数控车加工薄壁组合零件工艺分析与加工方案
典型薄壁零件数控铣削加工工艺

典型薄壁零件数控铣削加工工艺数控铣削是一种高精度、高效率的数控加工方法,广泛应用于模具、航空航天、船舶、汽车、电子、仪器仪表等行业。
在零件加工中,薄壁零件因其结构特殊、加工难度大,对加工工艺要求较高。
本文将针对典型薄壁零件的数控铣削加工工艺进行介绍和分析。
一、工件材料及加工要求1. 工件材料:典型薄壁零件常用的材料有铝合金、钛合金、不锈钢等,材料硬度一般在28-45HRC之间。
2. 加工要求:薄壁零件加工一般要求表面光洁度高、尺寸精度要求高、壁厚薄、结构复杂等特点。
二、数控铣削工艺分析1. 工艺方案选择:根据零件的结构特点和加工要求,选择合适的数控铣削刀具和切削参数。
对于铝合金等材料,一般选择硬质合金刀具,切削参数选择合适的进给速度和转速。
2. 夹紧方式选择:薄壁零件加工时,应选择合适的夹紧方式,避免加工过程中因变形而影响加工质量。
一般可采用夹具夹紧或磁力吸盘夹紧等方式,根据零件尺寸和形状特点选择合适的夹紧方式。
3. 切削力控制:在数控铣削过程中,控制切削力对薄壁零件加工至关重要。
要合理选择切削参数和刀具几何角度,降低切削力,避免引起零件变形和加工质量不稳定。
4. 节渣处理:薄壁零件加工过程中,切屑容易产生,特别是在高速切削时更为显著。
应采取合适的节渣方式,避免切削刀具堵塞,影响加工质量。
5. 冷却润滑:在数控铣削过程中,及时有效的冷却润滑对加工质量和刀具寿命有着重要影响。
对薄壁零件加工,更需要合理选择喷淋位置和冷却润滑液的使用方式,以防止零件变形和表面质量不稳定。
6. 加工精度控制:薄壁零件加工时,对尺寸精度和表面质量要求较高。
在数控铣削过程中,应严格控制切削参数,采取合适的刀具路径和切削刀具轨迹,避免因加工过程中引起加工质量问题。
7. 加工工艺优化:针对典型薄壁零件的形状特点和加工要求,应综合考虑工艺方案和加工工艺优化,在保证加工质量的前提下,提高加工效率和降低成本。
例如采用高速切削、干法加工等新技术,以提高加工效率和节约成本。
薄壁零件的数控车削加工探讨
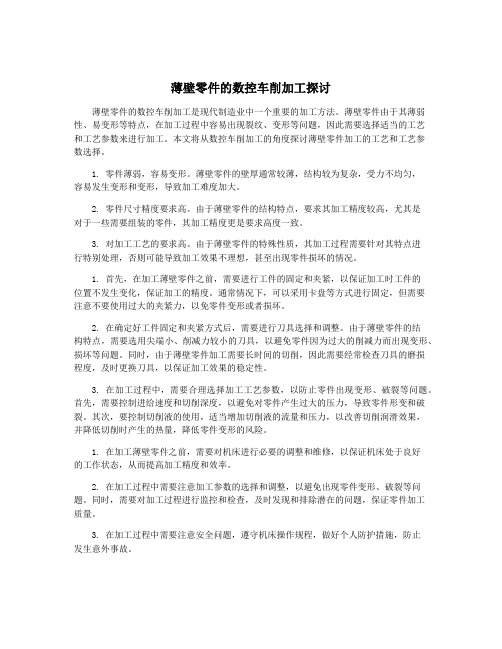
薄壁零件的数控车削加工探讨薄壁零件的数控车削加工是现代制造业中一个重要的加工方法。
薄壁零件由于其薄弱性、易变形等特点,在加工过程中容易出现裂纹、变形等问题,因此需要选择适当的工艺和工艺参数来进行加工。
本文将从数控车削加工的角度探讨薄壁零件加工的工艺和工艺参数选择。
1. 零件薄弱,容易变形。
薄壁零件的壁厚通常较薄,结构较为复杂,受力不均匀,容易发生变形和变形,导致加工难度加大。
2. 零件尺寸精度要求高。
由于薄壁零件的结构特点,要求其加工精度较高,尤其是对于一些需要组装的零件,其加工精度更是要求高度一致。
3. 对加工工艺的要求高。
由于薄壁零件的特殊性质,其加工过程需要针对其特点进行特别处理,否则可能导致加工效果不理想,甚至出现零件损坏的情况。
1. 首先,在加工薄壁零件之前,需要进行工件的固定和夹紧,以保证加工时工件的位置不发生变化,保证加工的精度。
通常情况下,可以采用卡盘等方式进行固定,但需要注意不要使用过大的夹紧力,以免零件变形或者损坏。
2. 在确定好工件固定和夹紧方式后,需要进行刀具选择和调整。
由于薄壁零件的结构特点,需要选用尖端小、削减力较小的刀具,以避免零件因为过大的削减力而出现变形、损坏等问题。
同时,由于薄壁零件加工需要长时间的切削,因此需要经常检查刀具的磨损程度,及时更换刀具,以保证加工效果的稳定性。
3. 在加工过程中,需要合理选择加工工艺参数,以防止零件出现变形、破裂等问题。
首先,需要控制进给速度和切削深度,以避免对零件产生过大的压力,导致零件形变和破裂。
其次,要控制切削液的使用,适当增加切削液的流量和压力,以改善切削润滑效果,并降低切削时产生的热量,降低零件变形的风险。
1. 在加工薄壁零件之前,需要对机床进行必要的调整和维修,以保证机床处于良好的工作状态,从而提高加工精度和效率。
2. 在加工过程中需要注意加工参数的选择和调整,以避免出现零件变形、破裂等问题。
同时,需要对加工过程进行监控和检查,及时发现和排除潜在的问题,保证零件加工质量。
浅谈薄壁零件数控车工加工工艺
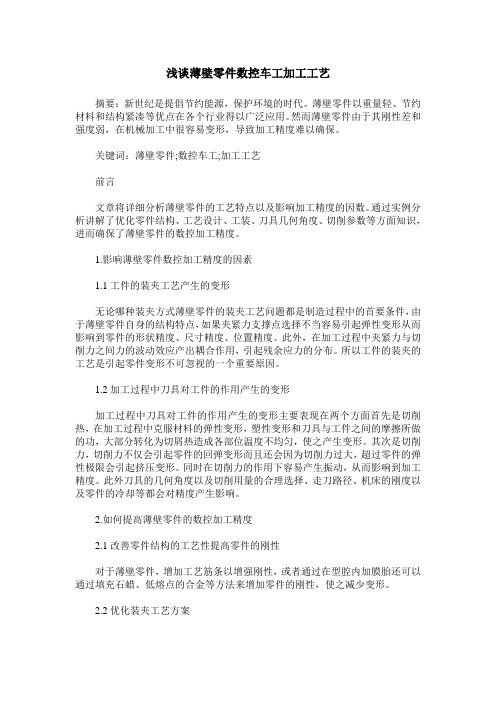
浅谈薄壁零件数控车工加工工艺摘要:新世纪是提倡节约能源,保护环境的时代。
薄壁零件以重量轻、节约材料和结构紧凑等优点在各个行业得以广泛应用。
然而薄壁零件由于其刚性差和强度弱,在机械加工中很容易变形,导致加工精度难以确保。
关键词:薄壁零件;数控车工;加工工艺前言文章将详细分析薄壁零件的工艺特点以及影响加工精度的因数。
通过实例分析讲解了优化零件结构、工艺设计、工装、刀具几何角度、切削参数等方面知识,进而确保了薄壁零件的数控加工精度。
1.影响薄壁零件数控加工精度的因素1.1工件的装夹工艺产生的变形无论哪种装夹方式薄壁零件的装夹工艺问题都是制造过程中的首要条件,由于薄壁零件自身的结构特点,如果夹紧力支撑点选择不当容易引起弹性变形从而影响到零件的形状精度、尺寸精度、位置精度。
此外,在加工过程中夹紧力与切削力之间力的波动效应产出耦合作用,引起残余应力的分布。
所以工件的装夹的工艺是引起零件变形不可忽视的一个重要原因。
1.2加工过程中刀具对工件的作用产生的变形加工过程中刀具对工件的作用产生的变形主要表现在两个方面首先是切削热,在加工过程中克服材料的弹性变形,塑性变形和刀具与工件之间的摩擦所做的功,大部分转化为切屑热造成各部位温度不均匀,使之产生变形。
其次是切削力,切削力不仅会引起零件的回弹变形而且还会因为切削力过大,超过零件的弹性极限会引起挤压变形。
同时在切削力的作用下容易产生振动,从而影响到加工精度。
此外刀具的几何角度以及切削用量的合理选择、走刀路径、机床的刚度以及零件的冷却等都会对精度产生影响。
2.如何提高薄壁零件的数控加工精度2.1改善零件结构的工艺性提高零件的刚性对于薄壁零件,增加工艺筋条以增强刚性,或者通过在型腔内加膜胎还可以通过填充石蜡、低熔点的合金等方法来增加零件的刚性,使之减少变形。
2.2优化装夹工艺方案不同的零件结构和加工方法对应不同的装夹工艺。
在已有的装夹工艺的基础上对其进行改进,优化设计是装夹工艺优化的基本方法。
机械加工中数控车加工薄壁组合零件工艺分析解汉三
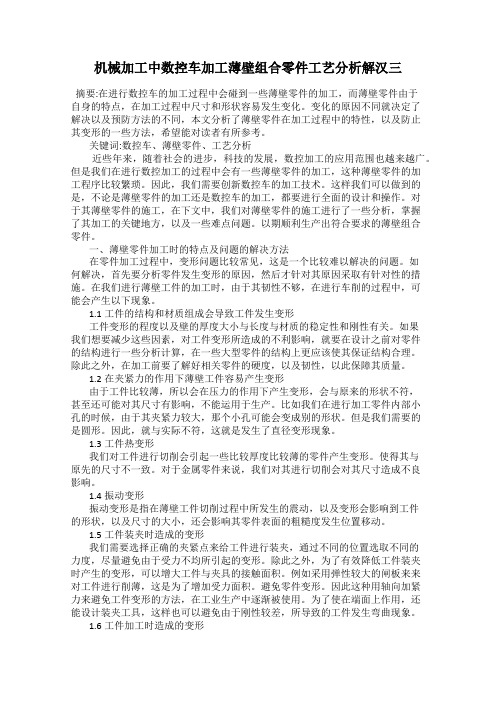
机械加工中数控车加工薄壁组合零件工艺分析解汉三摘要:在进行数控车的加工过程中会碰到一些薄壁零件的加工,而薄壁零件由于自身的特点,在加工过程中尺寸和形状容易发生变化。
变化的原因不同就决定了解决以及预防方法的不同,本文分析了薄壁零件在加工过程中的特性,以及防止其变形的一些方法,希望能对读者有所参考。
关键词:数控车、薄壁零件、工艺分析近些年来,随着社会的进步,科技的发展,数控加工的应用范围也越来越广。
但是我们在进行数控加工的过程中会有一些薄壁零件的加工,这种薄壁零件的加工程序比较繁琐。
因此,我们需要创新数控车的加工技术。
这样我们可以做到的是,不论是薄壁零件的加工还是数控车的加工,都要进行全面的设计和操作。
对于其薄壁零件的施工,在下文中,我们对薄壁零件的施工进行了一些分析,掌握了其加工的关键地方,以及一些难点问题。
以期顺利生产出符合要求的薄壁组合零件。
一、薄壁零件加工时的特点及问题的解决方法在零件加工过程中,变形问题比较常见,这是一个比较难以解决的问题。
如何解决,首先要分析零件发生变形的原因,然后才针对其原因采取有针对性的措施。
在我们进行薄壁工件的加工时,由于其韧性不够,在进行车削的过程中,可能会产生以下现象。
1.1工件的结构和材质组成会导致工件发生变形工件变形的程度以及壁的厚度大小与长度与材质的稳定性和刚性有关。
如果我们想要减少这些因素,对工件变形所造成的不利影响,就要在设计之前对零件的结构进行一些分析计算,在一些大型零件的结构上更应该使其保证结构合理。
除此之外,在加工前要了解好相关零件的硬度,以及韧性,以此保障其质量。
1.2在夹紧力的作用下薄壁工件容易产生变形由于工件比较薄,所以会在压力的作用下产生变形,会与原来的形状不符,甚至还可能对其尺寸有影响,不能运用于生产。
比如我们在进行加工零件内部小孔的时候,由于其夹紧力较大,那个小孔可能会变成别的形状。
但是我们需要的是圆形。
因此,就与实际不符,这就是发生了直径变形现象。
典型薄壁零件数控铣削加工工艺

典型薄壁零件数控铣削加工工艺数控铣削是一种精密加工方法,广泛应用于各种零件的加工过程中。
而对于薄壁零件的加工,由于其结构特点,需要特殊的加工工艺,以确保加工质量和效率。
下面介绍一种典型的薄壁零件数控铣削加工工艺。
1. 设计加工方案首先需要对零件进行结构设计和加工方案设计。
针对薄壁零件,需要注意材料选择、壁厚尺寸和加工顺序等问题。
在设计方案中,需要将零件分解为不同的加工步骤,并分析每个步骤中的工艺要求和工序参数。
2. 材料选择对于薄壁零件的加工,材料选择至关重要。
一般来说,薄壁零件使用的材料应该具有一定的塑性和韧性,以便于加工过程中的变形和切削。
常见的材料包括铝合金、钛合金和不锈钢等。
3. 刀具选择根据加工方案和零件设计要求,选择合适的刀具进行加工。
对于薄壁零件的加工,一般选择刚度较小、切削性能好的刀具。
还需要注意刀具的锋利度和几何参数等,确保切削效果和加工精度。
4. 加工顺序在进行数控铣削加工时,需要合理确定加工顺序。
对于薄壁零件而言,一般应先进行空间徐铣,即去除零件表面的余料和毛刺,然后再进行精确加工和表面处理。
加工顺序应根据零件结构和切削特点进行选择。
5. 加工参数在数控铣削加工过程中,需要合理设置加工参数。
对于薄壁零件而言,刀具进给速度和转速应适当降低,以减少切削力和热变形。
还需要注意切削深度和切削速度等参数,以确保加工质量和表面粗糙度。
6. 加工控制数控铣削加工需要精确的加工控制。
对于薄壁零件而言,需要特别注意切削力和卸刀等问题。
在加工过程中,应及时监控加工状态和切削力,以避免加工过程中的变形和划伤。
7. 加工精度检测加工完成后,需要进行加工精度的检测。
对于薄壁零件而言,主要检测加工尺寸、平行度和表面粗糙度等指标。
根据检测结果,可以进行调整和改善,以提高加工质量。
薄壁零件的数控铣削加工需要在材料选择、刀具选择、加工顺序、加工参数、加工控制和加工精度检测等方面进行精心设计和操作。
只有合理选择工艺和控制加工过程,才能确保薄壁零件的加工质量和效率。
数控车加工薄壁组合零件工艺分析与加工方案

数控车加工薄壁组合零件工艺分析与加工方案摘要:在数控车加工过程中,经常碰到一些薄壁零件的加工。
本文详细分析了薄壁零件加工的特点、防止变形的工艺方法、车刀几何角度及切削参数的选择,结合在教学实践中的实例设计出加工方案。
关键词:薄壁零件工艺分析加工方案1薄壁工件的加工特点车薄壁工件时,由于工件的刚性差,在车削过程中,可能产生以下现象。
1.1因工件壁薄,在夹压力的作用下容易产生变形。
从而影响工件的尺寸精度和形状精度。
当采用如图1所示三爪卡盘夹紧工件加工内孔时,在夹紧力的作用下,会略微变成三角形,但车孔后得到的是一个圆柱孔。
当松开卡爪,取下工件后,由于弹性恢复,外圆恢复成圆柱形,而内孔则如图2所示变成弧形三角形。
若用内径千分尺测量时,各个方向直径D相等,但已变形不是内圆柱面了,这种现象称之为等直径变形。
1.2因工件较薄,切削热会引起工件热变形,从而使工件尺寸难以控制。
对于线膨胀系数较大的金属薄壁工件,如在一次安装中连续完成半精车和精车,由切削热引起工件的热变形,会对其尺寸精度产生极大影响,有时甚至会使工件卡死在夹具上。
1.3在切削力(特别是径向切削力)的作用下,容易产生振动和变形,影响工件的尺寸精度,形状、位置精度和表面粗糙度。
2减少和防止薄壁件加工变形的方法2.1工件分粗,精车阶段粗车时,由于切削余量较大,夹紧力稍大些,变形也相应大些;精车时,夹紧力可稍小些,一方面夹紧变形小,另一方面精车时还可以消除粗车时因切削力过大而产生的变形。
2.2合理选用刀具的几何参数精车薄壁工件时,刀柄的刚度要求高,车刀的修光刃不易过长(一般取0.2~0.3mm),刃口要锋利。
2.3增加装夹接触面如图3所示采用开缝套筒或一些特制的软卡爪。
使接触面增大,让夹紧力均布在工件上,从而使工件夹紧时不易产生变形。
2.4应采用轴向夹紧夹具车薄壁工件时,尽量不使用径向夹紧,而优先选用如图4所示轴向夹紧方法。
工件靠轴向夹紧套(螺纹套)的端面实现轴向夹紧,由于夹紧力F沿工件轴向分布,而工件轴向刚度大,不易产生夹紧变形。
数控加工中心薄壁零件加工方法
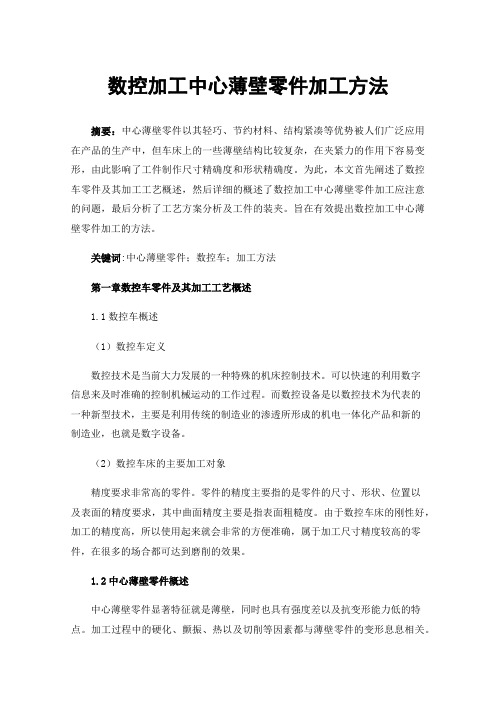
数控加工中心薄壁零件加工方法摘要:中心薄壁零件以其轻巧、节约材料、结构紧凑等优势被人们广泛应用在产品的生产中,但车床上的一些薄壁结构比较复杂,在夹紧力的作用下容易变形,由此影响了工件制作尺寸精确度和形状精确度。
为此,本文首先阐述了数控车零件及其加工工艺概述,然后详细的概述了数控加工中心薄壁零件加工应注意的问题,最后分析了工艺方案分析及工件的装夹。
旨在有效提出数控加工中心薄壁零件加工的方法。
关键词:中心薄壁零件;数控车;加工方法第一章数控车零件及其加工工艺概述1.1数控车概述(1)数控车定义数控技术是当前大力发展的一种特殊的机床控制技术。
可以快速的利用数字信息来及时准确的控制机械运动的工作过程。
而数控设备是以数控技术为代表的一种新型技术,主要是利用传统的制造业的渗透所形成的机电一体化产品和新的制造业,也就是数字设备。
(2)数控车床的主要加工对象精度要求非常高的零件。
零件的精度主要指的是零件的尺寸、形状、位置以及表面的精度要求,其中曲面精度主要是指表面粗糙度。
由于数控车床的刚性好,加工的精度高,所以使用起来就会非常的方便准确,属于加工尺寸精度较高的零件,在很多的场合都可达到磨削的效果。
1.2中心薄壁零件概述中心薄壁零件显著特征就是薄壁,同时也具有强度差以及抗变形能力低的特点。
加工过程中的硬化、颤振、热以及切削等因素都与薄壁零件的变形息息相关。
数控加工过程可主要分为设计与编程、加工与监控以及成品检验三个特殊的阶段。
对于薄壁零件的加工,最突出的问题是零件的变形不易得到及时的控制。
这也说明对薄壁零件的加工工艺、夹紧方法、刀具以及切割技术都有很严格的要求。
第二章数控加工中心薄壁零件加工应注意的问题2.1数控加工中心薄壁零件切削用量的选择切削的用量主要包括:切削的深度、进给的速度以及主轴的转速。
主要根据依据的原则是:最大程度的发挥数控机床的基本性能;充分的确保数控车表面得粗糙度与零件加工精度;降低生产成本,提高劳动生产率,增加经济效益。
数控车床加工薄壁零件的工艺及参数选择

数控车床加工薄壁零件的工艺及参数选择摘要:薄壁类零件本身的结构相对薄弱,加工难度较大,并且在目前数控机床操作环节,对于操作人员而言,最难的问题就是对薄壁零件的加工。
因此在设计过程中采取工装夹具等来分析具体电气设备中的支护件结构,然后利用数控车床进行加工,判断影响其加工精度的相关因素,以优化设计来促进后续加工工作顺利开展。
同时,也需注重后续加工质量的保障措施,提升薄壁类零件的加工精度。
关键词:数控车床;加工薄壁零件;工艺;参数选择引言对于在车削上具有薄壁结构的某些零件,由于零件的薄壁,在夹紧力作用下容易变形,从而影响零件的尺寸精度和形状精度。
在排程中,虽然存在工件和精加工,但工件和精加工通常是分开进行的,首先执行完整的工件加工,然后在精加工之后完成工件加工。
由于切削馀量大、切削力大、变形大,在加工过程中不一定能完全消除过度切削力所造成的变形。
由于前后厚度不同,尺寸很差,很难满足工艺要求如果在编程时合理安排毛坯和精加工路径以及合理分配加工馀量,可以解决零件变形问题的一些不良刚度。
一、薄壁零件简述薄壁零件是由厚度和内径曲率比小于5%的薄板和加强筋组成的轻元件,它们使用少量材料并产生低质量的产品。
薄壁零件的结构本身相对紧凑,硬度和刚度不足,易于在生产过程中变形和修复,这影响了薄壁零件的方向,但也影响了薄壁零件的使用效果。
薄壁零件具有特殊的尺寸和形状,即使是特殊材料,最常用的薄壁加工材料也是钛合金和复合材料,它们是在不同的生产场景和场景中制造的。
从分析薄壁零件的加工和工艺角度来看,薄壁零件的最终加工效果反映了加工等级,薄壁零件通常应用于高精度领域,加工等级直接影响下一个装配产品的质量。
从车削过程的角度来看,夹具的切削量和材料以及几何参数会影响薄壁加工的质量。
二、影响薄壁零件质量的因素分析(一)切割方式的选择切割薄壁零件时,必须选择适当的切割方法以避免影响零件过程的质量。
因此,结合薄壁零件的实际要求,应选择科学的加工方法来提高零件的切削精度。
铝合金薄壁套数控车削加工分析

切 削三要 素,切削速度 低 。 、进给 量慢些 、背吃刀量 小 。 些
一
些 ,完成 其余尺寸 精度制 作。力I 时的几 点注 意事项 : f 工
工件 要加紧 , 以防车 削时打滑 和扎 刀;在车削 时使用适 当 的冷却液 ;安全文 明生产 。
关键词 : 薄壁零件 ;解 决方案 ;加 工 步骤
D I 1 .9 9 J8n1 7 —6 9 .0 . 70 0 O : 5 6 / .s. 6 1 3 62 1 2 . 2 O i 1
l 引言
薄壁零件 已日益 , 泛地应 用在各 工业 部门 ,具 有重量 轻 ,节约材料 ,结 构紧凑等特 点 。但 由于溥 壁零件 的刚性 差 ,强度 弱 ,在 加 工 中极 易 变形 ,使零 件 的 形位 误 差增
形 、重 复定位精度 与增 加壁厚 。辅助夹具加 工步骤 :① 先 加 工 5外 圆 。②用 三爪 臼定心 卡盘夹住 5外 圆 ,加工 5 5 内螺纹 :先用 中心 钻定心 保证螺纹 中心与主轴 中心 同轴 , 用 中2 麻花 钻钻通 ,之后用镗 7加 工到 内螺纹 小径值 ,以 4 J 保 证M 7 圆柱度 ,再用 丝锥攻 出M 7 内螺纹 ,用 丝锥 2 x2 2 ×2
大 , 不 易 保 证 零 件 的 加 工 质 量 。在 加 工 时 , 应 充 分 考 虑 加 工工 艺 ,保 证 加 工 精 度 。
具 ,具有较好 的刚性 ,能减 少振动变形 和防止产 生振纹 。
( )外 圆粗 、精 车刀选 用6 。机 夹刀 。 ( )螺 纹刀选用 2 O 3 机夹刀 ,刀尖角度标准 ,磨损时易于更换。 5 具体操作步骤 ( )装 夹毛坯,平端面至加工要求 ,加工 ①4外 圆留 1 5 余量 。 ( )加工M 7 螺纹,加工到规定 的尺寸 值,由于 2 2 ×2
薄壁零件数控车工加工工艺

薄壁零件数控车工加工工艺随着科学技术的进步,经济的飞速发展,在工业生产中薄壁零件的应用范围正在不断的扩大,薄壁零件具有轻重量、密结构、节约材料等优点,但也不可忽略薄壁零件刚性不够、强度比较弱的特点,使它在加工生产中容易出现切削振动、加工变形等问题,使其加工质量难以保证。
本文将对影响薄壁零件精度因素进行分析,对薄壁零件的加工工艺进行简要的探讨,旨在提高薄壁零件的加工技术,进而提高生产效率。
标签:薄壁零件;数控;加工工艺薄壁零件的高效精密的数控加工技术是当代高新技术产业的基础,是制造业在核心技术竞争力方面的代表,也是体现国家的制造技术水平先进与否的一个标志。
薄壁零件在现代工业的各个领域都有应用,如汽车制造业、军事工业等。
不可否认在薄壁零件加工中是存在一定问题,常常会出现不合格的零件,造成浪费。
所以我们有必要通过对薄壁零件加工工艺问题的分析研究,优化薄壁零件制造加工措施,进而解决薄壁零件加工中所存在的问题,保证薄壁零件的精度和质量,提高所制造加工零件的合格率。
1 薄壁零件概述薄壁零件顾名思义,其显著特点就是壁薄,同时它还存在着强度差与抗变形能力低的特点。
加工过程中的表面硬化、颤振、热力、切削等因素都关系到薄壁零件的变形与否。
数控加工的过程可分为三部分,即设计与编程、加工与监控和成品检验三阶段。
对薄壁零件加工来说,突出问题就是零件变形不易控制。
这也说明薄壁零件的加工对加工技术、装夹方式、切割刀具及切割工艺都有着极高的要求。
2 影响薄壁零件数控加工精度的因素分析薄壁零件具有轻量化的动态性能,不过保障薄壁零件的加工精度却是工业生产的一个瓶颈,薄壁零件在数控加工过程中容易变形、损坏。
想要提高薄壁零件加工的精度就需要对影响其精度的因素进行研究。
对薄壁零件数控加工过程中易出现变形,影响零件精度的因素进行分析后,得出存在以下几种主要影响因素。
2.1 热因素导致薄壁零件变形。
通常情况下,比较薄的零件加工过程中受到切削热的作用时,都会不同程度产生热变形现象,导致零件的加工精度下降以及质量不合格等。
浅谈薄壁零件数控车加工工艺分析

浅谈薄壁零件数控车加工工艺分析摘要:伴随着我国科技技术与经济水平的飞速发展,很多行业也都在此背景下发展起来。
在零件质量和加工工艺方面,社会对其有了更高的要求。
在计算机技术的不断革新下,数控技术得到了飞速的发展。
基于这一点,薄壁零件的生产与应用得到了很大的发展。
但是,目前国内外对其加工工艺的研究还不够深入,加工质量很难保证。
在此基础上,文章重点对薄壁零件数控车工加工工艺进行了研究。
关键词:薄壁零件;数控车加工;加工工艺;改进措施1.薄壁零件的概念薄壁零件主要是通过现代数控车床工艺,使零件的内壁和外壁变薄,以达到节省材料的目的。
薄壁零件由于具有良好的机械性能而被广泛应用于航空航天、军事和机械等诸多领域。
在加工薄壁零件时,对加工精度的要求越来越高,而加工时产生的变形会严重地影响产品的质量与生产效率。
所以,对于薄壁零件,必须采用比较严格的工艺,才能确保其质量及合格率。
2.薄壁零件数控车加工工艺质量的影响因素2.1刀具角度对切削量的影响实验结果表明,当机床机构及刀具几何参数一定时,切削力的大小受到切削速度、进给速度和反向进给等因素的影响。
刀具角度是影响加工质量的重要因素。
在切削时,适当增大刀具前角和后角,可有效减小切削变形、降低摩擦、弱化切削作用力,使切削变形达到最大程度。
此外,主偏角和副偏角对切削精度的影响也很大。
在切削时,副偏角对刀具轴向和径向力均有影响。
对于刚性较差的零件,主偏角应尽量接近90度,这样才能提高零件的数控加工强度和加工精度。
2.2走刀方式与路径的影响刀具的走刀方式与路径对零件的数控车加工也有很大的影响,改进刀具的走刀方式与路径,可以有效地提高零件的数控车加工精度。
通过对走刀轨迹及走刀方式的优化,可使工件质量得到明显提高。
其中,一次粗加工法和阶梯粗加工法是一种新的、高效的零件粗加工工艺。
两种方法均沿高线轨迹,并以等量的切削量为切入点。
它克服了常规刀具路径在斜向上加工时存在的缺陷。
此时,刀具沿高线X和 Z两条高线水平运动,将多余的刀具去除,保证了刀具切削过程中均匀地切削多余的金属、延长了刀具的使用寿命,提高了加工质量。
典型薄壁零件数控铣削加工工艺

典型薄壁零件数控铣削加工工艺随着我国制造业的不断发展,数控铣削加工工艺在各个行业的应用越来越广泛。
而典型薄壁零件数控铣削加工工艺则是其中的一种重要形式。
本文将对其进行详细介绍。
一、背景介绍对于薄壁零件的数控铣削加工而言,主要考虑的是工艺的合理性和制造成本的降低。
在保证精度和质量的前提下,如何减少加工时间和提高生产效率是一项难度较大的任务。
近年来,数控技术的不断提高和应用,以及材料科学的不断发展等一系列因素,使得薄壁零件的生产制造进一步实现了自动化、智能化的过程。
而典型薄壁零件数控铣削加工工艺就是在这个背景下得以快速发展的。
1.精度要求高。
由于薄壁零件往往承受比较大的载荷,因此其加工精度和质量要求较高。
为了保证产品的稳定性和安全性,数控加工设备需要保证高精度的稳定性和重复性。
2.切削力小。
薄壁零件的加工需要掌握适当的切削量和进给速度,以避免对产品造成损伤。
为此,在加工时需要注意刀具的选择和切削参数的调整,保证切削力的控制在合理范围内。
3.加工速度快。
数控加工设备的优势在于能够实现高速切削,而薄壁零件的生产制造也需要在保证精度的前提下实现高效加工,这就要求在保证质量的前提下,实现加工时间的最小化。
4.工艺简单。
典型薄壁零件数控铣削加工工艺要求采用简单、方便、快捷的工艺流程,以减少制造成本。
同时,需要采用先进的数控软件,支持多种 CAD / CAM 数据格式,实现自动化编程,提高生产效率。
三、工艺流程1.零件设计。
在设计时需要考虑到构件的结构形式、加工要求和机床的加工能力等问题,确定CAD/ CAM 软件的使用方法、切削参数、刀具选择等细节。
2.加工前准备。
包括机床设备准备、零件夹紧方式的选择、工艺文献的准备等。
3.程序编写和校验。
通过CAD/CAM 软件编写加工程序,并进行模拟和校验,确保程序的正确性和合理性。
4.机床操作。
通过数控设备进行工件的加工,需要定期检查机床设备是否正常,保证加工的精度和质量。
薄壁零件数控车工加工工艺的探讨
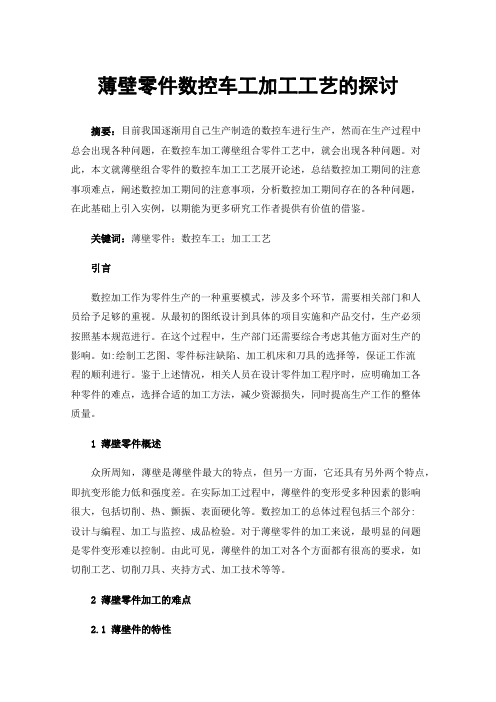
薄壁零件数控车工加工工艺的探讨摘要:目前我国逐渐用自己生产制造的数控车进行生产,然而在生产过程中总会出现各种问题,在数控车加工薄壁组合零件工艺中,就会出现各种问题。
对此,本文就薄壁组合零件的数控车加工工艺展开论述,总结数控加工期间的注意事项难点,阐述数控加工期间的注意事项,分析数控加工期间存在的各种问题,在此基础上引入实例,以期能为更多研究工作者提供有价值的借鉴。
关键词:薄壁零件;数控车工;加工工艺引言数控加工作为零件生产的一种重要模式,涉及多个环节,需要相关部门和人员给予足够的重视。
从最初的图纸设计到具体的项目实施和产品交付,生产必须按照基本规范进行。
在这个过程中,生产部门还需要综合考虑其他方面对生产的影响。
如:绘制工艺图、零件标注缺陷、加工机床和刀具的选择等,保证工作流程的顺利进行。
鉴于上述情况,相关人员在设计零件加工程序时,应明确加工各种零件的难点,选择合适的加工方法,减少资源损失,同时提高生产工作的整体质量。
1薄壁零件概述众所周知,薄壁是薄壁件最大的特点,但另一方面,它还具有另外两个特点,即抗变形能力低和强度差。
在实际加工过程中,薄壁件的变形受多种因素的影响很大,包括切削、热、颤振、表面硬化等。
数控加工的总体过程包括三个部分:设计与编程、加工与监控、成品检验。
对于薄壁零件的加工来说,最明显的问题是零件变形难以控制。
由此可见,薄壁件的加工对各个方面都有很高的要求,如切削工艺、切削刀具、夹持方式、加工技术等等。
2薄壁零件加工的难点2.1薄壁件的特性与一般零件相比,薄壁组合零件具有零件轻、省资源等特点,在各个领域均有体现。
但在实际加工时,薄壁组合零件具有不稳定、易变性等特性,而这也是加工过程应注重的问题。
从其结构来看,薄壁组合零件硬度低,易受压力、温度等因素影响而产生形变,既会影响零件整体尺寸,也会降低其在机械设备中的具体运行情况,进而造成不必要的损失。
2.2刀具的选择薄壁组合零件加工的另一个难点在于刀具的选择。
机械加工中数控车加工薄壁组合零件工艺分析
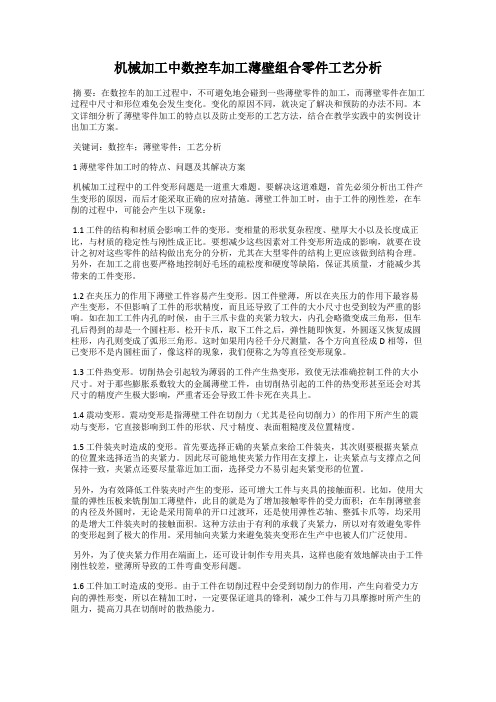
机械加工中数控车加工薄壁组合零件工艺分析摘要:在数控车的加工过程中,不可避免地会碰到一些薄壁零件的加工,而薄壁零件在加工过程中尺寸和形位难免会发生变化。
变化的原因不同,就决定了解决和预防的办法不同。
本文详细分析了薄壁零件加工的特点以及防止变形的工艺方法,结合在教学实践中的实例设计出加工方案。
关键词:数控车;薄壁零件;工艺分析1 薄壁零件加工时的特点、问题及其解决方案机械加工过程中的工件变形问题是一道重大难题。
要解决这道难题,首先必须分析出工件产生变形的原因,而后才能采取正确的应对措施。
薄壁工件加工时,由于工件的刚性差,在车削的过程中,可能会产生以下现象:1.1 工件的结构和材质会影响工件的变形。
变相量的形状复杂程度、壁厚大小以及长度成正比,与材质的稳定性与刚性成正比。
要想减少这些因素对工件变形所造成的影响,就要在设计之初对这些零件的结构做出充分的分析,尤其在大型零件的结构上更应该做到结构合理。
另外,在加工之前也要严格地控制好毛坯的疏松度和硬度等缺陷,保证其质量,才能减少其带来的工件变形。
1.2 在夹压力的作用下薄壁工件容易产生变形。
因工件壁薄,所以在夹压力的作用下最容易产生变形,不但影响了工件的形状精度,而且还导致了工件的大小尺寸也受到较为严重的影响。
如在加工工件内孔的时候,由于三爪卡盘的夹紧力较大,内孔会略微变成三角形,但车孔后得到的却是一个圆柱形。
松开卡爪,取下工件之后,弹性随即恢复,外圆逐又恢复成圆柱形,内孔则变成了弧形三角形。
这时如果用内径千分尺测量,各个方向直径成D相等,但已变形不是内圆柱面了,像这样的现象,我们便称之为等直径变形现象。
1.3 工件热变形。
切削热会引起较为薄弱的工件产生热变形,致使无法准确控制工件的大小尺寸。
对于那些膨胀系数较大的金属薄壁工件,由切削热引起的工件的热变形甚至还会对其尺寸的精度产生极大影响,严重者还会导致工件卡死在夹具上。
1.4 震动变形。
震动变形是指薄壁工件在切削力(尤其是径向切削力)的作用下所产生的震动与变形,它直接影响到工件的形状、尺寸精度、表面粗糙度及位置精度。
薄壁类金属零件数控加工工艺分析
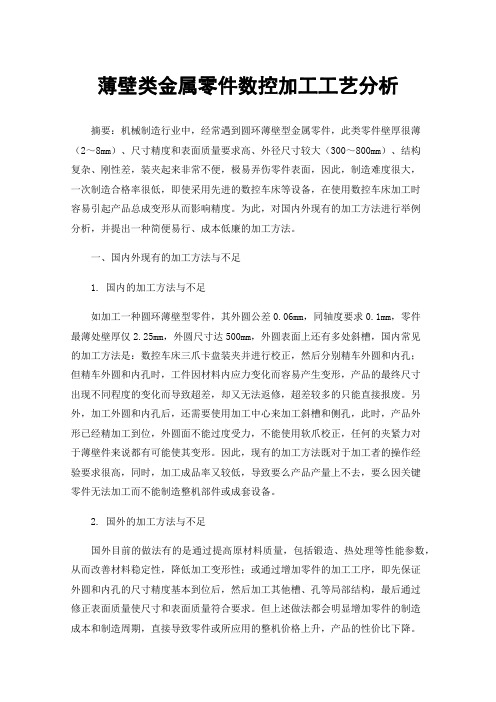
薄壁类金属零件数控加工工艺分析摘要:机械制造行业中,经常遇到圆环薄壁型金属零件,此类零件壁厚很薄(2~8mm)、尺寸精度和表面质量要求高、外径尺寸较大(300~800mm)、结构复杂、刚性差,装夹起来非常不便,极易弄伤零件表面,因此,制造难度很大,一次制造合格率很低,即使采用先进的数控车床等设备,在使用数控车床加工时容易引起产品总成变形从而影响精度。
为此,对国内外现有的加工方法进行举例分析,并提出一种简便易行、成本低廉的加工方法。
一、国内外现有的加工方法与不足1. 国内的加工方法与不足如加工一种圆环薄壁型零件,其外圆公差0.06mm,同轴度要求0.1mm,零件最薄处壁厚仅2.25mm,外圆尺寸达500mm,外圆表面上还有多处斜槽,国内常见的加工方法是:数控车床三爪卡盘装夹并进行校正,然后分别精车外圆和内孔;但精车外圆和内孔时,工件因材料内应力变化而容易产生变形,产品的最终尺寸出现不同程度的变化而导致超差,却又无法返修,超差较多的只能直接报废。
另外,加工外圆和内孔后,还需要使用加工中心来加工斜槽和侧孔,此时,产品外形已经精加工到位,外圆面不能过度受力,不能使用软爪校正,任何的夹紧力对于薄壁件来说都有可能使其变形。
因此,现有的加工方法既对于加工者的操作经验要求很高,同时,加工成品率又较低,导致要么产品产量上不去,要么因关键零件无法加工而不能制造整机部件或成套设备。
2. 国外的加工方法与不足国外目前的做法有的是通过提高原材料质量,包括锻造、热处理等性能参数,从而改善材料稳定性,降低加工变形性;或通过增加零件的加工工序,即先保证外圆和内孔的尺寸精度基本到位后,然后加工其他槽、孔等局部结构,最后通过修正表面质量使尺寸和表面质量符合要求。
但上述做法都会明显增加零件的制造成本和制造周期,直接导致零件或所应用的整机价格上升,产品的性价比下降。
二、一种新型加工方法在经过长期的经验积累和技术攻关,在不增加其他专用加工设备的前提下,充分利用数控车床、加工中心等自动化加工装置,应用专门设计的三个工装,即可以精确加工圆环薄壁型关键金属零件。
薄壁零件加工方法和工艺分析.pdf

薄壁零件的工艺分析及加工方法单位名称:陕西长岭电子科技有限责任公司作者:安小康2017年3月 2 日薄壁零件的工艺分析及加工方法作者:安小康职业技能鉴定等级:二级单位名称:陕西长岭电子科技有限责任公司单位地址:宝鸡市渭滨区清姜璐75号2017年3月2 日目录摘要 (1)关键词 (1)1工艺方案分析 (2)1.1薄壁零件图 (2)1.2零件图分析 (2)1.3确定加工方法 (2)2工件装夹 (3)2.1定位基准选择 (3)2.2确定零件定位基准 (3)2.3装夹方式选择 (3)2.4确定装夹方式 (3)3刀具和切削用量选择 (3)4零件加工 (5)5加工注意事项 (7)5.1安全文明生产 (7)5.2刀具的选择 (7)5.3削用量的要求 (7)6影响薄壁加工因素及解决方法 (8)6.1受力变形 (8)6.2受热变形 (9)6.3振动变形 (9)总结 (10)参考文献 (11)摘要薄壁工件因为具有重量轻、节约材料、结构紧凑等特点,薄壁零件已日益广泛地应用在各工业部门。
但薄壁零件的加工是比较棘手的,原因是薄壁零件刚性差、强度弱,在加工中极容易变形,不易保证零件的加工质量。
薄壁零件的加工问题,一直是较难解决的。
薄壁件目前一般采用数控车削的方式进行加工,为此要对工件的装夹、刀具几何参数、程序的编制等工艺分析方面进行试验,合理的选择加工方法从而有效地克服了薄壁零件加工过程中出现的变形,保证加工精度。
关键词:薄壁工件工艺分析程序编制加工方法1工艺方案分析1.1薄壁零件图1.2零件图分析该零件图是薄壁套类零件由外圆、内孔、外螺纹组成。
尺寸标注完整,表面粗糙度为1.6,选用毛坯是45号钢。
毛坯尺寸Φ35mm×50mm,表面无热处理等要求。
1.3确定加工方法确定加工方法的原则是保证加工表面加工精度和表面粗糙度。
薄壁类零件应按粗、精加工工序。
薄壁件通常需要加工工件的内、外表面。
内表面的粗加工和精加工都会导致工件变形,所以应按粗精加工分序。
典型薄壁零件数控铣削加工工艺
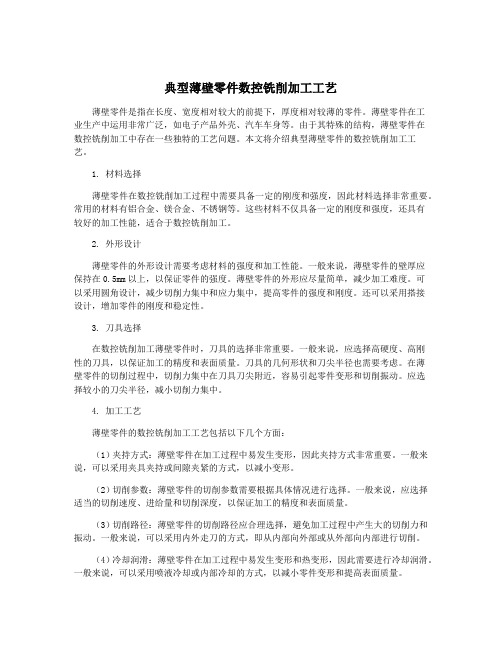
典型薄壁零件数控铣削加工工艺薄壁零件是指在长度、宽度相对较大的前提下,厚度相对较薄的零件。
薄壁零件在工业生产中运用非常广泛,如电子产品外壳、汽车车身等。
由于其特殊的结构,薄壁零件在数控铣削加工中存在一些独特的工艺问题。
本文将介绍典型薄壁零件的数控铣削加工工艺。
1. 材料选择薄壁零件在数控铣削加工过程中需要具备一定的刚度和强度,因此材料选择非常重要。
常用的材料有铝合金、镁合金、不锈钢等。
这些材料不仅具备一定的刚度和强度,还具有较好的加工性能,适合于数控铣削加工。
2. 外形设计薄壁零件的外形设计需要考虑材料的强度和加工性能。
一般来说,薄壁零件的壁厚应保持在0.5mm以上,以保证零件的强度。
薄壁零件的外形应尽量简单,减少加工难度。
可以采用圆角设计,减少切削力集中和应力集中,提高零件的强度和刚度。
还可以采用搭接设计,增加零件的刚度和稳定性。
3. 刀具选择在数控铣削加工薄壁零件时,刀具的选择非常重要。
一般来说,应选择高硬度、高刚性的刀具,以保证加工的精度和表面质量。
刀具的几何形状和刀尖半径也需要考虑。
在薄壁零件的切削过程中,切削力集中在刀具刀尖附近,容易引起零件变形和切削振动。
应选择较小的刀尖半径,减小切削力集中。
4. 加工工艺薄壁零件的数控铣削加工工艺包括以下几个方面:(1)夹持方式:薄壁零件在加工过程中易发生变形,因此夹持方式非常重要。
一般来说,可以采用夹具夹持或间隙夹紧的方式,以减小变形。
(2)切削参数:薄壁零件的切削参数需要根据具体情况进行选择。
一般来说,应选择适当的切削速度、进给量和切削深度,以保证加工的精度和表面质量。
(3)切削路径:薄壁零件的切削路径应合理选择,避免加工过程中产生大的切削力和振动。
一般来说,可以采用内外走刀的方式,即从内部向外部或从外部向内部进行切削。
(4)冷却润滑:薄壁零件在加工过程中易发生变形和热变形,因此需要进行冷却润滑。
一般来说,可以采用喷液冷却或内部冷却的方式,以减小零件变形和提高表面质量。
典型薄壁零件数控铣削加工工艺

典型薄壁零件数控铣削加工工艺典型薄壁零件加工是一种常见的数控铣削加工工艺,主要用于加工薄壁结构的工件,如航空航天零件、汽车零件、机械零件等。
本文将从加工方法、刀具选择、机床调整等方面介绍典型薄壁零件数控铣削加工的工艺。
薄壁零件加工的首要问题是如何有效地控制零件的变形。
由于薄壁结构的工件容易发生变形和振动,因此在加工过程中需要进行合理的设计和调整。
在设计时,应尽量减少工件的孔、槽和凹凸结构,以降低零件的变形概率。
在加工过程中,可以采用以下几种方法来控制变形:1. 采用合适的工艺参数。
控制切削速度、进给量和切削深度等参数,避免过大或过小,以减少切削时对工件的压力和热影响,降低变形的可能性。
2. 使用合适的工艺刀具。
对于薄壁零件的加工,建议使用铣削刀具和双刃切削刀具。
铣削刀具具有较大的切削表面,能够分散切削力,减少变形;双刃切削刀具可以减少刀具振动与切屑排除。
3. 采用合适的切削策略。
在薄壁零件的加工中,要根据工件的结构特点,合理设置切削路径和刀具轨迹,避免在工件薄弱部位过度切削,减少变形风险。
薄壁零件加工还需要注意机床调整和加工稳定性的问题。
薄壁零件的加工往往需要较高的加工精度和表面质量,因此机床的调整至关重要。
可以通过以下几个方面来提高加工稳定性和精度:1. 合理安装工件。
在安装工件时,要保证工件与机床的接触面积充分,避免产生倾斜和松动,以提高加工的稳定性和精度。
2. 选择合适的夹具。
夹具对于薄壁零件的加工至关重要,应选用刚性好、稳定性高的夹具,以保证工件在加工过程中不发生位移和变形。
3. 采用合适的切削液。
切削液可以起到冷却、润滑和防护作用,降低切削温度,减少变形风险。
要根据具体工件的材料和加工要求,选择合适的切削液。
典型薄壁零件的数控铣削加工工艺需要合理设计和调整,控制变形和振动,提高加工稳定性和精度。
通过合理选择刀具、调整工艺参数和机床,可以有效提高薄壁零件的加工质量和效率。
薄壁套类零件数控车削加工工艺分析

薄壁套类零件数控车削加工工艺分析摘要:随着加工制造业的发展,薄壁类零件的应用范围越来越广泛,技术要求越来越高。
但是在薄壁套类零件的数控车削加工中还存在很多问题,影响到了加工的效率以及零件的质量,因此需要不断改进数控车削加工工艺,提高加工质量。
关键词:薄壁套类零件数控;车削加工工艺;前言:在实际生产过程中,经常会遇到加工各种不同类型的薄壁零件,因为它具有结构小、质量轻、材料省、结构紧凑等优点,所以应用在各行各业,特别是在航空航天业应用更加广泛。
薄壁件加工时由于振动、夹紧力、切削热、内应力、车削力对变形的影响,使工件产生大幅度的形状变形,导致零件尺寸精度、形状精度和位置精度超差。
一、薄壁套类零件概述薄壁套类零件有着径向刚度差、外圆及内孔有着不规则变形导致壁厚不均匀、圆度不易控制等特点。
套类零件在机械结构中主要起支撑和导向作用,为此零件需具有较高的同轴度,端面与孔轴线或与外圆有较高的垂直度要求,除了尺寸的精度要求外还对零件的几何形状精度、表面粗糙度也要求较高。
在数控车削加工中急需解决的问题是控制零件装夹变形以及车削变形。
二、薄壁套类零件加工质量的影响因素①夹紧力对加工质量的影响:零件加工对装夹刚度有较高的要求,如果零件装夹的力度过小不仅会造成脱夹导致零件的报废,甚至会引发安全事故。
②工件材料的状态对切削力的影响:材料的状态会直接影响到切削力大小,随着材料硬度、强度增高切削力增大,同时还会涉及到加工硬化等问题,加工硬化不仅会使材料产生变形还会给材料的进一步加工带来困难。
③刀具角度对工件的影响:前角大时,切削变形量和摩擦力减小,切削力减小,表面粗糙度好;前角过大,刀具楔角减小,刀具强度降低,散热能力差,磨损速度快,刀具使用寿命降低;后角大,与工件切削表面间隙大,摩擦力小,切削力也相应的减小;后角过大,会形成刀具刃部变薄,强度不足,磨损速度快,刀具使用寿命降低。
④吃刀量与进给速度对切削力的影响:背吃刀量与切削速度对切削力的交互影响当背吃刀量为常数时,切削速度增大时,切削力变化的幅度不是很大;而当切削速度为常数时,背吃刀量增大,切削力增大较明显[3]。
- 1、下载文档前请自行甄别文档内容的完整性,平台不提供额外的编辑、内容补充、找答案等附加服务。
- 2、"仅部分预览"的文档,不可在线预览部分如存在完整性等问题,可反馈申请退款(可完整预览的文档不适用该条件!)。
- 3、如文档侵犯您的权益,请联系客服反馈,我们会尽快为您处理(人工客服工作时间:9:00-18:30)。
数控车加工薄壁组合零件工艺分析与加工方案
发表时间:2009-11-23T16:09:36.560Z 来源:《中小企业管理与科技》2009年6月上旬刊供稿作者:刘建宁周彩霞
[导读] 因工件壁薄,在夹压力的作用下容易产生变形。
从而影响工件的尺寸精度和形状精度
刘建宁周彩霞(烟台职业学院机械工程系)
摘要:在数控车加工过程中,经常碰到一些薄壁零件的加工。
本文详细分析了薄壁零件加工的特点、防止变形的工艺方法、车刀几何角度及切削参数的选择,结合在教学实践中的实例设计出加工方案。
关键词:薄壁零件工艺分析加工方案
中图分类号:TG519.1 文献标识码:B
1 薄壁工件的加工特点
车薄壁工件时,由于工件的刚性差,在车削过程中,可能产生以下现象。
1.1 因工件壁薄,在夹压力的作用下容易产生变形。
从而影响工件的尺寸精度和形状精度。
当采用如图1所示三爪卡盘夹紧工件加工内孔时,在夹紧力的作用下,会略微变成三角形,但车孔后得到的是一个圆柱孔。
当松开卡爪,取下工件后,由于弹性恢复,外圆恢复成圆柱形,而内孔则如图2所示变成弧形三角形。
若用内径千分尺测量时,各个方向直径D相等,但已变形不是内圆柱面了,这种现象称之为等直径变形。
1.2 因工件较薄,切削热会引起工件热变形,从而使工件尺寸难以控制。
对于线膨胀系数较大的金属薄壁工件,如在一次安装中连续完成半精车和精车,由切削热引起工件的热变形,会对其尺寸精度产生极大影响,有时甚至会使工件卡死在夹具上。
1.3 在切削力(特别是径向切削力)的作用下,容易产生振动和变形,影响工件的尺寸精度,形状、位置精度和表面粗糙度。
2 减少和防止薄壁件加工变形的方法
2.1 工件分粗,精车阶段粗车时,由于切削余量较大,夹紧力稍大些,变形也相应大些;精车时,夹紧力可稍小些,一方面夹紧变形小,另一方面精车时还可以消除粗车时因切削力过大而产生的变形。
2.2 合理选用刀具的几何参数精车薄壁工件时,刀柄的刚度要求高,车刀的修光刃不易过长(一般取0.2~0.3mm),刃口要锋利。
2.3 增加装夹接触面如图3所示采用开缝套筒或一些特制的软卡爪。
使接触面增大,让夹紧力均布在工件上,从而使工件夹紧时不易产生变形。
2.4 应采用轴向夹紧夹具车薄壁工件时,尽量不使用径向夹紧,而优先选用如图4所示轴向夹紧方法。
工件靠轴向夹紧套(螺纹套)的端面实现轴向夹紧,由于夹紧力F沿工件轴向分布,而工件轴向刚度大,不易产生夹紧变形。
2.5 增加工艺肋有些薄壁工件在其装夹部位特制几根工艺肋,以增强此处刚性,使夹紧力作用在工艺肋上,以减少工件的变形,加工完毕后,再去掉工艺肋。
2.6 充分浇注切削液通过充分浇注切削液,降低切削温度,减少工件热变形。
3 数控车削薄壁件参数选择
数控车床进行薄壁件加工时,具有较大的优势,对于直径较小(φ160mm以内),长度短(250mm以下),壁厚为2-2.5mm的薄壁工件,可以一次性车削成型。
但应注意不要夹持在薄壁部位,同时应选择合适的刀具角度,具体的刀具角度如下。
3.1 外圆精车刀 Kr=90°~93°,Kr’=15°α0=14°~16°,α01=15°,γ0适当增大,刀具材料为YW1硬质合金。
3.2 内孔精车刀 Kr=60°,Kr1=30°,γ0=35°α0=14°~16°,α01=6°~8°,λs=5~6°,刀具材料为YW1硬质合金。
3.3 精加工车削参数Vc=160mm/min,f=0.1mm/r,αp=0.2~0.4mm。
通过以上分析,本例的薄壁工件可采用悬臂装加的方式进行加工。
4 加工薄壁件难点分析
本例工件除了加工薄壁件的难点外,还有加工内凹半圆?外凸半圆以及T型槽的加工难点。
对于内凹半圆,采用R3的圆弧形车刀进行加工;对于外凸半圆,则采用外切槽刀进行加工;对于T形槽,则采用35°菱形刀片机夹式车刀进行加工,其主偏角取93°,副偏角取52°。
5 薄壁组合件加工方案
本例加工薄壁组合工件如图8所示,加工方案如下:
5.1 加工件3右侧内外轮廓如图5所示,注意先加工外轮廓,再加工外轮廓,保证φ58,ф52外圆尺寸,同时保证ф48,φ23内孔和内锥孔的精度要求。
5.2 掉头装夹,以φ23内孔表面作为校正面进行校正,加工件3左侧外轮廓及内锥孔,保证各项精度要求。
5.3 加工件2左侧内孔及外圆台阶如图6所示,保证φ70外圆尺寸,同时保证φ48,ф58内孔和M56×2-6H内螺纹的精度要求,用件3与之螺纹旋和,保证配合精度要求。
5.4 拆除件2,加工件1左侧内外轮廓如图7所示,先加工外轮廓再加工内轮廓,注意薄壁件的悬臂加工以及外凸半圆和内凹半圆的加工刀具及加工方式。
5.5 掉头采用一夹一顶的方式装夹件1,加工件1右侧外轮廓,保证φ58,φ48,φ23,φ16的外圆尺寸及M56×2-6g的外螺纹尺寸的精度要求。
5.6 不拆除件1,用螺纹连接方式安装件2,加工件2外轮廓,保证φ80外圆及T形槽的各项精度要求。
5.7 拆下件1,以件2的Ф80的外圆作为装夹表面,校正Ф48内轮廓后加工件2左侧内轮廓,保证Ф58内孔和M56×2-6H内螺纹的精度要求,用件3和件1与之试配,保证配合精度要求;如图8所示。
5.8 拆下工件,去毛倒棱,进行工件组合并进行自检。
本例的关键是进行合理的工艺分析,选择合理的加工方案,合理的选择刀具及切削参数,而工件的编程难度不大,这里就不再做叙述。
6 结语
本文阐述了薄壁工件的加工特点,减少和防止加工变形的方法,加工难点分析以及数控车削薄壁件参数的选择,确定了薄壁组合件加工方案。
经生产实践证明,该加工方案切实可行,能保证薄壁组合件的尺寸精度、形状精度、位置精度、表面粗糙度和装配质量都满足图
纸要求,可为类似零件和产品的机械加工提供一定的借鉴。
参考文献:
[1]刘立.数控车床编程与操作.北京:北京理工大学出版社.2006.8.
[2]职业技能鉴定教材编审委员会.车工.北京:中国劳动出版社.2004.7.
[3]穆国岩.数控加工编程与操作.北京:机械工业出版社.2008.8.。