(完整word)板式塔设计原理
6.6板式塔

3、浮阀塔
ห้องสมุดไป่ตู้
V- 浮阀塔板 V- 浮阀
4
三种塔板的比较: 1. 生产能力: 筛板 >浮阀 >泡罩 2. 压降: 泡罩 >浮阀 >筛板
3. 操作弹性: 浮阀 >泡罩 >筛板 4. 造价: 5. 板效率: 泡罩 >浮阀 >筛板 浮阀、筛板相当 >泡罩
5
6.9.2 板式塔的流体力学特性
一、气液两相接触状态
一、单板效率(默弗里板效率)
经实际塔板汽或液组成 的变化值 单板效率 经理论塔板汽或液组成 的变化值
(1)汽相
E MV , n y n y n1 y
* n
* yn
yn
y n1
yn1 x n
平均 组成
* yn yn
n
yn1
xn
11
(2)液相
E ML , n x n 1 x n
主要影响因素
气量↑ →夹带量↑
板间距HT↓ →夹带量↑
要求液沫夹带量 eG≯0.1kg液沫/kg干气
8
2. 气泡夹带 原因:液体在降液管中停留时间过短,气泡来 不及解脱,而被液体卷入下层塔板。 3. 气体沿塔板的不均匀流动 原因:液面有落差和液层波动,引起气体分布不均匀 4. 液体沿塔板的不均匀流动
9
四、不正常操作现象
1. 液泛 定义:液体进塔量大于出塔量,结果使塔内不
断积液,直至塔内充满液体,破坏塔内
正常操作,称为液泛。 液泛包括:夹带液泛、溢流液泛 2. 严重漏液 当气体孔速过小或气体分布不均匀时,使 有的筛孔无气体通过,从而造成液体短路,大 量液体由筛孔漏下。
10
6.6.3 塔板效率
板式塔的工作原理
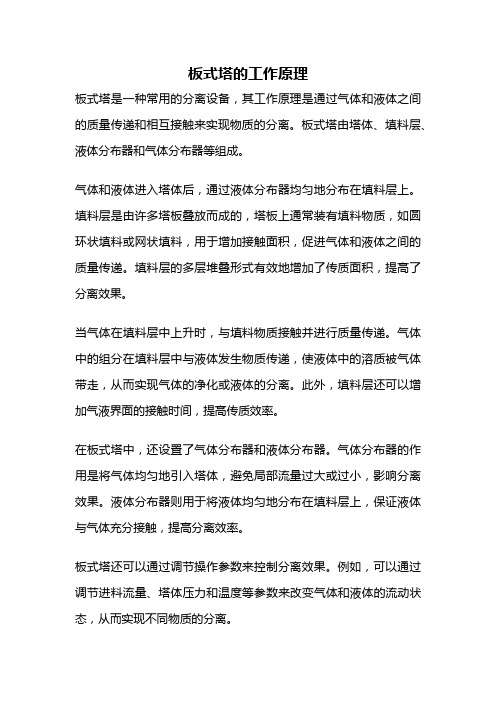
板式塔的工作原理
板式塔是一种常用的分离设备,其工作原理是通过气体和液体之间的质量传递和相互接触来实现物质的分离。
板式塔由塔体、填料层、液体分布器和气体分布器等组成。
气体和液体进入塔体后,通过液体分布器均匀地分布在填料层上。
填料层是由许多塔板叠放而成的,塔板上通常装有填料物质,如圆环状填料或网状填料,用于增加接触面积,促进气体和液体之间的质量传递。
填料层的多层堆叠形式有效地增加了传质面积,提高了分离效果。
当气体在填料层中上升时,与填料物质接触并进行质量传递。
气体中的组分在填料层中与液体发生物质传递,使液体中的溶质被气体带走,从而实现气体的净化或液体的分离。
此外,填料层还可以增加气液界面的接触时间,提高传质效率。
在板式塔中,还设置了气体分布器和液体分布器。
气体分布器的作用是将气体均匀地引入塔体,避免局部流量过大或过小,影响分离效果。
液体分布器则用于将液体均匀地分布在填料层上,保证液体与气体充分接触,提高分离效率。
板式塔还可以通过调节操作参数来控制分离效果。
例如,可以通过调节进料流量、塔体压力和温度等参数来改变气体和液体的流动状态,从而实现不同物质的分离。
板式塔利用填料层增加气液接触面积和接触时间,通过质量传递实现气体和液体的分离。
其工作原理简单明了,可以根据不同的需求进行调节和优化,广泛应用于化工、石油、环保等领域中的气体净化和液体分离过程中。
对于工业生产过程中的分离和净化操作,板式塔是一种高效可靠的设备。
精馏装置-板式塔的结构和原理
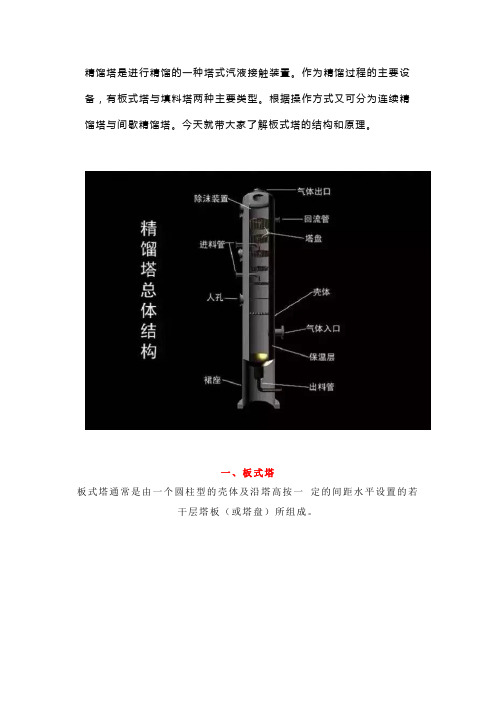
精馏塔是进行精馏的一种塔式汽液接触装置。
作为精馏过程的主要设备,有板式塔与填料塔两种主要类型。
根据操作方式又可分为连续精馏塔与间歇精馏塔。
今天就带大家了解板式塔的结构和原理。
一、板式塔板式塔通常是由一个圆柱型的壳体及沿塔高按一定的间距水平设置的若干层塔板(或塔盘)所组成。
板式塔实物图板式塔结构图二、板式塔塔板板式塔的塔板可分为有降液管及无降液管两大类。
有降液管的一般液体呈错流式,无降液管的液体呈逆流式。
板式塔由塔板不同可以分为泡罩塔、浮阀塔、筛板塔、舌型板和斜孔板等等。
其中以泡罩塔,浮阀塔和筛板塔在工业生产中使用最为广泛。
三、泡罩塔泡罩塔板是工业上应用最早的塔板,它由升气管及泡罩构成。
泡罩安装在升气管的顶部,分圆形和条形两种,以前者使用较广。
泡罩有f80、f100和f150mm三种尺寸,可根据塔径大小选择。
泡罩下部周边开有很多齿缝,齿缝一般为三角形、矩形或梯形。
泡罩在塔板上为正三角形排列。
泡罩边缘开有纵向齿缝,中心装升气管。
升气管直接与塔板连接固定。
塔板下方的气相进入升管,然后从齿缝吹出与塔板上液相接触进行传质。
由于升气管作用,避免了低气速下的漏液现象。
优点:该塔板操作弹性,塔效率也比较高,运用较为广泛。
缺点:是结构复杂,塔压降低,生产强度低,造价高。
四、筛板塔筛孔塔板简称筛板,其结构特点是在塔板上开有许多均匀小孔,孔径一般为3~8mm。
筛孔在塔板上为正三角形排列。
塔板上设置溢流堰,使板上能保持一定厚度的液层。
筛板塔的优点是结构简单、造价低,生产能力大,板上液面落差小,气体压降低,同时塔板效率较高。
缺点是操作弹性小,筛孔易堵塞,不宜处理易结焦、黏度大的物料。
五、浮阀塔浮阀是20世纪二战后开始研究,50年代开始启用的一种新型塔板,后来又逐渐出现各种型式的浮阀。
其型式有圆形、方形、条形及伞形等。
较多使用圆形浮阀,而圆形浮阀又分为多种型式。
其特点是浮阀取消了泡罩塔的泡罩与升气管,改在塔上开孔,阀片上装有限位的三条腿。
化工原理第六章第六节 板式塔
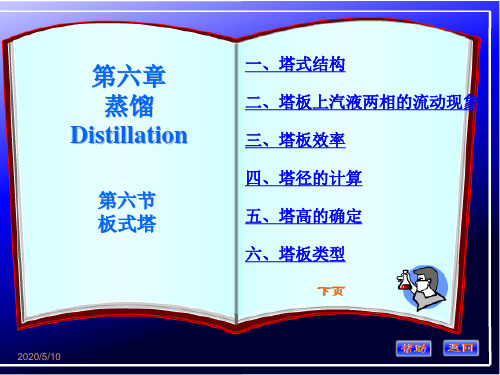
2013-1-7
三、塔板效率
在实际塔板上,汽液相接触的面积和时间均有限,分离也可能 不完全,故离开同一塔板的汽液相,一般都未达到平衡,因此实际 塔板数总应多于理论塔板数。 实际塔板偏离理论板的程度用塔板效率表示。塔板效率有多种表示 方法,这里介绍常用的单板效率和全塔效率。 (1)全塔效率:理论板数与实际板数之比称为全塔效率又称为总板
2013-1-7
2.塔板上的液面落差
液面落差:塔板进出口清液层高度差 减少液面落差的措施: 多溢流。
2013-1-7
当液体横向流过塔板时,为克服板上的摩擦阻力和板
上部件(如泡罩、浮阀等)的局部阻力,需要一定的液位
差,则在板上形成由液体进入板面到离开板面的液面落差。 液面落差也是影响板式塔操作特性的重要因素,液面落差 将导致气流分布不均,从而造成漏液现象,使塔板的效率 下降。因此,在塔板设计中应尽量减小液面落差。
2013-1-7
4.喷射型塔板 上述几种塔板,气体是以鼓泡或泡沫状态和液体接触, 当气体垂直向上穿过液层时,使分散形成的液滴或泡沫具 有一定向上的初速度。若气速过高,会造成较为严重的液 沫夹带,使塔板效率下降,因而生产能力受到一定的限制。 为克服这一缺点,近年来开发出喷射型塔板,大致有以下 几种类型。 舌形塔板 浮舌塔板
xn,xn-1——进入和离开n板、n+1板的液相组成; xn* ——与板上液体组成成平衡的液相组成;
2013-1-7
四、塔高的确定
板式塔的有效高度,由实际板数和板间距决定
Z N实 H T
全塔的高度应为有效段、塔顶及塔釜三部分之和 填料式精馏塔等板高度:是与一层理论板的传质作用相当 的填料层高度 填料式精馏塔的填料层高度
V
0.2
简述板式塔的工作原理及应用方法

简述板式塔的工作原理及应用方法1. 什么是板式塔板式塔是一种常见的化工设备,用于气体或液体的吸收、吸附、萃取和分离等操作。
它由大量平行排列的薄壁塔板组成,通过塔体内的气液反应、质量传递和热量传递等过程,实现物质的分离、纯化和反应转化。
2. 板式塔的工作原理板式塔的工作原理基于物质之间的质量和热量传递。
其核心机理是气体与液体之间的接触,以及气体和液体在塔板上的传递过程。
2.1 气液接触板式塔通过塔内的填料或特殊构造的塔板使气体和液体接触,以便进行质量传递。
填料通常具有高表面积和良好的润湿性,可以增加气液接触的面积和时间。
2.2 质量传递在接触过程中,气体和液体之间会发生物质的传递,例如物质的吸收、吸附、萃取等。
这种传递是由气体和液体之间的浓度差、温度差和压力差等驱动的,通常以物质的扩散为主要方式。
2.3 热量传递除了质量传递外,板式塔还能通过塔板上的传热介质(如冷凝液或加热介质)实现热量的传递。
这对于一些需要温度控制或热敏性反应的过程非常重要。
3. 板式塔的应用方法板式塔广泛应用于化工、石油、石油化工等领域,常见的应用包括气体吸收、吸附分离、萃取分离和气液反应等。
3.1 气体吸收板式塔可用于从气体中吸收特定成分。
例如,用于去除废气中的有害物质,净化空气中的污染物等。
3.2 吸附分离板式塔常用于吸附剂对气体或液体中的特定组分进行吸附,实现物质的分离。
这在石油化工和环保领域中非常常见,例如油品脱蜡、气体分离、有机溶剂回收等。
3.3 萃取分离板式塔可用于液液或液气物质之间的萃取分离。
例如,用于提取天然产物中的有效成分、分离石油中的油品等。
3.4 气液反应板式塔还可用于气液反应,例如气体与液体中的化学反应。
通过合理的塔板设计和操作条件控制,实现气体与液体之间的反应转化,常用于合成化学和燃料化工等领域。
4. 总结板式塔是一种重要的化工设备,它通过气液接触、质量传递和热量传递等过程实现物质的分离和反应转化。
在气体吸收、吸附分离、萃取分离和气液反应等方面都有广泛的应用。
第六节 板式塔

第六节 板式塔一、塔板的结构型式板式塔的壳体通常为圆筒形,里面沿塔高装有若干块水平的塔板。
传质机理:塔内液体依靠重力作用,由上层塔板的降液管流到下层塔板的受液盘,然后横向流过塔板,从另一侧的降液管流至下一层塔板。
溢流堰的作用是使塔板上保持一定厚度的液层。
气体则在压力差的推动下,自下而上穿过各层塔板的气体通道(泡罩、筛孔或浮阀等),分散成小股气流,鼓泡通过各层塔板的液层。
在塔板上,气液两相密切接触,进行热量和质量的交换。
在板式塔中,气液两相逐级接触,两相的组成沿塔高呈阶梯式变化,在正常操作下,液相为连续相,气相为分散相。
为有效地实现气液两相之间的传质,板式塔应具有以下两方面的功能: ①在每块塔板上气液两相必须保持密切而充分的接触,为传质过程提供足够大而且不断更新的相际接触表面,减小传质阻力;②在塔内应尽量使气液两相呈逆流流动,以提供最大的传质推动力。
由吸收章可知,当气液两相进、出塔设备的浓度一定时,两相逆流接触时的平均传质推动力最大。
在板式塔内,各块塔板正是按两相逆流的原则组合起来的。
但是,在每块塔板上,由于气液两相的剧烈搅动,是不可能达到充分的逆流流动的。
为获得尽可能大的传质推动力,目前在塔板设计中只能采用错流流动的方式,即液体横向流过塔板,而气体垂直穿过液层。
由此可见,除保证气液两相在塔板上有充分的接触之外,板式塔的设计意图是,在塔内造成一个对传质过程最有利的理想流动条件,即在总体上使两相呈逆流流动,而在每一块塔板上两相呈均匀的错流接触。
板式塔的结构1-塔壳体;2-塔板;3-溢流堰;4-受液盘;5-降液管 1 2 3 5 4塔板是板式塔的核心构件,其功能是使气、液两相保持充分的接触,使之能在良好的条件下进行传质和传热传递过程。
塔板上的气液两相流动方式有错、逆流两种,如图5—4所示。
错流塔板在板间设有专供液体流通的降液管(又称溢流管)。
从降液管出来的液体横过塔板,然后再溢流进入另一降液管而到达下一层塔板;气体则经过板上的孔道上升,在每一层塔板上气、液两相呈错流方式接触。
化工原理-板式塔设计-2016

目 录第一章 板式精馏塔的设计1.1概述 (1)1.2板式精馏塔的设计原则与步骤 (1)1.3理论塔板数的确定 (3)1.4塔板效率和实际塔板数 (7)1.5 板式精馏塔的结构设计 (8)1.6 板式精馏塔高度及其辅助设备 (27)1.7 板式精馏塔的计算机设计 (31)第二章 板式精馏塔设计举例2.1 苯-甲苯板式精馏塔设计 (33)2.2 乙醇—水板式精馏塔设计 (47)2.3 甲醇—水板式精馏塔设计 (66)第三章 塔设备的机械计算3.1 塔体及裙座的强度计算 (86)3.2 塔盘板及其支撑梁的强度、挠度计算 (104)3.3 塔盘技术条件 (105)3.4 塔盘支撑件的尺寸公差 (109)附 录 (111)第一章 板式精馏塔的设计1.1概述蒸馏是利用液体混合物中各组分挥发度的不同并借助于多次部分汽化和部分冷凝达到轻重组分分离的方法。
蒸馏操作在化工、石油化工、轻工等工业生产中中占有重要的地位。
为此,掌握气液相平衡关系,熟悉各种塔型的操作特性,对选择、设计和分析分离过程中的各种参数是非常重要的。
蒸馏过程按操作方式可分为间歇蒸馏和连续蒸馏。
间歇蒸馏是一种不稳态操作,主要应用于批量生产或某些有特殊要求的场合;连续蒸馏为稳态的连续过程,是化工生产常用的方法。
蒸馏过程按蒸馏方式可分为简单蒸馏、平衡蒸馏、精馏和特殊精馏等。
简单蒸馏是一种单级蒸馏操作,常以间歇方式进行。
平衡蒸馏又称闪蒸,也是一种单级蒸馏操作,常以连续方式进行。
简单蒸馏和平衡蒸馏一般用于较易分离的体系或分离要求不高的体系。
对于较难分离的体系可采用精馏,用普通精馏不能分离体系则可采用特殊精馏。
特殊精馏是在物系中加入第三组分,改变被分离组分的活度系数,增大组分间的相对挥发度,达到有效分离的目的。
特殊精馏有萃取精馏、恒沸精馏和盐溶精馏等。
精馏过程按操作压强可分为常压精馏、加压精馏和减压精馏。
一般说来,当总压强增大时,平衡时气相浓度与液相浓度接近,对分离不利,但对在常压下为气态的混合物,可采用加压精馏;沸点高又是热敏性的混合液,可采用减压精馏。
(完整)板式塔
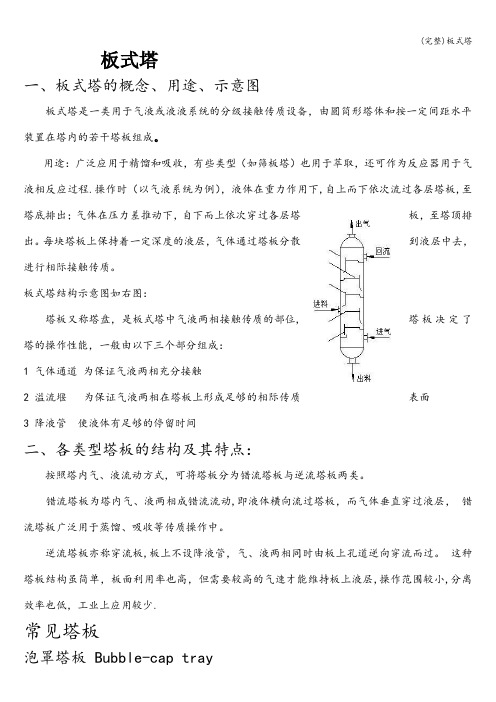
板式塔一、板式塔的概念、用途、示意图板式塔是一类用于气液或液液系统的分级接触传质设备,由圆筒形塔体和按一定间距水平装置在塔内的若干塔板组成。
用途:广泛应用于精馏和吸收,有些类型(如筛板塔)也用于萃取,还可作为反应器用于气液相反应过程.操作时(以气液系统为例),液体在重力作用下,自上而下依次流过各层塔板,至塔底排出;气体在压力差推动下,自下而上依次穿过各层塔板,至塔顶排出。
每块塔板上保持着一定深度的液层,气体通过塔板分散到液层中去,进行相际接触传质。
板式塔结构示意图如右图:塔板又称塔盘,是板式塔中气液两相接触传质的部位,塔板决定了塔的操作性能,一般由以下三个部分组成:1 气体通道为保证气液两相充分接触2 溢流堰为保证气液两相在塔板上形成足够的相际传质表面3 降液管使液体有足够的停留时间二、各类型塔板的结构及其特点:按照塔内气、液流动方式,可将塔板分为错流塔板与逆流塔板两类。
错流塔板为塔内气、液两相成错流流动,即液体横向流过塔板,而气体垂直穿过液层,错流塔板广泛用于蒸馏、吸收等传质操作中。
逆流塔板亦称穿流板,板上不设降液管,气、液两相同时由板上孔道逆向穿流而过。
这种塔板结构虽简单,板面利用率也高,但需要较高的气速才能维持板上液层,操作范围较小,分离效率也低,工业上应用较少.常见塔板泡罩塔板 Bubble-cap tray泡罩塔塔板上的主要部件是泡罩。
罩内覆盖着一段很短的升气管,升气管的上口高于罩下沿的小孔或齿缝。
塔下方的气体经升气管进入罩内之后,折向下到达罩与管之间的环形空隙,然后从罩下沿的小孔或齿 缝分散气泡而进入板上的液层。
优点:弹性大、操作稳定可靠。
缺点:结构复杂,成本高,压降大.对于大直径塔,塔板液面落差大,导致塔板操作不均匀。
现状:近二、三十年来已趋于淘汰三、板式塔的工艺设计筛板塔化工设计计算 (1)塔的有效高度 Z已知:实际塔板数 N P ; 塔板间距 H T ;有效塔高:塔体高度=有效高+顶部+底部+其他塔板间距和塔径的经验关系:(2)塔径确定原则: 防止过量液沫夹带液泛 步骤: 先确定液泛气速 uf (m/s ); 然后选设计气速 u ; 最后计算塔径 D.① 液泛气速pT N H Z ⋅=VVLf C u ρρρ-=2.02020⎪⎭⎫⎝⎛=σC CC :气体负荷因子,与 HT 、 液体表面张力和两相接触状况有关. 两相流动参数 FLV :② 选取设计气速 u 选取泛点率: u / u f一般液体, 0.6 ~0。
9-1板式塔

西北大学化工原理课件
八、塔板类型
评价塔设备性能的指标
① 生产能力大 即:单位塔截面能处理的气液负荷高; ② 塔板效率高 ③ 板压降低,两相流动阻力小 ④ 操作弹性大 即:上、下操作极限通过的气量之比大; ⑤ 满足工业对生产设备的一般要求 结构简单、造价低、安装维修方便等。
15
西北大学化工原理课件
2
hl = β ( h w + how )
由表面张力引起的压降值一般可忽略,故主要由前两项 组成,即:
h f = hd + hl
25
西北大学化工原理课件
5. 筛板的几个操作极限
① 漏液点:漏液点气速 u0´:发生严重漏液时筛孔气速。
u0 稳定系数: k = u ′ 0
⎞ 5.7 × 10 ⎛ u ev = ⎜ ⎟ ⎜ ⎟ σ ⎝ HT − H f ⎠
xn* xn xn-1
指气相或液相经过某板前后的实际组成 变化与经该板的理论组成变化之间的比值, 包括气、液相的莫弗里板效率Emv与EmL。
10
西北大学化工原理课件
例9-1 用一个蒸馏釜和一层实际板组成的精馏塔分离二元理想溶液。组成为0.2的 料液在泡点温度下由塔顶连续加入,系统的相对挥发度α= 2.5。若使塔顶轻组分 的回收率为80%,并要求塔顶产品组成为0.28,试求: ① 塔釜残液组成xW; F xF D xD ② 该层塔板的液相默弗里板效率EmL。 x0 y1 解: ① 由题意,塔顶易挥发组分回收率为:
3. 漏液
当气体孔速u0过小或气体分布不均匀时,使一些筛孔无气体 通过,从而造成液体短路,大量液体由筛孔漏下的操作现象。
工作录像
9
西北大学化工原理课件
六、板效率的表示与应用
板式塔
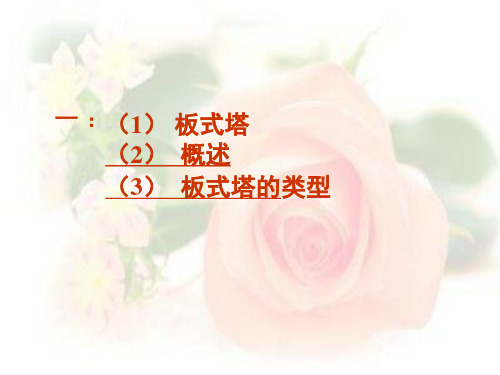
三、浮阀塔:浮阀塔是廿世纪五十年代初开发的一 浮阀塔: 种新塔型。 种新塔型。
阀片上各部件的作用:
• 阀脚:浮阀有三条带钩的腿。将浮阀放进筛孔后,将其腿 阀脚:浮阀有三条带钩的腿。将浮阀放进筛孔后, 上的钩扳转,可防止操作时气速过大将浮阀吹脱。 上的钩扳转,可防止操作时气速过大将浮阀吹脱。 • 定距片:浮阀边沿冲压出三块向下微弯的“脚”。当筛孔 定距片:浮阀边沿冲压出三块向下微弯的“ 气速降低浮阀降至塔板时,靠这三只“ 气速降低浮阀降至塔板时,靠这三只“脚”使阀片与塔板 间保持2.5mm左右的间隙 在浮阀再次升起时, 2.5mm左右的间隙; 间保持2.5mm左右的间隙;在浮阀再次升起时,浮阀不会 被粘住,可平稳上升。 被粘住,可平稳上升。 • 能力比较:浮阀塔的生产能力比泡罩塔约大20%~40%, 能力比较:浮阀塔的生产能力比泡罩塔约大20%~40%, 操作弹性可达7 板效率比泡罩塔约高15%, 操作弹性可达7~9,板效率比泡罩塔约高15%,制造费用 为泡罩塔的60%~80%,为筛板塔的120%~130%。 为泡罩塔的60%~80%,为筛板塔的120%~130%。
泡沫接触状态 更新的液膜表面
喷射接触状态 更新的液滴表面
1. 鼓泡接触状态 液体——连续相 气体 液体 连续相 气体——分散相 分散相 两相接触面积:气泡表面 两相接触面积:
2. 泡沫接触状态 液体 —— 连续相 气体 —— 分散相 两相接触面积:不断更新的液膜表面 两相接触面积:
3. 喷射接触状态 气体 —— 连续相 液体 —— 分散相 两相接触面积: 两相接触面积:不断更新的液滴表面
乱堆填料: 乱堆填料: 阶 梯 环
鲍 尔 环
填料
填料类型
乱堆填料
根据堆方的方式不同可分为两类: 根据堆方的方式不同可分为两类:
板式塔(筛板塔)设计

4.3 筛孔塔板的设计程序
塔板设计的基本程序是:
(1)选择板间距和初步确定塔径;
(2)根据初选塔径,对筛板进行具体结构的设计;
(3)对所设计的塔板进行流体力学校核,如有必 要,需对某些结构参数加以调整。
4.3.1板间距的选择和塔径的初步确定
一、板间距的选择 HT的大小与液泛和雾沫夹带有密切关系 理论上,存在一个经济上最佳的HT; 实际上, HT 的选择常取决于制造和维修的方便,可 参考下表选择。
Ls L eV 1 Vs V
若算出的ev > 0.1kg液体/kg干气,可增大塔径或 板间距使ev下降。
三、溢流液泛条件的校核 为避免发生溢流液泛,必须满足
H fdห้องสมุดไป่ตู้
Hd
H T hw
式中相对泡沫密度 与物系的发泡性有关: 对一般物系, 可取为0.5;对不易发泡物 系 可取为0.6~0.7; 对于容易发泡物系, 可取为0.3~0.4。
精馏可在常压、加压或减压下进 行。 沸点低、常压下为气态的物料必 须选用加压精馏;热敏性、高沸点 物料常用减压精馏。
1.2 进料状态
一般将料液预热到泡点或接近泡点后 送入塔内。这样可使: (1)塔的操作比较容易控制; (2)精馏段和提馏段的上升蒸汽量相近, 塔径相似,设计制造比较方便。
1.3 加热方式
1、 2、 3
—— 分别为塔顶、加料、塔底组成的相 对挥发度。
汽液相平衡关系:
pA pB
2.2 相对挥发度 对于理想物系
1 2 3 3
x y 1 1x
3. 工艺计算
3.1 物料衡算
物料衡算的任务 (1)由设计任务所给定的F、 x
板式塔
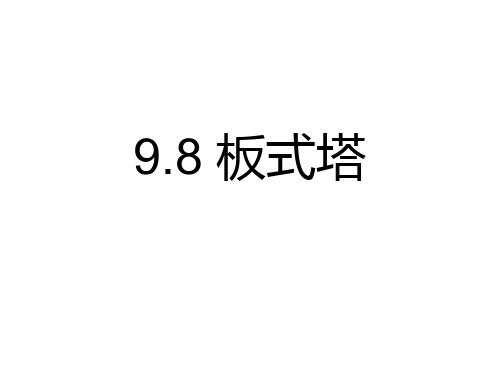
• 3. 浮阀塔板 • 浮阀塔板具有泡罩塔板和筛孔塔板的优点,应 用广泛。浮阀的类型很多,国内常用的有如图 示的F1型、V-4型及T型等。 • 浮阀塔板的结构特点是在塔板上开有若干个阀 孔,每个阀孔装有一个可上下浮动的阀片,阀 片本身连有几个阀腿,插入阀孔后将阀腿底脚 拨转90°,以限制阀片升起的最大高度,并防 止阀片被气体吹走。阀片周边冲出几个略向下 弯的定距片,当气速很低时,由于定距片的作 用,阀片与塔板呈点接触而坐落在阀孔上,在 一定程度上可防止阀片与板面的粘结。
• 如上所述,泡沫接触状态和喷射状态均是优良的塔板接触状 态。因喷射接触状态的气速高于泡沫接触状态,故喷射接触状 态有较大的生产能力,但喷射状态液沫夹带较多,若控制不好, 会破坏传质过程,所以多数塔均控制在泡沫接触状态下工作。
2、气体通过塔板的压降
干板压降
塔板压降 液层阻力 液体的表面张力 板上充气液层的静压力
舌型塔板的优点是:生产能力大,塔板压降低,传质效率较高;缺 点是:操作弹性较小,气体喷射作用易使降液管中的液体夹带气泡 流到下层塔板,从而降低塔板效率。
• (2)浮舌塔板 • 如图所示,与舌型塔 板相比,浮舌塔板的 结构特点是其舌片可 上下浮动。因此,浮 舌塔板兼有浮阀塔板 和固定舌型塔板的特 点,具有处理能力大、 压降低、操作弹性大 等优点,特别适宜于 热敏性物系的减压分 离过程。
9.8.3塔板的结构
• 9.8.3.1塔板结构参数 一、鼓泡区 二、溢流区 三、安定区 四、无效区
俯视图 安定区
开孔区
受 液 区
降 液 管
溢流堰
• 9.8.3.2塔板的溢流装置 一、降液管的类型及溢流方式 (一)降液管的类型 (二)降液管溢流方式 (a)U形流 (b)单溢流 (c)双溢流 (d)阶梯式双溢流 二、溢流装置的结构参数
板式塔原理

板式塔原理板式塔是一种常见的化工设备,其原理是利用气体和液体之间的传质和传热作用,实现气体和液体的分离和净化。
板式塔通常由塔体、填料、分布器、进料口、出料口等部分组成,其工作原理复杂而精密,下面将对其原理进行详细介绍。
首先,板式塔的工作原理基于气液两相之间的接触和传质。
在板式塔内,气体从底部进入,经过填料层,与从顶部流下来的液体接触。
在接触的过程中,气体中的有害物质会被液体吸收,从而达到净化的目的。
而填料的作用是增加气液接触的表面积,加快传质速度,提高净化效率。
其次,板式塔利用了气体和液体的重力作用。
在板式塔内,气体由下往上流动,液体由上往下流动,这种逆流运动有利于气液之间的接触和传质。
此外,板式塔中通常会设置分布器,用于均匀分布液体,保证填料层的充分润湿,进一步提高传质效率。
另外,板式塔还利用了气液两相的密度差异。
在板式塔内,气体的密度通常比液体小,因此气体会向上升腾,而液体则向下流动。
这种差异的运动方式有利于气液之间的接触和传质,使得板式塔能够有效地实现气液分离和净化的功能。
此外,板式塔还可以根据需要进行改良和优化。
例如,可以通过改变填料的形状和材质,调整分布器的结构,优化进料口和出料口的设计等方式,提高板式塔的传质效率和净化效果,使其更加适应不同的工艺要求。
总的来说,板式塔是一种利用气液接触和传质作用实现气液分离和净化的化工设备,其工作原理复杂而精密。
通过气液接触、重力作用和密度差异等原理的综合作用,板式塔能够高效地实现气液分离和净化的功能。
同时,板式塔还具有改良和优化的潜力,可以根据需要进行调整和改进,以满足不同工艺的要求。
通过对板式塔原理的深入理解,可以更好地应用和优化板式塔,提高工艺的效率和产品的质量。
板式塔设计06
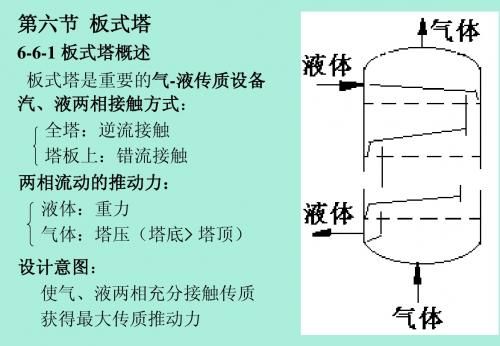
阀未全开时:
h 0 19.9u
0.175 0
/ρ L
使用方法:联立以下二式求临界阀孔气速u0,K 比较:若u0 ≥ u0,K,用上式(全开)计算h0 若u0≤u0,K,用下式(未全开)计算h0
七、塔板的校核 (2)液层阻力 ,
2、塔板阻力的计算和校核 m(液柱)
hl hW hOW
VS
2 d 0 u0
2 d0 n 2 D
2、在有效传质区均匀排列浮阀(数目≈n) •注意:分块式塔板(0.8---0.9m整)
400mm 450mm
25
列间距:75、100、125mm;排间距:自定 原则:与液流垂直方向上,各孔距离尽量基本相等
所排孔数≈n 要求:附浮阀排列图
3、按实际孔数n计算: u0,F0,υ
= 泛点率 ×uf
Vs A截面积 AT = 气体流通截面积 A +降液管面积 Ad 即: A = AT - Ad
塔截面积
A 2 AT D Ad 4 1 AT
故塔径
D
4 AT
其中: Ad / AT 根据经验选取
单流型弓形降液管: 0.06 -- 0.12 多流型:可适当增大;U 形流型:可适当减小
ev
5.7 10
3
u H H f T
3.2
式中Hf 为板上泡沫层高度:Hf = 2.5 (hW+hoW) 当ev≥或接近于0.1时,需要调整塔板结构尺寸,方法: 增大D,或减小Ad/AT(有限)→u↓→ev↓; 增大HT。
七、塔板的校核
1、液沫夹带量校核— 浮阀塔:
依据:塔径
流量
三、溢流装置设计
2. 降液管:液体通道 —弓形、圆形; 弓形降液管尺寸:面积Ad,宽bd,弦lw;由Ad/AT=0.06~0.12确定
- 1、下载文档前请自行甄别文档内容的完整性,平台不提供额外的编辑、内容补充、找答案等附加服务。
- 2、"仅部分预览"的文档,不可在线预览部分如存在完整性等问题,可反馈申请退款(可完整预览的文档不适用该条件!)。
- 3、如文档侵犯您的权益,请联系客服反馈,我们会尽快为您处理(人工客服工作时间:9:00-18:30)。
对于每个塔板结构参数已设计好的塔,处理固定的物系时,要维持其正常操作,必须把气、液负荷限制在一定范围内。
通常在直角坐标系中,标绘各种极限条件下的V-L关系曲线,从而得到塔板适宜的气、液流量范围图形,该图形称为塔板的负荷性能图,如图1—23所示,一般由下列五条曲线组成。
⑴ 漏液线线1为漏液线,又称为气相负荷下限线。
气相负荷低于此线将发生严重的漏液现象,气、液不能充分接触,使塔板效率下降。
筛板塔的漏液线由式(1—47)或式(1-48)作出,浮阀塔的漏液线由式(1-49)作出.⑵ 雾沫夹带线线2为雾沫夹带线。
当气相负荷超过此线时,雾沫夹带量过大,使塔板效率大为降低。
对于精馏,一般控制eV≤0.1kg液/kg气。
筛板的雾沫夹带线按式(1—50)作出。
浮阀塔的雾沫夹带线按式(1—51)或式(1-52)作出。
⑶ 液相负荷下限线线3为液相负荷下限线.液相负荷低于此线,就不能保证塔板上液流的均匀分布,将导致塔板效率下降.一般取how=6mm作为下限,按式(1—33)~式(1—37)中一式作出液相负荷下限线。
⑷ 液相负荷上限线线4为液相负荷上限线,该线又称降液管超负荷线。
液体流量超过此线,表明液体流量过大,液体在降液管内停留时间过短,进入降液管的气泡来不及与液相分离而被带入下层塔板,造成气相返混,降低塔板效率。
通常根据液相在降液管内的停留时间应大于3s,按式(1-24)作出此线。
⑸ 液泛线线5为液泛线。
操作线若在此线上方,将会引起液泛。
根据降液管内的液层高度,按式(1-46)作出此线.由上述各条曲线所包围的区域,就是塔的稳定操作区。
操作点必须落在稳定操作区内,否则塔就无法正常操作。
必须指出,物系一定,塔板负荷性能图的形状因塔板结构尺寸的不同而异.在设计塔板时,可根据操作点在负荷性能图中的位置,适当调整塔板结构参数来满足所需的弹性范围.操作时的气相流量与液相流量在负荷性能图上的坐标点称为操作点。
在连续精馏塔中,回流比一定,板上的气液比V/L也为定值。
在负荷性能图上,操作线可用通过坐标原点斜率为V/L的直线表示。
通常把气相负荷上、下限之比值称为塔板的操作弹性系数,简称操作弹性。
如图1-23所示,不同气液比的操作情况以OAB、OCD、OEF三条操作线表示,其控制上限的条件不一定相同,而且操作弹性也不相同.因此,在设计和生产操作时,要作出具体分析,抓住真正的影响因素,以利于优化设计和操作。
1.6 板式精馏塔高度及其辅助设备塔设备的总体结构如图1—24所示,包括塔体、塔体支座、除沫器、接管、手孔、人孔、塔内件等。
塔体是塔设备的外壳。
常见塔体由等直径,等壁厚的圆筒及椭圆形封头的顶盖和底盖构成。
随着化工装置的大型化,为了节约原材料,有用不同直径、不同壁厚的塔体。
塔体的厚度除应满足工艺条件下的强度外,还应校核风力、地震、偏心载荷所引起的强度和刚度,同时要考虑水压实验、吊装、运输、开停工的情况.塔体支座是塔体安放到基础上的连接部分,一般采用裙座,其高度由工艺条件的附属设备(如再沸器、泵)及管道布置决定。
它承受各种情况下的全塔重量,以及风力、地震等载荷,为此,它应具有足够的强度和刚度。
除沫器用于捕集在气流中的液滴。
使用高效的除沫器,对于提高分离效率,改善塔后设备的操作状况,回收昂贵的物料以及减少对环境的污染都是非常重要的。
常用的有丝网除沫器和折板除沫器.接管是用以连接工艺管路,使之与相关设备连成系统.有进液管、出液管、回流管、进气管、出气管、侧线抽出管、取样管、液面计接管及仪表接管等。
手孔、人孔和视孔是为了安装、检查的需要而设置的。
吊柱设置在塔顶,用于安装和检修时运送塔内件。
1.6.1 塔高塔高由下式计算(1—53)图1-24 板式塔总体结构1-裙座;2-裙座人孔;3-塔底液体出口;4-裙座排气口;5-塔体;6-人孔;7-蒸汽入口;8-塔盘;9-回流入口;10-吊柱;11-塔顶蒸汽出口;12-进料口式中H-—塔高(不包括封头、裙座)m;N—-实际塔板数;N F——进料板数;N P—-人孔数;H T——塔板间距,m;H F-—进料板处板间距,m;H P——设人孔处板间距,m;H D--塔顶空间(不包括头盖部分),m;H B——塔底空间(不包括底盖部分),m.塔顶空间H D的作用是安装塔板和除沫装置的需要,起减少雾沫夹带量的作用,一般H D=1。
0~2。
0m,塔径大时可适当增大。
人孔数N P是根据物料的清洁程度塔板安装的方便而定;对于易结焦、结垢的物料,每隔4—6块板开一人孔;对于清洁物料,每隔8—10块板开一人孔;若塔板上下都可拆,可隔15块板开一人孔。
常在进料口设置防冲设施,进料段高度H F应保证这些设施的方便安装。
塔底空间具有中间贮槽的作用,塔釜料液最好能在塔底有l0—15min的储量,以保证塔底料液不致排完,对于塔底产量大的塔,有时仅取3-5min的储量。
1。
6。
2 接管尺寸与结构接管的合适尺寸与在操作条件下管内的适宜流速的选择密切相关。
塔顶蒸气的适宜流速为:常压操作时取12—20m/s,绝对压力为6000-14000Pa时取30—50m/s,绝对压力小于6000Pa时取50-70m/s。
回流管内的适宜流速为:重力回流取0.2一0.5m/s,强制回流取1.5—2。
5m/s。
进料管内适宜流速为:由高位槽入塔时取0.4一0。
8m/s,由泵输送时取1.5一2.5m/s。
塔釜出料管内适宜流速一般取0。
5-1.0m/s。
由公式计算得到的尺寸均应圆整到相应规格的管径。
⑴ 进料管(包括回流管)当塔径D>800mm,且物料清洁不易聚合时,一般采用简单的进料管,如图1-25所示.当塔径D<800mm时,人不能进入塔内检修,为了检修方便,进料管应采用带外套管的可拆结构,如图1—26所示.进料管的安装尺寸可参考文献。
⑵ 塔釜出料管当塔支座直径小于800mm时,塔底出料管一般采用如图1—27(a)所示结构。
当塔支图1-27 塔釜出料管图1-26 可拆结构的进料管图1-25 简单的进料管座直径大于800mm时,出料管可采用图1—27(b)所示的结构。
为了安装方便,引出管通道直径应大于管法兰外径。
⑶ 进气管当对气体分布要求不高时,采用图1—28(a)所示结构的进气管;当塔径较大且进气要求均匀时,可采用图1-28(b)所示结构的进气管,管上开有3排小孔,管径及小孔直径与数量由工艺条件决定。
当蒸汽直接加热釜液时,蒸汽进入管安装在液面以下,管上小孔是朝下方或斜下方的。
小孔直径通常为5一10mm,各孔中心相距5一10倍孔径。
全部小孔截面积为进气管截面积的1。
25一1。
5倍。
当进气管安装在液面以上时,小孔是朝上方或斜上方的。
图1-28 进气管结构1.6.3再沸器再沸器的任务是将部分塔底的液体蒸发以便进行精馏分离。
再沸器是热交换设备,根据加热面安排的需要,再沸器的构造可以是夹套式、蛇管式或列管式;加热方式可以是间接加热或直接加热。
设计者应注意以下设计目标:①使设备成本低(保持较高的传热系数);②使换热表面尽可能清洁(防止传热管表面结垢);③对于易热分解的产品,应使其停留时间短,加热壁温低;④能满足分离要求.图1—29 塔底再沸器的形式小型再沸器可直接安装在塔底部,但再沸器的横截面积要略大于塔体的截面。
对于较大型的塔,再沸器一般安装在塔外。
工业上使用最多的形式见图1—29。
再沸器有立式和卧式之分:在立式再沸器中,被蒸发的液体在管内通过;在卧式再沸器中,被蒸发液体在管外通过。
再沸器容量大时塔的操作稳定,蒸气分离空间大时可防止蒸气中夹带液体,对易起泡系统尤为有利。
采用卧式再沸器,可以使塔和建筑物的总高度降低;由于产品在卧式再沸器中的停留时间较长,因此不适宜用于蒸发对热不稳定的产品。
热虹吸式再沸器利用再沸器中气—液混合物和塔底液体的密度差为推动力,增加流体在管内的流动速度,减少了污垢的沉积,提高了传热系数,装置紧凑,占地面积小。
凯特尔Ketile式再沸器一次通过蒸发的气液比可达80%,相当于一块理论板。
再沸器的传热面积可任意选用,釜液结焦时清洗方便,但金属消耗量和占地面积都大.当塔底产品是废水时,通常采用直接水蒸气加热,这样可节省再沸器的投资成本。
加热周期鼓泡管可参考下列数据进行设计:鼓泡管上吹气孔的孔径通常为5—10mm,各孔中心相距5一10倍孔径;吹气孔一般排列在鼓泡管的下方和侧面;全部吹气孔的总截面积约为鼓泡管截面积的1。
25—1.5倍。
1.6.4冷凝器冷凝器的任务是冷凝离开塔顶的蒸气,以便为分离提供足够的回流.部分冷凝的优点是未凝的产品富集了轻组分,冷凝器为分离提供了一块理论板。
当全凝时,部分冷凝液作为回流返回,冷凝器没有分离作用。
H T-—塔板间距,m;H F——进料板处板间距,m;H P——设人孔处板间距,m;H D—-塔顶空间(不包括头盖部分),m;H B——塔底空间(不包括底盖部分),m。
塔顶空间H D的作用是安装塔板和除沫装置的需要,起减少雾沫夹带量的作用,一般H D=1。
0~2。
0m,塔径大时可适当增大。
人孔数N P是根据物料的清洁程度塔板安装的方便而定;对于易结焦、结垢的物料,每隔4—6块板开一人孔;对于清洁物料,每隔8—10块板开一人孔;若塔板上下都可拆,可隔15块板开一人孔.常在进料口设置防冲设施,进料段高度H F应保证这些设施的方便安装。
塔底空间具有中间贮槽的作用,塔釜料液最好能在塔底有l0-15min的储量,以保证塔底料液不致排完,对于塔底产量大的塔,有时仅取3—5min的储量。
1。
6。
2 接管尺寸与结构接管的合适尺寸与在操作条件下管内的适宜流速的选择密切相关。
塔顶蒸气的适宜流速为:常压操作时取12—20m/s,绝对压力为6000—14000Pa时取30-50m/s,绝对压力小于6000Pa时取50—70m/s。
回流管内的适宜流速为:重力回流取0.2一0。
5m/s,强制回流取1。
5-2。
5m/s。
进料管内适宜流速为:由高位槽入塔时取0.4一0。
8m/s,由泵输送时取1.5一2.5m/s.塔釜出料管内适宜流速一般取0.5-1.0m/s。
由公式计算得到的尺寸均应圆整到相应规格的管径.⑴ 进料管(包括回流管)当塔径D>800mm,且物料清洁不易聚合时,一般采用简单的进料管,如图1-25所示.当塔径D<800mm时,人不能进入塔内检修,为了检修方便,进料管应采用带外套管的可拆结构,如图1—26所示。
进料管的安装尺寸可参考文献。
⑵ 塔釜出料管当塔支座直径小于800mm时,塔底出料管一般采用如图1—27(a)所示结构。
当塔支图1—27 塔釜出料管图1—26 可拆结构的进料管图1-25 简单的进料管座直径大于800mm时,出料管可采用图1-27(b)所示的结构。
为了安装方便,引出管通道直径应大于管法兰外径.⑶ 进气管当对气体分布要求不高时,采用图1—28(a)所示结构的进气管;当塔径较大且进气要求均匀时,可采用图1—28(b)所示结构的进气管,管上开有3排小孔,管径及小孔直径与数量由工艺条件决定。