气分MTBE装置技术讲座.
MTBE装置优化操作实现降本增效

1481 前言某石化企业MTBE装置建设规模为8万吨/年,主要由原料预处理部分、反应催化蒸馏部分、甲醇萃取回收部分和MTBE脱硫部分组成,产品质量要求为:MTBE 总醚类≥98%,MTBE是本公司的主要盈利产品。
原设计生产的 MTBE 硫含量≯300 μg/g ,为了满足汽油质量升级及市场需求,采用河北精致科技有限公司的脱硫专利技术,将MTBE 总硫降至 10μg/g 以下。
装置采用先进可靠的工艺技术:混相膨胀床 - 催化蒸馏深度转化合成 MTBE 组合工艺技术,反应部分采用洛阳工程公司开发的混相膨胀床合成 MTBE 技术,催化蒸馏系统采用齐鲁石化公司研究院开发的合成MTBE技术。
经预反应器后异丁烯转化率大于90%,经催化蒸馏后异丁烯总转化率大98%。
MTBE脱硫系统采用MTBE萃取蒸馏降总硫技术。
根据沸点差原理,对MTBE实施萃取再蒸馏技术,含硫MTBE 经过蒸馏将高沸点硫化物从MTBE当中切除,低硫的MTBE从塔顶蒸出,高硫馏分在塔底循环,高度富集了含硫化物的副产物从塔底抽出。
为降低MTBE损失,防止塔底生成胶质、缩聚、结焦反应,在MTBE进料中加入萃取防胶剂。
2 装置可优化方向装置控制参数在一定范围内能够满足生产需求,可以对装置工艺参数调整,实现降本增效,列出循环水、电、蒸汽等公用介质以及三剂耗量,达到进一步对装置细节优化的条件。
(1)装置停运部分机泵,或者降低机泵运行电流,节省电能;(2)满足装置冷负荷的前提下,切除部分冷却器,降低循环水耗量;(3)精馏塔优化操作,降低回流量,节省装置蒸汽耗量;(4)保证产品合格前提下,减少三剂注入量。
图1 MTBE装置节能优化3 装置可优化可行性分析3.1 装置停运部分机泵,或者降低机泵运行电流,节省电能(1)优化MTBE装置进料。
MTBE装置受进料混合碳四带碱问题,对装置催化剂活性影响较大,因此精制装置针对出装置液化气带碱问题,技改增加了两个聚结器,减少气分装置进料中的水及碱液杂质,效果较好,MTBE装置碳四原料罐脱液频率逐渐降低,后期装置原料罐已经不再带液,混合进料的PH值能够达到设计要求;气分装置出料混合碳四压力稳定且满足MTBE进料压力。
气体分馏_MTBE_烷基化装置组合优化_提高碳四资源利用水平_刘初春
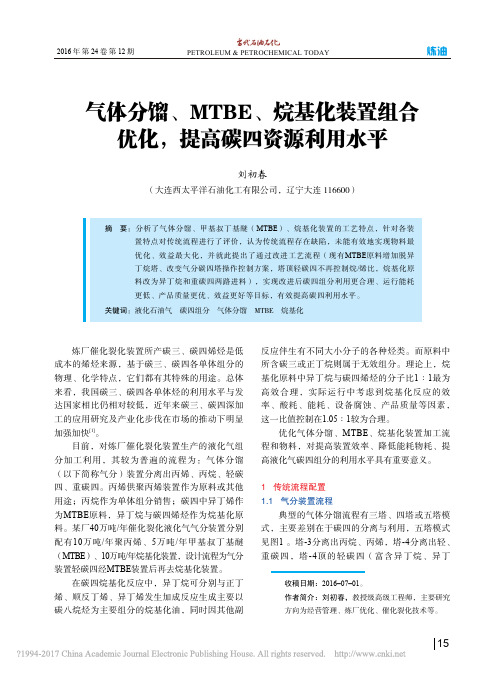
气体分馏、MTBE、烷基化装置组合优化,提高碳四资源利用水平刘初春(大连西太平洋石油化工有限公司,辽宁大连 116600)摘要:分析了气体分馏、甲基叔丁基醚(MTBE)、烷基化装置的工艺特点,针对各装置特点对传统流程进行了评价,认为传统流程存在缺陷,未能有效地实现物料最优化、效益最大化,并就此提出了通过改进工艺流程(现有MTBE原料增加脱异丁烷塔、改变气分碳四塔操作控制方案,塔顶轻碳四不再控制烷/烯比,烷基化原料改为异丁烷和重碳四两路进料),实现改进后碳四组分利用更合理、运行能耗更低、产品质量更优、效益更好等目标,有效提高碳四利用水平。
关键词:液化石油气 碳四组分 气体分馏 MTBE 烷基化炼厂催化裂化装置所产碳三、碳四烯烃是低成本的烯烃来源,基于碳三、碳四各单体组分的物理、化学特点,它们都有其特殊的用途。
总体来看,我国碳三、碳四各单体烃的利用水平与发达国家相比仍相对较低,近年来碳三、碳四深加工的应用研究及产业化步伐在市场的推动下明显加强加快[1]。
目前,对炼厂催化裂化装置生产的液化气组分加工利用,其较为普遍的流程为:气体分馏(以下简称气分)装置分离出丙烯、丙烷、轻碳四、重碳四。
丙烯供聚丙烯装置作为原料或其他用途;丙烷作为单体组分销售;碳四中异丁烯作为MTBE原料,异丁烷与碳四烯烃作为烷基化原料。
某厂40万吨/年催化裂化液化气气分装置分别配有10万吨/年聚丙烯、5万吨/年甲基叔丁基醚(MTBE)、10万吨/年烷基化装置,设计流程为气分装置轻碳四经MTBE装置后再去烷基化装置。
在碳四烷基化反应中,异丁烷可分别与正丁烯、顺反丁烯、异丁烯发生加成反应生成主要以碳八烷烃为主要组分的烷基化油,同时因其他副反应伴生有不同大小分子的各种烃类。
而原料中所含碳三或正丁烷则属于无效组分。
理论上,烷基化原料中异丁烷与碳四烯烃的分子比1∶1最为高效合理,实际运行中考虑到烷基化反应的效率、酸耗、能耗、设备腐蚀、产品质量等因素,这一比值控制在1.05∶1较为合理。
气分MTBE装置技术讲座ppt课件

*
五、装置工艺原则流程图
C2.C3 C2 C=3 C2C3C4C5 C3 C4C5 CO3
*
四、气体分馏装置的基本原理
板以下为提馏段,塔内进行精馏过程。原料进入进料板,其汽、液相在进料板的温度、压力下分别与塔内的汽、液相混合后,汽相上升到精馏段,液相下流到提馏段。通过塔板的精馏 作用,沿塔高向上,轻组分浓度递增,温度递减;沿塔高向下,重组分浓度递增,温度递增。塔顶馏出物经塔顶冷凝冷却器冷凝冷却,一部分抽出作为塔顶产品,一部分送回塔顶作塔顶回流。塔底由重沸器提供热量,将塔底物加热,使塔底物中所含部分轻组分蒸发,作为塔内蒸汽。塔底(或重沸器)液相抽出一部分送回塔内,一部分作为产品。
*
2、能量平衡
名 称
单耗 /吨原料
设 计
1996年 (标定)
2000年 (标定)
循环水
t/t
61.19
94.00
108.04
电
Kw.h(度)/t
11.84
9.15
5.276
1.0Mpa蒸汽
t/t
0.23
0.90
0.905
110℃热水
t/t
12.58
凝结水
t/t
*
四、装置的工艺原则流程图
2、产品分离部分采取先共沸蒸馏,分离出MTBE产品,然后用无离子水为萃取剂,萃取脱除C4中的MeOH,这种产品分离流程,可避免因水洗脱除MeOH,再蒸馏分离的C4和MeOH而引起的MTBE产品的部分损失和含水MTBE产品的干燥问题。
*
五、装置工艺原则流程图
2.4
2.4
T201顶回流温度℃
41.8
32
MTBE装置生产原理及工艺流程
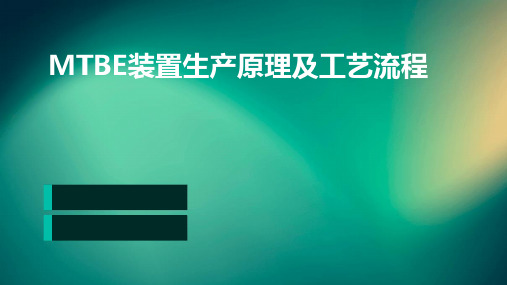
采用环保技术和清洁生产工艺,降低能耗和资源消 耗,减少污染物排放。
03
建立环保监测和报告制度,及时向相关部门报送环 保数据和信息。
THANKS FOR WATCHING
感谢您的观看
详细描述
原料的配比对于化学反应的平衡和速率具有重要影响,进而 影响产品的收率和质量。因此,需要精确控制原料配比,确 保其在工艺要求的范围内,以获得最佳的工艺效果。
05 安全与环保注意事项
安全操作规程
操作人员需经过专业培训,熟悉装置操作规程和 安全注意事项。
操作过程中应严格遵守工艺流程和安全操作规程, 确保生产安全。
MTBE装置生产原理及工艺流程
目 录
• MTBE装置简介 • MTBE生产原理 • MTBE装置工艺流程 • 工艺流程中的关键控制点 • 安全与环保注意事项
01 MTBE装置简介
MTBE的化学结构
甲基叔丁基醚(MTBE)是一 种有机化合物,其化学式为 C5H12O,结构简式为 CH3OC(CH3)3。
甲醇的合成原理
甲醇的合成主要通过一氧化碳和氢气 的反应制得,反应方程式为 CO+2H2→CH3OH。
甲醇的合成需要在高温高压条件下进 行,同时需要严格控制反应温度和压 力,以获得高收率、高纯度和低能耗 的合成效果。
在甲醇合成过程中,催化剂的选择同 样重要,常用的催化剂包括锌铬催化 剂、铜基催化剂和贵金属催化剂等。
分离过程
利用蒸馏原理,将MTBE从反应液 中分离出来,收集MTBE产品。
产品储存
将分离出的MTBE产品储存于指定 容器中,进行质量检测和包装,确 保产品质量符合要求。
04 工艺流程中的关键控制点
温度控制
总结词
温度控制是MTBE装置生产中的重要环节,它直接影响产品的质量和产量。
气分MTBE装置脱硫技措的实施与应用
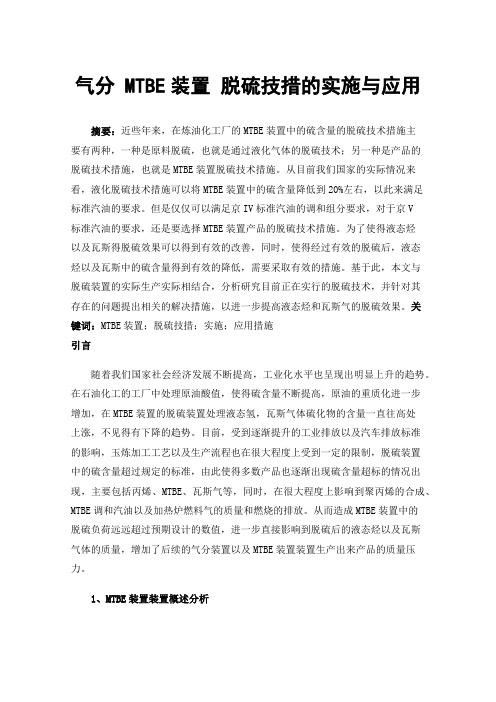
气分 MTBE装置脱硫技措的实施与应用摘要:近些年来,在炼油化工厂的MTBE装置中的硫含量的脱硫技术措施主要有两种,一种是原料脱硫,也就是通过液化气体的脱硫技术;另一种是产品的脱硫技术措施,也就是MTBE装置脱硫技术措施。
从目前我们国家的实际情况来看,液化脱硫技术措施可以将MTBE装置中的硫含量降低到20%左右,以此来满足标准汽油的要求。
但是仅仅可以满足京IV标准汽油的调和组分要求,对于京V标准汽油的要求,还是要选择MTBE装置产品的脱硫技术措施。
为了使得液态烃以及瓦斯得脱硫效果可以得到有效的改善,同时,使得经过有效的脱硫后,液态烃以及瓦斯中的硫含量得到有效的降低,需要采取有效的措施。
基于此,本文与脱硫装置的实际生产实际相结合,分析研究目前正在实行的脱硫技术,并针对其存在的问题提出相关的解决措施,以进一步提高液态烃和瓦斯气的脱硫效果。
关键词:MTBE装置;脱硫技措;实施;应用措施引言随着我们国家社会经济发展不断提高,工业化水平也呈现出明显上升的趋势。
在石油化工的工厂中处理原油酸值,使得硫含量不断提高,原油的重质化进一步增加,在MTBE装置的脱硫装置处理液态氢,瓦斯气体硫化物的含量一直往高处上涨,不见得有下降的趋势。
目前,受到逐渐提升的工业排放以及汽车排放标准的影响,玉炼加工工艺以及生产流程也在很大程度上受到一定的限制,脱硫装置中的硫含量超过规定的标准,由此使得多数产品也逐渐出现硫含量超标的情况出现,主要包括丙烯、MTBE、瓦斯气等,同时,在很大程度上影响到聚丙烯的合成、MTBE调和汽油以及加热炉燃料气的质量和燃烧的排放。
从而造成MTBE装置中的脱硫负荷远远超过预期设计的数值,进一步直接影响到脱硫后的液态烃以及瓦斯气体的质量,增加了后续的气分装置以及MTBE装置装置生产出来产品的质量压力。
1、MTBE装置装置概述分析甲基叔丁基醚就是所谓的MTBE,作为一种液体,其具有无色、透明、辛烷值较高的特点。
气分、MTBE及产品精制装置基本原理概述
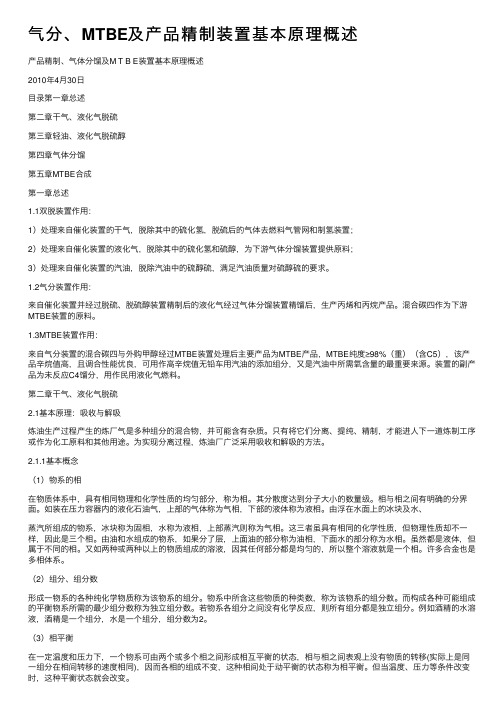
⽓分、MTBE及产品精制装置基本原理概述产品精制、⽓体分馏及M T B E装置基本原理概述2010年4⽉30⽇⽬录第⼀章总述第⼆章⼲⽓、液化⽓脱硫第三章轻油、液化⽓脱硫醇第四章⽓体分馏第五章MTBE合成第⼀章总述1.1双脱装置作⽤:1)处理来⾃催化装置的⼲⽓,脱除其中的硫化氢,脱硫后的⽓体去燃料⽓管⽹和制氢装置;2)处理来⾃催化装置的液化⽓,脱除其中的硫化氢和硫醇,为下游⽓体分馏装置提供原料;3)处理来⾃催化装置的汽油,脱除汽油中的硫醇硫,满⾜汽油质量对硫醇硫的要求。
1.2⽓分装置作⽤:来⾃催化装置并经过脱硫、脱硫醇装置精制后的液化⽓经过⽓体分馏装置精馏后,⽣产丙烯和丙烷产品。
混合碳四作为下游MTBE装置的原料。
1.3MTBE装置作⽤:来⾃⽓分装置的混合碳四与外购甲醇经过MTBE装置处理后主要产品为MTBE产品,MTBE纯度≥98%(重)(含C5),该产品⾟烷值⾼,且调合性能优良,可⽤作⾼⾟烷值⽆铅车⽤汽油的添加组分,⼜是汽油中所需氧含量的最重要来源。
装置的副产品为未反应C4馏分,⽤作民⽤液化⽓燃料。
第⼆章⼲⽓、液化⽓脱硫2.1基本原理:吸收与解吸炼油⽣产过程产⽣的炼⼚⽓是多种组分的混合物,并可能含有杂质。
只有将它们分离、提纯、精制,才能进⼈下⼀道炼制⼯序或作为化⼯原料和其他⽤途。
为实现分离过程,炼油⼚⼴泛采⽤吸收和解吸的⽅法。
2.1.1基本概念(1)物系的相在物质体系中,具有相同物理和化学性质的均匀部分,称为相。
其分散度达到分⼦⼤⼩的数量级。
相与相之间有明确的分界⾯。
如装在压⼒容器内的液化⽯油⽓,上部的⽓体称为⽓相,下部的液体称为液相。
由浮在⽔⾯上的冰块及⽔、蒸汽所组成的物系,冰块称为固相,⽔称为液相,上部蒸汽则称为⽓相。
这三者虽具有相同的化学性质,但物理性质却不⼀样,因此是三个相。
由油和⽔组成的物系,如果分了层,上⾯油的部分称为油相,下⾯⽔的部分称为⽔相。
虽然都是液体,但属于不同的相。
⼜如两种或两种以上的物质组成的溶液,因其任何部分都是均匀的,所以整个溶液就是⼀个相。
【精品】MTBE装置岗位操作法讲解

M T B E装置岗位操作法讲解MTBE 装置岗位操作法一.本装置岗位设置情况概述1.1装置的生产任务 MTBE 装置是盘锦和运实业集团新材料有限公司碳四项目的主要生产装置之一,主要担负着生产MTB 的任务,本装置采用山东科源生产力促进中心设计院设计,以碳四中的异丁烯和工业甲醇为原料,经过外循环式固定床反应和催化精馏后将MTBE 和剩余碳四进行分离,然后将多余的甲醇进行回收,回收后的甲醇进行循环使用。
1.2装置的岗位设置MTBE 装置设有岗位。
分别是反应、催化蒸馏岗位和脱二甲醚、甲醇回收岗位。
1.3装置图见附页二.本装置工艺流程及上下游装置、公用工程系统的关系说2.1装置工艺流程说明2.1.1工艺流程图见MTBE 岗位操作法附页2.1.2、工艺流程说明将来自罐区V -5407甲醇原料,经甲醇送料泵P-5403A/B,送入本装置甲醇原料缓冲罐V -3001中,甲醇原料经甲醇原料泵P3001A/B与来自球罐区的碳四原料分别经泵升压计量后,一同进入M-3001混合器,控制醇烯比在1.0-1.1:1之间,原料充分混合后直接流入预热器E-3001进行预热,温度控制在40-45度,原料从顶部进入第一醚化反应器R-3001。
在大孔强酸性阳离子交换树脂催化剂的作用下,发生醚化反应。
该反应为可逆放热反应。
为了防止反应器床层温度过高,采用外循环取热的措施,将R-3001出口的一部分物料在外循环冷却器E-3002冷却至40度,经第一外循环泵P-3002增压、计量后与新鲜物料在静态混合器M-3002混合,然后从顶部进入到R-3001中。
外循环物料主要目的是稀释原料中异丁烯浓度、吸收反应热,维持床层温度。
此时出口温度约50度,异丁烯转化率约40-50%。
另一部分经反应器R3001反应后的混合物料直接进到第二醚化反应器R-3002中,R-3002的入口温度50度、异丁烯含量约20%。
在R-3002中进行醚化反应,反应热可使物料温度升到80度。
MTBE装置培训教程【一份非常好的专业资料,有很好的参考价值】

甲基叔丁基醚装置操作工技能培训教材第一章基础知识1.1 概述1.1.1 发展历程1.1.2 目前状况1.1.3 发展趋势1.2 原料1.2.1 碳四1.2.2 甲醇1.2.3 碳四烯烃物化性质1.2.4 甲醇物化性质1.2.5 催化剂1.3 产品甲基叔丁基醚1-丁烯第二章工艺流程及技术特点2.1 MTBE合成2.1.1 MTBE化学反应热力学2.1.2 MTBE化学反应动力学2.1.3 MTBE反应典型工艺流程2.1.4 MTBE反应技术特点2.1.5 MTBE反应的主要影响因素2.2 MTBE分离技术2.2.1 热旁通压力控制原理及工艺流程2.2.2 三通阀塔顶压力控制原理和工艺流程2.2.3 卡脖子压力控制原理和工艺流程2.2.4 用冷却水量控制塔顶压力2.3甲醇萃取和回收2.3.1 甲醇萃取2.3.2 甲醇回收2.3.3 甲醇回收塔闪蒸罐的设置2.4 1-丁烯分离2.4.1 分离原理2.4.2 1-丁烯分离流程第三章主要设备3.1 MTBE合成反应器3.1.1 结构和作用3.1.2 检查和维护3.2 共沸蒸馏塔3.2.1 结构和作用3.2.2 检查和维护3.3 催化蒸馏塔3.3.1 结构和作用3.3.2 检查和维护3.4 萃取塔3.4.1 结构和作用3.4.2 检查和维护3.5 甲醇回收塔3.5.1 结构和作用3.5.2 检查和维护3.6 MTBE精制塔3.6.1 结构和作用3.6.2 检查和维护第四章装置开车操作4.1 开车注意事项4.1.1 检查4.1.2 引公用工程4.1.3 吹扫4.1.4 气密4.1.5 置换4.1.6 装催化剂4.1.7 催化剂水洗4.1.8 催化剂甲醇浸泡4.1.9 甲醇回收联锁调校4.2 醚化反应开车4.2.1 注意事项4.2.2 开车4.3 醚化分离开车4.3.1 注意事项4.3.2 开车4.4 甲醇萃取开车4.4.1 注意事项4.4.2 开车4.5 甲醇回收开车4.5.1 注意事项4.5.2 开车4.6 1-丁烯分离开车4.6.1 注意事项4.6.2 开车第五章正常操作5.1 正常操作注意事项5.1.1 切水操作5.1.2 联锁操作5.1.3 取样操作5.1.4 升降负荷操作5.1.5 控制阀改副线操作5.2 醚化反应的操作5.2.1 醇烯比调整的操作5.2.2 醚化反应转化率的调节5.2.3 醚化反应床层温度的调节5.2.4 醚化反应器催化剂甲醇浸泡指标5.2.5 外循环流量的调节5.2.6 反应器内催化剂的跑损及处理方法5.2.7 转化率的计算5.2.8 醇烯比的计算5.3 MTBE催化精馏的操作5.3.1 催化蒸馏塔中的催化剂装填结构5.3.2 MP-Ⅲ型催化剂的装填方法5.3.3 催化蒸馏塔反应段补加甲醇5.3.4 催化床层温度的调节5.3.5 塔顶压力的调节5.3.6 塔顶回流量的调节5.3.7 MTBE产品质量的调节5.3.8 精MTBE产品质量的调节5.3.9 选择性的计算收率的计算5.4 MTBE共沸分离的操作5.4.1 共沸混合物的特性及进料组成5.4.2 共沸蒸馏塔的主要控制条件及指标5.4.3 共沸蒸馏塔液泛的处理5.4.4 共沸蒸馏塔灵敏点温度控制5.4.5 共沸蒸馏塔的回流比影响5.4.6 共沸蒸馏塔操作压力和供热蒸汽量对MTBE纯度的影响5.4.7 回流比的计算5.5 萃取塔的操作5.5.1 萃取塔界面失灵处理方法5.5.2 萃取塔压控失灵处理方法5.5.3 萃取塔塔顶未反应C4带水原因5.5.4 萃取水对萃取效果的影响及调节5.6 甲醇回收塔的操作5.6.1 进料温度的调节5.6.2 塔顶温度的调节5.6.3 甲醇回收塔的甲醇进料调整5.6.4 甲醇回收塔的主要操作条件5.6.5 灵敏板温度的调节5.7 1-丁烯分离开车5.7.1 精馏塔液位调节5.7.2 精馏塔回流罐液位调节5.7.3 精馏塔塔顶压力调节5.7.4 1-丁烯中间罐的使用5.7.5 第一精馏塔塔底粗1-丁烯中杂质含量超标的调整5.7.6 第一精馏塔塔顶采出物料中1-丁烯含量的调整5.7.7 第二精馏塔塔顶1-丁烯产品中重组分含量超标的调整5.7.8 第二精馏塔塔底采出物料中1-丁烯含量超标的调整第六章装置停车操作6.1 停车注意事项6.2 停车准备6.3 醚化反应停车6.4 醚化分离停车6.4.1 共沸蒸馏塔的停车6.4.2 催化蒸馏塔的停车6.5 甲醇萃取停车6.6 甲醇回收停车6.7 二烯烃加氢停车6.8 1-丁烯分离停车6.8.1 正常停车6.8.2 临时停车6.8.3 紧急停车第七章事故判断及处理7.1 事故现象的判断7.2 事故处理的原则7.3 停公用工程事故的处理7.3.1 停水的处理7.3.2 停电的处理7.3.3 停汽的处理7.3.4 停仪表风的处理7.4 设备超压、超温的应急预案7.5危险化学品泄漏的应急预案7.5.1 甲醇7.5.2 MTBE7.6 防雷防震预案7.6.1 防雷7.6.2 防震7.7 防台防汛预案7.7.1 台风7.7.2 潮水7.8 火灾爆炸事故的处理7.9 典型事故案例分析第八章安全、环保和节能8.1 原料及产品的规格、特性及安全规定8.1.1 原料8.1.2 催化剂8.1.3 产品MTBE的性质8.1.4 危害性及安全规定8.2 安全使用与防护8.2.1 采用的主要标准、规范8.2.2 潜在危险性分析8.2.3 主要安全卫生防范措施8.2.4 特殊安全防护的要求的设备8.2.5 安全仪表系统(SIS)8.2.6 预期效果评价8.2.7 各类装置安全设施的使用方法8.3 消防、气防要求`8.4 装置的“三废”治理8.4.1 采用的主要标准规范8.4.2 主要污染物及其排放8.4.3 环保措施8.4.4 预期效果8.5 节能降耗8.5.1 节能的管理途径8.5.2 节能的技术途径第一章基础知识1.1 概述1.1.1 发展历程甲基叔丁基醚(methyl tertiary butyl ether,简称MTBE,又称2-甲氧基-2-甲基丙烷(2-methoxy-2-methyl-propane),结构式CH3OC(CH3)3,分子式C 5H12O,分子量88.15。
MTBE生产原理及工艺流程资料讲解
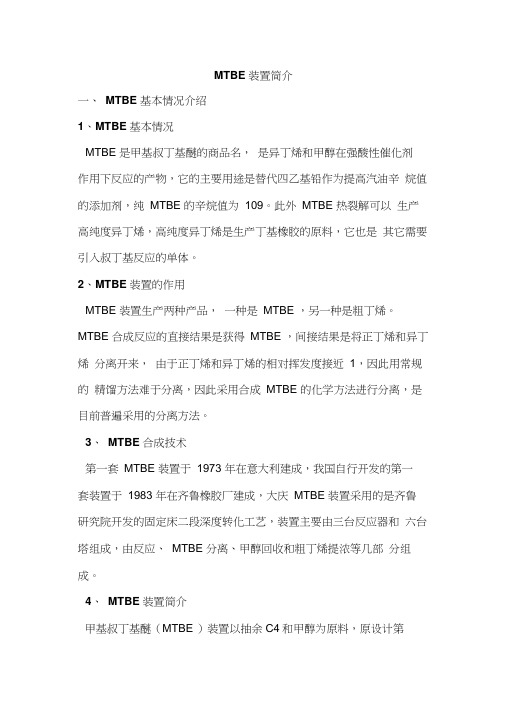
MTBE 装置简介一、MTBE 基本情况介绍1、MTBE 基本情况MTBE 是甲基叔丁基醚的商品名,是异丁烯和甲醇在强酸性催化剂作用下反应的产物,它的主要用途是替代四乙基铅作为提高汽油辛烷值的添加剂,纯MTBE 的辛烷值为109。
此外MTBE 热裂解可以生产高纯度异丁烯,高纯度异丁烯是生产丁基橡胶的原料,它也是其它需要引入叔丁基反应的单体。
2、MTBE 装置的作用MTBE 装置生产两种产品,一种是MTBE ,另一种是粗丁烯。
MTBE 合成反应的直接结果是获得MTBE ,间接结果是将正丁烯和异丁烯分离开来,由于正丁烯和异丁烯的相对挥发度接近1,因此用常规的精馏方法难于分离,因此采用合成MTBE 的化学方法进行分离,是目前普遍采用的分离方法。
3、MTBE 合成技术第一套MTBE 装置于1973 年在意大利建成,我国自行开发的第一套装置于1983 年在齐鲁橡胶厂建成,大庆MTBE 装置采用的是齐鲁研究院开发的固定床二段深度转化工艺,装置主要由三台反应器和六台塔组成,由反应、MTBE 分离、甲醇回收和粗丁烯提浓等几部分组成。
4、MTBE 装置简介甲基叔丁基醚(MTBE )装置以抽余C4和甲醇为原料,原设计第二生产方案年处理抽余C4 32500 吨,生产MTBE 19864 吨,粗丁烯9616吨,副产剩余C4 10224吨。
MTBE 装置由齐鲁石化公司设计院提供基础设计,大庆石化总厂设计院完成初步设计和施工图设计。
1988年5 月投产,投资37495162元,装置占地面积15600m2。
2001年10月装置进行了扩能改造,年处理抽余C4 处理能力提高到52000 吨,生产MTBE 29963 吨,粗丁烯29384 吨。
同时装置由原来的DDZ皿型仪表控制改为DCS控制。
2001年10月配合塑料厂丁烯精制项目改造,MTBE装置又增设了F103和H218两台设备。
二、工艺流程简述来自丁二烯抽提装置的混合C4原料进入原料罐R301/1.2,来自储运公司的CH3OH原料进入甲醇原料罐R101。
脱硫——气分——MTBE联合装置操作规程综述

脱硫——气分——MTBE联合装置操作规程装置简介:该装置为山东天宏新能源化工有限公司60万吨/年催化裂解、100万吨/年焦化配套炼厂气加工项目,该装置包括干气脱硫、液化气脱硫、气体分离、MTBE 等单元组成。
该装置主要产品:丙烯、丙烷、民用液化气、MTBE。
该装置有济南化工设计院设计,黑龙江省安装工程公司建设施工技术特点:1、液化气、干气脱硫采用常规醇胺吸收法,溶剂为复配高效MDEA溶剂,保证脱后效果。
脱硫塔采用板式塔;胺液再生塔采用波纹规整填料;液化气脱硫醇采用成熟的催化氧化法工艺。
2、液化气分馏采用三塔工艺,即脱丙烷丙烯塔、脱乙烷塔、丙烯精制塔(丙烷-丙烯分离),为了保证丙烯纯度高,设置两塔(A、B)。
3、MTBE采用离子反应、醚化、催化共沸蒸馏工艺,提高MTBE纯度和资源回收利用,节约能源。
4、液化气脱硫醇采用了两级混合器取代抽提塔,催化剂(聚酞菁钴),碱液里加入活化剂提高硫醇转化率,从而保证其脱除率。
5、气分各塔采用了高效导向浮阀塔板,提高板效率。
6、部分机泵采用变频调速技术,降低电耗。
7、采用了先进的DCS(集散型仪表)控制系统。
第一篇工艺流程第一章脱硫工艺流程第一节工艺控制流程图(见附图)第二节工艺流程说明一、干气脱硫干气自催化装置来,进入干气脱硫塔T-103底部,经与塔顶来的贫胺液逆向接触反应进行脱硫,脱硫净化后的干气进入全厂瓦斯管网,吸收硫的富胺液自塔底自压流出,经液控阀LT-1106并入液化气脱硫富液一起进入乙醇胺贫富液换热器E-101/4,3,E-101/2,1(管程),与再生贫液换热升温后,一路作为塔二段上回流,一路从塔进料段入塔再生。
二、液化气脱硫自催化装置(或外购)来的液化气经脱硫原料缓冲罐V-105、液位控制阀LT-1101进入罐内,由原料泵P-101/1、2经流控FT-1101进入脱硫吸收塔T-102底部与塔顶来的贫液逆向接触进行脱硫。
脱硫后的液化气去液化气脱硫醇,吸收硫的富胺液自塔底自压流出与干气脱硫富胺液一起进入E-101/4,3,E-101/2,1。
MTBE装置基础知识课件

3.1工艺流程
甲醇塔 萃取塔 共沸塔
净化器
混 碳 四
反应器
甲醇缓 冲罐
甲 醇
Thank you!
净化后的原料进入反应器,反应产物从反应器顶部
出来进入共沸塔,甲醇与未反应C4以共沸物形式从塔 顶馏出,塔底TBE产品自压到装置外MTBE产品罐。
工艺流程
3.3 甲醇回收部分 从共沸塔顶来的甲醇与未反C4的共沸混合物 进入萃 取塔底部,与塔顶进入循环萃取水经逆流萃取后,甲 醇几乎全部溶于水中。碳四馏分由塔顶馏出,送至液 化气罐区,含甲醇的萃取水进入甲醇塔进行甲醇回收, 循环利用。
2.2.2 醇稀比 醇稀比:原料中甲醇与异丁烯的摩尔比。一般控制为 1.0~1.05为宜。
醇稀比过大:可使异丁烯转化率增加,但多余的甲醇不
仅增加了共沸塔的分离难度而且增加了甲醇回 收塔的
负荷。
醇稀比过小:发生异丁烯聚合反应,放出大量热量,造 成反应器超温,烧坏催化剂。
三、工艺流程
工艺流程
3.1 原料预处理部分 混碳四进入脱碱罐(V-409),脱除混合碳四游离水 中所含的胺、碱、及碱金属离子等,然后与从罐区来 的原料甲醇经充分混合后进入净化器(R-402A/B)脱出 原料中的有害物质 。 3.2反应和产品分离部分
1.3 产品
1.3.1 MTBE理化性质: 物态:液体 外观:无色澄清液体 气味:醚样气味 沸点:54~55℃ 相对密度:0.76
毒性:属于低毒物质,对皮肤无明显的刺激作用。
辛烷值:马达法101;研究法117.
1.3 产品
1.3.2 MTBE的主要用途 MTBE作为汽油添加剂具有优良的性能,不仅具有
2.2.1反应温度 反应温度的高低不仅影响异丁烯的转化率,而且也 影响MTBE的选择性、催化剂的使用寿命和反应速度。 为延长催化剂寿命、减少副反应、提高选择性应采 用较低的反应温度,一般50~70℃为宜. 温度超过80 ℃, 副反应增加,催化剂寿命缩短,温度超过120℃,催化 剂失活。
人力资源MTBE装置岗位操作培训
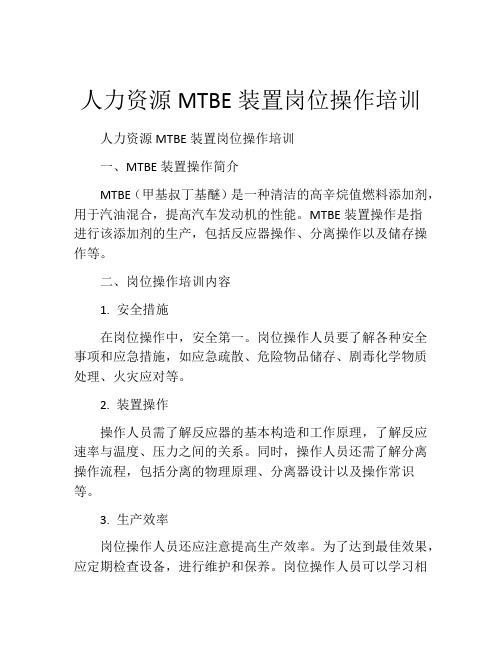
人力资源MTBE装置岗位操作培训人力资源MTBE装置岗位操作培训一、MTBE装置操作简介MTBE(甲基叔丁基醚)是一种清洁的高辛烷值燃料添加剂,用于汽油混合,提高汽车发动机的性能。
MTBE装置操作是指进行该添加剂的生产,包括反应器操作、分离操作以及储存操作等。
二、岗位操作培训内容1. 安全措施在岗位操作中,安全第一。
岗位操作人员要了解各种安全事项和应急措施,如应急疏散、危险物品储存、剧毒化学物质处理、火灾应对等。
2. 装置操作操作人员需了解反应器的基本构造和工作原理,了解反应速率与温度、压力之间的关系。
同时,操作人员还需了解分离操作流程,包括分离的物理原理、分离器设计以及操作常识等。
3. 生产效率岗位操作人员还应注意提高生产效率。
为了达到最佳效果,应定期检查设备,进行维护和保养。
岗位操作人员可以学习相关技能,如为自动控制系统的参数调整、PLC编程等,以提高生产效率,减少能源浪费。
4. 质量控制岗位操作人员应了解MTBE装置生产过程中的质量控制方法,保证生产过程的质量和安全。
操作人员需要学习质量检查流程和各项检查内容,包括原材料质量检查、生产过程监测以及成品检查等。
三、培训内容的实施培训内容的实施,需要分为课堂培训和现场操作培训两个部分。
1. 课堂培训首先,要给操作人员提供详细的岗位操作说明书,使得操作人员能够了解反应器的基本构造和工作原理,以及分离器等设备的使用方法等。
其次,应让操作人员系统地学习安全措施、质量控制内容和生产效率的调整。
最后,应邀请专业人员为操作人员讲解MTBE装置操作的参数调整、PLC编程等技能课程。
2. 现场操作培训在操作人员掌握了基本的知识之后,需要进行现场操作培训,让操作人员亲身参与装置操作。
通过操作实践,操作人员可以加深了解MTBE装置操作的实际流程、操作注意事项和解决问题的方法。
四、培训效果的评估和总结为了评估和总结MTBE装置操作培训的效果,应收集操作人员在岗位操作过程中遇到的问题并及时解决,确认操作人员的知识掌握情况和操作技巧是否符合要求。
气分、MTBE讲课知识
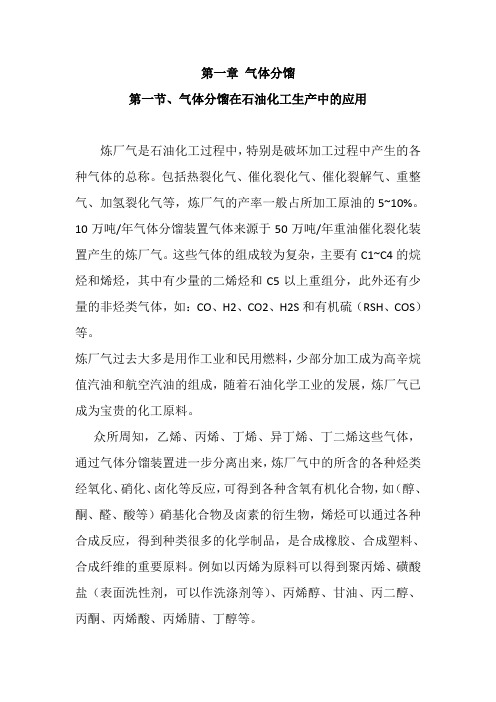
第一章气体分馏第一节、气体分馏在石油化工生产中的应用炼厂气是石油化工过程中,特别是破坏加工过程中产生的各种气体的总称。
包括热裂化气、催化裂化气、催化裂解气、重整气、加氢裂化气等,炼厂气的产率一般占所加工原油的5~10%。
10万吨/年气体分馏装置气体来源于50万吨/年重油催化裂化装置产生的炼厂气。
这些气体的组成较为复杂,主要有C1~C4的烷烃和烯烃,其中有少量的二烯烃和C5以上重组分,此外还有少量的非烃类气体,如:CO、H2、CO2、H2S和有机硫(RSH、COS)等。
炼厂气过去大多是用作工业和民用燃料,少部分加工成为高辛烷值汽油和航空汽油的组成,随着石油化学工业的发展,炼厂气已成为宝贵的化工原料。
众所周知,乙烯、丙烯、丁烯、异丁烯、丁二烯这些气体,通过气体分馏装置进一步分离出来,炼厂气中的所含的各种烃类经氧化、硝化、卤化等反应,可得到各种含氧有机化合物,如(醇、酮、醛、酸等)硝基化合物及卤素的衍生物,烯烃可以通过各种合成反应,得到种类很多的化学制品,是合成橡胶、合成塑料、合成纤维的重要原料。
例如以丙烯为原料可以得到聚丙烯、磺酸盐(表面洗性剂,可以作洗涤剂等)、丙烯醇、甘油、丙二醇、丙酮、丙烯酸、丙烯腈、丁醇等。
炼厂气作为化工原料,必须进行分离,分离的方法很多,就其本质来说可以分为两类,一类是物理分离法,即利用烃类的物理性质的差别进行分离。
如:利用烃类的饱和蒸汽压、沸点不同而进行气体分离过程,有些合成过程对气体纯度要求较高时,则需要高效率的气体分离,如吸附、超精馏、抽提精馏、共沸蒸馏等;另一类方法是化学方法,既利用化学反应的方法将它们分离,如化学吸附和分子筛分离。
目前,我国绝大多数炼油厂采用气体分离装置对炼厂气进行分离,以制取丙烯、丙烷、丁烷、异丁烷,可以说是以炼油厂气为原料的石油化工生产的龙头装置。
第二节、气体分馏的基本工艺过程气体分馏主要是指对液化石油气即碳三、碳四的进一步分离。
这些烃类在常温常压下均为气体,但在一定压力下成为液态,利用其不同沸点进行精馏加以分离。
- 1、下载文档前请自行甄别文档内容的完整性,平台不提供额外的编辑、内容补充、找答案等附加服务。
- 2、"仅部分预览"的文档,不可在线预览部分如存在完整性等问题,可反馈申请退款(可完整预览的文档不适用该条件!)。
- 3、如文档侵犯您的权益,请联系客服反馈,我们会尽快为您处理(人工客服工作时间:9:00-18:30)。
7
四、气体分馏装置的基本原理
气体分馏装置是以液化气为原料 , 通过分馏生产出精丙
烯、丙烷和混合C4馏分的过程。
分馏是利用烃类的物理性质的差异进行组分分离的物理
方法,即根据被分离组分的相对挥发度的不同进行分离,这
就是分馏过程。
气体分馏是根据在一定的温度、压力条件下,混合物中
各组分的相对挥发度不同而进行气体分离的一种方法。
17
第二部分:MTBE装置简介
18
一、装置慨述
本装置设计生产规模为年产2万吨MTBE产品,由洛阳工程
公司设计。
装置的原料为气体分馏装置生产的混合 C4 组分和外购的
甲醇,在催化剂作用下,经过反应、分馏、萃取、回收的工 艺过程,生产出MTBE(纯度≥95%)和未反应C4。
6
三、装置安全特点
气体分馏装置的任务是以液化石油气为原料生产合格的精
丙烯、丙烷和混合C4馏分,从原料到产品这些物质具有闪点低、 引烃能量小、爆炸下限低、爆炸范围大等特点,一旦发生泄漏, 遇着火源就有燃烧、爆炸的危险,所以它们均属于易燃易爆危
险品。根据国家有关规定,本装置属于甲A类火灾危险的场所。
冷却器
精馏塔 塔顶馏出物
进料Βιβλιοθήκη 重沸器塔底物10
五、装置工艺原则流程图
C2.C3 C2 C=3
C2C3C4C5
C3
C4C5
CO3
11
五、装置工艺原则流程图
C2.C3.C4.C5
V202 V201
C2.C3
V203
C2
C=3
V204
T201
T202
T203A
T203B
CO3 C4C5 C3
12
五、装置工艺原则流程图
5
二、装置的工艺特点
确定合理的流程方案,这涉及到生产能力、工艺要求、
产品质量、设备投资、消耗、操作等方面的问题,根据我公 司生产工艺总体流程安排,确定我装置为采用能生产精丙烯、
丙烷和混合C4的三塔流程,从操作和投资费用来考虑,此方
案优于其他方案,由于后部无配套装置,因此混合C4不作进 一步的分离
2
第一部分:气体分馏装置简介
3
(一)、装置慨述
本装置所使用的仪表为 FC系列可编程调节器,主要控制
方案有:T201顶压力采用分程控制、T203顶压力采用“热旁 路”控制、塔底温度采用与重沸器热源介质流量串级控制。
装置占地面积63×62=3906平方米。 本装置共有设备71台,其中塔10台,冷凝冷却器14台,空
塔高向下,重组分浓度递增,温度递增。塔顶馏出物经塔顶
冷凝冷却器冷凝冷却,一部分抽出作为塔顶产品,一部分送 回塔顶作塔顶回流。塔底由重沸器提供热量,将塔底物加热, 使塔底物中所含部分轻组分蒸发,作为塔内蒸汽。塔底(或 重沸器)液相抽出一部分送回塔内,一部分作为产品。
9
四、气体分馏装置的基本原理
气体分馏的基本工艺过程示意见下图。
气分、MTBE装置简介
1
主要内容:
一、气分装置 (一)装置概述 (二)装置的工艺特点 (三)装置安全特点 (四)装置的基本原理 (五)装置工艺原则流程图 (六)装置的工艺控制指标 (七)装置物料及能量平衡 (八)装置技术改造 (九)装置的现状分析 (十)、装置下一步的工作重点 二、MTBE装置 (一)装置概述 (二)装置的工艺特点 (三)装置的基本原理 (四)装置工艺原则流程图 (五)装置的工艺控制指标 (六)装置物料及能量平衡 (七)装置技术改造 (八)装置的现状分析 (九)装置下一步的工作重点
冷器3台,换热器5台,容器14台,机泵23台,升压器2台。
4
表1
设备名称 塔类 冷却器 换热器 容器
设备概况表
总数 气分 精制 设备名称 总数 气分 精制 (台) (台) (台) (台) (台) (台) 10 14 5 14 4 14 5 11 3 6 机泵 空冷器 升压器 合计 23 3 2 71 58 21 3 2 13 2
V-01
G-01/AB
G-02
G-03
G-04
精丙烯
丙烯来
13
六、装置的工艺控制指标
1、原料及产品质量控制指标 项 目 碳二含量%(重) 碳五含量%(重) 总硫PPM 设计指标 ≤2 ≤3 ≤20 实际控制 ≤1 ≤1 ≤20
水PPM 丙烯纯度%(重) 丙烯含水PPM 丙烯总硫PPM 丙烷纯度%(重)
T202顶回流比% T203/A底温℃
104.8 2.4 41.8 2.65
17.6 57.5
100 2.4 32 2.15 15
56.5-57.5
T203/B顶压MPA
1.85
1.70
15
七、装置物料及能量平衡
1、物料平衡:
物料名称 设 计 1999年 (改造前 标定) 收率% 100 34.48 7.39 56.65 1.48 94.27 2000年 (改造后 标定) 收率% 100 33.19 5.57 59.88 1.36 96.78
16
收率% 入 方 液态烃 精丙烯 丙烷馏分 出 方 叠合原料 燃料气+ 损失 丙烯回收率 100 33.10 9.24 55.41 2.25 93
2、能量平衡 名 称 循环水 电 1.0Mpa蒸汽 110℃热水 凝结水 新鲜水 单位能耗 单耗 /吨 原料 t/t Kw.h(度)/ t t/t t/t t/t t/t 万大卡/吨 设 计 61.19 11.84 0.23 12.58 -0.23 57.07 1996年 (标定) 94.00 9.15 0.90 2000年 (标定) 108.04 5.276 0.905 -0.905 85.11 0.30 74.94
气体分馏工艺最基本的设备是由精馏塔、冷凝冷却器和
重沸器组成的。塔内装设塔板。进料板以上为精馏段,进料
8
四、气体分馏装置的基本原理
板以下为提馏段,塔内进行精馏过程。原料进入进料板,其
汽、液相在进料板的温度、压力下分别与塔内的汽、液相混
合后,汽相上升到精馏段,液相下流到提馏段。通过塔板的 精馏 作用,沿塔高向上,轻组分浓度递增,温度递减;沿
≤500 ≥ 99.5 ≤100 ≤5 ≥87
≤500 ≥ 99.6 ≤100 ≤5 ≥90
14
六、装置的工艺控制指标
2、主要工艺控制指标 项 目 T201进料温度℃ T201顶压MPA T201底压MPA 设计指标 71 1.85 1.95 实际控制 70 1.80 1.85
T201底温℃ T201顶回流比% T201顶回流温度℃ T202顶压MPA