片,所以顶尖所受的磨削力可通过应变片的阻值变化而测出。
在工作中,切向磨削力使顶尖下弯,所以用1、2、3、4应弯片来测出Fc。
而径向磨削力是使顶尖前后弯曲,因此Fp可用5、6、7、8应变片测出。
上述电阻应变片式测力装置要进行精确的标定。