最新价值流程图(VSM)案例分析幻灯片
VSM价值流管理(PPT100页)名家精品课件

1.思維迷思 2.設計能力 3.計畫與
不足
管理不當
38
為何流動/快不起來?
思維迷思
-農耕心態 -追求利潤
最大化
設計能力 不足
-職能切割 -工程切割 -防坡堤設計 -分批-等待模式 -訂單/計畫的
不穩定 -轉換時間長 -物與情報
被切斷
計畫與管理 不當
-PMC中央管控 -預測式需求 -人為的不穩定 -不良多
• 傳統心理學研究: 找出不快樂的原因;給予消除
• 但,不滿足沒有不滿=/ 滿足 • 去除不滿足;並沒有得到滿足 • 因此,另外做不同的研究
46
如何才能快樂?
• 花25年對幾千人做研究 • 每人配帶call機 • 隨機響;就記下當時的作為與感受
• Flow:暢快;
順暢&爽快才能快樂
47
如何才能flow順暢?
11.開到 修理廠
消費時間:210分鐘
創造價值的時間:58分鐘
12.排隊、 描述問題
13.等候 借用車
14.委託 修理
創造價值的時間/總時間:28%
15分鍾
15.排除、 付款
20分鍾
16.駕車 回家
34
為何流動/快不起來 ?
35
價值流管理VSM
• 強調價值要快速流動
• 首先,要把沒有價值的去除: -以客戶角度定義價值 -給予價值最大化
• 搭配一個現場管理試驗,啟發思考 • 如何完成VSM的分析,不在此次課程
15
一.為何要做VSM 價值流管理?
常見老板的二大抱怨
• 交期長;又不準時 • 不要用的,一大堆; 要用的.卻沒有
17
為何要推動VSM?
1. 快速掌握企業經營系統 2. 全面瞭解企業的問題 3. 清析的瞭解瓶頸工程所在 4. 設備與人力配置研判 5. 日常管理執行與落實方向指引 6. 成為流程改善工具 7. 讓改善內容明確化與明確優先順序 8. 做為內外部的溝通工具
精益生产3VSM(价值流图及价值流分析)(ppt34页)

•机加工:87% •去毛刺:100% •弯曲:99% •检测:99% •打标记:99% 累计的正常运行时间计量标准=0.87*1*0.99*0.99 *0.99=0.844(即84.4%)。
在对所有的数据达成一致意见以后,团队成员将价 值流管理的有关信息记录在了演示图板上。
•
每天都是美好的一天,新的一天开启 。20.11.820.11.806:5306:53:3506:53:35Nov- 20
•
人生不是自发的自我发展,而是一长 串机缘 。事件 和决定 ,这些 机缘、 事件和 决定在 它们实 现的当 时是取 决于我 们的意 志的。2020年11月8日 星期日 6时53分35秒 Sunday, November 08, 2020
•
感情上的亲密,发展友谊;钱财上的 亲密, 破坏友 谊。20.11.82020年11月8日星 期日6时53分35秒20.11.8
谢谢大家!
公司的一个主要客户——考得联合公司,与其供 应基地进行了合并。考得联合公司一直在审查和 分析其供应商既能满足质量和发货方面的需求同 时又能降低成本的能力。普莱梅尔制造公司与考 得联合公司的长期协议即将到期。考得联合公司 愿意保持与普莱梅尔制造公司的业务关系,但是 要求:
• 在未来的7年中每年降低成本5%。
2、价值流图的用途
价值流图有助于全面观察和理解产品 通过价值流过程时的物料流动和信息流动, 以及其中的增值
和非增值活动,从而发现浪费和确定需要改善 的地方,更容易找出问题所在。为改善活动定 下一个蓝图和方向。同时也便于员工了解企业 的状态,提供参与改善的机会。价值流图还可 以避免只应用个别的精益工具,进行局部、孤 立的改善。通过绘制现状图,设计理想状态图 并尽快付诸实施,通过这种方法,可以全面的 改善价值流,从而为客户和供应商带来最大的 利益。
VSM价值流分析PPT课件
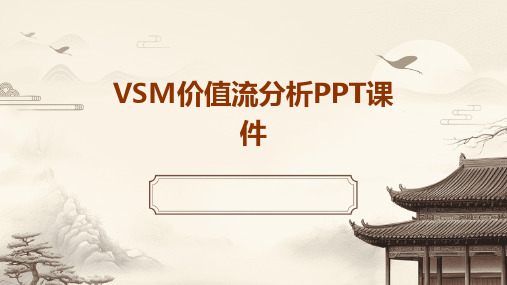
生产线平衡率计算
生产线平衡率 = 各工序时间总和 / ( 最长工序时间 * 工序数) * 100%。
提高设备利用率和员工工作效率,减 少在制品库存和等待时间,提高产品 质量和客户满意度。
生产线平衡方法
工序时间测定
通过秒表测时、预定时间标准等方法 ,准确测定各工序所需时间。
瓶颈工序识别
找出生产线上耗时最长的工序,即瓶 颈工序,进行重点改善。
02
收集数据
收集生产过程中的相关数据,如生产 周期、在制品数量、不良品率等。
01
03
绘制价值流图
使用标准的符号和工具绘制价值流图 ,包括流程图、数制定相应的改进计划, 包括优化生产布局、减少批量大小、 改进质量控制方法等。
05
04
分析浪费
在价值流图中标识出浪费的环节和原 因,如等待、运输、不良品等。
作业改善
通过作业分析、动作研究等方法,对 瓶颈工序进行作业改善,提高生产效 率。
生产线调整
根据改善后的工序时间,对生产线进 行调整,使各工序时间与节拍相等或 成整数倍关系。
改善措施制定
目标设定
原因分析
根据生产线平衡率和企业实际情况,设定 合理的改善目标。
针对生产线不平衡的原因进行深入分析, 找出根本原因。
收集生产过程中的相关 数据,通过统计分析识
别浪费现象。
员工参与法
鼓励员工积极参与,提 出生产过程中的浪费问
题和改进建议。
改善机会挖掘
01
02
03
04
消除浪费环节
针对识别出的浪费现象,制定 相应的改善措施,消除浪费环
节。
优化生产流程
通过改进生产工艺、调整设备 布局等方式,优化生产流程,
价值流图分析(PPT 59张)

—查找和发现浪费的-mail:lgddyangwenku@
价值流图分析 VSM
目的
了解价值流分析的作用
掌握绘制价值流图的步骤 加深对精益思想的理解
价值流图分析 VSM
主要内容
第一部分 价值流分析基础知识 第二部分 价值流图的绘制步骤 第三部分 价值流分析的作用 作业
采用5W1H方法
1. Who——确定谁来做 需要一位了解产品价值流而且能推进其改进的人,这个人具有领导职责 (价值流经理),由他来领导一个小组进行价值流图析工作。 2. What——确定做哪些产品的价值流图析(正确选择确定物流) 通常我们首先按照80—20原则,对影响企业最大的产品进行图析。 3. When——确定何时做(正确选择确定物流) 应在实施改进之前对价值流进行分析,以确定应首先改进哪些过程。 4. Where——确定在哪里做(如何获取真实、正确的数据信息) 在现场!只有在现场收集的数据才能真正反映价值流的状况。 5.Why—为什么做价值流图析 明确价值,消除浪费 6、 How ——进行图析
价值流图分析 VSM
价值流图基本概述
价值流图分析 VSM
价值流图基本概述
价值流图与流程图区别
价值流图: • 让所有人看见整体 情况 • 根据真实数据 • 改善蓝图 • 持续改善 流程图: • 只能反映局部工艺 周期、流程 • 根据工程标准或旧 数据 • 一年一次的大计划
价值流图分析 VSM
价值流图析步骤
(以前的认识是我们创造了产品的价值,并且由此确定了其价值。)
总之,永远站在客户立场上看待我们的工作价 值。谁对我们的工作进行最终评判和衡量,谁就是 我们的客户。 客户—我们从事一切生产经营活动并进行改善的最根本的出发点和落脚点
精益价值流程VSM培训PPT完美版
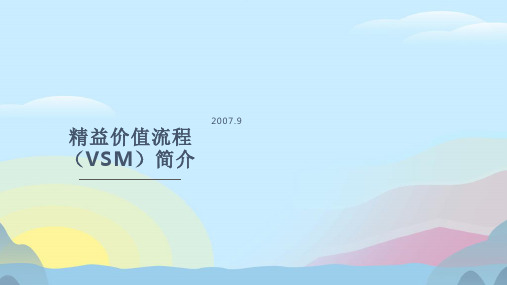
Final Thought
5-6min each Page 48 of 44
而且通常每一个大的流
Implement on all 3 DT Pack lines
都是由很多小的溪流汇流而成的 为了控制上游过程的生产你需要在哪儿使用超市拉动系统?
6s/台
客户需求 3000 units
NB ASM work time/wait time
Ergonomic Design
Travel time
Tool & Material access
缺陷 Internal Rework Supplier Final Test Inspection
过度加工
Material Shortages
Un-level Demand
Build to stock
Economic Lot Sizes
• 6 stations
• timers
• Objectives
• VSM
• LT
• CT
• Leave on whiteboard for Balancing discussion
标准化作业: 走向线体平衡之路
TAKT Time
A
B
CD
E
现状
TAKT Time
A B CD E
传统解决方案
TAKT Time
Kaizen
标准化(S) and Kaizen
Page 18 of 44
改善
S
K K
K S K
K
K S
K S
K
K
时间
Lean 游戏
L
MA L
I
H
E
2024版价值流程图VSM案例分析PPT课件

价值流程图VSM案例分析PPT课件目录•引言•案例分析:某制造企业生产流程优化•案例分析:某电商平台订单处理流程改进•案例分析:某医院患者就诊流程优化•总结与展望01引言提高生产效率降低成本提升产品质量目的和背景通过价值流程图VSM分析,识别生产过程中的浪费环节,优化生产流程,提高生产效率。
减少生产过程中的非增值活动,降低生产成本,提高企业竞争力。
通过价值流程图VSM分析,发现生产过程中的问题点,改进生产工艺,提升产品质量。
价值流程图VSM简介定义价值流程图VSM是一种可视化工具,用于描述产品或服务的整个价值流,包括从原材料到最终产品或服务的所有活动。
作用帮助企业识别生产过程中的浪费环节,优化生产流程,提高生产效率和质量。
适用范围适用于制造业、服务业等各个领域的企业。
02案例分析:某制造企业生产流程优化当前生产流程存在过多的环节和等待时间,导致生产效率低下。
生产流程繁琐资源浪费严重质量问题突出生产过程中的物料、人力和时间等资源未能得到充分利用,造成资源浪费。
产品质量不稳定,客户投诉率高,影响企业声誉和市场竞争力。
030201企业现状及问题分析深入企业生产现场,全面了解现有生产流程、设备、人员配置等情况。
流程调研收集生产过程中的关键数据,如生产周期、在制品数量、设备利用率等。
数据收集基于调研和收集的数据,绘制价值流程图VSM ,直观展示生产过程中的价值流动情况。
VSM 绘制价值流程图VSM 构建识别并消除生产过程中的浪费环节,如减少等待时间、降低库存等。
消除浪费优化生产流程,合并或取消不必要的环节,提高生产效率。
简化流程加强产品质量控制,采用先进的质量管理方法和技术手段,提高产品质量稳定性。
强化质量控制生产流程优化方案设计01020304生产效率提升资源利用率提高产品质量改善企业竞争力增强实施效果评估通过优化生产流程,提高生产效率,缩短生产周期。
充分利用物料、人力和时间等资源,降低生产成本。
通过生产流程优化,提高企业市场竞争力,实现可持续发展。
《VSM培训教材》课件

感谢您的观看。
《VSM培训教材》PPT课件
目录
VSM概述VSM的核心概念VSM实施步骤VSM实施案例VSM的未来发展
01
CHAPTER
VSM概述
01
02
它通过绘制产品从需求到交付的价值流图,帮助企业识别和消除浪费,提高生产效率和产品质量。
价值流图(Value Stream Mapping, VSM)是一种可视化工具,用于描述产品从概念到交付过程中所有活动和信息的流动。
服务业
02
CHAPTER
VSM的核心概念
价值流是指产品从原材料到最终成品的过程中,所有创造价值的活动和过程。
价值流定义
价值流识别
价值流分析
识别出产品在生产过程中的所有活动,包括原材料采购、生产、物流、销售等环节。
通过分析价值流,找出浪费和瓶颈,提高生产效率和降低成本。
03
02
01
价值流图是一种工具,用于可视化产品在生产过程中的所有活动和时间。
详细描述
05
CHAPTER
VSM的未来发展
数字化转型是当今企业发展的必然趋势,VSM作为价值流管理的工具,能够为企业提供全面的价值流视图,帮助企业更好地应对数字化转型的挑战。
VSM通过数字化技术,如大数据、云计算、物联网等,实现价值流信息的实时采集、分析和可视化,为企业决策提供有力支持。
VSM与数字化转型的结合,将进一步推动企业实现流程优化、降低成本、提高效率,提升企业的竞争力和市场地位。
制定改进措施
按照改进措施,逐步实施改进计划,并对实施过程进行监控和调整,确保改进计划的有效性。
实施改进计划
在改进计划实施后,持续监控价值流的运行情况,并根据实际情况进行优化和调整,以保持价值流的持续改进和高效运行。
VSM价值流程图ppt课件
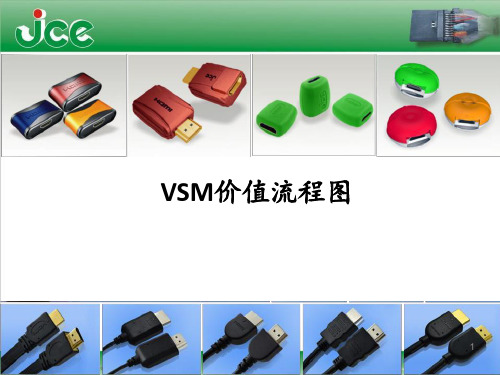
原材料到成品整个制程、工艺上的信息; 成品到顾客; 关注信息流部分。顾客公司系统供应商 计算Lean Time, 同时包含VA(有价值),NVA(无价值)部分及VA Ratio(有价值比例)。
Prep:
Appr:
Rev: PA1
4
Checked:
Date:
4 (43)
并有利于对生产流程进行指导,朝向理想化方向发展。
Prep:
Appr:
Rev: PA1
2
Checked:
Date:
2 (43)
什么是价 值流
所谓价值流,是当前产品通过其基本生产过程所要求的全部活动。这些活动包括 给产品增加价值和不增加价值两部分,包括了从产品最基本的原材料阶段一直到产品 交付顾客的全部过程,如一辆汽车的制造,包括了从顾客要求到概念设计、产品设计、 样车制造、试验、定型、投产到交付后的使用、信息反馈和回收过程,会经历很多车 间、工厂、公司,甚至可能经历过多个国家和地区。
价值流图分析 的作用
① 分析系统整体存在的问题,具有看到宏观生产流程的能力 ② 帮助发现浪费源 ③ 展示了信息流与物流之间的联系 ④ 广泛沟通的工具 ⑤ 确定优先次序 ⑥ 结合精益的概念与技术…避免“只挑容易的” 来改进难 ⑦ 形成实施计划的基础 ⑧ 建立起确定改善目标的数据基础
Prep:
Appr:
时同样要找出影响本公司的主要因素,避免影响图析的效果和后续改善的方向和目 标。
顾客需求节拍应根据实际供货的历史加以修正。 顾客拉动和成品仓库发货拉动两种方式实际上都是由顾客需求拉动的,关键区别在
于是否建立成品库存。在实施精益生产初期,建议采用成品发运仓库的方式,这样 能够保证准时交付顾客。随着精益生产施的深入,可以逐步减少成品库存,最终转 变成顾客拉动。
2024版精益价值流程VSM培训PPT
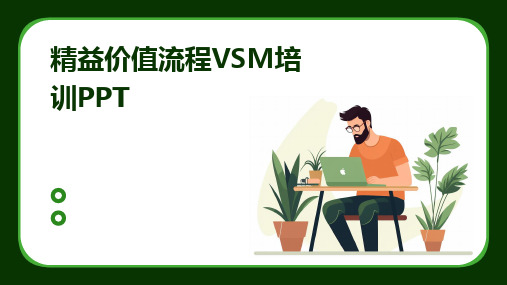
精益价值流程VSM培训PPT•精益价值流程VSM概述•精益价值流程VSM核心原理•精益价值流程VSM实施步骤•精益价值流程VSM在制造业应用案例目录•精益价值流程VSM在服务业应用案例•精益价值流程VSM培训总结与展望01精益价值流程VSM概述精益思想与VSM关系精益思想强调消除浪费,持续改进,追求卓越。
VSM 作为精益思想的重要工具,通过可视化价值流,识别浪费,推动流程优化。
精益思想与VSM相互补充,共同推动组织实现高效、灵活、优质的生产与服务。
VSM(Value Stream Mapping,价值流图)是一种可视化工具,用于描述产品或服务的整个价值流。
VSM通过识别价值流中的浪费,帮助组织优化流程,提高生产效率,降低成本。
VSM的作用包括:识别浪费、优化流程、提高生产效率、降低成本、增强组织竞争力。
VSM定义及作用010204 VSM发展历程VSM起源于丰田生产方式(TPS),是精益生产的重要工具之一。
随着精益生产的普及,VSM逐渐在制造业中得到广泛应用。
近年来,VSM的应用范围不断扩展,已经渗透到服务业、医疗、教育等领域。
未来,随着数字化、智能化技术的发展,VSM的应用将更加便捷、高效。
0302精益价值流程VSM核心原理选择具有代表性的产品族,明确其生产流程,包括从原材料到成品的所有环节。
确定产品族和生产流程收集数据绘制价值流图识别浪费收集各环节的生产数据,如生产周期、在制品数量、设备利用率等。
运用专业的绘图工具,将生产流程以图形化方式展现出来,包括物料流、信息流等。
在价值流图中标注出存在的浪费现象,如等待、运输、不良品等。
价值流图绘制方法识别浪费制定消除策略实施改进措施持续监控与改进浪费识别与消除策略持续改进文化培养树立持续改进观念建立改进机制培养员工能力营造改进氛围03精益价值流程VSM实施步骤现状调研与数据收集01020304明确调研目标收集现场数据了解客户需求分析现状价值流图绘制及分析确定价值流图的范围分析浪费和瓶颈A B C D绘制当前状态的价值流图制定改进目标改进方案制定与实施实施方案制定改进方案调整方案监控实施过程对实施过程进行监控,确保改进方案的顺利执行。
VSM(价值流图中文)ppt课件
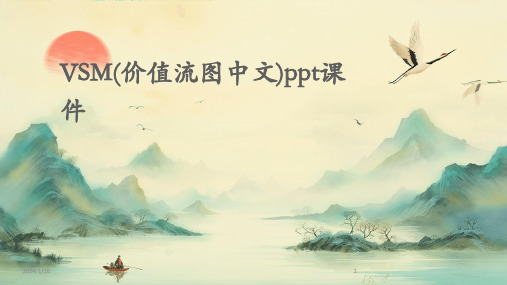
实施精益生产
引入精益生产理念和方法,通过持续改进和全员参与,不断优化生 产流程,降低生产成本。
18
供应链协同与整合
供应链可视化
通过价值流图将供应链各环节进行可视化展示,提高供应链透明度 和协同效率。
供应商选择与评估
利用价值流图对供应商进行全面评估,选择优质供应商并建立长期 合作关系。
5
价值流图发展历程
起源
价值流图起源于日本丰田汽车公司的 精益生产理念,旨在通过消除浪费来 提高生产效率。
发展
趋势
未来,随着数字化和智能化技术的发 展,价值流图将更加注重数据驱动和 实时性,实现更加精准和高效的流程 优化。
随着精益生产理念的普及,价值流图 逐渐被应用于其他行业和领域,成为 一种广泛使用的流程优化工具。
制定实施计划
制定改进方案的实施计划,包括 时间、资源、风险等方面的考虑
。
2024/1/26
16
04
价值流图在企业管理中应用实践
2024/1/26
17
生产流程优化与再造
2024/1/26
识别生产流程中的浪费环节
通过价值流图分析,发现生产过程中的无效等待、过度生产、不 必要的运输等浪费现象。
优化生产布局和设备配置
库存优化与物流管理
基于价值流图分析,合理规划库存和物流管理策略,降低库存成本和 运输成本。
2024/1/26
19
客户服务质量提升
2024/1/26
客户需求识别与响应
通过价值流图分析客户需求和反馈,及时响应并改进产品和服务 。
服务流程优化
优化客户服务流程,提高服务效率和质量,提升客户满意度。
精益价值流程VSM培训PPT完美版

03
价值流程图绘制与分析
价值流程图基本构成元素
流程步骤
物料流
信息流
表示价值流中的各个操 作步骤,包括增值和非
增值活动。
显示物料在价值流中的 流动情况,包括原材料、
在制品和成品。
反映价值流中的信息传 递情况,如订单、生产
计划和交货通知等。
时间线
浪费类型及识别方法
浪费类型 过度生产
等待时间
浪费类型及识别方法
不必要的运 过度加工
库存积压
浪费类型及识别方法
不必要的动作 缺陷与返工
识别方法
浪费类型及识别方法
价值流图分析
通过绘制价值流图,可视化生产流程 中的浪费。
现场观察
员工反馈
鼓励员工提出浪费问题和改进建议。
深入生产现场,观察并记录浪费现象。
未来发展趋势预测及建议
随着制造业的转型升级,精益价值流 程VSM的应用将更加广泛
数字化、智能化技术将在精益价值流 程VSM中发挥更大作用
企业将更加注重跨部门、跨领域的协 同合作,以实现整体最优
建议企业加强精益价值流程VSM的培 训和推广,提高全员参与度和持续改 进能力
THANKS
感谢观看
改善机会挖掘与评估
改善机会来源 生产过程中的瓶颈环节 高浪费、低价值的活动
改善机会挖掘与评估
01
员工创新和改进建议
02
评估方法
预期效益分析:预测改善措施实施后的经济效益。
03
改善机会挖掘与评估
实施难度评估
分析改善措施的实施难度、时间和资源需求。
风险评估
识别潜在风险,制定应对措施。
价值流图VSM绘图教程PPT课件

3. 物料流应按照工序从左向右绘制 而不是按照工厂的实际布局
4. 在车间沿物料流走一遍, 需要收集一些必要的、可以帮助 绘制未来状态图的数据, 并记录在数据箱中
• 周期时间 • 增值时间 • 设备开机率 • 工作时间 • 库存
• 员工数量 • 产品种类 • 良品率 • 换模时间 • 生产批次间隔(EPE)
6
绘制VSM Step1 — 客户栏
.
1. 绘图从客户需求开始 改善最重要的是从客户的角度 来确认产品的价值
2. 用数据箱记录客户需求 需求量/交货频率/交货单位 最小批次量/工作时间
7
绘制VSM Step2 — 生产工
序
.
1. 用工序框代表不同的工序 物料从一个工序向另一个工序移动 流程不连续或材料中断时, 物料流自然停止
某些特殊情况,超市并不适用 如订制品、保质期短的材料、少量但高价的零件等。 可设置一个“顺序拉动”即先进先出FIFO来取代超市。
• 定拍工序按客户订单来控制生产
• 定拍工序往往是价值流中连续流的最后一个工序
• 定拍工序后面的流程按FIFO方式移动
.
16
精益均改衡生善产
D1
集中 生产
D2
D3
成品库存量大,原材料及在制品多,适应变化的灵活性差。
.
21
感谢您的聆听
.
22
价值流图绘图教程
季正勇
.
1
目录
01
价值流图
02
VSM图标
03
绘制现状图
04
绘制未来图
.
2
价值流图 VSM
价值流程图(Value Stream Mapping,VSM)是丰田精益制 造(Lean Manufacturing)生产系统框架下的一种用来描述 物流和信息流的形象化工具。
VSM价值流图析-图形和步骤11课件PPT
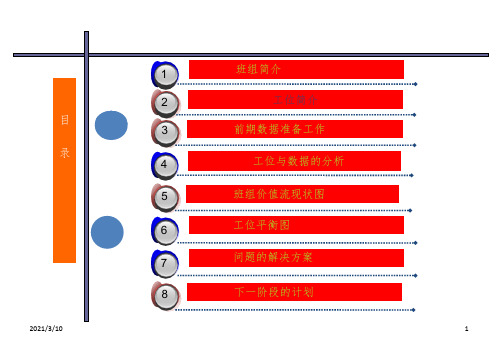
是一个量化的工具
2021/3/10
显示信息流、工艺流、材料流的联系
4
第一部分:价值流图简介
二、改善类型
高层面的管理
不是指职 位的高层
流程改善
价值流推进 焦点:物流和信息流
•平面改进 •库存减少 •拉动系统
过程改进
消除浪费 焦点:方法与人
•运转时间 •装换时间 •报废 •人员使用
面向生产线
工作小组的焦点
2021/3/10
5
第一部分:价值流图简介
二、改善类型
流程的改善
流程改善焦点在物流和信 息流; 流程改善的目的在于改进 在生产价值流中的物料流程; 流程改善的结果减少库存, 降低前置时间。
过程的改善
过程改善就是在生产现 场的小组层级消除浪费, 以人员和工艺流程为焦点。
2021/3/10
6
第一部分:价值流图简介
生 产 流
2021/3/10
关注整个 系统的流动
分析价值 流的现状 系统地 发现问题
识别和消除系 统
和流程中的浪 费
是讨论生 产过程的 共通语言
信 息 流
3
第一部分:价值流图简介
一、概念
实施改善计划的基础
可借助衡量指数来了解制造 过程绩效及改善目标
实施精益制造的蓝图
价值流图析—— 一个生产或服务基本分析工具
2001
Target Actual
1.52
2.62
O N D YTD 2002
Severity Rate 50
40
30
38.32
20 13.32 19.77 19.88 12.42
10
YTD J F M A M J J A
精益价值流程(VSM)培训PPT
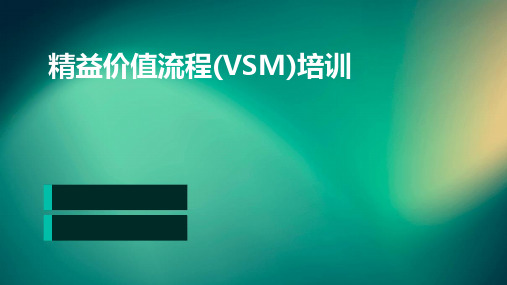
VSM在全球化环境中需要关注 供应链的协同和优化,实现整个
价值链的精益化。
VSM在可持续性发展中的角色和作用
VSM在可持续性发展中扮演着重要的角色, 通过优化流程、降低浪费、提高效率等方式 ,有助于企业实现可持续发展目标。
VSM可以促进企业内部的绿色生产和 管理,推动绿色供应链的发展,为整 个社会的可持续发展做出贡献。
VSM可以帮助企业识别和解决环境问 题,减少对环境的负面影响,提高企 业的社会责任感。
06 总结与展望
VSM的价值和影响
01
02
03
04
提高生产效率
通过消除浪费和优化流程, VSM有助于提高生产效率,
降低成本。
提升产品质量
VSM注重质量第一,通过减 少缺陷和不良品率,提升产品
质量。
增强客户满意度
VSM的应用范围和优势
应用范围
适用于各种规模的企业,无论是制造 业还是服务业。
优势
VSM可以帮助企业了解整个价值流, 发现并消除浪费,提高生产效率,降 低成本,增强客户满意度。
02 VSM的构建过程
价值流映射
识别产品或服务的价值流
01
明确产品或服务的整个流程,包括从原材料采购到最终交付给
客户的所有环节。
精益价值流程(VSM)培训
contents
目录
• VSM概述 • VSM的构建过程 • VSM实施的关键要素 • VSM实施案例分享 • VSM的未来发展和挑战 • 总结与展望
01 VSM概述
VSM的定义和重要性
VSM(Value Stream Mapping)是 一种用于识别、分析和改进产品或服 务从概念到交付过程中所有活动和流 程的工具。
- 1、下载文档前请自行甄别文档内容的完整性,平台不提供额外的编辑、内容补充、找答案等附加服务。
- 2、"仅部分预览"的文档,不可在线预览部分如存在完整性等问题,可反馈申请退款(可完整预览的文档不适用该条件!)。
- 3、如文档侵犯您的权益,请联系客服反馈,我们会尽快为您处理(人工客服工作时间:9:00-18:30)。
同时,可以考虑采用流水线生产和拉式生产相结合的生产 和管理方式。因为这样不仅有利于减少在制品库存,缩短提前 期,也非常有利于对装配工位需求的响应。此外,由于定拍工 序粗车节拍为60s,采取拉式生产有利于为减少生产过多过早的浪 费。
三、价值流程图案例分析
粗车
钻孔
精车、抛光
检验
物料搬运由1个专人负责,搬运设备为手推车。搬运工 每班从仓库向车间搬运一次毛坯,从车间向装配工位搬运 两次成品零件。装配工位每天对该零件的需求为700件,每 料盘25件,并把他们的每月预测和每日需求信息发给车间 调度部门。
车间调度部门把每周计划下发给零件加工车间各工位和搬 运工,此外,将其每月预测和每周计划信息发给原料、半成品 仓库。粗车工位零件毛坯在制品库存为350件,以后三道工序在 制品库存以及零件成品在制品库存均为175件。
价值流程图(VSM)案例分析
主要内容
一、价值流概念 二、价值流程图 三、价值流程图案例分析
一、价值流的概念
价值流是制造产品所需一切活动的总和,包含了增 值活动和不增值活动。
使用价值流分析意味着对全过程进行研究,而不 只是研究单个过程;改进全过程,而不是仅仅优化局 部。
据统计,增值活动约占企业生产和经营活动的5%, 不增值活动约占95%。因此,应在价值流中识别不增 值活动,通过持续不断地开展价值流改进,消除各种 浪费,降低成本。
各工序作业节拍分析
容易看出,车间加工时间最长的工序粗车时间为60s<72s, 因此目前生产会造成制造过多、过早的浪费。
各工序生产还不平衡,易造成等待浪费。
该零件加工周期=60+35+55+25=175(s),一个零件的生产 加工时间(包括物流等时间)即生产提前期 =0.5+0.25+0.25+0.25+0.25=1.5(天)。因此
因此,目前生产单位零件的生产过程时间过长,也就是说 生产提前期过长,这会造成生产响应需求的能力降低,不利于 企业竞争。
其次,各工序间在制品库存最小库存储备天数为0.25天,即
0.25x25200x2/60=210(min),很明显在制品库存水平过高,会 造成在制品库存的浪费。
此外,各工序作业统一由车间调度部门调度,各工序间实 行推动式生产,不利于及时响应需求的变化和减少在制品库存 。
(3) 动作的浪费
(7)等待的浪费
(4) 搬运的浪费
(8)管理的浪费
价值流程图分析特征
价值流程图分析以客户的观点分析现有价值流程图 每一个活动的必要性,画出期待的价值流的未来状态 图,并制定实施计划。
(1)绘制出并简单显示出物流和信息流 (2)揭示产生浪费的原因 (3)创建一个改善的价值流 (4)创建和协调一个跨部门团队方法
单一特征——复杂特征 方言——普通话——书面语言 简单形式——复杂形式 时间词:时间阶段、时间次序 空间方位词、指示代词、人称代词、量词
句子的 发 展
句子的产生 —不完整句(单词句——电报句) —完整句(简单句——复杂句——复合
句) 句子的理解 实践可能性策略、词序策略、非语言策略
第一节 儿童语言的发展
价值流改进重点在于物流和信息流。
VSM分析的对象
VSM分析的主旨是暴露存在的浪费问题,并彻底排 除浪费。在JIT 生产方式中,凡是超出增加产品价值 所绝对必需的最少量的物料、设备、人力、场地和时 间的部分都是浪费。
VSM分析关注的八大浪费包括:
(1) 不良/ 修理的浪费 (5)库存的浪费
(2) 过分加工的浪费 (6)制造过多/过早的浪费
第六章 儿童语言的发展
语言的发生 语言的发展 语言获得的理论
儿童语言的产生
儿童语言产生的准备 • 反射性发声阶段 未分化哭声——分化的哭声——凌乱发音 • 牙牙学语阶段
儿童语言理解的准备 • 语言知觉 • 语词理解
儿童语义的发展
名词(中间水平):语义扩张或语义缩小 形容词:特征描述——情景描述
粗车工序零件毛坯库存储备天数=350/700=0.5(天)
粗车和钻孔工序间库存储备天数=175/700=0.25(天)
同理依次计算出各工序间库存储备天数,并绘制出当前价 值流程图
绘制当前价值流程图
当前价值流程图
分析当前为700件,且其与车间和原 料、半成品仓库均实行两班制,每班有效时间25200s,使用率 100%,因此
价值流程图分析的好处
(1)目视化工具 (2)信息沟通方式 (3)有利于发现存在的问题 (4)创建一个改善的价值流
价值流程图分析步骤
选择一个 产品
从头到位聚焦一个产品、过 程或服务,搜集相关数据
分析当前问题: 信息、物料、交互
设计一个精益价值流 建立想要达到的理想状态
计划和实施
实施计划,达到的理想状态
设备布置也应作相应调整,具体布置如图所示
未来价值流程图
需要注意的是,由于钻孔、精车抛光、检验三道工序是2个 人在U形生产线中完成的,如采用逐兔式完成,因此每人115s完 成三道工序的生产即115s共完成两个工件的加工,同时粗车工 人120s完成两个毛坯加工,因此相当于U形生产线中57.5s完成 一个零件的加工。因此,图3-2中后面三道工序的加工周期标注 57.5s。
同时,我可以看出,依照新的方案安排生产,生产提前期可 减小到0.5天,比原来减少了66.67%((1.5-0.5)/1.5x100%) 。同时可实现流水线下的拉式生产,在制品库存也可明显减少 ,对装配车间的需求响应将更加的迅速准确。此外生产线平衡 率大大提高
这也将使作业者等待的浪费大大降低。由此可见企业应用 价值流程图分析可获得较为理想和客观的收益。
存在的问题
(1)目前生产会造成制造过多、过早的浪费; (2)各工序生产还不平衡,易造成等待浪费; (3)生产提前期过长,这会造成生产响应需求的能力降低,不利
于企业竞争; (4)在制品库存水平高,会造成在制品库存的浪费; (5)实行推动式生产,不利于及时响应需求的变化和减少在制品
库存。
改进方案设想