热处理检验方法和规范修订稿
AMS_2759-2C_低合金钢零件的热处理

3.3.1 零件类型:
热处理操作人员应确定零件类型。 1 类:热处理后所有表面机加余量大于等于 0.020 英寸(0.51mm)的零件以及具锻造,铸造,
热轧表面,热处理后须机加掉的零件。除非被告知零件所有表面都留有 0.020 英寸 (0.51mm)加工余量,否则热处理操作人员应将其视为无加工余量并按相应的 2、3 或 4 类另件进行控制。
4.1.1 收试验:
除 AMS 2759 规定的试验项目外,对每炉批零件应作(3.5.1 节)表面污染试验,假如 碳势为自动控制并有指示或记录,则可代之以 4.2 节规定的办法定期进行表面污染 检测。
4.1.2 试生产试验:
除 AMS 2759 规定的试验项目外,在热处理生产前应对每个炉子,每种使用的气氛 以及 B 级气氛在小于等于 0.40%和大于 0.40% 二种碳势情况下进行(3.5.1 节)的 表面污染试验。
-2-
AMS 2759/2C
3.3.1.1 假如不能确定另件的类型,则按 3 类另件处理。
3.3.2 气氛级别:
A 级:氩气、氢气、氦气、氮气、氮-氢混合气体、真空或中性盐浴。不允许使用由 氨气分解成的氮气。
B 级:吸热型、放热型或含碳的氮基气氛(见 8.2 节)。
C 级:空气或燃烧产品(氧化性气氛)
-3-
AMS 2759/2C
3.4.4 不完全退火:在硬化之前,将零件加热到 1150-1250℉(621-677℃)保温至表 4 规定的时间,然后冷却至室温。9Ni-4Co 类钢零件应按表 2 规定采用不完全退火。
3.4.5 硬化前的应力释放:零件在硬化前将其加热到 1000-1250℉(538-677℃)保温至不 少于表 4 规定的时间,然后冷却至室温。
热处理件表面检验验收标准

热处理件表面质量检验验收标准一、目的为保障产品的质量,建立和规范热处理件表面质量的检验方法,对热处理件产品生产、出厂或外购的外观检验提供科学、客观的依据,以保证检验结果一致性、全面性及准确性,同时防止材料表面缺陷影响后道工序的生产及品质,特制定本标准。
二、适用范围本标准适用于湘重公司生产及外购或委外加工的热处理件表面质量检验及验收三、规范性引用文件下列文件中的条款通过本标准的引用而成为本标准的条款。
凡是注日期的引用文件,其随后所有的修改单(不包括勘误的内容)或修订版均不适用于本标准,然而,鼓励根据本标准达成协议的各方研究是否可使用这些文件的最新版本。
凡是不注日期的引用文件,其最新版本适用于本标准。
GB/T15822 磁粉探伤方法GB/T226 钢的低倍组织及缺陷酸蚀检验法GB/T3721 磁粉探伤机JB/T9218 渗透探伤GB/T 231 《布氏硬度试验方法》GB/T 230 《金属洛氏硬度试验方法》GB/T 17394 《金属里氏硬度试验方法》GB/T4340 《金属维氏硬度试验方法》GB/T4341 《金属肖氏硬度试验方法》GB/T18449 《金属努氏硬度试验方法》GB/T 6402 《超声波探伤标准》四、表面质量检验项目及验收标准4.1对于生产或购买的热处理件,表面质量具体检验项目及标准如表1:表一表面质量检验项目及验收标准4.2热处理件有上述缺陷,允许清理,但表面清理深度不得大于5mm,清理处应圆滑无棱角,清理宽度和长度分别不得小于清理深度6和8倍,清理处的残存钢渣应予以铲除。
4.3其它未尽事宜,可由供方与需方协商解决处理。
五、热处理件表面质量检验方法5.1 对于生产或购买的热处理件,表面质量具体检验方法如表2:表二表面质量检验方法5.2 热处理件尺寸检验5.2.1 长度尺寸检验可用直尺、卡钳、卡尺或游标卡尺等通用量具进行测量。
5.2.2 高度(或横向尺寸)与直径检验一般情况用卡钳或游标卡尺测量,如批量大,可用专用极限卡板测量。
热处理工艺规范

➢ 本规范规定了本公司常用的金属的热处理 设备、工艺与质量检验方法
1
热处理工艺规范
目录
➢ 前言 1 规范范围 2 规范性引用文件 3 常用热处理方式定义 4 工艺分类代号 5 工件举例 6 热处理设备 7 工作要求 8 规范 9 热处理后工件的质量检验
2
热处理工艺规范
前言
本标准由技术部提出。 本标准由技术部起草。 本标准主要起草人:xx 本标准审核人:xx 本标准批准人:xx 本标准由技术部部归口并负责解释。 本标准于2019年10月首次发布,于2020年3月第一次修订。
14
热处理工艺规范
6 热处理设备 • 6.1 加热炉有效加热区实际温度偏差值(指炉罐内)
不应超过±20℃。 • 6.2 加热炉的每个加热区应配有温度测定及温度控制
自动记录装置。 • 6.3 加热炉的维护保养必须按制订的制度进行,并妥
善保管有关记录。
15
热处理工艺规范
7 工作要求 • 7.1 检查设备、仪表是否正常,并应事先将炉膛清理
干净。 • 7.2 核对材料与图样是否相符,了解零件的技术要求
和工艺规定。 • 7.3 选择好合适的工夹具,并考虑好装出炉的方法。
16
热处理工艺规范 8 规范 8.1 工艺的制定。应根据工件的特征(材料的牌号、处 理前的状态及形状、尺寸等)、热处理 目的、批量、热处理设备等具体条件来制定合理的热处 理工艺。 8.2 热处理工艺曲线见图1、图2
• 8.4 冷却时应以适当的速度,使工件各部分均匀冷 却。
• 8.5 如采用空冷,应在空气中散开冷却,不允许堆 放或置于潮湿的地上冷却。
20
热处理工艺规范 • 8.6 作为热处理后的辅助工序,清除工件的氧化皮
JB 8434—96 热处理环境保护技术要求

热处理环境保护技术要求JB 8434—96中华人民共和国机械工业部1996—09—03批准1997—07—01实施前言本标准为贯彻《中华人民共和国环境保护法》,防止和控制热处理对环境的污染而制订。
本标准由机械工业部环境保护机械标准化技术委员会提出并归口。
本标准负责起草单位:机械工业部武汉材料保护研究所。
本标准主要起草人:张炼、郦振声。
本标准于1996年9月3日首次发布。
1 范围本标准规定了热处理环境污染的分类及污染物的控制与排放标准等技术要求。
本标准适用于从事热处理生产的车间和工厂。
2 引用标准下列标准所包含的条文,通过在本标准中引用而构成为本标准的条文。
本标准出版时,所示版本均为有效。
所有标准都会被修订,使用本标准的各方应探讨使用下列标准最新版本的可能性。
GBJ 4—73 工业“三废”排放试行标准GB 87—85 工业企业噪声控制设计规范GB 3095—82 大气环境质量标准GB 5085—85 有色金属工业固体废物污染控制标准GB 5086—85 有色金属工业固体废物浸出毒性试验方法标准GB 5087—85 有色金属工业固体废物腐蚀性试验方法标准GB 5088—85 有色金属工业固体废物急性毒性初筛试验方法标准GB 8702—88 电磁辐射防护规定GB 8978—88 污水综合排放标准GB 12348—90 工业企业厂界噪声标准GB 14500—93 放射性废物管理规定JB/T 5073—91 热处理车间空气中有害物质的限值JB/T 6074—92 热处理盐浴有害固体废物无害化处理方法TJ 36—79 工业企业设计卫生标准ZB J71 00l一90 热处理盐浴有害固体废物污染管理的一般规定3 热处理环境污染的分类和来源热处理的环境污染分为化学性污染和物理性污染。
化学性污染来自原料、中间反应产物及废弃物中的各种行害物质,主要以废气、废水和固体废物的形式存在;物理性污染主要为噪声和电磁辐射。
其分类和米源列于表1。
CQI-9热处理系统评估在汽车零部件热处理过程中的应用

CQI-9热处理系统评估在汽车零部件热处理过程中的应用刘宏磊;李昌海【摘要】通过对CQI-9热处理系统评估进行简要的介绍,分析了CQI-9热处理系统评估在汽车零部件热处理过程中应用的必要性,对比第3版CQI-9热处理系统评估与前两版的主要区别.笔者结合长期从事热处理工作及进行CQI-9热处理系统评估工作,提出了一些审核技巧和应用中暴露出来的问题.【期刊名称】《金属加工:热加工》【年(卷),期】2016(000)013【总页数】3页(P18-20)【关键词】CQI-9热处理系统评估;汽车零部件;热处理过程【作者】刘宏磊;李昌海【作者单位】中信戴卡股份有限公司;中信戴卡股份有限公司【正文语种】中文热处理系统评估C Q I-9: Special Process: Heat Treat System Assessment (HTSA)由美国汽车工业行动集团AIAG的热处理工作小组开发,AIAG于2006年3月发布;2007年8月发布了第2版;2011年10月发布了第3版。
HTSA 提出的热处理要求是来自顾客和产品标准的附加要求。
热处理系统评审适用于评审一个组织满足HTSA的要求及顾客要求、政府法规要求和组织自身要求的能力;也适用于对供应商的评审。
HTSA的目标是在供应链中建立持续改进,强调缺陷预防,减少变差和浪费的热处理管理系统。
HTSA与国际认可的质量管理体系以及适用的顾客特殊要求相结合,规定了热处理管理系统的基本要求,旨在为汽车生产件和相关服务件组织建立热处理管理体系提供一个通用的方法。
美国戴姆勒克莱斯勒、福特、通用三大汽车公司在其顾客特殊要求中均对热处理系统评审提出要求,凡是热处理供应商都必须按CQI-9做过程审核。
热处理作为一个特殊的工艺过程,由于其材料特性的差异性、工艺参数的复杂性和过程控制的不确定性,以及其产品检验为破坏性抽样检验,及加大检验频次的不经济性,长期以来一直视为汽车零部件制造业的薄弱环节,并在很大程度上直接导致整车产品质量的下降和召回风险的上升。
GB5099修订版与GB5099-94_版主要变化2011
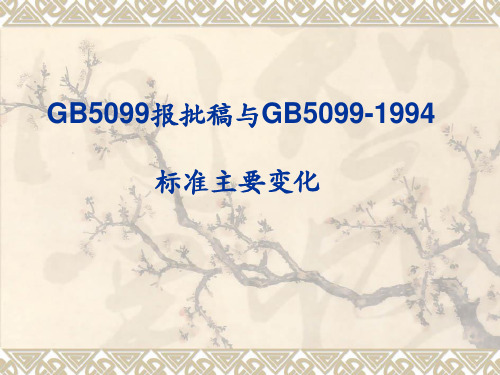
20
瓶口普通螺 纹设计要求
无
21
钢瓶组批
22
瓶阀装配扭 矩
GB5099报批稿与GB 5099-94主要变化
序号 修订内容 GB 5099-94 GB 5099-报批稿
23
无损检测要 求
淬火后回火热 处理的瓶体应 逐只进行超声 或磁粉检测
淬火后回火热处理的抗拉强度小于 1100MPa的钢瓶应进行超声检测, 但对于筒体长度小于200mm的钢瓶 可用磁粉检测代替; 正火处理用来充装氢气及其他具有 致氢脆性、毒性或腐蚀性介质的, 或淬火后回火热处理的抗拉强度小 于880MPa的钢瓶,应逐只进行超声 检测或磁粉检测。
充装混合气体 与不适用于具 有氢脆危险或 应力腐蚀倾向 介质 灭火用的气瓶
GB 5099-94
GB 5099-报批稿
GB5099.1钢瓶不适用于具有氢 脆危险或应力腐蚀倾向的介质; GB5099.1和GB5099.4的钢瓶 盛装介质增加可用于混合气体。
5
无
6
不适用于“灭火用 的气瓶” 一般地区钢瓶的使 用环境温度为20~60℃, 寒冷地区的使用环 境温度为-40~ 60℃。
GB5099报批稿与GB5099-1994 标准主要变化
GB5099报批稿与GB 5099-94主要变化
序号 修订内容 GB 5099-94 GB 5099-报批稿 根据不同热处理方式及强度范围分为4部 分: GB5099.1《第1部分:淬火后回火处理的 抗拉强度小于1100MPa的钢瓶》 GB5099.2《第2部分:淬火后回火处理的 抗拉强度大于或等于1100MPa的钢瓶》 GB5099.3《第3部分:正火处理的钢瓶》 GB5099.4《第4部分:淬火后回火处理的 抗拉强度小于880MPa的钢瓶》
Q-ZZ 30021锻件热处理验收规范-2011(下发 版)

Q/ZZ锻件热处理验收规范中国重型汽车集团有限公司发布前 言本标准代替QZZ 30021—1996《锻件热处理验收规范》。
本标准与QZZ 30021—1996相比,主要变化如下:——标准的编排格式按GB/T 1.1—2009《标准化工作导则 第1 部分:标准的结构和编写》的规定 进行了调整;——对原标准中3.2条、3.3条进行了修订,并取消了原标准中5.3.2条;——删除原标准3.4条对等温退火工艺晶粒度检测,增加调质工艺;——对原标准3.5条增加了“如没有规定,一般锻件按取样部位处总脱碳层深度,每边应小于或等于有效厚度的1%”——对原标准中3.6条进行了修订,增加了“但当锻件尺寸不够取拉伸试样时,则应按强度与硬度值进行换算后,对该锻件在取拉伸试样部位进行硬度检测。
”——对原标准中5.3.3条进行了修订,取消金相组织半级的规定;——在新标准中增加了3.8条和3.9条对过热和过烧的规定;——原标准中规定了拉伸性能,在新标准中修订为力学性能,并增加了对冲击韧性的检验规定; ——新标准中增加了非调质钢的有关规定;——取消了原标准5.3.2中所列出的各种具体钢号;——因GB/T 13320-2007较91版作了很大的改动,故金相组织评级图参照GB/T 13320-2007; ——原标准中取样位置已经不适用,对力学性能的取样位置按DIN EN 10083-1:2006-10重新作了规定;——增加了5.4.1和5.4.2条款,对热处理硬度的测定位置进行了明确规定;——对金相试样的取样位置重新作了规定,取消原标准中对边部和心部金相组织的判定依据; ——取消了原标准5.5.3中对金相试样的硬度检测;——因GB6397已取消,所以本标准中取消了GB6397标准;——本次修订删除了原标准中的“斯达—斯太尔汽车”、“等温退火”等词语;—— 增加了GB/T 229冲击试验标准和DIN EN 10083-1:2006-10 力学性能取样标准;——对原标准的附录A进行了修订。
热处理行业规范条件

热处理行业规范条件(报批稿)一、总则(一)为贯彻落实科学发展观,规范热处理生产经营秩序和投资行为,在保证产品质量和安全生产的基础上,改进企业组织方式,合理配置资源,加快淘汰落后产能和抑制低水平重复建设,推进节能减排清洁生产,引导热处理行业向精密、优质、清洁的集约化、专业化、规模化、现代化方向发展,根据国家有关法律法规和产业政策,特制定热处理行业规范条件。
二、建设条件和企业布局(二)投资新建或改扩建的热处理加工、热处理设备制造和热处理工艺材料生产企业(厂、点)要符合国家产业政策和产业规划,符合地区工业发展规划、产业发展导向和区域功能。
新建或改扩建的热处理加工企业生产能力应具有大于(含)1000万元/年产值的生产能力。
(三)热处理的生产场所一般应设置在地区规划部门规定的区域内,禁止设立在居民区、商业区、旅游区、蔬菜、粮食等农作物种植区与水源保护区。
(四)所有热处理专业化加工厂点的设立要坚决淘汰落后产能,要以加快“发展先进工艺,限制陈旧工艺,淘汰落后工艺”为导向。
推动企业转型升级,确保安全生产,强化节能减排。
促进开发低碳技术项目,发展高技术附加值的热处理企业。
三、工艺装备及工艺材料(五)热处理加工企业或厂点应采用先进技术装备,加热设备的有效加热、保温及炉温均匀性应满足工艺要求,少无氧化的热处理加热设备比例达50%或以上。
不得使用国家明令禁止和淘汰的热处理工艺和设备(参见《产业结构调整目录》、《工业和信息化部高耗能落后机电设备(产品)淘汰目录》、《部分工业行业淘汰落后生产工艺装备和产品指导目录》)。
(六)热处理加热设备应符合相应的电炉能耗分级标准,炉体表面温升、空炉升温时间和空炉损耗功率比应符合GB/T15318《热处理电炉节能监测》要求。
电阻炉加热效率不得低于70%,燃料炉综合热效率不得低于60%。
(七)热处理的加热设备应使用陶瓷纤维等性能优良的绝热、保温材料,禁止使用石棉类材料,保证设备和工艺的能耗符合国家、行业的相关标准要求。
AMS 2759-3C 沉淀硬化型不锈钢与马氏体时效钢零件热处理(中文)
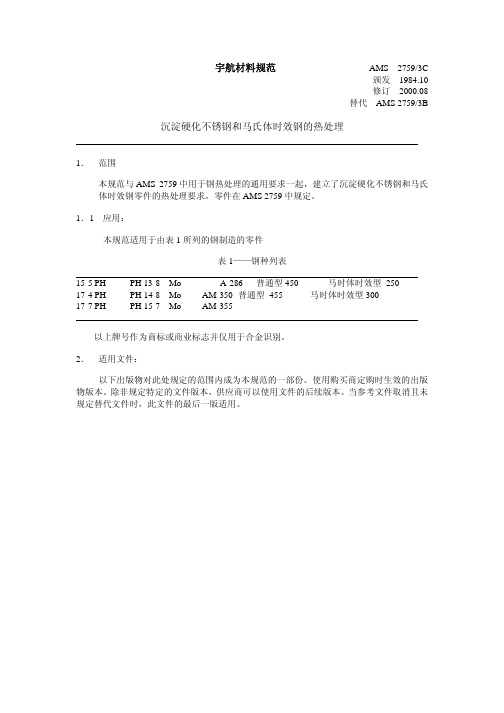
7. 拒收 参见 AMS 2759
8. 注意: 必须根据 8.1,8.2,8.3 和 AMS 2759
8.1 位于左边空白处的更改条(|)是为了方便用户定位技术更改的位置,不是编辑更改, 在本规范上一版已经做出。符号(R)在文件标题的左边,表示本规范完全修订版, 包括技术修订。更改条和(R)不用于原始版本,也不出现在不包含编辑更改的版本。
3.2.3 在温度低于 1300°F(704°C):±10°F(±6°)使用的炉子。
3.3 气氛
气氛必须进行控制,以使正在热处理的零件不受污染。炉子正在使用气氛来热处理 其他种类的钢,可能该气氛会污染沉淀硬化或马氏体时效钢零件,诸如:吸热、放 热、含碳的氮基。气氛必须清除循环使用,并且必须测试以确保零件的表面不受污 染而低于 3.5.3 规定的限制。能破坏或污染金属的材料不能接触零件。 盐浴的成份和维护必须防止零件的污染,盐浴必须根据 AMS2759 进行实验,在空气 中进行热处理必须是自然的马弗炉气氛。
1.1 应用:
本规范适用于由表 1 所列的钢制造的零件
表 1——钢种列表
15-5 PH 17-4 PH 17-7 PH
PH 13-8 Mo PH 14-8 Mo PH 15-7 Mo
A-286 普通型 450 AM-350 普通型 455 AM-355
马时体时效型 250 马时体时效型 300
以上牌号作为商标或商业标志并仅用于合金识别。
3.4.2
保温:在固溶热处理和奥氏体化状态期间,保温必须至所需的时间并且无中断。 加热必须根据 AMS 2759 所描述的进行控制,不管是热处理介质还是零件的温度, 作为适用的,应保持在表 3 的设置温度,保温时间表示在 2.3.4 或 6。当所有的 控制、指示、记录热电偶达到规定的设置温度,或使用的负载热电偶是由 AMS 2759 确定的,当零件热电偶在设置温度达到炉温均匀性的最小值,保温必须开始。
AMS 2759-3C 沉淀硬化型不锈钢与马氏体时效钢零件热处理(中文)
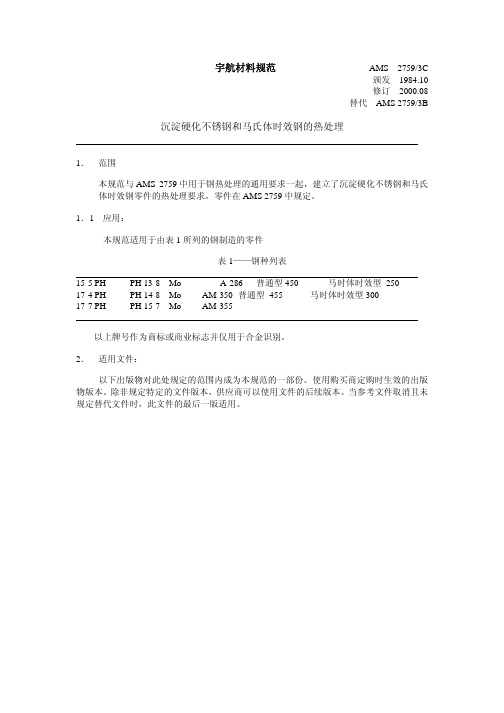
氮或氮氢混和物作为真空炉再充气淬火,在最高至 1925°F(1052°C)充许使用。 禁止使用从氨气中分离出来的氮气,对于无尺寸、无变色要求的零件,应避免使 用空气气氛和空气冷却。
3.3.2 保护涂层:当认定的工程组织批准后,充许使用补充涂层,以使完工机加表面的 氧化最小。
3.4 程序
3.4.1 酸洗:在随后的由铅、锌合金,或其它低熔温材料制成的模具成形前,零件必须 根据 ASTM A380 酸洗。
3.5.3.1 除非特别通知零件将全部机加,否则加热处理装置必须处理零件即使一些表 面没有后续的金属去除物,并且因此必须在受控的气氛中热处理至高于 1350
°F(730°C),该气氛必须符合表面污染要求,除非规定,受控的气氛对于仅 具有原材料表面零件不是必须的,除非零件是同薄板或条带制成。
3.5.3.2 专门用于热处理已去除污染的零件的炉子,不须试验。
表 2—碳化物固溶热处理时间
截面厚度
保温时间
毫米
小时,最小
<25
1
25-76(包括 25 和 76)
2
>76
3
3.4.6
校直: 当由认定的工程组织批准,校直必须或者是在环境温度,在时效期间,或 者是在加热至不高于 50°F(28°C)低于时效温度时完成。 在时效后,室温校直和热或暖校直必须随后进行应力释放。 充许校直后,在时效期间进行应力释放。
7. 拒收 参见 AMS 2759
8. 注意: 必须根据 8.1,8.2,8.3 和 AMS 2759
8.1 位于左边空白处的更改条(|)是为了方便用户定位技术更改的位置,不是编辑更改, 在本规范上一版已经做出。符号(R)在文件标题的左边,表示本规范完全修订版, 包括技术修订。更改条和(R)不用于原始版本,也不出现在不包含编辑更改的版本。
管道焊后热处理工艺流程
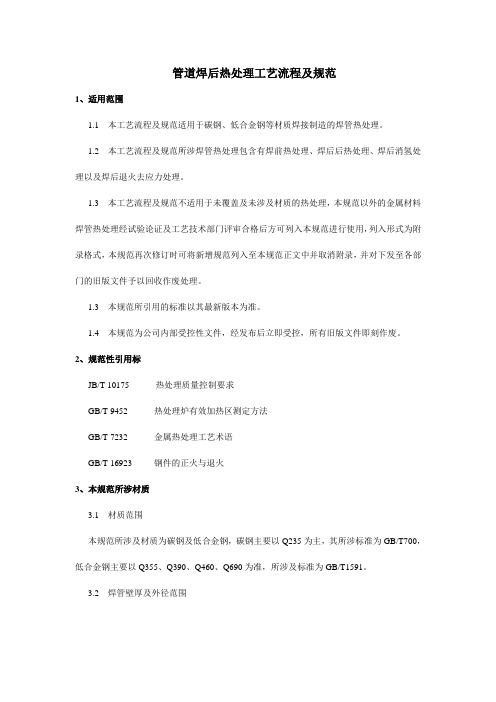
管道焊后热处理工艺流程及规范1、适用范围1.1 本工艺流程及规范适用于碳钢、低合金钢等材质焊接制造的焊管热处理。
1.2 本工艺流程及规范所涉焊管热处理包含有焊前热处理、焊后后热处理、焊后消氢处理以及焊后退火去应力处理。
1.3 本工艺流程及规范不适用于未覆盖及未涉及材质的热处理,本规范以外的金属材料焊管热处理经试验论证及工艺技术部门评审合格后方可列入本规范进行使用,列入形式为附录格式,本规范再次修订时可将新增规范列入至本规范正文中并取消附录,并对下发至各部门的旧版文件予以回收作废处理。
1.3 本规范所引用的标准以其最新版本为准。
1.4 本规范为公司内部受控性文件,经发布后立即受控,所有旧版文件即刻作废。
2、规范性引用标JB/T 10175 热处理质量控制要求GB/T 9452 热处理炉有效加热区测定方法GB/T 7232 金属热处理工艺术语GB/T 16923 钢件的正火与退火3、本规范所涉材质3.1 材质范围本规范所涉及材质为碳钢及低合金钢,碳钢主要以Q235为主,其所涉标准为GB/T700,低合金钢主要以Q355、Q390、Q460、Q690为准,所涉及标准为GB/T1591。
3.2 焊管壁厚及外径范围△—通常不需要,但板厚较厚(≥25mm)时,或相对湿度≥80%时一般需要进行焊前预热处理。
注1:当具备整体焊后退火去应力的条件下,焊后消氢处理可不执行;但当无法立即进行焊后退火去应力处理时,或设备受限等情况,Q460及Q690材质一般需进行焊后消氢处理。
注2:壁厚较薄时,一般无需进行消氢及焊后退火去应力处理,同时后热处理必须注意避免集中加热致使焊管变形。
5、热处理加热设备一般情况下,焊前预热处理及焊后后热处理采用氧乙炔或丙烷烘枪进行加热,焊后消氢处理及焊后退火去应力处理采用热处理炉或小型电加热器进行加热处理。
退火去应力加热炉必须符合以下要求:5.1、热处理炉的有效加热区必须定期检测,应符合JB/T10175标准中V类及以上要求,校检周期为一年一次,检验方法按照GB/T9452进行,校检后必须提供正规的校检报告。
热处理工艺守则

热处理工艺守则1、主题内容和适用范围本规程规定了焊后热处理的条件,热处理方法和工艺规范。
本规程适用于压力容器产品及其零部件的焊后热处理。
2、引用标准下列标准如已修订,则按最新版本执行。
TSG R0004-2009 固定式压力容器安全技术监察规程(简称《固容规》)第4.6条。
GB/T30583-2014 承压设备焊后热处理规程NB/T47015-2011 压力容器焊接规程GB150.4 压力容器制造、检验和验收第8条3、进行热处理的条件3.1 压力容器焊后热处理除遵守本守则外,还应符合设计文件与合同的要求。
3.2 焊后热处理应在产品焊接工作全部结束并且经过检验合格后,在耐压试验前进行。
3.3 钢制压力容器的焊后热处理应遵守GB/T 30583的相应规定。
3.4 碳钢和低合金钢制焊件低于490℃的热作用,高合金钢制焊件低于315℃的热作用均不作为焊后热处理对待。
3.5 《固容规》引用标准要求和设计图样要求进行焊后热处理。
3.6 钢板冷成形受压元件,符合下列任意条件之一,且变形率超过表9-1的范围,应于成形后进行相应热处理恢复材料的性能。
a)盛装毒性为极度或高度危害介质的容器;b)图样注明有应力腐蚀的容器;c)对碳钢、低合金钢,成形前厚度大于16mm者;d)对碳钢、低合金钢,成形后减薄量大于10%者;e)对碳钢、低合金钢,材料要求做冲击试验者。
表 9-1 冷成形件变形率控制指标3.7 GB150.4第8.2.2条规定,容器及其受压元件符合下列条件之一者,应进行焊后热处理,焊后热处理应包括受压元件及其与非受压元件的连接焊缝。
(1)焊接接头厚度(即焊后热处理厚度,δPWHT)符合表9-2的规定者。
(2)图样注明有应力腐蚀的容器。
(3)用于盛装毒性为极度或高度危害介质的碳素钢、低合金钢制容器。
(4)相关标准或图样另有规定时。
3.8 对异种钢材之间的焊接接头,按热处理要求高者确定。
但温度不应超过两者中任一钢号的下相变点A c1。
GB5099修订版与GB5099-94 版主要变化2011

D S= 1 − 2 FR e − 3 Ph FR e
15
Ph D S= 2 F σ e + Ph
16
GB5099.1中F取 中 取 或0.85的 的 对正火或正火后回 较小值 火热处理钢瓶设计F 火热处理钢瓶设计 设计应力系 值取用0.82, 值取用 , GB5099.3中F ≤0.85 中 数F值的取 值的取 对淬火后回火热处 用 0.6 理的钢瓶设计F值取 理的钢瓶设计 值取 GB5099.4中F取 Re Rg 或0.85的 中 取 的 用0.77 较小值
GB5099报批稿与 报批稿与GB 5099-94主要变化 报批稿与 主要变化
序号 13 修订内容 钢管探伤 GB 5099-94 气瓶制造厂应抽查 10%进行探伤 进行探伤 5.2.4.1条规定: 条规定: 条规定 淬火后回火处理的最 大抗拉强度不应大于 1000N/mm2, 小容积钢瓶最大抗拉 强度不应大于 1100N/mm2, 对具有应力腐蚀倾向 的介质,抗拉强度不 的介质, 应大于880N/mm2 。 应大于 GB 5099-报批稿 报批稿 要求钢管厂100%探伤,删去气 探伤, 要求钢管厂 探伤 瓶厂复探要求。 瓶厂复探要求。 不分大、中、小容积,对于铬钼 不分大、 小容积, 钢材料,淬火后回火热处理的 钢材料, Rm应小于 应小于1100 MPa;正火钢瓶 应小于 ; Rm小于 小于800 MPa。 小于 。 当选用淬火+ 当选用淬火+回火钢瓶设计取用 950 MPa≤Rm<100 MPa时,对 < 时 瓶体材料中S、 的含量限定为 瓶体材料中 、P的含量限定为 S≤0.010,P≤0.020,S+P≤0.025 对盛装具有氢脆危险或应腐蚀倾 向介质的钢瓶,应采用 应采用GB5099.4, 向介质的钢瓶 应采用 瓶体材料的最大抗拉强度不大于 880MPa。 。
JB 8434—96 热处理环境保护技术要求

热处理环境保护技术要求JB 8434—96中华人民共和国机械工业部1996—09—03批准1997—07—01实施前言本标准为贯彻《中华人民共和国环境保护法》,防止和控制热处理对环境的污染而制订。
本标准由机械工业部环境保护机械标准化技术委员会提出并归口。
本标准负责起草单位:机械工业部武汉材料保护研究所。
本标准主要起草人:张炼、郦振声。
本标准于1996年9月3日首次发布。
1 范围本标准规定了热处理环境污染的分类及污染物的控制与排放标准等技术要求。
本标准适用于从事热处理生产的车间和工厂。
2 引用标准下列标准所包含的条文,通过在本标准中引用而构成为本标准的条文。
本标准出版时,所示版本均为有效。
所有标准都会被修订,使用本标准的各方应探讨使用下列标准最新版本的可能性。
GBJ 4—73 工业“三废”排放试行标准GB 87—85 工业企业噪声控制设计规范GB 3095—82 大气环境质量标准GB 5085—85 有色金属工业固体废物污染控制标准GB 5086—85 有色金属工业固体废物浸出毒性试验方法标准GB 5087—85 有色金属工业固体废物腐蚀性试验方法标准GB 5088—85 有色金属工业固体废物急性毒性初筛试验方法标准GB 8702—88 电磁辐射防护规定GB 8978—88 污水综合排放标准GB 12348—90 工业企业厂界噪声标准GB 14500—93 放射性废物管理规定JB/T 5073—91 热处理车间空气中有害物质的限值JB/T 6074—92 热处理盐浴有害固体废物无害化处理方法TJ 36—79 工业企业设计卫生标准ZB J71 00l一90 热处理盐浴有害固体废物污染管理的一般规定3 热处理环境污染的分类和来源热处理的环境污染分为化学性污染和物理性污染。
化学性污染来自原料、中间反应产物及废弃物中的各种行害物质,主要以废气、废水和固体废物的形式存在;物理性污染主要为噪声和电磁辐射。
其分类和米源列于表1。
ASTM C 1048-04热处理平板玻璃标准规范-HS类、FT类镀膜和非镀膜玻璃

C 1048 -- 04热处理平板玻璃标准规范-HS类、FT类镀膜和非镀膜玻璃1本标准以固定名称C 1048发布;紧随其后的数字表示当前版本的年份,或修订的年份。
圆括号中的数字表示最近重批的年份。
希腊字母上标(ε)表示因最近修订或重批的版次变化。
本标准已由国防部代理机构批准使用。
1. 范围1.1 本规范规定了用于一般建筑物结构中的有涂层和非涂层平板热强化和平板全钢化玻璃的要求。
1.2 以国际标准单位规定的尺寸值视为标准。
圆括号中给出的单位仅供参考。
1.3 以下安全伤害警告仅适合于本规范的第11章测试方法部分:本标准无意涉及所有安全性能,即便有,也与其使用相联系。
本标准的使用者有责任在使用前,进行恰当的安全性和人身健康试验并决定整的其适用性。
22. 引用文件2.1 ASTM标准:C 162玻璃和玻璃产品术语3C 346 陶瓷材料45°镜面光泽试验方法4C 724 建筑型玻璃上陶瓷装饰材料抗酸性试验方法3C 978 透明玻璃基体使用偏光显微镜和光学迟滞补偿程序的残余应力光弹性确定试验方法3C 1036 平板玻璃标准规范3C 1203 陶瓷玻璃釉的抗碱性定量确定试验方法3C 1279 退火、热强化和全钢化平板玻璃边部和表面应力的非破坏光弹性测量的试验方法32.2 ANSI标准:Z97.1 建筑用安全玻璃材料的安全性能规范和试验方法52.3 其他文件CPSC 16 CFR1201-有关建筑玻璃材料的消费者产品安全委员会标准63. 术语3.1 定义:本规范所使用术语的定义参见术语C 162和规范C 1036。
4. 分类4.1 种类:按规定(见第6章),在本规范下加工的平板玻璃应为以下种类:4.1.1 HS类:热强化玻璃应是符合C 1036规范适用要求经进一步加工以符合下文有关热强化玻璃的规定要求的透明的或压花的平板玻璃。
4.1.2 FT类:全钢化玻璃应是符合C 1036规范并经进一步加工以符合下文有关全钢化玻璃的规定要求的透明的或压花的平板玻璃。
GB5099修订版与GB5099_94_版主要变化2011

880MPa。
GB5099报批稿与GB 5099-94主要变化
序号 修订内容
GB 5099-94 (中径公式)
瓶体设计最 S= Ph D
15 小壁厚计算
GB5099报批稿与GB 5099-94主要变化
序号 修订内容
GB 5099-94
GB 5099-报批稿
39 标志
8.1.1 钢印标记
钢瓶钢印标记中的实测水容积 更改为公称水容积。
谢谢 2011-4-25
放映结束 感谢各位的批评指导!
谢 谢!
让我们共同进步
知识回顾 Knowledge Review
GB5099.3中F ≤0.85
理的钢瓶设计F值取 用0.77
0.6
GB5099.4中F取 Re Rg 较小值
或0.85的
GB5099报批稿与GB 5099-94主要变化
序号 修订内容
GB 5099-94
GB 5099-报批稿
r≥0.075Do ;
17
凸形底底部 厚度确定
H/D≥0.22 时 S1≥1.5S,S2≥1.5S H/Do≥0.40 时
于1000N/mm2;
抗拉强度小于1100MPa,
4
强度值限 定
小容积瓶最大抗拉强 度不应大于 1100N/mm2;
GB 5099.2淬火后回火处理的钢瓶 抗拉强度大于或等于1100MPa, GB 5099.3正火处理的钢瓶瓶抗拉 强度小于800MPa,
对具有应力腐蚀倾向 GB 5099.4淬火后回火处理的钢瓶
原材料检验规范作业指导书修订稿

原材料检验规范作业指导书公司标准化编码 [QQX96QT-XQQB89Q8-NQQJ6Q8-MQM9N]I C S备案号:Q/SGXNY 神光新能源有限公司企业标准Q/S G X N Y S C00-11-45-2015原材料检验规范2015-08-15发布2015-8-20实施神光新能源有限公司发布目录1目的本规程对产品用外购钢材以及标准连接件、焊接材料进行了重要程度分级、规定了钢材以及标准连接件、焊接材料的抽样比例、检验检测方法和质量检验标准,以防止不合格钢材以及标准连接件、焊接材料的非预期入库,确保采购的原材料符合产品规定的要求。
2范围本规程适用于钢板、角钢、圆钢、焊材、标准连接件的入厂复验和入库验收。
3职责生产技术部技术员负责根据原材料对产品结构安全性的影响程度对原材料进行重要程度分级。
生产技术部理化试验室负责对原材料进行理、化性能试验、无损检测以及有关外部委托检验。
生产技术部质检员负责对原材料进行外观、尺寸检验,并负责组织取样、送样。
生产技术部工艺人员负责对采购焊材进行工艺试验。
生产技术部部长负责对质量异议的裁决。
采购部负责对检验不合格的原材料的退货和重新采购。
4相关标准G B700-2006碳素结构钢G B/T1591-2008低合金高强度结构钢G B/706-2008热轧型钢G B/T709-2006热轧钢板尺寸、外形重量及允许偏差G B5313-1985厚度方向性能钢板G B/T5213-2008冷轧低碳钢板及钢带G B/T3277-1991花纹钢板G B/T11263-2005热轧H型钢和剖分T型钢G B3274-2007碳素结构钢和低合金结构钢热轧厚钢钢板和钢带G B/T228-2002金属材料室内拉伸试验方法G B/T247-2008钢板和钢带检验、包装、标志及质量证书的一般规定G B/T2101-2008型钢验收、包装、标志及质量证书的一般规定G B/T2102-2006钢管验收、包装、标志及质量证书的一般规定G B/T8162-2008结构用无缝钢管G B/紧固件机械性能螺栓、螺钉和螺柱G B/紧固件机械性能螺母、粗牙和螺纹G B/T5780-2000六角头螺栓C级G B/T5781-2000六角头螺栓全螺纹C级G B/T13912-2002金属覆盖层钢铁制品热镀锌层技术要求G B/T3632-2008钢结构用扭剪型高强度螺栓连接副G B95-2002平垫圈C级弹性垫圈技术条件弹簧垫圈G B/T1228-2006钢结构用高强度大六角头螺栓G B/T1229-2006钢结构用高强度大六角头螺母G B/T1230-2006钢结构用高强度垫圈G B/T1231-2006钢结构用高强度大六角头螺栓、大六角头螺母、垫圈技术条件紧固件公差螺栓、螺钉和螺母紧固件公差平垫圈J B4730-2005压力容器无损检测G B/T5117-1995碳钢焊条G B/T5118-1995低合金钢焊条G B/T14957-1994熔化焊用焊丝G B/T5118-1995低合金钢焊条G B/T8110-2008气体保护电弧焊用碳钢、低合金钢用焊丝G B/T12470-2003埋弧焊用低合金钢焊丝和焊剂G B5293-1999埋弧焊用碳钢焊丝和焊剂5钢材以及标准连接件、焊接材料和锌锭重要性分级根据外购钢材以及标准连接件、焊接材料对产品结构安全性的影响程度将其重要性分为A、B、C三级。
碳钢铸件热处理检验规程范本(2篇)

碳钢铸件热处理检验规程范本1. 引言本规程是为了保证碳钢铸件的热处理质量,并确保其满足相关标准要求的,制定的检验规程。
本规程适用于碳钢铸件的热处理过程中的监督检验及验收。
2. 检验准备2.1 检验人员应具备相关的技能和知识,并严格按照规定操作。
2.2 检验设备应符合相关的国家标准和要求,保证能够正常使用。
2.3 检验样品应从合格的生产批次中选择,并进行标识。
3. 检验项目及要求3.1 外观检验3.1.1 确保加工精度和表面质量符合设计要求。
3.1.2 检查零件是否有缺损、裂纹、气孔等缺陷。
3.2 尺寸检验3.2.1 检查零件的重量、长度、宽度、高度等尺寸是否符合设计要求。
3.2.2 确保各部位的尺寸偏差在允许范围内。
3.3 组织结构检验3.3.1 采用金相显微镜方法观察和评估零件的金属组织结构。
3.3.2 确保组织结构均匀、细致,并无明显的缺陷。
3.4 硬度检验3.4.1 采用硬度计测量零件的硬度值。
3.4.2 确保硬度值符合设计要求,并无明显的不均匀性。
3.5 铸件缺陷检验3.5.1 通过X射线或超声波等方法检查零件的铸件缺陷。
3.5.2 确保零件无裂纹、夹杂、疏松等缺陷。
4. 检验方法4.1 外观检验4.1.1 目测外观,检查表面有无明显的缺陷。
4.1.2 使用放大镜或显微镜观察细节,检查是否有微小的缺陷。
4.2 尺寸检验4.2.1 使用测量仪器,如卡尺、游标卡尺等,对尺寸进行测量。
4.2.2 根据设计要求,对测得的尺寸数据进行比对和评估。
4.3 组织结构检验4.3.1 提取合适的试样,并使用金相显微镜观察其组织结构。
4.3.2 根据相关标准对观察到的组织结构进行评估。
4.4 硬度检验4.4.1 使用硬度计对试样进行硬度测量。
4.4.2 根据设计要求,对测得的硬度值进行比对和评估。
4.5 铸件缺陷检验4.5.1 使用X射线或超声波等设备对试样进行缺陷检测。
4.5.2 根据相关标准对检测结果进行评估。
- 1、下载文档前请自行甄别文档内容的完整性,平台不提供额外的编辑、内容补充、找答案等附加服务。
- 2、"仅部分预览"的文档,不可在线预览部分如存在完整性等问题,可反馈申请退款(可完整预览的文档不适用该条件!)。
- 3、如文档侵犯您的权益,请联系客服反馈,我们会尽快为您处理(人工客服工作时间:9:00-18:30)。
热处理检验方法和规范公司标准化编码 [QQX96QT-XQQB89Q8-NQQJ6Q8-MQM9N]热处理检验方法和规范金属零件的内在质量主要取决于材料和热处理。
因热处理为特种工艺所赋予产品的质量特性往往又室补直观的内在质量,属于“内科”范畴,往往需要通过特殊的仪器(如:各种硬度计、金相显微镜、各种力学性能机)进行检测。
在GB/T19000-ISO9000系列标准中,要求对机械产品零部件在整个热处理过程中一切影响因素实施全面控制,反映原材料及热处理过程控制,质量检验及热处理作业条件(包括生产与检验设备、技术、管理、操作人员素质及管理水平)等各方面均要求控制,才能确保热处理质量。
为此,为了提高我公司热处理产品质量,遵循热处理相关标准,按零件图纸要求严格执行,特制定本规范一、使用范围:本规范适用于零件加工部所有热处理加工零件。
二、硬度检验:通常是根据金属零件工作时所承受的载荷,计算出金属零件上的应力分布,考虑安全系数,提出对材料的强度要求,以强度要求,以强度与硬度的对应关系,确定零件热处理后应具有大硬度值。
为此,硬度时金属零件热处理最重要的质量检验指标,不少零件还时唯一的技术要求。
1、常用硬度检验方法的标准如下:GB230金属洛氏硬度试验方法 GB231金属布氏硬度试验方法GB1818金属表面洛氏硬度试验方法 GB4340 金属维氏硬度试验方法GB4342金属显微维氏硬度试验方法 GB5030 金属小负荷维氏试验方法2、待检件选取与检验原则如下:为保证零件热处理后达到其图纸技术(或工艺)要求,待检件选取应有代表性,通常从热处理后的零件中选取,能反映零件的工作部位或零件的工作部位硬度的其他部位,对每一个待检件的正时试验点数一般应不少于3个点。
通常连续式加热炉(如网带炉):应在连续生产的网带淬火入回火炉前、回火后入料框前的网带上抽检3-5件/时。
且及时作检验记录。
同时,若发现硬度超差,应及时作检验记录。
同时,若发现硬度越差,应及时进行工艺参数调整,且将前1小时段的零件进行隔离处理(如返工、检)。
通常期式加炉(如井式炉、箱式炉):应在淬火后、回火后均从料框的上、中、下部位抽检6-9件/炉,且及时作检验记录。
同时,若发现硬度超差,应及时进行工艺参数调整,且将该炉次的零件进行隔离处理(如返工、逐检)。
通常感应淬火工艺及感应器与零件间隙精度调整,经首件(或批)感应淬火合格后方可生产,且及时作检验记录。
3、硬度测量方法:各种硬度测量的试验条件,见下表1:测量硬化层深度不同的零件表面硬度时,硬度试验方法与试验力的一般选择,见表2:经不同热处理工艺处理后的表面硬度测量方法及其选择,见小表3:(2)若确定的硬度试验方法有几种试验力可供选择时,应选用试验条件允许的最大试验力。
4、检验设备与人员:所有硬度计及标准硬度试块均应在计量部门检定的有效期内使用,不允许在无检定合格证书或超过检定的有效期使用。
应设立专职检验人员,且经正规培训与考核,具有正式的资格证书;生产线的操作人员检验,应经一定培训,在专职检验人员的认可或指导下进行。
5、测量数据的表示与记录:硬度值的表示应按相应国家标准硬度试(检)验方法的规定,一般以硬度范围法表示,标出上、下限值,如60-65HRC;特殊情况液可以只标下限值或上限值,应用不小于或不大于表示,如不大于229HBS;若记录换算硬度值时,应在换算值后面加括号注明实测值【如:()】;若记录硬度平均值时,应在硬度值平均值后米那加括号注明计算平均值所用的各测点硬度值【如:(、、)】检验报告记录,包括零件名称、材料、检验数量、检验结果及检验人员与日期。
三、金相试验金相分析时用金相显微镜观察金属内部的组成相及组织组成物的内型以及它们的相对量、大小、形态及分布等特征。
材料的性能取决于内部的组织形态,而组织又取决于化学成分及加工工艺,热处理时改变组织的主要工艺手段,因此,金相分析是材料及热处理质量检验与控制的重要方法。
1、通常金相检验方法的标准如下:GB/T11354-1989 钢铁零件渗氮层深度测测定和金相组织检验GB/T9450-1988 钢铁渗碳淬火有效硬化层深度的测定与校核GB/T9451-1988 钢件薄表面总硬化层深度或有效硬化层深度的测定GB/T5617-1985 钢的感应淬火或火焰火后有效硬化层深度的参定JB/T9204-1999 钢件感应淬火金相检验JB/T9211-1999 中碳钢与中碳合金结合钢马氏体等级JB/T7710-1995 薄层碳氮共渗或薄层渗碳显微组织检验GB/T13298-1991 金相显微组织检验方法GB/T13299-1991 钢的显微组织评定方法GB6394-86 金属平均晶粒度测定法NJ309-83 内燃机连杆螺栓金相检验标准NJ326-84 内燃机活塞销金相检验标准2、金相试样的选取与检验步骤:金相试样的选取:2.1.1纵向取样:纵向取样是指沿着刚材的锻扎方向进行取样。
主要检验内容为:非金属夹杂物的变形程度、晶粒畸变程度、碳化物网、变形后的各种组织形貌、热处理的全面情况等。
横向取样横向取样指垂直于钢材的锻扎方向进行取样。
主要检验内容为:金属材料从表层到中心的组织、显微组织状态、晶粒度级别、碳化物网、表面缺陷深度、氧化层深度、腐蚀层深度、表面化学热处理及镀层厚度等。
缺陷或失效分析取样:截取缺陷分析的试样,应包括零件的缺陷部分在内;或在缺陷部分附近的正常部位取样进行比较。
为此,通常检验零件的最重要项目为表层显微组织观察和硬化层深度测定,应横向取样;但紧固体的螺纹部分的渗层检验需要纵向取样。
金相检验步骤:选样——金相切割机(或线切割机)取样—镶嵌机加热镶嵌-磨抛机磨光/抛光-化学腐蚀(通常用4%硝酸酒精溶液)-金相观察/硬化层深度(或显微硬度)测定-出具检验报告取样数量:通常连续式加热炉(如网带炉):1件/4小时通常周期式加热炉(如井式炉、箱式炉):2-3件/炉(装炉夹具不同部位)备注:(1)金相试样以磨面面积小于400MM2,高度15-20MM为宜。
(2)试样的制备过程中,部允许因受热而导致组织变化,应避免试样边缘出现圆角并防止改变斜截面试样的角度。
3、金相组织观察于判别:渗碳或碳氮共渗:适用于08F、Q235AF、20、20Cr等低碳或低合金钢的零件。
试样应从渗碳或碳氮共渗零件上切取。
液可用于钢件的材质,热处理状态,有效厚度一致,避过经同炉渗碳或碳氮共渗处理的试样。
薄层碳氮共渗件(层深≤),表层碳含量应不低于%,氮含量应不低于%。
薄层渗碳钢件(层深≤)表层碳含量应不低于%渗层显微组织评级在淬火状态下进行(放大倍率为400倍)。
针状马氏体级别及残余奥氏体级别评定:当渗层显微组织主要为针状马氏体时,依据JB/T7710-1995标准图谱共分1-5级,其中1-2级合格。
板条马氏体级别评定:当渗层显微组织主要为板条马氏体时,依据JB/T7710-1 995标准图谱共分1-5级,其中1-2级合格。
渗层(层深≤)碳化物级别评定:依据NJ326-84标准图谱共分1-5级,其中1-3级合格。
心部铁素体级别评定:依据JB/T7710-1995标准图谱共分1-5级,其中一般零件1-4级合格,重要零件1-3级合格。
渗氮或碳氮共渗(软氮化):3.2.1渗氮前调质组织的检验:渗氮前调质组织级别(对大工件可在表面2mm深度范围内检查),依据GB/T11 354-1989标准图谱(放大倍率为500倍),回火索氏体中游离体素体数量共分1-5级,其中一般零件1-3级为合格,重要零件1-2级为合格。
渗氮零件的工作面部允许由脱碳层或粗大的回火索氏体组织。
试样应从渗碳零件上垂直于渗氮表面切取,也可用与零件的材料、处理条件、加工精度相同,并经同炉渗氮处理的试样;检验部位应具有代表性,若检查渗氮层脆性的试样,表面粗糙度要求>-0.63mm,但不允许把化合物磨掉。
渗氮层脆性检验:经气体渗氮的零件,必须进行脆性的检验。
依据GB/T11354-1989标准图谱(放大倍率为100倍),渗氮层脆性级别按维氏硬度压痕边角碎裂程度共分1-5级,其中一般零件1-3级为合格,重要零件1-2级为合格。
检验渗氮层脆性,采用维氏硬度计,试验力规定用(10kgf),加载必须缓慢(在5-9s内完成),加载后停留5-10s,然后去载荷,同时,每制件至少测3点,其中2点以上处于相同级别时,才能定级,否则,需重新测定一次。
如由特殊情况经有关各方协商,亦可采用(5kgf)或(30kgf)的试验力,但需按下表4的值换算。
由磨量的零件也可在磨去加工余量后表面上测定。
渗氮层疏松检验:经氮碳共渗(软氮化)的零件,必须进行疏松检验。
依据GB/T11354-1989标准图谱(放大倍率为500倍)取其疏松最严重的部位,渗氮层疏松级别按表面化合物内微孔的形状、数量、密集程度共分1-5级,其中一般零件1-3级为合格,重要零件1-2级为合格。
渗氮扩散层中氮化物检验:气体渗氮的零件必须进行氮化物检验。
依据GB/T11354-1989标准图谱(放大倍率为500倍),去其组织中最差的部位,渗氮层中氮化物级别按情况共分1-5级,其中一般零件1-3级合格,重要零件1-2级为合格。
感应淬火:适用于中碳碳素钢(如45钢)和中碳合金钢(如40Cr)的机械零件。
零件淬火后,表面不应有裂纹,灼伤等缺陷。
零件经淬火,低温回火(≤200℃),金相组织按GB/T5617-1985标准共分1-1 0级,规定如下:硬度下限≥55HRC时,3-7级为合格。
硬度下限<55HRC时,3-9级为合格。
4、硬化层深度的测定方法:硬化层深度的测定方法分为金相法和硬度法两种,有争议时,以硬度法作为仲裁方法。
测定表面淬火【如感应淬火】、化学热处理【如渗碳、碳氮共渗、渗氮、氮碳共渗(软氮化)】及其他各种表面强化层深度时金相检验的重要内容。
根据硬化层深可以分为大于0.3mm的两种情况。
金相法:层深>0.3mm的表面硬化层测定方法:从零件表面垂直方向测量到规定的某种显微组织边界的距离。
测定层深时,各种强化工艺所规定的特征组织,见下表5:从表面垂直方向测量到与基体金属间的显微组织没有明显变化处的距离,即总硬化层深度。
硬度法:从零件表面垂直方向测量到规定的显微硬度硬化层处的距离。
测定层深时,各种强化工艺下有效硬化层评定的参数,见下表6:强化工艺有效硬化层界限硬度(HV)推荐试验力/N国家标准感应淬火DS2GB5617-1985渗C,CN共渗DC550GB9450-1988渗N,NC共渗(软氮化)DN比基体硬度高50说明1HVMS为技术要求规定的最低表面硬度2 ( )内的数值为允许试验力范围渗碳和碳氮共渗共渗有效硬化层(DC),经热处理至最终硬度值后,离表面三倍于有效硬化层处硬度小于450HV的零件,可采用比550HV大的界限硬度值(以25HV为一级)来测定有效硬化层深度。