影响连铸拉速因素
连铸工艺知识汇总高级工技师题库

河北钢铁杯职工职业技能大赛连铸工试题库(1309题)一、判断题1、钢中含磷高,会引起钢在低温时的韧性大为降低,引起“热脆”。
( )×2、冷却水喷咀的性能,不会影响铸坯质量和拉坯速度。
( )×3、事故冷却水的水量应不小于正常水量的1/5。
( )×4、适当降低过热度的浇注温度,可缩小铸坯中的柱状晶区,扩大等轴晶区。
( ) √5、所谓固相矫直是指铸坯进入矫直区域已全部凝固时进行的矫直。
( )√6、对涂料中间包要求耐热冲击性好,当从室温快速加热到1700℃时不炸裂,不剥落。
( )×7、对于大断面带液芯矫直的铸机,采用多点矫直比采用一点矫直好。
( )√8、二冷区冷却比按每吨铸坯消耗的冷却水体积衡量。
( )√9、钢水由液态变成固态的过程,必须满足一个条件,即一定的过冷度。
( ) √10、钢水在中包内的最佳停留时间为5min。
( )×11、钢液过冷度大,形核速度大于长大速度。
( )√12、连铸结晶器冷却水质要求比二冷水要求高。
( )√13、连铸坯按铸坯断面分类有方坯、板坯、园坯、异型坯。
( )√14、连铸坯常见的表面缺陷有鼓肚、扭曲、菱变。
( )×15、随着保护渣中碳含量的增加,保护渣的熔化速度加快。
( )×16、随着冶炼过程的进行,脱碳速度将越来越快。
( )×17、结晶器的铜板镀Ni是为了提高导热性能。
( )×18、铸坯振痕深度与结晶器振动负滑脱时间有关,负滑脱时间越短,振痕深度越深。
( )19、结晶器冷却水较二冷区冷却水压力低。
( )×20、沸腾钢比镇静钢的表面质量好,但成材率低。
( )×成份的含量不同。
( ) 21、刚玉、高铝和粘土质耐火材料的区别在于SiO2×22、钢包保护套管的作用是改善劳动条件。
( )×23、保护渣水份不会对保护渣的质量造成影响。
上引连铸的工作原理及影响因素分析

17电工材料2010N o.1上引连铸的工作原理及影响因素分析覃向忠,李镇鹏,刘辉(桂林金格电工电子材料科技有限公司,广西桂林541004)摘要:对用于生产金属或合金线材的上引连铸装置的工作原理及主要因素进行了分析,指出了影响上引连铸的关键因素,以期对实际生产有所帮助。
关键词:上引连铸;合金熔液;结晶器;固-液交界面中图分类号:TM205.1文献标志码:A文章编号:1671-8887(2010)01-0017-03Anal y sis of the Continuous U p Castin g Princi p leand the Aff ectin g FactorQ I N Xi a n g-z h o n g,L I Z he n-p e n g,L I U Hui(Guili n Coni nst Elect rical&Elect r onic Ma t eri al Co.L t d.,Guili n541004,Chi na) Abstract:The p ri nci p le of t he c o nti n uous u p casti n g e q ui p me nt w hic h ma n uf act ur es wi r ef r o m met al or all o y melt is i nt r oduce d.The mai n f act or t hat ma y i nf l ue nce t he q ualit y oft he c o nti n uous u p cast e d wi r e is a nal y ze d.K e y words:c o nti n uous u p casti n g;s ol uti o n of all o y;c o nti n uous casti n g m ol d;i nt e rf ace of t hes oli d a n d li q ui d1引言上引连铸是一种连续铸造的方法,其原理是利用金属熔液冷却结晶的机理,从熔融的金属或合金熔液中缓慢连续地抽出具有一定形状的固态金属线材、板材等。
连铸工考试试题题库
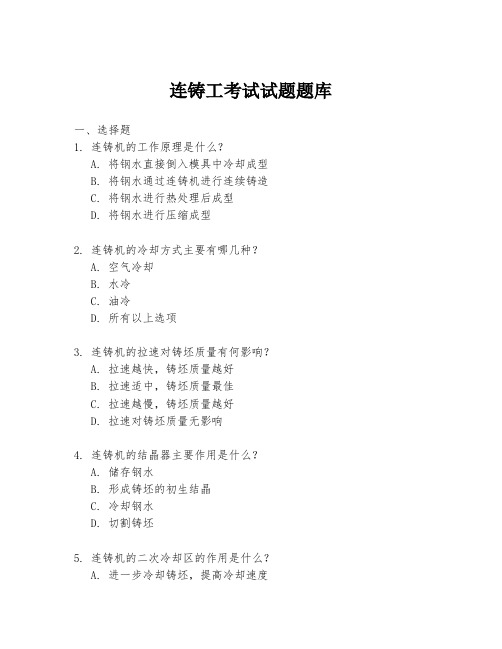
连铸工考试试题题库一、选择题1. 连铸机的工作原理是什么?A. 将钢水直接倒入模具中冷却成型B. 将钢水通过连铸机进行连续铸造C. 将钢水进行热处理后成型D. 将钢水进行压缩成型2. 连铸机的冷却方式主要有哪几种?A. 空气冷却B. 水冷C. 油冷D. 所有以上选项3. 连铸机的拉速对铸坯质量有何影响?A. 拉速越快,铸坯质量越好B. 拉速适中,铸坯质量最佳C. 拉速越慢,铸坯质量越好D. 拉速对铸坯质量无影响4. 连铸机的结晶器主要作用是什么?A. 储存钢水B. 形成铸坯的初生结晶C. 冷却钢水D. 切割铸坯5. 连铸机的二次冷却区的作用是什么?A. 进一步冷却铸坯,提高冷却速度B. 增加铸坯的厚度C. 减少铸坯的尺寸D. 储存铸坯二、判断题6. 连铸机的结晶器内壁通常采用铜材料。
()7. 连铸机的拉速越快,铸坯的内部缺陷越少。
()8. 连铸机的二次冷却区可以采用空气冷却。
()9. 连铸机的结晶器和二次冷却区的冷却方式是相同的。
()10. 连铸机的拉速是影响铸坯质量的关键因素之一。
()三、简答题11. 简述连铸机的连铸工艺流程。
12. 连铸机在生产过程中,如何保证铸坯的质量?13. 连铸机的结晶器和二次冷却区在连铸过程中各自承担什么角色?14. 连铸机的拉速对铸坯的内部结构和表面质量有何影响?15. 连铸机在生产过程中,如何进行故障排除和维护?四、计算题16. 假设连铸机的拉速为1.2米/分钟,铸坯的厚度为200毫米,宽度为1000毫米,请计算在连续工作1小时后,铸坯的总长度是多少?五、案例分析题17. 某连铸机在生产过程中发现铸坯表面出现裂纹,分析可能的原因,并提出相应的解决方案。
六、论述题18. 论述连铸机在钢铁工业中的重要性及其在现代钢铁生产中的应用。
七、结束语通过本次考试,考生应能够全面了解连铸机的工作原理、工艺流程、操作要点以及故障排除和维护知识,为今后在连铸机操作和维护工作中打下坚实的基础。
晋连铸高级工培训考试试题

晋连铸高级工培训考试试题一、单选题1.常用结晶器母材有()。
A.Ni-CoB.Ni-FeC.Cr-Zr-Cu(正确答案)D.Ni-Cr2.大容量中间包设置挡墙和挡坝的目的是()。
A.保证钢水温度B.促进夹杂物的上浮(正确答案)C.减少耐火材料的侵蚀D.减少钢流冲击3.连铸机冶金长度是指()。
A.根据最大拉速确定的液相穴深度(正确答案)B.根据最小拉速确定的液相穴深度C.根据结晶器内钢水液位确定的液相穴深度D.根据最大二冷水量确定的液相穴深度4.某厂按正弦方式振动的结晶器,其振幅A=10mm,振动频率F=70次/分,拉速V=1米/分时的负滑脱率是()%。
A.30B.40(正确答案)C.50D.605.某厂有一台三机三流连铸机,铸坯断面120×120mm2,平均拉速2m/min。
所浇普碳钢密度为7.6t/m,求该连铸机的小时产量是()t。
A.38.5B.39.4(正确答案)C.40.1D.42.76.确定结晶器长度的依据是( C )。
铸坯的最小断面尺寸 B.铸坯的切割长度 C.铸坯出结晶器下口时最小坯壳厚度D.铸坯出结晶器下口时所需时间(正确答案)7()不是由于浇铸温度低产生的后果。
A.钢水发粘B.夹杂不易上浮C.出结晶器坯壳薄(正确答案)D.结晶器钢水凝壳8.表示液态铁碳合金在冷却时开始结晶的温度是()。
A.固相线B.液相线(正确答案)C.磁性转变线D.温度线9.对于钢水流动性的表述,错误的是()。
A.碳含量越低,流动性则越差B.含有钛、钒、铝及稀土元素等成分时、钢液流动性变差C.夹杂物含量高时,流动性差D.钢液温度高时,流动性差(正确答案)10.多级结晶器在结晶器下口安装足辊,结晶器以下的辊子组称为()。
A.扇形段B.二冷区C.二冷零段(正确答案)D.二冷前半段11.关闭烘烤器时应()。
A.先关闭空气,再关燃气阀(正确答案)B.先关闭燃气阀,再关空气C.同时关闭空气和煤气阀D.关闭顺序无影响12.钢水温度过高,会加剧滑动水口砖的侵蚀,导致控制失灵,造成结晶器()事故。
连铸工教程1

第一章概况1.连铸机的机型经历了由立式、立弯式、直结晶器弧形、弧形、椭圆形到水平式的发展过程。
其铸机的高度由高到低。
2.连铸机按浇注铸坯断面分类有方坯连铸机、板坯连铸机、圆坯连铸机、异型坯连铸机、方、板坯兼用连铸机。
3.目前连续铸钢车间主要布置形式有两种:连铸机的中心线与厂房柱列线相垂直者为横向布置,连铸机中心线与厂房柱列相平行者为纵向布置。
4.一台连铸机具有独立传动系统的机组数目,称为连铸机的机数。
5.一台连铸机能同时浇注的铸坯根数称为连铸机的流数。
6.影响铸机拉速因素有钢种、断面、钢水温度等。
7.弧形连铸机的铸机半径与铸坯厚度有关。
8.立弯式连铸机比弧形连铸机,结晶器内夹杂易上浮。
9.连铸机的机型对铸坯内夹杂物的数量和分布有着重要影响。
10.对铸机而言,热装热送技术的关键是生产无缺陷_铸坯。
11.连铸坯按铸坯断面分类有方坯、板坯、园坯、异型坯。
12.目前,连铸只能浇镇静钢。
13.连续铸钢的三大工艺制度是温度制度,拉速制度,冷却制度。
14.高效连铸的含意包括高质量、高拉速、高作业率和高连浇率等四个方面的内容。
15.我国连铸技术的发展,总体而言,经历了达产、全连铸及当前正在进行的__铸机高效化等几个阶段。
16.近终形连铸机指的是:出铸机连铸坯接近成品。
17.为发挥冶炼设备的能力,保证连铸与炼钢匹配,连铸的能力应大于炼钢的能力10%~20%。
18.弧形连铸机的参数有:铸坯断面尺寸、拉坯速度、圆弧半径、液相深度、铸机流数。
19.直径是450mm的圆坯的断面尺寸表示方法是φ450 mm。
第二章冷却、传热1.钢液的凝固温度随着钢的成分而发生变化,溶于钢中的元素都具有降低钢液凝固点的作用。
2.钢水温度过高,气体在钢中的溶解度就过大,对钢质危害的影响也愈大。
3.连铸机拉速提高,铸坯液芯长度增加,引起铸坯出结晶后坯壳厚度变薄,二次冷却段的铸坯易产生鼓肚变形 ,矫直时由于铸坯仍有液芯而产生内裂等。
4.控制钢水温度的出发点,首先尽可能减少钢包过程温降 ,以降低出钢温度;其次尽可能稳定炼钢操作,提高出钢温度的命中率,避免高温出钢;第三是加强生产调度和钢包周转。
拉速计算公式以及与水口直径的关系

拉 速 计 算拉坯速度(简称拉速)是以连铸机每一流每分钟拉出铸坯长度(m )来表示。
拉速愈大,铸机的生产能力愈大,但它有一定的限度,因为钢水的凝固速度限制了铸坯出结晶器时的坯壳厚度,拉速愈高,坯壳愈薄,易产生过大变形甚至漏钢。
同时又会造成铸坯内部的疏松和缩孔,使质量变坏。
在一定的工艺条件下,为了得到很好的经济效益,在寻求最佳拉速时,必须满足两个基本要求:一是铸坯出结晶器下口时具有一定的坯壳厚度,以防止过大变形和拉漏;二是铸坯内、外部质量良好。
一、理论拉速实际上,连铸机的最大拉速取决于铸坯出结晶器时不致于发生变形或拉漏所需要的最小坯壳厚度。
根据这个原则,确定拉速的方法是:首先设法求得各种断面铸坯出结晶器时所需的最小坯壳厚度,以及为了获得这个厚度,铸坯在结晶器内所需停留的时间,然后由已定的结晶器长度便可求出拉速的理论值。
由凝固定律求铸坯出结晶器时的坯壳厚度δ为:结结τηδ式中 结τ---铸坯在结晶器内的停留时间,min结η---铸坯在结晶器内的凝固系数,mm/ m in ;他主要取决于结晶器的冷却条件,铸坯断面尺寸,钢液温度和性质,通常小断面铸坯结η取28~31 mm/ m in ;大断面铸坯取24~26 mm/ m in 。
根据目前的操作水平,铸坯出结晶器时所需的最小坯壳厚度如下:碳素钢:大断面为25mm 左右,小断面为10mm 左右,合金钢可略薄些。
为了获得此稳定的坯壳厚度,铸坯在结晶器内停留的时间为:结τ=δ2/结η 2由于结晶器内壁和铸坯之间存在气隙,因而铸坯并不是在结晶器的整个长度上都与结晶器接触。
设结晶器的有效接触长度为L max ,则最大拉速的理论计算公式为:V max =L max /结τ=结η2 L max /δ2结晶器的有效接触长度与结晶器的刚性、倒锥度和拉速有关。
二、工作拉速在实际生产中,为了改善铸坯质量(如内裂、偏析、表面质量等),使用的工作拉速应小于最大理论拉速,因此通常所说的连铸机拉速是指工作拉速。
连铸机工艺设计有关问题

关于连铸机工艺设计有关问题的探讨摘要:随着经济的日益发展,人民的生活水平逐渐提高,连铸机的应用也越来越广泛,关于连铸机的工艺设计问题的探讨也越来越白日化,本文就连铸机在工艺设计方面有关问题如参数的确定、主要工艺设计思想等进行讨论,为完善连铸机的工艺设计提供参考。
关键词:连铸机,工艺设计,问题,讨论前言:把高温钢水连续不断地浇铸成具有一定断面形状和一定尺寸规格铸坯的生产工艺过程叫做连续铸钢。
而完成这一过程所需的设备叫连铸成套设备。
浇钢设备、连铸机本体设备、切割区域设备、引锭杆收集及输送设备的机电液一体化构成了连续铸钢核心部位设备,习惯上称为连铸机。
近年来,随着钢铁工业的迅速发展,连铸设计理念也得到完善,但是与国际水平相平,我国的整体实力仍有所差距。
因此,努力提高连铸工艺设计水平有着重大意义。
正文:1.连铸机工艺设计的意义随着现代工业对特殊钢、高质量钢的需求不断扩大,以及连续铸钢技术的迅速发展,对连铸工艺过程也有了更高的要求。
连续铸钢工艺从原料到成品的过程中起着关键性作用。
连铸工艺的优与劣直接影响钢产品的质量、性能和企业的经济效益。
且随着炼钢和轧钢技术的进展,钢铁工业结构的变化和对产品的规格、质量的新要求,这使得采用常规和铸锭—开坯工艺难以满足一些大型钢铁企业的生产和发展,为此,研究连铸的新工艺和新技术是必要的。
2.大、小方坯的特点通常,把边长220 mm(含圆坯、矩形坯)的方坯连铸机叫做大方坯连铸机。
大方坯连铸机浇注的主要钢种为中、高碳钢、合金钢等,用于轧制重轨、硬线、无缝钢管、大中型h型钢、棒材、锻材等。
大方坯连铸机钢种特殊且断面较大,在浇注过程中易出现表面纵、横裂纹、星状裂纹、角部凹陷、表面和皮下大型夹杂物和内部缩孔、白亮带、中心疏松、中心偏析和内部裂纹等缺陷,各大钢铁设计公司在大方坯连铸生产操作技术、生产组织、装备开发上作出了很多科研创新工作,使大方坯连铸技术得到了迅速发展。
而小方坯的铸坯断面小,热熔量比较小。
连铸工艺讲义

1.1.4铸坯凝固组织的控制
1.2.2过热度的ΔT确定
中间包内钢水的过热度ΔT取决于钢种、铸坯断面及浇注条 件等因素。如钢中含碳低,铸坯断面小、过热度应大些;钢中 碳、硅、锰含量高,铸坯断面大,过热度可取低值。浇注条件 主要指钢包及中间包的热工状况,即钢水在钢包及中间包内热 量损失引起的温降。 ΔT=t出钢-Δt过程-tl 式中Δt过程是从出钢到开始浇注的过程温降,其表达式如下: Δt过程=Δt1+Δt2+Δt3+Δt4+Δt5 式中:Δt1--出钢过程中钢水的温降; Δt2--出钢后到钢包处理前钢水的温降; Δt3—钢包处理过程中钢水的温降; Δt4—处理后至钢包开浇前钢水的温降; Δt5—钢水从钢包注入中间包的温降。 钢水过程温降如下图所示:
干净,以确保最终产品的性能。
在连铸钢水准备阶段,为了尽量减少钢中非金属夹杂 物的含量,应在脱氧、挡渣出钢及炉外精炼等方面做好工 作。
四、连铸工艺控制
1.拉速的确定和控制
拉坯速度是指连铸机每一流单位时间拉出铸坯的长度 (m/min),或每一流单位时间拉出铸坯的重量(t/min),后者 也有称为浇注速度的。显然,在铸坯断面一定的情况下,提 高拉坯速度(或浇注速度)可以提高连铸机的生产能力。 拉坯速度是连铸机的重要工艺参数之一,其大小直接影 响到钢水的凝固速度及铸坯的内部质量,为了提高连铸机的 生产能力,通常要提高拉坯速度。但是,拉速过高会造成结 晶器出口处坯壳厚度不足,坯壳过薄的铸坯,不足以承受拉 坯力和钢水的静压力,以致坯壳被拉裂而产生漏钢事故。即 使未漏钢,也会造成铸坯鼓肚和裂纹等缺陷。因此,提高拉 速应以获得良好的铸坯结构和保证正常操作为前提,通常在 一定工艺条件下,拉坯速度有一最佳值。
连铸机拉速的提升和作业率的提高毕业论文
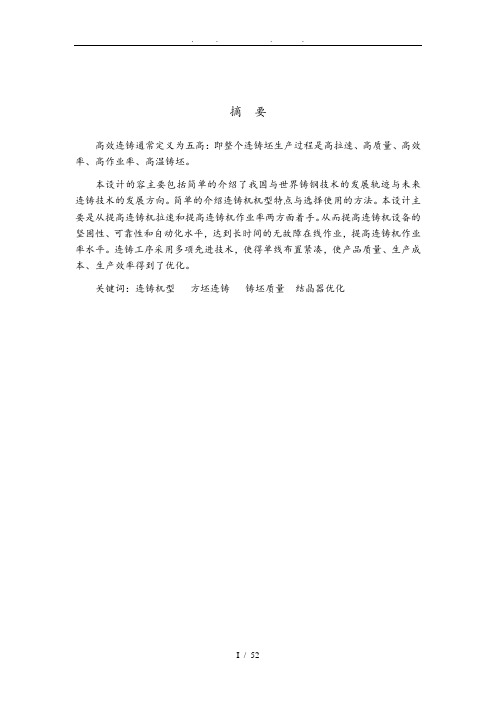
摘要高效连铸通常定义为五高:即整个连铸坯生产过程是高拉速、高质量、高效率、高作业率、高温铸坯。
本设计的容主要包括简单的介绍了我国与世界铸钢技术的发展轨迹与未来连铸技术的发展方向。
简单的介绍连铸机机型特点与选择使用的方法。
本设计主要是从提高连铸机拉速和提高连铸机作业率两方面着手。
从而提高连铸机设备的坚固性、可靠性和自动化水平,达到长时间的无故障在线作业,提高连铸机作业率水平。
连铸工序采用多项先进技术,使得单线布置紧凑,使产品质量、生产成本、生产效率得到了优化。
关键词:连铸机型方坯连铸铸坯质量结晶器优化AbstractEfficient continuous casting is usually defined as five high : that the entire billet production process is high speed 、high quality 、 high efficiency、high operating rates. High temperature slab.The design covers the brief introduction to China and the world steel technology development path and future direction of continuous casting technology. Brief characteristics of continuous casting machine models and select the method used. This design is mainly to increase speed and improve the continuous casting machine continuous casting machine of two aspectsContinuous casting machine equipment to enhance the robustness, reliability and automation level, to achieve long trouble-free online operations and increase the rate of horizontal continuous casting machine operation. Continuous casting process uses a combination of advanced technology, making single compact layout, product quality, production costs, production efficiency has been optimized.Key words: continuous casting billet Slab qualityMold Optimization目录摘要IABSTRACT II第一章绪论11.1连续铸钢技术简介11.2世界连铸技术的发展11.3连续铸钢的优越性71.3.1传统连铸进入工业成熟期的技术发展71.3.2连续铸钢技术的最新发展与未来81.4我国铸钢技术的开发与应用12第二章连铸机的机型和特征142.1连铸机的机型和特点142.2连铸机的结构特征162.3连铸机机型的选择17第三章总体设计183.1总体方案的确立183.2弧形连铸机总体设计计算与确定183.2.1铸坯断面193.2.2冶金长度(液心长度)203.2.3拉坯速度233.2.4连铸机生产能力的计算263.2.5连铸机生产能力的计算273.2.6校核铸坯是否完全凝固283.2.7带液一点矫直的可能性293.2.8连铸机流数的计算30第四章振动装置设计与计算314.1结晶器的振动参数314.2振动机构的驱动功率(P)334.2.1振动总负荷334.2.2动负荷334.2.3驱动功率P的计算34第五章 PROENGINEER软件简介34PROE的简介:34第六章结论41参考文献43附录45致48第一章绪论1.1 连续铸钢技术简介连续铸钢是一项把钢水直接浇铸成形的节能新工艺,它具有节省工序、缩短流程,提高金属收得率,降低能量消耗,生产过程机械化和自动化程度高,钢种扩大,产品质量高等许多传统模铸技术不可比拟的优点。
连铸坯质量控制
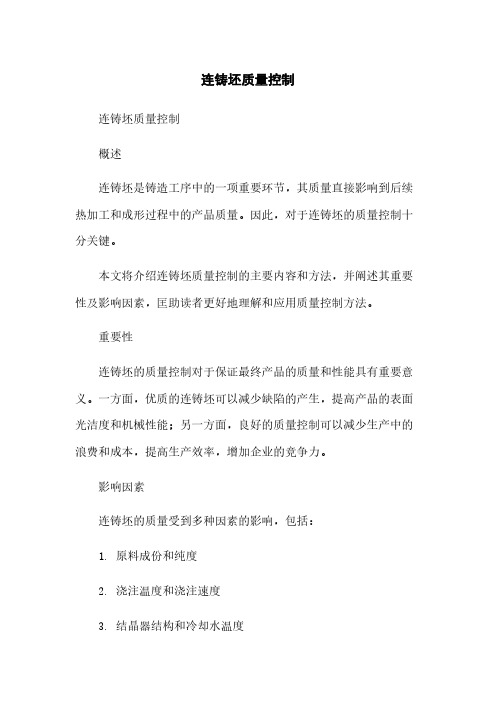
连铸坯质量控制连铸坯质量控制概述连铸坯是铸造工序中的一项重要环节,其质量直接影响到后续热加工和成形过程中的产品质量。
因此,对于连铸坯的质量控制十分关键。
本文将介绍连铸坯质量控制的主要内容和方法,并阐述其重要性及影响因素,匡助读者更好地理解和应用质量控制方法。
重要性连铸坯的质量控制对于保证最终产品的质量和性能具有重要意义。
一方面,优质的连铸坯可以减少缺陷的产生,提高产品的表面光洁度和机械性能;另一方面,良好的质量控制可以减少生产中的浪费和成本,提高生产效率,增加企业的竞争力。
影响因素连铸坯的质量受到多种因素的影响,包括:1. 原料成份和纯度2. 浇注温度和浇注速度3. 结晶器结构和冷却水温度4. 结晶器护盖的材质和形状5. 连铸速度和拉速6. 过度超熔度和段距这些因素的合理控制和调整,可以有效地提高连铸坯的质量。
质量控制方法质量控制步骤连铸坯质量控制主要包括以下几个步骤:1. 原料质量检验:对原料的成份、纯度及其它关键指标进行检验,确保原料的质量符合要求。
2. 浇注质量控制:合理控制浇注温度和速度,以避免过热或者过冷引起的坯体缺陷。
3. 结晶器质量控制:结晶器的结构和冷却水温度对坯体的结晶质量有直接影响,因此需加强结晶器的质量控制。
4. 连铸速度和拉速控制:坯体的连铸速度和拉速会影响坯体的晶粒细化程度和坯体的机械性能,需要进行合理的控制。
5. 坯体表面质量控制:通过加强护盖材料和形状的选取,合理调整过度超熔度和段距,以提高坯体表面的光洁度。
质量控制指标连铸坯的质量控制需要依据具体产品的要求和标准来制定相应的指标。
普通来说,常见的质量控制指标包括:1. 外观质量:包括表面光洁度、无裂纹、无疤痕等;2. 坯体几何尺寸:包括宽度、厚度、长度等;3. 结晶质量:包括坯体的晶粒细化程度、晶界清晰度等;4. 坯体力学性能:包括抗拉强度、屈服强度、延伸率等;以上指标应根据产品要求,通过实验和测试方法进行监控和评估。
连铸题库1 冶金特有连铸工复习资料及参考答案

冶金特有连铸工复习资料及参考答案一、判断题1.>夹杂物尺寸小于50μm时称为显微夹杂。
( )答案:√2.>N、H、O、S、P都是钢的有害元素。
( )答案:×3.>一台连铸机称为一机。
( )答案:×4.>同样条件下,冷却强度越大,拉坯速度越快。
( )答案:√5.>提高中间包连浇炉数是提高铸机台时产量的唯一途径。
( )答案:×6.>连铸机的冶金长度越长,允许的拉坯速度值就越大。
( )答案:√7.>连铸的主要优点是节能,生产率高,金属浪费小。
( )答案:√8.>立弯式铸机与立式铸机相比,机身高度降低,可以节省投资。
( ) 答案:√9.>立式铸机是增加铸机生产能力极为有效的途径。
( )答案:√10.>弧形连铸机的高度主要取决于所浇铸坯的大小。
( )答案:×11.>更换中间包和更换大包的操作可同时进行。
( )答案:×12.>对于弧形铸机,必须在切割前矫直。
( )答案:√13.>连铸对钢水温度的要求是高温、稳定、均匀。
( )14.>最新型的结晶器铜板是渗透厚度约1mm~2mm的渗透层,寿命比镀层长一倍。
( )答案:√15.>纵裂纹是来源于结晶器弯月面区初生坯壳厚度的不均匀性。
( )答案:√16.>自动脱引锭不掉,应通知中包工降拉速。
( )答案:√17.>铸坯内部质量与冷却强度有关。
( )答案:√18.>铸坯内部缺陷,主要决定于在二次冷却区铸坯冷却过程和铸坯支撑系统合理的二次冷却水分布,支撑辊的对中,防止铸坯鼓肚等是提高铸坯内部质量的前提。
( ) 答案:√19.>铸坯裂纹与钢水成份有关。
( )答案:√20.>铸坯不能带液芯矫直。
( )答案:×21.>中心偏析是铸坯中心钢液在凝固过程中得不到钢水补充而造成的。
连铸坯产生质量问题的原因
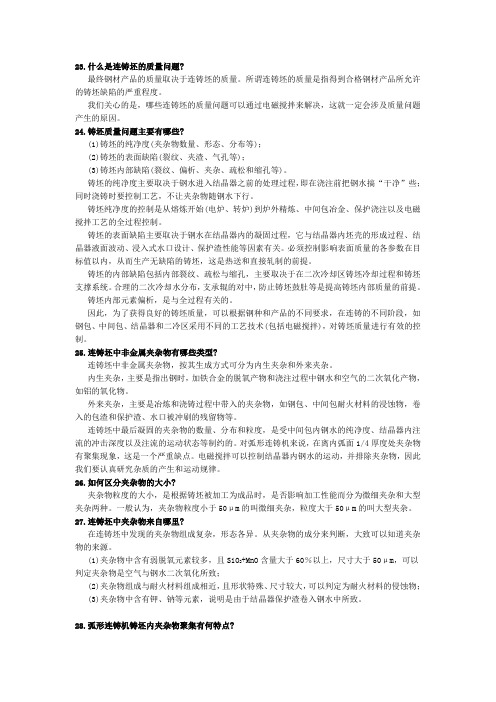
23.什么是连铸坯的质量问题?最终钢材产品的质量取决于连铸坯的质量。
所谓连铸坯的质量是指得到合格钢材产品所允许的铸坯缺陷的严重程度。
我们关心的是,哪些连铸坯的质量问题可以通过电磁搅拌来解决,这就一定会涉及质量问题产生的原因。
24.铸坯质量问题主要有哪些?(1)铸坯的纯净度(夹杂物数量、形态、分布等);(2)铸坯的表面缺陷(裂纹、夹渣、气孔等);(3)铸坯内部缺陷(裂纹、偏析、夹杂、疏松和缩孔等)。
铸坯的纯净度主要取决于钢水进入结晶器之前的处理过程,即在浇注前把钢水搞“干净”些;同时浇铸时要控制工艺,不让夹杂物随钢水下行。
铸坯纯净度的控制是从熔炼开始(电炉、转炉)到炉外精炼、中间包冶金、保护浇注以及电磁搅拌工艺的全过程控制。
铸坯的表面缺陷主要取决于钢水在结晶器内的凝固过程,它与结晶器内坯壳的形成过程、结晶器液面波动、浸入式水口设计、保护渣性能等因素有关。
必须控制影响表面质量的各参数在目标值以内,从而生产无缺陷的铸坯,这是热送和直接轧制的前提。
铸坯的内部缺陷包括内部裂纹、疏松与缩孔,主要取决于在二次冷却区铸坯冷却过程和铸坯支撑系统。
合理的二次冷却水分布,支承辊的对中,防止铸坯鼓肚等是提高铸坯内部质量的前提。
铸坯内部元素偏析,是与全过程有关的。
因此,为了获得良好的铸坯质量,可以根据钢种和产品的不同要求,在连铸的不同阶段,如钢包、中间包、结晶器和二冷区采用不同的工艺技术(包括电磁搅拌),对铸坯质量进行有效的控制。
25.连铸坯中非金属夹杂物有哪些类型?连铸坯中非金属夹杂物,按其生成方式可分为内生夹杂和外来夹杂。
内生夹杂,主要是指出钢时,加铁合金的脱氧产物和浇注过程中钢水和空气的二次氧化产物,如铝的氧化物。
外来夹杂,主要是冶炼和浇铸过程中带入的夹杂物,如钢包、中间包耐火材料的浸蚀物,卷入的包渣和保护渣、水口被冲刷的残留物等。
连铸坯中最后凝固的夹杂物的数量、分布和粒度,是受中间包内钢水的纯净度、结晶器内注流的冲击深度以及注流的运动状态等制约的。
连铸工艺、设备--09连铸坯质量控制
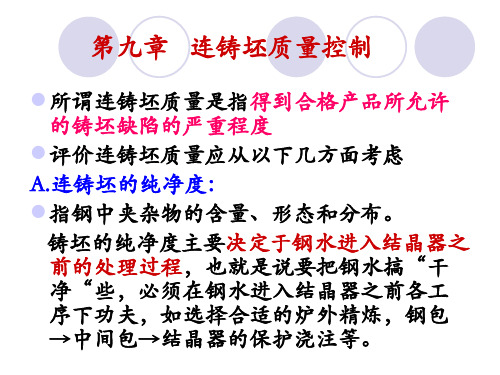
液相穴内夹杂物上浮示意图: a—带垂直段立弯式连铸机; b—弧形连铸机
B.连铸操作对铸坯中夹杂物的影响
连铸操作有正常浇注和非正常浇注两种情况。
在正常浇注下,浇注过程比较稳定,铸坯中 夹杂物多少主要由钢液的纯净度决定。
B.连铸坯的表面质量:
指连铸坯表面是否存在裂纹、夹渣及皮下 气泡等缺陷。
连铸坯的表面缺陷主要决定于钢水在结晶 器的凝固过程。它是与结晶器内坯壳的形 成、结晶器振动、保护渣性能、浸入式水 口设计及钢液面稳定性等因素有关的,必 须严格控制影响表面质量的各参数在合理 的目标值以内,以生产无缺陷的铸坯,这 是热送和直接轧制的前提。
2.钢包精炼。
根据钢种的需要选择合适的精炼处理方法,以均 匀温度、微调成分、降低氧含量、去除气体夹杂 物、改善夹杂物形态等。
3.无氧化浇注技术。
从钢包→中间包用长水口,中间包→结晶器用浸 入式水口(板坯、大方坯)或气体保护(小方 坯),中间包采用覆盖剂,结晶器用保护渣。
4.充分发挥中间包冶金净化器的作用。
C.在操作中,注温和拉速对铸坯中夹杂物也有 一定影响
当钢液温度降低时,夹杂物指数升高;随着 拉速的提高,铸坯中夹杂物有增多的趋势。
D.耐火材料质量对铸坯夹杂物的影响
注连铸过程中由于钢液和耐火材料接触, 钢液中的元素(锰和铝等)会与耐火材料中 的氧化物发生作用生成夹杂物,当其不能上 浮时就遗留在铸坯中。
2.连铸坯中夹杂物的类型和来源
类型:取决于浇注钢种和脱氧方法。在连铸 坯中较常见的夹杂物有Al2O3和以SiO2为主并 含有MnO和CaO的硅酸盐,以及以Al2O3为主 并含有SiO2、CaO 和CaS等的铝酸盐。此外还 有硫化物如FeS、MnS等。
炼钢厂连铸技师考试题库附答案(400题)

炼钢厂连铸技师考试题库附答案(400题)1.【判断题】炼钢过程中碳氧反应生产的产物是CO2。
正确答案:错2.【单项选择题】铸机生产时发现铸坯外弧有呈规律分布的凹坑,凹坑的间距为628mm,则产生凹坑处辊子直经为().A.314mmB.628mmC.200D.384正确答案:C3.【判断题】脱硫、脱磷都需高碱度、大渣量,不同的是脱硫需要高温,低氧化铁,而脱磷则相反。
正确答案:对4.【问答题】火焰切割机的主要参数包括哪些?正确答案:火焰切割机的主要参数包括气体压力、耗量、切割速度及最小本题解析:试题答案火焰切割机的主要参数包括气体压力、耗量、切割速度及最小定尺长度等。
这些参数随切割方式不同而有所变化。
5.【判断题】中间包水口堵塞有两种情况,一是冷钢堵,另一种是夹杂堵。
正确答案:对6.【填空题】拉矫机按矫直方式可分为单点矫直、()、渐近矫直、连续矫直等型式。
正确答案:多点矫直本题解析:试题答案多点矫直7.【判断题】弧形连铸机的高度主要取决于所浇铸坯的大小。
正确答案:错8.【判断题】按连铸机型不同,结晶器可分为直型和弧型两大类。
正确答案:对9.【填空题】用同位素法监测并控制结晶器液面是由()、探测器、信号处理及输出显示等部分组成。
正确答案:放射源本题解析:试题答案放射源10.【单项选择题】结晶器液面应控制在离上口()mm处.A.20-40B.60-80C.20-60D.20-100正确答案:B11.【问答题】对于250mm×1200mm连铸机断面,拉速1m/min,二冷水总量2340L/min,它的冷却比是多少?(铸坯密度为ρ=7.8t/m3,保留两位小数)正确答案:解:δ=W/(abVρ)=2340本题解析:试题答案解:δ=W/(abVρ)=2340/(0.25×1.20×1×7.8)=1000L/t答:冷却比是1000L/t。
12.【判断题】在中包修理模式中,将永久层全部更换,全新砌砖或浇铸则为全修。
连铸异常及对策
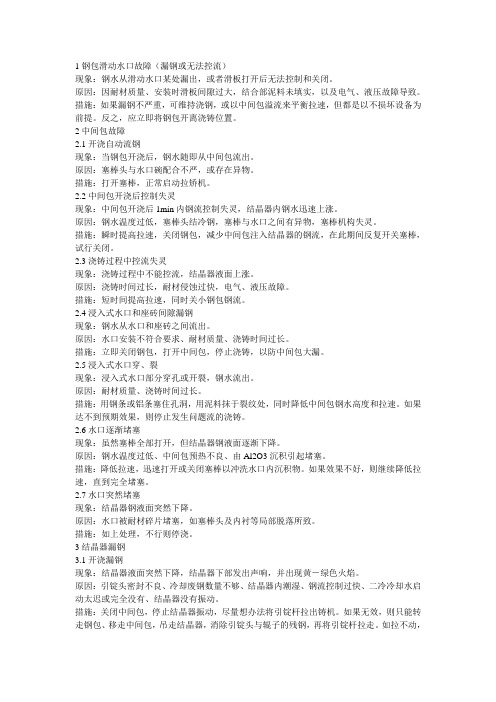
1钢包滑动水口故障(漏钢或无法控流)现象:钢水从滑动水口某处漏出,或者滑板打开后无法控制和关闭。
原因:因耐材质量、安装时滑板间隙过大,结合部泥料未填实,以及电气、液压故障导致。
措施:如果漏钢不严重,可维持浇钢,或以中间包溢流来平衡拉速,但都是以不损坏设备为前提。
反之,应立即将钢包开离浇铸位置。
2中间包故障2.1开浇自动流钢现象:当钢包开浇后,钢水随即从中间包流出。
原因:塞棒头与水口碗配合不严,或存在异物。
措施:打开塞棒,正常启动拉矫机。
2.2中间包开浇后控制失灵现象:中间包开浇后1min内钢流控制失灵,结晶器内钢水迅速上涨。
原因:钢水温度过低,塞棒头结冷钢,塞棒与水口之间有异物,塞棒机构失灵。
措施:瞬时提高拉速,关闭钢包,减少中间包注入结晶器的钢流,在此期间反复开关塞棒,试行关闭。
2.3浇铸过程中控流失灵现象:浇铸过程中不能控流,结晶器液面上涨。
原因:浇铸时间过长,耐材侵蚀过快,电气、液压故障。
措施:短时间提高拉速,同时关小钢包钢流。
2.4浸入式水口和座砖间隙漏钢现象:钢水从水口和座砖之间流出。
原因:水口安装不符合要求、耐材质量、浇铸时间过长。
措施:立即关闭钢包,打开中间包,停止浇铸,以防中间包大漏。
2.5浸入式水口穿、裂现象:浸入式水口部分穿孔或开裂,钢水流出。
原因:耐材质量、浇铸时间过长。
措施:用钢条或铝条塞住孔洞,用泥料抹于裂纹处,同时降低中间包钢水高度和拉速。
如果达不到预期效果,则停止发生问题流的浇铸。
2.6水口逐渐堵塞现象:虽然塞棒全部打开,但结晶器钢液面逐渐下降。
原因:钢水温度过低、中间包预热不良、由Al2O3沉积引起堵塞。
措施:降低拉速,迅速打开或关闭塞棒以冲洗水口内沉积物。
如果效果不好,则继续降低拉速,直到完全堵塞。
2.7水口突然堵塞现象:结晶器钢液面突然下降。
原因:水口被耐材碎片堵塞,如塞棒头及内衬等局部脱落所致。
措施:如上处理,不行则停浇。
3结晶器漏钢3.1开浇漏钢现象:结晶器液面突然下降,结晶器下部发出声响,并出现黄-绿色火焰。
连铸过程技师教程(三)
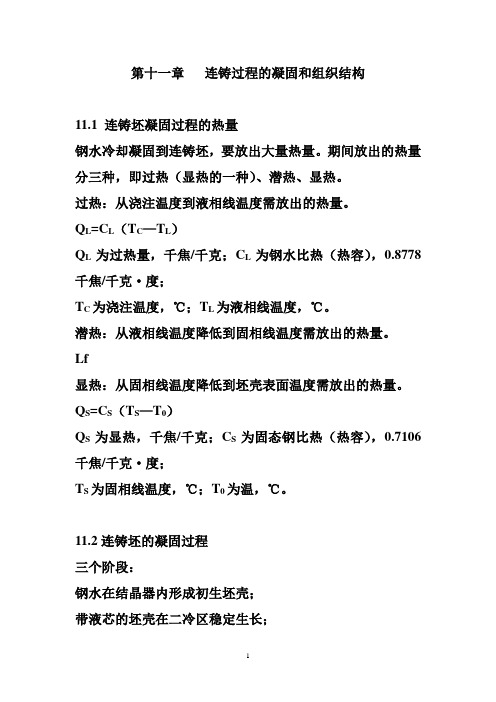
第十一章连铸过程的凝固和组织结构11.1 连铸坯凝固过程的热量钢水冷却凝固到连铸坯,要放出大量热量。
期间放出的热量分三种,即过热(显热的一种)、潜热、显热。
过热:从浇注温度到液相线温度需放出的热量。
Q L=C L(T C—T L)Q L为过热量,千焦/千克;C L为钢水比热(热容),0.8778千焦/千克·度;T C为浇注温度,℃;T L为液相线温度,℃。
潜热:从液相线温度降低到固相线温度需放出的热量。
Lf显热:从固相线温度降低到坯壳表面温度需放出的热量。
Q S=C S(T S—T0)Q S为显热,千焦/千克;C S为固态钢比热(热容),0.7106千焦/千克·度;T S为固相线温度,℃;T0为温,℃。
11.2连铸坯的凝固过程三个阶段:钢水在结晶器内形成初生坯壳;带液芯的坯壳在二冷区稳定生长;临近凝固末期的凝固。
11.3连铸坯的组织结构边部细小的等轴晶激冷层;中间树状晶区;中心等轴晶区。
第十二章连铸工艺12.1 连铸对钢水的要求总要求:四定:定量(炉产量)、定时(定时供给钢水,即周期恒定),定温度,定化学成分。
12.1 连铸对钢水成分的要求12.1.1 成分的稳定性:不仅要求同一炉(同一钢包内)钢水化学成分均匀稳定(吹氩搅拌),而且要求连浇上下炉钢水的化学成分要相对均匀,即C含量差≤0.02%、Mn含量差≤0.15%,因上下炉连浇,分坯不能严格做到一炉对一炉,在这样的成分范围内,钢材性能的均匀性才能得到保证。
12.1.2 钢水良好的可浇注性:要求水口不堵塞、不结瘤。
钢水纯洁度高、夹杂物少,气体含量低,其流动性好;在工艺规程范围内,适当提高浇注温度,其可浇性好。
钢水中Al,极易氧化成Al2O3,其熔点高,容易形成水口结瘤、断浇。
对一般结构钢控制其钢中Als含量,一般控制在0.006%以下就能防止Al2O3在水口沉积结瘤堵塞,同时做好保护浇注工作,减轻钢水的二次氧化。
对于铝镇静钢,如冷镦钢,其钢中Als高,除做好保护浇注工作外,钢水的变性处理是必不可少的,就是向钢中喂Ca 线,使钢水中Ca/Als达到一定的比值,钢中就不会形成高熔点的Al2O3夹杂,只生成3CaO·Al2O3低熔点的化合物,因此不会堵塞水口,解决了高Al含量钢水的可浇注性。
连铸工艺、设备--01连铸设备及主要工艺参数

连铸坯形状和尺寸: 小方坯: 70mm × 70mm ~200mm × 200mm 大方坯: 200mm ×200mm ~450mm × 450mm 矩形坯: 150mm × 100mm ~400mm × 630mm 板坯: 150mm × 600mm ~300mm × 2640mm 圆坯: Ф80 ~450mm
AA' A' C ' 0.5D 100 % 100 % 100 % CC ' OC R 0.5D
由于R>>D,故上式可近似写成:
ε=
0 .5 D ×100% R
ε ≤„ε‟ 则: R≥ 0.5 D (m) [ ]
式中 „ε‟:允许延伸率,它主要取决于浇铸钢种、铸 坯温度以及对铸坯表面质量的要求等。对普碳钢和 低合金钢 „ε‟=1.5 ~2.0%
×Vmax )-
2 h ] ∕π
②按铸坯矫直时允许最大延伸率计算铸机半径 原则: 矫直时内弧表面延伸率必须小于允许延伸率 值。 铸坯矫直时,内弧受拉,外弧受压,中心线 未发生变化,断面仍为平面,取C—C’段铸 坯,
铸坯矫直前后的延伸示意图: a—矫直前 b—矫直后
设外弧半径为R,铸坯厚度为D, 则内弧表面延伸率ε:
连铸机的实际作业时间=钢包开浇起至切割 完毕的时间+浇铸准备时间+正常开浇等待 的时间
五.金属收得率 η1=W1∕G1×100% η2 =W2∕W1×100% η = η1η2 = W2∕G1×100% η1—钢水收得率,%; W1—浇铸所得到的全部铸坯量,t; G1—钢水重量,t; η2— 铸坯合格率,% W2— 合格铸坯量,t; η— 金属收得率,%。
L 2
连铸机拉速控制故障的分析与处理

连铸机拉速控制故障的分析与处理作者:安伟来源:《中国科技博览》2013年第22期[摘要]分析了阳春新钢铁有限责任公司3#连铸机在浇铸过程中,拉速控制时出现的故障现象,并针对各个故障发生点进行相应实验,提出处理方案,应用于生产实际,运行可靠,效果良好。
[关键词]连铸机拉速手动控制故障现象处理方案中图分类号:TF341.6 文献标识码:TF 文章编号:1009―914X(2013)22―0341―010 引言阳春新钢铁有限责任公司在连铸机的生产中,二冷水的水量是影响铸坯质量的重要因素之一,而二冷水的水量跟随拉速的大小而变化。
换言之,连铸机的拉速控制是决定铸坯质量的关键工艺参数[1]。
本文针对连铸机拉速手动控制中出现的故障,从控制原理、故障现象与应急处理、影响因素及处理方案等方面入手,通过对各个故障发生点进行相应实验,分析实验数据,提出了有效的处理方案,采取措施,保证连铸机稳定生产。
1 控制原理连铸机的拉速设定分为手动和自动两种方式,选为手动方式时,由模拟量输出模块提供10V DC电源给现场操作箱的拉速电位计(实质为可变电阻),利用电位计分压原理将设定电位计阻值转换为0-10V DC标准电压信号,最后输入PLC模拟量输入模块作为手动设定拉速进行程序控制(原接线原理示意图见图1);当拉速控制选为自动方式时,由钢水液面检测系统根据设定液面与实际液面计算得出相应拉速,再以0-10V DC信号硬接线方式输入我方PLC,作为自动设定拉速进行程序控制。
2 故障现象与应急处理连铸机拉速控制设计范围在0~5m/min,启动速度从0.0m/min开始,之后慢慢提速,正常生产范围在2~3.8 m/min。
2012年3月,3#连铸第4流在开浇过程中拉速手动控制的情况下,出现手动设定拉速在小于0.66m/min时拉速控制失灵的现象,然而在停浇检查中并未发现异常。
在接下来的浇次中,手动拉速控制接连出现较之前更为严重的失灵状况,导致了因拉速突然跳变引起二冷水波动影响钢坯质量以及因拉速突然跳至最大值致使铸流断浇等生产事故的发生,严重影响本流次的正常开浇。
影响连铸拉速因素

4、铸坯质量对拉速的限制 (1)降低拉速可以阻止或减少铸坯内部裂纹和中心 偏析 (2)降低拉速可以防止铸坯表面产生纵裂和横裂 (3)为防止矫直裂纹,拉速应使铸坯通过矫直点时 表面温度避开钢的热脆区。
可编辑ppt
6
5、钢水过热度对拉速的限制 一般连铸规定允许最大的钢水过热度,在允许过
热度下拉速随着过热度的降低而提高。
可编辑ppt
4
式中:
Vm2
4K2 *Lm D2
Lm——结晶器至矫直点的距离,m K——综合凝固系数,m/min1/2
D——铸坯厚度,mm
Vm2——最大拉坯速度,m/min
可编辑ppt
5
3、拉坯力的限制 拉速提高,铸坯中的未凝固长度变长,各相应位
置上凝固壳厚度变薄,铸坯表面温度升高,铸坯在辊 间的鼓肚量增多。拉坯时负荷增加。超过拉拔转矩就 不能拉坯,所以限制了拉速的提高。
化的,只要选取足够的矫直长度,带液芯矫直是安全
的,也就是说矫直变形及由它产生的变形应力对拉速
的限制几乎不用考虑。
相反,对大型方坯连铸机来说,铸机有效冶金长
度是限制铸机最大拉速的主要因素。
本处所指铸机有效冶金长度为结晶器液面至火焰
切割机起切点处的有效弧线长度(通常为至切割点前
1.5m处)。
据此计算出最大允许拉速Vm2。
6、钢种对拉速的限制 就含碳量而言,拉坯速度按低碳钢、中碳钢、高
碳钢的顺序由高到低。就钢中合金含量而言,拉速按 普碳钢、优质碳素钢、合金钢顺序降低。
可编辑ppt
7
结晶器出口坯壳厚度对拉速的限制
铸坯厚度(mm)
150
铸坯宽度(mm)
150
结晶器铜管有效冷却长度(mm)
- 1、下载文档前请自行甄别文档内容的完整性,平台不提供额外的编辑、内容补充、找答案等附加服务。
- 2、"仅部分预览"的文档,不可在线预览部分如存在完整性等问题,可反馈申请退款(可完整预览的文档不适用该条件!)。
- 3、如文档侵犯您的权益,请联系客服反馈,我们会尽快为您处理(人工客服工作时间:9:00-18:30)。
6、钢种对钢中合金含量而言,拉速按 普碳钢、优质碳素钢、合金钢顺序降低。
结晶器出口坯壳厚度对拉速的限制 铸坯厚度(mm) 铸坯宽度(mm) 结晶器铜管有效冷却长度(mm) 结晶器凝固系数_km(m/min1/2) δ min结晶器出口安全坯壳厚度,mm Vm1结晶器出口最大拉坯速度,m/min
Vm 2
式中:
4 K 2 * Lm D2
Lm——结晶器至矫直点的距离,m K——综合凝固系数,m/min1/2 D——铸坯厚度,mm Vm2——最大拉坯速度,m/min
3、拉坯力的限制 拉速提高,铸坯中的未凝固长度变长,各相应位 置上凝固壳厚度变薄,铸坯表面温度升高,铸坯在辊 间的鼓肚量增多。拉坯时负荷增加。超过拉拔转矩就 不能拉坯,所以限制了拉速的提高。
4、铸坯质量对拉速的限制 (1)降低拉速可以阻止或减少铸坯内部裂纹和中心 偏析 (2)降低拉速可以防止铸坯表面产生纵裂和横裂 (3)为防止矫直裂纹,拉速应使铸坯通过矫直点时 表面温度避开钢的热脆区。
5、钢水过热度对拉速的限制 一般连铸规定允许最大的钢水过热度,在允许过 热度下拉速随着过热度的降低而提高。
结晶器的有效冷却长度
L有效 =Lm 50 750 50 700mm 0.7m
根据公式
K凝
t
出结晶器下口的坯壳厚度为
K 凝 L有效 /Vc =20 0.7 / 2.5 10.58mm
点评 :计算坯壳厚度要注意二点,一是凝固定律(即公式), 二是要用结晶器的有效冷却长度计算。 因此我们可以看出要在保证安全生产,不发生漏钢事故的前提 下,铸坯出结晶器下口的坯壳厚度对拉速的快慢起到至关重要 的作用。
例如分析漏钢事故时,需要考虑出结晶器下口 坯壳厚度的厚薄。 小方坯断面为150mmx150mm,拉坯速度Vc 2.5m / min 结晶器长度 Lm 750mm ,若浇注过程中结晶器液 面稳定在离上口50mm,结晶器凝固系数K凝 =20mm / min1/2 我们可以计算出铸坯出结晶器下口的安全坯壳厚 度 ?
影响连铸拉速的因素
1、结晶器出口坯壳厚度对拉速的限制 由于出结晶器的坯壳必须保持一定的厚度(δmin), 因此,限制了连铸机的拉速,即: 2 Lm * K m Vm1 2
min
式中:Lm——结晶器有效冷却长度,m Km——结晶器凝固系数,m/min1/2 δmin——结晶器出口安全坯壳厚度,mm Vm1——结晶器出口最大拉坯速度,m/min
2、矫直点两相区变形率及冶金长度对拉速的限制 对合金钢而言,每个矫直点的两相区最大允许矫 直变形率[ε]=0.10%,通常要求在0.1%以内。 对采用连续矫直技术来说,矫直变形率是连续变 化的,只要选取足够的矫直长度,带液芯矫直是安全 的,也就是说矫直变形及由它产生的变形应力对拉速 的限制几乎不用考虑。 相反,对大型方坯连铸机来说,铸机有效冶金长 度是限制铸机最大拉速的主要因素。 本处所指铸机有效冶金长度为结晶器液面至火焰 切割机起切点处的有效弧线长度(通常为至切割点前 1.5m处)。 据此计算出最大允许拉速Vm2。
150 150 900 22 11 3.6
矫直点两相区变形率及冶金长度对拉速的限制 铸坯厚度(mm) 铸坯宽度(mm) Lm 结晶器至矫直点的距离 m K 综合凝固系数,m/min1/2 Vm2最大拉坯速度,m/min
150 150 26 30 4.16