材料课件铸造讲稿
[课件]铸造基础知识讲座PPT
![[课件]铸造基础知识讲座PPT](https://img.taocdn.com/s3/m/159729324431b90d6c85c7b4.png)
1)结构钢、不锈钢、耐热钢熔模铸件允许的缺陷 2)铝合金熔模铸件允许缺陷 9、低倍组织检查 10、铸钢件表面脱碳层检查 11、密封性检验 四、铸件缺陷的修补 1、铸件的补焊 2、浸渗处理
3、热等静压处理
五、熔模铸件结构设计 1、熔模铸件结构工艺性要求
2、熔模铸件结构要素
1)壁厚 2)铸造圆角 3)壁的连接
入 库
回浇 用冒 口 及 废 品
图2熔模铸造工艺流程框图
2、石膏型熔模铸造
目前我们仅用此方法生产铝合金铸件。利用石膏型散热慢,石膏
浆料复制性能好的特点,在真空条件下浇注薄壁、复杂、整体、精密
的铸件。此种方法仍属熔模铸造,只是用灌注石膏浆料形成铸型代替
熔模铸造中的重复数次涂料、撒砂形成壳型,其工艺流程和熔模铸造
8)压铸机、压铸模投资大。
二、铸件材料的选用
铸造过程是金属液充填型腔并在铸型内冷却凝固得到铸件的过程。由于液 态金属与铸型相互作用及随后的冷却凝固,总是伴随着产生一系列物理化学变 化,如金属液的结晶、偏析、析出气体、冷却收缩和应力的形成等。合金的铸 造性能是反映铸件成型过程中获得正确外形、健全内部质量难易程度的性能, 它主要包括合金的流动性、收缩率和抗热裂性等。 在选择合金种类时,除了铸造性能之外,还应兼顾到合金的热处理、机械 加工、焊接、矫正等工艺性能。 常用的铸造合金有铸钢、铸铁、铸造高温合金、铸铜、铸铝、铸镁、铸基础知识
一、铸造方法简介 1、熔模铸造 2、熔模石膏型铸造 3、金属型铸造
4、压力铸造
二、铸件材料的选用 三、铸造缺陷和铸件质量检验
1、铸造缺陷种类
a.多肉类缺陷 b.孔洞类缺陷
c.裂纹、冷隔类缺陷 d.表面缺陷
e.残缺类缺陷 f.形状及重量差错类缺陷 g.夹杂类缺陷 h.性能、成分、组织不合格 2、铸件质量标准 3、熔模铸件尺寸公差 4、铸件粗糙度的评定方法 5、力学性能检验 6、铸件表面和近表面缺陷的检验 7、熔模铸件允许存在的表面和近表面缺陷 8、X射线透照熔模铸件内部允许的缺陷
材料成型工艺基础之铸造培训课件(ppt 75张)
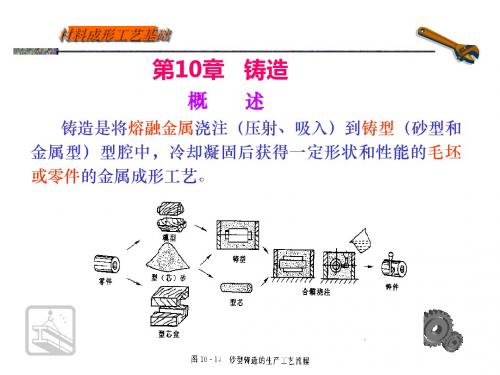
材料成形工艺基础
10.2 砂型铸造
一、砂型铸造的生产过程
材料成形工艺基础
二、砂型铸造工艺过程
1.造型
1) 手工造型
2) 机器造型 3) 造芯 4) 涂料 5) 开设浇注系统 6) 合型
2.熔炼与浇注 3.落砂与清理
材料成形工艺基础
二、工艺过程简介 1.造型: 手工造型——整模造型、分模造型、挖砂造型、假箱造型、 三箱造型。 机器造型——(紧砂特点)压实式、分模式、震压式、抛砂 紧实、射砂紧实。 造芯——芯盒造芯。用于孔下某些局部外形砂芯中有芯首, 砂芯烘干。 涂料——耐火材料、黏结材料、悬浮稳定剂等组成,涂刷 铸型,型芯表面。防止铸件粘砂、夹砂、砂眼等缺陷。 开设浇注系统——图10-16。开设浇铸系统的目的为了填充 型腔和冒口的一系列通道。 合型(合箱)——将上下箱、型芯等组合成完整的铸型。
材料成形工艺基础
三、压力铸造
液态金属在高压作用下快速压入金属铸型中,并在压力下结 晶,以获得铸件的成形工艺方法。 1. 压铸机和压铸工艺过程
材料成形工艺基础
2. 压力铸造的特点和适用范围 (1) 铸件的尺寸精度和表面质量最高。公差等一般为 IT11~IT13级,Ra为3.2~0.8μm。 (2) 铸件的强度和表面硬度高。抗拉强度可比砂型铸造
三、铸造内应力及铸件的变形、裂纹
铸件在凝固以后的继续冷却过程中,其固态收缩受到阻碍 或铸件各部分互相牵制,铸件内部将产生内应力。 1.热应力 热应力是由于铸件壁厚不均匀,各部分冷却速度不同,以 致在同一时期内铸件各部分收缩不一致而引起的应力。 热应力使铸件的厚壁或心部受拉伸,薄壁或表层受压缩。
材料成形工艺基础
材料成形工艺基础
(2) 冷裂 冷裂的特征是:裂纹细小,呈连续直线状,缝内有金属 光泽或轻微氧化色。 冷裂的防止: 1)使铸件壁厚尽可能均匀; 2)采用同时凝固的原则; 3)对于铸钢件和铸铁件,必须严格控制磷的 含量,防止冷脆性。
《铸造基础知识培训》课件
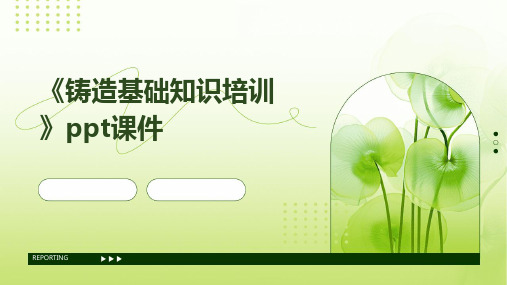
特种铸造
特种铸造是一种特殊的铸造方法,它 使用非传统的方法和材料来生产铸件 。
特种铸造的缺点是成本较高,技术要 求较高,需要专业的技术和设备支持 。
特种铸造的优点是可以生产出传统铸 造方法难以制造的复杂、高性能的铸 件,同时还可以提高铸件的质量和性 能。
铸造工艺流程
铸造工艺流程包括熔炼、 浇注、冷却、落砂、清理
等步骤。
浇注是将熔化的金属液注 入模具中,形成铸件。
落砂是将凝固后的铸件从 模具中取出,并进行清理
和加工。
熔炼是将金属加热至熔化 成液态,然后进行精炼和
除渣。
冷却是指铸件在模具中冷 却凝固的过程。
清理是去除铸件表面上的 残渣和毛刺,保证铸件的
质量和外观。
PART 04
铸造缺陷与质量控制
REPORTING
脱模剂
用于使铸件易于从铸型中 脱出,如石墨粉、滑石粉 等。
PART 03
铸造工艺
REPORTING
砂型铸造
砂型铸造是最常见的铸造方法 之一,它使用砂型作为模具来 生产铸件。
砂型铸造的优点是成本低、工 艺成熟、适用范围广,可以生 产各种形状和尺寸的铸件。
砂型铸造的缺点是生产周期较 长,需要经过多个步骤才能完 成一个铸件,且生产效率相对 较低。
THANKS
感谢观看
REPORTING
铸造技术的未来展望与挑战
智能化铸造
将人工智能、大数据等技术与铸 造工艺相结合,实现铸造过程的 智能决策和自动化控制,提高生
产效率和产品质量。
绿色铸造
发展环保、节能、低碳的铸造技 术,降低铸造过程的环境污染和
资源消耗,实现可持续发展。
高性能材料铸造
研究和发展高性能、高强度的新 型铸造材料,满足高端装备和新
PPT讲稿(铸造)
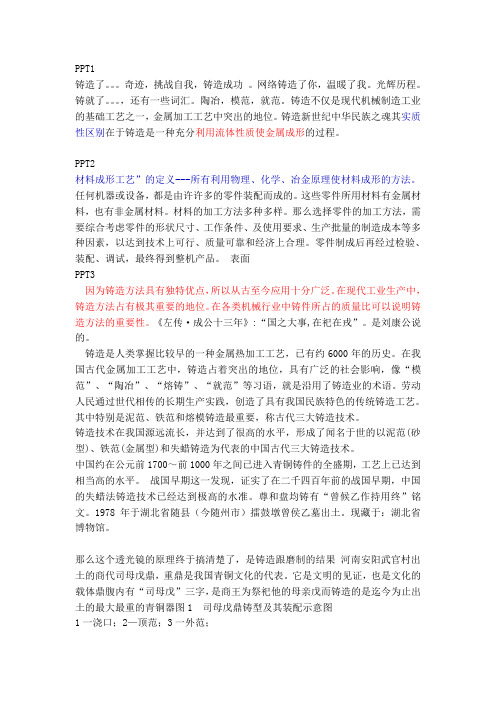
PPT1铸造了。
奇迹,挑战自我,铸造成功。
网络铸造了你,温暖了我。
光辉历程。
铸就了。
,还有一些词汇。
陶冶,模范,就范。
铸造不仅是现代机械制造工业的基础工艺之一,金属加工工艺中突出的地位。
铸造新世纪中华民族之魂其实质性区别在于铸造是一种充分利用流体性质使金属成形的过程。
PPT2材料成形工艺”的定义---所有利用物理、化学、冶金原理使材料成形的方法。
任何机器或设备,都是由许许多的零件装配而成的。
这些零件所用材料有金属材料,也有非金属材料。
材料的加工方法多种多样。
那么选择零件的加工方法,需要综合考虑零件的形状尺寸、工作条件、及使用要求、生产批量的制造成本等多种因素,以达到技术上可行、质量可靠和经济上合理。
零件制成后再经过检验、装配、调试,最终得到整机产品。
表面PPT3因为铸造方法具有独特优点,所以从古至今应用十分广泛。
在现代工业生产中,铸造方法占有极其重要的地位。
在各类机械行业中铸件所占的质量比可以说明铸造方法的重要性。
《左传·成公十三年》:“国之大事,在祀在戎”。
是刘康公说的。
铸造是人类掌握比较早的一种金属热加工工艺,已有约6000年的历史。
在我国古代金属加工工艺中,铸造占着突出的地位,具有广泛的社会影响,像“模范”、“陶冶”、“熔铸”、“就范”等习语,就是沿用了铸造业的术语。
劳动人民通过世代相传的长期生产实践,创造了具有我国民族特色的传统铸造工艺。
其中特别是泥范、铁范和熔模铸造最重要,称古代三大铸造技术。
铸造技术在我国源远流长,并达到了很高的水平,形成了闻名于世的以泥范(砂型)、铁范(金属型)和失蜡铸造为代表的中国古代三大铸造技术。
中国约在公元前1700~前1000年之间已进入青铜铸件的全盛期,工艺上已达到相当高的水平。
战国早期这一发现,证实了在二千四百年前的战国早期,中国的失蜡法铸造技术已经达到极高的水准。
尊和盘均铸有“曾候乙作持用终”铭文。
1978年于湖北省随县(今随州市)擂鼓墩曾侯乙墓出土。
铸造概述PPT课件

由于铸件结构不合理、浇注温度过低或冷却 过快等原因引起。
缺陷预防措施和补救方法
预防缩孔与缩松措施
改进铸件结构、降低浇注温度、 增加冒口补缩等。
预防裂纹措施
改进铸件结构、提高浇注温度、 控制冷却速度等。
预防气孔措施
控制型砂水分、烘干型芯、降 低金属液含气量等。
预防夹渣措施
提高型砂质量、改进浇注系统、 降低金属液含渣量等。
节能技术
采用先进的节能技术和设备,可以降低铸造过程中的能耗和排放, 提高能源利用效率和环保性能。
绿色材料
开发和应用绿色材料,如可再生材料、低污染材料等,可以减少 对环境的污染和破坏,促进可持续发展。
未来发展趋势预测
01 02
个性化定制
随着消费者需求的多样化,个性化定制将成为未来铸造发展的重要趋势 之一。通过数字化技术和3D打印技术等手段,可以实现快速、灵活的 生产个性化产品。
铸造概述ppt课件
contents
目录
• 铸造基本概念与分类 • 铸造材料选择与性能要求 • 铸造工艺流程及关键环节 • 典型铸造方法及设备介绍 • 铸件缺陷分析与防止措施 • 现代铸造技术发展趋势与展望
01
铸造基本概念与分类
铸造定义及作用
铸造定义
铸造是一种通过熔化金属或非金 属材料,并将其倒入模具中冷却 凝固,从而获得所需形状和性能 的工件的加工方法。
清理与检验标准
清理操作
去除铸件表面的型砂、芯砂、浇口、冒口等多余部分,使铸件表 面达到规定的粗糙度要求。
检验项目
对铸件进行外观检查、尺寸测量、化学成分分析、力学性能试验等 检验项目,确保铸件质量符合要求。
检验标准
根据铸件用途和重要性,制定相应的检验标准和质量等级要求,对 不合格的铸件进行返工或报废处理。
铸造课件论述可编辑全文
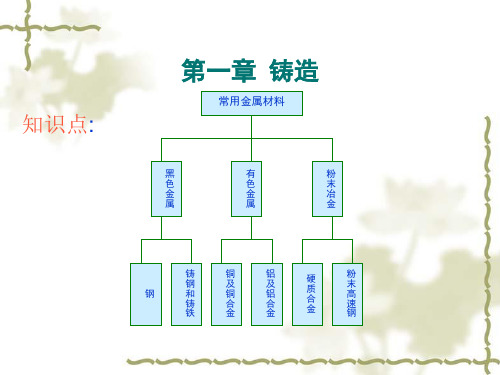
浇不足
冷隔
夹砂
气孔
夹渣
充型能力的决定因数
合金的流动性 铸型性质 浇注条件 铸件结构等
合金的充型能力
测试合金充型 能力的方法:
如右图,将合 金液浇入铸型中, 冷凝后测出充满型 腔的式样长度。浇 出的试样越长,合 金的流动性越好, 合金充型能力越好.
几种不同合金流动性的比较
比较下面几种合金流动性能 *铸钢的流动性
裂纹
当热应力大到一定程度会导致出现裂纹。
热应力的形成过程演示
热应力的消除方法
铸件的结构:铸件各部分能自由收缩
铸件的结构尽可能对称 铸件的壁厚尽可能均匀
工艺方面:采用同时凝固原则 时效处理:人工时效;自然时效
铸件的变形原因
结论: 厚部、心部受拉应力, 出现内凹变形。 薄部、表面受压应力, 出现外凸变形。
铸件的结构
凡能增加金属流动阻力和冷却速度,降低流速的因素,均能降低金属的流动性。 如型腔过窄,浇注系统结构复杂,直浇道过低,内浇道截面太小,型砂水分 过多或透气性不好,铸型材料热导性过大等,都会降低金属的流动性。
铸件结构对充型能力的影响
折算厚度:
复杂程度:
折算厚度也叫当量厚度 或模数,是铸件体积与铸件 表面积之比。折算厚度越大, 热量散失越慢,充型能力就 越好。
孕育铸铁应用:一般用于动载荷较小、静载荷较大, 对强度、硬度、和耐磨性要求较高的重要铸件,尤 其是厚大铸件,如床身、凸轮轴、汽缸体等
灰铸铁的铸造性能:流动性好、 收缩小,铸造性能好, 具有自身补缩的能力。
铸造工艺特点:冲天炉熔炼(金属炉料、燃料、熔剂) 砂型铸造 常采用同时凝固原则,高强度采用顺序凝固
成本低,原材料来源广泛, 价格低廉,一般不需要昂 贵的设备
铸造工艺介绍PPT讲座

2023-8-28
14
1.浇注位置旳选择原则
浇注位置是指浇注时铸件在铸型中所处 旳空间位置。
选择正确是否,对铸件质量影响很大。 选择时应考虑下列原则:
2023-8-28
15
浇注位置旳选择原则
①铸件旳主要加工面应朝下或位于侧面 ②铸件宽敞平面应朝下 ③面积较大旳薄壁部分应置于铸型下部或垂直 ④易形成缩孔旳铸件,较厚部分置于上部或侧面 ⑤应尽量降低型芯旳数量 ⑥要便于安放型芯、固定和排气
2.1 失蜡铸造法 用蜡复制所需要铸造旳物件,然后浸入含陶瓷(或硅溶
胶)旳池中并待乾,使以蜡制旳复制品覆上一层陶瓷外膜,一直 反复环节直到外膜足以支持铸造过程(约1/4寸到1/8寸),然后熔 解模型中旳蜡,并抽离铸模。对铸模屡次加以高温焙烧,增强硬 度浇入熔融物质凝固冷却后形成铸件旳铸造措施。
2023-8-28
2023-8-28
砂芯
30
⑥使型腔和主要型芯位于下箱
使型腔和主要芯位于下箱,便于下芯、合型和 检验型腔尺寸。
2023-8-28
31
3.铸造工艺参数旳拟定
铸造工艺参数
铸件尺寸公差 机械加工余量 收缩率
起模斜度 芯头和芯座
2023-8-28
32
①铸件尺寸公差
铸件尺寸公差:铸件尺寸允许旳变动量。 从CT1~CT16,分为16个等级, CT1精度最高。
汉青铜器,1969年出土于甘肃省武威市雷台汉
墓。东汉时期镇守张掖旳军事长官张某及其妻
合葬墓中出土。
7
铸造分类
按铸造工艺分类:主要有砂型铸造和特种铸造2大类。 1.砂型铸造 1.1.湿型(潮模砂)铸造; 1.2.干型铸造 1.3.树脂自硬砂铸造; 1.4.水玻璃自硬砂铸造; 1.5.覆膜砂造型铸造。 2.特种铸造 2.1.精密铸造,又称失蜡铸造,熔模铸造 2.2.消失模铸造,又称实型铸造 2.3.压铸,又称压力铸造 2.4.离心铸造 2.5.石膏型铸造 2.6.连续铸造 2.7.金属型铸造等
铸造知识培训.ppt

26
⑥ 减振性
物体吸收振动能的能力称为减振性。灰铸铁 的减振性比钢约大6~10倍。 ❖ 抗拉强度越低,减振性越好。 所以,灰铸铁 适宜用作减振材料,用于机床床身有利于提 高被加工零件的精度。
21
二、灰铸铁的牌号、性能和应用
1、 灰铸铁的牌号
灰铸铁的牌号以“灰铁”的汉语拼音字头“HT”为标 志符号,后面三位数字表示直径为30mm单铸试棒 测得的最低抗拉强度值(MPa)。表7-2为灰铸铁的 牌号、基体组织、力学性能和用途举例。
22
23
2、灰铸铁的性能和应用
① 抗拉强度 灰口铸铁的抗拉强度比同样基体的钢要低得多。一般说
13
②锰 ❖ 锰是一个阻碍石墨化的元素。 ❖ 锰能溶于铁体和渗碳体,起固定碳的作用,从而
阻碍石墨化。 ❖ Mn能与S结合生成MnS,消除硫的有害影响。 ③硫 ❖ 硫是一个阻碍石墨化的元素。 ❖ S阻碍碳原子的扩散,而且降低铁水的流动性,增
加铸件缺陷,恶化铸造性能。因此,硫是一个有害 元素,其含量应控制在0.15%以下。
24
② 抗压强度 抗压强度约为抗拉强度的2.5-4.0倍。灰铸 铁的抗压强度显著地大于抗拉强度,这是灰 铸铁的一种特性。因此,灰铸铁广泛地被用 作机床底座、床身和支柱等耐压零件。
③ 硬度 灰铸铁的硬度随其成分和组织的变化而变化, 一般在HB130~270范围内变化,随着共晶 度增加,铸铁的硬度降低。
孕育铸铁的抗拉强度可达300~400MPa、硬度 可达HB170~270。孕育铸铁主要用于动载荷较 小,而静载强度要求较高的重要零件,例如汽缸、 曲轴、凸轮和机床铸件等,尤其是断面比较厚大 的铸件更为合适。
铸造培训PPT课件课件

态度,不断提升自己的专业技能和创新能力,以适应行业发展的需求。
02
关注行业动态与发展趋势
个人需要关注铸造行业的最新动态和发展趋势,了解新技术、新工艺和
新材料的应用情况,以便及时调整自己的职业规划和发展方向。
03
培养跨学科综合能力
未来铸造行业将更加注重跨学科综合能力的培养,个人需要注重学习机
械、材料、计算机等相关学科知识,提高自己的综合素质和竞争力。
03
铸造工艺与操作
熔炼工艺与操作
01
02
03
04
熔炼设备选择
根据生产需求选择适当的熔炼 设备,如电弧炉、感应电炉等
。
熔炼材料准备
准备好所需金属原料、熔剂、 燃料等,并进行预处理。
熔炼过程控制
控制熔炼温度、时间、气氛等 参数,确保金属液质量。
熔炼安全操作
遵守安全操作规程,注意防火 、防爆、防烫伤等。
绿色环保与可持续发展
环保意识的提高将促使铸造行业朝着更加绿色环保的方向 发展,采用低污染、低能耗的生产工艺和材料,推动行业 可持续发展。
个性化定制与柔性生产
市场需求的多样化将促使铸造企业向个性化定制和柔性生 产方向转型,以满足客户多样化的需求。
对个人职业发展的建议和思考
01
持续学习与创新
随着技术的不断进步和市场需求的不断变化,个人需要保持持续学习的
铸造培训ppt课件
contents
目录
• 铸造基础知识 • 铸造设备与工具 • 铸造工艺与操作 • 铸造缺陷分析与防止措施 • 铸造安全与环保要求 • 总结与展望
01
铸造基础知识
铸造定义与分类
铸造定义
铸造是一种通过熔化金属或非金 属材料,并将其倒入模具中冷却 凝固,从而获得所需形状和性能 的工件的制造方法。
铸造知识PPT课件

尺寸精度和表面粗糙度控制方法
尺寸精度控制方法
采用高精度的造型和制芯设备;加强模样和芯盒的制造精度 ;严格控制型砂和芯砂的性能等。
表面粗糙度控制方法
选用细粒度的型砂和芯砂;提高铸型的表面光洁度;优化浇 注系统设计,减少铁液对型壁的冲刷等。
05
特种铸造技术简介
压力铸造(压铸)
定义
压力铸造是利用高压将熔融金属压入金属模具中, 并在压力下快速凝固成型的铸造方法。
冷铁应用
02
在铸件厚大部位放置冷铁,以加快该部位的冷却速度,实现顺
序凝固,防止缩孔和裂纹缺陷。
其他辅助措施
03
根据铸件特点和生产要求,还可采用其他辅助措施,如设置出
气孔、加强型芯的固定和排气等。
04
常见铸造缺陷及防止措施
气孔、夹杂等内部缺陷产生原因及防止方法
气孔产生原因
型砂水分过多或过少;造型操作不当; 浇注系统设计不合理;熔炼过程控制不
准备原材料
选择符合要求的金属原材 料,并进行必要的预处理。
铸造工艺过程
熔炼金属
将金属原材料按照一定比 例配料,通过熔炼设备将 其熔化,获得符合要求的 液态金属。
制造模具
根据铸件的结构和尺寸, 设计并制造相应的模具, 包括型腔、型芯、浇口、 冒口等部分。
浇注
将液态金属倒入模具中, 注意控制浇注温度、速度 和压力等参数。
智能化生产
应用机器人、自动化生产线等智能化设备,实现铸造生产的自动化、 柔性化和智能化,提高生产效率和产品质量。
数字化检测
采用三维扫描、无损检测等数字化检测技术,实现铸件质量的快速、 准确检测,提高产品质量和生产效率。
绿色、环保、可持续发展理念在铸造中体现
铸造工艺基础大全完整版.ppt课件.ppt

§2铸件的凝固与收缩
凝固—金属从液态转变为固态的过程。这个转变期 称为凝固期。
一 .铸件的凝固方式
实验:做几个直径相同
的球铸型,一次同时浇注
经过不同时间,先后拔掉
泥芯。倒出液态金属,
测量硬壳厚度,画出
凝固厚度—时间曲线。
泥 芯
精心整理
厚度 3 2 1
1--φ75
2—φ125
3—φ260
精心整理
3 . 中间凝固---凝固区介于1、2之间。大多数合 金的凝固方式属于这种凝固方式。
精心整理
铸件凝固方式对铸件质量的影响: 凝固过程实质是金属的结晶过程,它从两方 面影响铸件的性能: 1)形成的金相组织-----晶粒的大小、形状及晶 粒的内部缺陷等影响合金的机械性能; 2)金属的致密度-----液态金属结晶为固态,引 起的体积收缩所形成的孔洞,若得不到液态 金属的补缩,将产生铸造缺陷,影响合金的 致密性及强度。
精心整理
σ σ
精心整理
Al---Si 合金的高温强度
σ 500℃
固相线精心整理
T℃
影响热裂形成的因素 (1)合金性质
合金结晶温度 T℃
范围越宽,
热裂倾向性
越大。
热
裂
倾
向
精心整理
线收缩 开始温度
固 相 线
此外,合金中的一些其它元素对其热裂 倾向也有一定的影响。如:碳素钢中的S、
P、Si, Mn 四种因素对热裂性的影响。
精心整理
2 .机械应力(收缩应力)
由于收缩受阻,产生的都是拉应力或剪应力。
因为是产生在弹性状态下,落砂后随着产生弹 性变形而消失,为临时应力。(但产生弹性变 形的应力仍然留在弹性体内)
《铸造基础知识教程》课件

《铸造基础知识教程》PPT课 件
通过本课程,你将学习到铸造的定义和历史,材料和工艺分类,生产流程, 模具设计和制造,熔炼设备和工艺,铸造缺陷及其预防,以及铸造技术的未 来趋势。
铸造的定义和历史
铸造是一种使用熔融金属、合金或其他熔融物质,将其注入预先制定的模具 中并让其在模具中冷却凝固的过程。
铸造的历史可以追溯到公元前4000年左右,当时人们将铜熔化后铸造成各种 工具和装饰品。
2
模具制造工艺
冷模和热模是当前最常见的两种模具制造工艺。
3
模具试制
模具制造完成后,需要根据制作完整性和检测结果进行性能试制。
熔炼设备和工艺
铸造工艺中的熔炼过程也称为熔化,主要过程包括将所需材料放入熔炉中、升温、熔化并控制温度,选用不同 熔炉时需要有不同的技术和工艺。
熔炼炉
常见熔炼炉有电阻炉和电弧炉。
表面缺陷
原因:液态金属在注入模腔前 未过滤干净以及铸造前模具未 处理完毕。 解决方法:使用新颖的模具设 计工艺来达到更干净的铸造材 料。
铸造技术的未来趋势
随着科技的发展,数字模拟成型、虚拟现实实验等新技术不断涌现。 在3D打印铸造技术的发展进程中,不仅减小了热核装配步骤的不确定性,还 开创了铸造领域的想象空间,特别是在金属粉末增材制造方面具有巨大潜力。
光谱分析
通过光谱分析可以检测出熔炼后 材料成分。
熔金ቤተ መጻሕፍቲ ባይዱ
熔金可以匀质铸造实体,增加材 料的韧性。
铸造缺陷及其预防
缩孔和气孔
原因:铸造过程中熔液未充填 完全或有气体无法排除或排除 不彻底。 解决方法:合理的设计出口和 填充,增加压力等。
缺陷裂纹
原因:矿物夹杂,结构紧密、 强度低、易破裂、冷热空气交 替等。 解决方法:避免铸造温度过高。
材料课件铸造讲稿
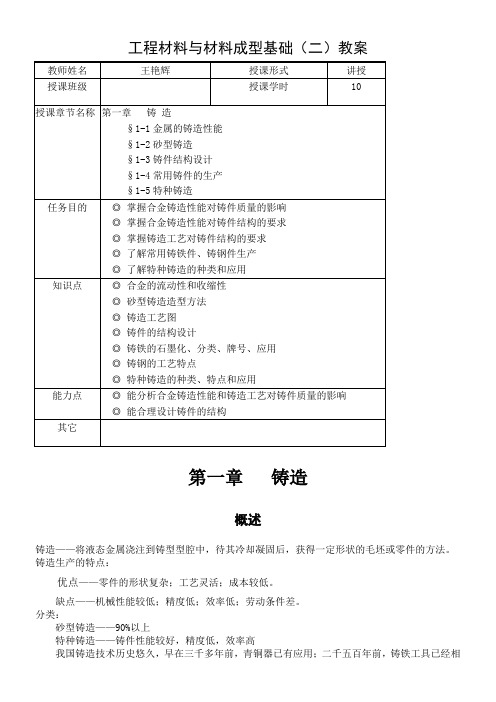
工程材料与材料成型基础(二)教案第一章铸造概述铸造——将液态金属浇注到铸型型腔中,待其冷却凝固后,获得一定形状的毛坯或零件的方法。
铸造生产的特点:优点——零件的形状复杂;工艺灵活;成本较低。
缺点——机械性能较低;精度低;效率低;劳动条件差。
分类:砂型铸造——90%以上特种铸造——铸件性能较好,精度低,效率高我国铸造技术历史悠久,早在三千多年前,青铜器已有应用;二千五百年前,铸铁工具已经相当普遍。
泥型、金属型和失蜡型是我国创造的三大铸造技术。
§1-1 金属的铸造性能合金的铸造性能是表示合金铸造成型获得优质铸件的能力。
通常用流动性和收缩性来衡量。
一、合金的流动性1、流动性概念流动性——液态合金的充型能力。
流动性好的合金:易于浇注出轮廓清晰、薄而复杂的铸件; 有利于非金属夹杂物和气体的上浮和排除; 易于补缩及热裂纹的弥合。
合金的流动性是以螺旋形流动试样的长度来衡量。
试样越长,流动性越好。
2、影响合金流动性的因素a 、合金性质方面纯金属、共晶合金流动性好。
(恒温下结晶,凝固层内表面光滑) 亚、过共晶合金流动性差。
((在一定温度范围内结晶,凝固层内表面粗糙不平))b 、铸型和浇注条件提高流动性的措施:提高铸型的透气性,降低导热系数; 确定合理的浇注温度; 提高金属液的压头; 浇注系统结构简单。
C 、铸件结构铸件壁厚>最小允许壁厚二、合金的收缩1、收缩的概念收缩是铸件中的缩孔、缩松、变形和开裂等缺陷产生的原因。
收缩的三个阶段:液态收缩形成缩孔、缩松(体收缩率) 凝固收缩固态收缩 ——产生变形和裂纹(线收缩率)缩孔的形成:纯金属或共晶成分的合金易形成缩孔。
缩松的形成:结晶温度范围大的合金易形成缩松。
缩孔和缩松的防止:定向凝固——在铸件可能出现缩孔的厚大部位,通过增设冒口或冷铁等工艺措施,使铸件上远离冒口的部位先凝固,尔后是靠近冒口的部位凝固,冒口本身最后凝固。
结果——使铸件各个部分的凝固收缩均能得到液态金属的补充,而将缩孔转移到冒口之中3、铸造应力铸造内应力有热应力和机械应力,是铸件产生变形和开裂的基本原因。
《铸造基础知识》课件

铸造工艺能够生产出形状复杂 的零件,且具有节约金属材料 、生产成本较低等优点。
02 铸造材料
铸造用金属材料
01
02
03
铸钢
用于生产承受较大载荷和 要求高强度、高耐磨性的 机械零件,如齿轮、曲轴 等。
铸铁
具有良好的铸造性能、减 震性能和耐磨性能,广泛 应用于制造各种铸件,如 汽缸体、底座等。
铝合金
流程
主要包括造型、制芯、熔炼、浇注 、冷却和落砂等步骤。
特种铸造
定义
特种铸造是一种采用特殊工艺和 材料的铸造方法,如消失模铸造
、金属型铸造、压力铸造等。
特点
特种铸造能够提高铸件质量、减 少废品率、提高生产效率,适用 于生产复杂、高精度和高质量的
铸件。
流程
各种特种铸造工艺的流程略有不 同,但通常包括模具设计、材料
质量轻、耐腐蚀、导热性 好,常用于制造轻量化要 求的零件,如汽车发动机 缸体、缸盖等。
铸造用非金属材料
树脂砂
以树脂为粘结剂的型砂,具有较高的强度和耐热 性,主要用于生产复杂形状的铸件。
陶瓷砂
具有高强度、高硬度和耐高温特性,适用于生产 耐磨、耐腐蚀的铸件,如轴承、密封件等。
石墨
具有良好的耐高温、耐腐蚀和润滑性能,常用于 生产高温、高压环境下工作的铸件。
《铸造基础知识》ppt课件
目录
• 铸造简介 • 铸造材料 • 铸造工艺 • 铸造缺陷与质量控制 • 铸造技术的发展趋势与展望
01 铸造简介
铸造的定义
01
铸造是一种通过将液态金属倒入 模具中,待其冷却凝固后形成固 态零件的工艺。
02
铸造工艺广泛应用于机械、汽车 、航空、船舶、轻工等工业领域 。
- 1、下载文档前请自行甄别文档内容的完整性,平台不提供额外的编辑、内容补充、找答案等附加服务。
- 2、"仅部分预览"的文档,不可在线预览部分如存在完整性等问题,可反馈申请退款(可完整预览的文档不适用该条件!)。
- 3、如文档侵犯您的权益,请联系客服反馈,我们会尽快为您处理(人工客服工作时间:9:00-18:30)。
材料课件铸造讲稿 Document number:PBGCG-0857-BTDO-0089-PTT1998工程材料与材料成型基础(二)教案第一章铸造概述铸造——将液态金属浇注到铸型型腔中,待其冷却凝固后,获得一定形状的毛坯或零件的方法。
铸造生产的特点:优点——零件的形状复杂;工艺灵活;成本较低。
缺点——机械性能较低;精度低;效率低;劳动条件差。
分类:砂型铸造——90%以上特种铸造——铸件性能较好,精度低,效率高我国铸造技术历史悠久,早在三千多年前,青铜器已有应用;二千五百年前,铸铁工具已经相当普遍。
泥型、金属型和失蜡型是我国创造的三大铸造技术。
§1-1 金属的铸造性能合金的铸造性能是表示合金铸造成型获得优质铸件的能力。
通常用流动性和收缩性来衡量。
一、合金的流动性1、流动性概念流动性——液态合金的充型能力。
流动性好的合金:易于浇注出轮廓清晰、薄而复杂的铸件;有利于非金属夹杂物和气体的上浮和排除;易于补缩及热裂纹的弥合。
合金的流动性是以螺旋形流动试样的长度来衡量。
试样越长,流动性越好。
2、影响合金流动性的因素a、合金性质方面纯金属、共晶合金流动性好。
(恒温下结晶,凝固层内表面光滑)亚、过共晶合金流动性差。
((在一定温度范围内结晶,凝固层内表面粗糙不平))b、铸型和浇注条件提高流动性的措施:提高铸型的透气性,降低导热系数; 确定合理的浇注温度; 提高金属液的压头; 浇注系统结构简单。
C 、铸件结构铸件壁厚>最小允许壁厚二、合金的收缩1、收缩的概念收缩是铸件中的缩孔、缩松、变形和开裂等缺陷产生的原因。
收缩的三个阶段:液态收缩形成缩孔、缩松(体收缩率) 凝固收缩固态收缩 ——产生变形和裂纹(线收缩率)几种铁碳合金的体积收缩率2、铸件的缩孔和缩松 缩孔的形成:纯金属或共晶成分的合金易形成缩孔。
缩松的形成:结晶温度范围大的合金易形成缩松。
缩孔和缩松的防止:定向凝固——在铸件可能出现缩孔的厚大部位,通过增设冒口或冷铁等工艺措施,使铸件上远离冒口的部位先凝固,尔后是靠近冒口的部位凝固,冒口本身最后凝固。
结果——使铸件各个部分的凝固收缩均能得到液态金属的补充,而将缩孔转移到冒口之中3、铸造应力铸造内应力有热应力和机械应力,是铸件产生变形和开裂的基本原因。
热应力的形成——热胀冷缩不均衡机械应力的形成——收缩受阻减少和消除应力的措施:结构上——壁厚均匀,圆角连接,结构对称。
工艺上——同时凝固,去应力退火。
同时凝固和定向凝固比较定向凝固——用于收缩大或壁厚差距较大,易产生缩孔的合金铸件,如铸钢、铝硅合金等。
定向凝固补缩作用好,铸件致密,但铸件成本高,内应力大。
同时凝固——用于凝固收缩小的灰铸铁。
铸件内应力小,工艺简单,节省金属,组织不致密。
4、铸件的变形对于厚薄不均匀、截面不对称及具有细长特点的杆件类、板类及轮类等铸件,当残余铸造应力超过铸件材料的屈服强度时,产生翘曲变形。
用反变形法防止箱体、床身导轨的变形。
5、铸件的裂纹铸钢件热裂纹(改善型芯的退让性,大的型芯制成中空的或内部填以焦碳)轮形铸件的冷裂(减少铸件应力,降低合金的脆性)§1-2 砂型铸造一、砂型铸造造型方法套筒的砂型铸造过程:造型方法:手工造型——单件、小批量生产机器造型——中、小件大批量生产机器造芯——中、小件大批量生产柔性造型单元——各种形状与批量生产(一)手工造型手工造型方法和特点(二)机器造型机器造型是将填砂、紧实和起模等主要工序实现了机械化,并组成生产流水线。
机器造型生产率高,铸型质量好,铸件质量高,适用于中小型铸件的大批量生产。
机器造型方法:振压造型、高压造型、抛砂造型。
1、振压造型工作原理a) 填砂 b) 振实 c) 压实 d) 起模2、多触头高压造型3、抛砂机(三)机器造芯在大批量生产中,常用型芯制作设备是射芯机和壳(吹)芯机。
射芯机工作原理和壳(吹)芯制造原理(四)柔性制造单元柔性制造单元通过在造型自动线上加设模板库及模板快换机构等,由计算机集中控制模板的调运与更换、造型机工作参数、铸型质量的检验等。
二、砂型铸造工艺设计铸造工艺图包括:铸件的浇注位置铸型分型面铸造工艺参数支座的零件图、铸造工艺图、模样图及合型图(一)浇注位置的选择浇注位置——浇注时铸件在铸型中的空间位置。
浇注位置的选择原则:铸件的重要加工面应朝下或位于侧面;铸件的大平面应朝下;面积较大的薄壁部分置于铸型下部或侧面;铸件厚大部分应放在上部或侧面。
(二)铸型分型面的选择三通的分型方案:四箱造型、三箱造型、两箱造型分型面的选择原则:便于起模,使造型工艺简化;尽量使铸件全部或大部置于同一砂箱;尽量使型腔及主要型芯位于下型。
(三)工艺参数的确定机械加工余量和最小铸出孔;起模斜度;铸造收缩率;型芯头设计。
(四)浇、冒口系统(五)铸造工艺设计的一般程序(五)铸造工艺设计的一般程序(五)实例分析1、气缸套方案Ⅰ,轴线处于水平位置,铸件易产生缺陷;用分开模两箱造型,分型面通过圆柱面,有飞边,易错箱。
方案Ⅱ,轴线处于垂直位置,铸件是顺序凝固;分型面在铸件一端,毛刺易清理,不会错箱2、支座方案Ⅰ,沿底版中心分型。
轴孔下芯方便,但底版上四个凸台必须采用活块且铸件在上、下箱各半。
方案Ⅱ,沿底面分型,铸件全部在下箱,不会产生错箱,铸件易清理。
但轴孔内凸台必须采用活块或下芯且轴孔难以铸出。
3、C6140车床进给箱体方案Ⅰ,能铸出轴孔,型芯稳定性好。
但基准面朝上易产生缺陷且型芯数量较多,槽C妨碍起模需用活块或型芯。
方案Ⅱ,从基准面分型,铸件大部分在下型,基准面朝上,轴孔难以铸出,且凸台E和槽C 妨碍起模,需用活块或型芯。
方案Ⅲ,铸件全部置于下型,基准面朝下,铸件最薄处在铸型下部。
但凸台EA和槽C都需用活块或型芯,内型芯稳定性差。
大批量生产时——选用方案Ⅰ,单件、小批量生产时——选用方案Ⅱ或方案Ⅲ。
车床进给箱体铸造工艺图§1-3 铸件的结构设计铸件的结构工艺性,是指所设计的零件在满足使用性能的前提下,铸造成形的可行性和经济性,即铸造成形的难易程度。
良好的铸件结构性应与金属的铸造性能和铸造工艺相适应。
大批量生产时,铸件的结构应便于采用机器造型;单件、小批量生产时,则应使所设计的铸件尽可能适应现有生产条件。
一、合金铸造性能对铸件结构的要求(一)铸件的壁厚1、铸件壁厚应合理2、铸件壁厚应均匀3、致密铸件应符合顺序凝固原则(二)壁的连接1、应有结构圆角2、应避免交叉、锐角接头3、不同壁厚连接应逐渐过渡(三)避免变形和开裂的结构1、结构对称2、合理设置加强肋3、应有利于自由收缩二、铸造工艺对铸件结构的要求(一)铸件的外形1、尽量避免外表面内凹2、尽量示分型面为平面3、尽量减少分型面的数量4、应具有结构斜度(二)铸件的内腔1、不用或少用型芯和活块2、有利于型芯的定位、排气和清理三、组合铸件对于某些大型复杂铸件,在生产条件不允许整体铸造时,可采用组合铸件。
§1-4 常用铸件的生产一、铸铁件的生产铸铁是含碳量超过的铁碳合金。
工业用铸铁实际上是以Fe、C、Si为主要元素的多元合金。
铸铁中碳的存在形式:渗碳体——化合状态石墨——游离状态铸铁分类:白口铸铁灰铸铁(片状石墨)灰口铸铁可锻铸铁(团絮状石墨)麻口铸铁球墨铸铁(球状石墨)(一)铸铁的石墨化1、石墨化过程石墨化——铸铁中析出石墨的过程。
石墨化形式:缓慢冷却时,L(A) →石墨加热时, Fe3C →石墨因此石墨是稳定相,是亚稳定相。
石墨是碳的一种结晶形态,具有六方晶格。
原子呈层状排列,同一层面上的碳原子呈共价键,结合力强;层与层之间呈分子键,结合力弱。
因此,石墨结晶形态常易发展为片状,强度、硬度、塑性极低。
2、影响石墨化的因素(1)化学成分碳和硅是强烈促进石墨化元素。
碳是石墨的基础,硅促进石墨析出(C:~% , Si:~%)。
碳和硅含量高时,石墨量多、尺寸大、铁素体多,因此强度、硬度低。
锰是微弱阻止石墨化元素,可促进珠光体基体形成,提高铸铁强度和硬度(Mn : ~%)。
硫和磷是有害元素(S≤~%,P≤)。
碳当量:C E = C + (Si+P)/3 %C E =% ,共晶成分;C E<% ,亚共晶成分;C E>% ,过共晶成分。
(2)冷却速度同一铸件厚壁处为灰口组织,而薄壁处为白口组织,这说明:缓慢冷却有利于石墨化过程的进行。
可见,当铁水的碳当量较高,结晶过程中缓慢冷却时,易形成灰口铸铁;相反易形成白口组织(二)灰铸铁1、灰铸铁的组织和性能特点灰铸铁的组织:铁素体灰铸铁铁素体+珠光体灰铸铁珠光体灰铸铁、灰铸铁的性能:(1)机械性能较差——强度低、塑性低、韧性低且壁厚敏感;抗压强度、硬度与相同基体碳钢相近。
(2)(2)其它性能耐磨性好、减震性好、缺口敏感性小、铸造性能和切削加工性能良好。
2、灰铸铁的牌号与用途HT200——表示灰铸铁,σb≥200N/mm2(壁厚增加,强度降低)3、灰铸铁的孕育处理孕育铸铁:HT250、HT300、H350T孕育处理:降低碳、硅含量,以提高铸铁的强度;浇注前向铁水中加入少量的孕育剂(75%硅铁),可以细化组织,促进石墨化。
孕育铸铁的特点:强度较高,冷却速度对其组织和性能的影响甚小。
特别适合生产厚大铸件如重型机床、压力机床身、高压液压件、活塞环、齿轮、凸轮等。
(三)球墨铸铁球墨铸铁是在浇注前往铁水中加少量的球化剂和孕育剂,获得具有球状石墨的铸铁。
1、球墨铸铁的组织和性能球墨铸铁的组织:铁素体球铁铁素体+珠光体球铁珠光体球铁2、球墨铸铁的牌号与用途QT500-7——表示球墨铸铁,σb≥500N/mm2, δ≥ 7 %牌号基体组织用途QT450-10铁素体农机具零件、中低压阀门、输气管道。
QT600-3铁素体+珠光体负荷大、受力复杂的零件。
如汽车、拖拉机曲轴,连杆,凸轮轴,蜗杆机床蜗杆、蜗轮,轧钢机轧辊、大齿轮。
QT700-2珠光体QT800-2珠光体高强度齿轮。
3、球墨铸铁的生产特点(1)严格控制化学成分(C、Si较高,Mn、P、S较低)(2)较高的出铁温度(1400-1420℃)(3)球化处理(获得球状石墨)(4)孕育处理(促进石墨化,细化均匀组织)(5)热处理退火——铁素体+球状石墨 QT400-18,正火——索氏体+球状石墨 QT600-3,调质——回火索氏体+球状石墨 QT800-2等温淬火——下贝氏体+球状石墨 QT900-24、球墨铸铁铸造工艺特点(1)流动性比灰铸铁差(2)收缩较灰铸铁大球墨铸铁件多应用冒口和冷铁,采用定向凝固原则。
在铸型刚度很好的条件下,也可采用同时凝固原则不用冒口或用小冒口。
(四)铸铁的熔炼冲天炉的熔炼过程冲天炉的燃料为焦碳;金属炉料有:铸造生铁锭、回炉料、废钢、铁合金;熔剂为石灰石和氟石。
在冲天炉熔炼过程中,高炉炉气不断上升,炉料不断下降:底焦燃烧;金属炉料被预热、熔化和过热;冶金反应使铁水发生变化。