玻璃的制备工艺设计
玻璃工艺设计方案

玻璃工艺设计方案可以根据不同的应用需求和设计目的进行定制,以下是一般的玻璃工艺设计方案的一些常见要点:
1. 玻璃工艺类型:
-雕刻工艺:利用激光或机械刀具对玻璃表面进行精细雕刻,创造出各种图案、文字或立体效果。
-印刷工艺:采用丝网印刷或数字印刷技术,在玻璃表面印刷图案、标识或装饰性设计。
-热弯工艺:通过加热和成形处理,使玻璃产生弯曲或曲面效果,适用于制作特殊形状的玻璃制品。
-镶嵌工艺:将不同颜色或材质的玻璃片镶嵌在一起,形成图案或装饰效果。
2. 设计元素:
-图案设计:根据客户需求或设计主题,精心设计图案、纹样或装饰元素,体现个性化和美学价值。
-色彩搭配:选择合适的玻璃颜色和色彩搭配方案,增强视觉效果和空间氛围。
-光影效果:考虑玻璃的透明性和折射性,设计能够利用光线产生独特光影效果的工艺方案。
-结构稳定性:确保设计符合玻璃工艺的结构强度和稳定性要求,避免因设计问题导致制品损坏或安全隐患。
3. 制作工艺:
-工艺流程:制定详细的生产工艺流程,包括玻璃切割、加工、装饰、烧制等环节,保证制品质量和工期。
-材料选择:选用高质量的玻璃原料和辅助材料,确保制品的透明度、光泽度和耐久性。
-工艺技术:结合先进的玻璃加工技术和设备,实现精准加工和高效生产,提高工艺品质和生产效率。
综合考虑设计元素、制作工艺和实际应用需求,定制适合的玻璃工艺设计方案可以创造出具有艺术感和实用性的玻璃制品,满足不同场景和用途的装饰需求。
在实际设计过程中,还需要与玻璃工艺专业人士密切合作,共同完成设计、制作和验收等环节,确保最终成品符合预期效果和质量标准。
玻璃制造工艺(3篇)

第1篇一、引言玻璃是一种常见的无机非金属材料,具有透明、坚硬、耐高温、化学稳定性好等特点。
随着科技的不断发展,玻璃在建筑、汽车、电子、光学等领域得到了广泛应用。
本文将介绍玻璃制造工艺,包括原料的选择、熔制、成型、退火、切割、磨光、清洗等环节。
二、原料选择玻璃制造的原材料主要包括石英砂、纯碱、石灰石、长石等。
这些原料经过破碎、筛选、混合等过程,制备成合格的玻璃原料。
1. 石英砂:石英砂是玻璃制造的主要原料,占原料总量的70%左右。
它主要来源于天然的石英岩、石英砂岩等。
石英砂的化学成分主要是SiO2,具有较高的熔点和良好的化学稳定性。
2. 纯碱:纯碱是玻璃制造中的一种助熔剂,其主要成分是Na2CO3。
纯碱在玻璃制造过程中起到降低熔点和改善玻璃性质的作用。
3. 石灰石:石灰石是玻璃制造中的一种助熔剂,其主要成分是CaCO3。
石灰石在玻璃制造过程中起到降低熔点和提高玻璃化学稳定性的作用。
4. 长石:长石是玻璃制造中的一种原料,其主要成分是K2O和Na2O。
长石在玻璃制造过程中起到提高玻璃的化学稳定性和改善玻璃性质的作用。
三、熔制熔制是玻璃制造工艺中的关键环节,主要包括以下步骤:1. 加热:将原料放入玻璃熔炉中,通过加热使原料熔化。
熔炉类型有电熔炉、燃油熔炉、燃气熔炉等。
2. 熔化:加热至一定温度后,原料开始熔化。
熔化过程中,原料中的杂质会逐渐析出,形成熔渣。
3. 混合:熔化过程中,通过搅拌使熔融的玻璃均匀混合,确保玻璃成分均匀。
4. 调节:根据玻璃成分和性能要求,对熔融玻璃进行成分和温度的调节。
四、成型成型是将熔融玻璃制成所需形状和尺寸的过程。
常用的成型方法有:1. 浇注成型:将熔融玻璃倒入模具中,冷却固化后取出。
适用于制造平板玻璃、瓶罐玻璃等。
2. 拉制成型:将熔融玻璃通过拉丝机拉制成细长的玻璃丝。
适用于制造玻璃纤维、玻璃丝等。
3. 挤压成型:将熔融玻璃通过模具挤压成所需形状。
适用于制造玻璃管、玻璃棒等。
微晶玻璃生产工艺设计
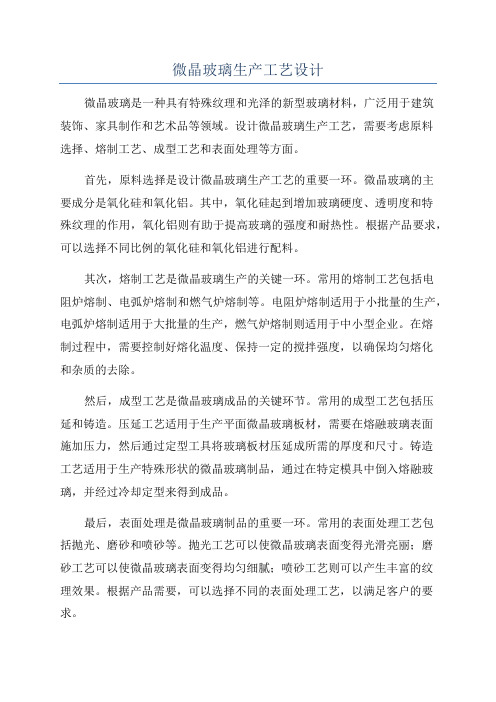
微晶玻璃生产工艺设计微晶玻璃是一种具有特殊纹理和光泽的新型玻璃材料,广泛用于建筑装饰、家具制作和艺术品等领域。
设计微晶玻璃生产工艺,需要考虑原料选择、熔制工艺、成型工艺和表面处理等方面。
首先,原料选择是设计微晶玻璃生产工艺的重要一环。
微晶玻璃的主要成分是氧化硅和氧化铝。
其中,氧化硅起到增加玻璃硬度、透明度和特殊纹理的作用,氧化铝则有助于提高玻璃的强度和耐热性。
根据产品要求,可以选择不同比例的氧化硅和氧化铝进行配料。
其次,熔制工艺是微晶玻璃生产的关键一环。
常用的熔制工艺包括电阻炉熔制、电弧炉熔制和燃气炉熔制等。
电阻炉熔制适用于小批量的生产,电弧炉熔制适用于大批量的生产,燃气炉熔制则适用于中小型企业。
在熔制过程中,需要控制好熔化温度、保持一定的搅拌强度,以确保均匀熔化和杂质的去除。
然后,成型工艺是微晶玻璃成品的关键环节。
常用的成型工艺包括压延和铸造。
压延工艺适用于生产平面微晶玻璃板材,需要在熔融玻璃表面施加压力,然后通过定型工具将玻璃板材压延成所需的厚度和尺寸。
铸造工艺适用于生产特殊形状的微晶玻璃制品,通过在特定模具中倒入熔融玻璃,并经过冷却定型来得到成品。
最后,表面处理是微晶玻璃制品的重要一环。
常用的表面处理工艺包括抛光、磨砂和喷砂等。
抛光工艺可以使微晶玻璃表面变得光滑亮丽;磨砂工艺可以使微晶玻璃表面变得均匀细腻;喷砂工艺则可以产生丰富的纹理效果。
根据产品需要,可以选择不同的表面处理工艺,以满足客户的要求。
综上所述,设计微晶玻璃生产工艺需要考虑原料选择、熔制工艺、成型工艺和表面处理等方面。
通过合理的工艺设计和优质的原材料,可以生产出质量优良、纹理独特的微晶玻璃制品。
玻璃生产工艺的课程设计
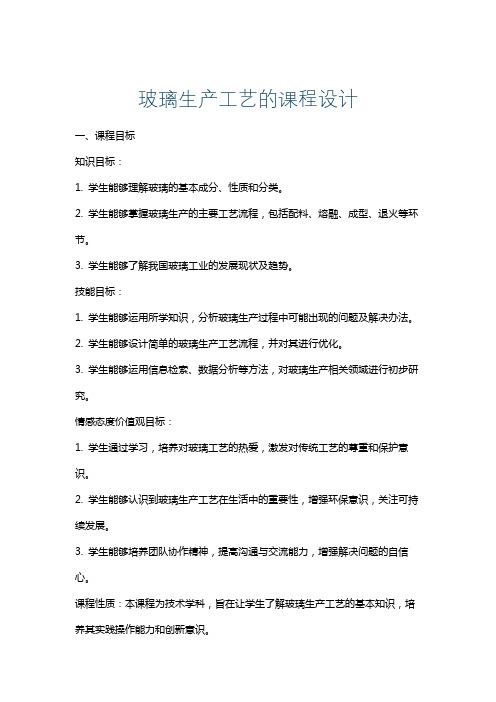
玻璃生产工艺的课程设计一、课程目标知识目标:1. 学生能够理解玻璃的基本成分、性质和分类。
2. 学生能够掌握玻璃生产的主要工艺流程,包括配料、熔融、成型、退火等环节。
3. 学生能够了解我国玻璃工业的发展现状及趋势。
技能目标:1. 学生能够运用所学知识,分析玻璃生产过程中可能出现的问题及解决办法。
2. 学生能够设计简单的玻璃生产工艺流程,并对其进行优化。
3. 学生能够运用信息检索、数据分析等方法,对玻璃生产相关领域进行初步研究。
情感态度价值观目标:1. 学生通过学习,培养对玻璃工艺的热爱,激发对传统工艺的尊重和保护意识。
2. 学生能够认识到玻璃生产工艺在生活中的重要性,增强环保意识,关注可持续发展。
3. 学生能够培养团队协作精神,提高沟通与交流能力,增强解决问题的自信心。
课程性质:本课程为技术学科,旨在让学生了解玻璃生产工艺的基本知识,培养其实践操作能力和创新意识。
学生特点:六年级学生具有一定的逻辑思维能力和动手操作能力,对新鲜事物充满好奇心,但注意力集中时间较短。
教学要求:结合学生特点,采用生动有趣的教学方法,注重理论与实践相结合,充分调动学生的主观能动性,提高课堂参与度。
通过课程学习,使学生在掌握知识技能的同时,培养正确的价值观和情感态度。
将课程目标分解为具体的学习成果,便于后续教学设计和评估。
二、教学内容1. 玻璃的基本知识:- 玻璃的成分、性质和分类- 玻璃在生活中的应用2. 玻璃生产工艺:- 配料过程:原料的选择、配比及作用- 熔融过程:熔炉结构、熔融原理及控制参数- 成型过程:吹制、拉制、压制等成型方法- 退火过程:退火的目的、工艺及设备3. 玻璃生产中的问题及解决方法:- 分析生产过程中可能出现的缺陷,如气泡、结石等- 探讨缺陷产生的原因及解决办法4. 玻璃工业发展概况:- 我国玻璃工业的现状、发展趋势及政策- 国内外玻璃生产工艺的对比及优缺点分析5. 实践操作与创新能力培养:- 设计简单的玻璃生产工艺流程- 分析并优化现有工艺流程- 创新设计玻璃制品,培养创新意识教学内容安排与进度:第一课时:玻璃的基本知识、应用及分类第二课时:玻璃生产工艺(配料、熔融、成型、退火)第三课时:玻璃生产中的问题及解决方法第四课时:玻璃工业发展概况及国内外对比第五课时:实践操作与创新能力培养教材章节关联:《技术学科》六年级上册第五章“无机非金属材料”,第二节“玻璃及陶瓷”。
玻璃制品生产工艺技术手册
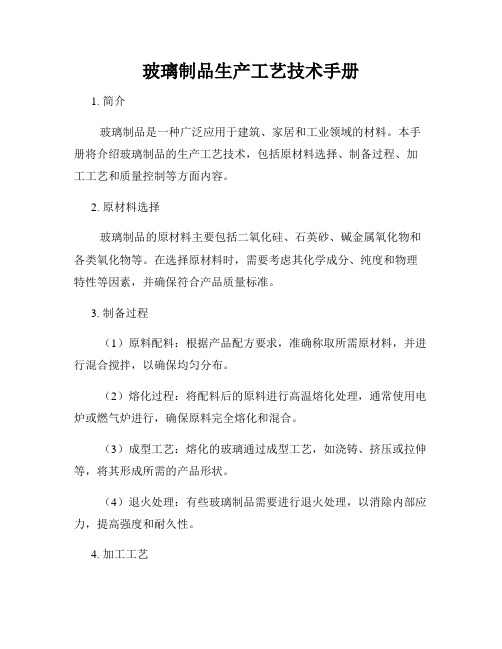
玻璃制品生产工艺技术手册1. 简介玻璃制品是一种广泛应用于建筑、家居和工业领域的材料。
本手册将介绍玻璃制品的生产工艺技术,包括原材料选择、制备过程、加工工艺和质量控制等方面内容。
2. 原材料选择玻璃制品的原材料主要包括二氧化硅、石英砂、碱金属氧化物和各类氧化物等。
在选择原材料时,需要考虑其化学成分、纯度和物理特性等因素,并确保符合产品质量标准。
3. 制备过程(1)原料配料:根据产品配方要求,准确称取所需原材料,并进行混合搅拌,以确保均匀分布。
(2)熔化过程:将配料后的原料进行高温熔化处理,通常使用电炉或燃气炉进行,确保原料完全熔化和混合。
(3)成型工艺:熔化的玻璃通过成型工艺,如浇铸、挤压或拉伸等,将其形成所需的产品形状。
(4)退火处理:有些玻璃制品需要进行退火处理,以消除内部应力,提高强度和耐久性。
4. 加工工艺(1)切割加工:将成型的玻璃制品进行切割,根据设计要求切割出所需尺寸和形状。
(2)打磨抛光:通过机械磨削和抛光,使切割的玻璃制品表面光滑、平整,并去除锋利的边缘。
(3)钻孔和刻字:根据需要,使用特殊工具进行钻孔和刻字,以便安装和定制化需求。
5. 质量控制玻璃制品的质量控制非常重要,以确保产品的安全和可靠性。
(1)原材料检验:对原材料进行严格的化学分析和物理性能测试,以确保其符合产品标准要求。
(2)生产过程监控:通过实施严格的工艺控制和现场监测,确保制造过程中各项参数和指标的稳定性和一致性。
(3)成品检验:对成品进行外观检查、尺寸测量和物理性能测试,以验证产品是否符合设计要求和客户需求。
(4)质量管理体系:建立完善的质量管理体系,包括内部审核、持续改进和客户反馈等环节,以不断提高产品质量和客户满意度。
6. 安全注意事项在玻璃制品生产过程中,需要严格遵守相关的安全操作规程,确保员工和设备的安全。
(1)佩戴个人防护装备:包括安全眼镜、手套、防护服等,以防止意外伤害。
(2)操作注意事项:严禁违规操作,如过度振动、边沿碰撞等,以避免玻璃制品的损坏和工人的意外伤害。
玻璃制备过程范文

玻璃制备过程范文玻璃是一种无机非晶固体,具有透明、坚硬、抗腐蚀、耐高温等特性,广泛应用于建筑、包装、光学仪器等领域。
玻璃的制备过程可以简单分为原料准备、熔融、成型和退火四个阶段。
下面将详细介绍每个阶段的过程。
原料准备:玻璃制备的主要原料包括硅石、碱金属盐、石灰石等。
首先,将这些原料按照一定比例进行混合,确保混合物的成分均匀。
然后,将混合物进行研磨,使其颗粒大小均匀且适合熔融。
熔融:熔融是制备玻璃的核心过程。
可以使用多种熔炉进行熔融,包括电炉、燃气炉、卫星溶池等。
其中最常用的是电炉。
首先,将混合物放入炉中,并进行加热。
随着温度的升高,原料开始熔化。
一旦温度达到玻璃熔点,混合物将变成一种粘稠的液体。
此时,可以通过调整温度和熔化时间来控制玻璃的性质。
熔融过程中熔液中的气泡和杂质也会被去除。
成型:在熔融的玻璃液体中,可以通过多种方式将其成型。
最常用的方法是浇铸和拉丝。
在浇铸过程中,将熔融玻璃倒入特定的模具中,然后冷却使其成型。
拉丝方法则是将一根铁棒插入熔融玻璃中,然后缓慢地将玻璃液拉伸成细丝。
这些细丝可以进一步切割成玻璃片。
除了浇铸和拉丝,还有压延、吹制等方法可以用来成型玻璃。
退火:成型后的玻璃往往会由于快速冷却而产生内应力,导致其强度下降。
为了消除这些内应力并提高玻璃的物理性能,需要进行退火处理。
退火是将玻璃加热至一定温度,然后缓慢冷却。
这个过程中,内部应力受到释放,玻璃变得更加坚固和耐用。
除了上述基本过程,玻璃制备还涉及一系列其他工序,如气体净化、表面处理、涂层等。
这些工序的目的是进一步提高玻璃的质量和性能。
总结:玻璃的制备过程包括原料准备、熔融、成型和退火四个阶段。
原料准备是将混合的原料进行研磨,确保成分均匀;熔融是将混合物进行加热,使其熔化成玻璃液;成型可以通过浇铸、拉丝等方式将玻璃液体成型;退火是消除内应力,提高玻璃的物理性能。
玻璃制备过程中还涉及其他工序,如气体净化、表面处理等。
这些工序的目的是进一步提高玻璃的质量和性能。
玻璃生产工艺(1)

第一节 概述
玻璃生产基本流程
成原 配
分 设 计
料 加 工
合 料 制
熔成 化型
备
缺一
退 火
陷次 检制
验品
二
深 加 工
检 验
次 制 品
第二节 原 料
1、种类
主要原料:在一般玻璃中,它的主要成分有SiO2、Na2O、CaO、 Al203、MgO等五种成分,为引入上述成分而使用的原料称主 要原料。
叶腊石
叶腊石
黄腊石
彩腊石
三、引人Na2O的原料
作用:提供游离氧,从而降低玻璃粘度,使玻璃易于熔
融,是良好的助溶剂。Na2O可增加玻璃的热膨胀系 数,降低热稳定性、化学稳定性和机械强度。 (一)纯碱
纯碱是微细白色粉末,易溶于水,它是一种含杂质少的工业 产品,主要杂质有NaCl(不大于1%)。
纯碱易潮解、结块,它的水含量通常波动在9%~10%之间, 应储存在通风干燥的库房内。
在高温放出氧气而起澄清作用。 由于As203的粉状和蒸气都是极毒物质,目前已很少使用。
氧化锑颗粒
纯氧化锑粉
纯氧化砷粉
2.硫酸盐原料
主要有硫酸钠,它在高温时分解逸出气体而起澄清作用。 3.氟化物类原料
以降低玻璃液粘度而起澄清作用。对耐火材料侵蚀大, 产生的气体(HF、SiF4)污染环境,目前已限制使用。
第四节 玻璃的熔制
一、玻璃熔制过程概述
配合料加热时的各种过程
物理过程
化学过程
物理化学过程
1.配合料加热
1.固相反应
1.共熔体的生成
2.配合料脱水
2.各种盐类分解
2.固态溶解、液态 互溶
3.各个组分熔化 3.水化物分解
浮法玻璃工艺流程

浮法玻璃工艺流程
《浮法玻璃工艺流程》
浮法法玻璃工艺流程是一种广泛应用于工业生产中的玻璃制造技术。
该工艺以其简单高效的特点,在玻璃行业中占据着重要的地位。
首先,原料混合进料区的原料仓。
主要有石英砂、石灰石、长石、硼砂、氧化铝。
其次,原料通过粉碎机经必要工序处理后混合成混合均匀的玻璃熔料。
制备好的玻璃熔料会被泵送到浮法玻璃生产线中。
在熔化窑中,玻璃熔料被放入并经过高温熔化。
之后,玻璃熔液经过搅拌,剔除其中的气泡和杂质。
熔液被抽到过渡池中。
过渡池位于浮法生产线的一端,通过预先合理设计的进气装置,使玻璃熔液以恒定的速度向下流动,均匀受热。
随后,玻璃熔液进入浮法池,通过气流将玻璃面铺平,使其在玻璃液面上“漂浮”,并在一定长度的钢带上持续流动。
在这个过程中,玻璃熔液经过调温、挤压和表面处理。
最后,经过冷却和切割、检验完毕后,流水线上产出的玻璃板取得品质合格的产品。
这些玻璃板可应用于建筑、汽车和家居装饰等领域。
浮法玻璃工艺流程以其高效、灵活和节约能源的特点,成为了
现代玻璃工业中最主要的制造工艺之一,为制造出品质优良的玻璃产品提供了可靠的技术支撑。
玻璃生产工艺及原料

玻璃生产工艺及原料玻璃是一种广泛应用于建筑、家居、工业等领域的无机非晶态物质。
它具有透明、坚硬、耐热等特点,广泛用于窗户、镜子、瓶子、容器等制造。
本文将介绍玻璃的生产工艺和原料。
一、玻璃生产工艺1.原料处理:玻璃的主要原料包括石英砂、碳酸钠、石灰石等。
这些原料经过破碎、研磨、筛分等处理后,成为玻璃的配料。
不同种类和用途的玻璃其原料配比也不同。
2.熔融制备:将配料放入玻璃熔窑中进行熔融制备。
熔窑是一个特殊设计的高温容器,通常由特殊材料如耐火砖等构成。
在熔窑中,原料在高温下熔化,形成玻璃熔体。
3.成型:将熔体从熔窑中输送到成型器中。
成型器通常通过旋转、压制等方式将熔体成型为所需的形状,如平板玻璃、玻璃瓶等。
成型完成后,玻璃制品还需要经过退火等处理,以消除内部应力,提高玻璃的强度和稳定性。
4.加工与装饰:将成型完成的玻璃制品进行进一步的加工与装饰。
这包括切割、磨边、打孔、喷涂等工序,以满足不同的使用需求。
同时,可以通过印刷、雕刻和涂层等方式,使玻璃具有不同的颜色、图案和功能。
5.质量检验与包装:对制成的玻璃制品进行质量检验和包装。
质量检验包括外观检查、尺寸检测和物理性能测试等。
合格的制品经过包装后,可上市销售。
二、玻璃生产原料1.石英砂:是玻璃的主要原料之一,其主要成分是二氧化硅(SiO2),具有优良的耐火性和化学稳定性。
石英砂通常由天然石英矿石经过破碎和研磨得到。
2.碳酸钠:是玻璃的主要碱性助熔剂,用于加速熔化和降低熔点。
碳酸钠可以用天然矿石提取或通过化学合成得到。
3.石灰石:主要成分是碳酸钙(CaCO3),用于调节玻璃的成分和性能。
石灰石可由天然矿石如大理石、白云石等提取。
除了以上主要原料外,玻璃生产中还常使用一些助剂和添加剂,如氧化铝、氧化镁、氧化钠等,用于改善玻璃的特性和性能。
三、玻璃的特殊工艺与加工除了常规的玻璃生产工艺外,还有一些特殊的玻璃工艺和加工方法,使得玻璃具有不同的特性和应用。
1.钢化玻璃:将普通玻璃在高温下急冷处理,使其表面形成压应力,提高玻璃的强度和抗冲击性能。
浮法玻璃生产的工艺

202X
浮法玻璃生产的工艺流程
玻璃的成型
原料与配合料的制备
原料的加工
玻璃熔融
主要内容
玻璃的退火
玻璃概述
一次退火:玻璃在成型后直接进入退火炉
玻璃的熔制过程
3
浮法玻璃池窑的结构
1
玻璃的原料和配合料制备过程
5
玻璃退火目的和退火工艺
4
玻璃浮法成型控制参数和锡液性质
本章学习小结
简述浮法玻璃成型的过程。
作业
玻璃熔制主要有哪些过程?
单击此处添加正文,文字是您思想的提炼,请尽量言简意赅的阐述观点。
纯碱(Na2CO3)和芒硝(Na2SO4)
(4)引入CaO的原料
石灰石、方解石,要求CaO≥50%,Fe2O3<0.15%
(5)引入MgO的原料
白云石,要求MgO≥20%,CaO≤32%,Fe2O3<0.15%
01
02
03
澄清剂
01
(7)着色剂
(8)乳浊剂
2.配合料的制备
配合料制备的质量控制:
2
存在于玻璃液中的气体状态: 可见气泡、物理溶解的气体、化学结合的气体
3
玻璃液澄清目的:排除可见气泡
4
影响玻璃液澄清的因素: 玻璃液的粘度、表面张力,澄清剂种类,澄清温度, 炉气压力与成分等
5
澄清剂种类及作用机理:变价氧化物、硫酸盐类、卤化物类
6
对普通钠钙硅玻璃,此阶段温度可低于澄清温度
玻璃液均化过程包括: 不均体的溶解与扩散的均化过程 玻璃液的对流均化过程 因气泡上升而引起的搅拌均化作用
玻璃幕墙加工制造的主要工艺方案

玻璃幕墙重要加工制造工艺方案玻璃幕墙重要加工制造工艺方案提纲:玻璃的磨削尺寸不不不小于。
磨削后尺寸偏差士,两对角线差值误差土。
边缘不得有缺口和斜曲自玻璃幕墙重要加工制造工艺方案一、玻璃加工制造工艺方案1、玻璃裁切加工制作工艺方案(1)玻璃裁切加工制作工艺方案玻璃板块裁切下料前,对设计施工图纸及项目经理部提供的玻璃构件规格、尺寸、加工规定进行符合后,方可进行下料裁切,玻璃板块裁切采用340BCnIS全自动电脑切割机或131BmA大型切割机进行。
(2)玻璃切割加工制作工艺技术保证措施A、采用高精度的数控切割设备,保证玻璃切割划线精度及切割分片精度。
B、玻璃板块尺寸容许偏差(1指玻璃板块的边长)玻璃板块尺寸容许偏差项目IW2m2m 边长偏差±±对角线偏差2、玻璃磨边加工工艺方案(1)玻璃磨边加工工艺方案玻璃磨边采用TITAN200大型电脑卧式双磨边机或点式玻璃加工中心进行。
(2)玻璃磨边加工工艺技术保证措施A、玻璃的!磨削尺寸不不不小于。
磨削后尺寸偏差土,两对角线差值误差土。
边缘不得有缺口和斜曲。
B、玻璃磨边的!外观规定机粗磨边:边部均匀,无崩边、崩角现象,边部有粗糙感,整体显白色,容许存在少许亮点出现;机细磨边:玻璃边缘,有滑腻感,不透明,无崩边、崩角现象;机精磨边:玻璃边缘宽度基本均匀一致,无明显发白和磨纹,边部有一定透明度,色泽发暗;机抛光边:玻璃边平滑、透明、光泽同玻璃表面一致;c、其他规定玻璃边部进行倒棱处理,倒棱l~2mπi;外角部进行倒圆处理,倒圆半径不不不小于玻璃厚度。
3、玻璃钻孔加工制作方案(1)玻璃钻孔加工制作方案点式玻璃板块钻孔前对设计施工图纸及项目经理部提供的玻璃构件孔位、孔径、加工规定进行复核后,方可加工。
玻璃钻孔在玻璃加工中心或HTk2030钻孔机进行。
(2)玻璃钻孔加工制作质量控制A、玻璃孔区)尺寸精度mm公称孔径容许偏差4〜,+51~,+>,÷B、玻璃孔的孔位精度孔中心至规定边容许偏差士;孔中心距离容许偏差土。
微晶玻璃生产工艺设计
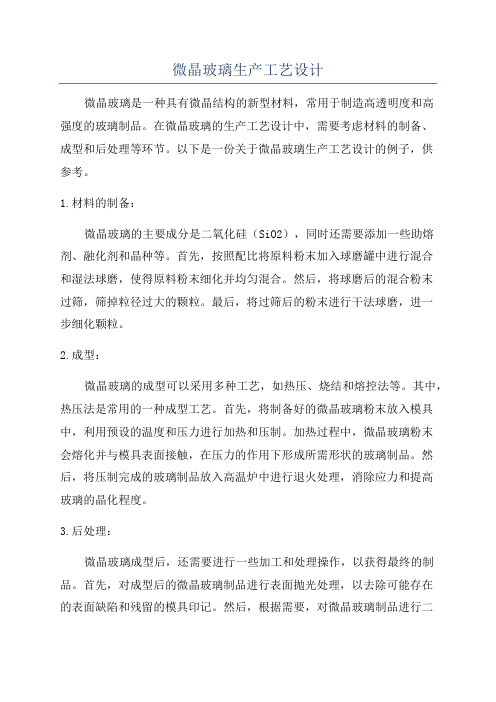
微晶玻璃生产工艺设计微晶玻璃是一种具有微晶结构的新型材料,常用于制造高透明度和高强度的玻璃制品。
在微晶玻璃的生产工艺设计中,需要考虑材料的制备、成型和后处理等环节。
以下是一份关于微晶玻璃生产工艺设计的例子,供参考。
1.材料的制备:微晶玻璃的主要成分是二氧化硅(SiO2),同时还需要添加一些助熔剂、融化剂和晶种等。
首先,按照配比将原料粉末加入球磨罐中进行混合和湿法球磨,使得原料粉末细化并均匀混合。
然后,将球磨后的混合粉末过筛,筛掉粒径过大的颗粒。
最后,将过筛后的粉末进行干法球磨,进一步细化颗粒。
2.成型:微晶玻璃的成型可以采用多种工艺,如热压、烧结和熔控法等。
其中,热压法是常用的一种成型工艺。
首先,将制备好的微晶玻璃粉末放入模具中,利用预设的温度和压力进行加热和压制。
加热过程中,微晶玻璃粉末会熔化并与模具表面接触,在压力的作用下形成所需形状的玻璃制品。
然后,将压制完成的玻璃制品放入高温炉中进行退火处理,消除应力和提高玻璃的晶化程度。
3.后处理:微晶玻璃成型后,还需要进行一些加工和处理操作,以获得最终的制品。
首先,对成型后的微晶玻璃制品进行表面抛光处理,以去除可能存在的表面缺陷和残留的模具印记。
然后,根据需要,对微晶玻璃制品进行二次退火处理,以进一步改善制品的晶化程度和机械强度。
最后,进行最终的质量检验和包装,将制品进行分类、包装和标识,以便于出售和存储。
除了以上所述的关键工艺环节,还需要考虑一些其他的因素。
例如,制备过程中的温度和压力控制、原料的纯度和配比、设备的选择和维护等。
同时,还需建立质量控制体系,对每个生产环节进行监控和检测,以确保微晶玻璃制品的质量和性能符合要求。
总之,微晶玻璃的生产工艺设计涉及材料的制备、成型和后处理等环节。
通过合理的工艺设计和严格的质量控制,可以实现高质量的微晶玻璃制品的生产。
钢化玻璃的制备工艺与流程
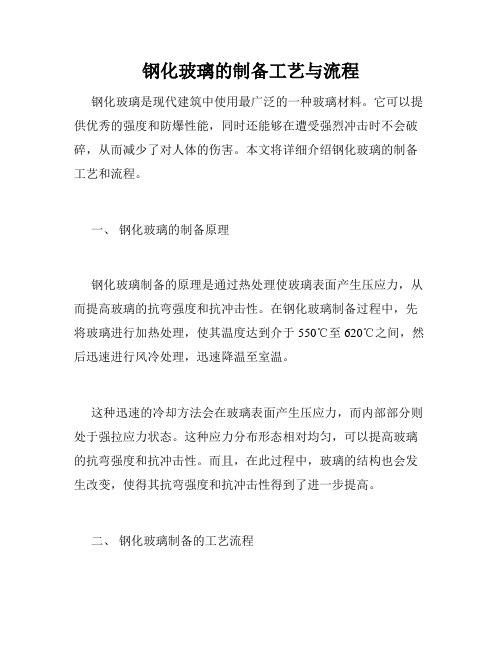
钢化玻璃的制备工艺与流程钢化玻璃是现代建筑中使用最广泛的一种玻璃材料。
它可以提供优秀的强度和防爆性能,同时还能够在遭受强烈冲击时不会破碎,从而减少了对人体的伤害。
本文将详细介绍钢化玻璃的制备工艺和流程。
一、钢化玻璃的制备原理钢化玻璃制备的原理是通过热处理使玻璃表面产生压应力,从而提高玻璃的抗弯强度和抗冲击性。
在钢化玻璃制备过程中,先将玻璃进行加热处理,使其温度达到介于550℃至620℃之间,然后迅速进行风冷处理,迅速降温至室温。
这种迅速的冷却方法会在玻璃表面产生压应力,而内部部分则处于强拉应力状态。
这种应力分布形态相对均匀,可以提高玻璃的抗弯强度和抗冲击性。
而且,在此过程中,玻璃的结构也会发生改变,使得其抗弯强度和抗冲击性得到了进一步提高。
二、钢化玻璃制备的工艺流程钢化玻璃制备的工艺流程通常分为以下几个步骤:1. 选择基材首先需要选择优质的玻璃基材。
在这个过程中,需要检查玻璃基材的表面是否光滑、平整,同时还需要检查玻璃基材的厚度是否符合要求。
钢化玻璃基材的生产商通常会对这些因素进行严格的检测,以确保玻璃的质量符合要求。
2. 切割玻璃在收到玻璃基材之后,需要根据设计要求进行切割。
在切割玻璃之前,需要将玻璃基材的厚度进行精确测量,以确保切割的尺寸符合要求。
3. 打磨玻璃将切割好的玻璃进行打磨,以去除边角毛刺和其他物质。
这样可以确保玻璃表面光滑,并且减少玻璃在加热过程中的破碎率。
4. 预加热在将玻璃加热到钢化温度之前,需要进行预加热。
这个过程可以直接使用玻璃基材的自然热量,在烤炉中回收来加热玻璃。
预加热可以让玻璃均匀受热,保证钢化效果的质量。
5. 加热这是钢化玻璃制备的关键步骤。
在此过程中,需要将玻璃材料加热到钢化温度,即550℃至620℃之间。
温度的选择要考虑到玻璃的厚度和尺寸,不同尺寸的玻璃需要的加热时间也不同。
6. 风冷在加热完成后,需要将玻璃材料迅速放入风冷室进行冷却。
在风冷室中,通过强风对玻璃进行风冷,迅速将其温度降至室温。
制备玻璃的实验报告(3篇)

第1篇一、实验目的1. 了解玻璃的制备过程及其原理。
2. 掌握玻璃熔制、成型、退火等基本工艺。
3. 学习玻璃的化学成分对其性能的影响。
二、实验原理玻璃是一种非晶态固体,主要由硅酸盐、氧化物等组成。
制备玻璃的基本原理是:将原料按照一定比例混合,在高温下熔融,然后通过成型、退火等工艺制成各种玻璃制品。
三、实验材料1. 原料:石英砂、石灰石、长石、纯碱等。
2. 设备:高温熔炉、成型模具、退火炉、实验台等。
3. 仪器:天平、温度计、秒表等。
四、实验步骤1. 配制玻璃原料:按照实验配方,准确称取石英砂、石灰石、长石、纯碱等原料。
2. 熔制玻璃:将称量好的原料放入高温熔炉中,加热至熔融状态。
熔融温度一般为1500℃左右。
3. 成型:将熔融的玻璃液倒入成型模具中,冷却凝固后取出玻璃制品。
4. 退火:将成型后的玻璃制品放入退火炉中,逐渐升温至一定温度(如500℃左右),保持一段时间,然后缓慢降温至室温。
5. 实验数据处理:记录实验过程中各阶段的温度、时间等数据,分析玻璃的制备过程。
五、实验结果与分析1. 实验结果(1)玻璃熔融温度:实验中玻璃熔融温度为1500℃左右。
(2)玻璃制品外观:制备的玻璃制品表面光滑,无气泡、裂纹等缺陷。
(3)退火温度:实验中退火温度为500℃左右。
2. 结果分析(1)玻璃熔融温度:玻璃熔融温度取决于原料的化学成分和熔融过程。
实验中,采用高温熔炉,确保玻璃熔融充分。
(2)玻璃制品外观:玻璃制品外观质量与原料质量、熔制工艺、成型模具等因素有关。
本实验中,通过严格控制原料质量和熔制工艺,制备的玻璃制品外观质量较好。
(3)退火温度:退火温度对玻璃制品的性能有重要影响。
实验中,退火温度为500℃左右,有利于消除玻璃制品的内应力,提高其机械强度。
六、实验结论1. 通过本实验,掌握了玻璃的制备过程及其原理。
2. 掌握了玻璃熔制、成型、退火等基本工艺。
3. 玻璃的化学成分对其性能有重要影响,本实验中通过调整原料比例,制备了性能较好的玻璃制品。
玻璃制作工艺流程
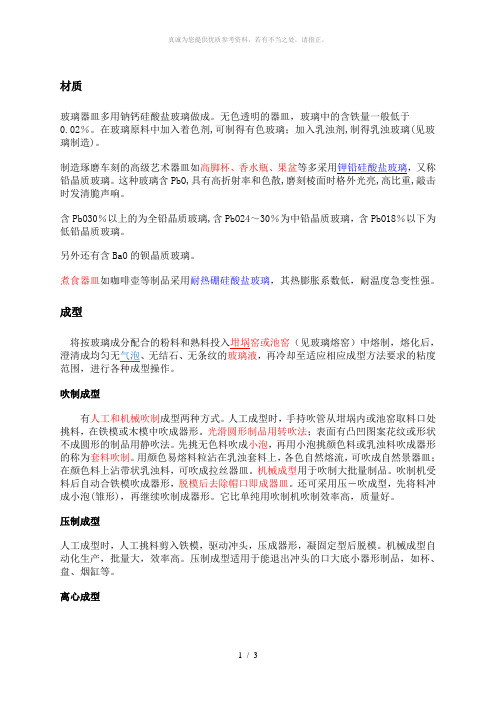
材质玻璃器皿多用钠钙硅酸盐玻璃做成。
无色透明的器皿,玻璃中的含铁量一般低于0.02%。
在玻璃原料中加入着色剂,可制得有色玻璃;加入乳浊剂,制得乳浊玻璃(见玻璃制造)。
制造琢磨车刻的高级艺术器皿如高脚杯、香水瓶、果盆等多采用钾铅硅酸盐玻璃,又称铅晶质玻璃。
这种玻璃含PbO,具有高折射率和色散,磨刻棱面时格外光亮,高比重,敲击时发清脆声响。
含PbO30%以上的为全铅晶质玻璃,含PbO24~30%为中铅晶质玻璃,含PbO18%以下为低铅晶质玻璃。
另外还有含BaO的钡晶质玻璃。
煮食器皿如咖啡壶等制品采用耐热硼硅酸盐玻璃,其热膨胀系数低,耐温度急变性强。
成型将按玻璃成分配合的粉料和熟料投入坩埚窑或池窑(见玻璃熔窑)中熔制,熔化后,澄清成均匀无气泡、无结石、无条纹的玻璃液,再冷却至适应相应成型方法要求的粘度范围,进行各种成型操作。
吹制成型有人工和机械吹制成型两种方式。
人工成型时,手持吹管从坩埚内或池窑取料口处挑料,在铁模或木模中吹成器形。
光滑圆形制品用转吹法;表面有凸凹图案花纹或形状不成圆形的制品用静吹法。
先挑无色料吹成小泡,再用小泡挑颜色料或乳浊料吹成器形的称为套料吹制。
用颜色易熔料粒沾在乳浊套料上,各色自然熔流,可吹成自然景器皿;在颜色料上沾带状乳浊料,可吹成拉丝器皿。
机械成型用于吹制大批量制品。
吹制机受料后自动合铁模吹成器形,脱模后去除帽口即成器皿。
还可采用压-吹成型,先将料冲成小泡(雏形),再继续吹制成器形。
它比单纯用吹制机吹制效率高,质量好。
压制成型人工成型时,人工挑料剪入铁模,驱动冲头,压成器形,凝固定型后脱模。
机械成型自动化生产,批量大,效率高。
压制成型适用于能退出冲头的口大底小器形制品,如杯、盘、烟缸等。
离心成型受料在旋转的模子内,由于旋转产生的离心力使玻璃展开并紧贴模子,凝固定型后取出。
适宜于器壁均匀的大型玻璃器皿的成型。
自由成型又称无模成型。
用人工挑料在窑前反复烘烤修饰或热粘结。
由于不与模子接触,玻璃表面光亮,制品形状线条光滑。
玻璃制造工艺

玻璃制造工艺玻璃制造工艺以酸性、碱金属、碱土金属氧化物为主要原料制成玻璃和玻璃制品。
不同玻璃制品的制造方法各有其特点,但主要工艺是相似的(图1)。
简史公元前2600年,巴比伦已有绿色玻璃棒。
公元前2500年,美索不达米亚地区和埃及已能制造玻璃珠。
最早的玻璃器物由玻璃块凿制而成。
以后埃及人用粘土和砂做成一定形状的砂芯,在砂芯上逐层蘸集玻璃液,经过拍打塑形和用颜色玻璃条围绕装饰,固化后再将砂芯除去,制得玻璃器物。
公元前1200年,埃及人采用开口模型将玻璃压成碗、盘、杯等制品。
中国古代玻璃制造技艺萌芽于西周。
战国时期出现含铅和钡硅酸盐玻璃。
汉代已有模压、铸压的玻璃壁、珠等。
公元前200年,巴比伦人首先使用吹玻璃的中空铁管。
用吹管吹制玻璃制品是玻璃制造中的一个突跃性进展。
公元1世纪,罗马人把各种颜色玻璃拉成棒,排列成捆烧熔,再切出具有一定图案截面的玻璃薄片,在模具上将这些薄片加热熔接,制出千花玻璃器。
他们已掌握在玻璃表面刻磨、用颜色釉彩绘和在玻璃中夹金等技艺,并会在暗色玻璃上镶套一层乳白玻璃,再磨去乳白玻璃,制出具有图案的套料刻花、雕花玻璃瓶。
7世纪,叙利亚人把玻璃吹成球,再用铁顶杆蘸少量玻璃液粘住球底部,然后切断吹管处玻璃,用顶杆将开口球在炉中加热软化,借快速旋转的离心力将玻璃球展平成平片玻璃,称冠冕法。
11~16世纪,威尼斯成为玻璃制造中心。
当时用软锰矿使玻璃颜色得到中和脱色制得无色透明的玻璃,并恢复了罗马人的颜色釉彩绘、玻璃夹金、玻璃磨刻等装饰方法。
1615年,英国用煤取代木柴作熔制玻璃的燃料,使熔化温度有所提高。
1635年又用燧石作原料并引入氧化铅,制成折射率高、色散大、易于刻磨的铅晶质玻璃。
1688年,法国用浇注法制出平板玻璃,经研磨抛光后用以制造镜子。
17世纪末,北欧用吹筒法代替吹圆球法,将圆筒沿长度剖开重新加热,以自身重量在铁台上展平成片,其平整度大为改善,产量增大。
1790年,瑞士人P.L.吉南发明用搅拌玻璃液的办法制出高均匀度的光学玻璃。
玻璃制造中的生产设备与工艺流程设计

原料准备:选择合适的原料,如石英砂、纯碱等
成型:将玻璃液倒入模具中,冷却成型
切割:将玻璃制品切割成所需的形状和大小
清洗:将玻璃制品清洗干净,去除表面的杂质和污渍
包装:将玻璃制品进行包装,准备发货或销售
熔化:将原料在高温下熔化成玻璃液
退火:将成型的玻璃制品进行退火处理,消除内应力
磨边:对切割后的玻璃制品进行磨边处理,使其光滑平整
玻璃制造中的生产设备与工艺流程设计
汇报人:
目录
01
添加目录标题
02
玻璃制造概述
03
玻璃制造的生产设备
04
玻璃制造的工艺流程设计
05
生产设备与工艺流程的优化设计
06
生产设备与工艺流程设计的未来发展
添加章节标题
玻璃制造概述
玻璃制造的定义和重要性
玻璃制造的工艺流程简介
原料准备:选择合适的原料,如石英砂、纯碱、石英石等
检测设备
光学检测设备:用于检测玻璃表面的缺陷和杂质
热学检测设备:用于检测玻璃的热学性能,如热膨胀系数、热导率等
力学检测设备:用于检测玻璃的力学性能,如抗拉强度、抗压强度等
电学检测设备:用于检测玻璃的电学性能,如电导率、介电常数等
玻璃制造的工艺流程设计
配料工艺
原料选择:根据玻璃类型选择合适的原料,如石英砂、纯碱、石英粉等
原料混合:将原料按照一定比例混合,保证原料的均匀性
原料研磨:将混合后的原料进行研磨,提高原料的细度
原料干燥:将研磨后的原料进行干燥,去除水分,保证原料的干燥度
熔炼工艺
检验:对玻璃制品进行质量检验,确保其符合标准和要求
退火:将玻璃制品放入退火炉中,缓慢降温,消除玻璃内部的应力和缺陷
微晶玻璃的制备原理及其工艺过程

微晶玻璃的制备原理及其工艺过程微晶玻璃是一种在玻璃基质中添加微小颗粒的专用玻璃产品,它具有独特的光学性能和化学稳定性,广泛应用于光学器件、医疗器械、通信设备、激光器件等领域。
微晶玻璃的制备原理主要包括原料选择、熔融工艺、成型工艺和热处理工艺等几个方面。
下面将详细介绍微晶玻璃的制备原理及其工艺过程。
1.原料选择微晶玻璃的基质是由硅酸盐玻璃组成,一般采用石英砂、石灰石、硼砂等天然矿物作为主要原料。
同时,为了赋予微晶玻璃特定的光学性能,还需要在基质玻璃中添加微小颗粒,比如氧化物、硫化物等。
这些添加剂的选择和比例对微晶玻璃的性能影响非常大,需要根据具体的应用需求进行合理的选择。
2.熔融工艺微晶玻璃的熔融工艺是制备过程中的关键环节。
首先,将原料按照一定的配方比例混合均匀,然后投入玻璃窑中进行高温熔融。
熔融温度通常在1400-1600摄氏度之间,要保证原料充分融化并混合均匀。
熔融的时间也非常重要,一般需要在熔融窑中持续熔融12-24小时以上,以确保各种添加剂与基质玻璃充分融合。
3.成型工艺熔融后的玻璃液体需要通过成型工艺得到具有特定形状和尺寸的微晶玻璃产品。
常见的成型工艺包括浇铸成型、挤压成型和拉拔成型等。
浇铸成型是将熔融玻璃液体倒入模具中,通过冷却凝固成型。
挤压成型是将熔融玻璃液体挤出成型。
拉拔成型是将熔融玻璃液体拉伸成细丝或薄片。
成型工艺的选择取决于产品的具体形状和尺寸要求,同时也要考虑工艺的稳定性和成本效益。
4.热处理工艺在微晶玻璃制备过程中,热处理工艺是必不可少的环节。
热处理可以调控玻璃产品的结构和性能,提高其化学稳定性和光学性能。
一般采用退火工艺和加热处理工艺。
退火是将成型后的微晶玻璃产品在较低温度下加热,使其内部应力得以释放,提高产品的强度和稳定性。
加热处理是将微晶玻璃产品在高温下保持一定时间,使添加剂与基质玻璃发生化学反应,进一步改善产品的性能。
通过上述工艺过程,可以制备出具有优良光学性能和化学稳定性的微晶玻璃产品。
- 1、下载文档前请自行甄别文档内容的完整性,平台不提供额外的编辑、内容补充、找答案等附加服务。
- 2、"仅部分预览"的文档,不可在线预览部分如存在完整性等问题,可反馈申请退款(可完整预览的文档不适用该条件!)。
- 3、如文档侵犯您的权益,请联系客服反馈,我们会尽快为您处理(人工客服工作时间:9:00-18:30)。
玻璃的制备工艺设计
1 原料
(1)原料的选择
(2)工艺流程
合理的选择和确定原料加工处理的工艺流程,是保证生产顺利进行和原料质量的关键之一。
选择和确定工艺流程时应根据原料的性质,加工处理数量来选用恰当的机械设备。
要尽量实现自动化,技术上既要先进可靠,经济上又要节约合理,流程要顺,不应有逆流和交叉现象。
设备布置要紧凑,能充分利用原料本身的重量,进行运输。
原料加工处理的工艺流程可分单系统、多系统与混合系统三种。
单系统流程,是各种矿物原料共同使用一个破碎、粉碎、过筛系统。
它的没备投资少,设备利用率高,但容易发生原料混杂,每种原料加工处理后,整个设备系统都要进行清扫。
这种工艺流程适用于小型玻璃工厂。
多系统流程是每种原料各有一套破碎、粉碎、过筛的系统。
这种流程适用于大、中型玻璃工厂。
混合系统是用量较多的原料单独为一个加工处理系统。
用量小的性质相近的原料,如白云石与石灰石,长石与萤石,共用一个加工处理系统。
多系统原料加工处理工艺流程如下:
——→
——→
——→
——→
——→
——→ ——→ ——→ ——→
3、原料的破碎和粉碎
原料的破碎与粉碎,主要根据料块的大小,原料的硬度和需要粉碎的程度等来选择加工处理方法与相应的机械设备。
砂岩或石英岩是玻璃原料中硬度高、用量大的一种原料,为了减小粗碎时它们对于机械设备的磨损,降低机械铁的引入,有些工厂在砂岩粗碎之前将它预先在1000℃温度以上进行煅烧。
这是由于砂岩或石英岩的主要矿物组成是石英,而石英有多种变体,随着温度的变化会发生晶形转变。
在晶形转变时伴随着体积的突然变化,因此在砂岩或石英岩的内部产生许多裂纹,提高了破碎率,减少了机械磨损。
在煅烧砂岩中主要的晶形转变为(标出了转变温度和体积变化):
β石英 %82.0573±℃
α石英
α石英%
82.014701000±℃~α方石英%8.2270180±℃~β方石英 α方石英℃>1300α鳞石英%2.0163±℃
β鳞石英%2.0117±℃
γ鳞石英
煅烧后的砂岩(或石英岩),用鄂式破碎机与反击式破碎机,或笼形碾进行破碎与粉碎。
煅烧的砂岩(或石英砂)虽然便于粉碎加工,但是要耗用燃料,生产费用增加,工艺流程多,工艺布置不紧凑。
而且小块的砂岩不好锻烧,矿石不能充分利用。
同时砂岩煅烧后质地分散,在运输过程申易于剥落颗粒,硅尘量增加,对工人健康不利。
因此,不少工厂采用鄂式破碎机与对辊破碎机或反击式破碎机,或项式破碎机与湿轮碾配合,直接粉碎砂岩或石英岩。
石灰石、白云石、长石、萤石通常用鄂式破碎机进行破碎,然后用锤式破碎机进行粉碎。
长石和萤石也有来用湿轮碾粉碎的。
萤石因含粘土杂质多,在破碎前,往往先用水冲洗。
纯碱结块时用笼形碾或锤式破碎机粉碎。
芒硝也用笼形碾或锤式破碎机粉碎。
原料的过筛
石英砂和各种原料粉碎后,必须经过过筛,将杂质和大颗粒部分分离,便其具有一定的颗粒组成以保证配合料均匀混合和避免分层。
不同原料要求的颗粒不同,过筛时所采用的筛网也不相同。
过筛只能控制原料粒度的上限,对于小颗粒部分则不能分离出来。
原料的颗粒大小是根据原料的比重,原料在配合料中的数量以及给定的熔化温度等来考虑的。
一般如下,
硅砂,通常只通过36~49孔/㎝2的筛。
因为在选用硅砂时,对其颗粒组成已进行分析,到厂后过筛的目的并不是对其颗粒进行控制,而是为了除去杂草、石块、泥块等外来杂质。
砂岩、石英岩、长石,通过81孔/㎝2筛。
纯碱、芒硝、石灰石、白云石通过64孔/㎝2筛。
玻璃工厂常用的过筛设备,有六角筛(旋转筛),振动筛和摇动筛。
也有使用风力离心器进行颗粒分级的。
4、粉状原料的输送与料仓分层(离析)
通常加工粉碎过筛后的粉状原料,输送入料仓,供制备配合料使用。
布置紧凑的车间,可以尽量利用原料本身的重量由溜管将过筛后的粉料直接送入料仓。
不能利用溜管的,用皮带运输机,斗式提升机等机械运输设备以及气力输送设备进行输送入仓。
料仓用钢板或钢筋混凝土制成。
各种粉状原料多采用圆筒状料仓,亦有采用四角柱状的。
对于原料的水分要特别注意,以防止原料在仓中结块和冬季冻结。
对于纯碱、芒硝等易于吸收大气中水分的原料,也要防止它们吸水。
硼酸在较高温度下会失去结晶水甚至失去B 2O 3。
因之热蒸汽管道,不宜接近硼酸料仓。
中心加料和中心卸料的粉料仓,会发生颗粒分层 (离析)现象,如图11-5所示。
当加料时,
原料在加料口自由下落,细颗粒部分很快地穿过粗颗粒空隙下落,并集中在料堆顶部,形成一个以细颗粒为中心的锥体,而大颗粒部分,由于粒度大,具有较高的能量,将围绕细颗粒位于锥形体外面,靠近仓壁。
当卸料时中心细颗粒部分先行放出。
直至在仓内形成凹形倒锥体时,粗颗粒部分才开始放出。
这样,在料仓放料的前一阶段,放出的料是小于平均粒度的细颗粒部分,而在后一阶段则是大于平均粒度的粗颗粒部分,结果使加入混料机中的各种原料,颗粒不匹配。
在混合后发生分层,从而影响熔炉的操作或玻璃的熔制质量。
图11-5 料仓原料颗粒分层情况
如果原料粗细颗粒间杂质的含量不等,则料仓分层将会影响到玻璃的化学组成,使它发生偏离。
原料的颗粒形状,表面性质,对料仓分层都有一定影响,但最主要的因素是原料的颗粒度差别,其次是原料的比重差别。
由于粉状原料的颗粒度和比重都具有一定的范围,存在着一定的差别,因而料仓分层实际上是不可避免的,只有小心地使它减少。
采用多个加料口和卸料口,可以减少原料细颗粒部分在料仓的中心形成锥体,也就是减少了料仓的分层程度。
此外,采用隔板,或采用便于卸料的其他加料设备(如回转加料器,中央管孔加料器等),也可以减少料仓的分层。
每隔1小时在各种原料的粉料仓下和混合的配合料中取出一定重量(通常为100g)的粉料和配合料,用单一筛号(譬如30孔/㎝2,或40孔/㎝2的筛)进行筛分析(配合料需先用20孔/㎝2的筛筛去碎玻璃)可以求出各个料仓分层和配合料分层的特性曲线,从而考虑它们之间的共同关系,研究减少分层的办法。
5、配合料的粒化
将配合料进行压块和成球,是解决配合料分层和飞料现象的有效办法。
配合料在输送和贮存过程中的分层、飞料,特别是往熔炉中投料时纯碱等的飞料会侵蚀耐火材料和蓄热室的格子砖,影响玻璃成分和熔制质量以及污染大气。
配合料在压块和成球后,可以避免上述现象的产生,而且由于配合料中各原料的颗粒接触紧密,导热性增加,固相反应速度加快,组份氧化物的挥发损失减小,特别是可以采用细粉状原料,能缩短熔化时间,有人试验可缩短熔化时间30%~40%。
同时能够提高玻璃的熔制质量,使玻璃中的结石和气泡减少,增加玻璃产量,提高熔化率30%~40%。
但是也有人持不同的看法,认为不能节省燃料,未经预烧的粒化料也不能降低烟囱的污染。
采用盘式粒化机是比较经济的玻璃成球方法。
其工艺过程是先按一般方法制成均匀的配合料,再将配合料在专门的盘式成球(粒化)盘上,边下料边添加粘结剂,边滚动而制成10~20mm的小球。
然后在干燥设备中烘干使球具有一定的运输及贮存强度,一般要求耐压166.7×104Pa(约17kg/cm2)以上。
其工艺流程大致如下:
——→——→——→
——→——→——→——→
——→——
→——→
——
粘结剂的选择,应使配合料易于成球,使成球后和干燥后的球粒具有一定的强度,对玻璃的熔制和质量不能产生任何不良影响,且价格不能过高。
可采用水玻璃、石灰乳、氢氧化钠液、粘土等。
采用废碱液较有经济价值。
成球盘是一个带边的倾斜圆盘,如图11-8所示。
一般直径为1米以上。
盘的边高H与直径D的平方成正比,盘的倾斜度在30~60°内调节,盘在倾斜面上绕中心轴旋转,转速10~25r/min。
配合料与粘结剂,自盘的上方连续加入,由于粒化料与未粒化料的摩擦系数不同,摩擦系数较小的粒化料逐渐移向上层,最后越过盘边而排出。
由于这样的分级作用,成球盘可以得到较均匀的料粒,盘的倾斜度不能小于湿配合料的休止角,否则配合料将在盘内形“死”垫,破坏粒化,斜度越大,盘的转速也应越大。
图11-8 成球设备
配合料的成球,除与成球子设备有关外,与配合料的组成,颗粒度,粘结剂的种类,用量,粘结剂与配合料的混合均匀性等都有关系。
配合料含硼、碱较多,颗粒细,易于粒化成球,反之则成球率低。
粘结剂的用量与配合料组成有关,用氢氧化钠液作粘结剂时,其用量对瓶罐玻璃来说,以球粒含水量13%左右为宜。
配合料与粘结剂应当均匀混合,混合愈均匀,成球的稳定性愈好。
球粒的干燥,在连续作业的隧道或干燥炉中进行,干燥温度一般为15O℃~2OO℃。
温度过高,会使球发泡,强度降低,温度过低,则干燥时间过长。