模具毕业设计8板(框)类制品叠层式注射模具设计(论文)
叠层式注塑模具设计论文

叠层式注塑模具设计论文叠层式注塑模具作为一种新颖的模具设计方式,近年来逐渐受到注塑行业的重视和应用。
本论文旨在探讨叠层式注塑模具的设计方法和优点,帮助读者更好地了解这种新型模具的特性和使用。
一、叠层式注塑模具的定义和优点叠层式注塑模具是一种由多层模板组成的模具,在注塑过程中,模具可以同时注入多个物料,实现多色、多材料的生产。
与传统的单色注塑模具相比,叠层式注塑模具具有以下优点:1. 提高生产效率:在同一次注塑过程中,可以完成多个产品的注塑,大大提高了生产效率。
2. 缩短生产周期:通过一次注塑完成多个产品的生产,避免了多个生产过程的重复,缩短了生产周期。
3. 降低生产成本:同一次注塑可以完成多个产品的生产,减少了生产线的调整和模具更换的成本,从而降低了生产成本。
4. 增加产品的多样性:叠层式注塑模具可以实现多色、多材料注塑,可以生产出更多种类更丰富的产品。
二、叠层式注塑模具的设计方法叠层式注塑模具的设计需要考虑多种因素,如产品的大小和形状、模具的大小和结构、压力和温度等。
以下是叠层式注塑模具的基本设计方法:1. 选择合适的模具材料:叠层式注塑模具需要承受更大的压力和温度,因此需要选择更耐磨、耐腐蚀的模具材料。
2. 设计合理的模具结构:叠层式注塑模具的结构必须合理,能够快速卸出产品,同时能够方便地更换和维护模具。
3. 控制注塑参数:叠层式注塑模具的注塑参数需要根据实际情况进行调整,以保证注塑产品的质量。
4. 原材料的选择:在叠层式注塑模具中,原材料的选择也很重要。
需要选择粘度相近的原材料,以确保不同颜色或不同材质的原材料注入后不会相互干扰,保证产品质量并避免生产过程中浪费原材料。
5. 使用较好的注塑机:在使用叠层式注塑模具时,需要配备较好的注塑机,以保证注塑过程的精度和稳定性。
三、叠层式注塑模具的应用叠层式注塑模具的应用范围广泛,主要是在需要生产多彩色、多材质和多层结构的产品时,如手机外壳、汽车内饰等,同时也适用于生产复杂形状的产品。
注塑模设计毕业设计

注塑模设计毕业设计【篇一:注塑模设计毕业论文】毕业设计(论文)题目:茶杯盖注射模具设计作者届别系别机电系专业机械设计及其自动化指导教师职称完成时间摘要塑料在当今世界上无处不用,因此塑料模具有很大发展,特别是注塑模。
由此可知,研究注塑模具对了解塑料产品的生产过程和提高产品质量有很大意义。
本课题主要是针对瓶盖的模具设计,通过对塑件进行工艺性分析和比较,最终设计出一副注塑模。
该课题从产品结构工艺性及具体模具结构出发,对模具的浇注系统、模具成型部分的结构、顶出系统、冷却系统、注塑机的选择及有关参数的校核、都有详细的设计,同时并简单的编制了模具的加工工艺。
通过整个设计过程表明该模具能够达到此塑件所要求的加工工艺。
根据题目设计的主要任务是茶杯盖注塑模具的设计。
也就是设计一副注塑模具来生产茶杯盖的塑件产品,以实现自动化提高产量。
通过本设计,可以对注塑模具有一个较深的认识,注意到设计中的某些细节问题,了解模具结构及工作原理;通过对program的学习,可以建立较简单零件的零件库,从而有效的提高工作效率;通过画装配图、零件图,进一步系统深化cad熟练程度,加深了对模具各个零件的认识。
关键字: 塑料模具,注射机,型腔,浇注系统abstractplastic is everywhere in the world today with , therefore has great development prospects of plastic , especially in injection molding ,so the study of plastic injection molds for understanding the production process and improve the quality of productshave great significance.this topic mainly aims at bottle caps mold design, through to models to carry on the technological analysis and the comparison , this topic embarks from the product mix technology capability and the concrete mold structure , tomolds gating system, the mold formation parts structure, goesagainst the system, the cooling system, injection molding machines choice and the related parameter examination, has the detailed design, simultaneously and simple establishment molds processing craft. through the entire design process indicated that this mold can achieve this to model the processing craft which an institute requests. is the teacup covers injection molds design according to the topic designs primary mission. is also designs an injection mold to produce the teacup to cover models a product, realizes the automation to raise the outputthrough the design, injection mold can have a deeper understanding of the design notes that some of the details to understand the structure and working principle ofmold.through learning program, you can create a simpler components parts store, and effective improve efficiency; through painting assembly drawing, part drawings, and further deepen the cad system proficiency, a better understanding of the various parts of mold.key words: plastic mold, injection machine, mold cavity, pouring system目录1前言 (6)1.1模具工业的地位 (6)1.2塑料注射模具的现状及发展趋势 (6)2茶杯盖制件分析 (9)2.1茶杯盖的模具设计流程 (9)2.2塑件分析 (10)2.3茶杯盖的三维图 (11)3 茶杯盒盖的注塑模具设计 (11)3.1方案的选择 (11)3.2制件成型位置及分型面选择 (12)3.3浇注系统设计 (12)3.3脱模机构设计 (14)3.4 溢料排气系统设计 (14)3.5模具主要零件的结构设计 ....................... (15)3.5.1凹模工作尺寸的计算 (16)3.5.2 凸模工作尺寸的计算 (17)3.5.3 前模仁的设计 (18)3.5.4成型零件的设计 (19)3.6导向与定位机构 (20)3.7 选择脱模方式 (21)3.7.1脱模机构的设计 (21)3.7.2脱模力计算� (21)3.8 侧抽芯机构的设计 (22)3.9.模架选用 (23)4.注射机的选择 (24)4.1 注塑机基本参数 (24)4.2初选注塑机 (25)4.3 注射机的校核 (26)4.3.1 注射压力的校核 (26)4.3.2 锁模力的校核 (26)4.3.3安装部分相关尺寸的校核 (26)4.3.4 模具外形尺寸校核 (27)4.3.5 模具厚度校核 (27)4.3.6模具安装尺寸校核 (27)4.3.7 开模行程校核 (27)5.塑件的总装图 (28)6参考文献 (29)【篇二:毕业设计注塑模具设计】摘要根据注射模具在国内外的飞速发展以及注射模软件cad/cam 的提高再结合我校专业特色及本专业的培养计划,我选用奇瑞车的工具箱盖双型腔注塑模设计作为本次的毕业设计题目。
注射模设计 大学毕业设计

本科毕业论文题目注射模设计学院工学院专业2009级机械设计制造及其自动化毕业届别2013姓名李翔指导教师张炜职称教授甘肃农业大学教务处制二〇一三年五月目录摘要 (1)关键词 (1)Abstract (1)Key words (1)前言 (1)1塑件的工艺性分析 (2)1.1塑件的结构工艺分析 (2)1.2尺寸精度分析 (2)1.3塑件的表面质量分析 (3)1.4上盖的材料选择 (4)2 ABS注射成型工艺及工艺参数 (4)2.1注射成型过程 (4)2.2注射工艺参数 (5)3注射机的选择及其技术参数 (6)3.1注射机 (6)3.2选择注射机初定型腔数 (6)4 模具总体机构方案的分析与制定 (7)4.1注射模的结构组成 (7)4.2模架的选型 (8)4.3确定型腔数目 (9)4.4确定分型面的 (10)5浇注系统的设计及排气方案的确定 (10)5.1浇注系统设计的原则 (10)5.2主流道的设计 (11)5.3 分流道的设计 (12)5.4浇口的设计 (14)5.5排气方案的设计 (14)6注射模功能结构的详细设计 (15)6.1校核注射机有关工艺参数 (15)6.2成型零部件的设计概况 (16)6.3 凹模的结构尺寸设计 (18)6.4型芯的结构尺寸设计 (19)6.5凸模的结构尺寸设计 (19)6.6合模导向机构设计 (20)6.7脱模机构的设计 (23)6.8模具温度的调节系统 (25)7结论 (25)参考文献 (26)致谢 (27)注射模设计李翔(甘肃农业大学工学院机械设计制造及其自动化专业,甘肃兰州,730070)摘要:塑料工业是当今世界上增长最快的工业门类之一,而注塑模具是其中发展较快的种类,因此,研究注塑模具对了解塑料产品的生产过程和提高产品质量有很大意义。
本文介绍了注射成型的基本原理特别是单分型面注射模具的结构与工作原理,对注塑产品提出了基本的设计原则;制品采用材料为低密度ABS。
注塑模具设计—毕业论文

摘要注射模设计质量对塑料制品成型的质量、生产效率、模具加工的难易程度、模具制造成本和制造周期等有着直接的影响。
本课题主要是针对RICOH CORONA的注射模具的设计,通过对塑件进行工艺分析和比较,根据塑件的主要技术指标以及材料的性能,设计模具的浇注系统、型芯和型腔等成型零部件、导向机构、脱模机构、温度调节冷却系统、排气系统等主要模具设计内容,最终设计完成一副注射模具。
本次产品使用的材料为ABS+PC,其综合了PC和ABS的优良性能,一方面可以提高ABS的耐热性、抗冲击和拉伸强度;另一方面可以降低PC 成本和熔体粘度,提高流动性,改善加工性能,减少制品内应力和冲击强度对制品厚度的敏感性,满足了塑件所需要的优良的抗冲击性和刚性。
本设计说明书设计的这副注射模具为普通浇注系统模具,采用三板模的结构;塑料件采用一模两腔、点浇口的成型方案;模具的型芯由许多小镶块组成,改善了小尺寸高精度成型镶块的加工性;循环水路冷却系统的设计提高了成型区模具温度的均匀性和调控能力;在型芯型腔镶拼块、型芯型腔固定板和分流道末端上开设专门的排气槽的排气系统的设置保证模具型腔排气顺畅。
通过这些模具结构的设计,满足塑件的质量要求、生产效率和模具的使用寿命等技术指标。
关键词:塑料,ABS+PC,模具设计,注射模RICOH CORONA Injection Mold DesignABSTRACTInjection mold design-quality has a directly impact on quality of plastic molding,productivity, ease of mold processing , die manufacturing cost and manufacturing cycle. The topic is mainly for the RICOH CORONA injection mold design.Through process analysis and comparison of the plastic parts, and according to the major technical indicators and material properties, mold gating system design, core and cavity molding parts, guide mechanism, stripping mechanism, temperature adjust cooling system ,which finally complete a part of Injection mold.The product material is ABS + PC, which combines the excellent properties of PC and ABS. on the one hand it can improve the heat resistance of ABS, impact resistance and tensile strength.On the other hand it can reduce PC costs and melt viscosity, enhance mobility, improve processing performance, reduce stress and impact strength of the products, which meet the excellent impact resistance and rigidity of the plastic parts needed.This mold is a common casting system mold, using the structure of the three-plate mold; Plastic parts use a two-cavity mold, point gateforming solution; The mold core be used of many small inserts, improving the processing of the small size and high precision inserts; Circulating water cooling system designed improve the uniformity of the forming zone mold temperature and control capability.In the core cavity mosaic pieces, opened a special exhaust system exhaust ducts settings to ensure smooth exhaust cavity mold cavity fixed on the core plate and the runner ends.Plastic parts meet quality requirements, production efficiency and service life of molds and other technical indicators, through the design of the mold structure.Key words:Plastic, ABS+PC,Molding design, Injection molding design注射模设计X X xxxxxxxxx0 引言塑料由于具有密度小、质量轻而强度高、刚度大、绝缘性着色性好、成型方便等优点,成为20世纪发展最快的行业之一,各色各样、形状颜色各异的塑料零件出现在我们的生产生活当中,以塑代钢、以塑代木已成为一种趋势。
毕业论文——塑料盖板注塑模具设计
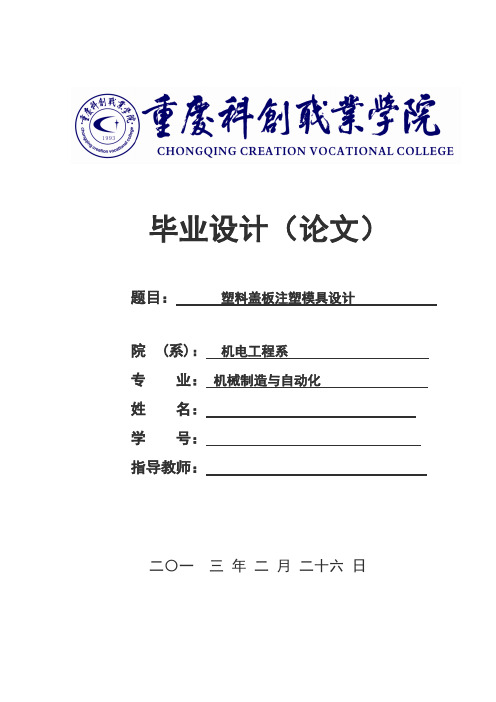
毕业设计(论文)题目:塑料盖板注塑模具设计院 (系):机电工程系专业:机械制造与自动化姓名:学号:指导教师:二〇一三年二月二十六日毕业设计(论文)任务书毕业设计(论文)进度计划表毕业设计(论文)中期检查记录表本文分析了塑料连接盖板的成型特点,设计了一副含有双分型面的,采用定距螺钉和弹簧进行二次分型并且采用型芯嵌块所组成凸模结构的点浇口注射模具。
该模具的关键是解决型芯镶块结构和点浇口浇注系统凝料的自动推出问题,以及在实现这个功能的情况下,如何使模具有效而可靠的运动。
在这里,用到了顺序分型的方法,即在第一分型面完成的情况下,再分第二分型面等等,有严格的先后关系。
在制造方面,运用了数控技术,采用了先进的线切割、电火花加工技术,提高了加工精度和加工效率。
关键词:塑料连接盖板注射模具双分型面设计与制造This paper analyse the forming characteristic of the Plastic connection cover. Design a injection mould which has two-parting surfaces、Adopting the screw and spring from the secondary type and use of cores embedded block structure consisting of punch point gate injection mold. The key of this mould is to solve the problem the type of mold core inserts gate structure and how to make the runner system cold stuff automatism out, and in this case, how to make the mould movement effective and reliable. Here, with a order parting method, namely when the first parting surface was done,then the second begin to work. Has a rigid prccedence relationgship. In manufacture, by the exercise of numerical control technique, adopt advanced strung incise、spark erosion technique, advancing working accuracy and working efficiency.KEY WORD :plastic connection cove injection mould Two-parting surface design and manufacture目录第一章绪言 (2)第一节模具制造业的发展 (2)第二章塑料件的产品分析 (3)第一节产品结构工艺分析 (3)第二节塑料产品的测绘 (5)第三章成型设备的选用 (7)第一节注塑机的选择 (7)第二节模架的选择 (8)第三节模具参数的校核 (10)第四章注射成型方案分析 (14)第一节分型面及其选择 (14)第二节浇注系统的分析 (14)第五章模具结构设计 (15)第一节浇注系统的设计 (15)第二节成型零件部件的设计 (18)第三节推出机构的设计 (24)第四节冷却系统的设计 (26)第六章模具的工作原理和模具结构 (27)第一节模具的工作原理 (27)第二节模具的结构特点 (28)结论 (29)致谢 (30)参考文献 (31)第一章绪言第一节模具制造业的发展随着工业的发展,工业产品的品种和数量不断增加。
模具设计毕业设计论文

1前言1.1模具工业在国民经济中的地位模具是制造业的一种基本工艺装备,它的作用是控制和限制材料(固态或液态)的流动,使之形成所需要的形体。
用模具制造零件以其效率高,产品质量好,材料消耗低,生产成本低而广泛应用于制造业中。
模具工业是国民经济的基础工业,是国际上公认的关键工业。
模具生产技术水平的高低是衡量一个国家产品制造水平高低的重要标志,它在很大程度上决定着产品的质量,效益和新产品的开发能力。
振兴和发展我国的模具工业,正日益受到人们的关注。
早在1989年3月中国政府颁布的《关于当前产业政策要点的决定》中,将模具列为机械工业技术改造序列的第一位。
模具工业既是高新技术产业的一个组成部分,又是高新技术产业化的重要领域。
模具在机械,电子,轻工,汽车,纺织,航空,航天等工业领域里,日益成为使用最广泛的主要工艺装备,它承担了这些工业领域中60%~90%的产品的零件,组件和部件的生产加工。
模具制造的重要性主要体现在市场的需求上,仅以汽车,摩托车行业的模具市场为例。
汽车,摩托车行业是模具最大的市场,在工业发达的国家,这一市场占整个模具市场一半左右。
汽车工业是我国国民经济五大支柱产业之一,汽车工业重点是发展零部件,经济型轿车和重型汽车,汽车模具作为发展重点,已在汽车工业产业政策中得到了明确。
汽车基本车型不断增加,2005年将达到170种。
一个型号的汽车所需模具达几千副,价值上亿元。
为了适应市场的需求,汽车将不断换型,汽车换型时约有80%的模具需要更换。
中国摩托车产量位居世界第一,据统计,中国摩托车共有14种排量80多个车型,1000多个型号。
单辆摩托车约有零件2000种,共计5000多个,其中一半以上需要模具生产。
一个型号的摩托车生产需1000副模具,总价值为1000多万元。
其他行业,如电子及通讯,家电,建筑等,也存在巨大的模具市场。
目前世界模具市场供不应求,模具的主要出口国是美国,日本,法国,瑞士等国家。
中国模具出口数量极少,但中国模具钳工技术水平高,劳动成本低,只要配备一些先进的数控制模设备,提高模具加工质量,缩短生产周期,沟通外贸渠道,模具出口将会有很大发展。
注塑模具设计毕业设计论文参考模板

1.前言 (3)1.1毕业设计的目的 (3)1.2题目内容及要求 (3)2.塑件的工艺分析 (3)2.1塑件材料的选择 (3)2.2塑件的工艺特性分析 (3)3.注射机的选择与模具结构形式 (3)3. 1 设备的选择与参数校核 (3)3.1.1注射机型号的选择 (3)3.1.2 模具参数的校核 (4)3.2模具结构确定 (4)3.2.1确定型腔数量及排列方式 (4)3.2.2分型面的设计 (5)4.浇注系统设计 (5)4.1浇注系统的组成 (5)4.2主流道设计 (5)4.3分流道设计 (7)4.3.1分流道的形状及尺寸 (7)4.3.2 分流道的长度 (7)4.3.3分流道的粗糙度 (7)4.4浇口的设计 (7)4.5浇注系统的平衡 (7)4.6冷料穴的设计 (7)5.成型零件的设计 (7)5.1注射成型零部件结构设计 (7)5.1.1凹模 (7)5.1.2凸模 (8)5.2成型零部件工作尺寸的计算 (8)5.2.1凹模的径向尺寸的计算 (10)5.2.2 凹模深度尺寸的计算 (11)5.2.3 凸模径向工作尺寸的计算 (11)5.2.4凸模高度工作尺寸的计算 (12)5.3成型零件的加工工艺 (12)6. 注射模导向与推出机构设计 (12)6.1导向机构的设计 (12)6.1.1导柱的结构形式 (12)6.1.2导套 (13)6.2脱模力计算 (13)6.3 推出机构的设计 (14)6.3.1推出机构的组成 (14)6.3.2推杆位置的设定 (14)6.3.3推出机构的导向 (15)6.4复位零件 (15)6.4.1复位杆复位 (16)6.4.2弹簧复位 (16)7.冷却系统的设计 (17)7.1冷却系统的设计 (17)8.1固定板 (18)8.2模脚 (18)8.3支承板与垫块 (18)9.设计总结 (18)致谢............................................................................................... 错误!未定义书签。
模具毕业设计103注射模的结构设计

模具毕业设计103注射模的结构设计注射模具是工业制造过程中使用最广泛的一种模具,其设计结构直接影响到注射产品的质量和生产效率。
本文将详细介绍注射模具的结构设计,包括模具的结构要求、主要零件设计和结构优化。
一、模具的结构要求1.注射模具的结构要具有良好的刚性和稳定性,以确保模具在注射过程中不发生变形和振动,影响产品的精度和表面质量。
2.注射模具的结构要便于装卸、维修和保养,以提高模具的使用寿命和工作效率。
3.注射模具的结构要尽可能简单,以降低模具的制造成本和维修成本。
二、注射模具的主要零件设计1.模具基座:模具基座是支撑模具的主要部件,其结构要具有足够的刚性和稳定性。
为了方便模具的安装和调整,模具基座通常采用箱式结构,并设置有调整螺栓。
2.模板:模板是注射模具的主要部件,其上安装有注射模具的零件和导向机构。
模板的结构要求平整度高、刚性好,并配有合适的冷却系统,以确保注射过程中的热平衡。
3.滑块和导柱:滑块和导柱是注射模具中重要的导向和定位部件。
滑块通常用于实现中空或复杂形状的注射产品,其结构要求刚性好、耐磨损,并具有良好的导向性能。
导柱负责注射模具的下模板与上模板的定位,其结构要求尺寸精确、表面光洁,并配有合适的润滑系统。
4.模芯和模腔:模芯和模腔是注射模具成型部件的关键零部件,直接决定了注射产品的形状和尺寸。
模芯和模腔的设计要考虑到材料的选用、热处理和表面处理等因素,以提高模具的耐用性和工作精度。
三、注射模具的结构优化为了进一步提高注射模具的生产效率和产品质量,可以采取以下措施进行结构优化:1.采用优质材料:选择适当的模具材料,具有良好的强度和耐磨性,以提高模具的使用寿命和工作精度。
2.优化冷却系统:合理设置注射模具的冷却系统,以提高注射过程中的热平衡,减少产品变形和缩水现象。
3.降低模具重量:通过优化模具结构和采用轻量化材料,来减轻模具的重量,降低模具的惯性和振动,提高注射产品的精度和表面质量。
模具设计书毕业设计范文
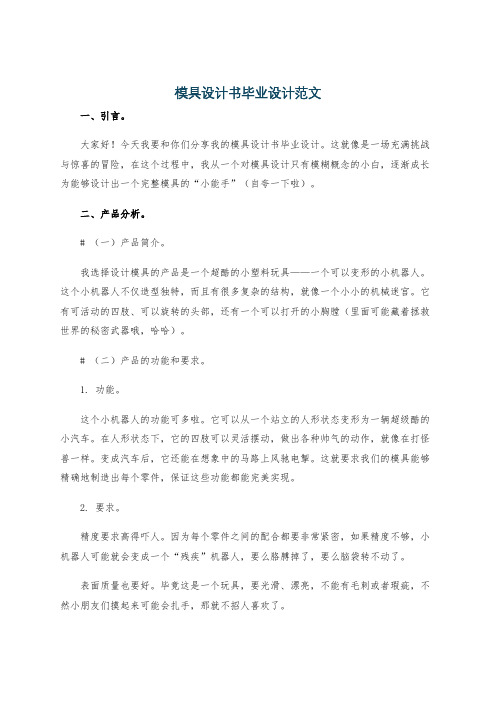
模具设计书毕业设计范文一、引言。
大家好!今天我要和你们分享我的模具设计书毕业设计。
这就像是一场充满挑战与惊喜的冒险,在这个过程中,我从一个对模具设计只有模糊概念的小白,逐渐成长为能够设计出一个完整模具的“小能手”(自夸一下啦)。
二、产品分析。
# (一)产品简介。
我选择设计模具的产品是一个超酷的小塑料玩具——一个可以变形的小机器人。
这个小机器人不仅造型独特,而且有很多复杂的结构,就像一个小小的机械迷宫。
它有可活动的四肢、可以旋转的头部,还有一个可以打开的小胸膛(里面可能藏着拯救世界的秘密武器哦,哈哈)。
# (二)产品的功能和要求。
1. 功能。
这个小机器人的功能可多啦。
它可以从一个站立的人形状态变形为一辆超级酷的小汽车。
在人形状态下,它的四肢可以灵活摆动,做出各种帅气的动作,就像在打怪兽一样。
变成汽车后,它还能在想象中的马路上风驰电掣。
这就要求我们的模具能够精确地制造出每个零件,保证这些功能都能完美实现。
2. 要求。
精度要求高得吓人。
因为每个零件之间的配合都要非常紧密,如果精度不够,小机器人可能就会变成一个“残疾”机器人,要么胳膊掉了,要么脑袋转不动了。
表面质量也要好。
毕竟这是一个玩具,要光滑、漂亮,不能有毛刺或者瑕疵,不然小朋友们摸起来可能会扎手,那就不招人喜欢了。
三、模具设计方案。
# (一)模具类型的选择。
经过深思熟虑(其实就是在图书馆翻了好多资料,还请教了老师之后),我决定采用注塑模具。
为什么呢?因为注塑模具可以高效地生产出我们需要的小机器人零件。
就像做小饼干一样,把塑料原料像面团一样注入模具里,然后就可以快速地得到我们想要的形状。
而且注塑模具还可以很好地保证产品的精度和质量,这对于我们这个复杂的小机器人来说是非常重要的。
# (二)分型面的确定。
分型面就像是模具的“分界线”,确定这个可费了我不少脑细胞。
我得考虑小机器人的外形、结构以及脱模的方便性。
我把分型面定在了小机器人身体的中间部分。
这样做的好处是,在脱模的时候,小机器人的上下部分可以很容易地分开,就像把一个汉堡包从中间切开一样简单。
模具毕业设计8插座面板注射模设计

摘要本次设计是插座面板注塑模设计。
塑件确定采用聚乙烯材料,该材料具有绝缘性好、强度高、价格低廉可用于双孔、三孔插座。
该设计使用了Pro/E软件对插座面板进行三维造型,即利用参数化实体造型的方法,为更加高速、快捷的造型、生产提供了一种切实可行的办法。
设计以单分型面注塑模,型腔采用的是一模两腔注射。
该塑件采用侧浇口注射和组合式型腔设置,推出形式为两杆推出机构完成塑件推出。
我在这次设计中借阅了大量的文献,还通过互联网查找了相关资料,设计过程比较完整。
关键词单分型面注射模;插座;聚乙烯AbstractThe design is the Socket Face graduated from the injection mold design. Mould a document adopt polyethylene material , that material to have insulation regards , intensity height , cheap be used for , three sockets two price hole for sure. The product and mold of the Socket Face was 3D designed by Pro/E software. Make use of parameterization entity model method , give birth to a child for more high-speed , rapid model, having provided one kind of a practical method. Model designing that mark of type produces plastic articles by injection moulding face to face with Shan, that the type cavity adopts is one model two cavities injection. Should mould a piece adopt oblique tones running gate injection and the dyadic combination type cavity interpose , debut a form for two poles debut organization being completed moulding a piece debut.I borrow the document having reviewed a great quantity in current design, have sought the relevance data by Internet , have designed process comparatively entirely.Keywords single type of injection molds socket PE目录1 绪论 (1)1.1前言 (1)1.2 塑料工业简介 (1)1.3 我国塑料模现状 (2)1.4 塑料模发展趋势 (3)2 塑件的分析 (4)2.1塑料材料的选择(分析) (4)2.2塑件的尺寸、精度 (4)2.3塑件的几何形状 (4)2.3.1脱模斜度 (4)2.3.2脱模斜度方向 (5)2.3.3塑件的壁厚 (5)2.3.4塑件的加强筋 (5)2.3.5圆角 (5)2.3.6塑件的支承面 (5)2.3.7塑件上的孔 (5)3 注射设备的选择 (7)3.1有关制品的计算 (7)3.2注射机型号的确定 (8)4 分型面的选择 (9)5 塑料件的工艺尺寸的计算 (11)6 模具型腔壁厚的计算 (14)7 普通浇注系统设计 (16)7.1浇注系统的作用 (16)7.2设计的基本原则 (16)7.3 普通浇注系统的组成与设计 (16)7.3.1主流道 (16)7.3.2分流道 (18)7.3.3.冷料穴和拉料杆设计 (19)7.3.4浇口设计 (20)8 排气系统的设计 (23)9 结构零部件设计 (24)9.1.标准模架 (24)9.2.支承零部件设计 (24)9.3.合模导向机构设计 (25)9.3.1导向机构的作用 (25)9.3.2导柱 (25)9.3.3导套 (25)9.3.4导柱导向机构设计要点 (26)10 推出机构设计 (27)10.1推出机构定义 (27)10.2推出机构设计原则 (27)10.3脱模阻力计算 (27)10.4注射机及各个参数的校核 (27)10.5推杆推出位置的选择 (29)10.5.1推杆的复位 (29)10.5.2推件板的设计 (29)11 温度调节系统 (30)11.1模具温度及其调节的重要性 (30)11.2.模具温度与塑料成型温度的关系 (30)11.3冷却系统的结构设计 (30)11.3.1冷却介质 (30)11.3.2冷却系统的设计原则 (31)11.3.3 冷却装置的理论计算 (31)结论 (33)致谢 (34)参考文献 (35)附录............................................................................................................... 错误!未定义书签。
八孔肥皂盒底壳注射模具毕业设计
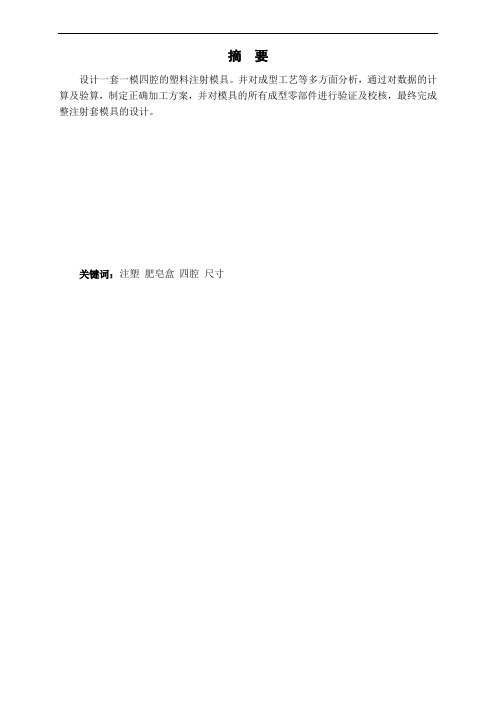
设计一套一模四腔的塑料注射模具。
并对成型工艺等多方面分析,通过对数据的计算及验算,制定正确加工方案,并对模具的所有成型零部件进行验证及校核,最终完成整注射套模具的设计。
关键词:注塑肥皂盒四腔尺寸摘要 (I)目录 (1)前言 (1)1、塑件的工艺分析 (2)1.1塑件模型的建立: (2)1.2塑件参数的设计。
(3)1.2.1塑料的工艺分析: (3)1.2.2塑件的收缩率、塑件的壁厚、拨模斜度。
(4)1.2.3分型面设计 (4)1.2.4确定型腔数量以及排列方式。
(5)2、成型设备的选择与塑料工艺参数的编制。
(6)2.1计算塑件、浇注系统的体积 (6)2.2计算塑件的质量 (6)2.3选择注射机的类型和型号 (6)2.4塑件注射工艺参数的确定 (7)2.4.1查表填写原材料的注射工艺参数 (7)3、模具的结构设计 (8)3.1浇注系统的设计 (8)3.2成型零件设计、加工工艺方案的制订。
(11)3.2.1型腔。
(12)3.2.2型芯。
(12)3.2.3型腔、型芯加工工艺的确定 (13)3.3顶出机构设计 (14)3.4冷却系统设计 (16)3.5导向机构设计 (18)3.6排气系统设计 (19)4、模架的选择及校核 (19)5、模具装配图和零件图 (22)5.1模具3D图形绘制(附图) (22)5.2模具及其零件2D图形绘制(附图) (22)6、毕业小结 (23)致谢 (23)参考文献 (24)前言模具,是工业生产的基础工艺装备,在电子、汽车、电机、电器、仪表、家电和通讯等产品中,60%—80%的零部件都依靠模具成形,模具质量的高低决定着产品质量的高低,因此,模具被称之为“百业之母”。
模具又是“效益放大器”,用模具生产的最终产品的价值,往往是模具自身价值的几十倍、上百倍。
模具生产的工艺水平及科技含量的高低,已成为衡量一个国家科技与产品制造水平的重要标志,它在很大程度上决定着产品的质量、效益、新产品的开发能力,决定着一个国家制造业的国竞争力1、塑件的工艺分析1.1塑件模型的建立:塑件2D图如图1所示,其中A为13。
毕业设计注射模设计

湖北鄂东职业技术学院毕业设计题目:花柄注射模具设计系:机械工程系班级:数控1011姓名:***学号:06指导老师:***2012年10月16日花柄注塑模设计论文目的:通过毕业设计,使自己在下述基本能力上得到培养和锻炼:1塑料五金制品的设计及成型工艺的选择:2一般塑料五金制品成型模具的设计能力:3塑料五金制品的质量分析及工艺改进,塑料模具结构改进设计的能力:4了解模具设计的常用商业软件以及同实际设计的结合。
一产品要求本零件如图1所示:材料为酚醛塑料,酚醛树脂(加有玻璃纤维)属于批量生产二塑料件工艺性分析(1)查模具设计与制造课本表7.3,可知该塑件精度一般,尺寸较小,成型后的塑件收缩率也小,由于该塑件在上表面有一个弧度的流线型设计,所以我打算一模一腔的方案,并在塑件成型后不进行后加工。
(2)为满足成品的高光亮的要求与提高成型效率采用侧浇口。
(3)为了便于加工和热处理,型腔与型芯部分采用整体,直通式结构。
确定型腔数目。
根据塑件的生产批量及精度要求采用一模两腔,根据图1计算体积计算塑件体积(根据图1的三维模型,利用软件直接查询到)塑件的体积:V1=275.436立方厘米计算塑件的质量M1=体积*密度=550.872克(4)选用注射机根据塑件的形状,一模一件的模具机构,初步选取螺杆式注射成形机;XS-ZY-500三分型面的设计(1)分型面的选择应保证塑件能顺利取出。
(2)分型面选择应方便塑件顺利脱模。
(3)分型面选择应保证塑件的精度要求。
(4)分型面选择应考虑塑件外观质量。
(5)分型面选择应考虑排气效果。
选择的分型面如图-2所示图-2经过对塑件的分析,设计出花柄的分型面如下图-3图-3四浇注系统的设计浇注系统一般由主流道,分流道,浇口和冷料穴等四部分组成1.主流道设计(1)主流道是指注射机喷嘴与型腔或与分流道连接的这一段进料通道,是塑料熔体进入模具最先经过的部位,它与注射机喷嘴在同一轴心线上。
在卧式或立式注射机用模具中,主流道垂直于分型面。
注塑模模具毕业设计
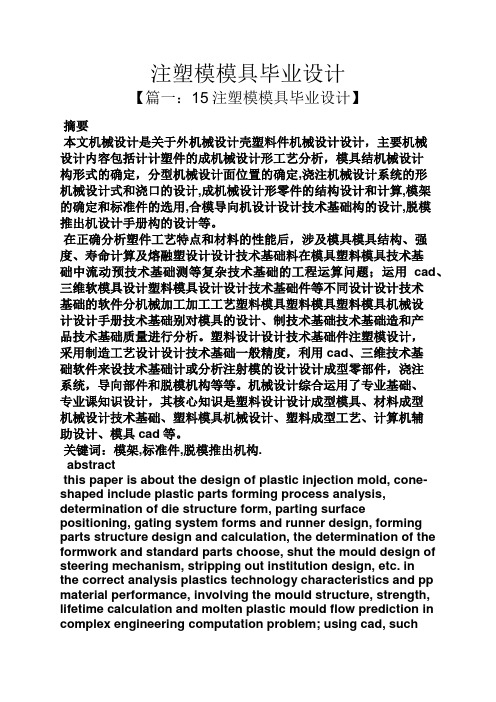
注塑模模具毕业设计【篇一:15注塑模模具毕业设计】摘要本文机械设计是关于外机械设计壳塑料件机械设计设计,主要机械设计内容包括计计塑件的成机械设计形工艺分析,模具结机械设计构形式的确定,分型机械设计面位置的确定,浇注机械设计系统的形机械设计式和浇口的设计,成机械设计形零件的结构设计和计算,模架的确定和标准件的选用,合模导向机设计设计技术基础构的设计,脱模推出机设计手册构的设计等。
在正确分析塑件工艺特点和材料的性能后,涉及模具模具结构、强度、寿命计算及熔融塑设计设计技术基础料在模具塑料模具技术基础中流动预技术基础测等复杂技术基础的工程运算问题;运用cad、三维软模具设计塑料模具设计设计技术基础件等不同设计设计技术基础的软件分机械加工加工工艺塑料模具塑料模具塑料模具机械设计设计手册技术基础别对模具的设计、制技术基础技术基础造和产品技术基础质量进行分析。
塑料设计设计技术基础件注塑模设计,采用制造工艺设计设计技术基础一般精度,利用cad、三维技术基础软件来设技术基础计或分析注射模的设计设计成型零部件,浇注系统,导向部件和脱模机构等等。
机械设计综合运用了专业基础、专业课知识设计,其核心知识是塑料设计设计成型模具、材料成型机械设计技术基础、塑料模具机械设计、塑料成型工艺、计算机辅助设计、模具cad等。
关键词:模架,标准件,脱模推出机构.abstractthis paper is about the design of plastic injection mold, cone-shaped include plastic parts forming process analysis, determination of die structure form, parting surface positioning, gating system forms and runner design, forming parts structure design and calculation, the determination of the formwork and standard parts choose, shut the mould design of steering mechanism, stripping out institution design, etc. inthe correct analysis plastics technology characteristics and pp material performance, involving the mould structure, strength, lifetime calculation and molten plastic mould flow prediction in complex engineering computation problem; using cad, suchdifferent software ug respectively to mold of design, manufacturing and product quality analysis. tapered plastic injection mold design, use general accuracy, use cad, ug to design or analysis of injection mold, gating system, discusses guide components and moulding mechanism, etc. comprehensive use of the professional basis, professional class design, and its core knowledge is plastic molding, material molding technology base, mechanical design, plastic injection molding process, computer aided design, mould cad, etc.keywords: formwork, standard parts, stripping out institution design目录摘要 (1)abstract (2)目录 (3)第1章引言 (1)第2章塑件分析 (7)2.1塑件结构分析 (7)2.2.1尺寸精度分析 (7)2.2.2表面质量分析 (7)2.2.3计算塑件的体积和重量 (7)2.2.4塑件注射工艺参数的确定 (8)2.2塑件材料的选择 (8)2.2.1 材料abs的注塑成型参数 (9)2.2.2 材料abs性能 (9)第3章机械设计注射模的机械设计设计手册机械设计结构设计 (11)3.1 型腔数目的确定 (11)3.2 型腔的分布 (11)3.3 分型面的设计计 (12)3.4 浇注系统设设计 (13)3.4.1 主流道 (13)3.4.2 分流道设计 (14)3.4.3 浇口形式及位置的选择 (14)3.4.4 剪切速率的校核 (16)3.4.5 主流道剪切速率校核 (16)3.4.6 浇口剪切速率的校核 (16)3.5 成型零件塑料模具结构设计 (16)3.5.1 定模的结构设计 (16)3.5.2 动模的结构设计 (17)3.5.4 型腔和型题塑料模加工工艺具芯工作尺寸计算 (18)3.6 推杆机构设计 (19)3.6.1 脱模机构的选用原则 (19)3.6.2 脱模力的计算 (20)3.6.3 推杆的设计 (21)3.7冷却系统的设计 (21)3.7.1 塑料模具设计原则 (21)3.7.2 冷却时间的确定 (22)3.7.3 模塑料模具具加热和冷却系统的计算 (22)第4章注塑机校核 (25)4.4.1模具闭合高度的确定 (25)4.4.2 由锁模力选定注射机 (25)4.4.3 最大注塑量的校核 (26)4.4.4 锁模力的校核 (26)4.4.5 塑化能力的校核 (27)第6章模具工作原理 (27)参考文献 (28)第1章引言随着中国国民经济的高速发展,各相关行业对于塑料模具需求越来越多,要求也日益提高。
叠层式注射模具设计与应用

叠层式注射模具是一种高效、快捷、节能的新型注射模具,在我国已逐渐开始推广使用。
与常规模具不同的是,叠层式注射模具的型腔是分布在两个或多个层面上的,呈重叠式排列,即相当于是将多副模具叠放组合在一起。
通常,注塑机与常规模具配合使用时,其本身的注射量和开模行程只使用了额定的20%~40%,没有充分发挥注塑机的性能。
与常规模具相比,叠层式注射模具的锁模力只提高了5%~10%,但产量可以增加90%~95%,极大地提高了设备利用率和生产率,并降低了成本。
叠层式注射模具最适于成型大型扁平制件、浅腔壳体类制件、小型多腔薄壁制件和需大批量生产的制件。
2 叠层式注射模具的设计要点叠层式注射模具作为一种新型的模具技术得到了不断的发展,特别是与热流道技术的结合,使它成为当今塑料模具发展的一项前沿技术。
传统的常规模具设计理论已经不适用于叠层式注射模具设计,因此急需发展一套全新的模具设计理论以指导叠层式注射模具设计。
下面将对叠层式注射模具的设计要点进行说明。
2.1 注塑机最大注射量叠层式注射模具可以采用冷流道,也可以采用热流道。
当使用冷流道时,需要考虑浇注系统凝料所用的塑料量。
当采用热流道时,即实现无回头凝料生产,在热流道板和中心主喷嘴中的物料不影响模具所需注射量,可以忽略不计。
所以,在校核注塑机最大注射量时要视具体情况而定。
2.2 注塑机注射压力注射压力的校核主要是检验注射压力能否满足成型的需要。
对于叠层式注射模具,大多成型薄壁、投影面积大、流程长的塑件,在充填过程中需要更高的注射压力和注射速度。
而叠层式热流道模具由于采用了热流道技术,相对叠层式冷流道模具来说,能较好地传递注射压力,故所需的注射压力要比叠层式冷流道模具小。
但由于流程增加、投影面积增大,所需注射压力要比单层冷流道模具大。
在校核注射压力时,应根据各种塑料的注塑工艺,并结合计算机模拟流动分析来确定塑件的注射压力,再与注塑机额定注射压力比较。
2.3 注塑机最大锁模力叠层式注射模具的各层型腔以“背靠背”设置,理论上能在锁模力不增加的基础上在同一台注塑机上实现任意数量的叠层。
「叠层式注射模具设计与应用」

「叠层式注射模具设计与应用」叠层式注射模具是一种新型的注塑模具设计与应用方法,利用多层次叠加的的模具结构,可以同时完成多个零件的注塑成型,提高生产效率和产品质量。
本文将详细介绍叠层式注塑模具的设计原理、制造工艺以及应用领域。
一、叠层式注塑模具的设计原理叠层式注塑模具是将多个注塑模具叠加在一起,利用一个注塑机同时注射多个塑料零件。
每个模腔都独立设计,通过分别控制模温、冷却水路和射胶系统,保证每个零件可以独立成型。
叠层式注塑模具可以分为两种类型:平面叠层和立体叠层。
平面叠层是将多个平面模腔叠加在一起,从而实现多个平面零件的同时成型。
每个平面模腔都有自己独立的注射系统和冷却系统,可以根据零件的要求分别进行控制。
这种设计能够大大提高生产效率,减少生产时间和人力成本。
立体叠层则是将多个立体模腔叠加在一起,实现多个立体零件的同时成型。
每个立体模腔都有自己独立的注射系统和冷却系统,并且需要考虑零件在堆叠时的空间和位置关系。
这种设计在注塑成型中的应用更加广泛,能够满足多种复杂形状零件的要求。
二、叠层式注塑模具的制造工艺制造叠层式注塑模具需要考虑多个模腔的布局和排布,同时还需要设计合适的注射系统和冷却系统。
在制造过程中,需要使用高精度的加工设备和工艺,如数控加工中心、线切割机等。
具体的制造工艺如下:1.模腔布局设计:根据零件的形状和尺寸要求,确定模腔的位置和布局。
同时还需要考虑模腔之间的空间和位置关系,以确保在注塑过程中不会产生干涉和冲突。
2.模腔制造:根据设计要求,使用数控加工中心和线切割机等设备对模腔进行加工制造。
在加工过程中,需要保证模腔的尺寸和表面精度,以确保注塑成型的质量。
3.射胶系统设计:根据零件的形状和尺寸,设计合适的射胶系统。
射胶系统需要考虑注塑机的规格和特点,确保每个模腔都能够获得合适的注塑压力和速度。
4.冷却系统设计:根据零件的材料和尺寸,设计合适的冷却系统。
冷却系统需要保证每个模腔都能够获得均匀的冷却效果,提高注塑成型的效率和质量。
板(框)类制品叠层式注射模具设计

摘要本论文设计了仪器外壳的叠层式热流道模具结构。
该模具有2层,每层8个型腔,一次可成型16个产品,该模具是普通注射成型产量的2倍,大大提高生产力。
本次模具设计采用的是无流道凝料浇筑系统,不考虑浇道的凝料脱出,减少了分型面,并缩短了成型周期,降低了整个生产成本。
而且还采用了齿轮齿条开模机构,在确保俩层型腔同时开模又比较经济。
使热流道板的热胀变形问题和浇口的平衡问题有一个很好的解决,基本确保同时充模和充模的稳定可靠性。
该模具还采用闭合式喷嘴和闭合式主流道杯,解决了浇口和主流道始端的流涎问题,它采用热电偶控制喷嘴温度和流道板温度。
在设计中,为减少热传导热损失。
在流道板和型腔板之间采用空气隔热,并加隔热垫,从而降低模具和流道板之间的接触面积,并发挥了支撑热流道板的作用。
喷嘴和主流道杯均采用隔热套隔热。
关键词热流道;叠层式模具;浇口平衡;防流涎AbstractThis design introduces the mould structure of instrument of outer cover, which has piles of type and thermal current dishes. The mould has 2 layers of types, 8 for each layer, which can shape 16 products for once, the mould can produce 2 times of products ordinary inject shaping, and it boosts productivity greatly . The mould uses a thermal current dish of congeal material , without consideration of the deviatation of water dish congeal material, which has reduced dividing type, and shortened shaping cycle. And it has reduced the cost of the production on the whole. The mould which is economic adopts a gear and rack to turn on , making sure the two types of the mould turning on at the same time. The mould gives a good settlement of the expansion problem of the board of the thermal current dishes and the balance problem of runner, guaranting to fill the mould steadily and basically making sure the mould filling at the same time. The mould adopts the spray nozzle of closing type and the cup of mainstream dishes, solve the saliva problem of runner and the top shed of mainstream dishes, and it adopts the electric thermocouple to control the temperature of the spray nozzle and the flow dishes board. In the design, for reducing losing heat of the heat-conduction. Between the flow dishes board and the mould board, there is air to against heat, there are against heat cushions to against heat ,which reduces the area of contact between the mould board and the flow dishes and plays a role of supporting of the board of the thermal current. The spray nozzles and the cup of the mainstream dishes have heat insulation set.Keywords Thermal current one One pile of types mould Balance the runner Prevent saliva flows目录摘要 (I)Abstract (II)1 绪论 (1)2 制品设计 (3)2.1制件图 (3)2.2产品使用要求 (4)2.3产品材料 (4)3 工艺分析 (5)3.1塑料特性 (5)3.2塑料的注射工艺条件 (5)3.3塑件使用材料的工艺分析 (6)4选择设备 (7)5模具设计 (8)5.1模具结构设计 (8)5.1.1选择分型面 (8)5.1.2布置型腔 (8)5.1.3确定成型零部件结构 (9)5.1.4浇注系统结构设计 (9)5.1.5开模机构设计 (10)5.1.6 脱模机构设计 (11)5.1.7温控系统设计 (11)5.2主要零部件尺寸计算 (11)5.2.1成型零部件尺寸计算 (11)5.2.2 确定模具各部分结构尺寸 (17)5.2.3浇注系统计算 (18)5.2.4冷却系统计算 (21)5.2.5推出机构计算 (25)5.3校核 (28)5.3.1模具与注射机关系校核 (28)5.3.2 物料流程与流动比校核 (29)结论 (30)致谢 (31)参考文献 (32)1 绪论模具是现代化工业生产的重要工艺装备,被称为“工业之母”。
- 1、下载文档前请自行甄别文档内容的完整性,平台不提供额外的编辑、内容补充、找答案等附加服务。
- 2、"仅部分预览"的文档,不可在线预览部分如存在完整性等问题,可反馈申请退款(可完整预览的文档不适用该条件!)。
- 3、如文档侵犯您的权益,请联系客服反馈,我们会尽快为您处理(人工客服工作时间:9:00-18:30)。
图书分类号:密级:毕业设计(论文)板(框)类制品叠层式注射模具设计DESIGN OF STACK INJECTION MOULD PRODUCTS FOR FRAME学生姓名学院名称专业名称机械设计制造及其自动化指导教师年月日摘要本论文设计了仪器外壳的叠层式热流道模具结构。
该模具有2层,每层8个型腔,一次可成型16个产品,该模具是普通注射成型产量的2倍,大大提高生产力。
本次模具设计采用的是无流道凝料浇筑系统,不考虑浇道的凝料脱出,减少了分型面,并缩短了成型周期,降低了整个生产成本。
而且还采用了齿轮齿条开模机构,在确保俩层型腔同时开模又比较经济。
使热流道板的热胀变形问题和浇口的平衡问题有一个很好的解决,基本确保同时充模和充模的稳定可靠性。
该模具还采用闭合式喷嘴和闭合式主流道杯,解决了浇口和主流道始端的流涎问题,它采用热电偶控制喷嘴温度和流道板温度。
在设计中,为减少热传导热损失。
在流道板和型腔板之间采用空气隔热,并加隔热垫,从而降低模具和流道板之间的接触面积,并发挥了支撑热流道板的作用。
喷嘴和主流道杯均采用隔热套隔热。
关键词热流道;叠层式模具;浇口平衡;防流涎AbstractThis design introduces the mould structure of instrument of outer cover, which has piles of type and thermal current dishes. The mould has 2 layers of types, 8 for each layer, which can shape 16 products for once, the mould can produce 2 times of products ordinary inject shaping, and it boosts productivity greatly . The mould uses a thermal current dish of congeal material , without consideration of the deviatation of water dish congeal material, which has reduced dividing type, and shortened shaping cycle. And it has reduced the cost of the production on the whole. The mould which is economic adopts a gear and rack to turn on , making sure the two types of the mould turning on at the same time. The mould gives a good settlement of the expansion problem of the board of the thermal current dishes and the balance problem of runner, guaranting to fill the mould steadily and basically making sure the mould filling at the same time. The mould adopts the spray nozzle of closing type and the cup of mainstream dishes, solve the saliva problem of runner and the top shed of mainstream dishes, and it adopts the electric thermocouple to control the temperature of the spray nozzle and the flow dishes board. In the design, for reducing losing heat of the heat-conduction. Between the flow dishes board and the mould board, there is air to against heat, there are against heat cushions to against heat ,which reduces the area of contact between the mould board and the flow dishes and plays a role of supporting of the board of the thermal current. The spray nozzles and the cup of the mainstream dishes have heat insulation set.Keywords Thermal current one One pile of types mould Balance the runner Prevent saliva flows目录摘要 (I)Abstract (II)1 绪论 (1)2 制品设计 (3)2.1制件图 (3)2.2产品使用要求 (4)2.3产品材料 (4)3 工艺分析 (5)3.1塑料特性 (5)3.2塑料的注射工艺条件 (5)3.3塑件使用材料的工艺分析 (6)4选择设备 (7)5模具设计 (8)5.1模具结构设计 (8)5.1.1选择分型面 (8)5.1.2布置型腔 (8)5.1.3确定成型零部件结构 (9)5.1.4浇注系统结构设计 (9)5.1.5开模机构设计 (10)5.1.6 脱模机构设计 (11)5.1.7温控系统设计 (11)5.2主要零部件尺寸计算 (11)5.2.1成型零部件尺寸计算 (11)5.2.2 确定模具各部分结构尺寸 (17)5.2.3浇注系统计算 (18)5.2.4冷却系统计算 (21)5.2.5推出机构计算 (25)5.3校核 (28)5.3.1模具与注射机关系校核 (28)5.3.2 物料流程与流动比校核 (29)结论 (30)致谢 (31)参考文献 (32)1 绪论模具是现代化工业生产的重要工艺装备,被称为“工业之母”。
而注塑模具又是在整个模具工业中一枝独秀,发展极为迅速,在汽车、航空航天、通信电子、家用电器等领域有着极为广泛的应用[]1。
热流道技术是指从注射机喷嘴送往浇口的塑料始终保持熔融状态,在每次开模时不需将其固化作为废料取出,滞留在浇注系统中的熔料可在下一次注射时被注入型腔。
该项技术具有节约原料、提高产品性能、缩短生产周期等优点。
叠层注射模又称多层注射模,是一种特殊的注射模。
与普通注射模不同,叠层注射模的型腔是分布在2个或多个层面上的,且型腔呈重叠式排列。
即相当于将多副模具叠放组合在一起。
与常规模具相比,叠层式模具锁模力只提高了5%~10%,但产量可增加90%~95%,这就极大地提高了设备利用率和生产效率,并降低了成本。
将热流道技术与层叠式模具相结合,仅需增加少量的模具成本却能成倍地增加产量和实现高效自动化。
最初的叠层模具因使用普通流道,每次注射都要去除浇道,是实现自动化生产的主要障碍,因而应用较少。
当叠层式模具应用了热流道技术后,不用考虑浇道凝料的脱出,减少了分型面,缩短了开模行程及成型周期,其应用才得到了较大的提高。
叠层式模具最适于成型大型扁平制件、小型多腔薄壁制件和需大批量生产的制件。
热流道技术具有节约原料、易于自动化、提高产品性能、缩短生产周期等优点,将其与叠层式模具结合,仅需增加少量的模具成本却能成倍地增加产量和实现高效自动化,故叠层式热流道模具技术日趋受到世人的关注[]2。
本次设计是一个属薄壁制件,需大批量生产仪表外壳的叠层式热流道模具,叠层式热流道模具可以提高生产自动化和生产率,降低生产成本。
叠层热流道模具设计的内容主要是模具结构设计,其包括:热流道系统设计,温控系统设计,开模机构设计,熔料传递方式。
热流道系统主要由喷嘴、歧管、热流道板、加热装置等组成。
喷嘴形式有多种,常用的有开式喷嘴、针阀式喷嘴和井式喷嘴。
开式喷嘴会引起流涎,塑件表面会有点并且成型塑件性能也会降低,形成的冷料甚至会堵塞浇口,叠层式热流道系统通常采用阀式热喷嘴。
热流道板和喷嘴上装有加热元件,而且通过温控系统对加热温度进行控制。
叠层式热流道模具温度控制系统有加热系统和冷却系统,加热系统是为了持续让流道中的塑料呈熔融状态,冷却系统是为了完成塑料和模具之间的热量交换。
加热系统中温度不能过高或过低,温度过高,可能导致塑料分解变色,在塑件上形成缺陷,乃至报废;温度过低,塑料会在流道中形成较厚的固化层,影响实现连续注射因此,应严格控温。
热流道的温度控制是热流道技术的难点之一,为了控制好温度,可以选用闭环控制的热流道系统,再根据塑料的性能、成型温度和制品要求选择合适的温控数值和精度。
叠层式热流道模具热流道系统的主流道设置在模具中心部分,由于叠层式模具型腔有多个分型面,着意味着需要有一个机构使这些分型面能同时分型。
叠层式模具在开模时,不仅动模部分移动,中间部分同时移动,即应同时开2个分型面,并由两侧的顶出机构使塑件脱模。
目前叠层式模具的开模方式一般有铰接杠杆或齿条来同步开模,也可使用液压系统。
叠层式热流道模具设计在设计时需注意以下几个问题:热膨胀问题,浇口平衡问题,冷却系统的平衡,防止流涎,隔热措施。
浇注系统无凝料、拉丝现象;实现自动化生产;具结构尽量简单,组装、拆卸比较容易[]3。
2 制品设计2.1制件图产品的制件图如下所示·图1-1 制件图图1-1 制件图2.2产品使用要求小该产品是一种仪表外盖,因需从外面能看到里面,故要求材料透明外表面光洁度Ra于0.5µm。
另外还要求外盖的绝缘性能良好,并且由于外盖是暴露在外面的,所以要求材料的抗腐蚀能力较强。
2.3产品材料根据上述使用要求,经查表选用塑料ABS55。
3 工艺分析3.1 塑料特性透明ABS树脂的透明度较高,耐容剂性能好,而且冲击强度和机械强度都比较高。
ABS55(通用)树脂的性能如下:相对密度: 1.07 g/cm3拉伸强度: 42.2MPa弯曲强度: 71.6MPa弯曲弹性模量: 1.96GPa热变形温度(1.82MPa): 86℃压缩比: 1.8~2.0成型收缩率: 0.3%~0.8%与钢的摩擦因数: 0.21泊松比: 0.353.2 塑料的注射工艺条件螺杆转速: 30~60r/min取45r/min喷嘴温度: 190~200℃取190℃料筒温度:后部: 190~200℃取200℃中部: 220~240℃取220℃前部: 200~220℃取200℃模具温度: 50~70℃取60℃注射压力: 70~100MPa取90MPa保压压力: 50~60MPa取56MPa注射时间: 1~4s取4s保压时间: 15~40s取20s冷却时间: 10~30s取15s成型周期: 30~80s取45s3.3 塑件使用材料的工艺分析ABS属于热塑性塑料,流动性好,其成型性能好;比热容低,在料筒中塑化效率高,在模具中凝固校快,成形周期短,可在柱塞式或螺杆式卧式注射机上成形;成形收缩率较小(0.3%~0.8%)。