Tufting缝合复合材料预制体的成型与研究进展
复合材料的成型工艺

复合材料的成型工艺复合材料是指由两种或以上组分构成的材料,通过合理的配比和加工工艺,在性质上综合体现出超过单一组分材料的优良性能,具有较好的力学、物理、化学和生物性能等特点。
常见的复合材料有碳纤维复合材料、玻璃纤维复合材料、陶瓷基复合材料等。
手工层叠成型是最早应用的成型工艺之一,适用于一些特殊形状的复合材料构件的制作。
这种成型工艺的原理是将预浸料层叠在一起,然后经过压力和温度处理使其固化成形。
虽然这种成型工艺操作简单、成本较低,但其生产效率低,工艺控制和质量控制困难。
注塑是一种常用的复合材料成型工艺,广泛应用于汽车、航空航天、电子等领域。
其原理是将预制的纤维增强材料与树脂熔融混合,通过模具将混合物注入至需要的形状中,然后冷却固化。
挤出是一种制备复合材料的连续成型工艺,适用于纤维增强材料含量较高的构件的制备。
其原理是将纤维和树脂混合物挤出成型,通过模具成形后冷却固化。
这种成型工艺能够快速制备大批量的复合材料构件,成本相对较低。
压制是一种常见的复合材料成型工艺,适用于制备高精度、大尺寸的构件。
其原理是将预制的纤维增强材料与树脂层叠放置在模具中,在一定的温度和压力下进行压制成型,然后冷却固化。
压制工艺对模具的要求较高,但可以获得较高的成品质量。
浸渍是将纤维增强材料浸透在树脂中,然后通过挤压或真空吸取等方式使其充分饱和,然后进行固化成型的工艺。
这种成型工艺适用于复杂形状、大尺寸的构件制备,但对工艺环境要求较高。
自动层叠成型是一种用于制备大型、高强度和高精度的复合材料构件的成型工艺。
其原理是通过自动层叠机械将纤维增强材料与树脂按照设计要求进行层叠,并进行热压成型。
该工艺可以实现连续、高效的生产,但对设备的要求较高。
综上所述,复合材料的成型工艺多样,选择合适的成型工艺可以有效提高复合材料的成品率和质量。
不同的复合材料成型工艺在应用领域、成本、工艺控制等方面存在差异,需要根据具体需求进行选择。
复合材料缝合技术的研究及应用进展
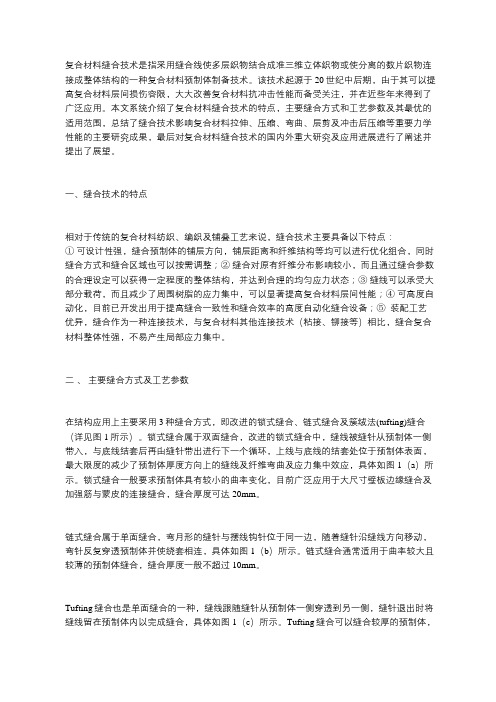
复合材料缝合技术是指采用缝合线使多层织物结合成准三维立体织物或使分离的数片织物连接成整体结构的一种复合材料预制体制备技术。
该技术起源于20世纪中后期,由于其可以提高复合材料层间损伤容限,大大改善复合材料抗冲击性能而备受关注,并在近些年来得到了广泛应用。
本文系统介绍了复合材料缝合技术的特点,主要缝合方式和工艺参数及其最优的适用范围,总结了缝合技术影响复合材料拉伸、压缩、弯曲、层剪及冲击后压缩等重要力学性能的主要研究成果,最后对复合材料缝合技术的国内外重大研究及应用进展进行了阐述并提出了展望。
一、缝合技术的特点相对于传统的复合材料纺织、编织及铺叠工艺来说,缝合技术主要具备以下特点:①可设计性强,缝合预制体的铺层方向,铺层距离和纤维结构等均可以进行优化组合,同时缝合方式和缝合区域也可以按需调整;②缝合对原有纤维分布影响较小,而且通过缝合参数的合理设定可以获得一定程度的整体结构,并达到合理的均匀应力状态;③缝线可以承受大部分载荷,而且减少了周围树脂的应力集中,可以显著提高复合材料层间性能;④可高度自动化,目前已开发出用于提高缝合一致性和缝合效率的高度自动化缝合设备;⑤装配工艺优异,缝合作为一种连接技术,与复合材料其他连接技术(粘接、铆接等)相比,缝合复合材料整体性强,不易产生局部应力集中。
二、主要缝合方式及工艺参数在结构应用上主要采用3种缝合方式,即改进的锁式缝合、链式缝合及簇绒法(tufting)缝合(详见图1所示)。
锁式缝合属于双面缝合,改进的锁式缝合中,缝线被缝针从预制体一侧带入,与底线结套后再由缝针带出进行下一个循环,上线与底线的结套处位于预制体表面,最大限度的减少了预制体厚度方向上的缝线及纤维弯曲及应力集中效应,具体如图1(a)所示。
锁式缝合一般要求预制体具有较小的曲率变化,目前广泛应用于大尺寸壁板边缘缝合及加强筋与蒙皮的连接缝合,缝合厚度可达20mm。
链式缝合属于单面缝合,弯月形的缝针与摆线钩针位于同一边,随着缝针沿缝线方向移动,弯针反复穿透预制体并使绕套相连,具体如图1(b)所示。
论复合材料成型工艺的发展-最新年文档

论复合材料成型工艺的发展一、复合材料成型工艺的概述根据复合材料的使用情况来看,质量较好的复合材料,性能、可设计性等都比较好,可以在医疗、化工等行业中得到合理应用。
一般在进行复合材料的成型工艺生产时,需要对制品的尺寸、性质、表面质量等给予高度重视,才能确保材料可以按照预设好的要求进行合理设置,从而保证制品的整体性能。
通过上述操作,结合面、增强材料能够很好的结合在一起,并将挥发出来的气体排出,最终有效降低制品的孔隙率。
但是,受到操作技能、操作人员专业水平等多种因素的影响,复合材料成型工艺生产过程会出现很多问题,大大降低制品的质量、性能等。
所以,根据制品的情况,做好生产前的准备工作,选择合适的工艺、设备等,才能真正降低生产陈本,最终满足各行业的发展需求。
二、常见的几种复合材料成型工艺对复合材料成型工艺进行全面分析发现,其与制品的使用效果、生产水平等有着直接联系,因此,必须根据制品的实际情况,选择最合适的复合材料成型工艺,才能达到制品的预期效果。
目前,最常见的几种复合材料成型工艺有如下几种:(一)模压成型工艺通常情况下,模压成型工艺是在预先加热过的模具内放入已经处理好的模压材料,然后将比较合适的压力施加到模压材料上,以确保模具内腔充满有模压材料,从而在一定温度下使模压材料被固化,最终将固化后的制品从模具内部取出,并进一步进行加工。
在整个生产过程中,很多因素都会给制品的质量带来不良影响,其中,压制工艺产生的影响最大。
目前,模压成型工艺有着生产效率快、尺寸非常精确、可大量生产、表面光滑与整洁等多种特点,因此,在中小型复杂制品的生产上非常适用。
但是,模具的设计、制造都有着较强复杂性,第一次进行模具制造需要较高的投资,并且,在受到设备限制的情况下,只能制作出比较小型的模具。
在先进技术不断推广的现代社会中,增强材料大部分变成了长短纤维,基础性材料基本上是热塑性、热固性树脂,从而促进上述符合材料模压成型工艺不断发展,不但可以提高制品的性价比、生产效率,还能减少环节污染,其中,树脂传递技术是非常重要的一种模压成型技术,在满足汽车、航天等多个领域的需求上有着重要影响。
复合材料长桁共固化成型工艺研究

复合材料长桁共固化成型工艺研究复合材料是一种人工合成材料,具有轻质、高强度、抗腐蚀、耐高温等优点,被广泛应用于航空、航天、汽车等领域。
长桁是一种承受纵向载荷的结构件,其制造质量和性能影响着飞机的安全和使用寿命。
本文将介绍复合材料长桁共固化成型工艺的研究进展和应用现状。
一、复合材料长桁的制造方法目前,复合材料长桁的制造方法主要有手工叠层法、自动叠层法、自动绕包法等。
其中,手工叠层法是最早采用的方法,其制造过程简单、成本低,但质量稳定性低,且生产效率低。
自动叠层法是在计算机辅助下进行生产,其精度和质量稳定性高,但需要昂贵的设备和技术人员支持。
自动绕包法适用于较小半径和复杂形状的零部件,但需要高度精细的控制,否则会影响其性能。
二、长桁共固化成型工艺的研究进展长桁共固化成型是一种新型复合材料制造工艺,采用预先制作好的长桁芯、复合材料薄板和粘合剂组成一体的芯腔模具,然后在芯腔中注入树脂粘合剂,将其固化形成一个整体。
这种工艺可以大大提高长桁的制造质量和生产效率。
为了探究长桁共固化成型工艺的制造工艺和性能,学者们开展了一系列的研究工作。
例如,进行了固化前和固化后的微观结构和力学性能的测试研究,采用数值模拟分析长桁复合材料的结构和性能,优化了模具结构和固化工艺等。
这些研究成果为长桁共固化成型工艺的发展提供了理论和数据支持。
三、长桁共固化成型工艺的应用现状长桁共固化成型工艺在飞机制造领域得到广泛应用,已经成为了复合材料整体成型的主流工艺之一。
例如,波音787客机采用了长桁共固化成型工艺,使该机的结构更加轻量化,采用环保性能更好的材料,大大降低了生产成本。
同时,国内也逐步推广并应用长桁共固化成型工艺。
中国商飞C919客机,长桁共固化成型工艺得到广泛应用,为中国的民机制造产业走向世界提供了技术支持和保障。
四、总结复合材料长桁共固化成型工艺的研究和应用推广,为提高飞机的安全性和性能、降低能耗和污染、推动民机制造产业的发展,发挥着重要的作用。
编织复合材料预制体铺覆成型的数值模拟

编织复合材料预制体铺覆成型的数值模拟王波;李昂;杨振宇【摘要】针对平面编织复合材料预制体在曲面铺覆过程中的局部变形,建立了三维有限元模型,利用商业有限元软件Abaqus模拟了预制体在铺覆成型过程中的纤维束变形规律.研究了0°和45°碳纤维织物在球面铺覆过程的变形过程和局部剪切变形.结果表明,纤维束之间的滑动和纤维束起皱是该预制体在球面铺覆过程中的典型变形模式.在0°织物的球形铺覆变形中,0°和90°纤维束的剪切变形角最小,45°方向纤维束的剪切变形角最大;在45°织物的铺覆变形中,0°和90°纤维束的剪切变形角最大,45°方向纤维束的剪切变形角最小.【期刊名称】《宇航材料工艺》【年(卷),期】2019(049)002【总页数】5页(P19-23)【关键词】编织复合材料;预制体;铺覆成型;有限元法【作者】王波;李昂;杨振宇【作者单位】中国航空工业集团有限公司防务工程部,北京100022;北京航空航天大学固体力学所,北京100083;北京航空航天大学固体力学所,北京100083【正文语种】中文【中图分类】TB30 引言编织复合材料在航空航天、船舶和汽车等领域具有非常广泛的应用。
随着结构的复杂程度不断提高,编织复合材料常常需要制备具有复杂曲率的三维结构,比如球面、锥面等[1]。
平面编织复合材料在纤维铺覆过程中,需要根据结构的形状对预制体施加预先的变形,因此铺覆过程中纤维的位置、纤维取向和局部纤维体积分数会重新分布。
复合材料内部的纤维分布和取向决定了各类载荷作用下的复合材料内部的传力路径,纱线束之间的相互作用形式也决定了复合材料的损伤和破坏机制[2]。
因此,获取预制体铺覆成型后纤维束的变形规律,对于认识最终复合材料结构的整体力学性能至关重要。
关于纤维预制体的在铺覆过程中的变形研究,受到国内外学者的广泛关注。
不规则平板预制体机器人辅助缝合路

不规则平板预制体机器人辅助缝合路径规划陈小明1,2,3,魏玉莹1,2,张一帆1,2,李皎1,2,陈利1,2(1.天津工业大学纺织科学与工程学院,天津300387;2.天津工业大学先进纺织复合材料教育部重点实验室,天津300387;3.天津工业大学机械工程学院,天津300387)DOI :10.3969/j.issn.1671-024x.2022.06.007第41卷第6期圆园22年12月Vol.41No.6December 2022天津工业大学学报允韵哉砸晕粤蕴韵云栽陨粤晕GONG 哉晕陨灾耘砸杂陨栽再收稿日期:2021-03-18基金项目:天津市科委科研计划项目(19JCTPJC45800);天津市教委科研计划项目(2018ZD13);天津高等教育创新团队项目(TD13-5043)第一作者:陈小明(1984—),男,高级实验师,博士,主要研究方向为纺织机器人装备及纺织复合材料。
E-mail :*************************.cn 通信作者:陈利(1968—),男,教授,博士生导师,主要研究方向为纺织复合材料。
E-mail :*******************.cn Robot-assisted stitching path planning for large-sized irregular flat preformCHEN Xiao-ming 1,2,3,WEI Yu-ying 1,2,ZHANG Yi-fan 1,2,LI Jiao 1,2,CHEN Li 1,2(1.School of Textile Science and Engineering ,Tiangong University ,Tianjin 300387,China ;2.Key Laboratory of Adva -nced Textile Composite Materials of Ministry of Education ,Tiangong University ,Tianjin300387,China ;3.School ofMechanical Engineering ,Tiangong University ,Tianjin 300387,China )Abstract :Aiming at the characteristics of a large number of stitching points and complex stitching paths for large-size ir鄄regular flat preforms袁a robot-assisted stitching path planning method suitable for large-size irregular flat pre鄄forms was designed.First袁the location design of discrete points and the batch output method of coordinates are studied曰further a CAD module for automatic sorting of discrete points and filtering of stitched points袁and a CAM module for robot program automatic generation based on Python are built曰finally袁the feasibility of the robot-as鄄sisted stitching path planning method was verified through the large-size irregular wing stitching experiment.The results show that discrete point design method袁discrete point coordinate batch output method袁automatic sorting of discrete point coordinates and filtering of stitched points CAD module袁and robot program automatic generating CAM module were feasible.The path planning method was efficient and reliable袁and it could be applied to large-size irregular flat preforms.The path planning method of large-size irregular flat preforms is universal袁andcan be extended to path planning of three-dimensional needle punching袁I fiber stitching and tufting forming oflarge-size irregular flat preforms.Key words :preform曰robot曰stitching曰path planning曰composites摘要:针对大尺寸不规则平板预制体缝合点数多且缝合路径复杂的特点,设计了一种适用于大尺寸不规则平板预制体的机器人辅助缝合路径规划方法。
多腔室复合材料结构件的气囊整体成型研究

多腔室复合材料结构件的气囊整体成型研究引言多腔室复合材料结构件是一种在工程应用中广泛使用的轻质高强材料,其制造过程中采用气囊整体成型技术能够实现复合材料结构件的良好成型效果。
本文将详细探讨多腔室复合材料结构件的气囊整体成型技术在制造过程中的关键问题和改进方法。
背景多腔室复合材料结构件是由多个腔室组成的结构体,以提供更好的结构刚度和耐力。
气囊整体成型是一种先进的制造技术,其基本原理是在复合材料结构件的内部放置气囊,并通过充气或者真空来实现整体成型。
气囊整体成型技术可以提高复合材料结构件的成型质量和生产效率,同时减少工艺复杂度和材料浪费。
气囊整体成型的优势•成型质量高:气囊整体成型过程中,气囊能够对复合材料进行均匀的外界压力施加,以达到更好的成型效果。
•生产效率高:气囊整体成型过程中,由于气囊能够提供内外压力,减少了复合材料结构件的梳理和复合工序,从而提高了生产效率。
•工艺简单:相对于其他制造方法,气囊整体成型的工艺流程较为简单,且适应性强,可适用于多种复合材料结构件的制造。
•材料利用率高:气囊整体成型过程中,气囊能够有效支撑复合材料,避免材料过度挤压或受损,从而提高了材料的利用率。
关键问题与改进方法在多腔室复合材料结构件的气囊整体成型过程中,存在一些关键问题,如气囊布置、成型工艺控制、气囊材料选择等,需要通过改进方法来解决。
气囊布置对于多腔室复合材料结构件,气囊的布置是非常关键的。
合理的气囊布置可以保证气囊能够对复合材料结构件进行均匀的外界压力施加,从而实现整体成型。
改进方法包括以下几点: 1. 根据复合材料结构件的形状和内部腔室的分布,合理确定气囊的形状和尺寸。
2. 采用多个气囊进行布置,以保证整体成型的均匀性。
3. 在气囊与复合材料结构件的接触面加装胶垫或硅胶等材料,增加气囊与复合材料结构件的粘附力,避免气囊在成型过程中移位。
成型工艺控制在气囊整体成型过程中,成型工艺的控制是关键的。
合理的成型工艺控制可以保证复合材料结构件的成型质量。
复合材料成型工艺方法及优缺点分析

复合材料成型工艺方法及优缺点分析
张小溪
【期刊名称】《科技与企业》
【年(卷),期】2014(000)018
【摘要】复合材料工业的基础和条件是复合材料成型工艺,复合材料应用的进一步拓宽,将使复合材料工业进入一个崭新的阶段。
热塑性复合材料是以玻璃纤维、碳纤维、芳纶纤维等增强各种热塑性树脂的总称,国外称Fiber Rinforced Thermo Plastics(简称FRTP)。
热固性复合材料是指在受热或其他条件下能固化或具有不溶(熔)特性的复合材料。
由于热塑性树脂和增强材料种类不同,其生产工艺和制成的复合材料性能差别很大。
复合成型工艺优点很突出,近十年在我国得到了快速发展但未能有重大突破,与其他发达国家相比还有距离。
【总页数】1页(P165-165)
【作者】张小溪
【作者单位】中国航空工业集团公司济南特种结构研究所 250023
【正文语种】中文
【相关文献】
1.复合材料小尺寸螺栓的成型工艺方法探讨
2.复合材料成型工艺方法的模糊综合评判
3.大型飞机复合材料结构相关成型工艺方法评述
4.复合材料成型工艺方法的研讨
5.复合材料尾梁蜂窝区避免凹陷成型工艺方法研究
因版权原因,仅展示原文概要,查看原文内容请购买。
复合材料的成型工艺ppt课件
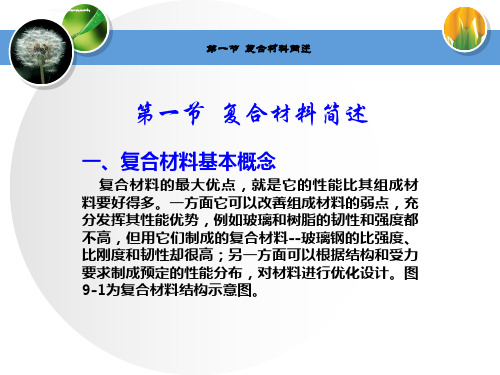
第二节 金属基复合材料(MMC)成形工艺
一、固态法
1.扩散黏结法(Diffusion Bonding) 如图9-2所示,扩散黏结是一种在较长时间、
较高温度和压力下,通过固态焊接工艺,使同类 或不同类金属在高温下互扩散而黏结在一起的工 艺方法。
2.形变法(Plastic Forming) 形变法就是利用金属具有塑性成型的工艺特点
2.复合材料的特点
(1)比强度和比刚度高 (2)抗疲劳性好 (3)高温性能好 (4)减振性能好 (5)断裂安全性高 (6)可设计性好
为 了 规 范 事 业单位 聘用关 系,建 立和完 善适应 社会主 义市场 经济体 制的事 业单位 工作人 员聘用 制度, 保障用 人单位 和职工 的合法 权益
第一节 复合材料简述
四 、 复 合 材 料 的 失 效 (Failure of Composite)
复合材料的失效一般是指其疲劳破坏过程。
1.制造加工损伤
此种损伤产生初始缺陷。,它包括:纤维铺设不 均,扭结、死扣等,树脂不均;纤维切断、错排; 固化不足;有孔隙、气泡;材质污染等。
2.使用引起的损伤
此种损伤导致缺陷发展。它包括:树脂裂纹或老 化;分层;纤维断裂;振动较大导致的纤维断裂; 温度变化较大;机加工产生内应力;碰撞等。
二、复合材料用原料
1.增强材料
(1)碳纤维(Carbon Fiber) (2)硼纤维(Boron Filament) (3)芳纶(Aramid Ring) (4)玻璃纤维(Glass Fiber) (5)碳化硅纤维(Silicon Carbide Fiber) (6)晶须(Whisker)
2.基体材料
3)基体能够很好地保护纤维表面,不产生表面 损伤、不产生裂纹。
复合材料预制体成形制造工艺与装备研究

纱梭口,引纬剑携多组填充纱穿过经纱梭口,捆绑
纱线穿过多组经 纱、填 充 纱 形 成 复 合 材 料 三 维 预
制体,所提方法可 用 于 制 造 异 形 截 面 的 复 合 材 料
图 2 三向正交复合材料预制体织造原理和设备 [22]
F
i
2 Pr
i
nc
三向正交预制体 的 细 观 结 构 中 无 纤 维 弯 曲,力 学
线波动排布 主 要 通 过 引 纱 管 来 实 现.KHOKAR
en
t
i
ngo
r
t
hogona
l
l
i
nd
i
ng,无 纤 维 交 织、正
yandb
交排列捆绑)织造 方 法,如 图 3 所 示,该 方 法 中 的
性能好.三向正交预制体包括经纱、填充纱、
与二维结构复 合 材 料 相 比,三 维 结 构 复 合 材
复合材料构件 [3].我国航空领域复合材料的应用
料具有层间性能好、抗冲击性能强、抗剪切性能强
料 用 量 可 达 到 12% ,预 计 国 产 大 型 宽 体 客 机
车片等关键 构 件 上 实 现 应 用 [5G9]. 三 维 复 合 材 料
OS
ID):
Re
s
e
a
r
chonFo
rmi
ng Manu
f
a
cHale Waihona Puke turi
ngTe
chno
l
o
i
to
f
gyandEqu
pmen
Compo
s
i
t
ePr
复合材料成型模具研究进展

复合材料成型模具研究进展复合材料因其轻质、高强度、耐腐蚀等优点而在航空、汽车、船舶等领域得到了广泛应用。
成型模具是复合材料制造的关键设备之一,其设计水平和制造质量直接影响到复合材料的制备效率和产品性能。
因此,对复合材料成型模具的研究具有重要意义。
本文将围绕复合材料成型模具的研究进展进行综述,主要涉及发展历程、研究现状、研究方法和发展趋势等方面。
早期复合材料成型模具通常是在金属或木板上进行手糊成型,随后逐步发展出了真空袋压成型、热压罐成型、树脂转移模塑(RTM)等多种成型技术。
随着计算机技术的进步,数字化模具设计逐渐成为主流,通过三维建模和仿真技术,实现了模具设计和生产的自动化与智能化。
目前,复合材料成型模具的研究主要集中在成型工艺、模具设计、生产流程等方面。
在成型工艺方面,研究人员针对不同种类的复合材料,开发了多种成型工艺,如手糊成型、真空袋压成型、热压罐成型、RTM、LFT等。
在模具设计方面,数字化模具设计技术已经得到了广泛应用,通过CAD、CAM等技术,实现了模具的高效设计与制造。
在生产流程方面,研究人员通过对生产流程的优化,提高了生产效率和降低了生产成本。
复合材料成型模具的研究方法包括传统的研究手段、现代的数值模拟方法、实验模态分析等。
传统的研究手段主要是通过试验和经验总结来指导模具设计和生产。
现代的数值模拟方法如有限元分析(FEA)和有限差分分析(FDA)等,可以帮助研究人员对模具设计和生产过程中可能出现的问题进行预测和优化。
实验模态分析则可以帮助研究人员了解模具的动态特性,为模具的优化设计提供依据。
随着科技的不断发展,复合材料成型模具的发展趋势主要体现在数字化、智能化、高效化等方面。
数字化技术使得模具的设计和制造过程更加精确、快速和高效。
智能化技术如人工智能和机器学习等的应用,使得模具的设计和制造过程更加智能和自动化。
高效化则要求在保证产品质量的前提下,尽可能提高生产效率和降低生产成本。
复材液体成型窗框预制体方案

link appraisement
上海飞机设计研究院
袁伟(1987-)男,江苏盐城人,硕士研究生,
本文针对复合材料窗框成型前的纤维预制体的设计与制造方案,提出四种不同的解决方案,并提出了自动铺缝
的最佳方案的观点。
在航空航天复合材料制造行业起到引领航空航天液体成型技术不断发展的作用。
如付诸现实将产生500
飞机全机共82个窗框计算,可以减重
图1 NCF布环向铺贴褶皱
图2 自动铺缝窗框预制体
自动铺缝技术类似,其具有纤维角度精度高,可设计性强,
自动化程度高等特点,适合批量生产制造。
同自动铺缝技术
相比,其同样存在较大的纤维设计难度以及面密度控制的问
题。
由于自动铺丝在Z向无缝线的连接,其预制体的稳定性
较差,可能会对纤维角度控制产生一定的不利影响。
(a)(b)(c)(d)
图3 He等离子体xz平面的电子温度图:
(a) Time =107 s; (b) Time = 10-6 s;(c) Time = 10−4s;(d) Time = 0.1 s.
(a)(b)(c)(d)
图4 He等离子体xz平面的气体温度图:
(a) Time = 0 s; (b) Time = 0.001 s;(c) Time = 0.01s; (d) Time = 0. 1s.。
Kevlar缝合复合材料的研究进展

Kevlar缝合复合材料的研究进展’艾涛王汝敏(西北工业大学应用化学系,西安710072)摘要Kevlar缝合复合材料具有良好的层间断裂韧性和高的抗冲击损伤容限,显示出广阔的应用前景。
介绍了Kevlar缝合复合材料的制备技术,综述了其测试方法、缝合工艺参数对复合材料性能的影响及其应用的研究进展。
关键词复合材料Kevlar缝合性能综述ProgressinStitchedCompositeswithKeVlarYarnsAITaoWANGRumin(DepartmentofAppliedChemistry,NorthwesternPolytechnicalUniversity,Xi’an710072)AbstractStitchedcompositeswithKevlaryarnsnotonlypossessgoodinterlaminarfracturetoughness,butalsoexhibithighimpactdamagetolerance.Therefore,theyhavewidepotentialapplications.Inthispaper,thefabri~catingtechnologyofstitchedcompositesisintroduced.Theirtestmethods,applicationsandtheeffectofstitchingpa~rametersoncompositespropertiesarealsoreviewed.1【eywOrdscomposites,Kevlar,stitched,properties,review0引言1制备技术传统的纤维增强树脂复合材料层板加工费用高、层间强度低、层间断裂韧性差以及抗冲击损伤容限低。
例如碳纤维增强环氧树脂复合材料(CFRP),在面内主方向的拉伸强度为500~800MPa,而层间拉伸强度却只有20~30MPa[1]。
复合材料液体成型工艺的发展及应用

复合材料液体成型工艺的发展及应用下载提示:该文档是本店铺精心编制而成的,希望大家下载后,能够帮助大家解决实际问题。
文档下载后可定制修改,请根据实际需要进行调整和使用,谢谢!本店铺为大家提供各种类型的实用资料,如教育随笔、日记赏析、句子摘抄、古诗大全、经典美文、话题作文、工作总结、词语解析、文案摘录、其他资料等等,想了解不同资料格式和写法,敬请关注!Download tips: This document is carefully compiled by this editor. I hope that after you download it, it can help you solve practical problems. The document can be customized and modified after downloading, please adjust and use it according to actual needs, thank you! In addition, this shop provides you with various types of practical materials, such as educational essays, diary appreciation, sentence excerpts, ancient poems, classic articles, topic composition, work summary, word parsing, copy excerpts, other materials and so on, want to know different data formats and writing methods, please pay attention!1. 引言在当今工业领域中,复合材料液体成型工艺因其独特的优势和广泛的应用而备受关注。
复合材料液体成型工艺的发展及应用

玻璃钢2019年第1期复合材料液体成型工艺的发展及应用徐竹(西安航空职业技术学院,陕西西安710089)复合材料液体成型工艺也称液体模塑成型技术(Liquid Composite Molding,简称LCM)是指将液态树脂注入铺有纤维预成型体的闭合模腔中,或加热熔化预先放入模腔内的树脂 膜,液态树脂在流动充满模腔的同时完成纤维/树脂的浸润并经固化脱模后成为复合材料制 品的一种成型工艺。
与其他纤维复合材料制造技术相比,LC M技术可生产的构件范围广,可按结构要求定向 铺放纤维,一步浸渍成型带有夹芯、加筋、预埋件等的大型构件。
LC M可以实现复合材料设 计、制备的一体化;既可制备大型整体复合材料制件,又可制备各种小型精密复合材料制件;既能显著缩短制件生产周期,又可保证制件的整体质量。
20世纪80年代后,随着飞行器的 承力构件及次承力构件、国防应用、汽车结构件以及高性能体育用品等的开发,RTM工艺取 得了显著的进展,并且在此基础上开发了 VARTM、SCRIMP、RFI、SRIM等这些先进的L C M工 艺技术。
1树脂传递模塑(RTM)成型工艺树脂传递模塑成型简称RTM(Resin Transfer Molding),是一种闭模成型技术,可以生 产出两面光的制品。
它的基本原理是先在模腔内预先铺放增强材料预成型体、芯材和预埋件,然后在压力或真空作用下将树脂注入闭合模腔,浸润纤维,经固化、脱模、后加工而成制品 的工艺。
随着材料技术和工艺的不断发展,R TM工艺制品已经在航空航天、交通运输、体育 用品、船舶、建筑等领域得到了广泛应用。
RTM在航空航天和军事领域的应用主要体现大型 结构部件的整体成型方面,国外R T M成型技术在航空航天领域的应用主要有雷达罩、螺旋桨、隔舱门、直升机的方向舵、整体机舱、飞机的机翼等。
R T M成型技术在舰船和装甲车辆上的 应用主要有舰船的防护板、船舶结构件及装甲战车的车体等部件。
复合材料缝合技术的研究进展

复合材料 内 部 纤 维 的 弯 曲 损 伤 受 缝 合 线 直 径 影 响 较
铺层纤维
大,直径增加,纤 维 弯 曲 损 伤 也 会 增 加,在 被 缝 合 件 内
支撑材料
线环
(
c)
图 2 单边缝合
部缝线处形成富树脂区,从而导致被缝合件拉伸、压 缩
以及形状较为特别的结构件,此外,缝合作为一种无 需
外部部件连接的 连 接 技 术,在 实 现 轻 质 化 的 同 时 还 使
材料的完整性更好。最后可通过树脂传递模塑成形 等
方式将缝合后的预制件进行固化。
(
b)
图 1 双边缝合
(
c)
图 1(
a)为锁式缝 合,底 层 线 与 表 面 线 相 交 于 被 缝
进展与述评
·3·
2021 年第 11 期
缝合复合材料的力学性能受缝合技术的影响较大。
合三维编织复合 材 料 弯 曲 性 能 研 究 中 发 现:复 合 材 料
3
.1 拉伸强度
的弯曲强度随缝 合 密 度 的 增 加 而 增 大,但 当 编 织 角 为
文章编号:
1673-0356(
2021)
11-0001-04
绍了双边缝合与单边缝合 2 种缝合方式。
1
.1 双边缝合
船只、机械工程、化工及公共基础设施等多方面起到 了
双边 缝 合 有 两 条 线 分 为 上 表 面 线 和 底 层 线,上 表
。随 着 应 用 规 模 不 断 扩 展,传 统 纤 维 增 强
1)缝 合 过 程 中 弯 针 只 在
被缝合件内部进 行 操 作,并 不 需 要 为 其 空 出 支 撑 操 作
复合材料的成型工艺与技术创新
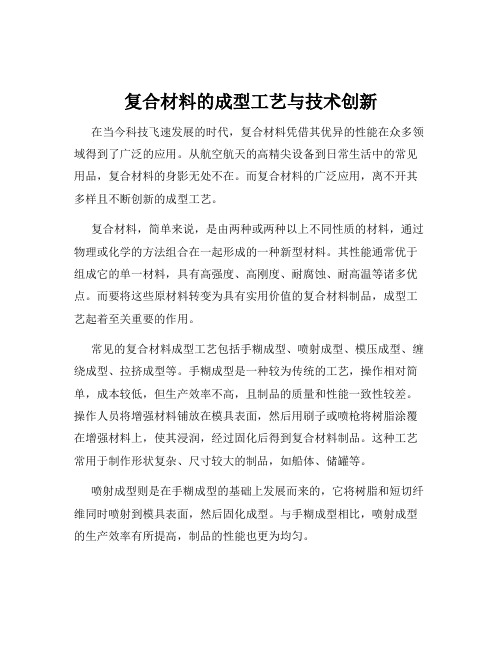
复合材料的成型工艺与技术创新在当今科技飞速发展的时代,复合材料凭借其优异的性能在众多领域得到了广泛的应用。
从航空航天的高精尖设备到日常生活中的常见用品,复合材料的身影无处不在。
而复合材料的广泛应用,离不开其多样且不断创新的成型工艺。
复合材料,简单来说,是由两种或两种以上不同性质的材料,通过物理或化学的方法组合在一起形成的一种新型材料。
其性能通常优于组成它的单一材料,具有高强度、高刚度、耐腐蚀、耐高温等诸多优点。
而要将这些原材料转变为具有实用价值的复合材料制品,成型工艺起着至关重要的作用。
常见的复合材料成型工艺包括手糊成型、喷射成型、模压成型、缠绕成型、拉挤成型等。
手糊成型是一种较为传统的工艺,操作相对简单,成本较低,但生产效率不高,且制品的质量和性能一致性较差。
操作人员将增强材料铺放在模具表面,然后用刷子或喷枪将树脂涂覆在增强材料上,使其浸润,经过固化后得到复合材料制品。
这种工艺常用于制作形状复杂、尺寸较大的制品,如船体、储罐等。
喷射成型则是在手糊成型的基础上发展而来的,它将树脂和短切纤维同时喷射到模具表面,然后固化成型。
与手糊成型相比,喷射成型的生产效率有所提高,制品的性能也更为均匀。
模压成型是一种高效、高精度的成型工艺。
将预浸料或模塑料放入预热的模具中,然后在压力和温度的作用下,使其固化成型。
模压成型制品的尺寸精度高、表面质量好,适用于生产大批量的中小型制品,如汽车零部件、电器外壳等。
缠绕成型主要用于制造圆柱形或球形的制品,如管道、储罐等。
将连续的纤维或带材经过浸胶后,按照一定的规律缠绕在芯模上,然后经过固化得到制品。
这种工艺能够充分发挥纤维的强度,制品的强度和刚度较高。
拉挤成型则是将连续纤维通过浸胶装置浸渍树脂后,在牵引力的作用下通过成型模具,经过固化得到连续的型材。
拉挤成型制品的性能稳定,生产效率高,适用于生产各种截面形状的型材,如工字梁、槽钢等。
随着科技的不断进步和市场需求的不断变化,复合材料的成型工艺也在不断创新。
复合材料预制体单边缝合技术研究进展

复合材料预制体单边缝合技术研究进展
董九志;耿争言;王立文;陈云军;蒋秀明
【期刊名称】《航空制造技术》
【年(卷),期】2022(65)16
【摘要】为更好地了解复合材料预制体单边缝合技术的研究现状,介绍了单边缝合技术的优点,简述了不同单边缝合方式的发展和应用。
对不同单边缝合方式的成型工艺和特点进行介绍,描述了已有的4种单边缝合方式的适用范围,分析了当前单边缝合技术在发展过程中存在的问题,方便研究人员有针对性地开展后续研究工作,推进单边缝合技术的高效化、智能化发展。
最后,分析了影响复合材料预制体单边缝合技术的发展因素,展望了复合材料预制体单边缝合技术的发展趋势。
【总页数】8页(P46-53)
【作者】董九志;耿争言;王立文;陈云军;蒋秀明
【作者单位】天津工业大学机械工程学院;西安航天复合材料研究所;天津工业大学电气工程与自动化学院
【正文语种】中文
【中图分类】TB3
【相关文献】
1.Tufting缝合复合材料预制体的成型与研究进展
2.缝合技术在复合材料液体成型预制体中的应用研究
3.复合材料预制体单边弯针缝合装备技术研究
4.碳/碳复合材
料预制体单边双针缝合工艺研究及改进5.复合材料单边缝合机械手线迹稳定成型技术研究
因版权原因,仅展示原文概要,查看原文内容请购买。
- 1、下载文档前请自行甄别文档内容的完整性,平台不提供额外的编辑、内容补充、找答案等附加服务。
- 2、"仅部分预览"的文档,不可在线预览部分如存在完整性等问题,可反馈申请退款(可完整预览的文档不适用该条件!)。
- 3、如文档侵犯您的权益,请联系客服反馈,我们会尽快为您处理(人工客服工作时间:9:00-18:30)。
研究论文RESEARCH复合材料预制体是指由连续长丝纤维或短切纤维通过纺织、编织或树脂等有机物复合等方法制成的具有特定结构的纤维预成形体[1]。
预制体是复合材料的骨架,预制体的结构对复合材料的致密化过程和各项性能均有重要的影响。
预制体成型方式决定着预制体的结构,按照复合材料预制体的成型方式,预制体可以分为2D 铺层预制体、2.5D 针刺预制体、3D 编织预制体、和缝合预制体等。
2D 铺成结构预制体z 向无增强纤维,复合材料层与层之间靠基体连接,层间抗剪切能力差,易产生裂纹分层;针刺预制体制备过程自动化程度高,但针刺只能在复合材料z 向引入短切纤维,而且针刺过程中,刺针上的倒钩会损伤面内纤维,降低复合材料的面内力学性能;预制体编织技术虽然可以在复合材料厚度方向引入连续纤维,但自动化程度低,预制体制备周期长;缝合技术是采用缝合线使二维织物构成准三维立体织物或使分离的数块织物连接成整体结构的技术[2]。
一方面,缝合技术能够将具有不同结构的纤维预制体连接在一起,形成整体结构;另一方面,缝合可以有效地引入z 向连续纤维,提高材料的层间性能。
缝合设备目前已实现自动化运行,预制体制备效率高。
缝合技术的最初应用是在1980年,通过缝纫技术Tufting 缝合复合材料预制体的成型与研究进展刘苏骅,李崇俊,嵇阿琳(西安航天复合材料研究所,西安 710025)[摘要] 缝合技术能够在复合材料厚度方向上引入连续纤维,改善复合材料的层间性能。
Tufting 缝合是一种新型单边缝合技术,通过将缝合机头与先进的高精度的机器人连结,提高了缝合过程的精度与灵活性。
介绍了Tufting 缝合预制体的成型过程、缝合参数及缝合对复合材料力学性能的影响。
关键词: Tufting 缝合;预制体;复合材料Manufacture and Advances of Tufting Composite PreformLIU Suhua, LI Chongjun, JI Alin( Xi’an Aerospace Composite Materials Research Institute, Xi’an 710025, China )[ABSTRACT] Continuous fibers can be inserted through thickness of materials by tufting, which improve interlaminar properties of composites. As a novel one-sided stitching technology, tufting robots make stitching process more accurate and flexible. Tufting process, parameters, and composites properties affected by tufting are introduced. Keywords: Tufting; Preform; Composite DOI: 10.16080/j.issn1671-833x.2017.14.088来缝合层合板预浸料达到提高材料损伤容限的目的[3]。
之后在美国波音公司与兰利研究中心联合开展的先进复合材料技术项目的支持下,自动化结构缝合连接技术得到大力发展[4]。
早期的自动化缝合采用双边缝合结构,缝合设备规模大,缝合技术并没有得到广泛应用。
为了克服传统缝合技术的限制,Alitin Nathechnik 生产了新型的单边Tufting 缝合设备[5]。
Tufting 缝合设备将缝合过程集成于缝合机头内,并将缝合机头与具有多自由度的高精度机器人连结,从而使得缝合预制体的形状与尺寸不再受设备的限制。
Tufting 缝合能够灵活地向复合材料z 向引入连续增强纤维,使得复合材料具有优良的层间力学性能,是一种简单、低成本的三维预制体成型技术。
1 Tufting 缝合预制体的制备缝合可以分为双边缝合与单边缝合。
锁式缝合、改进的锁式缝合和链式缝合属于双边缝合。
双边缝合原理类似于家用缝纫机,是从预制体两边通过底线和面线的配合进行缝合,面线由缝针带入后被底线固定,缝合线上存在张力。
单边缝合技术包括两针的ITA (Institute of Textiles, University RWTH Aachen)缝合[6]、OSS ®(One-Sided Stitching, Alitin Nathechnik GmbH) 缝合[7]、研究论文RESEARCH弯针(Blind Stitching, KSL)缝合[8]与Tufting(single-sided tufting, German Aerospace Center and KSL)缝合[9],依次为图1中(a)、(b)、(c)、(d)。
单边缝合技术除了缝合结构不同外,能缝合的预制体厚度方面也存在着差异。
ITA 最大可缝厚度最小仅为8mm,弯针缝合、OSS 和Tufting 缝合最大可缝厚度分别为10mm,20mm 和40mm。
Tufting 缝合属于单边无底线缝合,相比于传统的双边缝合,Tufting 缝合可只从预制体的一边进行缝合,缝合过程受预制体或芯模形状的影响小,对规则的平面或结构复杂的异形面、回转体等均可进行缝合。
预制体表面沿缝合轨迹留有面线,在底部留有缝合环,但无底线穿过缝合环锁定缝合线,缝合线上几乎不存在张力。
缝合时,先将铺好的干纤维布或预制体固定在支撑材料上,之后通过机器人控制面板调用缝合程序,使缝合机器人控制缝合机头在预制体上表面沿一定的轨迹进行缝合。
缝合针将缝合线沿铺纤维层厚度方向插入铺层干纤维布或预制体,缝合线通过与铺层纤维或支撑材料之间的摩擦力被固定在预制体内部,缝合线可以完全穿透或部分穿过铺层预制体,也可与预制体表面垂直或成一定的角度[10]。
压脚可以起到固定上一针缝合线与压实预制体的作用。
图1(e)为Tufting 缝合预制体结构单元示意图。
缝合可以在预制体厚度方向上引入连续准直纤维,见图2,但对面内纤维有挤开作用,在缝合线周围存在孔隙。
Tufting 原本是一种传统的地毯制造技术,现如今作为一种材料厚度方向增强技术,在轻工与复合材料领域开始被应用[11]。
Tufting 缝合设备现在已经是一种商业化制造的产品,通过专用的机器人语言编程并与硬件交互,可以实现直线、圆弧或圆周的缝合。
针、压的脚和传动轴由3个独立的伺服电机分别控制,通过齿轮与齿条之间的配合来运动,缝合精度高[10]。
针、压脚和传动轴末端配备了接近开关,通过机电配合,向控制中心反馈缝合的位置信息,辅助控制针、压脚和传动轴在一定的范围内运动。
虽然通过编程可以在一定精度范围内控制缝合过程,但机头内的针和压脚却是通过齿轮与齿条间的机械配合实现运动的,因此在大范围使用Tufting 缝合时,存在理论预测与实际位置之间的偏差。
2 Tufting 缝合过程可控参数缝合复合材料的性能与大量的过程参数有关,涉及了缝合线张力、纤维体积含量、缝合针的类型、缝合线的图1 单边缝合预制体结构Fig.1 Structure of one-sided stitching preform铺层纤维铺层纤维铺层纤维铺层纤维支撑材料支撑材料支撑材料支撑材料压脚缝合针缝合针缝合环缝合线缝合线铺层纤维孔隙缝合线(a )ITA 缝合(d )Tufting 缝合(b )OSS 缝合(e )单边缝合结构(c )弯针缝合yx图2 Tufting缝合预制体结构Fig.2 Structure of tufting preform研究论文RESEARCH类型(直径、刚度、强度)、铺层预制体的性能以及缝合过程的工艺参数(速度、花样)等。
由于参数众多,本文仅就缝合针、缝合线与铺层纤维、支撑材料、缝合密度4个方面进行概述。
2.1 缝合针缝合针对于Tufting缝合过程来说至关重要。
与传统的缝纫针不同,Tufting缝合针眼是倾斜的,这有利于退针时拔出缝合针(图3)。
缝合针眼后存在一个C型的通道,当缝合针刺入铺层纤维或预制体时,缝线由线轴拉出,穿过摩擦力极小的金属通道,当缝合针退针时,缝合针眼前端存在的凸出结构使针眼前端的纤维与铺层纤维之间紧密接触,让缝合线与周围纤维的摩擦力远大于C型通道内,从而通过摩擦力将纤维保留在铺层预制体内部。
缝合针表面光滑,下针时与面内间的纤维摩擦力很小,能够轻易地将面内纤维挤开而不是刺断,对面内纤维的损伤较少。
缝合针可与预制体表面垂直缝合,也可以与预制体表面成一定的角度(45°~135°)进行缝合。
2.2 缝合线与铺层纤维缝合线不但需要满足复合材料所要求的性能,而且要便于缝合工艺的实施。
在缝合过程中,缝合线与喂线装置之间存在着机械摩擦,使得缝合线起毛,在机器或缝合针狭窄处形成堵塞,导致喂线不畅,缝合线难以留在预制体中。
除此之外,缝合线会在缝合针眼端处弯折,碳纤维等脆性纤维缝合线易于在此处发生断裂。
缝合线加捻可以提高缝合线的耐磨损性能。
加捻可以起到压紧纱线的作用,并且加捻后的缝合线能够有效地抵抗纤维因弯折、剐擦而造成的损伤。
加捻后由于纤维弯曲,纤维强度和模量都会有明显下降(表1)。
缝合线上浆也可以缓解缝合线与喂线装置之间的摩擦起毛现象[12]。
铺层纤维的选取对于复合材料层面内力学性能具有较大的影响。
当铺层纤维松散排列时,面内纤维在缝针插入时,易被缝针挤开,缝合基本不会引起面内纤维的损伤;当铺层纤维紧密排列时,则会引起明显的纤维损伤。
缝合材料的厚度应当在2~35 mm之间。
一般来说,针织织物不适用于Tufting缝合技术,因为其内部连锁排列的纱线会阻碍缝合针的插入。
平纹或缎纹织布易于缝合,无纬布铺层是最理想的铺层结 构[12]。
2.3 缝合密度通过缝合引入z向纤维可以改善复合材料层间性能。
但缝合密度过大,缝合所引起的面内纤维的屈曲与损伤反而会引起面内力学性能的下降,因此缝合密度存在最优值。
图4是缝合结构单元示意图,S x, S y分别代表缝合针距与行距,S x可取3~18 mm,S y可取2~10mm。
2.4 支撑材料的选取合适的支撑材料对于缝合过程是十分重要的。
当缝针完全穿透预制体时,预制体底面的支撑材料应当具备易于缝合针的刺入和能够有效保留缝合线的作用。
选择合适的支撑材料对于缝合预制体的自动化操作是非常重要的:不合适的支撑材料不能有效地保留缝合线,使得缝合线在缝合针拔出时被带出,导致预制体不能被缝透。
发泡材料具有足够的刚度可用于缝合复合材料的支撑,同时,泡沫材料具有足够的弹性,有利于缝合针拔出时留住缝合线。
常用的发泡材料有适合于缝合平板的发泡硅和适合于缝合回转体的闭孔发泡塑料Airex®R63等。